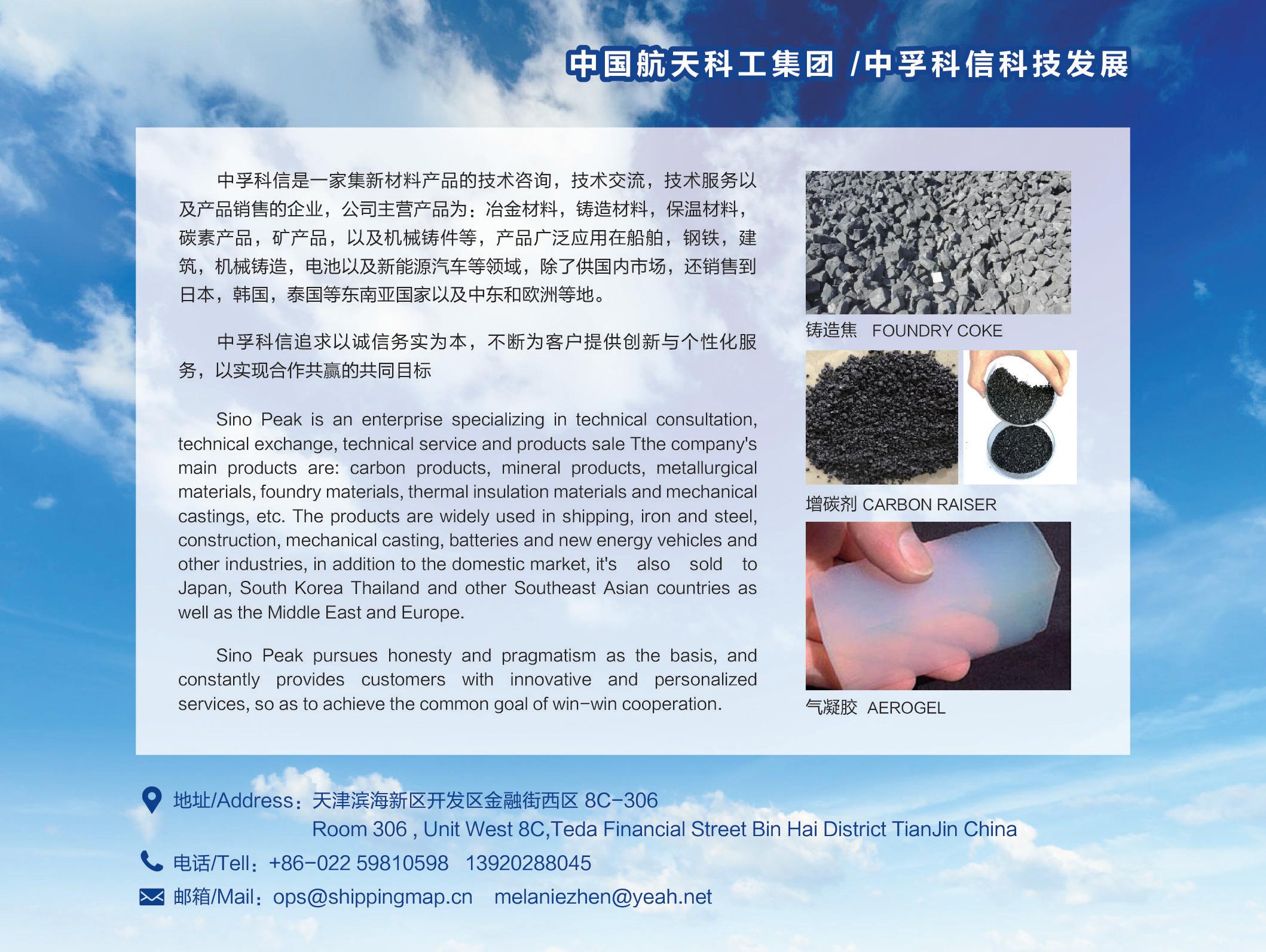
36 minute read
Franken Guss Gmbh & Co. Kg - from Battleship to Frigate
INDUSTRY NEWS / 行业新闻 Franken Guss Gmbh & Co. Kg - from Battleship to Frigate 弗兰肯古斯公司——从战舰到护卫舰
The successful mutation from a stock corporation to family business
Advertisement
Franken Guss will be 100 years old in 2022. In an interview with Wirtschaftsforum, managing director and shareholder Josef Ramthun talks about the "road to freedom" and how his company is adapting to the change in the automotive industry towards e-mobility.
Nowadays, medium-sized family businesses are usually incorporated into a corporate group in the course of their existence, but at Franken Guss GmbH & Co.KG it was just the other way round.
Iron casting and aluminium die casting for customers all over the world
The company was founded in 1922 as Metall- und Schrott AG. After that, it was inseparably linked with the name Sachs, now ZF Friedrichshafen, as a foundry for that company for many years. The forging and casting division was spun off in 2004 and taken over by the American company Metal Technologies. In 2009, the foundry went bankrupt in the wake of the Lehman Brothers crisis. In the same year, Ramthun bought it in a management buyout and continued to run it under the name Franken Guss Kitzingen. "We were able to shed the corporate burden as a result and mutated from a battleship to a frigate, so to speak. Since 2013, we have had a second location in Chemnitz, Sachsen Guss. It is the former foundry of the Siemens Group," says Josef Ramthun in the interview.
Today, Franken Guss has iron and aluminium castings under one roof. For the most part, the company is a supplier to the automotive industry and supplies OEMs, Tier 1 suppliers and end customers worldwide, whereby everything is possible from batch size 1 to series production. The foundry processes punching waste in iron casting, which is sand casting and secondary aluminium in die casting. In the company's technology centre, all possibilities are available to create functioning castings from ideas. Close cooperation between the customer's developer and the foundry enjoys the highest priority. Under the motto "in dialogue to the solution", Franken Guss also offers subsequent finishing, machining and coating as well as partial assembly.
The transformation in the automotive industry becomes clear - High vertical range of manufacture in the company
After the COVID-related lockdown and the associated production losses, things are now gradually picking up again and the order situation is so positive that extra shifts are being run in some cases. The company has taken advantage of the Corona period to acquire new parts for e-mobility and enquiries are increasing in this environment. Franken Guss supports its customers in the transformation and benefits from the high
弗兰肯古斯公司将在2022年迎来100岁生日。在接 受经济论坛采访时,股东、董事总经理约瑟夫·拉姆图恩谈 到了“通往自由之路”以及他的公司如何适应汽车行业向电 动汽车的转变。
如今,许多中型家族企业大多为了生存和发展,在逐步 转入股份制集团机制,但在弗兰肯古斯公司情况却正好相反。
公司成立于1922年,当时名为Metall-und Schrott AG。之后,它与Sachs,现为名为ZF Friedrichshafen 的公司紧密合作,多年来一直是该公司的铸造工厂。接下 来在2004年,锻造和铸造部门被分拆出来,由一家名为 Metal Technologies的美国公司收购。2009年,该铸造 厂受到雷曼兄弟危机波及破产。同年,拉姆图恩先生通过 收购管理层的方式将其买下,随之开始以Franken Guss Kitzingen的名字经营。“我们自此以后得以摆脱企业化 的负担,可以这样概括,我们实现了从战舰到护卫舰的突 变。2013年我们在萨克森古斯的开姆尼茨设立了第二家 工厂,它原是西门子集团的铸造工厂。”约瑟夫·拉姆图 恩在采访中说。
如今,弗兰肯古斯公司将铸铁和铝合金铸件的生产集 中在一起。公司最主要的产品是为汽车行业做配套服务, 为全球的OEM制造商、一级供应商和最终客户提供产品, 从单件小批量生产到大批量生产,所有产品都可生产。铸造 工厂的砂铸铸铁件可使用冲压废料,压铸生产使用再生铝。 在公司的技术中心,大家发挥创造力,设计出符合各种客户 需求的功能性铸件。公司还将客户的开发人员和铸造车间之 间的密切合作作为合作的重中之重,将“与解决方案对话” 这句话作为公司指导方针;弗兰肯古斯公司还提供后续清 理、机加工和涂层以及部分组装和集成服务。
近年受到新冠疫情影响,停产和减产时有发生,而现 在情况正在逐渐好转,订单情况变得较为乐观,甚至于在某 些生产领域开始安排额外的加班来保障生产进度。公司充分 运用疫情时期,为电动汽车生产购置了新的零部件,在疫情 环境下,询盘正在增加。弗兰肯古斯公司支持其客户进行汽 车行业的转型,并从公司高度的垂直制造范围中大大受益。 近年来,为了将有价值的生产环节整合到一起,公司已经
vertical range of manufacture in the company. A lot has been invested in recent years in order to have the value chain under one roof, which is proving to be a great advantage and plus point, especially with regard to developments for e-mobility, because it enables fast and versatile developments.
In addition, Josef Ramthun praises the ambition and commitment of his employees, who are always working on the best solution for customers and also offer special processes and materials for both iron and aluminium. Franken Guss has also taken a big step forward on the key topic of digitalisation and offers a tool named PROLUTION communication tool, that maps the entire value chain from the initial idea to series production capability. Especially in the pandemic period, they have already had very good experiences with this.
The course for the future has been set
Franken Guss wants to continue to be a valued company in the region where people enjoy working. For Josef Ramthun, it is part of the self-image of the successful medium-sized company to manage the company independently and flexibly and to be well prepared for all challenges. This also includes the constant search for suitable skilled workers such as pattern makers, foundry mechanics or plant electronics engineers and training in the company. The children of the Ramthun family are now also working in various positions in the company, a good signal for forward-looking action. ■
进行了大量投资,这已被证明是一个巨大的优势和竞争点, 特别是在电动汽车的发展方面,因为它可以实现快速和多元 化的发展。
此外,约瑟夫·拉姆图恩赞扬了他的员工的进取心和 奉献精神,他们始终致力于为客户提供最佳解决方案,并为 铸铁和铝合金件的生产贡献出不同的特殊工艺和材料。弗兰 肯古斯公司在数字化这一关键理念上也向前迈出了一大步, 并推广使用了一个名为PROLUTION的通信工具,该工具 将整个价值链从最初的创意到批量生产能力贯穿始终。尤其 是在疫情期间,他们已经积累了众多相关丰富经验。
弗兰克古斯公司希望继续成为一家能为大家带来价值 的公司,让员工可以享受工作的过程。对于约瑟夫·拉姆图 恩来说,目前这家成功的中型公司自我形象的一部分正在 于,可以独立灵活地管理公司并为所有挑战做好充分准备, 这包括不断寻找合适的技术工人,例如模具制造工、铸造机 械技术人员或车间电子工程师以及在公司开展培训。拉姆图 恩家族的后代们现在正在公司的各个岗位上工作,这是一个 可以预见的、能延续公司制度和传统的良好信号。■
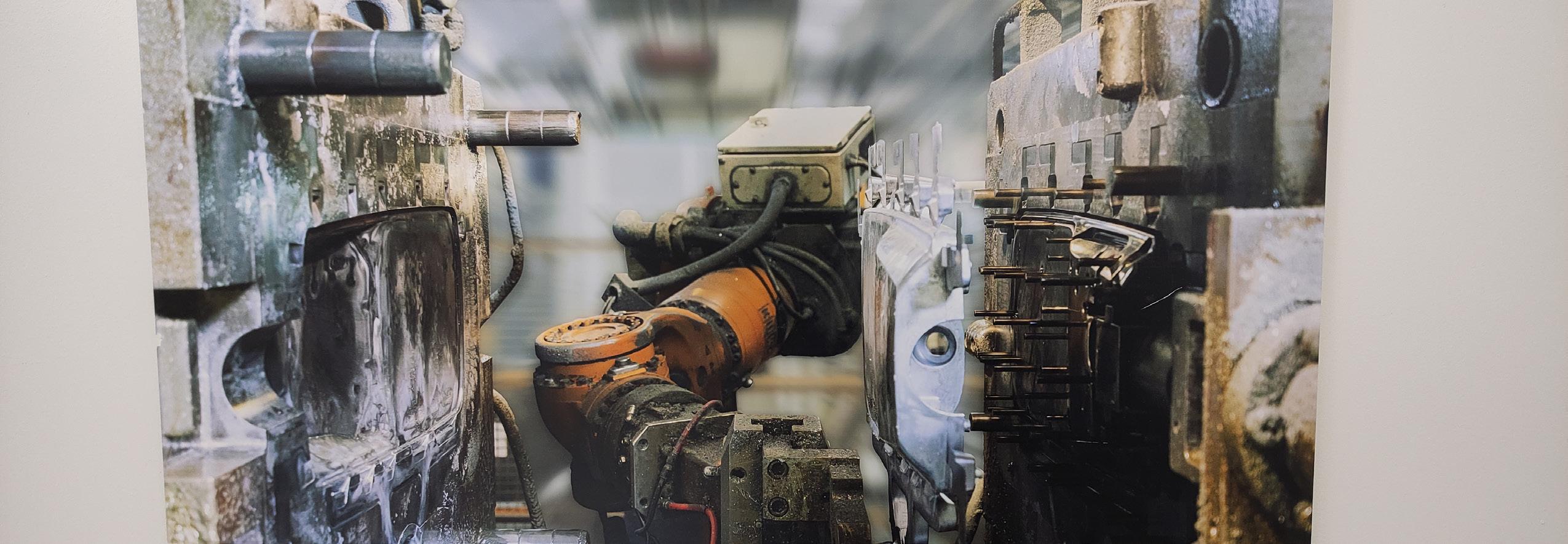
THE FOUNDRY SECTOR IN SPAIN
Marina Giacopinelli, Managing Director, Fundigex 西班牙铸造业概况
西班牙铸造出口商协会 董事总经理 玛丽娜·贾科皮内利
The foundry sector in Spain represents one of the most important industries in the country, being it also absolutely necessary in the production chain for most industrial sectors. It is also a widely internationalized sector that, thanks to its excellence, has been able to position itself as a preferential partner within the European market and is currently actively moving towards new markets, such as America and Asia.
