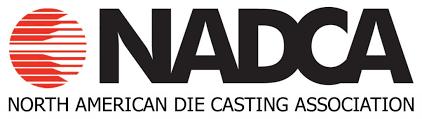
40 minute read
New Book from AFS Details Keys to Structural Aluminum Castings
Sure Cast, owned by Nordstern Group in Winnipeg, Canada, is primarily a green sand molding operation with some nobake sand casting. Employing approximately 20 people, the company also produces its own cores in-house and offers heat treating, cleaning, and grinding.
“We definitely want to grow and have a bigger offering for our customers,” said Sure Cast General Manager Andrea Lindquist. “And from a staffing perspective, it’s extraordinarily challenging these days––right now, everybody’s having issues with labor. The ownership team in Canada felt strongly about putting our best foot forward to have a comfortable facility for our employees, as well as for customers. We have an opportunity to bring in additional talent going forward because we have such a nice facility.”
Advertisement
New equipment added to the team’s excitement as movein drew to completion at the end of April. Chief among its capital investments is the newly installed Sinto FDNX 16 x 20 automatic molding machine that replaced old jolt/squeeze molding equipment. Sure Cast also added a fully automatic, customized sand return system from Green Sand Controls, which has been installed indoors due to severe Northern temperature fluctuations. Additionally, new conveyor systems within the new floorplan will facilitate improved mold handling. The move-in, which included the foundry’s nobake sand system with two large silos, was completed at the end of May.
“I’m really excited about the opportunity for a fresh start,” said Lindquist, “not only with a brand-new facility and a lot of brand new equipment, but the opportunity to really go deeper with lean manufacturing and continuous improvement principles that we haven’t had a chance to do before because of the way our facility was set up–– we were kind of boxed in at our previous space, which made it hard to change and make improvements. With this new space, we definitely will be able to do that.” ■
Sure Cast铸造公司隶属于加拿大温尼伯的 Nordstern集团,主要采用湿型砂工艺,兼有自硬砂工艺 的铸造企业。该公司有近20名员工,并可自行制芯,进行 热处理、清理和打磨等工序。 公司总经理Andrea Lindquist表示:“我们希望公司 业务不断增长,为客户提供更多的产品。但是,员工招聘是 非常具有挑战性的——现在,每个企业都存在用工难的问 题。加拿大的管理团队在尽最大努力为员工和客户提供舒适 的工作环境。我们具备很好的工作环境,因此我们有机会招 聘到更多的人才。” 4月底,随着工厂搬迁接近尾声,新设备的安装使团队 激动不已。其中,主要包括新安装的新东FDNX 16x20自 动造型线,它取代了旧的震动/挤压成型设备。Sure Cast 公司还安装了Green sand Controls公司的全自动、定制 化砂回收系统,由于当地气温变化较大,该系统安装在室内。 此外,新的运输系统将有助于改进铸型的传送。包括自硬砂 系统和两个大型筒仓在内的搬迁工作已于5月底完成。 Lindquist说:“公司将迎来新的开始,我感到非常高 兴。我们不仅将有全新的工厂和很多全新的设备,还将有机 会真正深入实施精益制造并持续改进,因为新厂就是按这样 的规划建立的,这在以前是不可能做到的。因为以前我们受 到很大的局限,很难做出改变和改进。现在有了新的工厂, 我们一定能够做到。”■
A new book from two of the aluminum industry’s most respected experts teaches metalcasters the keys to creating superior structural aluminum castings.
Written by Mahi Sahoo and David Weiss, Aluminum Castings for Structural Applications goes beyond the basics to explore the factors that affect mechanical properties of structural aluminum castings, the influence of alloying elements, solidification characteristics, heat treatment, and other advanced metallurgical concepts. The book, published by the American Foundry Society, originated as a well-received presentation delivered by the authors in 2015.
两位备受尊崇的铝合金专家出版新书,向铸造行业讲 解生产卓越铝合金结构件的关键。 由Mahi Sahoo和David Weiss编写的《铝合金结构 件的应用》,超出基础知识的范畴,深入探索了影响铝合金 结构件机械性能的因素、合金元素的影响、凝固特性、热 处理和其他先进的冶金学理念。本书由美国铸造协会出版, 作者曾于2015年发表相关演讲,获得好评。 全书共229页,共10章: • 结构件简介
At 229 pages, the book’s 10 chapters are: •Introduction to Structural Castings •Design of Structural Aluminum Castings •Influence of Alloying Elements for Structural Applications & Alloy Selection •Phase Diagrams and Solidifications Characteristics •Casting Processes •Gating and Riser Design •Alloys and Composites for High-Temperature Applications •Post-Casting Operations •Testing for Quality •Conclusions: Developing Trends and the Path Forward
Design engineers, manufacturing engineers, casting engineers, foundry metallurgists, and other aluminum foundry staff will benefit from this book. Additionally, Aluminum Castings for Structural Applications is a valuable resource for undergraduate and post-graduate students interested in casting technology.
This book is available exclusively from the AFS Store for $210, or $157.50 for AFS Members and $105 for AFS Corporate Members. About the authors
Mahi Sahoo is President at Suraja Consulting Inc. (Ottawa, Ontario, Canada). A longtime leader in the aluminum industry, Sahoo's expertise includes alloy development, process development, gating and riser design, heat treatment, sand casting, and failure analysis, among other topics. He earned his PhD in physical metallurgy from the University of British Columbia.
David Weiss is Vice President of Research and Development at Eck Industries (Manitowoc, Wisconsin). He is the recipient of the John A. Penton Gold Medal from AFS for his pioneering work and his willingness to explore new technologies in aluminum, magnesium, and metal matrix composite alloys. Weiss is a graduate of the Milwaukee School of Engineering.■
• 铝合金结构件的设计 • 合金元素对结构件应用的影响及合金的选择 • 相图和凝固特性 • 铸造工艺 • 浇口和冒口设计 • 高温合金和复合材料 • 铸件后处理 • 质量检测 • 结论:发展趋势和方向 设计工程师、生产工程师、铸造工程师、铸造冶金学 家和其他铝铸造从业人员将从本书中受益。此外,本书是对 铸造技术感兴趣的本科生和研究生的宝贵学习资源。 本书仅在美国铸造协会的图书商店有售,售价为210 美元;美国铸造协会个人会员可享受优惠价为157.50美元, 企业会员优惠价为105美元。
关于作者
Mahi Sahoo是Suraja咨询公司(加拿大安大略省 渥太华)总裁。作为长期服务于铝合金行业的领导者, Sahoo的专长包括合金开发、工艺开发、浇口和冒口设计、 热处理、砂型铸造和故障分析等。他在不列颠哥伦比亚大学 获得物理冶金学博士学位。 David Weiss是Eck Industries(威斯康星州马尼托瓦克) 公司的研发副总裁。他是美国铸造协会颁发的John A. Penton 金质奖章获得者,以表彰他在铝、镁和金属基复合合金新技术 方面的开创性工作。Weiss毕业于密尔沃基工程学院。■
MEITECH, International Summit of Die Casting & NADCA South Congress 20 23
APRIL 19, 20 & 21. 2023 Centro de Convenciones de San Luis Potosi. ADRIANA TAVARES VELASCO San Luis Potosi, México. adriana.tavares@meitechexpo.com 52 442 149 629 www.meitechexpo.com
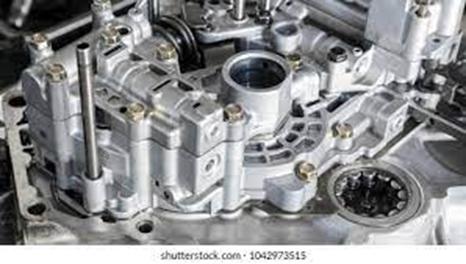
THE EUROPEAN FOUNDRY INDUSTRY IN 2020
CAEF-The European Foundry Association
2020欧洲铸造业概况
欧洲铸造协会
The Economic Situation in the Major Casting Customer Industries · Vehicle construction 主要铸件市场的表现
·汽车行业
The international passenger car markets were hit hard by the Covid-19 pandemic in 2020. Nearly all over the world sales decreased significantly. The European market, however, suffered by far the largest losses. Even a variety of purchase incentive programmes, which were often limited to vehicles with alternative engines, could only partially prevent sales figures from collapsing even further. The reason for the deep cuts is that the vehicle markets in 2020 faced major problems on both the supply and demand sides.
In Europe, almost 12.0 million passenger cars were newly registered in 2020, which was 24.3% less than in the previous year. All the five largest markets recorded double-digit falls. In Germany new car registrations lost 19%. Sales in France were down by one quarter. New registrations lost almost one third in Italy (-28%) and the United Kingdom (-29%). The Spanish market decreased most by 32%. All other countries in the European market finished the year 2020 with a negative result, too.
In the US, the light vehicle market (passenger cars and light trucks) finished 2020 with nearly 14.5 million vehicles sold (-15%). In 2020 the Japanese new car market totalled 3.8 million passenger cars, some 11%below the previous year’s result. Russia’s light vehicle sales fell by 9% last year, to 1.6 million units. In India the passenger car market also recorded a significant decrease in 2020 of 18% and Brazil even27%.
As in 2020, there will be production shutdowns and shorttime work among various manufacturers in 2021. The production forecasts have therefore already been adjusted downwards in the first half of 2021 and are only slightly above the
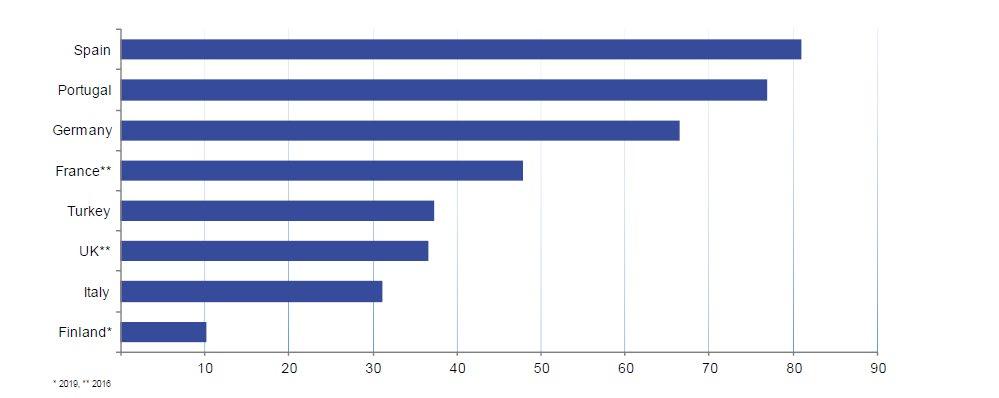
2020年,国际乘用车市场受到Covid-19疫情流行的 沉重打击,其销量几乎在全世界范围内大幅下降。而且,欧 洲市场遭受了迄今为止最大的损失。即使有各种平时仅针 对新能源汽车的鼓励消费措施,但也只能起到有限的作用。 而销量下降的原因是2020年的汽车市场在供需两方面都面 临重大问题。 在欧洲,2020年乘用车注册量为近1200万辆,比上 年减少24.3%。五个最大的汽车市场均表现为两位数的跌 幅。德国的新车注册量下降了19%。法国的汽车销量下降 了四分之一,意大利和英国的销量下降了近三分之一,分别 是意大利(-28%),英国(-29%)。西班牙市场跌幅最大, 为32%。欧洲其他国家的市场也是负增长。 2020年,美国轻型汽车市场(乘用车和轻型卡车)售 出近1450万辆(-15%)。日本新车市场总量为380万 辆乘用车,比上年下降约11%。俄罗斯的轻型汽车销量下 降了9%,为160万辆。印度的乘用车市场下降了18%, 巴西甚至下降了27%。 与2020年一样,2021年各厂家出现停产停工,因此已 经下调了2021年的产量预测。由于疫情,汽车行业也加快了 向替代驱动转型 的速度。在此背 景下,欧洲的汽 车制造商和政府 增加了研发新内 燃机的雄心。 ·机械工程 2020年, Iron Castings for the Vehicle Industry 2020 (in %) 世界各地的机械 2020年汽车行业铸铁件欧洲主要国家产量占比 设备制造商都受
figures for 2020. In the wake of the pandemic, the transformation of the vehicle industry towards alternative drives has also accelerated. In this context, vehicle manufacturers and governments in Europe have recently significantly increased their ambitions to replace combustion engines. · Mechanical engineering
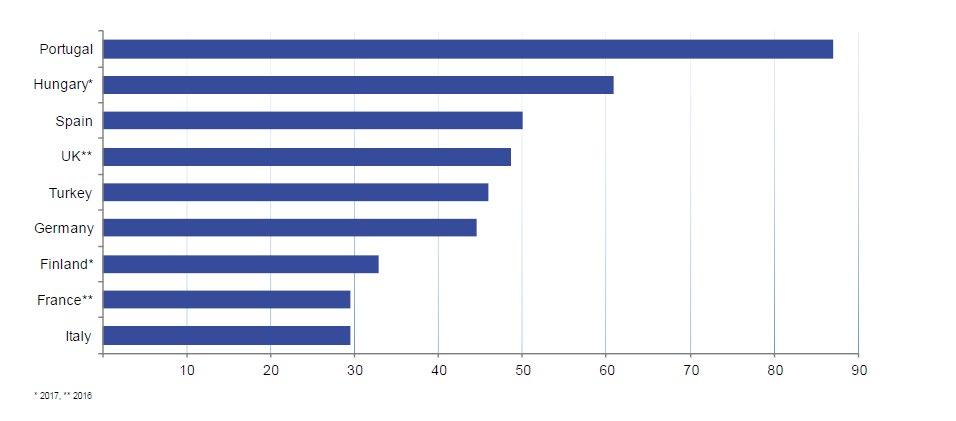
Machinery and equipment manufacturers worldwide suffered the effects of the pandemic. The biggest drop in production was in the EU's domestic market, since EU machine production decreased by around13% in 2020. This is the most significant decline since the financial crisis in 2009. Due to the diversity of the mechanical engineering industry, individual sectors have been quite differently affected by the negative impacts. While the casting-intensive machine tool industry is one of the biggest losers with production declines of around 30% due to the sales crisis and the ongoing transformation in vehicle manufacturing, the manufacturers of agricultural machinery were able to benefit from full order books even during the pandemic and close the year in the black.
While the Japanese (-12%) and the US-American (-9%) machinery and equipment manufacturers also clearly missed the previous year's figures.
There are signs of a solid recovery in European machinery and equipment manufacturing in 2021. It will probably take until 2022 before the pre-crisis level is reached again. · Steel industry
Global crude steel production reached 1,878 million tonnes in 2020, which was almost exact the same production volume like in the year before.
The EU produced 138.8 million tons of crude steel in 2020, a decrease of 11.8% compared to 2019.Germany produced 35.7 million tons of crude steel in 2020, down 10.0% on 2019. Turkey’s crude steel production for 2020 was 35.8 million tons, up by 6.0% on 2019.
