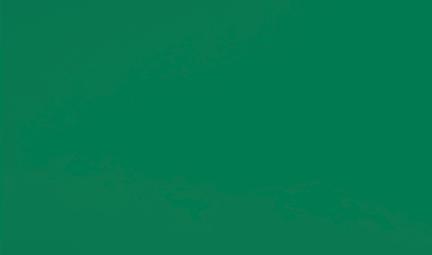

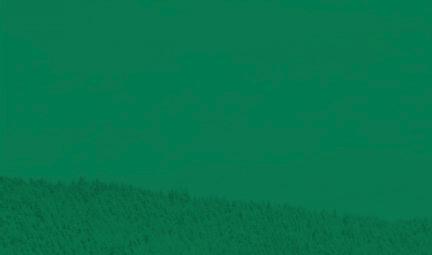
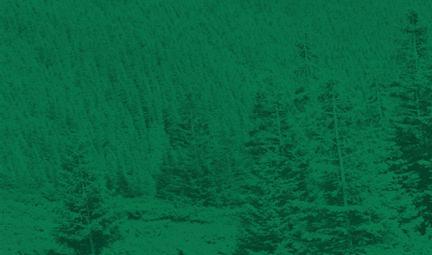
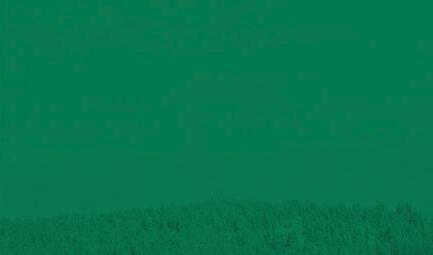
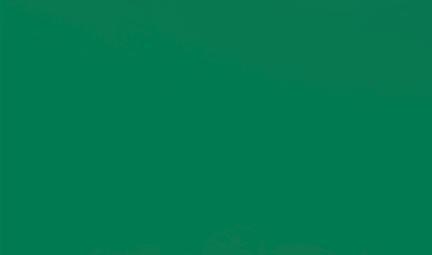
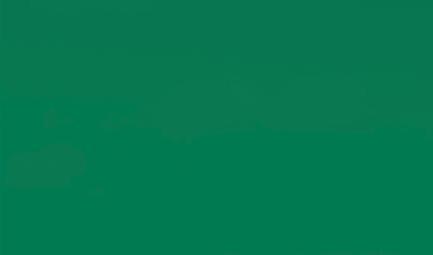
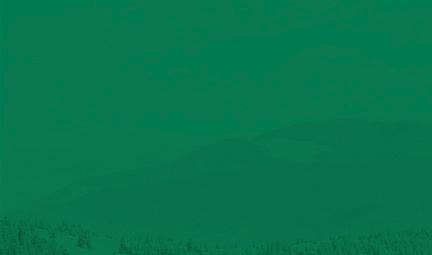
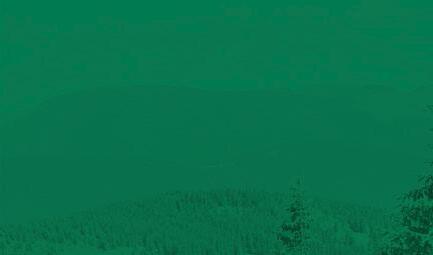
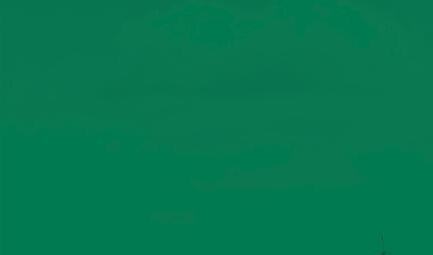

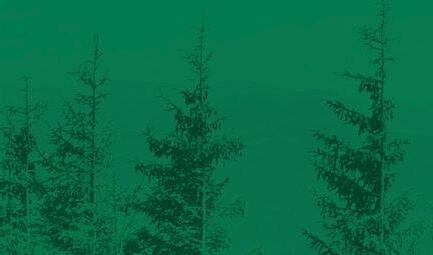
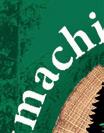
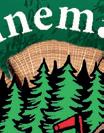
CUTTINGS FROM THE FOREST FLOOR DELIVERED DIRECT TO YOUR DOOR
JULY 2024 + ISSUE 47 + FREE PUBLICATION
READ MORE ABOUT GARY ROBERTS, ON PAGE 36
Winner of a £100 Amazon Voucher
Moving Stateside: Nokian Tyres opens a goods warehouse in Tennessee.
Smart Thinking: Komatsu Forest’s Maxi Fleet advances to a much higher level.
A Growing Company: Tubex showcases biodegradable tree protection for saplings at 18.KWF Tagung.
High Flyers: 5G Equipped Drone remotely controls forwarder.
Picture This: See if your photo made it into this issues gallery. Fire Danger: How effective land clearing can prevent wild fires.
Open
Diamond Jubilee: DAF Trucks celebrate three quarter of a century of truck building.
Making Headway: Cat’s new grading beam for easier forest road construction.
I Saw It Here: POSCH’s new quite circular saw blade that purrs like a kitten.
RAB EASTON Editor
GB LUBRICANTS GET THEIR KIT ON FOR THE GREAT NORTH AIR AMBULANCE
Nokian Tyres has opened a new finished goods warehouse in Dayton, Tennessee, marking the completion of a ramp-up process at the company’s US production facility.
Nokian Tyres began tyre production at the US factory in 2020 and has since expanded its operations by increasing production capacity, growing the team to approximately 500 employees, and enhancing capabilities to produce North American-specific all-season and all-weather car tyres. This year, production has been expanded to include light truck tyres.
“Nokian Tyres is pursuing growth in North America, and the Dayton factory is the centre of those efforts,” said Nokian Tyres Vice President of Passenger Car Tyres Lauri Halme. “It allows us to serve growing demand for our all-
season and all-weather tyres in the United States and Canada, which complements our decades-long legacy of winter tyre leadership.”
The finished goods warehouse, located adjacent to the US factory and spanning 32,500 square meters, was inaugurated last week. The warehouse can hold hundreds of thousands of tyres. Tyres are shipped from the finished goods warehouse to Nokian Tyres’ nine-warehouse network across North America, from which the company serves dealers in the United States and Canada.
“The opening of our finished goods warehouse marks the completion of a growth process that took us from a 60-member launch team to a 500-colleague workforce,”
Dayton Factory Operations Director David Korda. not have reached this point
without great dedication from our employees, and we are also grateful for the support we have received from the community, our customers and our colleagues around the globe.”
Nokian Tyres’ US factory is the first LEED v4 Silver-certified tyre
Digital development in the forest machine industry is seeing constant progress. Our digital solution, MaxiFleet, has offered you a comprehensive tool for simplifying the working days –
AD
n increasing threat of wildfires amid rising temperatures and Met Office warnings could have a “devastating” impact, according to the UK’s largest woodland conservation charity.
The Woodland Trust says uncontrollable wildfires put people, wildlife and natural habitats at risk. And with a Met Office amber alert issued in parts of the UK, the Trust has urged visitors to woods, parks and green spaces to stay fire free.
With school holidays fast approaching, the conservation charity is expecting increased numbers of visitors to its more than 1,000 free, public woods across the UK, but says barbecues, campfires and discarded picnic rubbish could spark disaster.
