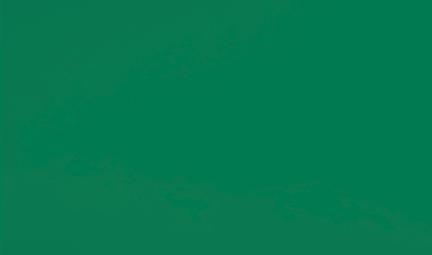
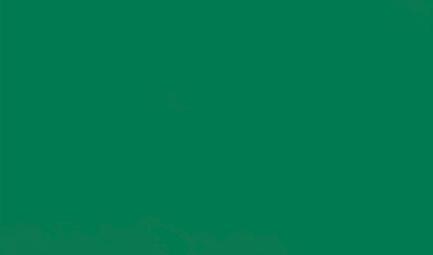
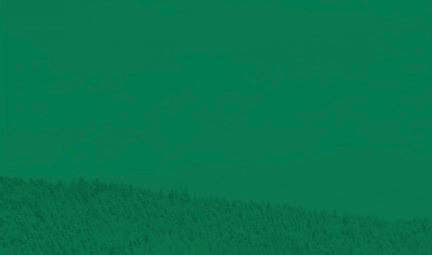
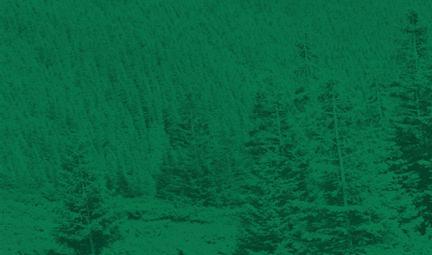
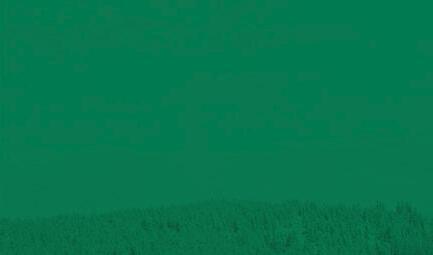
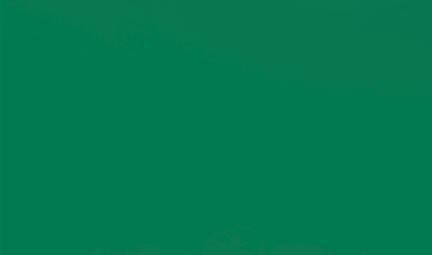
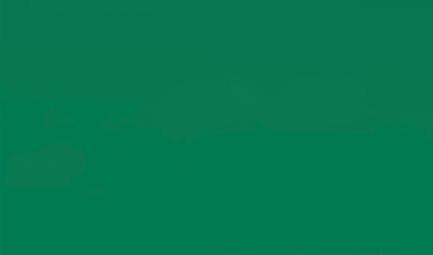
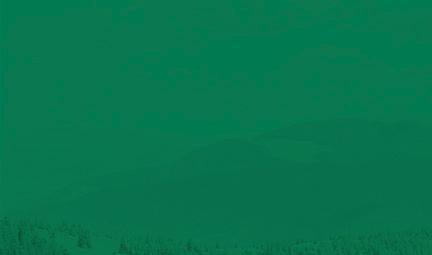
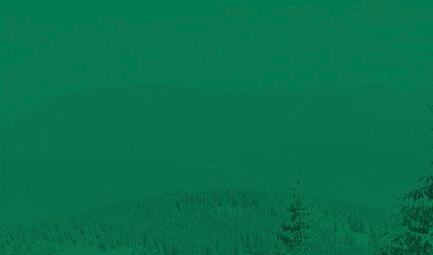
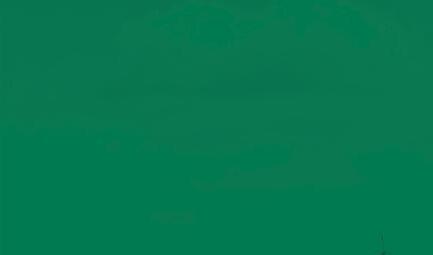
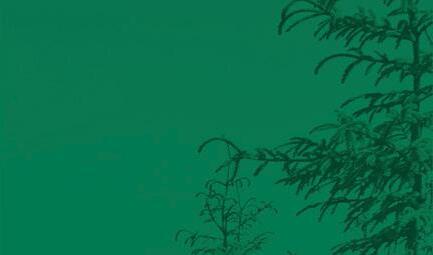
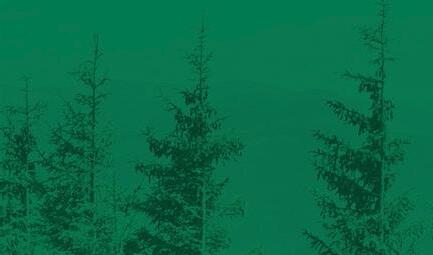
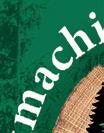

CUTTINGS FROM THE FOREST FLOOR DELIVERED DIRECT TO YOUR DOOR
MAY 2024 + ISSUE 46 + FREE PUBLICATION
READ MORE ABOUT AARON FERGUSON , ON PAGE 48
Winner of a £100 Amazon Voucher
Show season is upon us and I must say I’m looking forward to attending the KWF Tagung in Germany this June. The last event was cancelled due to
Covid, but the one held in 2016 was one of the best forestry showcase events I have ever attended. There’s more on this event inside. Another event for your diary is the DEMO International® taking place outside the Ottawa/Gatineau on September 19-21, 2024. It’s a world-class event for the forestry industry, with plenty of live demonstrations taking place.
I see the new John Deere H series is released, I was expecting to see an eight-wheel 1470H in the line-up but not yet, I hear a whisper though that one might be coming in the near future.
There might be a big change in the balance of forestry equipment coming up sooner rather than later. Some of the large Chinese construction equipment manufacturers are starting to mass produce forestry equipment. This isn’t the old gear of olden days, but modern, automated production facilities that use skilled operatives and good quality components.
You will get the “You won’t catch me operating one of those “comments from operators, but, in reality, if they manage to manufacture a modern, productive, reliable machine with a good network of dealers to back them up then who knows.
Escalating machine prices and unaffordable running costs are unsustainable for contractors, sawmills and forest owners, so if someone came along with a machine that will do the same work but costs less to purchase and run, then I’m sure it would be hard to turn them down.
The Eastern bloc did this successfully decades ago with cheaper agricultural equipment and cars so I see no reason why the Chinese manufacturers can’t do the same in forestry.
Get a regular dose of forestry on our Facebook page. Share your photos and experiences.
Stay in the loop with the latest news from the forest industry. We love to see your photos too!
Subscribe to our YouTube channel to enjoy our dedicated forestry videos.
Burning Issue: Komatsu Forest offer their easily transportable Multibox with foam fire extinguishers
Its Not Easy: Ponsse announces challenging first quarter for 2024.
The Tale Of The Lonesome Elm: The last ent of Affric is no longer alone
Stronger Than Expected: SSAB steel proves to be resilient in a weak market
Deere Do: John Deere launch the H series at press event in Finland
Rock and Roll: Cover competition winner Aaron Ferguson’s Tigercat 822.
Shush: Scania’s 70 tonne electric timber truck.
Remote Control: Alexey Beschastnov looks at future of AI in forestry. Cleaning Up The Forest: New
During hot and dry periods, there is a serious risk of wildfires. Moreover, a single spark can be enough to start one, in which case every second counts. Having fire extinguishing equipment close at hand can make all the difference between a few scorched trees and a fullscale wildfire.
According to the fire service, early intervention is the most important protection against forest fires. With the Multibox, foam extinguishers are close at hand and the chances of quickly extinguishing a fire are greatly increased.
Komatsu’s flexible Multibox is easily transported by a forwarder and can hold ten 9-litre foam fire extinguishers. When wildfire season has passed, the box can be easily emptied and used to store tools, chains, tracks and other items that are handy to have close at hand in the forest.
Komatsu forest machines are equipped with fire
extinguishers, but these are powder extinguishers that are adapted to when the machine catches fire. In the case of wildfires, foam is more effective, as it floats and thus covers a large area. The Multibox is loaded onto the forwarder’s load area using the grapple and the flexible bottom section of the box allows it to fit any forwarder configuration. www.komatsuforest.com
The Scottish Government has confirmed it is ditching a climate change target to reduce emissions by 75% by 2030, but maintains it still intends to meet a 2045 net zero goal.
The move came in response to a report published last month by the independent Climate Change Committee (CCC) that
said Scotland was too far behind meeting the target, making it no longer credible. Professor Piers Forster, interim Chair of the Climate Change Committee said “Scotland has laudable ambitions to decarbonise, but it isn’t enough to set a target; the Government must act. There are risks in all reviewed areas, including those with significant policy powers devolved to the
Scottish Government.”
Scotland missed its annual target for 2021, the eighth time in the past 12 years that they have missed a target. The only sectors to reduce emissions in 2021 were electricity supply and industry. Most key indicators of delivery progress, such as tree planting, peatland restoration rates and heat pump
Opticom Tech, a leader in industrial video monitoring solutions, announced today its new CC04IP5MV3 camera, an upgrade to the CC04-IP3MV camera.
The new CC04 camera offers a higher resolution than its predecessor—5 megapixel compared to 3 MP. It also supports artificial intelligence (AI) functions such as object detection, intrusion detection, line crossing, object counting, and more.
“We’re excited to offer these upgrades to new and existing customers,” said Heidi Schmidt, Global Sales Manager at Opticom. “High-resolution video
installations are off track.
While accepting the CCC’s criticism, McAllan said “With severe budgetary restrictions imposed by the UK Government, and under the continuing constraints of devolution, we are trying to achieve societal and economic transformation with one hand tied behind our back. Such is the UK’s unprecedented economic mismanagement that full delivery of our plans will be contingent on the UK Government reversing the 9 per cent cut to our capital budget.
“Considerable work has been
is vital for operations monitoring and security in industrial facilities. And AI is becoming a reality of our world, so having cameras equipped to support that emerging technology puts facilities ahead of their competition.”
The CC04 camera is NDAA compliant, utilizes the ONVIF protocol and can withstand high-vibration, hazardous and controlled environments. It can also withstand direct hits by logs, boards, rocks, and other objects, making it an ideal video monitoring solution for industrial facilities.
For more information, visit www.OpticomTech.com
undertaken, which brings us nearly halfway to net zero— narrowly missing our most recent annual emissions reduction target, but still decarbonising faster than the UK average. Quite rightly, however, and just as with the UK Government, the CCC challenges us to go further, and that is exactly what we will do. I am announcing a new package of climate action measures, which we will deliver with partners to support Scotland’s just transition to net zero.
“The race to net zero is one that we must all win, and I begin
Founded in 1973, Opticom Tech provides integrated video monitoring solutions for industrial applications, including sawmills, mines, food processing facilities, and more. Built to withstand harsh environments, Opticom’s rugged cameras and equipment stand the test of time. For more information, visit www.opticomtech.com
by affirming the Government’s unwavering commitment to ending our contribution to global emissions by 2045 at the latest, as agreed by Parliament on a cross-party basis.”
FIND US ON
Addressing misconceptions and aligning terminology with the FSC standard in Romania.
Old-growth forests, with their intricate and rich biodiversity found nowhere else, are indispensable to our planet’s health and resilience. Recognizing their importance, the Forest Stewardship Council (FSC) has diligently developed standards aimed at safeguarding these precious ecosystems.
Since FSC first developed the High Conservation Value (HCV) approach in the late 1990s, it has been used to identify and manage outstanding and/or critical environmental and social values in production landscapes, this includes old-growth, rainforest and mature forests.
It is essential to acknowledge the diversity of definitions surrounding old-growth forests as recognized by various formal entities including the European Commission, FAO, UNESCO, Carpathian Convention and others. The term ‘old-growth’ is often misused interchangeably with others such as primary, virgin, and primeval forest. These various definitions lead to different interpretations of how to identify and preserve them.
Moreover, distinguishing
between old-growth forests and managed forests with similar tree age and ecological attributes is crucial. While managed forests can exhibit characteristics similar to old-growth forests, they are designed and managed to support sustainable timber harvesting and economic development.
Restricting logging based solely on tree age, reduces the overall environmental value of managed forests. In Romania, trees can be harvested only after they reach their maturity: 120 years for beech and 140 years for oak. When limiting logging beyond this age, forests will be managed with shorter rotation periods, favouring younger trees for logging – a common practice in other parts of Europe. This prevents forests from reaching their natural structure and age and has detrimental effects on biodiversity and the wealth of ecosystems inside of them.
Starting in 2011, FSC worked closely with WWF Romania to promote the strict protection of old-growth forests (read more about this here and here). This laid the groundwork for significant achievements, culminating in the introduction of the National Forest Stewardship Standard (NFSS) for Romania in 2017. The NFSS
details specific rules and criteria aimed at safeguarding old-growth forests. These measures include provisions for maintaining biodiversity, protecting threatened habitats, and fostering stakeholder engagement. Notably, the NFSS was developed through an inclusive, multistakeholder approach with environmental NGOs actively participating in the process.
As we move forward, it is important to continue this collaborative approach, ensuring that our focus and actions align with the shared goal of preserving old-growth forests for generations to come. Together, we all stand with trees, advocating for their protection and nurturing the rich ecosystems they sustain.
We value the crucial role of NGOs and the media in alerting us to potential violations of the FSC standard in Romania and anywhere else in which FSC operates. While we take all allegations seriously and have established formal channels for receiving information and alerts of wrongdoings, we urge for substantiated claims and scientific rigour to support allegations and avoid unnecessary confusion.
www.fsc.org
Can you improve your energy efficiency when working with your excavator? The answer is yes, in Rototilt’s opinion – by using a tiltrotator. Both because of the way it changes how you perform your tasks, and according to early tests that indicate significant energy savings when using their latest tiltrotator series. “The results are impressive, to say the least,” says Sven-Roger Ekström, Product Manager at Rototilt.
“A tiltrotator makes it easier for you to work with an excavator, thanks to the increased flexibility of the work tool’s movements. It enables you to adjust the angle and rotation of the work tool, which in turn makes it easier to carry out tasks with fewer machine movements. This saves fuel, but it has even more advantages in the long run,” says Product Manager Sven-Roger Ekström.
