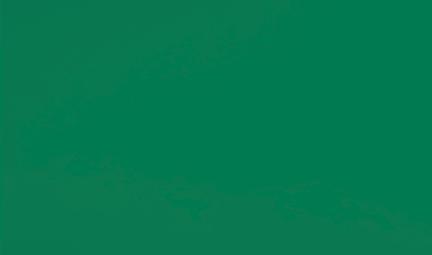
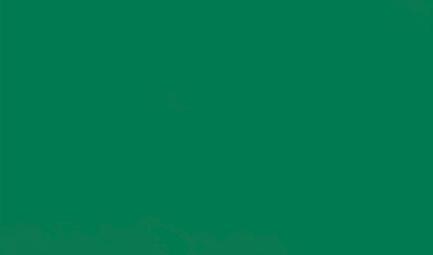
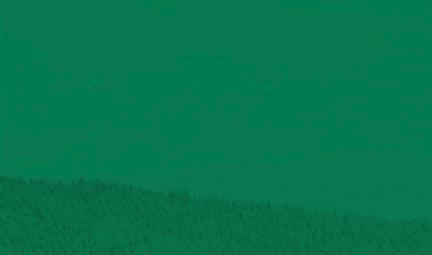

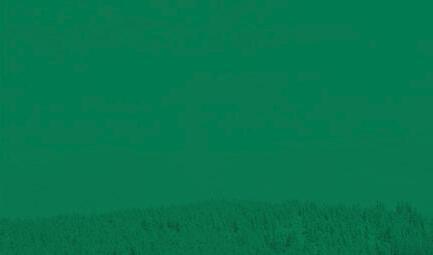
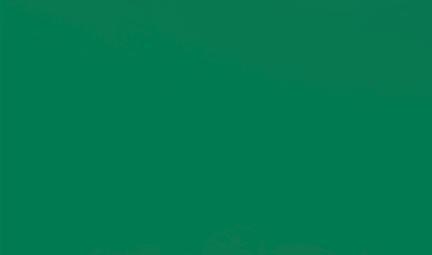
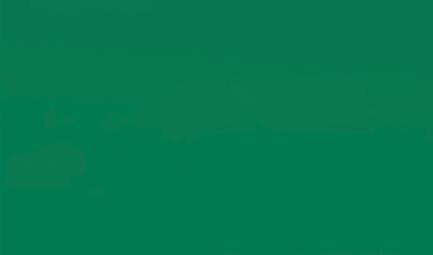

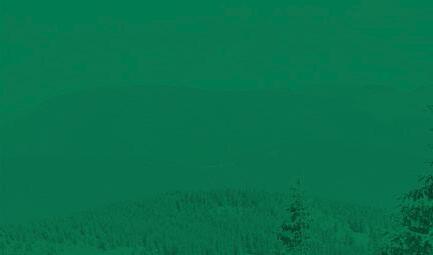
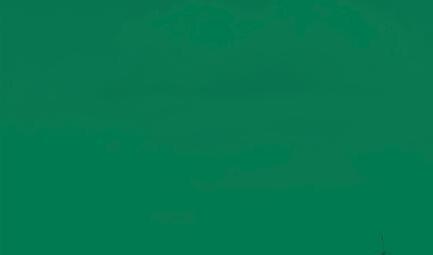
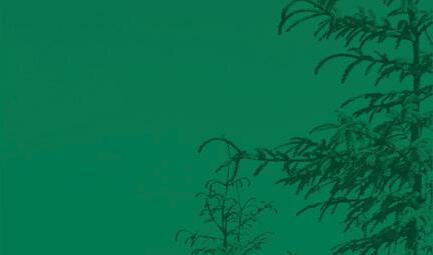
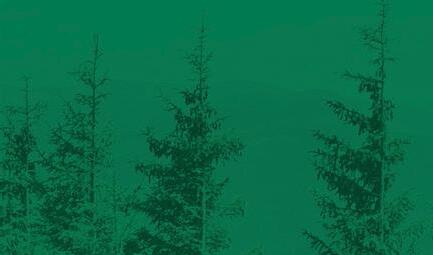

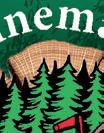
CUTTINGS FROM THE FOREST FLOOR DELIVERED DIRECT TO YOUR DOOR
NOVEMBER 2024 + ISSUE 49 + FREE PUBLICATION
JST ROAD TRAIN WORKING IN ABERFOYLE
Low ground pressure timber haulier
There is trouble at the mill: The profitable Sawmill in North Wales shuts it's gates for good as equipment and stock is sold off at auction.
Worker paralysed: A falling tree hit a worker in Dorset leaving him with life changing injuries.
World Wide Wood: we take a look at how global forestry is performing and the effect on overseas timber markets.
Engineering Masterpiece: Michel Kaiser gives us an insight into the history of the innovative MB trac forestry tractor.
Schools out: How Jim Wilmer has taken the initiative to start training the next generation of operators.
Cant see the wood for the trees: Fecon assists users in making the correct decision when choosing a mulcher.
New Kids on the block: Cat introduces eight new skid steer models.
Powering ahead: Sany sells it first medium sized electric excavator in the UK.
Take Charge: Sweden’s new electric timber truck takes to the road.
RAB EASTON Editor
Htaving passed retirement age I would like to have a bit more time to myself, so if we don’t manage to find a buyer, then this will be our last magazine. I am happy to keep you all up to date with
It will be a sad day on the 22nd of November 2024 when the gates of Glasfryn Fencing and Sawmill, located near Llanaelhaearn in north Wales, close for good. The Glasfryn estate trustees have taken the decision to shut the mill, after consultations with the Williams-Ellis family citing unspecified business reasons for the closure.
I was shocked and saddened to discover that this successful Sawmill was closing as it is an established profitable business with an impressive history in the heart of a beautiful rural farming community. My earliest memories of Glasfryn go back to the 1970’s and early 1980’s when my dad would take me with him when he went to buy Christmas trees from owner, Roger Williams-Ellis, to re-sell. Although my dad worked for the Forestry Commission, Roger had areas specifically for growing Christmas trees and they were of a far superior quality than our local ones.
It was great fun watching Roger, armed with his trusty axe, chop off the lower branches of the trees that my dad selected. Once he could get into the base, he would use the bushman saw to fell the trees. Dad and I would then drag them out
of the forest to load onto our trailer. I remember getting quite bored when they both took a break and started talking about forestry. The conversations seemed never ending to a youngster. In hindsight I wish I had spent a lot more time listening to them as they both had an encyclopaedic knowledge regarding the planning and establishing of new forests and many interesting and funny anecdotes of their experiences. People come from far and wide to buy their Christmas trees from Glasfryn. The company doesn’t create an excess of unsold trees, smaller trees that might have been cut down continue to grow into larger Christmas trees for the following year. Some of the older growth trees that were sold reached as high as 30ft as hotels, businesses and councils seek particularly grand trees.
