



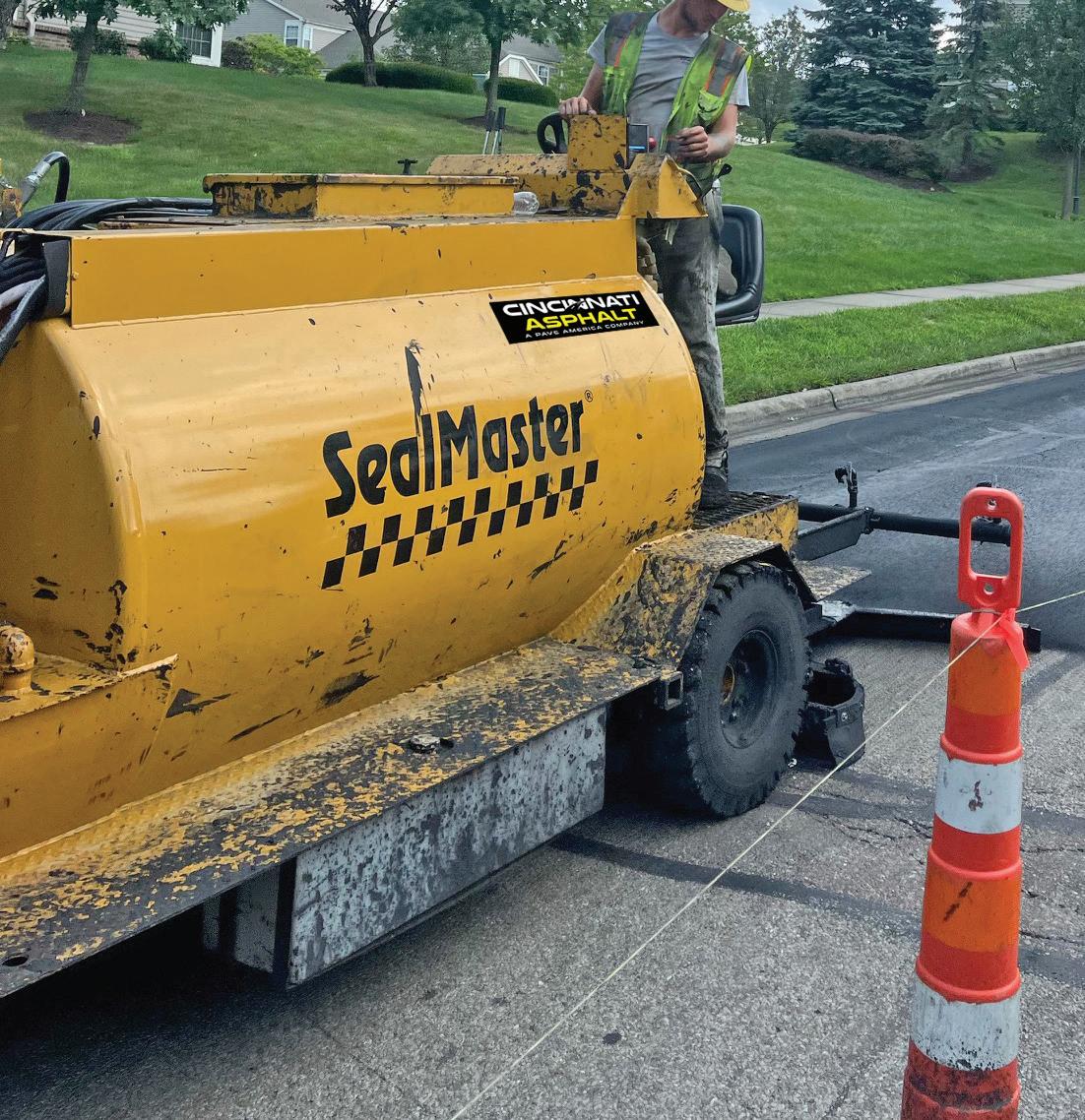
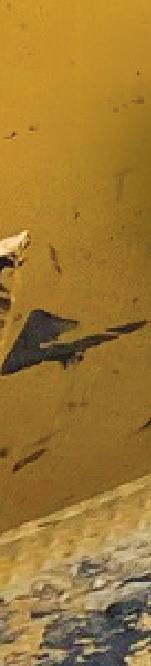

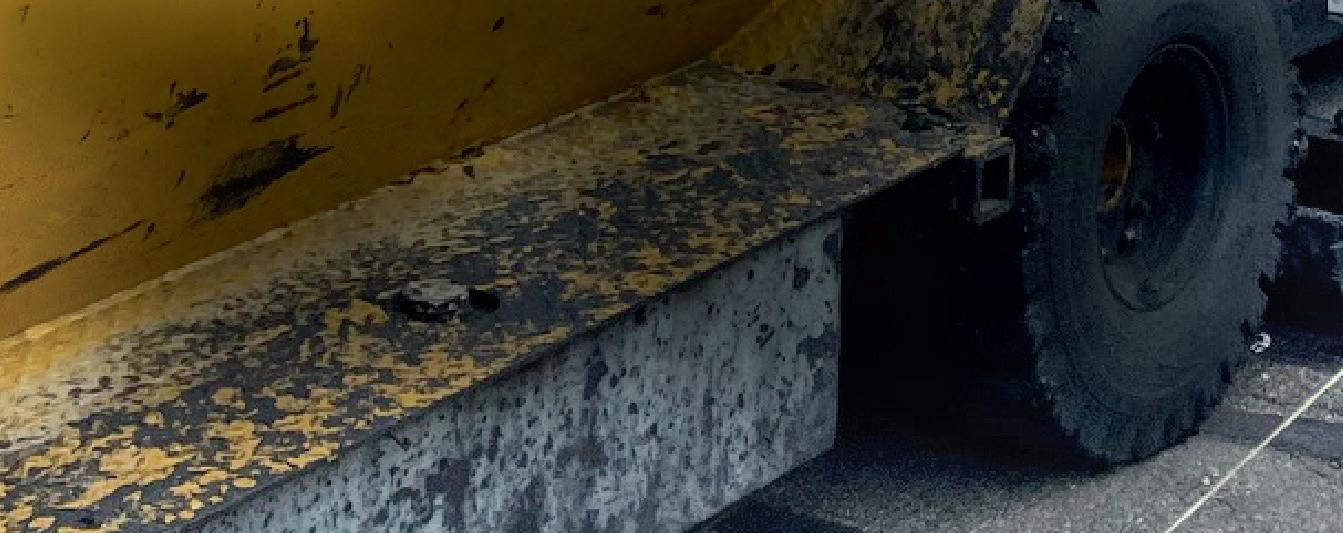
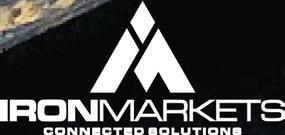
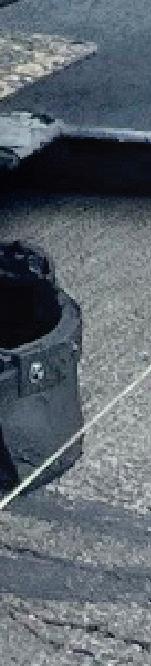
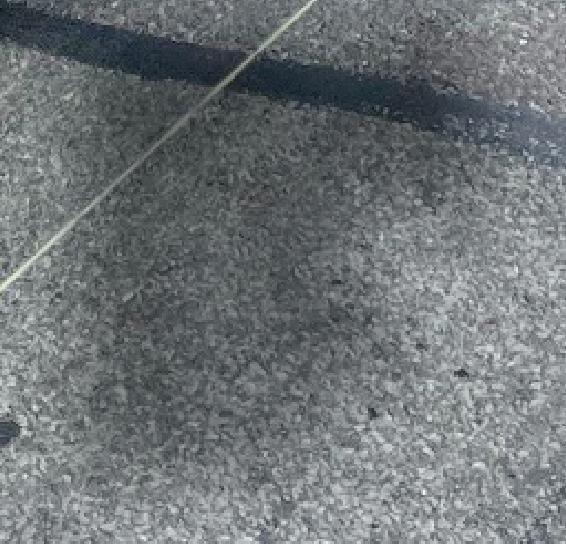
If you’re awarded infrastructure or large construction projects, profitability hangs on efficiency. These days, controlling dust, dirt and debris is a must, so your mechanical sweeper better not mess around.
When there’s no time for downtime, it’s time for Broom Bear ® or Broom Badger ® .
