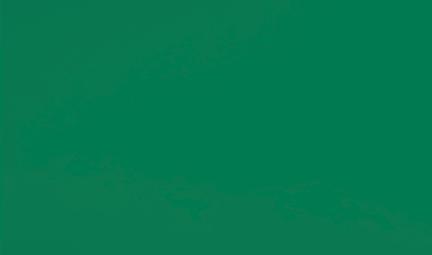
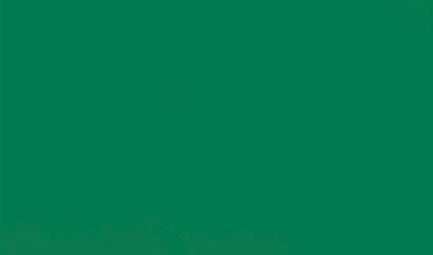
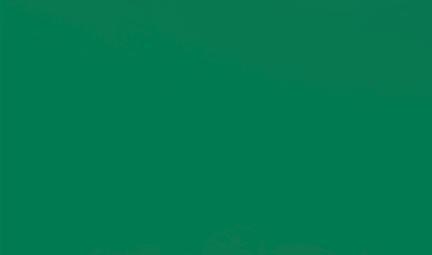
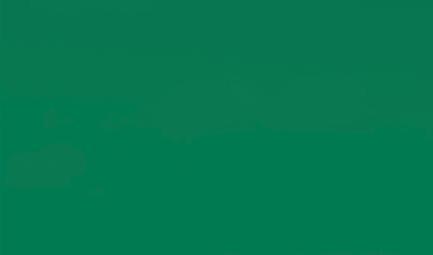
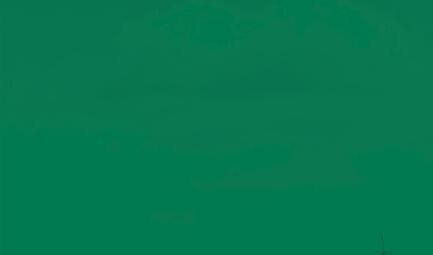
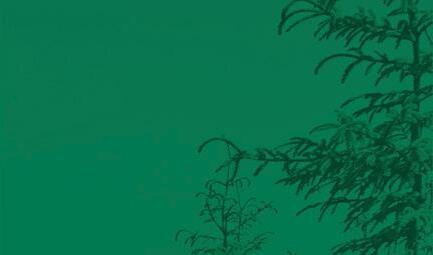
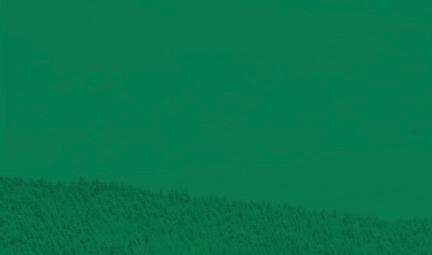
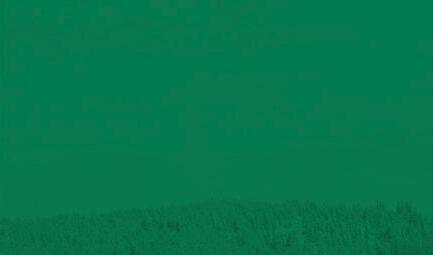
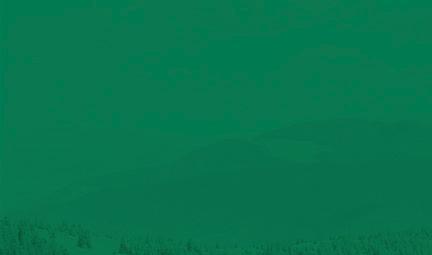
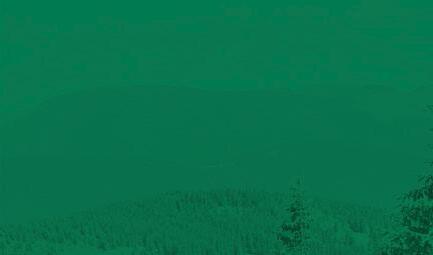
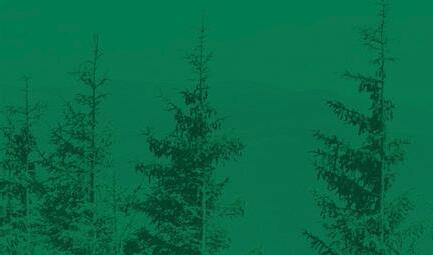
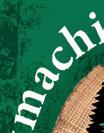


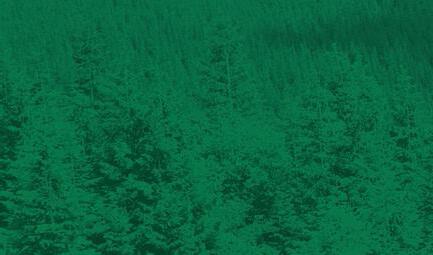
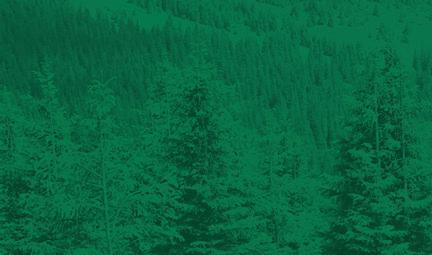
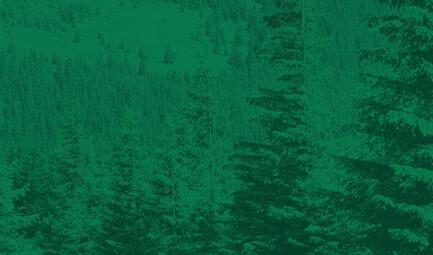
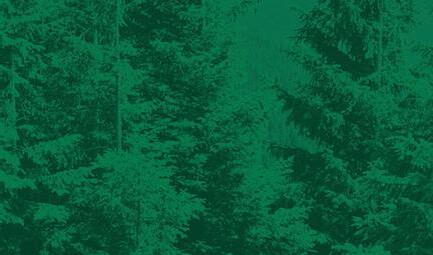
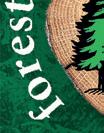
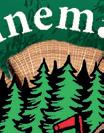



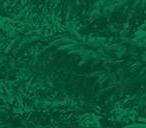
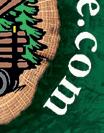
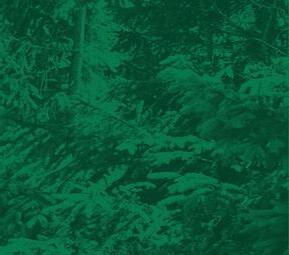
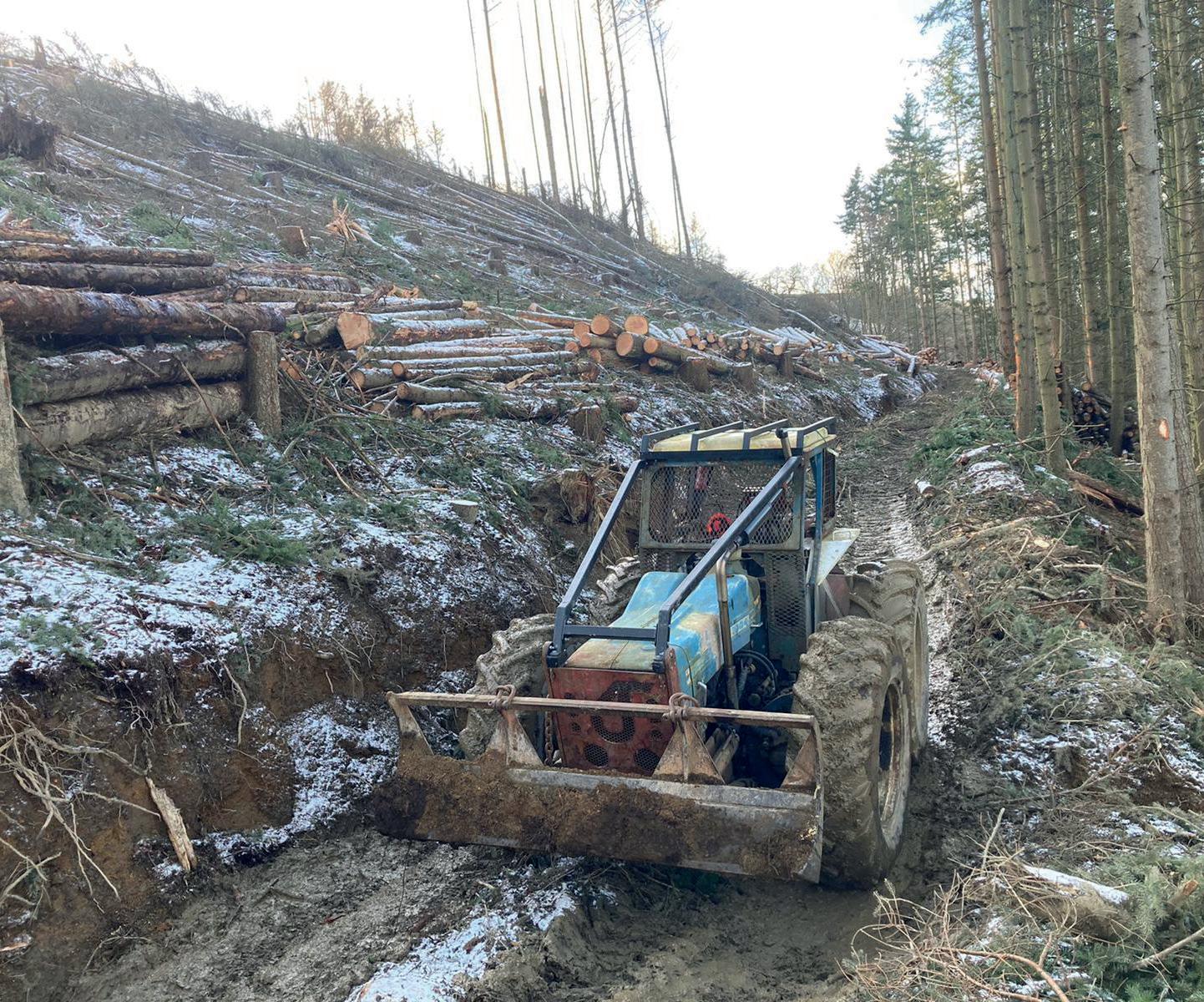
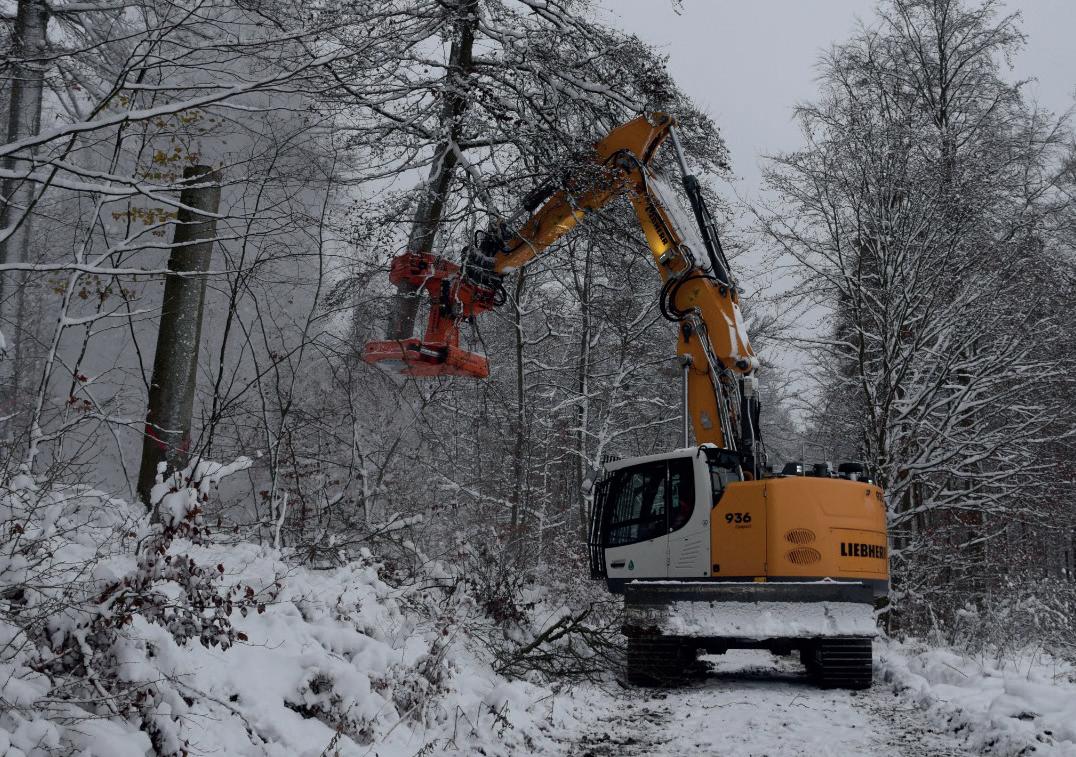
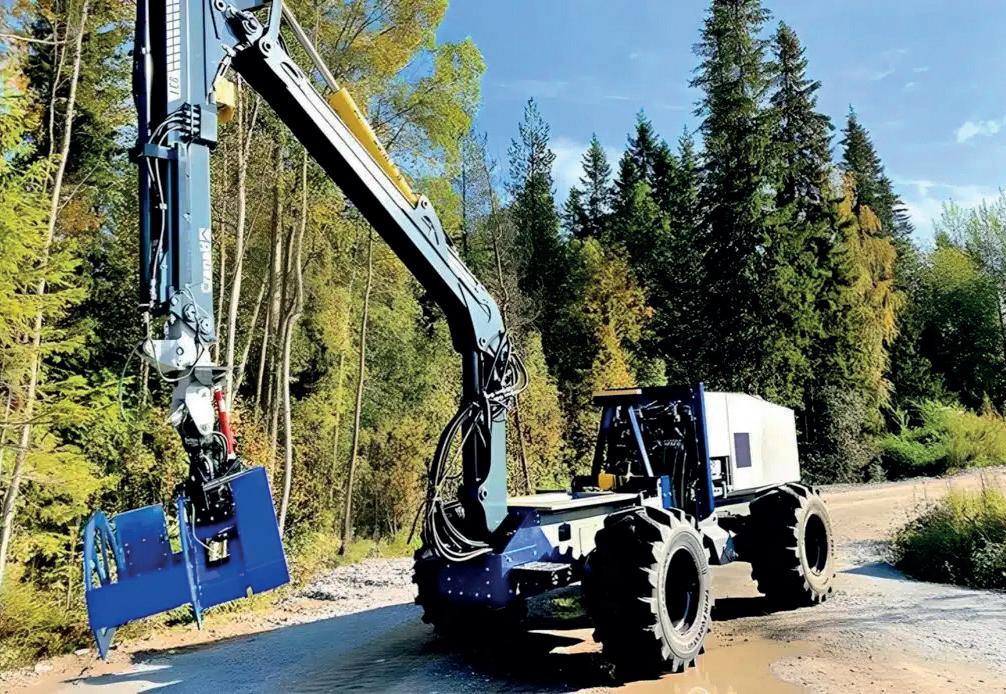
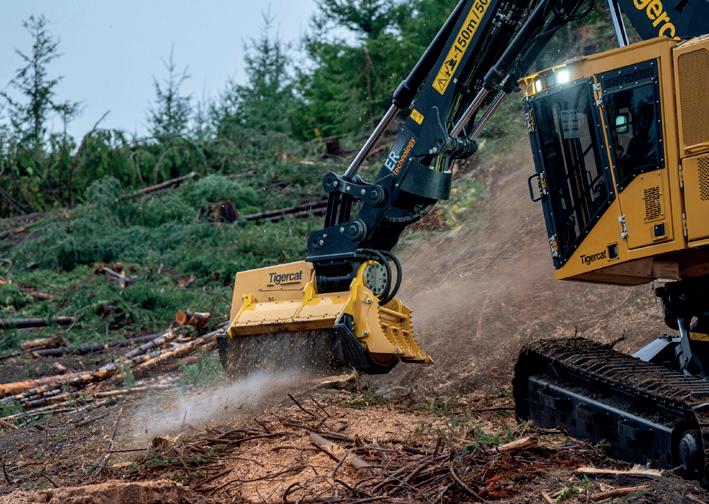
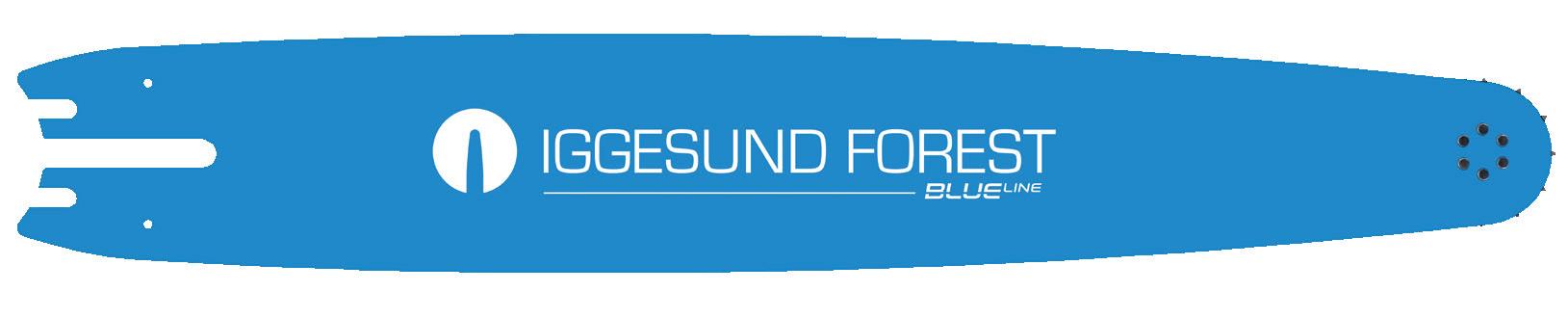
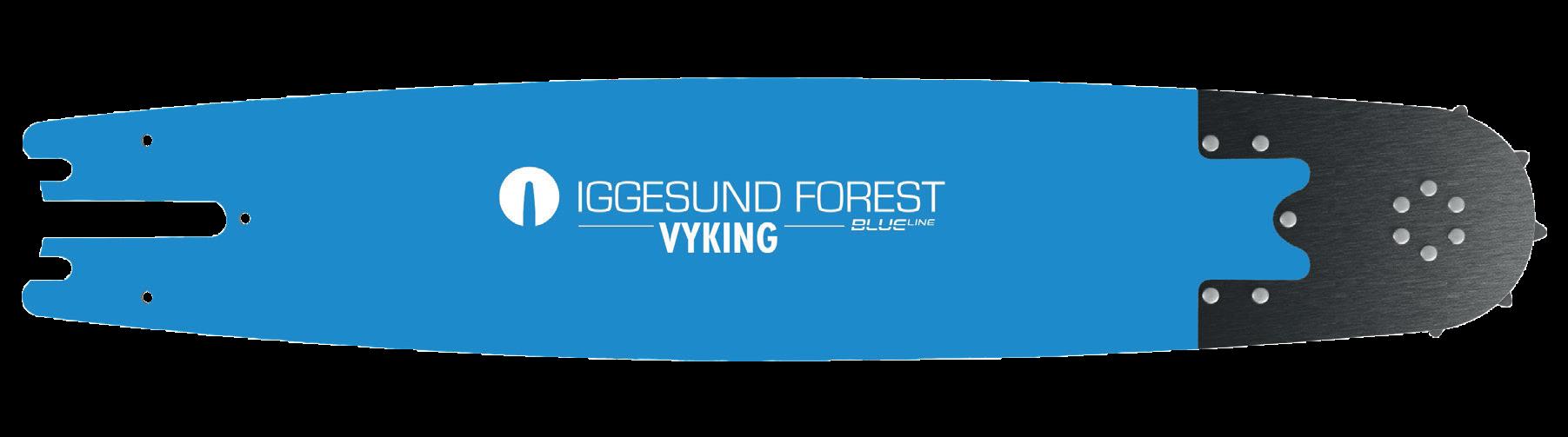
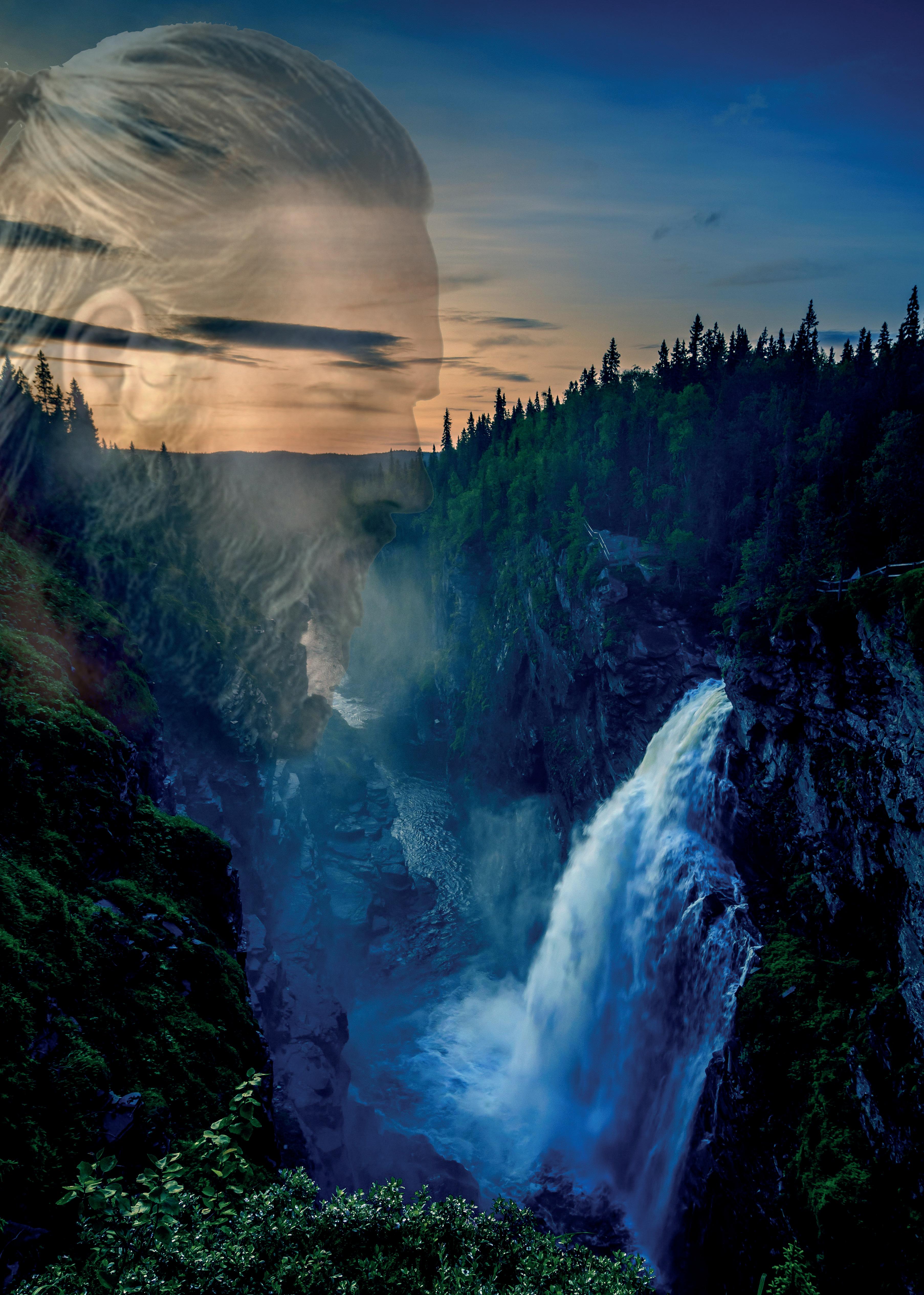
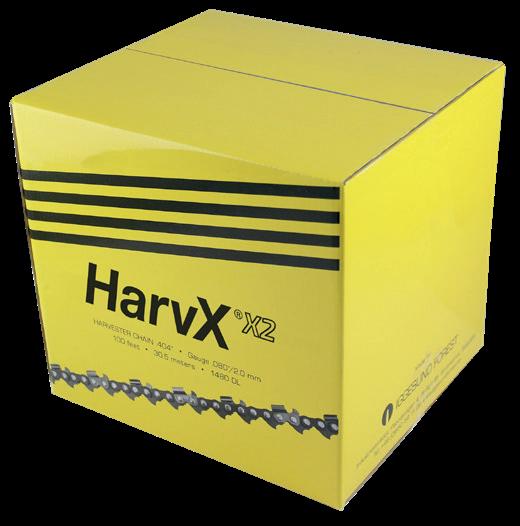

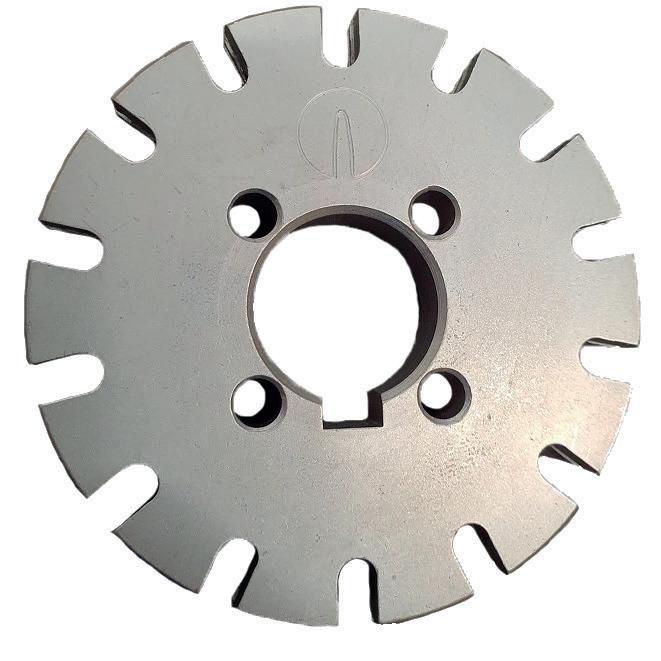
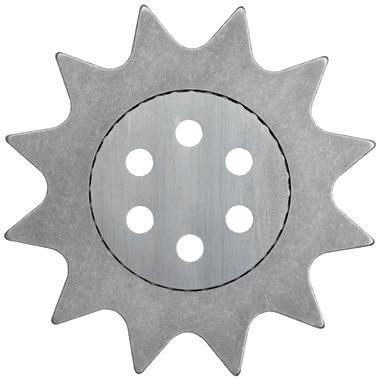
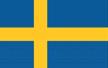
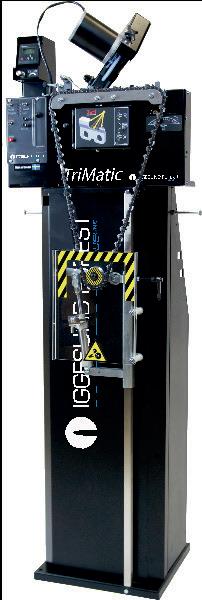
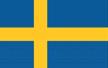
As you will read in this issue, Forest Machine Magazine is up for sale.
There is no need for alarm, as normal service will continue while we
look for a buyer or an editor to take over the day to day running of the magazine.
I am officially an OAP this year and have to admit that a lifetime of working in the forestry has taken its toll. I find site visits, attending exhibitions and rushing around airports a damn site harder than they once were.
Simply climbing up into machines is not an easy task anymore. Joints don’t bend the same, as I am sure those operators that are in their twilight years can agreed. Another step on the ladder wouldn’t go amiss. ☺
Bobby Melvyn summed it up in a nutshell when we attended the Swedish Forestry Expo last year. On our last day we decided after the show that we would discover what delights the bars of Stockholm held in store. The bars are fairly well spaced out and involve a fair bit of walking between them. While we were searching for our fourth pub Bobby asked if there was a supermarket nearby, Harold Taylor asked why he wanted a supermarket to which Bobby replied, “To get a trolly for Rab!”
Publishing the magazine has been one of the best things I have ever done. Wendy and I have had lots of amazing trips, been treated like royalty by distributers and manufacturers, and have made some great friends along the way. When we first started, I was extremely apprehensive as I thought that we were pushing the boundaries and neither Wendy, or I had university degrees or any publishing experience whatsoever. We flew by the seat of our pants into mysterious territories and hadn’t a Scooby what to expect. Almost eight years later we are still going strong and immensely proud of what we have achieved in that time. Why not give us a shout to find out more.