“We call this the tiltrotator effect,” Ekström explains. “We have always known that there is a big difference between working with and without a tiltrotator. Not only do you need to use fewer machines, but you can also carry out the task at hand with fewer movements and changes of position. This saves both fuel and time, as well as reducing the impact on the ground where you are working.
It therefore has a number of positive environmental effects.”
Tiltrotators provide multiple benefits when it comes to productivity and the environment, however - what is it that makes Rototilt’s tiltrotators unique? According to Ekström, the tiltrotators in the company’s new RC Tiltrotators series can further increase the positive impact thanks to their improved energy efficiency, as a result of Rototilt’s proprietary pressure-compensated hydraulics.
“We have taken measurements comparing our previous series with the new, pressurecompensated hydraulics in the RC4-RC9,” explains Ekström. “The results are impressive, to say the least. We have managed to improve the efficiency of our product, enabling it to perform
the same task with reduced energy consumption.”
The time saved simply by using a tiltrotator, coupled with the energy improvements in RC Tiltrotators, can consequently make a major difference to a project’s efficiency and energy consumption. But what level of fuel saving are we actually talking about?
“Our lab tests indicate a reduction in fuel consumption of between 1-2 litres per hour for a 20-tonne machine, compared to our previous tiltrotator series,” states Sven-Roger. “Out in the field, the savings are affected by a number of factors, such as the type of machine and the job in question. In terms of diesel per year, this could mean savings amounting to thousands of euros.”
www.rototilt.com
President and CEO Juho Nummela:
The first quarter of the year was challenging for Ponsse. A brief market recovery at the beginning of the year faded towards the end of the reporting period. Orders received amounted to EUR 163.5 million and the company’s order book stood at EUR 226.0 (336.9) million at the end of the period.
Our turnover decreased by approximately 16% to EUR 169.7 (201.7) million. Ponsse was significantly affected by the political strikes that took place in Finland at the beginning of the year. Export deliveries of new machines were interrupted by the strikes in March and machine invoicing remained weak. Turnover in service sales remained at a normal level thanks to the relatively good working conditions of our customers. Turnover at Ponsse’s technology company, Epec, also fell due to the general slowdown in machine building. We were pleased to see an increase in our used machine sales, and we were able to deliver used machines to our customers well. The factory operated partly in one shift during the period under review but is returning to two shifts in the second quarter. Our Vieremä factory is running very well and there are no problems with the availability of parts.
Our operating profit was poor in the first quarter and our relative profitability was 0.7 (8.2) percent. The weak operating profit was affected by poor invoicing of new machines and by challenges at Ponsse’s Brazilian subsidiary, Ponsse Latin America Ltda. The fullservice contract that underlies the challenges at our Brazilian subsidiary is moving in the right direction, but patient development work is needed to correct the challenging situation.
Cash flow for the period amounted to EUR 8.5 (2.4) million. In particular, cash flow improved due to an improvement in the turnover of materials and supplies and a slight decrease in the stock of used machines. Some of our capital is still tied up in raw material inventories and in the used machines stock, which increases our working capital. The company’s solvency has remained at a very good level.
The change in Ponsse’s operating model, published on 20 February 2024, is progressing and has been at its most intense at the end of the quarter. The change is important for Ponsse’s long-term development, but at the same time it is hard for the company’s staff. The global organisational structure that will come into force on 1 June 2024 brings new development opportunities for the staff,
improves the efficiency of the group’s operations, and allows the sales and services of our country-organisations to focus more on serving our customers. It is important to Ponsse that this change is promoted respecting the company’s strong values and culture.
Consolidated net sales for the period under review amounted to EUR 169.7 (201.7) million, which is 15.9 per cent less than in the comparison period. International business operations accounted for 71.2 (75.9) per cent of net sales.
Net sales were regionally distributed as follows: Northern Europe 50.4 (42.4) per cent, Central and Southern Europe 19.7 (21.3) per cent, North and South America 27.8 (33.5) per cent and other countries 2.1 (2.8) per cent.
The operating profit amounted to EUR 1.2 (16.6) million. The operating profit equalled 0.7 (8.2) per cent of net sales for the period under review.
Consolidated return on capital employed (ROCE) stood at -0.8 (17.6) per cent.
Staff costs for the period totalled EUR 27.8 (28.1) million. Other operating expenses stood at EUR 22.1 (19.5) million. The net total of financial income
and expenses amounted to EUR -3.8 (0.6) million. Exchange rate gains and losses due to currency rate fluctuations were recognised under financial items, having a net impact of EUR -2.7 (1.4) million. During the period under review, EUR 0.3 million of revaluation gains on interest rate swaps were recognised in the result. The parent company’s receivables from subsidiaries stood at EUR 119.2 (81.8) million net. Receivables from subsidiaries mainly consist of trade receivables.
Result for the period under review totalled EUR -3.4 (14.0) million. Diluted and undiluted earnings per share (EPS) came to EUR -0.12 (0.50).
At the end of the period under review, the total consolidated statements of financial position amounted to EUR 557.2 (592.8) million. Inventories stood at EUR 234.8 (239.1) million. Trade receivables totalled EUR 53.3 (63.5) million, while cash and cash equivalents stood at EUR 55.2 (61.7) million. Group shareholders’ equity stood at EUR 319.5 (334.3) million and parent company shareholders’ equity (FAS) at EUR 290.6 (245.8) million. The amount of interest-bearing liabilities was EUR 100.5 (93.8) million. The company has ensured its liquidity by credit facility limits and commercial paper programs. Group’s loans from financial institutions
are non-collateral bank loans without financial covenants. Consolidated net liabilities totalled EUR 45.4 (28.2) million, and the debt-equity ratio (net gearing) was 14.2 (8.4) per cent. The equity ratio stood at 57.6 (56.8) per cent at the end of the period under review.
Cash flow from operating activities amounted to EUR 8.5 (2.4) million. Cash flow from investment activities came to EUR -5.9 (-9.6) million.
Order intake for the period totalled EUR 163.5 (184.9) million, while period-end order books were valued at EUR 226.0 (336.9) million.
www.ponsse.com
An ancient elm tree that has stood alone in Glen Affric for hundreds of years is now the guardian over a new generation of its species. Known as the Last Ent of Affric in homage to the treeshepherds from Tolkien’s The Lord of the Rings, the tree has been chosen to help in the fight against Dutch elm disease.
Thirty-five young elm trees have been transferred from the Royal Botanic Garden Edinburgh and replanted next to the Last Ent of Affric, which was awarded Scottish Tree of the Year in 2019. These will be the first of 200 trees planted over the next two years, with our team working alongside the University of the Highlands and Islands and the Royal Botanic Garden Edinburgh. This work forms part of efforts to save the species from Dutch elm disease through the Scottish Plant Recovery project. The project involves cultivating disease resistant seedlings and then planting
them at suitable sites. It is hoped there will be cross pollination between the seedlings – and maybe even with the mature wych elm itself – to help in the recovery, from decades of loss, for one of Scotland’s most majestic native trees.
“Having lived hidden away, many miles from the closest tree of the same species, the old elm of Glen Affric has escaped the ravages of Dutch elm disease. It is fitting this site has been chosen as part of efforts
to save the wych elm.” Sam Brown, Forester at Forestry and Land Scotland
Sam adds “Glen Affric also benefits from ongoing conservation efforts between ourselves and our partners that includes managing deer populations. By limiting or removing the chance of deer damage to the young trees we can give them a better chance of survival.
Our local FLS teams - specifically the craftsperson squad – have worked very hard in all weather, on difficult terrain to install a fenced enclosure that has made the project possible.”
The recovery of the wych elm is part of a project aiming to increase the numbers and distribution of ten threatened native plants and is funded by a three-year grant totalling £715,000 from the Scottish Government’s Nature Restoration Fund.
Dr Max Coleman of the Royal
Botanic Garden Edinburgh explains: “Using surviving, large wych elms in the Scottish Borders, exposed to Dutch elm disease for around 40 years, we have bred a new generation of seedlings that we hope have inherited resilience to disease from both parents. The offspring of these rare, promising trees are being planted in carefully
selected sites that meet their needs and offer potential for natural spread. This work is assisting the formation of new populations of wild elms that have the genes and the genetic diversity that we hope will enable survival and adaptation in a changing environment.”
www.forestryandland.gov.scot
The globally recognised iF DESIGN AWARD is considered a symbol of outstanding design and is one of the most significant and prestigious design awards in the world.
The jury paid particular attention to the functionality and usability of the PONSSE Opti 5G information system. The user interface makes the forest machine operator’s work easier and produces other harvesting information, including operator working hours, production, machine operation and fuel consumption.
“The Opti 5G system is designed to be easy to use to reduce the cognitive load of the forest machine operator and improve productivity. The user interface was completely rethought in our project to meet the users’ needs in the forest industry of today and the future. Design based on a user study and the large-scale testing of results are key factors behind the development of Opti
5G,” says Juha Inberg, Chief Technology and R&D Officer at Ponsse.
“During the project, we addressed the needs of forest machine operators, machine owners, maintenance services and sawmills,” says UX Manager Panu Johansson.
“This award is for everyone who has participated in the software development of the 5G system. Software development is almost always the result of the efforts of a large group of people. Software is at the core of
modern forest machines to facilitate the use of the machine and make their operation more efficient. The user experience also plays an important role in improving efficiency, coping and comfort. Development at Ponsse focuses on understanding user needs,” says Inberg.
A total of 10,800 products and projects from 72 different countries were sent to the 2024 competition for evaluation. This year’s iF jury consisted of 132 high-profile design specialists from 23 countries.
www.ponsse.com
SSAB’s operating result for the first quarter of 2024 amounted to SEK 3,157 (4,733) million. The decrease compared to a year earlier was primarily due to US plate prices that reversed from a high level. The market in Europe continued to be relatively weak, whereas the market for high-strength steel was more stable. The transformation to fossil-free steelmaking continues and SSAB has taken a decision to invest EUR 4.5 billion in the steel mill in Luleå. Besides eliminating 7% of Sweden’s carbon dioxide emissions, the investment entails a string of other benefits including lower production costs, greater flexibility and a stronger product mix.
SSAB Special Steels had an operating result of SEK 1,781 (2,094) million and an operating margin of 23% (24%) during the quarter. SSAB Special Steels’ unique offering provides added value for our customers and this in turn translates into more stable prices than for standard products.
SSAB Americas’ operating result for the first quarter decreased to SEK 1,412 (2,675) million and
the operating margin was 23% (35%), as prices weakened from a high level. SSAB Europe had an operating result of SEK 163 (0) million and an operating margin of 2% (0%). The market was weak and the political strikes in Finland had a negative effect of around SEK 350 million, while the development of high-strength steel for the car industry was good. The strike in April is estimated to impact the second quarter negatively by around SEK 125 million.
Both Tibnor and Ruukki Construction have implemented cost saving programs, including reduction of personnel, which will continue to have a positive impact in coming quarters.
Safety performance continued to improve and LTIF decreased to 0.81 (0.92) during the quarter.
There is great interest in products with no carbon dioxide emissions and in early April SSAB took the decision to build a state-of-the art, highlyefficient mini-mill in Luleå. The new mill will have a capacity of 2.5 million tonnes a year with two electric arc furnaces,
advanced ladle metallurgy and an integrated rolling mill. The investment also includes a cold rolling and galvanizing complex to supply the vehicle industry with a broader offering of premium products.
The investment in Luleå amounts to EUR 4.5 billion including contingency. This will avoid replacement investments of around EUR 2 billion that would otherwise be needed until 2035 to sustain the current blast furnace, steel mill and coking plant in Luleå as well as the rolling mill in Borlänge. The value creation will be significant, compared to the alternative of continuing to invest in the current system, and the annual EBITDA improvement is estimated to be more than SEK 5 billion at current commodity forecasts. The mill design includes a production increase of 0.5 million tonnes a year and improved mix with 1 million tonnes of special and premium steels a year. The transformation of Luleå will reduce Sweden’s carbon dioxide emissions by 7% in addition to the 3% reduction from the conversion of the mill in Oxelösund. www.ssab.com
Scottish Woodlands Ltd is working on a large new native woodland project to plant more than 30,000 trees in a former coal mining area in County Durham.
The creation of the 35-hectare woodland was marked by a planting ceremony at the site, involving Vice Lord-Lieutenant of County Durham Michael Poole and local schoolchildren.
A silver birch was planted on the site at South Causey, close to the Beamish industrial heritage museum - the first of almost 33,000 trees to go into the ground. The trees are a wide mix of species, including alder, aspen, birch, cherry, hazel, rowan, Scots Pine, willow and Wych Elm.
Jonathan Harker, Regional Business Development Manager for Scottish Woodlands Ltd, said: “This is a great project to be involved with, bringing new green growth to a former industrial area. Scottish
Woodlands Ltd was very pleased to be selected in a competitive process to do the tree planting and site management, and our Forest Manager Sam Jama is leading on this project. We very much look forward to working with all partners to make the project a great success.”
The Woodland Trust was approached by the owners of the land in April 2022 for advice on woodland creation and said it had been “a delight to help bring their vision alive”.
Dr Rachel Penn, Outreach Adviser at The Woodland Trust, said: “The 35ha of new native woodland at South Causey in the former Durham Coalfield will bring a host of environmental benefits, not only to the land itself, but also to the adjacent ancient woodlands.”
“Woodland species, many of which are UK priority species for conservation, will be able to expand their range into the new woodlands, assisting in their
protection and survival.”
Ross Weddle, Chair of the North East Community Forest, said: “We are absolutely committed to bringing more greenery and woodland to our region, so I am pleased we are supporting this exciting project. Woodlands and green spaces are the beating heart of so many of our communities. We look forward to working with volunteers and partners to plant these new trees so they can be enjoyed by people for years to come.”
Phillip and Susan Moiser, the owners of South Causey Farm, said: “It’s been our ambition for a long time to convert the land which has been farmed and used for grazing for many years back to its original biodiverse and eco-friendly roots. We are really proud that so many people are getting involved and supporting the project, which will bring a wealth of benefits to our community for years to come.”
www.scottishwoodlands.co.uk
Jerry Rose, his son Davis, and daughter Stephanie Blythe, operate two logging businesses and a transport company out of Courtland, Virginia. Jerry started Jerry D. Rose Incorporated in 1983. Davis and Stephanie are third-generation loggers.
“Before our father started the company, he was the foreman on our grandfather’s job, Ben E. Babb Logging,” said Stephanie. The siblings founded a second company, Southeast Fiber Supply, in 2013. “We started Southeast Fiber Supply to handle the chips going to Enviva. Dad also started a trucking business, Chip Transit Inc., that does all of the hauling for our logging operations,” Stephanie explains.