Elgin brings 100+ years of hustle and reliability to every job-site. Broom Bear® and Broom Badger® are built for you — fast and dependable, with the best customer service in the business.
Best practices and methods for proper sealcoat tank maintenance.
How 3D Milling and Advanced Data Capture Can Save You Serious Paving Headaches
Portable EV Options To Keep You Charged Up: The next generation of service trailers might make-or-break your jobsite experience. A diverse mix of machine types means that your fueling trailers and trucks need to be able to handle every possible need to avoid a work stoppage.
Asphalt Pavement Repairs
101: Summer means shifting into high gear on pavement maintenance and repairs. The winter months and spring rains always take their toll on pavements, so it’s good to review a few basic, timely repair strategies.
The Slow Pace of Change: The more things appear to change, the more they stay the same, goes the cliché. How true that is, depends on you.
A roundup of the latest news in the industry.
The newest asphalt and pavement maintenance products hitting the market.
Stay up-to-date with info on the 2025 show!
What is your biggest power sweeping barrier?
Extending The Life Of Your Pavements: One of the primary benefits of power sweeping is minimizing surface degradation.
Planning: The Components of Contractor Success
PAVE/X 2025 will be hosted January 27-30 2025 at the Chattanooga Convention Center. Registration for courses and the hotel room block are now open.
Formoreinformationvisit
https://pavemg.com/kjxg5xeb
Everyone is dealing with the labor shortage in different ways, but some are having more success than others. In part two of our trip to Ocean County, New Jersey, we attend a massive construction-centered job fair for high school and vocational students.
Formoreinformationvisit
https://pavemg.com/87uo83b7
In a post on the Facebook group Asphalt Life, which has a community of almost 220,000 global members, the question of which manufacturer makes the best asphalt paver was discussed across hundreds of comments. The results will surprise you!
Formoreinformationvisit
https://pavemg.com/2g6hdslf
ADVISORY BOARD
Agua Trucks Inc
Wickenburg, AZ, Scott Duscher
Asphalt Contractors Inc., Union Grove, WI Robert Kordus
and copyrighted 2024 by IRONMARKETS. All rights reserved. No part of this publication may be reproduced or transmitted in any form or by any means, electronic or mechanical, including photocopy, recording or any information storage or retrieval system, without written permission from the publisher.
Subscription policy: Individual subscriptions are available without charge in the U.S. only to pavement maintenance contractors, producers and government employees involved in paving or pavement maintenance; dealers, and distributors of pavement maintenance equipment or materials; and others with similar business activities. Complete the subscription form at www.forconstructionpros.com or use your company letterhead giving all the information requested. Publisher reserves the right to reject nonqualified subscribers. One year subscriptions for nonqualified individuals: $35.00 U.S.A., $60.00 Canada and Mexico, and $85.00 all other countries (payable in U.S. funds, drawn on U.S. bank). Single copies available (prepaid only) $10.00 each (U.S., Canada & Mexico), $15.00 each (International). Pavement Maintenance & Reconstruction (ISSN 1098-5875), is published eight times per year: January, February, March, April/May, June/July, August/September, October/ November, December by IRONMARKETS, 201 N. Main St. Ste 350, Fort Atkinson, WI 53538. Periodicals postage paid at Fort Atkinson, WI and additional entry offices.
POSTMASTER: Please send change of address to Pavement, PO Box 3605, Northbrook, IL 60065-3605. Printed in the USA.
PAVEMENT MAINTENANCE & RECONSTRUCTION is proudly supported by these associations:
Asphalt Restoration Technology Systems, Orlando, FL Connie Lorenz
Brahney Paving, Hillsborough, NJ Steven Brahney
Eosso Brothers Paving; Hazlet, NJ ...................................................................... Tom Eosso
Maul Paving/Concrete/Sealcoating, PLainfield, IL ........................................ Chris Maul
Parking Lot Maintenance, Lake St. Louis, MO Todd Bruening
Petra Paving, Hampstead, NH Chris Tammany
Pioneer Paving, Albuquerque, NM Don Rooney
Roberts Traffic, Hollywood, FL Lisa Birchfield
Show Striping Inc. (SSI), Wisconsin Dells, WI Amber Showalter
T&N Asphalt Services, Salt Lake City, UT Nick Howell
Young Sealcoating Inc, Lynchburg, VA Steve Young
The Paving Lady Mauro Comuzzi
JMP Excelsior Services ............................................................................... Jim Panzenhagen
Sweeping Industry Veteran .................................................................................. Gabe Vitale
Flat Nickel Management
Wis-Coat Asphalt Maintenance
Clear Choice Sealing
Jacketta Sweeping Services
Royal Pavement Solutions
ASSOCIATION REPRESENTATIVES:
Michael Nawa
Marvin Joles
Warren Johnson
Debbie Jacketta
Kenneth Roy III
Pavement Coatings Technology Council ....................... Brian Riggs, Executive Director
The
more things change, the more
they stay the same. How true that is depends on you.
Iam still young enough (I’m knocking on 40) that I can clearly remember things I learned in high school. I wasn’t a five-star, straight A student by any stretch of the imagination, but in my junior-year Government and Economics class I remember the teacher explaining the different arms of our government.
In theory, the way that the separation of powers is meant to work is by splitting up the authority of our system to ensure that no one person or party has too much control. However, what really cooked my brain back then, was that he explained that it made change slow and difficult. As a 17-year-old kid, that seemed infuriating. Ironically, I still think that is the case.
Brandon Noel, Editor bNoel@iron.markets
234-600-8983
The longer I live, the more I see that our world, the society we exist in, and the economic forces that business has to navigate, incentivizes those groups and companies that are able to react, adapt, and change in quick and shrewd ways.
For two years now, I’ve heard the frequent refrain that our industry is resistant to change. They say that we are slow adopters, that we like to do things the way they’ve always been done.
While this may have been true, I believe that this industry is ripe and ready for a massive wave of change. The conditions are coming together for new paradigms in the way of doing things, and it’s coming from the place these things usually do: the next generation. I’ve seen it first-hand. Recently, I had the chance to travel to New Jersey and visit a vocational trade school there called Ocean County Vocational and Technical School. I was taken on a tour of their facility, allowed to interview some of their students, and then attended a county-wide job fair where hundred of kids from both traditional high schools and other vocational programs were in attendance.
What I saw truly surprised and inspired me. The kids are alight. Despite growing up through a historic set of adverse circumstances, this generation wants to work, yes, contrary to what mainstream media and your angry friend on Facebook would have you believe. Not only do they want to work, but they want to make their mark. They aren’t afraid of making mistakes, new technology, or about incorporating unfamiliar tools on the fly.
From the two dozen or so kids I spoke to, not a single one flippantly addressed their circumstances in the job market, nor did they take unserious their futures. They had a shocking prescient grasp on the world that they are stepping into, and they see the power of their emerging role in it. When I spoke to the companies there looking for the future of their labor forces, the sentiment I took away was this: If you’re having trouble finding workers, maybe it’s time you started looking in new places.
Maybe the ad in the paper doesn’t work anymore. Maybe good employees aren’t just going to show up on your doorstep or call. I’m not sure that placing job listings online is as effective anymore. I don’t know if your county has something like the job fair that Ocean County does, but maybe you need to find out, get involved, and meet them where they’re at. They’re out there, and they’re hungry.
See you on the road! ■
EDITORIAL
Editor Brandon Noel bnoel@iron.markets
Content Director, Marketing Services Jessica Lombardo jlombardo@iron.markets
Managing Editor Gigi Wood gwood@iron.markets
Senior Editor, Equipment & Workwear, IRONPROS Michael Cheng mcheng@iron.markets
Junior Editor Merina Shriver mshriver@iron.markets
AUDIENCE
Audience Development Manager ........................ Angela Franks
PRODUCTION
Senior Production Manager Cindy Rusch crusch@iron.markets
Art Director April Van Etten
ADVERTISING/SALES
Brand Director ........................................................... Amy Schwandt aschwandt@iron.markets
Brand Manager ..................................................... Megan Perleberg mperleberg@iron.markets
Sales Representative Sean Dunphy sdunphy@iron.markets
Sales Representative Kris Flitcroft kflitcroft@iron.markets
IRONMARKETS
Chief Executive Officer Ron Spink
Chief Revenue Officer Amy Schwandt VP, Finance ....................................................................... Greta Teter VP, Marketing & Audience Development Ronda Hughes VP, Operations & IT Nick Raether VP, Demand Generation & Education ....................... Jim Bagan
Corporate Director of Sales Jason DeSarle
Brand Director, Construction, OEM & IRONPROS .....................................................Sean Dunphy
Content Director Marina Mayer Director, Online & Marketing Services Bethany Chambers Director, Event Content & Programming Jess Lombardo
CIRCULATION & SUBSCRIPTIONS
P.O. Box 3605, Northbrook, IL 60065-3605 (877) 201-3915 | Fax: (847)-291-4816
circ.pavement@omeda.com
LIST RENTAL
Sr. Account Manager Bart Piccirillo | Data Axle (518) 339 4511 | bart.piccirillo@infogroup.com
REPRINT SERVICES
Brand Manager Megan Perleberg mperleberg@iron.markets | (800) 538-5544
Published and copyrighted 2024 by IRONMARKETS. All rights reserved. No part of this publication may be reproduced or transmitted in any form or by any means, electronic or mechanical, including photocopy, recording, or any information storage or retrieval system, without written permission from the publisher.
