
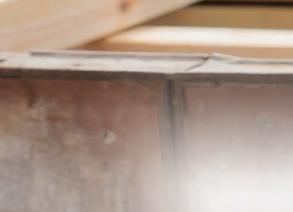


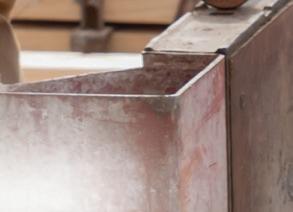

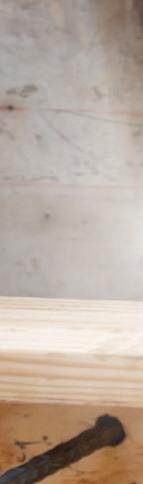
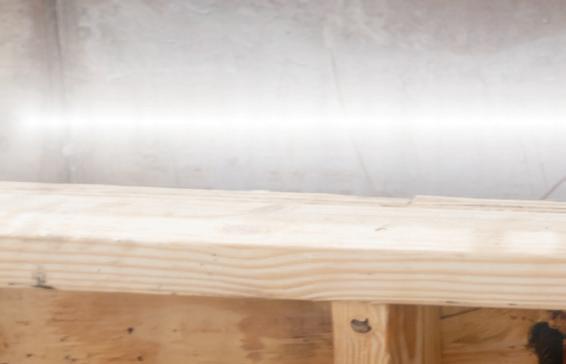
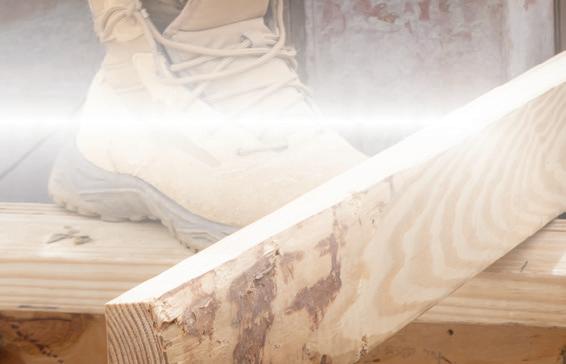
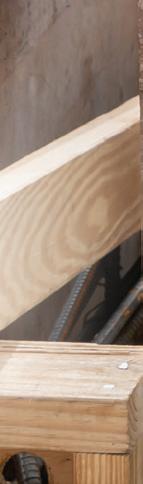
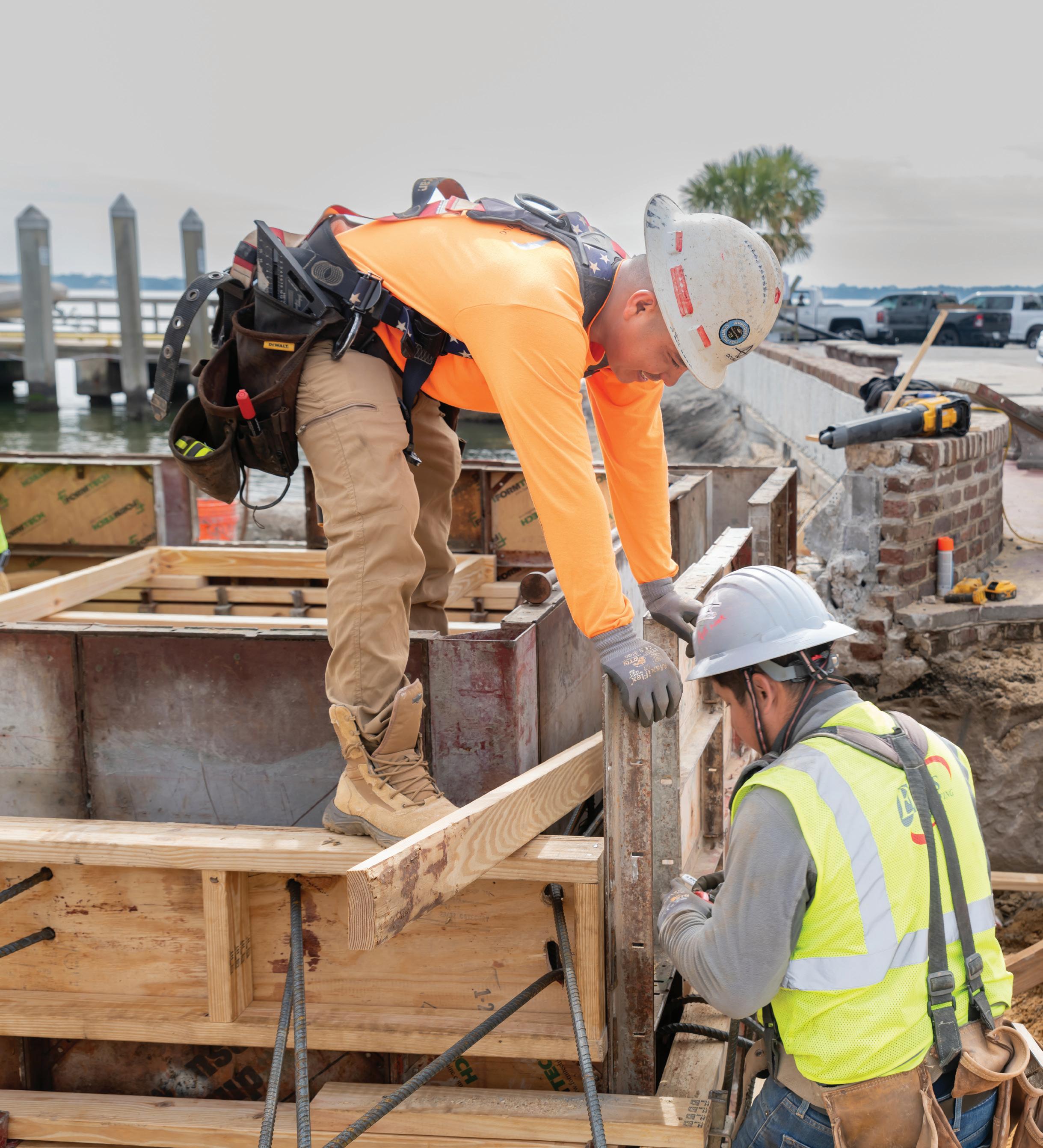
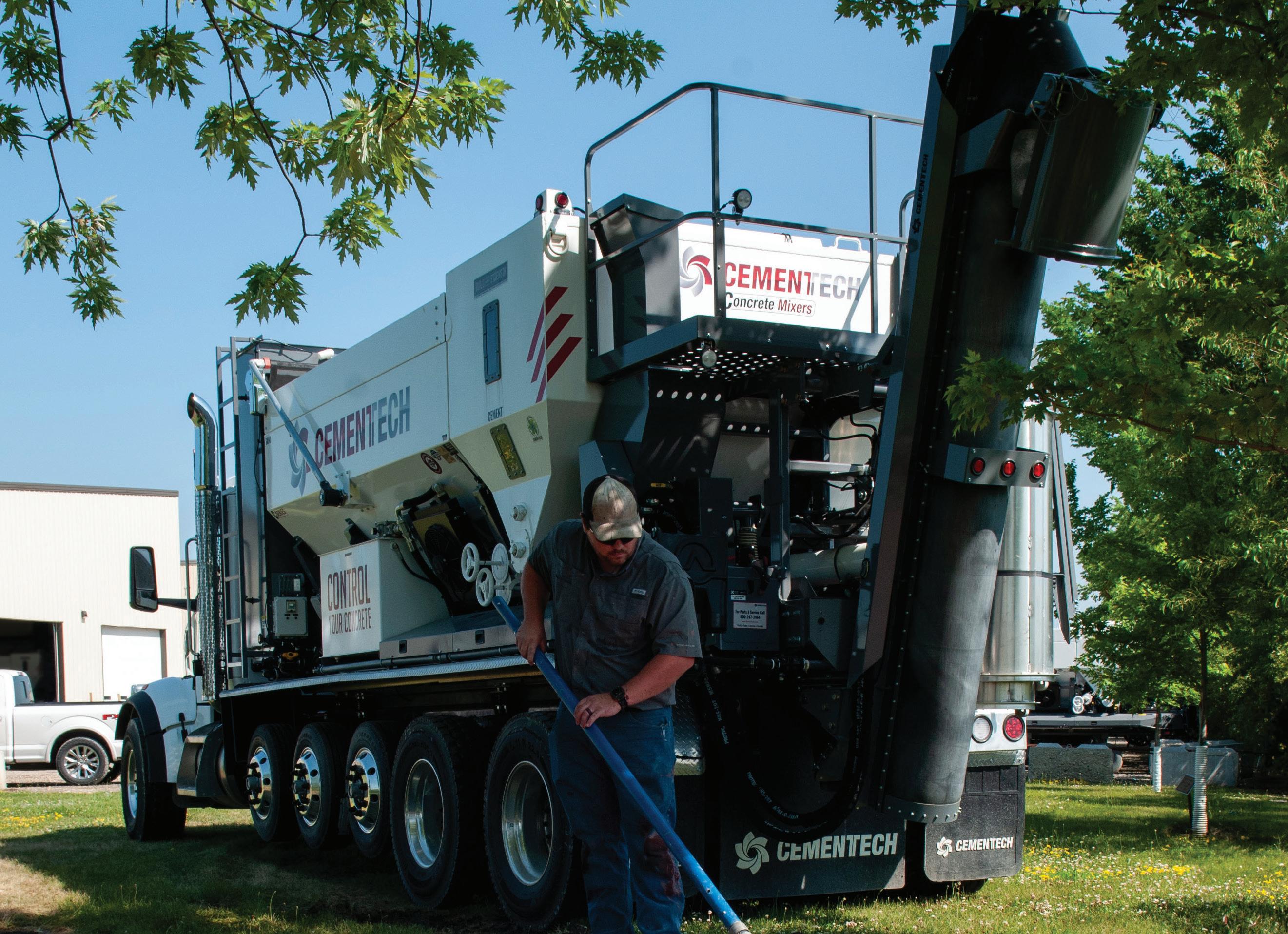
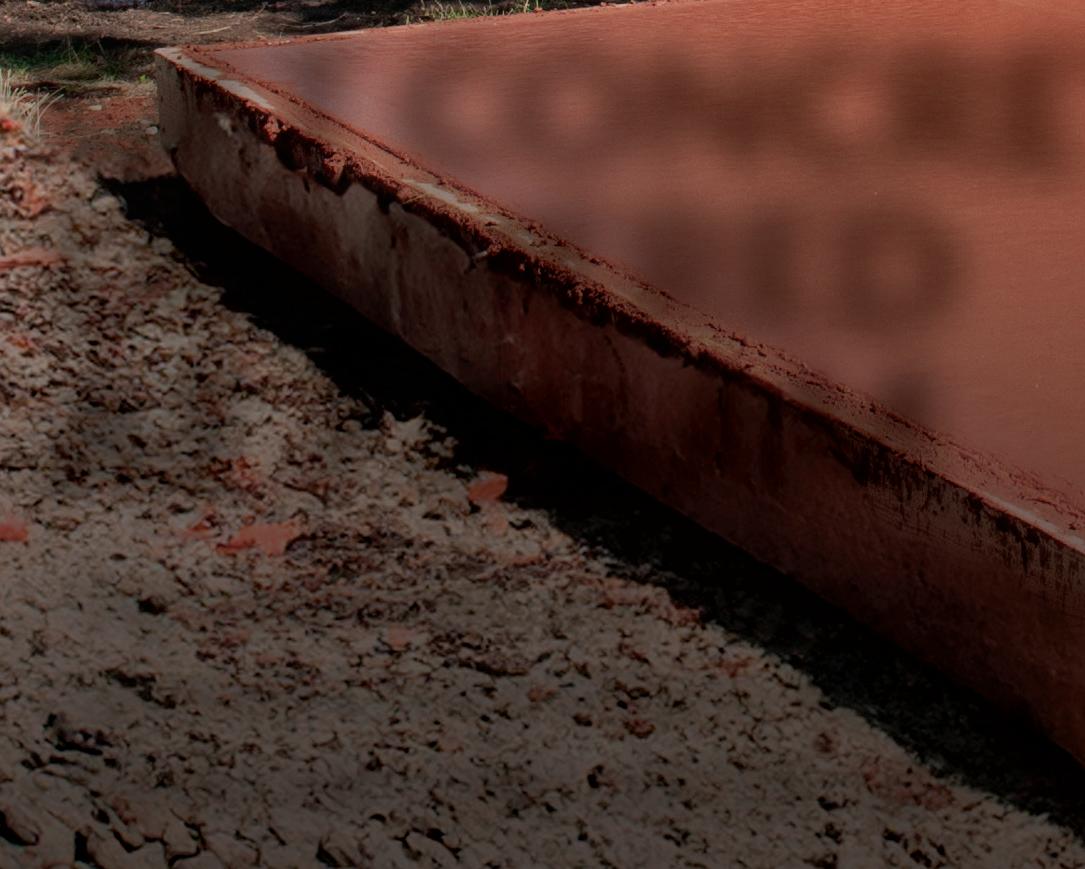


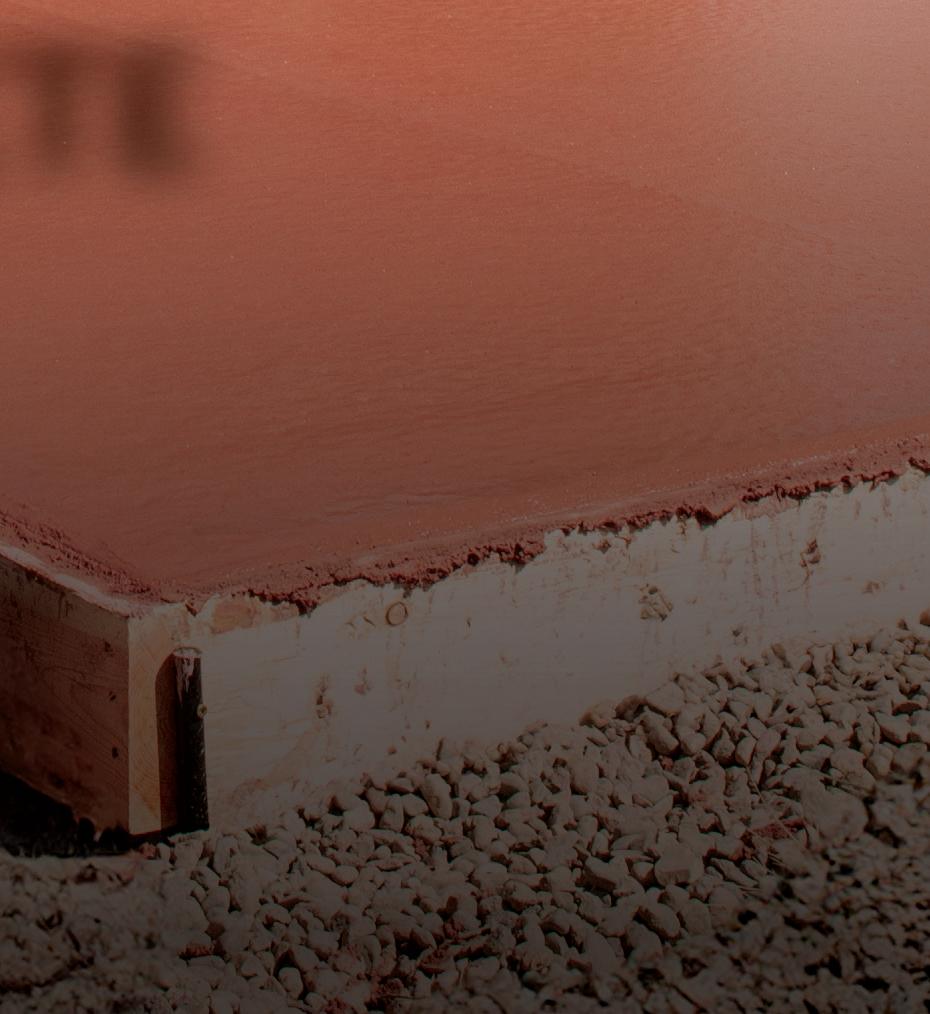

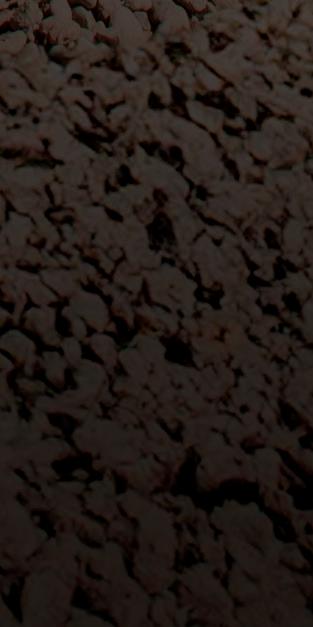
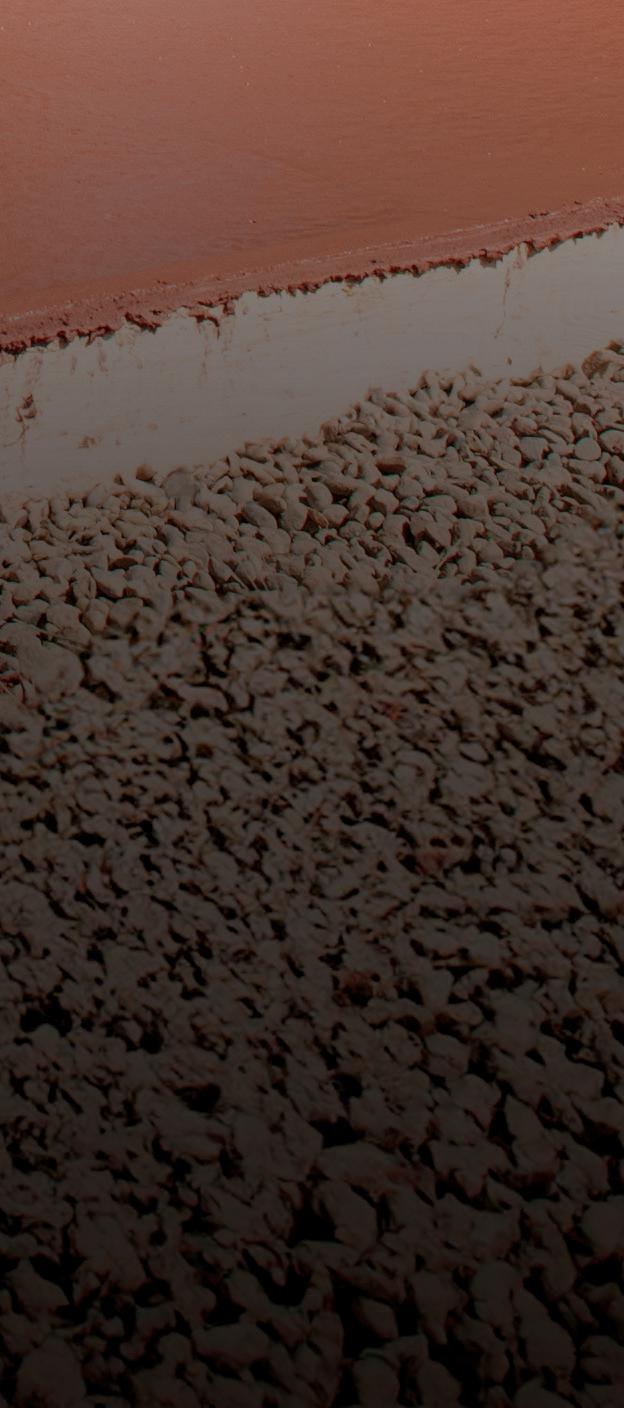
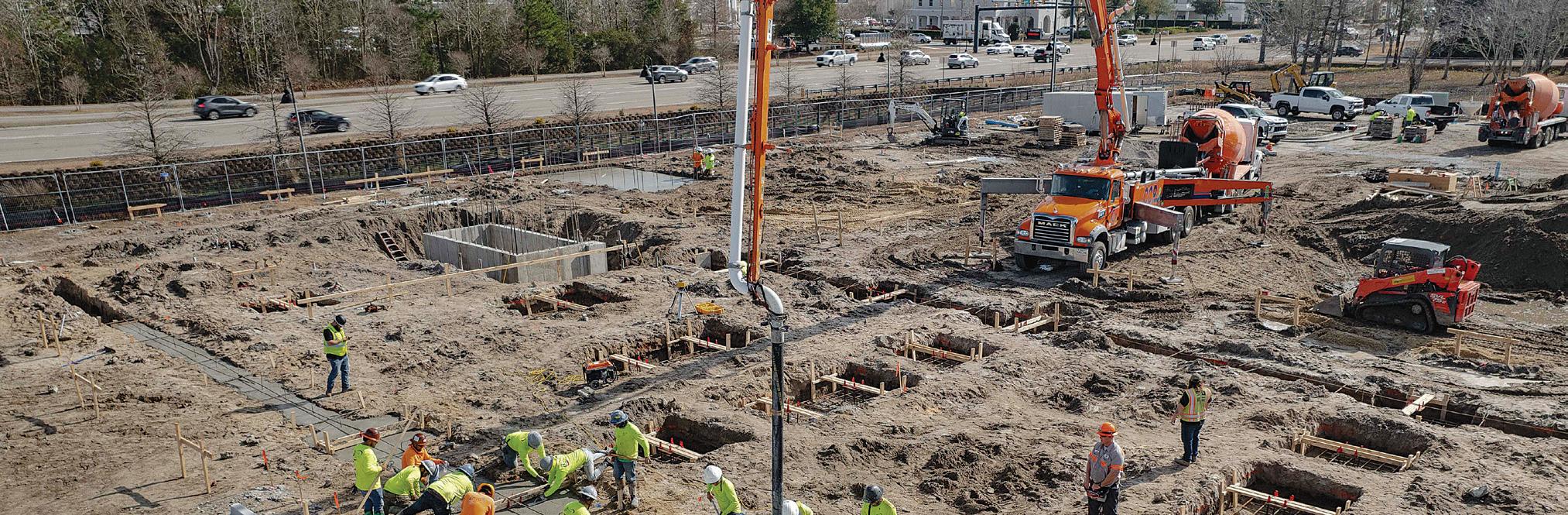

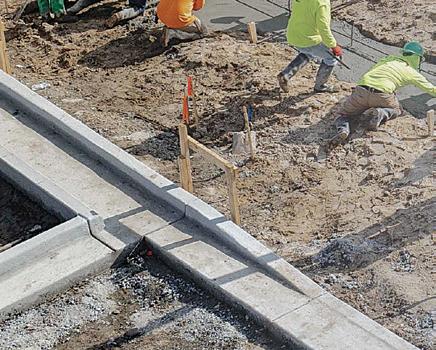
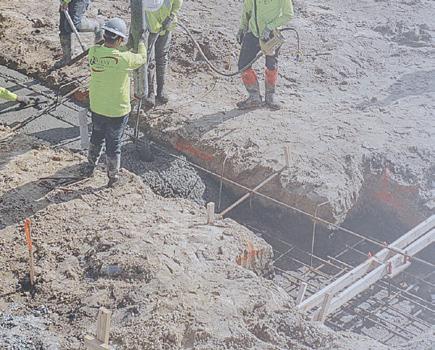
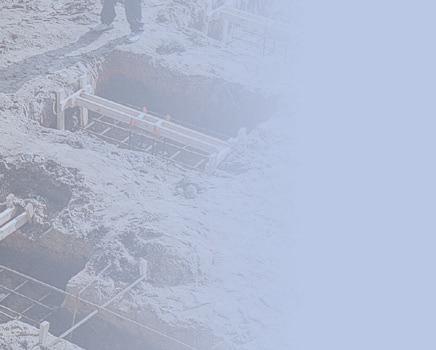

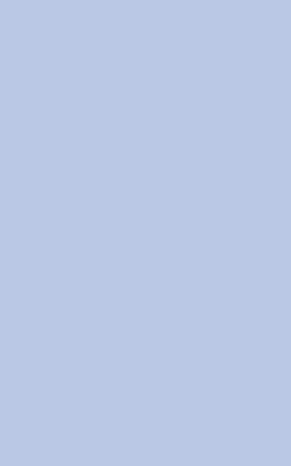
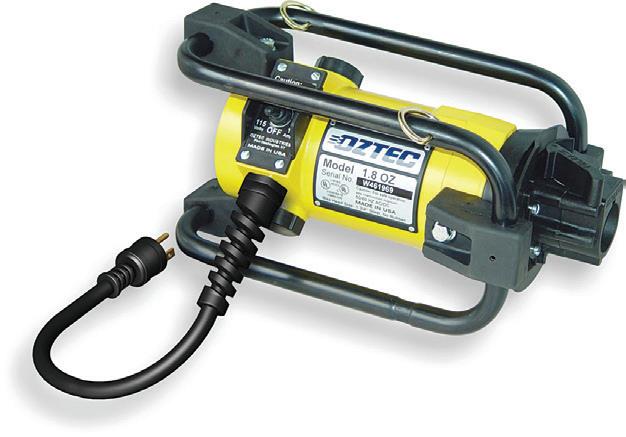
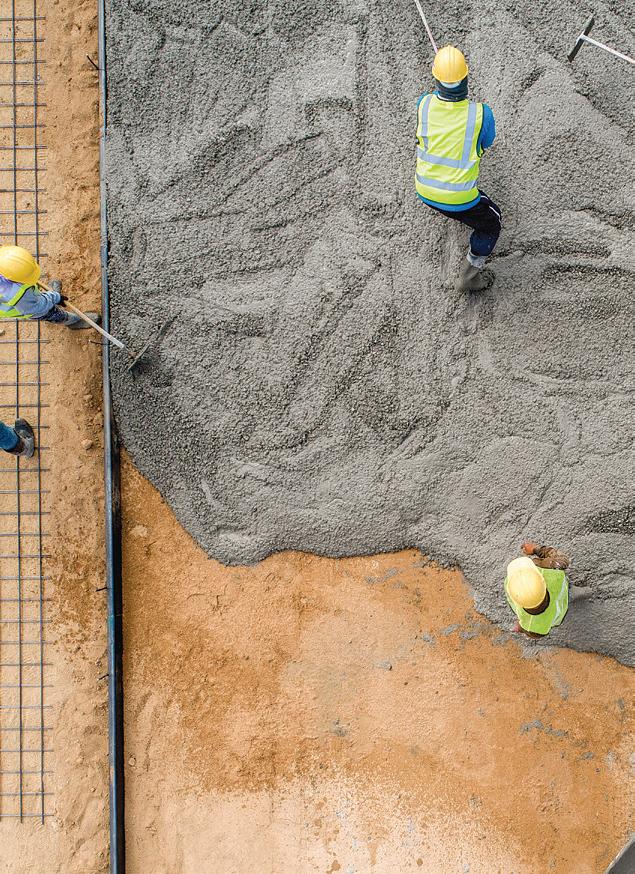
JONATHAN KOZLOWSKI, jkozlowski@iron.markets
JONATHAN KOZLOWSKI, jkozlowski@iron.markets
In general, it seems the largest issue facing the construction industry is a shortage of skilled labor. That and the cost of everything. Sadly, employee retention seems to be the foundation of many problems construction professionals and concrete