Nick Hall, head of safety at the Trust, says even a single ember from a disposable barbecue during prolonged spells of extreme hot weather can ignite wildfires that rage out of control. “I feel there is a clock ticking,” he cautioned. “It’s imperative that everyone stays alert to the dangers and doesn’t let fire get anywhere near the woods.”
Tinder-dry conditions and wind mean the potential for wildfires is greatly increased, and with
temperatures rising after a damp spring Hall says the Met Office’s warning for southern and eastern England must be taken seriously.
He added: “We could be in real bother, even if we have a reasonable amount of rain; if the temperature rises again in July and August the risk of wildfires is greatly increased.
“Wildfires pose serious threats to people, communities, homes and properties. There are grave concerns if you live on the edge of towns. The threat is not restricted to wildlife and green spaces.
“We know at first hand the damage that wildfires can cause. Winter Hill in Lancashire caught fire on 28 June 2018, devastating trees and wildlife habitats at our site Smithills, and it burned until the autumn before it was put out.”
According to UN scientists, 2023 was the hottest year ever recorded globally and heatwaves are becoming more likely and more extreme because of human-induced climate change.
The world has already warmed by about 1.1C since the industrial era began, and temperatures are set to keep rising unless there are big cuts to emissions.
A recent Forestry Commission report showed fire and rescue services attended more than 360,000 wildfire incidents in England over the 12 years from 2009-10 to 2020-21 inclusive –an average of more than 30,000 per year.
Many summer wildfires are started accidentally by lighting fires or disposable barbecues. But one stray spark or an abandoned pile of dying embers can have horrendous consequences for the countryside, destroying wildlife and causing long-lasting damage.
Fire and rescue statistics for 2022 showed there had been almost 1,000 larger-scale wildfires in England and Wales alone – the highest number since records began in 2018.
Rob Stacey, secretary for the England and Wales Wildfire Forum and wildfire team leader and project officer for Northumberland Fire and Rescue Service, said the consequences of wildfires can be “catastrophic”.
“If fires do take hold they can spread incredibly quickly and when it’s dry there is a much greater chance of the fire getting into the ground fuels,” Stacey added.
“Running fires in grass can go faster than a firefighter can run.
The Forest Stewardship Council (FSC) proudly announces the release of its flagship publication, Forest Futures. This pivotal work
conservation, and sustainable use. Leveraging these drivers, the three distinct trajectories were outlined and mapped out. These drivers are (1) Forests & Planet, (2) People, (3) Economy & Markets, and (4) Governance. These trajectories, developed through an innovative
Tubex showcased its full portfolio of tree protection solutions – including recyclable and biodegradable shelters – at KWF 2024 in Schwarzenborn, Hesse, Germany.
The Tubex Nature range are ideal for use in locations where collection and recycling is not feasible. The new, expanded selection now offers ventilated Tubex Ventex alongside Easywrap, Shrub Shelters and Vole Guard shelter styles to meet a broad variety of demands, industry requirements and applications.
Tubex’s biodegradable shelters are manufactured using a bio-based blend, including sugarcane, corn and starch. This means these shelters can be left to biodegrade in situ and will, over time, start to degrade and breakdown into water and CO2 through a microbiological process.
Last year, Tubex worked with Wageningen University to independently test the material used for Tubex Nature in order to find the most suitable formulation that achieves a balance between long-term protection and effective biodegradation. The findings of this project have since
been used to optimise the performance of Tubex Nature tree shelters.
There have also been several practical improvements made to its entire Nature range, such as doubling the tube’s resistance to force during zip tie tightening and refining the shelter’s flared rim for enhanced smoothness during installation.
The Tubex Nature biodegradable portfolio sits alongside its array of recyclable shelters made with an average of 35% recycled content, allowing customers to choose the shelter type that is most suitable for their planting circumstances.
Alongside promoting best planting practices, the company also advocated responsible collection and recycling at KWF, emphasising that recyclable shelters that are collected and recycled remain the lowest impact option for any tree that requires individual protection.
Tubex highlighted its Collection and Recycling Programme which is available in Germany and provides an accessible, low-cost solution for forestry, farming, and landscaping professionals looking to recycle their used tree shelters at end-of-life. Created and managed by Tubex
in partnership with RIGK, the recycling scheme enables old tree shelters to be collected on-site at a flat-rate price of €49 per bag. Once collected, used tree shelters are then recycled, ensuring that the recycled polymer is re-used locally to achieve the lowest environmental impact.
Speaking before the show, James Taylor, Commercial Director at Tubex commented “Tubex is delighted to participate in KWF 2024 and showcase our range of shelters to the German market. We eagerly anticipate many engaging and meaningful discussions with forestry
ew Cat® Grading Beams for Cat Tiltrotators
Skogforsk has conducted a literature study on the environmental effects of land preparation on mineral soil. The results based on studies in Sweden and Finland are summarized here.
The purpose of soil preparation is to improve the conditions for survival and growth of plants during regeneration (see also the knowledge article Soil preparation improves survival and initial growth ). The basic principle is to remove the surface organic soil layer (soil and humus) and expose the mineral soil underneath, sometimes making a pile of mineral soil, or mixing organic material and mineral soil. This can affect soil erosion, decomposition of organic matter, nutrient turnover and leaching, as well as the vegetation and its uptake of nutrients and water. In a new literature study from Skogforsk, the environmental effects of land preparation on mineral soil are reported based on studies in Sweden and Finland. The literature study includes roughly 40 scientific articles from studies in Sweden and Finland (approx. 50 experimental areas). Also included are some inventory studies. Harrowing and plowing were the methods investigated in most studies. Here are summarized the conclusions from the study (“ Environmental
impact of mechanical site preparation on mineral soils in Sweden and Finland — a review “) which is published in Silva Fennica.
In Sweden and Finland, significant areas of forest land are cleared annually, on average 140,000 (most harrowing) and 100,000 hectares (most piling) respectively during the 2010s. An important conclusion from the study is that despite the scope of the measure, the number of studies studies are few and the knowledge is limited. It is therefore difficult to draw far-reaching general conclusions about how land preparation affects various environmental factors. However, how the carbon dioxide exit from the ground is affected initially has been investigated at 18 premises.
An important conclusion is that today’s land preparation generally results in an unjustified large impact on the land in relation to what is required to create favourable conditions for regeneration. Therefore, methods and aggregates need to be better adapted to the actual needs.
Soil preparation generally has a favorable effect on regeneration and early stock development ( Soil preparation improves survival and initial growth ) and increases the storage of carbon in the young stock. The breakdown of “fresh” organic material (ie needles) under harrow tilts and piles seems to increase over a few years. When the emission of carbon dioxide, from the different soil environments that harrowing and stacking lead to, was weighed together, however, no increased carbon dioxide emission was demonstrated during the first two years. Land preparation thus appears to contribute to increased carbon
organic material changes, the soil water chemistry and the leaching of substances can be affected. Higher levels of certain substances, such as nitrate and ammonium, have been measured in soil water collected under piles and harrow tilts compared to under furrows and in undisturbed
vegetation and the effect can be long-lasting, probably longer than the 10–20 years documented in studies.
It is difficult to draw general conclusions about how land preparation affects the occurrence and degree of coverage of different ground vegetation species because it depends on the original species composition, the intensity of land preparation and how quickly different species are established. However, a common effect
With the help of a drone equipped with its own portable mobile base station, a forest machine has, for the first time, been remotely controlled via 5G in an area with limited connectivity. The test was carried out in a forest outside Västerås, central Sweden, as part of a research project involving Mittuniversitetet, Telia, Ericsson, Skogforsk, SCA, Volvo CE and Biometria, co-funded by Vinnova and the program for Advanced Digitalization.
