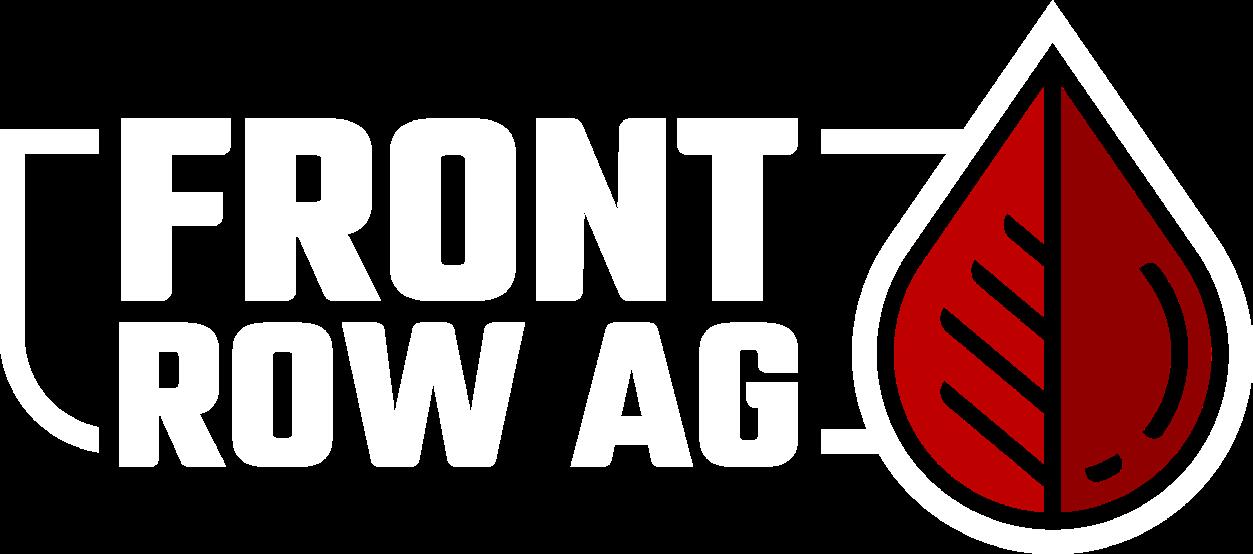
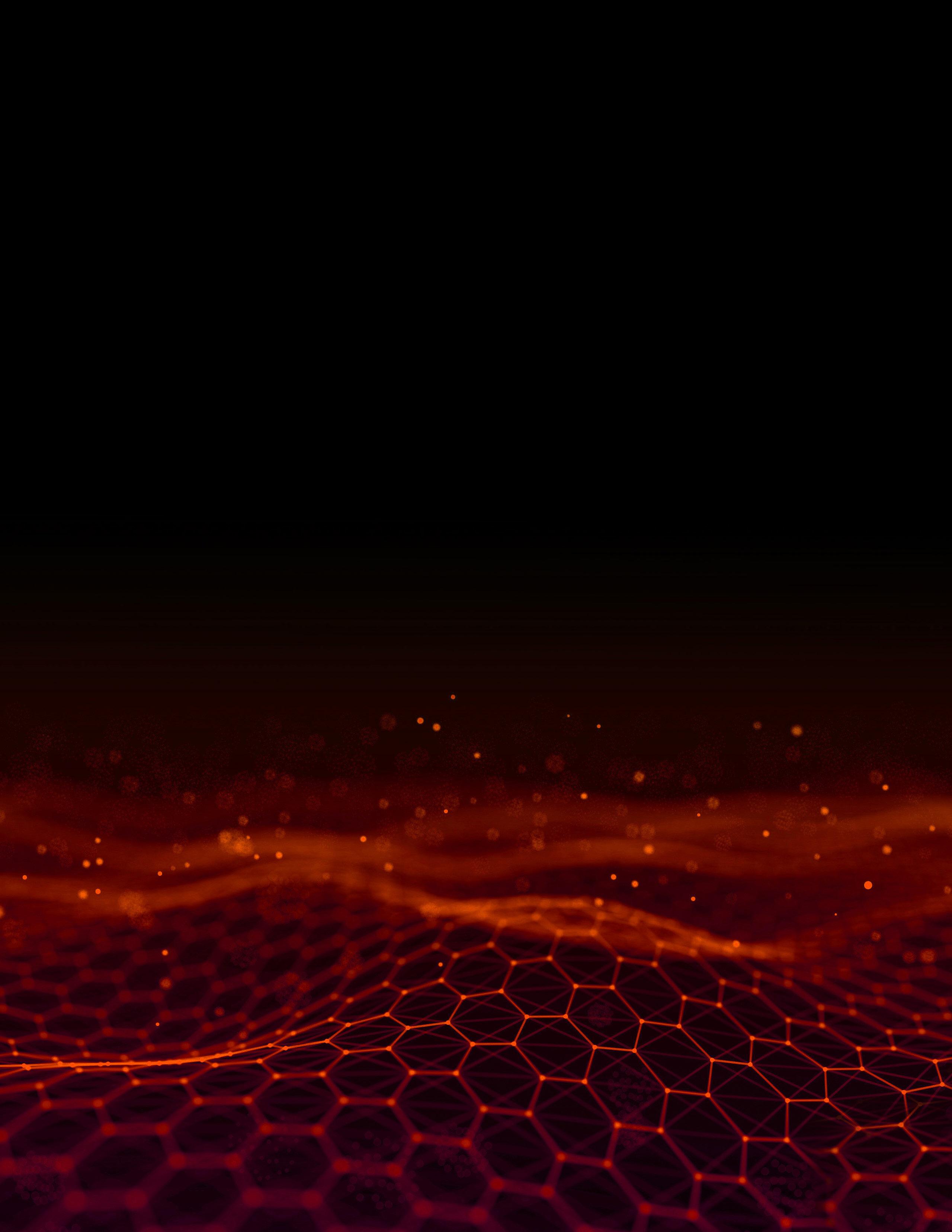
At Front Row Ag, we’re thrilled to share this Product Guide with you. Choosing to work with us means gaining access to much more than just top-tier fertilizers and cultivation products. As your fertilizer partner, we’re committed to providing expert advice, educational resources, and comprehensive support for your operations and systems.
Front Row Ag was founded with a mission to deliver cultivators unmatched customer service while offering the industry’s most effective, highest-quality fertilizers.
Stay connected with us as we continue to push boundaries, share knowledge, and lead the way in cannabis cultivation. With Front Row, you’re not just getting products—you’re gaining a partner dedicated to your success.
Matthew Curran, CEO, Front Row Ag
Matthew Curran Chief Executive Officer
Matthew Curran founded Front Row Ag in 2018 after years of exhaustive development and formulation of the Front Row 3-Part.
From caregiver to licensed commercial cultivator, Matthew has over 16 years of cultivation expertise in 3 countries, 16 states, 40+ operations, and millions of sq.ft. of canopy. This includes equity roles, executive and C-suite roles, and daily operations.
Curran Graduated from Colorado State University with a degree in Floriculture, his training ranged from agronomy to chemistry.
Egan O’Keefe Co-Founder
Egan O’Keefe, from Loveland, CO, joined the industry in 2008. He co-founded Calvin and Krebs Management Services in 2016 with Matt. In 2018, they launched Front Row Ag fertilizer line.
Egan helped Harvest Health and Recreation grow, leading to its 2021 acquisition by Trulieve.
Now at Story (a national MSO) as Director of Cultivation, he supports Front Row with industry expertise and connections.
Patrick Kanzler CEO of Solstice Ag
Patrick Kanzler’s journey in the cannabis industry catapulted him from managing a grow store in in 2007 to managing distribution for top fertilizer brands.
He launched Humboldt’s first cannabis vape brand in 2013 and his knack for spotting trends led to partnering with Front Row Ag as their exclusive distributor in 2019.
His background in managing cultivation supply chains and marketing top nutrient brands uniquely positions him for success as the exclusive distributor of Front Row Ag.
Zack Vondrak VP Sales, Solstice Ag
Zack Vondrak has an extensive history of managing sales relationships across the globe - adapting and evolving with the many changes in the industry.
His passion and tenacity has helped successfully launch several fertilizer brands. In the early 2000’s he was the top-performing sales rep in specialized fertilizers.
He has over a decade of experience with both liquid and soluble fertilizer sales.
The Front Row Ag and Solstice Ag team brings extensive commercial cultivation experience.
As current and former cultivation managers and executives, we understand challenges intimately and leverage operational experience for customers. Customers benefit from our team’s experience managing our own facilities as well as the several millions of square feet of canopy we’ve toured and advised.
