
5 minute read
USNR
The efficient layout affords ample room for the new technology in a very productive operation
Montrose Forest Products: Expanding fortunes
Advertisement
The bottleneck at this Colorado plant is gone and in its place is an efficient operation focused on a new line of high-value production
Montrose Forest Products recently added a new planer mill to its operation in Colorado, to expand its product mix and align it with its sister mills. Through this investment the mill also planned to ease the bottleneck that was constraining production at the sawmill. Today the new line is hitting the targets Montrose set out, and several more that were unexpected.
The Montrose operation comprises a sawmill, planer mill, and two lumber dry kilns, and prior to this latest project it was strictly processing Engelmann spruce and lodgepole pine into stud length lumber. The Neiman team wanted to expand the scope of this mill’s products to more closely align with its other three operations that produce 1x4, 1x6, and 1x8 lumber products.
The team contacted the US Forest Service and came to an agreement to include green ponderosa pine in the Montrose mill’s mix. This paved the way to add 1" products to the Montrose operation.
The vision
The existing planer mill technology had long become outdated, and was causing bottlenecks that adversely impacted the sawmill’s production and the overall several mills with USNR’s planer mill technology to see how it was benefiting those operations.
Service and support was another big factor in the decision making process, and the many positive business dealings the Neiman mills had with USNR was a strong motivation to trust USNR for this latest major investment. Mike reiterated: “That’s one of the reasons we chose USNR. We know we can get in contact with USNR folks any day of the year for phone support, parts, and service scheduling.”
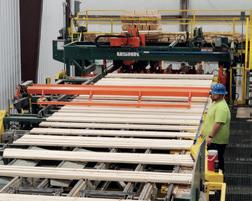
The low profile planer mill stacker is fitted with magazine lath placers, filled from above. This stacker operates at speeds in the range of 23 tiers/ minute efficiency of the operation.
Mike Kusar, Montrose Mill Manager explained: “With newer technology at the sawmill we were making more lumber than the planer mill could keep up with, so we knew we were losing out on opportunity. We were also interested in what automated grading technology could do for us.” Another Neiman mill, Devils Tower Forest Products in Hulett, Wyoming, had recently invested in a USNR Transverse High Grader (THG) for its dry mill, so the team was familiar with the benefits of this technology.
Mike said USNR was chosen to supply this project on a turn-key basis because of recent successful projects at the Neiman mills. In addition, his team traveled to
John Jacques, USNR Turn-Key Project Manager
The new line
The new planer mill line is designed to run at speeds of 180 lpm and above, depending on product size. The supply begins with the planer infeed featuring a Continuous Tilt Hoist, stick and dunnage collection, planer, Quad Cam lug loader, Multi-Track Fence,
Mike Kusar, Montrose Forest Products
back-to-back lineshaft multi-saw trimmer with P.E.T. saws on a second shaft downstream from the trim saws, 30-bin pusher lug sorter, low profile stacker with magazine lath placer, and quad paper feeder and cutter. The low-profile stacker is a real high speed design, operating at speeds in the range of 23 tiers per minute.
Included in the project is USNR’s THG with Deep Learning technology for the best automated grading capability available today. The THG features an end grain scanner used to locate a board relative to its parental log. This provides the optimizer with data for use in knot projection and pith location. The THG integrates USNR’s WinTally system for management of sorts for targeted products the mill wishes to produce.
USNR’s MillTrak machine visionbased system manages the flow of boards at the planer infeed, and the MyMill mobile sorter control monitors and controls the sorter from any location within the mill’s network.
The turn-key portion of the project contributed overall project management; site engineering for foundations, civil work, new metal building, and support steel; geotechnical soils reports and recommendations; electrical wiring; data and communications wiring; site utilities; excavation; residual systems; dust and shavings extraction; planer room; mill air system; embeds; grounding grid permits and inspections; construction management; and installation of all machinery.
John Jacques, USNR turn-key Project Manager: “We did not encounter any serious challenges during the construction phase. It was a pleasure working with the Montrose Forest Products and Nieman team. We had great communication and collaboration throughout the design and execution phases of the project.”
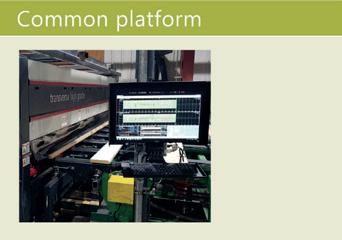
Results
Mike commented on the results the mill is experiencing with this project: “The new planer mill has improved our overall efficiency and relieved our bottleneck, resulting in a reduction of over 20% in planer mill run hours. In the new planer mill we are able to process all the products from the sawmill in 40 h/ week, and we are able to run our sawmill full out now. Our packages also look better and neater.
“Before the project I had concerns with the switch from human graders to the THG, but USNR did a great job of training our quality control staff prior to the startup.”
Mike also talked about the reduction of labour and increased employee satisfaction: “Through attrition we’ve lowered our headcount in the planer mill by more than 10 people. Our new facility has also resulted in improved overall employee satisfaction with a nice new building, new workstations, and everything automated. This will help with employee retention.
“Lastly, with this new technology we look forward to being able to offer more products to our customers than previously. That’s one of the key goals for taking on this investment. It will contribute to a safer, more efficient, and more profitable operation.”
The Transverse High Grader shares the same Deep Learning optimization platform with all other USNR vision grade scanning products: Lineal High Grader, BioVision for green mill grade scanning and AddVantage chop and rip scan products for the secondary manufacturing sector. Recent additions to this platform are the NV4g and GSc2000 for green and dry veneer grade scanning. This technology is proven on a variety of species and wood processing sectors.
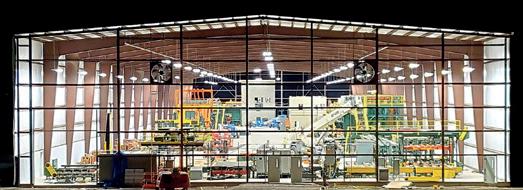