The metal industry has a long history in Spain, having traced the existence of foundries in the northern part of the country back to the XVII century. This has given us some time to excel and to create an industrial ecosystem around the foundry industry which enable us to give full services and cover all the stages in the process of a finished part.
A BRIEF OVERVIEW
There is no official census in Spain that can give us accurate statistics about the industry, however; in cooperation with the federation for foundries in Spain, we can give statistics that represent approximately 85% of the tonnage produced in our country.
To give a brief overview of what is produced in terms of metalcasting in Spain, we have the 2020 figures, that show us that approximately 1.6 M. tons were casted in total, of which approximately 89% would correspond ferrous parts and the rest to non-ferrous parts, although in terms of number of foundries, around 60 % correspond to ferrous foundries and 40% to non-ferrous foundries.
A HIGLY INTERNATIONALIZED INDUSTRY
As shown by the graphic, Spain is the fifth producer of casting parts in Europe, but ranks as number one when it
铸造行业是西班牙最重要的行业之一,是大多数工业 产业链中不可或缺的一部分。西班牙铸造行业也是一个国 际化的行业,由于其卓越的表现,已经能够将自己定位为 欧洲市场的优先合作伙伴,目前正积极向美洲和亚洲等新 市场进军。 金属工业在西班牙有着悠久的历史,其北部地区铸造厂 的发展可以追溯到十七世纪。因此,西班牙获得发展的先机, 可以围绕铸造行业创建一个工业生态系统,使西班牙能够提 供关于生产铸件的全面技术、工艺和服务。
概况
西班牙没有关于铸造行业的官方统计数据,但是, 通过与西班牙铸造联合会的合作,我们可以给出代表了约 85%的西班牙铸件产量的统计数据。 以2020年的数据为例来分析西班牙金属铸造行业的生 产情况。2020年,西班牙的铸件产量大约为160万吨,其 中黑色铸件约占89%,其他为有色金属铸件。但是,就铸 造厂数量而言,大约60%为黑色金属铸造厂,40%为有 色金属铸造厂。
高度国际化的行业
如图所示,西班牙是欧洲第五大铸件生产国。在黑色金属 零件出口方面,西班牙位居欧盟第一,出口比例大约为70%。 FUNDIGEX成立于1984年,始终以促进西班牙铸造 行业的出口为目标,很多企业已将进入国际市场作为他们的 首要任务。 FUNDIGEX通过各种方式积极协助企业,最重要的
comes to exports of Ferrous parts in the EU. Around 70% of our production is exported to other markets.
We believe in FUNDIGEX that, since the creation of our Association in 1984, with the aim to boost the exports of the Spanish Foundry Sector, the companies in our industry have made it their priority to be present on international markets.
From Fundigex, we are actively assisting them in all terms possible and above all, we are travelling around the world to make sure that the Spanish Casting Industry is being recognised with terms as Quality and Excellence; a reliable partner in industry.
As for now, more than 87% of our exports go to Europe, however; the tendency is to increase sales in overseas countries.
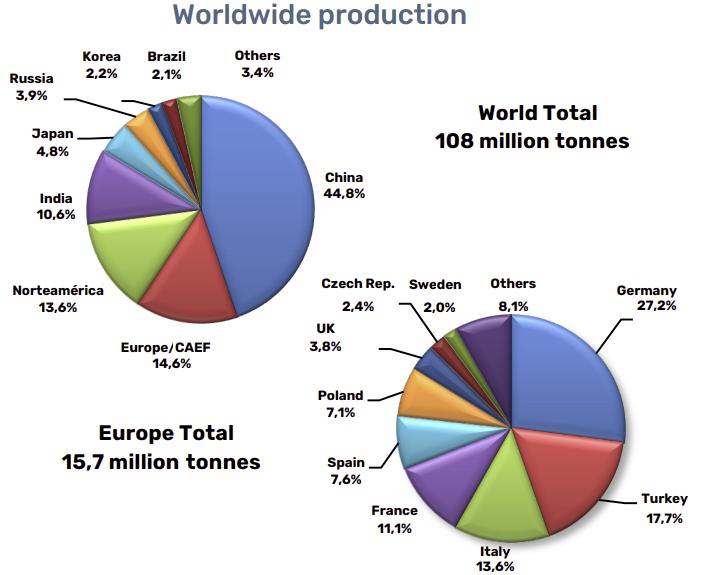
PRIORIY CLIENT SECTORS
When it comes to client sectors, around 60% is casted to the automotive industry, although it is true that due to different reasons, such as the global semiconductor shortage or the uncertainty of the automotive future in terms of electrical vs. combustion motors, have accelerated the change in tendencies. This has contributed to the diversification of our foundries.
THE FOUNDRY SECTOR:AN ESENTIAL INDUSTRY
Since the pandemic caused by the Covid-19 virus was declared in 2020, the foundry sector not only in Spain, but in the whole of Europe, has had to face a series of very challenging situations, such as increase in energy costs, rise in price and shortage of raw material, increase in the transportation costs. etc.
Nonetheless, we are talking about a mature and consolidated industry, one in which tradition is combined with new technologies. Step by step, it is adopting and endorsing the parameters of Intelligent Manufacturing, circular economy and sustainability, not only achieving sales records year after year, but also generating awareness about reducing the impact of its footprint on the environment and improving, therefore to the society in general..■

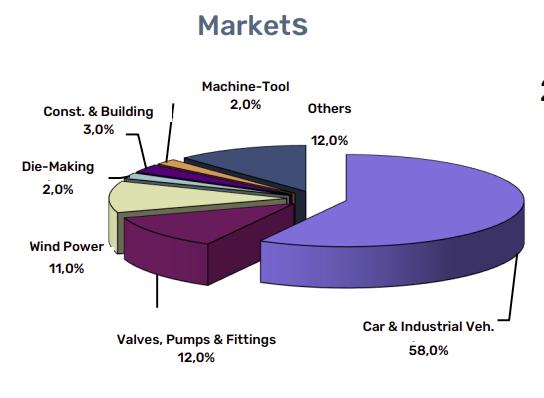
是,通过参加全球活动,确保西班牙铸造企业在质量和表 现得到认可,从而成为可靠的合作伙伴。 目前,西班牙有超过87%的铸件销往欧洲,出口呈增 长趋势。
优先客户领域
就客户领域而言,约有60%为汽车行业。尽管由于不 同原因,例如全球半导体短缺、电动汽车及内燃机汽车发展 的不确定性等因素加速了变化的趋势。同时,也促使铸造厂 的多元发展。
铸造业: 一个重要的行业
自2020年新型冠状病毒Covid-19在全球大流行以来, 西班牙乃至整个欧洲的铸造业都不得不面临一系列的挑战,例 如能源成本上升、原材料的短缺和价格上涨、运输成本增加等。 尽管如此,铸造行业仍是成熟且巩固的行业,是传统 工艺与新技术相结合的行业。铸造业在逐步采用智能制造 技术、使之符合循环经济和可持续发展的要求,不仅实现 了每年的销售目标,而且增强铸造业减少对环境影响的意 识,同时也提高了公众的环保意识。■
2020
IMPROVEMENT OF CORE MAKING EQUIPMENT THROUGH ANALYSIS OF THE CORE MAKING PROCESS
Jia Li,Xue Niu,Linlong Yang,Gaochun Lu, He Qiu,Suzhou Mingzhi Technology Co., Ltd.
基于制芯工艺研究的制芯装备优化
李嘉,牛雪,杨林龙,陆高春,邱壑(苏州明志科技股份有限公司,江苏 苏州215217)
Abstract
Research of the process for making cores was carried out and concludes that shortening the standby time of the core sand (referred to as uncured mixture of sand and binder) can reduce fluctuation in the quality of the sand core. Controlling sand temperature in a reasonable range and raising the temperature at which the catalytic gas is cured can maintain a good initial strength of the sand core at a high speed, which therefore improves the efficiency, in terms of quantity and quality. Based on these conclusions, the layout and functions of the production equipment have been rearranged by developing an integrated core-making unit, known as MICC (Mingzhi Technology Integration Core Centre). Verification within a production setting shows that the new layout effectively improves the measurement controls of standby time, core sand temperature, and catalytic gas temperature. This helps improve the production efficiency and quality substantially.
Key words: Core sand, Sand core quality, Core-making process, Core shooting machine, Integrated core-making unit.
1.Introduction
The conventional core-making technology utilizing core machines has disadvantages, which include: fixed volume in single batch sand mixing, large fluctuation of storage time, and uncontrolled storage environment. These factors cause the sand core quality to fluctuate and therefore lower the efficiency and effectiveness of production.
In previous analysis of the resin material characteristics, it is found that primarily the viscosity coefficient of liquid resin and the degree of spontaneous reaction affect the quality. Furthermore, as the sand shooting nature and law of resin hardening indicate, a good fluidity of core sand guarantees a high quality.