The project aims to investigate how drone technology and 5G technology could enable remote areas around Sweden to be worked with remote-controlled vehicles.
The project group passed a milestone in November 2021 when it was able to remotely control a timber loader at SCA’s Torsboda timber terminal outside Timrå in northern Sweden. After this success, the group set itself the challenge of using a drone equipped with its own portable mobile base station to extend 5G network coverage to an area where there would otherwise be none and to use that temporary connectivity to enable a forest machine to be remotely controlled.
At the beginning of May, successful tests were carried out in a forest in Virsbo outside Västerås.
After a basic technical briefing, the forest machine, a forwarder, was transported to a clearcutting site where it was connected using 5G technology mounted on a drone. During the test, the drone was approximately 500 meters from the forest machine but created a coverage area extending up to 3 kilometres. The driver of the forestry machine was in Skogforsk’s remote control lab in Uppsala, roughly 90 kilometres away.
For SCA, testing and developing this technology are crucial and something they have requested in dialogue with Telia.
“We need to find out how we can improve local coverage in areas where we currently don’t have access to existing networks. The ongoing shutdown of 2G and 3G networks makes this development even more important,”
Leonhardt, Head of Strategy and Innovation for Telia Sweden’s B2B business. The demand for secure communication to and from forestry machines with
accurate positioning has steadily increased over time, and we are moving more towards real-time data. Since we constantly move forestry machines, a mobile solution to enhance coverage is a good approach.
In the test conducted in Västerås, they chose to remotely control a forwarder to test the connection via a drone. The next step, is to test connecting and remotely controlling a soil scarification machine, which is much heavier and operates in inaccessible terrain. The goal is to improve the working environment for drivers, and soil scarification drivers, in particular those who operate in very tough environments.
Sam Launchbury is the founder and CEO of SDL Solutions, an innovative and forward-thinking forestry business and wood pellet manufacturer. Driven by sustainability, the company take their environmental responsibilities seriously.
In recent years, I have heard nothing but positive comments regarding SDL Solutions, so I was delighted when forestry manager Kevin Mitchell suggested visiting one of their harvesting teams, working on a steep and challenging site in Derbyshire.
I first went to the companies head office down in the Cotswolds and met Marketing manager Paul Williamson and Izzy Harris, Marketing Coordinator, before being taken on the short journey to their biomass powered, wood pellet manufacturing plant. On arrival at the plant, I met Sam
Launchbury who explained how SDL Solutions came to be. Sam started out on his own at the turn of the century and was initially carrying out clearance work and fencing for a local steam railway and other landowners whilst moving into civils “The company was started using a credit card with a very meagre credit limit” Sam explained with a smile.
Sam built up a solid reputation amongst his clients as he continued to work on his own for several years. His workload increased significantly so he began to recruit more staff to keep up with demand. In 2008 he diversified into larger tree clearances and became one of the first companies in the UK to operate a mechanical tree shear.
Sam is a true renewable energy pioneer and not frightened of embracing modern technology. In 2009 he began the installation of one of the UK’s first 100% renewable energy anerobic digesters. His experience in civil groundworks and meticulous planning skills were called upon with this project. Thanks to his dedicated team, a leading European Supplier and the private estate where the digester is housed, it was up and running eighteen months later.
Initially the digester was to run on agricultural feedstock, but it has since been converted so that it can use an alternative sustainable energy source. This is now fed by food waste and SDL installed a food waste reception hall to feed the
existing system.
The digester works by mixing organic waste with hungry microorganisms in a large silo allowing nature to intervene. The microorganisms digest the organic material and produce biogas (mostly methane gas) which is burned in generators to produce electricity. A transformer and substation
connect it to the national grid.
Whilst finishing the works at the AD Plant SDL continued to carry out site clearance work and were asked to clear a large area for the construction of a new road at the heads of the valley. To carry out this work SDL purchased a Jenz HEM561 to accompany the 360 excavator and shear. During this contract SDL produced 1000’s of tons of woodchip and so the process in finding a useful home for the material started. SDL started to supply a converted coal power station and newly installed biomass woodchip systems, that were being installed during the uptake of the RHI scheme. It became apparent that there were different specifications needed depending on the size of the boiler installation and that screening the product and drying where necessary. This would enable all the site clearance material processed to be utilised for maximum return. SDL ceased contract civil engineering and focused on its own development installing two 1mw boilers linked to a drying system. The boilers were able to burn a lower grade of fuel from the site clearance which
enabled the screened, more premium product to be dried and sold.
Whilst SDL continued to grow and carry out more site clearance, a lot more lower grade material was available and rather than sell to the larger power stations coming online (that paid very little), the opportunity was there to build a CHP Plant (Combined Heat and Power). The thought behind this was to enable SDL to produce its own electricity which would then give opportunities for further manufacturing/ processing with cheap electricity. Sam applied for planning in early 2016, following his submission visiting multiple CHP Plants and sawmills across Europe and settled on a supplier for the CHP unit and drying unit. Sam negotiated and purchased the equipment and started installation in October 2016 completing the install with its G59 grid connection on March 27th 2017. Only one to two engineers from the main suppliers helped SDL’s staff to complete the entire installation.
Having commissioned the CHP plant, Sam could see others joining the woodchip supply market and causing prices to drop to unsustainable levels. With this in mind, Sam took another bold step later in 2017 when he built a wood pellet production plant right next to the biomass boiler, utilising the heat and power from the CHP plant to produce EN Plus A1 wood pellets - the highest quality available and all
manufactured from sustainable local timber.
You can’t help but be in awe of Sam as not only had he brought his vision to life, but he designed the layout of this amazing facility himself and constructed it with his own skilled workforce.
The biomass plant and pellet line sit side by side. The biomass plant uses wholetree, lop and top and poorer quality timber to produce heat and electricity. The sawmill bi product and better-quality chip wood is used to manufacture the wood pellets next door. It is an impressive set up. The woodchipper, was working flat out in the yard making short work of the large stack of chip wood destined for manufacturing wood pellets.
The plant runs all year round and is only shut down for two weeks each year to conduct servicing and maintenance. I confess to not fully understanding the ins and outs of plants like these, but it was easy to see how effective and productive it is. The fact that it only needs a handful of operators to keep it running smoothly is all down to the articulate planning, design and layout that took place prior to construction.
The biomass plant and pallet line are situated on a very a large site with plenty of room for expansion and I would imagine there will be much
more to come.
SDL employs around 150 people in total. Up to four squads work on roadside/site clearances. SDL conducts a lot of site clearance and roadside work nationwide, removing Ash trees suffering from Dieback. Even with this type of work Sam has a unique approach. Although all of the trees will eventually die, instead of clearing them all away, initially only the unsafe or unstable ones are removed. By working this way, young natural regeneration trees can establish themselves. A young crop will be coming through by the time the last of the diseased Ash trees are removed. This improves the aesthetic impact as the roadside has continuous cover and never looks like a bomb site after a total clearance.
It is astounding what Sam has achieved in such a brief time span. In 2023 he took another brave step and purchased one of the last remaining sawmills in South Wales. The mill was destined to be closed, but having purchased sawmill residue for many years, Sam made an offer which was accepted. Staff were thrilled that the business was to continue under new ownership and committed their future to Sam and SDL solutions.
SDL Solutions are a completely self-sufficient company with sustainability at its heart. Nothing is wasted as they use every part of the standing timber they purchase. Even
the brash mats from their harvesting sites are extracted and chipped to fuel their biomass boilers.