Asia produced 1,374.9 million tons of crude steel in 2020, an increase of 1.5% compared to 2019.China’s crude steel production in 2020 reached 1,053.0 million tons, up by 5.2% on 2019. India’s crude steel production for 2020 was 99.6 million tons, down by 10.6% on 2019. Japan produced 83.2 million tons in 2020, down 16.2% on 2019. South Korea produced 67.1 million tons, down 6.0% on 2019.
The United States produced 72.7 million tons in 2020, down 17.2% on 2019. Russia is estimated to have produced 73.4 million tons in 2020, up 2.6% on 2019. Ukraine produced 20.6 million tons in 2020,down 1.1% on 2019. The Middle East produced 45.4 million tons of crude steel in 2020, an increase of2.5% on 2019. Iran is estimated to have produced 29.0 million tons in 2020, up 13.4% on 2019. Annual crude steel production for South America was 38.2 million tons in 2020, a decrease of 8.4% on 2019.Brazil produced 31.0 million tons in 2020, down by 4.9% compared to 2019.
The pandemic has accelerated some key trends, which
Ductile Iron Castings for the Vehicle Industry 2020 (in %) 2020年汽车行业球墨铸铁件欧洲主要国家产量占比
到了疫情的影响,产量降幅最大的是欧盟市场,其产量下降 了约13%。这是自2009年金融危机以来的最大降幅。由 于机械工程行业的多样性,不同行业受到的影响不尽相同。 与铸造紧密相关的机床行业受到的影响可谓最大,由于销售 惨淡和汽车制造的持续转型,机床行业的产量下降了30% 左右,但农业机械制造商却实现了增长。 日本(-12%)和美国(-9%)机械设备制造商的销 量也明显下降。 2021年欧洲机械设备制造业有稳健复苏迹象,但可能 要到2022年才能再次达到疫情前的水平。
·钢铁行业
2020年,全球粗钢产量达到18.78亿吨,与上年几乎 持平。 欧盟2020年的粗钢产量为1.388亿吨,比2019年 下降11.8%。德国的产量为3570万吨,比2019年下降 10.0%。土耳其的产量3580万吨,比2019年增长6.0%。 2020年,亚洲的粗钢产量达13.749亿吨,比2019 年增长1.5%。其中,中国的粗钢产量达到10.53亿吨, 比2019年增长5.2%。印度的产量为9960万吨,比 2019年下降10.6%。日本为8320万吨,比2019年下降 16.2%。韩国的产量为6710万吨,比2019年下降6.0%。 2020年,美国的粗钢产量为7270万吨,比2019年 下降了17.2%。俄罗斯的预计产量为7340万吨,比2019 增长了2.6%。乌克兰的产量为2060万吨,比2019年下 降了1.1%。中东国家的粗钢产量为4540万吨,比2019 年增长2.5%。伊朗的预计产量为2900万吨,比2019年 增长13.4%。南美的粗钢产量为3820万吨,比2019年 下降8.4%。巴西产量为3100万吨,比2019年下降4.9%。 一些重要的发展趋势在疫情下得到加速发展,也将引 起钢铁市场需求的转变。钢铁行业将通过数字化、自动化、
will bring about shifts in steel demand. The steel industry will see rapid developments through digitization and automation, infrastructure initiatives, reorganization of urban centers and energy transformation. · The Foundry Industry
In 2020, the iron and steel foundries of the CAEF member states produced 9.1 million (m.) tons of castings. Compared to the year before, this corresponds to a 19.8% decrease in production weight. The six countries that dominate the industry in terms of weight, namely Germany, Turkey, France, Spain and Italy, account for 79.8% of the production of ferrous metal castings. The production decreased in all countries with double digits compared to the previous year. The exceptions are Turkey and Hungary. While in Turkey the production was 4.4% lower than in 2019, Hungary showed even a positive sign with a plus of 0.3%.
In 2020, non-ferrous metal foundries in the CAEF member states booked a production decrease of19.1% to round about 3.3 m. tons. The countries that dominate the production of nonferrous metal castings, namely Germany and Italy, account for 43.2% of the total volume of non-ferrous metal castings produced in the CAEF member states.
The number of employees in iron and steel foundries increased in Italy, Slovenia and Turkey. All in all, however, the employment of foundries located in CAEF member states decreased by 7.5% to 130 700people.
In 2020 the non-ferrous metal sector was also dominated by negative employment trends. Compared with the figures of the ferrous foundries fewer people were affected by this. In the End of 2020, 113 000people worked for European foundries. Compared to 2019 the number of employees decreased by4.6%.
The share of cast iron with lamellar graphite in the output total of iron and steel castings was 48.5%, as lightly smaller share than in the year before. Correspondingly, the share of ductile cast iron logged(43.9%). The share of steel sector was slightly higher (7.5%).
The production of castings made of non-ferrous metal alloys is still dominated by light metals. The share was 86.6%. Furthermore, the share of copper alloys holds the level of round about 5.6%. Therefore, the share of components made of zinc alloys was 6.3%.
From the data available it appears that the export quota of the iron and steel foundries increased slightly from 39.5% last year to 42.3% in 2020. Calculation base is the foreign trade report of eight member countries. Germany, the country that dominated the export trade in castings in the past experienced the greatest decline with a volume of more than 1.05 million tons (-32.7%). Turkey reported an export volume of almost 0.98 million tons (-9.7%) and therefore is again the second biggest export nation of iron and steel castings. Spain exported a volume of 0.62 million tons (-16.7%) and is placed the third place. The fourth place is booked for Italy (386 600 tons, -20.8%). French foundries almost exported the same volume (384 300 tons) which equals a decline by 14.2%.
基础设施建设、城市中心重建和能源转型实现快速发展。
·铸造行业
2020年,欧洲铸造协会成员国的黑色铸造企业共生产 铸件910万吨,与2019年相比,产量减少了19.8%。德国、 土耳其、法国、西班牙和意大利这几个主要铸件生产国的黑 色金属铸件产量占比为79.8%。与上一年相比,几乎所有 成员国的铸件产量均表现为两位数的下降。但土耳其和匈牙 利是例外,土耳其的产量比 2019年减少4.4%,匈牙利甚 至增长了0.3%。 欧洲铸造协会成员国有色金属铸造企业的产量下降了 19.1%,产量为330万吨左右。有色金属铸件的主要生产 国德国和意大利占成员国总产量的43.2%。 意大利、斯洛文尼亚和土耳其的铸造厂员工人数有所 增加。然而,欧洲铸造协会成员国铸造企业的员工人数减少 了7.5%,减少到130,700人。 2020年,有色金属行业的就业率也是负增长趋势,但 受到的影响比黑色铸造行业小。到2020年底,欧洲有色铸 造企业的员工为113,000人。与2019年相比,员工人 数减少了4.6%。 灰铸铁占黑色铸件总产量的比重为48.5%,比上年略 有下降。相应地,球墨铸铁的产量占比为43.9%。铸钢件 产量略有增长(7.5%)。 有色金属铸件的生产仍以轻金属为主,占比为 86.6%。此外,铜合金的产量保持在5.6%左右的水平, 锌合金产量为6.3%。 从现有数据来看,黑色铸造厂的出口量从2019年的 39.5%小幅上升至2020年的42.3%,统计基数为8个成 员国的外贸数据。作为最大的铸件出口贸易国,德国的降幅 最大,超过105万吨(-32.7%)。土耳其报告的出口量 接近98万吨(-9.7%),因此再次成为黑色铸件的第二大出 口国。西班牙的出口量为62万吨(-16.7%),位居第三。 意大利位居第四位(386,600吨,-20.8%)。法国的出口 量与意大利相当,为384,300 吨,下降了14.2%。 如果仅从欧洲铸造协会成员上一年的铸件产量数据 来看,黑色铸件的产值下降了9.5%,铸件产量下降了 19.8%。从现有的有色金属行业数据来看,产值同比下降 15.6%,铸件产量大约降低了19.1%。 统计数据不包含缺少数据报告的国家。
不同材质铸件形势
·铸铁
2020年,欧洲铸造协会成员国的铸铁件产量为440
If we consider only those CAEF member states with current figures for the previous year, the value of the iron and steel castings produced decreased by 9.5%, in doing so the weight of castings fell by 19.8%.From the data that is available on the production value of the non-ferrous metal sector a yearon-year comparison shows a decline of 15.6%. It appears that the weight of castings produced was 19.1% lower.
All countries with missing data were excluded from the calculations.
The Situation in the Casting Material Sectors · Iron
万吨,下降了21.1%。只有土耳其的产量有所增加(增长 0.5%)。除瑞士和芬兰外,其他国家都不得不面对两位数 的负增长率。与以前情况一样,铸铁行业的可用数据太少, 因此无法确定总产值。由灰铸铁制成的部件主要用于汽车和 机械工程行业。在汽车行业,铸件使用量最高的分别是葡萄 牙(83.5%)、德国(66.5%)和土耳其(37.3%)。对 于机械工程行业,铸铁件需求量最大的是意大利(53.6%)、 土耳其(34.5%)和芬兰(28.9%)。 在意大利和土耳其,铸铁厂(包括球墨铸铁)的就业 人数有所增加,而瑞士则保持稳定。而其他国家的就业人数 下降,导致欧洲铸铁企业从业人数整体下降7.6%。
At 4.4 million tons, the output of the CAEF member states was down by 21.1%. A growing production was only logged for Turkey (0.5%). Except Switzerland and Finland all other countries had to deal with negative growth rates in double digits for the year 2020. As ever, the data available for the cast-iron sector is too sketchy to allow determining the overall value of production. The output of components made of cast iron with lamellar graphite is largely destined for the motor vehicle and mechanical engineering industries. For the motor vehicle industry, the highest absorption rates were reported from Portugal (83.5%), Germany (66.5%) and Turkey (37.3%) respectively. For the mechanical engineering in industry the highest shares in the output were posted for 2020 by Italy (53.6%), Turkey (34.5%), and Finland (28.9%).
The number of persons employed in iron foundries (incl. ductile cast iron) increased in Italy and Turkey and was stable in Switzerland. In all other countries employment decreased, leading to a 7.6% decline overall. · Ductile Cast Iron ·球墨铸铁
2020年,球墨铸铁企业报告的产量下降了19.4%, 下降至400万吨。 匈牙利的球墨铸铁件产量有所增长(4.2%)。除土耳 其的产量下降8.5%以外,所有其他国家均出现两位数的下 降。
含有球状石墨的铸铁产品传统上在球铁领域占据主导 地位,在过去几年中保持了99%的市场份额。相应地,作 为小众产品的可锻铸铁所占份额略高于1%。在这种情况下, 应该指出的是,可锻铸铁件的统计数据已经在一定程度上失 去了意义,因为在某些国家,无法计算出球墨铸铁行业的数 据。因此,自2016年以来,不再收集可锻铸铁件的数据。 球铸件主要生产于德国、土耳其、法国、西班牙和意大利。 与以往一样,球墨铸铁件主要应用于汽车和机械工 程行业,建筑行业位居第三。如果对那些已有数据国家的 汽车铸件产量进行分析,可以发现葡萄牙的产量最高, 为87.0%,土耳其45.9%,德国44.6%。机械工程铸件
The producers of ductile cast iron reported a decrease of output by 19.4% to 4.0 million tons.
Hungary only logged an upturn in production (4.2%). Apart from Turkey (-8.5%) all other countries closed the year 2020 with a double-digit decline.
Cast iron with spheroidal graphite traditionally dominates the ductile cast iron sector with an unchanged share of 99% during the last years. Correspondingly, malleable iron as a niche product holds a share of a little bit more than 1%. In this context, it should be noted that malleable casting statistics have lost some of their meaning because in some states it is impossible to break down the figures for the ductile castiron sector. Therefore, data for malleable castings are not collected any more
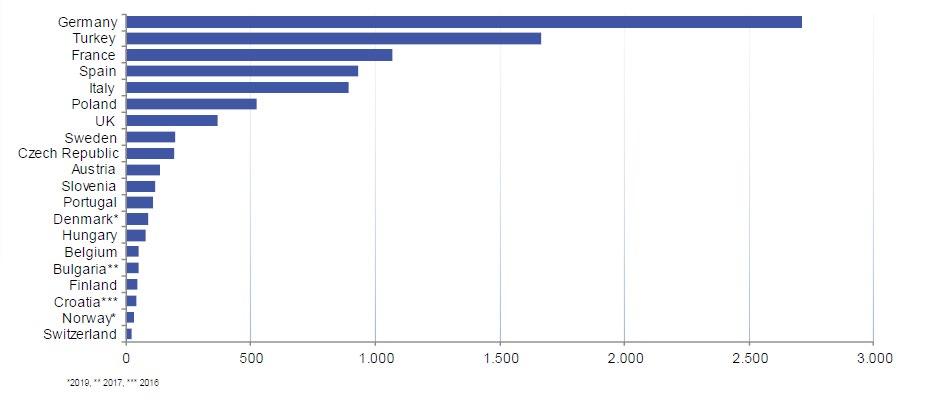
Production of Iron, Ductile Iron and Steel Castings 2020 (in 1000t) 2020年主要欧洲国家铸铁、球墨铸铁、铸钢件产量(单位:1000t)
since 2016. Nodular iron components are mainly produced in Germany, Turkey, France, Spain, and Italy.
As ever, components for the motor vehicle and mechanical engineering industries predominate in the production of ductile castings, with the building industry following in third place among the customer industries. If analyzing the shares of motor vehicle castings in those countries for which data are available, one sees that the highest shares are reported from Portugal at 87.0%, Turkey at 45.9%, and Germany at 44.6%. The mechanical engineering industry holds the highest shares in output in Finland(90.5%), Italy at 54.7%, and Germany at 33.2%. Unfortunately, it is impossible to present the share of the building industry. · Steel
产量最多的分别是,芬兰90.5%、意大利54.7%、德国 33.2%。遗憾的是,建筑行业的铸件产量无法统计。
·铸钢
In the year 2020 the output of steel castings decreased by 13.2% to 686 000 tons. Turkey, the leading producer since 2018, logged a stable production volume compared to the year before. For Germany, second in line, the production decreased by 22.6%. An increased production was only reported for Switzerland (8.7%). Production in all other countries decreased due to the pandemic.
In those member countries for which data for a year-on-year comparison was available, the value of the output of steel casting components decreased by 9.0%.
The number of persons employed in steel foundries was stable in Switzerland, and Italy. In Turkey and Spain, the number of employees increased, whereas the number of persons employed decreased in Germany, Finland, Portugal, and Poland. At the end of 2020 nearly 22 100 people were employed in European steel foundries. · Non-ferrous metal castings
The output of non-ferrous metal casting components in the CAEF member countries decreased by19.1% to 3.3 million tons. As before, the non-ferrous metal sector is dominated by Germany, Italy, Turkey, France, and Poland. The share of the first three countries equals 58.0% in 2020. In Belgium only an increasing production volume was logged. Hungary reported a slightly negative production(-1.9%), while all other CAEF member countries showed a doubledigit decrease.