Further process research is required to analyse the factors and laws that affect core sand fluidity and core curing, in 摘要:
通过制芯工艺试验研究,认为缩短芯砂待用时间,可减少 砂芯质量波动;控制砂温在合理的范围及提升催化气体温度, 可快速建立砂芯的初强度并提高制芯效率。基于工艺试验结论, 优化传统制芯单元功能布局,开发集成式制芯单元MiCC。生 产验证证明:集成式制芯单元实现了对“砂温”、“芯砂待用 时间”、 “催化气体温度”的有效控制,使整个制芯生产效率 及砂芯合格率得到大幅提升。 关键词:芯砂;砂芯质量;制芯工艺;射芯机;集成式制 芯单元
1 引言
现有传统式制芯单元的工序存在混砂机单批混砂量固 定,无法调整、芯砂待用时间波动大、芯砂存储环境不受控 等不利因素,导致制芯质量波动大、生产效率低。随着对树 脂材料特性的认识,发现液态树脂的粘度系数及自然反应程 度是影响砂芯质量的关键因素。进而随着对射砂原理和树脂 硬化规律的认识,芯砂良好的流动性是保障高质量砂芯的前 提条件。 因此,需进一步开展工艺试验研究,分析出影响芯砂 流动性和砂芯固化的因素及规律,从而优化制芯装备,提高 制芯质量、提升制芯效率。
2 制芯工艺试验研究
2.1.冷芯制芯工艺 2.1.1 试验仪器、材料与方法 试验仪器:混砂机、MLWA1试样机、SAC锤击式制 样机、智能型砂强度机、电子天平;
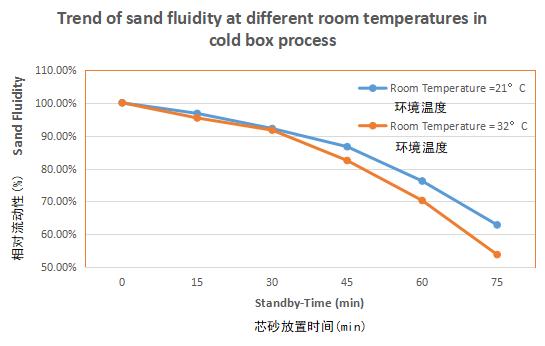
(Note: the fluidity of the freshly mixed sand is set as the reference) 注:刚混制完成的芯砂流动性为基准值 Figure 1. Trend of sand fluidity at different room temperatures in cold box process 图1 芯砂相对流动性
order to optimize core-making equipment, improve coremaking quality, and enhance efficiency. 2.Research of core-making process
2.1Cold box core-making process 2.1.1.Materials and methods
Equipment
The equipment used in this paper include a sand mixer, the proprietary MLWA1 sample machine from Suzhou Mingzhi Technology, SAC hammer sampler, strength tester, and electronic balance.
Materials
The materials used include a cold box resin (phenolic resin and poly-isocyanate), triethylamine and 50/100 recycled silica sand.
Methods
The cold box resin with the addition set at 0.6% for both components and recycled silica sand are first mixed. The influence of environment temperature and standby time on the fluidity of the core sand is studied. The method refers to the ‘side-hole quality test’ in Casting Manual Volume 4: Modelling Materials (Huang, 2002).
The initial strength is tested on the 8-shape sample made by the MLWA1 sample machine. After that, how the core sand temperature and catalytic gas temperature affect the initial strength is analysed. 2.1.2.Content and analysis1.1.1.1. 2.1.2.1Standby time and room temperature
As shown in Figure 1, the fluidity of the core sand shows a downward trend as the standby time increases. When the standby time remains constant, the higher the room temperature is, the more rapidly the fluidity of core sand decreases. 2.1.2.2Sand temperature
How the sand temperature affects the reaction speed of resin has a ‘10 °C’ rule (Qu & Ji, 2007). That is, with every temperature increase of 10 °C, the reaction speed doubles. As illustrated in Figure 2, in the range of 5~40°C, when the sand temperature is lower than 15 °C, the initial tensile strength is
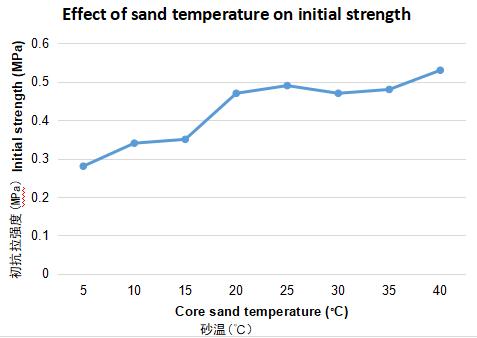
Figure 2 Effect of sand temperature on initial strength 图2 砂温对砂芯初抗拉强度的影响
试验材料:冷芯树脂、三乙胺、50/100再生硅砂。 试验方法:使用冷芯树脂(单组分加入量0.65%)和 再生硅砂进行混砂,研究芯砂存放环境温度和存放时间对芯 砂流动性的影响;其中芯砂流动性测试方法参照《铸造手册 第4卷-造型材料》中的侧孔质量法进行检测[1]。另外, 使用MLWA1试样机制8字试样,研究砂温和催化气体温 度对砂芯初强度的影响。 2.1.2 试验内容与分析 2.1.2.1 芯砂放置时间与环境温度对芯砂流动性的影响 从图1可以看出,随存放时间的延长,芯砂相对流动 性呈下降趋势;而且,在芯砂存放时间相同的情况下,存 放环境温度越高,芯砂的相对流动性下降幅度越大。所以, 为了避免芯砂的流动性下降而引起砂芯质量波动,应尽可 能缩短芯砂待用时间,减小环境温度对芯砂的影响。2.1.1.2 砂温对初抗拉强度的影响 砂温对树脂的反应速度影响遵循“10℃”原则,砂温 每增加10℃,将使树脂的反应速度加快2倍[2]。从图2 可以看出,砂温在5℃~40℃,当砂温≤15℃时,树脂反 应速度慢,初抗拉强度≤0.35MPa;当砂温≥20℃时, 树脂反应速度快,初抗拉强度≥0.47MPa。制芯时,砂芯 初抗拉强度须满足砂芯顶芯且不引起砂芯变形的需求,对于 形状复杂、薄壁的砂芯,砂温最佳控制在20℃~30℃;但 对于形状简单、厚大的砂芯,砂温可控制在15℃~35℃。
2.1.1.3 催化气体温度和吹气时间对初抗拉强度的影响 从图3可以看出,砂芯的初抗拉强度与催化气体温度 和吹气时间有关。催化气体温度150℃相比110℃,达到 相同的初抗拉强度所需要的吹气时间短,因此,在满足砂芯 初抗拉强度的条件下,较高的催化气体温度可以缩短吹气时 间,提升制芯效率。

Figure 3 Effect of catalytic gas temperature and blowing time on initial strength of sand core
图3 催化气体温度和吹气时间对砂芯初抗拉强度的影响
less than 0.35MPa; when the sand temperature is higher than 20 °C, the initial tensile strength is greater than 0.47MPa.
In the process of shooting, the initial tensile strength must be in a range that the sand core can be completely ejected and at the same time void of excessive deformation. Therefore, the sand temperature is best controlled at 20~30°C for sand cores with complex shapes and thin wall structure, while 15~30°C for those with simple shape and thick wall. 2.1.2.3Catalytic gas temperature and blowing time
The initial strength of sand core is influenced by catalytic gas temperature and blowing time, as can be seen in Figure 3. Compared to 110°C, a catalytic gas temperature of 150°C requires a lower blowing time for achieving a desired initial strength.
Summary of research on cold box process
The conclusions of this section are: 1.Shortening the core sand standby time after mixing can reduce the fluctuation of the quality. The time should not exceed 15 min for sand cores of complex shapes or thin walls, and 30 min for cores of simple shape or thick walls. 2.Controlling the sand temperature in a reasonable range and increasing the catalytic gas temperature allows the sand core to achieve the desired initial strength in a short timeframe. Therefore, the efficiency, as relates to lower defective core rates (see table 4), can be improved. 2.2 Inorganic core making process
As per empirical evidence in application, as well as testimony from technicians of inorganic material suppliers, it is believed that reaction to air and dehydration leads to crusting of the mixed core sand (Wei, Liu, Pi, & Qin, 2013). When room and sand temperatures rise, the speed of crusting will increase, which lowers the quality. To reduce encrustation, the temperature of the inorganic sand should be no more than 35°C at a standby time ideally that is lower than 10 minutes.
In the inorganic core making process, the core sand
2.1.3 冷芯制芯工艺试验结论 通过冷芯制芯工艺试验研究,得出结论为: 缩短“芯砂待用时间”,可减少砂芯质量波动;对于 形状复杂、薄壁砂芯,控制芯砂待用时间不超过15min; 对于形状简单、厚大砂芯,控制芯砂待用时间不超过 30min; 控制“砂温”在合理的范围及提升“催化气体温度”, 可快速建立砂芯的初强度并提高制芯效率。对于形状复杂 、薄壁的砂芯,砂温最佳控制在20℃~30℃;对于形状简 单、厚大的砂芯,砂温可控制在15℃~35℃。 2.2 无机制芯工艺 随着在无机材料的应用经验增加及与不同无机材料供 应商的技术人员交流,认为混好的芯砂因与空气接触反应 和脱水干燥而导致芯砂结壳[3];砂温越高,环境温度越高, 芯砂结壳越快,从而影响制芯质量。所以需要控制砂温不超 过35℃、控制芯砂待用时间不超过10min为佳。 无机制芯时将芯砂射入加热的芯盒,砂芯外轮廓周围 快速固化结壳,但中间的大量芯砂仍未固化。为此向砂芯
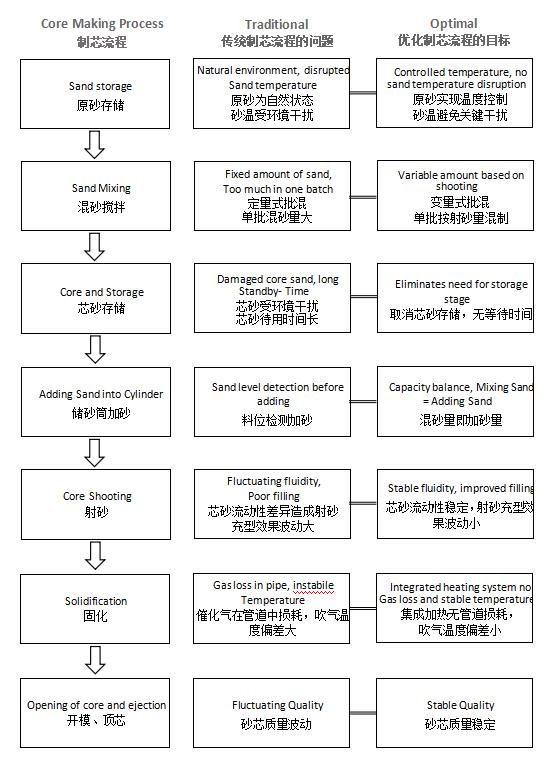
Figure 4 Comparison between traditional and optimised core making process
图4 传统制芯流程与优化制芯流程对比图
is first injected into the heated core box. Then, a quick curing and encrustation on the outer contour occurs, while the interior core sand is not yet entirely cured. Finally, hot catalytic gas is injected to increase the interior sand temperature and as curing occurs, drain water is released.
In the core making process of a high temperature heater product, verification of one type of cylinder block shows that increasing the catalytic gas temperature can reduce the blowing time as the mould temperature remains unchanged.
To summarize, during the inorganic sand core making process, it is found that: 1.To reduce quality fluctuations, sand temperature should be lower than 35°C and the standby time must be less than 10 min. 2.A higher catalytic gas temperature can increase efficiency.
