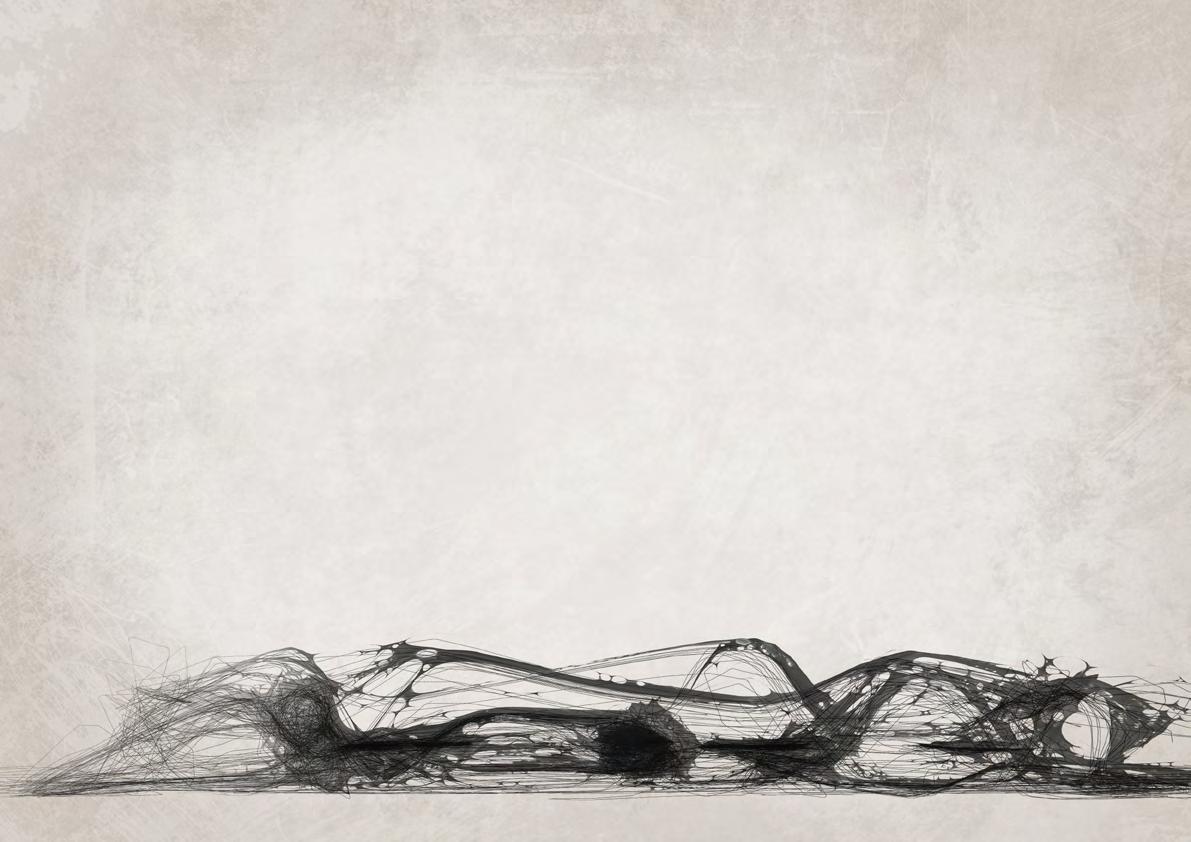
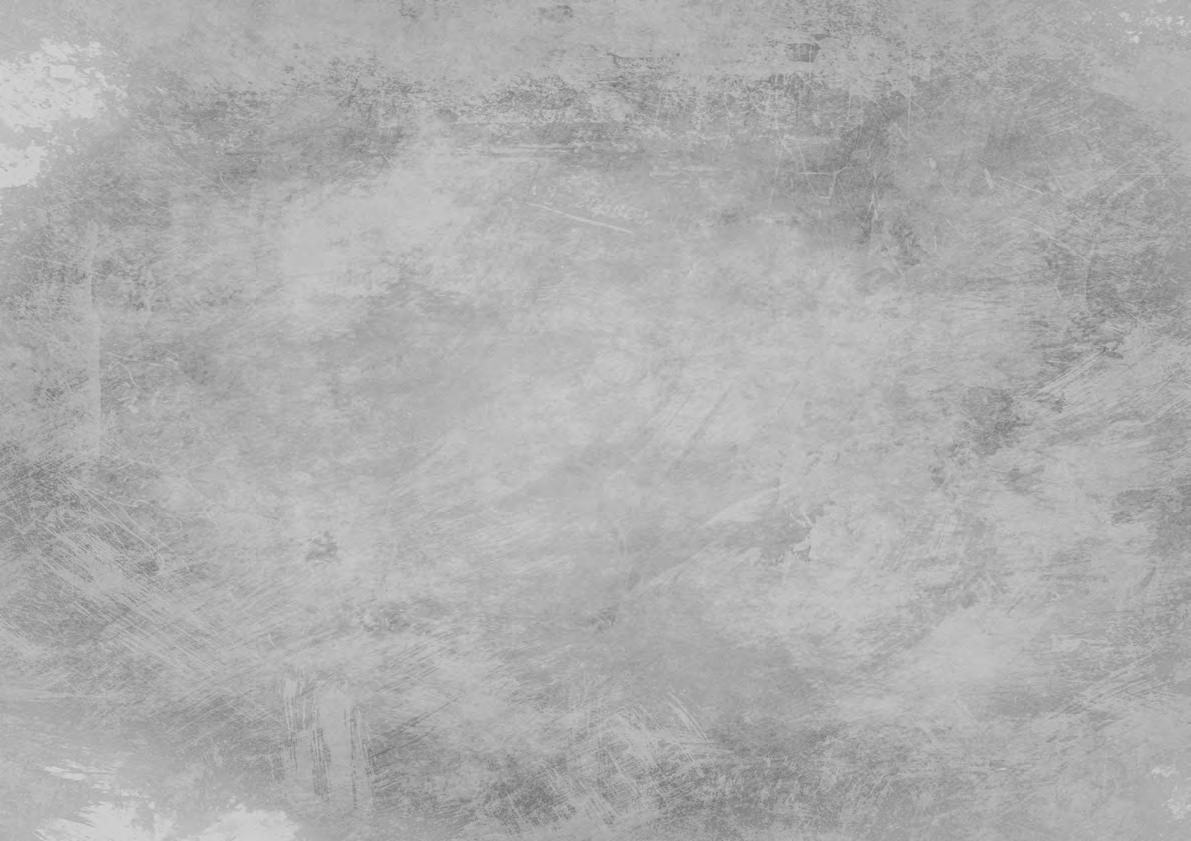







Location:
Year:
Instructor:
Description:
Location:
Year:
Instructor:
Description:
Suzhou, China
2021
Shuo Feng, Guosheng ChenIndividual Work
The design proposal centers around the construction of a community center, aimed at providing a secure and engaging environment for individuals, with a specific focus on children. In this unique setting, children aren't merely observers but active participants, present everywhere, interacting, and learning within their environment.
A multi-agent system is leveraged to simulate their movement patterns, thereby shaping the design volumes according to the trails within the existing buildings. Within these structures, children have the freedom to walk, run, slide, climb, and even construct their own secret base. The essence of this design is to foster active engagement and interaction in a safe, supportive space.
In this child-centered community center, children are observers and participants. They should be present everywhere, which allows them to interact with different environments.
Using the multi-agent system aims to simulate their trails and figure out an organic way to interact with the built environment.
Attraction
Agents will be attracted to the targets scattered in the buildings.
Velocity Matching
Agents attempt to match velocity with nearby flockmates
Attraction Strength
Wandering Wandering is a type of random steering which has some long term order.
Trail Searching Radius
Repulsion Radius
Searching Angle
Attracting Radius
Flock centering
Each agent attempts to stay close to nearby flockmates;
Collision Avoidance
Each agent avoids collisions with nearby flockmates
Direction
Stigmergy Agents will chase other agents' trails.
Slide "Forest"Based on the multi-agent system's simulation, volumes are generated according to the trails. These volumes provide children with a place to hold various activities and allow them to interact closely with the real world while still under proper protection.
Location:
Year:
Instructor:
Description:
An Efficient Robotic Approach to Geometrically Variable Ceramic Part Production
Philadelphia, Pennsylvania, United States 2023
Clay slip’s unique phase-changing properties make it an ideal material for crafting intricate, precisely-shaped components needed in industries such as fine porcelain and sanitary ware. However, its limitations in producing variable components without new molds present challenges for integration into architectural practices.