This sustainable sawmill has been a lifeline for the local community, it was established in the 1980’s by Roger WilliamsEllis and Sawmill manager Arwel Roberts as an outlet for timber from Rogers own woodlands. Arwel’s wife Olwen, who manages the office, has also been instrumental in the development.
When the sawmill started to
produce fencing Arwel knew exactly what was required, most fencing mills will peel, point, treat and then sell timber. Arwel and Roger had a completely different approach, all their timber is checked for quality, straightness, and stress. Stressed wood does not absorb the pressure treatment properly so will not last as long. Once peeled and pointed it is stacked for between 3-5 months until the moisture content is down to 28% then it is pressure treated. This involves a lot more work so was obviously more expensive to buy. Farmers are famous for having deep pockets and short arms, so it took time to educate them to the advantages of Glasfryn’s products. Once they realised that the timber far outlasted any others, word soon spread throughout the farming community and business flourished.
Firewood has been another lucrative market for the mill, customers could order large quantities for delivery or call in on their way past for a trailer, pick up or car boot load. As with everything this sawmill does, even the firewood is a quality product. Wood that has been rejected for sawing or fencing is stacked up, so it is fully air seasoned prior to being processed and sold.
Naturally, customers are devastated by news of the closure. The sawmill is not just a fencing mill but also a sawmill where bespoke gates, styles, fencing, troughs, garden furniture and other wood products could all be manufactured to customers specifications and designs. Glasfryn prided themselves on the fact that no order was too big or too small and whether a customer spent one pound or a thousand pounds they were both equally as important.
All nine members of their loyal staff will lose their livelihood and as Glasfryn is the only mill of its type in the area their prospects are bleak. Glasfryn is impressive and has had a zero turnover of staff. The shortest serving member has completed 12 years of service and the longest has devoted 34 years to the firm. Every member of staff has been trained on all the equipment in the mill and could chop and change so that boredom never set in.
All the equipment, including the County tractors will be sold off at an online auction. A good proportion of the sawmill equipment, although effective at Glasfryn, is almost worthless as it has been adapted and modified for their own use. Roger was recognised by his peers for his contributions to forestry, he served as the chairman of the Welsh Timber Growers Association, awarded the OBE for his services to
forestry and the Royal Welsh Agricultural Society awarded him the Sir Bryner Award at the Royal Welsh Show for reaching the highest level of achievement in their chosen sector. He sadly died in 2018 aged ninetyfour and having met him on numerous occasions over the years I am sure he would be devastated at the thought of the sawmill closing and his loyal staff losing their livelihood.
The future of the forest is also uncertain as orders for the continual replenishment of the harvested wood had to be scrapped, and I would imagine without the sawmill and the passion of the staff who work the mill and manage the woodland, it will become just another forest and not the vision Roger Williams-Ellis had for the future.
The loyal customer base come from every corner of North Wales. I find it difficult to get my head around why anyone would shut down a busy and established, and very lucrative business. Only days ago, £280,000 has been invested in a new forestry-related skills and training fund by the Welsh Government, with the aim of growing the workforce and expanding the production of quality Welsh timber!!!
We visited Glasfryn Fencing and Sawmill back in 2023. To read this fascinating article visit www.forestmachinemagazine. com
Caterpillar introduces eight new next generation Cat® Skid Steer Loader (SSL) and Compact Track Loader (CTL) models. Four new Cat SSLs – the Cat 250, 260, 270, and 270 XE –mark the introduction of the next generation design to the SSL line. Meanwhile, the new Cat 275, 275 XE, 285 and 285 XE mark the expansion of the next generation design for the CTL line. The largest CTLs ever produced by Caterpillar, the new Cat 285 and 285 XE compete in a new class size with greater lift height and lift and tilt breakout forces.
All next generation Cat SSL and CTL models feature a redesigned engine compartment that places the engine and cooling package lower into the frame for improved stability. The four new CTL models are powered by the Cat C3.6TA engine, while the 250 and 260 SSLs are powered by the Cat C2.8T and the 270 and 270 XE by the Cat 3.6TA. These new engines maintain horsepower across a wider RPM range compared to the previous engines powering the D3 series and boast significant torque increases. With a vertical lift design, the new machines feature significant increases in lift height, breakout forces and ROC to elevate loader flexibility and performance. www.cat.com
ANNOUNCES
Following its European debut in the Netherlands earlier this year, SANY has announced the sale of its first medium-sized electric excavator in the UK.
On Wednesday, the tractor maker told officials in Iowa and Illinois that nearly 300 workers are being laid off as demand slumps.
About 200 production workers will be laid off in East Moline, Illinois. Additionally, 80 workers in Davenport, Iowa will also lose their jobs, along with seven in Moline, Illinois.
It is the latest batch of layoffs this year after 103 jobs were lost in July, an annual total of 2,100 across several plants in Iowa.
John Deere announced that the layoffs are unrelated to its production moving to Mexico and attributed the job cuts to a decline in demand for tractors and other agricultural equipment. This has resulted from falling crop prices and farmers reducing their expenditures.
But the company said that the layoffs are unrelated to its production moving to Mexico. Instead, bosses attributed the job cuts to a decline in demand for tractors and other agricultural equipment, which has resulted from falling crop prices and farmers reducing their expenditures.
Movement of production to Mexico has attracted the attention of politicians.
Donald Trump said in September that he will implement a 200% tariff on John Deere imports into the US if the company goes
ahead with plans to move production to Mexico.
At the start of 2024, John Deere employed about 22,600 salaried and production workers across the two states. www.deere.com
A NEW HARVESTER CHAIN DESIGNED, DEVELOPED AND OPTIMIZED EXCLUSIVELY FOR IGGESUND FOREST
• EXCELLENT STAY SHARP
• FAST CUTTING WITH EXCELLENT CHIP REMOVAL
• AVAILABLE IN REELS AND ALL POPULAR LOOP SIZES ( 2O PCS/BOX )
Acontractor from Dorset has been fined after a tree fell onto a forestry worker and left him with lifechanging injuries.
The 61-year-old man, who was 58 at the time, is now paralysed from the stomach down after the 21-metre ash tree landed on top of him at The Fonthill Estate in Salisbury, Wiltshire on 12 January 2022.
Gerald Hayward, who had been contracted as part of an ash dieback clearance programme, had been cutting the tree before it fell. Mr Hayward, trading as G H Hayward Forestry Contractors, had been making a back cut to the tree when it fell in the wrong direction. It then landed on the injured worker, who was standing in a nearby bridle path.
