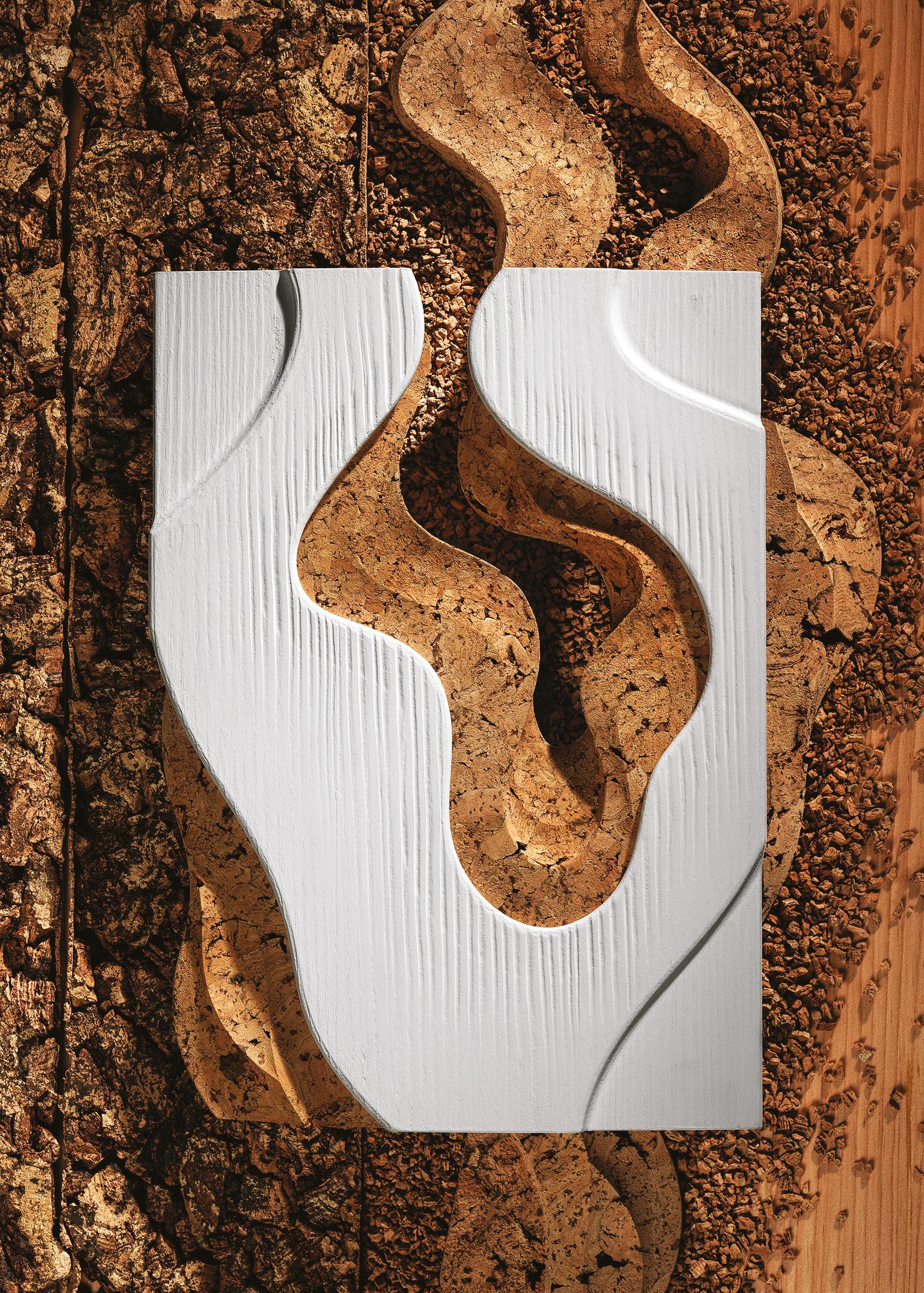
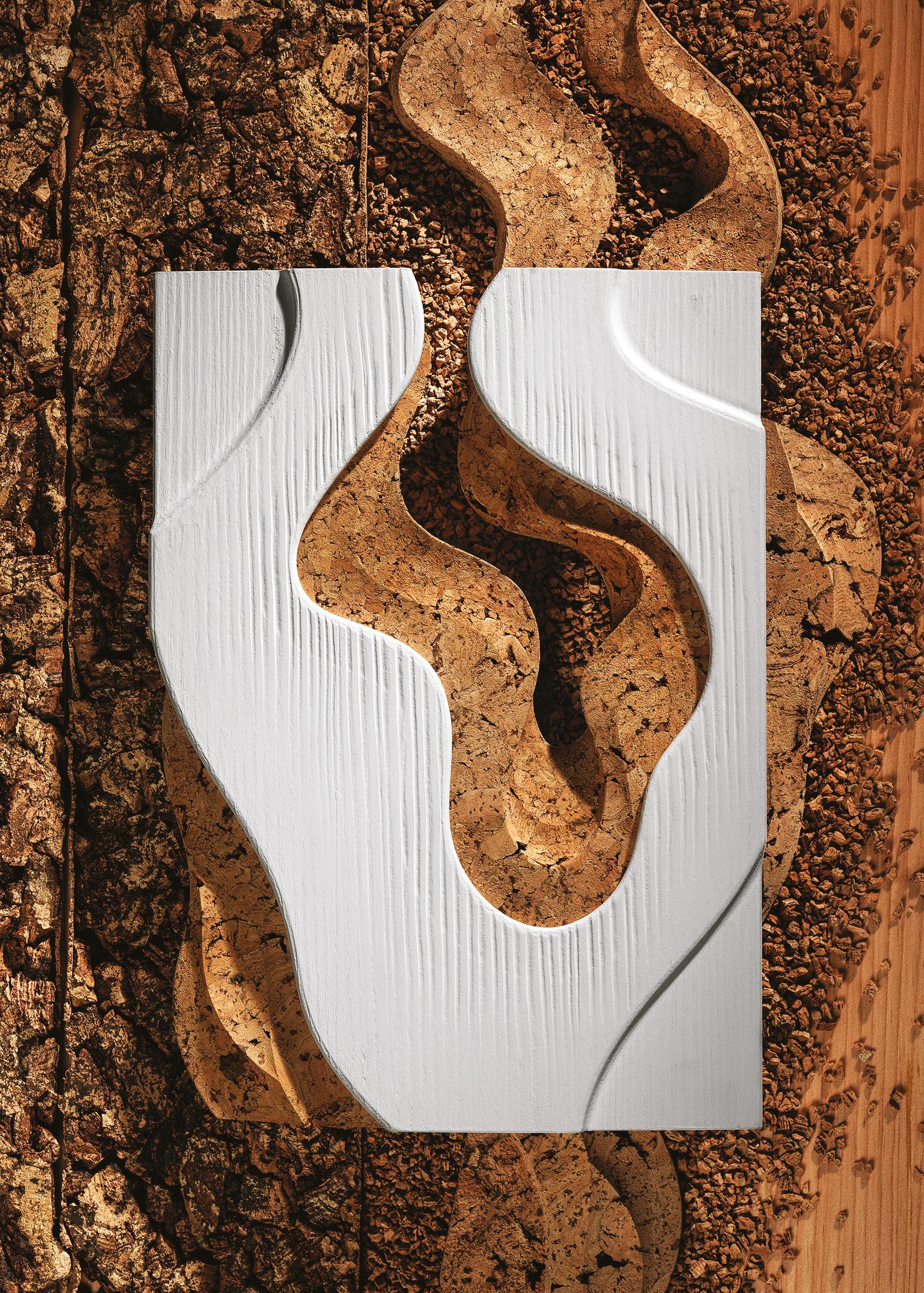
Sustainability
&
Flow by Silverlining
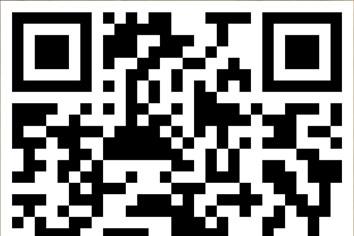
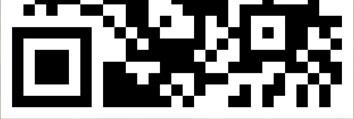
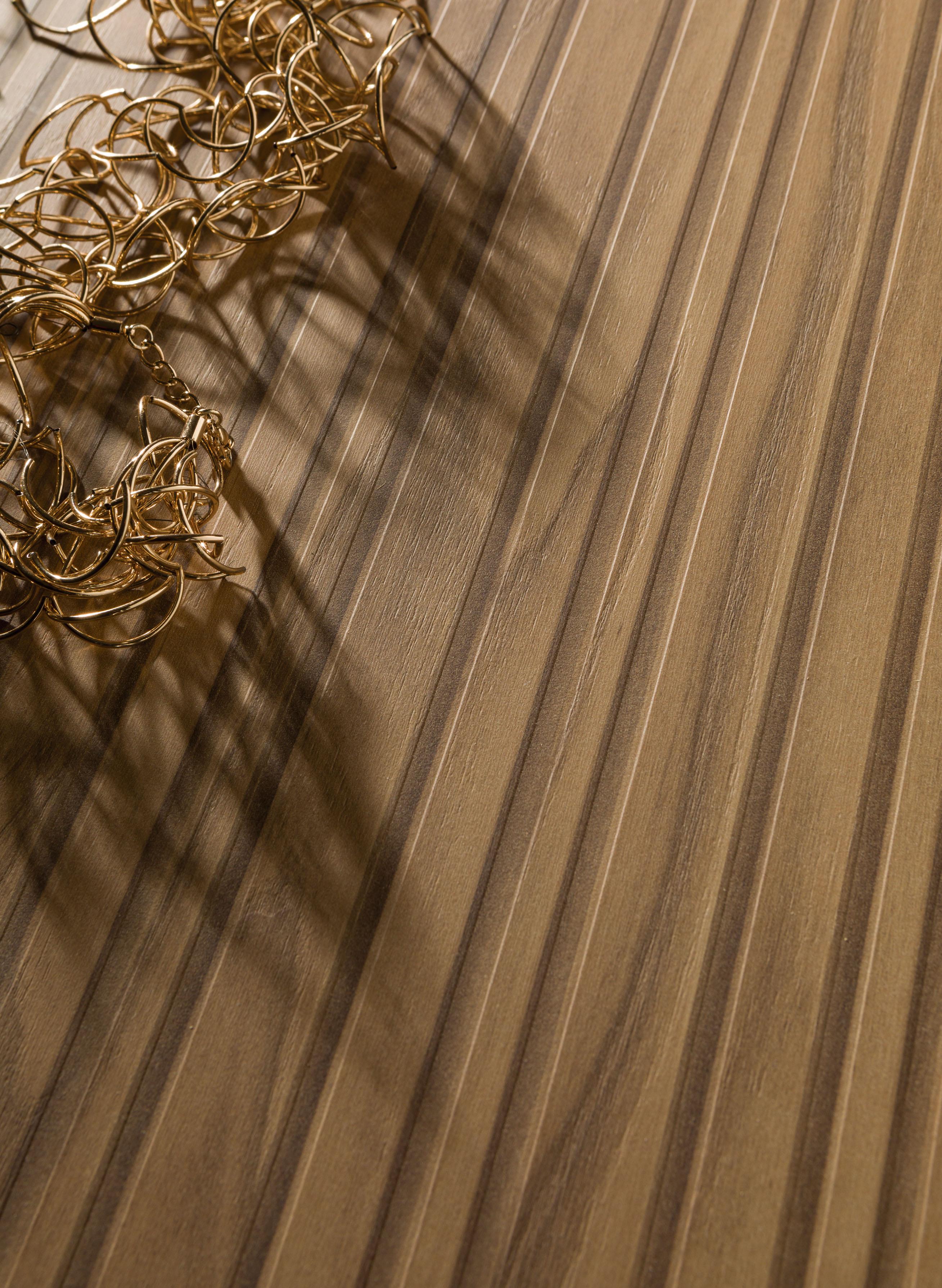
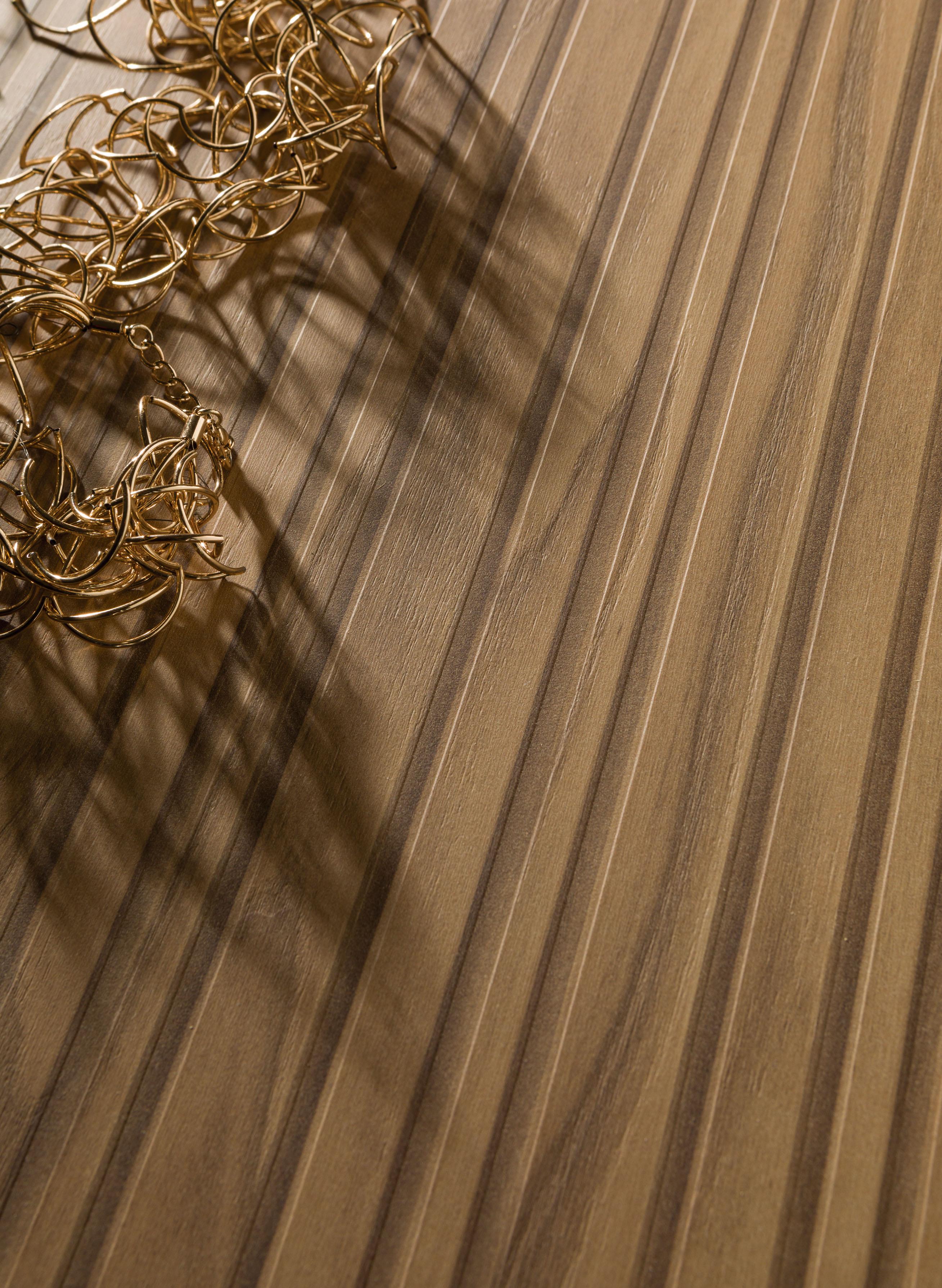
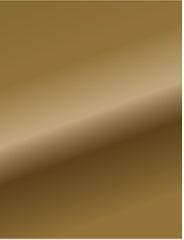
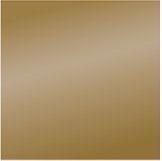
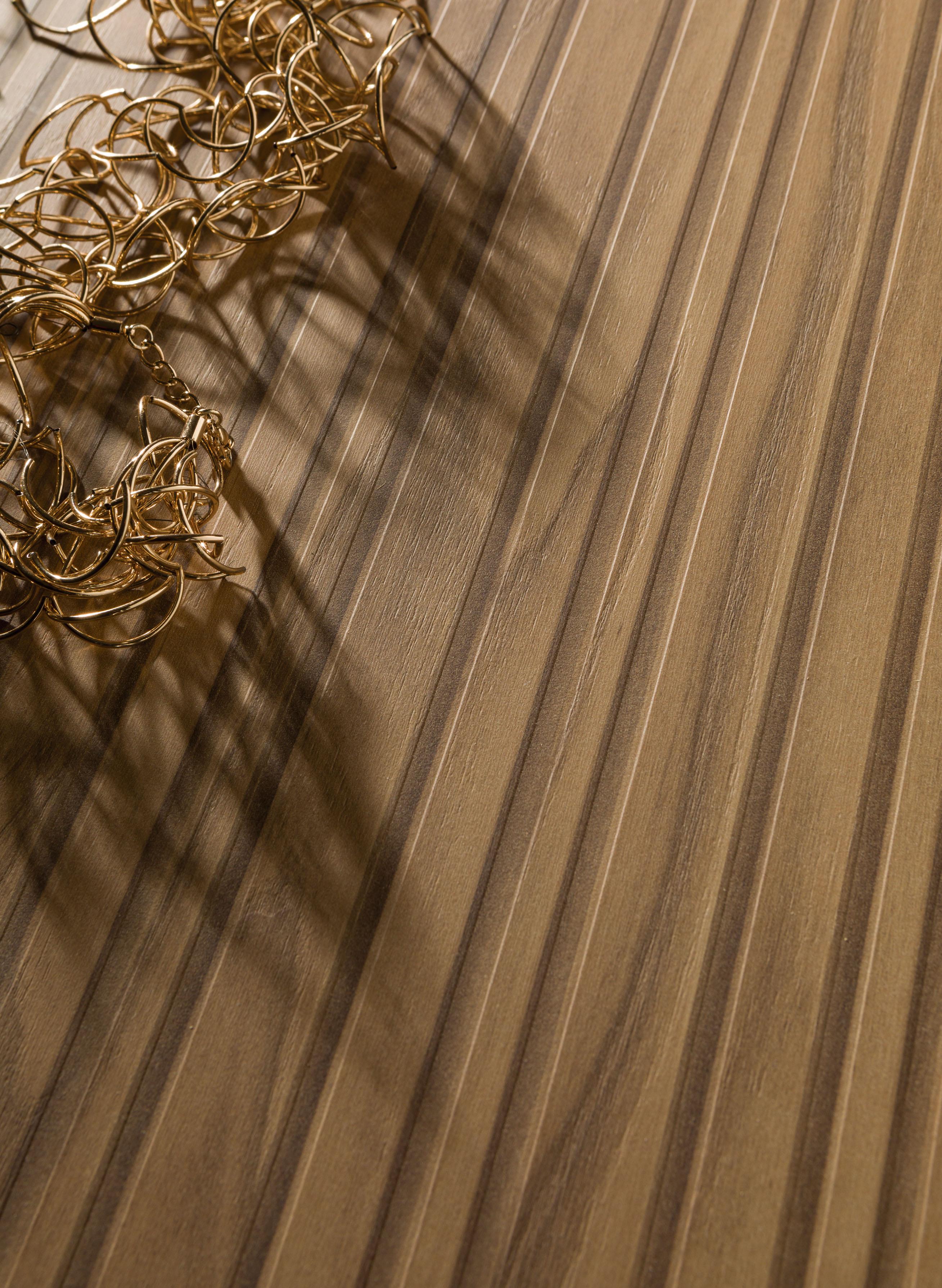
© Media66 Ltd 2024
ISSN 2396-9024
www.furnitureproduction.net
EDITORIAL DIRECTOR
John Legg
Tel: 01424 834973
john@media66.net
EDITOR
Gemma Lochhead gemma@media66.net
ADVERTISING MANAGER
Lisa Williams
Tel: 01424 834829 lisa@media66.net
MEDIA SALES EXECUTIVE
Jodie Griffin
Tel: 01424 834567 jodie@media66.net
PRODUCTION
James Ash studio@media66.net
DIGITAL CONTENT
Nyall McCurrach digital@media66.net
COPY ADMINISTRATION & DATA
Steve Merrick production@media66.net
REPRO, PRINT & DISTRIBUTION Stephens & George ACCOUNTS
Wendy Williams accounts@media66.net
SUBSCRIPTIONS: UK-free with sign up Europe-£85 / RoW-£95 lisa@media66.net
DISCLAIMER: All material submitted for inclusion in Furniture Production is done so entirely at the contributor’s own risk. No responsibility is accepted for the safe-keeping of contributors’ materials. Whilst all attempts are made to ensure accurate reproduction, Furniture Production accepts no responsibility for variations. Artwork undertaken by our studio remains the copyright of Media66 and may not be reproduced or stored without prior permission. Some articles in Furniture Production have been submitted by companies and organisations. Monies may have been accepted in some instances to offset production costs. All rights reserved. In respect of artwork originated free of charge as part of a booking, clients should know that excessive work (more than one set of corrections, known as ‘authors corrections’) is chargeable at £55 per hour. DATA PROTECTION “OPT OUT”
STATEMENT: Readership data held by Media66 may be shared with any member of the Media66 and associated companies for the purposes of customer information, direct marketing or publication. Data may also be made available to external parties on a list rental/lease basis for the purposes of direct marketing. If you do not wish data to be made available to external parties for list rental or lease please write to: Data Protection Co-ordinator, Media 66 Ltd, 36 Stirling Road, Castleham Business Centre East, St Leonards-on-Sea, East Sussex TN38 9NP.
SUBSCRIPTIONS: Refunds on cancelled subscriptions will only be provided at the publisher’s discretion, unless specifically guaranteed within the terms of the offer.
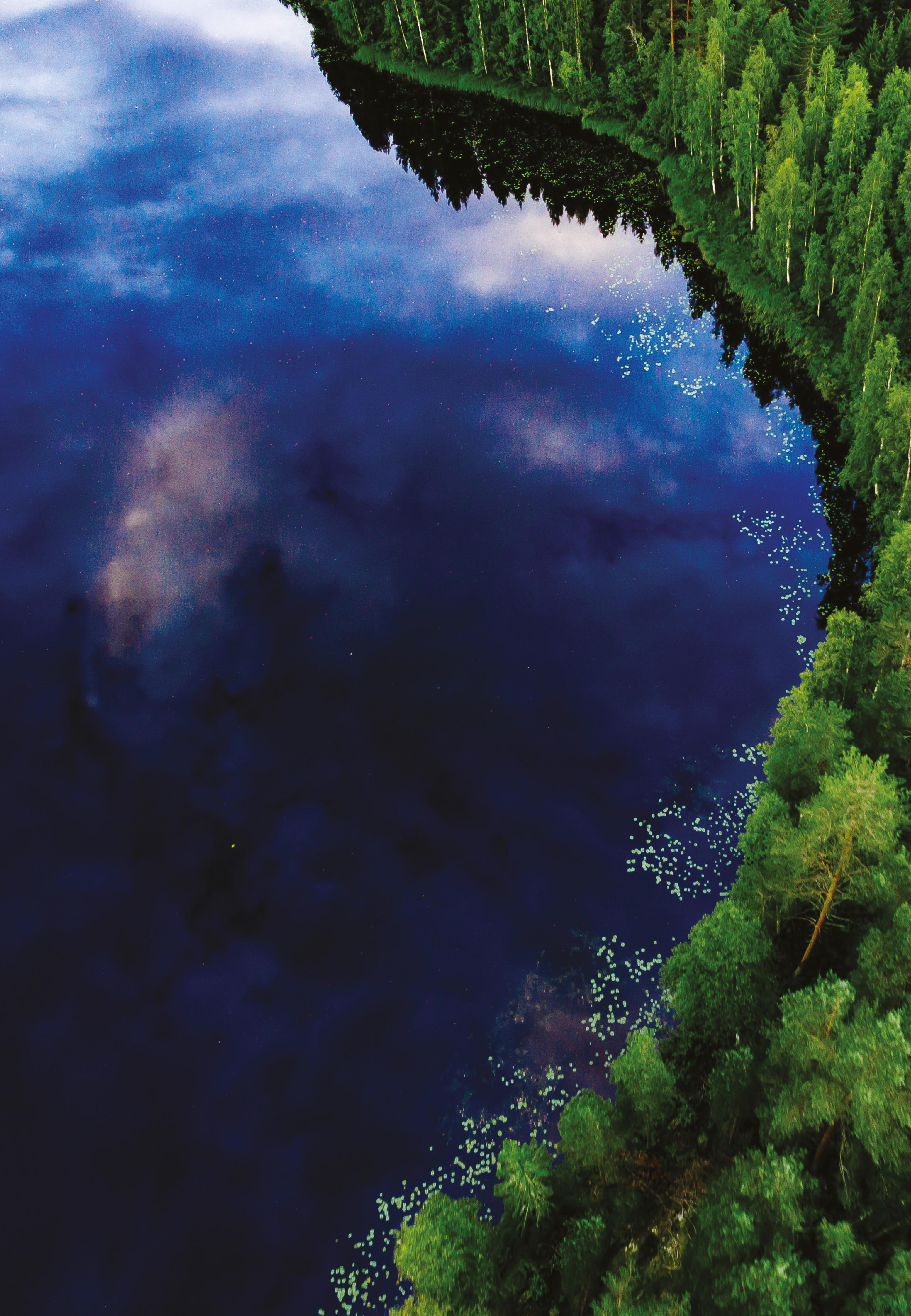
WELCOME
There are very few aspects of our daily lives that sustainability does not touch in some way. Whether it is a concern to us personally or not, there is an ever-present balancing act that brings stability to the lives we lead, the industries in which we work, and the future prosperity of generations to come.
Sustainability is, of course, a pivotal issue within the furniture manufacturing sphere. With consumers becoming more attuned to environmental issues and thus more inclined to furnish their homes accordingly, along with ever-more stringent regulations surrounding sustainable manufacture, there is significant pressure and incentive for the industry to partake in mitigating its own, significant, global footprint.
Indeed, according to market analysis by Grand View Research, the global eco-friendly furniture market size was valued at USD 43.26 billion in 2022 and is expected to expand at a compound annual growth rate (CAGR) of 8.6% from 2022 to 2030.
There’s no doubt that the challenges are many when it comes to investing in sustainable initiatives. With the ongoing labour shortage, fuel costs, technology adoption and political crises – amongst others – it’s certainly a difficult climate to negotiate. However, if businesses can embrace sustainable practices on some level, there is a twofold reward – the knowledge that they’re playing their part to reduce their environmental impact, as well as the significant competitive advantage of tapping into a burgeoning market.
Of course, the complete picture of a company’s environmental footprint is made up of many parts, from how it sources its raw materials, to the efficacy
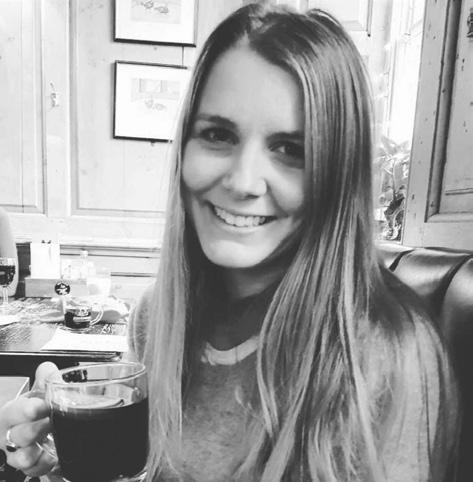
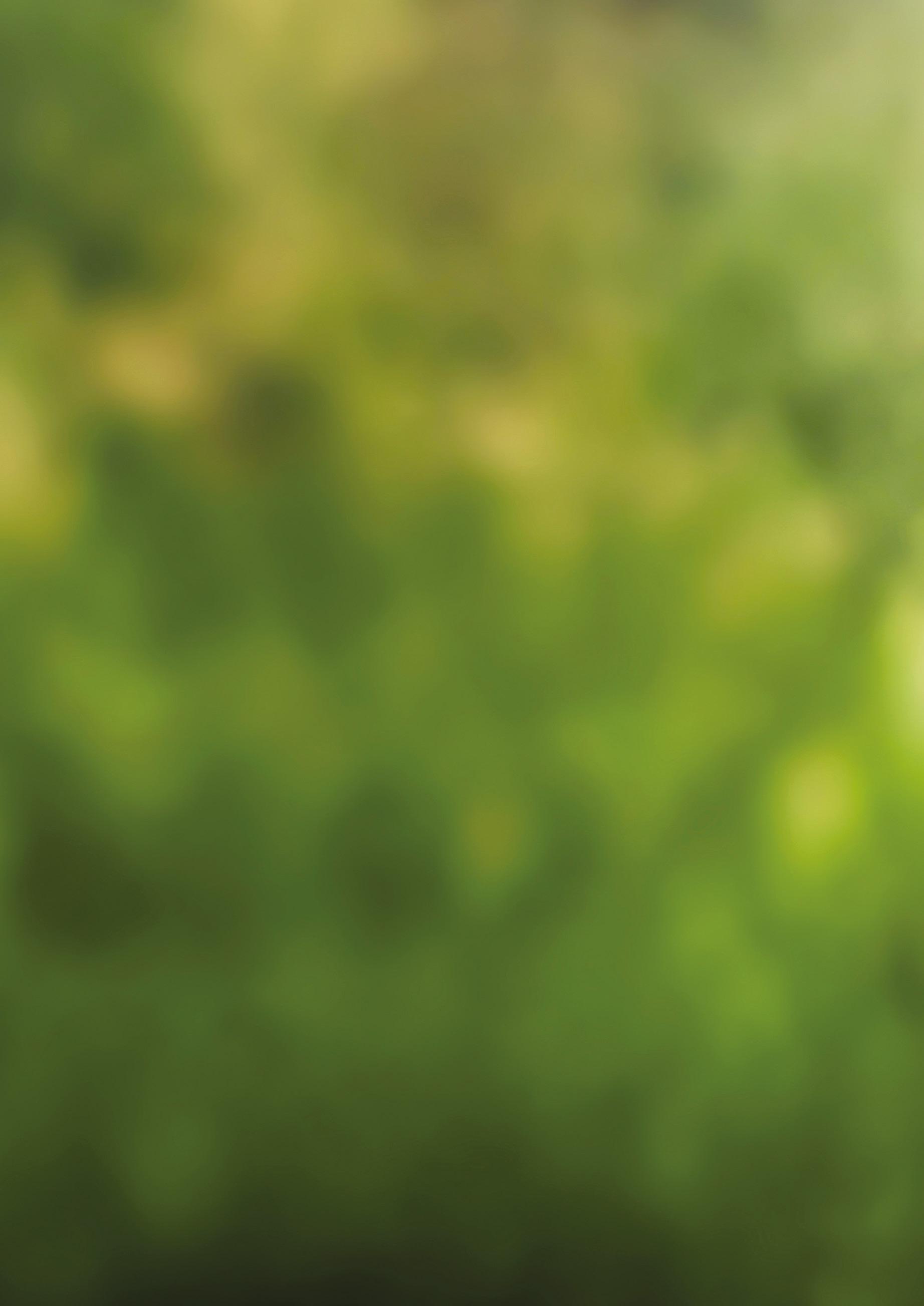
and nature of its production processes, to waste disposal, energy consumption, adoption of circular economy principles and more.
In the following pages, we’ve endeavoured to explore this multi-faceted topic and some of the many companies and trade bodies engaged with it.
You’ll find articles by some of the industry’s foremost trade bodies, including the BWF, BFM and FIRA who provide valuable insight into the opportunities and support networks the industry can take advantage of.
We have also included numerous profiles of companies – large and small, national and global – that have an inspiring or original approach to sustainable manufacturing and materials. Discover Organoid®’s unique materials, formed from regional, rapidly renewable and upcycled materials, for example, as well as the all-encompassing sustainability policies of Austrian fittings manufacturer, Blum.
You can also find a host of fascinating materials with outstanding sustainable qualities, from the likes of Silverlining Furniture, Finsa and Accoya, alongside guidance on everything from reducing carbon emissions to improving energy efficiency through voltage optimisation.
Though we’ve only scratched the surface of sustainability in furniture manufacturing within this supplement, we plan to expand our coverage across our varied platforms so that we may shine a light on the fascinating work being done to address this crucial issue. After all, what could be more important than ensuring the future prosperity and sustainability of this wonderful industry?
Gemma Lochhead, editorGemma
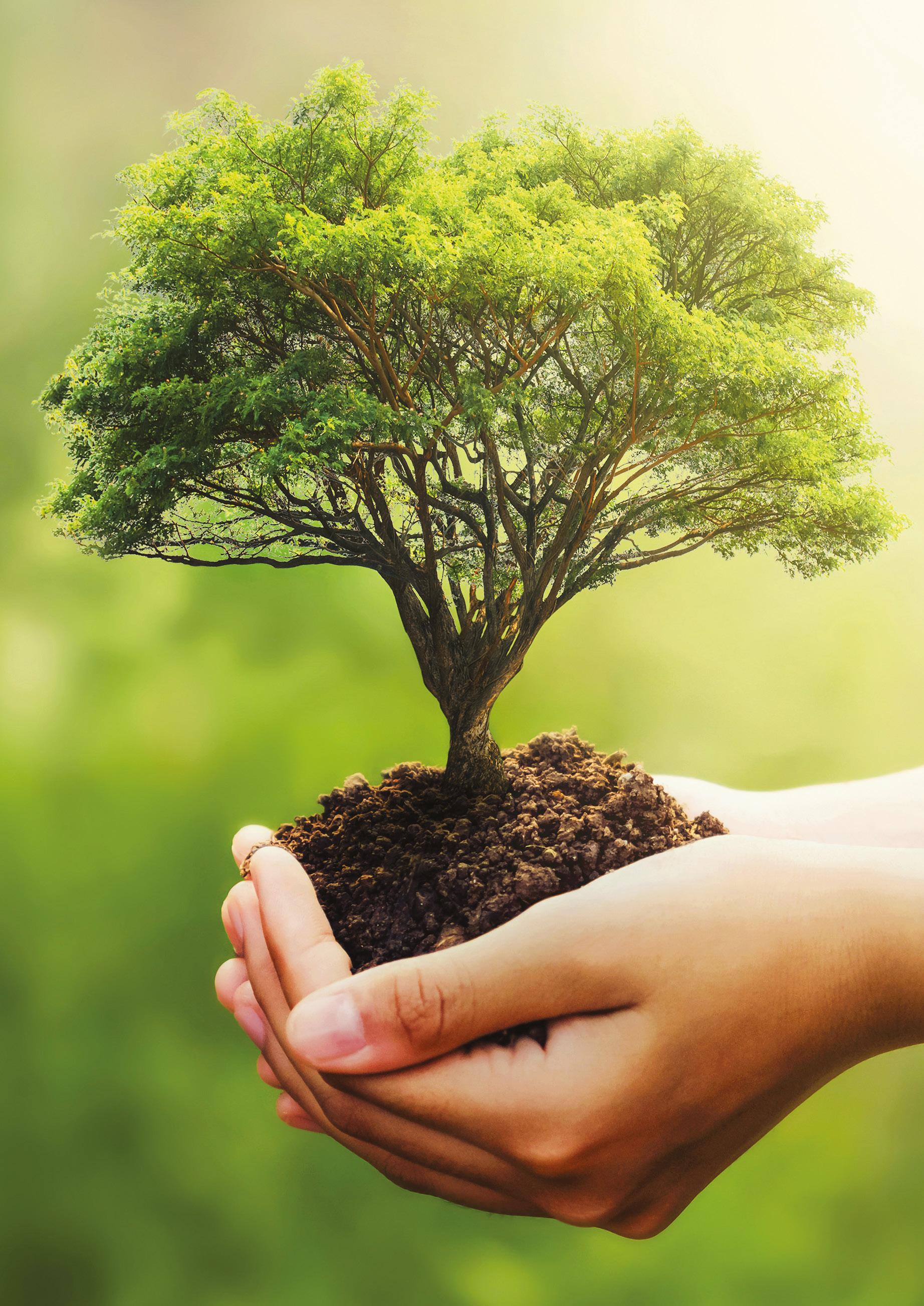
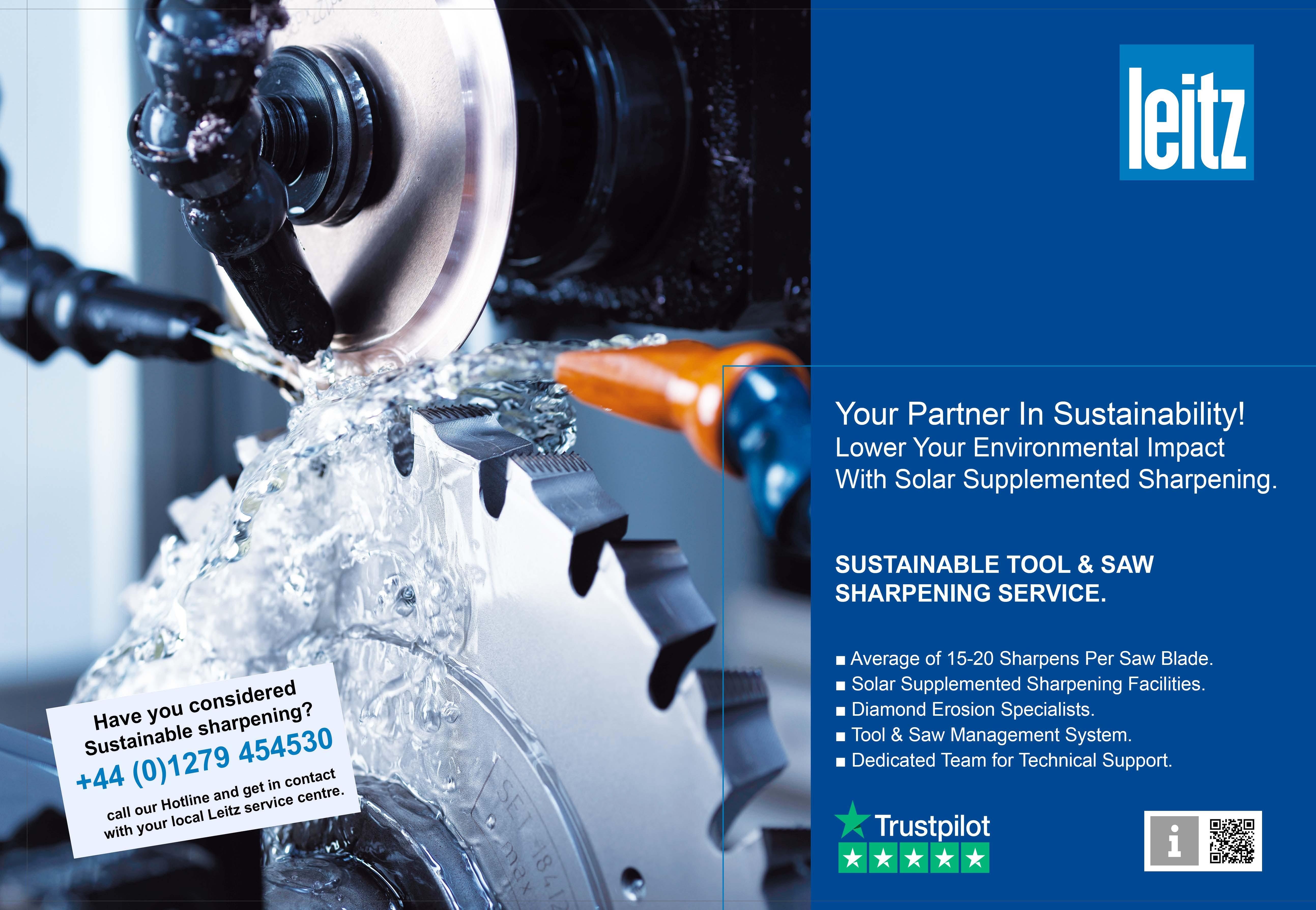
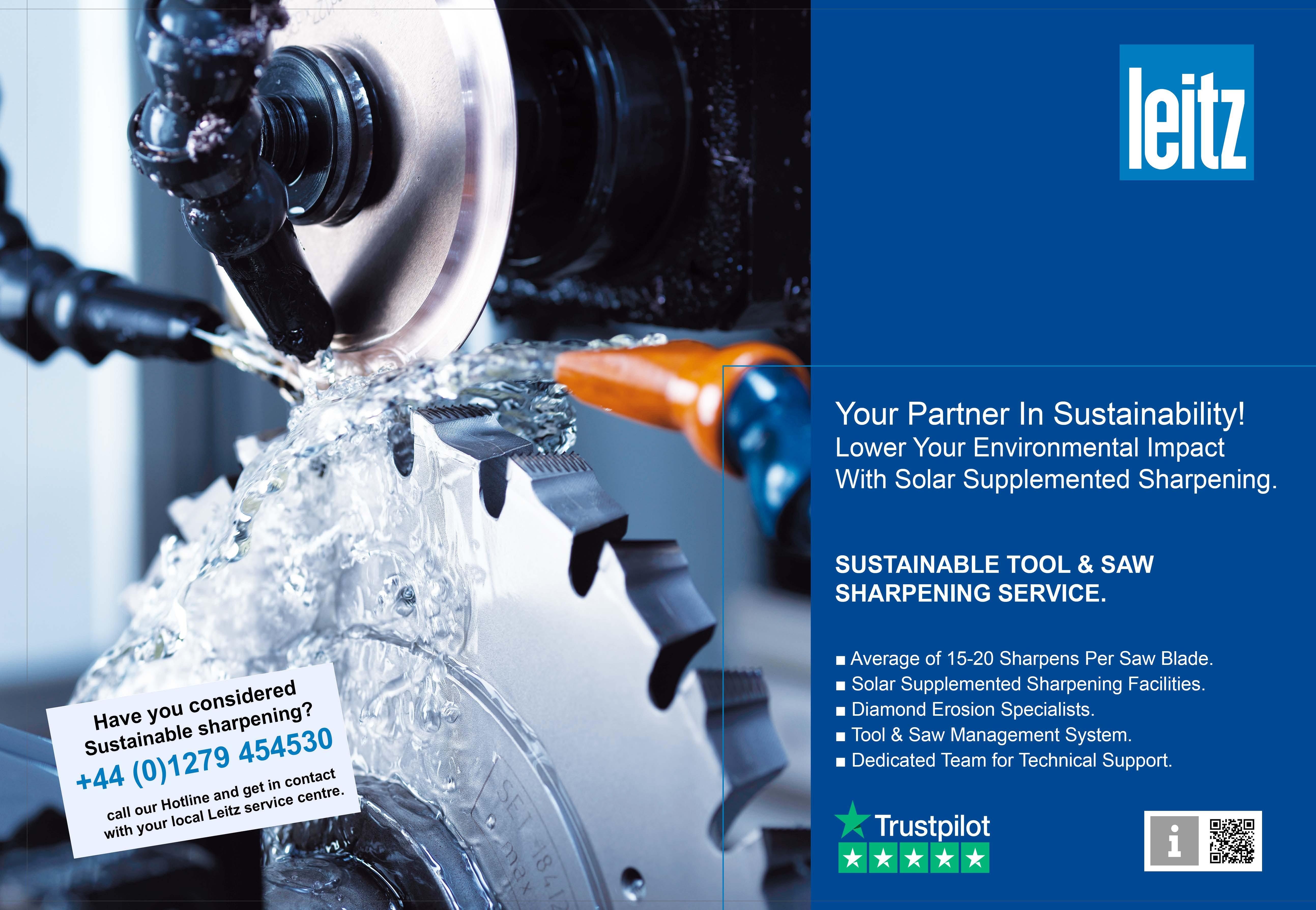
Sustainability is driving the Future of Furniture
As the voice of furniture manufacturers, retailers and suppliers across the UK, British Furniture Manufacturers (BFM) is taking clear steps to support the industry-wide shift towards sustainable working practices, writes Phil Spademan, BFM MD.
As demand for ‘sustainability’ increases, it’s important to understand what the term actually means. In my view, it essentially means creating a type of stability within a system that allows it to thrive.
In 1987, the United Nations Brundtland Commission defined it as: ‘meeting the needs of the present without compromising the ability of future generations to meet their own needs.’ In business terms, this comes neatly under the recognised ‘three pillars’ of sustainability:
• Environmental – protecting the environment in which we live and work, providing ongoing supply of natural resources
• Social – ensuring societal structures are robust, enabling healthy, educated people gain the skills needed to work and thrive in peaceful communities
• Economic – providing a system in which businesses and other organisations can grow, provide more jobs and improve economic outcomes.
All our member businesses use natural resources, require certain skills and are impacted by the wider economic climate, so creating sustainable, stable systems across these three pillars actually makes a lot of sense for every business, from the sole trader in a backyard workshop to major international manufacturers.
We know from our work with members and partners that sustainability is a factor that can influence the awarding of a contract, a partnership agreement or even a simple sale.
And this is why our Future of Furniture Awards – launched in 2023 – bring
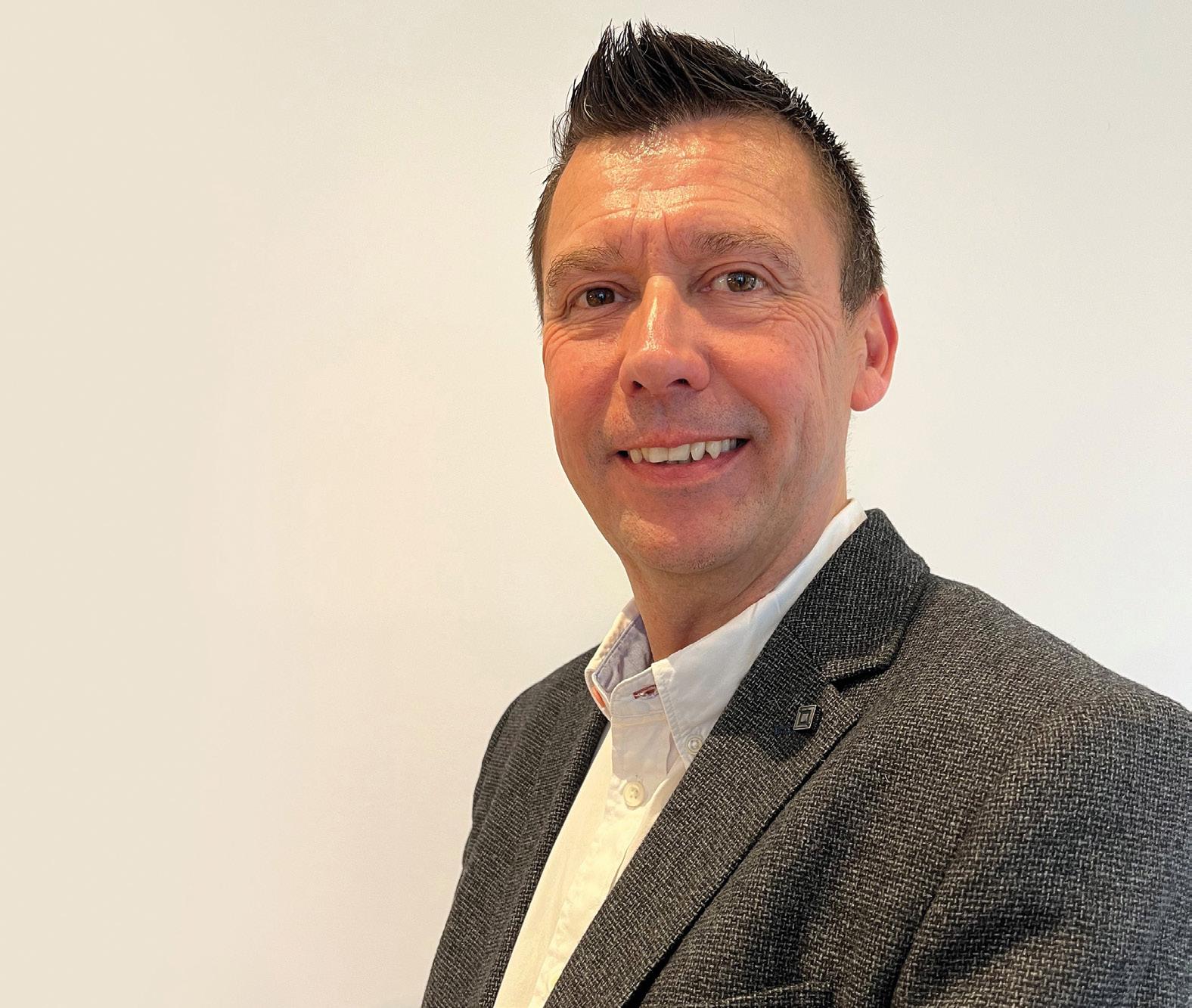
the efforts of BFM members who place sustainability at the heart of their business model into the spotlight.
