

TARIFF TENSIONS
Ongoing tariff threats have sparked reaction from government and industry
› Transportation technology
› Drafting drones
› Limited optimism in trucking sector
• Convenient, flexible ordering options for all Canada & USA LTL shipments
• Speak with an agent or book directly online anytime, anywhere
• Get an instant quote and book your freight travels in a single session
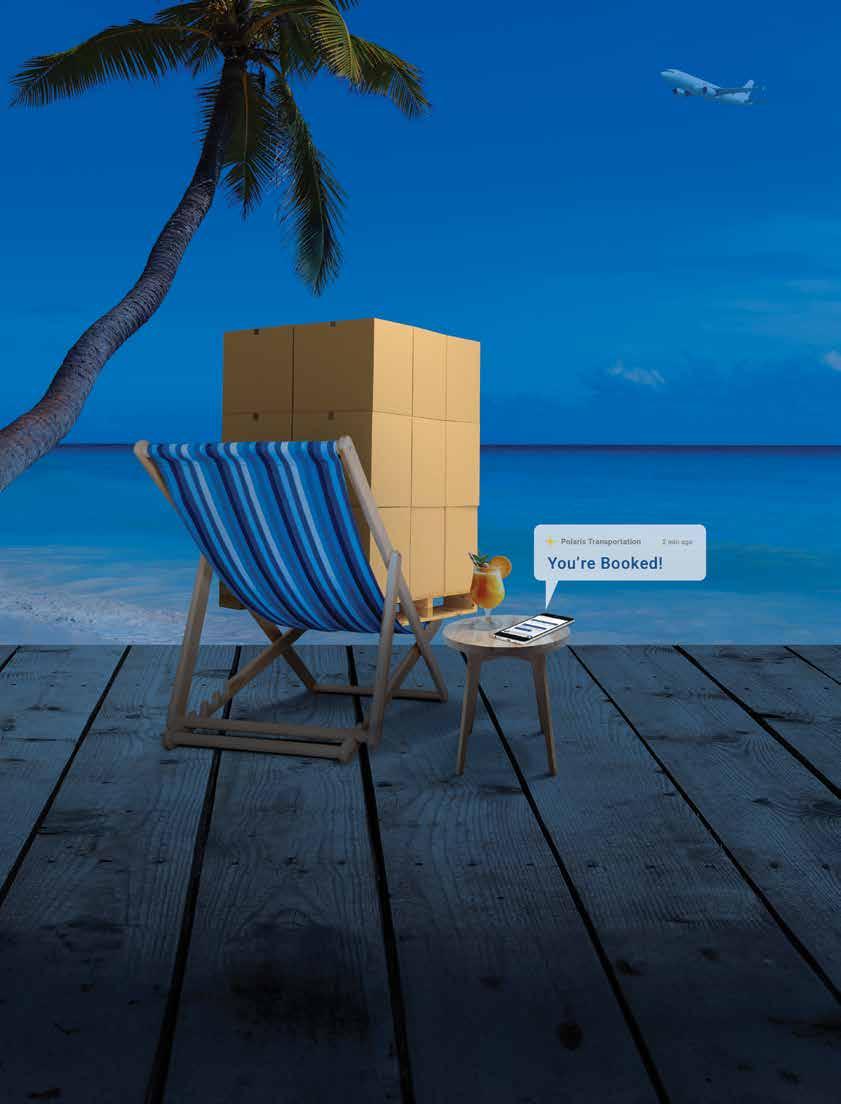
• Save quotes or book repeat orders using our online cart and history features
• Scheduled daily departures with featured next-day destinations
• Industry-leading cross border travel times with live updates & visual tracking
92.8% CUSTOMERS BOOKING ONLINE 17 CONSECUTIVE SHIPPER’S CHOICE AWARDS YEARS
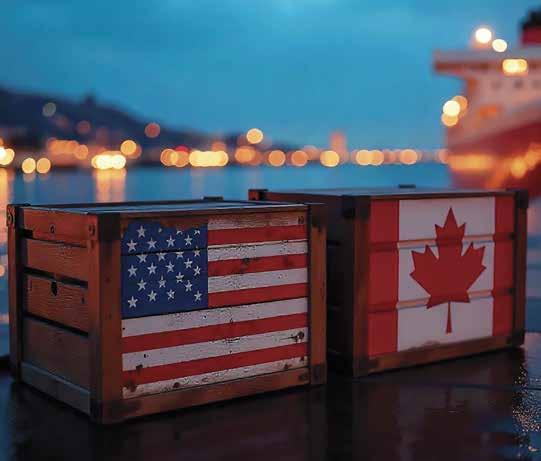
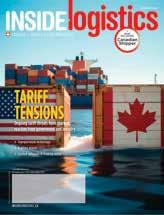
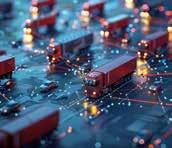

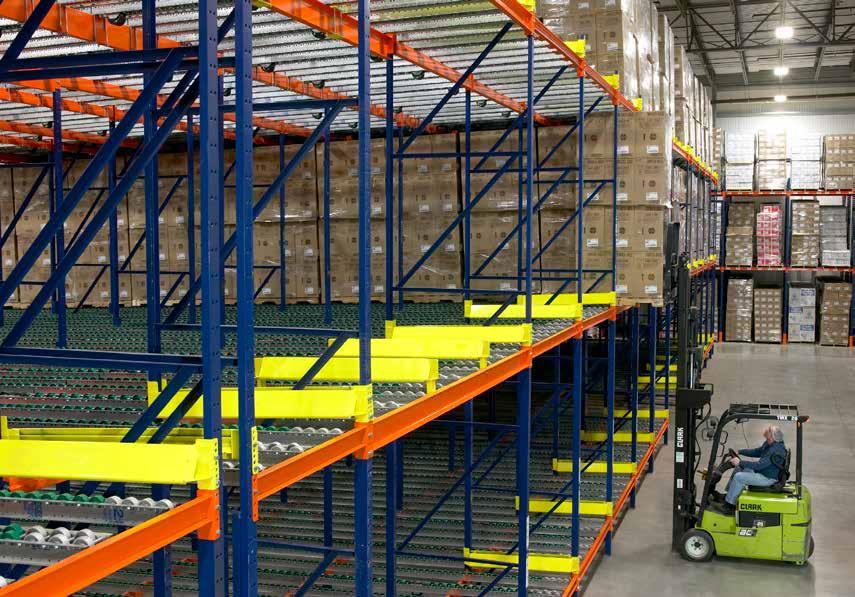
Engineered for Strength, Designed for Flexibility –3D Storage Solutions Delivers More Than Just Racks
3D STORAGE
For the past 30 years, 3D Storage has been designing and constructing warehouse storage solutions for a wide variety of industries including,
• Manufacturing
• Third Party Logistics (3PL)
• Retail
• Distribution Centers
• Cold Storage
• Ecommerce
Publisher | Delon Rashid (416) 459-0063 delon@turnkey.media
Editor | Derek Clouthier (416) 605-5346 derek@turnkey.media
Contributing Writers | Jeff Larson, Norm Kramer, Christian Sivière, Victoria Jones
Creative Director | Samantha Jackson
Video / Audio Engineer | Ashley Mikalauskas, Nicholas Paddison
Sales | Delon Rashid, (416) 459-0063 delon@turnkey.media
Peter Bulmer, (585) 653-6768 peter@turnkey.media
Production and Ad-ops | Tracy Stone tracy@turnkey.media
Inside Logistics magazine is published by Turnkey Media Solutions Inc. All rights reserved. Printed in Canada. The contents of this publication may not be reproduced or transmitted in any form, either in part or full, including photocopying and recording, without the written consent of the copyright owner. Nor may any part of this publication be stored in a retrieval system of any nature without prior consent.