Results
The research results in section 2 show that, irrespective of process employed (cold box or inorganic process), sand temperature, core sand standby time, and catalytic gas temperature are always important parameters to control. 3.Analysis and improvement of core making process and equipment
3.Comparison of core making processes
Focussing on 3 key parameters --sand temperature, core sand standby time and catalytic gas temperature—weaknesses in the relative stages of the traditional core making process are optimised, as is shown in Figure 4. The optimised version avoids the storage of core sand and improves or simplifies the other stages. It results in improved control of the 3
内吹热空气(催化气体)使砂芯内部芯砂温度提高,同时 可将固化期间释放的水导出[3]。在615缸体上的制芯验证 表明:在模具温度不变的情况下,提高热空气温度(“催化 气体温度”)可以减少吹气时间。另外,我司给某客户提 供的高温加热器,制某形状简单、厚大的砂芯,之前“催化 气体温度”240℃~250℃,制芯循环时间55s~75s; “催化气体温度”300℃~360℃时,制芯循环时间 30s~55s。 通过无机的应用经验,得出结论为: 控制“砂温”不超过35℃、缩短“芯砂待用时间”不 超过10min,可减少砂芯质量波动; 提高“催化气体温度”,可以提高制芯效率。 2.3 小结 不论是冷芯工艺还是无机工艺,都需要控制“砂温”、 “芯砂待用时间”、“催化气体温度”。
3 制芯流程及装备的分析改进
3.1 制芯流程对比分析 针对“砂温”、“芯砂待用时间”、“催化气体温度” 三个工艺关键要素,从传统制芯流程分析,找出工艺关 键要素所对应的工序并优化,见图4。优化后的制芯流 程取消了芯砂存储工序,及改善了其它工序,实现了对 “砂温”、“芯砂待用时间” 、“催化气体温度”的有 效控制。
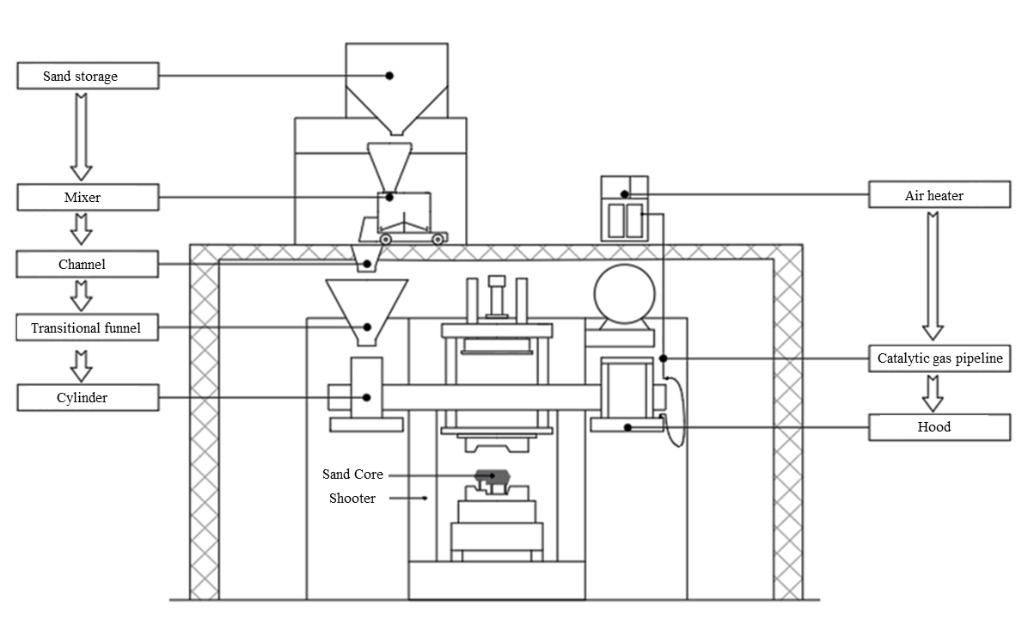
Figure 5. Layout of a conventional core-making unit 图5 传统制芯单元布局
Figure 4 Comparison between traditional and optimised core making process 图4 传统制芯流程与优化制芯流程对比图
parameters noted.
Layout and optimization
In accordance with the proposed changes in the core making process, the layout of the traditional core making unit, as shown in Figure 5, is modified to improve control of the 3 variables. Applying an integrated design concept, a new type of core making unit MiCC (Mingzhi Technology Integration Core Centre) is developed, which is illustrated in Figure 6. Additionally, an intelligent control system MiCL (Mingzhi Technology Intelligence Core Control) is developed for this unit, enabling closed loop control of these variables in the core-making process.
Improved temperature control of sand
Since silica sand has poor thermal conductivity, a sand temperature control device in the form of an air heat exchanger is developed. It is designed as a compact structure, easily integrated with the sand storage structure. Aided by MiCL’s calculation of the monitoring core sand temperature, the temperature range of input sand can be broadened from 5~35°C to 0~50°C. That is to say, the addition of the temperature controller offers more effective and precise control of the input temperature than without it.
Core sand standby time
3.2 制芯单元布局与改进 按照制芯流程分析结果,进一步开展对“传 统制芯单元布局”(图5)结构的改进。实现对“砂温”、 “芯砂待用时间”、 “催化气体温度”的精准控 制,保证制芯质量的稳定。最后,应用“集成”设 计理念,开发新型集成式制芯单元MiCC(Mingzhi Technology Integration Core Centre),如图6 所示。同时开发匹配的智能控制系统MiCL(Mingzhi Technology Intelligence Core Control),实现制 芯过程变量的闭环控制。 3.2.1 原砂温控的改进 依据硅砂导热性差的原理,研发了一种空气 热交换形式的原砂温控装置,再通过紧凑的结构设计实现与 制芯单元原砂存储结构集成设计。同时通过对单元芯砂的温 控监测及MiCL智能控制系统的计算。可使制芯单元输入 原砂温度范围由原先的5~35℃扩大到0~50℃,此原 砂温控装置的增加既满足集成制芯单元的紧凑布局又实现 原砂热交换温度的有效控制。 3.2.2 “芯砂待用时间”的改进 集成式制芯单元简化了“芯砂”流转过程,取消了“下 砂通道”及“过渡储砂斗”,“混砂装置”根据MiCL智能 控制系统对单批混砂量、单次射砂量、单次制芯节拍的逻辑 换算定义混砂量并将混合好的“芯砂”直接加入至“储砂筒”。 实现“芯砂”的即混即用,“芯砂待用时间”大幅度缩减。 按照传统制芯单元布局,测算“芯砂待用时间”见表1。 改进后的集成制芯单元“芯砂待用时间”是传统制芯 单元的10%。 3.2.3 “催化气体温度”的改进 传统制芯单元布局,催化气体加热器一般布置在钢结 构平台上。从加热器至吹气罩的管路长度约3m~8m,加 热的催化气体在进入吹气罩前温度损失约50%,且冬季更 为明显,其主要原因是较长的管路产生了热量损失。

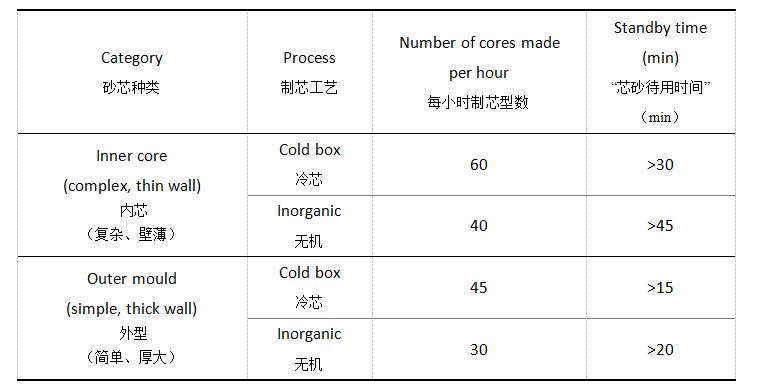
Table 1 Core sand standby time of traditional unit
表1 传统制芯单元“芯砂待用时间”
Table 2 Core sand standby time of optimised unit
表2 集成式制芯单元“芯砂”待用时间
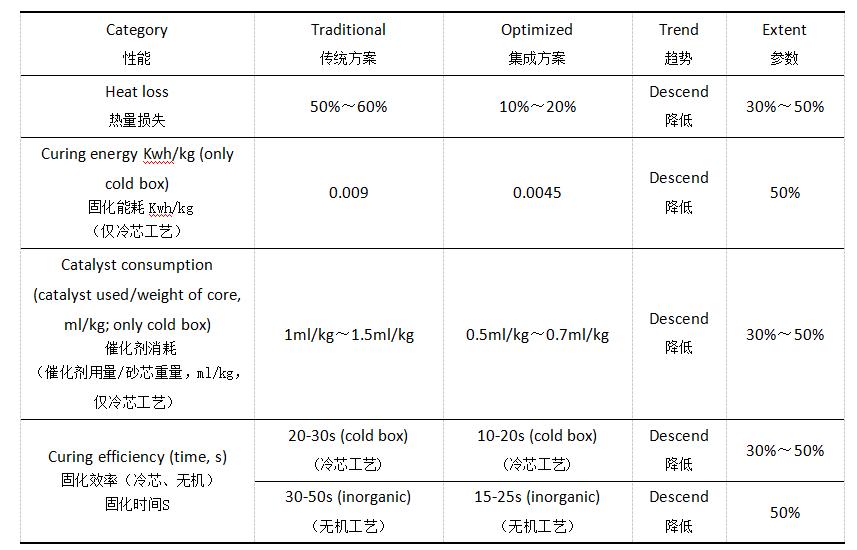
The integrated core making unit simplifies the cycle of the core sand transportation. The channel and transitional funnel (shown in Figure 5) are cancelled. The sand mixer defines the sand addition through the conversion of MiCL calculation results based on the amount of mixed sand, the volume of shot sand, and time of one patch. Then, it adds the core sand to cylinder directly, which means instant use of core sand and a shorter standby time
The measured standby time of the traditional unit is listed in Table 1, whilst that of the integrated core making unit is in Table 2. After optimization, the core sand standby time becomes 10% versus the traditional time.
Catalytic gas temperature
In the traditional core making unit layout, the catalytic gas heater is generally set on the steel platform, which means the pipe connecting it to the hood is 3~8 m. As a result, there is approximately 50% loss of gas temperature before gas is transferred into the hood, due to the length of pipeline, which is a more notable phenomenon in cold environments and seasons, such as wintertime.
The integrated core making unit applies the high-efficiency curing technology. It accomplishes a ‘0 distance’ (<0.5 m) catalytic gas transfer into the hood by nature of the integrated design of the heater and hood. The heat loss and catalyst used are both reduced, so the efficiency increases. The comparison data is in Table 3 (Yang & Xu, 2021). 4.Production verification
The integrated core-making unit enables the control and improvement of sand temperature, core sand standby time, and catalytic gas temperature, of which the effects of core sand standby time and catalytic gas temperature are the most obvious.
The quality comparison between the traditional core making unit and the optimised unit, when manufacturing 5,000 pieces of product, is illustrated in Table 4. 5.Results and discussion
1.Through analysis of the core-making process, it is found that the sand temperature, core sand standby time, and catalytic gas temperature are the significant factors that affect the fluidity of the core sand and the initial strength of the sand core. 2.Focusing on improving these key factors, the traditional core-making unit is optimized and improved by development of the integrated core-making unit, MiCC. Quality and efficiency have been greatly improved, while material energy savings is achieved. It can reduce customer operating costs and offer an improved manufacturing environment.