Get a regular dose of forestry on our Facebook page.
Share your photos and experiences.
Stay in the loop with the latest news from the forest industry. We love to see your photos too!
Subscribe to our YouTube channel to enjoy our dedicated forestry videos.
#homeoflogging
March 2024 Issue 45
ISSN 2398-8568
Editor and Publisher
Robert Easton
Advertising
Rab Easton
Social Media Manager
Rab Easton
Layout and Design
Wendy Easton
Subscriptions
Wendy Easton
Photography
Wendy Easton
CONTACT US
forestmachinemagazine@mail.com
+44 (0)7582055748 / +44 (0) 7951 473 846
Website: www.forestmachinemagazine.com
Address: 33 Holm Gardens, Bellshill, ML4 2PB. UK
Forest Machine Magazine assumes no liability or responsibility for any inaccurate information, errors or omissions. Forest Machine Magazine considers its sources reliable and verifies as much data as possible. However, reporting inaccuracies can occur and consequently readers using this information do so at their own risk. The opinions expressed in each article are those of its author and do not necessarily reflect the opinions of Forest Machine Magazine. Therefore, Forest Machine Magazine carries no responsibility for the opinions expressed thereon. Through the magazines you are able to link to other websites which are not under the control of Forest Machine Magazine. We have no control over the nature, content and availability of those sites.
The inclusion of any links does not necessarily imply a recommendation or endorse the views expressed within them.
No part of this publication and/or website may be reproduced, stored in a retrieval system or transmitted in any form without prior written permission of the Publisher.
© 2024 Forest Machine Magazine. All rights reserved.
www.forestmachinemagazine.com
A quick, easy and secure way to subscribe
Name:
Address:
Postcode:
Email Address:
Tel No:
If you are taking out this subscription as a gift for someone else. Please complete the gift recipient’s details.
Name:
Address:
Postcode:
Email Address:
Tel No:
UK only - I wish to pay £15 p&p for 6 issues of Forest Machine Magazine
Europe - I wish to pay £35 p&p for 6 issues of Forest Machine Magazine
Rest Of World - I wish to pay £45 for 6 issues of Forest Machine Magazine
Please make cheques payable to:
Robert Easton Ltd
Please return your completed form to:
Forest Machine Magazine, 33 Holm Gardens, Bellshill, ML4 2PB.
Government Let down: Scottish Ministers show no commitment to forestry by slashing the replanting budget.
Your Oil I Need: GB Lubricants recognised as a global leader for sustainability and minimal environmental impact.
Business Opportunity: Forest Machine Magazine, website and social media pages are looking for a new owner.
Cutting Edge: Vimek presents their new thinning harvester.
Hands Free: The first real trials exploring the feasibility of autonomous forestry operations were held in Sweden.
Gripping Story: We find which are the best selling profiles of band tracks from the leading manufacturers.