contractors like yourself face today. The disparity between new workers that stay versus experienced people retiring or leaving has been such an issue that it’s often the first subject that comes to mind in conversations about industry challenges.
Don Weaver, president of Weaver-Bailey Contractors Inc., tells me that according to the latest information for every 5 Baby Boomers who retire, only 2 workers from a younger generation are taking their place. Weaver is also first vice chair (incoming chair) of the American Concrete Pavement Association Board of Directors.
Weaver-Bailey are engaging their community, recruiting at local high schools and colleges. In the last 18 months, the company has hired 150 employees only to find 50 who stayed. They attend local events like “Be Pro Be Proud” sponsored by their state chamber of commerce. As described on their website, this event is one of the leading movements to bring a new generation of pride, progress, and professionals to the country’s skilled workforce. So far, they’ve taken root in 6 states: Arkansas, Georgia, North Carolina, South Carolina, Tennessee, Texas, and New Mexico.
Weaver explains that the organization holds events at high schools with engaging activities like providing an opportunity for students to experience simulators and introduce them to trade equipment like track hoes, dozers, trucks, and welding equipment. Sounds pretty cool. In that mindset, how are you reaching out and filling your ranks? Let me know—help me share your story because your efforts will change things.
Before you turn the page, the ForConstructionPros.com family have announced a brand new award designed for the people who make this industry great: you. We’re calling it the PACER award to celebrate those who truly are making an impact.
Find details on page 35, via the QR code above, or at https://CONC.me/PACERaward. Ok, that’s enough out of me. Enjoy this issue. Thank you.
Get industry news and expert insights delivered straight into your inbox. Stay up to date on the latest happenings across the concrete industry with our our e-newsletter, In The Mix. Scan the QR code to subscribe. https://CONC.me/newsletters
ADVISORY BOARD
Kim Basham
KB Engineering Cheyenne, Wyo.