Solstice Agriculture is the exclusive worldwide distributor for Front Row Ag. Solstice Ag handles sales, marketing and logistics for Front Row Ag products. Solstice has been a distributor of dry soluble fertilizers since 2015. Together the two companies work as one team to provide the best products and services in the industry.
At Front Row Ag, we are more than just a fertilizer company; we are your dedicated nutrient partner.
Our mission is to empower cultivators with the tools, technology, and information they need to achieve success in every square foot of their cultivation efforts.
With years of experience in the industry, we understand the challenges you face and are here to support you every step of the way.
We pride ourselves on using the highest grade inputs to ensure consistency and reliability in our products. Our commitment to quality control is paramount, and our on-site lab allows us to maintain the rigorous standards that our partners expect.
This dedication ensures that you receive products that perform consistently, allowing you to focus on what you do best—cultivating excellence.
Front Row Ag empowers you with a secure supply chain sourcing only premium inputs and holding years of raw materials.
Our strategic blending partner offers you unfettered access to hydrology and analytical lab services. These on-site lab services ensure every lot meets our exacting standards.
At Front Row Ag, we believe in building strong, lasting relationships with our clients. Our dedicated account management team and crop advisors are here to provide personalized support tailored to your unique needs.
Whether you have a question about our products or need advice on optimizing your nutrient strategy, our team is always ready to assist.
Front Row Ag is your fertilizer partner and crop consultant. Our decades of combined, industry experience allows us to provide unparalleled customer service that helps cultivators maximize quality, yield, and exceed their next benchmark. We have consistently improved results for operators all over the globe.”
Formulator and CEO, Matthew Curran
We are committed to empowering cultivators by providing access to cuttingedge technology and comprehensive information. Our goal is to equip you with everything you need to maximize your yield and quality. This includes access to our partner network covering all aspects of cultivation operations.
By partnering with Front Row Ag, you gain a trusted ally invested in your success.
Join us and experience the difference of working with a partner who truly understands and supports your cultivation journey.
“nothing short of excellent”
“Their customer service is amazing!”
“Quick to respond and value the relationship we have built. 10 out of 10”
“Super knowledgeable and always available to help. A true asset to my business.”
Front Row Ag offers comprehensive support services, including fertilizer usage estimation, KPI analysis, and onboarding for new and conversion customers. We provide water and mineral analysis at our Hydrology and Technical Lab. Our dedicated account managers and crop advisers provide continuous tech support, remote crop steering data reviews, and access to our partner network. We cater to any size or type of operation, providing handson support for licensed commercial cultivators and educational content for all. Customization is key; our team reviews your facility’s processes and limitations to offer tailored feedback on implementing Front Row Ag practices. Our approach to optimizing $/sqft/ day helps maximize your facility’s revenue, efficiency, and profitability. Our product performance has led to
multiple cannabis cup winners and increased thousands of cannabis brands quality, making sure they are on the Front Row of dispensary shelves across the globe.
We believe in continuous improvement and are constantly working to innovate new products that deliver agronomical value. Front Row Ag has expanded into international markets and continues to deliver tremendous value to established and emerging markets through education platforms like the Front Row Ag Certified Program.
Learn more about the Front Row Ag Certification Free Online Course at Frontrowagcertified.com
At Front Row Ag, we understand how important it is for cultivation facilities to have well-trained, knowledgeable staff. That’s why we continually publish comprehensive educational resources and host our Certified Technician training course. (See pg. 114.) Our free online Technician Course gives you the essential Front Row Ag fertilizer information to thoroughly train new hires or improve the skills of current employees. Taught by Front Row Ag experts, the course covers essential topics like nutrient mixing, fertigation systems, runoff analysis, and more. Upon completion, your staff will have a solid technical foundation and be certified
in proper deployment of Front Row fertilizers.
Rather than spending hours creating your own materials or flying staff elsewhere for training, you can access our resources anytime from any device.
In addition to the Technician Course, we regularly publish new articles on our industry-leading blog. Written by top cultivation specialists, these in-depth reports break down the latest advances in hydroponics, cultivation management strategies, nutrient formulation updates, and more. Commercial cultivators also receive access to an exclusive library of resources. Apply for a commercial account today to learn more!
Access our robust affiliate network of businesses that can support every aspect of your cultivation operation.
Apply for a commercial account today!
Set your team up for success with Front Row Ag onboarding. We offer leaf tissue testing to commercial customers to maximize crop health. Deploy best practices through your custom water test using our hydrology lab, and ensure every crop is fed with precision with our batch-to-batch mineral analysis.
Front Row Ag starts our relationships by testing customer water. Typically including but not limited to pre-filtered source water, filtered irrigation water, and irrigation water from zones. Our hydrology professionals identify filtration recommendations, ions of risk, bacteria and mold potential with treatment plan, plus outline best use practices for deploying Front Row Ag.
Your operation is unique. Leaf tissue testing enables you to exceed your goals by establishing baselines, relating data to environmental performance, and identifying areas to improve crop nutrition. Front Row Ag provides professional plant tissue analyses and recommendations to all our cultivator customers. Our proprietary testing processes establish a site-specific, nutrient management program improving crop performance harvest after harvest.
Front Row Ag manufacturing includes a robust Mineral Analytical Lab. On arrival, all our premium sourced inputs are tested for purity, guaranteed analysis, and are sorted. Every sub-batch of a larger lot is sampled and tested while each ingredient is added to blend to specification versus minimum guaranteed analysis. This means your fertilizer doesn’t vary in EC and provides unwavering performance.
Be proactive early through laboratory testing, it is key to avoiding more serious deficiencies down the line. It helps optimize harvest yields and quality. These reports also provide a record over time so you can monitor progress.
Don’t gamble with your crops’ health when Front Row Ag analysis services are an affordable way to check for issues. Our certified labs and accredited staff are here to support your growing operation’s success. Rely on data as part of an integrated nutrient management plan for top-tier results crop after crop.
Front Row Ag’s three-part system creates a complete, balanced nutrient profile through the interaction of Part A, Part B and Bloom.
The ratios of these components can be adjusted to influence growth patterns, support specific developmental phases, enable precise crop steering and optimize plant responses.
Part A maximizes morphology, aromatics, and potency with a robust and diverse micronutrient package complimented by perfect quantities of calcium and nitrogen.
We like that their 5-phase recipe tapers nitrogen over the plant life cycle. Our trial run of A/B/Bloom outcompeted our dialied-in comparison run of a competitor product line. That’s why we switched.”
Lead Cultivator, Montana, Front Row Ag Client
Part B optimizes photosynthesis with high magnesium concentrations, while sulfur, potassium and phosphorus set a foundation for high performance flowering.
Bloom transitions metabolism from veg to flower by enhancing magnesium ratios and giving generative cues with boosted levels of potassium, phosphorus and sulfur.
We know that you need to know what you are feeding your plants.
Here’s why our customers choose Front Row Ag:
ITS CONSISTENT
Our stringent quality assurance ensures that every batch meets the highest standards, so you never have to worry about inconsistencies.
YOU CAN COUNT ON IT
With our robust supply chain, even a global pandemic can’t disrupt your operation. Our inputs are reliable, and we deliver them right to your door.
WE ARE HERE TO HELP
We offer technical assistance as part of your onboarding package, giving you peace of mind and freeing you from operational headaches.
Choosing A/B/Bloom allows you to focus on what you do best — growing award-worthy plants.
Derived from
• calcium nitrate
• potassium nitrate
• boric acid
• copper EDTA
• iron EDTA & iron DTPA
• manganese EDTA
• sodium molybdate
• zinc EDTA
2-13 -17
0-35-29
Derived from
• potassium nitrate
• monopotassium phosphate
• potassium sulfate
• magnesium sulfate
Derived from
• potassium nitrate
• monopotassium phosphate
• potassium sulfate
• magnesium sulfate
PhosZyme is a concentrated enzyme product with biostimulant effects targeted towards increasing yield and quality. It’s a soluble powder containing high concentrations of mannanase and phosphatase, enzymes that enhance water availability, nutrient uptake, and microbial activity.
The activity of these enzymes have a number of positive effects on plants including:
• Increased water and nutrient absorption
• Greater fertilizer efficiency
• Enhanced microbial activity in rootzone
These effects contribute to improved stress and drought tolerance that ultimately leads to greater rates of photosynthesis, increased production of flowers, and secondary metabolic products including cannabinoids and terpenes.
• Mannanase works by breaking down starches around the root exudate. This process draws water and nutrients towards the plant roots and yields plant available sugars for absorption at the roots. These sugars are used later for metabolism, protein creation, tissue building, and generating terpenes.