Canada Post Canadian Publications Mail Sales Product Agreement No. 43734062
“Return Postage Guaranteed” Send change of address notices, undeliverable copies and subscription orders to: Circulation Dept., Inside Logistics magazine, 48 Lumsden Crescent, Whitby, ON, L1R 1G5
Inside Logistics magazine (ISSN No.: 0025-5343 (Print); 1929-6460 (Digital) is published six times per year by Turnkey Media Solutions Inc., 48 Lumsden Crescent, Whitby, ON, L1R 1G5
From time to time we make our subscription list available to select companies and organizations whose product or service may interest you. If you do not wish your contact information to be made available, please contact us.
President & Managing Partner | Delon Rashid Head of Sales & Managing Partner | Peter Bulmer
Corporate Office
48 Lumsden Crescent, Whitby, ON, L1R 1G5

ISSN 0025-5343 Online 1929-6460
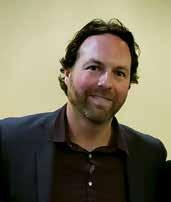
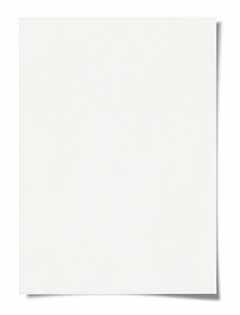
Canada’s self-inflicted trade barriers
THIS MAY NOT BE the most popular topic of conversation for many Canadians right now, particularly those who have rekindled their patriotism amid the threat of U.S. tariffs, but it is worth pointing out—Canadians pay interprovincial tariffs in various forms and have for several years. And yes, those tariffs—imposed by Canadian politicians, both provincially and federally, whom we elect—increase the cost of goods such as meat, dairy, grains, alcohol and several other products individuals and families use every day. The reason this is worth shining a spotlight on is not because Canadians should roll over and accept the Trump tariffs. On the contrary, U.S. tariffs on our goods would have a significant impact on many Canadian sectors, including manufacturing, farming and energy—well, let’s just say everything. Canada, however, or more specifically its politicians, can sometimes be its own worst enemy.