This research introduces an innovative slip casting approach that allows for the production of diverse clay forms using a single mold by employing a 6-axis robot that simultaneously rotates the mold during the solidification process. A key innovation in our research is the development of a simulation program specifically designed for the dynamic slip casting process. This breaks away from the traditional notion of slip casting as a “black box” process, where what happens inside the mold remains hidden. By providing insights into the mold’s interior, our simulation program adds significant value to the field and enhances our understanding of the process.
The simulation program predicts the solidified slip’s shape in real-time, and a customized end effector attaches the mold to a robotic arm and injects additional slip for precise edge control. The proposed method combines traditional slip casting with industrial robotics, offering greater control over geometric qualities without increasing mold demands. By overcoming conventional limitations, we hope that this unique ceramic workflow can be used in architecture and art, and inspire other fields of study.
Robert Stuart-Smith, Jeffery Anderson, Nathan King, Billie Faircloth Partner: Renhu (Franklin) Wu, Shunta Moriuchi, Yinglei (Amber) Chen, Sihan LiOur research revolved around process of Slip Casting. Slip casting, or slipcasting, is a ceramic forming technique, and is widely used for shapes that can not easily be formed by other techniques. The technique involves a clay body slip (which is the liquid clay), usually prepared in a blunger, being poured into plaster molds and allowed to form a layer, the cast, on the internal walls of the mold.
It is suited for the consistent and precise shaping of complex shapes. It is the standard shaping technique for sanitary ware, such as toilets and basins, and is commonly used for smaller pieces like figurines and teapots.
Our research aims to create diverse cast shapes to produce geometric variations by integrating robotic motion and simulation into the slip casting process for enhanced flexibility, precision and efficiency.
The proposed workflow involves the following components of Digital environment & physical environment. In this workflow, a slip casting simulation software to estimates the resulting cake’s shape and thickness distribution following robotic movements was developed to address the unpredictability of this process. Robotic motion is employed to effectively produce variations in cast pieces.
Our
Typical Slip Casting Process
Comparison between
The proposed workflow involves the following components of Digital environment & physical environment. In this workflow, a slip casting simulation software to estimates the resulting cake’s shape and thickness distribution following robotic movements was developed to address the unpredictability of this process. Robotic motion is employed to effectively produce variations in cast pieces.
Mold Creation
The mold is the negative space into which the slip is poured. Molds can be made from plaster, silicone, or other materials.
Slip-Pouring
The slip is poured into the mold slowly and carefully to prevent air bubbles from forming. The mold should be filled to the top.
the top.
Once the desired thickness is achieved, the excess slip is poured out of the mold. This can be reused for future slip castings.
Once the desired thickness is achieved, the excess slip is poured out of the mold. This can be reused for future slip castings.
Cake Growth
Left slip to sit for a period of time, to allow the clay to thicken and settle, called the cake growth.
Left slip to sit for a period of time, to allow the clay to thicken and settle, called the cake growth.
Our proposed alternative tries to create variation in the casted piece from the same through partially filling and tilting the mold partial cast piece.
Comparison between different casting methods
Once the clay has set, the mold is removed and the cast is allowed to dry.
Once the clay has set, mold is removed and the cast is allowed to dry.
Once the cast is dry, it can be trimmed, sanded, and smoothed to remove any imperfections or excess clay.
Once the cast is dry, it can be trimmed, sanded, and smoothed to any imperfections or excess clay.
Digital simulation of the dynamic slip casting process. The red dots indicate the thickness of cake.
To address the challenge of unpredictability of slip behavior inside the mold and advance the field of slip casting, we introduce a novel approach: robot dynamic casting. In this method, the mold is continuously rotated during the casting process, allowing for the creation of more intricate and precise geometries. However, implementing dynamic casting effectively requires a deep understanding of the underlying physics and an ability to predict the outcomes of the process. This is where our simulation program comes into play.
While our simulation program has proven effective in predicting the shape of dynamic slip casting results, it currently does not account for shrinkage during the solidification and drying processes. This limitation may lead to discrepancies between the simulation predictions and the actual outcomes. Future improvements to the program should include incorporating shrinkage calculations to enhance the accuracy of the final shape predictions.
The choice to determine the thickness of the solidified slip (cake) based on the coverage time for each mesh vertex is grounded in previous research findings. Studies have shown that during the casting process, the cake thickness grows with the increased amount of time.