Traditionally, the production of non-ferrous metal castings is
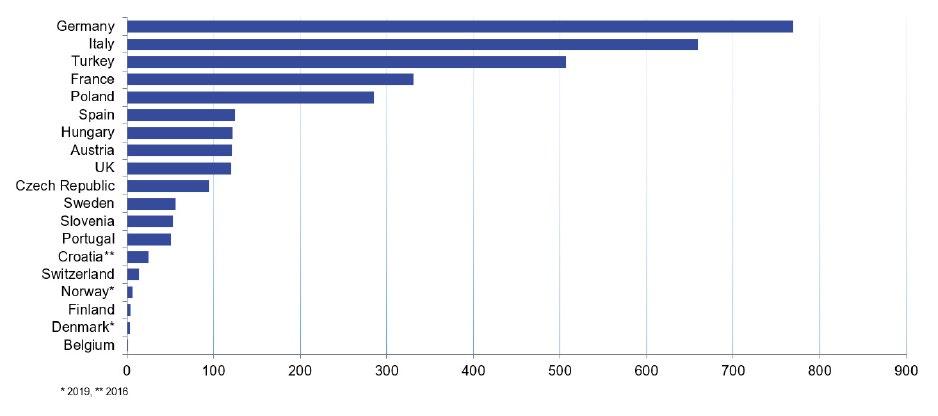
2020年,欧洲铸钢件产量下降13.2%,下降至68.6 万吨。其中,土耳其是自2018年以来产量最大的国家, 与2019年相比,其产量保持稳定。排在第二位的德国的 铸钢产量下降了22.6%。仅瑞士报告的铸钢产量实现增加 (8.7%)。由于疫情大流行,其他国家的铸钢产量都下降了。 在可进行同比数据计算的国家中,其铸钢件的产值下 降了9.0%。 在瑞士和意大利,铸钢企业的就业人数保持稳定。 土耳其和西班牙的员工人数有所增加,而德国、芬兰、葡 萄牙和波兰的雇员人数有所减少。到2020年年底,有近 22,100人受雇于欧洲铸钢企业。 ·有色金属铸 件 2020年, 欧洲铸造协会成 员国的有色金 属铸件产量为 330万吨,下 降了19.1%。 和以前一样,有 色金属铸件产量 最大的国家是德 Production of Non-ferrous Metal Castings 2020(in 1000t) 国、意大利、土耳其、
2020年欧洲主要国家有色合金铸件产量(单位:1000t)
法国和波兰,前三 个国家的产量占比 为58.0%。仅比利时报告了产量增加。匈牙利报告的产量 略有下降(-1.9%),而所有其他欧洲铸造协会员国的产 量均出现两位数的下降。 传统上,有色金属铸件的生产以轻金属铸件为主。汽 车行业是最重要的用户。2020年,欧洲轻金属铸件(铝合 金和镁合金铸件)的产量较2019年下降了21.7%,产量 近290万吨。德国、意大利和土耳其三大生产国的产量占 总产量的58.0%。 2020年,在欧洲主要国家的轻金属产量中,德国下降 了33.4%,意大利下降了20.7%,土耳其下降了10.7%, 而且没有一个成员国报告为增长数字。其中,匈牙利产量下 降了2.8%,其轻型和超轻型铸件产量几乎与2019年持平。 在轻金属合金中,镁合金在产量方面占据第二位。德国是主 要生产国,产量为20,500吨,其次是意大利(3,700 吨)
dominated by light metals. The motor vehicle industry is the foremost customer. In the year 2020 the output of light metal castings (aluminum and magnesium) decreased by 21.7% compared to 2019, reaching nearly 2.9 million tons. Together, Germany, Italy and Turkey, the three major producers, account for 58.0% of the light-metal castings.
The production for these leading countries went down by 33.4% for Germany, by 20.7% for Italy and10.7% for Turkey. There was not a single CAEF country reporting growth numbers in 2020. Only Hungary (-2.8%) almost produced as many tons of light and ultra light castings as last year. Among the light metal alloys, magnesium plays a subordinate role in terms of output weight. Germany is the major producer with 20 500 tons followed by Italy (3 700 tons) and the United Kingdom (2 000 tons).
The second most important material category in the non-ferrous metal sector is that of copper and its alloys. For countries with registered production for 2020 the level decreased by 21.7%. The reported volume in 2020 reached a level of almost 192 000 tons. Because of the missing data of some countries it is difficult to estimate the real market volume. Hungary and Spain recognized a growth rate for production, while the rest reported significant decrease.
The output of zinc castings fell by 16.9% with a volume of nearly 209 600 tons. Italy, Germany, and Turkey are the major producers, together holding a share of 75.0% in output total. A positive production was logged for Italy and Hungary. All other countries reported decreasing production volume in 2020.
The statistical data available for the category of 'other non-ferrous metal alloys' are fragmentary. In addition, some countries include copper and zinc in this category, because there is no facility for segregating these. Therefore, it is impossible to analyze this category more extensively.
Source: ifo Munich, IMF, ACEA, VDA, VDMA, Euroconstruct, Worldsteel, CAEF ■
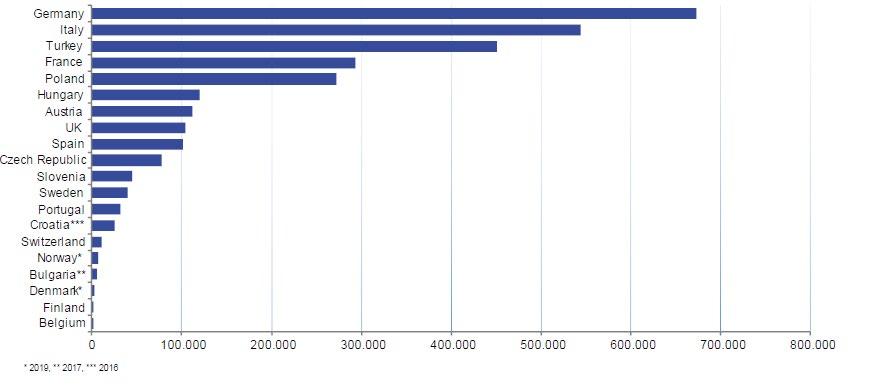
Major Producers of Magnesium Castings 2020 (in t)
2020年欧洲主要国家镁合金铸件产量(单位:t)
Production of Light and Ultralight Castings 2020 (in t)
2020年轻合金和超轻合金铸件产量(单位:t)
和英国(2,000 吨)。 除铝镁外,有色金属行业第二重要的材料是铜及其合 金。在报告了2020年产量的国家中,铜合金铸件产量下降 了21.7%,达到近19.2万吨的水平。由于一些国家的数据 缺失,很难估计出真实的市场规模。匈牙利和西班牙称其铜 铸件产量增长,而其余国家则报告产量显著下降。 锌合金铸件产量下降了16.9%,达近20.96万吨。意 大利、德国和土耳其是主要生产国,共计占欧洲铸造协会成 员国总产量的75.0%。意大利和匈牙利的产量实现正增长, 其他国家均报告产量下降。 可用于“其他有色金属合金”类别的统计数据是零散的。 此外,由于无法分离数据,一些国家将铜和锌包括在这一类 别中。因此,无法对这一类别做更多的分析。 信息来源:ifo Munich, IMF, ACEA, VDA, VDMA, Euroconstruct, Worldsteel, CAEF ■
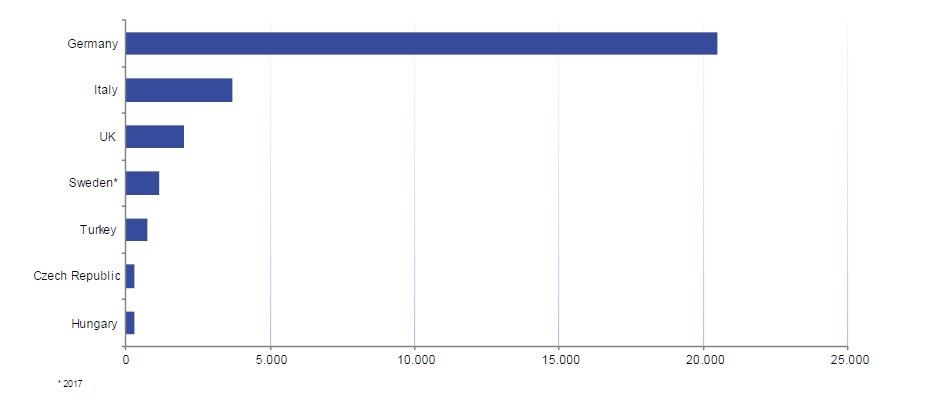
Challenge and Opportunities for Indonesian Foundries during Covid-19 Pandemic
ErwanYulianto, Chairman of Indonesia Foundry Association (APLINDO)
疫情期间印度尼西亚铸造行业面临 的挑战和机遇
印度尼西亚铸造协会主席Erwan Yulianto
The primary type of foundries under APLINDO are doing cast iron and alumunium. These commodities has not seen enough supply locally, causing many foundries to rely on imported raw materials. While Indonesia has a considerably large Bauxite reserves, namely in West Kalimantan, Bintan Islands, and Riau Islands, the number of facilities to refine them into proper alumunium is still not enough. Many secondary producers of alumunium ingots for the automotive die casting facilities have to resort in importing alumunium raw materials, further complicated by the recent global sea freight crisis. This is also the case with the iron industry where there are plenty iron ore deposits but not enough smelters to refine them. PT. Krakatau Steel Tbk, one of the oldest steel making company, has also been forced to resort to importing a huge portion of their iron scrap raw materials.
Since the start of the Covid-19 pandemic, Indonesia has also been subject to the challenges that the pandemic brought. Decrease for the global casting demand became a very difficult challenge for foundries across the world. In an effort to combat these hard times, the government of Indonesia introduced a series of new regulations to help promote growth and investment for Indonesian industries. After the second wave of Covid-19 in the middle of July 2021, there is a positive trend for the demand of castings in Indonesia. Supported by government regulations and increase in commodity prices, the growth of the casting industry from 2020 to 2021 saw an increase of 65% (year on year). Furthermore, the industry saw a further increase of 5% in the first quarter of 2022 compared to first quarter of 2021.
The government further implemented regulations to promote more upstream processing of the vast mineral resources in Indonesia in order to achieve positive economic impact for the national industry. Indonesia has seen many
对于一国的经济体系而言,铸造和金属加工行业 是工业体系的脊梁和支柱。铸件产品广泛应用于各行各 业,这些应用领域是经济增长的重要组成部分,比如汽 车和重型设备、电力设备、石油天然气、机械零部件、 泵阀、医疗、建筑等众多需要铸件的行业。在印度尼西 亚,对于铸件产品的需求一直处于持续增长之中,但是 铸造行业本身产能的增长速度不足以满足这一需求。截 止到目前,在印度尼西亚有大约300家铸造企业,服 务于印尼市场2.7亿人口的庞大市场。尽管铸造行业在 印尼如此重要,印尼铸造行业本身一直受限于原材料供 应不足这一困境。
印尼铸造协会的会员企业中从事铸铁件和铝合金铸 造的企业占多数。这些原材料在本地供应不足,导致严 重依赖原材料的进口。尽管印尼本身有大量铝土矿产储 备,主要集中在西加里曼丹岛、民丹岛和廖内群岛等地, 但是可以用来开采和加工这些矿藏,使之成为铝合金原 材料的设备仍然不足。许多给汽车用铝压铸件供应铝锭 的二级生产商,目前只能大量储备从国外进口的铝锭, 而由于海运价格的上涨,进口铝锭面临成本上的巨大挑 战。这样的情形同样发生于铸铁件生产企业中,铁矿储 备是有的,但是没有足够多的企业来开采和加工。比如 这家本土企业PT. Krakatau Steel Tbk,是印尼本 地历史最久的一家钢铁企业之一,目前面临着不得不从 国外进口大量废铁原材料用做生产储备。
自从新冠疫情以来,印度尼西亚一直面临着随之而 来的种种挑战。全球范围内的铸件需求下降是世界各国
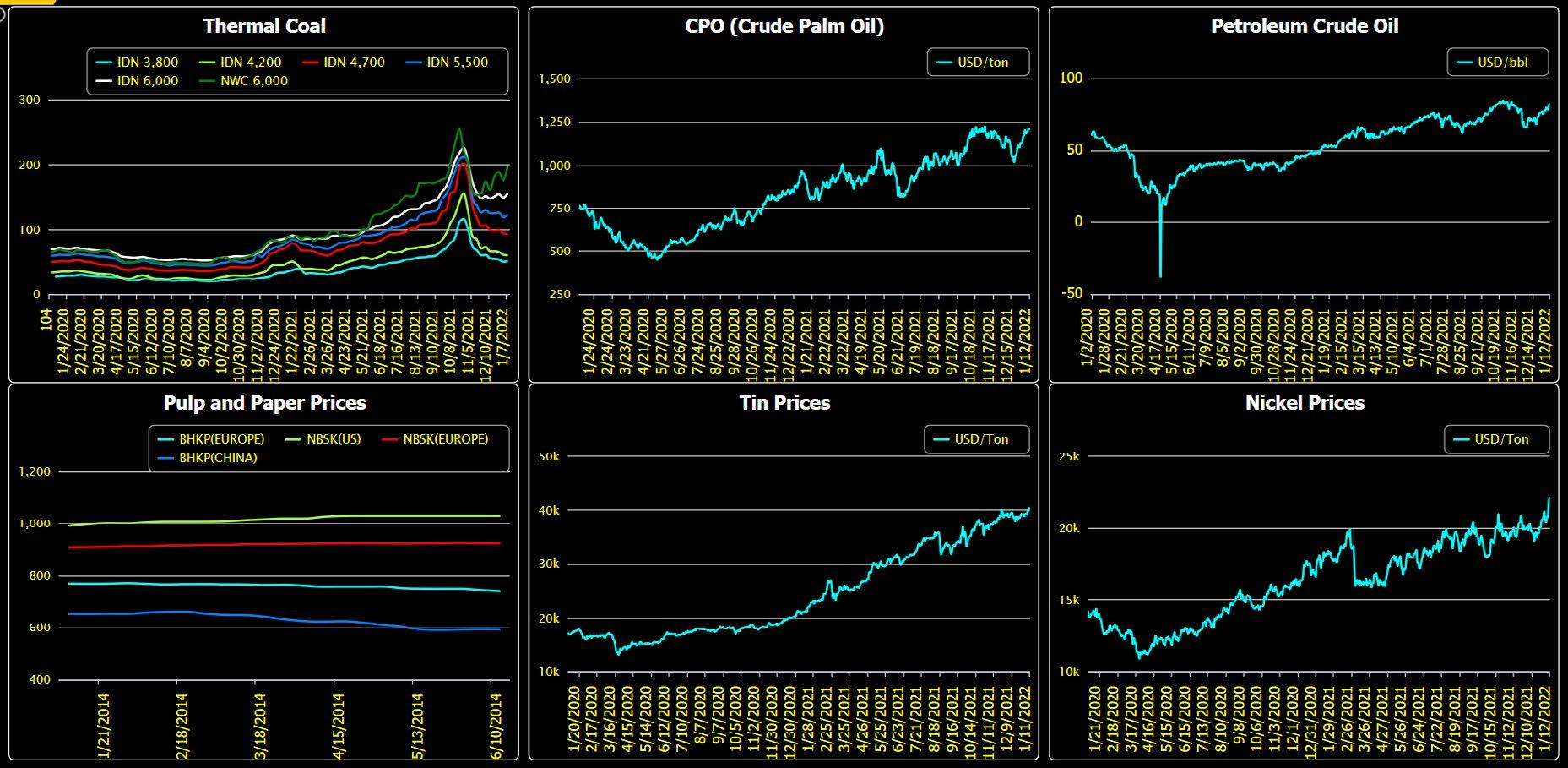
new smelters in response to these regulations. However, it will still take some time for positive effects to be realized, but when it does, Indonesia hopes to develop a more competitive ecosystem for its casting industry as a whole.