Donald Trump is not Canada’s prime minister. His job is not to act in the best interests of Canada but rather to do what he thinks is best for the U.S. Ironically, the rules and regulations imposed by Canadian provinces (essentially tariffs) are based on the same rationale Trump uses to justify placing tariffs on Canada, Mexico, China and several other countries. The goal is to create an environment where local businesses, manufacturing and overall production can thrive without relying on outside help.
A recent CBC News article said that just the threat of U.S. tariffs was driving investment out of Canada and into the U.S. Why? Because businesses looking to avoid paying tariffs will decide to set up shop in the U.S. This is precisely what Trump campaigned on, so it should be no surprise that he is following through.
Perhaps, instead of Canadians focusing their anger solely on the U.S. (like booing the national anthem at sporting events, which is juvenile, misdirected and does nothing to help find a solution), we should also look inward and question why our own governments make doing business within Canada more difficult and expensive. Why is it cheaper and easier for B.C. to ship a bottle of wine to Europe than to Ontario? Why do transportation regulations differ in every province, increasing costs to businesses and, subsequently, for consumers? Why do the government’s supply management rules for dairy and meat producers allow them to control the supply and quantity of their products, creating a monopoly and driving up food prices?
These are just some examples of how interprovincial tariffs impact Canadians, often without notice. Our politicians are supposed to act in our best interests, and while the issue is, of course, more complex than can be covered in a 500-word editorial, Canadians should stop turning a blind eye simply because it’s easier to hate the “bully” to the south.
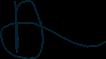
Canadian businesses brace for impact as U.S. tariffs on China take effect
By Inside Logistics Staff
LEAVING QUEBEC
8 EXPANDING
9 MOVERS + SHAKERS
Appointments and promotions 14
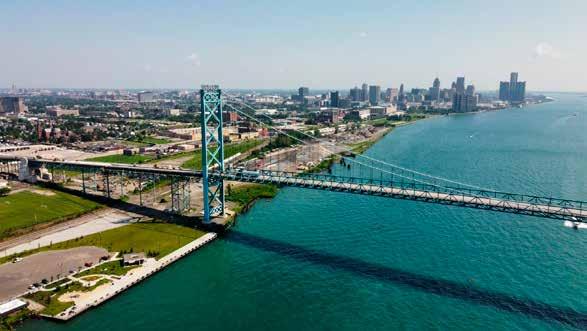
ALTHOUGH TARIFFS ON CANADIAN goods are temporarily on hold, nearly two-thirds of Canadian businesses are experiencing the impact of new 10 percent U.S. tariffs on Chinese imports, according to recent research from KPMG Canada.
The study, which surveyed 250 business leaders across Canada, found that supply chain disruptions and the threat of additional trade barriers are forcing many companies to rethink their operations. With the possibility of 25 per cent tariffs on Canadian exports still looming, experts at KPMG say businesses need to prioritize resiliency and agility within their supply chains.
“The uncertainty caused by potential tariffs on Canadian goods and newly imposed tariffs on China has made it very difficult for Canadian companies to plan, operate and stay competitive,” said Alain Sawaya, national leader of KPMG in Canada’s supply chain practice.
In response to the tariffs, 88 per cent of surveyed businesses said they had already diverted or were considering diverting goods to countries not currently affected by trade restrictions. Nearly half (44 per cent) reported actively reconfiguring their supply chains to bypass the U.S. market, while an equal proportion said they were exploring this strategy.
Additionally, 57 per cent of respondents indicated they were shifting production away from China due to both U.S. tariffs and concerns over forced labour. Overall, 63
“The
uncertainty caused by potential tariffs on Canadian goods and newly imposed tariffs on China has made it very difficult for Canadian companies to plan, operate and stay competitive,”
– Alain Sawaya, national leader of KPMG.
per cent said the latest U.S. trade policies would negatively impact their businesses.
“With Canada caught in the trade crosshairs of the U.S. and China, industries that depend on suppliers and
Amazon shuts down its facilities in Quebec
Walmart Canada grows its distribution network across the country
Courtesy of Paul Cicilian/Flickr
customers—such as manufacturing—are especially vulnerable to increased costs, delayed shipments and disrupted production and planning schedules,” Sawaya said. “Smaller suppliers with fewer options may struggle to absorb added costs, leading to a heightened risk of insolvency.”
Recognizing these challenges, 83 per cent of Canadian businesses said they need to enhance their supply chain resilience. Many are exploring solutions such as alternative materials sourcing, inventory optimization, predictive demand management and AI-driven supply chain monitoring.
KPMG suggests that companies leverage digital tools to map their supply chains and conduct scenario planning.
“Organizations that digitally map out their supply chains for probable scenarios have a competitive advantage when new risks arise,” Sawaya said. “If the digital map is a real-time model that’s part of the decision-making process, the supply chain and the business will ultimately be more resilient.”