SDL are very well equipped with machinery and have their own fleet of HGV’s Lorry’s with walking floor, timber, low loader, and bulk tipping trailers for transporting round wood, sawn timber, wood pellets, woodchips, and equipment. Other equipment includes their powerful self-propelled Albach Diamant 2000 which is used for on and off-site chipping, various McClosky Trommel three-way screeners, excavator Magni and Liebherr machines equipped with various Westtech tree shears, Fendt 828 tractors with various attachments, two wheeled based harvesters, one track based, four forwarders, skyline and winch.
Sam understands that to be a good leader you must be able to translate your vision into a reality and he has done this by putting experienced and skilled leaders in key positions throughout the company. When Sam takes on a new project, he makes sure he has the right people in place to look after the day to day running of their departments. He has invested heavily in making sure that operatives are fully trained and multi-skilled so they can cover other assignments if required, and he makes sure that they are well looked after.
The following day I met up with harvesting manager Kevin
Mitchell at a steep and challenging site being harvesting in Derbyshire. The diseased larch trees along with some Sitka Spruce were being taken out. It was mostly a clear fell, but there were smaller areas where it was more of a mixed crop and the Larch was being removed by thinning. 12,000m³ was being harvested and the average tree had a volume of 1.1m³.
Driving down to the parking area I was surprised by the lack of timber at roadside, I would have expected to see over a thousand of tonnes of timber stacked at roadside considering there was two harvesting teams working there. I asked Kevin about the lack of stacked timber, there was less than one hundred tonne in the landing, and he explained that none of their sites ever had large timber stocks.
“As soon as wood hits the stacking area its straight off to our sawmill or biomass plant. Landowners are delighted as the wood is never left stacked up to dry out, many are realising that they are getting much more value from their wood from SDL Solutions.”
A Komatsu 875 forwarder was being unloaded by operator Heffyn Owen at the stacking area and a Komatsu 931 harvester was nearby which was being serviced by operator Craig Ferguson.
It was quite a walk to where the timber was being harvested as
they were working the site in accordance with the weather conditions. The forest road, which was thatched up for the extraction route, cut through the middle of the steep site and as it was dry they were working at the furthest most point.
Two very fit young chainsaw operators, Connor Harris, and Jacob Peters manually felled the trees, and I did not envy them in the slightest as it was a very steep site. The trees were felled and left unbrashed so that they could be processed mechanically next to the extraction track. A much safer way to work as de-limbing trees on steep slopes can put chainsaw operators’ safety at risk.
The full trees were being extracted by a Doosan DX 300LC which had been converted to a skyline in a joint venture by Baden Powell Ltd and Toby J Hyde Ltd. The trees were extracted uphill away from a main watercourse using a TST Carriage.
Aaron and Alfie Pond were chockering for the skyline at the bottom of the hill and Finlay operated the skyline. It was not an exceptionally large extraction distance, around 200m so it was not long before the trees began piling up, making unhitching the chockers a bit awkward. Craig finished servicing the Komatsu 931 and was kept busy processing the timber. Due to the exceptionally long extraction distance, a Komatsu 840, operated by Robert Cowie,
assisted the Komatsu 875 forwarder.
With the speed of the skyline extracting the timber I thought they would soon run out of trees and would need to relocate the machine and cables frequently, I assumed that this would slow down production. Kevin assured me they had it down to a fine art and could move the excavator and cables and be back up and running in less than an hour. Although this was not the easiest of harvesting sites, the team produced an average of 700m³ to roadside each week.
The quality of the work being conducted was first class and there was no water issues anywhere, the on-site excavator was mostly used for preventative measures. I observed areas where the harvesting had been completed and it was left in an immaculate
8 - 15 t 54 cm
TECHNICAL FEATURES:
• Powerful gripper
• Automatic chain tensioner
• Endlessly rotatable Tiltator
• Spring-mounted saw box
APPLICATION AREAS:
• Safe removal of trees in several parts.
• Maintenance work along traffic roads and routes.
• Felling of dangerous trees.
• Quick processing of fallen trees.
what was expected of them and they worked perfectly in unison as a team. Kevin pointed out that SDL also had another harvesting squad working in Wales. Carl Osborne operates the John Deere 1270G harvester and his son Jack extracts behind him on a John Deere 1510G.
We drove around to the other
My name is Gary Roberts and I have lived in the great border city of Carlisle for 60 years, I work in the Lake District, Southern Scotland and Yorkshire.
My first job was in farming where I attended Newton Rigg College. This was a great job but not enough money when you have just bought your first home and a child on the way. I got a job offer for a timber
truck for a company in Longtown, Cumbria. While there I was involved in the clear up from the great storm in 1987.
Following this I was offered a job with Sheffield & Co who are now a wholly owned subsidiary of Euroforest. Since Euroforest took the business over we have gone from strength to strength and we have seen massive investment and support in the business which has resulted in the
fleet expanding and we now have wagons stationed at our base in Nairn and also some in South West Scotland. This supports our own harvesting activities and also helps
work. It is a job I love.
I currently drive a Scania 540 and drag with Kesla double telly crane, 44-ton gross. These are changed every 4 years.
I want to continue in timber haulage as long as I can. I would like to see more younger people come into the industry as most of us are now in our 50’s and 60’s. Not a lot of
young people seem interested in doing the job but they are missing a trick, it’s a great life and we are now looking for young drivers and we will invest in training for them as we see them as the.
I don’t have many hobbies but enjoy caravaning, running Timber Trucks UK on Facebook which I started 10 plus years ago and now has over 8000 members.
Iwould imagine organising a forestry expo during the Euro’s was probably not an easy job. Edinburgh airport was teaming with kilted Scotsmen, along with the distinct wail of bagpipes, as the tartan army made its way over to Cologne for Scotland’s second football match against Switzerland.
Although the airport was choco-block, staff coped admirably. The majority of travellers were in a jubilant mood even if it was taking almost two hours to get through security. Once through the rest of the journey ran reasonably smoothly. After an overnight stay close to Frankfurt airport I met up with colleagues that flew over that morning.
The show ground was about one and a half hours drive from the airport and as we arrived just after lunchtime there was no traffic delays, so we got parked easily. It was a drizzly sort of day with warm, clammy and humid weather. The excitement started to build as we neared the show entrance, and the unmistakable chunking of the large chippers could be heard munching their way through vast quantities of timber.
This show is in a forest setting and many of the exhibitors were situated either side of a forest road which wound its way
around a 5km track. Germany has been experiencing one of the wettest years in history, May alone had 48mm more rainfall than normal, making it the third wettest since 1901. Despite all the rain, the field for parking was relatively clean with no major rutting to be seen. Parking was arranged so that access was at the top of the hill and the exit to the main road at the bottom. There was a middle lane to travel with parking to the left and right, bottom to top. Everyone left enough room to pull out from the car in front, so that the direction of travel was always downhill.
The path leading from the parking area to the Expo was three or four inches deep with woodchips which was just as well as I had only brought trainers with me.
Two entrances and two parking areas with marshals directing traffic from the main road prevented any hold ups. Once through, the atmosphere was really buzzing with machinery noises, loudspeakers blaring away and the chinking of Steins and laughter from the many beer gardens near the entrance. The main area is not exactly a working show as such, there were excursions to nearby forests where a selection of demos were being held, but
seeing the equipment standing proudly in its natural habitat is enough for me.