• Phosphatase enzyme catalyzes the conversion of phosphorus into forms that are readily available for absorption, without requiring additional microbial action in the root zone.
• Improvements to water and nutrient exchange plus the heightened phosphorus leads to a healthier rhizosphere that supports improved microbial activity.
SHOP NOW
We now recommend mixing Phoszyme directly into the Part B stock tank rather than maintaining a separate Phoszyme stock tank. This change offers two benefits:
• Eliminates the need for a dedicated injector, freeing space in your fertigation panel
• Protects against bacterial contamination from source water which can thrive on Phoszyme's MAP contentPart B's acidity and salinity prevent this bacterial growth
If your current standalone Phoszyme setup (160 g/gal) works well, you can continue using it. For alternative stock solution combinations, please consult the Phoszyme compatibility and rate charts at frontrowag.com/phoszyme
Enzymes such as phosphatase and mannanase drive critical processes like digestion and nutrient cycling. Learn how enzymatic products like Phoszyme are made, how they work, and the positive effects they have on your grow.
Enzymes are remarkable biological molecules that act as catalysts, enabling and accelerating chemical reactions in both living and “non-living” systems. In the natural world, enzymes drive critical processes like digestion and nutrient cycling. For example, the human digestive system uses a suite of enzymes to break down food molecules into absorbable nutrients. In soil, enzymes produced by microbes depolymerize complex organic matter, releasing mineral nutrients for plant uptake. Now, innovative hydroponic cultivators are harnessing the power of enzymes to revolutionize their growing systems and maximize plant productivity.
Two enzymes that hold particular promise for hydroponics are phosphatase and mannanase.
Phosphatase enzymes catalyze the hydrolysis of organic phosphorus compounds, converting them into bioavailable inorganic phosphate that plants can readily take up. Many substrates contain abundant phosphorus, but it is locked up in forms that are inaccessible to plants without enzymatic mineralization. Harnessing phosphatase in hydroponic systems can liberate this trapped phosphorus pool. Mannanase’s primary function is to break down starches in the exudate that surrounds the outermost layer of the root tips. This chemical reaction creates a draw of water and nutrients to the root zone and releases sugars to the plant. This in turn boosts root growth and increases microbial activity. By supplementing hydroponic nutrient solutions with phosphatase and mannanase, growers can enhance phosphorus and micronutrient availability to their crops.
In nature, extracellular enzymes like phosphatase and mannanase are produced by a diverse array of soil bacteria and fungi. Researchers have identified certain bacterial genera as especially prolific enzyme producers:
• Bacillus
• Pseudomonas
• Streptomyces
These enzyme-secreting bacteria play a key role in organic matter decomposition and nutrient cycling in soil ecosystems. They help liberate carbon, nitrogen, phosphorus and micronutrients from complex organic polymers, making them available for uptake by plants and other microbes.
Some companies in the hydroponics industry are now culturing and packaging these enzyme-producing bacterial strains for use as microbial inoculants. Adding carefully selected bacterial cultures to hydroponic systems can create a “living” nutrient solution, continuously generating enzymes to optimize nutrient mineralization and uptake.
Microbial inoculant products often contain a combination of a food source, usually high in a sugar, supporting the living bacterial strain creating the perfect environment for explosive biofilm. Purified enzymes, like PhosZyme, eliminate the additional risk of biofilms and clogged emitters.
However, relying on microbes for the production of enzymes is a delicate strategy. Using enzymes produced via substrate microbes requires maintaining live organisms, building a large enough population size, and keeping substrate parameters within the right range for those microbes. With products like PhosZyme, cultivators can now get the benefit of enzymes directly, without having to maintain live microbial colonies.
So what kind of benefits are hydroponic growers seeing with enzyme supplements? Numerous research trials and grower experiences have demonstrated promising results. Studies have found that crops grown with phosphatase and mannanase enzyme treatments show:
• Increased growth rates
• Greater final yields compared to untreated controls
• Higher concentration of bioactive compounds
• Enhanced root development
Trials
have reported 10-30% yield increases in crops treated with phosphatase enzymes. Enzymes appear to boost the efficiency of nutrient uptake and utilization by plants, leading to improved crop performance.
Phosphatase breaks chemical bonds that bind phosphorus to metal ions in the root zone, liberating it for plant uptake. Mannanase degrades mannans in plant cell walls, primarily at the root tips, potentially increasing the availability of sugars and micronutrients while drawing water and nutrients towards the root tip.
One example of a precision enzyme product now available to hydroponic growers is Front Row Ag’s PhosZyme. PhosZyme is a soluble powder that combines phosphatase and mannanase enzymes with monoammonium phosphate fertilizer.
• The phosphatase breaks chemical bonds that bind phosphorus to metal ions in the root zone, liberating it for plant uptake.
• The mannanase degrades mannans in plant cell walls, primarily at the root tips, potentially increasing the availability of sugars and micronutrients while drawing water and nutrients towards the root tip.
• The monoammonium phosphate provides a targeted boost of nitrogen and phosphorus to further drive growth.
PhosZyme is applied at very low usage rates, and delivers high quantities of enzymes and almost undetectable levels of fertilizer. PhosZyme enhances root growth, nutrient uptake, and harvest weights across a range of hydroponic crops. It can be used alone or combined with other fertilizers to improve overall nutrient efficiency. Products like PhosZyme exemplify how innovative growers are leveraging enzymes to optimize hydroponic fertilizer programs.
The use of enzymes in hydroponics is still an emerging area with ample room for further research and optimization. Key questions include determining optimal enzyme dosage rates and application timing for different crops and growth stages. Potential interactions between enzymes and other hydroponic solution components also need to be evaluated to ensure compatibility. Continued research will help refine best practices for integrating enzymatic biostimulants into hydroponic production. Going forward, enzymes are an increasingly valuable tool in advancing hydroponic crop nutrition. By harnessing the metabolic power of soil microbes and translating it into bioavailable plant nutrition, enzyme supplements can help growers maximize fertilizer efficiency while reducing costs and environmental impact. Phosphatase and mannanase are two enzymes with demonstrated potential in hydroponics, but many other candidates are also being explored, including:
• Cellulases to break down root-bound cellulose
• Proteases to enhance nitrogen mineralization
• Phytases to liberate more phosphorus from inorganic sources As research progresses, an expanding toolbox of targeted enzymatic biostimulants is expected to emerge, tailored for different crops and growing conditions. The integration of hydroponic systems with microbial biotechnology and synthetic biology may open up new pathways. It’s our prediction that enzymes will likely play a central role in shaping the future of sustainable, productive hydroponic agriculture.
Customer-reported results provided by a Maryland commercial cultivator show an average yield boost of 31% after integrating PhosZyme into their nutrient program.
REQUIRED TO BE LABELED AS 10% SILICON DIOXIDE
These beneficial outcomes are mediated through a number of pathways:
• Mechanical effects: As it’s incorporated into plant tissues, it increases the weight and strength of cell walls, creating a physical barrier to insects and fungal pathogens. The increased strength also leads to improved plant posture and resistance to drought, temperature, and wind.
• Nutrient absorption: Silica improves the uptake of beneficial elements and interferes with the absorption of harmful ones such as heavy metals.
• Water balance: By modulating the leaf transpiration rate and enhancing root water uptake, silica alleviates drought stress.
• Regulation of plant hormones and genetic expression under abiotic stress conditions.
• Enhanced activation of plant immune and antioxidant systems.
Silicon (Si on the periodic table), while being the second most abundant element in the earth’s crust and 8th most abundant element in the universe, is not directly available for absorption into plants. Although some water-soluble Si exists naturally, the majority of Si on earth is in the form of insoluble oxides or silicates in the soil.
Silicon Dioxide (SiO2), commonly referred to as silica, is the main component of sand and quartz. Although silica affects the physical properties of soil, it’s also not directly available for plant absorption and has limited use in hydroponics as it takes months to years to break down into a form that can be absorbed by plants. The main use of silica sand in horticulture is as an additive to increase drainage and aeration of heavy soils, to help prevent waterlogged conditions. Silica sand can also be utilized as a growing media in certain types of hydroponic systems, such as subsurface drip irrigation, and when coated in plastic as a substrate for ebb and flow flood trays. Note that silica sand alone is an inadequate substrate for most types of plants as it does not provide nutrients or moisture-retention capabilities. When used properly as an additive in soil or certain hydroponic substrates, silica sand can open soil structure, improve aeration, and increase drainage. Silicates refer to when Si is bonded with cations of Ca, K, Mg, and Na, forming a variety of crystalline compounds. The most common silicate used in horticulture is potassium silicate, K2SiO3, although calcium silicate and magnesium silicate can also be used. When dissolved into solution, these silicate products will yield a small amount of plantavailable silica (PAS) as monosilicic acid. At high concentrations, potassium silicate solutions can be unstable and gel. Potassium silicate is alkaline, so it must be used carefully in hydroponic fertilizer solutions to avoid changing the pH. Overall, silicate compounds are of limited use in hydroponics due to their low solubility, alkaline nature, and the small amount of plant-available silica they release.