Beyond immediate supply chain adjustments, KPMG’s research found that 79 per cent of respondents anticipate the U.S. will impose tariffs on the European Union, suggesting that few trading partners will be spared from escalating trade tensions.
Nancy Chase, National Risk Services Leader at KPMG Canada,
cautioned that while modifying supply chains can help businesses avoid some tariff-related costs, it also introduces new risks.
“Reconfiguring supply chains could help businesses avoid the hit from tariffs on affected countries, but it also creates a whole new set of risks because they’re turning to new, third-party suppliers that are relatively unknown,” she said. “Businesses thinking of switching thirdparty suppliers need to ensure their contractual obligations are properly reviewed and revised, and they also need to have effective risk controls in place. For example, how will they manage fraud or cybersecurity risks—both of which tend to rise when businesses engage new suppliers with an unproven track record?”
To mitigate these risks, Chase recommends companies conduct comprehensive enterprise risk assessments, refresh contract terms and leverage AI-driven analytics to monitor vulnerabilities in their supply chains.
Survey methodology
KPMG in Canada conducted the survey between Jan. 21 and Jan. 27, 2025, through Sago’s premier business panel, using the Methodify online research platform. Of the 250 respondents, 88 per cent export or sell to the U.S. The surveyed companies varied in size, with annual revenues ranging from $10 million to over $1 billion.
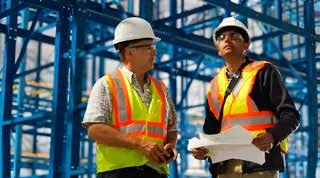
Maximize efficiency and storage with high-performance racking solutions—backed by 50+ years of expertise. sales@naseco.ca / 905.668.3300


Amazon to close its Quebec facilities, return to third-party delivery model
AFTER REVIEWING ITS operations, Amazon has decided to close all seven of its Quebec locations and revert to a third-party delivery model in the province.
“Following a recent review of our Quebec operations, we’ve seen that returning to a third-party delivery model supported by local small businesses, similar to what we had until 2020, will allow us to provide the same great service and even more savings to our customers over the long run,” Barbara Agrait, a spokesperson for Amazon, said in a statement. “This decision wasn’t made lightly, and we’re offering impacted employees a package that includes up to 14 weeks’ pay after facilities close and transitional benefits, like job placement resources.”
As a result of the closures, approximately 1,700 regular employees will be affected, along with 250 temporary seasonal workers whose contracts will be honoured by Amazon.
Kristin Gable, senior manager of corpo-
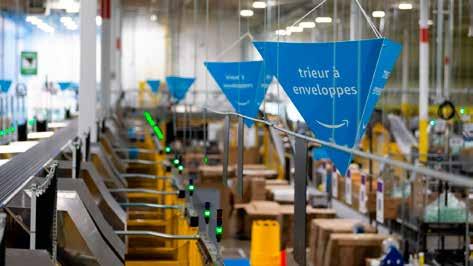
rate communications in Canada with Amazon, said the company used the third-party business model in Quebec prior to opening locations in the province in 2020. She added that the change aligns with Amazon’s goal to provide better service, selection and savings to its customers.
“Amazon determined that it just made sense. It was in the best interest of our customers
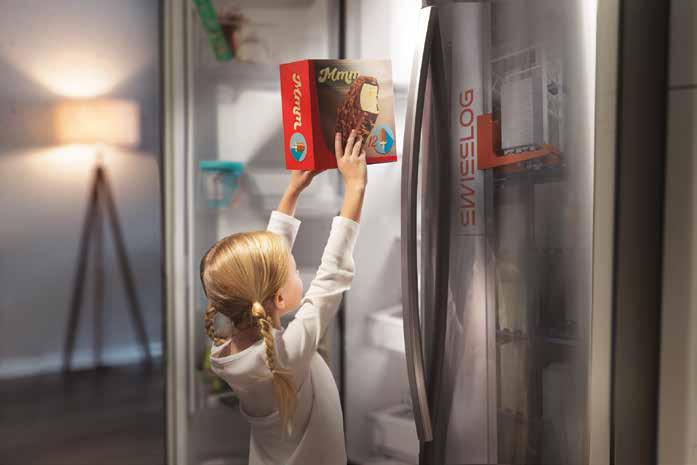
Swisslog’s automated intralogistics solutions for ambient and frozen food are designed to increase speed, accuracy, and e iciency even in demanding temperature-controlled environments.

swisslog.com/vectura
Photo courtesy of Amazon Canada
to go back to that model that we had until 2020,” Gable said. “The goal of this is not only to maintain the level of service that customers receive but even to continually improve it over the long term.”
Asked whether the recent unionization of Amazon warehouse employees in Quebec factored into the decision to shutter the seven operations, Gable said it did not.
“This was about returning to a model that we used successfully prior to 2020, that’s going to allow us to provide the same great service and savings to customers,” she said.
Gable said Amazon will work with more third-party logistics companies to ship items to customers.