Detroit Diesel Remanufacturing LLC (Detroit Reman), a brand of Daimler Truck North America, celebrated the grand opening of its plant expansion in Hibbing, Minn., increasing its manufacturing and remanufacturing footprint by twice its size. This marks a milestone in the company’s mission toward innovation and sustainability for battery electric vehicles (BEV).
The expansion allows Detroit Reman to expand its focus to BEV-specific remanufactured parts, including a dedicated space for high-voltage manufacturing components, such as batteries and inverters. The facility supports the increasing demand for electric vehicle components, which is expected to grow significantly in the coming years.
The new space will focus on the repairing, remanufacturing, and repurposing of commercial batteries.
The facility expansion will be located on the Range Regional Airport property. A long-term lease agreement highlights the business investment goals for the Hibbing community, supported by collaboration with local agencies, including the Department of Iron Range Resources and Rehabilitation, whose mission is to promote and invest in business, community, and workforce development for the betterment of northeastern Minnesota.
With a total of 120,000 sq. ft., including 12,000 sq. ft. dedicated to BEVs, DTNA’s strategic investment reflects the growing demand for electric vehicle components in the marketplace. With a 33% increase in warehouse and storage space, the expanded facility increases efficiency and storage capacity, enabling smoother operations and faster turnaround times.
A roundup of recent news, moves and events impacting the pavement maintenance industry
Caterpillar Inc. has announced a $90 million investment to prepare its facilities in Schertz and Seguin, Texas, to produce the all-new Cat C13D industrial engine. The investment will create 25 jobs at Schertz starting in 2026.
“We appreciate the support from the local community as we prepare our Seguin and Schertz facilities to produce the C13D engine,” said Mark Stratton, vice president and general manager of Caterpillar’s Industrial Power SystemsLarge Engines. “The Caterpillar team in Texas will produce the quality parts and engines we need for our customers as we help them build a better, more sustainable world.”
The C13D is a new 13-liter diesel engine platform designed to achieve bestin-class power, density and fuel efficiency. The engine optimizes the performance of heavy-duty off-highway applications such as material handling, construction, mining, and aircraft ground support.
The investment includes new equipment installations at both facilities, $70 million in Schertz to make C13D engine components and $20 million in Seguin to assemble the engines. The new equipment installations will not impact current operations, which include manufacturing Cat and Perkins engines and generator sets. C13D engine production is slated to start in 2026.
Liebherr has appointed Alexandra Hobgood as general manager of corporate responsibility and sustainability. This position will oversee sustainability initiatives throughout Liebherr’s U.S. locations by educating stakeholders, implementing new processes, and providing additional structure to current programs.
Hobgood earned a bachelor’s degree in biology and a master’s degree in environmental science from Christopher Newport University. With a desire to positively affect her local community, Hobgood worked at the Hampton Roads Sanitation District, where she completed lab work and water testing. She later transitioned to the Virginia Aquarium, where Hobgood developed a taste for program management implementing safety and environmental programs for the aquarium.
As the new general manager, Hobgood aims to build a strong program with potential initiatives including redirecting waste streams, diverting organics to composting, and completing energy studies.
“There are a lot of great processes already being implemented at Liebherr, so the structure for building a strong program is already in motion,” Hobgood said.
Hobgood plans to improve Liebherr’s current sustainability processes by not only implementing new programs but verifying they are being utilized and maintained throughout Liebherr’s U.S. locations.
For more information visit https://pavemg.com/2a6kgs
The 190 X4S excavator features a 120-hp Yanmar Tier 4 finalcompliant engine. With an upsized undercarriage compared to its little sibling, the 170 X4S, the 190 X4S offers superior lift performance, improved stability, and productivity.
These DOT-compliant fuel trailers allow contractors, farmers and others to refuel equipment on jobsites. The base model is available with fuel trailer only. An optional front box is also available for storage of tools, grease, lubes or other service supplies. The rugged chassis is constructed from 6-in. C-channel for service life. The tank features 7-gauge steel which is double seam welded for strength and durability. Each tank features internal fuel surge baffles and cross bracing, a fuel shutoff valve, a lockable vented fill cap, a tank pressure relief vent and a fuel gauge.
With eight electric rollers in the compact class, the HD 10e model (drum width: 1.00 m/ 39.4 in. and operating weight: 2.5t/5,512 lbs.) and the HD 12e model (drum width: 1.20 m/47.2 in. and operating weight: 2.7t/5,953 lbs.) offer the same compaction power as their combustion engine counterparts but produce zero local emissions. The e-rollers are operated in almost the same way as the other models in the HD CompactLine series. A 48V li-ion battery with 23.4 kWh capacity provides the energy for driving, steering and dynamic compaction. Charging from 0% to 100% takes four hours on 220V. The roller is designed to operate in ambient temperatures of up to 113° F. The battery supplies enough energy for an average working day.
Designed with the paving professional in mind, this heavy-commercial paver is guaranteed to impress. The 8520B incorporates enhanced features including an above deck generator, increased fuel capacity, and front adjustable conveyor chains that eliminate the need to lift conveyors to fine-tune tension. And as always, LeeBoy’s ultra-efficient material management system with a wide, slow-moving conveyor system moves material consistently from the truck to the screed which ensures a flawless mat. Includes dual electronic steering.
The Cat 299D3 XE Compact Track Loader, with its powerful engine, high output hydraulic system, high lift forces, vertical lift design and torsion axle suspension, provides the maximum performance for work tool productivity, digging, truck loading and material handling in a wide range of underfoot conditions and applications. The sealed and pressurized cab option provides the operator with a cleaner and quieter operating environment with excellent work tool visibility.
by Brandon Noel, Editor
Get hyped about it!
Are you all getting as excited as we are for PAVE/X 2025 in Chattanooga, Tenn.? We are happy to announce the registration for the event, to be held Jan. 27-30 2025, is NOW OPEN. We can’t wait until you see the updates we’ve made to make Year Two even BETTER than Year One. You can visit www.pavexshow.com to sign up!
WHAT YOU CAN EXPECT:
10+ Hours of LIVE Outdoor Equipment Demos
• Four Equipment Lanes + Operator Seat Time
• Static Outdoor Demos to Maximize Hands-On Opportunities
• Safety Kick-Off Meetings
• Food + Beer from Naked River Brewing
90 + Hours of Education
• Up from 60 Hours in 2024
• NEW 4-Hour Pre-Conference Workshop with Brad Humphrey
• 90-Minute Workshops for In-Depth Topics
• Over 70% of Sessions are NEW topics
More Networking Opportunities
• Monday 1/27: Official PAVE/X Kickoff Party Hosted by Blacktop Banter at BarrelHouse BallRoom
• Tuesday 1/28: PAVE/X Networking Night + Pavement Awards
• Wednesday 1/29: Sweepers Night Out
• Thursday, 1/30: NEW Expanded Roundtable Hours
• Thursday, 1/30: PAVE/X Hosted After-Party Event
“We are so excited for everything we brought to Year One of PAVE/X and wanted to make sure we expanded on what contractors wanted for Year Two,” Amy Schwandt, PAVE/X Co-Founder said. “Most notably in 2025, we are changing up the outdoor demo experience a bit so that contractors are able to get ON the equipment and operate it. We will do this in a controlled space with manufacturer representatives onhand to answer any and all contractor questions during the event.”
PAVE/X will also be expanding showfloor and education hours so contractors can choose where their time is best spent.