In the future, the unit will provide core-making producers with a reasonable solution for upgrading process transformation and meet the needs of high-end casting production. In summary, the proposed integrated casting core-making equipment leads to a more environmentalfriendly, efficient, and intelligent solution. ■
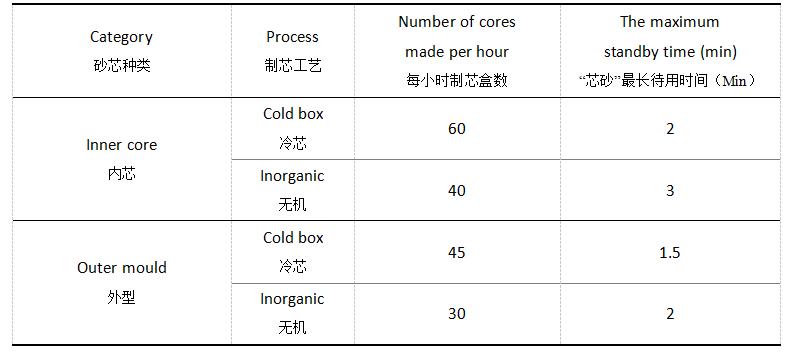
Table 3 Comparison of heater performance 表3 传统方案与集成方案加热器性能对比
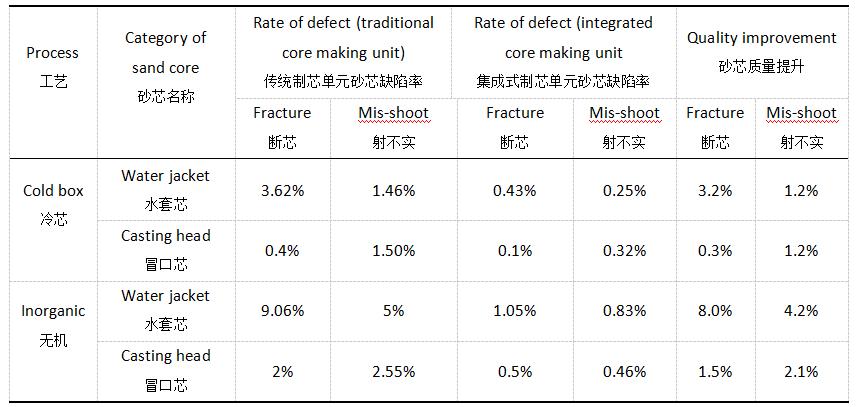
Table 4. Quality comparison between traditional and integrated core making unit 表4 传统制芯单元与集成式制芯单元制芯5000件质量对比
集成式制芯单元应用了集成高效固化技术,通过加热 器与吹气罩的集成设计,实现催化气体“零距离”(<0.5m) 进入吹气罩,减小了热损失、催化剂耗量,提升了固化效率。 对比数据见表3[4]。
4 生产测试及验证结果
集成式制芯单元实现了对“砂温”、“芯砂待用时间”、 “催化气体温度”的控制改善,其中“芯砂待用时间”及“催 化气体温度”产生的效果最为明显。 传统制芯单元与集成式制芯单元制芯5000件质量对 比数据见表4。集成式制芯单元上制芯质量稳定,射不实缺 陷率和断芯率都有明显降低。
5 结语
通过开展制芯工艺试验研究,找出了“砂温”、 “芯砂待用时间”、“催化气体温度”是影响芯砂流动 性、砂芯初强度的关键因素;围绕改善这些关键因素, 对传统制芯单元进行优化升级,研发了“集成式制芯单 元-MiCC”,砂芯质量及制芯生产效率得到大幅提升, 同时实现了节材、节能,降低了客户运营成本,改善生 产环境。鉴于集成式制芯单元的研发经验及成果,可为 制芯生产的客户在工艺转型升级上提供合理的解决方案, 引领铸造制芯装备向环保、高效、智能方向发展,满足 高端铸件生产的需求。■
THINK BEYOND. SHAPE THE FUTURE.
拓界.铸未来
We’re excited to unveil our new company tagline “Think beyond. Shape the future”. The new tagline reinforces our position as an innovative and sustainable partner within the foundry and steel industries.
As the pace of global change accelerates, our customers are in more need than ever of truly innovative partners. As Vesuvius and Foseco, we are, a company that invests in R&D and new technologies to enable our customers to shape their own future – and that of our planet. But what does the new tagline stand for?
Think beyond.
The first part ‘Think beyond’ reflects our role as innovators. To shape the future, we need to think beyond what we did in the past, beyond what we are today; our focus is on what we want to be. We need to think beyond preconceived ideas about what we are and what our customers are. We and our customers do not operate in an industry of the past; we are the future. The world has changed over the past decades thanks to our industry. We need to recognise the problems that have come with it, but we also need to be part of the solution.
We think beyond
• partial solutions to deliver end-to-end value and shape the future success of our whole operations, combining breakthrough innovation with our trusted knowledge and expertise. • technical disciplines and combine all types of expertise to deliver enhanced results and shape the future of our solutions, taking ownership of tomorrow’s problem before we’re asked to. • existing consumables to collect data that shapes the future of our products and solutions, exploring new ways to integrate continuous data capture into our solutions to give customers vital insights. • today’s technologies, and shape the future through advanced mechatronics, providing our customers with unique and useful tools.
Shape the future.
By thinking beyond, we’re shaping the future by delivering solutions that will increase our customer’s efficiency, enhance quality, improve safety and reduce environmental impact. With global governments setting challenging environmental targets such as emission reduction and sustainability measures, it’s important to understand these challenges in order to stay ahead
很高兴推出我们公司新的宣传标语:“拓界.铸未 来”。新的概念进一步加强了我们在铸造和钢铁行业中 一直期望展现出来的行业地位——我们是具有创新精神 的可持续合作伙伴。 随着行业全球化变革步伐的加快,我们的客户比以 往任何时候都更需要真正富有创新精神的合作伙伴。作 为维苏威和福士科这一知名品牌,我们是一家致力于新 技术研发和应用的公司,我们追求的是使我们的客户有 能力塑造自己的未来——以及我们星球的未来。接下来 我们要讲述一下新标语所代表的含义是什么?
拓界
第一部分“拓界”反映了我们作为创新者的这一角色 特点。为了塑造未来,我们需要超越过去所做的,超越我 们今天的想法;我们的重点应该是着眼于我们未来想实现 的事情上。我们需要超越过去我们所具有的、那些关于我 们是什么以及我们的客户是什么的先入为主的想法。我们 和我们的客户要运营的不是已经过去的行业;我们自己要 达成的目标就是未来。在过去的几十年中,由于我们的行 业发展,世界也发生了变化。我们需要认识到随之而来的 问题,但我们也需要让自己成为解决方案的一部分。
我们想得更长远
我们可以将突破性创新与值得信赖的知识和专业 知识相结合,提供实现终端价值的部分解决方案, 塑造我们整个运营体系的成功未来。 我们将技术规范和相关所有类型的专业知识加以 整合,以提供更好的成果并进一步塑造我们未来的 解决方案;同时提高自主意识,对未来可能出现的 问题做好应对准备。 致力于收集现有产品的数据并进行分析,这些数 据塑造了我们产品和解决方案的未来,进一步探索如 何将持续采集到的数据集成到我们新的解决方案和方 法中去,从而为客户决策提供重要的数据支持和依据。 关注当前技术潮流,通过先进的机电一体化塑造未 来,为我们的客户提供独特实用的工具。
and support our goal of becoming the supplier of choice for our customers. We’re being proactive in our approach to assess the impact to the industry and develop innovative solutions as our customers adapt.
We’re shaping the future of industries that will shape the future for everyone. The future of industry is sustainability. And the future of sustainability is industry. The world needs engineering to build tomorrow. It needs the metals, concrete and castings that are essential to modern life. It’s our role to help our customers make these industrial processes more efficient, safe and sustainable than ever before.
So, we think beyond today to create solutions that will shape the future for everyone. Talk to us about how we can help you to shape the future and meet and exceed your needs for today and tomorrow. Do you have a challenge or problem for the future that you’ve been putting off tackling, because it feels too hard? - Let’s discuss You’ll start to see our new tagline rolled out across the board, through our website, LinkedIn and Facebook and across all our marketing and reporting documents
About Foseco
FOSECO, the Foundry Division of VESUVIUS plc, is a global leader in products and solutions for improving foundry performance. Our aim is to enable improved foundry performance by working alongside our customers to develop and apply products and services that produce better casting quality and higher productivity at lower costs in a safe and healthy working environment.
About Vesuvius
VESUVIUS PLC is a global leader in metal flow engineering, providing a full range of engineering services and solutions to its customers worldwide, principally serving the steel and foundry industries. VESUVIUS PLC is a signatory to the United Nations Global Compact, making a formal public commitment to support its principles on human rights, labour, environment, and anti-corruption, and to engage in activities which advance the development of the UN’s Sustainable Development Goals. Our environmental objectives revolve around fighting climate change by reducing our own CO2 emissions and helping our customers reduce their own CO2 footprints. We have set ourselves the goal of reaching a net zero carbon footprint at the latest by 2050. ■ 铸未来
通过超前思考,我们正在通 过提供能够提高客户效率、提 高质量、提升安全性和减少环 境影响的解决方案来塑造未来。 随着各国政府相继出台节能减 排和可持续性发展措施等具有 挑战性的环境目标,我们亟需 了解这些政策上的挑战,这对于我们保持行业领先 地位,争取成为客户的首选供应商非常重要。我们 正在积极主动地评估政策措施对行业的影响,并适 应客户需求积极开发创新解决方案。 我们正在塑造行业的未来,行业发展的方向同时 也将塑造每个人的未来。工业的未来必须具有可持续 性。可持续性发展的未来着眼点在于工业如何发展。 世界的发展离不开工程建设的明天。工程建设包含了 目前建设中不可或缺的金属、混凝土和铸件。我们的 职责是帮助我们的客户使这些工业生产和工艺比以往 任何时候都更加高效、安全和具备可持续性。 因此,我们要超越今天进行思考,创造出能够为 每个人塑造未来的解决方案。请与我们讨论我们如何 帮助您塑造未来,如何满足并超越您今天和明天的需 求。你有没有一些因为技术困难而迟迟无法推进的未 来挑战或问题? - 我们愿意与您展开讨论,我们的新 标语正在通过我们的网站、LinkedIn 和 Facebook 以及我们所有的宣传和营销渠道全面推出。
关于福士科
FOSECO福士科是 VESUVIUS plc维苏威的铸 造部门,是旨在提高铸造产品性能解决方案的全球领导 者。我们的目标是通过与客户合作开发和应用产品以及 服务,在安全和健康的工作环境中,以更低的成本和更 高的生产率,生产质量更好的铸件,从而提高铸造性能。
关于维苏威
维苏威集团是熔融金属工业领域的全球领导者, 为全球客户提供全方位的工程服务和解决方案,主要 服务于钢铁和铸造行业。维苏威集团是联合国全球契 约的签署方,正式公开承诺支持其关于人权、劳工、 环境和反腐败的原则,并参与促进联合国可持续发展 目标发展的活动。我们的环境目标围绕着通过减少我 们自己的二氧化碳排放量和帮助我们的客户减少他们 自己的二氧化碳足迹来应对气候变化。我们为自己设 定了最迟到2050年实现净零碳足迹的目标。 ■


PRODUCT NEWS / 产品新闻 Product News Table of Contents 产品新闻目录
MOLD, CORE & SAND PREPARATION MELTING, POURING & HEAT TREATMENT
SOFTWARE
A Giant Among Core Shooters - The New Laempe Lhl200 - 1700 42 射芯设备中的巨擘——兰佩LAEMPE LHL200-1700
Elkem Supports Its Customers With Solving 44 Shrinkage Issues 埃肯公司为客户解决缩松问题 New Requirements Demand Innovative Solutions 45
新的需求急需创新的解决方案
Keeping A Close Eye On Everything Thanks To Digitalization 46 数字化进程使密切监控生产过程成为可能
射芯设备中的巨擘——兰佩LAEMPE LHL200-1700
As an innovative developer of complete solutions, the longestablished company Laempe offers a comprehensive portfolio of core shooters, gassing devices, sand mixers, sand preparation plants and core finishing solutions as well as networking and intelligent control for the entire core shop. The company implements automation solutions according to customer requirements up to the planning and realisation of a turnkey core shop. A comprehensive range of services in the areas of engineering, innovation and service round off the profile.