Although the main problem of difficult access to scrap and raw materials, the demand for casting products in Indonesia has been recovering and increasing steadily. The government has been supportive and are implementing policies that support growth for the foundry industry. Policies and regulations must be further improved in order to secure raw materials in order to support growth. It is hopeful that more upstream industries involved in producing raw materials will be developed in Indonesia to combat scarcity of raw material and support the ever growing demand for castings in Indonesia and the world.
We also would like to invite you all to International Metal Technology Indonesia exhibition scheduled for 21 to 23 September 2022 in Jakarta as an exhibitor or visitor. IMT Indonesia is dedicated for the Indonesia’s metal industry development that APLINDO hosts. Our show will be the new industrial exhibition that offers you and international metal industry leaders profitable businesses in Indonesia. ■
面临的共同难 题。印度尼西 亚政府一直在 努力,与这段 艰难时期进行 博弈,从政府 层面引入一系 列新的举措, 希望可以促进 对印度尼西亚 工业领域的投 资和规模增 长。 在2021 年7月中旬, 经过第二波新 冠疫情之后,我们发现对印尼铸件的需求呈现出回升走 势。总体来说,在政府加大政策扶持,提高商品指导价 的帮助下,铸件行业产量从2020年到2021年年度实 现了65%的明显增长。此外,在2022年第一季度, 行业数据显示去年同比增长了5%。 印度尼西亚政府还实施了一系列举措,希望可以 加强对印尼本国大宗原材料矿的开发与加工,以获得 对本国工业体系的更多推动。目前在新政策的刺激下, 已经有很多新的冶炼厂涌现出来。尽管仍需要一些时 间来体现这些政策对经济的正面推动作用,但是印尼 坚信一旦政策奏效,将会使得印尼本国铸造行业更具 国际竞争力。 虽然对于原材料缺乏这一困难仍需解决,印尼铸件 产品的需求量已经回升并且开始稳步增长。印尼本国政 府一直以来十分支持并推行了一系列政策,以推动铸造 行业增长。而对于保障原材料安全这一问题,政府将会 推行新的举措来保障生产安全。我们希望看到在印度尼 西亚,可以吸引更多原材料生产和加工企业,来改善原 材料稀缺的现状,同时进一步缓解印尼和全球铸造企业 面临的需求日益增长而产能不足的问题。 我们在此诚挚发出邀请,希望全球铸造业同业,关 注和参加将于2022年9月21-23日在雅加达举行的 国际金属技术展览会。IMT印尼金属技术展览会是由 印度尼西亚铸造协会举办的金属加工行业的盛会。我们 主办的该展会将会为参展商和参观观众带来行业内的一 流技术和产品,带来印尼市场中全新的商机。■
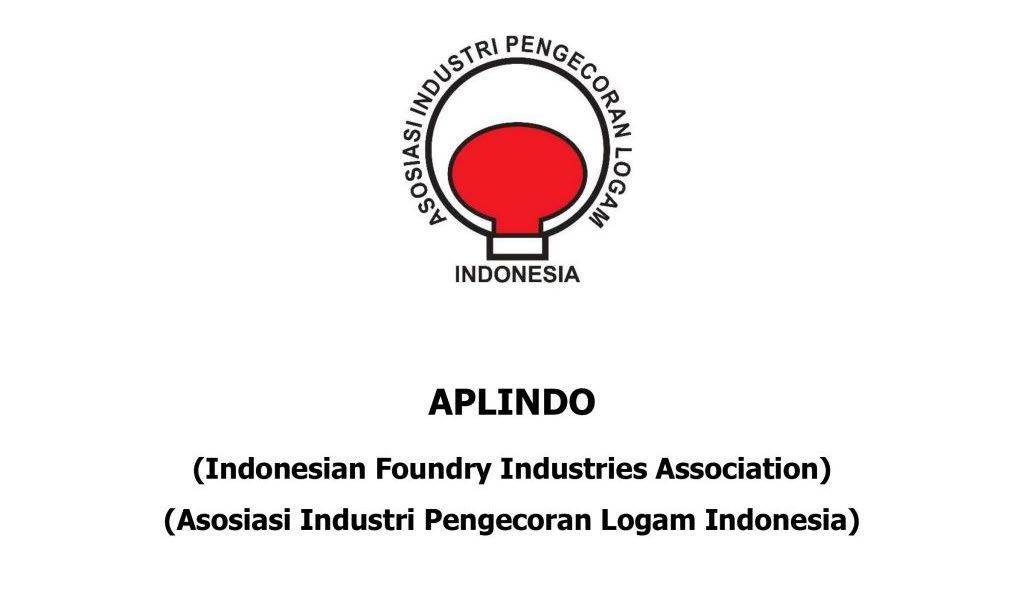
Obsolete Part Replacement in Two Weeks – Sand 3D Printing to the Rescue 在两周内更换废弃零件:3D砂型打印 技术的救援
Marine engines operate in harsh environments with constant exposure to humidity and water, often salt water, that will deteriorate engine components. Because diesel engines create combustion from high cylinder pressure and heat, they must run at high compression ratios in order to generate enough heat to auto-ignite the diesel fuel.
Cylinder heads are critical components in the engine that support other important parts such as the fuel injectors and inlet and exhaust valves. Located on top of the liner flange and secured to the cylinder block with nuts and bolts, they are exposed to extremely high temperatures and pressures, expanding and contracting as the engine rapidly heats and as it cools.
Because of these environmental conditions, marine diesel engines must be built to withstand the extreme pressures involved with high cooling requirements.
Hi-Tech Marine Engineering, a shipyard in Thailand, was faced with a cylinder head with cracks caused by the large amount of stress from overheating. With a business that operates every day of the week, the cargo boat needed a fast repair to return to service, yet the broken component was nearly a decade old and no longer in production from the OEM supplier. “Time to delivery is critical in our business – we cannot wait for parts because we are in constant operation, so we need fast turnarounds on-budget,” said Aomthep CheinSuwan, Owner of HiTech Marine.
A traditional replacement part had a lead time of over 10 months and would come at a very high investment cost. Because the cylinder head is a legacy part without tooling, an entirely new pattern and core box set would have to be manufactured first to produce the replacement casting. Yet Hi-Tec Marine required a replacement part within four weeks any overseas order would require at least eight weeks with increased costs for shipping.
Speed 3D Mold, a casting and prototype development shop located in Thailand had the solution to offer a highquality replacement part supplied with a fast turnaround. “For our customers in the maritime industry where there are many legacy parts that need replacement, speed is
船用发动机的运行环境恶劣,经常暴露在潮湿环 境和水中,通常是海水,发动机零部件会受到腐蚀。 由于柴油发动机通过高缸压和高热量燃烧,必须以高 压缩比运行,以产生足够的热量来自动点燃柴油燃料。 气缸盖是发动机中的关键部件,是其他重要部件 的支撑,例如燃油喷射器、进气阀和排气阀。它们在 缸套法兰顶部并用螺母和螺栓固定在气缸体上,暴露 在极高的温度和压力下,随着发动机的快速加热和冷 却而膨胀和收缩。 在此环境条件下,船用柴油发动机必须能够承受 与较高的冷却要求相适应的极端压力。 泰国造船企业Hi-Tech Marine Engineering 公司面临气缸盖因过热产生的大量应力而出现裂纹 的问题。货船需要得到快速维修才能继续投入使 用,但损坏的部件已使用近十年,并且不再由OEM 厂商提供。对此,Hi-Tech Marine公司的老板 Aomthep CheinSuwan说:“交货周期对我们的 生意至关重要——我们不能长时间等待零件,因为我 们不能停止运营,我们需要在预算内快速进行周转。” 一般情况下,新零件的交货时间超过10个月, 而且成本非常高。由于气缸盖需要模具生产,因此必 须首先制造全新的砂型和砂芯组才能生产新的替换零 件。然而,Hi-Tec Marine公司需要在4周内更换 零件,所有的海外订单都需要至少8周的时间,会增 加运输成本。 Speed 3D Mold公司是一家泰国铸件和原型 产品开发企业,可以提供高质量替换零部件的解决方 案,并能快速周转。Speed 3D Mold公司的工程 部主管Nattinee Valunaraya表示:“对于我们 的海运行业客户来说,需要更换很多旧零件,因此更
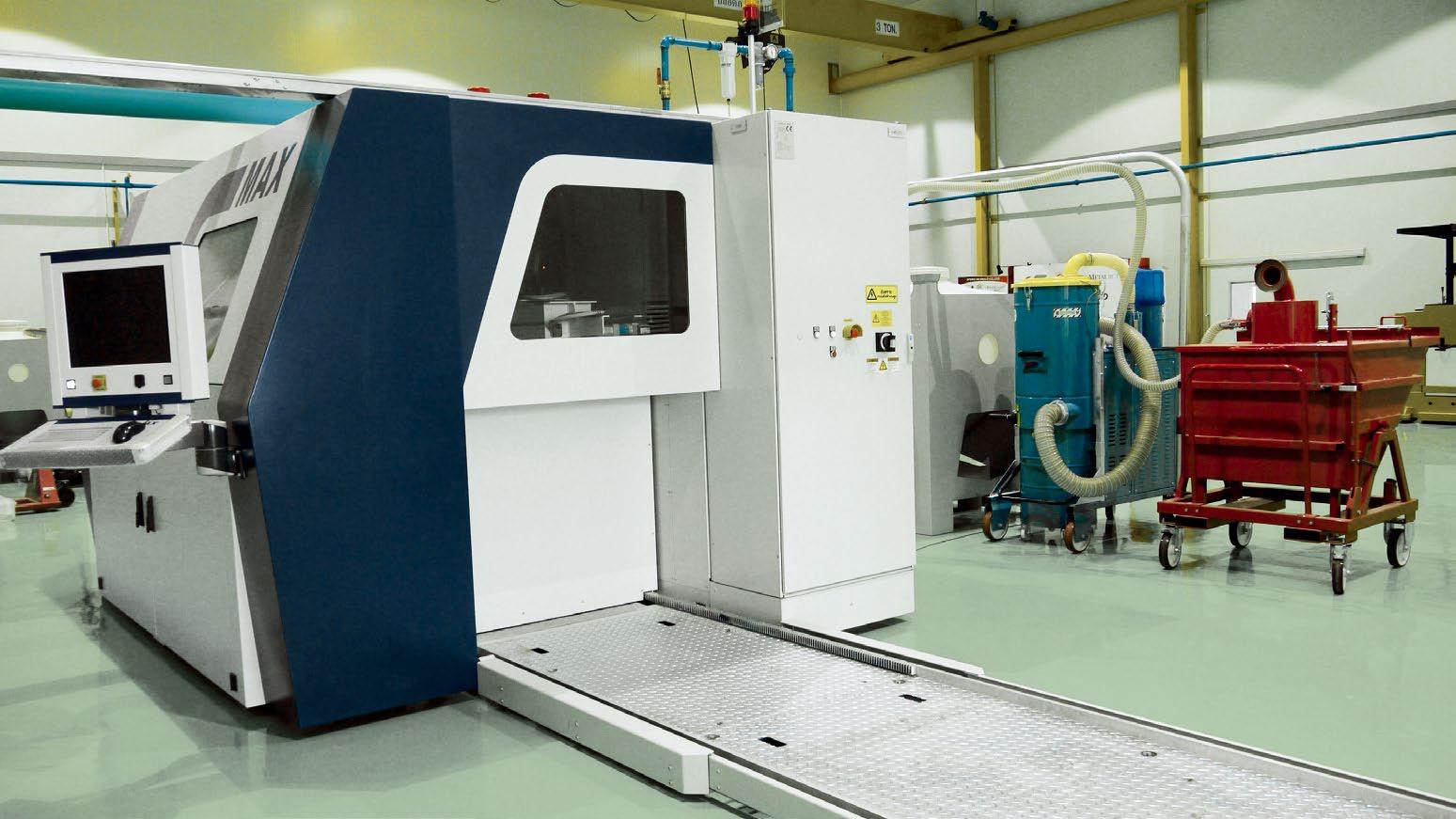

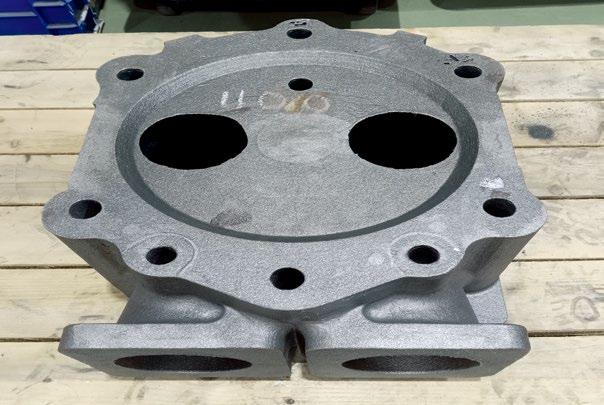
the most important factor for timely maintenance to keep systems in service,” said Nattinee Valun-araya, Head of Engineering at Speed 3D Mold.
With over a decade of experience providing casting simulation support, sand 3D printing, and prototype and replacement casting, Speed 3D Mold’s engineering department supported Hi-Tech Marine with reverse engineering services. The team 3D scanned the original part to create a digital CAD file that could be used to develop a 3D printed mold and core package for casting a new component. With binder jet 3D printing no hard tooling is needed to create the replacement casting, rather the mold and cores are built layer by layer in sand directly from the CAD file.
With digital casting, Speed 3D Mold was also able to make fast iterations to the part to ensure the optimal quality for Hi-Tech Marine’s replacement cylinder head. The part contained many complex features, including large thickness differences and small cooling channels, yet could be easily modified with the digital casting process. The design freedom of additive manufacturing also allowed Speed 3D Mold to update the design of the cooling channel as well as freely place the rigging system within the mold without the traditional limitations to casting design.
The complex 725 x 630 x 572mm mold package contained 19 pieces 3D printed on the S-Max binder jetting system in just 10 hours with no unexpected errors in dimension or shape.