James Baty II
Concrete Foundations Association Mt. Vernon, Iowa
Dennis Purinton Purinton Builders, Inc. East Granby, Conn.
Jim Cuviello Cuviello Concrete Polished | Stained | Crafted Stevensville, Md.
Chris Klemaske
T.B. Penick & Sons, Inc. San Diego, Calif.
@vaivirga - stock.adobe.com
EDITORIAL
Editor Jonathan Kozlowski jkozlowski@iron.markets
Managing Editor Gigi Wood gwood@iron.markets
Junior Editor Merina Shriver mshriver@iron.markets
AUDIENCE
Audience Development Manager Angela Franks
PRODUCTION
Senior Production Manager Cindy Rusch crusch@iron.markets
Art Director Flatworld Solutions
ADVERTISING/SALES
Brand Manager, OEM & Construction Nikki Lawson nlawson@iron.markets
Sales Representative Kaylee Kidd kkidd@iron.markets
IRONMARKETS
Chief Executive Officer Ron Spink
Chief Revenue Officer Amy Schwandt VP, Finance Greta Teter VP, Marketing & Audience Development Ronda Hughes VP, Operations & IT Nick Raether VP, Demand Generation & Education Jim Bagan
Corporate Director of Sales Jason DeSarle
Brand Director, Construction, OEM & IronPros ......... Sean Dunphy
Content Director .................................................Marina Mayer
Director, Online & Marketing Services ......... Bethany Chambers Director, Event Content & Programming .......... Jess Lombardo
CIRCULATION & SUBSCRIPTIONS
P.O. Box 3605, Northbrook, IL 60065-3605 (877) 201-3915 | Fax: (847)-291-4816
circ.ConcreteContractor@omeda.com
LIST RENTAL
Sr. Account Manager Bart Piccirillo | Data Axle (518) 339 4511 | bart.piccirillo@infogroup.com
REPRINT SERVICES
Brand Manager, OEM & Construction ................ Nikki Lawson nlawson@iron.markets
Published and copyrighted 2024 by IronMarkets.All rights reserved. No part of this publication may be reproduced or transmitted in any form or by any means, electronic or mechanical, including photocopy, recording, or any information storage or retrieval system, without written permission from the publisher.
DAP has introduced the new HD Max Construction Adhesive, a hybrid formula with polyurethane strength that provides durability and powerful adhesion even in extreme temperatures. Built for tough applications, DAP’s HD Max is available in a 28-fl.-oz. cartridge. Featuring polyurethane strength, HD Max bonds on various materials and surfaces from non-porous substrates like aluminum, PVC and mirror to porous, textured materials like brick, concrete and drywall in both indoor and outdoor environments. Whether working in scorching heat or freezing cold, HD Max features the ability to bond in extreme temperatures, as it can be gunned out and bonded anywhere from 0-120° F.
https://CONC.me/blon5mih
MCI-2018 X is a 100% silane penetrating water repellent for concrete surfaces and is MCI-2018 minus the migrating corrosion inhibitors. Its primary function is to line concrete substrate pores with a hydrophobic layer that reduces the ingress of moisture, chlorides and carbonation, extending the service life of the structure. If applied after a penetrating surface applied corrosion inhibitor, MCI-2018 X prolongs the protection period of the corrosion inhibitor. MCI2018 X allows the surface to stay breathable and retain its original appearance. MCI-2018 X can be used for routine maintenance every five to 10 years or used as part of the finishing touches to a concrete repair. Because it does not change the substrate’s appearance, MCI-2018 X serves as an option for historical restorations.
https://CONC.me/7e5tehu2
MAX USA’s RB443T is the company’s newest addition to its TwinTier platform. The RB443T features an integrated autoload assist mechanism, which accelerates wire loading. Additionally, the RB443T is equipped with an accessible trigger that requires 50% less effort compared to its predecessor, the RB441T. This tool provides a tying speed of less than half a second per tie, approximately 40% faster than its predecessor, the RB441T.
https:// CONC.me/6gbrwoyq
INDCO Quic Mixers provide a portable, lightweight solution for mixing materials in 5-gal. pails. A ring mount provides a low center of gravity for steady mixing in open-topped or closed 5-gal. pails with lids to 12.25 in. Stainless steel folding impellers fit through a 1.5-in. opening. Air or electric motors are available and all models are supplied with quick-change coupler and shaft design featuring a shaft pin that locks in place during rotation. Air operated versions are available with 0.75- or 1.5-hp air motor equipped with control valve to regulate speed from 300 to 3,000 rpm and muffler. Powered by a 0.5-hp totally enclosed fan cooled motor that is ready to plug in to a standard outlet, the single-phase electric motor option operates at a fixed speed of 1,750 rpm (EP version supplied with motor leads only).
Multiquip offers the battery-powered Mix-N-Go Concrete Mixer for concrete projects, rental applications and construction sites. The product features zero emissions and a rechargeable battery drive. Designed with durability, the MixN-Go features a polyethylene drum designed for removal of dried concrete. Complementing this is a heavy-duty steel frame that not only supports the motor and battery assembly but also offers stability during use. Its versatile design includes a pedestal assembly, facilitating the dumping of material into a wheelbarrow. Moreover, equipped with standard pneumatic tires, the mixer can also be used as a wheelbarrow for maneuverability around the jobsite.
https://CONC.me/4rktqgia
RoboFlat is a cloud-based product for concrete floor flatness and levelness testing that is designed to address floor
challenges in a variety of robotic-equipped facilities, and supports testing operations. With RoboFlat, contractors and building owners can meet the required flatness specifications of floors. Users can also upload point cloud data generated from laser scanners, enabling analysis and evaluation and automating multistep processes. RoboFlat supports a range of floor standards that can be tailored to meet specifications. RoboFlat helps remediation teams identify the exact location of flatness issues on the floor slab, generating heat and contour maps with cut and fill values and detailed output that can be overlaid onto the floor design. The product also includes a report generation feature, allowing users to customize reports to share with stakeholders.
https://CONC.me/15vn8rsg
https://CONC.me/6w413qrr
Built to exceed your expectations and outperform the competition. With results in mind, our vibrators are engineered for control and durability, ensuring a smooth and flawless pour every time. With more control over your results and a longer lifespan than other options on the market, our flex shaft concrete vibrators are the perfect choice for the professional looking to take their work to the next level.
EVANS CONTRACTING GROUP OF CHARLESTON, SOUTH CAROLINA, REMINDS US THAT HARD WORK TRUMPS HARDSHIPS AND THE AMERICAN DREAM IS STILL ABLE TO FLOURISH EVEN IN OUR LAGGING ECONOMY.
What would be more rewarding or productive than obsessing over our current cultural division? For two minutes today, tune out the bombastic rhetoric, forget about our polarized political landscape for just a moment, and celebrate one family’s truly remarkable accomplishment and contribution to the concrete industry.
Brothers Jack and JP Evans are on a mission to revitalize the American Dream one construction job site at a time. Raised in rural Tennessee and living off of food stamps, experiencing the tragedy of being orphaned, instead of seeing themselves as victims, today they have a message for America: Work hard and you can be anything you want to be.
The business owners of Evans Contracting Group of Charleston, South Carolina, know firsthand the struggles of poverty and adversity. Statistically speaking, they feel they should have ended up in jail. Their parents were fatalities of America’s substance abuse epidemic, and later after their grandfather who took them in also passed away, their high school guidance counselor took custody of them.
Faced with the choice of being bitter or making life better, they are living examples of how effort and determination pay off. They still believe in the American Dream and beyond that they are working daily to
inspire others to experience the rewards of hard work.
Jack was medically retired from the military after two and half years of Special Forces training led to a disability, and JP rode his football scholarship through college football to graduate in engineering. With military-influenced leadership values and a background in engineering, their combination of talents have allowed these brothers to build a successful company from the ground up.
Jack had spent his entire career after the military working for various subcontractors and general contractors and saw an
opportunity to start the business. JP had spent much of his career working for various vendors and subcontractors—most recently for the largest real estate development company in Chattanooga. With defined roles and responsibilities, the brothers found their skillsets complementary; finding it rewarding to be working together after everything they’ve been through.
Ask any construction company nationwide today, and you will hear about the difficulties of recruiting workers. Because of Jack’s Army background, the brothers have developed a recruiting relationship with the Veterans Affairs so that when military
veterans take off their combat boots they can lace up their work boots. With their cash flow concerns in the rearview mirror, their greatest challenge these days is managing the rapid growth of their company. They have worked on projects from Pittsburgh, Pennsylvania to Tampa, Florida, and recently they have expanded their operations to include having a presence in Chattanooga, Tennessee. This success has motivated the Evans brothers to offer a standard of living to their employees they hope creates intergenerational wealth for their workforce, promising wages that provide the opportunities they didn’t have growing up; they are planning to transition their own company into a 100% employee-owned company to help other construction workers have a standard of living that provides for home ownership and prosperity.
They take the craft of concrete construction seriously and instill a sense of accountability, empowerment, and mentoring throughout their leadership teams. They value emotional intelligence over perfection and have a strong sense of vision and workplace culture. They believe in the power of a strong work ethic, and the value of rewarding workers based on meritocracy.
Amazingly, both of these brothers are under the age of thirty. Last year their concrete construction company grossed $10 million. This year they anticipate grossing over $30 million. It is refreshing to see a family-owned company that takes care of our veterans, respects blue-collar workers, and values the concrete industry all while overcoming some of life’s greatest challenges.
Concrete is the second most used commodity on the planet, our civilization as we know it is completely
built on concrete. Concrete is the vital material that allows us to enjoy the benefits of an infrastructure as advanced as we have, it supports our skyscrapers as well as the foundations for the homes we live in. Therefore, their combination of overcoming serious challenges and contributing to the essential concrete industry is worthy of our attention.