She also stressed that Amazon would continue to support thirdparty sellers to maintain a high level of service.
“There are many third-party sellers in Canada and in Quebec who sell their products on Amazon.ca; that doesn’t change,” said
Gable. “We will continue to work closely with third-party sellers in Quebec and elsewhere to make sure they’re getting their resources and the support they need to be successful when they sell their products in our store.”
Each of the seven facilities being closed are leased, and Amazon plans to work with landlords to determine the next steps for the properties.
“The facilities in Quebec are leased and will remain in use over the coming months as we wind down operations,” Agrait said. “As we complete this process, our team will work with relevant landlords – as they do any time we exit a leased facility – to determine what’s next for them.”
The sites will close progressively, with each shutting down on different dates. The entire process is expected to take about two months.
Walmart Canada investing $6.5B to expand distribution network, add new stores
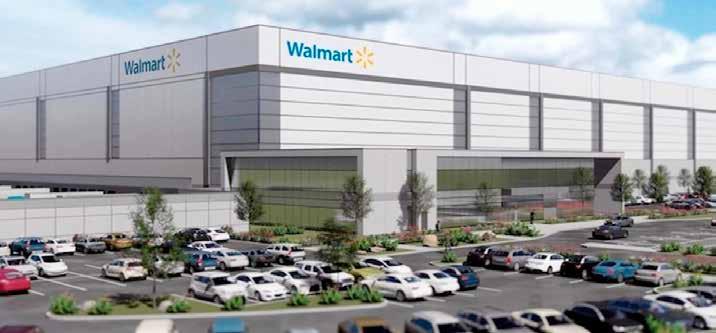
WALMART CANADA IS investing $6.5 billion over the next five years to grow its presence in Canada, modernize its supply chain and open new stores.
The company will open its new Vaughan Distribution Centre this spring, calling it its “most advanced facility.”
“Walmart Canada is on an ambitious growth journey to serve even more Canadians – better and differently than ever before,” said Gui Loureiro, regional CEO for Walmart Canada, Chile, Mexico and Central America.
As part of its expansion, Walmart Canada has signed an agreement to sell its fleet business to Canada Cartage, which will take over its dedicated transportation operations.
The retailer will also open dozens of stores nationwide, starting with five new Supercentres in Ontario and Alberta by 2027. The first, in Port Credit, Ont., is set to open in summer 2025, followed by an Oakville location later that year.
Three more stores will be built in Calgary, Edmonton and Fort McMurray.
The announcement comes as the company concludes a $3.5-billion investment launched in 2020 that included store renovations, new locations and multiple distribution centres.
Walmart Canada says it is also investing in its workforce, putting nearly $200 million toward wage increases for frontline employees in 2024.
Photo courtesy of Walmart Canada
Loan saves Pride Group Logistics, preserves 300 jobs
MAYNBRIDGE CAPITAL HAS issued a senior secured term loan to Pride Group Logistics (PGL), averting a significant liquidation and safeguarding nearly 300 jobs across Canada and the U.S.
The financing enabled PGL’s founders, Sam and Jas Johal, to reacquire the company following a court-ordered sale triggered by two years of market challenges. The loan allowed the Johals to retain ownership of the business they built over 15 years.
“This partnership is a great example of why we built Maynbridge: supporting Canadian
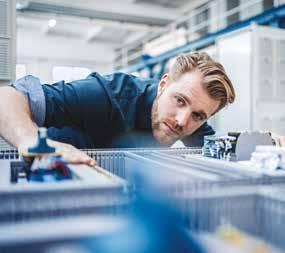
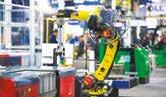
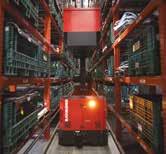
THE FUTURE OF INTRALOGISTICS IS INTEGRATED
Build smart. Stay agile. Now is the time to take a broader look at your overall intralogistics strategy and optimize. Making adjustments to combat today’s challenges will prepare you for a strong and sustainable future. And we can help.
Together, we’ll analyze the strategy and systems you’ve built to move, manage, store and protect goods and bring forward new ideas to enhance or secure the investments you’ve already made. Let’s get started.
RUN BETTER.
MANAGE SMARTER.™
Discover how Johnston Equipment can help optimize your facility.
businesses when traditional banks have turned their backs,” said Dean Shillington, president of Maynbridge Capital.
Maynbridge specializes in asset-based lending and transitional financing. The firm has helped more than 100 companies avoid bankruptcy over the past decade.
Amal Johal, president of Pride Group Logistics, said Maynbridge’s support was crucial to securing the deal and preserving the company’s legacy.
“Two years of declining customer demand and rising interest rates created immense challenges, but their unique approach gave us the confidence and financial support we needed to navigate this pivotal moment for PGL,”
– Amal Johal, President of Pride Group Logistics.
“Two years of declining customer demand and rising interest rates created immense challenges, but their unique approach gave us the confidence and financial support we needed to navigate this pivotal moment for PGL,” he said.