The nearly 100kg replacement cylinder head was cast in gray iron and the final component was delivered to Hi-Tech Marine in just two weeks. The large capital investment to make tooling for just one replacement part would not have been economical, but Speed 3D Mold’s solution to directly print the mold package with ExOne sand binder jetting can save 40% compared to conventional production.■
换速度是及时维护船只以保持系统正常运行的最重要 因素。” Speed 3D Mold公司的工程部门在提供铸造过 程模拟分析、砂型3D打印以及原型和替换零部件生 产方面有十多年的经验,为Hi-Tech Marine公司 提供逆向工程服务。3D打印团队通过扫描原始零件 创建数字CAD文件,用于开发出3D打印的砂型和 砂芯组合,铸造新的零部件。粘结剂喷射3D打印技 术直接通过CAD文件,在砂子中逐层构建砂型和型 芯,不需要复杂的模具就能生产出新的铸件。 采用数字化铸造工艺,Speed 3D Mold公 司还可以对零件进行快速迭代,以确保Hi-Tech Marine公司的新气缸盖达到最佳质量。零件包含很 多复杂的特征,包括较大的厚度差和较小的冷却通道, 但数字化铸造工艺可以轻松修改。增材制造的设计自 由度还允许Speed 3D Mold公司更新冷却通道的 设计,并在模具内自由放置浇冒口系统,而不受传统 铸件设计的限制。 复杂的725x630x572mm砂型包包含19件由 S-Max粘合剂3D打印设备在短短10小时内生产出 来的零部件,其尺寸或形状不会出现无法预料的错误。 新的气缸盖采用灰铁铸造,重达近100Kg,最 终部件在短短两周内即交付给Hi-Tech Marine公 司。仅为更新一个零部件而生产模具并不经济,与传 统生产方式相比,Speed 3D Mold使用ExOne公 司的砂型3D打印设备直接打印砂型和芯子组合的解 决方案可节省40%的成本。 ■
PRODUCT NEWS / 产品新闻 Product News Table of Contents 产品新闻目录
MOLD, CORE & SAND PREPARATION MELTING, POURING & HEAT TREATMENT
Refining the Process: Mat Dalian Creates Superb Automotive Castings with DISA and Wheelabrator 42 卓越工艺:大连迈艾特选择迪砂和维尔贝莱特设备生产卓 越汽车铸件 Handtmann Orders Fourth Westomat Duo Dosing Furnace from Strikowestofe 45
汉特曼从史杰克西订购第四台Westomat Duo定量炉
PRODUCT NEWS / 产品新闻 Refining the Process: Mat Dalian Creates Superb Automotive Castings with DISA and Wheelabrator 卓越工艺:大连迈艾特选择迪砂和维尔贝莱特设 备生产卓越汽车铸件
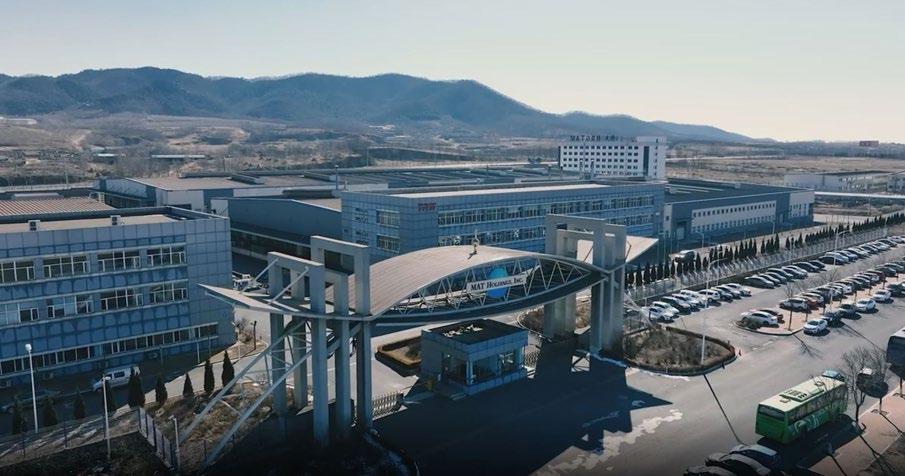
MAT Dalian Auto Parts Co., Ltd. is a state-of-theart foundry and machine shop run by MAT Foundry Group. It was purpose-built in 2012 on a 37,000 square metre site in the city of Dalian, in Liaoning Province, China. For more than 10 years, a two-line Complete Foundry solution from DISA and Wheelabrator’s CT3 shot blasting equipment has helped MAT Dalian deliver consistently excellent castings.
MAT Foundry Group Ltd is one of the largest auto part manufacturers in the world. It operates seven state-of-theart foundries and 11 machining and assembly facilities on 3 continents.
MAT Dalian produces automotive parts like brake discs, calipers, and brackets, and hydraulic valves and pumps, with casting weights ranging from 0.5kg to 25kg. As well as its two moulding lines, it can machine up to 5 million brake discs annually using state-of-the-art CNC equipment and offers in-line coating and packing developed specifically for brake discs. "In the Chinese automotive industry, around 30% of the
迈艾特(大连)汽车零部件有限公司(以下简称大连 迈艾特)是MAT铸造集团旗下最先进的铸造和加工厂。 2012年建于中国辽宁省大连市,占地面积37,000平方米。 10多年来,两条包含迪砂造型线和维尔贝莱特CT-3连 续通过式抛丸设备的整体铸造解决方案协助大连迈艾特始 终如一地提供出色的铸件。 MAT铸造集团是世界上最大的汽车零部件制造商之 一。它在三大洲运营着7家最先进的铸造厂和11家加工 装配厂。大连迈艾特主要生产刹车零部件,卡钳、支架、 刹车盘等,铸件重量从0.5kg到25kg不等。除了两条 全自动造型线外,还有最先进的CNC设备每年加工多达 500万个刹车盘,并提供专门为刹车盘开发的在线喷涂和 包装工序。 “在中国汽车工业中,约有30%的零部件是铸件, 全国每年的需求量约为1000万吨,”大连迈艾特总经理
total parts are castings and the annual demand is about 10 million tons nationwide,” says Mr Liu Kai, General Manager of MAT Dalian. “It’s a very promising industry with huge potential.” High speed production with scrap below 1%
In 2011, MAT Dalian purchased and installed a two-line DISA Complete Foundry solution, comprising DISAMATIC 230-X vertical moulding lines, DISACOOL cooling drums and Wheelabrator CT3 shot blast machines. One line is used to produce grey iron brake discs and the other is for ductile iron components, with a combined annual production capacity of about 60,000 tons. "These lines have been running well for more than a decade,” says Mr Liu. “They are very well suited to producing auto parts and we are very satisfied with their performance and high uptime. The average scrap rate of our brake discs is below 1%.”
All castings pass through Wheelabrator Continuous Through-Feed Tumblast (CT) machines for desanding and cleaning. The CT’s design ensures all parts of a casting are evenly blasted while cooling both castings and sand.
Offering high capacity and throughput speeds, its barrel rotation speed and abrasive throughput are electronically controlled so it can adapt automatically to any fluctuation in line speeds to maintain a continuous production flow. MAT Dalian produces many different types of brake discs, both solid and ventilated. These must be processed separately and the CT copes easily with the demands of these shorter runs. "The CT is exactly the right machine for cleaning brake discs,” says Mr Liu. “Brake discs are relatively flat structures and the CT ensures the inner surface is completely clean. Its reliable and predictable high quality is vital as we supply many top automotive plants. The CT process is also very stable, fast and efficient and it can easily keep up with the high volume production of our DISAMATIC moulding lines.” A consistently superb surface finish
"The surface finish of our castings is very smooth with almost no bumps,” explains Mr Liu. “That reliable high quality is one of the big advantages of the CT, and it’s the main reason we chose it. Bumps are very, very few, almost zero, and this cuts our costs significantly.”
There are other benefits from this fast, economical surface finishing method. Shot blasting with the CT machines ensures that all MAT Dalian’s foundry returns are very clean and can be re-melted as scrap without any issues. "Some argue that you shouldn’t blast scrap like the gating system that will just be remelted, but that is a false economy,” says Mr Liu. “Remelting a clean gating system means the electric furnace will consume less energy and only produce a small amount of slag. The operators will use less slag remover and need less force to remove slag. On the other hand, if you produce a lot of slag then more will remain
刘凯先生说。“这是一个非常有希望、具有巨大潜力的市 场。”
高速生产,废品率低于1%
2011年,大连迈艾特安装了两套迪砂整体铸造解 决方案,其中包括DISAMATIC 230-X垂直造型线、 DISACOOL冷却滚筒和维尔贝莱特CT-3抛丸机。一条 生产线用于生产灰铁刹车盘, 另一条生产线用于球墨铸铁 部件,总年产能约为6万吨。 “十多年来,这些生产线一直运行良好,”刘先生说。 “它们非常适用于汽车零部件的生产,我们对设备的性能 和高正常运行时间非常满意。我们刹车盘的基本废品率在 1%以下。 所有的铸件和浇冒系统都会通过维尔贝莱特的CT-3 连续通过式抛丸机进行清理。CT的设计可确保铸件的每 个面都得到均匀的抛丸清理,铸件光洁,同时确保所有回 炉料干净,以利于后续重新回用熔炼。 CT抛丸设备可配合高产能和吞吐速度,工件停留时 间和丸料抛射量根据工件量控制。这提供了最佳的清理效 果并使设备部件和丸料磨损降到最低。自动适应生产率是 一个标准功能。履带转速和丸料抛射根据预先设定参数电 子控制。大连迈艾特生产许多不同类型的刹车盘,包括实 心和通风刹车盘。这些都必须单独处理,CT设备可以轻 松应对这些较短周期运行的需求。 “CT是清理刹车盘最理想的选择,”刘先生说。“刹 车盘是相对扁平的结构,CT可确保内外表面完全清理干 净。其可靠和可预测的高质量至关重要,因为我们为许多 顶级汽车工厂供货。CT工艺也非常稳定、快速且高效, 可以轻松跟上DISAMATIC垂直造型线的大批量生产。”
始终如一的表面光洁度
“我们铸件的表面非常光洁,几乎没有磕碰,”刘先 生解释道。“可靠的高质量是CT的一大优势,也是我们 选择它的主要原因。磕碰非常非常少,几乎为零,大大降 低了我们的成本。 这种快速、经济的表面处理方式还有其他好处。使用 CT抛丸机进行抛丸处理可确保大连迈艾特铸造厂的所有 回料都非常干净,可以直接作为废料重新熔化,而不会产 生任何损失。” “有些人认为铸件肯定是需要抛丸的,但浇注系统浇 冒口这些如果不抛丸,会节省很多成本。”刘先生说。“其 实不然。因为把浇冒系统抛的非常干净之后,回到电炉里 重新使用,电炉需要消耗的能量就少,产生的炉渣也非常 少,工人就会用更少的除渣剂,用更少的力气除渣。如果
in the liquid iron and end up in the castings, which will increase your scrap rate.”
Reliability is also excellent: the overall uptime rate of the machines is around 99%, aided by MAT Dalian using only original spare parts for servicing. The support from DISA and Wheelabrator’s global service network is equally dependable. As well as a 24/7 DISA hotline, there’s also an annual service agreement with DISA that guarantees a response within 24 hours. Both DISA and Wheelabrator’s engineers will arrive rapidly on site if necessary. "We have our own professional maintenance team with experienced electrical, mechanical and hydraulic engineers and technicians,” says Mr Liu. “We have built up our own experience, with DISA´s and Wheelabrator's aftermarket teams giving us a lot of guidance and technical instruction. That’s helped us to fully understand the operating principles and internal structure of this equipment, which has helped us optimise our daily basic maintenance routines too.”
渣子除不尽会 怎么办?它会 跟着液态铁水 带到你的铸件 里面,会使你 铸件的废品率 升高。” CT的 设 备可靠性也非 常出色:设备 的整体正常运 行时间可达到 99%,大连迈艾特一直坚持使用原厂备件进行维护。诺瑞 肯全球网络的支持同样可靠。除了24/7迪砂热线外,我们 还与迪砂签订了年度服务协议,保证在24小时内回复。如 有必要,迪砂和维尔贝莱特的工程师也会迅速到达现场。” “我们拥有自己的专业维护团队,拥有经验丰富的电 气、机械和液压工程师和技术人员,”刘先生说。“迪砂 和维尔贝莱特的售后团队为我们提供了大量的指导和技术 支持。这有助于我们充分了解该设备的工作原理和内部结 构,也帮助我们优化了日常基本维护方案。
快速、高效、清洁,运行成本最低
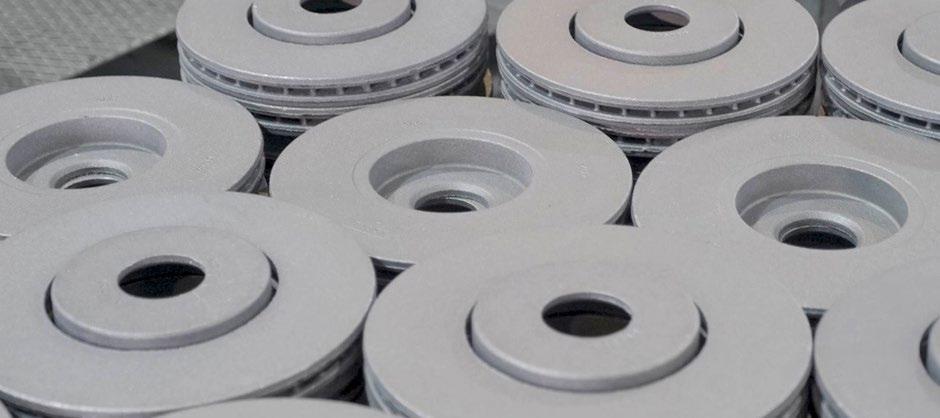
Fast, efficient and clean, with the lowest operating costs
An entire line can be run by two or three operators, far fewer than lines from other suppliers in China that can require 10 or more personnel. With high availability and minimal labour costs, overall operating costs have been consistently low. "Of course, we do add extra steel shot and replace wear parts on the CT,” continues Mr Liu, “but, rather than the cost of the parts or consumables, you need to look at the overall operating cost per ton of processed castings – and that is actually extremely low. Our experience in operating the CT has really helped too, for example, we have cut shot consumption by 80% over the last decade.”
MAT Dalian’s factory was expertly planned from the start to offer a clean, safe and pleasant working environment. The entire production line is equipped with dust extractors that feed 11 large outdoor dust collectors. These capture any dust produced, from sand mixing to quality control. Dust cloth bags are changed annually to ensure maximum suction. "The Wheelabrator CT3 gives you a very efficient and economic shot blasting method to produce car calipers, brackets, and brake discs,” says Mr Liu. “We will stick with this CT blast machine and, if a new factory is built in the future, I will support using DISA and CT machines there too.”■
一条生产线可以由两到三名操作员运营,远远少于中 国其他供应商需要10名或更多人员的生产线。由于设备 可靠性高,人工成本低,整体运营成本一直很低。 “当然,24小时运转的CT设备会有很多丸料消耗, 设备本身的易损件也需要定时更换,”刘先生继续说道,“但 是,您需要考虑的是每吨铸件的总运营成本,而不是单一 零件或易损件的成本 - 这实际上非常低。我们在操作CT 方面的经验也确实有所帮助,例如,在过去十年中,仅丸 料的消耗量就减少了80%。这就是一个不断摸索的过程。” 大连迈艾特从一开始就经过精心规划,以确保清洁和 安全的工作环境。整条生产线遍布集尘管道,链接室外11 个大型除尘器。它们可以捕获产生的任何粉尘,从混砂开 始到最后质量检验。除尘布袋每年更换一次,以确保最大 的除尘能力。 “维尔贝莱特CT-3为我们提供了一种非常高效、经 济的抛丸方法,用于生产汽车卡钳、支架和刹车盘,”刘 先生说。“我们会坚持使用CT抛丸机,如果将来建造新 工厂,我也同样选择使用迪砂的造型线和维尔贝莱特的这 款CT抛丸机。”■
PRODUCT NEWS / 产品新闻 Handtmann Orders Fourth Westomat Duo Dosing Furnace from Strikowestofen 汉特曼从史杰克西订购第四台 Westomat Duo定量炉
Compact and energy-efficient with maximum uptime
Handtmann Group’s light metal casting division has ordered its fourth Westomat Duo dosing furnace for its Annaberg site in Germany. With five StrikoMelter melting furnaces, fifteen Westomat Classic and three Westomat Duo dosing furnaces already in operation at the facility and another one to be installed, Annaberg’s new line – its 22nd – will produce battery compartment parts for electric vehicles.