Monosilicic acid (MSA) (Also known as orthosilicic acid) is H4SiO4, the only form of silicon that can be directly absorbed and used by plants. All of the previously mentioned forms of Si must break down into MSA to be absorbed and exert beneficial effects on plant physiology and structure. Since SiO2 and silicates break down slowly and yield a small amount of monosilicic acid, product formulations containing pure and stabilized MSA are desirable for hydroponics. These products, such as Front Row Si, contain fully plant-available silica in a stable aqueous solution. MSA products allow precise control of silica levels in hydroponic fertilizer, do not change pH, and can be applied as a foliar spray or root drench.
The chemistry of Si in fertilizer solutions can be quite complicated, but the important fact to keep in mind is that plants can only absorb MSA and that other forms of Si are only as beneficial as their capacity to yield MSA to the plant roots.
To achieve an equivalent ppm of MSA in the fertilizer solution with one of the various silicate compounds (e.g. potassium silicate), much higher usage rates are required. Front Row Si is 10 times stronger than most other Si alternatives, resulting in lower usage rate and cost savings. With alternative Si products, the higher usage rates comes with the complication of adding excess potassium or other ions to the fertilizer solutions and these changes must be accounted for in the overall elemental ratios of the fertilizer solution. For example, to achieve 13 ppm of soluble silica in the fertilizer solution using potassium silicate (assuming 8.5% plant available silica), the usage rate would be 0.6 g/gal, resulting in the addition of 40+ ppm potassium in addition to the silica. This excess potassium must be accounted for to maintain proper ratios of other major elements such as nitrogen and phosphorus. Additionally, silicates will significantly raise the pH of the fertilizer solution and must be mixed appropriately to prevent reaction with acidic ions. Front Row Si adds 13ppm of MSA in solution at a rate of 0.5 ml/gal, without contributing any additional K ions or changing solution pH.
Given the above issues, an increasing number of cultivators are using stabilized, high-purity MSA products to deliver silica directly in the form the plants can use, both in the feed solution and through foliar application.
Silica’s beneficial effects are mediated through a variety of mechanisms including mechanical strengthening, controlling water balance, regulating nutrient absorption, gene regulation, and activation of plant immune systems.
As plants incorporate silica into tissues, this increases the mechanical strength of stems, leaves, and cell walls creating a physical barrier to insects and fungal pathogens. Research in many varieties of high-value agricultural crops shows that silica substantially decreases the frequency and intensity of diseases and pest infections. The increased density and weight of plant tissues also contributes to the yield increases seen in a variety of crops with Si application. Silicon deposition in plant tissues provides abrasion and penetration resistance to
fungal hyphae and insect mouthparts, decreasing their ability to successfully invade plant tissues.
Water deficiency can be caused by low rootzone water content, excessive salinity in the rootzone, or high water loss from transpiration due to high VPD and wind. Si application improves the plant’s resistance to water stress and ability to maintain turgor by enhancing water uptake from the roots and adjustments to transpiration rate by reducing water loss through leaves. Silicon enhances aquaporin production, the water channel proteins responsible for rapid water movement through roots and leaves. By improving water uptake and reducing water loss, Si allows plants to maintain favorable water balance and turgor even under drought conditions. This leads to sustained photosynthesis, growth, and yield, even when water is limited.
Si also improves plant nutrition under adverse conditions by increasing the uptake of beneficial nutrients and interfering with the absorption of harmful ones, especially heavy metals. Research shows that plants treated with Si are protected against heavy metal toxicity and don’t show the drop in photosynthesis and growth that we would expect when exposed to heavy metals in the soil. At the same time, Si enhances activity of plasma membrane H+ATPase, improving nutrient uptake into root cells. By both blocking toxic elements and improving uptake of beneficial nutrients, Si helps plants maintain optimal nutrition even when growing in suboptimal conditions.
In summary, Si exerts a number of beneficial effects on plant physiology, leading to:
• Enhanced resistance to biotic stress: decreased frequency and degree of infection with powdery mildew, botrytis, and insect. Silicon deposition in plant tissues creates a physical barrier to penetration and feeding.
Figure 1. (A) Leaf blast symptoms in rice after inoculated with Magnaporthe grisea for 10 days. Rice plants were continuously treated with (+Si) or without silicon (–Si). (B) Silica layer was formed in the cell wall of Si-treated plants and enhanced plant resistance to fungi infection by physical barriers. (Wang et. all, 2017)
• Enhanced resistance to abiotic stress: better plant health and performance under conditions of water stress, high salinity, wind, and adverse climate conditions. Si enhances water uptake and reduces water loss, allowing plants to maintain turgor and growth under drought conditions.
• Increased yield and quality of crops: Stronger and heavier tissues as well as increased photosynthetic growth rates leading to yield and quality improvements.
• Improved nutrient absorption: Resistance to heavy metal toxicity and improved absorption of beneficial nutrients.
These benefits are seen from both rootzone application in hydroponics as well as foliar applications. Front Row Si allows for root drench or foliar application, helping deliver the benefits of MSA in your garden.
Chen, D., Wang, S., Yin, L. and Deng, X., 2018. How Does Silicon Mediate Plant Water Uptake and Loss Under Water Deficiency?. Frontiers in Plant Science, 9.
Savvas, D. and Ntatsi, G., 2015. Biostimulant activity of silicon in horticulture. Scientia Horticulturae, 196, pp.66-81.
Wang, M., Gao, L., Dong, S., Sun, Y., Shen, Q., & Guo, S. (2017). Role of Silicon on Plant-Pathogen Interactions. Frontiers in plant science, 8, 701. Yongchao Liang, Wenhua Zhang, Qin Chen, Youliang Liu, Ruixing Ding, Effect of exogenous silicon (Si) on H+-ATPase activity, phospholipids and fluidity of plasma membrane in leaves of salt-stressed barley (Hordeum vulgare L.), Environmental and Experimental Botany, Volume 57, Issue 3, 2006, Pages 212-219.
Zellner, W., Tubaña, B., Rodrigues, F. and Datnoff, L., 2021. Silicon’s Role in Plant Stress Reduction and Why This Element Is Not Used Routinely for Managing Plant Health. Plant Disease, 105(8), pp.2033-2049.
Silica products not only increase plant growth rates and yield, but also protect plants from various stresses, making them a valuable addition to any horticulture operation. These products are highly effective against biotic stresses (bacteria, fungi, viruses, insects) and abiotic stresses (heat, drought, acidity, salinity).
One way or another, to confer these benefits all silica products must ultimately increase the MSA concentration around the roots or foliage. It’s important to note that traditional forms of silica (potassium silicate, for example) generally aren’t absorbed via foliar action. While there is evidence of prevention of powdery mildew, applying foliar potassium silicate with this method won’t produce the growth or yield benefits that foliar MSA confers. Potassium silicate must remain at a very high pH to maintain solubility.
This points to another major benefit of stabilized MSA solutions: they don’t contain additional minerals that need to be compensated for in your main fertilizer formulation. For example, using potassium silicate at 0.3 g/gal will add 22ppm of K along with the 20ppm of elemental Si, and this will require compensation. As mentioned, plants benefit greatly from MSA, however it is highly reactive and needs to be stabilized to ensure that its reaching the plant surfaces as monosilicic or disilicic acid. At higher pH levels, MSA disassociates into silicate ions, and at high concentrations, unstabilized MSA polymerizes creating larger molecules. Since only the smaller molecules of mono- and di- silicic acid can be absorbed by plants, this polymerization into oligomeric and polymeric silicic acid needs to be prevented.
The commercial availability of MSA products has been made possible with the development of processes that prevent the
polymerization of silicic acid, enhancing stability at a variety of concentrations, pH levels, and over longer durations.
One common method of stabilizing MSA solutions include acid stabilizations in combination with molybdenum, zinc, choline, or polyethylene glycol (PEG). These methods allow concentrations of up to 2.5% silicic acids, however these stabilized silica solutions must remain at a very low pH to prevent polymerization in concentrated form. Another method involves using organosilicon precursors, such as tetraethyl ortho-silicate. These products don’t contain water and are very concentrated, allowing up to 40% equivalent concentration of MSA after conversion. As precursors, they don’t actually contain MSA but their components break down into MSA once diluted in water. Unfortunately, they also produce other organic compounds such as ethanol (alcohol) in the solution, which can exert strong negative effects on root growth and plant development.