PGL operates in the North American logistics sector and will continue business under its existing leadership following the transaction.
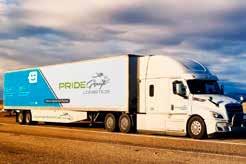
Photo courtesy of Pride Group
CIB funds $60.7M Indigenous-led logistics park at Port of Prince Rupert
THE CANADA INFRASTRUCTURE BANK (CIB) has completed a $60.7-million loan agreement to assist in developing the Indigenous-led South Kaien Import Logistics Park at the Port of Prince Rupert.
The loan, provided through CIB’s Indigenous Community Infrastructure Initiative, will help the Metlakatla Development Corporation (MDC) and the Prince Rupert Port Authority prepare 56 acres of serviced land near Fairview Terminal and CN Rail.
“Our second investment at the Port of Prince Rupert will help enable British Columbia’s first Indigenous-led logistics facility,” said Ehren Cory, CEO of CIB. “We proudly support the opportunity for the Metlakatla Development Corporation to own a majority stake in the project, which will provide a stable stream of revenues and create jobs for Metlakatla First Nation members and other Indigenous communities in the region.”
More than half of the park has been leased for a logistics and ware-
housing complex, with the remaining 23 acres available for lease. Site preparation, including heavy civil construction and land removal, is expected to take two years, followed by private sector investment in transloading and warehousing infrastructure.
MDC plans to develop an additional 280 acres in future phases.
“SKILP is step one: MDC plans to develop the remaining 280 acres in subsequent phases to support regional growth and provide economic opportunities for the region and next generation of Metlakatla members,” said Harold Leighton, CEO of Metlakatla Development Corporation.
CIB previously announced a $150-million loan in May for the CANXPORT export logistics hub at the port.
“This investment is vital to anchoring the Port of Prince Rupert as a full-service trade gateway,” said Shaun Stevenson, president and CEO of the Prince Rupert Port Authority.
Purolator acquires Livingston International to expand global trade services
PUROLATOR HAS ANNOUNCED its acquisition of Livingston International, a global trade services firm that specializes in customs brokerage, freight forwarding and trade consulting, from Platinum Equity.
The acquisition strengthens Purolator’s international capabilities, particularly in Canada, the U.S., Mexico, Europe and Asia, as businesses navigate increasing complexities in global trade.
“Strategically, this transaction represents a generational opportunity to acquire a highly complementary and growing international business with a proven track record of success,” Purolator president and CEO John Ferguson said in a statement. “With these broader capabilities and increased breadth, we can offer more choice and greater flexibility to current and future customers.”
Livingston, founded in 1945, serves more than 30,000 businesses engaged in cross-border and international trade. The company has worked with Purolator for over 30 years, supporting its customs and global trade service needs.
“Livingston is excited to join an iconic transportation brand with considerable growth opportunities,” said Robert Smith, CEO of Livingston International.
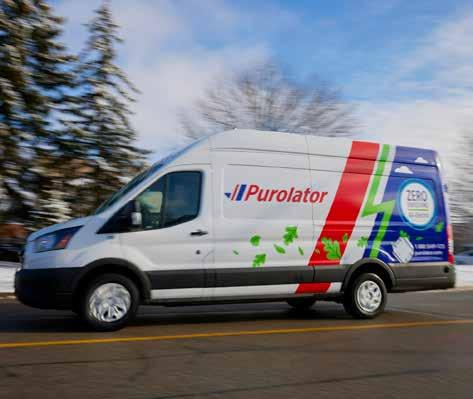
“This builds on the successes of each business’s operating models and corporate cultures.”
Livingston will operate as a wholly owned subsidiary of Purolator under its existing leadership team.
Financial details of the transaction were not disclosed.
Photo courtesy of Purolator
ShipAlberta launches to simplify shipping for Alberta businesses
WITH THE OFFICIAL LAUNCH of ShipAlberta, businesses in Alberta now have an efficient shipping solution designed to support their growth, exports, and global competitiveness.
A collaboration between Edmonton International Airport (YEG), Edmonton Global, Port Alberta and Machool Technologies, ShipAlberta offers businesses a cost-effective shipping solution. The platform connects users with trusted couriers and provides competitive rates, alongside seamless tools to automate shipping processes.
Historically, small and medium-sized enterprises in Alberta faced challenges accessing reliable and affordable shipping options, hindering their ability to expand into national and international markets. ShipAlberta addresses these issues by simplifying logistics and offering a user-friendly interface to reduce costs and complexity.
“Businesses and retailers are the driving force behind Alberta’s economic growth. YEG is proud to be a partner in bringing ShipAlberta to the market with its innovative and cost-effective solution for businesses to ship products to their customers seamlessly,” said Myron Keehn, president and CEO of Edmonton International Airport.