The worker, from Frome in Somerset, sustained eight broken ribs, a broken pelvis, two
broken ankles, a collapsed lung and internal bleeding. He was placed in an induced coma for two weeks and later spent four months in hospital.
An investigation by the Health and Safety Executive (HSE) found Mr Hayward, who was in charge of the tree felling, failed to implement a safe working zone around the tree as it was being felled. A safe working zone is usually twice the size of the tree, with only the felling operator permitted inside the zone. The tree fell in the unintended direction as the cut made by Mr Hayward did not leave a functioning hinge.
Gerald Hayward, of Blandford Forum, Dorset pleaded guilty to breaching Section 3(2) of the Health and Safety at Work etc. Act 1974. He was fined £1,000 and ordered to pay £1,000 in costs at Salisbury Magistrates’ Court on 15 October 2024.
HSE inspector James Hole said: “This was a serious incident that has led to an individual sustaining life-changing injuries meaning he is now unable to work and requires lifelong care. Mr Hayward failed to create a safe working zone around the tree while it was being cut down – this is a standard working practice for tree felling in woodland.
“He failed to implement the correct control measures and a safe system of work. Had Mr Hayward done this then this incident would have been prevented and the individual would not be paralysed and facing the rest of his life without the use of his legs.”
This HSE prosecution was brought by HSE enforcement lawyer Gemma Zakrzewski and supported by HSE paralegal officer Gabrielle O’Sullivan. www.hse.gov.uk
Center Parcs has unveiled £350-400 million plans for the creation of its first holiday village in Scotland amidst ‘significant’ demand for domestic short breaks.
A site approximately three miles from Hawick in the Scottish Borders has been identified for the new village, with Center Parcs signing an agreement with the land owners, Buccleuch
Group, for 1,000 acres of land –with the development expected to extend to 400 acres.
The proposed village would be a similar concept to its existing six holiday resorts in England and Ireland, with plans for the creation of approximately 700 lodges. The site would also offer a range of indoor
destination for families in the UK and Ireland and there is robust demand to support a seventh village.
“Throughout our history, we have demonstrated that a Center Parcs village provides significant economic benefits locally, regionally and nationally. Many Scottish families already visit Center Parcs villages in England, and this village will offer the chance for people to enjoy their holidays closer to home, which in turn will benefit the local economy.
SCA has become a coowner of SE technology and the pilot facility developed and operated by SweTree Technologies. With SE technology, it is possible to quickly and efficiently produce more plants from the best seed material from forest breeding. SweTree Technologies is running a pilot project to develop automated plant production via Somatic Embryogenesis (SE) in collaboration with forestry companies Stora Enso, Sveaskog, Södra, and Holmen.
Now, SCA has also joined the project as an SE company and become a co-owner of SE technology and the pilot facility developed and operated by SweTree Technologies.
So far, the development has focused on spruce plants, but with SCA’s involvement, SweTree has also started the development of SE technology for pine. This is being done jointly with all participating companies, parallel to the ongoing development for
spruce.
SweTree Technologies has been working for several years to develop the automated SE technology. With this technological leap, it is possible to quickly and efficiently produce more plants from the best seed material from forest breeding, resulting in plants with both higher growth and resistance to diseases and pests. This is positive for both forest economy and the environment. www.sca.com
The KESLA 165 marks the beginning of a new era for tractor driven forestry trailers. The robotic welded boxframe structure has a standard load space area of 4m² which can be easily expanded to an impressive 5m² by simply extending the bolsters.
Fitted with a KESLA 326T timber loader the gross weight of the trailer is 22,000 kg, a 6,000 kg dead-weight and 16,000 kg payload. It has an articulated tow bar and ISOBUS connected traction system so that the trailer follows the tractor perfectly, especially on steep hills and tight turns. The nave driven bogies have been
designed to climb over obstacles easily and increase overall traction to help prevent any soil disturbance.
The trailer has the 167/2013 EU approval and can be driven legally on public roads. www.kesla.com
The Tigercat 610H cable skidder aims to be a simple, lower cost addition to Tigercat’s highly regarded H-series skidder lineup.
The Tigercat FPT N6.7 engine delivers 151 kW (202 hp) to the same hydrostatic driveline as the other H-series skidders. The machine is equipped with 620H sized axles for add durability. The operator’s cabin however, is simplified compared with the other H-series machines. Rather than Tigercat’s signature
turnaround seat, the 610H is fitted with a fixed position seat angled at 30 degrees.
The heavy-duty winch provides maximum line pull at any engine speed. The winch can drop loads
loads and drive away and reel in a load while driving using a wetdisk dynamic clutch. It also has very low free spool resistance which allows for easier cable extraction using a mechanical jaw clutch. www.tigercat.com
Said by Komatsu Forest to be ‘a well-deserved model year upgrade’, a new valve block and new hydraulics design for the feeding system are some of the
Log Max 6000V Top Saw is well-suited for both wheeled and tracked harvesters. With the Top Saw, you can maximize the timber yield from every log, and the new function, Tilt Control, enables you to place the head at any desired tilt angle. 6000V Top Saw will be available on the market during Q1 2026.
Tilt Control comes as standard and the valve for this function is mounted below the existing tilt valve on the left block.
Tilt Control is a game changer when processing heavily limbed trees or when working in steep terrain. The saw box has been redesigned and extended to
accommodate saw bars up to 90 cm in length, a new root protection plate providing enhanced protection to the chain against roots and enables easier cutting of larger trees with a maximum diameter of
78,4 cm (30.9”). Furthermore, the footprint of the saw box has been reduced, making it particularly advantageous in snowy conditions.
www.logmax.com
Austria’s industrial and construction sectors remain in recession. In the meantime, private consumption has also deteriorated and remains at a low level despite last year’s wage increases and declining inflation. Current economic indicators do not point to any improvement soon. The paper, pulp and board industry sites are currently well stocked with coniferous industrial timber. Demand is normal and is currently mostly in line with supply. Demand on the energy wood market is very low due to persistently high stock levels.
According to the latest reports from International Tropical Timber Organization (ITTO), the value of Brazilian exports of wood-based products (except pulp and paper) in August decreased 10.8% compared to August 2023, from US$300.7 million to US$268.4 million. On a monthly basis, exports declined 21% due to shipping difficulties. Uncertainties related to maritime transport are negatively impacting the sector, even as exporters manage to overcome challenges such as high production costs and internal logistics. Competition for space on ships and rising freight costs are among the
main factors affecting the sector. Pine sawn wood exports decreased 9.2% in value to US$48.3 million in August, down from US$53.2 million in August 2023. In volume, exports decreased 10.4%, from 230,100 m³ in August 2023 to 206,200 m³ in August.