“While the education program in 2024 was a pretty big lift, we realized we could do better,” Jessica Lombardo, PAVE/X co-founder said. “We wanted to be able to provide 90-minute workshops for more in-depth topics, while also offering one-hour sessions for contractors who want to expand their knowledge in multiple areas. We’re happy the Chattanooga Convention Center has the space to be able to accomodate so many sessions in 2025 and will have more space in each classroom.”
The 2025 event will also feature expanded opportunities for roundtable discussions on Thursday afternoon during the event. These roundtables provide contractors with the chance to have detailed conversations about the jobsite issues they face every day. Attendees can
ask questions from been-there experts and network with their peers.
“What happens inside the classroom is important, but we know the face-toface interactions with those who do the same work as you outside of the sessions are one of the biggest benefits of an event like PAVE/X,” Lombardo said.
“The roundtables were great in 2024, but there will be more topics in 2025 for contractors to choose from and more promotions so attendees don’t miss these important conversations.”
OFFICIAL HOURS:
Monday, Jan. 27
• Education: 1-4 p.m.
• Official PAVE/X Kick-Off Party with Blacktop Banter (time TBD) Tuesday, Jan. 28
• Education: 7 a.m - 12:30 p.m.
• Outdoor Demo: 12-4 p.m.
• Indoor Exhibit Hours: 5- 7 p.m. Wednesday, Jan. 29
• Education: 7 a.m - 12:30 p.m.
• Indoor Exhibit Hours: 9 a.m. - 2 p.m.
• Outdoor Demo: 12-4 p.m. Thursday, Jan. 30th
• Education: 7 a.m - 12:30 p.m.
• Indoor Exhibit Hours: 9 a.m. - 2 p.m.
• Roundtables: 12:30 p.m. - 4:30 p.m.
• Official PAVE/X Afterparty: (time TBD)
Registration for courses and the hotel room block are now open at www. pavexshow.com ■
For more information visit https://pavemg.com/ mz1q1r
By Brandon Noel, Editor
At World of Asphalt 2024, Kevin Garcia from Trimble discusses BIM, digital twins, Trimble’s Roadworks Paving Control and how the real way to fix your asphalt mat is by fixing what is underneath it.
FCP: Help me understand the qualitative or quantitative improvement this has over previous generations?
Kevin Garcia (Trimble): What Roadworks does, is it migrates to the the newer platform, which is Android based. What’s really cool about it as we’re sitting here in this Trimble/B2W booth is, you can be running B2W software and machine control software at the same time.
So if, for example, I’m standing on the mill, and one of my jobs is to track
the number of trucks that are hauling the millings away, I can keep an idea of how many tons we’ve milled out. I’m using my machine control screen for how to manage that up-down-left-right of the mill, which I’m changing the profile or I’m optimizing the profile of the road for smoothness, material management, quality, and QC type stuff. At the same time, I could also just swipe right, and now I’m in my B2W track window. I can see I’ve just hauled away another truck, that’s another 20
tons going to this yard and then keep track of that.
Now, if I’m a vertically integrated customer who’s got dirt moving solutions, milling solutions, and paving solutions, all of those are on the works platform, which means I can be moving the more expensive and smart parts of the machine control system from machine-to-machine and maximize my investment.
Also, Roadworks migrating into the next generation will also allow us to do more with that kind of office-to-field workflow. So, you can create your model, push it through works manager out into the field, it shows up on the tractor, and you’re not worrying about transferring USB sticks. You’re always on the latest-greatest model, because you’re on a connected site. You can query the cloud, we can pull back the digital asbuilt data into the office. You can say, “Here’s what we said we were going to build, and here’s what we did build, and how closely those two things aligned.”
FCP: It creates a way to easily search or query the data or the metadata from those projects?
Garcia : Right.
FCP: What’s the biggest impact the 3D milling has on the roadwork itself?
Garcia : I always say, “If Trimble doesn’t sell anymore 3D asphalt pavers, because we’re selling 3D Milling, we’re doing it the right way.” Fix it with the mill. The mill is the easy machine to control.
Asphalt pavers have a floating screed and are just inherently more difficult. Things can go wrong, mix types can change, gradation of the mix can change, temperatures can change, material can run thin and the screed drops, or if you flood the paver the screed rises, even though that’s not the intended outcome. Because of the floating nature of a screed, it’s harder to control. A mill is a very fine thing, I know exactly where the drum tooth is at. I move the cylinders up or down to put it where I want
it. Fix it with the mill. Okay, cool?
Say we’re going to do a thin lift overlay on a job, I’m gonna go take an inch-and-a-quarter off the top of the existing surface, and we’re going to refill it with new asphalt. Great, sounds easy. And in most worlds, that means today you mill out about an inch-and-aquarter. If that surface is wavy, I’m still going to be wavy, I’m just going to be an inch and a quarter lower. Let’s make it smooth with the mill.
FCP: How do they turn their data into something actionable?
Garcia : I can start comparing my as-planned versus as-performed data. If it’s not meeting standards, what happened? What changed? We know how many hours we were in the field, we know how much dirt we moved, and we know how much we paved. Why didn’t it go according to plan? All the data is going to be there to teach you, you can start to hone in on what was that root cause, so that we don’t do it again next time or that you bid accordingly so that it doesn’t overrun.
It’s also going to become a differentiator for certain levels of contractors. You can give the client a set of detailed information, so that if you ever decide to do a renovation later, it can tell you where the utilities are, it can tell you exactly how thick your asphalt is, it can tell you what the mix type was, in case you need to use that information later.
FCP: I think that the more that data is educational and actionable, I think that it’s almost as valuable as the tool on the day itself.
Garcia : I fully agree, I think you’re gonna get to a world where the updown-left-right of the machine is the commodity and the data of what we use will become invaluable.
FCP: Ultimately, the bleeding edge question is: How could artificial intelligent models take this data, this raw information, and process it algorithmically? Could it be able to tell us what we can learn from it in ways that are insightful beyond our own ability to analyze?
Garcia: AI will play a future role with data processing. AI is interesting, especially in construction, because this is an orchestration of the jobsites. It’s not one machine does a task and leaves and I just measure that. It’s lots of machines working together, I might have four dozers or excavators. It could potentially help modeling all that stuff, and you’re digitally building the job before you build it. What if you could build a job before you ever put a single boot on the ground? That’s the kind of stuff where you’re on the cutting edge of the future. [This interview was edited for content and length.] ■
Brandon Noel, Editor
For those who live in colder, northern climates where temperatures fall below freezing for consistent weeks each year, it’s important to take proper care of your sealcoat storage tanks. Even in warm climates, at least once per year, they should be drained and cleaned to keep them in use for years to come.
By properly maintaining the interior of your sealcoat storage tanks, you ensure that the pumps and agitation motors stay in top condition for a long busy season. As we reach the mid-point of that for many contractors who live in cold weather climates, it’s important to start thinking about implementing best practices. For those who live in parts of the country that don’t experience cold weather offseasons, and can work virtually all year long, these steps should still be put into place at least once a year, and finding a time for it could make the difference between costly breakdowns and delays. In some situations, contractors have the proper space and facility to move their sealcoat tanks indoors to climate controlled conditions, even when they’re in an offseason and not sealcoating regularly. During these spans of time,
they regularly stir the tanks to keep the mixture from separation and/or settling.
1
DRAIN — Drain the tank as close to empty as possible by the end of the season, usually no later Thanksgiving for those headed into a cold off-season, but it varies by region and climate.
NOTE: It’s important to carefully manage your end of year sealcoat supply, in order to reduce waste.
2OPEN — Leave the top hatch and the back plate open allowing for air to flow through the tank to dry out any remaining material.
3WAIT — Allow the material to harden and solidify over the winter months as the tank drops to freezing temperatures.
4
CHIP — In late January or February when temperatures are consistently below freezing, chip away the solidified material from the inside of the tank walls and the agitator using pneumatic hammers or impact drills with 2-to-4 inch chisel attachments.
NOTE 1: Work from the top down or by sections to fully remove all residue down to the bare metal of the tank.
NOTE 2: Proper PPE (eye protection, rebreather masks, gloves, hearing, etc. are essential to protecting yourself and/or employees while working in the tank’s confined space.
NOTE 3: Chisels should be held at an angle of 45 degrees or less in order o prevent damaging the tank wall.
For more information visit https://pavemg.com/gdxf5q
5
CLEAR — Use air hoses to sweep out loose chips and thoroughly blow out the tank.