A Bright Future: We visit Western Bio-Energy’s chipping operation, power plant and harvesting contractors in South Wales.
Kids Corner: Puzzles to keep the young loggers entertained.
Another Milestone: Tigercat manufactures and sells their 30,000th machine.
Keep On Trucking:Volvo introduce their most powerful lorry engine to date.
NEXT ISSUE AVAILABLE From 25th April 2024
Just when logistics teams were beginning to breathe a sigh of relief after the challenges of the pandemic, they begin 2024 with new issues. Backed by Iran, Houthi rebels have attacked several commercial vessels in the Red Sea in recent weeks and this has led to all commercial containerships avoiding the Suez Canal and rerouting via the Cape of Good Hope. The alternative route adds thousands of nautical miles and 13-14 days of travel time.
Ola Holgersson, Södra Cell’s Logistics Manager: “Södra’s shipments in this region are delivered via our trading house partners and we have longstanding relations with shipping companies. Our own chartered vessels sail only within Europe. Pulp shipments through the Canal are dominated by
softwood rather than hardwood, primarily from Finland but also with small amounts from Sweden and Germany.
“We are liaising closely with all our partners in the logistics chain, but some global supply disruption is inevitable, and we are no exception. There is always a knock-on effect when one link in the chain is changed, and we are now looking at holding stock in European ports for several weeks as we wait for delayed containers.”
“Sea freight costs to Asia from Europe have increased significantly as a consequence of the situation in the Red Sea,” adds Knut Omholt, Södra’s Market Research Manager, “but this rise is nothing like the price hikes we witnessed during the pandemic, and nor is the disruption so far. There will
inevitably be delays to shipments, for us and for everyone else shipping rerouted goods, and this combined with delays to goods arriving late at their destinations will likely lead to some inflationary pressures. But again, we are hopeful it will not be anywhere near the scale witnessed during the pandemic.
“It’s also worth noting that the route works both ways,” continues Omholt. “While shipments from Europe to Asia are adversely affected, so too are those from Asia to Europe. In the short term, this could prove a temporary boost for European paper producers as we see the cost of Asian paper exports to Europe increasing.”
“We learned a lot from the pandemic’s supply chain disruptions,” adds Holgersson. “We have emerged more responsive and agile and are working hard to find the best solutions for all affected customers.”
www.sodra.com
Forest Live, the summer concert series presented by Forestry England, has announced that British pop superstar Paloma Faith will perform a headline show in the unique outdoor setting of High Lodge, Thetford Forest on 27 June 2024.
Paloma Faith is the latest
headliner to be announced for the esteemed concert series, along with Canadian rock icon Bryan Adams, Sting, Tom Jones, The Charlatans, Johnny Marr, Becky Hill, Anne-Marie and Richard Ashcroft.