This year the awards expanded from two to four categories, with the Excellence in Education and Excellence in Sustainability titles joined by new accolades for Environmental, Social and Governance Reporting and Sustainability Champion.
Award entries were evaluated by a panel of judges, who considered a number of criteria, including evidence of a commitment to continuous improvement in sustainability and a willingness to lead and empower others.
Harrison Spinks received a double award, with the company receiving the Excellence in Sustainability award, while their Group Sustainability Manager, Emma Linney-Taylor was named Sustainability Champion.
The company’s drive to source raw materials more responsibly, reduce environmental impact and conserve resources while improving product performance led to a number of supply innovations including the use of natural fillings grown at the company’s farms near Tadcaster, reducing chemical use by weaving mattress fabrics in-house, introducing digitalisation to reduce energy consumption and shifting from offshore carbon offsetting to environmental restoration.
“All our member businesses use natural resources, require certain skills and are impacted by the wider economic climate, so creating sustainable, stable systems across these three pillars actually makes a lot of sense for every business”
Excellence in Education winner, Ercol, was recognised for a successful reinstatement of its apprenticeship programme in 2017, alongside outreach work in schools and colleges as well as providing work experience and factory tours for students.
Vita Group was awarded the Excellence in ESG Reporting accolade after giving a detailed account of a three-year journey working with partners to establish a workplace culture that aligns with its goals and advances its sustainability mission.
This example of partnership working echoes the partnership agreement between BFM and ethical auditor Verisio, which seeks to set an industry standard for auditing.
Verisio’s Sedex Members Ethical Trade Audit (SMETA) is a comprehensive social compliance audit based on International Labor Organization (ILO) standards and the Ethical Trade Initiative (ETI) base code.
By helping companies identify improvements and ensuring that manufacturers can demonstrate ethical practices across their supply chain, the audit aims to create a standard that is informed by both manufacturers and retailers.
We are working towards setting an industry standard to allow our members to undergo just one test, rather than
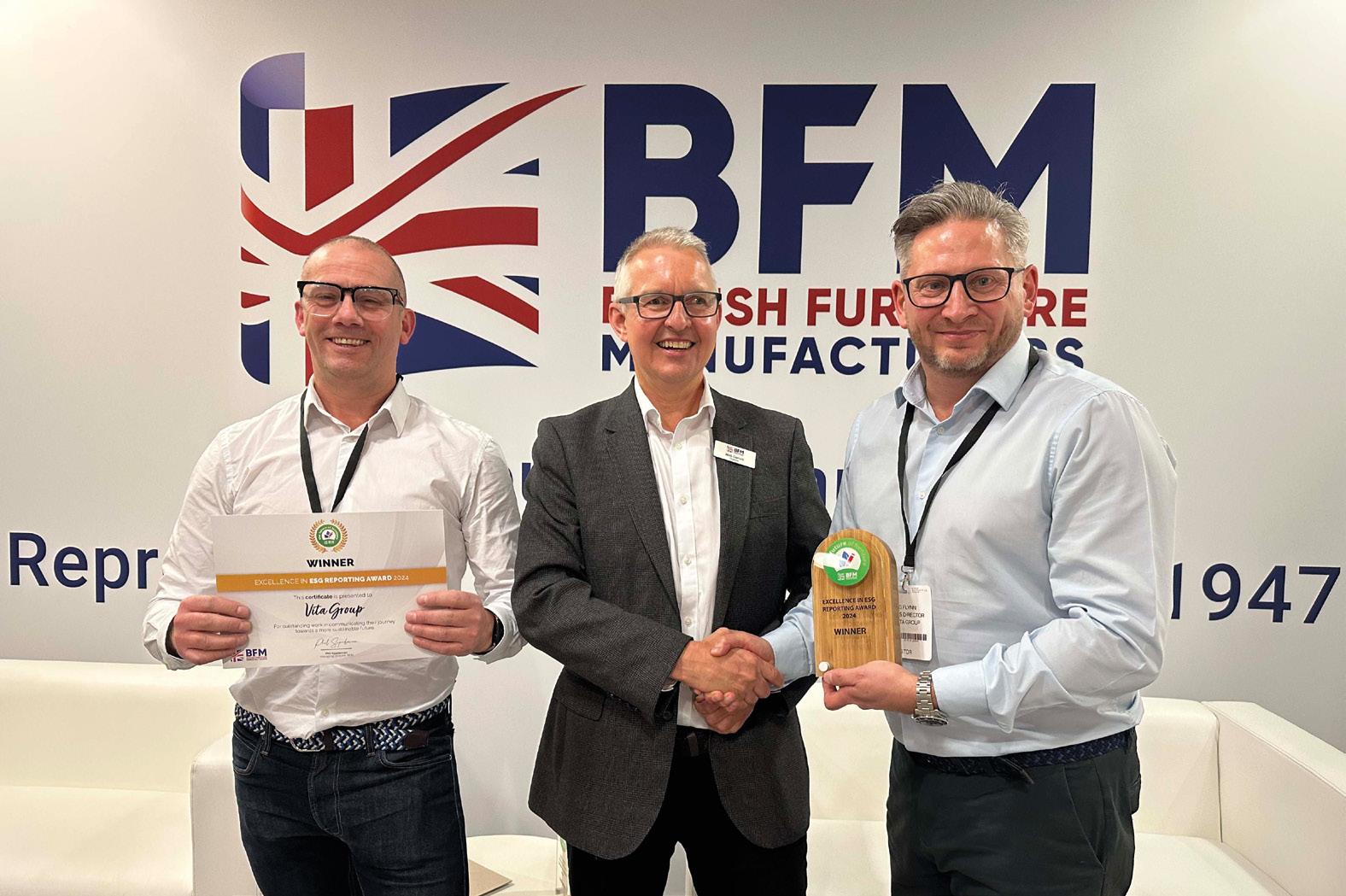
doing several audits, repeating things, and spending far more money than they actually need to.
The Verisio team work with a number of BFM members and are experienced in furniture factory audits in the UK and globally.
It’s an excellent way of health-checking a business and adds value by having independent verification that the systems in place are robust.
BFM members can work with Verisio at a discounted rate, thanks to the partnership agreement, and I discuss the benefits of the SMETA audit with Verisio’s Leon Reed and Director at One-Call Furniture, Paul James, in a recent episode of our Industry Matters podcast: Podcasts – British Furniture Manufacturers (bfm. org.uk).
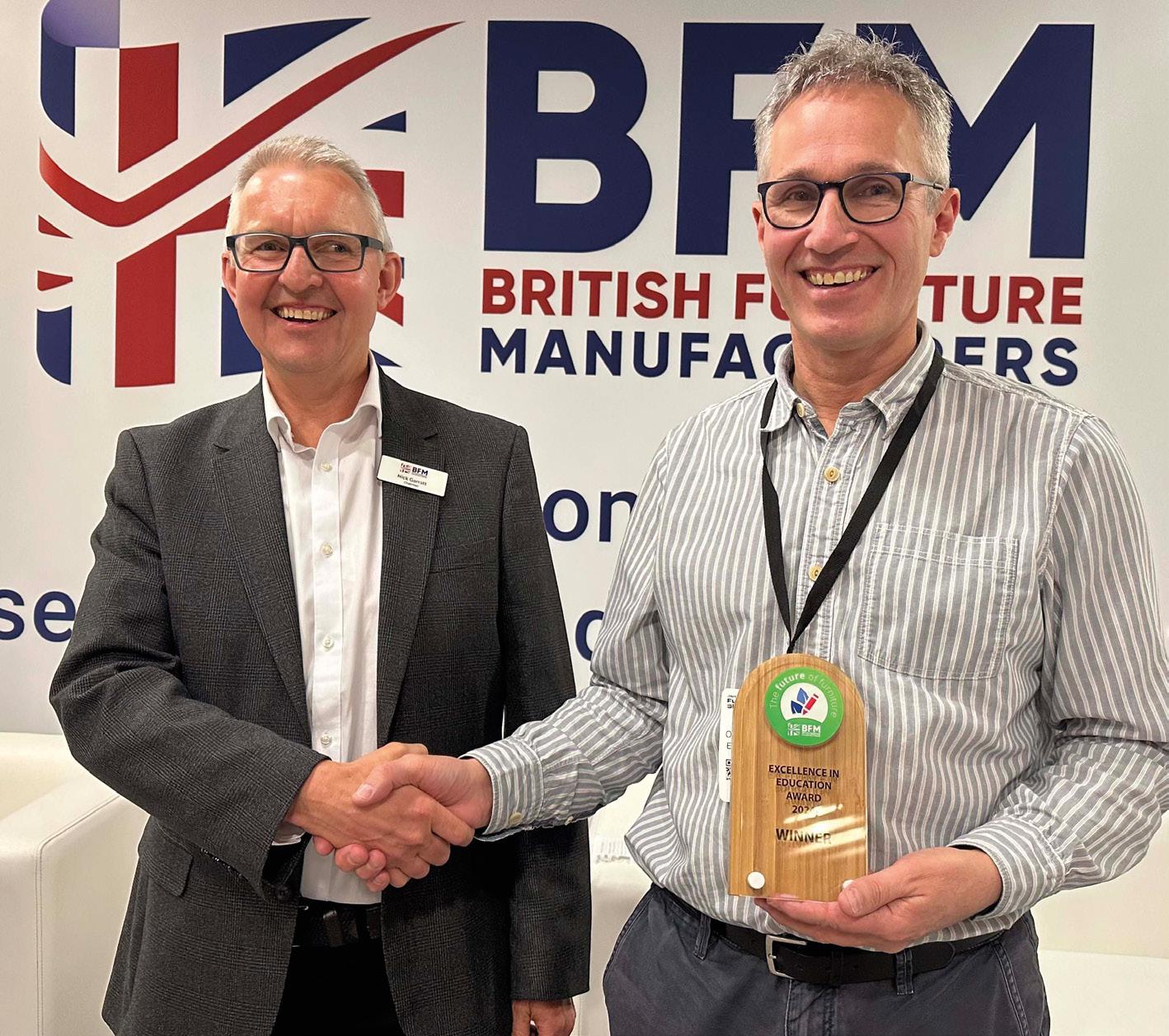
Alongside our Future of Furniture Awards and partnership with Verisio, BFM works with a number of organisations to provide members with the support and information they need to operate more sustainably.
The Furniture Industry Sustainability Program, launched in 2006, is the benchmark for sustainable practices in the UK furniture industry and considers all aspects of social, ethical and employment issues as well as waste, energy and emissions, from purchasing and procurement to end of product life.
We have also partnered with Planet Mark, a sustainability certification and net zero provider for organisations and the built environment.
For over a decade, Planet Mark has supported organisations to radically reduce carbon emissions, create operational efficiencies, enhance profits and work towards the global transition to net zero.
Our partnership means we offer webinars and workshops to members so that they feel confident to take measurable steps to reduce their carbon footprint. In addition, there are many toolkits and resources available to download from the Planet Mark website.
BFM is committed to increasing awareness of the elements that make British-made furniture great in the eyes of consumers, retailers, contract specifiers, architects and the wider international audience – and sustainability is one of the key factors that will drive the future of furniture.
www.bfm.org.uk
Excellence in Education winner, Ercol
Excellence in ESG Reporting Award winner, The Vita Group
Communicating sustainability in the furniture supply chain
Sustainability is now a major consideration across the supply chain, driven by investors, corporate clients, and domestic customers. FIRA’s John Hubbard reports on the current situation.
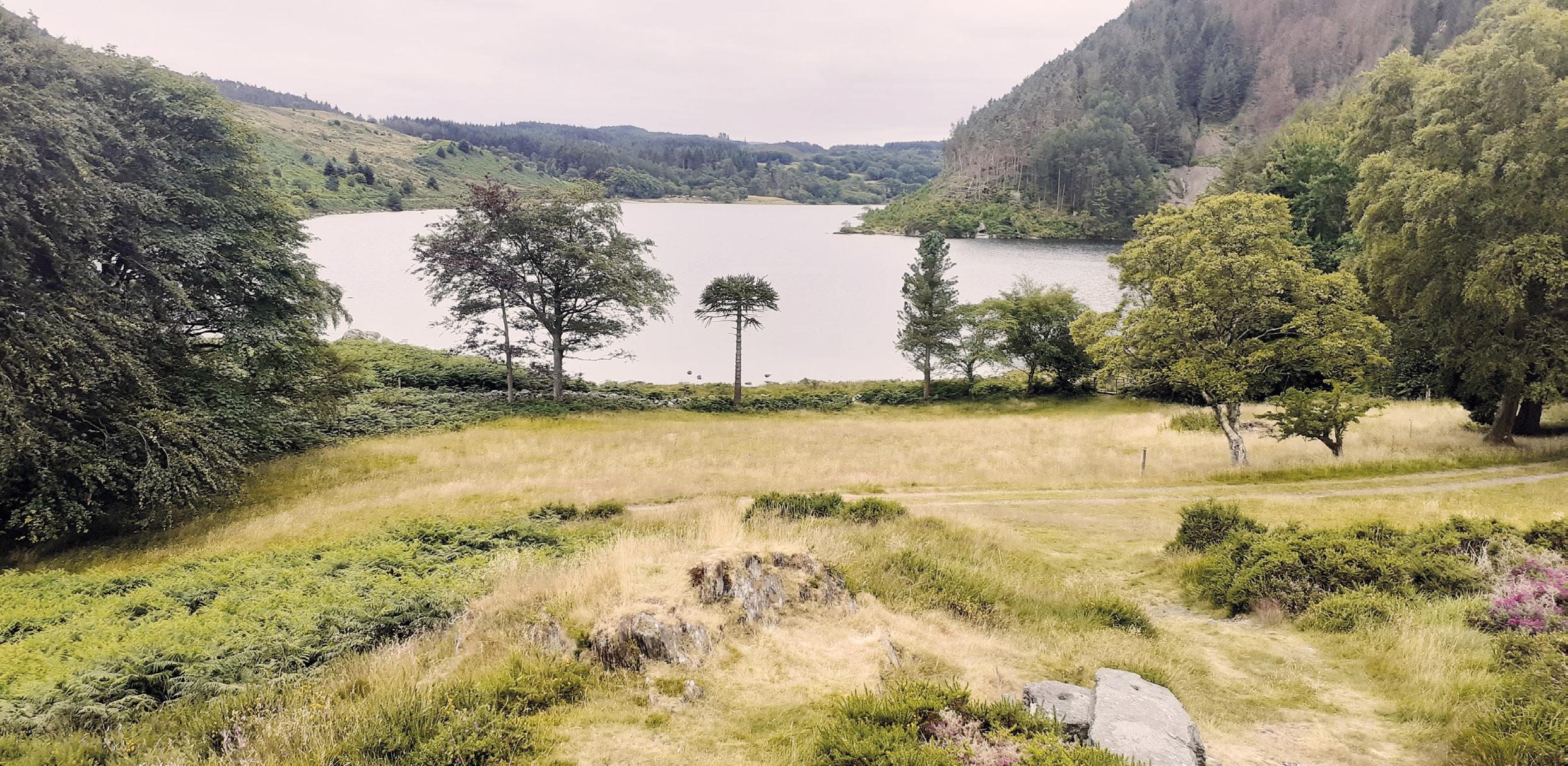
Each company’s sustainability journey will be different. Nevertheless, the first step is to determine where this fits into your business and what you aim to achieve, whether it involves meeting customer demands in tenders or establishing your company as a sustainability leader in the sector. Many companies look to International Standards for guidance on implementing sustainability. One of the most common environmental certifications is accreditation to ISO 14001 Environmental Management Systems – requirements with guidance for use. This certification addresses how to implement an environmental management system and commit to continual improvement. However, because this scheme is primarily concerned with the management system and applies across a wide range of industries, it does not explicitly address the specific concerns of the furniture industry.
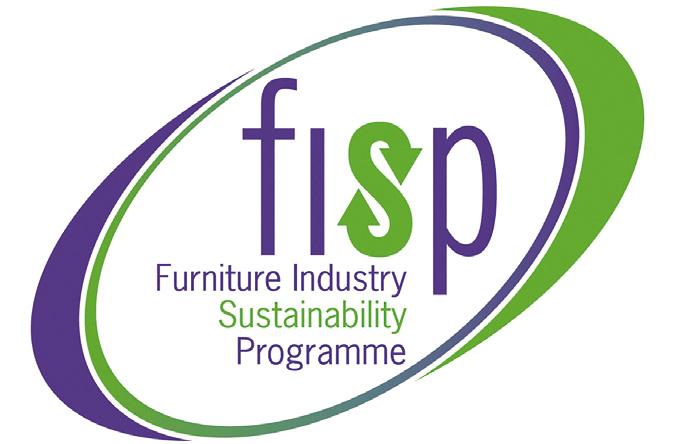
To address this gap, the Furniture Industry Sustainability Programme was created. This auditing scheme was developed by a collaboration of industry bodies, including the British Furniture Manufacturers (BFM), Contract Interiors UK (CIUK), The Furniture Industry Research Association (FIRA), and the National Bed Federation (NBF).
The scheme is modular, compatible with ISO 14001, and designed to be accessible across a wide range of organisations, from very large suppliers to smaller design practices and specialist workshops. The scheme has two sets
of criteria; one set is designed for manufacturers and assemblers, and the other is for distributors, retailers, and fitout companies. The main difference in the criteria is which modules are mandatory. The scheme covers environmental, social, and economic criteria and is recognised by other schemes such as SKA.
During a FISP audit visit, the auditor will examine the site and management system for evidence supporting the progress made against the scheme criteria. The criteria, developed by the industry steering committee, are designed to be challenging, going beyond what national legislation requires. They provide an opportunity for the company to understand where they currently are and what opportunities might be appropriate for them in the future.
The criteria are divided into three areas. The first section is mandatory and focuses on environmental policies and a system for assessing compliance with
legal obligations. The second section covers ten environmental criteria and allows the organisation to select those most appropriate to their business. These modules cover:
• Environment management systems
• Energy management and efficiency
• Waste management
• Packaging management
• Transport management
• Procurement
• Sustainable timber
• Air and water management
• Eco-design
• End-of-life management
The applicant organisation is required to select six of the modules, including any that are mandatory, and must score at least 50% of the available marks for each.
The third section addresses the economic and social aspects of sustainability. Here, the applicant organisation would need to meet four out of the following modules:
• Community relations and charity work
• Healthy work environments and personal wellbeing
• Workforce development and Training
• Employment
• Business resilience
• Communications and commitments
Companies joining the programme are audited every two years if accredited to ISO 14001 or annually if not.
Following an audit, the applicant organisation will receive a confidential report detailing its performance against the specified criteria. As a member of the scheme, they will receive a certificate, which will also be displayed on their profile page on the FISP website (www. fispfurniture.com). On this page they can add other information such as their product range, markets served, and contact details.
The scheme currently has around 80 member organisations spanning the entire supply chain. Members include manufacturers of components such as textiles, foam, and hardware, as well as distributors and installers. The scheme has also been designed to be accessible to businesses of all sizes, from small studios and workshops with a few employees to the largest suppliers of
office furniture, kitchens, and bedrooms.
The scheme was initially developed for the UK market, but now about 10% of its members are from mainland Europe, including Austria, France, Germany, Italy, Lithuania, and Turkey.
One of the scheme’s main principles is to avoid being too specific in the requirements and recognise that companies can come up with new innovative solutions to sustainability challenges. By not enforcing specific requirements, the scheme allows organisations to share their own sustainability journey, which should align with the needs of their customers, their
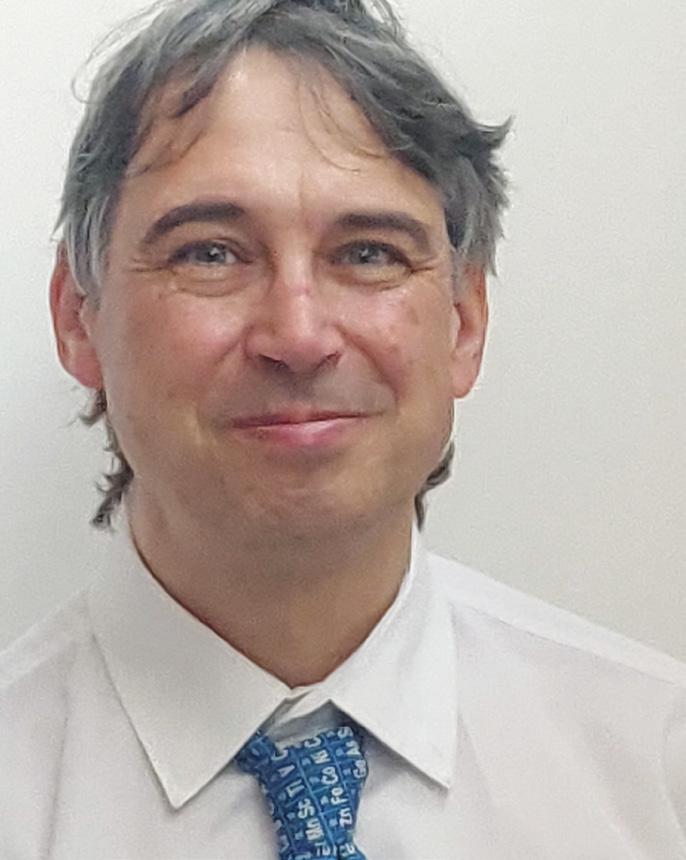
‘This certification addresses how to implement an environmental management system and commit to continual improvement.’
distribution methods, and the materials used in their products. However, we are always seeking companies dedicated to enhancing their products’ sustainability and striving for ongoing improvement across the supply chain.
In 2023, a review of the criteria led to some changes being introduced. This includes separating eco-design and end-of-life considerations as separate modules to account for different methodologies. This helps when considering how products perform across their life cycle and what options are available to customers to extend
their products’ lifecycle, renew, or give products a second life with a potential new customer.
In addition, some social and economic modules were merged to avoid double counting, and some were renamed to improve internal and external communication about completed sustainability achievements and future targets.
The scheme was designed to be compatible with other certifications, such as ISO 14001 and other timber certification schemes. This allows new companies to start with FISP on their sustainability journey and work towards obtaining other certifications.
The furniture industry does have a positive sustainability story to tell, thanks to strong local supply chains and products that have a long lifecycle and are responsibly managed at the end of their useful life. However, the industry cannot be complacent and needs to prepare for future sustainability challenges in the face of stricter regulations. It is hoped that those organisations that are members of the Furniture Industry Sustainability Programme will be better prepared for potential legislative changes in the coming years and that this industry recognised scheme can serve as a model for sustainable furniture assessment outside the current parameters of the scheme.
To apply for membership of the Furniture Industry Sustainability Programme, there is an application form on the scheme website. When submitting your application, please include copies of any existing certifications. Following this, an assessor organisation will coordinate an audit and help you develop your profile for the program’s website. If you are unsure whether your organisation is ready to join the scheme, the assessor organisations will provide guidance and support, along with consultancy and training, as you work toward program membership.
For enquiries please email contact info@ fispfurniture.com. Alternatively, contact the author.
John Hubbard john.hubbard@fira.co.uk
FIRA’s John Hubbard
Championing timber as a sustainable solution
To reduce emissions and achieve netzero goals, the broader construction industry has been increasingly turning to timber as a building material that can help achieve sustainability objectives, writes Helen Hewitt, CEO of the British Woodworking Federation (BWF).
Driven forward by the Government’s Timber in Construction Roadmap, which outlines Parliament’s strategy for increasing the safe use of timber within
the construction industry, the BWF has long championed the benefits of timber and played a key role in the development of the industry Roadmap.
In fact, research conducted by the BWF on attitudes of homeowners’ and housebuilders’ towards timber products revealed an overwhelmingly positive sentiment. Added to this, our data found that for 60% of people it is important to know that products have been sourced
and manufactured in an environmentally friendly way.
With consumers turning toward more sustainable solutions and the Government striving toward net zero, it’s more important than ever to understand the role that timber and timber products can play in helping achieve a lower carbon future. Here, we explore the benefits of timber and how the BWF is championing its use as a sustainable material.
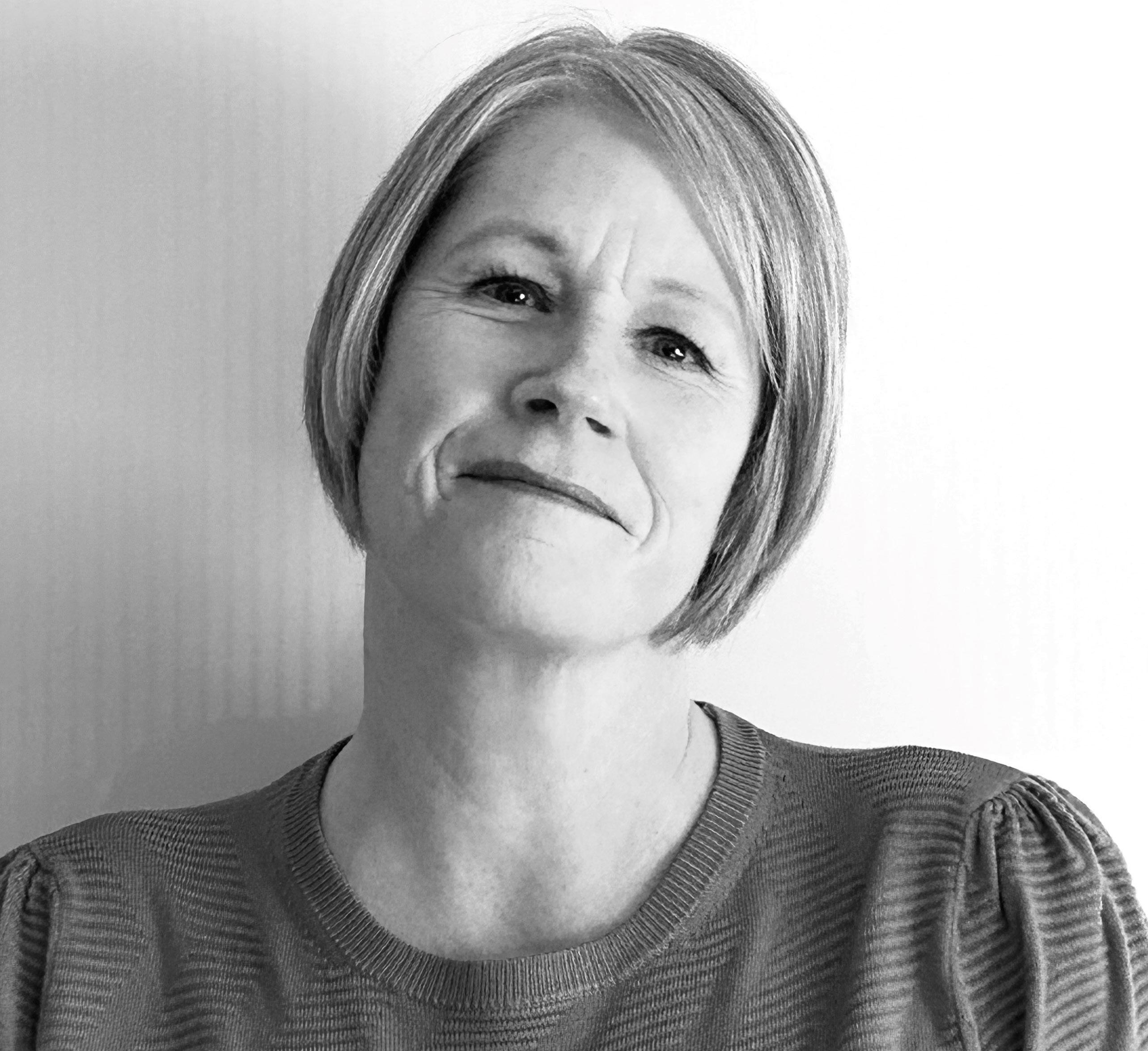
Helen Hewitt, CEO of the British Woodworking Federation (BWF)
“Timber will play an essential role in helping the construction industry and the Government meet its net zero ambitions, and together as a sector, we can champion its use while working toward our individual carbon reduction ambitions”
Timber and sustainability
Wood is the only building material that is inherently renewable. As trees are harvested, new seedlings can be planted and by supporting timber certification schemes such as the Forest Stewardship Council (FSC) or Programme for the Endorsement of Forest Certification (PEFC), businesses and customers can be reassured that raw timber is sourced from sustainably managed forests.
Wood also has a significantly lower embodied carbon footprint (emissions from production through to end of life) as it requires less energy-intensive manufacturing processes compared to other materials. Added to this, as trees grow they sequester atmospheric carbon, and according to The Forestry Commission, the stored carbon is estimated to make up 50% of timber’s dry weight.
Timber products not only boast sustainable credentials but also offer aesthetic appeal and exceptional long-term value.
As new influences impact business and consumer choice, including Government net zero targets, sustainable forestry and the continued focus on health and wellbeing, it’s important that the wide range of benefits of timber are effectively communicated.
Misconceptions surrounding the use of timber
Despite housebuilders and homeowners recognising the appeal of timber, the lack of awareness over its benefits means that myths have continued to persist. This is particularly apparent when looking at timber windows and other high-value assets.
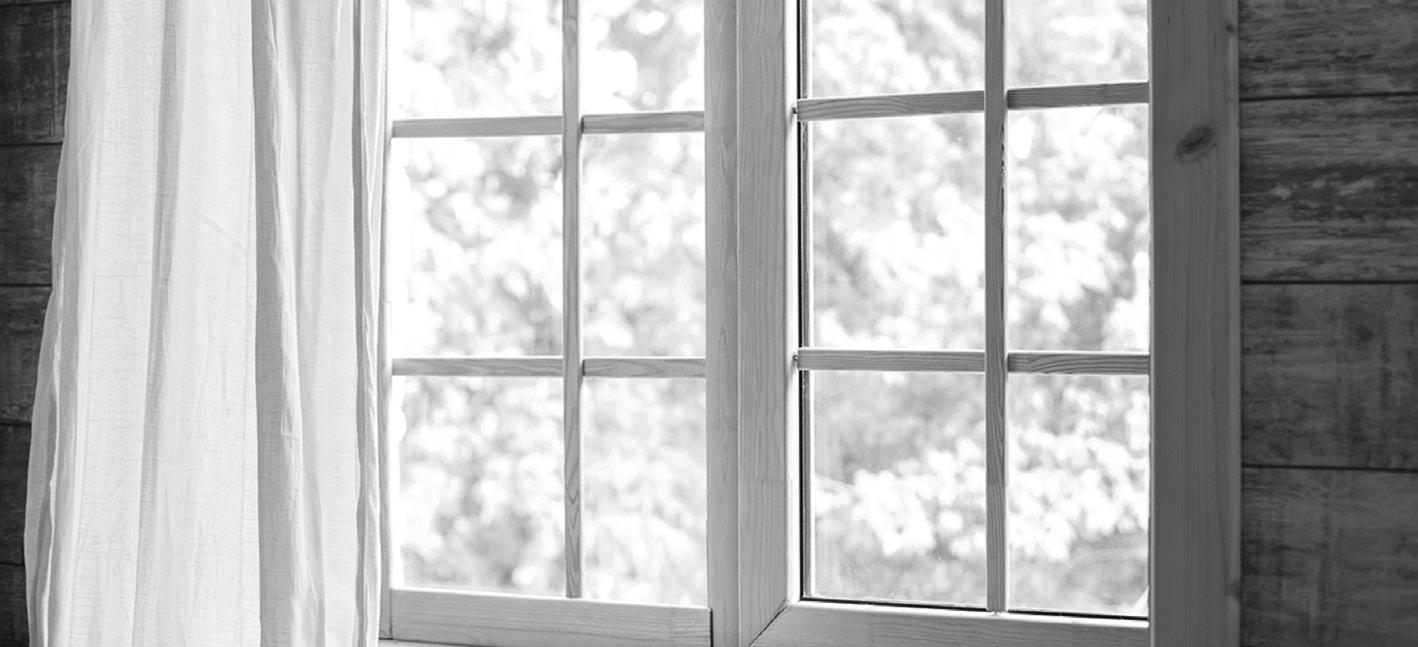
Myth 1: Timber windows are less energy efficient
Timber is a naturally insulating material and timber windows can offer the same thermal performance as alternatives. However, the energy efficiency of a window is much more than just the frame. The glazing and draft-proofing also have a major impact on performance.
Myth 2: Timber is more expensive than alternative materials
In our ‘Challenging misconceptions, homeowner and housebuilder attitudes to timber windows and doors’ survey, cost was highlighted as one of the main reasons why housebuilders are deterred from using timber in windows . While materials such as uPVC tend to be cheaper than timber in the short term, the improved durability of timber window frames means that they exceed the lifespan of alternatives.
Timber windows can achieve lifespans of up to 50 years and beyond, while other popular window materials average just 20-30 years and still require maintenance to achieve this.
The improved durability of wood window frames means that they can last longer and therefore actually provide better value over their lifetime. Not only can wood window frames have a long service life but they also offer lower through-life costs when maintenance and replacement are factored in.
Myth 3. Timber products require a great deal of maintenance
Maintenance was listed as the top misconception among homeowners and housebuilders. Though 49% of
housebuilders indicated that the length of product guarantee for their windows was the most important factor, modern wood window frames actually require much less maintenance than commonly believed. In addition, window manufacturers provide industry-standard warranties.
In fact, many BWF members offer 10-year guarantees on products with an opaque finish and seven years for products with a translucent finish.
BWF’s commitment to promoting timber and driving sustainable best practice
As a champion of timber, the BWF is committed to highlighting the benefits of wood through our Build It Better with Wood messaging and ongoing educational awareness campaigns. In addition, our involvement in the development of the Government’s Timber in Construction Roadmap will help bolster the use of wood within the construction industry and shape the future of our sector.
We are also helping our members advance their sustainable practices. Our BWF Code of Conduct includes an eight-point assessment with a strong focus on sustainability. As well as this, the new 2024 BWF Sustainability Award celebrates those in our sector who are leading sustainable practices. Through these initiatives, we support our members in their goals to help the industry achieve net-zero goals.
Timber will play an essential role in helping the construction industry and the Government meet its net zero ambitions, and together as a sector, we can champion its use while working toward our individual carbon reduction ambitions. www.bwf.org.uk
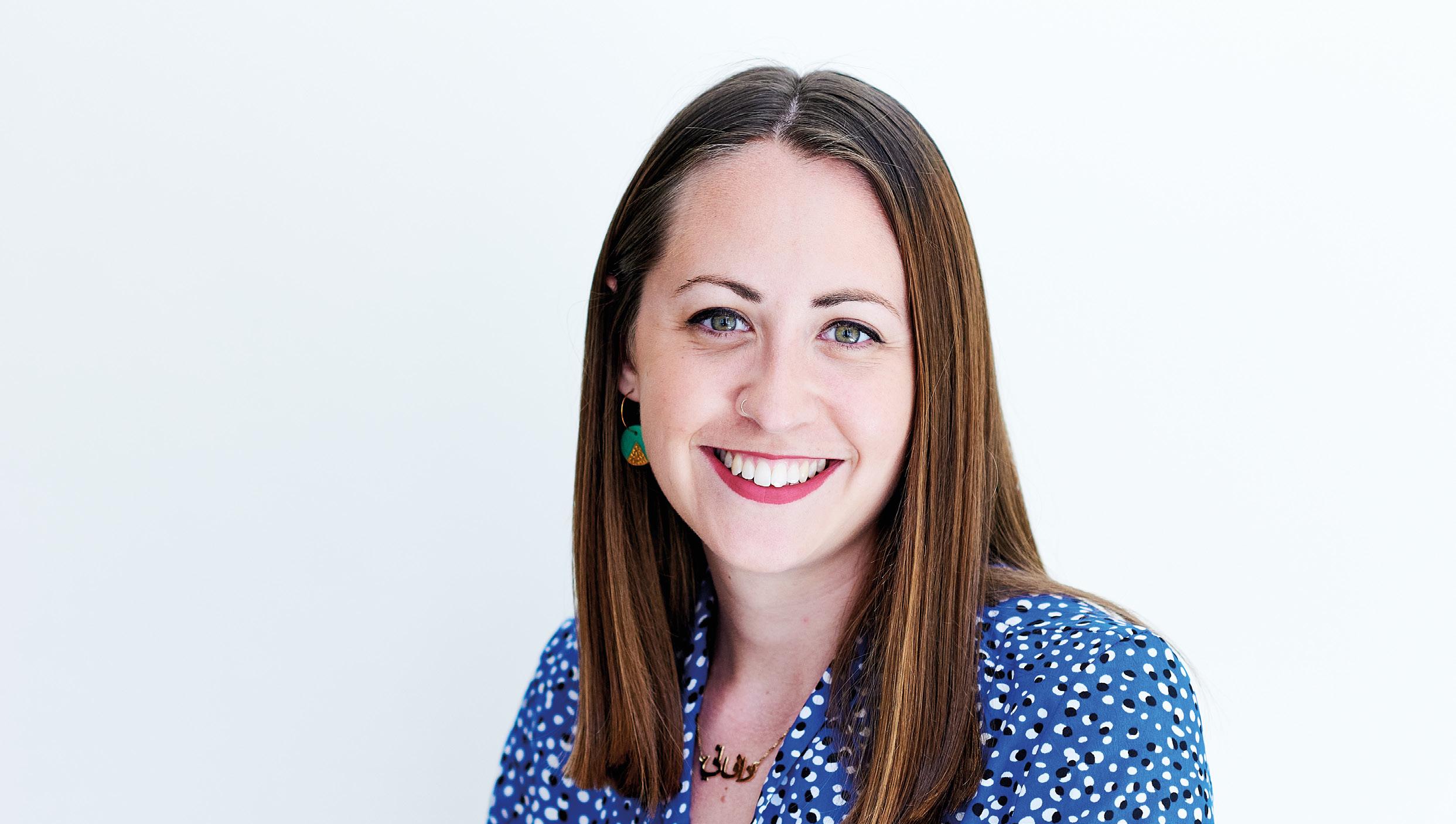
Q&A – Planet Mark Jo Little, Senior Sustainable Business Manager
Could you provide a brief overview of Planet Mark as a whole, please?
Since our launch in 2013, Planet Mark has been on a mission to help businesses of all sizes reduce carbon emissions, reach net zero, and drive positive change for society, business and nature.
Operating at the centre of climate tech, advisory and legislation, our unified model helps businesses achieve tangible results that stand for meaningful climate action.
To do that, we begin by measuring what matters, providing the insight needed to make informed decisions about when and how your organisation will make the transition towards net zero. Alongside this, we educate and inspire your people, acting as a catalyst for behaviour change
“All manufacturers have the opportunity to be part of an industry-wide transition to net zero, and some businesses will be left behind if they don’t act soon!”
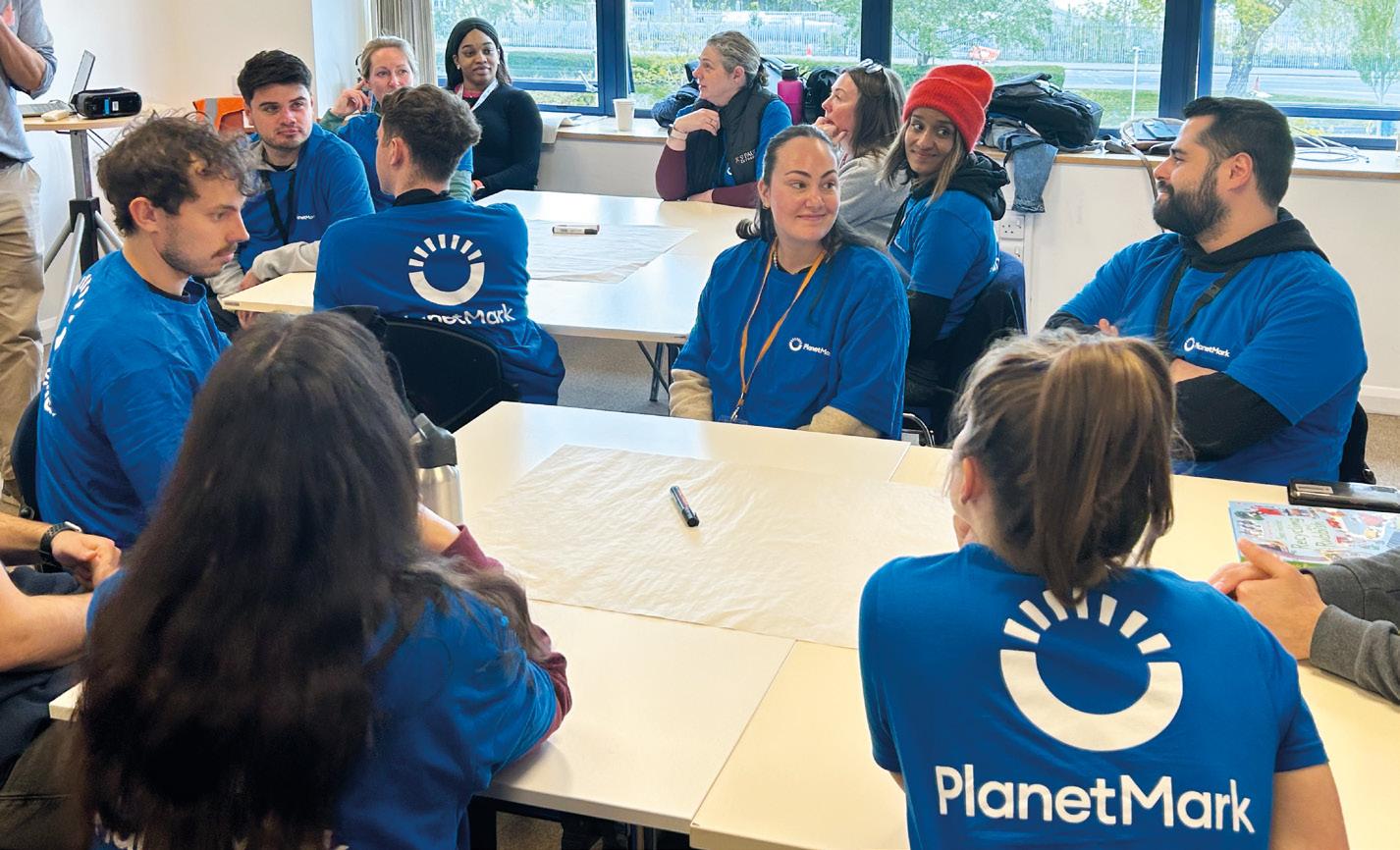
that not only immediately reduces carbon emissions but drives cost savings through lowering consumption.
As one of ten global partners of the UN-backed Race to Zero campaign, our process and certification are recognised by government and business standards, driving assurance in sustainable progress.
We have a firm belief that in the near future, every business will be regenerative.
Communicating your status as a Planet
Mark Certified Business further supports customer preference for your brand and provides accurate and independent verification that your organisation is measuring and reducing your carbon emissions, ultimately contributing to your environmental, social and governance (ESG) criteria.
The regenerative economy will support and reward those organisations that truly contribute to society and the planet.
Jo Little
Could you tell us more about the resources and services you can offer the furniture manufacturing sector?
Carbon reporting involves measuring and disclosing the amount of carbon emissions produced by a business.
Understanding your carbon footprint is the first step on your journey to becoming net zero. By becoming Planet Mark certified, it helps your business:
• Implement an effective carbon reduction strategy.
• Stay ahead of legislation and mitigate risks.
• Eliminate greenwashing.
• Boost operational efficiency while saving costs.
• Enable supplier procurement support
If you could impart one nugget of wisdom to furniture manufacturers looking to shape their business strategy with sustainability in mind, what would it be?
All manufacturers have the opportunity to be part of an industry-wide transition to net zero, and some businesses will be left behind if they don’t act soon!
Understanding your carbon footprint baseline will help decide on businesscritical decisions from the near term to the long-term changes.
“The regenerative economy will support and reward those organisations that truly contribute to society and the planet”
It is crucial to develop your transition to a circular economy in the long term, this will be most critical to a furniture manufacturer’s sustainable business strategy. Therefore, mitigating emissions from any natural resource materials to removing all waste streams should be a priority. This could be through take back schemes or working collaboratively with other industries to repurpose end-of-life materials.
What do you feel are the main challenges the furniture manufacturing industry faces in terms of meeting sustainability targets, and how might these be overcome?
I would say the most challenging aspect for the furniture manufacturing industry is the complexity of their supply chain. However, this is where the most impactful changes could come from.
Working together and collaboratively to request data and encourage their suppliers to do more will help reduce
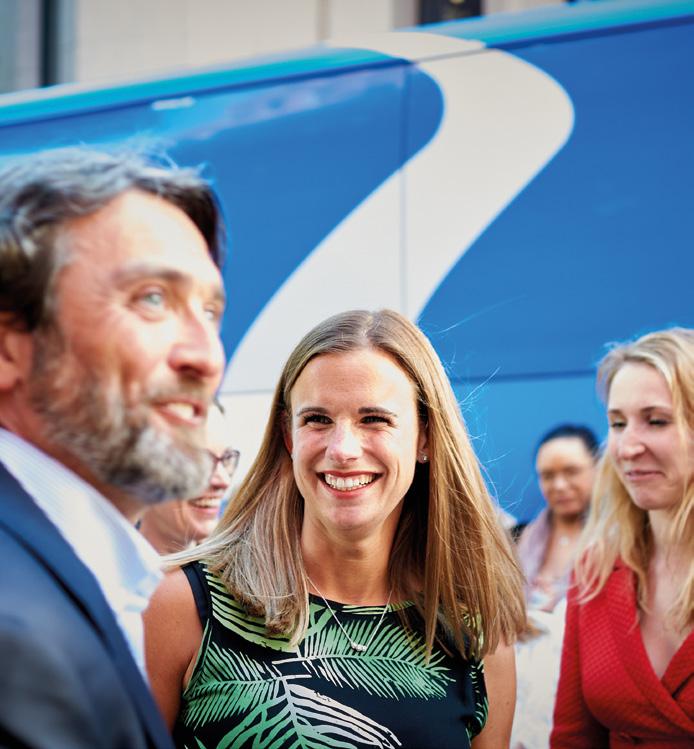
manufacturing emissions as well as transportation emissions.
Holding suppliers accountable yet supporting the transition is key.
What do you foresee being the key environmental focuses shaping manufacturing businesses in the coming decades?