Today, two Jerry D. Rose Incorporated crews supply International Paper in Franklin, Virginia, with clean pine pulp chips. The third crew, working
under Southeast Fiber Supply, markets fuel chips to an Enviva pellet manufacturing plant, as well as a Dominion Power facility. The main differences between the pulpwood crews and the fuel chip crew are in the tract type, and of course, the type of chip produced.
“The Southeast Fiber Supply crew cuts more mixed tracts with smaller hardwood,” Davis explains. “We try to target tracts with a lot of pulpwood but sometimes we will run into hardwood logs.” The company merchandises the saw timber, “It’s maybe about 5% of our weekly quota. We cut private tracts that we buy, and we cut a fair amount for the big timber holding companies, like Westervelt, John Hancock and Roseburg. A lot of the work we do for them is thinning work.”
Between the two companies,
five Tigercat 724G feller bunchers equipped with 5600 bunching heads are working full time, with three spares available. The machines were purchased from Bullock Brothers Equipment. There will usually be two feller bunchers deployed for a thinning crew and just one machine for a clear fell job. “For us, the 724G is perfect for thinning,” says Davis. “In a lot of the clearcut operations, we will run a 44-inch tire because it is best for our ground conditions. When we move to thinning, we will put a 30.5 tire on that same machine. It makes the machine more versatile.”
The company is meticulous on maintenance. A full-time mechanic cycles through the three crews, compiling service notes on every machine. The Roses tend to hang on to their Tigercat bunchers, trading them
with up to 13,000 hours.
Jerry, Stephanie, and Davis have established strong relationships with their employees. “We employ 40 full time people across the board at all three companies,” says Stephanie. “We run sixteen of our own trucks and anywhere between five to seven contract trucks daily. We are producing in the neighbourhood of 275 to 300 loads per week. Our record is 356 loads.”
One particular employee stands out in many ways. Roland Murphy, who goes by Peter, is a feller buncher operator.
Peter is 81 years old and has worked in the logging industry all his life. “Peter worked for Ben E. Babb Logging in the seventies,” says Stephanie. “At some point after that, around 1983, Peter came to work for our father at Jerry D. Rose Inc. Since then, he has worked with all three of our crews.”
Peter has driven a log truck and operated a chipper, and he is a highly accomplished feller buncher operator. “He is remarkable,” says Stephanie. “At times, there is one cutter here and sometimes it should possibly be two, but Peter can do what two men can do, any day, at 81 years old.”
Davis adds, “I would say he has probably cut down more trees than anybody in the world. I mean, he has been doing this since he was fifteen years old. He has been working for highproduction logging crews his whole life.”
Last year, Peter was forced to take time off work to recover from surgery. In his absence, the company made do, but Peter was sorely missed. “Everybody was happy the day he came back. Very happy,” says Stephanie. Peter, who is not one to miss even a single day of work, was happy too. “He doesn’t miss any time,” adds Stephanie. “He just lives and breathes it.”
“If you don’t love it, you’ll never do a good job,” said Peter, “I keep working because I love my job and I love the people that I work with.”
In some ways his wealth of experience is difficult to quantify. For example, he knows how sites should be laid out and where to build the deck. He has an intuition on how to log a tract. Stephanie recalls occasions when they would move into a new tract and the conditions were quite wet. “Davis and Dad would bring Peter to the site, like ‘tell me right now, is this going to work or is it not going to work’ because Peter just knows, immediately.”
Just as often, the benefits that his experience brings to the table are easy to measure. Peter’s steady, unrushed style, and the efficiency of movement that characterizes his work keeps his production high. An added benefit is that he is easier on the machine.
The crew loads the first chip van at 5:00 am, and the chipper generally runs eleven hours per day. Peter also starts around
5:00 am, and he will cut until he feels he’s got enough wood on the ground, usually around seven hours. Then he parks the machine and goes home.
C.W. Jones is the site supervisor out here. “He and the rest of the crew take the best care of Peter,” says Stephanie. “If he pulls up, it is like a full-service fuel station. I mean, they hop out and fuel his machine. They just really cater to him. It leaves him to focus on what he does best – running the machine.”
“If he pulls up here and it’s got mud on the windshield, these guys know what to look for because they take care of him. They know what he is doing when he is on the way. They are so used to tending to him. They respect him,” says Davis.
It is easily apparent that C.W. highly values the time he spends with Peter, describing the start to a typical early morning. “Normally he will stand around for fifteen minutes, talking,” says C.W. “We will talk about our day, what our plans are. He’ll tell me
some cool stories now and then. They did a lot of felling manually with chainsaws. But they were cutting bigger timber. He said that a lot of the tracts that we have cut, he has cut before. When he first cut it, it was virgin timber. He said they left a lot of stuff. A lot of the stuff we are cutting now, they had left that.”
It is remarkable that Peter has cut the same sites two and even three times before, but even more noteworthy is that he remembers the details.
“We have a map of the timber harvest area that we give to the operator, and a lot of the time Peter will tell us that he doesn’t need the map because he had cut it before,” says Stephanie.
It is the old stories that C.W. appreciates most. The recounting gives clues and insights into the man. “Growing up in the depression instilled a work ethic in Peter that is difficult to replicate in younger workers. They don’t have that same drive and determination that comes with the struggles of his lifetime. And it shows in his work ethic.”
Peter can cut. In good clear fell timber, he can cut three-anda-half loads per hour, putting down 100 loads each week. He always has a very good idea as to how much wood is on the ground at any given time. He knows exactly when to park the machine and go home, calculating that there is enough wood to feed the chipper for the remainder of the day and the start of the following day.
Peter doesn’t count bunches and doesn’t have any apparent system to back up his estimating accuracy. He can’t say how he knows; he just does.
Peter also ran a Tigercat track feller buncher for ten years. He says the track cutter is easier to operate because there is less travel and he doesn’t get bounced around nearly as much. “They are good machines. A whole lot easier to work in the woods with them too.” However, Peter has refined his operating techniques over many years. “If you cut the stump down, you won’t have to run over it. I cut them as low as I possibly can. It makes it easier on you. It won’t throw you around and bounce you up. If you don’t do it, it will wear you down,” he explains.
“Another thing, you’ve got to cut the wood and put it down so it’s not in the way. Because you can’t drive over top of it. You’ve got to learn how to cut the
wood, back up, and throw the wood down where you have already cut.” Peter never looks at the rear camera view when clear felling and rarely turns to look. Instead, he maintains a spatial awareness. “When I back up, I know there isn’t anything left behind me. In thinning, the camera will help you a whole lot, but in clear cutting, I don’t pay it no matter, I don’t even look at the camera. I don’t want to lose any time.”
Peter says that he doesn’t have to move quickly to achieve high production. The important thing is to operate at a steady pace. “You go one speed, and you go all day at that speed. If you stop for fifteen or twenty minutes, look at what you don’t log,” he explains. Another thing, by going steady and not so fast, you won’t break anything because you have more chance to see what you are doing.
“If you get going too fast, you can’t see what you are doing.”
C.W. explains it this way. “I could get into a feller buncher right beside him and I could probably keep up with him for about two days and after that, he is going to be pulling away from me. It’s just amazing.”
Peter doesn’t partake in any of the daily distractions that have become so prevalent in modern society. He is not checking his cell phone or scrolling social media. He is focused and completely immersed in the present until he decides he has put enough wood on the ground for the day. “He doesn’t even listen to the radio,” says C.W. “I asked him once if he wanted to turn the radio on. He said, ‘I don’t listen to the radio. I just want to hear the trees fall.’”
Having seen a lot of people come and go in the industry, Peter offers this advice to younger workers. “Someone new will come in and start doing the same work I do, and they get tired and broken down, because they break themselves down.” Peter stresses that pace is key. “If you move yourself at the right pace, it won’t make you tired; you can go all day and you won’t be tired. I learned that years ago. Don’t let the machine beat you, because it will beat you if you let it.” Passion is another critical element for Peter. “You’ve got to want to do it. If you don’t love it, you’ll never do a good job. I keep working because I love my job and I love the people that I work with. I love them.”
Peter has been working in the woods since he was a teenager. He has seen a lot of change in
the industry over those sixtyfive years. In his earliest days in the logging industry, horses or mules, and later, rudimentary tractors were used to transport topped and limbed treelength logs to an infield sawmill. When they packed everything up and left the site, great piles of sawdust remained. He started off felling with a two-man crosscut saw and witnessed firsthand the technical advances that brought the early twoman power saws, and the advancements that led to lighter weight saws that one man could operate.
When the southern United States began to mechanize the felling function in the eighties, and people climbed into wheel feller bunchers for the first time, Peter was there. He says he has probably run every rubber tire feller buncher brand ever made and acknowledges a steady improvement in comfort and reliability over the years. The current 724G “is the best machine that I have been on.
There is nothing better than this.”
He stresses that the performance and reliability of the 5600 bunching saw has been outstanding over the years. “You don’t have any trouble with cracks and breaks and all that. I have been running them about twenty years or more. I have never had a crack in one; never had an arm break or anything.”
Peter climbs up into his machine like a man half his age. He can focus on a physically and mentally challenging task day after day. He is still at the top of his game. For now, Jerry, Davis, and Stephanie will take a page from Peter’s playbook and take each day as it comes. “We know that it’s not going to last forever,” says Stephanie. “He said he will tell us when he is ready. I said don’t you worry, when it is time for you to retire or whatever, I want you to tell us and be honest. He said, ‘I am not ready,’ so I said, OK.”
Autonomous wood harvesting is developing rapidly and will likely be viable by the end of the decade, increasing competitiveness of forest industry players – especially in high labour cost countries. The most likely places for the initial spread of the new technology will be North America, Scandinavia, and Brazil, with different change drivers in each case. The most likely initial technology might be electric or hybrid harwarders (combined harvesters and forwarders). The most likely pioneers of the new technology: current leading machinery suppliers and large forest industry holdings.
AI-based technologies are developing rapidly driven by the transformational and disruptive potential and high expectations in terms of business opportunity. AI has even managed to enter the traditional and slow-paced industries like forest products. Forestry, from nurseries via silviculture to harvesting and wood logistics is an ideal testing ground for implementation of AI in autonomous operations due the characteristics of the processes and the high share of logistics combined with limited risk:
• repetitive and predictable tasks in processes in silviculture, harvesting and wood logistics
• availability of large data sets to train AI models
• low risk of safety incidents during operations due to remote locations of the operations
• clear business case through reduction of labour costs by implementation of technology – especially in high labour cost, forestrich countries like Finland, Sweden, Canada, and the US
• Solution for labour shortage of perceived unattractive jobs in remote forestry regions
In this publication we will discuss scenarios and potential outcomes of the AI revolution in forestry. In our opinion, the technological benchmark in this segment will be the “dark forest” - almost completely autonomous operations, similar to the “dark warehouses” in modern warehousing.
Autonomous harvesting and wood logistics is likely to improve competitiveness
through adoption of new technologies, especially for companies in countries with already high labor costs and low availability of skilled labor. People harvest some 4 billion m³ of wood every year from a bit over 4 billion ha of forests on the planet. Half of the harvested round-wood (app. 2 bln m³/a) goes to industrial processing, the other half is used as firewood. Total cost of harvesting and forwarding of in-dustrial roundwood is approximately 12 EUR per m³ (real, 2022) in high labor cost regions – see the chart, above right,WW with the example of Finland. This number excludes long-distance transportation.
Labour cost as part of the total cost of industrial harvesting/ forwarding is 1-5 EUR/m³, depending on geography (including wood logistics to the roadside but excluding support functions and long-distance transportation). This equates to over EUR 5 bln per year spent on labour. The potential savings opportunity through automation can be estimated around a billion EUR per year globally with the bulk of savings stemming from harvesting operations rather than long distance transportation.
can potentially self-charge in the forest via electricity generated from wind, hydro or solar power. Even in the case of hybrid solutions, expected fuel savings are estimated at 20% in addition to an increase in power and performance.
Labor cost as part of the total cost of industrial harvesting/forwarding is 1 - 5 EUR/m³, depending on geography (including wood logistics to the roadside but excluding support functions and long- distance transportation). This equates to over EUR 5 bln per year spent on labor. The potential savings opportunity through automation can be estimated around a billion EUR per year globally with the bulk of savings stemming from harvesting operations rather than long distance transportation.
The case for fully electrified or hybrid solutions in autonomous forestry can be made based on general sustainability argumen ts but also through direct benefits of reduced maintenance costs and lower energy costs. Electrified vehicles and machinery have co nsiderably less parts to be maintained and can potentially self - charge in the forest via electricity generated from wind, hydro or solar power. Even in the case of hybrid solutions, expected fuel savings are estimated at 20% in addition to an increase in p ower and performance.
The status quo
The case for fully electrified or hybrid solutions in autonomous forestry can be made based on general sustainability arguments but also through direct benefits of reduced maintenance costs and lower energy costs. Electrified vehicles and machinery have considerably less parts to be maintained and
And it is not only about potential cost savings and sustainability benefits. The slowgrowth Northern hemisphere fibres might become more competitive again when compared to fast-growth plantations in more southern or equatorial regions of the world thus potentially narrowing the gap. Naturally, plantation forestry can equally make use of autonomous technologies thus providing an equal potential for next level cost savings.
of this publication, fleet electrification is already seen as a feasible way forward both technologically and financially. Fully autonomous operations are however not yet fully mature. However, the path towards driverless technologies based on AI is already drafted in pilot phases and on the horizon. A swift adoption can be forecasted, if benefits are con-firmed, as the risks to implementation are limited for a roll-out in remote locations (especially when compared to autonomous personalized driving in population centres).
And it is not only about potential cost savings and sustainability benefits. The slow - growth Northern hemisphere fibers might become more competitive again when compared to fast - growth plantations in more southern or equatorial regions of the world thus po tentially narrowing the gap. Naturally, plantation forestry can equally make use of autonomous technologies thus providing an equal pot ential for next level cost savings.
Based on interviews conducted in preparation of this publication, fleet electrification is already seen as a feasible way for ward both technologically and financially. Fully autonomous operations are however not yet fully mature. However, the path towards driverless technologies based on AI is already drafted in pilot phases and on the horizon. A swift adoption can be forecasted, if benefi ts are confirmed, as the risks to implementation are limited for a roll - out in remote locations (especially when compare d to autonomous personalized driving in population centers).