With humble beginnings as onetime wards of the state to sharing an impressive amount of ambition, the Evans brothers remind us that hard work trumps hardships and the American Dream is still able to flourish even in our lagging economy. They exemplify the value of exploring opportunities and pursuing financial success.
Our challenges do not define us, but they do shape our perspective. Turning
MOST MOST CONSISTENT CONSOLIDATION POWERFUL ,
1.75" HEAD, 7' WHIP PER CHARGE, 130 YDS3
MX FUEL™ High Cycle Concrete Vibrator Kit
MXF372-2XC
MX FUEL™ Backpack High Cycle Concrete Vibrator Kit w/ 7' Whip / 1.75" Head
MXF372-2XCB
LEARN MORE
a blind eye to our nation’s problems will not solve them, but obsessing over the negative is equally unhealthy. With all that is supposedly wrong with our country, may we learn the value of focusing on the positive. As depression and suicide continue to skyrocket, perhaps a small fraction of our solution to our collective crisis can be found by highlighting more positivity. Start today by giving some attention to a couple of brothers who beat the odds, because they are a Star Spangled success story.
Craig Cottongim is a second-generation concrete contractor, he writes about the concrete industry and leadership, he can be reached at craigcottongim@gmail.com.
FREES UP LABOR FROM MIXING
ELIMINATES MIX ERRORS
MIXES UP TO 120 GALLONS PER HOUR
SUPPORTS FULL RANGE OF RATIOS FROM 1:1 TO 6:1
REDUCES MATERIAL WASTE
MAXIMIZES MATERIAL WORKING TIME
Oztec Electric Motors are manufactured to exacting specifications to withstand the rough day-to-day abuses associated with construction sites. Lightweight, compact and fitted with the Oztec Quick Disconnect system, this one-man power unit will speed through the stiffest concrete. All Oztec vibrators meet or exceed ACI specification #309.
The ACBe cordless concrete vibration system consists of the backpack with integrated converter, removable/ replaceable BP1000 lithium ion battery and internal vibrator.
• Backpack adjusts for varying heights, sizes with lightweight fabric, padded shoulders and even weight distribution
• Vibrator shaft connects to bottom center of backpack, allowing for easy left-hand or right-hand operation
• Modular vibration system allows use of 1.5-in., 1.8-in. and 2.3-in. internal head diameters and 5-, 10- and 16-ft. shaft lengths
• Integrated converter enables vibrator to provide high-cycle/high-frequency performance
The DEWALT POWERSHIFT
Vibrator delivers the power, ergonomics, and run time that you need to tackle the most demanding placements. A roll cage surrounds the vibrator to protect the battery and the power unit. It delivers 2-1/4 in. head performance and a consistent 12,000 VPM to handle the stiffest slump. This vibrator has 16 head and shaft combinations available (1 1/2, 1 3/4, 2 and 2 1/2-in. heads and shafts at 7’, 10’, 16, and 21’ to complete the day’s work. It also includes remote activation via DEWALT’s Wireless Tool Control technology.
Leveraging a POWERSTATE Brushless Motor, the Milwaukee Tool MX FUEL High Cycle Concrete Vibrator tool sustains 11,500 vpm in stiff concrete. Compliant with ACI and DOT standards for high cycle concrete vibrators, operators can maintain the power to push up to a 2 1/4-in. head and accepts whips from 7-32 ft. An integrated tool-free Quick Connect allows for head and whip swap outs. When paired with a MX FUEL REDLITHIUM FORGE XC8.0 Battery Pack, it consolidates up to 130 cubic yards per charge with a 1-3/4-in. head and 7-ft. whip. Wireless remote provides an operating range up to 30 ft. away from the power unit. Integrated ONE-KEY technology provides tracking and asset management capabilities. Available as a backpack or a kit.
The Control Speed Vibrator is a lightweight, durable, electric flex shaft concrete vibrator controlled through connectivity.
• Operator can use Bluetooth and the Minnich app on an iOS or Android device to choose between set speeds of 6,000, 8,000, 10,500 and open vpm
• Maintains preset speed as the concrete load changes
• 15-amp (115-volt) universal motor drives a full line of the company’s shafts and heads and comes with a quick disconnect to adapt to many other vibrator brands
• Frame-handle position offers many ergonomic user features and comes with a shoulder harness
Martin Engineering offers the MHF-1500 Brushless Concrete Form Vibrator for compaction, consolidation and leveling applications on construction sites. The external VFD/Inverter converts the single-phase 110-120V 60 Hz power to three-phase 230V, 100 Hz power in the electric rotary motor which runs at 6,000 rpm producing 1,500 lbs. of force. This allows for a brushless environment where magnetic fields rotate in space for the rotor to follow, lowering heat output which reduces wear and tear on internal components. The whole unit is sealed in a totally enclosed, non-ventilated aluminum housing rated IP66 and NEMA 4 with seals that comply with North American and EU standards.
Handle any job with the Simpson Strong-Tie ® 3G family of epoxy and hybrid acrylic anchoring adhesives. Code listed for cracked and uncracked concrete, they’re easy to install and provide a high-strength hold. SET-3G™ epoxy is our most versatile adhesive with ultimate bond strength for heavy-duty, structural work. Choose ET-3G™ epoxy for general rebar doweling and threaded rod. For a fast-cure option, AT-3G ™ hybrid acrylic allows same-day bolt-up in a wide range of temperatures, including extreme cold. Stocked nationwide at local retailers, our adhesives are backed by expert service and technical support.
To learn more about our entire line of 3G adhesive anchors, installation tools and accessories, visit go.strongtie.com/3G or call (800) 999-5099.
Protect yourself, your workers, and your concrete for a successful and safe placement.
nless the weather is really extreme, not placing concrete isn’t really an option. There may be other factors that force a stop work but temperature is often a challenge that can be worked around.
There are different things contractors can do. One of the most common solutions is to start pouring in the middle of the night when it’s cooler in the “hot” climates or seasons to avoid dealing with a blazing sun bearing down on you—and your concrete—the entire time. According to OSHA, a lot of the U.S. is on track for the hottest summer on record. Likewise, the Center for Construction Research and Training states that even though construction workers account for only 7% of the country’s workforce, they experience 38% of all heat-related deaths at work in 2020.
No matter the time of day, if hot weather is going to be a hazard; treat it as such. The first item on the day’s agenda should be the toolbox talk. Take this opportunity and remind the workers of how the body reacts to hot weather conditions and dress appropriately. How you dress is key. “Sometimes people think that not wearing the shirt or just wearing their safety vest will keep them cooler,” notes Nick Demonte, Operative Plasterers’ & Cement Masons’ International Association-ITF (International Training Fund) Cement Mason Coordinator. “It’s actually the opposite.”
His recommendations:
• Wear lightweight loose-fitting clothing –there are clothing options available today that help wick sweat away and keeps you cooler once a breeze comes through.
• Take breaks in shaded, cooler, or
air-conditioned areas to escape the sun and heat.
• Stretch
• Stay hydrated. Take water breaks during the course of the pour when you can depending on manpower. Hydrate the day before too, not just the day of or during. Do not wait until you are thirsty to drink water. Avoid alcohol and caffeine as much as possible.
“If you see a co-worker with symptoms of heat exhaustion, speak up,” says Demonte. “Seek medical attention immediately.” Contractors should have a heat illness prevention program and emergency plan in place for training on heat hazards and steps to prevent heat-related illnesses.
According to OHSA’s Hazard Alert on extreme heat, employers are responsible to:
• Provide workers with water, rest, and shade.
• Allow new or returning workers to gradually increase workload and take more frequent breaks during the first week of work as they build a tolerance for working in the heat.
• Plan for emergencies and train workers on prevention.
• Monitor workers for signs of illness
Because the biggest issue when placing concrete in hot weather is the fact that it’s setting quicker, you’ll have to move at a faster pace. How the concrete sets, will dictate the pace and how fast you’ll have to work so contractors may need to call on a few extra hands to get things moving as quickly as possible.
“Hot weather” conditions can create difficulties in placing and finishing fresh concrete like:
• Increased water demand and accelerated slump loss
• Increased rate of setting times resulting in finishing difficulties
• Increased tendency for plastic and drying shrinkage cracking to occur
• Potential difficulties in controlling entrained air characteristics
• Inability to reach desired strength requirements
ACI 305.1-14 (Specification for Hot Weather Concreting) provides recommendations and best practices for concrete placement when environmental conditions can have detrimental impacts on concrete quality. Hightemperature placement of concrete can sometimes cause challenging and difficult conditions to ensure that concrete quality and desired properties are maintained. However, it is not just the temperature of the concrete that must be controlled during placement as other factors such as ambient temperature, humidity, wind speed and exposure to sunlight can also play a significant role in the hydration process of cement and ultimately alter the physical setting characteristics of the concrete mixture.
Although many local and national requirements vary, it is generally recommended to consider taking precautions for placing concrete in “hot weather
conditions” when the concrete temperatures are in the range of 77-95º F (25-35º C).
ACI 305.1-14, sections 3.2 and 3.3, recommends a maximum temperature of fresh concrete at time of discharge to not exceed 95º F (35º C), unless supporting field experience or pre-construction testing is available.
Mix Design— Understand the material you’re working with is vital; know what chemicals are in the mix and the design. “How the mix design is composed of is going to be key and how fast its’ going to set itself off when it hits the ground as [you] start to pour,” says Demonte. Admixtures like retarders can help control concrete and offset the accelerating effects of hot weather. The opposite rings true for cold weather where accelerating admixtures can be used to speed up the setting process and early strength development. This would allow forms to be removed sooner and improve the concrete resistance to freezing at an earlier age.