6
NOTE: It’s important to review local environmental waste regulations and follow them accordingly when disposing of the removed material.
WASH — Fill the tank 3/4 full with water and a detergent-based solution and circulate the agitator for 45-60 minutes to clean the inside of the tank.
7
FLUSH — Pump the cleaning water through the system to flush out all lines.
8
CHECK — Inspect pumps, lines and strainers and replace any components if needed before shutting down for the season.
NOTE: Any uncleared debris left in pump lines will result in costly and time consuming clogs, which requires the entire tank to be drained all over again.
Jobsite
fueling trailers and trucks
need
to be
able to handle every possible need to avoid a work stoppage.
Fueling trailers in the field are becoming increasingly available in the market to provide charges to electrical equipment on a jobsite. Federal, state, and local incentives are a part of the driving factor toward EV equipment adoption.
“The grid is very fragile, especially with the increase in natural disaster activities,” pointed out Keith Marett, CEO of Portable Electric. “This is where solutions like Portable Electric really fit in as well as just general use around construction sites.”
Marett noted his company’s mission, “is to remove the need for carbon based fuels at industrial sites, whether that be the power generation to power tools or whether that is inside the equipment itself they are using at the site. Our goal is to eventually migrate away from the use of those carbon-based fuels.”
In 2015, Portable Electric started making what it classifies as an e-Generator.
“This is a battery-based generator solution that allows us to produce in varying sizes AC power for all jobsite activities,” he said. “At the same time, we have combined it to have DC charging capabilities. You can power your tools and you can fast charge your electrified equipment.”
The company offers two portable generators and three mobile units that provide various levels of kWh capacity and output, peak power, charge time and lifecycle.
The Voltstack 30k features ‘Smart Hybrid’ technology, which seamlessly integrates a diesel generator to provide off-grid power when the battery reaches a low charge state.
The Voltstack ecosystem of portable electric generators and mobile hybrid energy systems can be recharged via the Portable Electric Sunstack folding solar kit. Integrating the Voltstack 5k with the company’s NeuronOS software enables users to track, analyze, and optimize energy consumption in real-time.
A 3-inch touchscreen display enables users to check critical alerts and monitor the Voltstack 5k’s charge status.
The generators are powered by grid power.
“You can bring our unit up to site and leave it for a few days depending
on the power needs of that site,” Marett points out. “Then you would bring it back to your warehouse, charge it up overnight, and bring it back to the jobsite the next morning.
“If you are truly remote and you do not have the ability to come back to the grid or facility, you can hook up a small gas generator or diesel generator to just purely charge up our unit. You are not running that generator all day. You are just running it for a period of time to charge up our unit, and then it would shut down.”
Because the charging solutions are coupled within a single unit, contractors do not have to invest in onsite charging infrastructure at their sites, Marett noted, adding that it aligns with construction companies’ goals to save costs.
“Another benefit is there’s no fuel handling, so you don’t have to have the diesel certification tickets in order to handle our equipment,” Marett pointed out. “Anybody can operate it. Everything is touch safe. There is no special skill or technician required.”
Marett said the fact that the company’s trailer solutions can be towed behind any class vehicle provides the benefit of not requiring a CDL or special license.
“It’s quite easily transportable as a
power source,” he added. “It works in lots of different scenarios. You might be off the grid quite a bit and it allows for that. We also do a lot of urban applications where there might be grid power at the site, but it might not be specifically where you are working at that site. It is basically a grid extension cord.”
Equipment and Portable Electric
To add to off-grid electric equipment charging, Volvo Construction Equipment and Portable Electric recently introduced the PU130. Designed, engineered, and built by Portable Electric, the unit enables rapid recharging of electrified construction equipment aimed at significantly reducing downtime and increasing jobsite productivity.
technology integrated, the PU130 is
With Portable Electric’s 48-Volt Direct Current Fast Charging (DCFC) technology integrated, the PU130 is designed to offer construction sites the ability to rapidly recharge equipment – such as during a lunch break – to service a full workday and beyond.
As with all Portable Electric power and charging solutions, the PU130 is designed to offer seamless connectivity with Neuron OS for remote monitoring through real-time data, analytics, and GPS tracking to optimize charging schedules and ensure maximum efficiency.
Ray Gallant, Volvo Construction Equipment vice president, noted that adding the PU130 to Volvo’s product offerings, “Represents a significant milestone in our journey toward sustainable construction practices.”
Throughout time, humans have adopted new technologies that create more efficiencies in work and life. Initially, they may not be cost effective, but eventually the trajectory of all electronic technologies – such as laptops, for example – become less expensive over time.
“We know a lot about the benefits of electrification,” Marett noted.
“Besides the ESG (environmental, social and governance) or ‘feel good’
side of it, there is obviously the reduction in greenhouse gases.
“A lot of electrified equipment has better efficiencies and can get better productivity than what the diesel equivalent vehicles can. Same
thing with our generators – the fact that there is no need for down time to replace the filters and oil, you get higher productivity.”
That does come at a premium, Marett added.
• True Rubberizing additive. Improves performance.
• Meets FAA-P-631.
• Builds viscosity for sand suspension
• Faster drying time
• Improves durability
• Excellent sand suspension
• Blackening Additive
• Speeds up drying by 75%
• Builds viscosity for sand suspension
• Improves durability
• 100% Acrylic and speciality chemicals
• Speeds up drying by 50%
• Does not change viscosity Improves performance
“Our products are a premium over the diesel equivalent,” he said. “It will come down progressively over time. A computer that cost thousands years ago now costs hundreds. That is the same thing with these solutions over time. Electric vehicles are going to get less expensive regardless of what is happening on the government side in terms of incentives.”
Marett noted the health benefits of EV equipment to workers.
“There’s definitely the benefit of no emissions,” he said. “The other benefit from a health perspective that relates to productivity is no noise. Our units are completely silent, so you do not have to worry about any hearing damage.
Marett said the biggest challenge he sees is that while contractors understand the benefits of having EV equipment, they have concerns about the time it takes to recharge it in the field, let alone finding grid access in doing so.
“At a jobsite, they want to make sure you’ve got the power there to charge the electrified paver or whatever they’re working with,’ he said. “You do not want to be down for hours on end while you are waiting for the unit to recharge.
“That is where our solution offers the ability to do a 20-minute quick charge. It can be done over lunchtime to get the work back up and running in a very high productivity way.”
Desmond Wheatley, Beam Global president and CEO, noted that while full electrification of transportation is starting with sedans and lighter duty vehicles, BEAM has already deployed its products for construction equipment.
“There are lots of markets where construction equipment is increasingly coming under regulations which are designed to minimize their particulate matters and other exhaust fumes, noise pollution in already built-up environments,” he noted.
As such, Wheatley predicts prices on EV technology – including construction equipment – will start to come down dramatically.
“If you’re laying asphalt down on roads, highways and parking lots, there’s not a ready supply of electricity at scale that’s required to recharge these types of vehicles,” he pointed out.
BEAM solves for that by delivering products to the site which generate and store their own electricity.
The EV ARC 2020 system is designed to generate and store its own electricity by tracking the sun to generate up to 25 percent more energy.
Battery storage allows users to charge during the night, inclement weather, and power outages. It is designed to fit inside a standard parking space.
“We don’t have to rely on a grid connection,” Wheatley said. “We do not have to connect to existing wiring or extend the utility grid to those locations in order to be able to charge. We are able to drop off a product which generates and stores electricity, and then delivers that to those pieces of equipment.
“What we find with the construction equipment we have already energized is looking at the way they typically duty cycle. People take breaks or the equipment is used for a while and then it is not used for a while.”
That means the equipment can be periodically charged during the course of the day instead of running it until it is empty and then trying to recharge it all the way, Wheatley noted.
One does not need a special license to transport the EV ARC 2020. The ARC Mobility Trailer can be used to tow the unit to the jobsite.
“If you have the skill set to tow a boat, then you can deploy one of these units,” Wheatley said.
The transport uses remote controlled
hydraulics enabling one person to stow, transport, place, and unstow.
While it essentially needs a flat surface, it can be deployed on grass, gravel, and sand. Although it weighs 10,000 pounds, its weight is dispersed.
With the trailer, users can deploy the units to where it is needed, “Which is perfect for construction because they finish one area of a project and they just pick it up and take to the next project,” Wheatley said.
The unit is rated independently to withstand 160 mph winds.