Demonstrations took place in the main area as well. Westtech Woodcracker had a fantastic display of equipment and their live demonstrations continued throughout each day. Pfanzelt Maschinenbau demonstrated the versatility of their PM Trac forestry tractor and the mini-Moritz tractor, which is best described as a forestry Swiss Army Knife. This clever little tracked machine is such a versatile tool with so many attachments that it make it an invaluable tool for commercial forestry and private estates.
Timber trailers and timber cranes were in use throughout the show. PALFINGER Epsilon had their usual large working area where visitors could try their cranes and controls.
Stihl Timber sports had a huge display area and a stage where visitors could participate and get hands on (and aching shoulders) cutting logs with crosscut saws to a cheering audience. The professionals were holding axe, chainsaws, hot saws and crosscut saw demonstrations throughout each day.
I was there for two and a half days and still didn’t manage to
see everything, there was in excess of five hundred exhibitors covering every aspect of forestry. Equipment with the latest technology for road building/maintaining, fencing, planting, weed suppression, fire control, thinning, final harvesting, wood transport, equipment transport, wood processing, firewood, tree surgery, chipping- you name it, and they had equipment to make the job easier. There was even equipment that you didn’t know existed, but once you had seen, it you knew you needed it lol.
Of all the shows I had ever visited this one is my absolute favourite. The lay out, fantastic atmosphere and amenities are second to none. The toilets throughout the show, although temporary, were proper flush toilets where you didn’t have to hold your nose while using them and were cleaned and emptied regularly. Whenever wet or muddy areas appeared a large loader with woodchip appeared and immediately remedied the problem.
An event like this has been much needed for our German forestry colleagues. Speaking to forestry contractors and equipment manufacturers/ suppliers, the last seven months has been a pretty turbulent time for them. Germany has seen much higher rainfall than usual since the back end of last year, and this has prevented many people from working.
Forestry accounts for around
one third of the land mass in Germany so it is a large industry that employs 1.3 million people (population is eighty-four million so in excess of 1.5%) and accounts for about €170 billion.
Droughts from previous years have weakened around 80% of the spruce trees in Germany and left them vulnerable to beetle attack. Hard frosts used to keep the beetle damage under control, but the damp and warmer weather has allowed the beetle to thrive so many of the trees are now dead. It is sad to see so many dead mature spruce trees in the forest. What is good though is to see the amount of good straight timber that is up and coming from the hardwood forests that Germany has planted. Beach is one of the preferred species, although much slower growing it can withstand climate change and beetle attacks better.
The KWF was a great event and helped to raise peoples spirits. A break away from the stress of every day life can offer a bit of clarity. Everyone in our group from the UK were of the same opinion. Harold Taylor thought it was a well organised show that ran like clockwork from start to finish. George Dunlop and his son Callum were amazed at the selection of equipment on display. When I asked George what the highlight of the trip was, I didn’t quite get the answer I thought. “The show was brilliant, but the best moment for me was when Harold took a wrong turn onto the motorway, forgot what side
of the road we were driving on and shot back up the slip road the wrong way. The oncoming German motorists scattered left and right to avoid a collision and I still laugh now when I recollect their look of sheer terror at the oncoming kamikaze Ford Focus driver.”
Jos Dodd has been to other forestry events in Germany and Sweden but had never seen anything like the scale of the KWF. Michael Johnstone and his son loved everything about it and Michael managed to catch up with people he hadn’t seen in years.
From my point of view, the KWF couldn’t have organised it better, no traffic delays, no queuing to get in and a great mix of equipment throughout. Everything was mixed up together, no dedicated sections.
Stallholders kept us fed and watered, the catering facilities looked good and not overpriced, Draught beer was available throughout the show and being able to get close to equipment without the health and safety police intervening made all the difference. Forestry workers are responsible adults who work in a high risk occupation and it’s great to see that the KWF organisers can rely on visitors good old common sense to prevent accidents.
Maybe other exhibition organisers should visit events like this and learn how to organise and host a great show. www.kwf-tagung.net
As wildfire seasons grow longer and more intense, communities worldwide are seeking effective methods to mitigate these natural disasters. One critical approach to reducing wildfire risk is through strategic and effective land clearing. CBI, a leader in innovative land clearing equipment, offers solutions that not only manage land more efficiently but also contribute significantly to wildfire prevention.
Land clearing involves removing vegetation, underbrush, and other combustible materials from an area. This practice is essential in creating defensible spaces around properties, reducing fuel for fires, and enabling firefighters to protect communities more effectively. Proper land clearing can create firebreaks, which are barriers that prevent the spread of fire, and maintain the health of forests by removing dead or decaying plant matter.
CBI’s range of powerful, reliable equipment is designed to tackle the challenges of land clearing efficiently. Here’s how CBI machinery contributes to
wildfire prevention:
1. High-Efficiency Grinders and Chippers
CBI’s horizontal grinders and industrial wood chippers transform large volumes of brush and trees into manageable mulch. This mulch can be used to create firebreaks or reduce the combustible materials in high-risk areas. The 6800CT Horizontal Grinder, for example, is famous for processing large amounts of wood waste quickly, ensuring that fire-prone areas are cleared efficiently.
2. Durable and Powerful Mulchers
Mulchers like the CBI 5400BT can handle thick vegetation and trees, turning them into fine mulch. This not only clears the land but also helps in soil stabilization and erosion control, further reducing the risk of wildfires spreading through dry, loose soil.
1. Reduced Fire Risk
By removing excess vegetation and dead plant matter, effective land clearing minimizes the available fuel for wildfires. This makes it harder for fires to start and spread, protecting homes and ecosystems.
2. Enhanced Firefighter Access
Cleared land provides easier access for firefighting equipment and personnel. This can be crucial in containing and extinguishing fires before they reach populated areas.
3. Improved Ecosystem Health
Regular clearing of underbrush and dead trees promotes the growth of healthier plants and reduces the likelihood of disease outbreaks. Healthy forests are less susceptible to devastating wildfires.
4. Economic Savings
Preventing wildfires through proactive land clearing can save millions in potential firefighting costs and property damage. It also protects valuable timber
site-clearances
Fecon LLC, a leading global manufacturer of heavyduty site preparation attachments and forestry accessories, recently acquired TREEfrogg LLC,a manufacturer of tree trimming saw attachments for skid steers and compact track loaders. The acquisition expands the right-of-way clearing solutions offered by Fecon in the forestry mulching and vegetation management industry. Designed to fit small to midsize carriers, TREEfrogg’s patented tree trimming saws allow landscapers, landowners and DOT’s to perform tree maintenance with machines they already have quickly, safely and economically. Fecon will rebrand the saw attachments as Trim Ex.
“We are excited to add the TREEfrogg trimming saws to the Fecon line,” said Jeff Stanley, Fecon’s senior vice president of product development. “This addition expands the offering to our agricultural, rural and dot customers, giving them a productivity enhancing solution for selective tree trimming.”
The innovative attachments offer the ideal solution for tackling overhanging tree limbs and other vegetation along easements, right-of-ways, roads, fence rows, paths and other applications. Cutting faster than a chainsaw bar, the Trim Ex 26S saw attachment features a 24-inch carbide-tipped
forestry blade that spins at 3,000 rpm and operates with standard flow machines between 10 gpm to 27 gpm with no high flow needed. The operator hydraulically rotates the saw head from the cab as much as 180 degrees to optimize the cutting angle and increase productivity. The boom telescopes to 18 feet total length, which provides a working height of 26 feet. Combined, the high-speed saw, rotating head and telescoping boom allow the operator to make continuous, clean cuts from one machine position.