The most likely fit for pioneering the commercial use of autonomous harvesting and wood logistics is likely driven by:
Based on interviews conducted in preparation
• large-scale harvesting operations
The most likely fit for pioneering the commercial use of autonomous harvesting and wood logistics is likely driven by:
• large local forest industry
Figure 2. Cost of harvesting and transportation in Finland (€/m³, real 2022), 2000-2022e, Source: Analysis of the author based on data from Statistics Finland and Luke)• holdings, ready for pilot projects
• local development and manufacturing of forestry machinery
• a proven track-record of innovation and scaling of commercial solutions in areas like autonomous driving, electric powertrains, solar and wind energy generation, autonomous agriculture (agriculture is developing at a much faster pace than forestry so that solutions can be scaled from the experience in this field)
• current state development - rocky terrain, swampy ground, steep slopes, selective cuts in natu-ral forest
• National importance of the forest sector for a given country: The higher the importance, the more motivation to innovate
industrial roundwood production are US, Russia, China, Brazil and Canada. The top-5 countries represent over 50% of industrial wood production on the globe.
Additional considerations might be:
Additional considerations might be:
• Risk concerns: How trustworthy and reliable is the country/region for autonomous operations (including risk of theft or vandal-ism)
The next 5 largest industrial roundwood producers are Indonesia, Sweden, Ger-many, Finland, India. The total share of the top-10 countries is 2/3 of the global industrial round wood production.
• a proven track- record of innovation and scaling of commercial solutions in areas like autonomous driving, electric powertrains, solar and wind energy generation, autonomous agriculture (agriculture is developing at a much faster pace than forestry that solutions can be scaled from the experience in this field)
• Forest uniformity: The best- case scenario is uni - species pulpwood- dedicated plantations with flat terrain and relatively soil; worst case scenario – given the current state development - rocky terrain, swampy ground, steep slopes, selective in nat ural forest
• Forest uniformity: The best-case scenario is unispecies pulpwood-dedicated plantations with flat terrain and relatively dry soil; worst case scenario – given the
Regionally the transformation will likely also correlate to the current volume and importance of roundwood production by country in combination with country specific labor costs and availability.
• National importance of the forest sector for a given country: The higher the importance, the more motivation to innovate
• Risk concerns: How trustworthy and reliable is the country/region for autonomous operations (including risk of theft or ism)
The most likely candidates for autonomous forestry from the Top-10 are USA, Brazil, Finland and Germany including the respective neighboring countries such as Canada, Uruguay, Sweden and Austria. The drivers and obstacles for those countries are a bit different in each case:
Regionally the transformation will likely also correlate to the current volume and importance of roundwood production by country combination with country specific labor costs and availability.
The largest countries by
• The key drivers of the
Figure 3. Top-15 producers of industrial roundwood globally, 2022• development towards electric and autonomous harvesting in the US/ Canada and in Scandinavia are largely the same.
High labor costs and the lack of available labor are pushing towards autonomous solutions.
Large forest industry holdings can generate the necessary economies of scale to support pilot programs together with forest machinery producers (including machinery suppliers from agriculture such as John Deere)
• Germany/Austria are behind US and Scandinavia in our ranking, mostly due to lack of large local forestry machinery manufacturing but agriculture machinery
• can potentially fill the gap
• The key drivers for Brazil are uniformity of forests, abundance of solar energy, large vertically integrated forest industry hold-ings with private plantations and with a track record of fast adoption of innovative solutions in wood supply chain
• Low (labor) cost countries like Russia are unlikely to lead the transformation as the business case for automation will likely not justify the investments in the first phases (not even considering the current investment climate and sanctions)
Assuming equal weight of the change drivers in the table
below, the probability of emergence of autonomous harvesting is highest for Finland/ Sweden, US/Canada, and Brazil. In our view the importance of uniform forests, the abundance of solar energy and presence of large innovation-ready forest industry holdings might outweigh other factors –pushing Brazil (and, to some extent, China) even fur-ther forward in this comparison even if the direct payback due to labor cost savings is lower than in the other countries.
How likely is the electrification and AI scenario to develop? Who will produce the first commercially viable autonomous machines?
A scoring model based on assessment of the key drivers for each country is shown below.
Currently it looks like the largest incumbent players are already in the leading positions. Specifically, two machinery producers seem to be well positioned to lead the race:
Other machinery manufacturers might become important in this race as well, partially building on similar initiatives:
• (no longer with harvesting machinery, after this part of the business was sold to Weiler Forestry)
• Komatsu a large producer of machinery for various industries with headquarters in Japan, and forestry machinery production in Finland, expects to have an electrified forest machine on the market by the end of the decade; and the company already has electric excavators in the product range
• Malwa Forest (Sweden) with a recently introduced fully electric harvester for thinning (in cooperation with Regal Components AB, Traktorarvid AB, Micropower AB and Powerswap AB).
• Other/smaller Western players like Rottne, Weiler Forestry, HSM etc.
• Several Chinese players in forestry machinery, with possible support from outside of the industry
Assuming equal weight of the change drivers in the above table, the probability of emergence of autonomous harvesting is high est for Finland/Sweden, US/Canada, and Brazil. In our view the importance of uniform forests, the abundance of solar energy and p resence of large innovation- ready forest industry holdings might outweigh other factors – pushing Brazil (and, to some extent, China) even further forward in this comparison even if the direct payback due to labor cost savings is lower than in the other coun tries.
• John Deere (production of forestry machinery in Canada and Finland) already has several autonomous and semi-autonomous electric vehicles for agricultural purposes. In 2024, John Deere announced a strategic partnership with Starlink to provide satellite internet connectivity to John Deere machinery to support technology development in autonomy, real-time data sharing, re-mote diagnostics, enhanced self-repair solutions, and machine-tomachine communication in agriculture. The first Starlink terminals are planned to be installed already in 2024 starting with machinery in US and Brazil
• Ponsse (Finland) has a concept hybrid forwarder, with a fully electric drivetrain and electricpowered hydraulic system for the loader
• Volvo/Geely (Sweden/ China) with electric logging trucks, electric construction machines from Volvo Construction Equipment, electric cars by Geely, electric powertrains for forestry by Volvo Penta, and (together with Air Burners and Rolls-Royce) mobile energy generator based on woody biomass
Additionally, initiatives led directly by forest industry holdings can play an important role. Recent examples of work in a similar direction and the potential for synergies are:
How likely is the electrification and AI scenario to develop? Who will produce the first commercially viable autonomous machi nes? Currently it looks like the largest incumbent players are already in the leading positions. Specifically, two machinery produ cers seem to be well positioned to lead the race:
• Caterpillar (large producer of machinery for various industries, HQ in US) with electric construction and loading machinery, and with manufacturing of log loaders
• LTU, in collaboration with the Swedish Agricultural University and the Forestry Technology Cluster (supported by SCA and Holmen), is testing an autonomous research forestry machine and an autonomous forwarder (AORO platform, project
• John Deere (production of forestry machinery in Canada and Finland) already has several autonomous and semi - autonomous electric vehicles for agricultural purposes. In 2024, John Deere announced a strategic partnership with Starlink to provide satellite internet conn ectivity to John Deere machinery to support technology development in autonomy, real -time data sharing, remote diagnostics, enhanced self- repair solutions, and machine - to- machine communication in agriculture. The first Starlink terminals are plan ned to be installed already in 2024 starting with machinery in US and Brazil
• Ponsse (Finland) has a concept hybrid forwarder, with a fully electric drivetrain and electric - powered hydraulic system for the loader
• active since 2014); the field tests of the forwarder are taking place in 2021-2024
• Skogforsk University (Sweden) with work on remotely controlled and autonomous forwarders, as well as soil preparation machines
• Autonomous machine for planting seedlings Södra (not quite harvesting, but a step in approximately the same direction); and a similar project from Vinnova/SCA (Autoplant project)
• Autonomous transportation of chips by Stora Enso (inside one of the Stora’s plants); SCA and Södra (in cooperation with Scania) and Metsa with testing of electric timber and electric woodchip trucks, incl. on public roads. By March 2024, the SCA (Scania) electric timber truck has been operating for a year and a half and has travelled almost 50 thousand km during this time. MAN (part of the VW Group, the same as Scania) should also be mentioned in this group with the launch of an autonomous truck (tests of the autonomous system are taking place in Germany, news from April 2024).
Additionally, players outside the industry may see an opportunity to adapt recent advances to the realities of forestry. Companies involved in autonomous agriculture and artificial intelligence in general are well positioned here. There are several recent examples of similar development such as:
• Platooning of logging trucks, autonomous or not (FPInnovations, NFMC);
• autonomous log loaders (FPInnovations)
• Autonomous and semiautonomous electric trucks, including logging trucks introduced by Swedish unicorn Einride (although developments on the logging truck project might have stalled after 2020).
In a sense, this is a “tug of war”: The combination of the most advanced machinery producers and innovative forest industry holdings are largely present in the Northern hemisphere where the forest conditions are much more demanding and difficult for autonomous machinery. On the other hand, innovative forest industry holdings in lessdemanding geographies need support of (Western) machinery suppliers and AI specialists. Similarly to other leading-edge developments in forestry in the past, Brazil might provide the testing ground here.
Industrial harvesting nowadays is done primarily with the cut-to-length method (CTL, harvesters + forwarders) or with the tree-length method (TL, feller-bunchers, skidders, processors). More exotic combinations include e.g. fellerbunchers followed by processors fol-lowed by forwarders. A more exotic option is the harwarder – a combination of a harvester and a forwarder in one machine, without the need to load logs to forwarders from the ground, but with a need to move the whole machine to the roadside once it is fully loaded. In our view, harwarders are among the most promising
ways towards autonomous & electrified forestry.
The main reasons for harwarders to be a promising path are reliability and universality:
• Problems with any of the harwarders would not affect other harwarders in the same area (which would inevitably happen in combined teams of CTL and TL operations) – and that might be important in case of remote operations without human supervision or without ability to fix the problem in a prompt manner
• More universality means more flexibility in managing the teams (no need to organize smooth cooperation between the cutting and the hauling part of the operations, no need to load logs from the ground)
Harwarders are, probably, the fastest path towards autonomous operations in forestry. However, this path requires a cultural and operational switch in the operating model from CTL/TL to harwarders. However, there might be substantial barriers to be overcome, in which case alternative or intermediate paths might prevail, such as:
• Autonomous forwarding with harvesting remaining at least for some time, in the hands of human operators. At a later stage harvesters might become autonomous as well
• “Timber swarm” of small machines like “harvester heads on wheels” or even
• “harvester heads flown by copters” with delimbering done on the standing trees and hauling done by smaller machines or pully systems
Driverless electric harwarder (combined harvester and forwarder). Loading is done directly onto the bed, i.e. no loading from the ground is needed. Rotating bed for more flexibility in loading and unloading
Detachable tractor (driverless; fully electric or hybrid with diesel) – for towing support and recharging of the harwarders in the field. The tractor can be charged from mobile solar panels, wind turbines, biomass burners or the grid at the upper landing, or from onboard diesel engine, if a hybrid machine is used
Additional solutions, depending on the conditions like terrain type, forwarding distance, volume per hectare etc. might include dedicated autonomous forwarders (without or without cranes and rotating beds) or trains of double- bed harwarders (with one harvesting head for two trailers, and with possibility to separate sawlogs from pulpwood already at the point of cutting)
by Andrew Beschastnov
The main reasons for harwarders to be a promising path are reliability and universality :
1. USD/m³) and improving profitability of the operations
• Problems with any of the harwarders would not affect other harwarders in the same area (which would inevitably happen in combined teams of CTL and TL operations) – and that might be important in case of remote operations without human supervision or without ability to fix the problem in a prompt manner
• Transition towards more functions performed in field: including e.g. chipping, drying of the chips prior to long distance transportation, soil preparation, planting new trees, other works – with larger fleet of specialized or multi-function machines controlled and maintained by on-site operators.
In parallel, further development in digitalization and customization in forestry is expected in:
1. Selection and genetic modification of the tree species to tailor species to certain climatic and soil conditions, improving rotation periods and yields (both m³/ha/year and
2. Information technologies for the management of wood resources – e.g. leading to virtual “log passports” for eventually every tree and every log, with individual database entry for every log (3D model, “fingerprints” of the ends, RFID or similar IDs). This will enable further yield improvements and maximize competitiveness by considering best products at best market prices for every log
• More universality means more flexibility in managing the teams (no need to organize smooth cooperation between the cutting and the hauling part of the operations , no need to load logs from the ground)
AI and digitalization are transforming society and global supply chains. New technologies are already and will further find their way into forestry. The imperative for the electrification and automation of forestry will be driven by a variety of reasons:
• The availability of technology to substitute labour-intensive forestry practices
• The opportunity to reduce total costs both in labor as well as maintenance and energy costs
• The opportunity to operate 24/7 x 365
All these initiatives would further improve competitiveness of those companies or regions with the most forward-looking thinking and business stamina, maximising maximizing value of supply chains based on the optimal characteristics of trees.
• The opportunity to overcome the labor shortage in many forestry areas across the globe
• The opportunity to make forestry practices more sustainable in terms of reducing or eliminating the CO2 footprint created by current harvesting
Figure 6 Illustrational 3D -model of autonomous harwarder Figure 7 Illustrational 3D -model of autonomous harwarder Harvester head is swoped for a grapple for unloading Illustrations• and forest management practices
It will therefore only be a matter of time when current practices will be gradually replaced by autonomous and electrified technology. The benefits of technology in other labour-dependent industries and supply chains have been proven and are part of the continuous development of mankind. As the saying goes –one can’t sometimes see the forest for the trees. But in the future one doesn’t really have to. Operations, like labour-free operations in modern “dark” warehouses can equally operate without light – thereby enabling the global expansion of “dark” forestry.
We are ready to support this development, as well as “more traditional” ways to improve profitability in forest activities, including forestry, wood products, pulp, paper and packaging. Please contact the authors to exchange ideas and learn more about our possible support.
Authors:
• Alexey Beschastnov,
• management consulting in the forest industry, alexey.v.beschastnov@gmail. com
• Andrew Beschastnov, illustrations
• Find Us On Linkedin
Tigercat adds fifth model to harvesting head lineup with the new threewheel drive 573.
In late September 2023, visitors to the PLC live demo event held in Washington state got a sneak peak of the new Tigercat 573 harvesting head processing logs on the end of a Tigercat 875E logger. Since then, multiple units have been testing in far flung regions from Alberta to Australia and the results are in. The 573 is shaping up to be a high performing, reliable head for roadside processing and harvesting.