Tropical sawn wood exports declined 33.1% in volume to 17,600 m³ in August, down from 26,300 m³ in August 2023. In value, exports decreased 48.4% over the same time period, from US$12.6 million to US$6.5 million.
Statistics Canada (StatCan) reported that Canadian lumber production decreased 10.9% month-over-month to 3,988.5 thousand cubic meters in June. Year-over-year, lumber production was 3.3% higher. Canadian sawmills shipped 4,081.2 thousand cubic meters of lumber in June. That is down 9.9% from May and down 2.0% from June 2023.
More than 60,000 cubic metres of softwood logs are still arriving at Chinese ports every day, and despite a slight increase in demand, Chinese imports of softwood logs and timber remain well below past levels. That’s according to Scott Downs,
director of sales and marketing at PF Olsen, who reports that Chinese softwood log stocks are now stable at 3.5 million cubic metres, including 2.85 million cubic metres of radiata pine. Russia now accounts for 45 per cent of all timber imports, according to Chinese customs data - while Thailand, China’s second largest importer, now accounts for more than 18 per cent of the timber trade in the world’s largest forest economy.
The volume of timber trade in August was higher than usual and exceeded the average for the previous five years by a fifth. Cumulative timber trade volumes for January-August were 7% higher than last year and almost a fifth higher than in the previous five years.
From January to July, Germany exported 5.5 million m³ of softwood lumber. This corresponds to a decrease of 370,000 m³ compared to the five-year average. The sharpest decrease was recorded in the US, Germany’s main foreign market. Exports to Austria stable, decreases on remaining foreign markets.
From January to July, Germany exported 243,000 m³ of beech lumber, recording a 13% increase compared to the
same period of last year, when exports had totalled 215,000 m³
September was another month with more of the same for New Zealand log markets and the forestry sector in general. The big news was the announcement that both Winstone Pulp International
we still see 3% GDP growth in 2024 as strong consumption compensates for weak exports and investment
In the first seven months, the Swedish sawmill industry exported 7.8 million m³ of softwood lumber, recording a year-on-year decrease of 6.5%. This export volume corresponds exactly to the ten-year average of 7.8 million m³.
By Michel Kaiser
The 1980s started with a new highlight for agriculture and forestry. An important gap in the MB-trac program came in 1981 with the introduction of the MB-trac 900 (85 HP built from 1981-1982). The original MB-trac 900 was replaced over time by successor models, the MB-trac turbo 900 (85 HP built 1982-1987) and the MB-trac 900 turbo (90 HP built 1987-1991). The 900 Model MB-tracs were the best-selling tractors for forestry.
Over the following years there were changes to the MBtrac series with a completely new range of agricultural and forestry tractors from 65-156 HP, the MB-trac 700-1600 turbo.
In later years it was no longer Mercedes alone but an amalgamation with Deutz as TTVG (Trac Technik Vertriebsgesellschaft) where you could buy both the MB-trac and the IN-Trac. The last major appearance of the MB-trac came in 1990 with the MB-trac 1800 Intercooler (180 HP), only 190 of these units were built.
After 41,365 MB-tracs had been made this era ended on December 17, 1991, with the last one sold to a customer, it was an MB trac 1600 turbo.
MB Trac
Sales of MB-trac forestry tractors grew steadily in the 70s, replacing the Unimog, and logging companies gave the following reasons:
The Unimog’s disadvantages were entering the cab, the seating position, the relatively small wheel diameter and the visibility. The suspended rear axle was also said to be a problem during sensitive work, on a positive note the driving comfort was appreciated by users.
Logging companies demanded a powerful MB-trac with a fixed forestry structure to complete their daily work. The early MB-trac’s of the 1970’s had minor problems but were soon improved. Changes were made like the frames reinforced and brakes protected.
The forestry MB-trac was presented at demonstrations and the logging companies were convinced that this was the future, thus it became the best-selling forestry tractor of the 80s.
The Werner company had a so-called demonstration train to take out to customers with a double drum winch tractor and a logging tractor. The Werner demonstrators were skilled users of the MB-trac and the interaction between man and machine was so balanced that
there was no weather or ground conditions to frighten them. Even their harshest skeptics soon changed their opinion.
The MB-trac was designed differently to standard tractors, it had a portal front and rear axle, which resulted in high ground clearance and a static axle load distribution of 60% on the front axle and 40% on the rear axle. This was unique as when loaded it had an evenly distributed axle weight balance 50:50.
The front axle was suspended, which improved terrain adaptation and driving comfort. Driving on the road the MB-trac could drive quickly from one location to another with its 40 km/h top speed transmission and was extremely comfortable over long distances.
The all-wheel drive was distributed over the four equal wheels, which meant that it was a "real" all-wheel drive. This means that four wheels of the same size transfer the engine power to the ground. These wheels are forced-driven, which means that they are connected to the engine via clutches and gears. This guarantees greatest power transmission even when the ground conditions change significantly.
Both axles are equipped with 100% claw differential locks and engine power is equal to drive power. There is no slip clutch or torque limiter on the front axle; this ensures a constant flow of power to the front wheels. The front and rear wheels cover the same distance at the same speed, i.e. there is no forced slip of the front wheels. This is found in normal four-wheel tractors, the front wheels "rush" ahead of the rear wheels. The four-wheel drive and differential locks can be switched on or off while driving under load.
Werner & Co were founded in 1902 as a metalworking company and were a specialist company from Trier who manufactured winches and logging equipment for forestry.
They initially got involved in forestry when in 1928 a local timber haulage and logging contractor came up with the idea of using his Lanz Bulldog for logging and approached Werner with this idea.
To be able to drive a cable winch, a mechanical drive was needed so the gearbox housing was drilled through, and an external gear shaft was attached. With this conversion their first step from a metalworking business to a winch manufacturer was made.
1958 saw their first involvement with Unimog, a 32hp 411 model. A demonstration took place and those present were
delighted with the ability of the Daimler Benz. The company bosses at the time, Peter Werner, and Hans Werner, decided to build equipment for the Unimog’s from that day on. It wasn’t long before a front cable winch was built for the Unimog 404S.
Up until 1965 Werner cable winches were available for all tractor manufacturers but in 1967 the decision was made to specialize with Unimog’s.
From 1974, forestry equipment for the MB-trac was added to the list and from the mid-1970s, the supply of cable winches was moved to the Glogger company, which built the winches according to Werner's wishes.
For the whole MB-trac series (50kW-115kW), Werner offered a complete range of forestry equipment which could be fitted and used altogether or individually for each operation. This was considered unique in Europe. All Werner’s forestry equipment was FPAevaluated (Forestry Technical Examination Committee) and was given the seal: "suitable and recommended for forestry". Today, MB-tracs with Werner attachments are still in daily use in our forests.