Forestry England uses the money Forest Live raises to maintain beautiful natural
areas for everyone to enjoy, run important conservation projects and keep growing trees. Last year they planted some 7.4 million trees, caring for the nation’s 1,500 woods and forests sustainably and welcoming 291 million visits in 2022-23. Everyone in England lives within a one-hour drive of one of the nation’s forests. Over
A200-year-old Moray nursery growing millions of seedlings for new woodland creation has been left devastated after the funding for tree planting targets has been cut.
Christies of Fochabers, have 130 million seedlings growing as part of the Scottish government’s expanding forestry targets, which is critical for tackling climate change. As part of its commitment, the Scottish government stood to increase planting targets to 18,000 ha from this year onwards, which would require 28 million seedlings annually. This latest cut will result in around 9,000 ha being created.
Yet again the Scottish government shows its lack of commitment to forestry by slashing the 2024 budget from £77.2 million to £45.5 million, a cut of 41%.
As our population increases so does our demand for timber products and our need for more forestry areas for recreation.
two million people have enjoyed the Forest Live gigs over the last twenty-three years.
This year, they present the concerts in partnership with Live Nation’s Cuffe & Taylor for the first time. Gigs will take place at six forests throughout England
The public should be made aware that sustainable, well managed timber forests, and timber harvesting is essential so that forests are profitable. This allows the money to be reinvested into recreational forests so that they are well maintained and therefore safe for the public to visit.
Mr Christie, who owns the Fochabers nursery, is shocked by the cuts as it is a three-year cycle to grow the seedlings. If the government refuses to change its decision, ten million seedlings will have to be destroyed and skilled workers laid off. Some of the seedlings that will have to be destroyed include Caledonian pine which cost around £3,000 per kg for seed.
Scotland was leading the UK in tree planting with an ultimate aim to increase tree cover from 19% to 25% of the land mass. Unfortunately, in recent years, Scottish ministers have missed both their tree planting and greenhouse gas emissions targets. This will further widen
— Delamere Forest, Dalby Forest, Sherwood Pines, High Lodge Thetford Forest, Westonbirt Arboretum and Cannock Chase Forest. Fans can sign up for information, announcements, and exclusive pre-sale access at www.forestlive.com.
the gap between targets and results.
It has been proven that tree planting is the cheapest way to lock up carbon yet last year alone we had a tree planting target of 15,000ha but managed to plant just over half of this at 8,200ha. Now is the time for action before it’s too late. Forestry and wood processing employs almost 40,000 people and is worth virtually £3 billion to the UK economy but is still ignored by government. We need someone with courage that isn’t afraid to roll up their sleeves and fight hard, to represent forestry.
Can you imagine the outrage when forests left to their own devices have to be closed to the public. Roads and footpaths would soon become overgrown with hung up and blown trees rendering them unsafe due to neglect. If something isn’t done soon, we will lose yet another home-grown industry and be solely dependent on imports for all of our timber requirements.
Gateshead-based GB Lubricants’ mission to be recognised as a global industry leader for sustainability and minimising environmental impact has received a massive boost.
The company, which has been blending high quality oils, lubricants and greases since 1877, has achieved the highest possible EcoVadis Platinum rating in Sustainability and CSR (Corporate Social Responsibility).
Having achieved a gold rating since 2019, GB Lubricants now joins the elite top one per cent of companies that are evaluated from the industry worldwide. EcoVadis independently audited GB Lubricants on the company’s business practices. These included environmental, labour and human rights, ethics and sustainable procurement assessments. GB Lubricants scored an impressive 81% overall, against an industry average of 50%.
Aiming to achieve net zero carbon manufacturing by 2030, the company’s long-term mission is to be as sustainable as possible in its purchasing of raw materials, manufacture of products and delivery of finished goods.
A series of projects implemented during 2023 contributed to GB Lubricants
achieving the Platinum award. They include minimising waste, capital investment into new production facilities and infrastructure, as well as becoming the first private company to connect to green solar generated electricity and mine water heat provided by an award-winning Gateshead District Energy Scheme. This green electricity and heat are used throughout the production and administration process at their Gateshead, UK site.
In preparation to connect to the green energy, GB Lubricants had to make major investment in groundworks, large scale pipework, electrical infrastructure and, monitoring systems to ensure that the company utilises the electricity and heat in the most efficient way.
By signing up for 20 years, the company is demonstrating its commitment to sustainable electricity and heat to power the business in the future. GB Lubricants’ Managing Director Paul Booth explained “For the company to achieve the highest award possible is certainly a highlight of my career to date. I could not be prouder of the team in working together to achieve this and it’s the culmination of incremental improvements in many areas of our business activities.”
“A result like this doesn’t
happen overnight and sustainability has been an integral part of our long-term strategic plan ever since I arrived in 2016. Our aim is to be at the forefront of low carbon, sustainable manufacturing for lubricants worldwide. The Platinum award further cements our position as the supply partner of choice for customers and potential customers wishing to improve the sustainability of their own supply chain.”
“There is a strong emphasis on continuous improvement, so our targets get higher each year. The success in achieving the EcoVadis Platinum award is the culmination of cross departmental teamwork and incremental improvements in many areas of our business activities.”
Richard Knowles, Health & Safety and Business Systems Manager, added: “Using such a globally respected auditor as EcoVadis, with its rigorous approach to continuous improvement, has really helped drive our sustainability strategy forwards.”
“We focused heavily on environmental and social values in 2023 and I’m delighted to see our scores for both of these areas rise significantly in reflection of this.”
“It’s has been a real team effort and personally it is pleasing
to work for a company that is making tangible strides forward with respect to long term sustainable goals. It is great the business has been recognised in this way. We are already planning further improvements for 2024 and beyond.”
GB Lubricants’ success over its long history has been built on a solid foundation of quality manufacturing processes, continual product innovation and excellent customer service. The company’s long-term goal is to reduce its carbon footprint and improve the sustainability of all its operations and across its supply chain. This flows from raw material supply, production through to transportation and customer service, all underpinned by the EcoVadis rating.
Paul’s mission is to help ensure a positive, prosperous, and sustainable future for the company, its workforce and the local community, but also, it’s wider global network of both suppliers and customers. He continues,“We have a responsibility not only to our local community, but to our environment as well as securing a sound future for the business and our diverse customer base across the globe,” he said. “Our customers rely on us for oil and lubrication products that ultimately help improve the efficiencies of a wide variety of vehicles, equipment and specialist machines.
“We all have a part to play. Businesses need to be flexible and forward-thinking when discussing aspects of sustainability and future
strategy.”
GB Lubricants’ products, which are used in many industries, reduce friction, control heat and minimise wear, thereby helping to lower emissions, improve fuel efficiencies, increase reliability and reduce downtime of engines and mechanical equipment.”
GB Lubricants operates to numerous ISO standards, including 14001 (Environmental Management) and 50001 (Energy Management). The company identified the need to be externally audited and certified for sustainability in 2016 to benchmark its performance and help set strategy.
As a United Kingdom Lubricants Association (UKLA) Board member Paul believes the transition from traditional hydrocarbon fuelled internal combustion engines to alternative forms of drive presents the sector with an opportunity to spearhead sustainable solutions as new technologies emerge.
“The importance of forward-
thinking research and development to incorporate the most sustainable formulations, which can crucially achieve full OEM approvals, is key for the lubricants sector in the next 10 years,” he said.
“We are already seeing signs of this coming through. However, there is a need for continued investment to accelerate these approvals and ensure more sustainable technology available to the market.”
With sales of the GB Lubricants’ biodegradable products having grown for each of the last six years, the company is proud to support customers, particularly in the plant and off-highway sector where end users work in sensitive areas and near water courses.
“The sophistication of the formulations we are manufacturing to match the increasingly higher levels of performance demanded by our customers is a major trend and it has been rewarding to be successful in achieving this,” concluded Paul.
www.gblubricants.co.uk
Swedish manufacturer Rototilt has won a German Design Award for its recently launched joysticks –RC Joysticks.
The German Design Awards set an international standard when it comes to innovative design and global competitiveness.
The winners are selected by a high quality international jury that works to identify design trends across multiple sectors.
It has now been announced that Rototilt is one of these winners.
In 2022, the Vindeln-based
tiltrotator manufacturer launched a new product concept by the name of Rototilt Control. This included the new product RC Joysticks, for which the company has now received an award – for the third time.
Nowadays, good design is about more than just appearance and function. It involves supplying answers to the market’s demands and needs, as well as taking into account how the product or service affects society. This is how the German Design Awards describe the way
they themselves view and judge design. And it is an approach that Rototilt seems to share, according to Jonsson.
“Our aim is to solve problems in the user’s everyday life in unexpected and innovative ways. An important aspect of this work is to involve them in the design process and identify new methods that cater to the needs of our users and customers,” says Jonsson. “In the case of RC Joysticks, we have worked on several fronts, but one of the most important has been the field tests we have conducted with real machine operators. With their help, we have been able to develop a product that a great many people seem to appreciate.”
The Board of Directors of Kesla Oyj has appointed Pasi Nieminen) as the CEO of Kesla. Nieminen will assume his new position no later than August 2024. Nieminen will join Kesla from Toyota Material Handling Europe, where he has worked in management position of the company’s SAP Transformation Program in Europe. Prior to that, Nieminen served as Managing Director of Toyota Material Handling Finland for over ten years, before which he worked in various positions within the technology industry.
“In line with its strategy, Kesla focuses on profitable growth
in all its three business areas: tractor attachments, truck and industrial cranes, and logging equipment. Growing beyond the company’s current size requires deep expertise in implementing an innovative business and transformation strategy and experience in mechanical engineering business as well as production management. I would like to warmly welcome Pasi Nieminen to Kesla. He has strong international experience from the comprehensive development and successful implementation of different business areas,” says Vesa Tuomi, Chairman of the Board of Directors of Kesla.
“A skilled staff, deep industry expertise, flexible production, competitive products, a strong brand and partner network as well as high customer satisfaction are inherent characteristics of Kesla. I am extremely happy about getting to lead this traditional Finnish company with international operations and to build the next steps of the company’s growth path and success together with the staff. In addition to strong technological know-how and production, I believe that the systematic development of customer understanding, customer relationships and sales is key to success,” states Pasi Nieminen.
Tigercat Industries is pleased to announce that it has built and shipped its 30,000th machine in January 2024, just over 30 years into its existence. From humble beginnings in 1992 when Tigercat had a single product, very little dealer representation, and produced just a handful of machines, the company has grown steadily, expanding both its production capacity and product breadth.
A few quick facts
• Tigercat debuted the 726 feller buncher in April 1992 at a forestry equipment show in Quitman Georgia.
• By 1995, Tigercat had two drive-to-tree feller bunchers, two track feller bunchers, and two bunching shear models with distribution in Canada and the United
• States.
• By 1997, Tigercat had a full product line to offer southern US dealers with the addition of a knuckleboom loader and the industry’s first successful, serial production hydrostatic skidder.
• In 2000, Tigercat was well on its way to becoming the dominant player in steep slope harvesting applications, offering a six-wheel drive skidder and the L830 feller buncher. Both were destined to become flagship products for the company. In addition, Tigercat entered the vegetation management sector with its first mulcher carrier. The range of carriers and attachments that have followed are crucial inputs to wildfire mitigation
• strategies in many regions globally.
• By 2005, Tigercat was present in Chile, Brazil, Uruguay, Australia, New Zealand, South Africa, UK and Sweden among other countries.