For almost 27 years, production has been carried out in Meitzendorf-Barleben, north of Magdeburg, while design work has been done in Schopfheim, and the staff around André Klimm is very busy, because high-quality mechanical engineering for foundries is booming and is finding markets all over the world, with a particularly high level of activity in North America at the moment. The global positioning of the company and the cooperation in the Sinto Group enable synergies and provide for a worldwide network.
Our visit on site had a special occasion this time, because in the large halls at SKET GmbH (Schwermaschinenkombinat "Ernst Thälmann") in Magdeburg, the huge LHL200 - 1700 was set up for trial operation before it is shipped. In future, the machine will produce cores for the casting of ship engines in Weifang, China.
Henri Ackmann's team loves the big machine
The machine is so big that we had to move to the huge, historic halls of SKET GmbH in Magdeburg to set it up for the test run, Laempe team leader Henri Ackmann tells us proudly.
The huge construction made of iron, steel and a lot of technology impresses with its compactness and the imposing dimensions of 11m height, 16m length and 30m width with a weight of approx. 300t.
The sand cores can weigh up to 2,600kg with a maximum shot volume of 1,700l and a cycle of 6 cores per hour is possible. The machine can be operated by one person plus gripper, the mixer processes approx. 9t of sand per hour.
After the complete installation of the plant, Henri Ackmann's team also produced the first test cores and the results are impressive. They all worked perfectly, explains Ackmann to everyone's delight, and the cores are impressive. Rudolf Wintgens, Managing Director of Laempe Mössner Sinto, was also able to see this for himself and took the
作为铸造完整解决方案的创新企业,历史悠久的兰 佩公司可以提供全面的射芯机、除气装置、混砂机、制 砂设备和砂芯精整解决方案以及整个制芯车间的网络化 和智能化控制技术。根据客户要求,兰佩公司从规划到 完成交钥匙制芯车间都采用自动化解决方案。全面的工 程、创新和服务使项目圆满结束。 近27年来,公司一直在马格德堡北部的梅岑多夫巴莱本进行生产,而设计工作一直在肖普夫海姆进行。位 于安德烈·克里姆附近的工作人员总处于忙碌状态,因为 铸造厂的高质量机械制造正在蓬勃发展,而且铸造企业正 在努力开发世界市场,目前在北美的业务较多。公司的全 球定位以及与新东集团的合作可实现协同效应并提供全球 网络。 本次实地访问正好碰到一个特殊的情况,在马格德堡 的SKET (恩斯特·台尔曼-机械制造联合体)的大厅里, 巨大的LHL200-1700设备已经试运行,做好发货前的 准备。未来,该机器将在中国潍坊用于制造船舶发动机的 砂芯。
亨利·阿克曼的团队擅长大机器的制造
兰佩公司的团队负责人亨利·阿克曼自豪地告诉我 们,这台机器太大了,因此不得不搬到位于马格德堡的 SKET公司,在那里的历史悠久的超大场地进行试运行。 这台由铸件、钢结构和诸多技术制成的紧凑的巨型设 备令人印象深刻,高11m、长16m、宽30m,重量约 为300t。 砂芯可重达2,600Kg,最大射砂量为1,700L,每 小时可循环生产6个砂芯。该机器可以由1个员工操作, 包括使用夹具,混砂机每小时可处理大约9t砂。 在完成组装后,亨利·阿克曼的团队生产了第一批测 试砂芯,结果令人印象深刻,它们都可以完美地进行生产。 阿克曼表示,大家对此感到很高兴。兰佩莫斯纳新东公司的 董事总经理鲁道夫·温特根斯也见证了这一刻,并肯定了肖

opportunity to emphasise the excellent cooperation of all departments at the Schopfheim, Mannheim and MeitzendorfBarleben sites on this major project.
Laempe likes it big, no question about it, because Laempe's LHL200 is the largest core shooter built anywhere in the world to date, and it did so without an accident and with the passionate commitment of the entire team.
The Giga core shooter is now being disassembled again and sent on its journey to the customer in China via Hamburg. Those reponsible in Schopfheim and Barleben are convinced that the efficiency of the machine with its ability to shoot large cores in one piece will also be of interest to other foundries.
About Laempe Mössner Sinto GmbH
Laempe Mössner Sinto GmbH is the world market leader in core shooting machines for the and with its comprehensive product and service portfolio covers all areas of modern core areas of modern core production. The traditional German company is a complete solution developer with headquarters in Barleben/Meitzendorf, Saxony-Anhalt. At modern production site and in the branch offices in Schopfheim in the Black Forest and Mannheim, a total of 340 people are employed. www.laempe.com ■
普夫海姆、曼海姆和梅岑多夫-巴莱本工厂的所有部门在 这个重大项目上的出色合作。 毫无疑问,兰佩公司非常擅长大型机器的制造,因为 兰佩的LHL200是迄今为止世界上最大的射芯机,而且 它在没有意外的情况下做到了这一点,整个团队都充满了 热情。 巨型射芯机现在再次被拆解,并经德国汉堡发往中国 客户。肖普夫海姆和巴莱本的负责人相信,机器的高效率 以及能够一次性射大型砂芯的能力也会引起其他铸造厂的 兴趣。
关于兰佩莫斯纳新东公司
兰佩莫斯纳新东公司是射芯机的全球市场领导者,其 全面的产品和服务组合涵盖了现代型芯生产的所有领域。 这家传统的德国公司是一家完整解决方案的供应商,总部 位于萨克森-安哈尔特州的梅岑多夫-巴莱本,其现代化 生产基地及分公司位于黑森州肖普夫海姆和曼海姆,共有 340名员工。■
埃肯公司为客户解决缩松问题
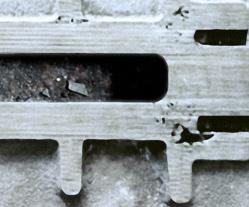
The growth and diversity of iron casting in the Asian markets has led foundries to re-examine their inoculation processes. New iron grades demand new process solutions and end users require higher specifications.
Elkem recognizes these challenges and has a dedicated team of metallurgists and process engineers capable of supporting foundries. Backed up by extensive laboratory facilities and a R&D group, we work together with our customers to solve issues, improve processes and eliminate waste.
Traditionally, the Asian market has used calcium/barium based inoculants and these are widely available, although of hugely variable quality. However, their low potency leaves them unsuited to many applications in this challenging market, such as shrinkage control in both grey and ductile irons, producing higher strengths in thinner section light weight castings and matrix structure. All of which offer the opportunity for an examination of the inoculants available today.
In light of this, Elkem’s technical experts recently consulted a foundry that manufactures ductile iron castings for critical machinery parts, weighing up to 10 tonnes. They experienced challenges with shrinkage, which resulted in rejects at a cost of $365,000 per year as they were only detected after machining. The foundry’s end user questioned the continuity in supply and quality, and thus business was at stake.
Design solutions undertaken by the foundry resulted in minor improvements, which were insufficient for the end user’s situation. Trials with chills improved the shrinkage defects but unfortunately, they were not able to remove the defects to an acceptable level.
Together with the foundry staff, Elkem technicians went on-site and analysed the situation. The foundry used a 7% Mg, 1.5% TRE alloy in the treatment system, covered by steel coins. A calcium / barium inoculant was used in both the first stage and subsequent in-stream process.
Samples were sent to one of Elkem’s regional research labs where expert metallurgists performed extensive analysis. As a result, they recommended changing the alloying materials.
Elkem technicians then performed a trial with Lamet® 5922, a nodulariser containing 5.9% Mg and 0.5% La. Elkem’s Lamet® has been proven in helping to eliminate shrinkage. The cover material was changed to FeSi. Ultraseed® Ce inoculant was then used in-stream, because of
亚洲市场对铸铁件及其多样性需求的增长,促使铸造 企业重新审视孕育工艺。更高等级的铸铁产品需要新的工艺 解决方案,最终用户要求更高性能的产品。 埃肯公司意识到这些挑战,而且拥有一支由冶金学家和 工艺工程师组成的专门团队,能够为铸造厂提供相应的支持。 在全面的实验室设施和研发团队的支持下,公司与客户一起 解决问题、改进工艺并消除废品。 传统上,亚洲市场使用基于钙/钡的孕育剂,尽管质量 参差不齐,但这些孕育剂是市场常见的。然而,产品的低效 使它们不再满足于充满挑战的市场需求,例如灰口铸铁和球 墨铸铁的缩松控制,铸件轻 量化要求更薄的壁厚和基体 结构更高的强度。这些都导 致需要对目前可用的孕育剂 进行讨论。 因此,埃肯公司的技术 专家最近接到一家铸造厂的 Casting results before and after the modified alloy additions 咨询,该企业为关键机械零部 合金材料改良前后的铸件效果对比 件生产重10t的球墨铸铁件。 这家工厂遇到了缩松问题,由于问题在铸件加工后才被发现, 这就导致公司每年产生价值约36.5万美元的废品。最终用 户对产品供应和质量连续性产生质疑,因此铸造厂的业务受 到影响。 铸造厂采用的解决方案产生了微小的改进,但对 于客户的情况来说是不够的。冷铁试验改善了收缩 缺陷,但不幸的是,他们无法将缺陷消除到可接受 的水平。 埃肯公司的技术人员与铸造厂员工一起前往现场分析情 况。铸造厂在处理系统中使用了7%Mg、1.5%TRE合金, 并用钢制硬币覆盖。钙/钡孕育剂用于第一阶段和随流孕育 过程。 样品被送到埃肯公司的一个区域研究实验室,冶金专 家进行了充分的分析,他们建议更换合金材料。 之后,埃肯公司的技术人员使用Lamet® 5922进行 了试验,这是一种含有5.9%镁和0.5%镧的球化剂。 埃肯公司的Lamet® 已被证明有助于消除缩松。覆盖材料
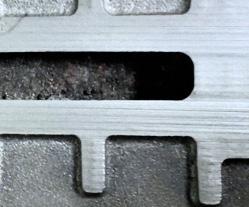
its’ strong potency in reducing the irons tendency to shrink.
After the trial it was clear that the casting results improved significantly with shrinkage porosity eliminated.
Introducing Lamet® 5922, Ultraseed® Ce, and FeSi to the process resulted in major improvements:
The scrap rate dropped from 30 % to 2 %. There was also a very low shrinkage level, accepted by the end user, and there was no need for the use of chills or any other production process change.
Not only was the foundry able to save annual costs immensely by reducing the scrap rate, but the foundry’s customers’ satisfaction also improved resulting in a continuation of the business.
For more information on new inoculation technologies, please contact your local Elkem representative or visit our website www.elkem.com/foundry. ■
改为硅铁。在工艺中使用Ultraseed® Ce孕育剂,因为 它在减少铸铁的收缩趋势方面具有强大的效力。
试验效果很明显,铸件得到显著改善,缩松消除。 Lamet® 5922、Ultraseed® Ce和FeSi的应用使工艺 显著改进: 废品率从30%下降到2%。最终用户也接受了非 常低的缩松率,并且无需放冷铁或改变任何其他生产 工艺。 铸造厂不仅能够通过降低废品率来极大地节省年度 成本,而且客户满意度也有所提高,从而业务得以延续。
更多关于新的铸造孕育技术信息,请与您当地的埃肯代 表联系或访问我们的网站www.elkem.com/foundry。■
New Requirements Demand Innovative Solutions 新的需求急需创新的解决方案
Fill has developed a vacuum metering system in the form of the robocast v, which revolutionizes the casting process for new types of drive system.