Among the various methods of stabilizing silica, polyol-stabilized MSA solutions stand out for their remarkable properties and effectiveness. One such example is Front Row Si, which contains 16% MSA (10% Silicon Dioxide). This product uses sugar alcohols, which form soluble 2/1 (sugar alcohol/silicic acid) silicate complexes with basic silicic acid. Silicate is very selective about the sugar alcohols it reacts with, but certain combinations result in readily soluble complexes at high concentrations. While potassium silicate solutions require very high pH levels to stay in solution and acid-stabilized MSA products require very low pH to prevent polymerization, the polyol stabilization process used in Front Row Si overcomes this challenge.
Front Row Si has significantly improved mixing properties compared to other silica products on the market; the mono- and di-silicic acid components are stabilized to be soluble at all pH levels, making them easier to use in a variety of applications and methods. Additionally, Front Row Si does not contribute any potassium or other minerals that would require adjustment of the overall nutrient recipe.
The low-molecular weight MSA in monoand di-silicic forms created by the polyol stabilization process in Front Row Si are easily available for plant absorption in contrast to the higher molecular weight Si polymers that are less effective for plant uptake. This superiority in terms of cost, stability, solubility, and availability for plant absorption makes polyol-stabilized MSA solutions like Front Row Si a valuable choice.
Much of the research literature reports the effective ppm ranges for elemental Si rather than a silica salt or of MSA. It may be useful to see how to calculate the elemental ppm of Si from MSA in a solution.
Let’s walk through the steps for deriving the percentage by weight of Si in MSA. MSA’s molecular composition is H4SiO4, or Si(OH)4, meaning it contains silicon, hydrogen, and oxygen.
To find the percentage of Si by weight, you need the molar masses of each of these elements:
• Silicon (Si): 28.085 g/mol
• Hydrogen (H): 1.008 g/mol
• Oxygen (O): 16.00 g/mol
• Calculate the total molar mass of MSA: Take the sum of the molar masses of all elements in the compound multiplied by their respective number of atoms:
• 1 Si atom: 1 × 28.085 g/mol
• 4 H atoms: 4 × 1.008 g/mol
• 4 O atoms: 4 × 16.00 g/mol
• Molar mass of MSA = (1 × 28.085) + (4 × 1.008) + (4 × 16.00) = 28.085 + 4.032 + 64.00 = 96.117 g/mol
• Calculate the percentage of Si by weight: Divide the molar mass of Si by the total molar mass of MSA and multiply by 100% to get the percentage:
• Percentage of Si by weight = (Molar mass of Si / Molar mass of orthosilicic acid) × 100% = (28.085 g/mol / 96.117 g/ mol) × 100% ≈ 29.20%
So, the percentage of Si by weight in MSA is approximately 29.20%.
Many product labels or labs report Si concentrations as SiO2 equivalents.
To determine the percentage of silicon (Si) by weight in silicon dioxide (SiO2), we first need to know the molar masses of silicon and oxygen:
• Molar mass of silicon (Si): 28.0855 g/mol
• Molar mass of oxygen (O): 16.00 g/mol
Silicon dioxide has one silicon atom and two oxygen atoms, so its molar mass can be calculated as: Molar mass of SiO2 = (1 x 28.0855 g/ mol) + (2 x 16.00 g/mol) = 28.0855 g/ mol + 32.00 g/mol = 60.0855 g/mol
Now we can calculate the percentage of silicon by weight in silicon dioxide:
Percentage of Si = (28.0855 g/mol / 60.0855 g/mol) x 100% ≈ 46.74%
Thus, the percentage of Si by weight in SiO2 is approximately 46.74%
Since 2003 a number of trials in various crops have been carried out to determine the effects of foliar application of Si. Most research uses solutions of 7-45 ppm Si, sprayed 3-4 times starting early in the crop life cycle. The excellent 2018 review paper by Laane and colleagues reports on these effects, summarized below:
• Five studies exploring the effects of on potato growth, yield, and infection rate showed increased disease resistance, yield improvements of up to 40%, and other growth enhancements.
• Four sprays of 30 ppm Si applied to two different onion cultivars grown in clay soil in the Netherlands resulted in yield increases of 9.9% and 10.8% respectively.
• In a Colombian study, four sprays at 30 ppm Si using two different spraying regimes led to increased papaya plant height (6.3% and 7.8%), stem diameter (7.3% and 8.2%), fruit weight (11.9% and 13.2%), superior fruit flavor.
• Three studies on rice demonstrated that MSA sprays led to various growth and yield improvements, including increased grain size and quantity, shorter crop cycles, and enhanced nutrient uptake, with yield increases up to 32%. Additionally, the studies found that MSA application reduced infection rates, such as a 70% reduction in one study, and allowed for decreased pesticide usage while maintaining high yields.
• A study on strawberries found that three sprays with 7 and 14 ppm Si significantly improved growth parameters, including root length, root mass weight, diameter of root neck, and leaf blade area, across all tested soil types.
• Two studies on grapes found that MSA sprays at various concentrations led to significant improvements in growth parameters, yield, and quality, with one study reporting a maximum yield increase of 39%. The treatments positively influenced factors such as nutrient uptake, total soluble solids, acidity, total sugar, and reduced the percentage of rotten berries, while another study observed increased berry length, diameter, bunch weight, and overall quality.
• A study on ten different finger millet varieties found that two sprays of 15 and 30 ppm Si significantly increased grain and straw yield, with the greatest increase at the 4 mL/L rate, and improved Si uptake by 54.6% over the control. Additionally, the MSA sprays reduced blast disease by 50.469.8% across the different genotypes.
• MSA sprays led to various improvements in sugarcane growth, yield, and quality in three studies. One study found a 26% yield increase with foliar MSA sprays, and the combination of soil and leaf application provided a 33% yield increase. Another study demonstrated that MSA sprays significantly decreased mite populations and leaf dryness.
• A study on seasonal ornamental plants found that three sprays with 15 and 22 ppm Si from MSA led to increased growth and quality. The number of lateral shoots, buds, and flowers or inflorescences increased in all ornamental plant varieties, with flower diameter also dependent on the concentration of the spray.
• MSA sprays improved growth, yield, and quality in white oat and wheat. In wheat, the sprays increased nutrient concentrations, shoot dry matter, and resulted in a 26.9%
The effects of foliar application of PEG-sSA on wheat grown in very saline soil (area of 3 ha) in Romania during 2014. Half of the plot was sprayed four times with AB Yellow® (=4 mL/L PEG-sSA plus B, Mo and Zn). The visual differences between the sprayed plants (taller plants) and the control (small plants) can be seen.
grain yield increase. MSA sprays also showed efficacy in alleviating drought stress, increasing relative water content, and improving growth and quality parameters.
• MSA sprays improved growth, yield, and quality in soybean, common bean, and peanut. Four sprays of 15 ppm Si from MSA increased seed yields by 14% for soybean, 15% for common bean, and 9.6% for peanuts. In soybean, three sprays were the most effective foliar application, increasing plant height, leaves, pod and seed yield, as well as protein and oil yield.
• MSA sprays improved growth, yield, quality, and infection rates in tomato plants. Three sprays of 30 ppm Si led to taller transplants with larger stem diameters and increased nutrient concentrations. MSA sprays of 15 and 30 ppm Si reduced powdery mildew disease by 26% and 56%, respectively, with the latter sprays being more effective than the standard fungicide.
• A study on maize found that MSA sprays at concentrations of 7, 15, and 22 ppm Si applied at 20-day intervals, along with the application of silicon granules, improved growth and yield parameters in both sandy loam and clay loam soils. The highest yield resulted from the combination of the foliar MSA application at 22 ppm Si with the soil application of silicon granules.
• A study on mango trees compared the efficacy of four 4 30 ppm Si from MSA sprays applied at three-week intervals with other silicon treatments and a control. All soil and foliar silicon applications enhanced growth and yield, but the MSA foliar sprays were more effective in terms of yield increase,
total soluble solids (TSS), and shelf life. The shelf life of the fruits from MSA treated trees increased by five days compared to other silicon-containing product applications.
• A study on mandarin plants evaluated the efficacy of one, two, and three MSA sprays at concentrations of 7, 15, and 30 ppm Si applied at 30-day intervals during the pea stage and ripening stages. Sprays with 15 ppm at the pea stage enhanced nutrient status, increased fruit size by 25%, and improved juice volume during the ripening stage, particularly with 30 ppm sprays. The treatments increased biogenic silicon layers in the rind, sugar content in the juice, nutrient ionic status, and fruit shelf life.