“The biggest issue is we are relying on light to make electricity. It does not have to be direct sunlight. But if you are in very cloudy, prolonged conditions you are going to generate less electricity than you do in situations where you have got a good sunlight. That is something that needs to be taken into consideration.”
Addressing concerns about having knowledgeable mechanics to fix any issues, Wheatley said the EV ARC 2020 has very few moving parts.
“We get live telemetry from the units – we’re able to see the state of health and manipulate them remotely,” he added. “They all connect either to a cellular network, or if there is no cellular, then we can use satellite. Just like your laptop, we can reboot them remotely. If it requires a visit, then we are sending somebody from our service team.”
For those contractors who do not want to invest in an EV fueling trailer, the units can be rented.
For example, Sunbelt Rentals offers portable and stationary EV charging stations, including DC fast chargers, Siemens Level 2 chargers, and more.
Sunbelt Rentals also has portable battery energy storage systems (BESS) with 5kW and 7kWh of energy. ■
Carol Brzozowski is a freelance writer covering the construction and related industries.
Since its introduction, the Weiler P385 has set the standard for commercial pavers. The P385C raises that standard.
Variable speed and reversible conveyors and augers and a 25% increase in tunnel height provide optimal material output.
Increase to 120 hp with the Cat® C3.6 Tier 4F/Stage V engine.
Modular conveyor drive and sealed chain case increase feeder system reliability and life.
Enhanced heat system performance with direct-drive hydraulic generator and elimination of GFCI breakers.
Summer means shifting into high gear on pavement maintenance and repairs. The winter months and spring rains always take their toll on pavements, so it’s good to review a few basic, timely repair strategies.
The winter freezing cycles and spring rains can cause weak spots in our pavement, often in the form of potholes. Patching potholes should be considered ‘urgent.’ They can pose a real safety hazard to vehicles – especially motorcycles and bicycles, and left unrepaired, they pose
a big liability for the roadway owner. So repairing them should be a very high priority. Also, unrepaired potholes are very conspicuous to the pubic, so bad for PR.
Fortunately, there are some excellent ‘quick patch’ products for making simple and immediate repairs to hazardous potholes. They usually produce good service life and excellent ‘bang for the buck.’ These special cold mix products use small, high-quality aggregate and proprietary asphalt binders to produce a very sticky mass that will adhere well and stay put in smaller, deeper potholes and small patches – even in the presence of water. But be careful… trying to use them as patches in larger, less confined areas will usually lead to their displacement /
movement, and their rutting or shoving out of the patch area. But in the proper application, with only minimal compaction via a hand tamper or a truck tire, these products densify to form a strong cohesive mass. A light sanding of the surface will help them blend in for aesthetics and prevent any pick-up or tracking of the asphalt binder. But always be sure to sweep up any excess sand, as it can become a slip / skid hazard –especially to motorcycles.
Various brands of quick-patch products are available – some even at the local home stores in 40-50 lb. bags. A few bags of these special materials in the back of a maintenance pickup can make everyone a pothole patcher. The products are also available in bulk for stockpiling.
Of course, conventional hot mix asphalt (HMA) can also be used for
patching potholes, as long as it can be kept hot. This will usually require a heated HMA trailer or patcher truck. Another helpful resource for a road agency is establishing a special ‘pothole hotline’ where citizens can report problems.
For larger localized failed areas, it’s usually necessary to remove the severely failed material and replace it with hot mix asphalt (HMA). Warm mix asphalt can also be used, but rubberized asphalt mixes (e.g. RHMA) do not lend themselves to hand work and should be avoided for patching applications. Best practices for these ‘digout’ patches include laying out a cut line at least 1 foot beyond the visible cracking and making the cut with a pavement saw, a jackhammer or a small milling machine.
The old pavement should be excavated deep enough to allow placement of HMA at least 50% thicker than the old HMA layer that failed. Making a thicker repair is based on the fact that the major costs are in the lane closures and crew time, so these thicker, more durable patches are cost effective. The underlying material – often aggregate base (AB) – should always be leveled and re-compacted. A heavy tack coat should be applied to the vertical faces of the HMA cuts to help provide a perimeter seal. When possible, heated patcher vehicles (trucks or trailers) should be used to keep the HMA material hot for making multiple patches. You should place enough loose material so that it requires 3 to 4 passes of the roller to make it flush with the old pavement. Multiple passes are required for good compaction. The end goal is a flush and well-compacted patch.
Checking the final surface of your patch with a straightedge can help prevent a patch bump or dip, especially important on higher speed roadways.
It’s important to note that a steel drum roller should only be used in ‘vibratory’ mode if it’s not touching the old (cold) pavement surrounding your patch. A vibratory steel drum contacting cold pavement will cause cracking surrounding your new patch. This means that on many smaller patches, rollers should only be used in ‘static’ (non-vibratory) mode.
Hot mastic products can also be used for patching – for both potholes and larger patches. Mastics can be used to fill wide cracks – say wider than about 2 inches – where conventional crack sealers aren’t recommended. These proprietary products use hot thermoplastic elastomeric binders, which tend
With
Understand
to retain flexibility to accommodate pavement movement. They contain high-quality aggregate to provide a repair that stays stable under wheel loads. The hot mastic materials require special heating/melting equipment, which can be purchased or rented.
The ravages of winter also can contribute to a rough-riding pavement due to raveling of the HMA surface in the wheelpaths. Often these pavements are in structurally sound condition, and just need a surface smoothing and leveling. Short of placing a new HMA overlay, microsurfacing is a lower cost way to improve smoothness – and provide a surface-sealing benefit.
Microsurfacing is an enhanced form of slurry seal that contains polymer modifiers, and filler such as cement, that combine with high-quality aggregate to create a tougher, more stable
slurry blend that can help smooth out a rough or rutted pavement. These treatments are also enhanced by the addition of chemical additives, allowing placement in cooler air temps, or even night work. Roughness or ruts deeper that an inch should be done using two lifts.
Spring and fall are the ideal seasons to do crack sealing – mainly because air temperatures are more moderate and cracks are open enough to allow for an optimum amount of sealant to be placed in the crack. Cracks greater than .25 inch can usually be effectively sealed. For wide cracks (greater than 2 inches) use a hot ‘mastic’ product (discussed above).
Asphalt sealant materials may be hot or cold (asphalt emulsion). To make them ‘sticky and stretchy,’ asphalt modifiers (e.g., polymers, rubber) are used. Material manufacturers should
be consulted as to the proper grade of material for your climate and traffic conditions. On higher speed routes, avoid ‘over-banding’ and sealant bumps, which can cause a rough ride. In harsher climates, consider pre-routing to widen linear cracks.
Since crack sealing can be unsightly, it is often done in advance of a full resurfacing. So, it’s important to understand that pavement maintenance and timely repairs of localized pavement problems can be very cost effective, since the ‘stitch in time will usually save nine’! ■
Roger Smith is a pavement consultant/ trainer in California and editor of the California Pavement Preservation Center Newsletter, www.csuchico.edu/cp2c/
For more information visit https://pavemg. com/7ew2qqvg
If you’ve been in business long, you know that having the right team in place is critical to a profitable and sustainable business.
If you’re doing things right, you’ve got a thought-out interview process and you’re spending time to select the right talent for your team. But, you’re not done once you’ve found them. Finding the right person is just the first step. Once they are on board, you’ve got to train them!
Great people can only do so much on their own. Without the right processes and systems in place, including adequate knowledge of those processes and systems, your team will not reach their full potential.
It is important to formalize your training program. Have a plan. Here are some key considerations when developing a training program.
• Training Point of Contact: Have someone responsible for overseeing the training of each new hire. Whether this person is performing all the training with the employee, this person should be responsible for developing the training plan, coordinating the schedule with appropriate parties, and checking in on the new hire’s progress. This POC may be the new hire’s manager or it may be someone who’s role is to oversee the training of all new hires.
• Consistent Schedule: For each new hire that starts, there should be a training schedule template that is used to develop their individualized training program. You want to ensure that all new hires who start with your company are trained in the same manner. Set out a Week 1, Week 2, and Week 3 schedule. Some companies may need a six-week training program, while others may only need to formalize two weeks.
No matter the complexities in your business, take time to develop a wellthought-out plan for showing your new hires the ropes.
• Systematize: When possible, systematize your training. If you need to train every new hire on your project management software, create a video of you training someone on the key components. This will ensure that every employee is trained on the same content and in the same manner. This also gives team members something they can refer back to after they have completed their formal training. Systematizing your training saves time, creates consistency, and provides ongoing support.