A compact version of the Westomat Classic dosing furnace, which is highly focused on footprint savings in relation with the HPDC cell layout. The Westomat Duo is a perfectly suited addition to the Annaberg site. With a 14% smaller footprint than the Classic, the Duo will allow the company to run 8 die casting cells using floor space that would previously have accommodated only 7, fully optimizing the foundry space available. 紧凑、节能并最大限度延长正常运行时间
汉特曼(Handtmann)集团的轻金属铸造部门已经 为其在德国安娜贝格的工厂订购了第四台Westomat Duo 定量炉。安娜贝格工厂现有5台StrikoMelter熔炼炉、 15台Westomat Classic定量炉和3台Westomat Duo 定量炉投入使用,另有一台即将安装,该工厂的新生产线(第 22条生产线)将生产电动汽车的蓄电池舱零件。 Westomat Classic定量炉的紧凑型版本高度重视与 HPDC单元布局有关的占地面积节省。Westomat Duo 是对安娜贝格工厂的完美补充。Duo型定量炉的占地面积 比Classic型小14%,这样该公司就能够在以前只能容 纳7个压铸单元的建筑面积里运行8个压铸单元,充分优 化了可用的铸造空间。
Space-saving productivity boost for light metal casting 节省空间,提升轻金属铸造生产效率
A leading automotive supplier for drivetrain castings as well as body and chassis parts, Handtmann currently operates aluminium casting lines at its Annaberg site that employ a mix of die and gravity casting processes. It produces a total of 12,500 tons of castings in 2020 and, in 2021, up to 1600 tons per month.
The Westomat Duo’s compact size and reliable performance really appealed to Handtmann. The extra casting cell they are able to run as a result of space saved will certainly help boost productivity.
With two alternative positions for the riser tube, the Westomat Duo can be positioned in parallel with the die casting machine (DCM), saving space while making pouring, cleaning and maintenance access easier too. By using the
汉特曼(Handtmann)公司是一家行业领先的汽车 供应商,主要生产动力传动系统 铸件以及车身和底盘零件。目前 该公司在其安娜贝格工厂拥有多 条铝铸造生产线,同时采用高压 压铸和重力铸造工艺。该工厂在 2020年共生产12500吨铸件, 2021年的最高月产量达1600吨。 Westomat Duo尺寸紧凑, 性能可靠,对汉特曼极具吸引力。 这种定量炉节省了空间,能够运 行额外的铸造单元,因而有助于 提高生产效率。 由于升液管有两个可选位置, Westomat Duo可以与压铸机 (DCM)平行放置,在节省空间 的同时,也方便了浇注、清理和
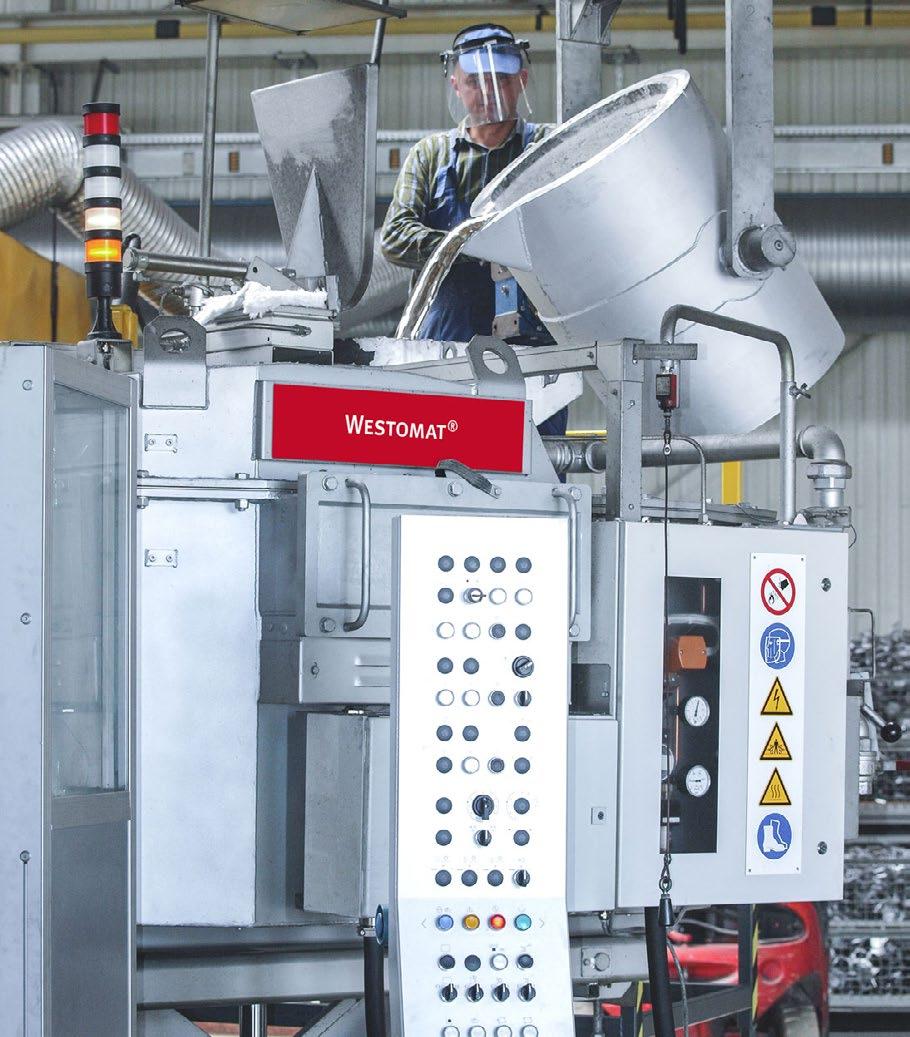
second riser tube opening for sampling, Handtmann is also taking advantage of the fact that sampling can be carried out as far away from the refilling position as possible, giving the most accurate possible results as well as simplifying the sample-taking process. Reliable performance that puts safety first
This latest investment demonstrates how satisfied the company is with the performance of its existing StrikoWestofen equipment – and especially the Westomat Duo.
To lower the metal density index after filling, Handtmann’s existing Duos employ degassing lances for purging instead of porous plugs, and the new Duo will use this option again. The Westomat Duo’s new modular pneumatic unit also makes it much easier to upgrade with digital sensors and other components. "We are a forward-thinking business always looking to leverage new technology. With our new Westomat Duo, we know we have guaranteed performance now and have an easy way to enhance our lines in the future”, Heiko Blei, Foundry Manager at Handtmann Annaberg.by ■
维护。通过使用第二个升液管开口取样,可在离加料位置 尽可能远的地方取样,从而得到最准确的结果,并简化了
取样过程,汉特曼也利用了这一点。
性能可靠,安全第一
这项最新的投资表明,该公司对其现有的史杰克西设 备的性能,特别是Westomat Duo定量炉的性能非常满意。 为了降低加料后的金属密度指数,汉特曼现有的Duo 采用除气喷枪代替除气砖进行除气,并且这台新的Duo也 将再次采用这一方案。Westomat Duo采用了新的模块 化气动装置,因此可以非常方便地用数字传感器和其他部 件进行升级。 汉特曼安娜贝格铸造厂经理Heiko Blei说:“我们 是一家有远见的企业,不断寻求利用新技术。有了新的 Westomat Duo,我们就知道公司的业绩有了保证,并且 我们将能够轻松地增强我们未来的生产线。”■
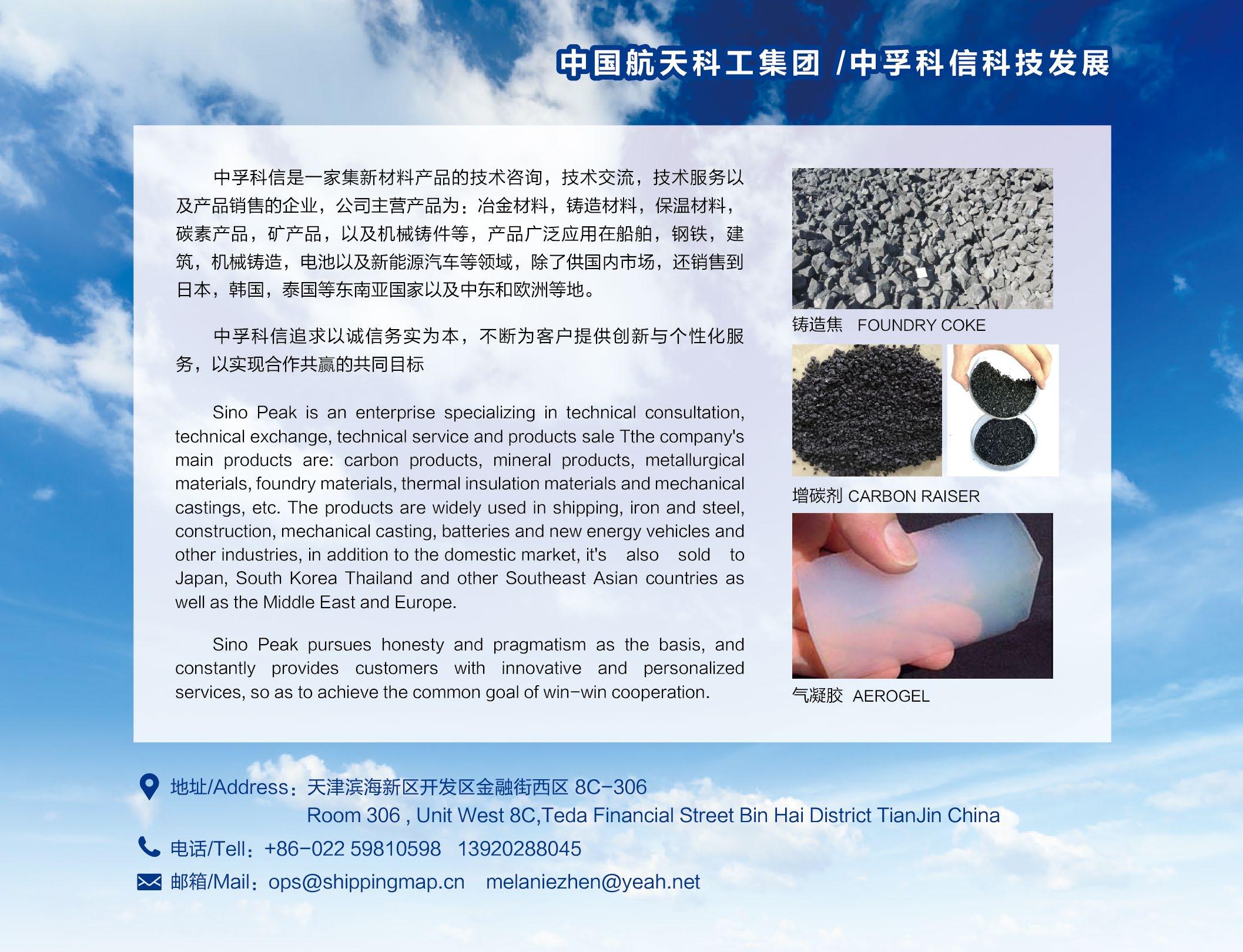
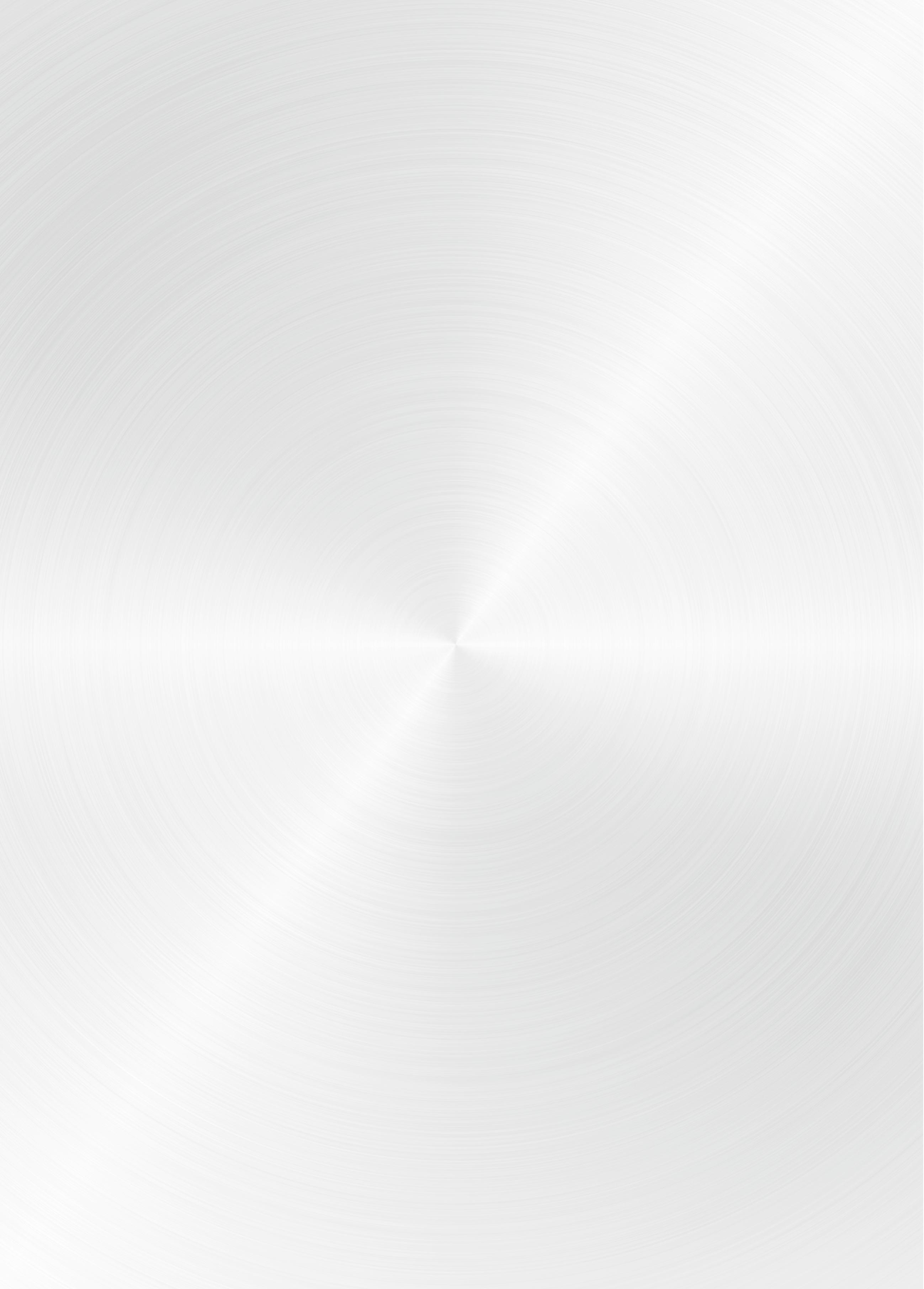
INTERVIEW / 采访 Abrasive Trend to Move From Surface Cleaning Towards Surface Preparation
Thomas Fritsch, CEO of Foundry-planet 磨料行业发展趋势:从表面清理到表面处理
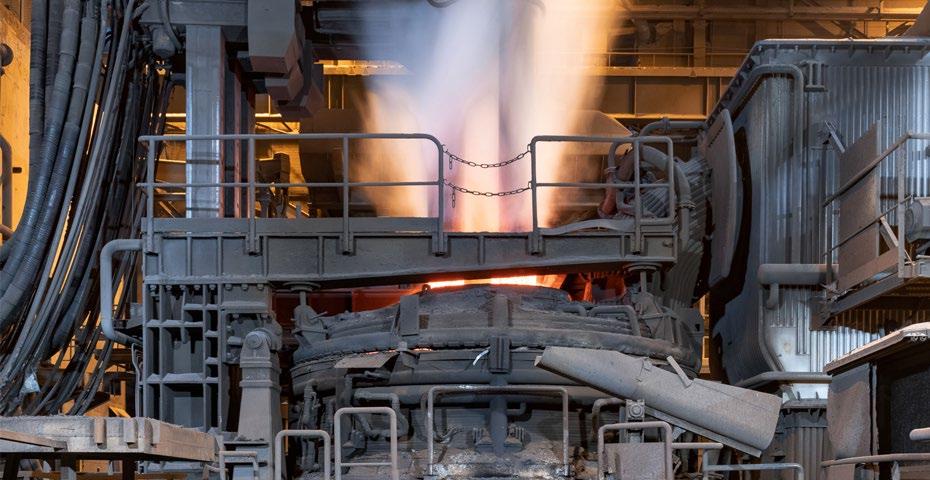
Wheelabrator has launched a new digital tool that tracks and dispA visit to the biggest steel abrasive plant in the worldInterview with Christophe Bertoncelli, France General Manager/Group C.O.O. Winoa S.A.