Stabilized silica products are a game changer in horticulture, offering numerous benefits to plant growth and protection. By understanding the importance of stabilizing monosilicic acid and the methods used to achieve this, growers can make informed decisions when selecting silica products for their horticultural operations. With the right stabilized silica product, such as the polyolstabilized Front Row Si, growers can enjoy higher growth rates, yields, and improved plant health.
Getting the benefits of MSA with Front Row Si is easy: In practice, 3 - 5 foliar applications with 1-2 ml/gal over the first 5 weeks of a plants life ensures the crop is receiving the benefits on growth rate, yield, disease resistance, and quality.
Laane H. M. (2018). The Effects of Foliar Sprays with Different Silicon Compounds Plants (Basel, Switzerland), 7(2), 45. https://doi.org/10.3390/plants7020045
Front Row pH Up is a powdered, dry soluble water conditioner intended to control alkalinity.
Front Row pH Up uses potassium carbonate to buffer fertilizer acidity, thus increasing pH.
Front Row pH Up is designed for use when cultivators are using low to zero alkalinity source water and need to raise the pH of their solution. Consult a hydrology expert or representative for appropriate usage and dosage for your system.
Use rate is based on solution conductivity and recipe. Make test solutions of all nutrient recipes and conductivities. When targeting a specific pH value, avoid using an acid and base in the same solution.
Use minimum amount of Front Row pH Up to achieve desired pH. Allow variance of ±0.1 pH. Check pH at the emitter or as close to the crop zone as possible.
Carbonates take time to react. For automated systems, reading pH too close to Front Row pH Up injection or batch tank may lead to incorrect usage.
Triologic is a powerful microbial root inoculant designed to boost plant growth by promoting mycorrhizal colonization. It contains high concentrations of rhizobacteria that facilitate the uptake of essential minerals, enhance fertility, and improve yield. These beneficial bacteria help plants utilize nutrients more efficiently and resist pests and diseases, especially when applied early in development. By fixing nitrogen and cycling essential nutrients like phosphorus and potassium, Triologic supports robust root health and aids mycorrhizae formation.
Triologic’s highly concentrated bacteria work within the substrate to increase yield, improve fertility, and enhance resistance to pests and disease. Applying these bacteria to the root zone early in a plant’s development can reduce the effects of abiotic stresses while making more efficient use of fertilizers.
Plant growth-promoting rhizobacteria colonies in the substrate fix nitrogen and cycle essential nutrients, including phosphorus and potassium, into forms easily available to the plant roots. Additionally, these beneficial bacteria help supply nutrition to the mycorrhizae that protect the plant roots, aiding the formation of beneficial fungal colonies.
1 ml/Gal (0.26 ml/L), 1x per week. See Page 36-37 for more usage recommendations. Best used as a hand water drench.
With TRIOLOGIC, you can expect healthier, more resilient plants and higher yields.
BY DR. TRACY LETAIN
Mycorrhizae are symbiotic fungi that colonize plant roots, offering several advantages for plants, including:
• Extending the root system for better access to nutrients and water
• Forming a protective barrier against root pathogens
• Mitigating plant stress response through multiple mechanisms. Given these advantages, it’s clear why many growers consider mycorrhizal products a key part of their growing system.
In this context, why recommend Triologic? Isn’t it a bacterial root inoculant that contains no mycorrhizae? The answer is straightforward: If you want to maximize plant nutrient uptake and mycorrhizal root colonization, incorporating Triologic into your grow program is essential.
For mycorrhizae to effectively colonize plant roots, the surrounding root environment, called the rhizosphere, must support this colonization process. Triologic’s specialized group of bacteria, known as Mycorrhization Helper Bacteria (MHB), are central to this process.
The rhizosphere - area surrounding root and root hairs - supports mycorrhization when inoculated with Triologic The rhizosphere (area surrounding root and root hairs), supports mycorrhization when inoculated with Triologic.
MHB are not only essential for initiating mycorrhizal colonization but also play a vital role in maintaining the mycorrhizal-plant root relationship. A less successful colonization could lead to rapid mycorrhizae die-off, leaving the roots unprotected.
The MHB in Triologic facilitate mycorrhizae-root colonization through various mechanisms:
In sterile soils, spore germination is much lower than in soils inoculated with MHB. MHB produce specific metabolites that are believed to act as signals for germination.
MHB play a key role by forming a rhizosphere environment that can support mycorrhizae growth and development on plant roots. MHB do this by providing sufficient nutrients that mycorrhizae need to colonize plant roots, and by breaking down and removing harmful material – such as antifungal compounds – that actively prevents mycorrhizal growth.
Mycorrhizae cannot randomly colonize any part of the plant root that they encounter. Instead, they preferentially grow on “short” or “fine” root hairs – newer root growth which has a softer cell wall that the mycorrhizae can penetrate. The ability of MHB to help promote new root growth is well-documented. MHB can also
“soften” older roots using a variety of enzymes, which can allow for mycorrhizal colonization on older root tissue.
The root colonization process is complex, with both fungi and plants producing a variety of chemical signals such as phytohormones, organic acids, sugars and adhesions during the initiation of colonization. MHB also produce these signaling compounds, and can alter existing compounds that may interfere with the colonization process.
To practically apply these insights, consider the following strategies for using Triologic alongside mycorrhizae:
Initiate co-inoculation with mycorrhizae and Triologic via clone feeds as soon as the first roots emerge from the clone plug.
This early application ensures the plant’s root system benefits from both agents from the start.
Triologic can be applied at a rate of 1-2 ml per gallon of water, optimizing colonization without overwhelming the plant’s environment.
At the time of planting the clone, apply Triologic and mycorrhizae at 2ml per gallon, with granular mycorrhizae directly to the planting hole, supporting root growth in various mediums, including soil, rockwool, and coco. One test we use to ensure full activity involves inoculating Triologic into substrate containing seeds, and charting the growth of mycorrhizae compared to uninoculated substrate. With Triologic, we see rapid mycorrhizal growth within 72 hours which persists to the end of the two-week test, while with uninoculated substrate we find spotty growth which rapidly dies back. See photos below.
Front Row Ag’s protocols allow for a flexible, synganic approach that integrates the best synthetic nutrients with targeted biologicals to ensure high yields, healthy plants, and top quality.
The practical application of Triologic and mycorrhizae as detailed here exemplifies our commitment to enhancing plant health through innovative, synergistic approaches, ensuring growers can leverage the full benefits of mycorrhizal colonization.
Triologic is a plant root inoculant formulated with a potent blend of plant growth promoting rhizobacteria. These beneficial microorganisms colonize plant roots, aiding in nutrient acquisition and stress response. Here’s what Triologic does for your plants:
Enhanced Nutrient Absorption: The healthy rhizosphere created by Triologic promotes better nutrient uptake during crucial growth stages, resulting in increased yields, improved plant health, and enhanced crop quality and uniformity.
Comprehensive Growth Support: Triologic supports plant development throughout the entire growth cycle, from clone to harvest. It ensures availability of a full range of nutrients, including NPK and trace elements, maximizing cannabinoid levels and contributing to improved plant health.
Stress Management: By reinforcing the plant’s natural defenses and fostering nutrient availability, Triologic helps plants cope with various stressors, such as disease, nutrient imbalances, and temperature extremes. It also aids in preventing stress-related injuries.
31% Increased THC Levels in Cannabis
A 31% increase in THC content in Triologic-treated cannabis compared to the control group. The application of Triologic contributes to elevated THC levels, benefiting cannabis growers.
55% Table Grapes Yield Enhancement
Triologic treatment lead to a 55% higher yield of exportquality table grapes compared to the control group, resulting in increased revenue per acre and improved fruit quality.
6% Almond Yield Improvement
5-acre almond trees treated with Triologic experience a 6.19% higher almond meat yield, leading to increased revenue and positive Return on Investment (ROI).
23% Higher Strawberry Yield + Improved Quality
Triologic-treated strawberries show a 23% higher overall yield and improved fruit quality.
Brix levels and moisture content also indicate favorable outcomes.
Triologic unlocks plant potential through a dynamic partnership between roots and beneficial rhizobacteria.
Within the rhizosphere, (the few millimeters of soil surrounding plant roots,) this partnership facilitates growth, resilience, and nutrient absorption.
Plants ‘feed’ Triologic microbes organic acids and oxygen, putting them in close proximity to the plant root. In return all nutrients the bacteria make available for themselves are also available to this plant root.