By eliminating the need for chainsaws, bucket trucks or otherwise expensive, dedicated machinery, the Trim Ex 26S attachment can reduce the often manual labour of tree trimming to a tenth of its cost. The attachment’s low maintenance is another costsaving factor, as it does not have loose chains or require any bar oil for lubrication. Additionally, no operator components are near the actual cutting apparatus and the assembly allows the operator to trim from a distance safely inside a cab.
A smaller saw attachment, the Trim Ex 18C, can fit on skid steers with a 1,300-pound rated operated capacity. Compact in size, the Trim Ex 18C takes up as little as four inches on the front of an equipment trailer and the boom can be straight, offset to
the machine side or folded for transport. The tree trimmer requires 10 gpm auxiliary flow and has a 10-foot forward reach with an 18-foot working height. Fecon also partnered with the founder of TREEfrogg to develop and design a dialectric saw attachment, the Trim Ex 26D, which offers added safety when trimming trees around power lines. It is also lighter in weight than the 26S model.
For over thirty years, Fecon has produced more than 25,000 mulcher heads with a presence in every continent. The acquisition of the TREEfrogg saw attachments complements Fecon’s current line of mulching attachments and extends Fecon’s reputation as a leader in the forestry mulching and vegetation management
European softwood production declined by 6.4% in 2023 to 80,894,000m³ (2022: 86,518,000m³) with a further slight drop expected in 2024, according to the European Organisation of the Sawmilling Industry (EOS).
The forecast for 2024 is 79,459.000m³, which if accurate will be the lowest production output for EOS countries for about nine years. But the EOS says there is hope in the industry that the market will bottom out this year.
James Jones & Sons Ltd is proud to announce the 25 year anniversary of its Timber Systems Division based in Forres.
The Timber Systems Division was launched 25 years ago as the UK’s first I-Joist production line and has since grown to become the UK’s largest manufacturer of certified I-Joists, branded as JJI-Joists. Today JJI-Joists have a 40% share of the UK’s I-Joist market and are used by every major UK house-builder in addition to supplying customers across Europe, Australia and New Zealand.
Tom Bruce-Jones, Chairman of requirements.”
James Jones & Sons Ltd, said “This is a major milestone for the Timber Systems Divisionand the extensive programmes of capital expenditure and innovation. Since its inception we have produced well in excess of 100 million lineal metres of JJI-Joists, and stored over 455 thousand tonnes of embedded carbon in approximately 1 million new homes. In recent years developments have included £8.5 million investment into the commissioning of a new world leading I-Joist production line, a stock yard extension and the addition of JJI-Wall stud to our EWP portfolio to help housebuilders meet new Part L building regulation
Angus Macfarlane, General Manager of Timber Systems Division added “We are delighted to celebrate our anniversary and it is testament to the hard work and dedication of our team over the past 25 years. Many employees that started with us in the beginning are still with us today and will have witnessed a great deal of change and progression in that time. To mark the occasion, all employees signed a JJI-Joist that was produced on the day of the anniversary and it will be displayed inside the building.”
www.jamesjones.co.uk
POSCH’s revolutionary new circular saw blade sets a new benchmark in firewood processing. Its name is the game: It’s called “purr” and
idle, it emits 72 dB(A) instead of 92 dB(A)* as before.
The “purr” saw blade is produced in Germany and is now installed as standard in all POSCH tilting saws and tilting saws with conveyor belts. Of course, this
New X-ray technology at Norra Timber’s sawmills in Sävar and Kåge will be able to identify the internal properties of logs, such as knots and other imperfections.
The sawmill in Sävar bought its first X-ray equipment back in 2017, which led to an increase in production of 6,000 cubic meters of timber planks a year - equivalent to 100 fullyloaded truck trailers. Now Norra Timber has bought even more advanced equipment, which it hopes will lead to an additional increase in profits. In addition to providing information on how the logs should be turned to produce more planks, the new equipment utilizes AI to provide information on the quality of the log and the type of products that different parts of the log are most suited for.
“The equipment produces X-rays just like in a hospital. The difference is that scanning is faster. Each log only takes two seconds to process”, says Norra Timber’s Industry Manager, Henrik Jönsson.
Norra Timber is investing a total of SEK 400 million in the new equipment being installed at its sawmills in Sävar and Kåge in northern Sweden. The new X-ray technology, which should be completely operational by the autumn of 2025, will be
utilized at the very beginning of the production process. As trucks arrive with the logs, each log will be scanned to calculate dimensions and provide an overview of the log’s internal properties.
“By scanning the logs from the outset we can sort them according to their quality and unique internal properties. If a customer wants high-quality planks for furniture without knots that are suitable for undergoing the special drying process required, we can identify which logs would be best before we even start sawing them”, says Henrik Jönsson.
He adds: “Thanks to the X-rays we can also calculate the optimal number of planks we can generate from each log, which reduces wastage. We can therefore extract the maximum value from each log. A log with a large branch can be turned with the help of the X-ray machine so that the branch only ends up on one plank and the next plank is free of imperfections. Logs account for 75 percent of our costs, so we want to get as much value from them as possible”.
The primary purpose of the investment is to be able to assign production data to each individual log. In the future each log can also be marked with a
Henrik Jönsson, Industry Manager Norra Timber
unique ID number - a kind of ‘log fingerprint’.
“The ability to trace our products and get data about the timber’s environmental impact will give us a competitive advantage. It will also be a driving force in how we can improve our environmental credentials”, says Henrik Jönsson, who concludes: “By mapping each plank we can easily go back and see if something has gone wrong during the production process. We can also see how much energy was used for each product, which gives us much better control over costs and our environmental impact”.
This latest investment will ensure Norra Timber’s sawmills continue to be at the technological forefront of its industry and remain competitive in the years to come.
www.norratimber.com
Norra Timber is investing heavily in its sawmill in Kåge. A brand new 300 meter-long log sorting facility is now up and running, while a new CT scanner providing full reconstructions of the internal features of every log has recently been installed and is undergoing testing.
“Being able to look at every log with a computer tomography scanner and follow each one through the entire sawing process means we can maximize our revenue and get the absolute most out of our raw
forest material”, says Joakim Larsson, who is the Sawmill Manager at Kåge.
Kåge Sawmill is a modern plant that is constantly developing and improving the efficiency of its operations. The sawmill is specialized in the production of high-quality spruce and pine products. Recent investments mean all logs can now be scanned and 100 percent of the raw forest material utilized.
“We now use 100 percent of the logs, as any residual products from sawing them are also put
to good use. Bark, chips and sawdust are used as biofuel and heating by the sawmill, while any surplus is sent to the nearby district heating network”, says Joakim Larsson.
He adds: “The timing of this investment couldn’t be more perfect. Because our products last for hundreds of years we can now maximize our revenues knowing that the more timber products we produce, the more we help the green transition. Just look at Bonnstan church village in Skellefteå and Lövånger church village. Both were built out of wood in the 17th century and are still in great condition even today”.
Norra Timber Industry Manager Henrik Jönsson is very happy the technology investments are now in place.“The expansion of the new timber sorting facility represents a decisive technological advance for us at Norra Timber. We can now optimize our process and ensure the highest quality of our products thanks to our ability to trace every log”, he says.
A reconstruction of the grading mill intake has also been completed at Kåge Sawmill, which has increased capacity by as much as 10 percent.
This year, DAF Trucks is celebrating 75 years of truck-building. A milestone in a long line of highlights driven by innovation, revolutionary technologies and smart design. These same building blocks form the fundament for the newest generation of DAF trucks that, like their predecessors in their time, have set the benchmark with regard to efficiency, safety and driver comfort.