The initiative is expected to boost Alberta’s
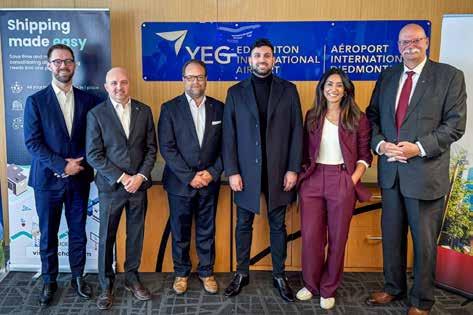
position as a logistics hub, attract more retailers, and strengthen the province’s access to global markets.
“This is a testament to what regional collaboration can achieve,” said Malcolm Bruce, CEO of Edmonton Global. “By leveraging the unique strengths of Port Alberta, we are creating a transformative shipping solution that enables
Alberta-based companies to take their products across the region, the country and the world.” Kamyar Asadibeiky, CEO of Machool Technologies, added, “ShipAlberta harnesses our technology and platform to move beyond the traditional ‘more volume, better rates’ model, delivering seamless and cost-effective shipping for every user.”
Canadian government provides $1B in repayable funding to Canada Post
THE FEDERAL GOVERNMENT will provide Canada Post with up to $1.034 billion in repayable funding through the 2025-26 fiscal year to help the Crown corporation tackle financial difficulties.
The short-term financing measure, which falls under the Canada Post Corporation Act, aims to maintain the postal service’s solvency while the government and Canada Post work on a long-term strategy.
“This approach will maintain continuity of Canada Post’s operations but will not solve the corporation’s structural issues,” the government said in a statement.
Canada Post said in a release that it has recorded significant annual losses since 2018 due to shifts in the postal and parcel delivery sectors, high labour costs and regulatory measures that hinder its ability to compete. Without this funding, the corporation said in its 2023 annual report that it would run out of cash reserves by the second quarter of 2025.
“Significant change is urgently needed to modernize the operating model and preserve the national postal service,” Canada Post said, adding that it is working to improve service through facility upgrades,
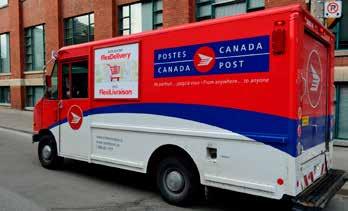
new sorting equipment and digital platforms.
The funding is intended as a temporary financial bridge while the government and Canada Post develop a sustainable plan for the future.
James Jackson, Alex Lowe, Myron Keehn, Kamyar Asadibeiky, Manisha Arora and Malcolm Bruce.
Photo courtesy CNW Group/ShipAlberta.
Photo courtesy of Canada Post
DHL Global Forwarding expands ocean bulk service to Canada
DHL GLOBAL FORWARDING, the freight division of DHL Group, has expanded its ocean bulk service to Canada, providing an ecofriendly transportation solution for bulk liquids such as edible oils and ethanol. This expansion boosts Canada’s agricultural exports, a vital part of the global trade network.
The service utilizes state-of-the-art ISO tanks and flexitanks to ensure safe and efficient shipments. The service’s capacity of up to 27,000 liters per container significantly reduces the environmental impact compared to traditional methods, such as drums or IBCs.
“Canada’s agricultural sector is a key player in the global market, and our ocean bulk service is built to address the industry’s logistical challenges while contributing to a lower carbon footprint,” said Richard Patry, country manager for DHL Global Forwarding in Canada.
The technology behind the service includes advanced heating systems for temperature-sensitive cargo. DHL says its ocean bulk service is the only fully integrated flexitank service globally, with capabilities that cover the entire supply chain, from manufacturing to transport and equipment recovery.
DHL’s ocean bulk service aligns with the company’s target of

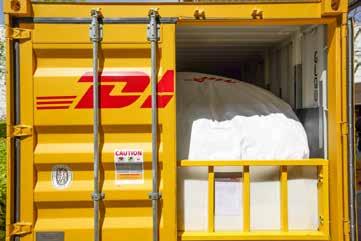
zero emissions by 2050, optimizing container utilization to reduce CO2 emissions. The service is now available in 45 countries globally, including the Americas.
Start May 5th and you’ll be done this fall.
You’ll earn a marketable, standalone credential from industry’s most respected logistics experts. You’ll gain the base abilities leading companies value and demand now. Plus, you’ll get credit toward earning industry’s premier professional logistics designation (CCLP) if you want your career to go even farther.
It’s one easy decision. One quick registration. Let us help you today
Photo courtesy of DHL
movers + shakers

Railway Association of Canada
The Railway Association of Canada (RAC) announced that Eric Harvey will lead RAC effective Feb. 3.
Harvey has more than 25 years of experience in legal and regulatory transportation matters. His most recent role was as assistant general counsel on policy and legislative affairs at CN. During his time at CN, Harvey worked on key files such as reviews of the Railway Safety Act and the Canada Transportation Act. He also led many advocacy initiatives by engaging with elected and non-elected officials for CN. Prior to this, Harvey worked in Ottawa for federal agencies regulating transportation.
Walmart Canada
Walmart Canada announced Venessa Yates as its new president and CEO.