By nurturing mycorrhizal colonization, Triologic optimizes water and phosphate uptake, bolsters defense against pathogens, and ensures nutrient availability.
When and how do I use Triologic in my growing schedule?
Apply Triologic when starting fertilization or early in the growth cycle. Even if the season has begun, applying Triologic can still benefit plants.
Is Triologic compatible with other treatments?
Triologic works well with most fertilizers, herbicides, and pesticides. Apply it before or after herbicide/pesticide use for optimal results.
Clean your lines, emitters, & equipment without harming your plants or beneficial microbes downstream.
BioFlo is an all-natural bio-enzyme solution that uses biological and enzymatic action to clear biofilm. Contains biologically active ingredients without any harmful chemicals and is 100% safe on plants, animals and rootzone.
• BioFlo restores irrigation systems to full capacity by clearing clogged lines and emitters.
• Unlike chemical irrigation line treatments, BioFlo does not harm plants or soil and is safe to use throughout the growing process.
• Compatible with injectors, reservoirs, and tank application systems.
• BioFlo can be used to treat existing clogs and to prevent future clogs.
• BioFlo cleans out hydroponic and nutrient water reservoir accumulations.
Biofilm clogs form rapidly in cool, moist environments – exactly the environments found in irrigation lines. Microbes come from common additives such as fertilizers. Fertilizer nutrients act as food for biofilm microbe growth.
Once a biofilm starts to grow, it “sheds” microbes, which then make even more new biofilms. Biofilms are extremely difficult to remove, as chemical treatments can’t penetrate past the biofilm surface.
In order to clear biofilm irrigation line clogs, your line cleaner must have the ability to rapidly break down the macromolecules that make up the biofilms.
Standard irrigation line clog treatments use chemicals that only treat the surface of irrigation line clogs, and damage plants and soil. BioFlo is comprised of microbes that actively “digest” and break down biofilm
clogs entirely, not just clog surfaces. BioFlo microbes are 100% natural and can be used throughout the growing season. BioFlo works on irrigation lines, emitters, reservoirs - any surfaces with biofilm and scale accumulations.
Use the PVC Volume Chart to calculate your irrigation line volume of water.
Turning dry soluble fertilizer into concentrated liquid fertilizer.
Stock Concentrates are highly concentrated solutions prepared in advance. They can be added as a DTR solution, or injected using dosing or fertigation equipment. This method allows for precise control and automation, less mixing frequencies, and lasts longer than DTR due to higher salinity.
Adding fertilizer part-by-part into liquid to create ready-to-feed solution.
In DTR, fertilizer is directly added to a batch tank or reservoir following the prescribed order and mixing between each addition. This solution is fed directly to plants.
DTR a common practice for facilities that do not have access to dosing or fertigation equipment. Fertilizer can be added directly to water holding reservoirs of any size/capacity.
With either method, the order in which you mix the products matters.
By following the prescribed mixing order for Front Row Ag’s 3-part fertilizer system, you ensure optimal solubility, effective pH management, efficient micronutrient delivery, balanced nutrient ratios, and minimized risk of precipitation.
When using Front Row Ag’s 3-part “A, B, and Bloom” dry-soluble fertilizer system, following the correct mixing order is important for creating an effective and stable Ready-To-Use (RTU) fertilizer solution. Here’s why the mixing order matters:
Part A goes in first because it contributes the most weight and electrical conductivity (EC). Starting with the highest weight product that has the least salinity makes it easier to dissolve. As we progress through Part B and Bloom, the EC and weight contributions gradually decrease while acidity of the parts increases. This helps maintain solubility as new components are added.
Non-organic additives that might form precipitates are added early in the process. This ensures they mix with the lowest EC water and are at their most dilute when encountering the main fertilizers, reducing the risk of precipitation.
Micronutrients are included with Calcium Nitrate in Part A.
This strategy serves multiple purposes:
1. It provides a high concentration and quality ratio of micronutrients, which are crucial for plant performance.
2. By combining micronutrients with Calcium Nitrate, we ensure that an optimal and precise quantity of micronutrients will be applied automatically with the macronutrients.
3. This combination makes it easier to validate the presence of micronutrients, as independent micronutrient packages can be difficult to verify due to their low EC.
While Calcium is important, it’s easy for a formulation to have too much. By including Potassium Nitrate in the mix, we maintain the necessary Nitrogen values while reducing Calcium to ideal levels.
More acidic components are added later in the process to aid in solubility. Additionally, we recommend the principle of “pH down first, pH up last” to maintain optimal solubility throughout the mixing process. Most minerals have higher solubility at lower pH. By the time you reach the Bloom part, which is more acidic, the other components are already well-dissolved.
On each Front Row Ag Feed Chart, you’ll see that there are several “Recipes” that are used strategically at different stages: Stretch, Stack, Swell and Ripen. These recipes represent different ratios of the input fertilizers, that create different elemental ratios of plant nutrients. This allows cultivators to deliver the general ratios of minerals appropriate for each phase of plant development.
Clones and Mother Plants
Most nitrogen forward recipe favoring calcium for biomass growth.
Weeks 1 & 2 of Flower
Introduces Bloom, first increases of P&K, giving cues to initiate flower.
Weeks 3, 4, 5 of Flower
Most balanced flower recipe. Heighten levels of P, K plus Mg and S.
Prefer to keep it simple?
Weeks 6, 7, 8 of Flower
Highest P&K relative to equal parts A & B for promoting density and flower swell
Final 2 Weeks of Flower
Decreases N for finishing cues promoting optimal aroma, yield, color, and cure.
While using all the recipes can be quite beneficial, it’s important to note that most cultivars don’t need to have the recipe changed across the growth phases and perform optimally running the “Stack” recipe for the entire flowering cycle.
Standard or High Strength
Standard strength charts are designed for general use, high strength feed charts are tailored for more intensive agricultural practices where plants require higher concentrations of nutrients, often due to specific growth conditions, higher lighting intensity, and advanced cultivation techniques.
Feed Charts show the usage rate for each part in “grams per gallon” or “grams per liter” for dry powder and “mL per gallon” or “mL per liter” for liquids. When mixing tanks, multiply the usage rate by the total number of gallons or liters being mixed to determine how much fertilizer to use.
Each input row on the feed chart contains the usage rate e.g. g/gal or ml/gal as well as the EC contributed from that part. This indicates the EC in the batch tank that is directly contributed from that part alone. Ex. In the High Strength Chart Veg Recipe, Part A is contributing 2.0 EC, Part B is contributing 1.0 EC. This can be used as a good way to verify accurate additions of fertilizer.
We also provide the Contributed EC per gram per gallon. We rounded to the nearest tenth on the chart in order to match most EC meter displays.
3-2-2 refers to the number of 25 lb. bags of each product that are added to individual stock concentrate drums:
• Part A: three 25 lb. bags per 50 gal. water
• Part B: two 25 lb. bags per 50 gal. water
• Bloom: two 25 lb. bags per 50 gal. water
Mixing with the 3-2-2 method allows each fertilizer part to be injected equally if using fertigation.
It’s use of whole bags to create equal volumes of stock concentrates which are used at the same rate makes it the perfect match for operations seeking consistency and simplification. Works great for facilities running fertigation.
1. Start with clean stock tanks marked at target volume.
2. Add RO water to 50% of target volume; begin agitating the tank.
3. Add fertilizer over 5 minutes, while continuing to agitate the tank.
4. Add RO water to target volume; mix for 10 more minutes.
5. Validate and adjust stock tank as necessary.
• Remove exactly 250 ml of well-mixed stock concentrate and add to 5 gallons of RO water.
• Mix and check EC against validation chart. Adjust stock concentrate strength as necessary to match validation EC.
• Repeat for each stock concentrate, validating against EC.
3-2-2 HIGH STRENGTH
* “Stack” recipe can be used from start to finish
Notes
Si usage rate depends on feed EC, please refer to Si vs EC Table.
Recommended to be used 1x per week.
Use as necessar y to remove biofilm from irrigation lines.
Usage rate shown is for 0.03-0.3% injector at 90g/gal stock rate. Contact us for alternate usage rates.
1. Fill reservoir to target volume; begin agitation.
2. Add Front Row Si*; agitate 3-5 minutes.
3. Add Part A; agitate 3-5 minutes.
4. Add Part B; agitate 3-5 minutes. If using PhosZyme, add & agitate 3-5 minutes.
5. Add Bloom; agitate 3-5 minutes.
6. Add Front Row pH Up in 0.05 g/gal steps until target pH is achieved.
* Only use Front Row Si if reservoir will be fully used within 48 hours.
• When using Front Row Si, reservoirs should be fully used within 48 hours.