The foundations for DAF were lain in 1928. In the first years, the company was known in Eindhoven as ‘Van Doorne’s Machine Factory’. When Hub and Wim introduced trailers to the market in the early 1930s, the first contours of DAF as we know it started to become visible. Unlike other vehicles on the market, the chassis were not rivetted but welded, making them a lot lighter than usual, and they were an enormous success. The machine factory switched its focus and became Van Doorne’s Aanhangwagenfabriek or DAF for short.
DAF began to shift quickly through the gears when the demand for transport grew explosively during the rebuilding of Europe. A production line for trailers and semi-trailers was set up and definite plans were made for the construction of a
truck factory. In 1949, the A30 was launched. A 3-tonne truck aimed primarily at the domestic market. The grill featured seven characteristic chrome stripes.
A few months later, the first model was rolled out of the factory and it was quickly followed by the A50 (5-tonne) and the A60 (6-tonne) for heavyduty work. A delivery truck – the 1-tonne A10 – first saw the light of day in 1950, with a spinoff pick-up model – the A107 ¬– following later. The number of models increased rapidly, including vehicles with a special chassis for tipper and garbage trucks and a series of military vehicles. Within a short space of time, DAF had developed into a truck brand that would become an unmistakable part of the scenery.
At the time, all of the trucks were rolled off the line as a chassis with engine and grill. The building of cabs was still in the hands of body builders. This all changed in 1953 when DAF began to manufacture its own cabs. In 1955, the factory celebrated the production of its 10,000th chassis – an occasion that was made extra special thanks to an order from the Dutch Army for 3,600 vehicles. Shortly afterwards, DAF also began developing and building its own (diesel) engines. DAF would become the first to
add a turbo compressor to its trucks’ power source for extra horsepower and greater efficiency.
In 1957, DAF presented the DO, a truck with a characteristic design and a 10-tonne rear axle developed specially for this series. It made the DO particularly suitable for heavy and international transport, which was gradually becoming more popular. The second generation of the DO even featured a rudimentary bed – a novelty at the time.
At the start of the 60s, the Dutch truck builder surprised everyone again, this time with the DAF 2600, a truck that was aimed even more directly at international transport than the DO. The cab was revolutionary. Its square shape maximised the living space – and comfort – for the driver, who was sometimes away from home for weeks at a time. The cab had room for a bed and even a bunkbed if required. The large windows provided plenty of light and an unparalleled all-round view, which improved safety. The 2600 series became known as ‘the mother of international transport’.
In 1970, DAF launched the F1600 – F2200 series. The
vehicles featured a tilt cab, making DAF one of the first to introduce it. The advantages of the tilt cab were huge. It made it easier for mechanics to carry out maintenance, and better and faster too, and offered the driver a much quieter work space because the engine was encased in the cab.
The revolutionary 2600 made way in 1973 for the completely new 2800 (and later the 3300 and 3600). The 2800 had not one but two beds and, thanks to the incredible comfort, it became the number one truck for long distances. DAF was also the first manufacturer to launch the turbo intercooler for more torque, more power and lower fuel consumption.
In the 1980s, DAF gave long distance transport and heavy transport a new impulse with the introduction of the DAF 95, which could also be fitted with an extra high roof for unrivalled driver comfort: the SpaceCab. It was even followed by a Super SpaceCab, the ultimate in space and luxury. For regional and national transport, DAF introduced the DAF 65/75/85.
In the following years, this series of vehicles – and their successors, the CF and XF –made a name for themselves in Europe and also became increasingly popular further afield. The same applied to the new LF series, which was launched around the turn of the
century and was aimed at regional and local distribution. In 2010, DAF was the first to introduce a hybrid truck to the market. The LF Hybrid reduced fuel consumption and CO2 emissions by 20 per cent, thanks to the use of an electric motor in urban areas. The LF Hybrid exemplified DAF’s number one position with regard to making road transport more sustainable, a position that was further underlined by the introduction in 2018 of the DAF CF Electric, the first fully electric truck to be built by a European manufacturer.
During these years, the European Union had been drawing up new regulations for the weights and dimensions of trucks. When these came into force at the end of 2020, DAF was the first truck manufacturer to be ready to work with them. This made the New Generation DAF trucks that were launched in 2021 as revolutionary as the famous DO, 2600, 2800 and XF had been in their time.
The regulations offer truck manufacturers the opportunity to make their cabs slightly longer, provided the extra length is to the benefit of the environment, the safety of the vehicle and the man or woman behind the wheel. The New Generation DAF trucks offer considerably more space to the driver, are significantly more efficient, thanks to their streamlined design, and with their extremely low windscreen belt lines and intelligent camera
systems are built to maximise safety on the road. DAF’s XF, XG and XG+ for heavy-duty work and long distance transport and the XD series (for national and regional distribution) won the ‘International Truck of the Year Award’ twice in a row.
The XD and XF are also available with a fully electric powertrain and have a range of up to 500 emission-free kilometres on a single charge. The XD and XF Electric are built in the Electric Truck Assembly Line, a completely new production line that went into operation in 2023 at the DAF factory in Eindhoven. DAF has also introduced a fully electric version for urban distribution – the New Generation DAF XB – which is being manufactured by Leyland Trucks in Great Britain.
DAF is fully prepared for the future. Not only thanks to its
trucks were built last year. DAF’s customers rely not only on the dependability of its trucks but also on the extensive portfolio of supporting services – from its international recovery service, first-class parts supply and financial services to fast chargers for electric trucks and even the installation of
Renault Trucks have been touring Europe for the first time with a unique 100% electric truck. This vehicle, a Renault Trucks E-Tech T called “Diamond Echo”, features a unique electroluminescent design, and set off in April from the Bourg-en-Bresse plant where it was manufactured. By the time the tour ends in July, it will have travelled more than 10,000 kilometres across 7 countries, making over 60 stops to meet the transport community and demonstrate
the operational reality of electric mobility.
The Renault Trucks E-Tech T Diamond Echo is painted with light. The result of a collaboration with drivers and design and paint specialists, this exceptional truck reveals itself in the dark. Based on Lumilor technology, the paint, applied by Demon Paint, glows when subjected to an electrical stimulus.
Committed to an energy
transformation based primarily on electric mobility, Renault Trucks offers a complete range of 100% electric vehicles, from 650 kg e-cargo bikes to 44 t tractors and urban construction trucks.
Renault Trucks is part of the Volvo Group, one of the world’s leading manufacturers of trucks, buses, construction equipment and industrial and marine engines. The group also provides complete financing and service solutions.
The new Volvo FH16 is Europe’s most powerful truck but also a very fuel efficient one – and it can run on 100% renewable fuels. On-road tests confirm that the all-new engine in the FH16 achieves 5% better fuel economy and lower emissions while adding 7% more torque - a combination that increases efficiency and productivity for the most demanding transport tasks.
Volvo’s all-new D17 engine in the iconic Volvo FH16 has been engineered for the toughest transport assignments to deliver outstanding performance and durability. Comparing the new 17-litre 780 hp Volvo FH16 with its predecessor, the new truck adds 7% torque while achieving 5%* less fuel consumption and carbon dioxide emissions.
The all-new engine is also available in the new Volvo FH16 Aero, offering even better fuel economy when it is combined with the aerodynamic truck cab.
“Our engineers have delivered an engine that combines the highest torque and power level in any European truck, with superior fuel efficiency. The facts speak for themselves –more torque and power with significant fuel and CO2 savings is a fantastic result. This means that our customers can carry out their assignments more
efficiently and with higher productivity”, says Jan Hjelmgren, Head of Product Management and Quality at Volvo Trucks.