Over the coming decades as we transition to a net zero industry the focus will be around circularity. No longer will a linear model be effective or economically viable. Therefore, understanding your product line and customer relationship will be key in improving and assisting a circular economy.
www.planetmark.com
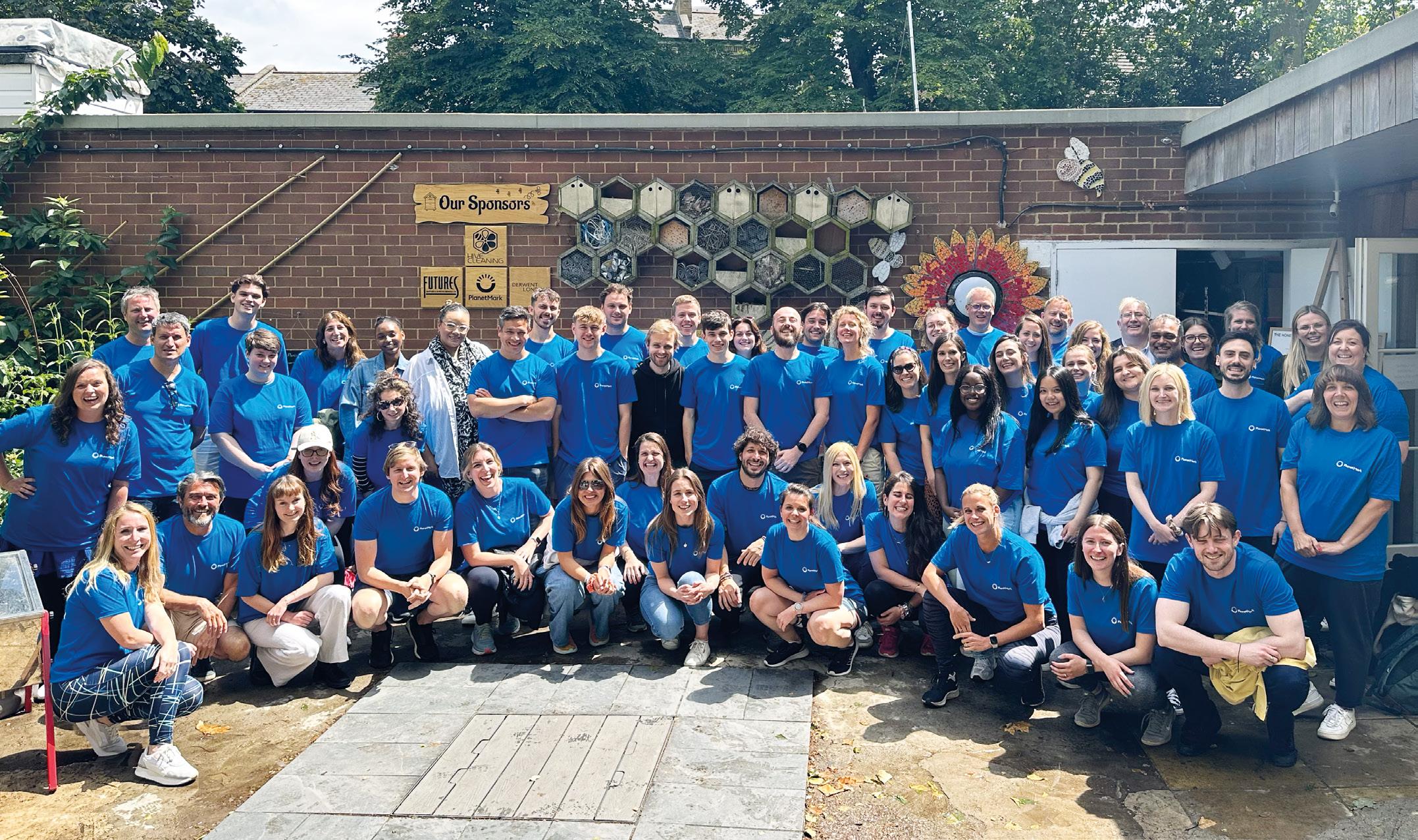
Unlocking a greener and more profitable future with VO
The vast majority (98%) of manufacturers across all sectors use electricity, but only around a third (36%) regularly monitor their energy use, and even fewer (11%) monitor both energy use and energy efficiency, according to the Department for Energy Security & Net Zero. Across all sizes and sectors of manufacturers, 66% have taken steps in the last five years to improve energy efficiency at their site, with the most common steps including investing in building improvements (47%), implementing behavioural and cultural changes (27%) and replacing industrial equipment (24%).
With high energy prices and growing pressure for businesses to improve energy efficiency and operate in a more sustainable way, there is more that can be done. For manufacturers in the
“For manufacturers in the furniture sector, voltage optimisation (VO) could help save money, improve energy efficiency, prolong the lifespan of machinery and other equipment, and help them become a more sustainable business”
furniture sector, voltage optimisation (VO) could help save money, improve energy efficiency, prolong the lifespan of machinery and other equipment, and help them become a more sustainable business. But what exactly is VO and how could it help furniture manufacturers? UK manufacturer of leading voltage optimisation solutions, GWE, tells us more ...
An introduction to VO
In the UK, electrical equipment is designed to work at 220 volts, however, the national grid can supply businesses and homes with up to 253 volts. This extra voltage is ultimately wasted energy, costing the business money on its bills and increasing its carbon footprint. On top of this, the extra voltage can overload electrical equipment, reducing its lifespan and increasing maintenance needs. VO works to address these problems by reducing the voltage levels supplied to electrical equipment, ensuring their individual optimum voltage is provided whilst preventing overloading devices. For businesses like furniture manufacturers that use a high level of energy on everything from machinery to lighting, VO offers multiple benefits; it reduces wasteful energy consumption, improves energy efficiency, cuts carbon footprint,
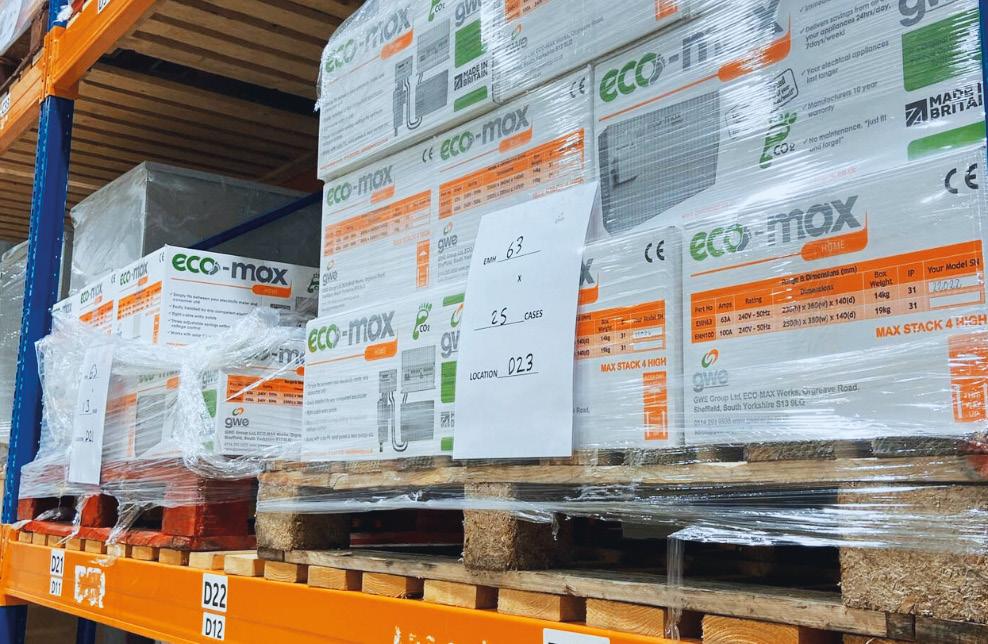
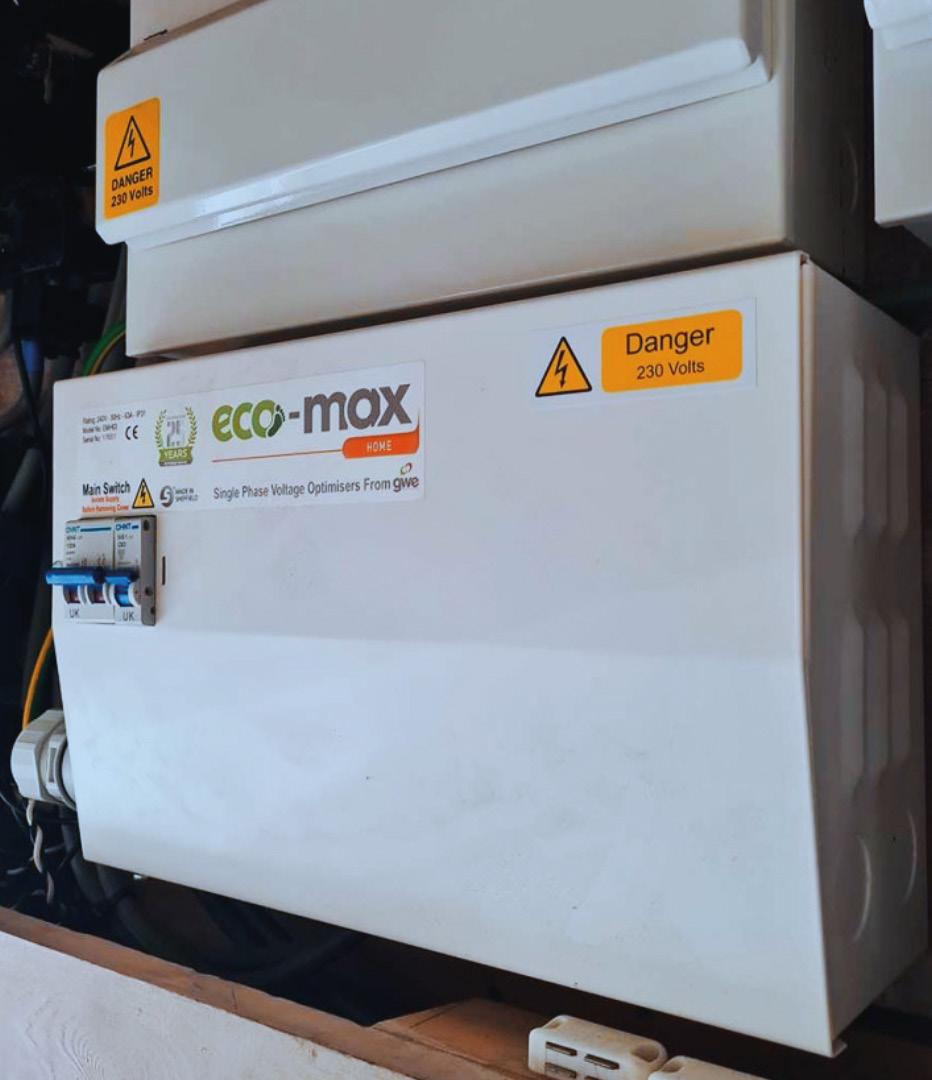
reduces downtime and costs associated with equipment maintenance, and saves money on energy bills.
Since 1994, GWE has been a leader in VO and manufactures its VO units in its factory in Sheffield. It has worked with many well-known brands from Asda to Kellogg’s. Working with Ikea, GWE helped it reduce the annual electricity bill of its Peterborough site by £39,502, as well as cut CO2 emissions by 158 tonnes in the process. Another example, saw its VO solution eco-max reduce the energy consumption of Amazon’s Milton Keynes distribution centre by 11.75%, delivering a pay back on the investment in just eight months.
Sarah Cramer, MD of GWE, explains what opportunities VO presents for manufacturers: “Energy intensive businesses such as those in manufacturing have never been under so much pressure to operate in a greener, more efficient way while also watching their costs. The last couple of years in particular have seen a lot of businesses struggle with rising energy prices. VO is a relatively simple and efficient way that manufacturers can resolve these problems and ultimately help them run a greener, more profitable business.
“Taking steps like improving the building fabric and replacing old equipment are positive, but when businesses are
“Since 1994, GWE has been a leader in VO and manufactures its VO units in its factory in Sheffield”
ultimately receiving and paying for more voltage than they need, if they don’t find a way to control and optimise this then they could well be paying too much for their electricity, damaging their equipment and adding to their carbon footprint.”
Starting your VO journey
It’s estimated that only 50,000 business properties in the UK currently have VO fitted, with a further 2.5 million potential business properties that would be suitable for the technology.
For manufacturers that are interested in finding out how VO could help them, their first step should be to work with a reseller, such as energy efficiency consultants, facilities managers, electrical contractors or energy management companies.
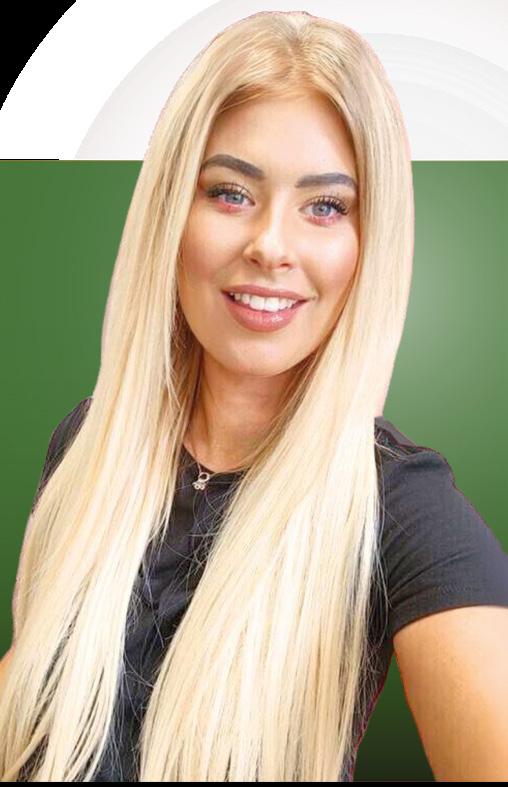
What’s been the highlight of your journey at GWE?
There have been so many incredible moments, but our recent move to a much larger headquarters ranks high. Seeing our team flourish and needing quadrupled space is a fantastic testament to their hard work and dedication. It’s a symbol of how far we’ve come, and it fuels our excitement to keep pushing the boundaries of sustainability and efficiency.
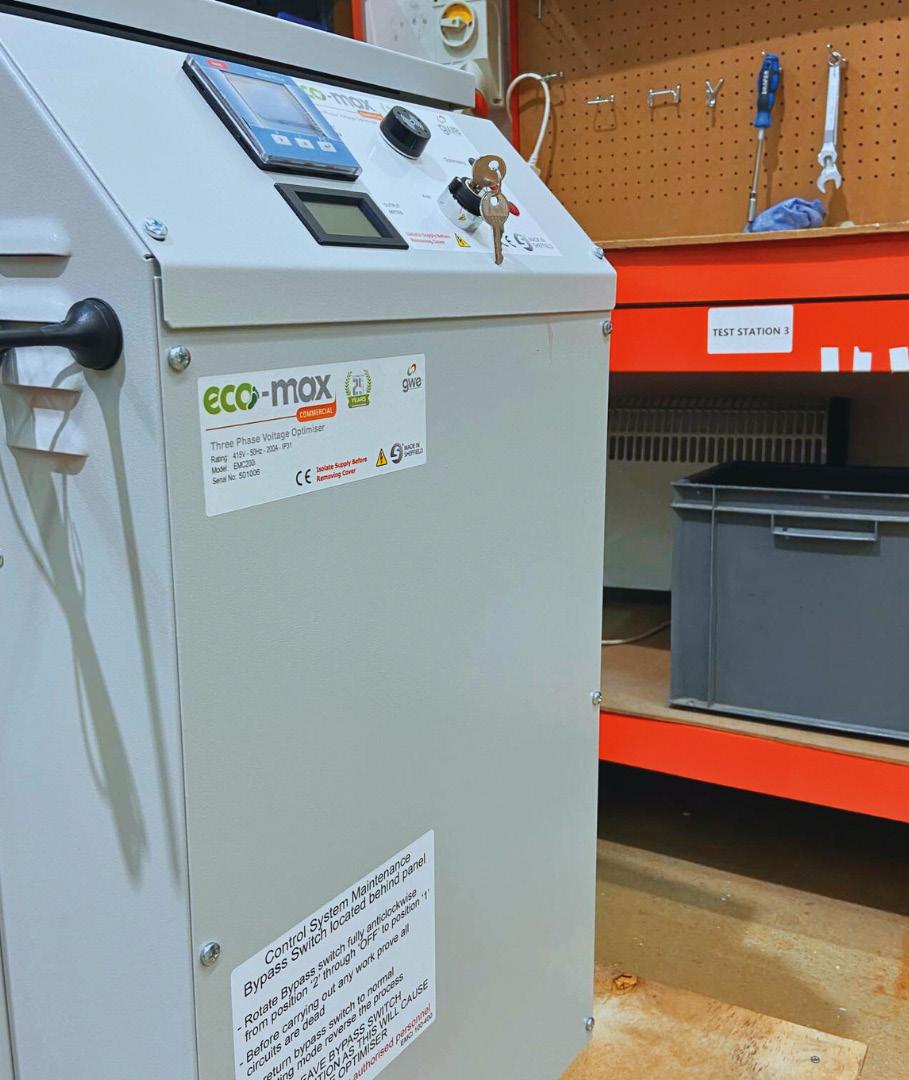
Working with a reputable VO manufacturer, they will carry out surveys and deliver a report to calculate how much you could save if VO was installed, as well as specify what solutions would be most effective.
Installation can be quick, with regular reports following to illustrate energy and cost savings.
“The Department of Energy Security and Net Zero’s Energy Efficiency in the Manufacturing Sector report showed that 32% of manufacturers who seek advice on how to improve their energy efficiency
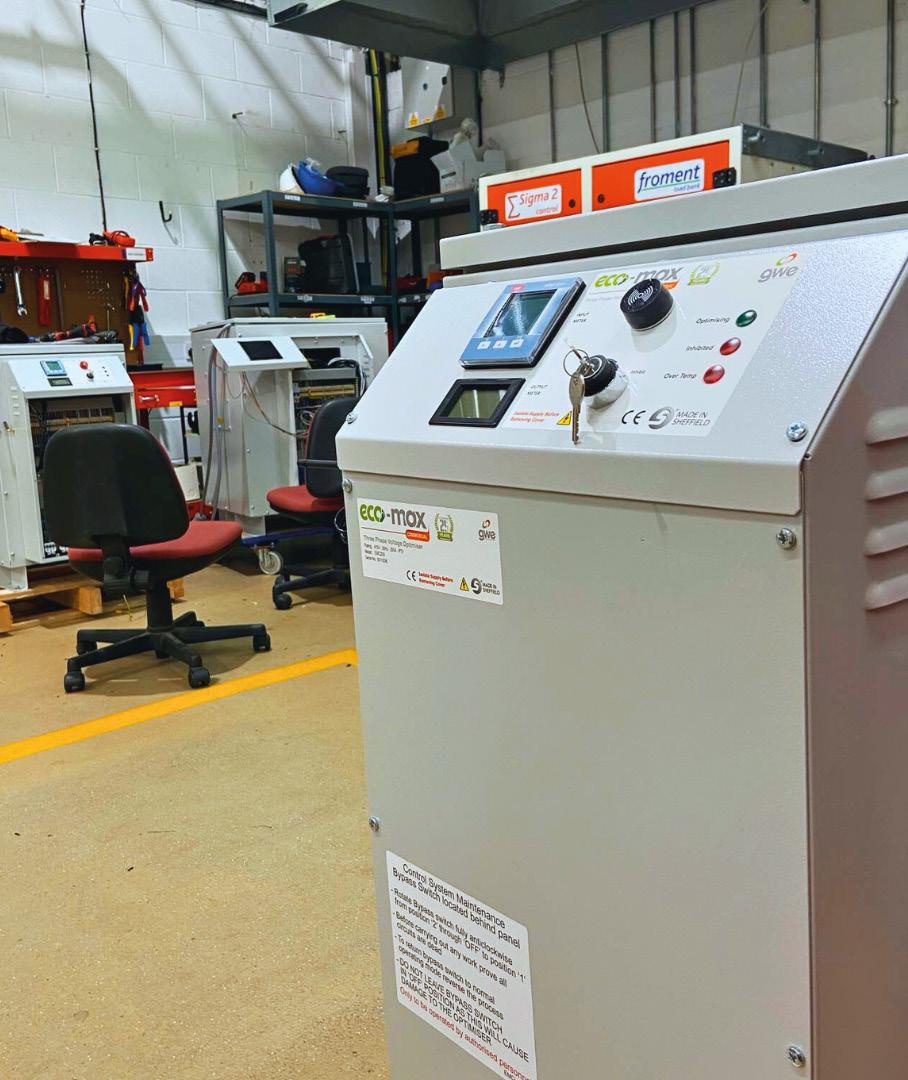
will contact external consultants, followed by 21% who will explore online tools and resources,” says Sarah. “It’s positive that nearly a third are seeking external advice, but manufacturers keen to explore how VO could help them should seek resellers and expert third parties who specialise in the technology and who can run the necessary surveys and audits to demonstrate what savings can be made. Online tools like this Energy Saving Calculator are also a helpful starting point.”
www.gwenergy.co.uk
MEET THE MD: SARAH CRAMER
What initially drew you to the sustainable energy industry?
The opportunity to be a part of a fundamental shift towards a healthier planet. Sustainability isn’t just a buzzword for me. It’s about making conscious choices, both personally and professionally, to minimise our impact on the environment. What excites me most is that these green practices often align with streamlining business operations. It’s a winwin for everyone.
Looking ahead, what are the biggest opportunities in the sustainable energy market?
The market is ripe with potential. Consumers and businesses are increasingly eco-conscious, driving
demand for innovative solutions like energy-efficient products. We’re seeing a significant shift towards renewable energy sources and a growing interest in technologies like VO that can significantly reduce energy consumption.
Why should manufacturers consider adopting VO?
VO offers a fantastic range of benefits for manufacturers. It allows for significant energy savings, which translates to lower operational costs and a reduced carbon footprint. This enhances your environmental responsibility and strengthens your brand image among eco-conscious consumers. VO also reduces your equipment
energy consumption, carbon footprint, and equipment replacement frequency.
What are the longterm implications for manufacturers who install VO?
Implementing VO positions manufacturers as sustainability leaders in their industries. Consumers are increasingly making purchasing decisions based on a company’s environmental practices. VO not only reduces energy usage but also demonstrates your commitment to a greener future. This forward-thinking approach can give you a significant competitive edge. www.gwenergy.co.uk
Longstanding leadership in sustainability
Established in 1983 by CEO Bob King, Humanscale is widely-respected as a global leader in the design and manufacture of ergonomic products. The company, which is headquartered in New York, first made its mark in the industry in the 1990s with the introduction of revolutionary articulating keyboard systems. This was cemented in 1999 with the launch of the Freedom chair, created by renowned ergonomics designer, Niels Diffrient. This executive task chair melded exceptional functionality with minimal manual controls – setting the tone for a further series of Diffrient seating designs.
Today, Humanscale operates in more than 28 countries, with an award-winning portfolio of office solutions spanning self-adjusting seating, sit/stand desks, monitor arms and task lighting.
Sustainability is truly entrenched in Humanscale’s creative process. Above all, the company designs for longevity, and this is front and centre from concepting
“Humanscale’s own factories are TRUE® Zero Waste certified and are third-party audited to ensure waste diverts at least 90% from landfills, the environment, and incineration”
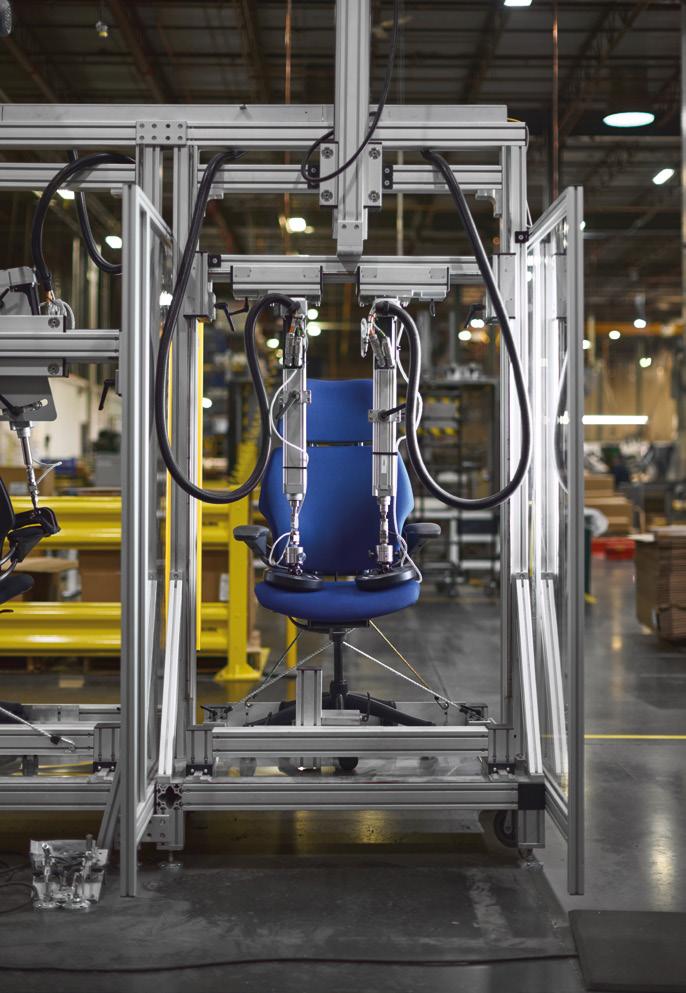
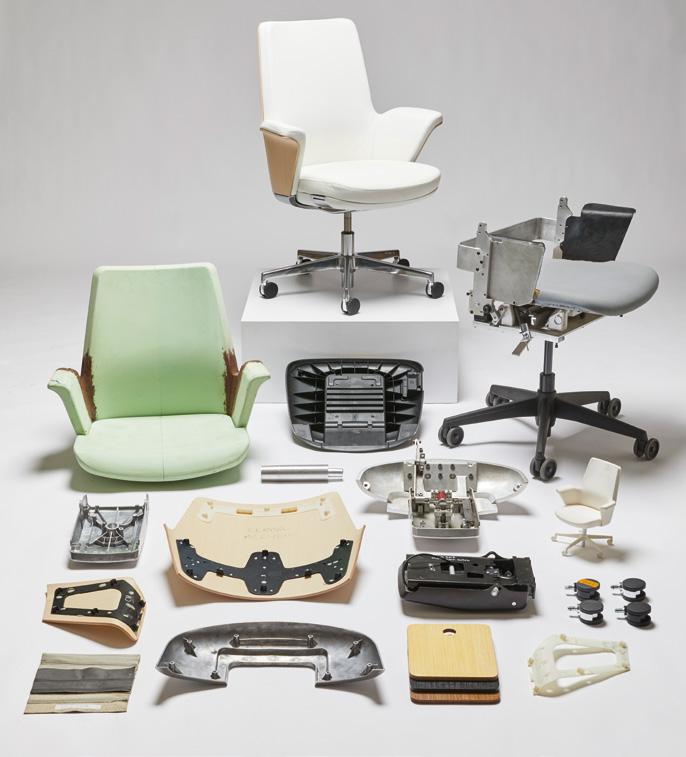
through to manufacture. Bringing the stunning simplicity and functionality that characterises the Diffrient designs through to the present day, Humanscale uses as few parts as possible, rejecting the waste of complex mechanics and components.
In addition to carrying out rigorous analysis and testing to ensure the maximum longevity for its products, Humanscale designs products that are ideally suited to being upgraded, refurbished or repurposed with minimal effort, even after their warranty period has expired.
Indeed, Humanscale’s own factories are TRUE® Zero Waste certified and are thirdparty audited to ensure waste diverts at least 90% from landfills, the environment, and incineration.
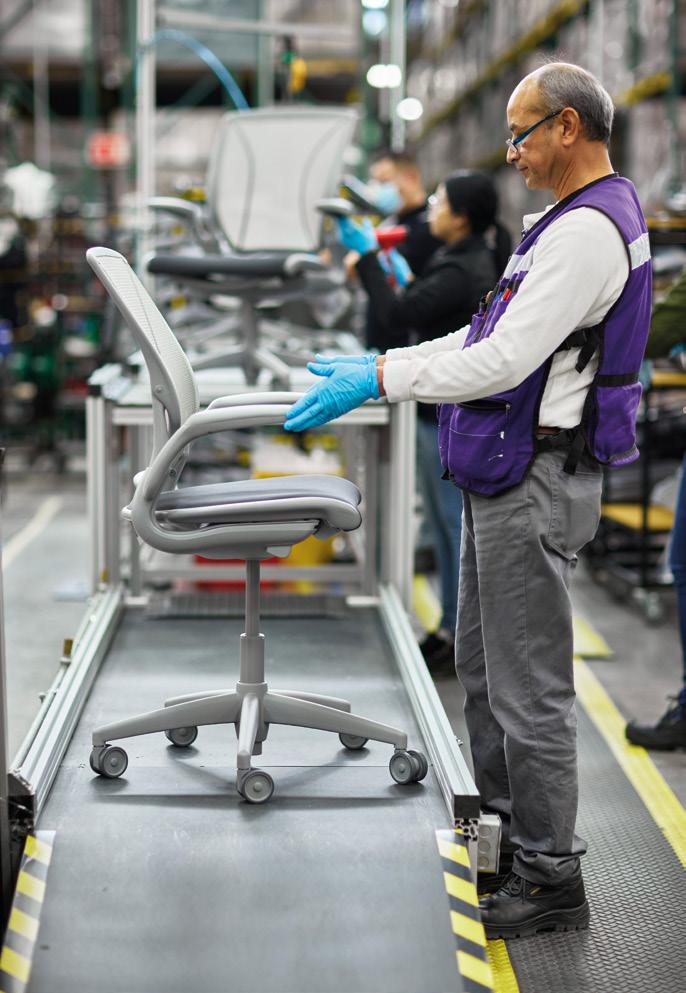

Humanscale’s overall ambition when it comes to sustainability is to create a net positive environmental impact, as opposed to just aiming for net zero. An impressive 70% of the products it sells are certified net positive.
In order to fulfil this goal, Humanscale has divided its targets into six crucial areas: climate & energy, water, circularity, wildlife preservation, and social responsibility.
Given the announcement in April of this year that Humanscale had earned B Corp Certification, it is clear the company’s dedication in this arena is paying off.
The company was able to meet B Lab’s rigorous standards for social and environmental impact; making a legal commitment to stakeholder governance, and demonstrating accountability and transparency by disclosing this record of performance in a public B Corp profile.
“At Humanscale, we believe that it’s our responsibility to ensure that both people and the planet are better off because we’re here,” concludes Bob King, Founder and CEO of Humanscale.
“We have led the industry in embracing systemic change for multiple decades, from implementing transparency labels on our products and eliminating many of the commonly used Red-List chemicals, to launching the world’s first task chair made from reclaimed fishing nets. By putting in the hard work and making tough decisions, we hope to lead the rest of our industry to be more responsible.”
www.humanscale.com
USM lays out ambitious 2030 sustainability targets
Modular furniture manufacturer USM, is making strides in its sustainable policy, following on from its 2021-22 Sustainability Report which detailed its ambitious future commitments.
The principles of circular design have been at the very core of USM’s philosophy since the 1960s. It was during this decade that Paul Schärer, the third generation of this family-run business, commissioned architect Fritz Haller to design a new factory and, two years later, created the iconic USM Haller modular storage system. With its modular nature and durability, this product was designed to be forever reconfigured.
In recent years, USM’s outlook on sustainability has extended circularity principles beyond its product portfolio, and seeks to apply this philosophy across the whole enterprise, from communications to operations.
Significantly, USM’s targets have been officially approved by the Science Based Targets initiative (SBTi) – the global climate action organisation which shows companies how much and how quickly they need to reduce their emissions to prevent the worst effects of climate
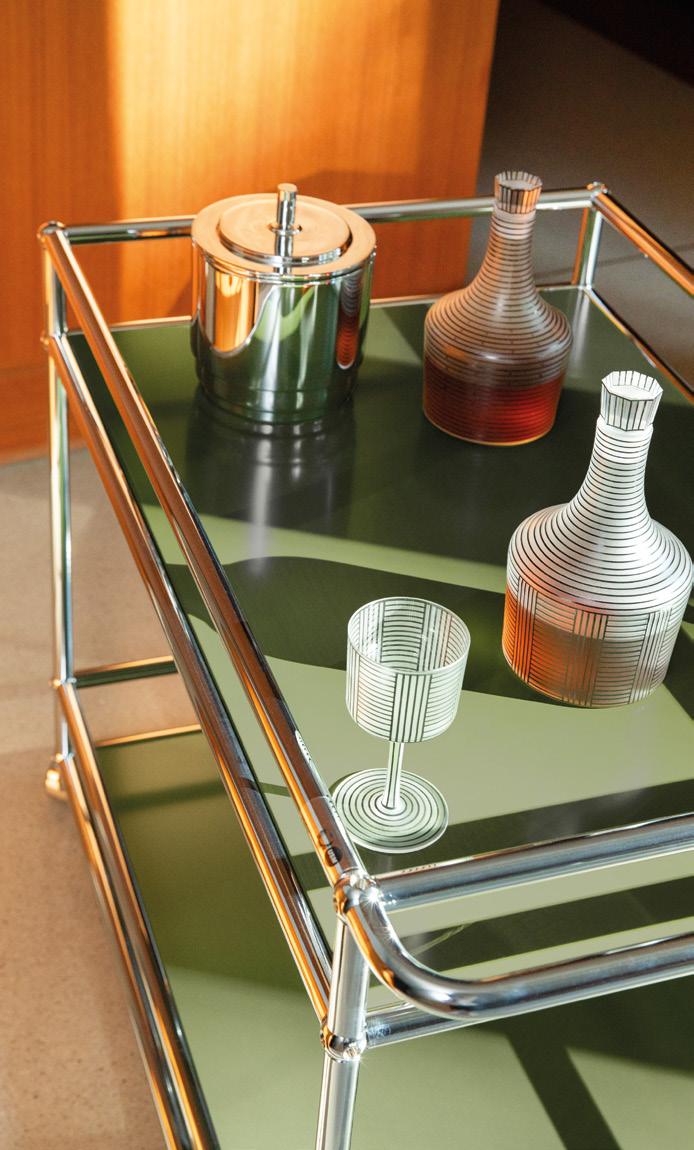
change.
“The target approval is an extremely rigorous process and we are proud to have achieved this status,” comments Ian Weddell, USM Sustainability Executive.
“The SBTi commended our targets for our operational emissions, currently the most ambitious designation available through the SBTi process.”
USM has committed to reducing absolute scope 1 and 2 GHG emissions by 42% and scope 3 emissions by 25% by 2030 (from a 2021 base year). Scope 1 and 2 refers to operational emissions directly within the company’s control, such as heating, electricity and combustion from its vehicle fleet. Examples of scope 3 emissions include production materials, purchasing of manufacturing equipment, logistics (supply and distribution) and commuting.
Within the sustainability report, USM laid out its roadmap for emissions-reduction. Key measures include purchasing CO2-reduced steel for 20% of supply in 2024, applying air freight policies and electrifying its vehicle fleet.
“Reducing our emissions at such a challenging rate is a stimulating challenge for a company with such a rich heritage in design and engineering,” comments Dr Thomas Dienes, Director of Sustainability at USM.
“One of the solutions that appeals to us the most is the circular economy. The flexibility and longevity that comes with a modular system such as USM Haller brings enormous opportunity for reuse, repair and remanufacturing as well as different business models like rental or furniture-as-a-service. We are exploring how these can work for our customers in order to fully maximise the lifespan of our products.”
In addition to its science-based targets, USM also holds Cradle to Cradle certifications for its two main product lines, USM Haller and USM Kitos M, and Greenguard Gold certification for USM Haller and USM Kitos.
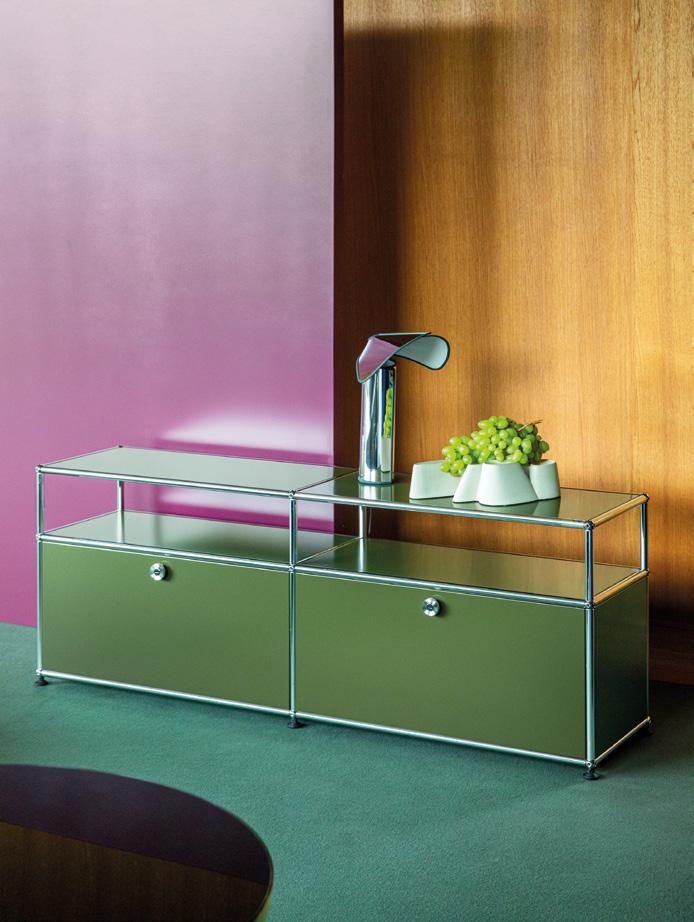
“The flexibility and longevity that comes with a modular system such as USM Haller brings enormous opportunity for reuse, repair and remanufacturing”

It’s inspiring to witness a company re-evaluate its approach right across the board, ensuring that every aspect of the business is performing in as sustainable a manner as possible. Given its dedication and the ambitious nature of its targets, USM’s progress will certainly be something to behold.
www.uk.usm.com
Q&A – Steve Winscott Managing Director at Nine Zero Timber Windows and Doors
Could you provide a brief overview of the business as a whole?
Nine Zero is a manufacturer of bespoke timber windows and doors. The business was born in 2017, merging 30 years of business and joinery experience at just the right time. Our roots stem back to 2005 when our sister company launched a window and door business, choosing products specifically suited to London properties. We gained extensive knowledge through development and market research, which led us to manufacturing.
At first, we researched overseas, as was common in the industry, but soon realised the logistical challenges of a long supply chain. This brought us back to the UK, where Cornwall stood out as a growth hub for construction. Our mission was, and is, to surpass the standards of overseas mass production, often plagued by quality and time management issues. We’ve made significant investments, resulting in major growth and advancements – like our 6,000 sq/
ft workshop in Cornwall and cutting-edge digital systems.
Could you tell me a little more about the sustainable initiatives the company has adopted, please?
At Nine Zero, sustainability is key in everything we do, especially in how we manufacture our sustainable timber windows and doors. By using FSCcertified suppliers, we are supporting global forestry conservation efforts, and ensuring our customers receive products made from materials that are as ecofriendly as they are exquisite. We also
“We want to keep the sustainability conversation alive by educating and supporting our trade customers to feel confident in selling timber windows and doors, and meet the demand we know is going nowhere but up”
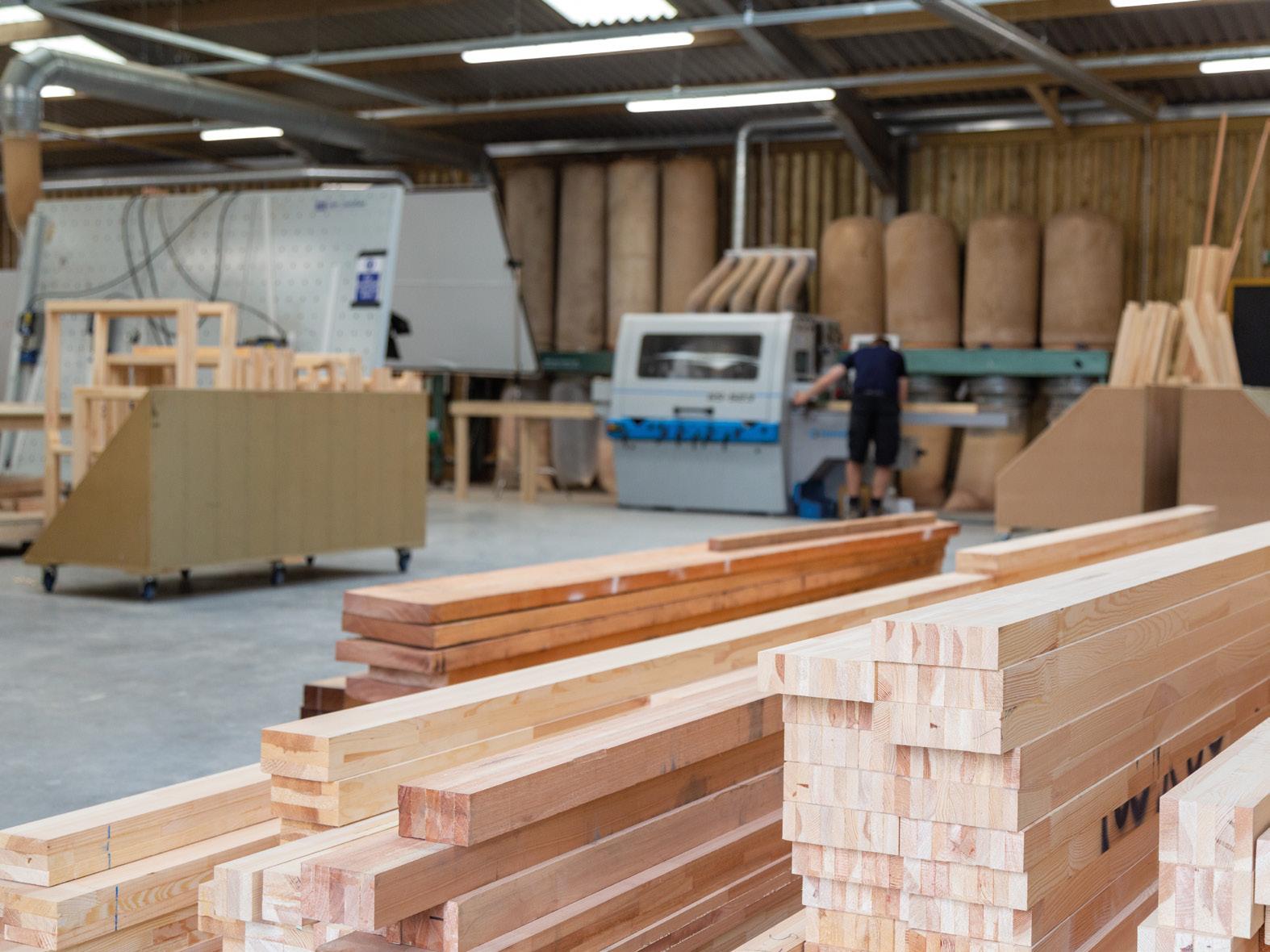

recycle timber waste, provide renewable energy to local homes, plant a tree for every order we take, and partner with Pozitive Energy for green electricity. We repurpose leftover timber for animal bedding and composting, helping local farms and reducing landfill waste. The energy we generate from recyclable materials is converted into renewable power for local homes, promoting a greener community. We work with a company called More Trees to plant a tree for every order we take. As an example, last month this equated to 165 trees being planted in Rwanda. We also use Pozitive Energy to ensure our operations use electricity from renewable sources like solar and wind.
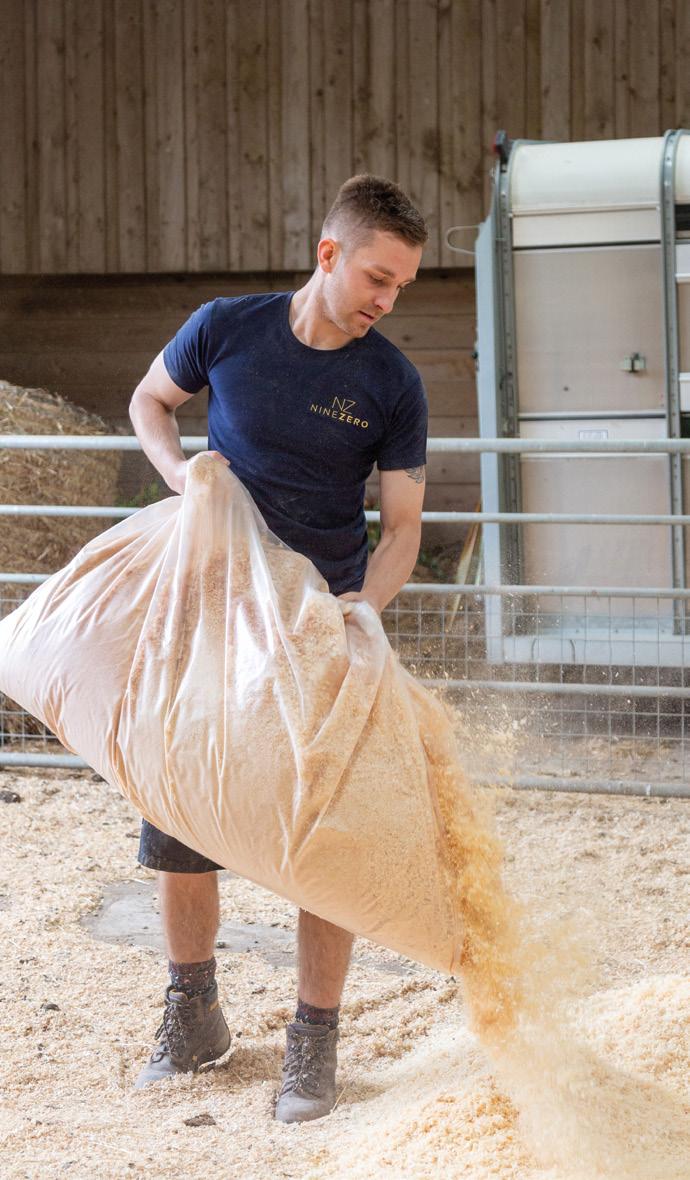
“The energy we generate from recyclable materials is converted into renewable power for local homes, promoting a greener community”
What are you noticing in terms of your customers’ awareness/attitude to sustainability, and how have customers responded to the sustainable measures you’ve put into place?
The industry shift towards eco-friendly and sustainable building materials has never had so much momentum. With the uncertainty around Building Regulations, we have seen within the window and door industry this year, it has become critical for installers to understand the environmental implications of the materials they are using – as more and more of their business depends on it. Regardless of where legislation takes us, we know that homeowner demand for sustainability is only getting stronger. In fact, a study by Ovo Energy earlier this year revealed 83% of active British homebuyers are seeking properties with energy-efficient upgrades, reduced carbon emissions, and high EPC ratings.
What do you feel are the main challenges you and the wider timber industry face in terms of meeting your sustainability targets?