• Provide Refreshers: Starting any new job can be daunting, no matter how good your training program is. When new team members are being trained, they don’t have the background information and context to fully grasp every aspect of what they are learning. Providing a refresher training regularly can help team members to apply the knowledge they’ve learned through the formal training as well as the on the job training, allowing the information to “click.” Everything makes more sense after you’ve had some time under your belt.
• Make sure your training program includes a general overview of the business, your history, why you exist, and where you’re heading.
• Provide an initial overview of the systems and tools used in the business, but don’t dive too deep until the team member has had the opportunity to see your operations. This will help them to utilize the systems more effectively.
• Create a training vault or repository to store your training videos, schedules, handouts, and templates.
• Review your training program annually to update as your business evolves and systems change. Don’t skimp on your training program. Inadequate training can lead to less productivity, disgruntled customers, and employee turnover. The investment on the front-end is worth the long-term benefit. ■
Shauna Huntington is the founder and CEO of Fortiviti.
For more information visit https://pavemg. com/9zys7k
BY NICK HOWELL
IWhat happens when you have a lifelong client who retires, quits, is fired or promoted?
’ll admit I have never been to the United Kingdom, although I do want to go. Thanks to TikTok, I can spend hours glued to short reel-type videos. Some that have been popping up in my feed are of the U.K. King’s Guard.
I’m sure if you didn’t know of them, you may have heard the term “Changing the Guard.” This is a ceremonial process (also known as Guard Mounting) that happens a few times a week at Buckingham Palace. Watching these fascinating King’s Guards, it got me thinking of another changing of the guard. What happens when you have a lifelong client who retires, quits, is fired or promoted?
In my 27 years of business, I have been affected by this more than once. They say never to put all your eggs in one basket, but are you supposed to not take work from them in fear that they might leave one day? Of course not.
Here are a few “changing of the guard” instances I’ve been affected by:
• A very loyal client was a facility manager at Sears. We were his guy. If a job involved anything related to asphalt or striping, it was ours. As we all know, Sears succumbed to the evolving retail industry and is no more – and that was a client we had no way of trying to keep. That didn’t happen overnight, but still, when you lose such a loyal, long-term client, it can be tough.
• Another client in charge of many credit unions we service unexpectedly passed away. He was in his early 40s too, who would have thought?
• Another loyal client who was a manager at a local truck stop — which just happened to have acres of asphalt that always needed work — got promoted to a district-level job in an area that we don’t service.
My biggest and most-challenging change was about seven years ago. A retail facility manager at a large chain of stores that we worked for was offered an early buyout. First of all, this company gave us a lot — and I mean a lot — of work. So much work that I have enjoyed work trips on their corporate jet, being privy to executive planning meetings, etc. We had a great relationship and I and my company had become an integral part of their pavement maintenance operation. Well, one day out of the blue, in that perfect world, the company — needing to reduce costs — offered a companywide early buy out.
Oh no! Please don’t do it! But my friend and client had eyes bigger than a kid in a candy store as he stared at a huge six-figure payout. As luck would have it, he took it and ran. Can’t say I blame him (except I do think he failed to realize just how much of that prize was going for taxes). Anyway, I was now in a position that our best client had a new decision-maker coming in…what would I do? There were big dollars and steady work at stake, and I couldn’t fathom what was happening.
Luckily, we still had work under contract. So, as things turned out, I decided to do … nothing out of the ordinary.
We just continued to do what we do best and provid top-notch service to the
new boss. We worked as hard as we ever had and made sure that he didn’t have to worry about asphalt or striping; we made sure he knew we had it covered. The plan worked. To this day, our relationship continues, strong as ever. I do miss my old pal, though. Almost overnight, in each of these instances our work was gone — and in most cases we haven’t been able to get back in. Things can go either way, you just have to prepare. ■
Read the rest of the story online at https://pavemg.com/rfklha0t
Nick Howell, president of T & N Asphalt Services, Salt Lake City, UT, has been a regular presenter at National Pavement Expo since 2008 and a member of the Pavement Advisory Board since 2007. Let him know your thoughts on “From the Owner’s Desk,” and if you have a question or topic you’d like covered – let him know that too! You can reach Nick at nick@tnasphaltservices.com.
Finding skilled operators, is the most significant challenge in the industry.
by Nancy Terry
SweeperSchool is a comprehensive online learning platform that offers a wide array of programs and courses. These educational resources are the result of years of collaborative effort among NAPSA’s most experienced and respected industry professionals. Each program and certification path is carefully crafted to provide power sweeping operators and other industry personnel with essential knowledge about the trade, industry standards, and best practices. The ultimate goal is to elevate the level of professionalism across the entire power sweeping field.
While NAPSA currently provides three distinct certification paths catering to operators, managers, and general
staff, let’s focus on the opportunities available for Certified Sweeper Operators (CSO).
The CSO certification program offered by NAPSA is a cornerstone of professional development in the power sweeping industry. These courses provide comprehensive, in-depth training that covers best practices for operating power sweepers. The program offers specializations tailored to three key environments: municipal areas, parking lots, and construction sites. This certification path encompasses a wide range of crucial topics, including:
• Sweeper basics and troubleshooting techniques
• Health issues: Covering important aspects like nutrition, sleep, and safety protocols
• Pre-start procedures
• Safe sweeper operation guidelines
• Accident procedures and proper
response protocols
• Paperwork and recordkeeping best practices
The certification program is tailored to specific work environments:
• The parking lot credential is an extensive course covering 51 comprehensive lessons
• The construction credential is even more detailed, spanning 68 in-depth lessons
• Municipal sweeping currently has 27 lessons ■
NAPSA is dedicated to providing beneficial support to the membership and enhancing services to the sweeping industry. NAPSA is committed to promoting and educating the power sweeping community while enhancing the environment. For more information on NAPSA membership, please visit www.powersweeping.org or call (888) 757-0130.
by Ranger Kidwell-Ross
Power sweeping is a crucial maintenance practice that significantly extends the lifespan of pavement surfaces. It is by far the best way to remove debris, dirt, and other contaminants from roads, parking lots, and other paved areas, contributing to their longevity and overall condition. By regularly removing abrasive materials like sand, gravel and small stones, power sweeping reduces wear-and-tear on the pavement. When left unchecked, debris can act like sandpaper under the weight of vehicles, gradually eroding the surface and leading to premature deterioration. This includes more rapid degradation of pavement markings like parking area striping and lane control paint. Power sweeping also plays a vital role in preventing water damage. By
clearing away debris that can clog drainage systems, it ensures proper water runoff during rain or snow events. This is crucial because standing water can seep into small cracks or pores in the pavement, potentially causing expansion and contraction cycles that lead to more significant damage over time, especially in regions with freeze-thaw cycles.
Regular power sweeping also helps maintain the aesthetic appeal of paved surfaces. Clean, well-maintained pavements not only look better but also contribute to a safer environment by improving traction and visibility for both vehicles and pedestrians. This can be particularly important in commercial areas where appearance and safety are paramount.
Regular power sweeping can also aid in the early detection of pavement issues. During the sweeping process, operators can identify small cracks, potholes or other surface irregularities before they develop into more serious
problems. This early detection allows for timely repairs, potentially saving significant costs in the long run. By removing pollutants and debris, power sweeping also contributes to environmental protection. It prevents these materials from being washed into storm drains and ultimately into local waterways, helping to maintain water quality and protect aquatic ecosystems. Because of all of the above, power sweeping is truly the most cost-effective and efficient method for preserving paved assets. ■
By Merina Shriver, Junior Editor |
Pothole Heroes is striving to make a difference in the asphalt industry.
Potholes are a problem in the world of asphalt and everyday life. Pothole Heroes’ board of three key leaders has been working in the asphalt industry for varying amounts of time starting as early as 2017. While relatively fresh in the industry, the team has been making waves in Florida and some of the southeast areas of the United States.
Pothole Heroes strives to make a difference and be the difference in the asphalt industry. The company serves as an environmental and asphalt rescue crew of sorts.
As serial entrepreneurs, the three of them have been going between different industries and happened to find the asphalt world to be interesting.
Zach Young, chief operating officer at Pothole Heroes said, “Like many in the industry, we didn’t necessarily choose asphalt, asphalt chose us. I feel fortunate to have found this industry, I
get to work with a lot of great people.”
They agreed it’s a great business opportunity. They were each drawn to the industry for different reasons and each had their own skills and strengths they brought to the table.