This all-new fuel-efficient engine is one example of Volvo Trucks’ continuous strive to reduce fuel consumption and carbon emissions from existing driveline technologies, in parallel to introducing new technologies.
Volvo’s new 17-litre Euro 6 engine comes with three power levels; 600 hp, 700 hp and 780 hp. Torque levels have been increased to 3000 Nm, 3400 Nm and 3800 Nm in the top version. The gearbox has been updated to handle up to 3800 Nm, and internal gearbox efficiency has been further improved on the 3000 Nm and 3400 Nm versions.
The new D17 engine is certified to run on HVO (Hydrotreated Vegetable Oil) in all power ratings. The 700 hp version is also certified to run on 100% biodiesel (B100).
The Volvo FH16 and FH16 Aero with the all-new D17 engine will be available for ordering as from mid-2024 and production will start in the second half of 2024.
*on-road test result D17 780 hp vs D16 750 hp, 55T GCW
Volvo Trucks supplies complete transport solutions for discerning professional customers with its full range of medium- and heavy-duty trucks. Customer support is provided via a global network of dealers with 2,200 service points in about 130 countries. Volvo trucks are assembled in 12 countries across the globe.
In 2023 approximately 145,000 Volvo trucks were delivered worldwide. Volvo Trucks is part of the Volvo Group, one of the world’s leading manufacturers of trucks, buses, construction equipment and marine and industrial engines. The group also provides complete solutions for financing and service. Volvo Trucks’ work is based on the core values of quality, safety and environmental care. www.volvotrucks.com
Cranab is expanding their product range for truck crane customers with a new cooperation. The new partner METSATEK offers solutions of the highest quality in the manufacture and installation of timber truck superstructures.
METSATEK is a leader in the Baltic automotive industry. The company has produced and installed machinery for timber transport since 1993. Since 2007, METSATEK continues dynamic development and implements ambitious projects on a national and international scale.
In April of this year, METSATEK concluded a 1.1 million euro investment project, unveiling the latest equipment for the modernization of the production plant. It includes large-scale paint and shot blasting chambers, a CNC metal bending press and a welding robot.
“All four production facilities open up technically new possibilities in the production process of METSATEK products. This modernization strategy will strengthen the course taken by the company - a convincing leadership position in the production of timber truck and other superstructure solutions in the Baltics, as well as the
expansion of the customer base in Scandinavia. These production improvements are available to our customers today,“ explains Guntis Bukalders, METSATEK Managing Director.
With the welding robot METSATEK can currently perform at least twice as many welding work hours. Ensuring a consistently high precision welding job. Largeskale paint and shot blasting chamber installation allows processing of parts up to 12 meters long, which is a rare availability in Latvia. The technological advantage of the chosen painting chamber is the possibility of dividing it into two separate zones. This means the possibility to carry out two different dyeings at the same time and separately control the temperature to ensure suitable drying conditions.
The shot blasting chamber is probably the only one of its kind in Latvia at the moment. It processes ferrous metal parts with metal shot. This method, in contrast to the usual sandblasting, ensures the preparation of almost perfect quality parts for painting. Additionally, with CNC metal bending press acquisition, METSATEK will strengthen the independence of the production processes. As previously the bending of metal parts was used
as an outsourcing service.
From the total investments, EUR 638,353.99 were invested in the purchase of four new production equipment machines. Additionally, more than EUR 400,000 of METSATEK funds were invested in the reconstruction of buildings and territory. As part of the investment, two new production workshops were built, a wellequipped technical area and increased security conditions of the territory.
The implemented project allows the company to become the most modern automotive manufacturer in the Baltics, to increase the volume of production, to provide
The Penny Hydraulics
Lightweight LoadLift is a safe and cost-effective platform lift for loading toolboxes, white goods or other similar items into vans. Simple to install and simple to operate it can eliminate the manual handling operation associated with loading your van.
Designed to simplify repetitive loading tasks on and off vehicles, a Penny Hydraulics Lightweight LoadLift is the ideal solution for a multitude of business owners and industries.
When considering the right lifting solution, it’s essential to understand the specific needs of your operations. The Lightweight LoadLift is ideal where a van-mounted lift is needed but the payload cannot be jeopardised. Suitable for industries such as logistics, maintenance and healthcare, our Lightweight LoadLift supports loads up to 100kg, ensuring efficient and safe handling of items such as oil drums, tool chests, and components.
LIGHTWEIGHT LOADING PLATFORM CAPACITY AND SIZE CONSIDERATIONS
The capacity and dimensions of our Lightweight LoadLifts are tailored to optimise space and functionality. With a working platform size of 500mm (front to back) x 450mm (flat platformwide) and an 800mm loading height, our Lightweight LoadLift provides ample space for various goods while maintaining a compact footprint. Its lightweight design, weighing approximately 47kg, ensures it doesn’t significantly impact the vehicle’s payload capacity.
Safety is paramount when integrating lifting equipment into your operations. The Lightweight LoadLift is designed with user safety in mind, minimising the risk of manual handling injuries. Its electronically activated mechanism, controlled via remote control, allows for smooth and safe operation, meeting all relevant safety standards and ensuring reliable performance and peace of mind.
The Lightweight LoadLift enhances operational efficiency by allowing for quick and easy loading and unloading of goods. Its foldaway design ensures
it takes up minimal space when not in use, maximising the usable area within the vehicle, and its remotecontrol operation and simple installation make it a practical choice for businesses looking to streamline their loading processes.
Seamlessly integrating into both side door and rear door installations, the Lightweight LoadLift offers flexible loading solutions tailored to your vehicle’s configuration. Its sleek spray black finish ensures it complements the vehicle’s aesthetics while providing durable performance, and its compact design and easy storage capabilities make it an ideal choice for various vehicle types. When you change your vehicle the Lightweight LoadLift can be moved to your new van.
Investing in a Lightweight LoadLift from Penny Hydraulics means choosing a solution that enhances safety, efficiency, and productivity. Designed to meet the diverse needs of modern businesses, our Lightweight LoadLifts integrate seamlessly into your operations, ensuring a reliable and cost-effective lifting solution.
www.pennyhydraulics.com
Proven to offer the best traction with the lowest ground pressure
TXL tracks are also available in extra wide width where machine design allows.
Travis Perkins plc, a TDUK member and distributor of building materials, has fitted its latest batch of electric forklift trucks with what
Group’s forklift truck drivers. The SIVAS sound was selected from the shortlist of three based on its high level of detectability and positive reception by forklift operators,” explained Dr Antonio Torija Martinez, Reader in Acoustical Engineering at the University
Ponsse Elephant Timber Forwarder
Year 2014
9600 Hours ( Very low for its age)
Full service history from Ponsse UK
Last serviced December 2023
Balanced Bogies, One set of tracks
Location County Durham, England
£110,000.00 + Vat o.n.o.
All serious offers considered
Ready to go to work
Telephone 07967 588739
Valtra 6550 tractor
Year 2004
9000 Hours c/w
Botex XL Pro 14 Timber Trailer
Year 2019 and
Botex 570C Timber loader
Year 2019
Takes 2 x 3M lengths of timber
Location Carlisle
Cost £36,000 + Vat o.n.o.
John Deere 1110G Timber
Forwarder
Year 2018
13100 Hours
Intelligent Boom Control
Recent full service ( all oils & filters changed)
Excellent working order - ready to go to work
Location Aberdeenshire