When the MB-trac was finally stopped in 1991, Werner built a logging tractor that was remarkably like the MB-trac, the WF-Trac. The WF-Trac logging tractors were available as 900 and 1100 with Werner bodies.
Due to the increasing demand in the forest for large logging tractors, Werner developed a WF-Trac over time that can easily compete with other logging tractors in terms of size and can be seen in our forests with up to 8 wheels as a forwarder/skidder/harvester or combination machine, but it no longer looks like the MB-trac.
The Nagel company was founded in 1954 as an agricultural machinery dealer and repair shop. In 1968, they started manufacturing forestry equipment for Güldner and Hanomag tractors. In the beginning their cable winches were supplied by Glogger.
A so-called market calm, which suited Mercedes-Benz for the MB-trac forestry vehicle, was disrupted in 1977 because Nagel offered a range of forestry equipment for the MB-trac.
The front polder device was constructed like a front loader, which allowed a large lifting height and made it possible to attach various tools such as a front polder shovel.
The strong support was optimally built in terms of size and supporting surface, so that the transport of strong and weak wood was possible, and a logging grapple could also be installed on the strong support. A cable outlet with a
hydraulically adjustable height was introduced and forestry protection equipment was tailored to the MB-trac. All modifications were conducted in such a way that the vulnerable parts of the tractor were optimally protected.
Nagal was simply unable to gain a "firm" foothold in this sector due to minor problems and disagreements with DaimlerBenz although their products were well received by the few customers they had.
Their annual production remained at an average of 6-7 machines even though the MBtrac with their equipment could be offered for around 10-15,000 DM cheaper than a comparable machine from Werner.
The Ritter company was started in 1924 as a mechanical engineering workshop. It manufactured and repaired industrial and agricultural machinery. Due to the mechanization of agriculture, RITTER began manufacturing hydroelectric plants, turbines, fruit presses, fruit mills, circular saws, cable winches and material cable cars not long after the company was founded. Their main partnership was with Deutz tractors although they also manufactured forestry attachments for Steyr, Schlüter, Fiat, Renault, John-Deere and Same tractors.
In 1974 their first single-drum
winch was installed on an MB-trac 65/70 followed with their first complete forestry conversion on an MB-trac 800 in June 1978. The first MB-trac 1000 for forestry was rolled out in March 1984 with the first MBtrac logging crane tractor fully installed in 1989.
Despite an FPA-tested and approved MB-trac turbo 900 complete with forestry equipment it was difficult for Ritter to get a foot in the door at Daimler-Benz so only managed to manufacture between 3 and 5 machines per year.
The MB-trac was the most popular and best-selling forestry tractor in the 1980s, its image, capabilities or sales couldn’t be matched by any other manufacturer of forestry vehicles.
In the forestry sector, the following has always been true for agricultural tractors: If it can be used in forestry, it is also suitable for all other tasks.
The MB-trac was the perfect logging tractor, it passed all its challenges and exceeded all expectations, it was classed as a grade 1 vehicle which made it the most popular forestry tractor. As difficult as it was to achieve this position, it was no easy task keeping it. The practical requirements were clearly laid down by the foresters:
• High drive power with the
• lowest possible slip
• Dimensions suitable for forestry
• Performance-maintaining workplace
• The ability to use a wide range of forestry and attachment equipment
• A stable construction to minimize downtime
• High ground clearance, favorable slope angles
• Good view of the work area
• A good power-to-weight ratio (low ground pressure, large load reserves)
• Sufficient protective equipment
• Manoeuvrability to minimize damage to existing stocks
• Efficient forestry equipment
• The ability to convert to wide forest tyres
• Short downtime of the tractor
• Well-functioning repair and spare parts service
The MB-trac met all requirements and proved itself even under the toughest conditions, It simply was the better alternative.
It was clear that the collaboration between the tractor manufacturer, body manufacturer and end user worked perfectly, and that the development and advancements of practical solutions was the focus.
It was a tough business for both man and machine in the forest, and sometimes families suffered greatly as a result. No matter which logging operator and family I met, they told me
that it was a good time, even if it was difficult to earn money for the machine and the family “from the log”, and that in all weathers. The machines and people were put to the test, but the MB-trac mastered its tasks to the complete satisfaction of the customers. The reliability of the MB-trac logging tractor and the ease of work that came from the technology made its owner happy to have chosen such a tractor.
It must be noted that a fully equipped Werner Forst MB-trac turbo 900 cost around 170,000 DM, and that had to be proven. One forestry contractor I visited said to me: “Without the MBtrac I wouldn't be where I am today, a successful entrepreneur with 14 machines and a reliable workforce!” Another said, “I made money with the MB-trac, it was a great time even though it was tough!"
I heard an interesting comment from a logging contractor I visited for a photo shoot: “I will never sell my MB-trac, only pass it on!”
Today logging tractors with the star can still be found in challenging work.
The next part is: The MB-trac with a single or double drum winch. Michel Kaiser Book author and MB-trac expert For more great pictures/videos and information on the iconic MB Trac and Unimog follow Michel’s Instagram page at www.instagram.com
The Bell Skogger is developed to be a flexible and cost-effective timber handling solution for mechanised timber operations
The four-wheel drive (4WD) Bell Skogger design concept has versatility at its core. “It’s not a logger or a skidder – it’s a Skogger.”
While developed with primarily an extraction application in mind, the boom and grapple configuration lends itself perfectly to the accumulation of timber infield for extraction, sorting, stacking, and loading timber. There is also an option to install a felling kit, which utilises a felling head where tree size, terrain, or underfoot conditions necessitate a heavier 4WD carrier.
Skogger utilises a simple and efficient hydrostatic-mechanical drivetrain with good ground clearance and a low centre of gravity. Its comfortable and ergonomic rubber-mounted operator cab is air-conditioned and boasts a 180° swivelling operator seat and excellent allaround visibility.
The Bell Skogger, powered by the JCB Diesel Max 444 T2 Turbo engine, delivers an impressive 74kW of power at 2,200rpm, ensuring a powerpacked performance for timber extraction operations. The
overhead boom is equipped with dual lifting cylinders and internal hose routing to ensure efficient and reliable timber handling. With frame articulation of 86 degrees, stop to stop, the Bell Skogger exhibits outstanding manoeuvrability, effortlessly navigating through tight spaces during timber extraction operations. The operator joystick ensures precise steering control for smooth and efficient operation that enhances the overall productivity and ease of use for the operator.
The Bell Skogger’s rigid front axle and oscillating rear axle make it a master of uneven terrains, effortlessly conquering challenging landscapes during timber extraction operations. With a rear axle oscillation travel of 30 degrees, stop to stop, the Skogger has exceptional manoeuvrability, allowing operators to navigate tight spaces and difficult terrain with ease.