These days, the leading supplier of blasting abrasives celebrated its 60th anniversary in the French Alps together with employees, customers and representatives from all over the world.
During this on-site visit, Foundry-Planet was able to see how complex the production of high-quality abrasives is and how the challenges of the future are being addressed here. Read here our interview with Winoa’s COO, Christophe Bertoncelli:
1) Winoa just recently celebrated its 60th Anniversary, that means a lot of experience, an international presence and a large portfolio. How do you tackle the great challenges of the time?
Christophe Bertoncelli: The experience accumulated throughout those years and Winoa unique worldwide presence are key assets to leverage our knowledge of this industry to the highest standard. Practice sharing, should they be in product development or production technologies to take two examples, are standard
参观世界上最大的钢铁磨料企业——采访Winoa集团法 国公司总经理/集团首席运营官 Christophe Bertoncelli。
最近,行业领先的金属磨料生产企业与来自世界 各地的员工及客户相聚法国阿尔卑斯山,庆祝公司成 立60周年。 通过参加这次活动,Foundry-Planet的工作人 员了解了高质量磨料复杂的生产过程,以及公司是如 何应对未来的挑战。
以下是我们对Winoa首席运营官Christophe Bertoncelli的采访:
1)Winoa公司刚举办了60周年庆祝活动,60年 的历史意味着公司拥有丰富的经验、强大的国际影响 力和庞大的产品组合。公司是如何应对巨大挑战的? Christophe Bertoncelli:Winoa公司多年来 积累的经验和在全球的影响力,是公司成为行业标杆
processes for us. It allows the whole organization to benefit from good ideas wherever they were initiated. Let's take as an example the recent development of our Hybrid shot, a steel abrasive specifically designed for grit removal in foundries, or the WA Clean, a unique device for reading the cleanliness of surfaces. It is thanks to our vast experience, the work in concert with our technical centers and the long partnership with our customers that have enabled the development and production of these products. This has clearly been a key advantage of Winoa group over the years and will continue to be so for the years to come.
Additionally, to meet our customers' demand, we have continued to invest and grow over the past 12 months: With the recent acquisition of Peerless Abrasives in the USA, the creation of 2 new technical centers (USA and Eastern Europe) and the development of a shot peening service center in India. 2) In your opinion, where are the most important areas of application in the abrasive blasting market and did you noticed any change in market?
Christophe Bertoncelli: The main markets for our products are the automotive market, road and non-road transport. These markets represent more than 35% of our volumes. Mainly used for desanding and descaling of casted iron or forged parts (i.e. driveline, engine, axles.), applications also include surface preparation prior to coating (i.e. frames) or peening (i.e. springs, gears…). Another important sector is the Metallurgy market, where our products can be used anywhere from descaling to surface preparation.
And, generally, the trend is to move from surface cleaning towards surface preparation with an increased level of requirement on both quality and productivity levels: The right selection of steel abrasives is key to optimize these two parameters. Other trends have developed with the evolution of blasted materials. Increased use of stainless steel and aluminum alloys into produced goods (e.g.: automotive & transport industry) will call for more specific media such as stainless and cut wire abrasives, which Winoa has been promoting quite strongly on the market. Finally, the need to preserve natural resources and increase recycling should boost the use of steel abrasives vs. mineral ones too. 3) Are there any current problems from the crisis scenarios with Covid-19 or the Ukraine conflict?
Christophe Bertoncelli: Indeed, the crisis that started with Covid early 2020 and continued early 2022 with Ukraine conflict is posing new great challenges to Winoa and across the industry in general. The two keywords here are anticipation and reactivity. In our way to conduct business, we must anticipate various scenarios and prepare
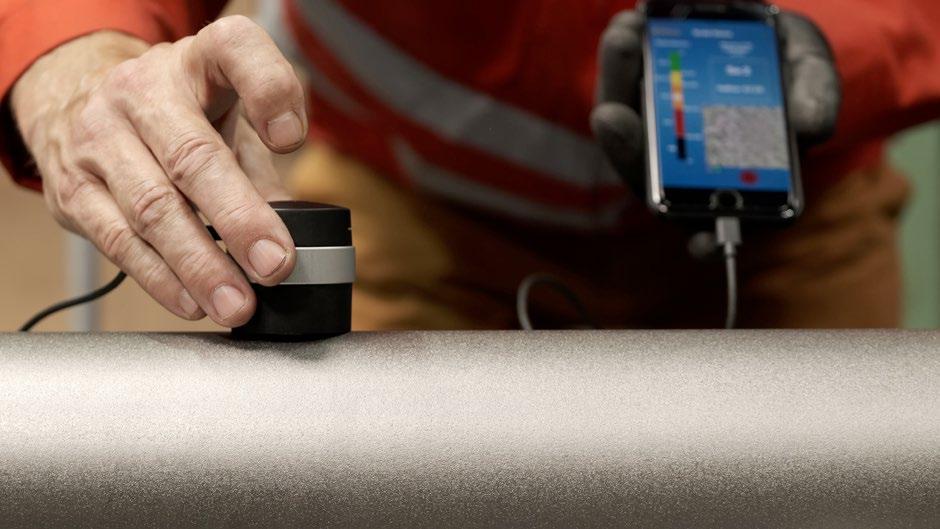
企业的关键。举例来说,无论是在产品开发还是生产 技术中,实践经验分享都无处不在,这对我们来说是 标准流程。它使整个组织都可以从好的想法中受益, 无论这些好想法是在哪里发起的。例如,我们最近开 发的新产品Hybrid shot,这是专为铸件表面清理而 设计的钢制磨料,或WA Clean,一种用于读取表面 清洁度的特殊设备。正是由于公司丰富的生产经验、 与技术中心的合作以及与客户的长期合作伙伴关系, 使这些产品的开发和生产成为可能。多年来,这已然 是Winoa集团的一个关键优势,并将在未来几年保持 这一优势。 此外,为了满足客户需求,我们在过去的12个 月中继续增加投资和研发:最近公司收购了美国的 Peerless Abrasives公司,创建了2个新的技术中 心(美国和东欧),还开设了位于印度的喷丸服务中心。
2)您认为磨料行业最重要的应用领域在哪里?您 是否注意到市场的任何变化? Christophe Bertoncelli:我们产品的主要市场 是汽车行业、公路和非公路运输,占总产量的35%以 上。主要应用于铸铁件或锻造零件(传动系统、发动 机、车轴)的砂和氧化皮的去除,还包括涂层(框架) 或喷丸(弹簧、齿轮等)之前的表面处理。另一个重 要的应用领域是冶金市场,我们的产品可用于从除垢 到表面处理的全过程。 而且,一般来说,磨料产品的发展趋势是从表面 清理转向表面处理,对质量和生产力水平的要求越来 越高:正确选择金属磨料是优化这两个参数的关键。 而且随着磨料材料的发展,产品也将变化。不锈钢和 铝合金在汽车和运输行业中使用的不断增加需要更细 分的材料,例如Winoa集团一直大力推广的不锈钢和 切割线磨料。最后,从保护自然资源和促进循环利用 的角度考虑,与矿物磨料相比,也应促进不锈钢磨料 的使用。 3)Covid-19及乌克兰冲突是否对公司发展产生 影响? Christophe Bertoncelli:确实,危机始于 2020年初的新冠疫情,并已持续到2022年初的乌 克兰冲突,这对Winoa集团和整个行业构成了新的巨 大挑战。我想说的两个关键词是预期和反应。对于我 们开展业务的方式,我们必须预测可能发生的各种情 况并做好相应的准备。如果预期是基础,有一点是肯 定的,事情的发展可能与我们的预期不同!这就需要
ourselves accordingly. If anticipation is the basis, there is one sure thing, events will likely be different than our anticipations! This is where reactivity will come into play to navigate those periods at best, based on adjacent scenarios. Apart from the significant costs increases induced, components availability has been for sure a daily topic for the past 2 years. 4) Keywords such as Industry 4.0, transformation, sustainability and climate neutrality have become basic conditions today. Can customer and competitive advantages be derived from this?
Christophe Bertoncelli: We already observe that some of our customers are becoming much more sensitive to those aspects in their request for quotes. We expect this trend to develop and, as for ISO certification, to become a requirement for any supplier homologation. Beyond this aspect, those development axes push us to relentlessly search for new, more efficient solutions that will ultimately translate into increased competitiveness. As an illustration, ISO 50 001 certification (Energy efficiency management) obtained by our French facility in 2013 has been a driver toward lower energy consumption and therefore positions us well in our journey towards carbon neutrality. 5) We understood you have a Zero Carbon Green Pledge through your Green Agenda 2025, can you tell us more about it? What are the technologies you are investing in to achieve this objective?
Christophe Bertoncelli: With its headquarters in the middle of the beautiful French alps, Winoa has been for a long time very sensitive on minimizing its impact to its environment. The alarming reports from GIEC has pushed us further on a path of carbon neutrality. For years, we have been modernizing our production tools with techniques such as frequency variators, high efficiency burners, heat recovery systems, LED lighting, etc. In our journey towards carbon neutrality, we have already identified and planned some technologies such as electricity self-generation, moving away from natural gas usage…. Regarding the latest steps that will bring us to full neutrality, as some technologies are still in early development stage, we monitor closely R&D developments to be ready for investing as soon as they translate into industrial solutions.■
公司能够根据类似的情况做出反应。在过去的2年, 除了明显的成本增加外,零部件的供应问题肯定是大 家的日常话题。 4)工业4.0、转型发展、可持续性和碳中和等关 键词已成为当今时代的特征。我们是否能够从中获得 客户和竞争方面的优势? Christophe Bertoncelli:我们已经看到一些客 户在他们的询盘中对这些方面变得更加关注。我们预 计这些趋势将会继续发展,而且就ISO认证而言,将 成为任何供应商获得认证的要求。此外,这些方面将 促使我们不懈地寻找新的、更有效的解决方案,从而 最终转化为更高的竞争力。例如,我们的法国工厂于 2013年获得的ISO 50 001认证(能源效率管理) 一直是降低能源消耗的驱动力,因此有助于我们达到 碳中和的目标。 5)据我们了解,公司在2025年绿色议程中做出 了零碳排放的承诺,您能给我们分享更多的信息吗? 为了实现这一目标,您将采取哪些新技术? Christophe Bertoncelli:Winoa集团总部位 于美丽的法国阿尔卑斯山中部,长期以来一直非常注 重环保。GIEC发布的令人警醒的报告将我们进一步 推向走碳中和的道路。多年来,我们一直在使用变频器、 高效燃烧器、热回收系统、LED照明等技术对我们的 生产设备进行现代化改造。在实现碳中和的过程中, 我们已经明确并计划采用一系列新技术,包括自发电、 不使用天然气等……关于为完全实现碳中和而采取的 最新步骤,由于某些技术尚处于早期开发阶段,我们 将密切关注研发进展,以便在它们转化为工业解决方 案后立即进行投资和使用。 ■
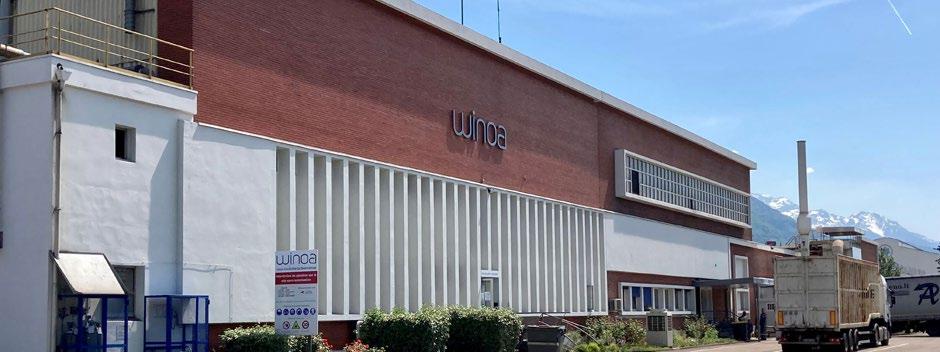
CULTURE / 铸造文化 Bronze Casting for the Beijing Winter Olympics
国礼青铜,致敬冬奥
山西宇达青铜文化艺术股份有限公司 胡春良
As a national cultural industry demonstration base, Shanxi Yuda Bronze Culture and Art Co., Ltd. has been authorized to produce a number of bronze sculptures for the Beijing Winter Olympics, which add luster to the events, and has been widely praised. National Gifts
作为国家文化产业示范基地的山西宇达青铜文化艺术 股份有限公司,被授权承制了包括北京冬奥国礼在内的多 件青铜雕塑艺术品,为北京冬奥会给力添彩,受到广泛的 赞誉和好评。
冬奥国礼
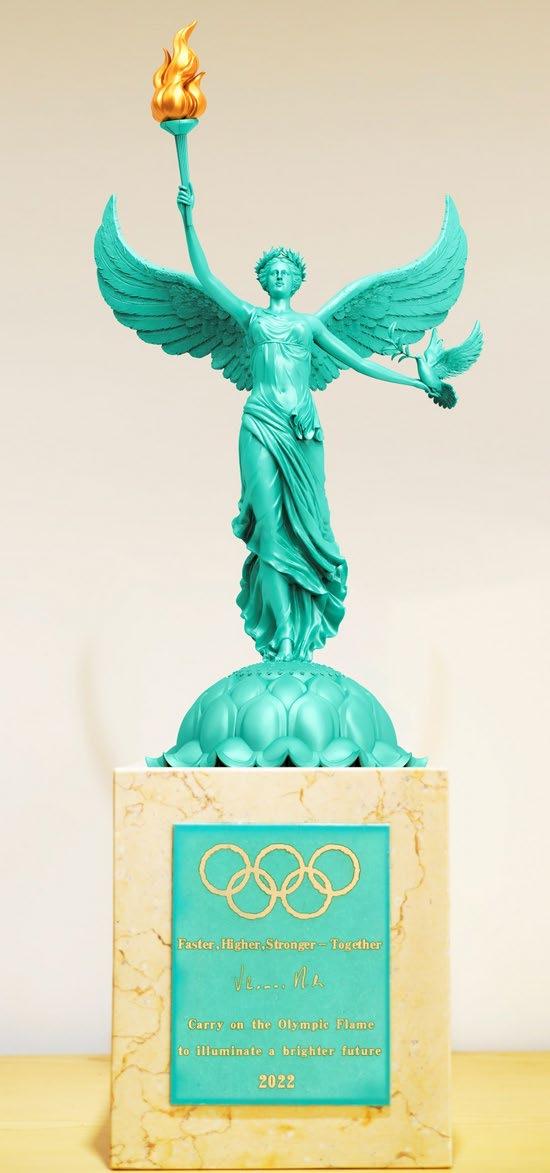
The bronze sculptures for the Winter Olympics national gifts "Winter Olympics Torch" manufactured by Yuda has two shapes: "Winter Olympics Torch" and "Dreams Come True with One Heart". They are designed by Huang Jian, the world's first Chinese artist who has been awarded the "Olympics Art Envoy" by the International Olympics Committee.