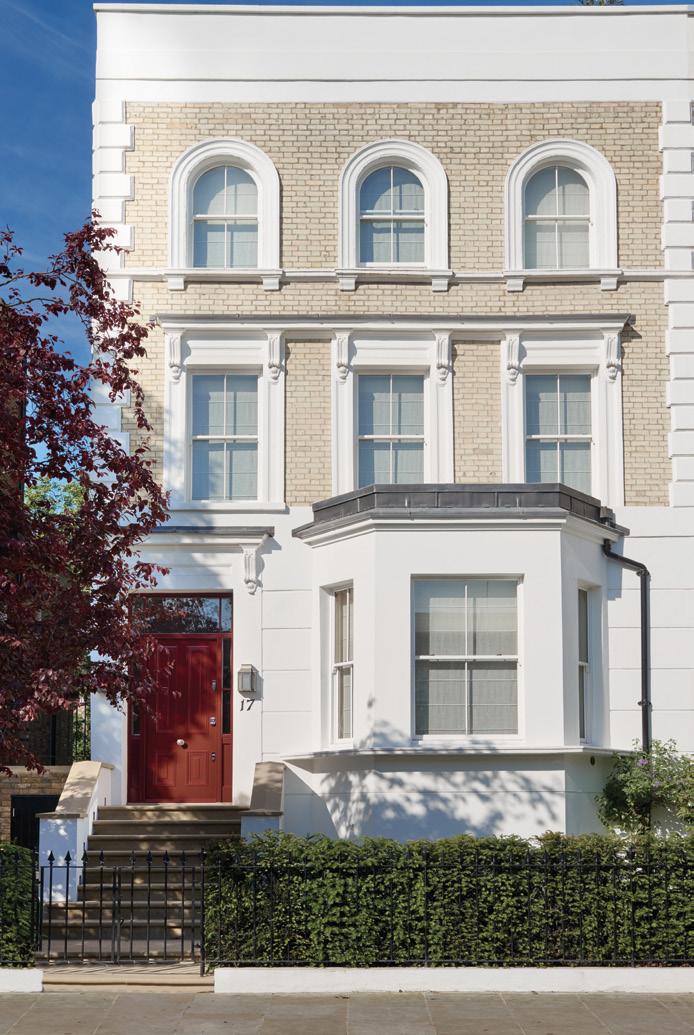
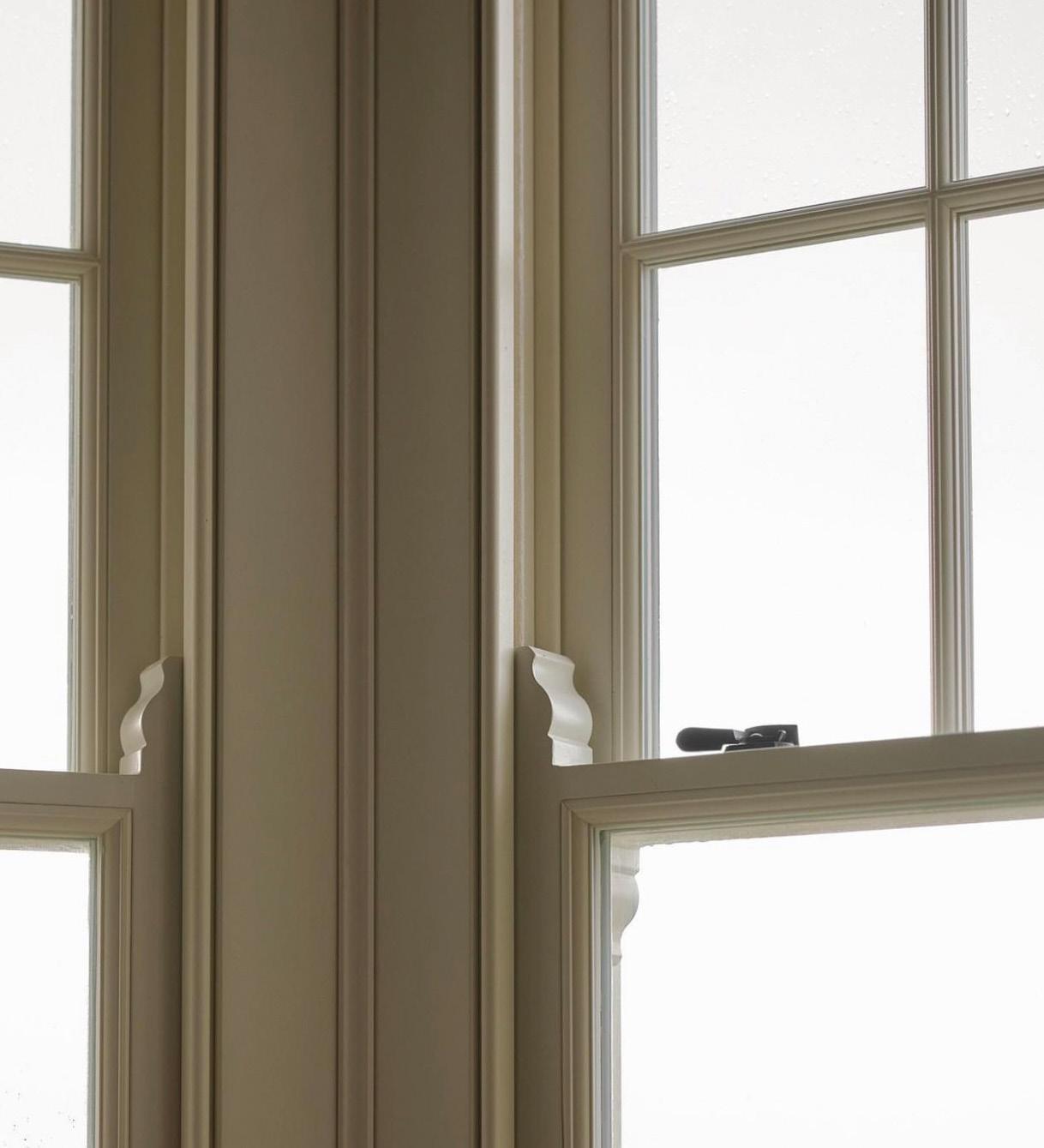
We’re still in the education phase for timber products. While awareness has grown, more needs to be said about its sustainability and insulation benefits. Timber absorbs CO2 during growth and, when harvested responsibly, has a sustainable life cycle. It’s also energyefficient, reducing consumption and costs. There’s a misconception about
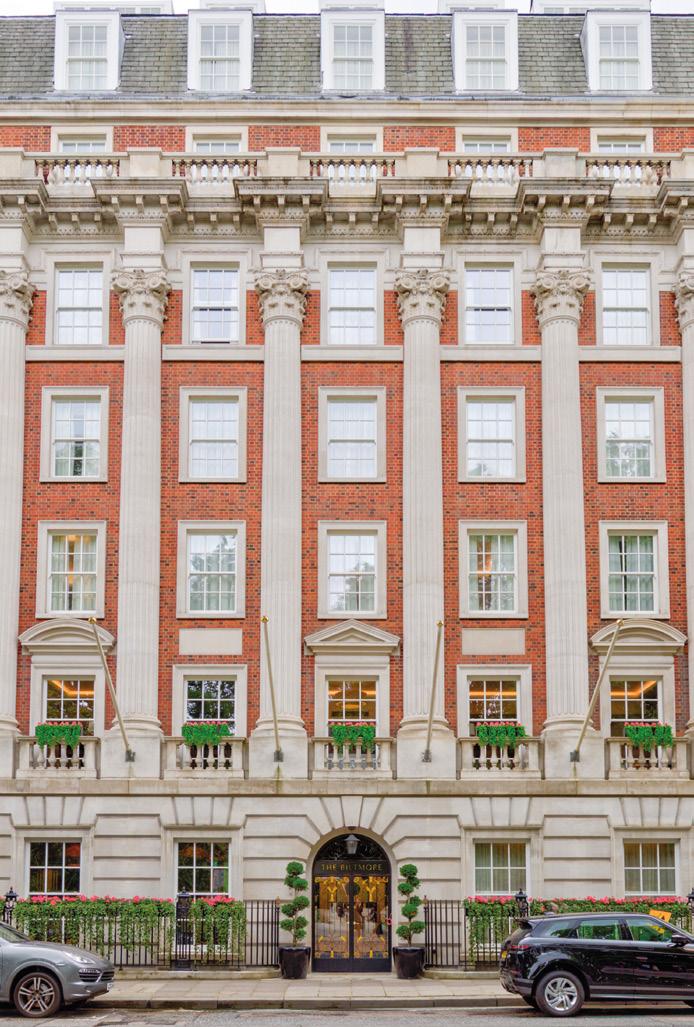
the costs associated with timber on the whole. Timber windows and doors, when considering their whole life cost, are 14-25% more cost-effective than other materials. Though initial outlay may be higher, construction with timber is quicker and easier, lowering labour costs. Plus, timber requires less maintenance and is more energy-efficient, saving money on repairs and energy bills over time.
What are Nine Zero’s plans for the future with regard to sustainability?
We want to keep the sustainability conversation alive by educating and supporting our trade customers to feel confident in selling timber windows and doors, and meet the demand we know is going nowhere but up.
We’re passionate about preserving London’s traditional heritage homes, and our experience means we join the dots between maintaining heritage, ensuring quality craftsmanship and providing sustainable, high-performance timber products using cutting-edge CNC technology.
www.nine-zero.co.uk
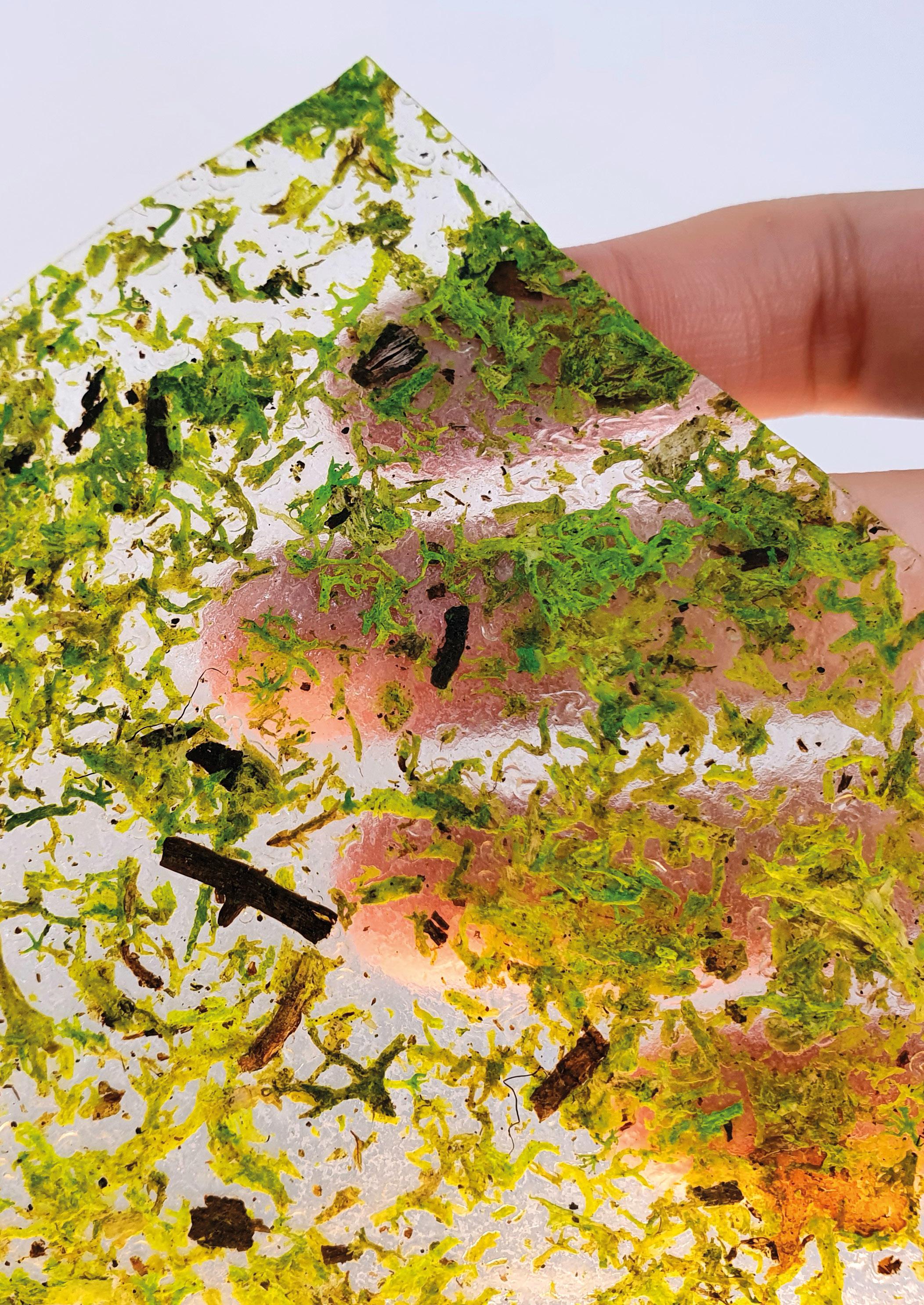
Organoid® – creators of immersive natural worlds
Organoid®’s spectacular surfacing designs are as exceptional and naturally beautiful as the company’s locale in the heart of the Tyrolean Alps.
Company founders, Christoph Egger and Martin Jehart, were united by their shared drive to create something meaningful and sustainable for the common good. They began to experiment with organic shapes in a barn, with the help of Alexandra Jehart & Marco Unterlercher, and in 2010, after several years of product development, Organoid® natural surfaces came to fruition.
Organoid®’s designs have multiple applications, whether it be as a decorative element in sustainable furniture making,
“From
upcycled moss and handcut hay,
to a beautiful array of delphinium, lavender, marigolds and cornflowers, Organoid®’s designs create a sensory experience for the end user”
or indeed as wallpaper, on glass or for lighting elements.
Since its founding years, Organoid® has gone from strength to strength. From moving into its headquarters in Fließ Nesselgarten in the heart of the Alps and partaking in exhibitions on the international stage, to the launch of a semi-automatic production line with rolled goods, the company is determinedly finding its feet.
Today, the company has a new CEO team – Christoph Egger & Florian Föger – and an expanded portfolio and reach, but it has stayed true to its founding principles of sustainable and authentic surfacing that enriches wellbeing.
As you’d expect from a company that works so symbiotically with natural materials, Organoid® demonstrates the utmost regard for the environmental impact of its operation. The company is rightly proud to call itself “climate-neutral”, utilising 100% green energy in its plant and actively avoiding or reducing CO2 emissions wherever possible.
In cases where emissions are unavoidable, Organoid® offsets them by supporting a climate protection project. Strict criteria are applied when selecting the raw materials for its products, with a focus on regional, rapidly renewable and upcycled materials. From upcycled moss and hand-cut hay, to a beautiful array of delphinium, lavender, marigolds and cornflowers, Organoid®’s designs are not simply aesthetically pleasing and sustainably produced, but create a sensory experience for the end user. Materials such as the Alpine hay and flower petals are sourced from farmers in Organoid®’s close vicinity. In this way, the company is active and demonstrative in the way it supports local farmers and works to create value in the region. Organoid®’s portfolio gives these natural materials a new lease of life, with the added reuse of food waste such as peppermint and spelt. Any leftover material is donated to local social institutions or kindergartens.

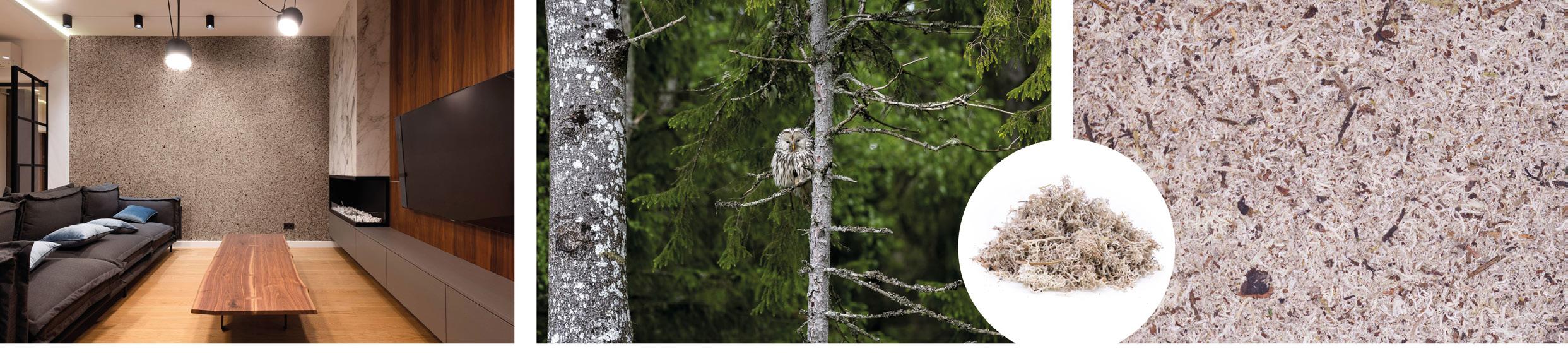
Zirbenwald
Moos Grau
Organoid®’s new collection for 2024 brings all these elements together to create inspiring sensory experiences inspired by the boundless abundance of nature. The collection draws upon themed natural worlds, from “Forest Bathing”, to an “Alpine Paradise”. These worlds are explored in more detail within the striking 2024 collection book, produced in high-quality linen and full of inspiration and technical detail. Four new, masterful creations made from the finest natural materials have been unveiled within the new collection:
ZIRBENWALD
This surface evokes the effects of the Austrian stone pine forests, incorporating real Austrian stone pine, fern, moss and needles. These ancient trees only grow in certain Alpine regions and altitudes in the purest, clearest mountain air. Its fragrance is thought to have an extraordinary effect on our body and mind, bringing inner peace, balance and a restful night’s sleep.
MOOS GRAU
A Nordic-inspired forest experience, thanks to the elegant light grey surface with mystical upcycled moss. The moisture-regulating properties of the moss create a feeling of freshness.
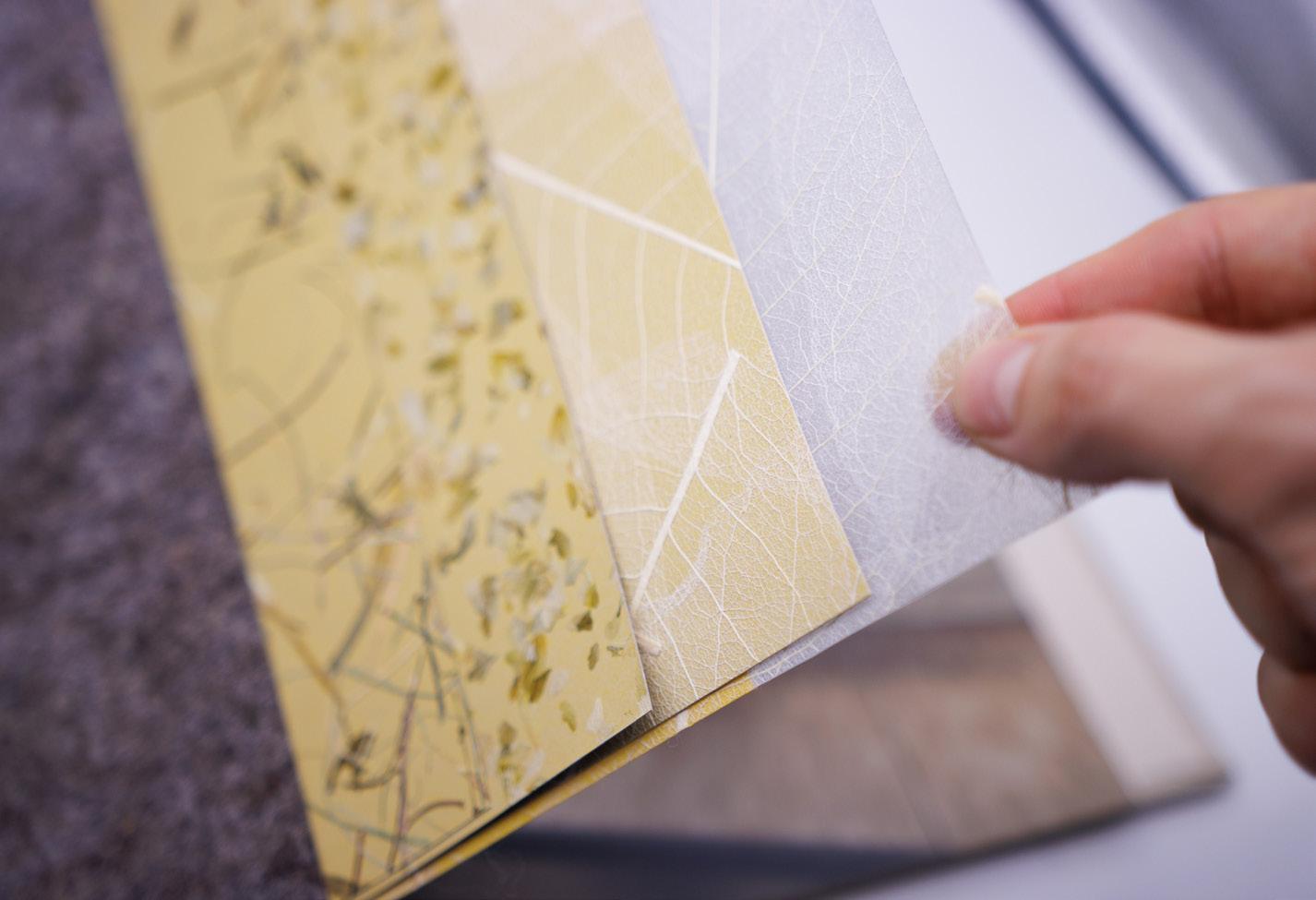
CARPE DIEM
Carpe Diem is designed to capture the scent of the Mediterranean, bringing Summer, sun and pure relaxation, thanks to its delightful blend of olive leaves, Greek mountain tea, magnificent cosmea flowers, delphinium, lavender, marigolds and cornflowers on natural flax fleece.
WILDSPITZE GOLD
Wildspitze Gold is a design of contrast – the rustic charm of genuine, hand-cut hay from the Tyrolean Alps meeting
glamorous gold paper. The elegant contrast of golden shimmer and hay is reminiscent of delightful, warm summer evenings in the Alps. There are many companies with mightily impressive sustainability policies, but those such as Organoid®, who live and breathe the natural world, harnessing its beauty while respecting and safeguarding it from beginning to end, are far and few between.
+43 5449 200 01 info@organoids.com www.organoids.com

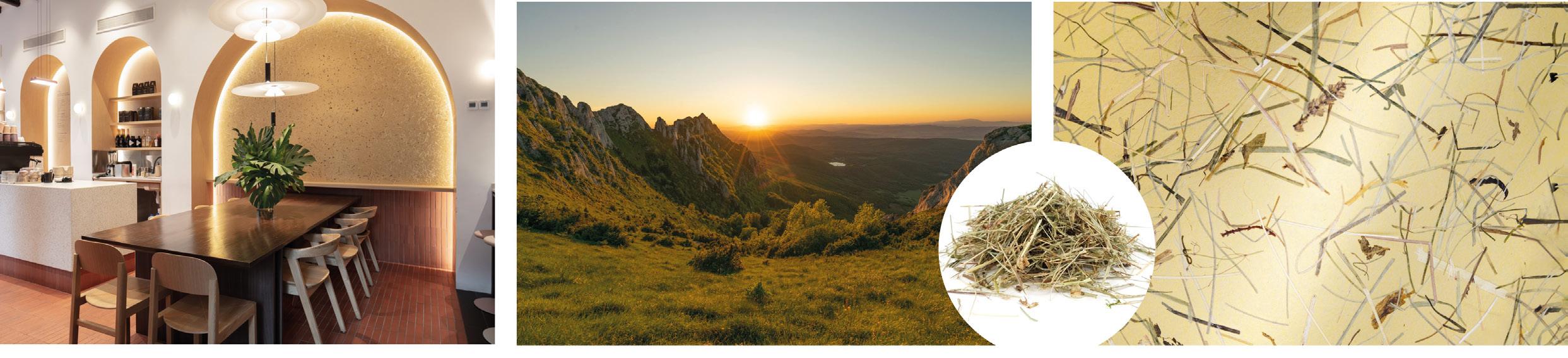
Carpe Diem
Wildspitz Gold
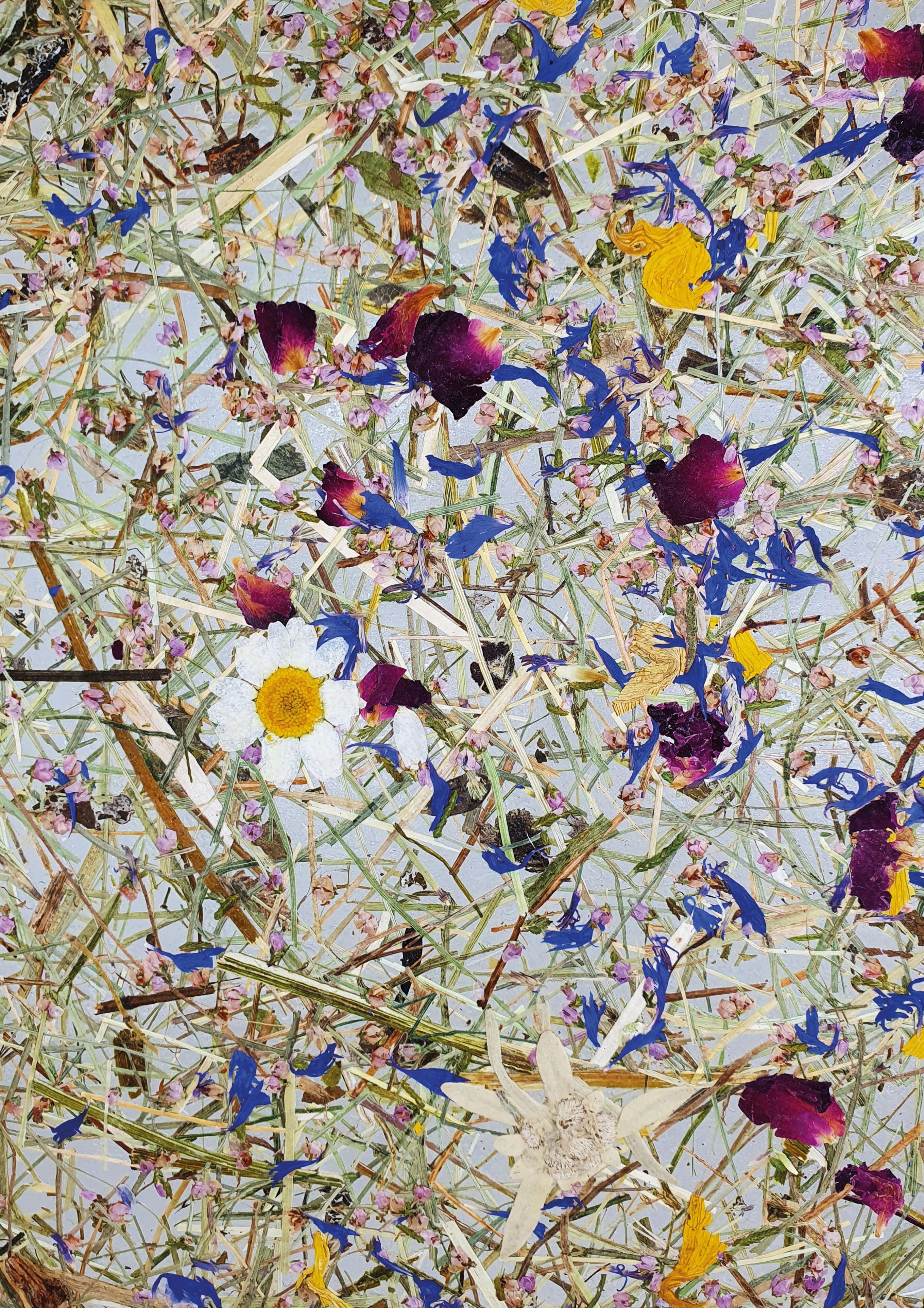
How Blum is helping protect our planet for the future
Promoting everything from the circular economy to biodiversity, transport power and social responsibility

Sustainability and long-term thinking are core values of Julius Blum GmbH, a world market leader in furniture fittings. The Austrian family-owned company, which was first granted ISO 14001 environmental accreditation in 1997, has implemented countless initiatives to promote sustainability within its own business and beyond under the tagline ‘moving ideas for sustainability’.
United Nations 17 Conventions –sustainable development goals
The overarching ethos that Blum endeavours to live and work by has been long established, but in today’s world can be encapsulated in the UN17 SDGs. These range from no poverty and zero hunger, through to climate action, and good health and well-being. In the UK, Blum partners
with some local non-profit organisations and charities, donating time, money and physical things such as furniture from exhibitions, merchandising and left-over food. This forms the basis of all the brand’s physical goals and endeavours in the business as well, all of which are led by Blum in Austria.
Using waste heat and promoting biodiversity
One area highlighted is Blum’s efforts to develop a sustainable energy supply: 95% of the company’s ventilation systems are now equipped with heat recovery technology, meaning that in spring and autumn, the Blum plants in Austria are heated entirely using the waste heat from its production processes.
The company also uses district heating,
“We understand our responsibilities as an industry player and want to take action wherever we can” company owner and CEO, Philipp Blum
groundwater cooling and solar systems installed at its premises. The vast majority of its buildings are compact, multi-storey structures in order to minimise land use, and in the last 40 years, Blum has optimised its space utilisation by 35%.
That means that for a 14,000 m2 plot, the business now boasts 50,000 m2 of usable space, saving the equivalent of five football pitches’ worth of land, which can instead be preserved as near-natural areas.
Transport
Fittings manufacturer Blum has developed an environmentally-friendly round-trip concept for container transport between Blum Austria and Blum USA. Thanks to its partnership with JCL Logistics and international shipping company ICL, containers have been successfully shipped to the USA by rail and water.
Blum’s Transport Logistics department teamed up with Independent Container Line (ICL) and JCL Logistics and set themselves an ambitious goal: To not use roads at all from Dornbirn to Charlotte. And they did it by developing an environmentally-friendly round-trip concept. “The key to success was to come up with an intermodal solution using water and rail transport,” explains Ingmar Blum, Head of the Transport Logistics team at Blum. Trucks were to be used only sparingly or as a backup. In fact, road transport is only used for some of the containers for the last few kilometres from the train station in Charlotte to Blum USA in Stanley.
The intermodal round-trip concept works as follows: Every week several containers embark from Blum’s logistics centre in Dornbirn, Vorarlberg to Blum USA. The containers with goods destined for the US subsidiary are loaded directly onto the train in the sidings of the logistics centre. They are transported by rail to the Wolfurt terminal and from there to Neuss, Germany. No time is lost due to traffic congestion. As well as speed, the clear advantage of this mode of transport is its
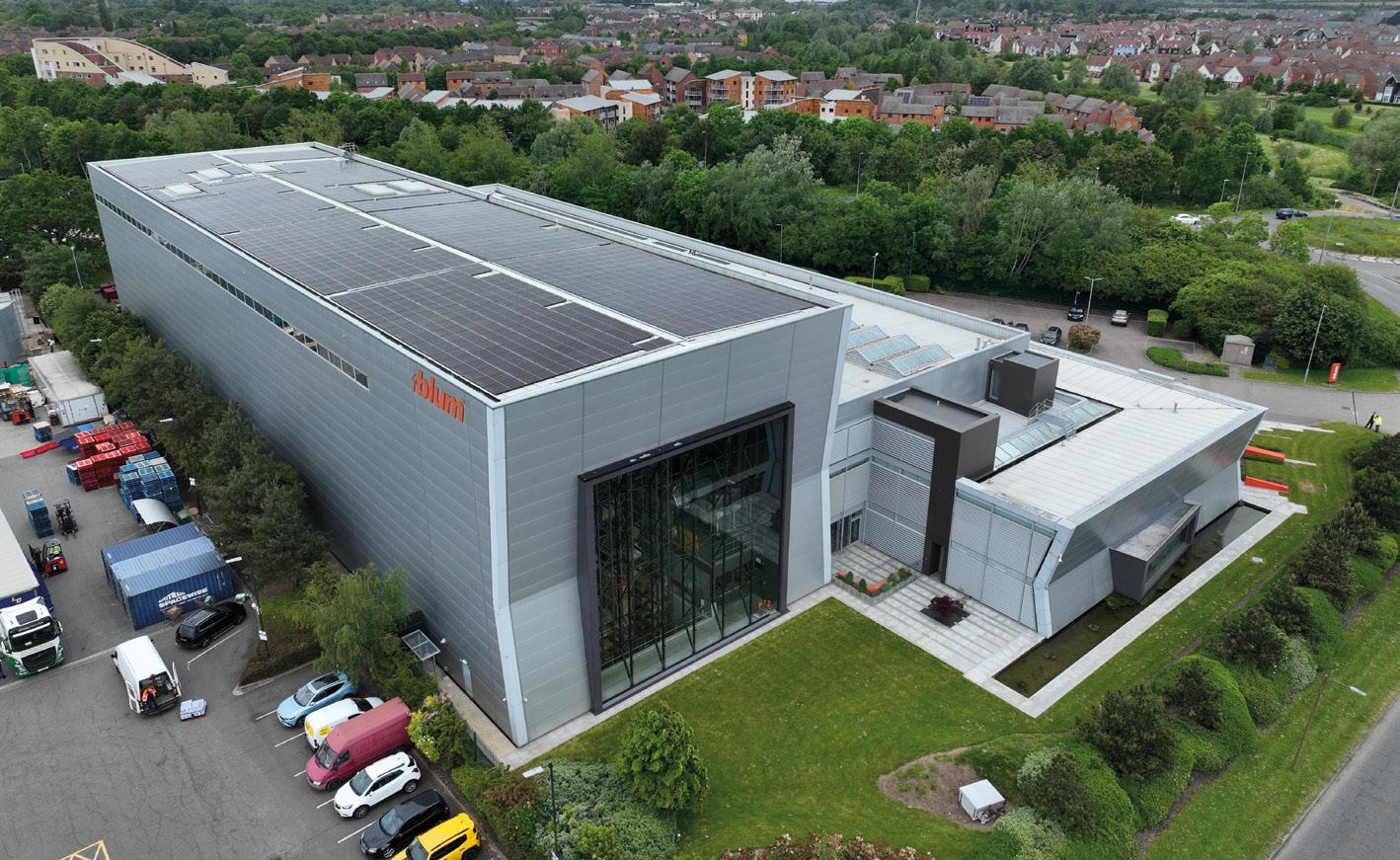
sustainability: According to data from the Environment Agency Austria, the average truck produces 85.7 g of CO2 per tonnekilometre. In contrast, transporting goods by rail produces just 2.8 g of CO2 per tonne-kilometre (as of July 2023*). On top of this, it also reduces traffic on the roads. Once at Neuss, the containers switch to a different mode of transport. A barge chartered by international shipping company ICL takes the goods to the port in Antwerp via inland waterways. “Marine and waterway services have made major steps in terms of sustainability in recent years. Freight movement by barge is a highly-efficient mode of transport, so why not benefit from it ourselves? Transport by barge is head and shoulders above road transport, especially when it comes to noise, tyre wear and particulates,” says Ingmar Blum.
ICL provide targeted barge services in order to control the supply chain
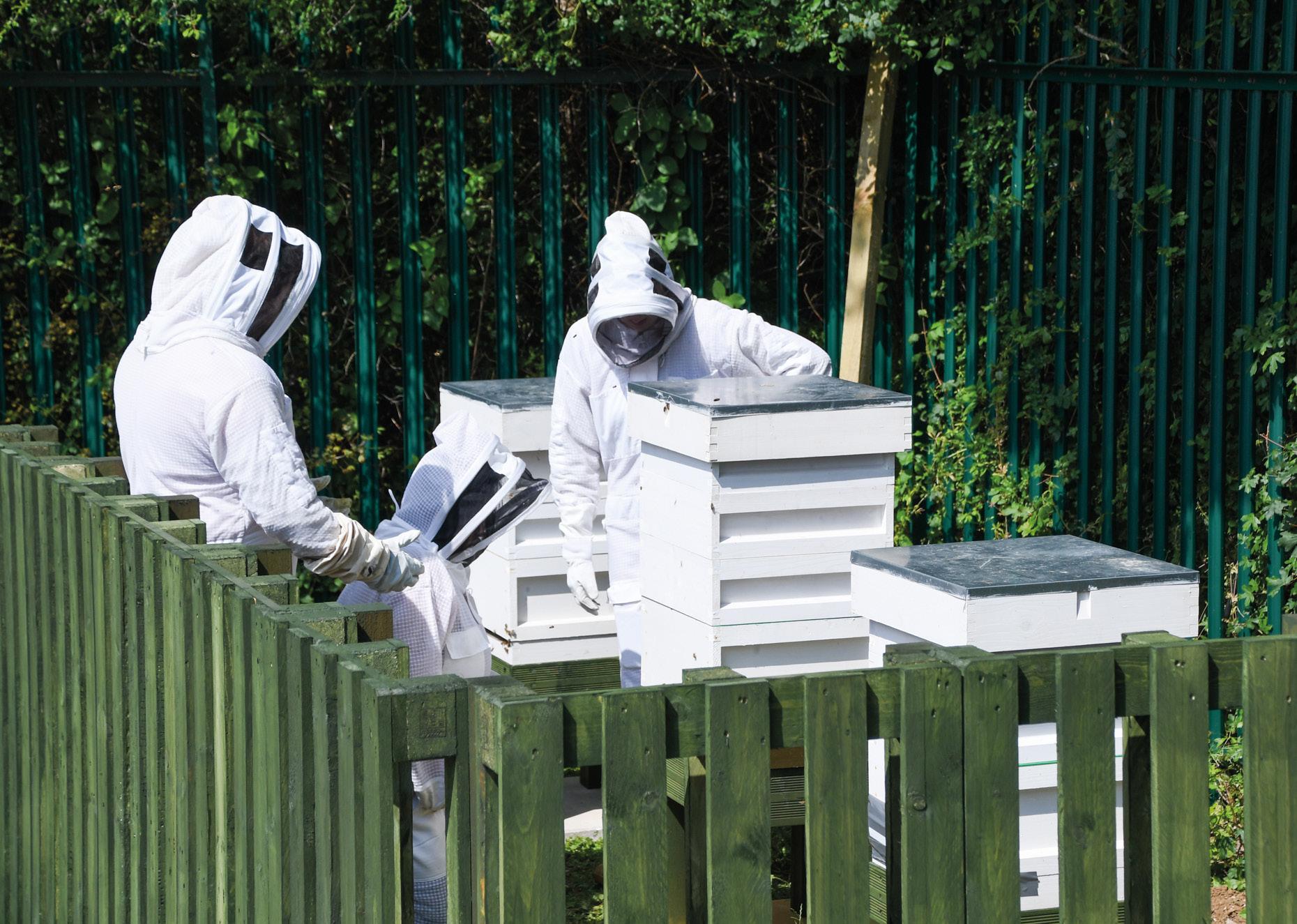
“In the UK, Blum has recently installed 904 solar panels on its UK headquarters’ roof, generating 75% of the building’s power needs and estimated to save 94 tons of carbon per year”
themselves and ensure excellent throughput times. This means that there is a timely connection to deep sea shipping services in Antwerp, and all ports and transfers can be monitored to ensure smooth round-trip transportation. In turn, this means reliable deliveries to customers. The containers are shipped along the Rhine to Antwerp, where they are loaded onto an ocean-going vessel to begin their journey across the Atlantic.
Once they arrive at the port in Wilmington, some of the containers continue their journey by rail again. The train takes them to Charlotte, and it is only at this point – for the very last few kilometres of their journey – that they are loaded onto trucks to reach Blum USA in Stanley, which is around half an hour away. “It would be unrealistic to think that such a long and complex container journey could be done without any trucks at all. But we have come as close as currently possible to a solution without road transport,” reports Ingmar Blum, adding: “Nonetheless, we’re looking ahead and planning to reduce the number of truck trips even further and transport all containers from Wilmington to Charlotte
Blum UK
by rail, rather than only some. In the long run, we want to apply this or similar concepts to as many routes as possible. We also hope that many will follow our example.”
In practice, the mode of transport depends on several different factors such as the rail infrastructure, the destination, the freight and customer requirements.
The containers’ journey does not end in Stanley, USA, however. Return transport is provided through collaboration with ICL. To avoid empty runs, goods are also transported on the return journey. Thanks to its customer base, ICL can ensure a load factor of 95 percent in both directions. The strategy of establishing closed-loop routes not only enhances efficiency but also ensures continuous availability.
“With ICL and JCL, we have two experienced partners, who fully support us in our efforts to use more sustainable transport and come up with innovative ideas for new solutions,” says Ingmar Blum in praise of this partnership of equals and adds “In the long run, we want to keep our CO2 emissions as low as possible and we are working day in day out to reach this goal.”
Green Roofs
Blum has been greening its roofs for over 20 years now – six of its eight plants in Austria have green roofs. These cover every area where they are deemed suitable for the company’s infrastructure development plans and where the building’s structure will allow it. At Blum’s
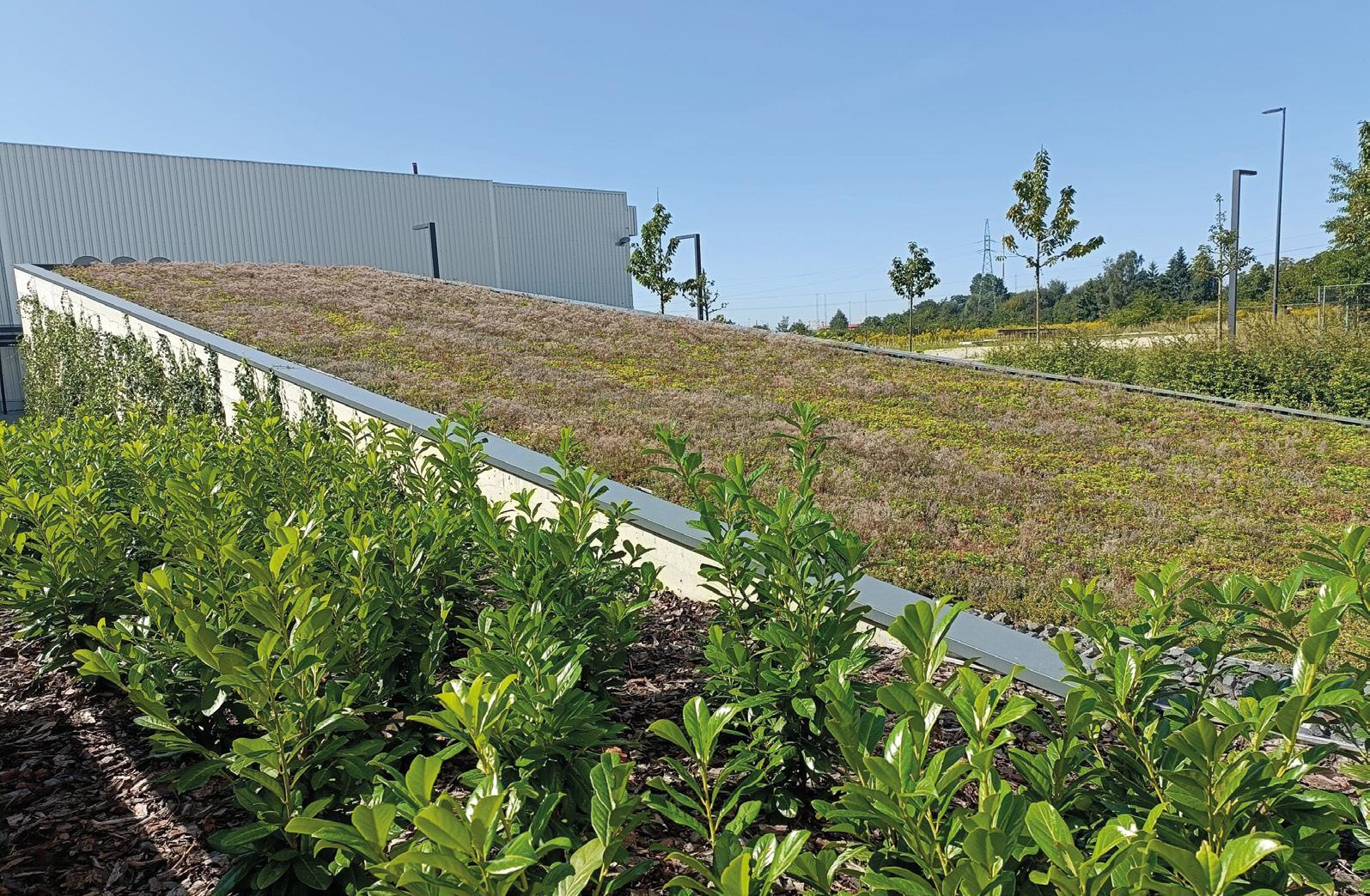
plant in Poland, more than one hectare of the roof’s surface will be greened in the final expansion stage.
“A green roof has so many advantages that speak for themselves,” comments Laura Erhart, Project Manager for biodiversity and outdoor design at Blum. She notes that these include a natural insulation effect that compensates for temperature fluctuations in the building, reducing the need for cooling in the summer and heating in the winter. Plus, green roofs bind CO2 and particulates and act like a filter that helps give us a healthier environment in which to live and work.
Erhart also mentions a number of other positive effects, including a certain reduction in noise as well as water retention when it rains, which reduces the load on the sewer system. “Given these advantages, it’s worth the effort,” she says, referring to the construction measures that – providing the building’s design and structure will allow it – can
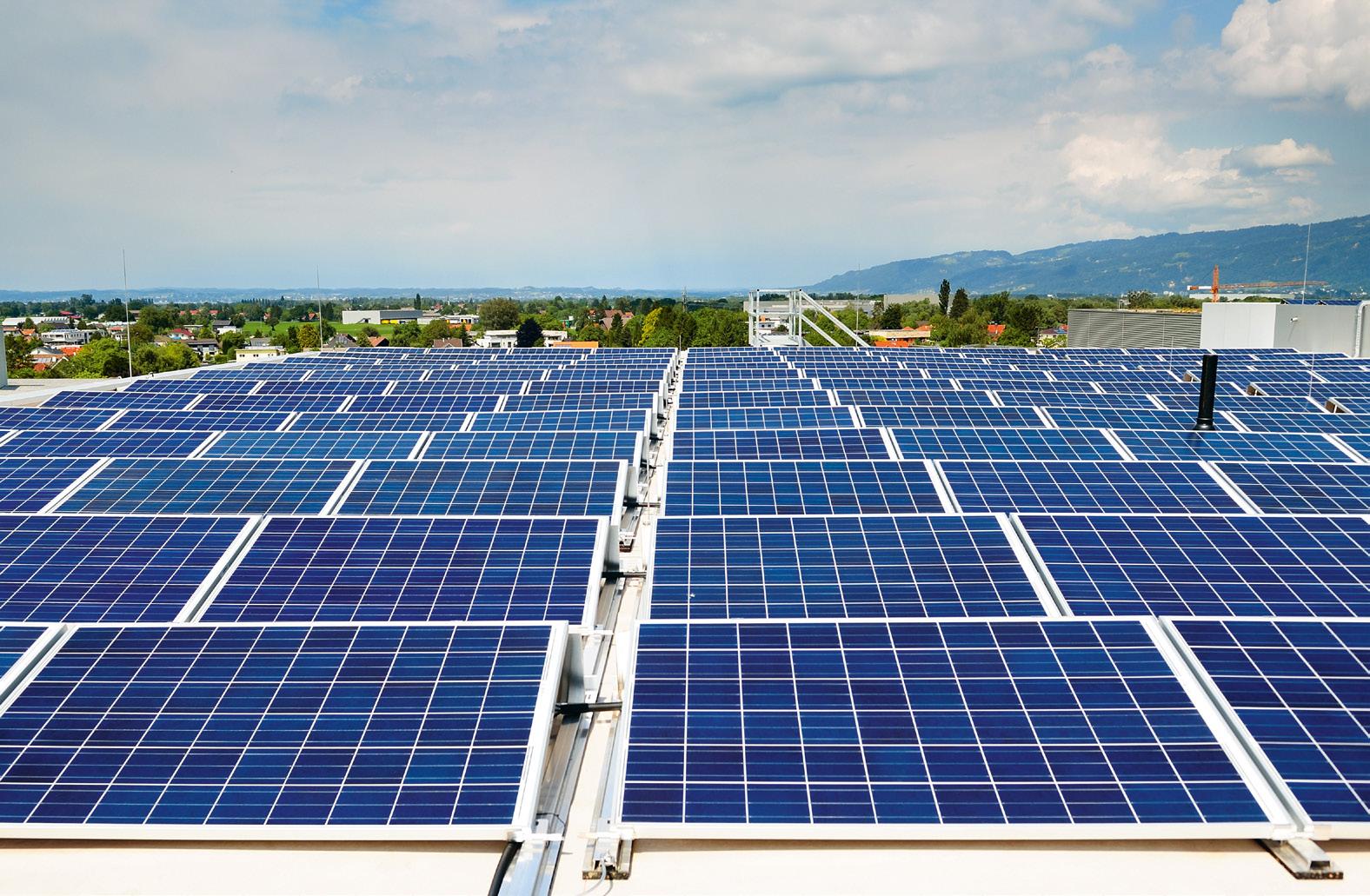
be put in place with regard to sealing and drainage before the actual greening can begin, which involves applying substrate enriched with organic material and the plants themselves.
Once planted, the spaces created by greening provide a new habitat for many different species of flora and fauna. And Blum makes an effort to not only maintain but enhance biodiversity in its own infrastructure where possible. In keeping with its sustainability targets, the company sets up additional green areas on roofs and façades and enhances the ecological value of existing ones. This also includes targeted measures aimed at maintaining the diversity of species, such as designing roofs to be “insect-friendly” using various materials such as sand and gravel. In this case the subsurface is shaped such that it offers suitable nesting places for insects, as demonstrated on an area covering more than 7,300 m2 on the roof of Plant 6 in Gaißau. “There are also extra piles of dead wood where they can hide,” explains Laura Erhart, “and a number of small biotopes help them get through longer dry periods and create a habitat for additional species with standing water. The effort involved in this is manageable and is basically limited to maintenance work that has to be carried out twice a year.”
Environmentally friendly commuting
Blum is also committed to raising awareness of sustainability issues among its staff in Austria. The family company has a number of exciting initiatives in place to support its employees, including
Green roof at Blum Austria
Green roof at Blum Austria
its mobility concept where the business covers the costs of an annual public transport ticket for its staff.
“The ticket can be used for both commuting and leisure, so we’re encouraging people to use sustainable transport outside of work too,” explains Katharina Schön, Blum’s mobility expert. Blum also supports employees with the cost of buying a new bike and, as an added incentive, employees that make sustainable commuting choices can collect ‘Ecopoints’ and convert these into rewards. Before the mobility concept was introduced in 2021, 38% of employees at Blum Austria travelled to work using sustainable transport; today that figure stands at 46% on average.
‘Vision 2045’ project
To mark the UN Climate Change Conference, which took place in 2023, Blum joined forces with the ‘Vision 2045’ project to produce a video showcasing its sustainability initiatives. By creating a series of documentaries of this kind, the ‘Vision 2045’ project aims to highlight the actions different businesses around the world are taking towards achieving the UN’s Sustainable Development Goals. “We understand our responsibilities as an industry player and want to take action wherever we can,” explains company owner and CEO, Philipp Blum.