• In 2012 Tigercat had grown in 20 years from two to 1,000 employees and introduced the 880 logger, the first in a series of versatile, forest duty swing machines.
Today, Tigercat has the most complete full-tree product lineup in the industry, along with a growing range of CTL harvesters, forwarders and harvesting heads.
Tigercat launched a new brand, TCi in 2022 and put the TCi badge on its first dozer, the
Vimek presents a brandnew harvester model, the Vimek 470. This new harvester is stronger, bigger, and more efficient than ever but still retains all the gentle Vimek characteristics.
The 470 is also built on the same NextGen platform as the Vimek 870 Forwarder and therefore has many common technical features.
Although the 470 and 870 are
920. In the last four years, the company has been developing a line of material processing products with two launches to date – the 6500 chipper and 6900 grinder. 2024 will see a slew of new and exciting products introduced to the market.
Tigercat recently opened a new facility dedicated to the material processing product line and is currently building an additional facility. When complete the company will have over 1.4 million square feet of manufacturing capacity. That’s 130 000 square metres or 32 acres under roof. Over 160 dealer locations in 25 countries represent the Tigercat and TCi brands, along with an extensive factory support network. The company employs over 2,000.
One thing that hasn’t changed over the years is Tigercat’s dedication to the customer base and its relentless pursuit of innovation and improvement. www.tigercat.com
bigger and stronger than their predecessors they are still gentler on the environment. The machines are designed specifically to work with thinning trees and causing minimal damage to the ground and remained trees. The engines are Stage V certified, can run on HVO fuel and have very low diesel consumption and thus low CO2 emissions. The weight of the machine is low and is distributed well on all wheels. The driver sits low for good visibility and the cabin offers a good driver environment. www.vimek.com
October 2021 revealed the world première of a self-driving forest machine which was able to work autonomously – it was able to collect and transport round wood without human intervention. The researchers behind the successful experiment saw it as a key step towards more sustainable forestry.
“This will redraw the map for the industry and how other players in the field view operations like these. We have worked extremely intensively with this test, and it feels exceptionally good that it works,” says Magnus Karlberg, professor at Luleå University of Technology.
In February 2024, the first real trials exploring the feasibility of autonomous forestry operations took place in Hörnefors in Västerbotten. The project was the result of a collaboration between Luleå University of Technology, the Swedish University of Agricultural Sciences, and the Cluster of Forest Technology. By being programmed to conduct the work on its own, the forest machine was able to pick up and transport logs to the intended pick-up point on its own. A job conducted by forwarder operators in machines built for the purpose, but this time people could stand on the sidelines and watch.
The AORO platform has been
under development since 2014 as part of different projects of Luleå University (LTU) These projects included course projects in the mechanical engineering program, as well as masters’ and doctoral thesis. The mechanical design was developed with the intention of utilizing a wide range of readily available off-theshelf components, aiming to reduce manufacturing and construction time. Components not found in the marketplace were manufactured in-house at a local workshop. It is important to note that no external companies had active participation in the engineering development of the AORO platform, making LTU the sole entity responsible for the machine’s construction.
The AORO platform uses the FC8 crane made by CRANAB fitted with a CR250 grapple which has two active degrees-of-freedom for orientation and grabbing. It is important to note
that the grapple system is underactuated, meaning it lacks actuation at the attachment joint indicated as the boom-tip in Figure 2. This under actuation results in the grapple system exhibiting behaviour akin to that of a free pendulum.
This FC8 crane belongs to a new line of products from CRANAB developed to support the introduction of smart crane functions in the industry. The distinctive feature of this crane is to have built-in analogue encoders as joint position sensors. At present, CRANAB and its partner companies don’t offer similar features for the grapple, as it is difficult to add sensors for measuring the rotation and the opening of the grab.
They equipped the electrohydraulic valve with pressure sensors to measure pressure at each cylinder’s chamber. Referring to Figure 3, all sensors connect to the 18-bit DAC
from the main UEISIM unit. The UEISIM is the main processor where all algorithms for motion control are applied. Therefore, the UEISIM unit is charged with providing the control signals to transform desired motion commands into mechanical motion by activating the hydraulic system.
1. Planning the mission
Referring to Figure 4a, at this stage, the human supervisor provides the route for the mission by defining GPS coordinates, which work as waypoints for autonomous navigation. These are set through a user interface that communicates wirelessly with the main Jetson computer. The logs to be loaded lay on the ground around this route in the crane’s reach.
2.Lifting the vehicle height for navigation
The pendulum arms for the wheels are initially on their lowest position. To initialize navigation, they are lifted to a drivability height, to easily traverse the forest over medium size rocks and stumps.
3.Autonomous navigation
Referring to Figure 4b, the machine starts traversing the forest at a constant speed of 2.3 km/h, using GPS information, according to the plan specified initially. As the terrain refers to clear-cut, no obstacles exist on these paths, a part of stumps and rocks that the vehicle can drive over.
Figure 2 Figure 3Referring to Figure 4c, the system constantly scans for logs on the ground during vehicle navigation, using the stereo camera placed in front of the machine.
Once a log or groups of logs have been found, the machine stops at 4 m to get a better visual recognition and positioning of the logs. This information is transferred to the machine’s coordinate system, which is used to provide coordinates to the crane’s motion control unit.
At this stage, the vehicle travels an average distance of 5 m passed the logs and stops at a distance where the logs lay almost next to the load bunk. This facilitates the crane’s tasks, by minimizing the crane’s distance of travel. When logs are found, the system stops at a distance where the crane will be able to reach all logs in a nearby area without the necessity to move the vehicle.
At this stage, the vehicles height is lowered so it has a lower centre of gravity and better stability when the crane is moving and carrying logs.
Referring to Figure 4d, at this stage, the crane’s motion control system plans the necessary trajectories to reach the logs and load them into the load bunk. From this point, the
sequence starts all over again from step 2 and ends when the last waypoint or by manual means.
The machine navigates between an initial and destination by following a trajectory that connects GPS waypoints. In this study a straightforward approach was used based on the direction of the machine’s front end. The algorithm calculates the difference between the bearing of the current waypoint and the heading of the machine’s front end and feeds this information into a P controller that determines the desired rate of steering angle. The controller then sends this information to a hydraulic valve that controls the cylinders that adjust the articulation angle. When the machine approaches a certain distance from the waypoint (based on the machine’s steering radius), it switches to the next.
Tests were conducted to verify the machine’s ability to autonomously navigate by defining waypoints in GPS format. These tests consisted of defining a rectangular path defined by four waypoints and let the machine traverse this route for four consecutive laps. To evaluate the robustness
and converge to the same path from different initial conditions, the machine’s initial position was changed for each new test sequence.
To conduct this research, the team has developed and invested in a testbed infrastructure based on a dedicated autonomous off-road vehicle platform with weight of ten ton and can carry a payload of about three ton. Modular chassis enable different units to be replaced to fit certain research. Four individually pendulum arms are attached to the chassis. These arms can be actively (and individually) controlled or passively through a float control valve connecting positive and negative ports of left- and right-hand side pendulum arm cylinders. Due to the modular design, the drivetrain and the auxiliary equipment can easily be reconfigured.
The platform is equipped with proprioceptive sensors logging all relevant internal properties such as positions, pressures, velocities and accelerations in addition, the platform has been equipped with exteroceptive sensors enabling sensing of the surrounding environment and positioning. The infrastructure also includes a load changer truck carrying a customized
mobile lab in which the platform can be fitted thus enabling flexibility to perform tests in different environments.
To process the data gathered in real time, dedicated GPU: s is used. In addition, a powerful I/O processing unit is used for management of signals and execute algorithms. The software architecture is based on Robot Operating System (ROS), Matlab/Simulink, Python and C.
“With the AORO testbed, autonomous technology will be developed to significantly improve the sustainability of utility vehicle activities in off-road environments,” said Magnus Karlberg, professor in machine design at Luleå University of Technology.
For the second time in succession, our winner is from North Wales. Bedwyr Jones graces this issues front cover with a cracking photo of his County Skidder.
Many of us who worked in forestry in the 1970’s, 1980’s and 1990’s have fond memories of the time when County’s ruled the forest. My first introduction was with the Forestry Commission (FC), I was a young chainsaw operator and we had two FC Falstone County skidders in our squad. These were based on a 754 County and had extra guarding, logging blade and either Igland 4000 or 5000
double drum winches. The FC had a workshop based at Chapelhall which carried out their conversions by their own engineers.
Many other tractors used by contractors at the time as skidders,were Fordson Majors and Ford tractors with the Roadless 4WD conversions. Although some of the others did the work efficiently, County’s were considered the dog’s bollocks of skidders, they were simple, reliable and stable workhorses.
Each morning you filled them up with diesel and off they went,
it was a rare occurrence to see one broken down. Any problems that did occur, were usually either caused by abuse or neglect.
County’s were first manufactured in 1948 and were tracked machines. These were used in forestry for ploughing as there was a big establishment drive to replenish timber reserves, which had been depleted after the war.
The first equal 4WD county was manufactured in 1961 and was based on a Fordson Supermajor. It was named the Super Four and was a simple
4WD conversion with the front wheels driven by twin shafts from the rear hubs, which allowed a standard differential to work on all four wheels. 1962 brought the introduction of the 95hp Super Six County which was a popular model until production ceased in 1965.
The second generation of County’s commenced in November 1964, the four cylinder 654 which was succeeded by the 754 in 1968.
In May 1965, the six cylinder 954, was introduced until it was also replaced by the 100hp 1004 Super Six, the tractor Bedwyr owns today. Many other models sizes were manufactured over the years including the flagship models, the 1124 and 1174.
County ran into financial trouble in 1980 and were sold to the Benson Group in Knighton, Powys for £3.2 million. They continued to manufacture County’s up until 1990. The group made around 150 tractors. Manufacturing the County’s went well but the
Benson Group struggled to obtain suitable safety cabins which would conform to UK and EU regulations. This proved to be a step too far with 56 County tractors incomplete. The company were reduced to selling spare parts and converting Ford Transits into four-wheel drive vehicles before selling the County name to South Essex Motors (SEM).
SEM and its engineering director Eric May changed the County twin driveshaft four-wheel drive system for use on Ford New Holland series 40 tractors. The idea was to move the dual prop shafts closer to or even beneath the centreline of the tractor which would increase the steering angles. Eight skid units were bought from Ford New Holland to complete an order for eight equal wheel drive tractors due for delivery the following February. With Ford New Holland used as the tractor base, SEM could use the UK/EU approved Q Cab. Before completion, the receivers were called in at SEM, plunging the job into jeopardy. Luckily, it was
saved by the Benson Group, who stepped in and completed the order in May 1995. By then the order had increased to ten tractors, seven 754-40’s without cabs which were destined for Canada, two 1184-40’s with cabs to the Falkland Islands and finally one 1164-40 without a cab to St Helena.
The 1164-40 was the last ever County tractor built. It was commissioned at the request of the British Overseas Territory Island of St Helena for its Environment and Natural Resources Directorate (ENRD) which needed the tractor for forestry use.
It’s touching to see younger people taking this iconic brand to their hearts and helping to preserve these magnificent tractors so that they will be around for many years to come. Bedwyr Jones fits right into this category, he is just 26 years old and lives with his girlfriend Katie and young daughter Cali on the outskirts of Bala in North Wales.
Forestry is very much a family tradition in the Jones family, Bedwyr’s father, his uncles and his grandfather have all worked in forestry, so he caught the spruce bug at a very young age. As a young lad, he couldn’t wait for weekends and school holidays when he would head out to the forest with his dad. He started out chokering the trees ready for skidding and progressed to operating the skidder, then he was shown how to use the chainsaw. Bedwyr was a natural and it wasn’t long before he was able to fell edge trees and work safely in windblown timber.