If requesting a retarder or accelerator to the mix, inform your supplier exactly how much you’re looking for. The OPCMIA goes over many of these issues in its education: understanding the testing, understanding the
formulas, how many gallons per yard, etc.
“Every job is different. It’s not one formula that works for everything,” says Demonte. Take a step back and try and see the whole picture. Note how your current job is different than others. If pouring on a roof deck, for example, consider that the sun will have heated the surface already and that heat can accelerate the concrete. There are a lot of moving parts that go on that contractors may not be thinking about when they order a truck. The optimal situation is receiving your delivery first thing in the morning. If the pour is scheduled for later in the afternoon, it raises the chance that that truck has been on multiple sites. It’s gone through more revolutions during the course of the day–trapping heat inside even more and affecting how fast the concrete sets. While rare, the drum may also have remnants of previous jobs with leftover material which can set off the material quicker than you want.
Batch Temperature— Another big component is the temperature of the material. Ask if (and how) your supplier is keeping it cool overnight and how long the concrete sits in the drum.
ACI Resource Centers — Southern California, Chicago/Midwest, and Mid-Atlantic
Helping meet the increasing need for ACI knowledge through hands-on training, educational offerings, and on-demand access to ACI Certification programs. Designed for the trades, contractors, inspectors, designers, and engineers, ACI Resource Centers are a great fit for new-hire onboarding, employee education, and customer or member training.
Learn more at ACIResourceCenters.org
Look at the ticket and take note of the time it was batched from the plant. The more revolutions the drum spins, the hotter the drum gets.
If required for the job, a testing company will test the temperature of the mix when it arrives.
Cold water or ice are common solutions for a bit of insurance against the heat. On the opposite end, hot water can help set up the concrete quicker in the colder winter. Remember to consider your water-to-cement ratio.
“Some batch plants will keep the aggregates cool,” says Demonte. “Sometimes they’ll spray it down with water and keep that material cool. If it’s been sitting in the blazing sun, that material gets hot. Once you put all the ingredients together – it just makes it set off quicker.”
Site Situation— Direct sunlight is also a big component. Treat the job differently based on if you are working in a covered building vs direct sun. “Depending on the structure of the building, you have to think about where the sun starts and where it ends,” says Demonte.
Consider the structure of the building you may be working on. Will you be in the sun all day? Will you have trades overhead while pouring a slab? Perhaps decking will be installed overhead creating shade. Look at the big picture and how the site changes throughout placement and finishing.
The key: plan ahead and use time wisely. Consider the sun’s movement. Keep the team together to make the placement and finishing easier and more efficient. Depending on the size of the placement more manpower might be needed.
“How you plan your pour, how you bring your equipment onto the slab is going to be key,” says Demonte. If the equipment is staged in the shade and you start pouring in the sun – that could be a problem and not allow you to get the equipment across the slab.
It’s all organizing and planning. Consider where the sun rises and sets; how to stage equipment, where to
begin the pour, and where to end to avoid cold joints. Some additional key elements to consider here include the type of substrate you’ll be working on: metal, a vapor barrier, gravel, aggregate, compacted, etc.
“By understanding mix designs is something that is going to be really beneficial in working with the material. Doing your homework before the pour is just as important as while you’re doing the pour.”
The following recommendations may also reduce potential problems associated with hot weather concreting:
• Schedule concrete placement to limit exposure and place during ‘cooler’ periods of the day, i.e. at night.
• Use a concrete consistency that will allow for rapid placement and consolidation.
• Reduce the time of transport, placing, and finishing.
• Consider the use of retarding or hydration-stabilizing chemical admixtures and supplemental cementitious materials, such as fly ash and silica fume, to reduce the heat of hydration.
• Employ the use of temporary moisture-retaining films immediately after placement.
• Use methods to limit the exposure of the concrete such as windscreens and sunshades.
• When possible, schedule slab placement after roof structures and walls are in place.
• Provide curing methods to maintain adequate moisture and favorable concrete temperature
• Cool the concrete itself by using chilled water during production and aggregates that have been ‘watered’ down.
Additives can help protect concrete during hot weather conditions through the use of set-retarding admixtures, fibers, hydration stabilizers,
evaporation retarders and curing compounds.
• Eucon Series set-retarding and hydration stabilizing admixtures to lower water demand, extend working time, and maintain strength.
• PSI Fiberstrand and TUFSTRAND fibers to minimize cracking and reduce crack widths.
• Eucobar evaporation retarder to maintain moisture during placement.
• Kurez DR VOX (curing compound) and Diamond Clear VOX (curing and sealing) are membrane forming curing options to protect concrete from moisture loss. Kurez VOX White-Pigmented is a curing compound that also reflects sunlight to help keep concrete cool.
AMERICA’S CEMENT MANUFACTURERS AVOIDED MORE THAN 3.9 MILLION METRIC TONS OF CO2 LAST YEAR. THEY’RE ON TRACK TO OUTDO THEMSELVES EVERY YEAR TO COME.
For decades, the key metrics for concrete in constru ion were durability, reliability, safety and cost. In recent years, however, sustainability has been added to that list by customers seeking to reduce carbon emissions on new proje s. This growing customer consideration sets a new performance standard for constru ion materials—and is one that America’s cement manufa urers can meet.
Cement is the main ingredient in the 400 million cubic yards of concrete consumed every year across the country, and U.S. cement manufacturers—which are represented by the Portland Cement Association—are committed to reducing emissions at every turn. From fueling the kiln to the final product, the cement industry’s goal of carbon neutrality isn’t just for reducing the carbon footprint of the cement industry, but for construction projects nationwide.
Toward its goal of reaching carbon neutrality, the U.S. cement industry is focusing on three major priorities in the near future: the adoption of lower-carbon blended cements; using alternative fuels in cement manufacturing as opposed to fossil fuels; and carbon capture utilization and storage (CCUS). These efforts benefit project owners, design teams, and contractors, who need a durable material that meets a project’s sustainability goals.
After spending years on the sidelines, portland limestone cement (PLC) has gone mainstream in the U.S., hitting multiple milestones in 2023. PLC is a lower-carbon alternative to traditional portland cement that reduces carbon emissions by up to 10% while maintaining quality and durability in concrete structures.
Last year, Type IL PLC became the most common blended cement in the nation for general concrete construction. As a result, working with PLC and other blended
cements has become the norm rather than the exception.
Statistics from the U.S. Geological Survey showed that by mid-year 2023, the market share for blended cements was 54.5%, and PLC’s share of blended cement was 95%. What is more remarkable is the speed at which PLC has gained this level of market share and acceptance. As recently as mid2021, the market share for blended cements remained below 5%.
Notably, as of early 2024, all 50 state departments of transportation (DOTs)— major consumers of concrete have formally
approved the use of PLC. This is a milestone in efforts to decrease the emissions associated with our nation’s roadways and infrastructure. In California alone, a 100% shift to PLC for all Caltrans projects could result in 866,000 tons of CO2 potentially saved per year.
Another indicator that the use of PLC will continue to grow: alongside resilience and durability, the current administration has placed sustainability at the heart of its Bipartisan Infrastructure Law goals, including millions of dollars in environmental provisions that specifically call for the use of lower-carbon cements in government construction.
The demand for PLC is rising—but what does production look like? As of March 2024, approximately 50% of the cement produced by PCA members is PLC, with some companies exclusively producing PLC. And PLC is only the beginning. The U.S. cement industry is committed to creating new cements using existing and even alternative materials to reduce emissions.
PCA’s second focus area, alternative fuels, is working to unlock more carbon-reduction options for cement producers. Efficiencies in energy use and moving toward renewables lower the embodied carbon of all cements and the concrete made with it.
The industry has made notable strides in this area, and 73% of PCA member companies now use alternative and/or renewable fuels. One example is Buzzi Unicem USA’s implementation of solar energy at its plant in San Antonio, Texas. The company’s 10-megawatt capacity solar panel farm allows the plant to reduce its power use from the grid while increasing its sustainability and energy efficiency.
GCHI (Giant Cement Holding, Inc.) replaced coal with natural gas to lighten the environmental impact of cement production at its Harleyville, South Carolina, plant. In 2021 alone, the company replaced approximately
In August 2023, the Alamo Cement Company’s San Antonio cement plant earned the Energy Efficiency Award from the Portland Cement Association for the solar plant project.
Portland Cement Assocation | Buzzi Unicem USA
25,000 metric tons of coal with natural gas and reduced CO2 emissions by an estimated 26,000 metric tons. In addition to natural gas, GCHI’s Giant Resource Recovery company provides discarded materials—things that would otherwise end up in landfills or incinerated without any corresponding environmental or energy recovery benefit—as an energy source.
Summit Materials’ Green America Recycling company is a waste treatment, storage, and disposal facility that allows it to replace coal with biomass and other waste-derived fuels. Summit Materials currently has a 42% fuel substitution rate, and in 2019, it used more than 130,000 tons of discarded materials as fuel at its two locations. This approach has two key benefits: reducing landfill waste and significantly cutting net emissions.
CCUS is the heavyweight in getting the cement industry and other manufacturing industries to carbon neutrality. Most of these efforts are still in the research and development stage but hold promise for large-scale emissions reductions.
Powerfully
simple whiteboard-like scheduling made for people like us.
In a unique approach to carbon capture, Votorantim Cimentos North America’s St. Marys Cement is exploring algae as a solution. The company is piloting a program using a bio-reactor filled with algae, which feed on light and CO2 By directing a stream of the plant’s CO2 emissions into the bio-reactor, the algae effectively consume a portion of the emissions as they use it for their photosynthesis. Furthering their usefulness in the process, algae could one day serve as a source of biofuel for the plant. While the pilot is being conducted at a much smaller scale, it’s an interesting example of how emissions can potentially be put into a circular system and essentially recycled as fuel.
Light-filled tanks grow algae that consume CO2. This algae can be harvested and used as biofuel.