Company-wide initiatives
In the UK, Blum has recently installed 904 solar panels on its UK headquarters’ roof, generating 75% of the building’s power needs and estimated to save 94 tons of carbon per year. One of the project leaders, Matthew Glanfield, says, “At Blum UK, sustainability lies at the heart of everything we do. Now we have gone the extra mile by installing a magnificent solar farm, embracing renewable energy as much as we can and nurturing a brighter tomorrow. Our passion for sustainability has driven these steps, as we ramp up our efforts and continue to live by our values.” The solar panels will generate energy during both working hours and out-of-hours, as well as weekends, and any excess energy will be sold back to the main grid.
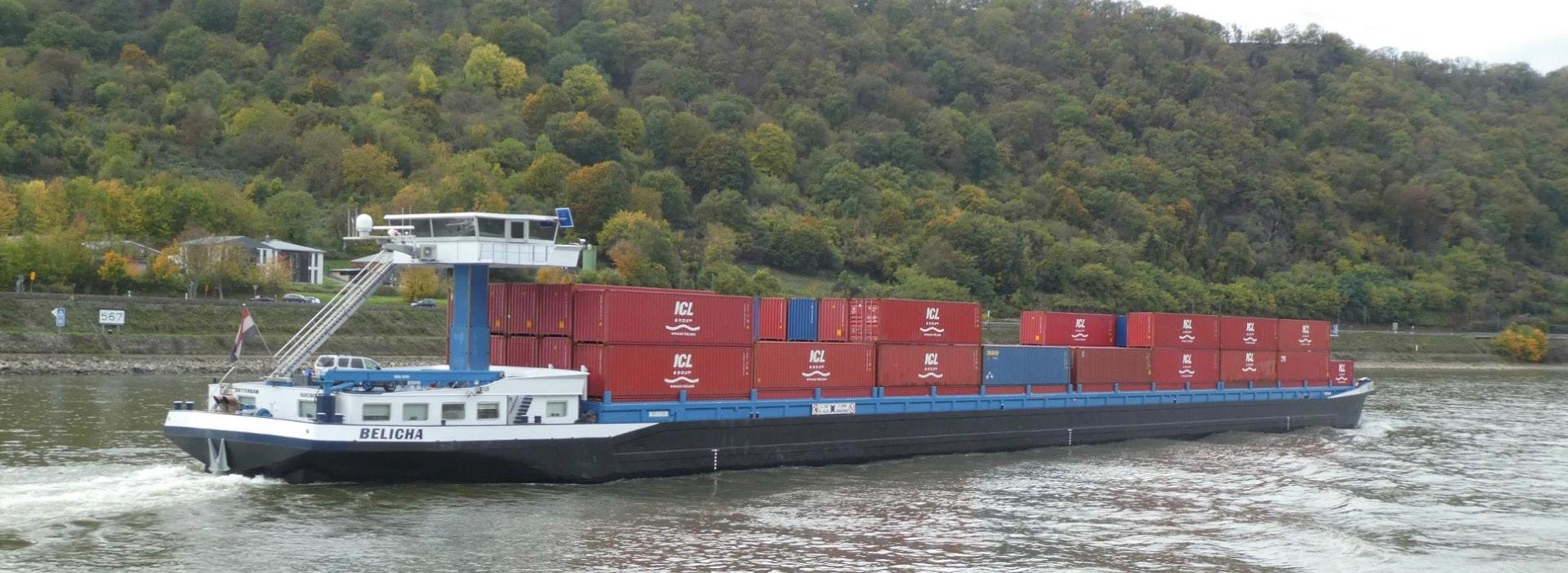
“In the UK, Blum has recently installed 904 solar panels on its UK headquarters’ roof, generating 75% of the building’s power needs and estimated to save 94 tons of carbon per year”
A few months ago, Blum took another step on its sustainability journey, with the initial installation of ten beehives in the Blum garden. Almost 90% of wild plants and 75% of global crops rely on bee pollination. Bees pollinate many of the crops used in animal feed, wild trees and flowers. An amazing one in every three mouthfuls of our food depends on these pollinators. Through this new addition, Blum hopes to support the environment and wildlife in the area, whilst also producing delicious honey in the process. The bee hives were installed by Home Farm MK on a sunny morning in June 2023.
“We are thrilled about the launch of our ten bee hives, which could potentially house a buzzing half a million bees!” says warehouse manager, Raj Tanna. “Doing our part for the environment, we are also looking forward to harvesting our own delicious Blumble honey. Our beehives are managed by a local company intent on helping make the world a more sustainable place.”
But this doesn’t end with green roofs in Austria and Poland, or solar panels and bees in the UK. Blum China and a large number of other Blum sites are working towards a more sustainable, eco-friendly infrastructure by installing photovoltaic systems that cover a large part of the respective site’s energy consumption. The company is aiming to pursue this path in
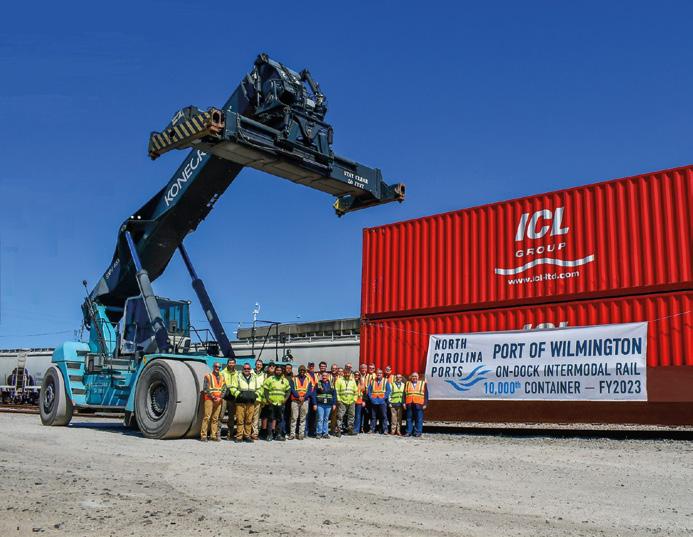
a more consistent manner in future while taking into account as many sustainability aspects as possible. These include energy efficiency, a conscientious approach to resources, climate friendliness and, of course, biodiversity.
As these examples show, Blum understands its responsibility as a global player to be a role model for the furniture industry and is committed to investing in a sustainable future. At the same time, however, Blum knows that there is still much work to be done. Everyone must play their part, both within Blum and across the industry as a whole. It will take a willingness to change, a healthy dose of tenacity and, above all, flexibility, versatility and creativity – along with some “moving ideas for sustainability”.
As Philipp Blum puts it, “Change requires all of us. Every one of us has a vital role to play, because sustainability impacts us all.”
For further reading, Blum has also produced a sustainability brochure to illustrate its commitment and measures taken over the past business year. The 80-page brochure features the new sustainability logo and makes operational, ecological and social figures transparent and easily comparable. You can view it here – www.blum.com/gb/en/company/ sustainability/overview/ 01908 285700 www.blum.com
Blum Austria – round trip container barge
Ferwood: a sustainable solution
The woodworking industry has firmly placed the spotlight on sustainability in recent years, with UK furniture manufacturers working hard to respond to global and consumer demands to reduce carbon footprint by prioritising renewable resources and energy efficient production processes.
The role of used and reconditioned machinery in achieving sustainability goals is one area that continues to gain momentum, as manufacturers recognise that purchasing choices not only make a significant impact in carbon reduction, but help create a more sustainable industry for the future.
For panel processing machinery, a circular economy that maximises machinery life – by reconditioning, reusing and recycling - reduces our negative impact on the environment and improves our ability to meet and adapt to increasing market variables.
One company that has been working hard to transform the used machinery market and providing manufacturers keen to reduce their operational footprint
with a real alternative to new machinery purchase, is the Ferwood Group. As the leading global supplier of used and reconditioned machinery, Ferwood has to date, recycled 4,000 machines, saved 6,000 and currently carries 150,000 recycled spare parts.
Specialists in their field, Ferwood UK’s team of experts’ source and supply machinery from leading machinery manufacturers, including Homag Group, Biesse Group, SCM Group and IMA Schelling Group. As well as selling used machinery from its UK showroom, the Ferwood Group refurbishes high production panel processing machinery and complete production lines for many of the world’s biggest furniture manufacturers from its headquarters in
Pollenzo, Italy. From edgebanders, beam saws and CNC routers to full production lines, every Ferwood Approved machine is fully reconditioned, extending machinery life and reducing an unnecessary carbon footprint.
And those carbon savings are impressive: In 2023 alone, Ferwood customers purchased over 500 used machines and helped save 4,625 tonnes of carbon. The steel required to produce this much new machinery would result in an average of 9.25 tonnes of carbon dioxide emissions, amounting to a staggering 46,250 tonnes over 10 years. With growing demand, continued investment in stateof-the-art factory facilities and highly skilled technicians providing high-tech customisation of full production lines, the
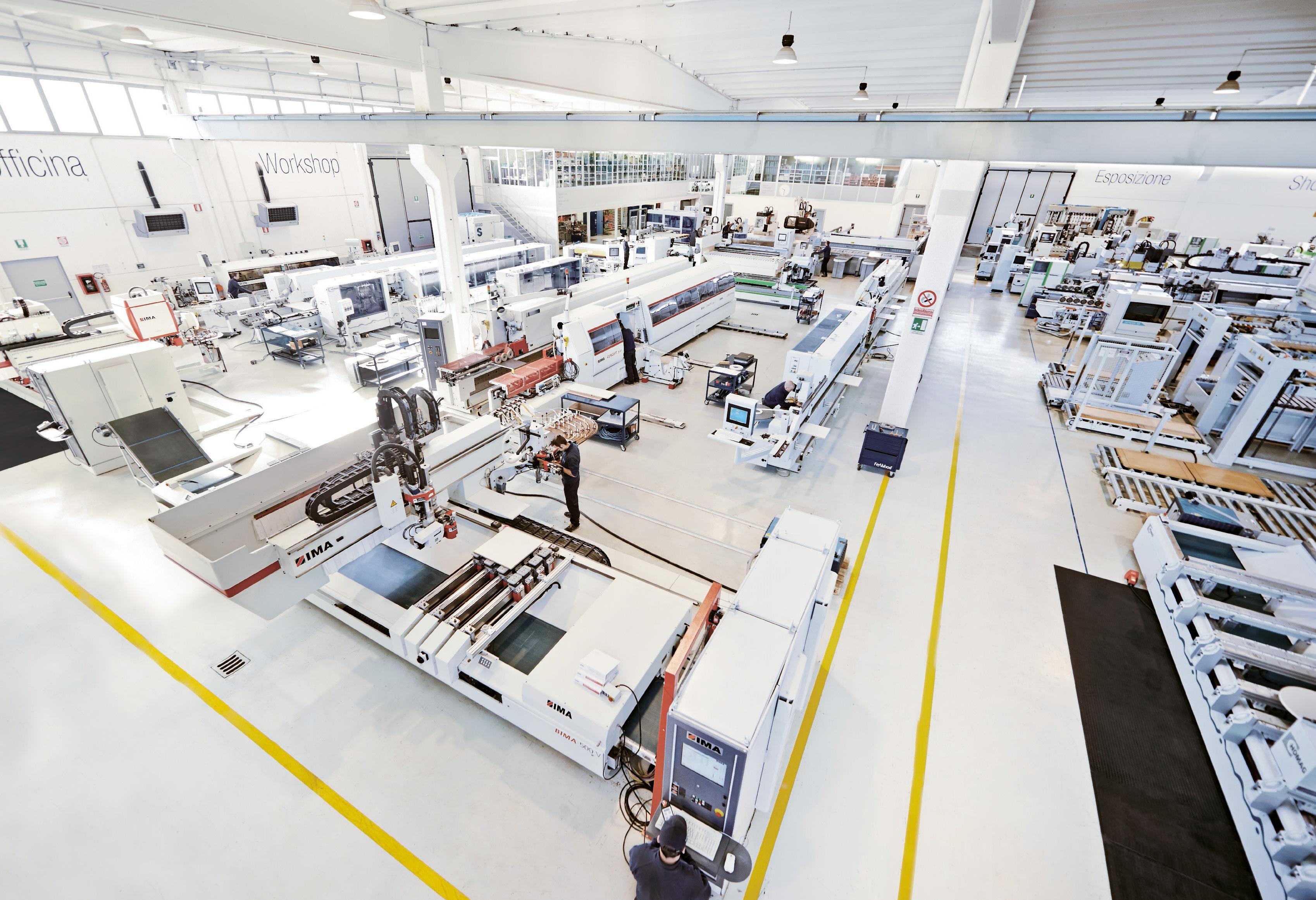
Ferwood Group anticipate that carbon savings will continue to increase, making an impressive contribution to reducing carbon footprint in the furniture production industry.
Whatever the scale of production, the investment in panel processing machinery is a large part of any budget, and the financial implications of strategic sustainability can cause concerns.
For manufacturers that recognise the importance of incorporating sustainability commitments into planning, used machinery is an effective and easy to implement purchasing strategy, whilst reducing unnecessary financial exposure.
“Reducing carbon footprint is not a new versus used machine scenario,” says John Wilson, CEO of Ferwood UK. “Most manufacturers with new machinery on order are likely to have old ones that can be reconditioned and every highquality machine provides potential to be reconditioned and re-used.
“By committing to place machinery into the circular economy, you help create affordable options for other manufacturers to streamline production and further reduce waste. This is positive action that supports efforts to reduce carbon emissions and helps create a sustainable industry.”
John continues: “Whether purchasing used machinery or making used machinery available, we can all play a role in making our industry more sustainable. For any manufacturer looking at waste management, incorporating machinery disposal as part of the overall company sustainability policy makes sense.”
With a fast and straight-forward
‘By committing to place machinery into the circular economy, you help create affordable options for smaller manufacturers to streamline production and further reduce waste. This is positive action that supports efforts to reduce carbon emissions and helps create a sustainable industry’
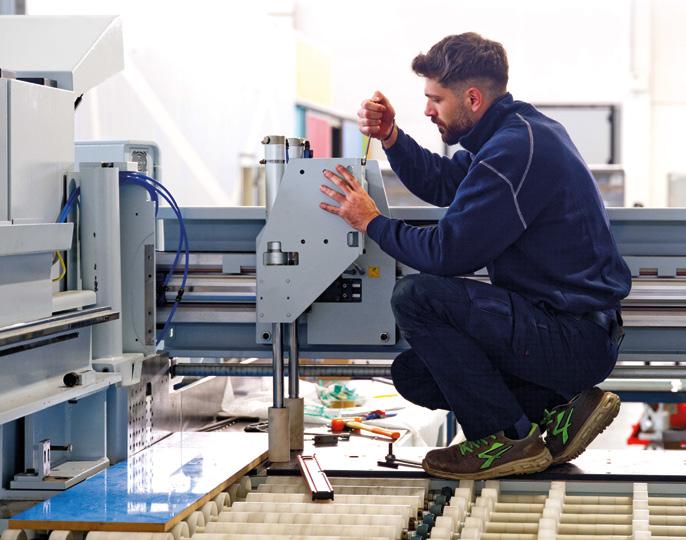
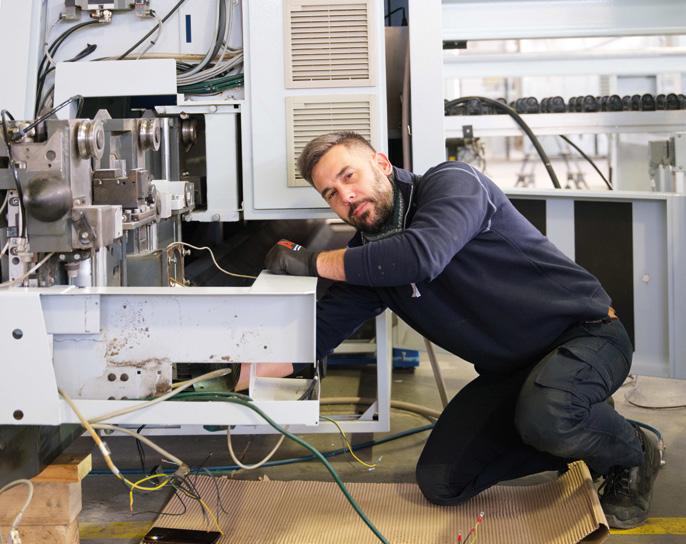
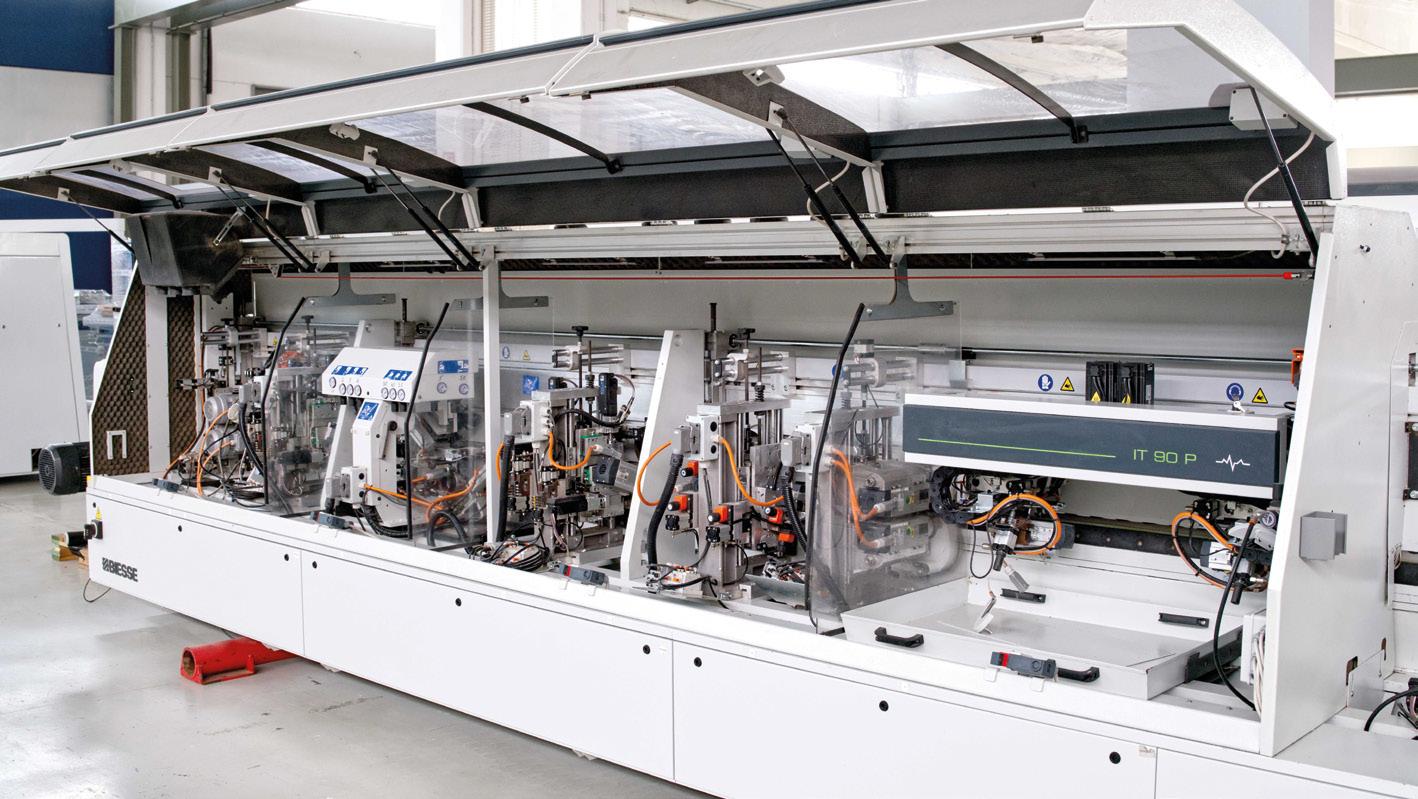
purchasing service, Ferwood can even coordinate the dismantling of old machinery with the delivery of new ones, avoiding costly breaks in production.
John adds, “Your robust sustainability commitment improves your own sustainability credentials and helps reduce the carbon footprint for another manufacturer.”
The UK furniture manufacturing market remains a key player in the overall economy, with the UK government’s adoption of the Climate Change Act (2008) which set a target to reduce the UK’s carbon emissions in 2050 to 80% below 1990’s levels. We all play a role in reducing carbon footprint in the industry, and we will achieve more by continuing to work together.
Thanks to Ferwood’s ability to recondition used machinery to the highest level and offer a sound alternative to new machine, more manufacturers look to incorporate used and reconditioned panel processing machinery as part of their sustainability process. The positive impact in the industry can only increase. Manufacturers can achieve significant benefits which can extend further than those all-important green credentials.
High-quality used furniture production machines provide all manufacturers with the opportunity to update machinery without being hindered by prohibitive capital expenditure increases. For growing businesses, this makes streamlining production, minimising error and increasing flexibility more achievable, and helps build in additional protection from the more difficult to control economic and market variables.
In a circular economy, what goes around, comes around - and it’s naturally and mutually beneficial. Let’s also not forget the smaller manufacturers with a focus on bespoke designs that often kickstart consumer trends which shape the future of high output production. With growing consumer demands for sustainable products, customised designs and affordability, manufacturers that align with sustainable practises can benefit from increased customer loyalty.
“The furniture production industry has faced unprecedented challenges in a very short period,” says John. ”From escalating materials costs, supply chain difficulties and labour shortages, to unpredictable economic climate. Committing to sustainability and reducing carbon
footprint can feel like an onerous task for many manufacturers already concerned about budgets, but it doesn’t need to.
From the largest manufacturers to smaller bespoke outfits, introducing used and reconditioned machinery into purchasing and disposal choices are an effective way to reduce waste, conserve resources and create a more sustainable environment and a more sustainable industry.”
The success of a circular economy is dependent on all parts having the same goals and aiming for the same high standards. Ferwood Groups reputation is built by only supplying premium brands whose build quality and reputation are already market leading and combining with second-to-none consultation, refurbishment and personalisation. Ferwood’s success led to investment that has seen their headquarters grow to accommodate more than 300,000
‘From escalating materials costs, supply chain difficulties and labour shortages, to unpredictable economic climate. Committing to sustainability and reducing carbon footprint can feel like an onerous task for many manufacturers already concerned about budgets, but it doesn’t need to’
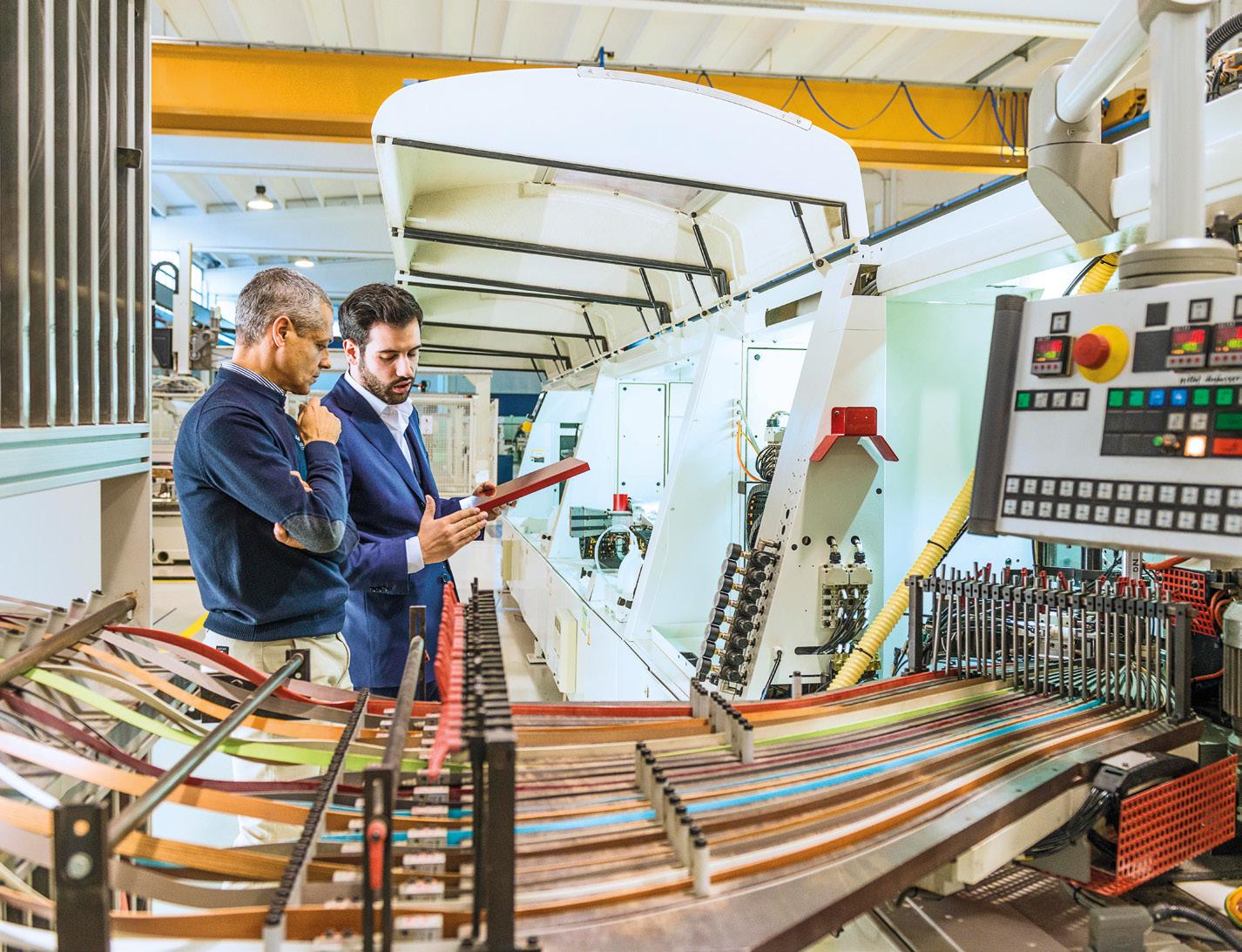
sq. ft of factory space, with separate areas designed for handling, cleaning, painting and refurbishing. Whilst the impressive showroom, which is fed by Ferwood’s large workshops, is sectioned and categorised by product lines for customers to view in operation.
“At Ferwood, we believe that the success to growing a sustainable economy is in supporting a shared vision,” says Riccardo Rossi, CEO of Ferwood Group. “We invest in the best brands, the latest technology and importantly, the best employees. In doing so, we work together to create further resilience and sustainability in an industry we care passionately about. Ferwood saw 50% revenue
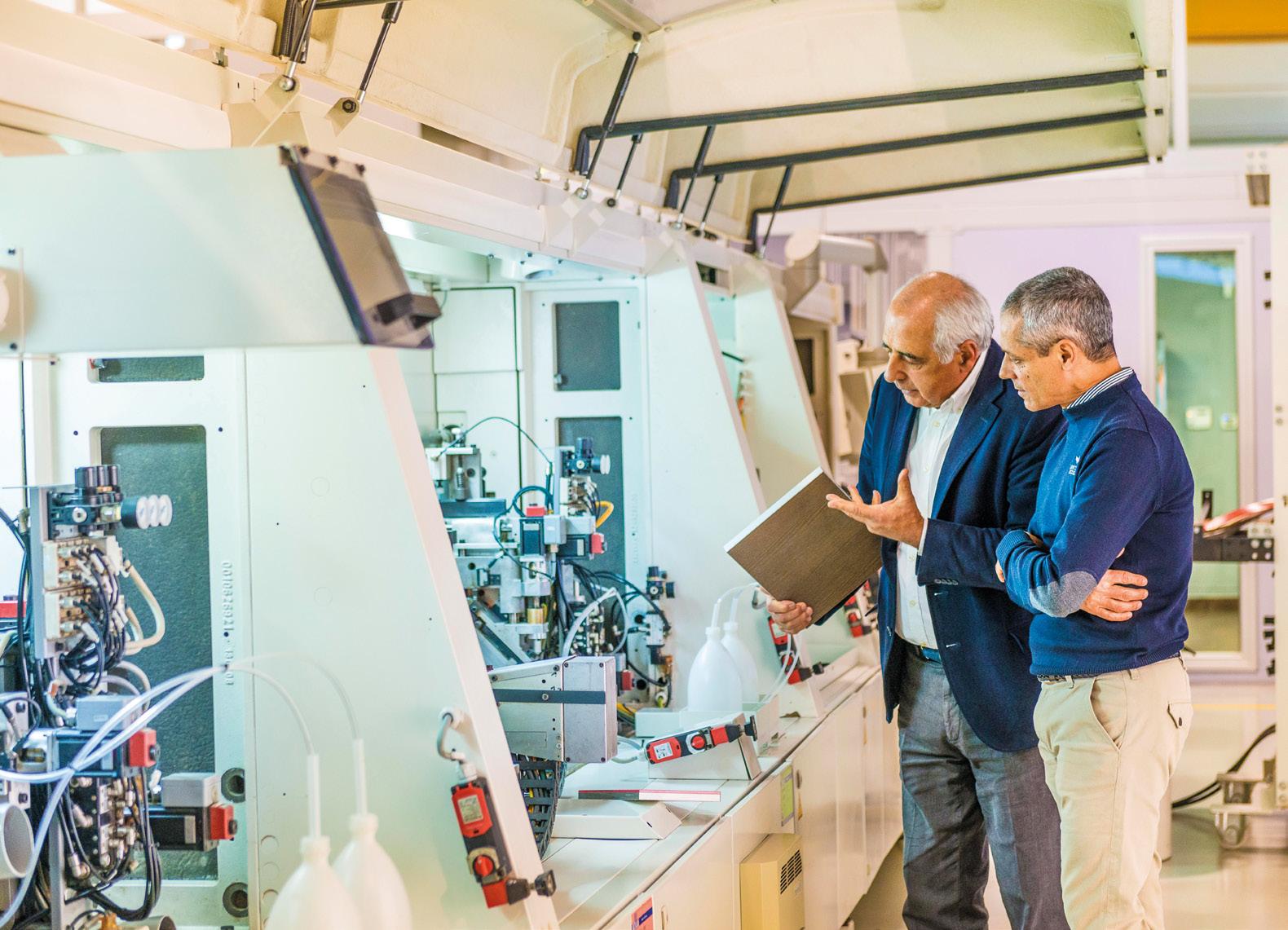
growth between 2020 and 2022, and with demand for high quality used and reconditioned machinery continuing to increase, we have extended our presence in Europe and the USA.
“Successful sustainability policies can reduce resources and create growth in new areas and at Ferwood, we are part of this progression. We continue to look at ways to improve our internal organisational sustainability and include wellbeing and experience within our plans. We’ve introduced virtual tours as an alternative option for customer visits, invested in solar panels for the Ferwood HQ factory and showroom, and opted for recycled materials for the new staff room. These are just some of the small steps in our journey to becoming more sustainable, and like the industry as a whole - these are the little steps that begin to build a brighter future.”
The importance of sustainable furniture production in today’s society can only increase. With growing awareness of environmental and social issues and global initiatives likely to expand - the industry will continue to develop sustainable practices that minimise the impact on the planet and promote a stronger industry. Ferwood are committed to their part in providing machinery solutions which can create a more sustainable industry for the future.
www.ferwoodgroup.com
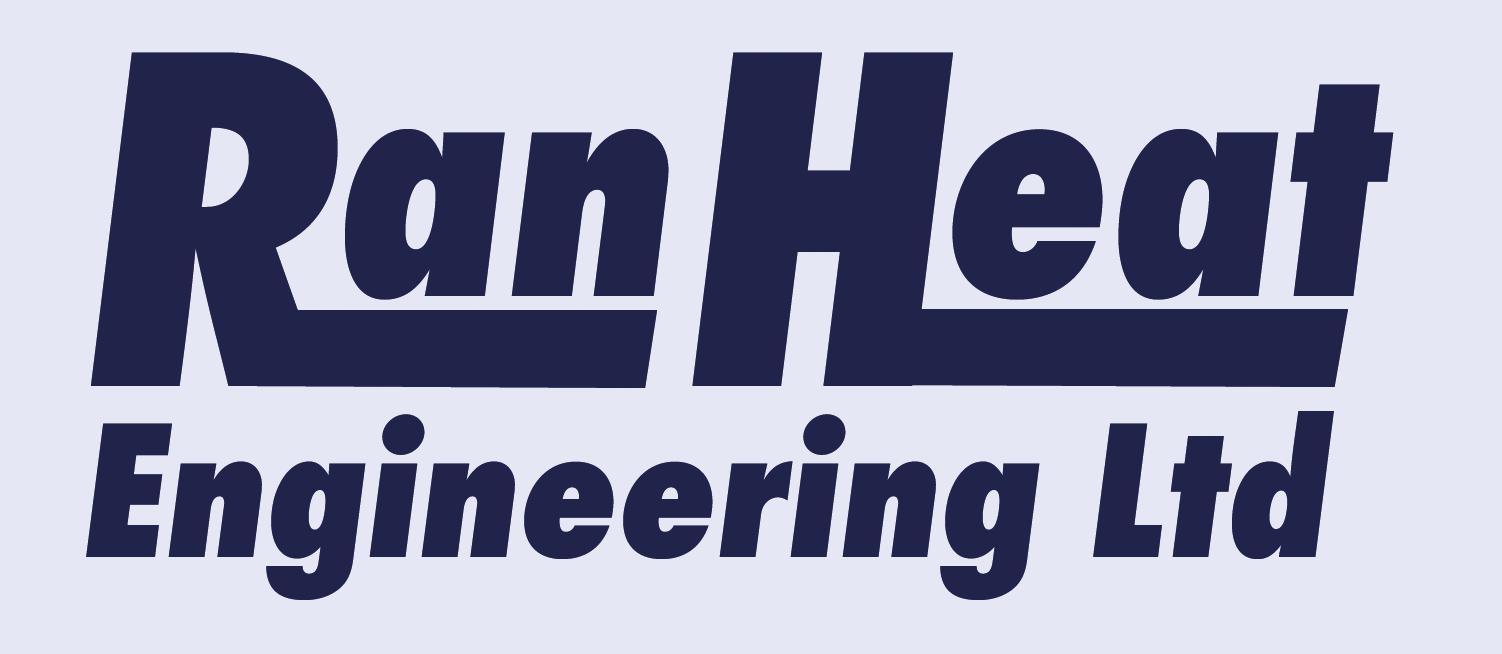
WOOD COMBUSTION EQUIPMENT
INDUSTRIAL HEATING SYSTEMS
SPECIALIST METAL FABRICATIONS
Ranheat design and manufacture the complete range of equipment including Boilers, Heaters, Stokers, Grit Arrestors, Chimneys etc.
Manual & automatic woodburning systems, gas & oil fi red, turnkey installations for disposal and/or heating purposes, outputs up to 3MW.
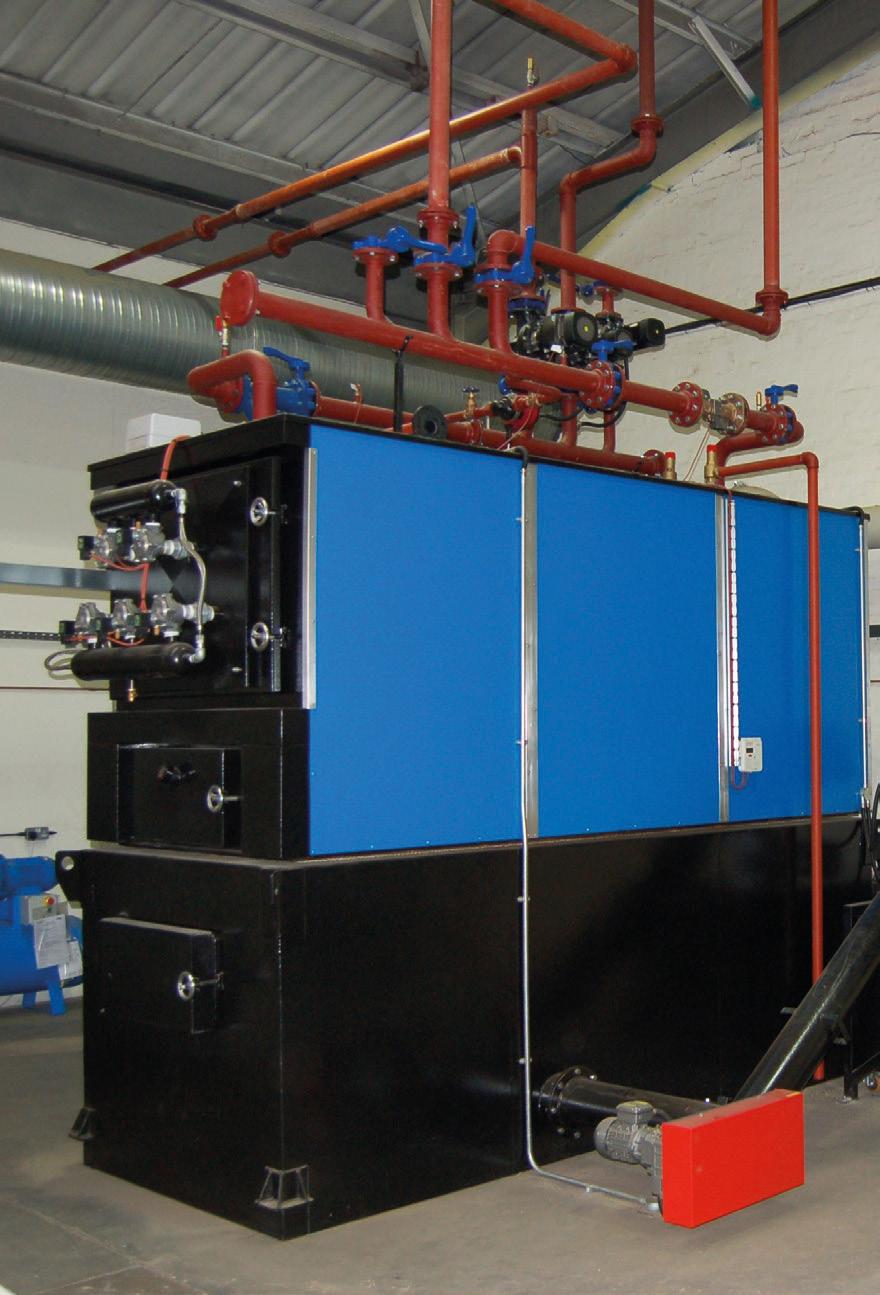
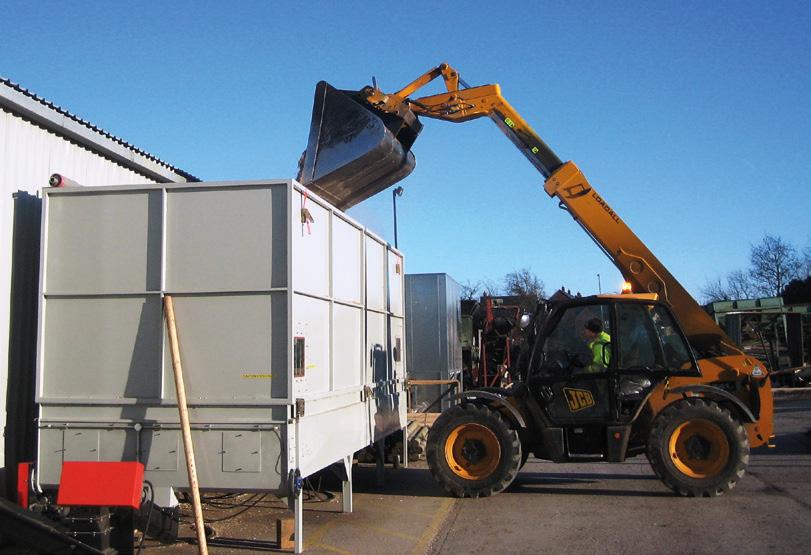
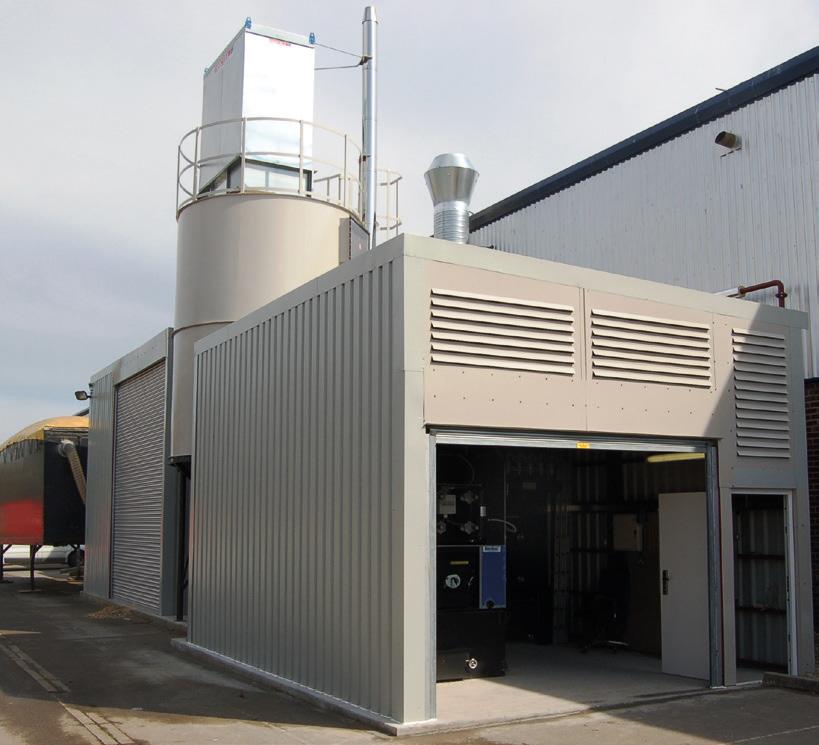

EGGER Group pushes ahead with Net Zero target
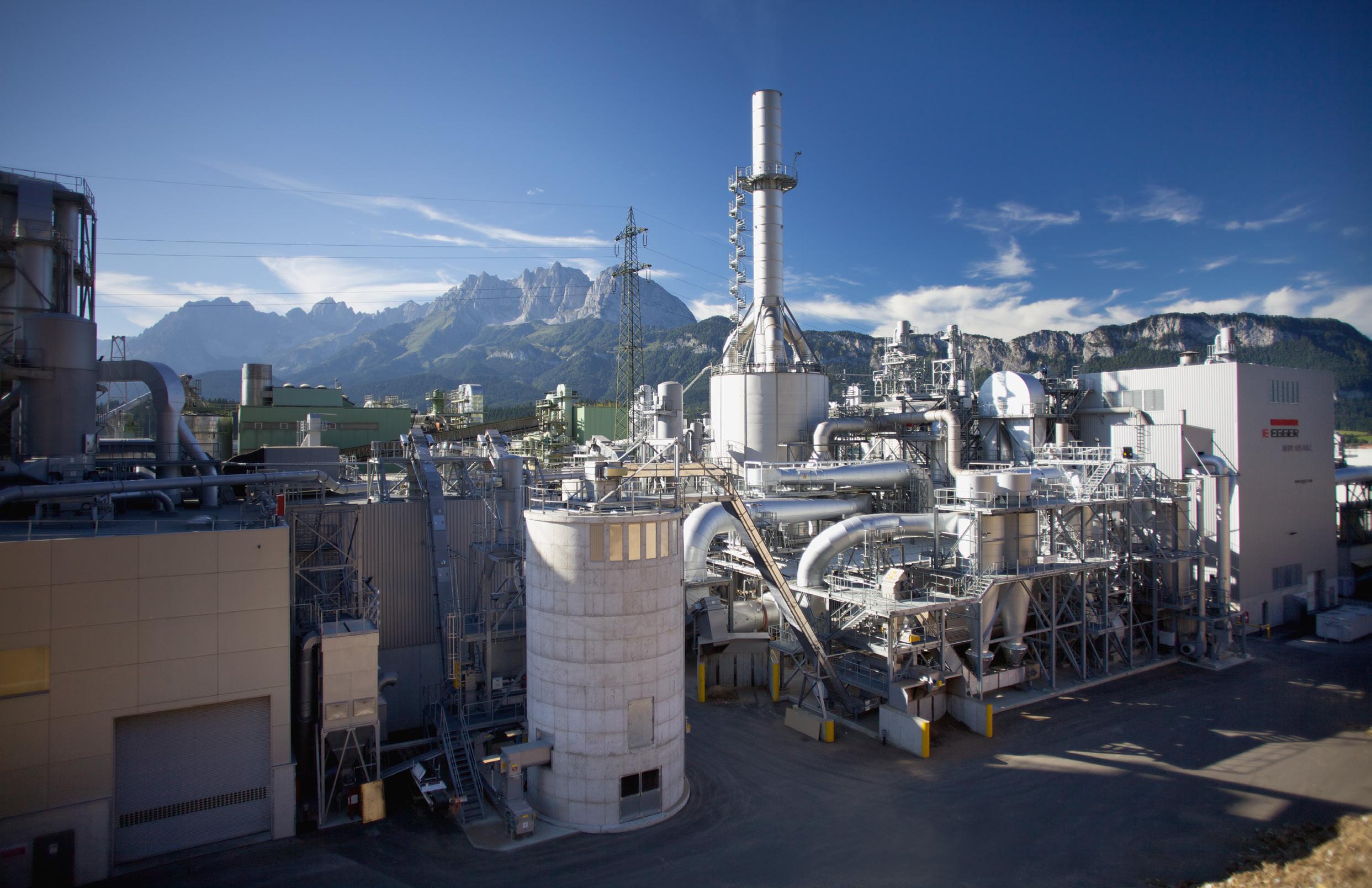
Founded in 1961, the international manufacturer of wood-based materials packs some serious clout, with more than 11,000 employees and 22 production locations worldwide. EGGER has always been at the forefront when it comes to sustainable living and working, as well as the sustainable sourcing of wood and the recyclability of its products. Now, the EGGER Group has indicated its resolve to meet its Net Zero Target by 2050.
Meeting this target will, naturally, be no mean feat, and EGGER has set a number of interim targets for 2030 in order to stay on track. By 2030, direct emissions from the company’s own plants (Scope 1) will be reduced by at least 30%, indirect emissions from purchased energy (Scope 2) by at least 40% and indirect upstream
and downstream emissions (Scope 3) by at least 10%. The base year of the climate targets is 2022.
Even before the company embarks on this journey, it has already instigated an array of measures and made a significant investment in climate protection. For example, EGGER’s regular operation at its plant in Unterradlberg (AT) is now free of natural gas thanks to the installation of a new heat exchanger. It is used to heat
“This path will continue to be pursued consistently; it will still require many measures, but we are convinced that we will achieve the targets we have set ourselves”
the thermal oil needed for operating the rawboard press and the four lamination lines – a process that previously required the use of natural gas. The new heat exchanger is now operated with steam from the existing biomass power plant.
EGGER also has big plans for its plant in St. Johann in Tirol (AT), where it is investing around EUR 80 million in a new power plant and thus in renewable energy supply at this location. By supplying both heat and electricity for its own production processes using a steam boiler and combined heat and power generation from biogenic fuels, EGGER will reduce the use of fossil fuels at the location to almost zero and can also supply the surrounding communities with even more sustainable district heating. The new power plant, which is being built to the
EGGER is investing EUR 80 million in a new power plant at its St. Johann in Tirol (AT) location Photography: EGGER Holzwerkstoffe
latest industrial standards, is scheduled to be commissioned in the first quarter of 2026.
In a further step, EGGER has also switched on a large scale to binding agents produced with CO2-neutrally generated electricity. Since 1st January 2024, the three resin plants have only used electricity that is CO2-neutrally generated. It comes from hydro, wind or solar energy, for example.
This switch applies to all EGGER boardproducing plants in the EU and UK and affects the chipboard and MDF product groups. EGGER is taking the first step towards reducing the CO2 footprint of the binding agents used.