• Without Front Row Si, reservoirs should be used within 5-7 days.
• Avoid mixing strong oxidizers, especially peroxides into reservoirs. If running a sterile reservoir, use calcium hypochlorite at 1-3g / 100 gallons. Review our Cleaning Best Practices on page 58. All feed charts are based on using RO water. If your starting water has any EC, be sure to account for that in the total EC.
7. Validate ph/EC and adjust as necessary. ADD FRONT ROW while agitating. Wait 3-5 minutes between each component addition.
Continue agitation, adjust pH and check solution after 510 minutes
* “Stack” recipe can be used from start to finish of the flower cycle.
These feed charts are not a prescription, but an example of the general ranges and relationship of EC and recipes that can be used. Each facility and cultivation methodology will require customization of EC values. See the “EC Considerations” section on page 60.
What is the proper injection order for Front Row Ag?
• Front Row pH Up (if necessary)
• Front Row Si
• Part A
• Part B
• Bloom
• Front Row pH Down (if necessary)
Note: pH Up can be added first if adjustments to raise pH are needed prior to other inputs. If pH Down is necessary, it should be added after all other components. See pg. 72 for fertigation setup examples.
What EC should I feed at?
Given the variance in facility infrastructure, cultivation methods, and cultivars, it’s impossible to give a specific EC prescription that applies to all scenarios. Most facilities feed at 2.0-3.0 EC with Front Row Ag, and our “Standard” and “High Strength”
Feed Charts reflect effective feeding strategies in this range. The following table shows some considerations that affect EC choice:
EC CONSIDERATIONS
Smaller pots
Larger pots
Frequent irrigation Infrequent irrigation
Consistent runoff Less runoff
Substrate monitoring No substrate monitoring
Higher PPFD
Lower PPFD
Heavy feeding strains Lower feeding strains
Higher CO2
Tight environmental control
Why feed at higher EC early in the cycle?
Plant nutrition requirements are highest during the stages at which plants are growing most quickly, veg and during the first three weeks of flower. At this stage the crop will have a smaller root mass and drybacks will take much longer. As the plant finishes stretch, mineral requirements will be reduced and substrate EC should also be reduced via lower feed EC and/or increased runoff.
How much does each FRA part raise the EC per gram per gallon?
Lower CO2
Less environmental control
Do I need to use Cal Mag with Front Row Ag?
No, our formula contains ideal ratios of calcium and magnesium based on years of testing and plant tissue analysis. If deficiencies are observed, raise EC by increasing all parts equally to maintain ideal mineral ratios.
Do I need a bloom booster with Front Row Ag?
No. you will not need an additional bloom booster - Front Row Ag Bloom contains all the required micronutrients with ideal quantities of phosphorus and potassium to maximize density, yield, and quality.
How is Front Row Ag different from other mineral fertilizers?
Front Row delivers more micronutrients and magnesium which are some of the largest contributors to quality, density, yield, and aroma. We also have the added technology of the surfactants and proprietary, solubility agent.
What is the easiest way to use Front Row Ag?
Using our 3-2-2 stock concentrate mixing method with venturi injectors or with batch tanks. This allows use of whole 25lb bags in 50 gal stock barrels that can be injected at equal injection ratios.
For Direct to Reservoir mixing what is the required mixing time between adding each part?
• 3-5 minutes between Si, A, B, Bloom.
• 5-15 minutes between additions of Front Row pH Up, to allow for full pH adjustment effect.
How do I spray Front Row Si?
0.5-2 ml/gal, sprayed weekly up to day 21 of flower.
Can Front Row Si be injected?
Yes, at 0.1 - 0.5 ml/gal. There are two important considerations with injecting Si:
• Higher feed EC requires lower usage rate of Si.
• If the injection system is filling batch tanks, they must be fully used within 48 hours.
How long can Front Row Ag be stored for?
Solutions should be stored in opaque containers in climate controlled areas.
$0.08-$0.10 per gallon with additional discounts available based on volume.
How often should I clean my batch tanks?
As needed, depending on each facility’s inputs and water quality. Generally every 10-14 days is recommended, although facilities running a sterile irrigation system will require cleaning less frequently and facilities running microbial additives may require more frequent cleaning.
How often should I clean my fertigation skid?
1-2 times per month is an ideal cleaning frequency to ensure cleanliness and consistent functioning of fertigation equipment.
How often should my irrigation components be replaced?
Generally everything downstream from hard plumbing (primarily poly line and drip emitters) should be replaced annually.
How do I prevent growths and contamination?
Run a sterile system by using the correct amount of calcium hypochlorite. Use cone bottom tanks and design systems so 100% of the water can be evacuated. Keep cleaning logs and SOPs.
What causes color change or cloudiness of fertilizer solution in a reservoir?
Turbidity or “haziness” of the feed solution can be caused primarily by bacteria or mold growths, swings in pH above 6.3, increases in water temperature, and/or oxidizing chemicals commonly used to clean, forming suspended particles and changing the solution color. While this does not cause any functional problems with the fertilizer, it can be an aesthetic or cleaning issue.
Turbidity can be avoided by following a few key practices in water quality and sanitation. Most often it is caused bacteria or mold growths, swings in pH above 6.3, increases in water temperature, and/or oxidizing chemicals commonly used to clean, especially hydrogen peroxide compounds, reacting with the high concentration of micronutrients in Front Row Ag.
Turbidity can be avoided or minimized with proper system design, controlled monitoring of pH and temperature, maintaining a sterile system, and by removing oxidizers from the feed solution and triplerinsing tanks prior to cleaning with these solutions.
Why does Front Row Ag improve quality, aroma, and yield?
Our formula’s high quality soluble minerals and full spectrum of micronutrients has been engineered specifically for the plant’s needs.
Do Front Row Ag users test for heavy metals?
Yes, we have hundreds of customers in markets with stringent heavy metal limits that use Front Row Ag to ensure finished products have low levels of heavy metals.
What’s the best way to contact Front Row Ag if I have a question?
Commercial Account Holders can contact their Rep directly. Otherwise we can be reached by phone email or DM.
R.O. Water Parts List
HYKSTART-STD x 1
D14MZ2VFBPHY x 3
D14MZ2AFBPHY x 1
HYKMC34 x 4
+MC34-SHADE x 4
WHA34-SS-KIT x 1
Optional
HYKMON x 1
Add 1 Doser+Mixer Set Each for Si and/or CalHypo:
D14MZ2VFBPHY
HYKMC34 +MC34-SHADE
City Water Parts List
HYKSTART-STD x 1
D14MZ2VFBPHY x 4
HYKMC34 x 4
+MC34-SHADE x 4
WHA34-SS-KIT x 1
Optional
HYKMON x 1
Add Doser+Mixer Set Each for Si and/or CalHypo:
D14MZ2VFBPHY
HYKMC34 +MC34-SHADE
There are two options for start kits, depending on whether the water pressure is set prior to coming into the panel or needs to be regulated by the panel itself.
There are two seal options for pH adjustment dosers, for either acidic or basic solutions.
Use Aflas (AF) seals for pH up and Viton (VF) seals for pH down. *D14MZ2AFBPHY is a special-order item.
When pH increase is required, that doser should be *last in the injection sequence.*
When pH lowering is required, that doser is best placed *first in the injection sequence.*
All Mixing Chambers should have a light protection sleeve part MC34-SHADE. If using Calcium Hypochlorite for water sanitation, inject first in sequence using D14MZ2.
Why HYKMON is optional: We recommend monitoring the solution in the batch tank and at the dripper, NOT at the exit of the panel which may give false pH readings while the chemical reaction is still taking effect.
Need A Custom Fertigation Setup? We Can Help
Front Row Ag works with every commercial fertigation system. Contact your commercial rep for help with other systems and layouts.
CONTINUE YOUR EDUCATIONAL JOURNEY
In March 2024, Front Row Ag opened an online school offering a free Technician certification course.
The Front Row Ag Certified Technician e-course is designed to provide comprehensive knowledge and practical skills for aspiring hydroponic fertilizer technicians. Professionals interested in learning about cutting-edge cultivation knowledge and techniques, this is for you. Scan the QR code on the next page to join today!
• Accurate measurements & proper agitation
Stock Concentrates
• Preparing concentrated solutions & validation
Fertigation System Considerations
• Different fertigation systems, compatibility, & best practices
• Injection order & specific needs for systems
Runoff Collection & Analysis
Cleaning & Maintenance
• Procedures for regular & deep cleaning of Irrigation Systems
Sensors
• Troubleshooting common issues in fertigation systems
• Calibration & maintenance of pH and EC sensors to ensure accurate readings