Recently, Heidelberg Materials North America has received funding from the U.S. Department of Energy to advance the integration of full-scale carbon capture, transport, and storage at the company’s new cement plant in Mitchell, Indiana. The funding will build on prior funding that has been awarded by the DOE toward successfully completing the Front-End Engineering and Design work necessary to verify the project’s technical feasibility.
The cement industry is taking a leading role in CCUS pilot projects, with six projects currently underway at U.S. cement plants, providing learnings and blueprint approaches for other manufacturing industries looking to leverage this technology.
The cement industry hasn’t let its goal of carbon neutrality by 2050 out of its sight since launching its Roadmap to Carbon Neutrality in 2021. PCA member companies have reached numerous milestones over the last three years and have their sights set on accelerating progress—not just for cement manufacturing, but for the industry as a whole.
Editor’s Note: More on PCA’s member companies’ decarbonization efforts can be found at cementprogress.com.
Rick Bohan is the Senior Vice President, Sustainability at the Portland Cement Association.
THEY MAY BE USED AS INPUTS FOR THE EVALUATIONS CONDUCTED UNDER RATING SYSTEMS LIKE LEED AND GREEN GLOBES BUT THEY ARE NOT A RATING SYSTEM THEMSELVES—HERE’S WHAT YOU SHOULD KNOW.
The world’s first near zero-carbon 3D printed home used Eco Material’s PozzoCEM Vite by automated construction company, Hive 3D in Round Top, Texas. Hive 3D and Eco Material have worked together to create a system to mix Eco Material’s cement replacement products with locally-sourced aggregates onsite using modified commercial mixing equipment.
As project developers and governments embrace “green” construction practices, contractors, architects, engineers, and other speci ers are using Environmental Product Declarations (EPDs) to compare materials like cement based on their environmental impacts and selecting the ones that reduce carbon emissions without sacri cing performance. An EPD is an independently veri ed and registered document that informs building professionals and consumers about a product’s environmental impacts based on lifecycle assessment studies. Similar to a nutrition label, EPDs provide transparency on a product’s potential impact on global warming, acidification, fossil fuel depletion, and other environmental concerns. The building and construction industry produces nearly 40% of global greenhouse gas (GHG) emissions, and as a result, EPDs have become key to reducing a proje ’s carbon footprint through procurement of low-carbon materials at the start of construction.
It is paramount to note the difference between EPDs, which are becoming a requirement for material manufacturers, and green building rating systems such as LEED and Green Globes. While entirely voluntary, these rating systems are still expected to play a role in reducing the environmental impact
resulting from construction and operation. EPDs may be used as inputs for the evaluations conducted under these rating systems, but they are not a rating system themselves. They assess product manufacturing from raw material extraction and transportation to the waste generated at the end of a product’s lifetime, and follow consensus-based standards certified by third-party experts. A published EPD is valid for a period of five years.
While EPDs are not mandated by law, they are often requested by government agencies that seek to lower the carbon footprint of construction projects. Most notably, EPDs are used for state and federal “buy clean” procurement policies in which governments purchase concrete, steel, asphalt, and glass that have lower embodied GHG emissions as indicated by their ecolabels. California, Colorado, Maryland, Massachusetts, Minnesota, New Jersey, New York, and Oregon require EPDs for public procurement.
At the federal level, the Federal Buy Clean Task Force—which includes 14 federal agencies and accounts for 90% of all federally purchased construction materials—provides instructions for integrating “buy clean” practices into procurement and funding processes. According to the Federal Highway Administration (FHWA),
transportation agencies “are beginning to require and collect EPDs during project procurement to prepare for implementing EPDs as part of procurement decisions.” State DOT adoption and implementation of procurement using EPDs has steadily increased over the past five years. As FHWA notes: “The use of EPDs is not required under title 23, U.S. Code; however, the Federal government has outlined related efforts through Executive Order (EO) 14057. Under the EO, several Federal agencies are advancing activities related to EPDs.”
EPDs have already been developed for concrete, cement, and slag products. Soon construction pros can expect to see labels for supplementary cementitious materials (SCMs) such as fly ash, a popular substitute for traditional cement used in more than half of the concrete produced in the U.S. Many of the world’s most famous dams, bridges, skyscrapers, and roads have been built using high-performance fly ash concrete mixes to achieve superior strength and longevity while lowering carbon emissions.
Presently, SCM-specific EPDs are being developed with input from representatives of the American Coal Ash Association, the National Ready Mixed Concrete Association, the Portland Cement Association, and the Federal Highway Administration, among other stakeholders. The documents will
cover lifecycle assessments specific to fly ash, bottom ash, harvested ash, raw natural pozzolan, calcined natural pozzolan, and alternative SCMs. Creation of EPDs are, ultimately, the responsibility of SCM ash marketers and cement and concrete producers, and they can provide a competitive advantage where project owners require transparent information about the lifecycle environmental impact of materials.
Contractors need to understand what EPDs reveal about a product. In the case of SCMs, fly ash sourced directly from a power plant essentially starts with a zero-carbon footprint. Then, any carbon inputs resulting from transportation or processing of material before reaching the loadout silo get factored in. Moreover, any carbon-generating activities—such as beneficiation—carried out by the ash purchaser after loadout also would need to be computed and published by the end user responsible for producing the EPD. The lifecycle assessment needed to produce the final EPD is performed according to ISO 14040 and 14044 requirements, and final EPD product labels are developed in accordance with ISO Standard 14025 (ISO 2006).
EPD labels don’t rank products. Instead they offer details about organizational information, the assessed product and its specifications, the declared or functional unit of assessment (e.g., m3 of the assessed product), materials incorporated in the product and their origin, and environmental emission results by lifecycle stage. Type III EPDs, which are developed for an individual product sold by a manufacturer, are best for analyzing the embodied carbon of a product. In contrast, industry-wide EPDs apply to industry averages for a product type and act as a useful benchmark.
Whether working with buildings or infrastructure, contractors can expect to see greater use of EPDs, especially in the use of concrete mixes. Project managers have the choice of substituting recycled materials — like fly ash and other coal combustion
products — for conventional products to achieve sustainable design and drastically reduce a host of environmental impacts. In many cases these materials cost less, are available locally, and are
technically equivalent or superior to virgin materials.
Technologies.
INTEGRAL AGGREGATE, SINGLE-COAT APPLICATION, POLYURETHANE WATERPROOFING & TRAFFIC BEARING COATING
Pecora-Deck HB1100-SA is a two-component, self-leveling, fast curing, UV and weather resistant, low VOC, polyurethane traffic coating system specifically designed for use in both exterior and interior applications exposed to pedestrian and vehicular traffic.
This coating is applied as a one-step traffic coating system that includes an integral aggregate and functions as both a waterproofing and traffic bearing deck coating system.
ULTIMATELY, REALISTIC COST ESTIMATION, METICULOUS SCHEDULING, RISK ANALYSIS, DESIGN COORDINATION, AND VALUE ENGINEERING ARE THE FOUNDATIONS OF THE PRECONSTRUCTION PHASE.
@Ngampol - adobe.stock.com
Preconstruction is the critical stage that lays the groundwork and sets the trajectory for the entire endeavor, establishing the schedules, budgets, and foundational elements upon which success will be built.
While eager stakeholders may be tempted to expedite this process, sufficient time and diligence in preconstruction is invaluable. The work completed during this period will dictate priorities, prevent wasted efforts, uncover cost savings, and minimize risks over the course of the project. A reported 23% of companies reported increased productivity when their preconstruction process was improved.
One fundamental preconstruction task is to develop accurate cost estimates and budgets, and the most important prerequisite here is to have access to all detailed project files and blueprints within one’s estimation toolkit. This process involves more than number-crunching, and requires
gaining an intimate understanding of the financial landscape of the project. Meticulous analysis of the needed materials, labor, equipment, and other resources is essential. And yet only 35% of general contractors reported having dedicated technology to create and manage bids. The goal is to create a budget that is not just correct on paper, but also practical and actionable, and is streamlined to save everyone time.
• Analyzing required materials, labor, and equipment is the starting point. Determining the exact quantities and types of physical resources needed informs cost projections.
• Market research provides indispensable data on current pricing for materials and labor rates in the project’s location. This enables estimators to make realistic cost estimates based on present-day figures.
• Past projects with similar specifications and scope serve as
handy references for comparison. Historical data helps estimators understand typical costs and make proper adjustments for inflation or market fluctuations.
• Including contingency reserves in the estimate is prudent to account for unexpected expenses or shifts in project requirements down the line. Contingency funds set aside resources to handle unforeseen circumstances.
• Once cost estimation is complete, the next step is to develop a detailed budget plan outlining total projected expenditures, divided into line items such as materials, labor, equipment, permits, fees, overhead, and contingencies.
• The budget allocates fixed amounts of funds to each aspect of the project according to the cost estimate. This provides a clear roadmap for spending and guides financial decision-making.
• Throughout the construction process, project managers monitor actual costs against the established budget. This allows early detection of potential overages and the ability to make adjustments to stay on track financially.
• Budgets must maintain enough flexibility to accommodate changes in project scope. As requirements evolve, the budget may need revision to accurately reflect modified plans. Additionally, accurate upfront cost estimation can reveal opportunities for potential savings without compromising project quality or goals. These insights empower stakeholders to proceed prudently, while still satisfying objectives.
Another fundamental component of preconstruction. This process involves far more than simply generating a to-do list—it means creating a comprehensive roadmap that charts the course for the entire project timeline.
Careful planning ensures resources are allocated appropriately across activities, and tasks are sequenced in a logical order to prevent delays, keep stakeholders on track, and enable the project to meet prescribed deadlines. Without a comprehensive, centralized pre-planning system, errors can surface, which represents nearly 48% of rework in the U.S. Breaking down the work into digestible phases with realistic timeframes helps managers better budget their time and resources, and ensures fewer errors in the long run.