Crucially, EGGER applies high standards to its own sustainability management and its transparent reporting system. While pursuing continuous improvement, the wood-based material manufacturer regularly undergoes analyses by external and renowned ESG rating agencies. These rating agencies have once again issued a good report: EGGER was awarded Prime status in the ISS ESG
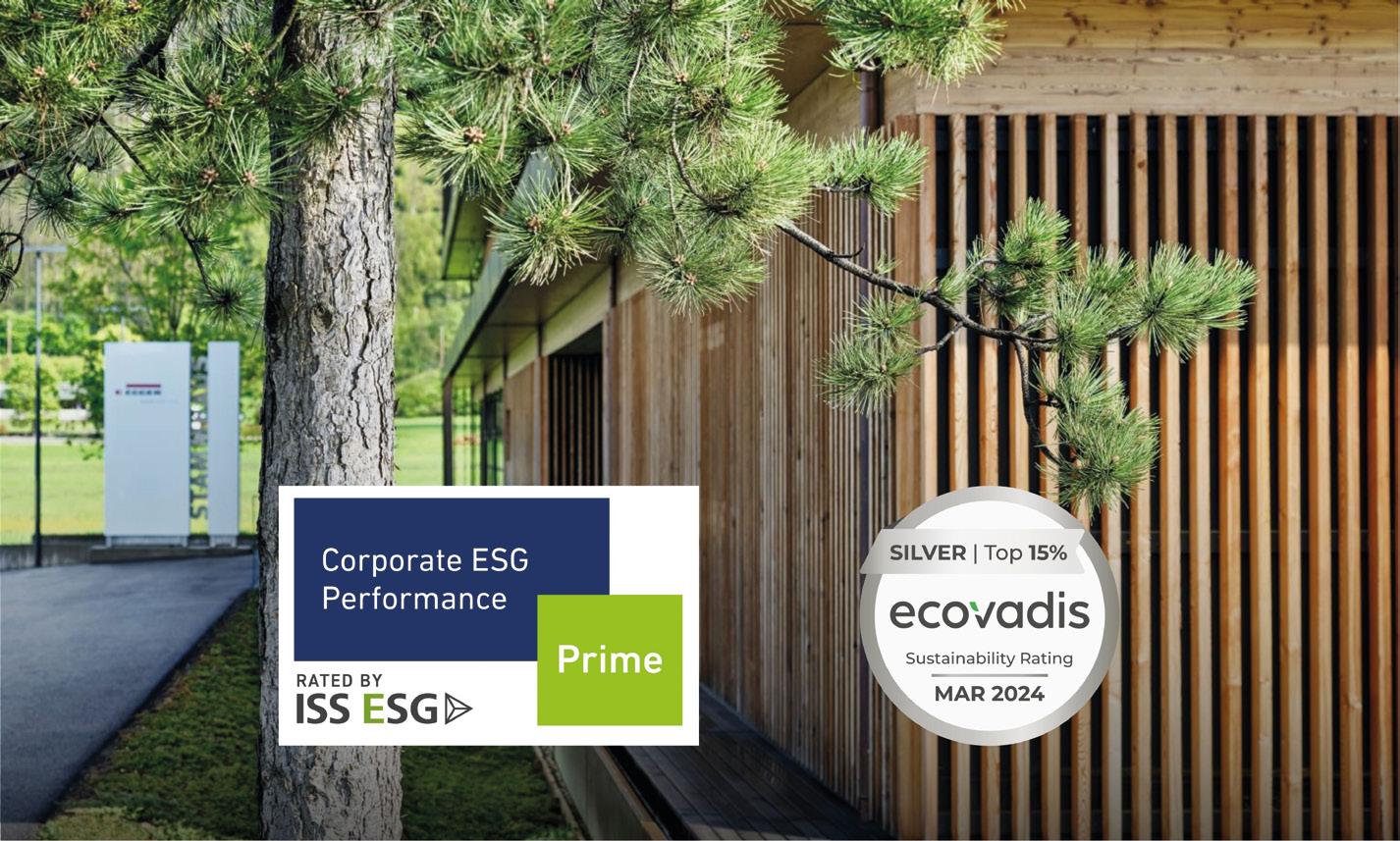
Corporate Rating for the fourth time and the EcoVadis silver medal for the fifth time. The family company is delighted with the great recognition and the findings from the ratings, which in turn represent important guidelines for further improvements.
“We have built up considerable expertise in carbon footprint accounting,” comments Thomas Leissing, Chief Financial Officer EGGER Group. “The
causes of our emissions are known in detail and we are aware of where we need to intervene. We are delighted that we can now report further steps on the way to Net Zero.
“This path will continue to be pursued consistently; it will still require many measures, but we are convinced that we will achieve the targets we have set ourselves.”
www.egger.co.uk
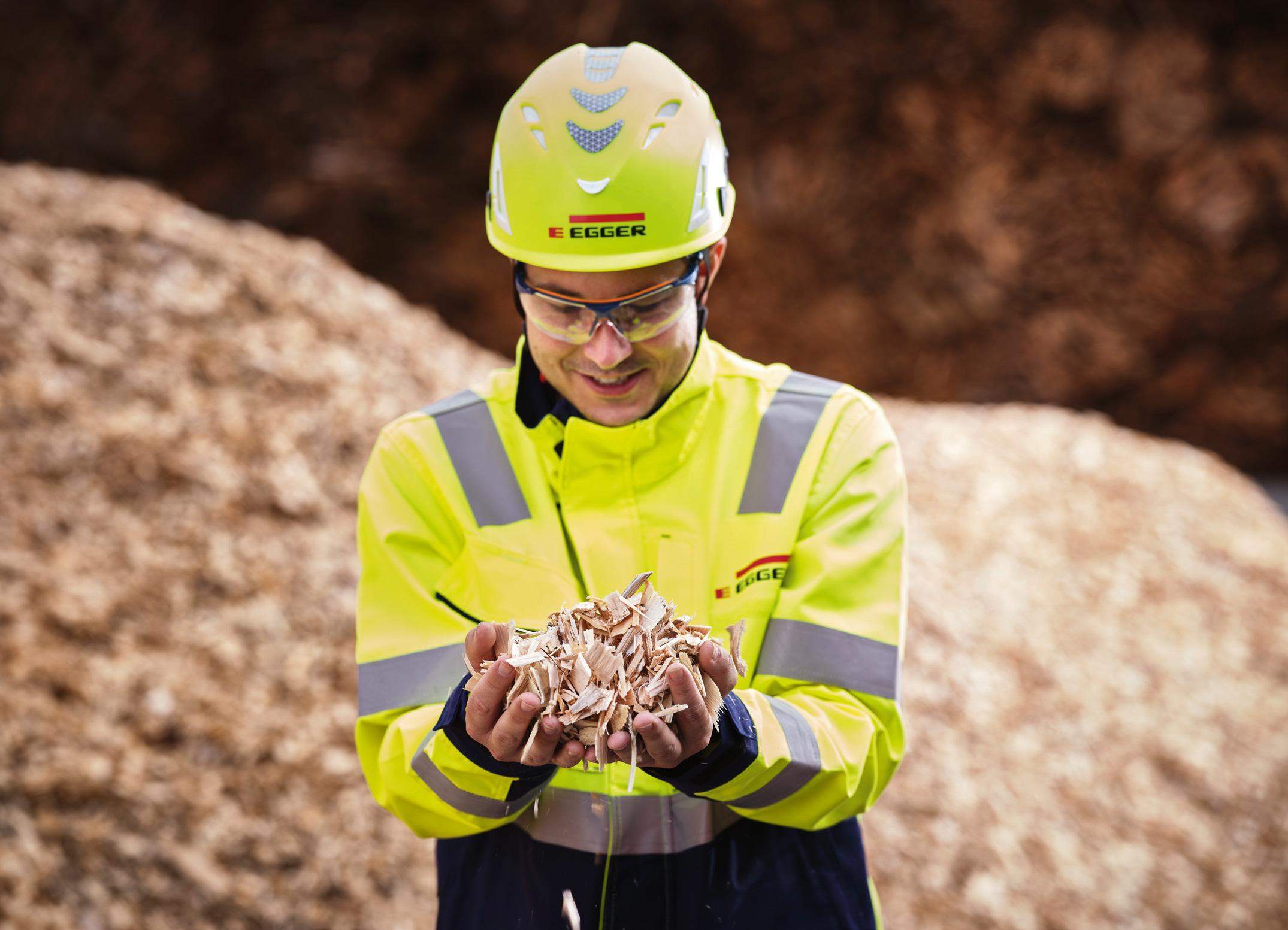
Photography: EGGER Holzwerkstoffe
The EGGER Group’s sustainability performance was once again recognised with ISS ESG Prime status and the EcoVadis Silver Medal
saviola. the power of green
2,8 M TREES SAVED EVERY YEAR
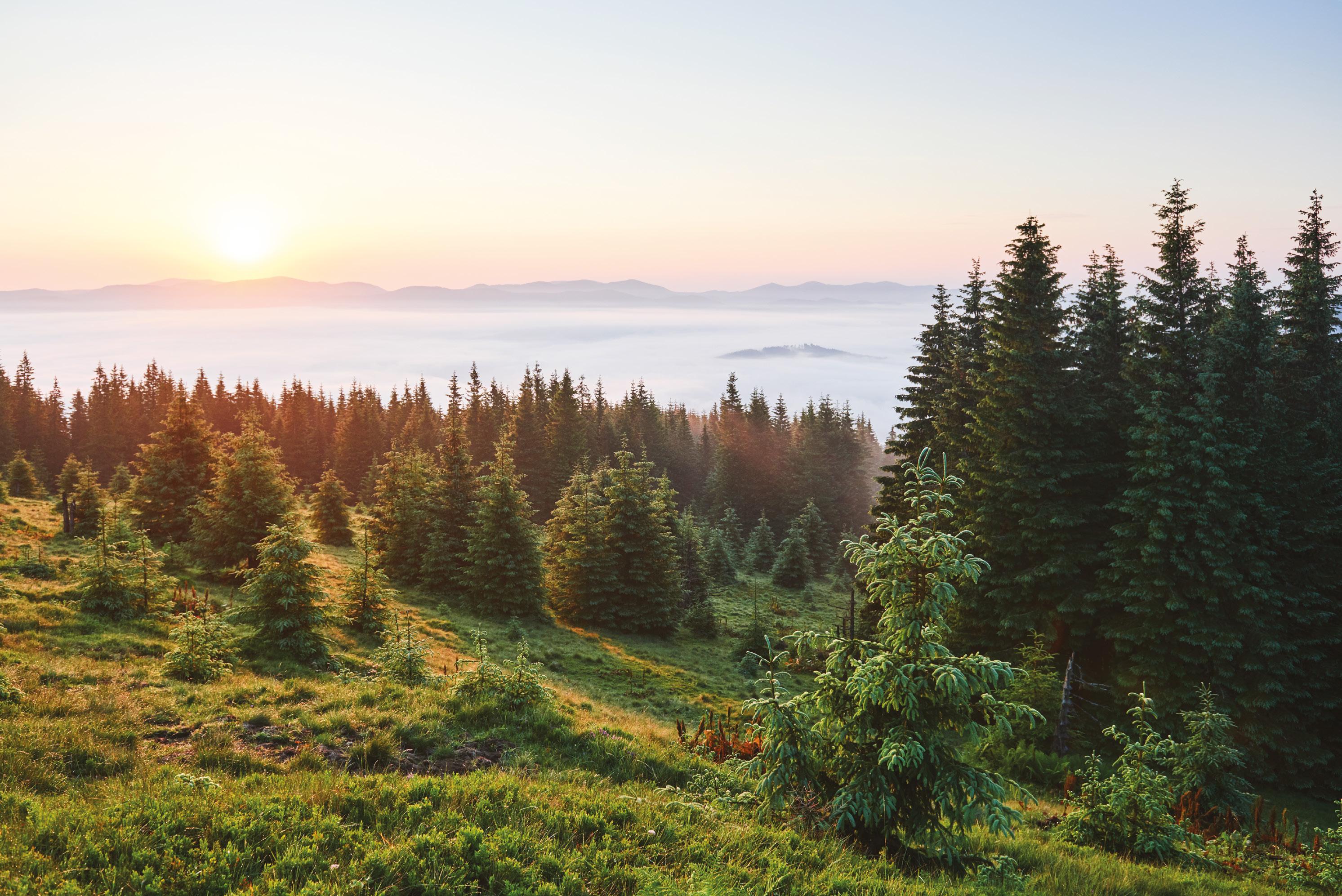
1° STILL THE FIRST IN THE WORLD TO DO IT
Mauro Saviola Group.
Everything started from a big love for nature and it became the first 100% recycled wood company, when nobody talked about sustainability.
The Saviola Group synergistically integrates national and international companies divided into 5 business units: wood with Saviola, chemistry with Sadepan, furniture with Composad, biosciences with Saviolife, and used wood collection network with Savionet for a total of 14 factories around the world.
In 1992 Saviola set itself the ambitious goal of achieving the production of a chipboard panel made 100% from recycled wood. A futuristic project, greeted with distrust, which required enormous economic e orts in research and development. The Ecological Panel® was born, produced with materials that were defined as waste. These were the dawn of the circular economy and the beginning of a new era: that of the Eco-Ethical Company.
Ecological Panel, produced with materials that were defined as waste, the first to be 100% FSC® Recycled Certified
saviola.com ecologicalpanel.com
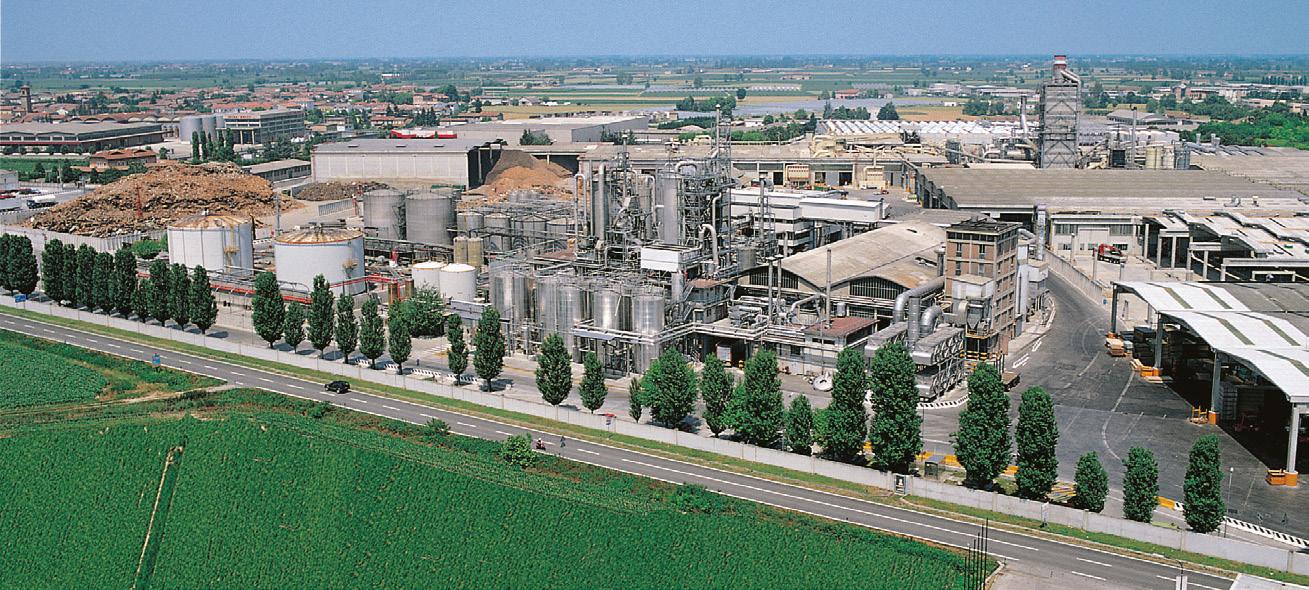
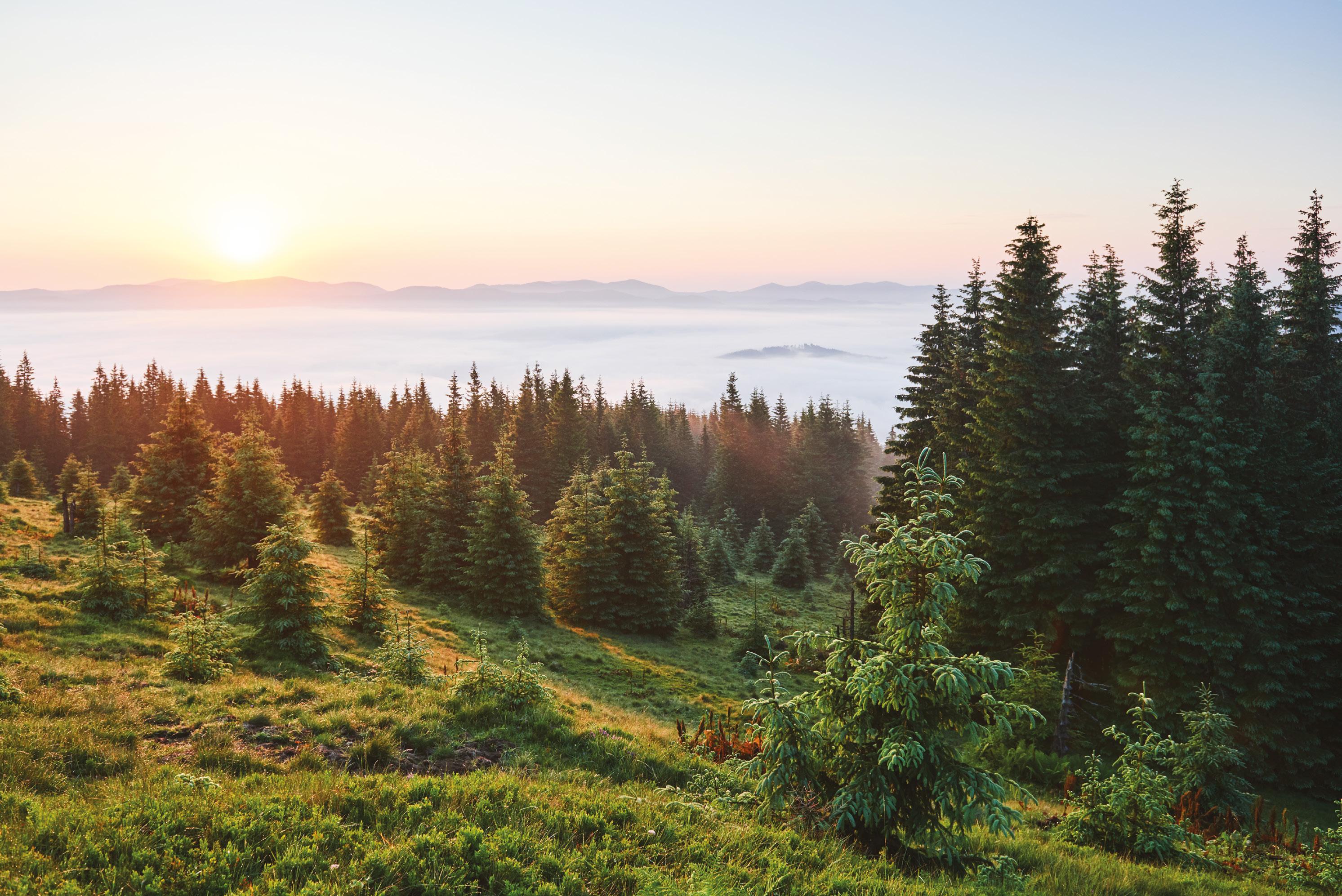
A Beacon of Light of the circular economy
Today the circular economy is an important part of the urgent discussions and challenges faced by our world. It slows down the use of natural resources and reduces the total amount of greenhouse gas emissions. Saviola placed their ecological panel as a priority in the market three decades ago giving it a second life as a new product, making the Group Saviola a global beacon.
With our process we also return annually these materials back into the circular economy
28 tons of copper equivalent to a cable from Naples to London there and back.
959 tons of aluminum equivalent to approximately 78.5 million cans
16 thousand tons of iron equivalent to 2 Ei el towers
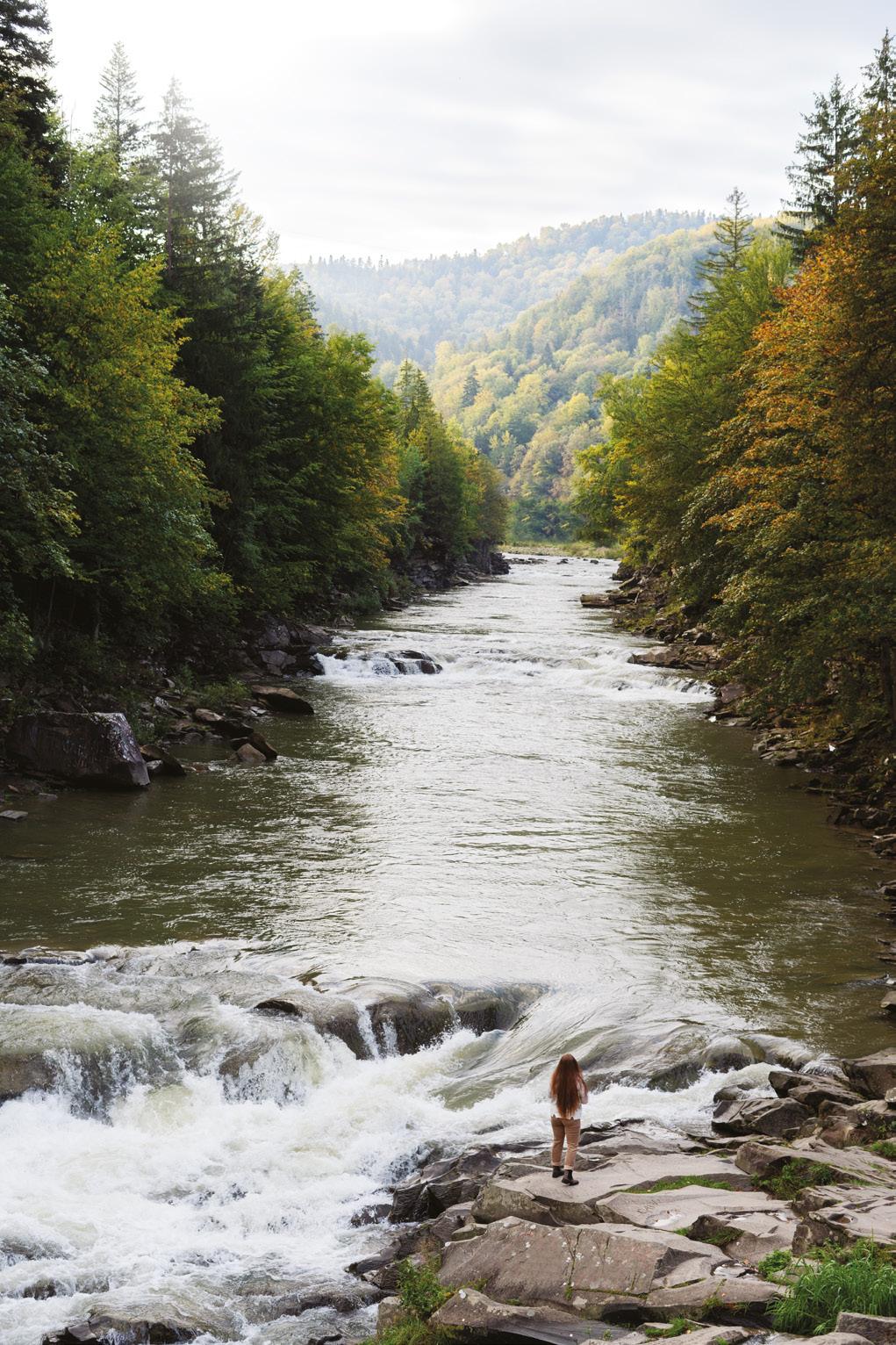
When waste is transformed into value, The beauty of reclaimed wood
By equipping itself with new technologies and expanding its production plants, the Saviola Group challenges the giants of the sector with an integrated and sustainable production logic. The commitment is not trivial, since the wood must be cleaned of nails, paper, organic residues and more, but Mauro Saviola is convinced of the need to spread the recycling activity in a widespread way.
Continuing to invest in research and in the acquisition of companies specialized in specific processes, in 1997 a fundamental milestone was reached: 100% of production is made up of ecological panels. In other words, from that moment on all Saviola panels would be made without cu ing down a tree.
From that moment on, the company concentrated on the design of surfaces, achieving three-dimensional and material e ects of the highest level. With a range of melamine in various sizes available in water-repellent, fire-retardant and also Leb, low emission board versions, the Saviola range serves the furniture industry but also conceptual projects and architectural studios that make use of the ready-to-deliver collection.
The Saviola Group is therefore an example of sustainability in the industrial sector, but also with regards to corporate governance: its story tells of an entrepreneurship driven by passion, innovation and a profound respect for the environment. The quality of its solutions, with the goals and results achieved, confirm once again how the circular economy model can and should be applied successfully.
TotWood recycled
Totdecors produced
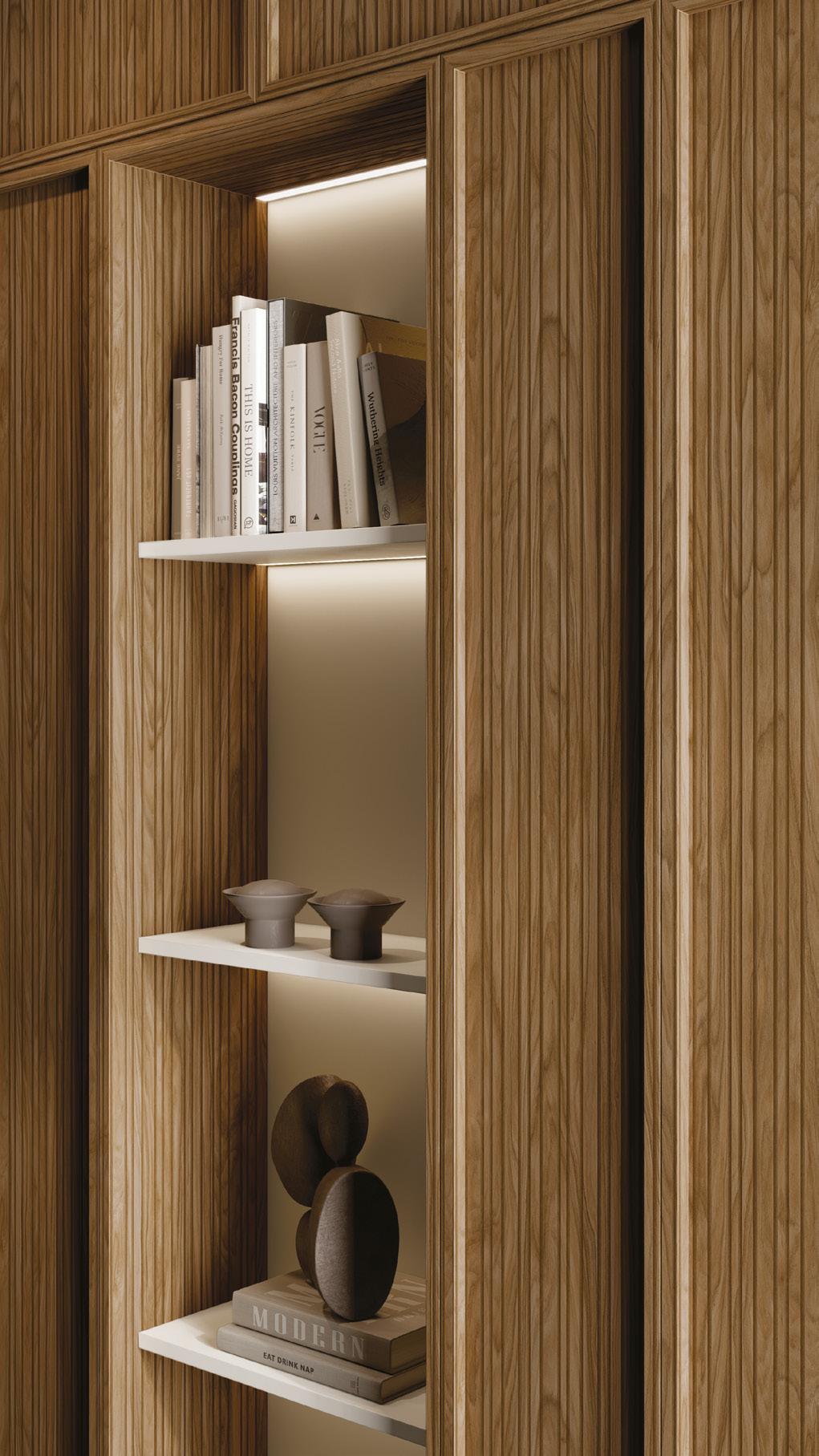
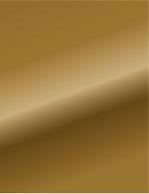
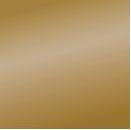
Silverlining – when technology and nature collide
Wrexham-based Silverlining Furniture is renowned for its pioneering approach to new materials. The company was formed more than 35 years ago, and has forged a 70-strong team of designers, makers, project managers and specialists that apply the very best of old and new techniques to transform flora and fauna into exquisite furniture finishes.
“Working with natural materials abundant in nature, and turning them into robust, structural materials, that can withstand the toughest conditions, whilst creating a spectacular finish, is our big focus,” affirms Daniel Lloyd-Davies, Silverlining’s head of R&D. “Whether it’s ordinary woods, straw or cork, these materials can be sourced responsibly from widely available sources, and then through creative processes, be turned into luxury finishes.”
Here, Daniel shares his top new materials:
Cork
“Cork, primarily harvested from the Cork Oak tree native to the Mediterranean basin, plays a pivotal role in sustainable agriculture. This renewable material is harvested without harming the tree. Each harvest enables the Cork Oak to absorb carbon dioxide—up to five times more than unharvested trees.
“Beyond its environmental benefits, cork is celebrated for its durability and resilient qualities, making it suitable for demanding settings like luxury yachts. Its natural composition provides water resistance, anti-microbial properties, and an innate ability to withstand wear and tear, positioning cork as an ideal material for both interior and exterior furniture.”
Karuun™
“Karuun™ is a new material made out of rattan palm’s stems, which are a naturally renewable resource. The stems
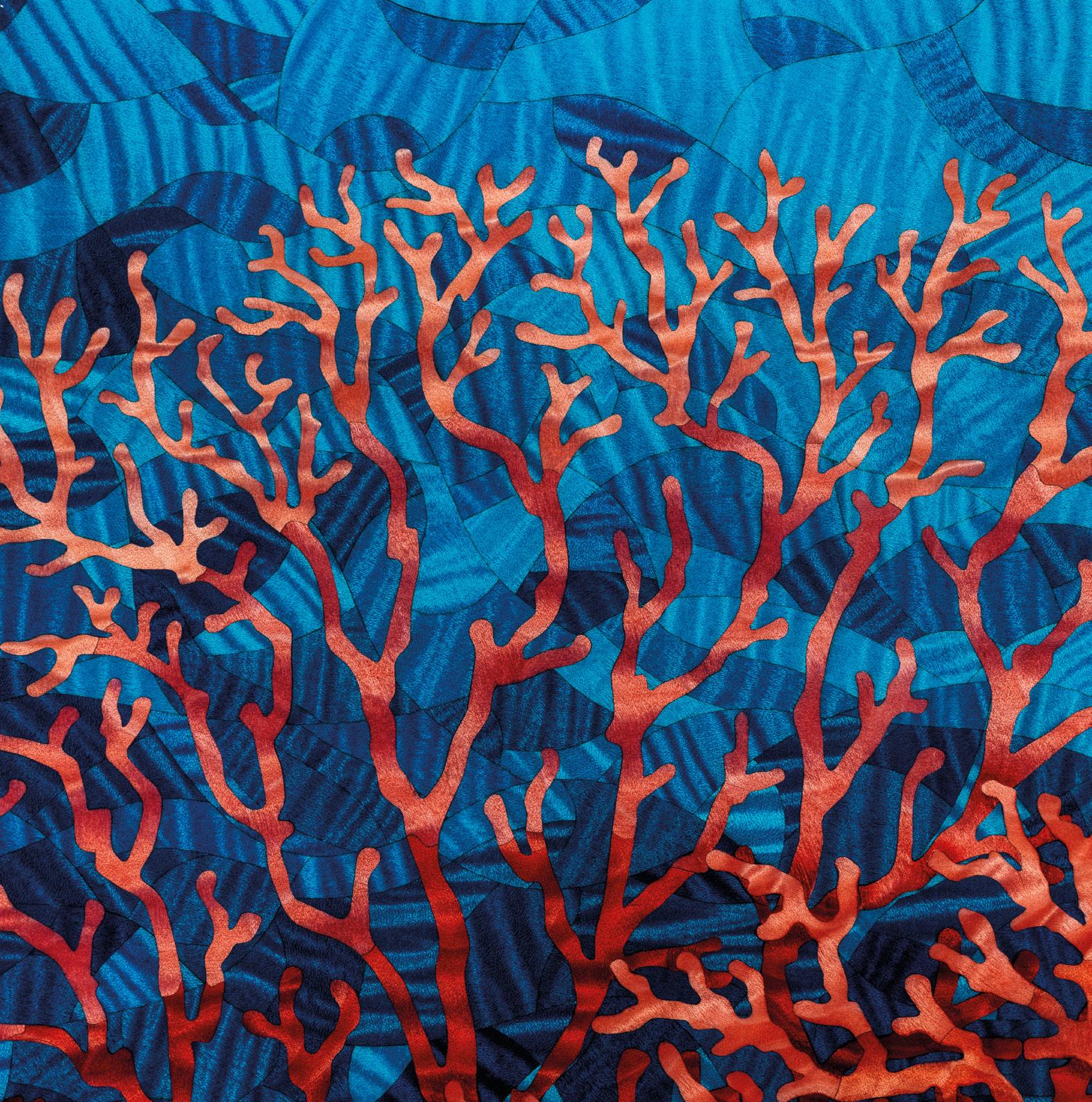

“Working with natural materials abundant in nature, and turning them into robust, structural materials, that can withstand the toughest conditions, whilst creating a spectacular finish, is our big focus”
are transformed into a high-tech, highperformance material that’s a natural alternative to plastic. The material is also fully recyclable, and flame-resistant due to its silica content.”
Flax fibre
“We can now replace man-made carbon fibres with extremely durable flax fibres, derived from abundant in nature linseed. To achieve this finish, the bark is first removed and the plant then scraped to remove other layers, gums, and pectins. Finally, the residual cortex material is washed, dried and degummed to extract the spinnable fibre.”
www.silverliningfurniture.com
Cork - Flow
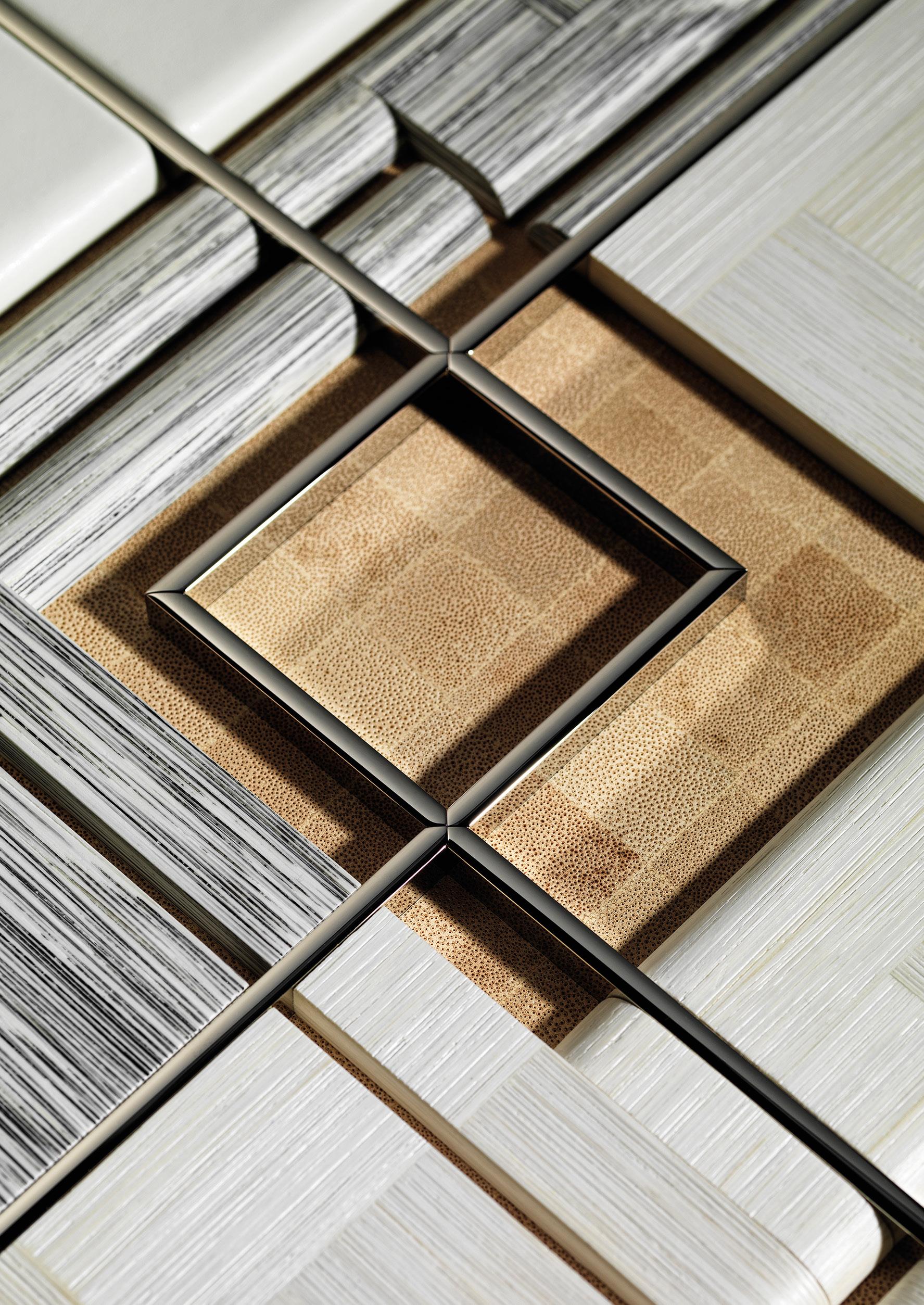
Karuun™
Accoya brings sustainability and durability to Gascoigne Park
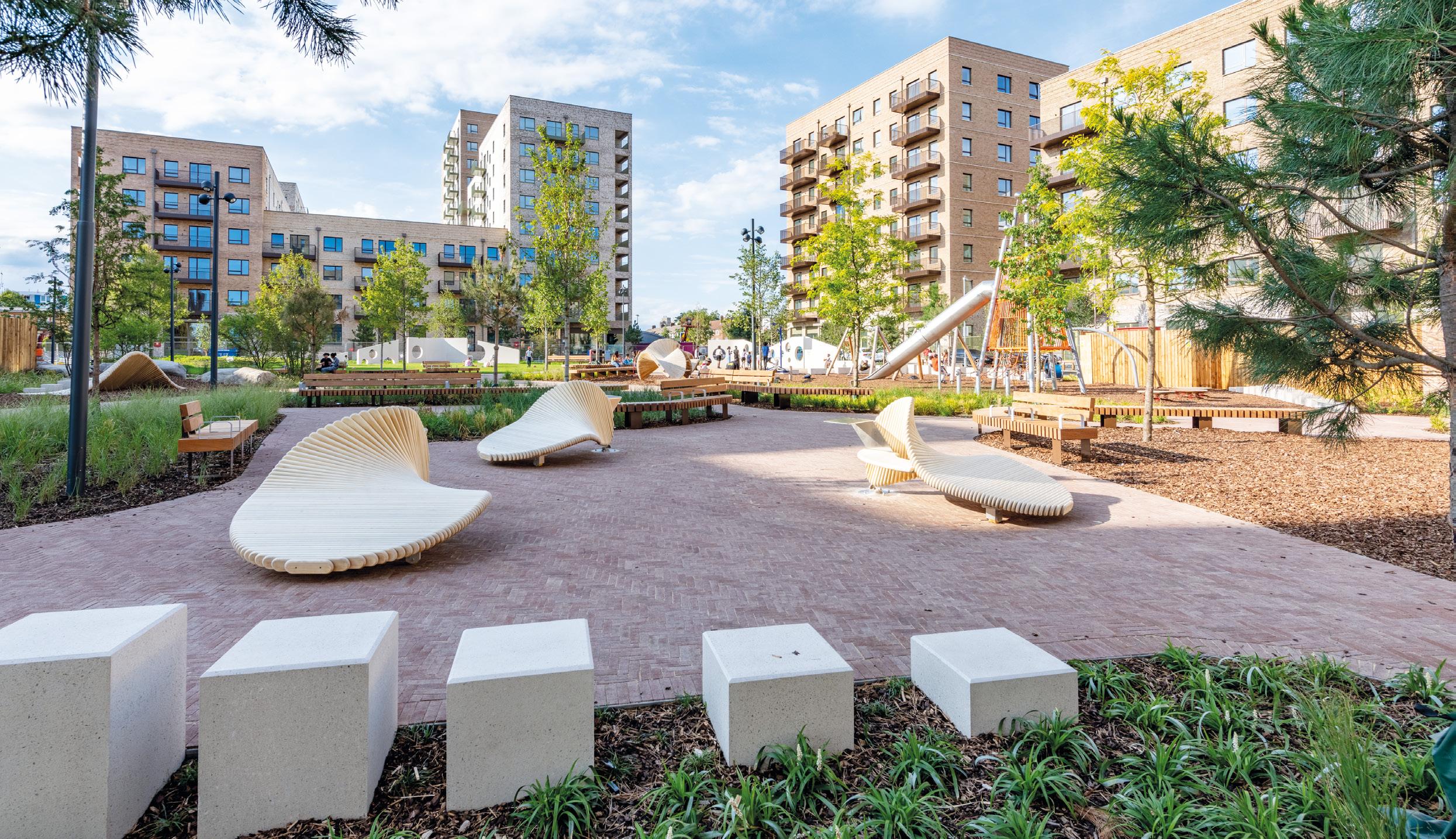
When selecting materials for outdoor use, several key qualities are paramount. Outdoor materials must endure a range of weather conditions, including rain, snow, wind, and UV radiation from the sun. Durability is crucial, as it minimises maintenance needs and reduces both costs and environmental impact. Additionally, longevity is essential to decreasing the frequency of replacements, further conserving resources.
In today’s world, sustainability is more important than ever. The materials chosen for outdoor applications should therefore be responsibly sourced, recyclable, or have a low carbon footprint. This not only supports environmental conservation but also aligns with global efforts to combat climate change. Historically, wood has often been overlooked for outdoor use due to its inherent limitations. Traditional wood
is prone to decay, insect damage, weathering, and water absorption, which leads to swelling, warping, and cracking. These issues necessitate frequent maintenance and can result in the wood losing its structural integrity and aesthetic appeal over time.
Innovations in wood modification, such as the acetylation process used to create Accoya wood, have revolutionised its use in outdoor applications. By modifying the wood from surface to core, the acetylation process changes the cell structure, making Accoya highly resistant to decay and moisture, significantly
“Accoya is one of the few building materials to be Cradle to Cradle Certified® Gold in recognition of its circular economy benefits”
extending its lifespan. This transforms fast-growing, sustainable softwoods into a durable material suitable for demanding outdoor applications.
By overcoming the historical limitations of traditional wood, innovative products like Accoya offer a viable and attractive option for outdoor use. Accoya combines the natural beauty of wood with enhanced performance characteristics, making it ideal for modern architectural and landscaping projects that demand both sustainability and durability.
An example of this is Gascoigne Park, located in Barking, London. This project aimed to create an inviting environment for young children that effortlessly blends functionality with aesthetic appeal. Approximately 15 cubic metres of raw Accoya wood were used in the construction of Gascoigne Park. This FSC (C012330) certified material was sourced by Moveart, a supplier known for
their innovative structures that integrate seamlessly with the natural environment. Accoya is one of the few building materials to be Cradle to Cradle Certified® Gold (Platinum for Material Health) in recognition of its circular economy benefits. Uncoated Accoya wood was chosen for Gascoigne Park due to its exceptionally high performance and barefoot-friendly nature, offering visitors a comfortable experience free from the risk of splinters. As a result, children can enjoy the play structure barefoot with no risk of splinters.
Landscape architect Turkington Martin focused on integrating Accoya wood into the landscape of Gascoigne Park. The architects recognised the unique long-lasting properties, highlighted by its impressive 50-year above ground warranty, and its minimal maintenance requirements. These high-performance benefits led to the specification of Accoya for various elements of the park’s design, contributing significantly to the project’s overall success.
Many softwoods require high levels of maintenance to preserve them, and sustainably sourced hardwoods are often challenging to find in good supply. Innovative processes and ways of naturally modifying timber, like Accoya’s acetylation process, enhance wood performance.
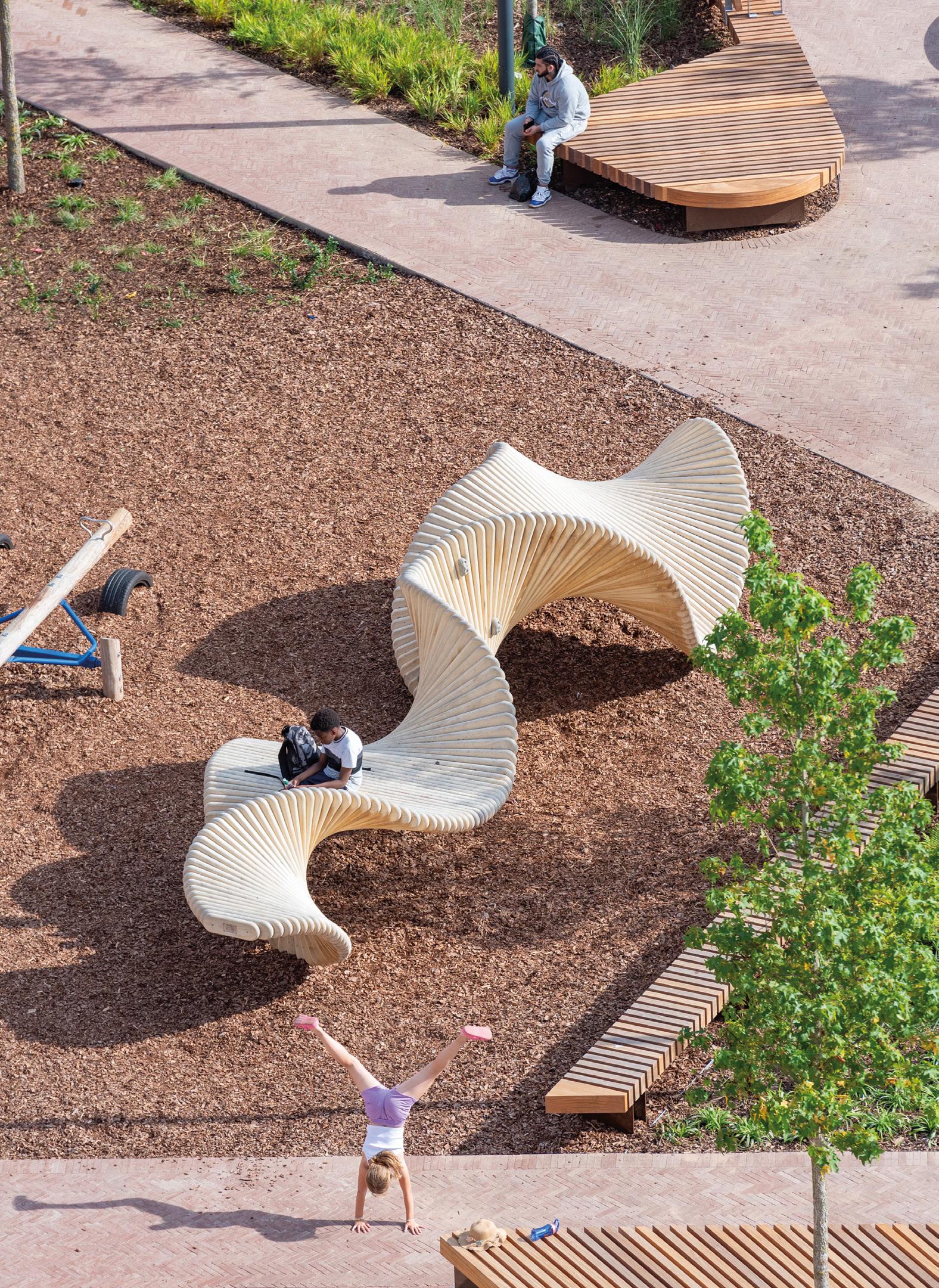
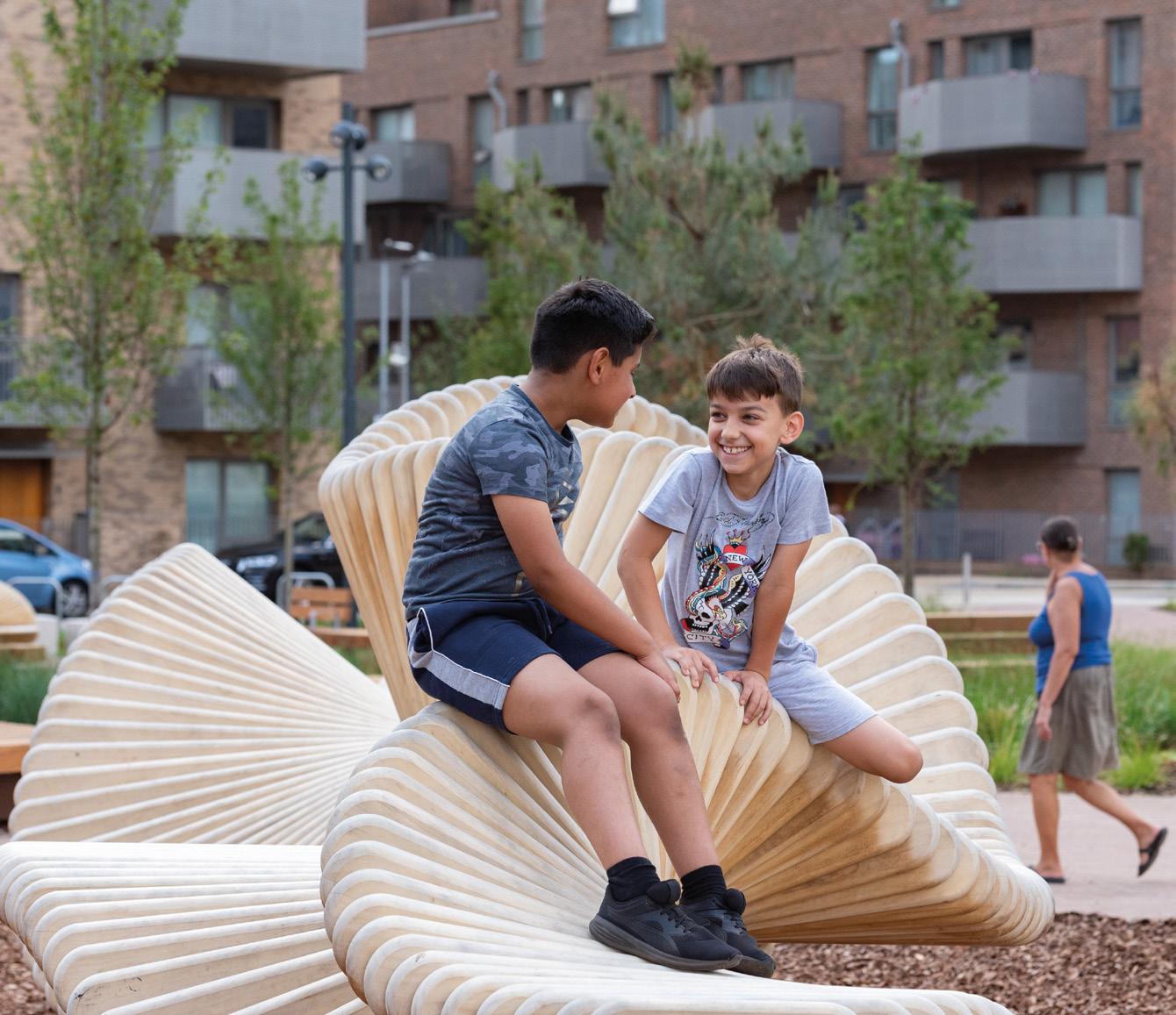
“Accoya wood undergoes a treatment that modifies its cell structure, making it highly resistant to decay and moisture, significantly extending its lifespan”
This project is particularly unique due to the inclusion of three object circles, which are the first moveable Moveart sculptures ever. They allow users to adapt common public spaces in their own individual way, reflecting the changing nature of each object.