By tracking the coverage time for each vertex, we can estimate the thickness distribution of the solidified slip in the cast part, which is essential for optimizing the dynamic casting process.
Although the final piece was smaller due to part shrinkage, a comparison between the simulation results and the 3D scan of the model demonstrated the simulation’s effectiveness in reverse engineering and generating the robot’s trajectory based on the desired design geometry. However, this process also highlighted challenges related to the edge condition of the resulting piece.
Similarly as each robotic motion was repeated to build up thickness, we discovered that the amount of slip inside the mold decreases resulting in a brittle edge condition. Reduction of slip inside the mold occurs as robotic motion is repeated and development of method for adding additional slip inside the mold was necessary.
Movable slip volume is calculated to get a better understanding of the rate off decrease of slip as each robotic movement was repeated.
To address the decreasing slip inside the mold, we’ve designed a unique Arduino controlled slip injector that adds more slip as needed as each cycle of robotic routine is repeated. This helps maintain balance and ensure a smooth casting process while reducing the thin brittle edge condition. The design integrates an stepper motor that is controlled by robot’s i/o that actuates a syringe for precise slip volume injection and a LCD screen with a button system for easy adjustment of slip amount for different robotic routine.
To further fine tune our workflow, we designed and fabricated a larger mold and a custom end-effector with aluminum extrusions. The design integrates a series of CNC foam inserts that would hold various types of mold in different initial starting orientation while also allowing for ease of interchanging of the molds for different robotic routines.
To further explore our workflow for creating geometric variations and to potentially informing future research into architectural applications such as facade screen assemblages, series of grid system studies has been done for nodebased geometry and workflow has been tested to fabricate a full scale mock-up. Node-based geometry is a versatile tool for producing intricate shapes and patterns. By adjusting the size of individual nodes, we can generate even more variation in our designs. Manipulating node size allows us to refine the overall scale and visual appeal of our design. Whether we’re aiming for dense, tightly packed grids or more open and airy structures, the spacing between nodes is also a crucial factor in achieving our desired effect. Furthermore, there are various node types and configurations to choose from, each offering distinct visual possibilities.
1 type of component with same node size, 5 types of component with two types of node size.
Prototype was designed for fabrication to fully test our extended research. The prototype consists of 28 pieces based on a tetrahedral grid system for it’s symmetrical nature and 4 mold variations for fabrication feasibility.
The plaster mold was fabricated using a 3D printed shell which liquid plaster was poured and got melted away with a heat gun after the mold has cured. The plaster mold is an 4-part mold with interchangeable lid at each node that allows for selection of injection point depending on the desired casted piece and initial starting position of the robotic routine.
The prototype consists of 28 parts with 4 different component variations with different radius at the node with different partial cast piece to fully explore the capabilities of the proposed workflow.
Location:
Year:
Instructor:
Philadelphia, Pennsylvania, United States 2022
Andrew Saunders, Riley Studebaker, Claire Moriarty
Partner: Shunta Moriuchi, Jingyu Luo, Renhu Wu, Shuoxuan Su
Description:
We proposed a 900 square feet speculative ceiling for the Upper Gallery of Meyerson Hall. The ceiling scape deploys a series of hierarchical variations. The variations in the depths of the lilies and the peaks form different zones under the ceiling that resembles an infinite mushroom forest. Peaks stick out like vines and low plants, and lilies bump up to create circular spots on the ground. Like getting lost in the woods, the ceiling scape stimulates the wanderlust and Deja vu feeling of the person below.
We chose to study the Linear Construction in Space No. 4 by Gabo in which he created ruled surfaces using bronze wires strung between curved steel rails and Pevsner’s Construction of developable Surface which used bronze, oxidized brass, and a black marble base to construct developable surfaces.
Through a careful analysis of both sculptures, we digitally reproduced the ruled surface forms through which we were able to extract and digitally model specific geometric qualities.We transposed those ruled surfaces into volumetric implications of rulings in space to deconstruct the geometric moves made by the sculptures and to depict the geometry in light and shadow for input into neural networks.
We fed the images of these new distinct but identifiable and reproducible elements from our sculptures into the Convolutional Neural Network. Through this process, we were able to generate an outline for us to extract the threedimensional unprecedented geometric ceiling arrangements.