Equipped with standard 23.1 – 26 (16 ply) tyres, the Bell Skogger provides reliable traction. For enhanced performance and even greater traction, an optional 18.4 – 30 (16 ply) tyres configuration is available for the toughest logging environments. With high and low range options and a maximum speed of 20km/h
(12.5mph), the Bell Skogger effortlessly manoeuvres through challenging landscapes, ensuring timely and efficient timber extraction.
The Skogger’s four-wheel drive system guarantees optimal traction, while the heavy-duty outboard planetary limited slip differential lock provides stability and control for safe and reliable operation even in rugged logging environments.
The Bell Skogger focuses on operator comfort and productivity with its rubbermounted, glazed, and airconditioned operator cab providing a comfortable working environment even in challenging conditions. The ergonomic operator controls, including the mini-coordinate joystick, make operating the Skogger precise and effortless, enhancing productivity and reducing operator fatigue.
The 180º swivel seat of the Bell Skogger improves visibility and manoeuvrability, allowing operators to navigate logging operations with ease. A reverse camera is available as an option to improve visibility when reversing. The ROPS/FOPS/OPS compliant operator cab further enhance safety and convenience for the operator.
Fixed Head for tree fellings due to safety reasons 20 - 28 t
TECHNICAL FEATURES
Two strong, independently closing grippers
dualGrip
Automatic chain tensioner, grease lubricated chain
Saw box: swinging chassis with active suspension
Power-Tiltator, endlessly rotatable
OPERATIONS
• Safety tree removal
• Chipper feeding
• Sorting
• Loading
• Storm area clearing
• Bundle cutting
• Material handling
Forestry is one of the only industries in the UK that has few facilities for training new machine operators. The UK harvested ten million tonnes of timber last year. We have the resources to produce over fifteen million, but not the skilled labour needed to do this.
The sawlog market is quiet just now, but what will happen when we see an upturn and there is neither the equipment nor workforce to supply the demand. There are currently well over forty UK vacancies for forest machine operators, and when you consider we only have around seven hundred harvesters and forwarders in total, which is a large number of machines parked up. At over £500K for a harvester and over £350K for a forwarder who in their right mind is going to invest on an empty promise of work. Some longterm harvesting contracts guaranteeing X amount of tonnage per year are worthless and can be withdrawn at the drop of a hat when the demand for timber lessens.
Contractors make huge finance payments on equipment that can sit idle with no one available to run them. Their only option is to advertise unsustainable
high operator rates in the hope that someone will jump ship. Talk about caught in a tricky situation.
After finding it near impossible to recruit skilled operators, Jim Wilmer, of Jim Wilmer and Sons Timber Harvesting, decided to test the water by advertising for trainees via his social media pages and was flabbergasted by the results.
His criteria was for young trainees to be local to the Ayrshire area with an excellent work ethic and full driving license, and his phone never stopped. He had over fifty applicants within 48 hours, most were from the UK and a couple from as far away as South America. Jim pointed out that he had tried an earlier training programme and learned from his mistakes. He soon found out that when taking on trainees from other areas, once they achieved a reasonable level of competency, they started looking for work with contractors nearer to home. He found this disappointing as he had invested considerable time and money in the project only to see no return whatsoever.
Seventeen candidates met his criteria, and after whittling it down to fourteen, he started to interview the potential
applicants. A final six were selected with three on a reserve list.
Two used John Deere Forwarders were bought, and put through the workshop, a 2004 1410D and a 2011 1910E to be used purely as training machines. The trainees are to start at separate times over the coming months so that they could work on a one-to-one training regime.
Jim laid out his training programme and I was impressed by the way he had structured it. A trainee spends the first three days on a simulator, which had been donated by John Deere and introduced to the health and safety aspect of the work by going through risk assessments. This is so they understand working and site constraints, emergency procedures and exactly what is expected of them by their employer and Forest Works Manager.
Once the apprentices have completed this stage to Jim’s satisfaction, the next step is one to one tuition on a forwarder at the workshop and yard near Daily. This involves daily maintenance, refuelling, loading, traversing the forest track and unloading the forwarder. This is continued until a proficient level of crane
forwarder operator and keep in radio contact; he has been brilliant by offering some useful hints and tips and is incredibly supportive.”
Jim has been lucky as most of the trainees are from agricultural type backgrounds so are not afraid of demanding work or getting their hands dirty. An interesting point is that none of the applicants were unemployed, every one of them was making a career change. The 1910 was being serviced when I was there but trainee Rory Grey was using the 1410.
Jim and his son Gary and sonin-law Rich, are the instructors for the initial basic training on simulators and forwarder training in the yard, both keep a close eye on the trainees and are on hand to offer reassurance and encouragement. Training each candidate occurs a considerable cost in both time and money. Until they reach a level of competency where they are productive workers, Jim pays just above minimum wage with no restriction on the hours they work. With the trainees salary, mentors expenses, equipment costs and fuel, it equates to a cost of around £20K per trainee before he starts to see any return on his investment.
It is good to see the support Jim has from other contractors who are in full support of what he is trying to do. “Hat’s off to Jim Wilmer who once again is taking the lead in education in our industry” said Rob Cubby,
owner of the Lake District based family business Fin Forest Logging. “This isn’t the first time Jim has put up his own time, resources and hard-earned cash to try and inject some meaningful training and new, young blood into UK forestry.
“Over the years Jim has given me his time, knowledge and advice, not for monetary gain but because he has a great passion for the industry and others who love it and want to excel within it. It is such a shame that yet again it is the contractor, the person at the sharp, real and often very tough end of the job, who is pioneering training and employment.
“It is about time the government and the private sector timber buyers, sawmills and forest management companies stood up and engaged properly. If they all had just a half of Jim Wilmer on their board of directors, forestry in the UK would be in a better state of affairs. Look up and follow the lead Jim and his company are taking before it is too late. Jim, I wish you all the best in this endeavour.”
Rob echoes what many of us think! If there are no educational facilities to train new recruits, then surely timber merchants, sawmills, wood processing plants, management companies, the government and forest bodies must help address this issue.
I asked Jim if he was getting any support with his program.
“John Deere have been helpful by supplying us with the training simulator but there has been no other help or financial assistance forthcoming so far from any other areas of the industry. I have since resigned from CONFOR as I don’t understand why they expected me to support an organisation that doesn’t appear to offer any worthwhile support in addressing this impeding crisis. We are however contacting harvesting firms requesting their support. I am not just talking about doing something with this, I have taken the bull by the horns and have this up and running but I need help and support from others within the industry and will be making contact with these firms in the coming weeks .”