Thorough upfront planning also helps identify potential bottlenecks, obstacles, or scheduling conflicts early on, so they can be resolved proactively. Visualizing the project’s schedule and milestones enables the team to anticipate where task dependencies, resource constraints, or other issues could arise, and address them ahead of time. Detailed plans also enhance communication and collaboration by ensuring all parties understand their roles, responsibilities, and timelines clearly from the start.
An essential pillar of the preconstruction phase is comprehensive risk analysis and management planning. Conduct thorough assessments to identify any potential challenges, uncertainties, or risk factors that could impact the project if not addressed proactively.
These risks might stem from a wide range of sources, such as unforeseen weather events, disruptions to supply chains, changes to permits or regulations, or other external factors that could affect the project. Recognizing these potential threats early allows stakeholders to develop strategies to prevent issues from occurring or mitigate their effects if they do materialize.
An effective risk management approach also involves forming contingency plans and backup options to minimize delays and limit disruptions. Laying this groundwork during preconstruction significantly enhances the project’s resilience and flexibility.
Cross-functional design coordination and collaboration are instrumental in shaping the direction. This collaborative process involves synthesizing input from architects, engineers, contractors, clients, and other stakeholders to ensure the design aligns with the client’s vision, while remaining realistic and feasible to execute.
Tight coordination during preconstruction maximizes the likelihood that the final design not only meets aesthetic and functional goals, but can also be successfully constructed within practical constraints. It provides the opportunity to work through any potential conflicts or constructability issues while plans are still flexible, avoiding extensive rework later.
Effective design collaboration requires clear communication between teams to navigate any needed design modifications based on budget limitations, technical requirements, or construction considerations. Addressing these adjustments proactively leads to optimal outcomes.
Value engineering aims to maximize the value derived from each dollar invested in the project. Value engineering entails a holistic examination of the project plan to identify areas where alternative materials, methods, or design approaches could achieve comparable or superior outcomes, while enhancing efficiency or reducing costs.
The preconstruction phase offers an advantageous window to thoroughly explore these options before construction is underway. At this stage, modifications can still be made relatively easily, without causing major disruptions or delays down the line. The focus of value engineering is not solely cost reduction, but more importantly, improving overall performance, quality, and functionality in a financially responsible manner.
A collaborative, multidisciplinary approach ensures that potential value improvements are explored from all perspectives. Architects, engineers, contractors, and other experts contribute their insights to uncover optimization opportunities, leading to economical solutions without compromising quality or vision.
Ultimately, realistic cost estimation, meticulous scheduling, risk analysis, design coordination, and value engineering are the foundations of the preconstruction phase. Diligent planning and forethought during this stage enable fiscally responsible resource allocation, enhanced collaboration, proactive issue resolution, and maximized value from every dollar spent.
With a sturdy preconstruction foundation, construction teams can approach projects with the confidence that challenges will be minimized and success is primed. More importantly, with the impending construction industry slowdown in 2024, it’s vital to have a smooth-running construction project that starts with the diligence and vision established in preconstruction.
Ro Bhatia is the CEO of PlanHub.
When we think of guillotines, our minds turn to scenes of the French Revolution, which have been graphically depi ed in so many Hollywood movies. While it may have been inspired by the original device, in the surface preparation industry, the term has a different, more positive meaning.
By using either a walk-behind or a ride-on scraper, contractors can remove the remnants of an old floor—whether
THE IMPORTANCE OF GUILLOTINE BLADES IN SCRAPING AND WHEN THEY CAN BENEFIT FLOOR REMOVAL PROJECTS.
this is vinyl, carpet, woodblock or any traces of adhesive. As well as purchasing or renting the right scraper, it’s important to select the right tool, or blade, for the job.
The guillotine blade was developed as an angled alternative to the traditional heavy-duty straight blade. The latter is popular among contractors because it’s available in many standard sizes and is suitable for both ride-on and walkbehind scrapers.
The main difference is that while the heavy-duty blade is straight, the guillotine has a slightly angled edge. This allows contractors to slide into heavier materials and stay under them during removal, which can improve productivity by pulling up the surface effectively without damaging the substrate. Contractors should match the blade to the application to deliver a high-quality floor effectively. Though effective, a guillotine shank is not a one-size-fits-all blade, and its suitability will vary depending on the application.
Working with a floor preparation specialist when purchasing or renting a scraper can ensure that contractors make the right choice.
Take this example. A floor is located several levels up in the narrow hallway in an apartment block. The carpet is decades old, and the building’s owner wants to remove it as part of a larger renovation. Because of the weight and space restrictions, a walk-behind scraper is recommended.
While the edge on a guillotine could be beneficial in these settings, the contractor needs a self-scoring blade so that they can crosscut the carpet, vinyl or linoleum. They will also need a blade with the bevel down so that they could skim over while protecting the wooden subfloor.
We would recommend using a selfscoring wing-tipped blade for carpeted, vinyl, PVC or linoleum floors. While a guillotine can remove soft goods, carpet and vinyl flooring, these applications aren’t always the best use of it, and a wing-tipped blade would be more practical.
Generally, guillotine blades are suitable for any application where contractors would use a standard heavy-duty blade. While it can technically remove soft goods, it is best suited to removing ceramics and thick, hard materials over a wide area. A wing-tipped tool would be inappropriate for these applications, and the blade could snap if the contractor forced it through the material.
If the contractor is working on a concrete floor and there are relief cuts that are obscured by ceramic tiling, a square blade would simply go over the area and the machine could bounce up as a result. Not only would this be startling to the operator, but the blade could also snap.
Meanwhile, because a guillotine has a leading edge, unlike a flat heavyduty blade, it can go over the intentional ridges in the floor. This means
it can continue to remove the material without stopping the operator in their tracks, which would usually happen with a flat shank.
However, the guillotine blade shouldn’t be treated as a blanket
solution. Contractors must always choose the right blade type for the application and machine.
Tom Dunn is the vice president of sales and surface preparation expert at National Flooring Equipment.
65 YEARS OF MADE IN AMERICA
GRINDER
FLOOR GRINDERS - are used for topical applications up to a 1/16” deep. These models are for smoothing, cleaning, thin coating removal, and prepping surfaces. Floor Grinders are contractor and homeowner friendly.
edcoinc.com • sales@edcoinc.com • edcoed.com
TURBO GRINDERS - machines designed for residential, commercial, and industrial tasks like leveling expansion joints, high spots and bridge decks; removing thick coatings, and smoothing rough surfaces.
At the first PAVE/X Conference in San Antonio this past February, I must have hit a real nerve for many contra ors and field leaders. When asking leaders if they had a challenge with workers making mistakes that needed to be reworked or that caused a “go back,” the response ranged from smiling, nodding their heads in agreement, or just displaying frustration. To make matters even more realistic, I then shared what the “cost of quality” is for mistakes that are made.
The “Godfather of Quality,” Dr. Edward Deming, found that when a mistake is made, the actual cost of correcting the mistake is some three “times” the amount of the cost associated with doing something right the first time. Let me give a brief and simple example.
A paving contractor has a crew that overlays a mat that is ten-thousand square feet, with a cost of $5,000.00. That’s not what we sold the mat for but what the cost of putting the mat in. Now, our crew makes several mistakes requiring the complete removal of the one-to-two-inch mat and then replacing the mat. Here’s what the numbers look like, per Deming:
1st Placement $5,000
2nd Remove/Replace $5,000
3rd Lost Opportunity Cost $5,000
Total Cost $15,000
The third cost always surprises contractors but think about it for a minute. While your crew is reworking a mistaking, they could have been executing another project, for the first time.
Aside from not having enough money to make payroll for the startup contractor, poor quality can bring any contractor to their financial knees.
The Cost of Quality is a real separator of contractor between those who do things right the first time from those who just seem to always have issues causing rework and call-backs. So, what’s a contractor to do? Consider the following brief tips reduce, if not eliminate your quality issues.
Start taking more focused time on defining exactly what each project will require, including more accurate descriptions of the property the work will be executed.
Have a focused “pre-start” meeting with the estimator and the crew that will be doing the asphalt, sealcoating, striping, etc. project.
There should be a written plan for larger or more complicated projects. Always provide your crews with the right equipment and tools to execute the job.
Depending on the complexity of the project, the estimator, senior field leader, or the owner should be visiting the project to ensure that we are completing the work as planned.
The Cost of Quality is zeroed out when we do things right the first time. Spend more time on the front-end of the project, addressing the five tips above, and watch your production, safety, and profitability all improve!
Here’s to NO BAD JOBS!
Brad Humphrey, known as The Contractor’s Best Friend, is President of Pinnacle Development Group. For more information about Brad, his company, or this article, email him at brad@pinnacedg.com.
For more information visit https://CONC.me/ bestfriend
DESIGNED TO HONOR CONSTRUCTION PROFESSIONALS FOR THEIR ACCOMPLISHMENTS IN SHAPING THE INDUSTRY
Construction professionals - working in the heavy equipment, asphalt, pavement and reconstruction, concrete, and rental segments - can be nominated for any of the following categories:
• Women in Construction: Honors females in the construction and rental industries, whose accomplishments, mentorship and examples set a foundation for women in all levels of a company’s network.
• Rising Professionals in Construction: Recognizes outstanding young or newer construction professionals whose achievements, hard work and vision have shaped the construction network. Rising/emerging professionals must maintain 1-9 years of experience in the construction industry.
• Lifetime Achievement: Honors contractors, workers and owner/operators who’ve made outstanding contributions to the construction and rental industry. Must have at least 10 years of documented accomplishments in construction.
• Jobsite Excellence: Recognizes outstanding workers on the job site whose leadership and work ethic set a strong example companywide. https://myfc.pro/paceraward