Best suited to medium and large tree profiles, the 573 has a 800 mm (31 in) maximum cut capacity and offers optimal performance in 400-600 mm (16-24 in) diameter timber. The feed rollers close down to 60 mm (2.4 in), allowing the 573 to smoothly delimb and process smaller diameter trees and thus achieve higher value fibre recovery.
The compact frame design deftly handles poor stem form and contributes to tidy delimbing performance. The triangulated feed wheel arm configuration operates in locked three-wheel drive. This, combined with timed knife arms, provide the operator with fast picking and positive stem control for high productivity
in roadside processing applications. Independently mounted, trailing-arm length measuring ensures reliable tracking and accuracy.
The top knife and lower/back knife pivot on the same side of the chassis frame, aligning the position and flow of each stem centrally through the head. This arrangement promotes positive contact with all three feed rollers and the measuring wheel at all times. The result is better quality and accuracy, reduced fuel consumption, and greater processing speed. The orientation also provides the operator with a clear sightline to the measuring wheel.
The 573 is standard equipped with continuous rotation for ease of use and superior hose
routing and protection. Quick, stable WiFi connectivity between the cab and attachment modules reduces wire routing along the boom and provides excellent command response.
The Tigercat D7 control system is available with Priority or Optimization levels and is fully compatible and compliant with StanForD Classic and 2010.
The 573 is a great fit for the H250D, 850 and 875E for roadside processing applications and the H822E and H855E carriers for in-stand harvesting.
Due to improved drive systems, band tracks and traction aid winches, the limitations of machines that work in forestry is continually increasing. However there are still circumstances where high lead winches are necessary to extract timber. My personal experience with high leads is limited, but I have witnessed the advantages of using them on very wet areas and steep ground.
A highlead is a much less complicated system than a skyline, as it requires only two winches, a mainline and a haul back line. Highleads are effective over shorter distances and are designed for extracting timber up to maximum distances of 250 - 300m. Two highleads I have seen recently working were both mounted onto excavators and manufactured by R J Fukes
Forestry Services - one was in the Scottish borders and the other in South Wales.
This self-contained Highlead system was attached to the quick hitch of a thirty tonne Doosan DX 300LG excavator. It had an extension added to the dipper boom to give extra height.
It was being operated by a team from the Elliot Henderson Group and was clearing diseased larch trees, to help contain the spread of Phytophthora ramorum, from a narrow gulley with a watercourse at the bottom. Many of the larch trees had snapped off or had blown over and were blocking the flow of water.
The only point of access was following the gulley down
towards the forest road as there was a young spruce plantation on either side of the gulley. The trees were being felled by chainsaw operators and then extracted by the highlead operator and chocker. It was surprising how effective it was, considering the two-man team were only taking one or two trees at a time and each tree was around 0.1m³ average.
Little and often was the secret and it worked well. This prevented any excess strain on the equipment which returned remarkable fuel economy and prevented downtime of the winch cables breaking due to overzealous chockering.
This was a good system as once the trees started piling up too high - they had a few areas like this to do in this block and once they were all completed
This photo details how a Highlead system works, the 30-tonne excavator does not require the guy lines as the trees being extracted are not particularly large, and the excavator is stable as it is on a forest road.
a harvester would arrive to process and stack the extracted timber - all they had to do was lift the dipper boom and track along a few meters and start extracting again in a clear area. The main and haul back line did not need re-positioning so this operation only took a moment.
I visited this site twice, at the start where it was a tangled mess, and towards the end where there was only a day or so left and the results spoke for themselves.
This was the first highlead winch system John Fukes had mounted on an excavator. The two winch drums were mounted in line, on a solid platform above the engine, just behind the cab. The platform could be raised and lowered hydraulically to allow full access to the engine compartment. This highlead had an extended dipper boom for extra height but still had the excavator bucket for making platforms, removing stumps, or repairing extraction routes.
The highlead winch was owned by forestry contractors Coed Camddwr Ltd and was working at the top of a steep ravine about 3-400 meters away from the forest road. The trees were being extracted trees up a steep ravine where a Ponsse Ergo processed the trees into the desired lengths as they arrived.
This was an efficient system as the landing area was always clear and removing the chockers was a straightforward task for the highlead operator.
Dan Bulman, operator of the harvester, would switch to the Ponsse Buffalo forwarder as soon as the processed produce mounted and took it to roadside. The three-man team – a chokerman down the ravine, highlead operator and harvester/forwarder operator all worked well together. The highlead operator and chokerman were in radio contact with each other and their production rate was impressive as the harvester was kept busy.
I had the opportunity to operate the highlead and I couldn’t
believe how simple it was to use. My last experience was on a Forestry Commission Chapelhall Skyline. That was quite physical as you pulled on both clutch and brake levers on an Igland double drum winch to maintain the correct tension. Operating this highlead was idiotproof via a single joystick. Pushed forward it sent the chockers down the hill, pulled backwards, it brought the trees back up. One other button was to release the cable when chokering and that was it. The winches did all the work and had slack rope sensors keeping the cables at the correct tension so there was never any fear of tangling or damaging the winch ropes. Winch drum cameras with the onboard monitor means the operator always has peace of mind with visual contact of the winches.
I was mightily impressed with the speed of production and the minimal impact this system had on the soil structure. There was a fast-flowing river at the bottom of the ravine which found its way into a reservoir. This is a high rainfall area and there could have been severe repercussions if machines were used on the steep hillside.
Both teams in Scotland and Wales were extremely impressed with the quality, reliability, and performance of their highlead winches. Being mounted on an excavator allows them to travel off road thus reducing the extraction distance and increasing production.
The RJ Fukes Forestry Services highlead winches have a quick set up time of just 30 minutes, they are a non -invasive
installation onto customers equipment and operator training is given with every purchase. Removal of the winch head is quick and straightforward allowing the base excavator to return to an unimpeded state. The system can be removed and installed onto another carrier at minimal cost.
RJ Fukes Forestry Services offer three sizes of highlead winches.
M3.1
Is the smallest with a single speed with a 3 to 5 tonne pull, the minimum excavator base size is fourteen ton. The working range is 200m maximum using wire rope with a steel core from 10mm to 13mm diameter. Wire rope sizes is dependent on winch force settings.
M3.2
This is a mid-size winch with variable speed motors with a 5-6 tonne pull, the minimum excavator base needed is seventeen tonnes. The working range is 300m maximum using wire rope with a steel core from 11mm to 14mm diameter. Wire rope sizes is dependent on winch force settings.
M3.3
The largest model with variable speed motors with a 6-9 tonne pull, the minimum excavator base needed is twenty-five tonnes. The working range is 400m maximum using wire rope with a steel core from 12mm to 14mm diameter. Wire rope sizes is dependent on winch force settings.
M3 winch systems are specifically designed for track base mounting but can also be mounted to wheelbase
machine bases. The hydraulic components are selected for their durability and long service life so that operating costs are kept to a minimum.
The winch drums are manufactured to give optimum storage and optimum bend radius for minimal rope fatigue and all winch drums also incorporate a split drum system for storage.
M3 rope sheaves are custom machined for low friction and low rope fatigue and are heattreated and fitted with the highest quality roller bearings to give smooth operation and a long service life.
Their hydraulic valve chests are specifically designed for optimum flow with minimal loses and minimal heat generation and quality valves are used with a proven history of reliability.
• Inbuilt fail safe, unmatched line speed and pulling force.
• Fully proportional remote controls
• Fully synchronised rope tension with infinitely variable control for operator from
• Cabin or remote-control unit
• Simple one lever control for ease of use and low operator fatigue
• Slack rope sensing
• Winch drum cameras.
• Base machine movement sensing
• Non-invasive fitment to base carriers
For more information, please contact. RJ Fukes Forestry Services on
+44(0)1550721641 www.rjfukes.co.uk
John Deere is rolling out its first H Series wheeled cutto-length forest machine models. The large size class machine models – the 1270H and 1470H harvesters and the 2010H and 2510H forwarders – are making their debut at a launch event in Helsinki on April 24, 2024. The forwarder size class is new and includes the 20-ton load capacity 2010H and the 25-ton load capacity 2510H forwarders.
The high-performance engine of the new H Series harvesters has 10% more power and torque. New hydraulics with three dedicated pumps offer more hydraulic power and higher work pressure for feeding. The optimized system ensures balanced fuel economy. The new Active Frame Lock brings more stability, whether working on steep slopes or flat ground. This makes it easier to work when the boom is sideways and
gives the operator a larger working area.
Compared to the G Series, H Series harvesters enable significantly increased productivity and remarkably lower fuel consumption per harvested cubic meter.
New harvester booms. The new H7 boom for harvesters offers approximately 10% more lift power and slewing torque. The new H9 boom also has the same 10% increase in lift power, and the slewing torque is 5% more than in the previous model.
John Deere’s large size class H Series harvesters 1270H and 1470H feature a new rear chassis and new placement of the engine, hydraulic oil and fuel tanks, and pumps. The design of the machines reflects John
Deere’s collaboration with BMW Design Works. In both harvester models, the engine has been turned 180 degrees, the hydraulic oil and fuel tanks, and the pumps have been placed at the front of the engine, and the cooler and the fan at the rear of the machine. The changes make the cabin very quiet. At the same time, the back of the machine has been lowered, significantly improving rear visibility. The new cabin has increased the rotating angle by 30 degrees to each side. Altogether the cabin now rotates 220 degrees. The rotating and levelling cabin is now standard in the large H Series.
The benefits offered by the Intelligent Boom Control have been acknowledged since 2013. The popular and unique IBC 2.0 is now a standard feature in our large H Series harvesters. John Deere is continuing to develop IBC technology.
Cylinder frame lock, torque, kNm
The new design in large size class forwarders – 2010H and 2510H – share the same new engine space and the hood designed in collaboration with BMW Design Works.
The new large size class 20-ton and 25-ton forwarders offer 25% more load capacity. The new twin motor driveline in the 2510H forwarder also offers a 50% faster driving speed. The twin motor driveline is also an available option for the 2010H forwarder.
The new booms, F9 and F10, offer more power and longer reach. The F10 has a new longer reach of 10.2 meters. The corresponding longer reach in the F9 boom is 10.7 meters. The
hydraulic hosing and hose routings have been improved. The new F10 is the strongest forwarder boom in the market. With the 40% increased boom lift torque and 22% higher slewing torque, larger grapple options are now available. The new F9 boom has 13% more boom lift torque and 10% more slewing torque.
The new geometry of the booms, five joint connections between the main boom and jib boom, provide better controllability and load handling accuracy and a more constant speed for the whole loading cycle. To facilitate working on steep slopes, the backwards tilt angle is 22 degrees to the rear, which improves the slewing function of the boom.
The new frame lock brings more stability, even with a full load. The new cylinder-based frame lock enables stability in forwarding the big loads over long distances.
New solutions for eucalyptus forwarding. Our offering includes an extra-long rear frame suitable for 7.2-m eucalyptus. The new eucalyptus headboard is a more durable and stronger design. The main headboard is rigid, and the separate upper headboard moves hydraulically.
IBC 3.0 with automated functions – back to bunch, back to load and automatically to transportation mode – is now standard in the large H Series forwarders.
From intuitive interfaces to ergonomic designs and from the quiet cabin to accessible service points, every aspect is crafted to enhance the operator’s experience and ease of use. John Deere understands the value of minimizing fatigue and preserving energy for what truly matters. The cabins support the well-being of harvester and forwarder operators, and ergonomics play an important role in productivity.
The new cabin design is based on operator feedback. The modernized cabin design is matched to the design of the H Series machines. Noiseisolating materials are used in the cabin interior. The relocated fresh air intakes and improved climate control ensure a stable temperature in changing conditions. The new H Series comes with more and betterquality lighting for increased visibility around the working area.
The new interior design gives the operator more storage spaces. A phone tray with wireless charger, a place for shoes, and a water bottle, cooler and lunch tray table. Other features include a new secondary display for base machine functions and cameras, multiple charging outlets, new pedal for selecting drive direction, new premium audio system with subwoofer and treble speakers. New armrests and controls and configurable key buttons. Programmable
button joysticks are now available in the H Series harvesters.
New seat options include a leather fabricated seat and a heavy-duty seat. Basic and comfort seats are also available. Seat ventilation is available with all seat options.
John Deere is introducing the new Intelligent Cabin Key - a personal remote key to unlock the machine door now also turns on the PC and TimberMatic control system with operator-specific configurations. The intelligent
Cabin Key can also be personalized for service personnel and trailer drivers, and it includes an immobilizer.
New TimberMatic H automation offers a visually improved, intuitive user interface designed for forestry professionals. The totally new control system supports the operator’s ability to achieve a superior logging performance. The completely redesigned user interface is more straightforward and easily accessible. The H automation
system creates a common and consistent user experience for all forestry products. The new visualisation includes options for night and daylight view. And the info relevant to the situation is shown on the display.
John Deere is introducing the longest service intervals in the market – up to 1000h with John Deere ProtectTM service agreement products.
Daily servicing is made easy. The refill points are all located in the same easily accessible place. All machines have an electric engine oil level sensor and a totally new central greasing system for ease of use.
THE NEW H216 HARVESTER HEAD FOR H1270 AND H1470 HARVESTERS AND TRACKED HARVESTERS. A new two-roller harvester
head, designed for hardwood and softwood applications. The new head is designed for large size class harvesters and will replace the previous H270 head. The H216 harvester head is fully compatible with H Series harvesters and tracked harvesters.
The new H216 harvester head includes a top-saw option,
long processing knives, HD-tilt, standard tilt, a find end laser sensor, and Multispeed feed motors. The saw unit enables using wide, less vibrating, and long saw bars for large trees. The new head is available for the 1270H harvester with 8.6and 10.0-meter boom reaches and for the 1470H harvester with 8.6-, 10-, and 11-meter reaches.
Winning photo features on our front cover and wins a £100 Amazon voucher.
Forestry was not Aarons first choice of jobs. He started out as a commis chef at the University of Stirling in Bridge of Allan. A trainee chef’s wages were not sufficient to fund a young person’s lifestyle in the early eighties, so he began helping his dad, who was a tree surgeon, on weekends and holidays to make up the shortfall.
It didn’t take Aaron long to realise that the wages from the part time work surpassed his full-time work, hence he decision to make a career change. Collaborating with his father developed his chainsaw
skills so he decided to move away from hardwoods and tree surgery, into commercial forestry.