Gascoigne Park stands as an innovative example of Accoya wood’s high performance and sustainability, ensuring it remains a timeless attraction for generations of children to enjoy for years to come.
www.accoya.com
Finsa presents Fibrapan Bio and Fibranatur Bio
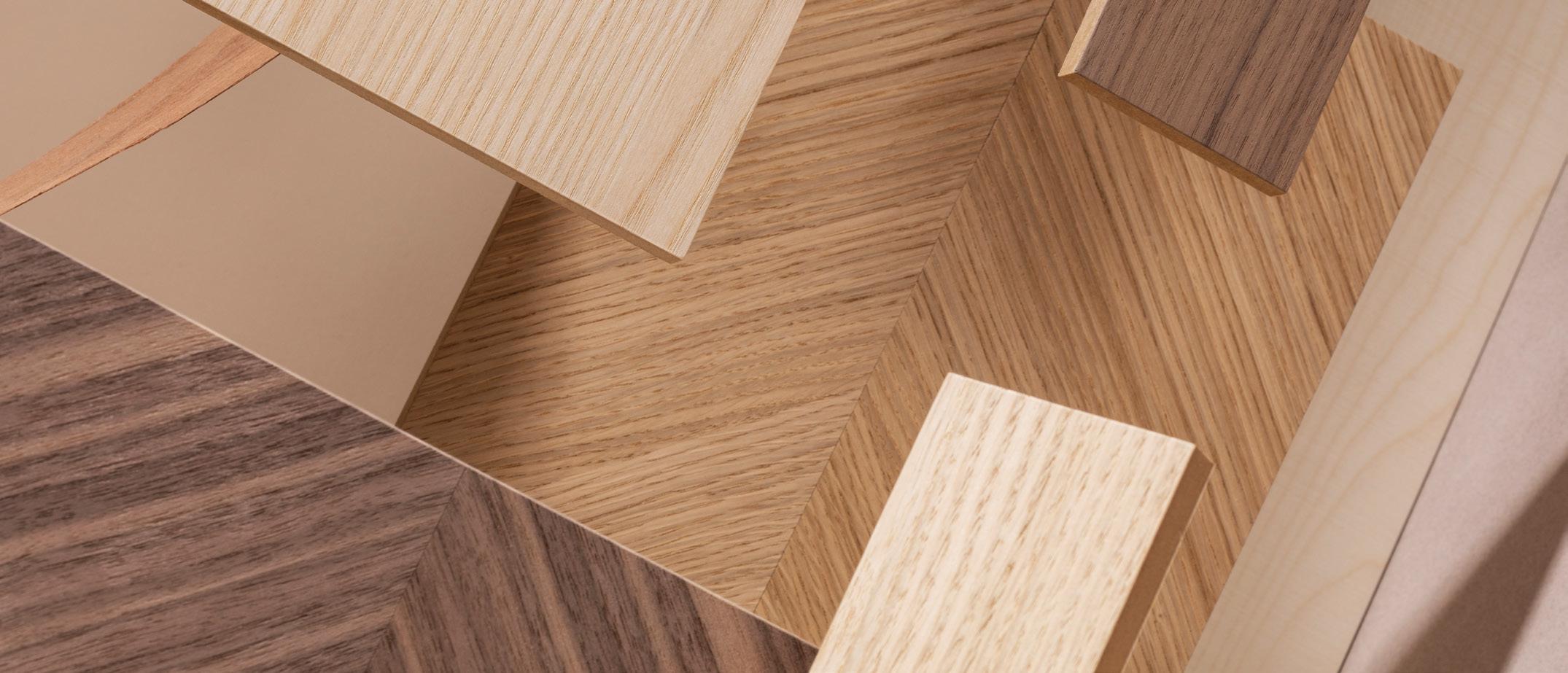
For more than 90 years, Finsa has devoted its efforts to continuous improvement and investment in production and product development, bringing an artful selection of decoratives, veneers and textures to the interior design and manufacturing industries. One of the latest additions to its portfolio – Fibrapan Bio and Fibranatur Bio – is testament to this investment.
The award-winning Fibrapan Bio is a wood fibre board manufactured with bioadhesives that have been obtained from the bark of the tree itself, and with a paraffin of plant origin that allows the board to have a content of natural components greater than 99%.
Made with local wood from sawmill by-products and responsibly managed
forests, with PEFC/FSC certification, Fibrapan Bio is BREEAM, LEED, WELL and LBC certified for its sustainability properties as a healthy and responsible alternative that uses an adhesive whose production does not interfere with the food chain. Due to its biological origin, Fibrapan Bio has no added formaldehyde, holding the same emission levels as natural wood.
Fibrapan Bio is manufactured using Finsa’s exclusive SIPS (Steam Injection Press System) technology, which allows rapid curing of the bio resin and exhaustive control of the density profile and moisture distribution. This process allows for unrivalled machining properties and quicker preparation times to reach a quality finish.
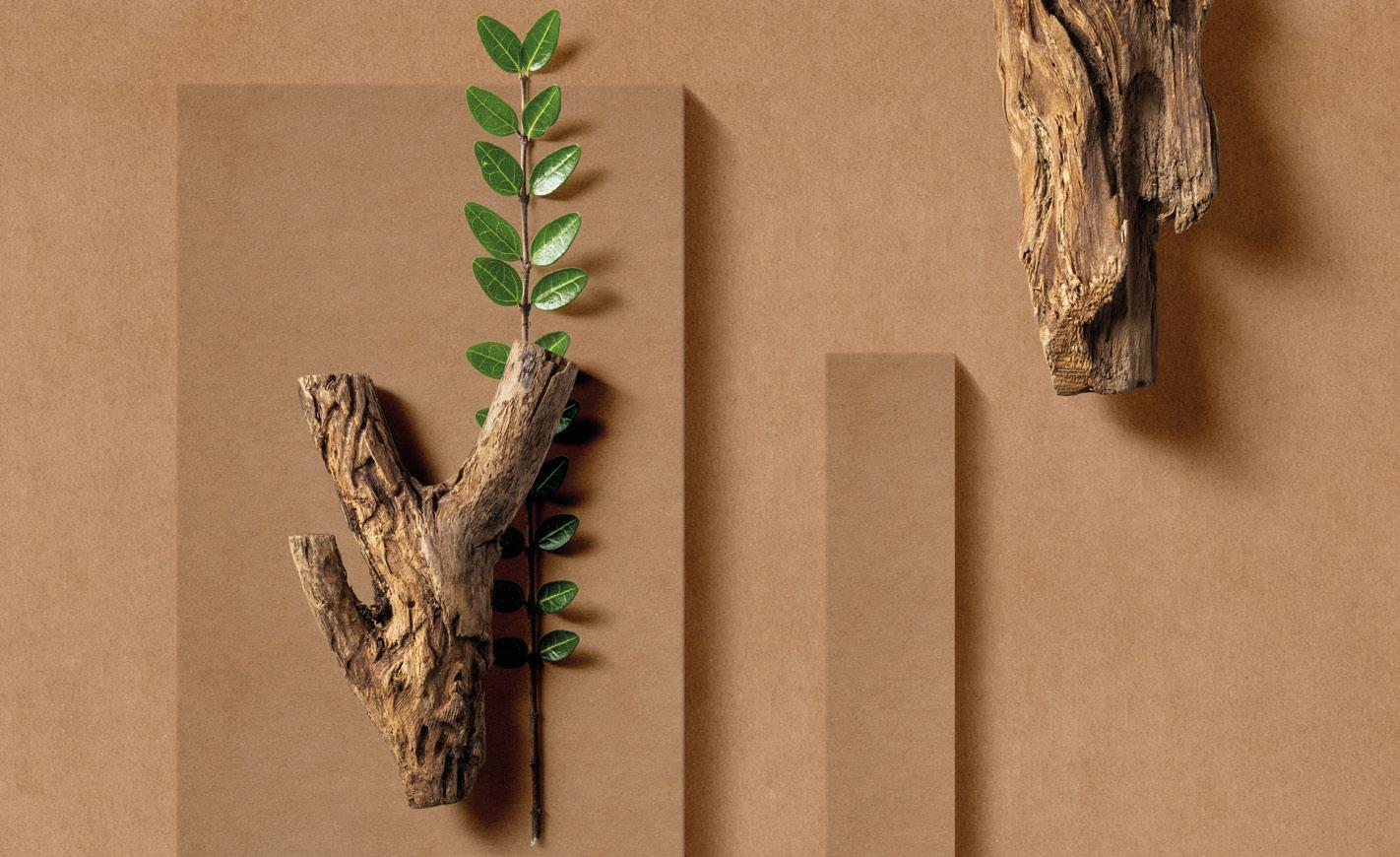
“The award-winning Fibrapan Bio is a wood fibre board manufactured with bioadhesives that have been obtained from the bark of the tree itself, and with a paraffin of plant origin”
As a panel that is Service class 2, Finsa is proud to claim that its moistureresistant properties make Fibrapan Bio “the first MR MDF to be made from over 99% biological material”. This makes it eminently suitable for demanding applications in humid environments.
To provide a decorative solution, Finsa has also launched Fibrapan Bio combined with a natural wood veneer: Fibranatur Bio. Finsa is considered a market-leading brand for veneered boards – recognised for their consistent quality – and possesses one of the largest production facilities in Europe.
Fibranatur Bio will be added to Finsa’s extensive UK stock range in Plus Grade European Oak, sourced from sustainably managed forests and available through its distribution network. Other species are also available from the Natur and Studio Natur ranges. www.finsa.com
Fibrapan Bio
Sustainable is the new normal at GRASS Group
Since the end of 2010, the GRASS Group has been certified in accordance with the ISO 14001 international standard for environmental management systems. However, its high level of environmental awareness and projects built on this go back many years. Taking personal responsibility is part of the company’s identity.
The GRASS Group sees the present as part of the future, and therefore believes that environmental protection is an important prerequisite for sustainable company success. Working with this mindset means conserving resources and creating ecologically sound production conditions – something the GRASS Group works on every single day.
Key measures and success’ that have had an impact include:
• 75% green energy – 75 per cent of energy demand at the Höchst site is met by the company’s own combined heat and power plant.
• 636 tons – As a result of wideranging energy efficiency measures, CO2 emissions have been reduced by 636 tons per year.
• 100% recycled steel – 100% of steel waste generated during production is recycled.
• Annual power consumption has been reduced by 11 million kW/h. This corresponds to an average annual consumption of around 2500 single-family homes.
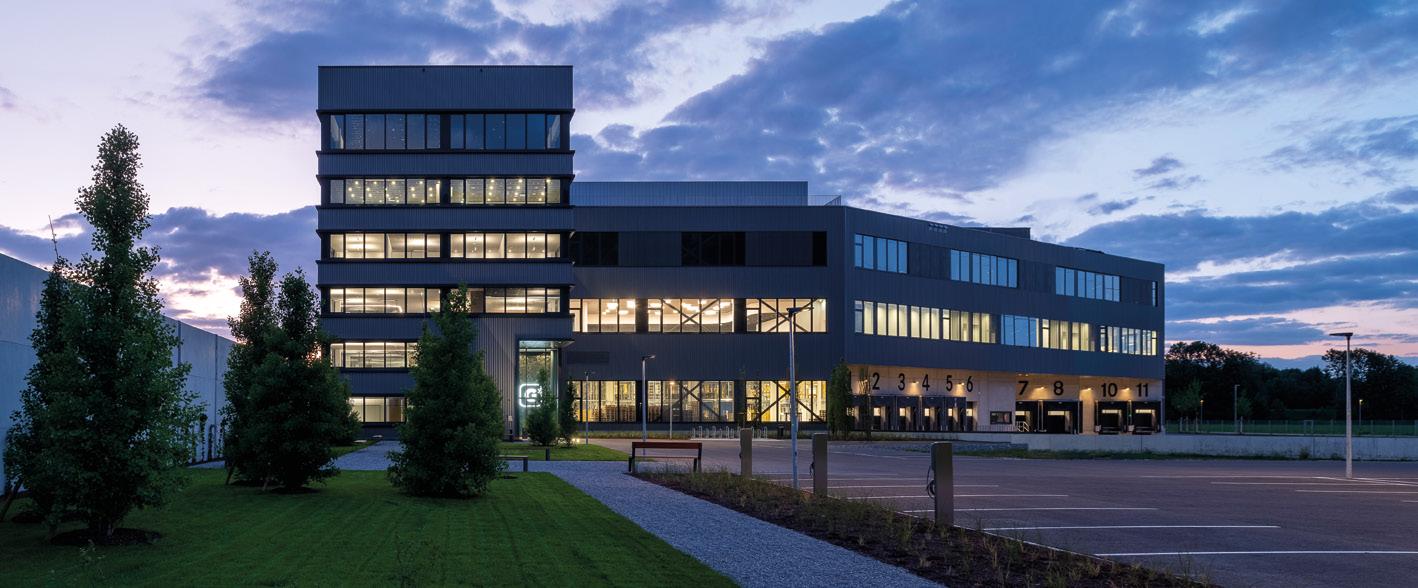
• 50% waste reduction – The volume of non-recyclable waste was reduced from 1,530 t to 756 t per year.
• 100% recycling of steel waste. approx. 6,000 tons per year.
• 30 electric charging stations for the increasing number of electric vehicles.
• 1140 Solar panels – with an output of 421kWp generate around 400,000 kWh of electricity every year. This means that GRASS Group generates more than 70% of its electricity requirements and also avoids around 200 tonnes of CO2 emissions.
• New headquarters in Hoenems built as a fully passive building. It’s not just in production that GRASS Group is treading new, sustainable ground. Its drawer systems are almost 100 per cent recyclable and contain no hazardous materials or substances listed in the REACH regulation.
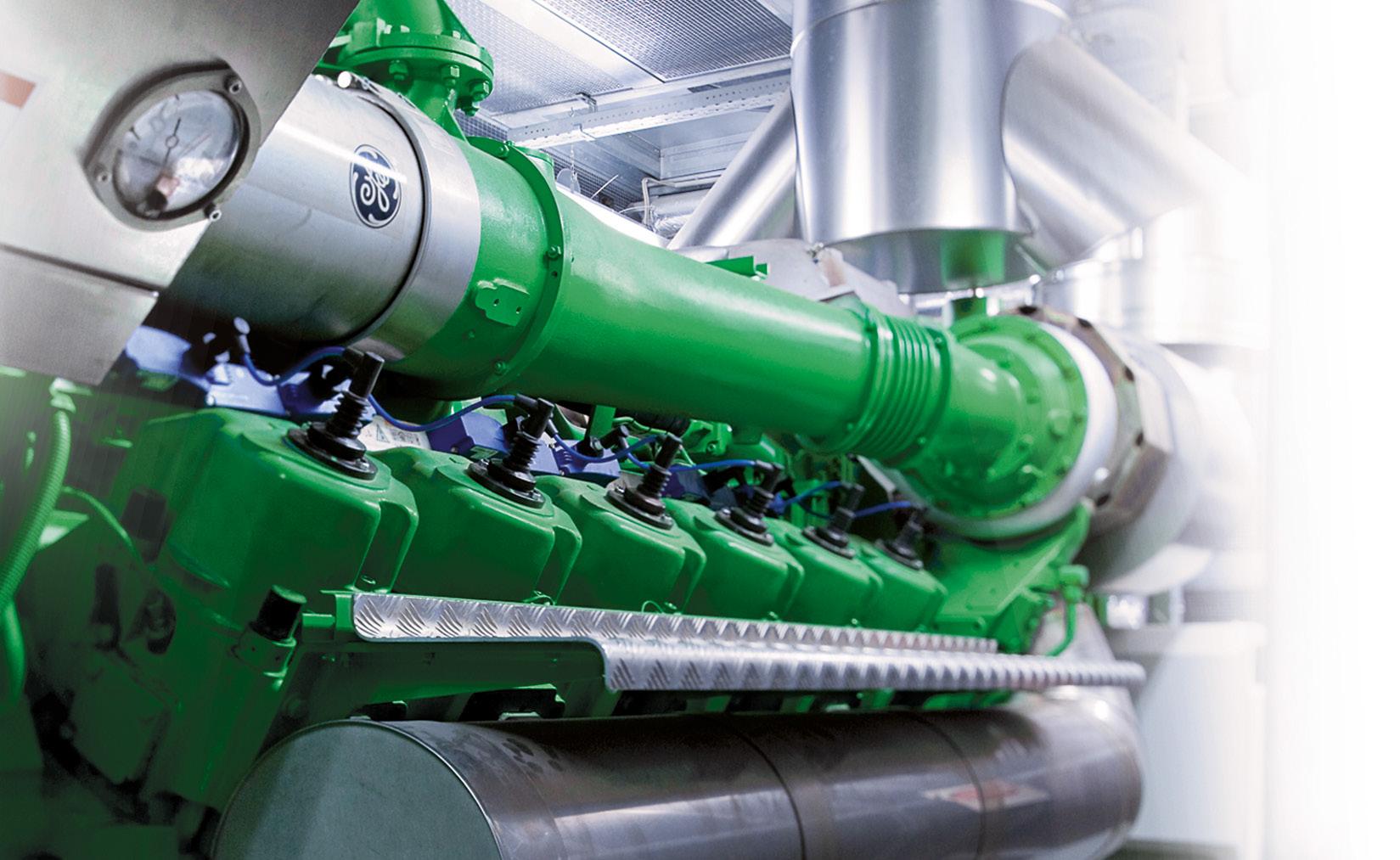
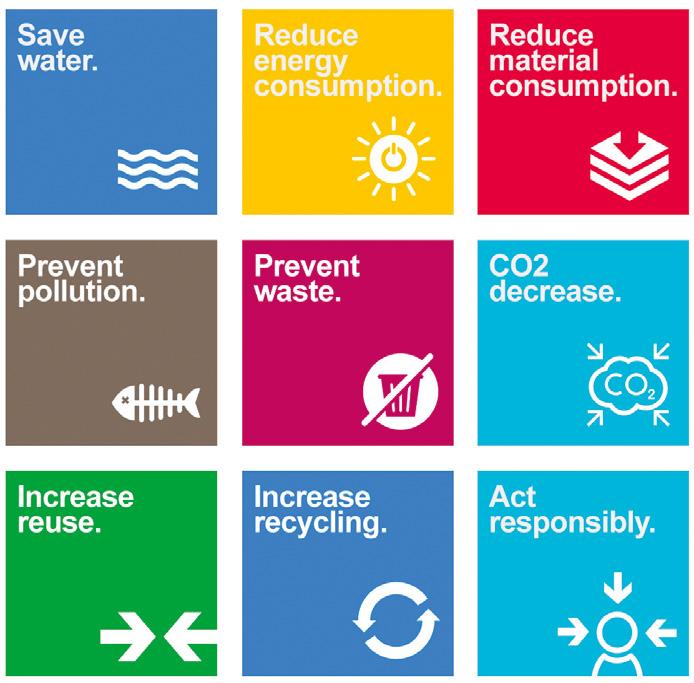
“The GRASS Group sees the present as part of the future, and therefore believes that environmental protection is an important prerequisite for sustainable company success”
The company has developed in Vionaro V8 a sustainable drawer system which not only can be produced and coated in an environmentally friendly manner, but whose materials can also be recycled by material type.
The concept of the world’s first allmetal drawer side resulted from this. Consequently, GRASS Group has completely dispensed with plastic elements, foams and adhesives in pursuit of robustness, sustainability and recyclability.
The company is convinced that climate protection begins with the small things. And with the V8 Slim Drawer System, every consumer can make a contribution! www.grass.eu/en/
HOMAG leads the way towards sustainable manufacturing with HOMAG CARES initiative
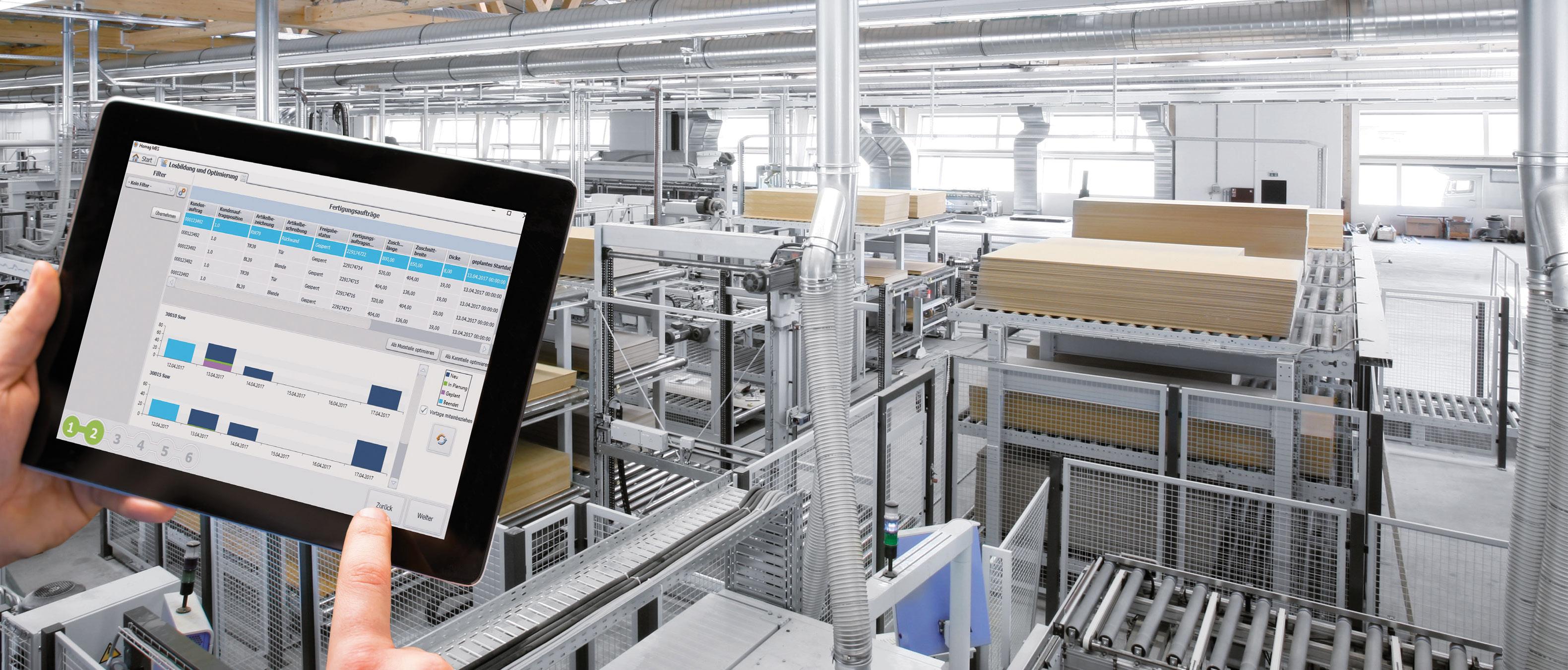
HOMAG, a global leader in woodworking machinery, has long been dedicated to environmental stewardship and sustainability. Now, with the launch of HOMAG CARES, the company is intensifying its commitment to sustainable practices and setting ambitious climate targets for the future.
“HOMAG has always prioritised environmental responsibility,” says Simon Brooks, Managing Director at HOMAG UK. “With HOMAG CARES, we are consolidating all our sustainability efforts under one comprehensive initiative to achieve our climate targets by 2030: a 70% reduction in emissions by HOMAG and a 15% reduction by our machines.”
Smart software solutions for sustainable production
HOMAG offers a suite of software solutions designed to optimise woodworking processes and support sustainable practices. These include intelliGuide for intuitive machine operation, and intelliDivide Cutting & Nesting for minimising waste and
maximising machine productivity.
Additionally, the ControllerMES software enables intelligent planning and monitoring of production processes, while materialManager provides real-time insights into inventory status and material usage. And lastly, with HOMAG’s Edge Data Package, manufacturers can access digital edgeband management solutions for enhanced transparency and efficiency.
“These software solutions represent a significant leap forward in efficiency and sustainability within the woodworking industry,” explains Simon. “Working hand-in-glove with our machines, they’re helping manufacturers to optimise processes, reduce waste, and achieve their sustainability goals.”
“With HOMAG CARES, we are consolidating all our sustainability efforts under one comprehensive initiative to achieve our climate targets by 2030”
Efficient machines built for sustainability
HOMAG’s commitment to sustainability extends to its machine manufacturing processes, where durability, environmental considerations, and operator comfort are paramount.
The company employs innovative technologies to reduce noise and dust emissions, utilising low-noise tools and motors alongside Dust-Flow-Control systems for optimal dust extraction.
The machines are also designed with ergonomic operation in mind, featuring adjustable controls and operating units that cater to individual operator preferences. Moreover, HOMAG offers comprehensive life cycle services to ensure the longevity and performance of its machines.
“We’re committed to ensuring HOMAG machines are not only up-to-date for years but also considerate of both people and the environment. In other words, our goals for customer satisfaction and environmental responsibility are seamlessly aligned.”
Networked production with HOMAG
Reducing energy demand
Through strategic initiatives and cuttingedge solutions, HOMAG aims to reduce energy demand and promote renewable energy sources. One key aspect of this commitment is an investment in photovoltaic systems which harness solar power to adapt the company’s infrastructure to sustainable energy practices. Another is the presence of an economy mode on HOMAG machinery, which enables energy-saving standby mode at the touch of a button, further enhancing resource conservation.
In addition, HOMAG prioritises efficiency and sustainability in its supply chains, development, and manufacturing processes through a “Local for Local” approach. “By sourcing materials and manufacturing locally whenever possible, we can reduce energy consumption and support regional economies.”
Promoting renewable materials and supporting local communities
With a vision of contributing to a sustainable future, HOMAG advocates for the use of renewable materials, particularly wood, and supports local forestry projects and timber house construction initiatives.
“At HOMAG, we believe in the importance of promoting renewable materials and supporting local communities. Through targeted donations and initiatives, we contribute to the preservation and enhancement of
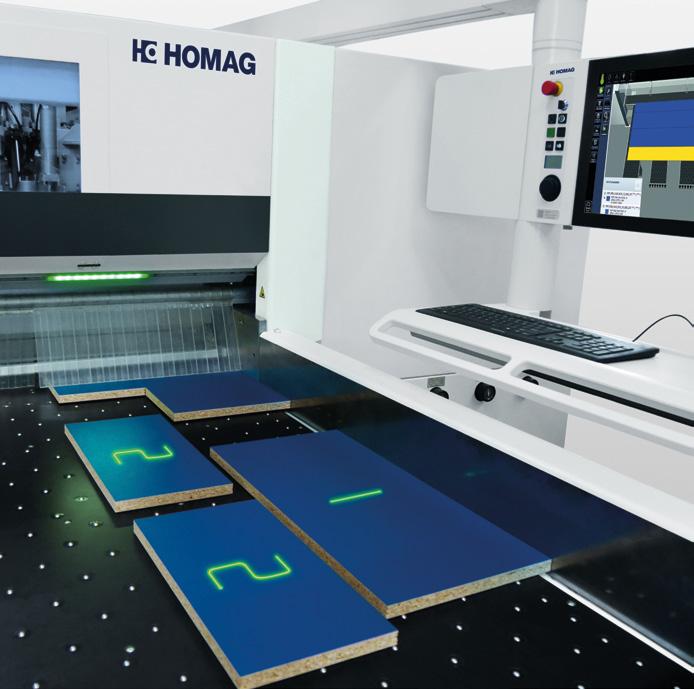
regional forests and provide technology and expertise to advance sustainable timber house construction.”
Creating
a positive work environment
HOMAG values its employees and is committed to providing a positive and supportive work environment through talent management, flexible working arrangements, and social engagement initiatives.
“We believe our success is intrinsically tied to the well-being and satisfaction of our team members,” explains Simon. “Over the years we’ve cultivated a work environment in which employees feel challenged, supported, and valued. A big part of this is our talent management approach, which focuses on promoting and developing qualified personnel to ensure that we remain properly positioned for the future.
“We also provide attractive working models that align with the spirit of the times, offering flexible working that
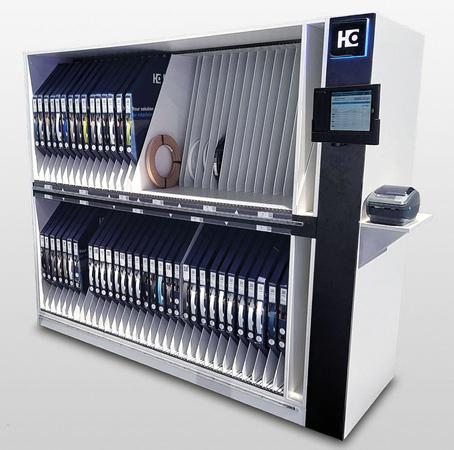
caters to individual needs, including options for remote work and home office arrangements.”
Along with prioritising the well-being of employees, HOMAG extends its commitment to social responsibility through supporting global institutions with donations and gifts in kind. “It’s our privilege to partner with and support several organisations who are doing fantastic work in local communities across the globe.”
With HOMAG CARES, HOMAG reaffirms its commitment to sustainability, innovation, and social responsibility, setting a new standard for the woodworking industry. As Simon Brooks concludes, “HOMAG is your solution for sustainable success in the future.”
For more information about HOMAG, its machines, and its sustainability initiatives, please visit homag.com. 01332 856424
info-uk@homag.com www.homag.com
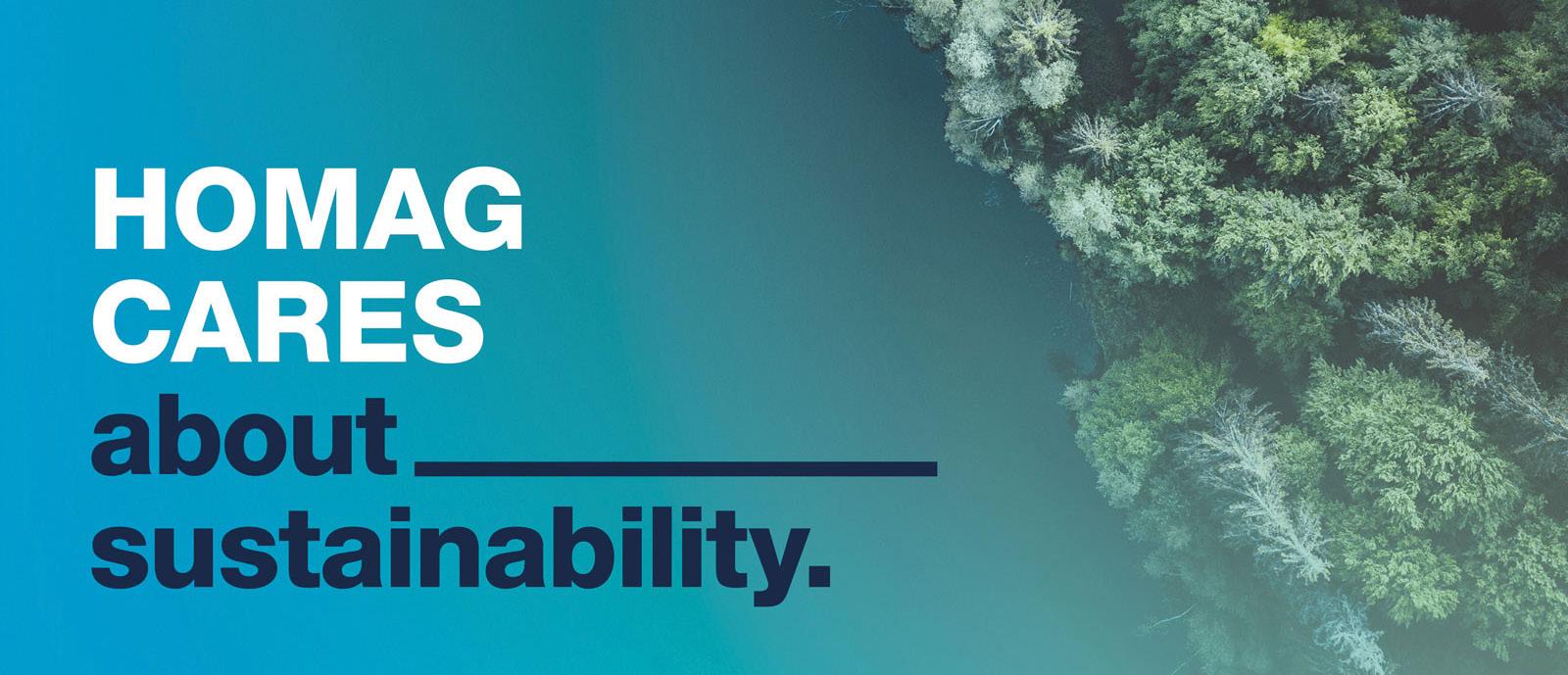
How your tooling supplier can help your business strive towards a sustainable future
As the world grows increasingly globalised, material and electricity costs rise and consumers are looking for sustainable products – it’s time for furniture and joinery manufacturers to consider the sustainability of their suppliers as well as their products.
Sustainability is one of Leitz Tooling’s core values and sustainable practices are implemented across the entire business, from tool design to the way Leitz manufactures and services its products.
During manufacturing, Leitz embraces the circular economy by using recycled materials from their global tool recycling programme. The programme collects endof-life and damaged tools from across the globe so they can be broken down and their materials, like carbide, can be recycled. These materials are then reused to manufacture new tools at the many Leitz manufacturing plants across the globe. The Leitz tool recycling programme is open to the public, not just for Leitz customers.
In the UK and many other locations, Leitz also supplements their manufacturing centres with solar power: In 2023 Leitz UK saved 88 tons of CO2 through its solar panels. All unused electricity is put back into the national grid so others can also benefit from the solar power.
However, sustainability isn’t just about recycling and sustainable manufacturing, Leitz products themselves also help their
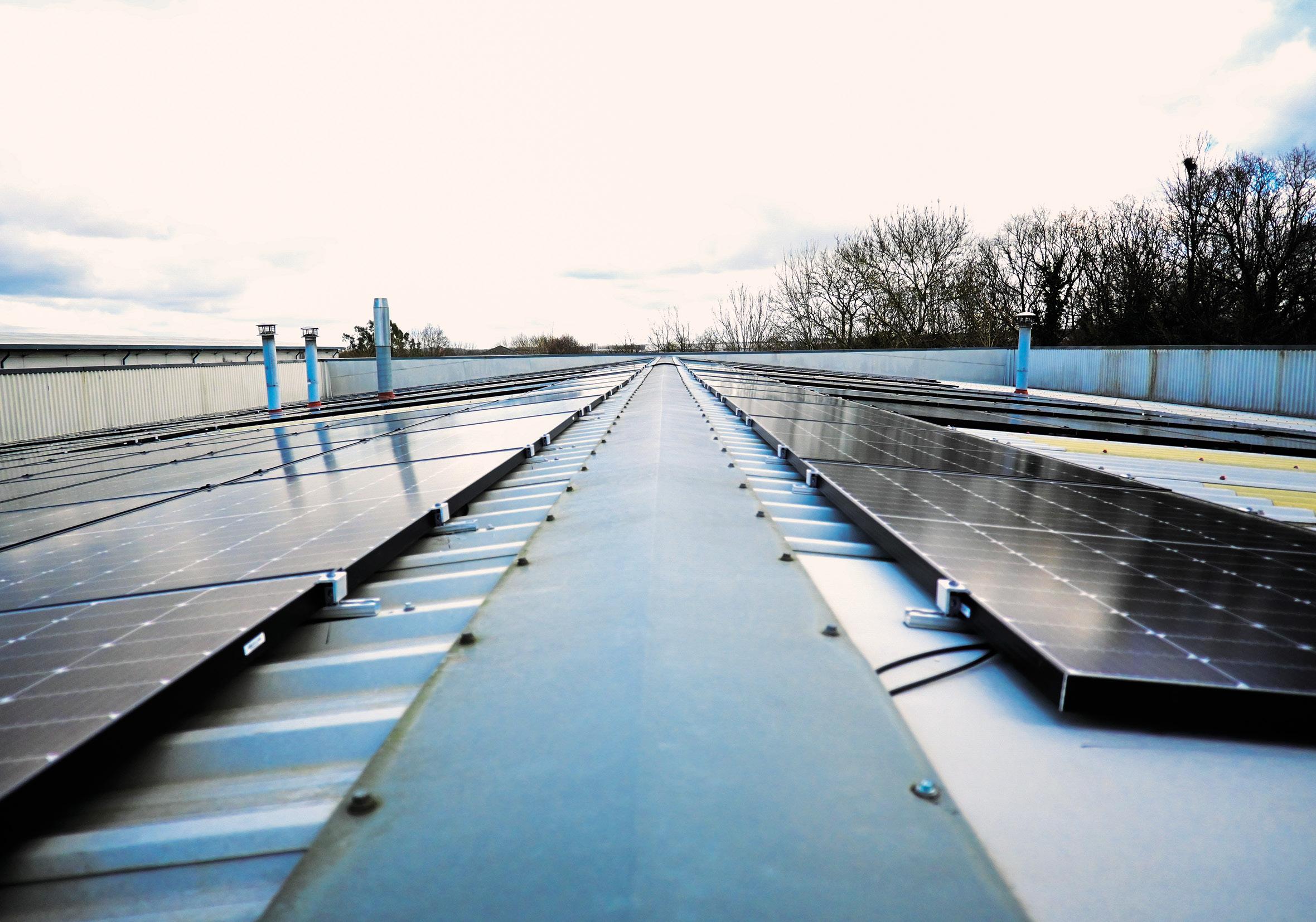
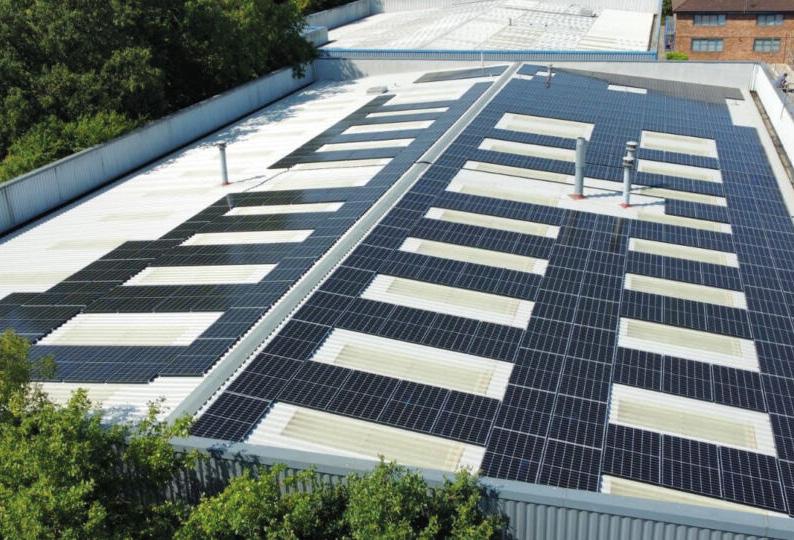
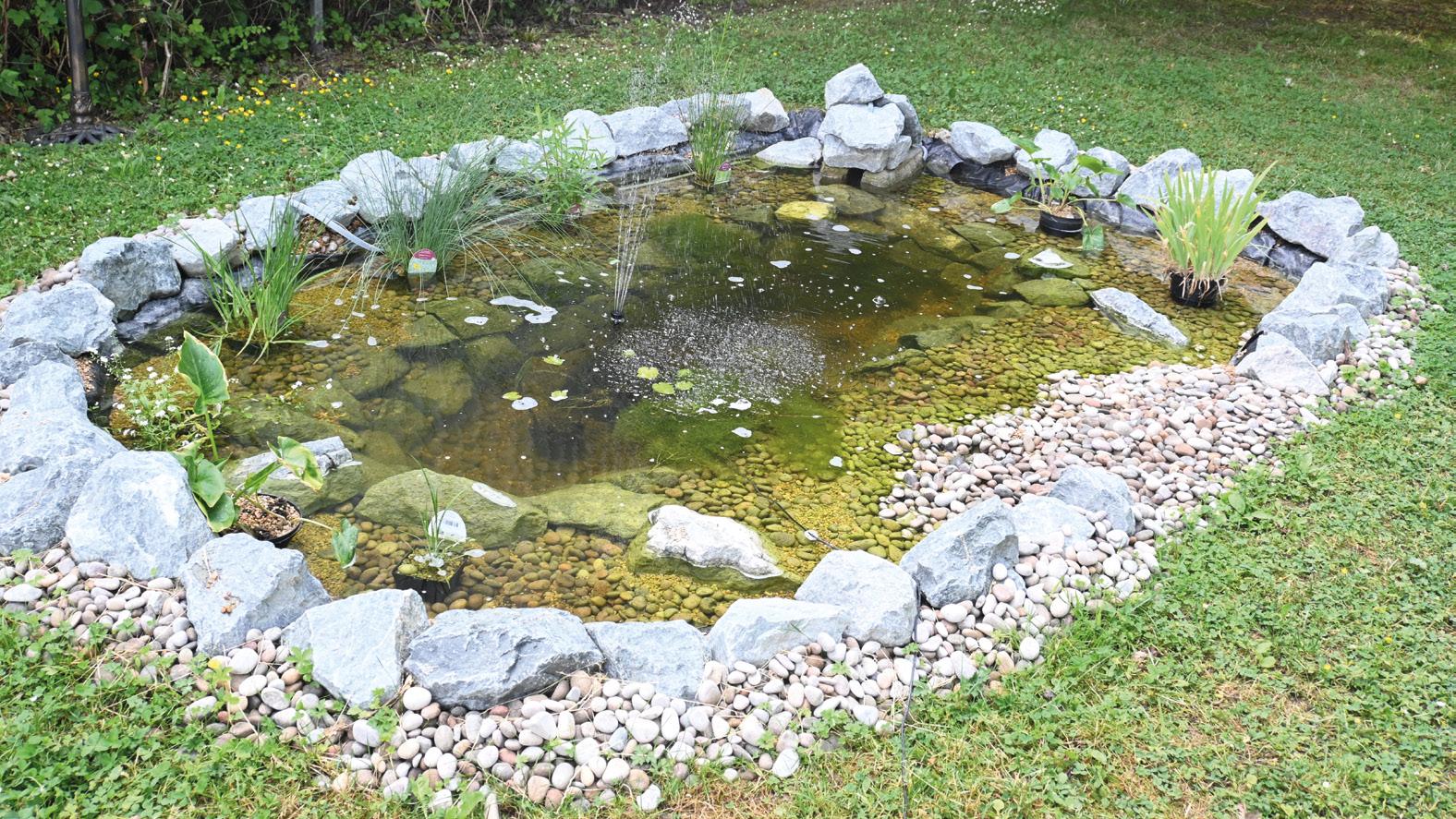
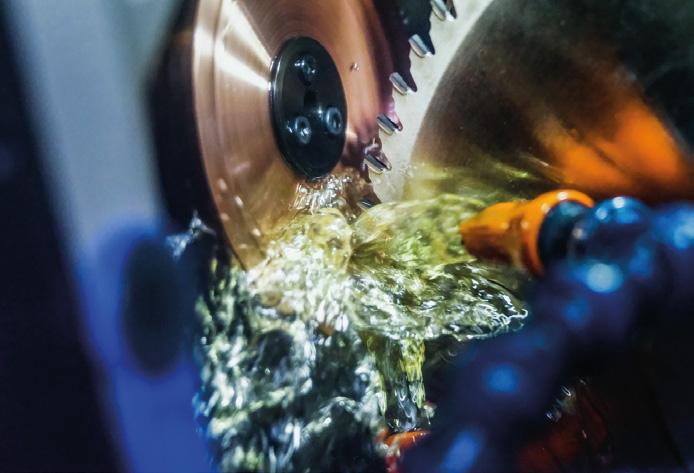
customers achieve sustainability goals.
As a provider of high-quality tooling, Leitz products are engineered to provide finish cut quality. This can severely reduce the volume of rework, rectification and wasted material throughout the production process.
Additionally, Leitz has many product groups specialised in reducing waste such as thin kerf sawblades designed to reduce the amount of material being cut during sawing operations. The solid construction and precision engineering
Solar panels used to supplement manufacturing and tool service
A newt pond installed at the Leitz production centre in Harlow
Solar panels
Sustainable sharpening of a carbide saw blade
of Leitz tools also means that they last longer when run correctly than tooling from other suppliers.
When partnered with technological innovations like Marathon coating, which reduces friction for faster machining and extends tool life by about 30%, Leitz customers are having to replace their tooling far less frequently – enabling a more sustainable and efficient manufacturing process for their customers.
In addition to supplying sustainable tooling and implementing sustainable business practices, Leitz also emphasises sustainability through their tool service and tool management programmes.