Although CNN excels at creating two-dimensional novel designs from learned arrangements of embedded information, it lacks the knowledge and struggles to produce perfect 3D outcomes that can be built. To overcome these limitations, we modeled explicitly CNN outcome images of the selected geometry to choreographed paths for multi-axis robotic hotwire cutting routines to be prototyped, using our in-depth understanding of distinct identifiable elements and the geometric hierarchy according to shape, brightness, and stacking relationship.
We proposed a 900 square feet speculative ceiling for the Upper Gallery of Meyerson Hall. The ceiling scape deploys a series of hierarchical variations. The variations in the depths of the lilies and the peaks form different zones under the ceiling that resembles an infinite mushroom forest. Peaks stick out like vines and low plants, and lilies bump up to create circular spots on the ground. Like getting lost in the woods, the ceiling scape stimulates the wanderlust and Deja vu feeling of the person below.
Location:
Year:
Instructor:
Religion, life, and epidemic
Dharavi, Mumbai, India
2020
Zhengwei Xia, Hengliang Tang
Partner: Haoxian Wang
Description:
Popularly known as Asia’s largest slum, Dharavi has active economic activities but poor living conditions. Such a problem is even more evident during the epidemic. People here lack proper medical treatment and a clean housing environment because they cannot protect their interests by speaking with a common voice. Therefore, many of them lost their jobs and struggled to live.
Besides, most residents here have their religious beliefs. Unfortunately they cannot fulfill their rituals because large assemblies are forbidden during the epidemic.
Based on the local features and slums dwellers' material and spiritual needs, the goal of this design is to improve their current life, maintain their rituals and make the community adaptive to the epidemic.
Religious behavior sequence
Pious
Dwellers in Dharavi
Life production
Low shanty towns
Recite Scriptures
Individual Public Group
Private
Large-scale cultural events
Group praying
Living Scaffolding
Playground
Holi Festival
Roof
Commercial Industry
The stepwell is considered an essential monumental structure beyond its functional purpose of the source of water supply.
Besides, people can use it during the dry or rainy season, which shows adaptability due to its vertical stratification.
Set the center of "stepwell". Split the site by traffic flow. The courtyards. Rectraction for public space. Connections and Platforms. Vertical transportation.
Site Plan
Religious Living Community Commercial Production Anti-epidemic
Religious Living Community Commercial Production Anti-epidemic
Behaviors type
Behaviors type
Use time Policies during the pandemic
The basement floor is used for production and storage activities, serving for the stores on the ground floor.
Religious Living Community Commercial Production Anti-epidemic
Behaviors type
Use time Policies during the pandemic
People in Dharavi use to stay outside their home and communicate with neighbours or do some work in front of their homes.
New dwellers can buy a container home. Their homes can be installed on the structure by using the tower cranes.
Dewellers can plant vegetables, dry clothes, play, and do some manual work here.
Explosive View
In this design, the central plaza is the buttom of the "stepwell". It shares similar spatial sequence with the traditional indian stepwell, arousing residents' emotional resonance.
Roof
Canopy
Fixed roof
Above
Stairs
The 'temple'
Container home
First Floor
The 'temple'
Stairs
School
Ground Floor
The 'temple'
Courtyard
Playground
Retail store
Tower crane Open plantform Community service Production areaFamily members: one pair of parents, three children
Containers used: 6m*2.1m*2.7m*2
Decoration elements
Originated from Hinduism
Family members: one pair of parents, two teenagers, four children
Containers used: 6m*2.1m*2.7m*1, 12m*2.1m*2.7m*2 Center
Location:
Year:
Instructor:
Partners:
Description:
The renaissance of automotive industry
Detroit, United States
2021
In this context, we predict boldly that the model of internal-centralized production will regain its importance in the near future. The Detroit, which was trying hard to return to its roots as a vibrant city center in the past decades, was emptied the streets again by pandemic.
Therefore, we decide to propose our skyscraper design solution in the motor city Detroit, aiming to revive the development and transformation of traditional industrial cities.
Due to the pandemic, the industrial globalization was impacted heavily. However, the current situation provides an opportunity for those industrial cities which declined under globalization to revive again. In terms of production, the pandemic will certainly not terminate the industrial globalization, but it will help transform the globalization into a new form, a form of regional, limited globalization. Strikes and lockouts happening all around world right now reminds every country that it is important to have its own industrial chain.