“Andre’s familiarity with the larger mainline operations - he recognized that there was a segment that was not being fulfilled in the most efficient, eco-friendly manner and that’s how we then started developing the idea of Pothole Heroes,” said Rebecca Neidich, co-founder of Pothole Heroes.
The trio jumped into the asphalt industry with a more eco-friendly concept in mind. They wanted to fill the gaps in the industry that had all too often been forgotten and overlooked.
While focusing on the environment, the company is also providing a wide variety of services.
Young said the company does fullservice asphalt maintenance, patching, seal coating, and striping with a focus on infrared asphalt repair and patching.
Pothole Heroes is focused on ecofriendly methods and asphalt repair and patching. This consists of things like using less equipment and more restoring of material.
Andre Neidich, CEO and cofounder of Pothole Heroes said, “We go to the jobsite, we heat up the asphalt, we restore it, and renew it right at the jobsite. And make the repairs that way.”
On the typical jobsite, there are a lot of things going on. People are using lots of different kinds of equipment and are often going back and forth. This can create a lot of chaos and leave a huge environmental and physical impact during the repair process.
“Rebecca and I and Zach sat down and discussed [if] we [could] use a different type of technology to do these typical repairs where they would cut with a saw, and guys would pick it all out, throw it into a dump truck, and then haul it away,” said Andre Neidich.
Andre Neidich said that the three of them brainstormed on how they could reduce the amount of back and forth
Infrared technology is a less negatively impactful method of repairing and restoring asphalt. It allows for smaller crews with less equipment necessary.
Pothole Heroes
and equipment needed to complete jobs. They determined that if the job requires it, they will still do that type of repair, but when possible, they use infrared.
“Infrared technology seemed to be underutilized in so many areas, and so many states that we that it’s a known product, and it’s a known service that performs very well,” Andre Neidich
said. “It’s just a different way [to repair], it has a lower carbon footprint because we’re not running around with all these trucks and dump trucks and all this equipment. So, we felt it was a better way to do the job.”
Infrared technology is a less negatively impactful method of repairing and restoring asphalt. It allows for smaller crews with less equipment necessary.
While many asphalt companies might hand the repair job off to a subcontractor, Pothole Heroes does the work themselves. Due to the infrared technology that they are using, they can be a lot more hands-on.
“It’s a large, self-performing footprint. The customer’s experience really is everything. Just delivering on the promises we make I think is what differentiates us from most,” said Young.
The Pothole Heroes team strives to reduce the impact of their work to provide their customers with a better experience.
Young said, “Our clients have tenants who have expectations of access to property, and our goal is to minimally impact that. We can do it many ways but infrared [is] one of them, and maintaining a small footprint as we do it.”
Young discussed that some of the benefits of using infrared technology to repair asphalt include the physical imprint, as well as the environmental imprint.
The team at Pothole Heroes is making an example of themselves that positively impacts their company by simply picking up the phone.
NR-201 is a one-part, selfleveling, moisture-curing, isocyanate free sealant based on a unique hybrid STPU (Silyl Terminated Polyurethane) designed for use as a traffic loop sealant and applications requiring jet fuel resistance.
300SL
300SL is a self-leveling onepart, ultra low modulus elastomer designed for sealing joints in roadways.
301NS
301NS is a non-sag, one-part, ultra low modulus product designed for sealing joints in concrete or asphalt.
322FC
Pecora 322FC is a two-part, coldapplied, self-leveling, fast-curing, ultra-low modulus 100% silicone material designed for the sealing of concrete pavement joints that experience thermal movement.
All too often, companies fail to pick up the phone when it rings or have set up an AI or robotic answering system. If not an answering system, customers often get their calls answered by a call center or someone who only answers calls all day and might not even know anything about the industry at all. Pothole Heroes takes the idea of customer service very seriously and strives to always have a live human pick up customer calls. On top of that, the human is someone who can answer important and specific questions.
Pothole Heroes aims to fill multiple areas that are often lacking in the asphalt industry. The company has a goal of being environmentally friendly, having a small footprint while also selfperforming, and being a company that is accessible to the public. It aspires to be a place that customers can go to and feel comfortable and pleased with its work and communication. ■
For more information visit https://pavemg.com/ q01ooo95
After more than 35 years of consulting with contractors of different sizes and specialties, one common ailment might be the lack of more in-depth planning for project success.
What makes contractors NOT plan?
A few reasons I’ve witnessed include:
• “Got to get to the next job…NOW!”
• “We have too many jobs to really plan out the execution of each one.”
• “I’ve got experienced guys…they’ll figure it out.”
• “100% of the projects are going to change 100% of the time.”
• “We do small jobs; I’d spend more time planning than it would to just do the job.”
The truth is that most contractors have simply never been educated on the components of planning. Let’s explore the six pieces of planning that can put greater success into your next project.
TIME is the most important. Planning is a forward-projecting exercise, setting out time requirements and deadlines, which are the very crux of planning. Time can be represented as project time, the next week of activities, monthly scheduling, etc.
WORK TASKS are the actual hands-on tasks that must be identified, prioritized, and set in order, for the project to be completed right.
PEOPLE are the human resource who develop, execute, support, and monitor the plan and project fulfillment. By planning, leaders can leverage their people with clarity and confidence, placing their people in the best position to be effective, productive, and safe. It may be as simple as adding one more finisher to a concrete project or as complicated as figuring out how to have your best equipment operator on two projects on the same day.
RESOURCES include the obvious: materials, equipment, tools, information, people, etc. Any plan needs to clearly assess what resources are needed, before the project begins, to account for all needed resources, thus strengthening the fact that we have all needed resources to complete the project the right way the first time. Never allow your crews to go to a project without a clear plan on what is needed, are the items on the trucks and trailers, and whether all the mechanical resources in working order.
NEEDS/EXPECTATIONS are seldomly documented in a plan, yet they are crucial to
planning. Both can be applied to recognizing what your needs or expectations are to complete the project, what the needs or expectations are of your crew leader and members, and who is executing the plan. Even your customer has needs or expectations that may be associated with the completion of the project, both quality and time requirements. What are your needs or expectations for your crew on completing work? What is expected or needed from your customer?
COMMUNICATION AND NETWORKING drives ongoing communication between all participants and recipients of a project. Calling to confirm or to set up a material delivery is obviously needed, yet I have witnessed contractors who assume that the asphalt, concrete, or sealcoat plant are up and operating. Networking provides you faster access to a change that is suddenly confronting your schedule; “it’s who you know sometimes that is more critical than what you know.”
So much of planning today is executed on an app or on software, yet all the same six components listed above need
to be considered when planning and on whatever platform you use when planning. There is an old axiom, “Failing to Plan is Planning to Fail!” It still applies today. Do not fail to plan as you tackle projects of all sizes and complexity. Sometimes it’s the smallest project that was supposed to be your “slam dunk” project that winds up costing you three times what it should have cost to complete the job. There are enough “hiccups” that can show up on any project, planning helps to mitigate many of the surprises while also giving you an even faster turnaround time toward changing directions on a solution without it costing you too much in time and resources.■
Known as The Contractor’s Best Friend, Brad Humphrey continues to write and speak in support of the construction industry. His international podcast, sponsored by IRONMARKETS, continues to be one of the favorites of suppliers and contractors alike. As vice president of Pavecon Ltd., a large and growing pavement maintenance contractor, Brad continues to develop, teach, write, and share his 35-plus years of industry knowledge.
DESIGNED TO HONOR CONSTRUCTION PROFESSIONALS FOR THEIR ACCOMPLISHMENTS IN SHAPING THE INDUSTRY
Construction professionals - working in the heavy equipment, asphalt, pavement and reconstruction, concrete, and rental segments - can be nominated for any of the following categories:
• Women in Construction: Honors females in the construction and rental industries, whose accomplishments, mentorship and examples set a foundation for women in all levels of a company’s network.
• Rising Professionals in Construction: Recognizes outstanding young or newer construction professionals whose achievements, hard work and vision have shaped the construction network. Rising/emerging professionals must maintain 1-9 years of experience in the construction industry.
• Lifetime Achievement: Honors contractors, workers and owner/operators who’ve made outstanding contributions to the construction and rental industry. Must have at least 10 years of documented accomplishments in construction.
• Jobsite Excellence: Recognizes outstanding workers on the job site whose leadership and work ethic set a strong example companywide.
https://myfc.pro/paceraward