On leaving school, Bedwyr worked as an apprentice mobile mechanic, which involved repairing and servicing machinery out on site. He enjoyed learning how the equipment worked, but the pull of the forest was too strong and aged 18 he secured a job in establishment. His work involved the re-spacing and spot spraying of young seedlings, but it wasn’t long before he was felling trees and back on a chainsaw.
After a couple of years of felling, an opportunity arose to operate a forwarder which he grabbed with both hands. Bedwyr thoroughly enjoyed the experience of operating forestry equipment, and he was offered a position operating an excavator on ground preparation for planting. He worked on ground prep for five years, two years on the excavator and a further three years operating a Menzi Muck on very steep preparation sites. He decided to return to the
harvesting side of forestry but wanted to be a bit more hands on with manual forestry like he had done previously with his dad. He found a County 1004 Super Six which was for sale in Machynlleth complete with an Igland 4000 double drum winch, a James Jones logging blade and front guard which he is now the proud owner of.
Bedwyr grew up listening to his dad fondly reminiscing of his time operating County’s and all the areas in which he had worked in, and he hopes one day he will have created his own County stories to pass on.
The County is a work in progress and has a few minor issues which are being carried out while it is still working. The winch has been replaced with a stronger Igland 5,000, this one has the remote control which saves a lot of walking. Once all the minor leaks and squeaks have been sorted, it will have a full respray so that it is as neat and tidy as the day it left the
workshop. Bedwyr’s main work at the moment is in Clocaenog Forest, where he is working for Andrew Holmes creating habitat areas for the RWE windfarm. Bedwyr finds it very interesting as it involves working with chainsaws, excavators, flails, fencing and many other bits and pieces in between lol.
“The winch work that I do with the County isn’t full time, the winning photo was taken on a job I was carrying out for Gethin Jones in North Wales,” said Bedwyr. “It was on a local estate, and we were clearing windblown timber and winching in the edge trees, the remotecontrolled winches come into their own on these types of jobs.
I love County tractors and I hope to be able add more to my working collection. Hopefully, my daughter Cali will take an interest in forestry, its looking promising as she is in love with the County and loves nothing better than going to work with her dad.”
Many forestry harvesting sites demand the use of bandtracks so that sites can be worked safely. Improved bandtrack technology allows us to work safely and securely on steeper, and wetter sites, than ever before. They also enable the large forestry equipment to distribute weight over a larger surface area, reducing soil compaction.
Although manufacturers have many different track profile options designed for specific ground conditions, they also make a good “all rounder”. This is a bandtrack aimed at the smaller contractor, owner/ operator and estate forest where it wouldn’t be financially viable to run with sets for a specific purpose.
On a forwarder, I found that around 6,000 hours is roughly the expected life of a set of bandtracks, and I worked a selection of both wet and steep sites. I worked for a large harvesting company, and we found that swapping the bandtracks off a new harvester, for half worn ones on a forwarder, reduced the cost of replacing bandtracks. A harvester only travels a fraction of the distance of a forwarder and is never carrying a load.
Keeping tracks tensioned properly is crucial, so that wear is kept to a minimum, and maximum traction is obtained. There is no excuse for running tracks too loose or too tight.
We have included a brief introduction of three of the main bandtrack manufacturers, a summary of the profiles available.
Clark Tracks Ltd are based in Dumfries, Southwest Scotland, and have been manufacturing a wide range of superior forestry tracks since 1988.
The company was acquired in 2007 by Gunnebo Industries AB and moved to a new location in Dumfries. The capacity of the company increased vastly, more than doubling within a year. Beginning with a single factory, they quickly outgrew the space and expanded track operations into the two neighbouring factory spaces in 2012 and 2019. With this larger space came innovation, development and automation creating the manufacturing facility and
trusted brand of products we know today.
Over the years the company has been acquired by various investment businesses that have supported growth and development. The current owner is the Swedish Investment Company AB Max Sievert. This expansion further solidified the company’s position as a trusted provider of forestry tracks. Clark Tracks has led the way by developing track models in extreme climbing, high flotation and multi-terrain categories all done with close relationships with tyre and machine manufacturers to ensure top quality products.
Clark Tracks continues to uphold its legacy of innovation and quality and looks towards a future of pushing track technology and driving advancements to ensure the
highest quality products are available for the worldwide forestry market.
Jason McCallie has been a welder at Clark Tracks for ten years, he said “We have made big changes in the tracks we make now. There are more choices for customers for extreme climbing tracks and now the heavy-duty option for Grouzer and CX is available which are very popular. Flotation tracks have also gotten much wider too to support the larger machines on the wet ground.”
The Dumfries based company offers 15 different track profiles and have tracks specifically designed for use in temperate, ice and snowy climates with multi terrain, demanding and flotation profiles.
Garry Henderson, director at Clark Tracks, has been with the company for twenty nine years, “When I first started with the business the tracks used in forestry at that time are completely different than what is used today. Machines are bigger, heavier and have more horsepower, so part of our product development has been to produce tracks which are stronger and more durable and designed for the demanding ground conditions that forestry contractors are working in today. We see harvesting operations in extreme climbing conditions and in incredibly soft conditions, so our products have to be of such a high quality to meet this challenge.”
The Terra 85 is the preferred
option for machines up to 15 tonne and the Terra 95, for machines over 15 tonne and are the company’s most popular profiles of bandtracks.
Rebecca Kerr, Order Fulfilment Manager said “Our factory is worlds away from when I first started. Over the years we have had an expansion of products and advancements in the durability of the tracks we produce. Multi-terrain tracks have always been a customer favourite but with the forestry machines getting bigger, terrain specific tracks have become very popular. The demand for climbing tracks like the FXS and CX has grown.
“These tracks have advantages for those working on steep ground as they give better gripping properties. When we launched ATF, it was a huge success for the flotation market and since the inclusion of 930mm and 1 metre TXL tracks in our standard range customers have been pleased with the
performance of our offering for wet and soft terrain conditions as well.”
Graham Mitchell, a machine operator for twenty four years concludes with, “In the time I’ve been with Clark Tracks there have been multiple changes to different products with flotation tracks becoming much wider for accessing forests in softer ground condition and they are more popular than when I first started because of these benefits, especially for the larger machines. The factory where we make the tracks has also improved.
“The introduction of automation has sped up production but also created better health and safety.”
T: +44 (0)1387 722370
F: +44 (0)1387 720978
E: clarktracks@clarktracks.com
www.clarktracks.com
Technical & Production
Garry Henderson
The Pewag group is one of the oldest chain manufacturers in the world and its history can be traced back to the 15th century. Their long history of innovation ensures that all products manufactured by the Pewag group are the ultimate in their respective markets, both now and in the future.
Pewag’s main areas of business are snow chains, forestry chains, hoist and conveyor chains, do-it-yourself products, engineering, lifting and lashing chains and accessories and tyre protection chains. Their modern chain manufacturing facilities in Europe allow them to offer a variety of high quality products.
The profile of the Duro track, expected to be Pewag’s biggest seller, has been revised to provide better track to tyre grip, especially on wets, muddy slopes (ie typical UK conditions). The new profile has a more aggressive tyre grouser.
The stubs have been revised with three options, although in the future only the Starwave stub and Starwave XL stub will be sold in the main. The starwave stub has the additional benefit of slightly rounded edges, making it less likely to bring up brash and stick from the forest floor and damage the cab or bodywork of the machine.
The new stub is forged and
approximate dimensions are 87 – 93mm wide and 45 – 47mm high (forging tolerances).
A new side support works better with TRS2 tyres.
The core strengths remain though…
Heat treated and case hardened C-Links and Forged Links. Customers report they are tensioning once compared to 2 or 3 times with some other brands and they are not having to remove track pads as frequently. The tracks require less maintenance and adjustment. This procedure was introduced nearly 3 years ago and was developed side-by-side with the tyre chain operation.
The bars are preheated prior to welding the stubs on, and post welding, the bars are tempered, reducing the chances of breakages near the stubs.
This change in procedure was introduced 5 years ago and remains key to the Pewag Bluetracks durability.
The tensioners seems well received and although the tensioner isn’t included by default, it’s a paid option with Pewag.
Coming up and in development is a new all round, all terrain track. It is a further development of the soft ground track range and features addition friction bars and a new profile. The current FLOW track has good weight distribution and is very gentle to the forest floor, tree roots and forest tracks.
Sometimes additional traction is required, in Europe you have slopes and you also have flat marshy conditions but in the UK (Scotland and Wales in particular), they also have flat, wet boggy terrain and steep slopes, but unlike anywhere else, there are bogs on the slopes!
Olofsfors AB is one of Swedens oldest companies, founded in 1762 it has a long history of innovation with products made from steel. The focused products from the company in modern times are Tracks for forestry machinery, wear steel for the mining industry and plow steel for graders and snowplows.
Olofsfors is the market leader in the forestry track business. And are supplying the highest quality product with an extra big focus on customer support and user experience. This together with a focus on innovation and sustainability, gives Olofsfors a competitive edge.
Olofsfors have a wide range of products with around 2000 different versions of tracks. With 22-30 mm link system, and different version of cleatings
The main focus is on Olofsfors 8 different base models. From the EX track, which gives the
absolutely best grip on the market. To the extra wide CoverX 180 tracks, which gives the user extreme flotation for the softest of conditions.
Since Olofsfors is a global company, selling tracks all around the world. The popular models differ from area to area.
But our biggest selling track is our EVO track together with the MAX link system, That is a strong crossmember and together with the shorter MAX link system provides an perfect all round track for heavy machines.
Another popular product is our new CoverB Track.
It’s a new innovative crossmember that keeps the extra flotation from the traditional flotation tracks but gives much better grip. Both towards tire and ground.
This together with its unique design to provide excellent side grip. Makes it the ultimate flotation track.
Phone:
+46 (0) 930 396 00
Customer service:
+46 (0)930 311 40 info@olofsfors.se olofsfors.com
Komatsu 931XC with Olofsfors #EVO Tracks. A good choice for for hilly conditions.15 - 20 t 61 cm
TECHNICAL FEATURES:
• Powerful gripper
• Automatic chain tensioner
• Optional: Power-Tiltator
APPLICATION AREAS:
• Safe removal of trees in several parts.
• Maintenance work along traffic roads and routes.
• Felling of dangerous trees.
• Quick processing of fallen trees.
In a cold and snowy Knullwald, a twohour drive west of Frankfurt airport, Westtech Woodcracker held a demo day, to showcase their latest innovations.
It promised to be an interesting event as you could see the latest Woodcrackers working in a real environment.
Werner Steininger, the CEO and owner of Westtech Woodcracker, and his team never fail to put on a good display and this occasion certainly didn’t disappoint.
There was a good gathering of people from all over Germany and Austria who were interested in seeing the new innovations.
The CS 810 is a versatile, powerful grapple saw designed for use in both forestry and tree management. It has a cutting diameter of up to 800mm with an actively suspended saw unit. The grapple saw is manufactured out of Hardox®
steel and is rigidly mounted to the excavator so that if required it can manoeuvre trees and heavy branches vertically away from buildings or any other hazards.
The CS 810 section felled a mature beech tree and removed each heavy vertical limbs with ease. It placed them gently on the ground out of the way. Once all the limbs were removed it dismantled the main stem into sawlog lengths, ready for transporting to the mill.