The ROBOCAST V from Fill ensures maximum casting quality while reducing the amount of return scrap material. The innovative casting system is used for low-oxide collection, manipulation, and metering of molten aluminum. Consistent, reproducible casting parameters are decisive factors for ensuring constant casting quality. This is now a reality with the development of the ROBOCAST V. The world premiere will take place at the leading international trade fair for die casting, Euroguss 2022, which will be held in Nuremberg in June 2022.
A rapid transition to alternative drive concepts is taking place in the field of mobility. Existing casting systems are often only suitable to a limited extent for producing the new types of drive component. "The challenge for the automotive industry and machine builders is to develop and implement completely new manufacturing concepts. With the ROBOCAST V, we have succeeded in taking a decisive step forwards," reports Thomas Rathner, Head of the Casting Technology Competence Center at Fill.
Dynamic, precise, reproducible
Molten metal is metered dynamically in the new ROBOCAST V. This enables delivery rates of 0.5 to 2.7 kilograms per second. And the delivery rate is varied and adapted automatically during pouring to comply with the requirements of the die. The delivery process can be parameterized such that the mold is always filled from below the molten metal level after casting starts. Oxide formation in the system is prevented by permanent application of a
Fill公司开发的真空计量系统ROBOCAST V,彻 底改变了新型驱动系统的铸造工艺。 Fill公司的ROBOCAST V系统可确保铸件具有最 高的质量,同时减少废品的出现。这个创新的铸造系统用 于低压铸造工艺铝液中氧化物收集、处理和计量。一致、 可重复的铸造工艺参数是确保铸件质量稳定的决定性因 素。随着ROBOCAST V研发成功,这个要求已成为现 实。ROBOCAST V的全球首发仪式将于2022年6月 在德国纽伦堡举办的国际压铸展览会Euroguss 2022上 举行。 驱动系统领域正在快速向替代驱动概念过渡。一般 情况下,现有的铸造系统对生产新型驱动部件的适用性 有限。“汽车行业和机器制造商面临的挑战是开发和践 行全新的制造理念。借助ROBOCAST V,我们成功地 向前迈出了决定性的一步,”Fill铸造技术能力中心负 责人Thomas Rathner说道。
动态、精确、可重复
熔融金属在新的ROBOCAST V中的计量是动态 的,这使得输送速率为每秒0.5至2.7Kg。而且,在浇 注过程中,为符合铸型要求,输送速率会自动变化和调 整。输送过程可以参数化,以便在铸造开始后,铸型总 在熔融金属液位以下填充。通过在熔融金属中始终加入
protective atmosphere to the molten metal.
Seamless data acquisition and storage
The CYBERNETICS PRODUCE software tool integrated in the ROBOCAST V casting system ensures seamless recording and storage of all the relevant process parameters. This enables efficient and reliable component traceability. CYBERNETICS PRODUCE allows foundries to analyze reproducible processes and optimize the procedures accordingly using key performance indicators.
Simple operation and easy to maintain
The ROBOCAST V also scores highly with simple handling, clear user guidance, and clearly arranged, "grippy" controls. The system is extremely easy to maintain. All wearing parts can be easily replaced without great effort in a special service unit as and when required.
Fill is a leading international machine engineering company based in Gurten, Upper Austria. With sophisticated high-tech systems and custom manufacturing solutions for metal, plastics and wood, Fill makes its customers the best in their fields. The automotive, aviation, sports and building industries all benefit from Fill’s expertise. Since it was founded in 1966, the company has distinguished itself through enormous innovative strength, strong values and the best jobs.
Further information can be found at: www.fill.co.at ■
保护气体,防止系统中形成氧化物。
无缝衔接的数据采集和存储
ROBOCAST V铸造系统中集成的CYBERNETICS PRODUCE软件可确保无缝记录和存储所有相关工艺 参数,从而实现了组件的高效和可靠追溯。铸造企业可 以使用CYBERNETICS PRODUCE软件分析重复的 工艺过程并使用关键性能指标相应地进
行优化。
易于操作和维护
ROBOCAST V凭借简单的操作、 清晰的用户指导和清晰的“抓取”控件 获得好评,而且非常易于维护。所有易 损件都可以在需要时通过特殊服务单元 进行轻松更换,毫无费力。 Fill是一家国际领先的装备制造公 司,总部位于奥地利上奥地利州的古尔滕。凭借先进 的高科技系统和针对金属、塑料和木材行业的定制解 决方案,Fill公司使自己的客户成为各自领域中的佼 佼者。汽车、航空、体育和建筑行业都受益于Fill公 司的专业知识。自1966年成立以来,公司凭借强大 的创新实力、深厚的价值观和优越的工作岗位成为行 业领军企业。 ■
Keeping A Close Eye on Everything Thanks to Digitalization
数字化进程使密切监控生产过程成为可能
Eirich presents digital solutions for increased efficiency in service and production plants
With the onset of the era of Industry 4.0, digitalization is rapidly gaining momentum in the industry with intelligent networking of machines and lines. This digital transformation is enabling companies to open up new ways to control and organize the entire value chain. The longestablished company Maschinenfabrik Gustav Eirich has developed a range of digital solutions for Lifecycle Services and Process Analytics to boost efficiency and streamline production processes.
With the onset of the era of Industry 4.0, digitalization is rapidly gaining momentum in the industry with intelligent networking of machines and lines. This digital transformation is enabling companies to open up new
爱立许公司推出数字化解决方案,极大提升了工厂 生产和服务环节的效率
随着工业 4.0 时代的到来,数字化在行业中呈现出 迅猛的发展态势,其中显著特点是机器和生产线上的智 能联网趋势。这种数字化转型使公司能够开发出控制和 协调整个生产过程的新方法。古斯塔夫·爱立许机械制 造公司是一家历史悠久的知名企业,现已为产品生命周 期服务和生产工艺分析研发出一系列数字解决方案,可 以大大提高效率并简化生产流程。
许多公司将数字化视为实现未来成功的关键步骤, 因此他们正试图优化流程以加强自己的市场地位。对于家
ways to control and organize the entire value chain. The long-established company Maschinenfabrik Gustav Eirich has developed a range of digital solutions for Lifecycle Services and Process Analytics to boost efficiency and streamline production processes.
Many companies see digitalization as a key step for future success, and as a result they are attempting to optimize their processes in order to strengthen their own market position. For the familyrun company Maschinenfabrik Gustav Eirich, the optimization of production processes and intelligent networking of production lines is a step toward more efficiency and greater sustainability. This creates flexible manufacturing structures, which play an incredibly important role in such a dynamic market. With its digital product portfolio, Eirich has also taken the topic of closeness to the customer to the next level: From fast ordering of spare parts to technical support provided by Eirich personnel, the company is aiming to offer customers even better service and barrier-free accessibility via its digital offerings.
Stephan Eirich runs the company now as CEO in the fifth generation of family ownership, and his focus is now on digitalization. He believes that digital transformation is a natural evolution for the industry:
“How can we ensure that a preparation system we deliver to a customer today will continue to operate in the optimum range, without the customer needing to rely on the input and experience of experts – who are becoming increasingly more difficult to find? It is up to the machine supplier to implement this knowledge in the system right from the start. We see this as a great opportunity and believe we owe it to our customers. With Lifecycle Services and Process Analytics we offer our core industries genuine added value to help make production processes more reliable and more sustainable in the long run.”
Lifecycle Services enable transparent servicing – from real-time monitoring of lines to maintenance services based on augmented reality. The solutions focus on optimizing machine downtime and minimizing line outages: • myEirich
With the aid of the electronic spare parts catalog from Eirich, customers can access visual models that enable them to intuitively identify installed components themselves. The shopping basket is the final link in the ServiceExpert ECD software – machine and line components that are required are simply added to the basket, and the order is placed directly by e-mail. In the myEirich application, customers can track the progress of a service order in real time and monitor its
族企业古斯塔夫·爱立许机械制造公司而言,生产流程的 优化和生产线的智能联网是迈向更高效率和更可持续性发 展的重要一步。这一转变使得制造流程和生产单元变得更 灵活,在当前充满高度活力的市场中发挥着极其重要的作 用。凭借其数字化产品组合包,爱立许公司可以提供更贴 近客户要求、高水平的个性化服务:从快速订购备件到爱 立许专业技术支持服务,公司旨在为客户提供更好的服务 体验,通过其数字化产品达到无障碍全方位的即时服务。 斯蒂芬·爱立许先生现在作为该家族企业的第五代 CEO对公司进行管理,他的关注点主要在数字化流程方 面。他认为,数字化转型是行业中必然发生的自然演变: “在专家经验越来越难获得的今天,我们如何确保 今天交付给客户的砂处理系统,可以让客户在无需依赖 专家的意见和经验的条件下,一直维持在最佳状态内运 行?实际上,作为设备供应商,我们应该从一开始就在 系统中预设好这些知识和数据。我们认为这是一个很好 的提升机会,并且我们的客户应当从产品中感受到这种 提升。通过产品生命周期服务和工艺分析数据,为我们 的核心行业提供真正的附加值,以帮助生产流程变得更 加可靠,并且从长远来看更具可持续发展的潜力。” 产品生命周期服务,提供的是一种接近透明的服务模 式——从实时监控生产线到基于增强现实的维护保养服务。 以下这些解决方案专注于优化机器停机时间和最大限度地 减少生产线中断:
我的爱立许产品手册
借助爱立许电子备件目录,客户可以访问可视模 型,从而直观地识别已安装的组件本身。 购物篮是 ServiceExpert ECD服务专家软件中的最后一个步骤——
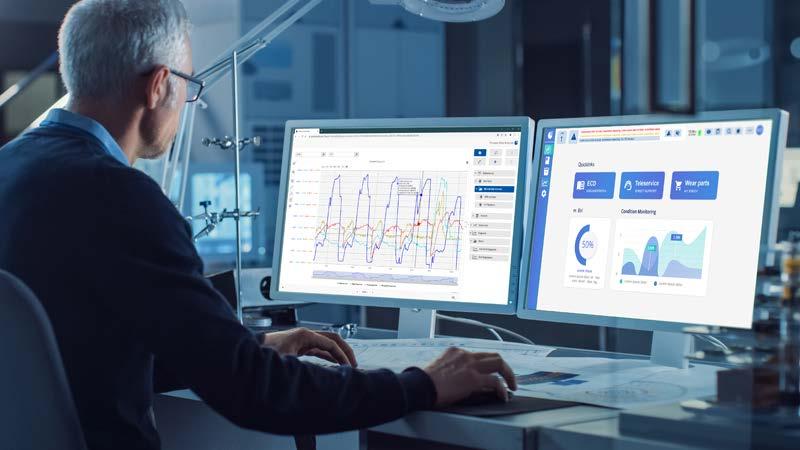
dispatch status live. • Condition Monitoring
With this system, physical parameters are measured and analyzed to determine the current status and condition of a machine. Sensors supply data in real time. Continuous data analysis highlights trends and identifies possible damage to components before failure actually occurs. Crashes, bearing damage, imbalance, gearing faults, and wear are all detected early on and displayed. This allows the customer to order replacement parts in good time or contact the Service department before the machine fails – without having to allow for waiting times before service engineers can visit. • Teleservice
Online service without service technicians present on-site – with remote servicing and remote diagnostics. The automatic collection and analysis of machine and process data means that faults can be isolated and located remotely. Once approved by the customer, measures can be put in place immediately to remedy faults, and customized software updates can be implemented without a presence on site. • EIRICH-AR
Services With the aid of augmented reality, specialists can gain an overview of the current status and condition of the system using a smartphone camera and smart glasses. Thanks to advanced 3D object tracking, arrows, notes, and markings can be superimposed on the display to make it easier for the user to follow the instructions of the expert. This maximizes productivity, reduces downtime and – more than anything – saves time and money. With digital tools for Process Analytics, Eirich offers optimization solutions that safely and reliably improve production processes. • QualiMaster
with EIRICH ProView The individual QualiMaster systems are a guarantee of quality in their relevant fields of application. The system continuously and automatically takes samples from the material being mixed, measuring the properties of the material in a range of ways. The ProView software visualizes and analyzes the measured data. With exceptional user friendliness, an incredibly clear visual presentation of the information and an array of adjustment options, this system offers users a wide range of options for monitoring and controlling engineering processes. The results can be analyzed by experts or with the aid of artificial intelligence so that subsequent batches can be successively improved. This boosts quality and hugely reduces waste, making your production more stable and more efficient. QualiMaster systems are already available for optimizing molding material properties, moisture content, consistency, and flow properties as well as for optimizing the production of granulates.