The "Winter Olympics Torch" expresses peace and the Olympics spirit. This piece of work integrates the eastern and western elements for peace culture, such as lotus, olive branch, dove, etc., perfectly interpreting the dream of peace, the Olympics and the world. The new Olympics motto "Faster, Higher, Stronger-Together" signed by President Bach is inscribed on the marble base of the sculpture, implying that the Beijing Winter Olympics will become a monument to the Olympics spirit in the new era. "Dreams Come True with One Heart" expresses the friendship between China and Greece, as well as the culture of the Winter Olympics. The "Olympics goddess" holding the torch connects the holy mountain of Olympia and the Badaling Great Wall and the Xiaohaituo Mountain, connects the ancient Greek arena and the Bird's Nest Stadium in Beijing, implying that the Chinese and Greek people will jointly lift the Olympics flame of peace and carry
宇达公司制造的冬奥国礼《冬奥圣火》系列青铜雕塑有 两款造型:《冬奥圣火》和《同心圆梦》。由全球首位被国 际奥委会授予“奥运艺术使者”的中国艺术家黄剑创作设计。 《冬奥圣火》表达了和平和奥运精神。作品集荷花、 橄榄枝、和平鸽等东西方和平文化元素于一体,完美地诠释 着和平梦、奥运梦、世界梦。雕塑大理石基座上铭刻着巴赫


forward the Olympics spirits.
In the center of the back of the sculpture, there is the logo of the Beijing Winter Olympics, surrounded by 24 Winter Olympics sports icons, and the olive branches and the Winter Olympics theme slogan "Together for a shared future" form a beautiful laurel crown, implying that athletes from all over the world gather at the Winter Olympics, try their best and achieve better results . Production
The production of the Winter Olympics sculptures hilights the distinctive features of "intelligent manufacturing". The mold of the work adopts 3D printing photosensitive resin to ensure accuracy; in terms of the shell-making process, in order to ensure excellent molding effect and casting quality, the silica sol shell-making process is adopted. The wax is removed by steam. The casting process is one of the three major casting technology achievements in ancient China, the lost wax method, which is developing into the investment casting technology now.
The surface coloring and decoration of the works adopts the international advanced thermal color technology, as well as local gold paste, polishing and three-dimensional computer engraving, etc., to create a colorful, fashionable and elegant Olympics fine arts.■
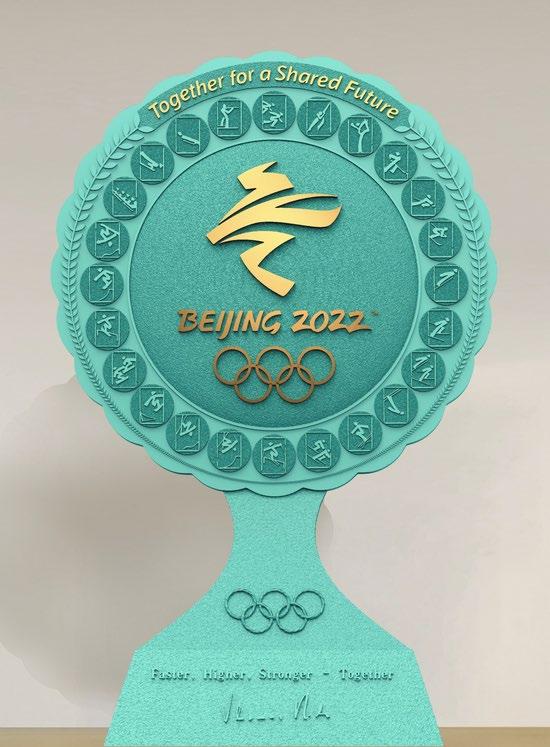
主席签名的奥林匹克新格言“更快、更高、更强——团结”, 寓意北京冬奥会将成为新时期奥运精神的一座丰碑。 《同心圆梦》,表达了中希友谊和冬奥会文化。以浮 雕的表现形式塑造了高举圣火的“奥运女神”分别连接: 奥林匹亚圣山与八达岭长城和小海坨山,古希腊竞技场与 鸟巢体育场,寓意中希两国人民将共举奥运和平圣火,将 奥运精神发扬光大。 雕塑背面中央为北京冬奥会标志,周围环绕24个冬 奥体育图标,外围橄榄枝与冬奥主题口号“一起向未来” 组成美丽的桂冠,寓意五洲健儿欢聚冬奥会,奋力拼搏, 更创佳绩。
冬奥雕塑的制作
冬奥系列雕塑的制作工艺,体现了当代“智能制造” 的鲜明特点。作品的模型采用了3D打印光敏树脂模型, 确保了模型的精度;在制壳工艺方面,为了保证优良的成 型效果和铸造质量,采用了硅溶胶制壳工艺。型壳脱蜡采 用了蒸汽脱蜡。铸造工艺为中国古代三大铸造技术成就之 一的失蜡法、在当代发展的熔模精铸技术。 作品表面着色装饰采用了国际先进的热采色技术,以 及局部贴金、抛光和三维立体电脑雕刻等工艺,打造了色 彩丰富,时尚高雅的奥运精品艺术品。■
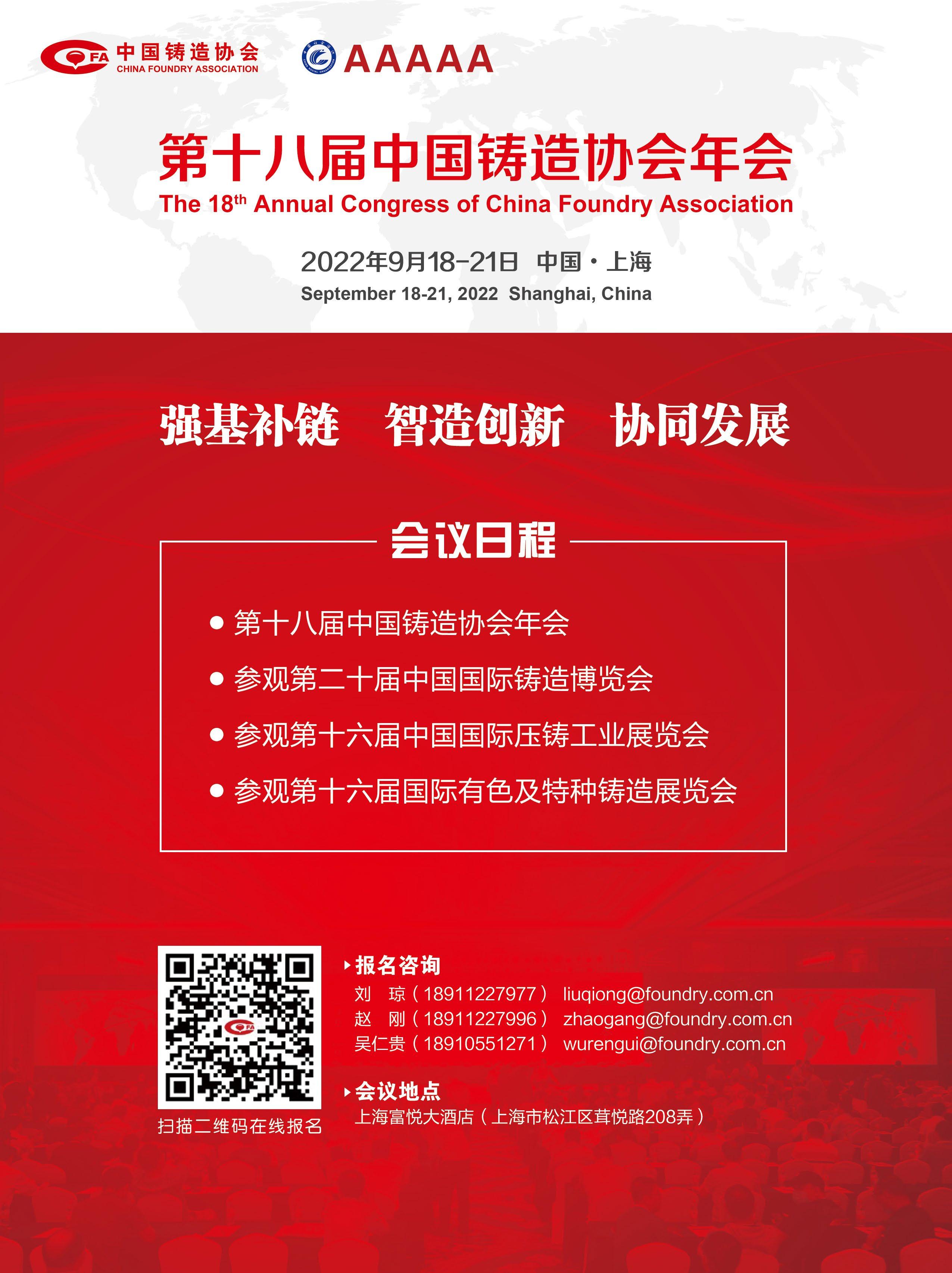
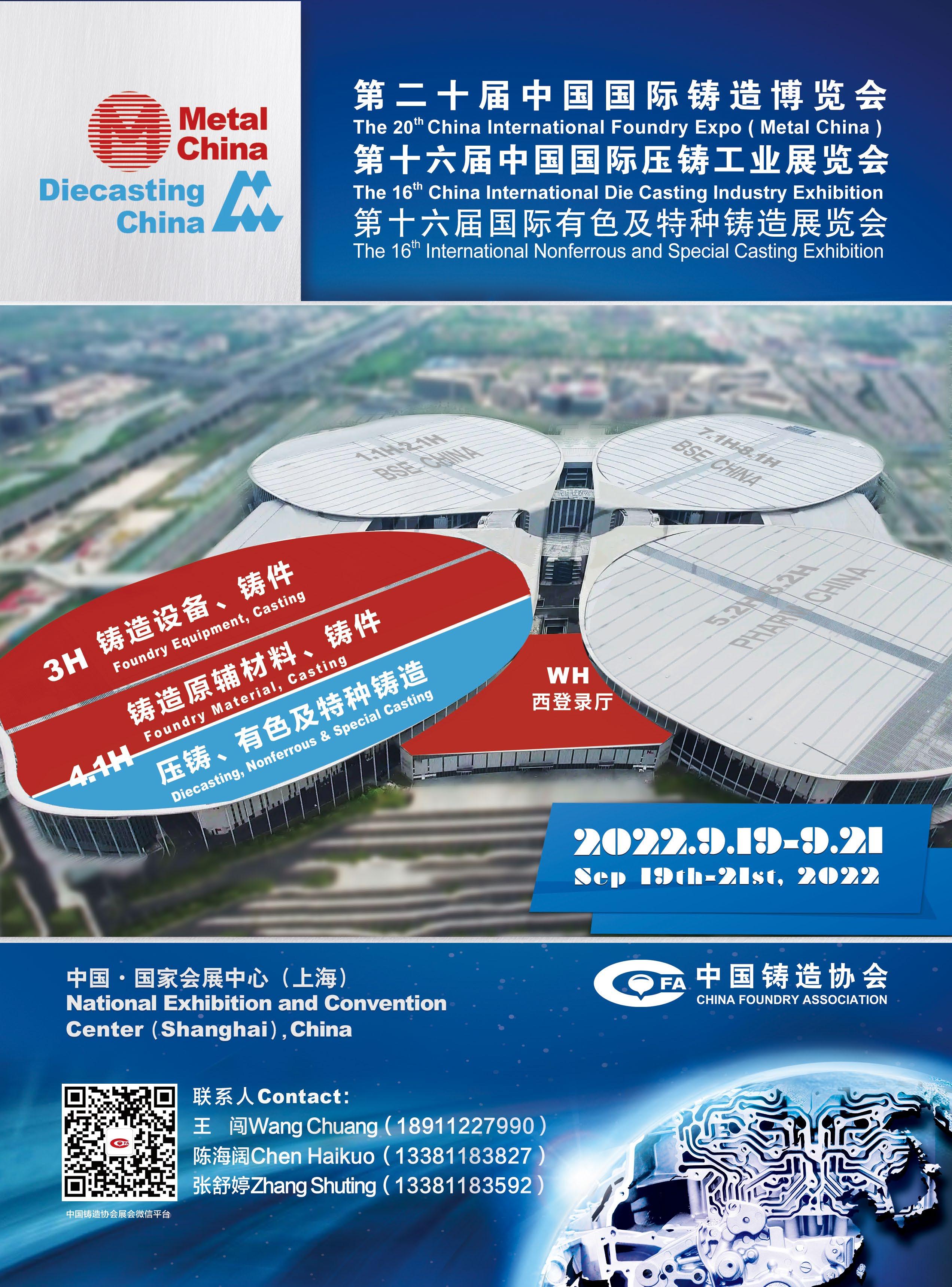