The CS 545 is ideal for use on machines of the 8-tonne weight class and above. The grab opens to 1270mm, and the saw can cut up to 540mm diameter limbs in a single cut. The CS545 has an endless tiltrotator, actively sprung saw bar, and the chain is lubricated with grease. For efficient operation it requires a hydraulic delivery of 50-100 litres per minute with between 200 and 280 bar operating pressure.
Again this grapple saw was dismantling a beach tree but a bit smaller than the previous one. Coupled to the JCB it was highly manoeuvrable and stable during felling.
This is the first time I have had the opportunity to see the Fellertruck and grapple saw and have always thought that it was a useful combination for roadside tree clearance.
This Fellertruck has a multi telescopic crane which can reach upwards to almost 21m, an outreach of 18m and a downward reach of 11m. It has two sets of wide stabilising legs so the grapple saw can be used to its full potential. Other crane options are available.
The crane and grapple were being operated via remote control. This allows the operator to position himself for a clear view of the work area.
The CS 750 Smart has been specifically designed for use
on the Fellertruck and other telescopic handlers. It can cut stem and branch diameters up to 750mm and the jaws open out to 1280mm. It weighs 900kg with an actively suspended saw unit, and the chainsaw chain is lubricated with grease.
This is an excellent choice for safely removing dangerous and diseased trees which are near roads or railway lines as the high reach allows it to cut limbs and stems into easily manageable sizes and dismantle the tree in record time. The grapple saw can cut and lift sections from above and below any hazards and is a great option for dealing with diseased trees which are dying or brittle like Ash Dieback.
There was also a demo showing the effectiveness of the CS 750 Smart when fitted onto an Ebert RTH 6.30 telehandler.
COUPLED TO A 258HP
This is a monster of a shear which can cut stems up to 70cm
in diameter. The gripping force on the three-finger grapple has been significantly increased so that big stems and full trees are held firmly and securely.
Everything about this shear is strong, bolt bearings have been used to increase robustness. The felling grapple is also made of durable and wear-resistant Hardox® steel, and the body is cathodic dip-painted (KTL primed), as is customary in the automotive industry. The advantage of this type of primer is good corrosion protection and an even coating in all cavities. A powder coating is baked onto the primer, making it ideal for outdoor use. The cutting unit consists of a high strength blade which is easy to sharpen. Thanks to the patented blade attachment, the blade can easily be replaced if required.
This shear is designed for use on carriers between 28 and 40 tonnes. The hydraulic hoses are well routed and out of harms way and the shear can be fitted with an optional tilt rotator.
The C650 was felling large mature beach trees, and they were being removed in their entirety or in two half sections if they were heavily branched. Watching this large excavator tracking along the forest road with a mature beach tree held vertical in its grasp was a quite a sight to behold. I watched the Liebherr remove five large beach trees before heading back to Westtech’s main demo area for a bratwurst sausage in a roll and a hot cuppa.
After saying our goodbyes to Werner, we set off back to Frankfurt for a few glasses of refreshing German bier before our flight home the following morning.
www.westtech.at
For videos see www.youtube. com/user/eschimax
Wildfire is proving to be one of the greatest challenges facing foresters, landowners, governments and environmental organizations in the 21st century. The summer fire season over the last several years in North America has devastated millions of hectares of forest land, destroying wildlife habitat and carbon sinks, while releasing massive amounts of carbon and particulate matter into the atmosphere. Excessive fuel build-up on the ground is having a devastating effect.
Tigercat recently released a mulching head designed to mount on a Tigercat LX830E carrier. This machine can tackle steep slopes and operate within dense stands to reduce build-up of woody debris as a mitigation measure to guard against future wildfires.
The new 4161-15 head has a 1,5 m (59 in) mulching swath, 130
degree wrist pivot, and a pinon rake for added utility. Like all Tigercat mulching heads, it is strength-to-weight optimized and fitted with large bearings.
Many of the components including the bearings, sprockets, seals and timing belt are common to the Tigercat 4061 series mulching heads and thus field proven. Hydraulic
hoses are routed through the open tip boom into the top of the wrist, providing excellent protection. The replaceable wear liner is field serviceable. Removable covers allow easy access to all service points.
The LX830E carrier is powerful, compact and extremely capable on steep terrain.
www.tigercat.com
Nisula Forest Oy and Forest System Co., Ltd. have signed a dealership agreement. Under the terms of the agreement Forest System Co., Ltd. will sell Nisula Forest products, parts and offer
services in Southern Japan, together with the support of our main distributor Forest Limited Company.
“At Nisula we are very excited about our new cooperation with Forest System Co., Ltd.! Mr.
www.forestmachinemagazine.com
Fujihara and his team have a lot of experience and long history in the sales and after-sales service of forestry machinery, says Timo Savornin, Sales and Marketing Director at Nisula Forest Oy.
www.nisulaforest.com
hen I was offered the opportunity to visit Western Bio-Energy’s plant in Margam, Port Talbot, to see some of their forestry operations, I realised that for me timber harvesting in South Wales was a bit of an enigma.
I knew that South Wales was once a hub of industry with steel production and coal mining at its core. These industries have gone now, with the exception of Port Talbot Steelworks, which is still the UK’s largest steel producer and one of the biggest in Europe.
The Welsh Valleys industrial past has been replaced with urban regeneration, tourism multinational investment. Large works and factories lie empty or have been turned into retail units and bear witness to the lack of success in replacing some of the older industries.
Western Bio-Energy have taken possession of two sites in Port Talbot. One is the stockyard where some of the roundwood is brought in from local forests and stacked ready for chipping. The other is a six-acre site where the biomass power plant stands. Both sites are proximate to the local industrial area and M4 motorway which is ideal for access, wood deliveries and grid connections. Western Power, an electricity distribution network
operator for South Wales, provides the grid connection.
The construction of the thirtythree-million-pound biomass plant was a “first of its kind” commercial scale plant in Wales. It is owned by Western BioEnergy LTD, which is an asset under the green investment fund, Greensphere LLP. Building began in October 2006. The plant first produced power in July 2008 and was fully operational by October 2008.
Our visit began at the stockyard where we met Harvesting Manager Tim Williams and his team. Tim invited us into the office for a coffee and after spending two minutes with him I wished I had learned how to do shorthand! Tim has a brain that works at the speed of light and my pen got so hot trying to keep up with him it was on the verge of burning my fingers. ☺
Tim was a contractor himself prior to taking on this management role, so it was almost a case of poacher turned gamekeeper. All too often the people in management roles have no idea of what the job entails as they have never properly experienced it for themselves. Contractors and hauliers find it much easier to work along with people like Tim as they tend to help rather than hinder.
Roundwood is brought into the stockyard, chipped and fed straight into one of their walking floor trailers prior to being delivered to the power plant. Western Bio-Energy own a lot of their own equipment, and this includes a walking floor lorry, a wagon and drag, timber trailer Tigercat harvester and a Logset 6F forwarder
Kelvin Jones, Tim’s second in command, also looks after the family-owned harvesting business who work directly to Western Bio-Energy. A highlead/ skyline tackles the steep and tricky areas along with a Doosan DX235 Excavator with a Logset TH 75 head, a John Deere 1270 harvester, a John Deere 1210 forwarder and a Logset 5F and 6F forwarder. They also own a selection of timber lorries and excavators, the Albach chipper and two road sweeping lorries. Tim still has an interest in the family business, and they harvest around 30,000 tonne per year. Two further contractors, Keith Morgan and Baden Powell, work on direct contracts and standing sales.
Tim explained the company’s somewhat radical and unique working relationship with their contractors. As Western Bio-Energy oversee the whole process, from buying standing timber to producing electricity, they have eliminated the
middlemen taking a cut. This increases the value of the woodchips and allows them to look after their contractors. Contractors are offered a price for the job and don’t have to compete against each other in a cutthroat manner. The generous rates and the regularity of payments keep the contractors happy and productive. This is a breath of fresh air approach to timber harvesting. All too often contractors are at the mercy of greedy merchants who like nothing better than to pit contractors against each other so that they get the work done at bargain basement prices. Western Bio-Energy’s system allows contractors to be able to complete the work methodically and safely without having to cut corners. It gives them financial security and confidence, so they are able to invest in their business.
Tim then gave us a tour of the stockyard where the Albach chipper was in the process of filling a walking floor trailer. The Diamant is an impressive chipper and produces chips from 15mm to 60mm. It has a MAN 790hp motor at its heart and roundwood is fed via the Epsilon Palfinger 10.1m reach crane. It can produce up to 100 tonne of woodchips per hour, so filling a trailer takes a relatively short time.
There is a constant flow of roundwood coming into the yard and chip wood leaving. Stocks of roundwood timber are kept at a consistent level so if bad weather arrives or transport problems occur, they can maintain a continuous supply of wood chip to the power plant.
Next on the agenda was a tour of the imposing power plant which is only a few minutes’ drive from the stockyard. Steven Pemberton the Operations and Maintenance Manager was there to greet us and start our tour. I suddenly realised that I had no idea of the principle behind bioenergy. I understood wood went in one side and electricity came out the other but the bit that happened in the middle was a complete mystery to me, so I was looking forward to discovering how electricity was actually produced from woodchips.
Steven explained that the plant consists of the chipping and storage yard, vehicle manoeuvring areas and the
power generation unit. We started with a tour of the outside where the chips are stored.
The three different categories of woodchips are kept in separate dry storage bays - round timber that has been chipped, whole tree with lop and top woodchips and recycled timber. Each type of woodchip has different burning properties, so Steven has to assess the optimum blend of woodchips for the furnace each day to keep the plant working to its maximum efficiency.
The power generation unit comprises of a single drum boiler integrated with a firing system which ensures the complete burnout of the woodchips to minimise the formation of Nitrous Oxide. The dust and other particles present in the combustion gases are removed by a bag filter. Woodchips are fed as fuel into the boiler to produce heat at a rate of 20 tonne per hour. The
Albach Diamant Chipper filling a walking floor trailer.combustion chamber then heats up water to 512°C to convert it to a superheated steam.
The high-pressure steam is passed to the turbine chamber where it drives the two shaft steam turbines which generate electricity. The steam emanating from the turbines flows through an air-cooled condenser which then converts it back to water and then feeds it back to the boiler through the condensate unit.
The company require 160,000 tonne of wood each year to keep the plant operational, much of which is purchased from national Resources Wales.
Western Bio-Energy has had a positive effect on the South Wales economy as around 35 lorries each day, from 15 haulage companies, deliver the wood. The plant employs a staff of 25 and supports a further 130 local engineering and forestry jobs.
The figures are very impressive. The biomass plant producing 14Mwe of electricity each year, that’s enough energy to power 31,000 homes while saving a massive 47,000 tonnes of carbon dioxide emissions.
This was my first ever visit to a bioenergy plant and it was incredible to see how the whole system works, Steven was a fantastic guide with an incredible knowledge that made it a mesmerising visit.
I thought my day was over, but Tim had yet another visit planned so off we set to see one
of the harvesting contracting teams employed by Western Bioenergy.
Heading into the forest I was pleased I was in a 4X4 as the condition of roads were pretty shocking. This is one of my bugbears that there is a distinctive lack of attention to the upkeep of forest roads. We were lucky working in the Cowal and Trossachs district as they looked after the roads but since starting the magazine, some of the sites we have visited have forest roads that have deteriorated into shocking conditions.