This was a fun time to be working in forestry there was plenty of work felling with skidders or skylines and Aaron soon found himself felling with a local forestry contractor. Although it was hard graft there was great camaraderie within the squads. Aaron furthered his forestry skills spending time on the skidder where he learned how to correctly choker trees and manoeuvre the skidder successfully in off road conditions.
The opportunity arose to work in Germany assisting with the clearing up of windblown timber after recorded winds of up to 138mph had decimated forests. He worked out there for five months and gained valuable felling experience in dealing with storm damaged trees. He also had the opportunity to hone his skills as a machine operator using a Bruunett and Kockum’s forwarder along with a bulletproof Timberjack 380B grapple skidder.
On his return he began work with a skyline squad in and around the Aberfoyle Forest District. Every day was different
as he could be felling, working along with the skyline, or operating the skidder, he enjoyed the variety of work immensely.
In 1994 an opportunity arose to work with the Dick Brothers Ltd from Galashiels who were putting together a skyline team. The skyline work took them all over Scotland and Northern England and they built up an excellent reputation for working to a high standard while being productive.
This was the heyday of Skylining in the UK. James Jones and Sons Engineering had the trailered Alp Skyline, GR Smith had the trailered Timbermaster, the Forestry Commission had the Chapel Hall Skyline and ABS Services at Killin were instrumental pioneers in experimental skyline setups.
Aaron worked with many of these systems including a “first of its kind” A&B Services skyline set-up mounted onto the rear body of a Volvo BM forwarder.
The first time I met Aaron was in 1999 and it was in Ae Forest in Dumfries and Galloway. I had just started working for the Dick Brothers as well, and we were trialling the new red cab Valmet 860 to see how it would perform on a long steep climb. The timber was at the bottom of the valley and had to be taken up to the top by a forwarder to be stacked ready for collection to the respective mills.
Aaron was operating the digger winch and had dug out the track I was travelling. It was a versatile tool as it was wired and piped
for attaching a Keto 150HD harvesting head. Once the winched trees started piling up, he would attach the Keto head and process the timber to clear space. He worked this for about four years until a serious fire saw it damaged beyond repair. Aaron then progressed to a Daewoo 220LC-V excavator which was fitted with a Ponsse harvesting head and began to harvest more of his own sites with this harvester.
Aaron’s first purpose-built harvester, a tracked levelling Timberjack 759G with a 758-harvesting head was in 2005. The Timberjack climber lent itself well to the steep terrain and larger sized trees he was harvesting throughout the central belt.
In 2008, after a brief stint working in America, I started back with the Dick Brothers. I got a call to see if I would work in the Trossachs area following Aaron’s harvester, as his regular forwarder operator Sandy McLoed, had been taken ill. Aaron and I worked together for about a year until Sandy returned and had a great working relationship. Jump forward another few years and Aaron found himself with his first new Tigercat, an 845 LH with the LogMax 9000 head. The Timberjack was passed on to another operator who had just joined the company.
As Sandy approached retirement age, he preferred working closer to home, so once again I started forwarding behind Aaron’s harvester. We worked together for the next
four or five years. The Tigercat was replaced with a larger Tigercat, the 855LH with the LogMax 10,000 harvesting head fitted with a top saw. This was particularly useful especially when harvesting snapped storm damaged trees. This saw the end of our partnership as Aaron was destined for a role as a roaming harvester, going from site to site to harvest large and heavily branched trees that wheeled purpose-built harvesters would not look at.
This did not go to plan as the enforcement of movement orders for transporting large equipment made it a bit more difficult to move the Tigercat as frequently as originally intended.
About 4 years ago the 855 was replaced by the smaller Tigercat 822LHD with a LogMax7000 twin harvesting head and this was the one that features in the
winning photo. The photo was taken at an awkward site near Glenample near Lochearnhead in Stirlingshire.
Aaron cannot think of any other work he would enjoy doing more. He has been collaborating with Dick Brothers Ltd for over 30 years and has been fortunate to see some of the best scenery Scotland has to offer. When not working, you will find Aaron in some forest or other, in his other role as a Rally Car Marshall.
Near-natural reforestation and forest conversion
The Moritz felling tractor is the basis for near-natural and sustainable reforestation. The remote-controlled implement carrier impresses with its possibilities, from surface preparation to sowing and planting to surface care.
Attachments for reforestation:
• MAX forestry tiller
• Sowing strip milling machine optionally with plough module
• Plantomat container-planter
NEW
“Sustainable and near-natural reforestation” project
Accompany reforestation work with two Moritz mini felling tractors on a 1.5 hectare calamity area, which will be part of the KWF conference area in 2024 : www.pfanzelt.com
In this Spotlight, Savills report on the performance of the UK forestry investment market during the 2023 forest year (1/10/22–30/9/23). Reviewing the targets and incentivisation for tree planting and focusing on the impacts, mitigation and risk of climate change on the UK’s forests and woodlands.
£96m
7,000
gross area of hectares traded in the 2023 forest year
UK forestry investment in the 2023 forest year -46% less commercial forestry hectares traded in 2023 compared to 2022
Figure 1: Total market value and total market area
Market value (LHS)
Market area (RHS)
Source: Saville Research
A quieter year for forestry investment, but the demands on trees continue
The demands on woodlands and forests are increasing due to the expectations by government and the public that they provide a solution to climate change, improve biodiversity, produce timber for new homes and contribute positively towards wellbeing.
Furthermore, COP26 (2021 United Nations Climate Change Conference) showed that the focus of future timber production should be on plantation forests. This is a clear
justification for investment in productive timber, and in part, has resulted in strong demand leading to rising commercial forestry capital values in recent years. However, the commercial forestry market was less active in 2023 and as a result, for the forest year 2023, we report on fewer transactions. This reduction in activity led to a contraction by volume and value of the market for the first time since 2019 (figure 1). At the time of writing, our analysis suggests an increase in market activity for the 2024 forest year to date, so why the pause during 2023?
It became clear in 2021 that rising inflation would significantly influence investment, with a series of rapid rises not seen since 1990 –the first occurring in December 2021, followed by repeat rises to the peak of 5.25% in August 2023. This period included the market shock from the minibudget in September 2022 coinciding with the start of the 2023 forest year, leading to a marked drop in market activity. Q4 2023, which is out of the 2023 forestry reporting year, saw falling inflation and no interest rate rises, facilitating a return of confidence to forestry and other investment classes.
The commercial forestry market was less active during the 2023 forest year; however, provisional research suggests an increase in market activity for the 2024 forest year.
Urgent action is needed if the target of 17–19% forestry cover for the UK is to be met by 2050.
In a world facing more severe impacts from climate change, proactive woodland management to mitigate impacts can be taken from planting through to harvesting.
Total Market - area and value
Our research on the UK commercial forestry market is based on our database of all forest sales over 50 hectares including, where we are aware, off-market transactions. 2023 follows three years of
exceptional growth in forestry transactions, culminating in a record-breaking year in 2022 when just over £300 million of UK forestry transacted. In contrast, the total value of the UK forestry investment market
contracted by -68% to just under £96 million during 2023. According to our research, this is the lowest total value of commercial forestry sold since 2016, when the total value traded was £90.5 million.
“2023 follows three years of exceptional growth in forestry transactions, culminating in a record-breaking year in 2022, when just over £300 million of UK forestry transacted
- Nicola Buckingham, Associate Director, Rural ResearchSource: Saville Research
In line with the lower value of the market, for the third year in a row, the total area of forestry traded fell by -46% to 7,000 hectares in 2023, which is significantly lower than the tenyear average of around 18,000 hectares.
Further analysis of our transactional database
Source: Saville Research
All forests have unproductive areas such as tracks, rivers and lochs, so it is important to consider the value of the net productive area as this influences future timber
illustrates how long it has taken for publicly marketed properties to sell. Figure 2 shows that during 2021 and 2022 when the forestry market was at its busiest, properties sold faster than other years. Although there were fewer properties sold in 2023 there was a higher proportion of properties that took six months or more to sell, compared to 2021 and 2022.
Less than 6 months
Figure 3 illustrates the exceptional growth in average values recorded in the commercial forestry market over the past decade. Between 2014 and 2023 the average gross value increased by a significant 220% to £18,500 per hectare. In contrast, and in line with a quieter market, the average gross value decreased by -8% per hectare during 2023 from around £20,000 per hectare in 2022.
6-12 months
removals. The average price per net productive hectare dropped by -11% to £25,200 per hectare during 2023. This compares to just over £28,000 in 2022.
The limited sample size makes it hard to draw firm conclusions; however, it is clear that those properties that did sell would have most likely achieved higher prices if sold in the preceding
year, therefore we can be confident market values fell, rather than simply observing a distortion to average values based on the actual properties traded. Among the attributes making forestry attractive is the defensive nature of timber as a
store of value, so it is quite likely we have simply witnessed a pause rather than a change in the course of direction of the asset class, and we are confident that increased buyer activity and rising timber prices will lead to a reversion
in value growth quite quickly. In addition, UK commercial forestry has consistently outperformed other asset classes over the medium to long term (figure 4).
Source: Saville Research
In line with the national trend across all regions, fewer hectares sold but the pattern of
market share and sales activity across them is broadly similar to recent years, with Central Scotland recording the most
hectares sold, closely followed by South Scotland, England and Wales (figure 5).
Figure 5: Forestry transactions and values 2023
Source: Saville Research
• In North Scotland, market activity for commercial forestry was so quiet it is impractical to analyse and report averages for 2023. However, although forestry values are generally lower in North Scotland, the average price achieved quadrupled between 2014 and 2022.
• Central Scotland continues to see the strongest market activity and, for the third year running, recorded the highest number of forest hectares sold across all regions. For the first time since 2016, the annual average value fell to £24,300 per productive hectare.
• South Scotland recorded -44% less commercial forestry hectares sold in
• 2023 compared to 2022. This is, in part, due to the attractiveness of the region for forest ownership, with fewer properties trading because of the desire to hold assets here. Average productive values fell to around £26,000 per hectare.
• The number of forest hectares sold across England increased by 84% compared to 2022. However, the market for commercial forestry is small, and the average productive value of properties sold was slightly higher than 2022 at just under £28,000 per hectare.
• There were very few sales of commercial forestry in Wales during 2023, which makes accurate reporting
• difficult. The area traded was -61% lower than in 2022, and the average price per productive hectare fell to £25,300.
This report principally focuses on average values of commercial forestry transactions; however, it is important to note the market is diverse and average values hide regional and local variations. The average value per hectare is influenced by factors such as the location, size, species, age and purpose of the properties sold in each region during each year. As a result, due to the smaller number of properties sold during 2023, caution must be taken when interpreting and comparing this year’s average values per hectare.
There’s no doubt that it is becoming more of a challenge to protect our forests and woodlands from a growing range of tree pests and diseases.
One fungus that has cropped up in a few headlines is Curreya pithyophila, which we know can affect our national tree – the Scots Pine.
Scottish Forestry’s Tree Health Policy Officer, Flora Donald, answers some of the key questions about Curreya pithyophila and whether we need to be worried about it at this stage.
IS THIS A NEW TREE DISEASE TO SCOTLAND?
Well – it’s not a straight answer – you could say yes or no!
The impacts we’re noticing are new but the ‘disease’ is really a symbiotic fungaladelgid complex involving two native species and a previously rare fungus called Curreya pithyophila, which was actually first mentioned as occurring in Scotland way back in 1907.
It encases populations of our native pine woolly adelgid (Pineus pini) on tree branches, protecting the aphid-like insects from predation. The adelgid nymphs feed on the branch tissues and then, when they drop off, the wound sites are colonised by a secondary,
native, canker-causing fungus called Crumenulopsis sororia. A few records of Curreya pithyophila in association with P. pini were made in the 1960s in Deeside and Moray but the widespread distribution and cankering we’re now seeing is new.
Genetic analyses funded by the Plant Health Centre revealed two genetically different types of C. pithyophila are present in Scotland so we’re supporting researchers at Forest Research and the Royal Botanic Garden Edinburgh to explore if this could explain why the fungus is now more common.
Work is also underway to date the cankers and find out if they became more prevalent in different parts of the country at the same time.
It’s been found across mainland Scotland including parts of the south-west, north-west, east and central belt.
Only one other site has been found in the rest of the UK, in Devon. Samples sent to Forest Research last year confirmed C. pithyophila is present on a range of site types where Scots pine grows including native woodland, commercial, and amenity plantings, as well as in the Caledonian pinewood.
All confirmed findings found over the past two years have been on Scots pine (Pinus sylvestris). Historically, C. pithyophila has been reported to occur occasionally on spruce and fir trees in Britain, although no verified records exist for these observations. Our Tree
Health Officers will help Forest Research look for symptoms on these species over the summer but there’s currently no evidence to suggest it’s causing problems on these trees.
Trees planted in suitable conditions still grow well. The fungal-adelgid complex causes progressive dieback of branches in the lower crown. Young Scots pine growing on wet sites they are poorly suited to appear to be the most vulnerable. We’re funding further research this year to understand the likely impacts of C. pithyophila
across Scotland more fully, including the importance of climatic conditions for fungal establishment and spread.
As ever, we ask woodland managers to become familiar with the symptoms on Scots pine which are present as black cankers, often at shoot junctions, with multiple cankers on the same branch. Photographs of symptoms and some interim management recommendations for those intending to plant Scots
pine are published in a blog and project report on the Plant Health Centre website. Forest Research’s Principal scientist – pathology, Sarah Green, also released a video on WoodlandsTV called “How to identify Scots Pine Fungus Curreya pithyophila”.
No specific action is required for Scots pine stands showing symptoms of C. pithyophila but we encourage everyone to report their sightings to TreeAlert so we can build up a wider picture of its distribution and impacts.
www.forestry.gov.scot
France’s agriculture ministry plans to subsidise tree felling and ease regulations on biomass burning as part of a push to stop the spread of bark beetle, a voracious pest decimating French forests whose spread has been boosted by global warming.
Since 2018, successive droughts and high temperatures in northeast France have made trees more vulnerable to beetle attacks, sparking massive mortality of spruce and fir, with an estimated 110,000 of the 520,000 hectares of forest in that region infested.
To contain the insects’ spread, France will finance preventive felling of trees and debarking
equipment, make it easier to burn infested wood for biomass, and help sell timber that has been infested but is still usable. Debarking felled trees in atrisk areas can help stop the beetles’ spread by preventing freshly felled healthy trees from becoming new breeding grounds.