Leitz tool service in the UK is also supplemented by solar power, allowing them to perform complex operations like diamond erosion at a minimal cost to the environment. With the sharpening service, Leitz can typically get between 15-20 sharpens on a saw blade depending on the blade type and the wear. This is significantly more sharpens than most service providers in the country, allowing

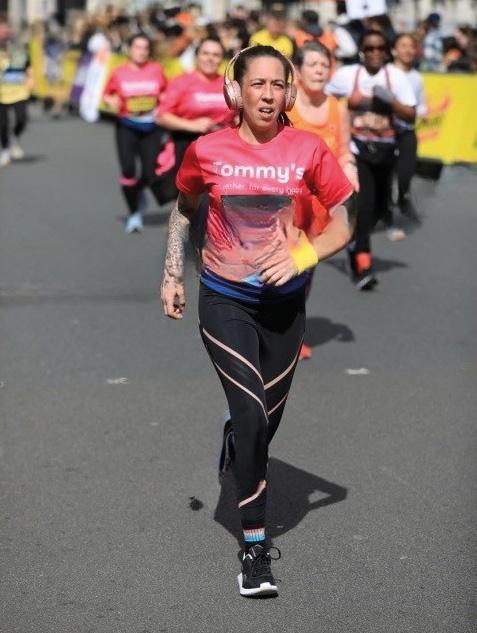
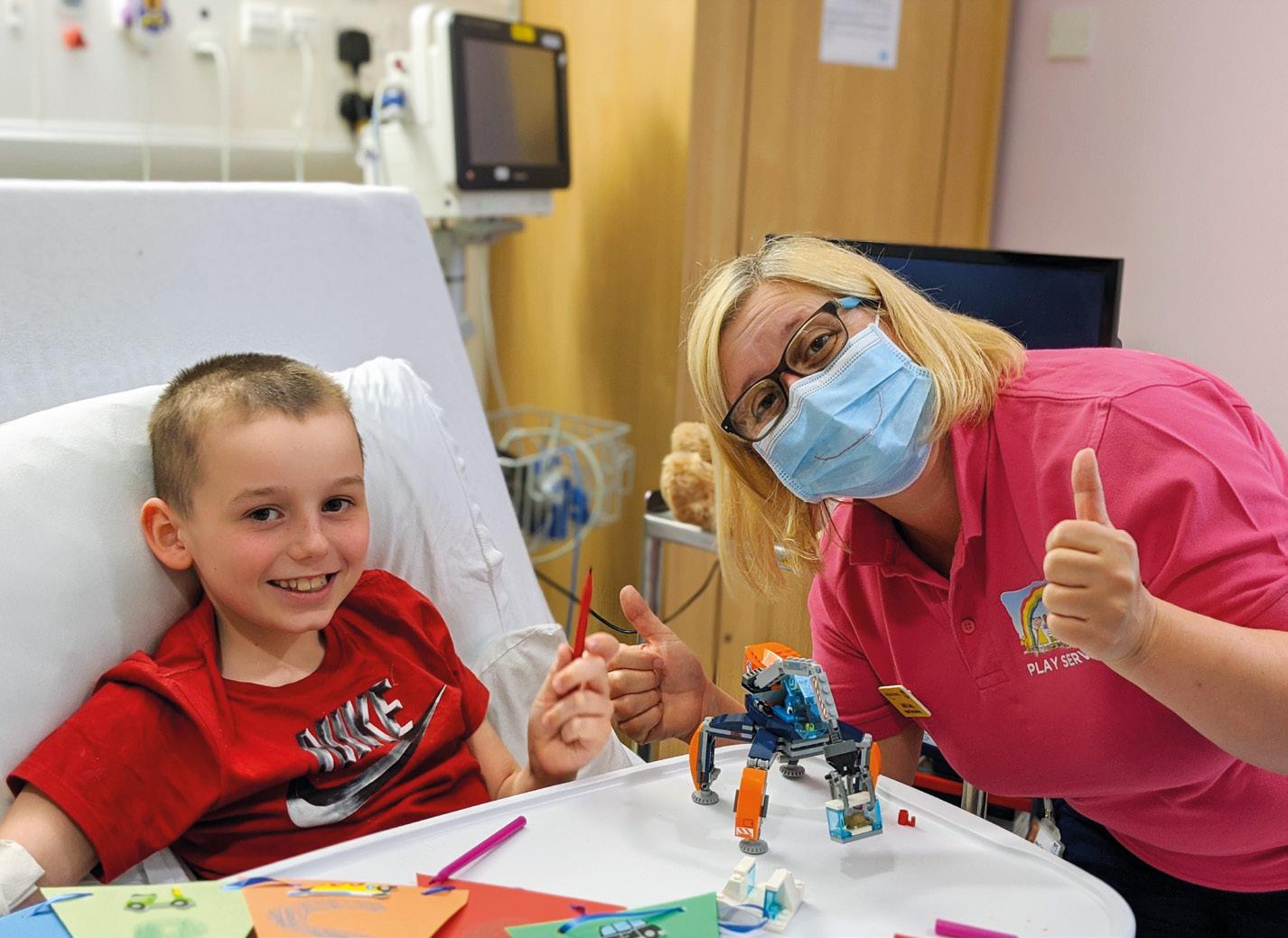
manufacturers to use their tools for far longer before needing to replace them, as well as saving costs on new tooling.
The Leitz tool management program is a system that tracks the life, number of sharpens and condition of tooling as it is sent off to be sharpened and serviced by Leitz. The system allows Leitz to collect
“Leitz tool service in the UK is also supplemented by solar power, allowing them to perform complex operations like diamond erosion at a minimal cost to the environment.”
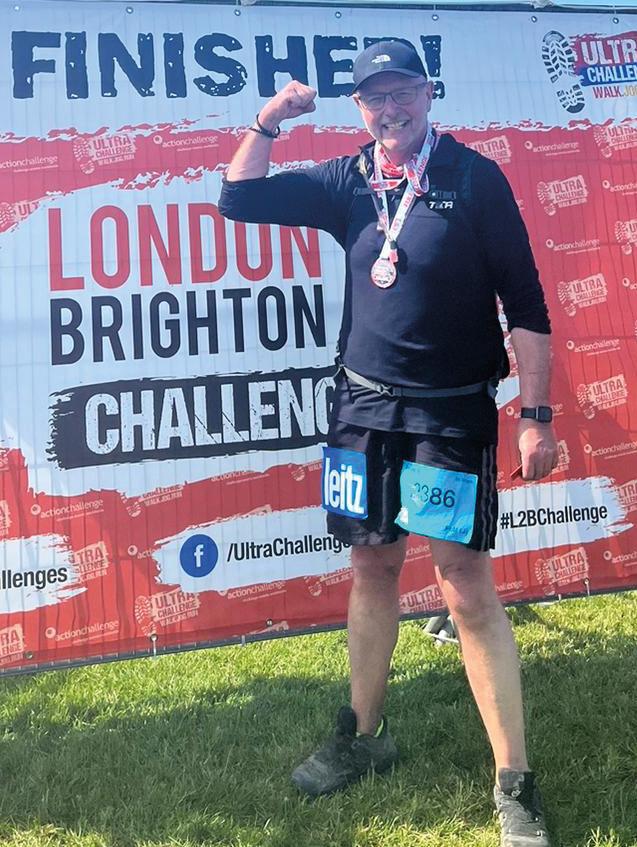
lots of data on the tool use, which is used to provide manufacturing, machining and process optimisation recommendations. Leitz can analyse damage to the tools and suggest improvements to reduce waste and wear during the manufacturing process. This technical support helps manufacturers keep their tools for longer – reducing the number of materials needed for producing timber products and also helps Leitz to set expectations on how many sharpens a tool should get.
The WeCare program is Leitz Groups’ international sustainability campaign that takes place throughout April every year. Currently in its third year, this program brings together over 4000 employees in over 40 different countries together to complete sustainability and social projects. Leitz UK used this as an opportunity for a litter pick in the forest located behind the company’s headquarters in Harlow, to build a pond to provide a safe environment for endangered newts, and also installing bird houses and insect hotels across their grounds. The WeCare campaign also includes social sustainability through partnering and raising funds for influential British charities such as: The Brain Tumour Charity, Glasgow Children’s Hospital Charity and Haven House Hospice. 01279 454530 contact-uk@leitz.org https://shop.leitz.org
Carbide tips being manufactured from recycled Tungsten Carbide
Leitz partners with Glasgow Childrens Hospital Charity to donate all revenue from Joinery Network events
Jo tackles Tommy’s Marathon
Sustainability has always been at the forefront of Ranheat’s DNA
Chris Franklin discusses Ranheat’s many attributes when it comes to sustainable manufacturing ...
Ranheat’s origins were in a small city in Denmark, called Randers. Denmark had no oil, no gas and no coal. The UK was, in contrast, an island of coal in a sea of oil.
Denmark’s lack of fossil fuels led them to utilise what was sustainable, in this case – wood and straw. With a cold sub-zero winter climate, wood and straw became Denmark’s fuel source, which led to a dependence on these fuels.
During the energy crisis in the 80’s the United Kingdom began to look at sustainable fuels, wood and straw, as an alternative to oil, mainly due to OPEC raising prices on the world market. So, the shift in the UK to renewables began out of rising costs, not the need for sustainability.
Ranheat Engineering Ltd. started manufacturing in the UK in 1990 for a number of reasons. Denmark was an expensive place to manufacture and shipping heavy bulky goods across the North Sea by ships was expensive. The rise in oil prices hit transport costs severely. Ranheat Energy A/S was unsustainable to manufacture in
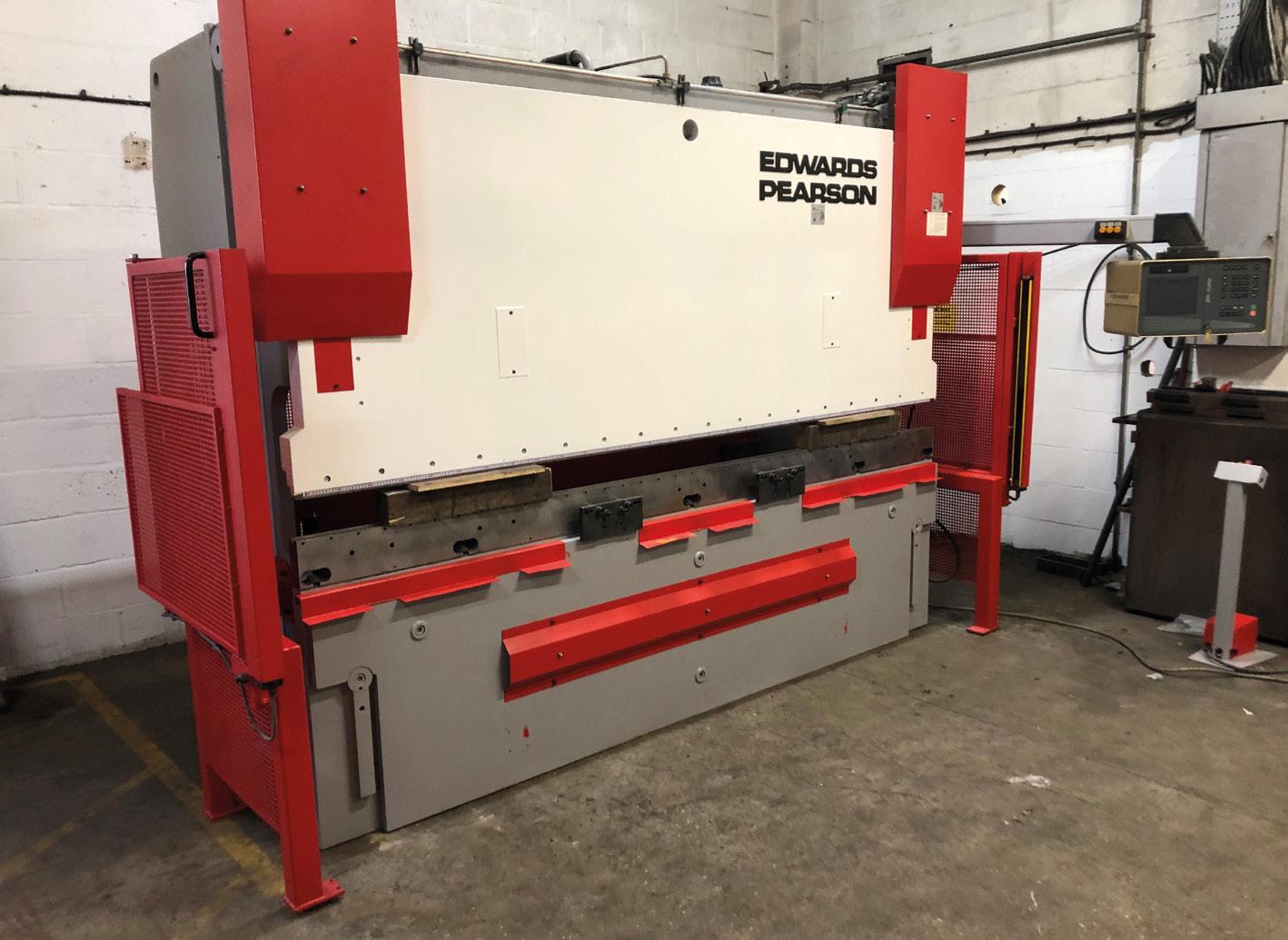
so closed. Ranheat
Ltd started manufacture in February 1990 and was 100% owned by Chris and Barbara Franklin.
New designs emerged using the Danish experience and know-how Chris had gained while working for the Danish Company. He then applied the technology but tailored the designs to suit manufacturing in a sustainable way in the UK.
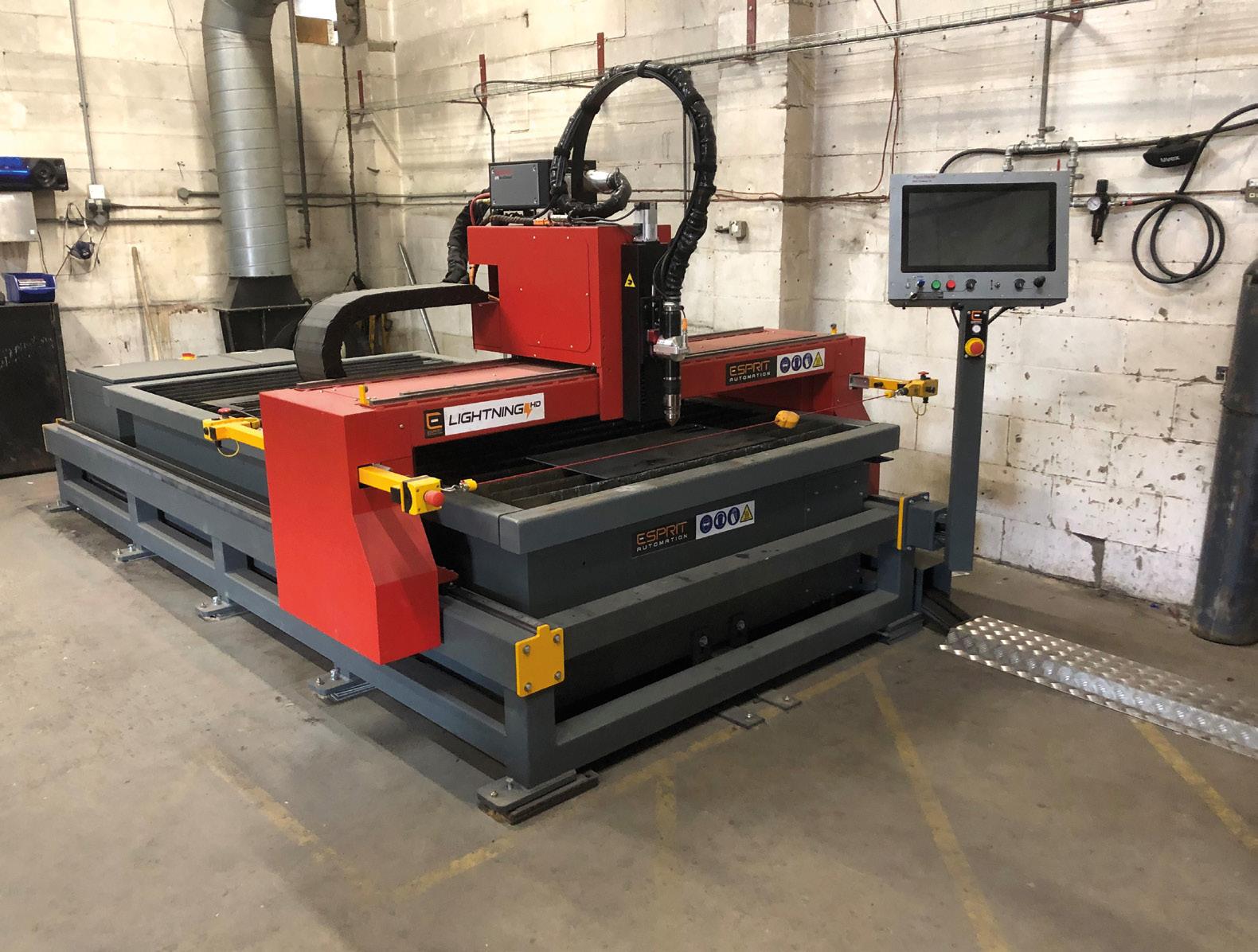
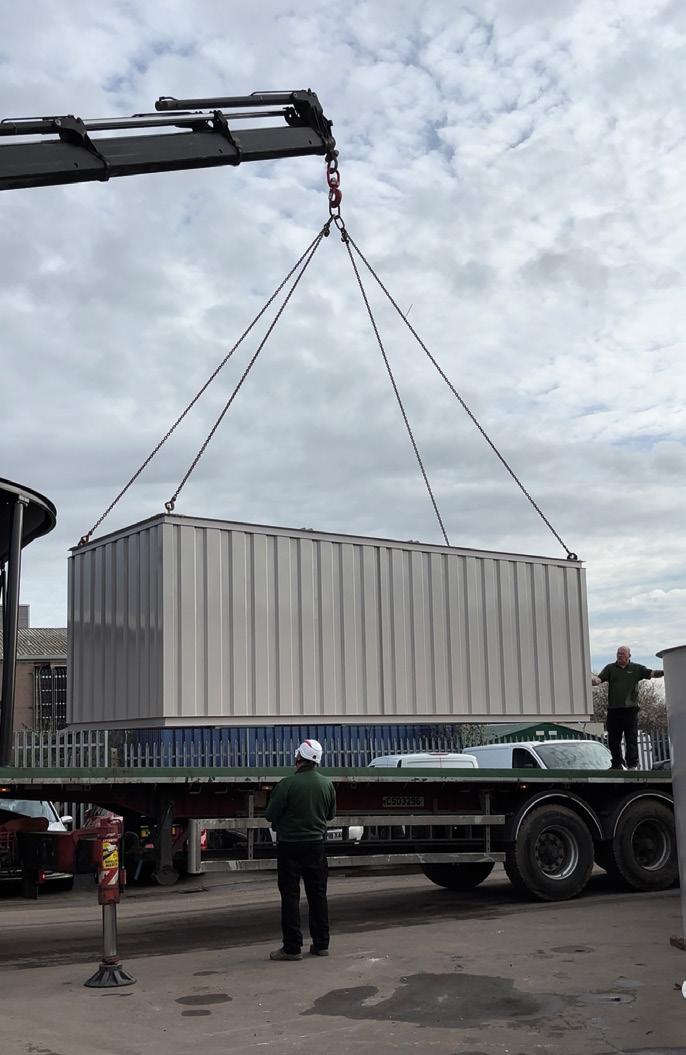
“New designs emerged using the Danish experience and know-how Chris had gained while working for the Danish Company. He then applied the technology but tailored the designs to suit manufacturing in a sustainable way in the UK”
Denmark,
Engineering
Ranheat’s current 100 tonne seven-axis CNC Brake Press for folding metal has a 3m bed
Ranheat’s current CNC plasma cutter capable of cutting 25mm plate with ease
Ranheat Engineering Ltd establishes itself in the UK
The first step was to re-design the equipment around standard sheet sizes, to reduce waste of raw materials, then to invest in folding equipment, known as a Brake Press.
In the early days, metal was mainly cut using a guillotine, which restricted cuts to straight lines.
CNC plasma cutters were beginning to appear. These machines were able to cut metal up to 8mm thick in any shape that could be drawn on a computer. This enabled “tube nests” to be designed and cut.
High-definition plasma cutters are accurate to within 0.4mm, ideal for leaving a welding clearance around the tube nest holes.
Energy costs during manufacture
To be sustainable in manufacturing, energy costs need to be considered. How much energy was used in the manufacturing of the metal sheet? How far did it travel to be delivered? How close is the local stockist? This is in addition to buying in an economic quantity, to ensure that the transport efficiency is maintained.
As far as tube nests are concerned, how many tubes can I cut from a standard length? All of these considerations are taken into account when designing Ranheat equipment.
Manufacturing in-house
To increase sustainability in manufacture, Ranheat try and manufacture as much as possible in-house.
This has led to the development of steel buildings manufactured from standard mild steel sheet sizes, profiled (folded) on the seven-axis CNC Brake Press to give the sheets strength, and painted for protection. The alternative would be a brick or block building to house the installation, which would mean using materials with a high carbon footprint.
As well as sustainability in manufacture, Ranheat also look at the sustainability of a system when in use. How long will the installation take to install? How many journeys will be needed to make the installation? How much fuel is used
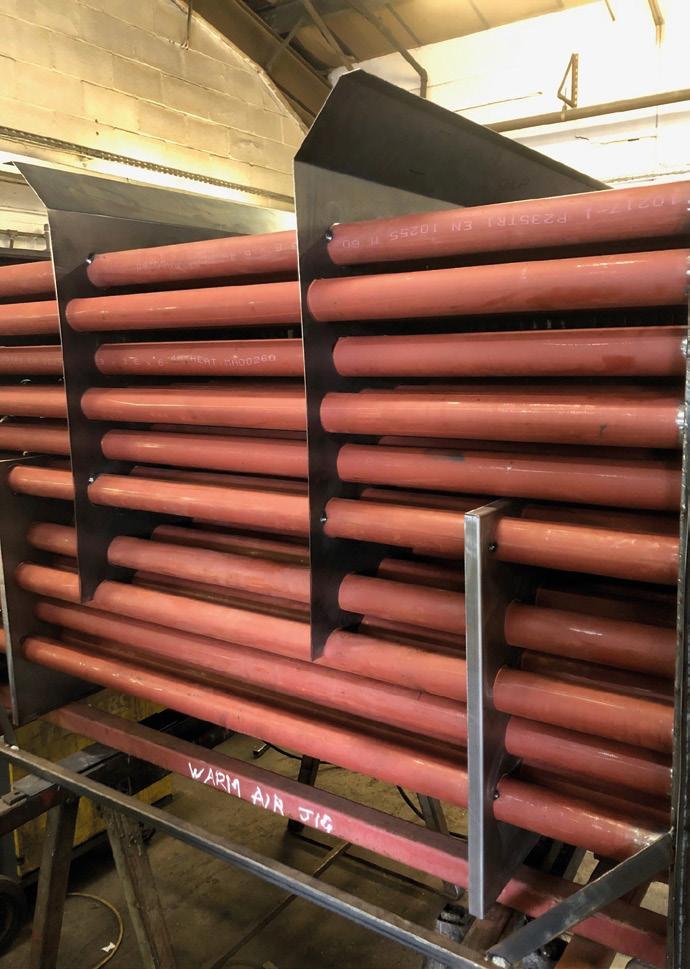
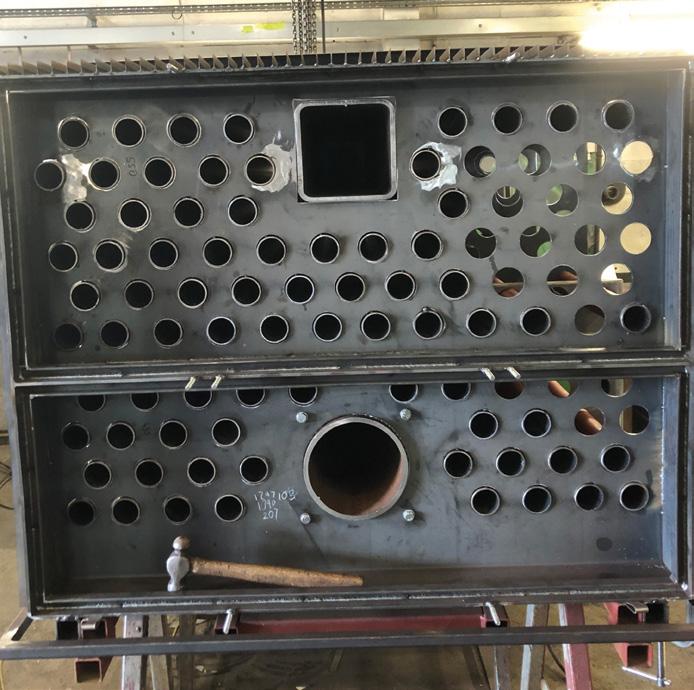
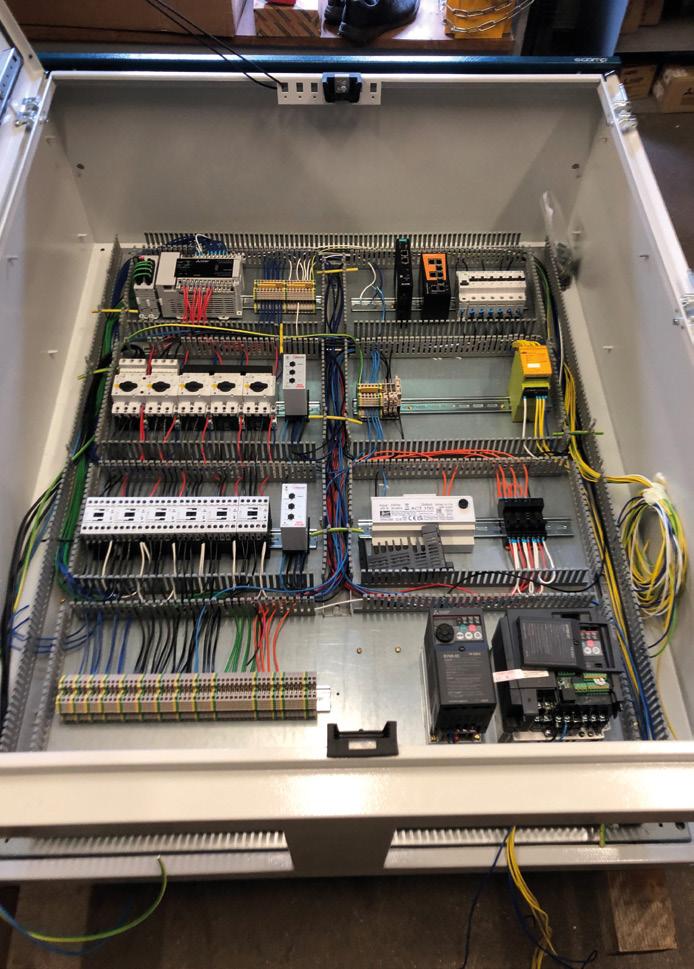

in making these journeys? Can the number of journeys be reduced if more of the system can be manufactured and delivered at one time? How many lorries are needed to deliver a system? Can this be reduced by good design and manufacture without compromising quality and reliability?
Storage silos for the wood-waste prior to combustion need to be sustainable in manufacture. The best designs in terms of storage versus material is to use a cylinder and a conical outfeeder to empty the silo. This only requires one small motor (0.75 kW0 and this is only running intermittently.
This design of silo maximises the storage capacity for a given utilisation of raw materials. It also gives a strong
construction for longevity in service and low maintenance in use.
Control panels are also made in-house in Ranheat’s electrical department, again, to achieve sustainability. The more that can be made in-house the larger the reduction in transport and manufacturing costs. The use of inverters aims to reduce electrical consumption.
Continuing with the theme of sustainability in manufacture, pipework installations are drawn accurately in auto-cad and then the pipework is manufactured in-house to maintain quality and fit, once again reducing transport costs and labour.
01604 750005
sales@ranheat.com www.ranheat.com
300kW warm air tube nest with 95 tubes, 50mm in diameter cut out using Ranheat’s CNC plasma cutter. This multi-pass design gives a high thermal efficiency and low flue temperatures. This maximises the energy released from the fuel. Although using a waste as a fuel to maintain sustainability as much energy as possible is taken from the combustion process.
By using 95 x 50mm tubes, maximum heat exchange is maintained when using one of Ranheat’s warm air heaters
Control panel
Two views on sustainability
When you think of sustainability, you can look at it from the environmental standpoint but also in terms of what Mirka is offering its customers when it comes to sustainable products and helping them be financially sustainable.
At Mirka, when we look at it from an environmental viewpoint, sustainability aligns neatly with our clean commitments. These are a set of four global principles that embrace Performance, Partner, Production and Proactivity, and reinforce the business’ journey towards becoming a more sustainable company.
As a business, Mirka is proactive when it comes to sustainability, and this is highlighted by what is going on in Finland. The company has a focused investment when it comes to sustainable technology such as hydropower, which has enabled the business to produce fossil-free electricity at all its production facilities in Finland. This has also led to a 56% reduction in carbon dioxide emissions within scope 1 and 2. In addition in Jakobstad, Finland, there has been a focus on geo-energy from geothermal holes, which has allowed the site to reduce its annual carbon dioxide emissions by around 900 tonnes. There was also investment in a purification and heat recovery system for the Oravais plant in Western Finland. This has led to a transition from oil heating to recycled energy using the extra heat and since it was implemented the site has not gone back to oil heating.
Alongside what is going on in Finland, Mirka is also putting sustainability first at
production facilities in sunnier climates such as Fino Mornasco in Lombardy, Italy. At this site, the business has installed solar panels which has led to the operation harnessing the sun’s energy and enabling it to be entirely powered by solar.
Another way Mirka is putting sustainability first on an industry level is through its membership of the Federation of European Producers of Abrasives (FEPA). Mirka had a central role in the founding of the Sustainable European Abrasives Manufacturer (SEAM) program, which was launched in 2020. The aim of the SEAM program, which aligns with Mirka’s core values, is to set a European sustainability standard that pulls the industry upward, where it can find the right balance between environmental efficiency, production performance, and labour safety for the whole abrasives industry in Europe, uniting to lead an even stronger sustainable development. Since its launch, there have been many large, medium and smaller abrasive manufacturers, suppliers and distributors that have joined the program, and it has shifted the industry towards a balance of environmental efficiency, production performance, and labour safety.
The other way to look at sustainability is from a financial perspective. For Mirka, it is all about providing a high-quality abrasive at a price point that makes sense
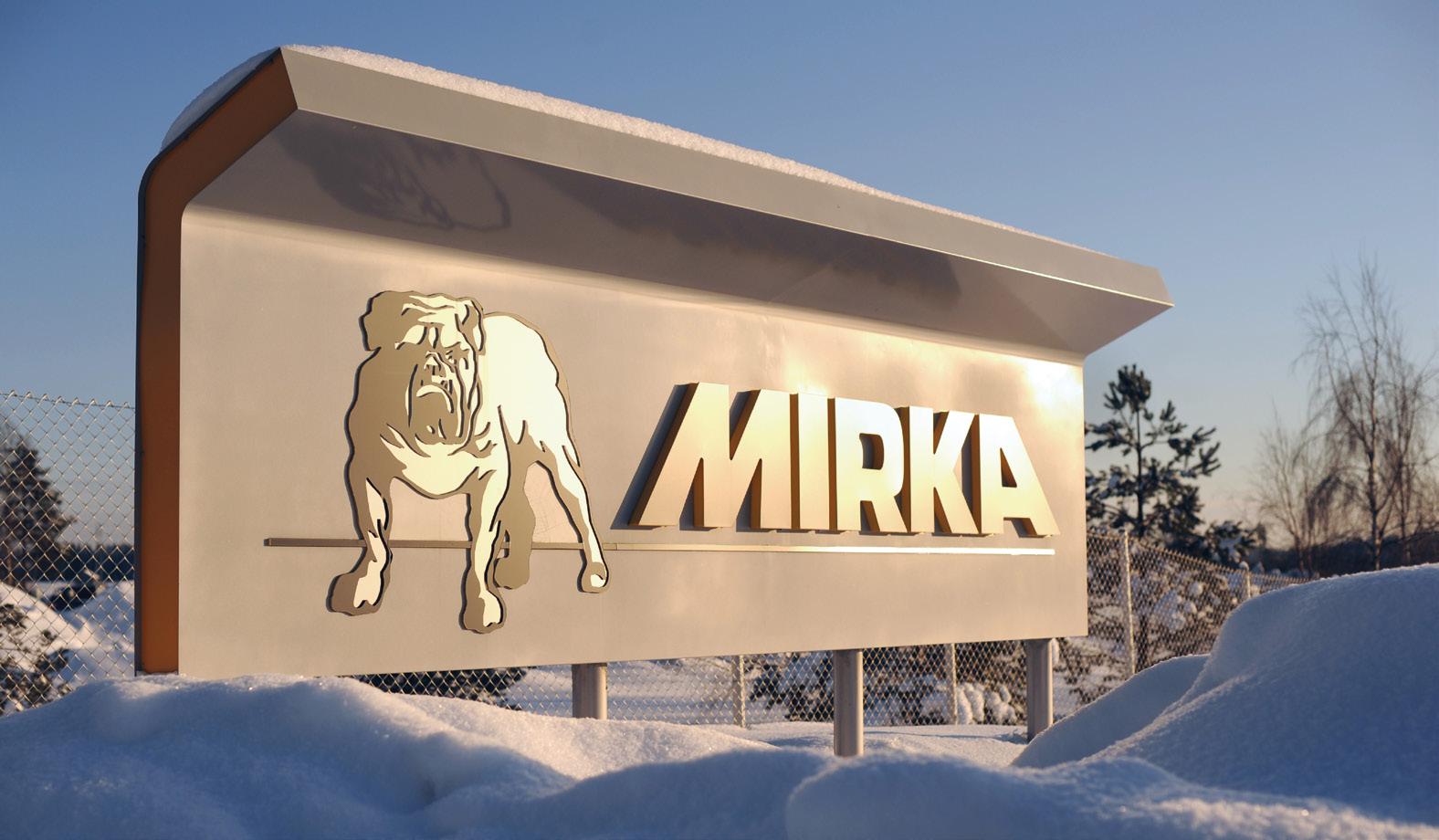
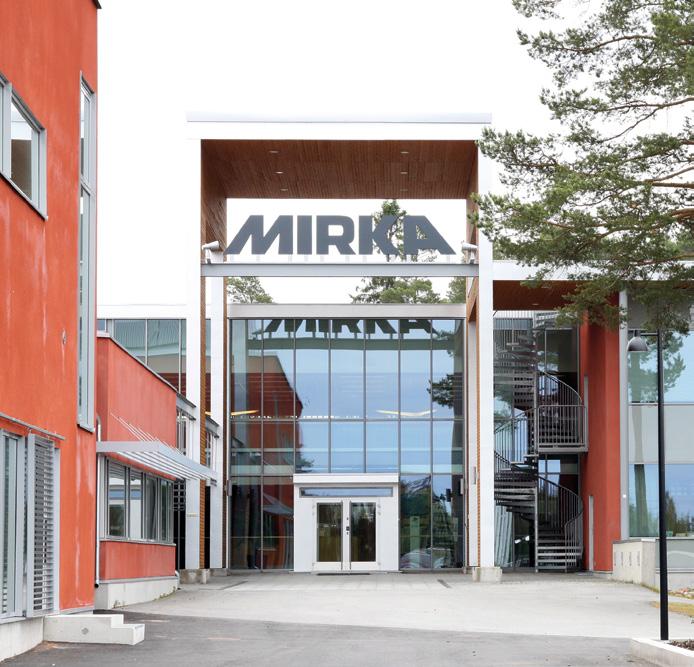
‘The company has a focused investment when it comes to sustainable technology such as hydropower, which has enabled the business to produce fossil-free electricity at all its production facilities in Finland
for the business but also the customer purchasing the product. By doing this, Mirka is seeing a concerted switch to more premium products. This move is taking users away from the slippery slope that is buy cheap buy twice. The reason for this is simple. It is because cheaper options might provide a slight monetary saving in the beginning however, it is quickly wiped out when the user has to purchase the same product very quickly down the line. In comparison, premium products are built to last, and they will provide the same end product or service, whether it is being used for the first or hundredth time.
Overall, sustainability in a multitude of forms, whether that is the sustainable values of the business or providing what is seen as a sustainable product that has a long life span, is enduring at Mirka. The business is also committed to researching and investing in sustainable technology that will benefit the business in the short, medium and long term.
www.mirka.com
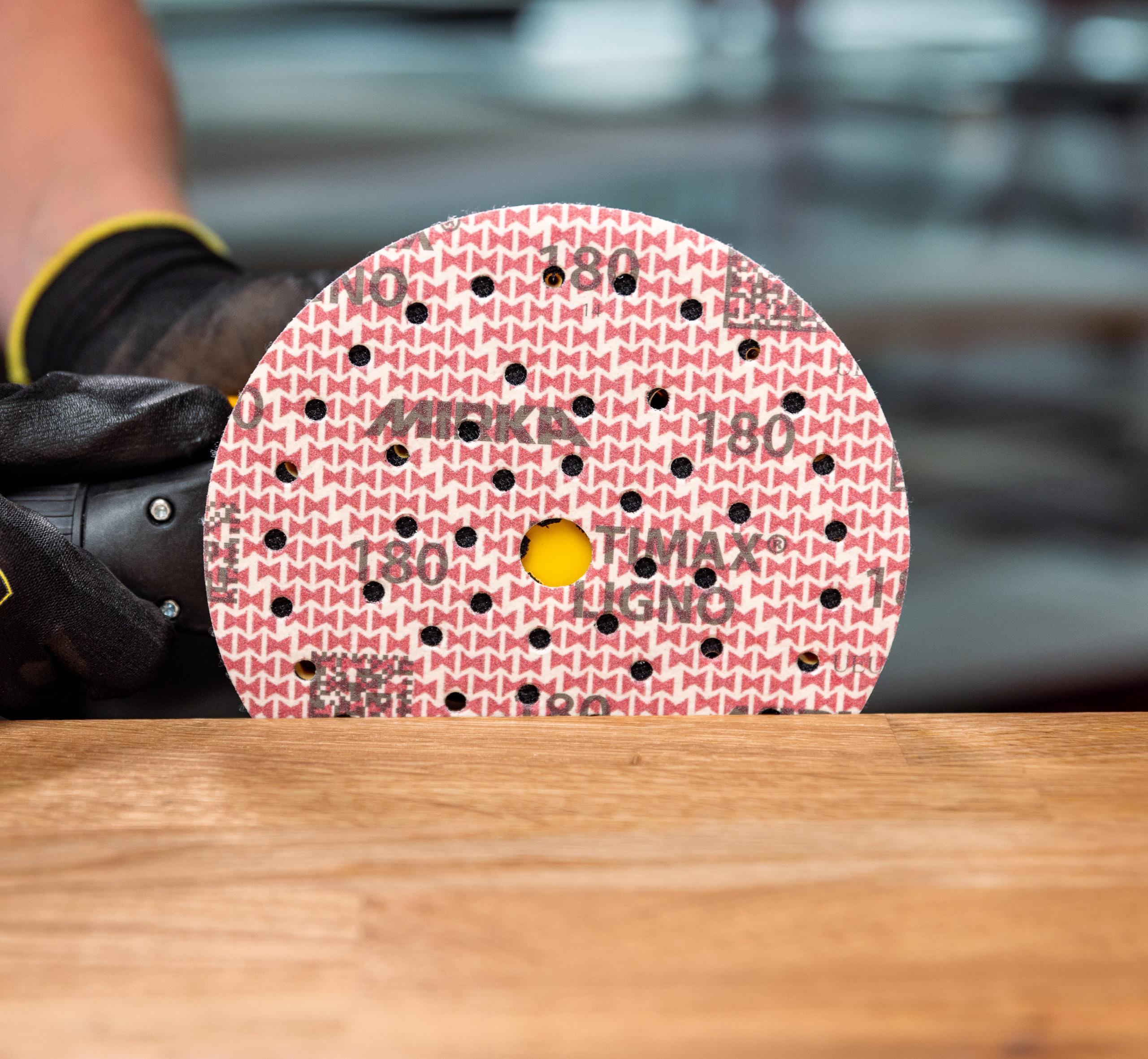
Ultimax® Ligno
Ultimax® Ligno is where innovation meets sustainability. In a world marked by rapid growth and material consumption, we‘re championing a balance between progress and the planet.
For further information or to arrange a demonstration, please contact Customer Services on 01908 866100.
Dedicated to the finish.
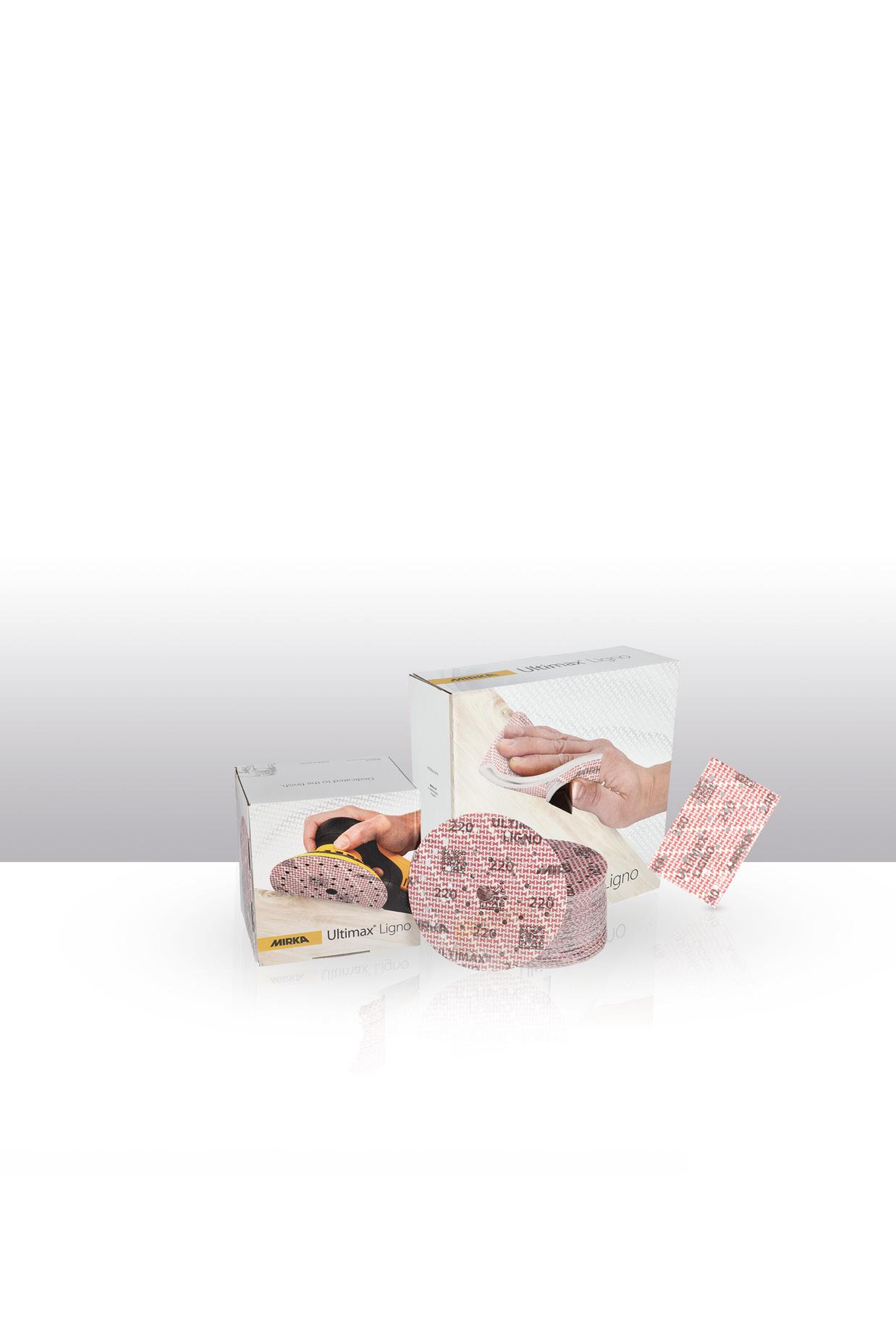
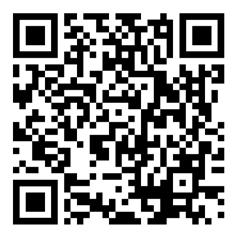
Everything. Except ordinary.
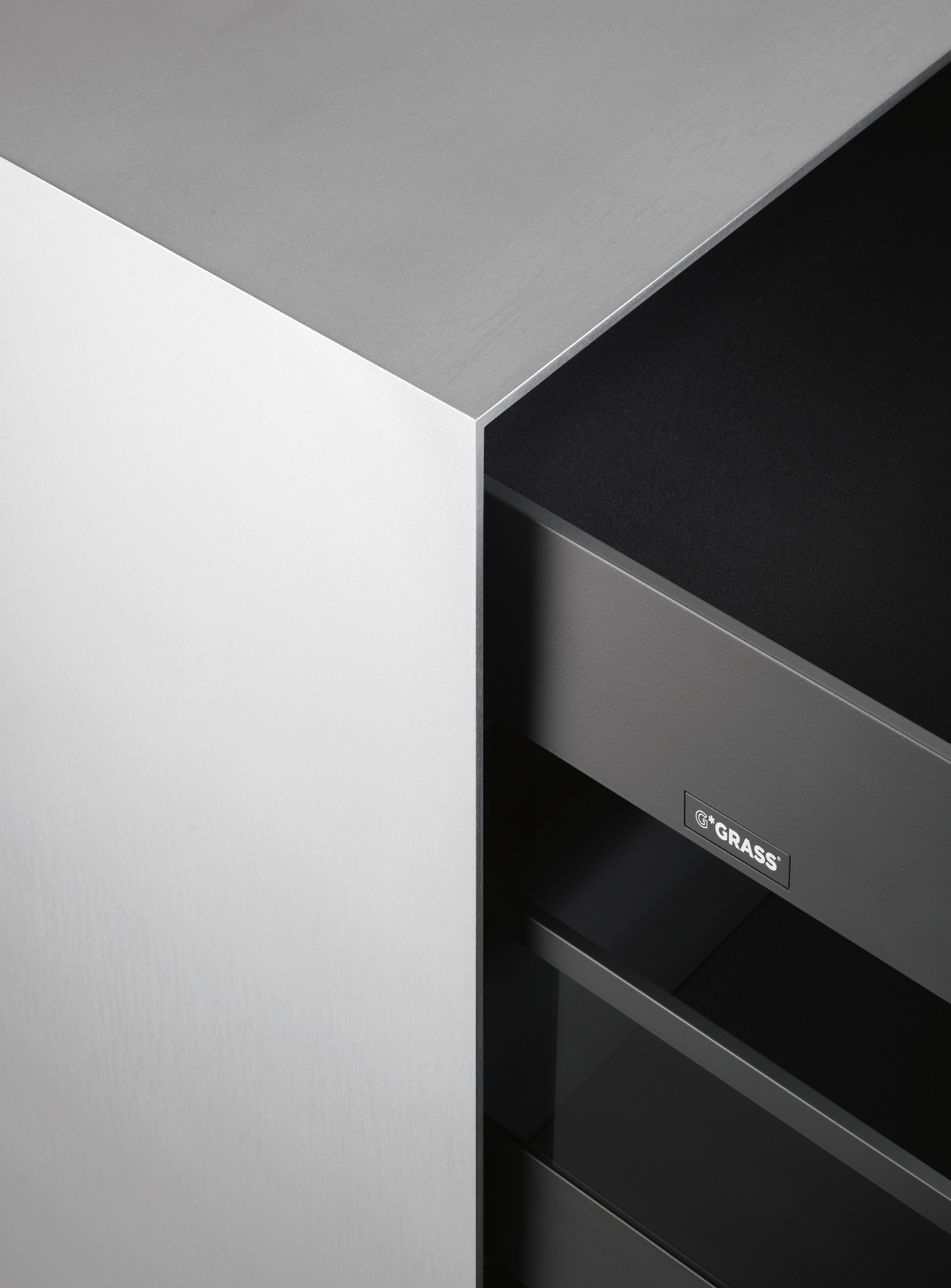
Until recently, the very idea of reducing a drawer side to 8 millimetres and, above all, making industrial production commercially viable would have been unthinkable. With Vionaro V8, this vision has now been turned into reality. The new slim drawer system not only offers the only 8-millimetre one-piece steel drawer side in the world –Vionaro V8 is also the first pure-metal drawer side with no plastic elements. All parts are made of steel and joined using cutting-edge laser welding technology. That produces maximum stability plus longevity and ensures an almost 100 per cent recycling rate.
Vionaro