This is unfair as surely the roads should be fit for purpose, our vehicles suffer excessive wear and tear, timber lorries end up with punctures and damage and how do we expect emergency service vehicles to access sites when roads are almost nonexistent. Landowners blame harvesting equipment, but they rarely travel on the road and forwarders unload timber from the woodside whenever possible. Rant over!
The forest we visited was being harvested with the Doosan and Logset TH75 harvesting head and the timber extracted by the John Deere 1210 forwarder. It was a lovely stand of Sitka Spruce and as I approached from a distance, I thought it such a waste that good log material was being cut into biofuel. As I got closer, I could see why, some scroats had obviously thought it would be a good laugh to start a forest fire, so the harvesting crew were
clearfelling the large area of fire damaged trees. On closer inspection I could see the trees had been too badly burnt to be of any other use.
The areas that had been harvested were immaculate. Giving the contractors a good rate allows them to be able to produce top quality work and this was a perfect example. Stumps were nice and low, brash mats were perfect with any broken tops and deadwood laying around pulled into the mat, there wasn’t a stray length laying anywhere on site and the main forwarder extraction routes were well thatched with no ruts or any muddy slurry.
An advantage of cutting biofuel is that the tree is run down to a couple of cm top diameter, almost every bit of wood is used leaving almost a pure brash mat. Cutting at 5m lengths offers quick harvester production too and is an easily handled size for the forwarder, haulier and Albach chipper. It goes to show that there is never really a bad job, just a bad rate. It’s great to see the job being done properly by professional operators who don’t have to work silly hours to make a living.
Tim is great company to be with, the energy and enthusiasm he has for his work is incredible and his man management skills are exceptional. This sense of fair play is something I thought I would never see in forestry, there must be a shortage of long sticks in South Wales as that carrot dangling on the end of it, is well within all Western BioEnergy’s contractors grasp.
Steven Pemberton the O & M Manager explaining how electricity is produced while John Fukes and Tim Williams in the background enjoy a good Chip Chat.
John Deere 1210 forwarder heading to the landing.
DoosanDX235 with a Logset TH75 harvesting head.
Looking down onto the high lead harvesting site
Tim Williams and Steven Pemberton outside the offices at the the power plant.
The Energy Plant’s control centre
Woodchips on their way to the boiler.
Inspection windows for the boiler.
Volvo Trucks is introducing a new engine for its iconic FH16. Delivering up to 780 hp and 3,800 Nm, the new 17-litre engine – also certified to run on biofuels – can handle the toughest transport assignments with ease while delivering outstanding fuel efficiency and durability.
Driving continuously at high speeds with heavy loads can be a challenge – but not with Volvo’s 17-litre Euro 6 engine powering its FH16 truck. The new engine comes with three power levels – 600 hp, 700 hp and 780 hp – while torque levels have been increased to 3,000 Nm, 3,400 Nm and 3,800 Nm respectively, translating into faster engine response, better driveability, maximised productivity and improved fuel efficiency.
Marcos Weingaertner, Product Manager at Volvo Trucks, says: “I’m proud to present our new engine – it really is a masterpiece and the result of world-class engineering. The 780 hp version is the strongest engine in the industry.
“When climbing steep grades on a road with maximum loads, you don’t want to get stuck with too little torque and power. That is why we have focused all our efforts on making the D17 engine very powerful, reliable and responsive. For our
customers, this translates into getting the job done faster with improved fuel efficiency.”
The D17 engine is equipped with a single efficient turbocharger that boosts engine responsiveness and improves the driving experience. Volvo’s innovative patented wave piston design optimises combustion and reduces emissions, while the new injection system ensures the best fuel economy, while increased peak cylinder pressure enables high power output.
The engine brake power across the entire speed range has been greatly improved with outstanding engine response. This enables fast gearshifts, resulting in less wear and tear on the brake pads and disc, while also being more efficient when travelling downhill.
The new D17 engine is certified to run on HVO (Hydrotreated Vegetable Oil) in all power ratings. The 700 hp version is also certified to run on 100
per cent biodiesel (B100). The gearbox has been updated to handle up to 3,800 Nm, and internal gearbox efficiency has been further improved on the 3,000 Nm and 3,400 Nm versions.
“I’m confident that customers and drivers will appreciate the higher engine brake power as well as the ability to run on HVO and biodiesel,” adds Weingaertner. “The D17 is a fabulous engine for a fabulous truck, and all our customers who rely on the Volvo FH16 in their daily work will now have an even more powerful tool to help them.”
Sales for the Volvo FH16 with the new engine start in mid2024, with production due to start in the second half of 2024 for European markets and Australia.
The new engine is available in the all-new Volvo FH16 Aero and the latest version of the Volvo FH16.
www.volvotrucks.com
As I reflect on the past few weeks since introducing my new training and lifestyle package for busy forestry workers, I received a WhatsApp message from one of my clients, Jamie, who has been part of the program for three weeks now.
Jamie had insisted on avoiding the traditional route of using bathroom scales, a decision I respected. I never impose such measures on individuals as they can become either addictive during successful periods or problematic during challenges. So, I let him make that call.
The message reads:
“I did weigh, Lost a good stone, and I’m not being very ‘rigid,’ as you know
Dunc.
Duncan Gillies shares four simple strategies to add to your daily routine to increase health and mental well-being.
Trying to make sure the daily habits are paramount, Thank you very much, Mr. Gillies.”
Considering Jamie hasn’t lifted a single weight, hasn’t engaged in any form of resistance training, and certainly hasn’t been hitting the pavements for hours on end, this came as a pleasant surprise. But it’s not uncommon.
In fact, another client, Colin, who also joined the program three weeks ago, has lost just under a stone. When I asked him how he was feeling, his reply was:
“Yeah, I’m in shock, knew I had maybe dropped a bit but nothing like that. I feel good, a hell of a lot more energetic,
sleep is getting better as well.”
Just like the rest of the small group of clients within the ForestryFit community, these individuals are reporting shifts in mood, increased energy levels, better digestion, improved sleep quality, being more productive at work, and even a raised libido!
So, these new lifestyle changes are also having a positive impact on their significant others too!
A couple of the lads have mentioned that their kids are getting involved with their workouts now, and that is what it’s all about at the end of the day - setting a good example for their children who will hopefully adopt some of these healthy
lifestyle choices going forward into adulthood.
Since the launch of the 8-week lock-in challenge over Christmas and New Year, I successfully enrolled the ten new clients I was aiming for. I am delighted that they put their trust in me as their coach because the rewards are extremely satisfying.
To further show my commitment to the ForestryFit community, I have purposely downsized my harvesting business from a harvester and forwarder to just a harvester. Now I’m only needed on-site when my brother is finished with the harvester at the winch landing, and it is free of its processing duties, and there is some harvesting to do again.
This is something that we’ve been toying with for a long time now and makes perfect sense for all involved - the flexibility is ideal for the growth of ForestryFit and my studies, but also for my brother as it’s fewer machines and headaches to worry about for his business. WIN WIN!!
Now that the dust has almost settled, and I’ve found my feet with this new online side of the coaching business, I have decided to steadily grow our small community of like-minded
“wood tinks” by offering an ongoing enrolment opportunity into the program for anybody else who also wants to see results like the guys above.
You too can achieve incredible results whether you decide to get in touch or not, just by implementing some simple strategies into your daily routine like the ones below:
1. Aim for 10k steps per day.
2. Drink 2-3 litres of water per day.
3. Get 7-8 hours of sleep per night.
4. Eat the correct amount of protein for your body weight per day.
However, if you decide that you’d like to become part of this growing community where we all help each other out by sharing stories, wins, tips, hacks, and questionable banter among other things, then it might just be the ticket you’ve been looking for. As your coach, I take pride in keeping you accountable and guiding you towards the best version of yourself. It’s not just about the community; it’s about the individualised attention and education you receive to make lasting changes.
I look forward to helping you achieve greatness
To find out more, you can connect with me on:
RATED THE WORLDS NO1 FORESTRY MAGAZINE BY FEEDSPOT FOR 2023 & 2024.
GLOBAL SOCIAL MEDIA PRESENCE WITH OVER 800,000 FOLLOWERS
Forest Machine Magazine is up for sale and includes the printed magazine, digital magazine, all social media channels, website, contacts and photo gallery.
This year I will be reaching official retirement age and a lifetime in forestry has left my joints not quite as supple as they once were. So after seven great years of writing and publishing Forest Machine Magazine, it is finally time to hand over the reins. Rab
FOR MORE INFORMATION CALL OR EMAIL RAB
FORESTMACHINEMAGAZINE@MAIL.COM
+44 (0) 7582 055 748
Printed and digital magazine.
Facebook, Instagram, Twitter, Youtube, Linkedin, TikTok and Threads
Website, contacts and photo library.
Jim Wilmer & Sons require a Field Service Technician to carry out servicing and repairs to a wide range of forestry machinery. Knowledge and fault-finding experience of hydraulics, modern electrics and computer systems are essential but in house and manufacturer training on forestry machines will be provided.
Jim Wilmer & Sons are the UK Distributors for Rottne and Ecoforst T-Winch machinery. Repairs would be carried out on our own fleet of machinery as well as customers machinery based throughout south west Scotland and argyll areas the occasional night away might be required. A background in forestry machinery, construction or agriculture would be preferred.
You will be joining an ambitious, growing, family run business. C ontact Callum McKenzie on 07826 753303 to discuss.
Mounding operator looking for work around the Central Belt, Dumfries and Galloway, long term if possible. Give a call on +353 892704932.
Taiga Upland is recruiting to our team of skilled excavator operators!
We are specifically looking for operators with experience in restock mounding and associated operations such as drainage, brash raking and ATV path work. Our company is committed to providing year-round, sustainable, full-time employment, so please note that these are permanent positions, not seasonal roles. Selfemployed operators will not be considered for these positions. You will be required to work as part of a team working on forestry projects from our base in Pitlochry, Highland Perthshire and throughout East and Central Scotland. Due to the demanding nature of the work, a strong agricultural / forestry / plant operation background is essential as well as a full driving license, FMOC and EFAW+F certification.
You will be joining a successful and hardworking team with an established quality-based reputation; therefore, a strong work ethic and positive attitude are essential.
To reflect your commitment, loyalty and hard work within the company, the right candidates will be rewarded with top level rates of pay, benefits including BUPA Healthcare and a company vehicle.
rab@taiga-upland.co.uk 07808 739 027
For sale. 2013 Tigercat H855C, brand new engine, 2018 Ponsse H8 head, 12 metre boom, 14k hours. £105k. Scotland. Phone 07920 116297FIND THE TOP 15 COUNTRIES BY FOREST
CAN YOU FILL IN THE MISSING VOWELS FROM THE NAMES BELOW TO FIND THE UK’S TOP TEN LARGEST FORESTS?
AT 297 SQUARE MILES.
SUDOKU Maze
3 1 FILL IN THE GRID SO THAT EACH COLUMN, ROW AND BOX CONTAINS EACH OF THE NUMBERS FROM 1-4
1 3
4 3 1
DRIVER ANGLE TRACKS IMPACT GRINDER ALLEN CHAINS GREASE
DRAW A LINE TO MATCH TWO WORDS TO CREATE A NEW WORD
• Pulling force: from 45kN to 90kN
• 3-plate clutch
• AUTOSTOP
• TERRA Remote control
• Uniforest Connect
• Pulling force: from 65kN to 120kN
• From 4- to 8-plate clutch TERRA Remote control
• Uniforest Connect
• Pulling force: from 35kN to 85kN
• Up to 3-plate clutch
• Plenty of storage space
• With or without gear reducer