For more information please visit: www.eirich.de/de/ digitale-loesungen/ ■
只需将所需的机器和生产线组件添加到购物篮中,并通过电 子邮件直接下订单。 在 myEirich这一应用中,客户可以实 时跟踪服务订单的进度并实时监控其派单状态。
使用状况监控
使用该系统,可以监控和分析物理参数以确定机器 当前的工作状态和使用状况。传感器可以提供实时数据 用于分析。持续的数据采集可以快速分析出发展趋势并 在故障实际发生之前,提前提示组件可能的损坏。 碰撞、 轴承损坏、不平衡、齿轮故障和磨损都可以在早期检测 中发现并做出预警。这使客户能够及时订购更换零件或 在机器出现故障之前开始联系服务部门——进而避免了 等待服务工程师上门维修的无必要停机时间。
电子服务
无需服务技术人员到场的在线服务——远程服务和 远程诊断。实现机器运转和生产过程数据的自动收集和 分析,意味着技术人员可以远程甄别和定位故障点。 一 旦得到客户的批准,可以立即采取措施修复故障,并且 可以在技术人员不到场的情况下为客户定制软件更新。
爱立许-增强现实
借助增强现实提供服务,专家可以通过使用智能手机 摄像头和智能眼镜,了解系统的当前状态和状况。得益于 先进的3D对象跟踪和捕捉技术,箭头、注释和标记可以 叠加显示在屏幕上,使用户更容易遵循专家的指示。这最 大限度地提高了生产力,减少了停机时间,而且最为重要 的是大大节省了时间和资金成本。借助用于流程分析的数 字工具,爱立许产品能够提供优化解决方案,得以安全可 靠地改进生产流程。
质量控制系统
使用 EIRICH ProView工具,各个 QualiMaster 质 量控制系统为产品相关应用领域提供了质量保证。该系统 连续自动地从被混合的材料中取样,以多种方式测量材料 的特性。ProView 软件还可以对数据进行可视化分析整理。 凭借出色的用户友好性、令人难以置信的清晰视觉信息呈 现和一系列调整功能和选项,该系统让用户得以对流程进 行全方位监控,并且可以控制生产进程。采集的数据结果 由专家或借助人工智能加以充分分析,以便在后续批次生 产中可以获得连续性不间断地改进。这提高了产品质量并 大大减少了浪费,使客户的生产工艺更富稳定性和高效性。 QualiMaster系统已经应用于优化成型材料特性、水分含 量、稠度和流动特性,以及优化颗粒的生产过程。 欲了解详情,请访问官网:www.eirich.de/de/ digitale-loesungen/ ■
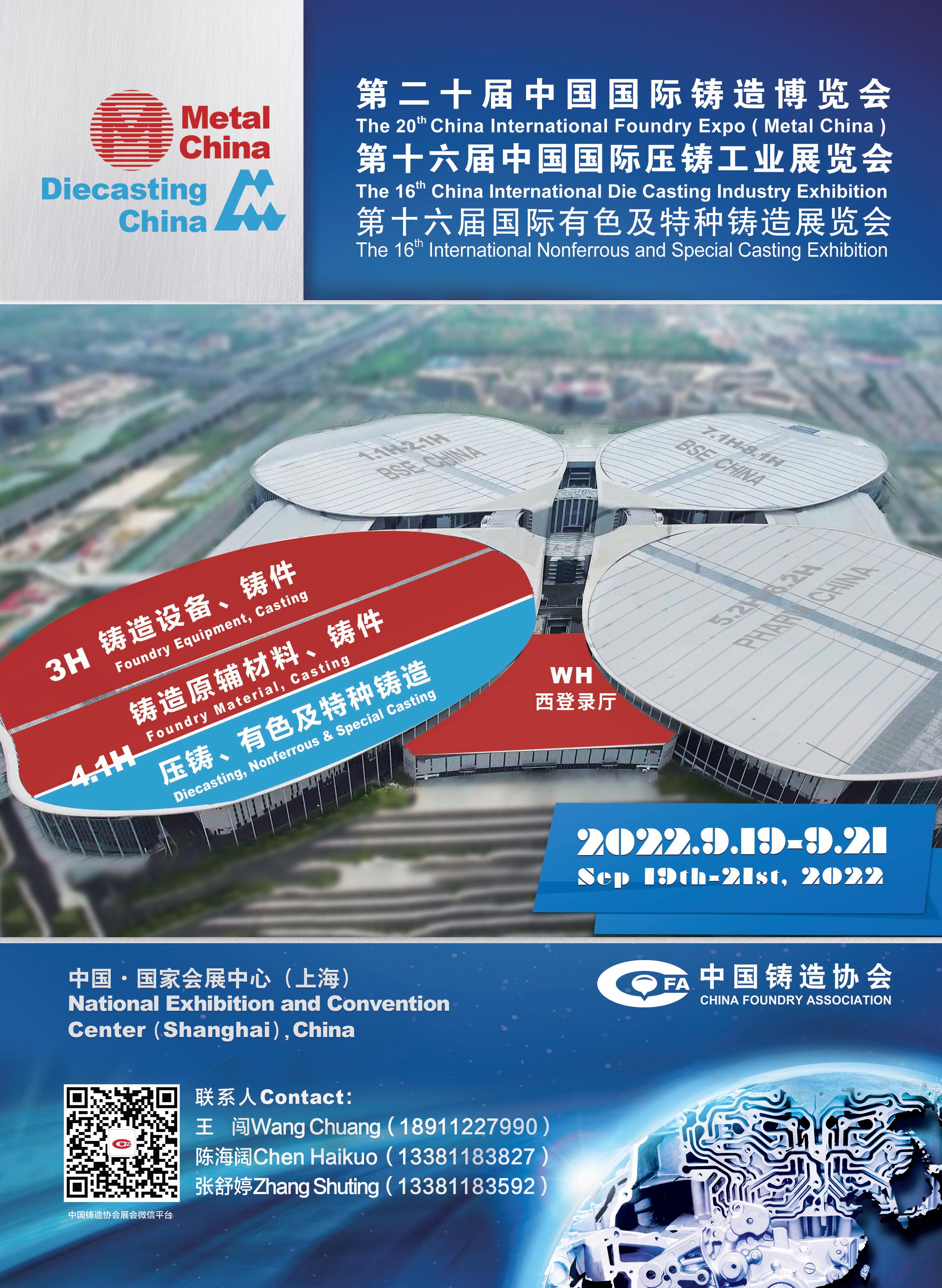
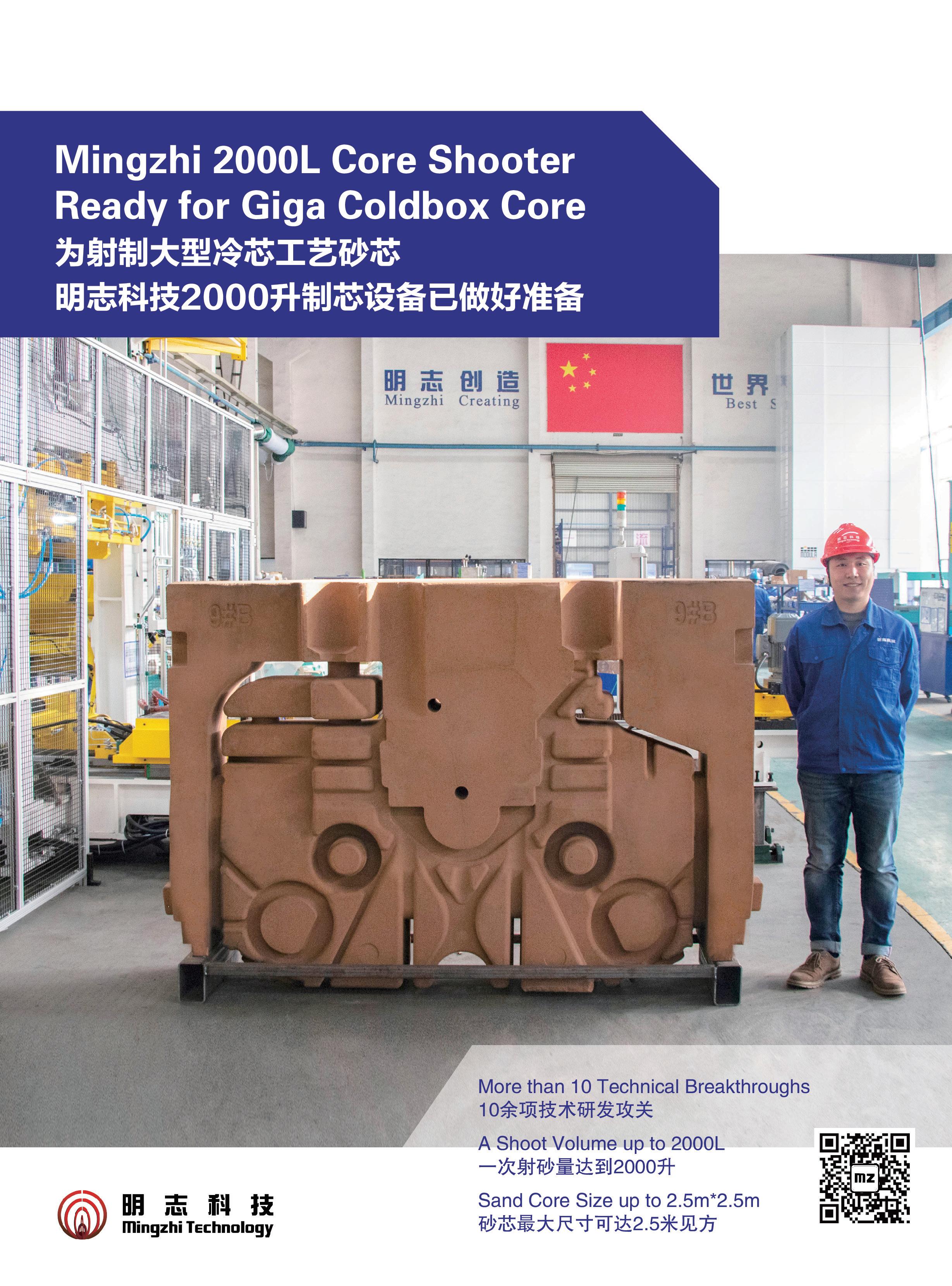