The government will subsidise timber companies’ acquisition of felling-debarking equipment, which debarks trees as they are cut, funding up to 65% of the cost up to 8,000 euros ($8,510) per unit.
“The more advanced the infestation is, the less effective control measures are,” the ministry said in a statement. The government is also setting
up national and regional crisis units to better map and control the insects’ spread.
Spruce and pine are widely used for construction, furniture and paper. The ministry said that when identified at an early stage and felled at the right time, bark-beetle infested wood is perfectly suitable for construction. For wood that can no longer be used as timber, the government will ease regulations on burning it in biomass-fueled power or heating plants, allowing wood to come from regions further away from the burning site.
It will also boost state support for replanting forests.
($1 = 0.9401 euros)
MAN has become the first commercial vehicle manufacturer to send an autonomous truck onto the German motorway. On board of the test truck, which drove around ten kilometres on the A9 between the Allershausen and Fürholzen junctions, were Federal Transport Minister Dr Volker Wissing and MAN CEO Alexander Vlaskamp.
MAN has been intensively driving forward the development of autonomous trucks for use in logistics hubs and for hub-to-hub traffic on motorways for some time and recently became the first commercial vehicle manufacturer to receive a Level 4 test permit based on the law on autonomous driving on German motorways.
Freight volumes and, in particular, transport between logistics hubs – such as the warehouses of large online department stores – are growing steadily. The use of autonomous trucks in this socalled hub-to-hub transport is particularly suitable for this. The trucks are always on the road, extremely efficient in terms of consumption and safe to drive. There are no driving time breaks, so the vehicles can be perfectly integrated into tightly synchronised logistics processes. In the long term, the efficient use of autonomous trucks can
reduce overall operating costs by ten to 15 per cent. The new technology can also alleviate the driver shortage. There is already a shortage of up to 100,000 truck drivers in Germany alone.
”The first Level 4 test drive of an autonomous truck on a German motorway proves that Germany has taken a leading position in Europe with the law on autonomous driving. Our goal is to become the leading market for automated and connected driving. Today is a milestone for logistics in Germany. The ever-increasing volume of transport, coupled with the worsening shortage of drivers, is a challenge for society as a whole. Autonomous trucks can help to alleviate the situation. In addition, the intelligent networking of freight transport offers the opportunity to make transhipment from road to rail more efficient and
thus strengthen climate-friendly combined transport”, says Dr Volker Wissing, Federal Minister for Digital Affairs and Transport.
“Today we are taking another big step towards autonomous commercial vehicles, the second major future field alongside the switch to CO2-free drives. This year, we are initially running tests with prototypes on the motorway. Further hub-to-hub projects will follow from 2025, but then in typical customer applications. We are thus taking the next development step towards series production of autonomous trucks towards the end of the decade. The law on autonomous driving gives our industry the necessary planning security. To realise autonomous driving, however, we also need to work closely with infrastructure operators such as Autobahn GmbH. Only together can we put autonomous driving
on the road,” says Alexander Vlaskamp, Chairman of the Executive Board of MAN Truck & Bus SE.
“Autobahn GmbH des Bundes plays a central role in autonomous driving on German motorways,” explains Dirk Brandenburger, Technical Managing Director of Autobahn GmbH des Bundes. “We not only approve autonomous driving on certain motorway sections, but also actively promote networking and communication between motorway infrastructure and vehicles with so-called cooperative intelligent transport systems. This is of crucial importance for the authorisation and therefore the safety of autonomous vehicles on the road.”
For the test drive of the first autonomous truck, Autobahn GmbH examined MAN’s concept as part of the application for a test licence before the Federal Motor Transport Authority officially granted MAN approval at the beginning of April. In future, Autobahn GmbH
will also be responsible for approving operating areas on motorways for the series approval of autonomous vehicles. The vehicle operator specifies the routes on which its vehicles with autonomous driving functions are to drive, and Autobahn GmbH then checks whether these routes are suitable for the operation of these vehicles with autonomous driving functions.
MAN has been driving autonomous driving forward for many years with various research and development projects. From 2017 to 2019, MAN developed and tested electronically coupled trucks in a joint research and development project with DB Schenker. These particularly safe and fuelefficient platoons were used for more than six months in regular general cargo transport on the A9 motorway between Neufahrn and Nuremberg. From 2019 to 2023, the ANITA project with partners Deutsche Bahn, Fresenius University of Applied Sciences and Götting KG focused
on the complete digital integration of an autonomous truck into the logistics process of container handling from road to rail. And since 2022, MAN has been working together with Autobahn GmbH and other partners from industry, science and technical testing in the ATLAS-L4 project to develop an autonomous truck for use in motorway transport between logistics hubs. The project is thus specifically implementing the law on autonomous driving passed in Germany in 2021, which already allows driverless driving on clearly defined routes and with technical supervision. Practical test drives of the prototype with a safety driver on the motorway are planned at the end of the project. To date, MAN has filed 133 patent applications in the field of autonomous driving, 33 of which have already been granted. By participating in the @CITY, BeIntelli and MINGA projects, MAN is also involved in the development of automated driving for city buses. www.man.eu
Sections of highway in southern Germany for which MAN has received approval from Autobahn GmbH for Level 4 test drives with an autonomous truck
SCA’s first electric timber truck is a Scania with a technical capability of up to 70 tonnes total weight. SCA is Europe’s largest private forest owner and maker of sawn wood products, packaging materials and pulp.
Every year, SCA transports about 8.5 million cubic metres of wood to industries. By running just one electric truck between their terminal in Gimonäs and its papermill in Obbola, the reduction of carbon emissions is about 55,000 kg per year.
The timber truck has been operational for two years now. “It is going very well,” says Mikael Sundelin, Head of Business Development at Industrial Supply, SCA Skog. “We have also tried using the truck to collect timber in the forest, and
it was a very successful trial.
“Therefore, we feel it is time to take the next step in electrifying our heavy transports together with Scania,”
Unlike the electric timber truck in Umeå, the new truck will be equipped with a crane, which is common for most timber trucks collecting timber in the forest.
“Our new electric timber truck has a better range and will drive to timber storage areas in the forest where it loads the timber for further transport to one of our timber terminals. We expect the truck to reduce carbon dioxide emissions by 170 tons per year compared to a regular timber truck,” says Anton Ahlinder, Business Developer at Industrial Supply, SCA Skog.
The truck will be owned and operated by a haulage company with whom SCA has a close partnership.
“We support the haulage company, but they will be the owners of the truck. We do the same with our conventional timber transports, and we want more haulage companies to dare to transition to electric vehicles when it becomes possible,” says Anton.
The exact location where the truck will operate will be announced later. Currently, Scania is manufacturing the truck, and then they will conduct some tests on it before it is delivered to SCA and the haulage company for inauguration and operation in the fall.
www.sca.com www.scania.com
Kesla is the leading expert in modern truck-mounted and industrial cranes. Based on decades of experience in the field, we know how challenging the working conditions can be. That’s why we always put the user first, offering the best ergonomics and usability for the most demanding needs, never compromising on responsibility.
Howie Forestry Solutions +447792 804273 www.howieforestry.co.uk adam@howieforestry.co.uk
Mark Beach Forestry Engineer +44 7502 484198 http://www.markbeachforestry.co.uk mbforestry@yahoo.co.uk
www.kesla.com
ZF have two types of transmissions available for forestry, stepless low emission and fuel efficient CVT transmission and their zero emissions eTrac.
It operates at lower engine speeds which increases forwarder and skidder operators comfort while increasing overall efficiency. The CVT transmission offers much more tractive power for safer operation on steep slopes and is beneficial when working on soft ground conditions or in deep snow. Heavy loads, continuously adjustable speed and easy manoeuvrability – the fully power-split CVT (Continuously Variable Transmission) technology of the cPOWER combines these characteristics with improved fuel consumption of up to 25 percent. The cPOWER operates at low engine speeds, thus increasing
efficiency and driver comfort in forestry equipment like forwarders and skidders even more.
The fully powersplit, continuously variable technology benefits from the long-term experience gained in the agricultural machinery sector and offers significant consumption benefits as well as productivity increases for the vehicle owner.
The cPOWER transmission series deploys well-known and -proven construction kit modules and benefits from ZF competence in transmission and vehicle system engineering.
High loads at low speeds in combination with high dynamic are the outstanding requirements for off-highway machinery. These criteria are met optimally by the new ZF CVT transmission technology
with a degree of efficiency that was inconceivable up to now.
• Continuously variable drive over complete drive range forward and reverse
• Smooth, hydraulic start due to continuously variable power-split technology
• High efficiency through low engine speeds, independent of vehicle speed
• Up to 25 percent less fuel consumption
• Also available for Wheel Loader, Grader and Material Handling
Not only in wheel loaders does ZF’s cPOWER transmission help reduce fuel consumption and increase productivity. Also in other applications a trend towards lower engine speeds and the demand for engine stabilization by a constant speed concept are the future challenges.
The continuously variable cPOWER meets both requirements.
As for forestry equipment, ZF is already supplying the cPOWER transmission design for the skidder and forwarder applications
1. cPOWER CP210 Engine power 228hp, Engine RPM governed to 1800, Empty weight 19,000kg Payload 14,000kg
2. cPOWER CP230 Engine power 255hp, Engine RPM governed to 1800, Empty weight 21000kg Payload 16,000kg
3. cPOWER CP260 Engine power 281hp, Engine RPM governed to 1800, Empty weight 23,000kg Payload 18,000kg
4. cPOWER CP290 Engine power 335hp, Engine RPM governed to 1800, Empty weight 25,000kg Payload
• 20,000kg
This is a newly launched low noise level, zero emissions electric drive system with a two speed powershift transmission for forestry. It also features an electric motor and inverter along with an ePTO to run the working hydraulics.
It is the “best in class” solution for power density with efficient electrical components, integrated park brake and a robust mechanical driveline. Regardless of whether full-tree or cut-to-length applications, ZF is already seeking into zeroemission drivelines for forestry equipment today. In addition to the eTRAC electric central drive, system supplier ZF offers the associated power electronics as well.
CENTRAL
• One supplier for transmission, e-motor and inverter
• Available for various vehicle applications
• 650 V with up to 80 kW of continuous power
• Liquid cooled PSM e-motor
• 2-speed powershift transmission
• Integrated park brake
• Optional axle disconnect (2WD/4WD)
This system can be integrated into both battery electric vehicles and fuel cell battery electric vehicles which are playing a big role in the future of forestry and construction vehicles. www.zf.com
Forest Machine Magazine assumes no liability or responsibility for any inaccurate information, errors or omissions. Forest Machine Magazine considers its sources reliable and verifies as much data as possible. However, reporting inaccuracies can occur and consequently readers using this information do so at their own risk. The opinions expressed in each article are those of its author and do not necessarily reflect the opinions of Forest Machine Magazine. Therefore, Forest Machine Magazine carries no responsibility for the opinions expressed thereon. Through the magazines you are able to link to other websites which are not under the control of Forest Machine Magazine. We have no control over the nature, content and availability of those sites. The inclusion of any links does not necessarily imply a recommendation or endorse the views expressed within them.
No part of this publication and/or website may be reproduced, stored in a retrieval system or transmitted in any form without prior written permission of the Publisher.
© 2024 Forest Machine Magazine. All rights reserved.
Only around 15% of Germany’s surface area is built up, with most of the country covered by agricultural land and forests. In these areas, fires can spring up anywhere. And when they do, the fire service needs to get there. And the federal state of North Rhine-Westphalia is no exception. The voluntary fire service in Bad Salzuflen is prepared for any terrain and requirements: its extreme offroad Unimog U 5023 is used as a tanker fire-fighting vehicle both on the road and off-road, and even takes part in towing races!
The decision to opt for the Unimog was made based on a wealth of experience: Andre Schüler knows all about the challenges of working as a firefighter in the North RhineWestphalian district of Lippe – and also the reliability that the Unimog stands for. After more than 30 years in active fire service, Andre Schüler has been responsible for technology, procurement and logistics at the Bad Salzuflen fire service for five years.
FEATURES, GOOD PARTNERS.
When purchasing the extreme off-road Unimog with the 3000 VARUS tank fire-fighting vehicle body, particular attention was paid to its suitability for firefighting operations in the event
of forest fires – and therefore to the vehicle’s off-road capability. After a Europe-wide tender, a decision was made to go with a Unimog U 5023 demonstration vehicle. For Andre Schüler, the decision was clear: “this Unimog was a worthwhile purchase for many reasons: not only because of its features, but also because of the shorter waiting time.”
The fire service professionals were able to rely on the Unimog professionals for the project’s implementation: RKF-Bleses GmbH, the Unimog general distributor for the Westphalian region and the Rhineland, took care of this while Schlingmann adapted the fire-fighting body to the fire service’s needs.
So when the Unimog then first arrived at the Wüsten site in 2021, it had a wide range of extinguishing and rescue tools at its disposal: with its 3,000-litre tank and S3000 centrifugal fire-fighting pump
from Schlingmann, the Unimog is not only able to effectively supply water when fighting fires, but is also indispensible for creating water barriers.
IMPRESSIVELY ADAPTABLE.
The Unimog’s pump-and-roll function ensures a constant water supply and is now fitted as standard in many fire-fighting vehicles. In addition to the four front spray nozzles, the tank fire-fighting vehicle is also able to fight fires using a fog nozzle through the roof hatch. The vehicle also features a folding water canon mounted on the roof, which can be activated and operated from the cab.
The ability to overcome uneven terrain and steep slopes is also crucial when fighting forest fires. With its all-wheel drive and portal axles providing exceptional ground clearance, this is no problem for the Unimog. Whether on a motorway, muddy country lane or steep forest road – with the
TireControl plus tyre pressure control system, emergency services can adjust the tyre pressure to different terrain conditions in seconds.
The Unimog guarantees optimum performance with maximum off-road capability, all the while remaining unaffected by fires: all lines under the vehicle are fire-resistant, enabling fire fighters to continue driving the vehicle even in the most critical of situations. What’s more, when they need to reverse, the video reversing system provides a clear view of their surroundings, enabling them to drive quickly and in a controlled manner.
Since the fire service in Bad Salzuflen needs to be ready to work in all light conditions, the Unimog is equipped with ambient lighting. The pneumatic light tower with its four LED spotlights makes even a forest in the middle of the night shine as bright as day. On top of all this, full use has been made of the Unimog’s high transportation capacity, with the vehicle well equipped with extinguishing agents. The Unimog also comes with the latest communication technology, mobile radios and standard-compliant equipment such as hand lamps, first aid equipment, protective blankets and slings – or, as Andre Schüler sums it up succinctly, “we’ve got absolutely everything on board.”