I can see Jim’s point and that he was at his wits end when I spoke to him, as this is a crippling situation which he cannot afford but doesn’t know what else to do. He has spent a lifetime building his business, starting out on a chainsaw and is immensely proud of what he has achieved. His ambition is to leave a successful business for his family to take over as many of them are actively involved in the day to day running of it.
I feel very strongly regarding this as in 2001 I was employed by the SRUC at the Barony College in Parkgate near Dumfries as a forest machine instructor. We were running a threemonth training course where youngsters got the opportunity
to acknowledge this problem exists, but then do little or nothing to work together for the greater good. This is an industry wide problem that requires the collective effort of everyone in the sector and not just one contractor.
I have since contacted Confor, Mairi Gougeon (the MSP for Rural Affairs) and the SRUC to see if they intend to do anything to address this. I have had one reply and that was from Professor Davy McCracken, BSc, PhD, FRSE, The Head of Department of Integrated Land Management SRUC
“Thanks for your email to Hugh which he has passed on to me. I head up the wider Department in which Hugh’s forestry and arboriculture team sit. And although I am not a forester, I have been managing that wider department for the last five years and am hence familiar with many forestry education and training needs.
“The lack of training for Forestry Machine Operators – and the wider industry need for such operators – is something that we (and the wider Trees & Timber Skills Group chaired by Scottish Forestry) are well aware of. Indeed, back in 2019 we worked with Scottish Forestry and Forestry & Land Scotland to run a pilot Forestry Machine Operator [FMO] Modern Apprenticeship [MA] programme. Part of the rationale behind this pilot was to help get a small number of
additional trained operators into the industry, but the primary rationale was to consider what the associated costs were for training operators to a standard acceptable to the industry.
“With regard to the latter, the total delivery costs for the small cohort of candidates [4 in our case] that could be put through such a bespoke course was in the region of c £12+K per candidate. And that was before factoring in the costs that FLS bore in providing access to facilities, equipment and dayto-day candidate supervision [which were estimated at an additional £7K-£8K]. So roughly £20K per candidate and equivalent to the example you provide for Jim Wilmer.
“As you are likely aware, Skills Development Scotland [SDS] put tight requirements [around age and previous experience] on the amount of funding available for different MA candidates. In addition, the actual SDS Contribution Rate is £3,700 for the Level 5 MA and this hasn’t changed for over 10 years [and so it has not kept pace with inflation and other costs].
“The fundamental issue therefore was – and remains – that the gap in true delivery costs was too big for SDS to ever think of considering closing via directing additional public funding into such training. And even – as you recognise – if industry was willing to contribute access to equipment, without the ability to cover the
true delivery costs borne by SRUC any such training remains unviable to run.
“The only potential solution going forward would be for there to be some package of public and private funding which helped meet those true costs of delivery. Andy Leitch oversaw the pilot while he was at Scottish Forestry, and I am aware that he still recognises the issue in his role within CONFOR. We remain in contact with Andy over this and other – possibly easier to tackle – forestry education and training needs. FMO training is not an easy nut to crack and certainly not one that SRUC could ever crack on its own.”
From my understanding of this, training courses for machine operators through the education system is highly unlikely now or in the future. It would appear that on-site training like Jim Wilmer and Sons have initiated is going to be the only practical way to address this crisis. As an industry, it is time to dig deep into your pockets and offer your support, ultimately every one of us will benefit in the long run.
Other countries manage to find money to pay trainers and fund apprenticeships. In southern Germany many older, skilled operators leave full time work and get paid by the government and forest bodies to train the next generation of operators at forestry schools. This is a great move as they can pass on a lifetimes worth of hints and tips which would otherwise be lost.
The well-known and popular Prinoth Raptor 300 with the associated Grizzly M650m mulcher has been optimized with a number of improvements to better meet
Land management takes many forms, but forestry mulching has gained quite a reputation in recent years. And for a good reason— the benefits are far-reaching, from economic impacts to environmental ones. Read on to uncover how forestry mulching can positively affect the environment, save you time and money, enhance the aesthetics of landscapes, and more.
Before we discuss the benefits of forestry mulching, let’s define it. This tried-and-true technique involves a machine that cuts, grinds, and clears vegetation, which then becomes mulch. The positive environmental impacts of forestry mulching cannot be overstated. While traditional land-clearing methods typically rely on burning or hauling away vegetation, forestry mulching leaves organic material on the ground, and that’s when the magic happens.
As the mulch decomposes and organic material returns to the ground, it releases nutrients, enhancing soil fertility. The result is a nutrient rich environment that supports healthy plant growth and a thriving ecosystem.
Erosion has become increasingly common in areas with less vegetation. However, forestry mulching is proven to help combat this issue, providing a protective layer of mulch on the soil surface. The added layer of mulch keeps moisture, protects root systems, and prevents the soil from being washed away by rainwater.
Forestry mulching helps native plants thrive by eliminating invasive species and creating a great environment for local flora. The mulch layer keeps invasive weeds at bay and gives native plants a nutrientrich place to grow, boosting biodiversity and restoring natural habitats.
Forestry mulching is not only environmentally friendly but also highly efficient compared to traditional land clearing methods. This efficiency translates into considerable time and cost savings.
Traditional land clearing usually involves several steps, such as cutting, hauling, and disposing of vegetation. Forestry mulching, on the other hand, combines all these steps into one. The machine cuts and grinds vegetation on-site,
leaving the mulch behind. This streamlined process saves considerable time, letting landowners and contractors finish projects much faster.
When you rely on forestry mulching, you can say goodbye to expensive project costs, unnecessary equipment, and excess labour for hauling and disposal (which tends to be exceptionally pricey when moved off-site). Since the mulching process is so efficient, it means less time on projects, lower fuel use, and reduced labour costs, making it the budget-friendly choice for landowners and developers looking to manage and clear land.
Looks aren’t everything, but they do matter to some people. The best part about forestry mulching? It offers aesthetic benefits that also result in environmental improvements. The practice can transform landscapes, creating visually appealing and functional spaces for everyone to enjoy.
Keep your natural habitats thriving! Forestry mulching equipment grinds trees, brush, and other vegetation into mulch on-site, allowing for the quick
and effective removal of invasive species without the need for transport or burning.
The organic mulch left behind by forestry mulching looks natural, plus it’s great for the environment. As it breaks down, it enriches the soil, helps plants
direction.
As a quick refresher, forestry mulchers are powerful machines designed to clear brush, trees, and other vegetation by grinding them into mulch. There are three main types of forestry mulchers: deck mulchers, disc mulchers, and drum mulchers:
• Deck mulchers: Deck mulchers utilize swinging blades to quickly and efficiently cut small vegetation. They excel in managing dense undergrowth, delivering a moderately fine finish. While they can cut larger material into sections, their strength lies in quickly clearing brush, making them an ideal choice for projects requiring speed and efficiency in processing lighter vegetation.