During this crisis, however, Tesla, a new giant of car industry emerged. Apart from its main service of electric vehicles showing its concern on the environment, the key factor that contribute Tesla's being a game changer is the Tesla Gigafactory, which is designed to be a net zero energy factory and one of the largest building on earth. The Gigafactory include not only the assembly line, but also the production of batteries and electricity generation. In the Gigafactory, the designing apartment work closely with the producing apartment, which make it easier for new technoloy to put in to use and get the feedback in the first moment. All of these could are good examples for the traditional car makers to imitate.
As one of the biggest cities in the United States, Detroit was the symbol and prize of American industry. However, due to the decline of the motor industry, the factories were discarded, and the population declined rapidly downtown. The once prosperous city was filled with violent crimes, a high unemployment rate and a severe financial crisis. The pandemic made people try so hard to change back to the original point.
Considering the current situation, we propose to establish a vertical factory in the form of skyscrapers, which allows for a complete production chain of the automobile. The skyscraper is armed with energy production, raw material transportation, product development, production and assembly, performance testing, tourist etc.
In terms of the design, we decide to revive the famous high-tech style after combing the historical facers and industrial background of Detroit. The goal is to change the current situation of the city by emphasizing on the development of science and technology, as well as making it regain its confidence.
The newest fusion generator on the roof will provide clean energy for the operation for the whole skyscraper. The production workshops in the center each have their own responsibilities to produce assembly component for the assembly line.
On both sides of the tower are office area for staff. The side-building also serves the function of transporting people to different higher platform.
The assembled car will be temporarily stored in the cylindrical parking area at the bottom, waiting to be tested and sold.
The main body of the building with the spiral conveyor belt around makes all the steps of production and the assembly more efficient.
At the bottom is a user experience center where the public interact with the product. People can see the testing and professional equipment of the cars. Moreover, they can complete test drive experience on the outdoor runway directly.
Location:
Year:
Instructor:
Description:
Suzhou, China 2020
Individual Work
Suzhou is a city with profound cultural deposits, including classical gardens, ancient buildings and old streets. And the site is located in Suzhou Industrial Area that has been developing rapidly since 1994.
Next to the site is the Xietang Old Street, a famous antique commercial street that attracts visitors from all over the city. The art museum is designed to respond to the history of the site and combine it with the modern way of design.
Space Strategy
Main exhibition
The main exhibition room is a spirling linear space. Visitors can enjoy the view of the river and the historic district at the end.
Temporary exhibition
The temporary exhibition room is the reverse extension of the main exibition room, which is semi-underground.
Auxiliary area
The auxiliary area half-encloses the visiting area, allowing more connections.
Space optimization
Smooth the surface for the entrance and extrude new volume, a slope, connect the exit of the main exhibition room and the ground level.
The lecture hall
The volume of the lecture hall is extruded near the starting point of the main exhibition. Its roof can be used as a garden for the visitors.
THE SITE is located in Soochow Industrial Area that has been developing rapidly since 1994. Soochow is a city with profound cultural deposits. There are many classical gardens and ancient buildings here.
SURROUNDING the site is Xietang Old Street, which has a history of more than 760 years and has been rebuilt several times. Nowadays, it is an antique commercial street that has been completely rebuilt in the past few years.
The exhibition space is spirling linear space, which reminds the visitors of traditional scroll painting. They can enjoy the art work and the view of Xietang Old Street at the same time.
The new buildings are incompatible with the old street.
Space Evolution
Through addition, overlapping, reduction, and separation, the intersection of two linear spaces, one spirling and one semicircular, generates multiple space types.
We do not want our life to be disturbed by tourists.
It is enjoyable to sit by the river.
It takes hours to come here.
I feel like I was in a traditional chinese painting.
Exhibition rooms Exhibition rooms Gathering space Exhibition rooms Office rooms
Explosive View
The Art Museum creates different exhibition spaces. Through penetration and dislocation of different kinds of space, the design breaks the isolation of different rooms. The whole museum is covered by the roof, which inherits traditional Chinese roofs' basic form and structure but differs from that in material and building techniques. So the new roof can be more stable and versatile to provide more possibilities to the space under the roof.
Location:
Year:
Instructor:
Description:
Suzhou, China
2021
The gymnasium is designed for students at Soochow University. In this design, I used the tensile membrane structure to create a natural and organic environment that benefits students physically and mentally.
Apart from holding large sports events, this gymnasium can also be used by every student for everyday exercise and club activities. The running track on the second floor is open to students and also stabilises the whole structure.