Since the fire service in Bad Salzuflen also regards the Unimog as a multifunctional allrounder, it has tried to use the
vehicle for as many applications as possible. “In order to further increase the value of the vehicle, we equipped the Unimog with a submersible pump”, explains Andre Schüler. This is particularly useful in storm and flood applications,
for example when we need to pump cellars dry. The fire service can also rely on a telescopic loader that can be used in combination with the Unimog to quickly clear roads and paths of mud and debris. Unimog
BSW Timber won the Local Community and Social Value award at Friday’s (22/03) Scottish Timber Trade Association’s Awards 2024.
The award was presented to an STTA organisation that best demonstrated the contribution and social value of their business within a local community.
BSW won the coveted award for community work undertaken by its Fort William site, in which 200 employees were involved in three large community projects.
The projects included creating a useable low maintenance
garden space for elderly residents of a care home in the town. Creating an access road that was suitable for vehicles to be able to park close to a mental health charity in Fort William and designing and installing an outdoor decked area with wheelchair and buggy access for patrons of “The Caddy Shack” restaurant at the nearby Fort William golf course.
Oliver Stephen, Mill Manager, BSW Timber Fort William, said: “It was fantastic to be recognized by the industry for the community work we have done. BSW in Fort William, is one of the main employers in the area and we are proud to be able to give back to the
community where we can.”
In total 25 people from the site played a role in the completion of these three key community projects. With over 500 members of the local community benefiting, some daily, from the completion of the projects.
The awards were held at The George, in Edinburgh and were attended by representatives of member companies of the STTA. The STTA is an industry group that represents those who supply timber and wood products in Scotland, including importers, sawmillers, timber merchants, timber agents, builders’ merchants, and others.
Agroup of Swedish landowners visited our Lockerbie site last week as part of a tour of Southern Scotland looking at rural land use. Many in the group have been involved with timber supply and we discussed species choice, rates of growth, timber processing capability and logistics in relation to the forest product supply chain the UK. We also discussed the scale of sawn timber imports into the UK and the impact this has on our
www.jamesjones.co.uk
This years much awaited KWF Tagung will take place on the 19-22 June in Schwarzenborn/Hesse which is about a one and a half hour drive from Frankfurt Airport.
2024’s KWF is the World’s Largest Forestry Demo Event and Industry Meeting. The previous KWF was postponed due to Covid, but I visited the event in 2016 and found it to be one of the best represented events I have ever attended.
Open from 9am to 6pm every day and features;
• Forestry Technology Solutions for Timber Harvesting and Timber Logistics – LIVE
• Timber transport – efficient and resource-saving
• Safety Tools & Apparel
• Municipal Technology, Components, Tools and Accessories
• Solutions for all sizes of forestry operations
• Comprehensive presentations of bioenergy/ firewood technology
Plus special shows – which include these current topics:
• Follow the timber -> Tracking and tracing in the timber supply chain
• Integrated forest fire management > Before –during – after forest fires
• Forests – Insects – Damage -> Insect Pest Groups –Monitoring, Prevention and Control
• CampusForst – researcher for forestry -> Showcasing of
• Forest Science
These will take place in forests close to the KWF-Expo from the 19th to the 21st (no excursions on the final day) from 9am to 6pm and include;
Neutrally moderated practical demonstrations with technology demonstrations from neutral experts
There will be more than 30 complete work chains in practical operations with new working methods that have been tried and tested in practice.
Modern forestry technology tested by the KWF will be shown in use and complete work chains will be demonstrated in real operations. There is information on a number of new and best practices. The focus of the topics is on the environmentally friendly use of technology, energy wood production, logistics chains and forest protection. Neutral experts are available to discuss operating conditions and costs.
In order to ensure everyone’s safety, please note that helmets are mandatory on the excursion.
With an excursion card, a shuttle service will take you from the
expo to the excursion and back.
• Excursion Topic 1 will feature area preparation and establishment of the timber stands
• Excursion Topic 2 will include inventory management
• Excursion Topic 3 features harvesting
• Excursion Topic 4 will deal with special topics including - INTELLIWAY –Intelligent Roads – Condition Monitoring and Predictive Maintenance for Forest Roads, ForestSatCert, Digitisation of detailed development, Passive exoskeletons in forestry operations and Timber harvesting and road construction methods including water retention.
The purpose of the congress is to impart knowledge in an application-oriented manner, by means of specialist lectures and discussion forums.
In terms of content, the three major topics of climate change, silviculture and wood as a resource, technology and processes as well as forests and society are dealt with.
The main focus of all formats and content is on operational implementation, i.e. on applicability in practice.
In addition, the content depicts individual facets of the megatrends of climate change, digitalization and social transformation.
Formats within the framework of the KWF Congress:
• Lectures
• Professional and political panel discussions
• Short presentations on projects and new developments (company contributions) in the form of the Future Workshop.
In 2016 it was a huge event with
over 500 exhibitors spread over 145,000m² and 30 excursion points, over 50,000 visitors.
My tickets and accommodation are booked and I am looking forward to seeing what this years event has in store. www.kwf-tagung.net
The lubricant experts from Zeller+Gmelin are presenting their complete range of high-performance lubricants for agriculture and forestry at the world’s largest event for forestry work and technology, the KWF-TAGUNG. A highlight is Divinol SynthoHyd Eco 46, a fully synthetic and biodegradable multigrade hydraulic oil for use in environmentally sensitive areas. The programme also includes other Divinol organic hydraulic oils and AquaChainFluid, an organic chain oil.
Zeller+Gmelin has expanded the existing product portfolio of organic hydraulic oils for environmentally sensitive areas with a polyalphaolefin-based product: Divinol SynthoHyd Eco 46 is particularly suitable for highly loaded hydraulic units, for large mobile machines or stationary applications and is the result of intensive research and development work. Thanks to the high-quality zinc and ash-free additives, excellent corrosion and wear protection is guaranteed.
The new PAO-based premium organic hydraulic oil is in no way inferior to the traditional variants of organic hydraulic oils based on saturated esters and enables the longest oil change intervals as well as excellent low and high temperature behaviour. Since it uses both mineral and esterbased products, users benefit from a simplified re-oiling of the machine. One of the most important advantages is that the Divinol SynthoHyd Eco 46 behaves like a mineral hydraulic oil towards hose materials and seals, i.e. the customer does
not have to replace any hose materials regardless of what type of hydraulic oil is used - Divinol SynthoHyd Eco or mineral hydraulic oil. The package is rounded off by improved water compatibility, filterability and venting time, as well as reduced formation of oil sludge.
Overall, the advantages mentioned result in significant savings potential in operating costs and greater flexibility with regard to the use of the fleet. The organic hydraulic oil is tested according to OECD 301 B
and meets the requirements of the EU Ecolabel and the Swedish Standard.
With Divinol HE 32 and Divinol HE 46 as well as Divinol SynthHyd Eco 46, the lubricant manufacturer is also presenting three biodegradable hydraulic oils that, according to the manufacturer, are ideal for efficient continuous operation in forestry and agriculture. These hydraulic oils are formulated based on synthetic esters and are easily biodegradable in accordance with OECD 301 B and have been awarded the EU Ecolabel.
“For us, the KWF conference is the most important event on the topics of forestry and wood. We are deliberately visiting them this year as a manufacturer of high-quality lubricants for environmentally sensitive areas, which continually set new standards in terms of sustainability and environmental friendliness,” emphasizes Michael Peter, product manager for lubricants at Zeller+Gmelin.
Zeller+Gmelin is bringing a whole range of lubricants to Schwarzenborn that are ideal for environmentally sensitive areas. When it comes to performance, the products always meet the highest requirements. Such as the Divinol Bio-Kettenöl HV (organic chain oil) for wood harvesters, which can be used all year round and will also be on display at the trade fair. It impresses with its high viscosity
and excellent lubricating properties.
We will also be presenting our chain fluid at the trade fair: the Divinol AquaChainFluid. It is a biodegradable, water-based, high-performance saw chain fluid for chainsaws. Compared to conventional chain oils, the use of AquaChainFluid results in a minimal release of substances into the environment due to loss lubrication on the chain. This not only protects the environment, but also resources.
“Trade fair visitors can also get an idea of our wide range of Divinol high-performance lubricants, such as the Divinol Zweitaktöl FF (two stroke oil) or the two lawn mower oils Divinol Spezial-Rasenmäheröl HD 30 (special lawn mower oil ) and Divinol Rasenmäheröl 10 W-30 Spezial (lawn mower oil) ,” adds product manager Michael Peter. He also has the Divinol Bio-Kettenöl R (organic chain oil) inhis trade fair luggage, which is ideal for hand-held chainsaws. Based on renewable ra
w materials, it has been awarded the Blue Angel, the EU Ecolabel, the Austrian Ecolabel and the KWF test mark.
Zeller+Gmelin is an independent, mediumsized family business that was founded in Eislingen in 1866. Over the decades, ZG has developed into an international partner for highquality lubricants for industry, vehicles and machines as well as printing inks and chemical products. With around 1,000 employees and 16 subsidiaries worldwide, Zeller+Gmelin delivers to 80 countries around the world and, in addition to Eislingen, has a production location in the USA, China and Great Britain. The company has been working successfully on reducing its ecological footprint for years and, the research and development departments are continuously working on innovative solutions that reduce the burden on the environment and improve customer processes. www.zeller-gmelin.de
ROTTNE RAPID YEAR 1996 - 23516 hrs
Suit thinnings working width 2770mm
Headboard to bunk 4400mm
Machine weight 15 ton - 10 ton load capacity
NOKIAN 600 tyres good condition
Just been trough workshop for welding repairs to bunk, pins bosses bushes on top of kingpost and crankshaft oil seal
Overall very good condition for age
Price £25,000 plus vat
Clark climbing tracks available extra for negotiation
Any enquiries please call David Wilmer on 07879417170 / 01465 811600 option2 or email stores@jimwilmer.co.uk
Valtra 6550 tractor - Year 2004
9000 Hours
c/w Botex XL Pro 14 Timber Trailer Year 2019 and Botex 570C Timber loader Year 2019
Takes 2 x 3M lengths of timber
Cost £38,500 + Vat o.n.o.
Telephone 07967 588739
Ponsse Elephant Timber Forwarder
Year 2014 - 9600 Hours ( Very low for its age)
Full service history from Ponsse UK Ltd
Last serviced December 2023
Balanced Bogies
One set of tracks
Location County Durham, England
£110,000.00 + Vat o.n.o.
All serious offers considered Ready to go to work
Telephone 07967 588739
VALMET 840 black cab year 1994 - 28435 hrs
Canab crane - 700/50 26.5 tyres
Just had engine rebuild, centre joint done and front hub seal
Floatation tracks available at extra negotiation
Overall good condition for year
Price £19000 plus vat
Any enquiries call David Wilmer on 07879417170 / 01465 811600 option 2 or email stores@jimwilmer.co.uk
Komatsu 875.1 Timber Forwarder
Year 2021 – first delivered March 2022
2,387 Hours at present
Machine is currently covered by a Komatsu Service Contract
Ready to sell immediately
£250,000.00 + Vat o.n.o.
Telephone 07967 588739
Jim Wilmer & Sons require an experienced harvester operator in the Argyle / South Kintyre area.
Immediate start required.
We can offer top rates of pay, weekly payments and excellent mechanical back up.
For more information contact David Wilmer on 07879417170.
• New and Used Equipment
• Forestry and Arboriculture Sectors
• Cars & Commercial Vehicles
• Refinancing Facilities
Bridie Ward 07498238672
bridie@agcredit.co.uk
luke@agcredit.co.uk
Timberjack 1270C Timber Harvester
Year 2000
26,000.00 Hours worked
c/w Waratah 270H Harvester Head
Year 2014
One owner since 2005
Very good condition for its age
Used daily until recently when a replacement machine was purchased
Engine overhauled recently and new turbo fitted
£20,000.00 + Vat o.n.o.- all serious offers considered
Telephone 07967 588739
John Deere 1270G, 8WD, 2016 YOM - 15,485 hours
NOKIAN FKF 710 45 R26.5 TYRES
D 480C Harvesting Head
CH7 Crane
Overall good condition, harvester with an 11 metre reach crane extension. Tracks available at an additional cost if required.
Price £120,000 GBP Plus VAT
Any enquiries please call David Wilmer on 07879417170 /01465 811600 option 2 or email stores@ jimwilmer.co.uk
John Deere 1470e, 2015 YOM 17,124 hours
NOKIAN FKF 750 55 R26.5 TYRES
JD 480C Harvesting Head
CH9 Crane
Overall good condition, harvester with an 11 metre reach crane extension. Tracks available at an additional cost if required. £70,000 Ono plus vat Any enquiries please call David Wilmer on 07879417170 /01465 811600 option 2 or email stores@ jimwilmer.co.uk
Logset 8H Harvester c/w Logset 8L harvesting Head
Year 2006 - 12000 Hours
£30,000.00 + Vat o.n.o. Telephone 07967 588739
Three quarter drive socket set with extending ratchet
£80. T: Rab 07582 055 748 Near Glasgow
RATED THE WORLDS NO1 FORESTRY MAGAZINE BY FEEDSPOT FOR 2023 & 2024.
GLOBAL SOCIAL MEDIA PRESENCE WITH OVER 800,000 FOLLOWERS
Forest Machine Magazine is up for sale and includes the printed magazine, digital magazine, all social media channels, website, contacts and photo gallery.
This year I will be reaching official retirement age and a lifetime in forestry has left my joints not quite as supple as they once were. So after seven great years of writing and publishing Forest Machine Magazine, it is finally time to hand over the reins. Rab
MAGAZINE
Printed and digital magazine.
SOCIAL MEDIA
Facebook, Instagram, Twitter, Youtube, Linkedin, TikTok and Threads
Website, contacts and photo library.
• Pulling force: from 45kN to 90kN
• 3-plate clutch
• AUTOSTOP
• TERRA Remote control
• Uniforest Connect
• Pulling force: from 65kN to 120kN
• From 4- to 8-plate clutch
TERRA Remote control
• Uniforest Connect
• Pulling force: from 35kN to 85kN
• Up to 3-plate clutch
• Plenty of storage space
• With or without gear reducer