• Disc Mulchers: Disc mulchers utilize a spinning disc with fixed cutting teeth and operate quickly and efficiently. While they can fell larger trees, their primary function is rapid timber processing. They are unmatched in their ability to quickly process standing trees, making short work of material that other types might process more slowly. However, the trade-off for speed is a more coarse finish.
• Drum Mulchers: Drum mulchers offer the most versatility, capable of
• processing both large and small material effectively. While they might not match the speed of a deck mulcher in clearing brush or a disc mulcher in processing standing timber, they excel at delivering a fine, even finish across various materials. This makes them a go-to choice for operators who need to handle a variety of tasks with a single attachment.
Each is suited for different tasks and terrains, so assess your specific needs first.
Now that you know about the different types of mulching equipment, let’s talk about key features to consider when choosing your machine and attachments:
When choosing a forestry mulcher, understanding each type’s cutting and processing capacities is essential, as well as the desired finish you want to achieve. Each shines in different applications; sometimes, a combination of these is necessary to achieve optimal results. Deck mulchers are highly effective for rapidly clearing brush and smaller vegetation, delivering a medium finish. Disc mulchers are unrivalled in high-speed timber processing, excelling with
standing trees but leaving a coarser finish. Drum mulchers provide the greatest versatility, handling both large and small materials while offering a fine, even finish across various conditions.
The performance of a forestry mulcher is heavily influenced by the hydraulic horsepower provided by the carrier machine. When selecting a mulcher, it’s crucial to ensure that the carrier offers sufficient hydraulic flow and pressure to match the mulcher’s specifications. Balancing hydraulic power with efficiency not only optimizes performance but also helps in reducing overall operating costs by maximizing productivity while minimizing fuel consumption.
Durability is critical when it comes to land clearing. Choose mulchers made from highquality materials designed for longevity. Also, make sure they’re easy to maintain. Look for machines with accessible parts and straightforward maintenance routines to minimize downtime and keep operations running smoothly.
Safety cannot be overstated when it comes to heavy machinery. Choose mulchers with safety features like reinforced cabins, emergency shut-off switches, and protective
guards to help prevent accidents and keep everyone safe.
Compatibility is key! Make sure whichever mulcher you choose works with your current equipment, whether it’s an excavator, skid steer, or tractor, to ensure smooth integration
might be tempting to spend less, investing in a high-quality and reliable mulcher will save you time and money in the long run.
Put your trust in people who have taken on similar projects. Their reviews and testimonials can provide essential insights into the performance and reliability of different mulchers. Pay attention to feedback on durability, efficiency, and ease of use.
SCA’s new electric timber truck with a crane is finally rolling in the Östavall area. The truck, which is a collaborative project between SCA and Scania, is the first in the world to collect timber in the forest for further transport to a timber terminal. On October 21, the truck was showcased to the media.
The yellow timber truck moves almost silently into the timber terminal in Östavall. Behind the wheel sits Rolf Lövgren of Lövgrens Åkeri & Entreprenad. He owns the new timber truck with support from SCA and has driven it for a few days.
“It is very quiet and comfortable to drive, and I don’t get as mentally tired as I can after a full day with background noise from the engine. It is very positive,” says Rolf and continues: “It takes a while to get to know the truck and learn how to drive it in the best way to conserve the battery. You want to charge more than you consume. If I have 50 percent battery left at the end of the day, I have stood still and charged unnecessarily. It will be exciting to see how it performs during the winter.”
The new electric timber truck marks another important
milestone for SCA and the work to electrify heavy timber transports. The truck is expected to result in 170 tons lower carbon dioxide emissions per year compared to a regular timber truck.
“This is an important project for us to continue contributing to a more sustainable society,” said Ulf Larsson, CEO of SCA.
“By managing the forest and making renewable products that can replace those with a high carbon footprint, SCA creates about 13 million tons of positive climate benefits each year. That figure can become even better as we transition the heavy road transports in our value chain.”
“It is exciting that it’s finally in place. From the first
conversations with Scania, it took just over two years for this electric timber truck with a crane to become a reality. Our first electric timber truck only runs between the terminal and Obbola paper mill, but now our development work continues as we electrify the transports from the forest to the terminal,” said Anton Ahlinder, Business Developer at SCA Skog.
The new electric timber truck is part of the forest industry’s innovation project TREE, which stands for Transition to efficient electrified forestry transport and aims for half of the new trucks in the forest industry to be electric by 2030. SCA is one of several participants. If the project reaches its goal of having 50 percent of the new
trucks in the forest industry electrified by 2030, it will result in a reduction of 260,000 tons of emissions.
“Östavall is one of the places where there should be electric timber trucks. We are aiming for a total of 12 trucks, six like this one that SCA has now put into operation and six chip trucks,”
SCA is responsible for a significant part of the financing of the electric timber truck, but the vehicle is owned by Lövgrens Åkeri & Entreprenad.
“To make the transition successful, we need to have haulage companies with us, and therefore it is good that this vehicle is owned by a local
a better power grid, and that working time regulations offer flexibility related to charging. Then the heavy traffic will gradually move towards more electrification,” says Ulf Larsson.
Photo: Olle Melkerhed
After almost a decade of successful operations in North America, PALFINGER EPSILON expands its market penetration by bringing the tested and customer approved M13A crane to South America. The choice fell on the Chilean province of Araucanía, a center of the country’s timber industry, where the demand for powerful and reliable machines is constantly growing.
The project to introduce the M13A80 in Chile began back in 2020, and the first units were delivered to the region the following year. Since then, more than 20 units already populate Chile’s landscape, and the demand continues to grow. One of the five countries with the highest gross domestic product in South America, Chile is increasingly relying on advanced and high-quality machines.
The M13A is specially designed to transport timber from steep and hard-to-reach forest areas to sawmills in industrial centers. With its high speed, endless slewing system, comfort seat, and the ability to perform many loading cycles per day, the M13A helps to increase efficiency and thus the profitability of timber transporters. In recent field visits operations were confirmed to be running smoothly,
and the cranes have proven themselves in Chile’s demanding environment.
With the successful launch of the M13A in Chile, PALFINGER EPSILON continues to increase its market share. By introducing customized crane models to new and challenging markets, we continue our path of delivering innovative and
reliable solutions to the global timber industry.
Special thanks go to our Chilean partner SIMMA, who has worked hard to establish the M13A on the market. SIMMA not only offers excellent technical support, but also a state-of-the-art service that ensures our customers are always well looked after.