“Venessa is a tremendous retail leader with experience in multiple countries and functions,” said Guilherme Loureiro, regional CEO, Walmart Canada, Chile, Mexico and Central America. “She is

the right person to continue to drive Walmart Canada’s growth trajectory and its transformation to become the country’s leading omnichannel retailer.”
Walmart Canada also announced Steve Schrobilgen is joining the company as chief operating officer, end-to-end, overseeing operations, supply chain, real estate and format.
Schrobilgen currently serves as the senior vice-president, business unit leader for Walmart in the Western U.S., a role he assumed in 2023. Over his 35-year career with Sam’s Club and Walmart, Schrobilgen has demonstrated exceptional leadership and operational expertise. His commitment and results-driven approach propelled him through a series of increasingly senior roles at Sam’s.
Port of Quebec
The Port of Québec’s board of directors announced the appointment of Olga Farman as CEO, succeeding Mario Girard’s 14-year service in that position.
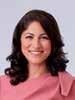
Farman was a corporate lawyer, until very recently, the managing partner of the Québec office of Norton Rose Fulbright Canada. She is also a member of the board of directors of the Caisse de dépôt et placement du Québec, Beneva, insurance and financial services, and the Fondation du Musée de la civilisation de Québec.

DP World
DP World, a logistics and supply chain solutions company, has announced the appointment of Brittany Caskey as senior vice-president of commercial logistics for the Americas, effective Dec. 30.
With nearly two decades of leadership in logistics and supply chain management, Caskey brings a wealth of experience and a proven track record in driving strategic growth and commercial excellence. In her new role, Caskey will spearhead the development and execution of DP World’s commercial logistics strategy across the Americas region.
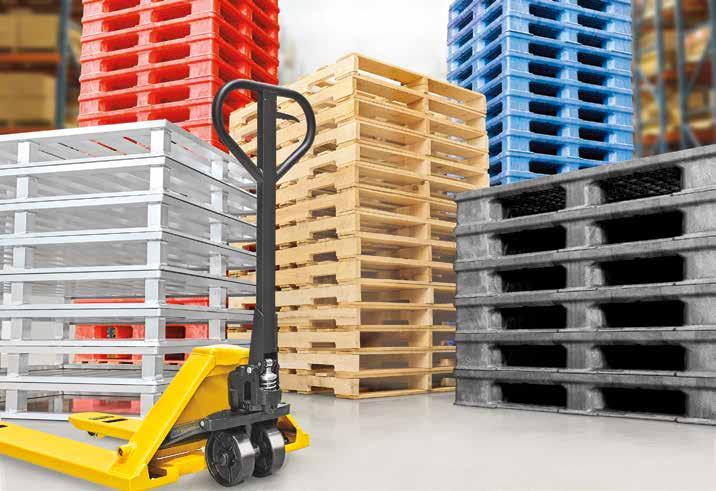


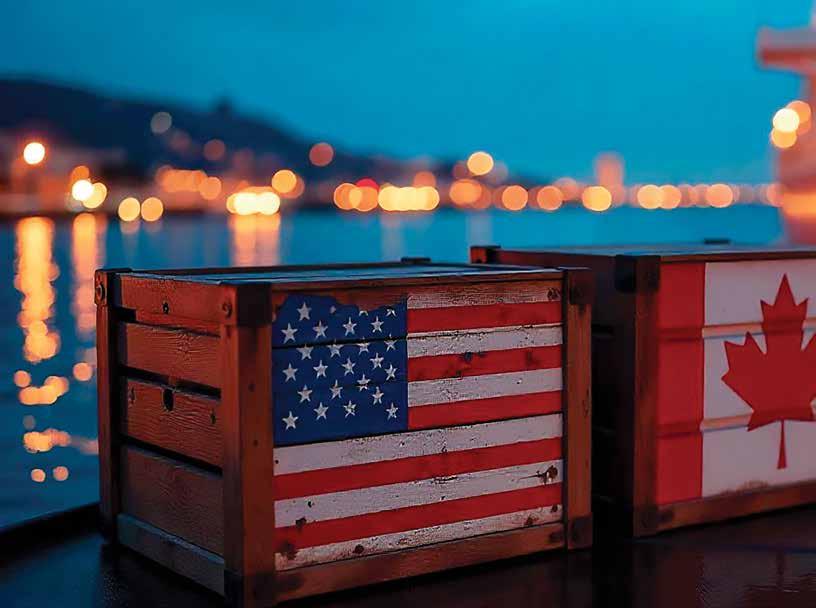
TARIFFS DELAYED
Canada and U.S. agree to delay tariffs for 30 days; steel and aluminium targeted
After two conversations between U.S. President Donald Trump and Canadian Prime Minister Justin Trudeau, the countries agreed to delay their 25 per cent tariffs for 30 days.
Following the conversation, Trudeau posted on social media, saying, “I just had a good call with President Trump. Canada is implementing our $1.3-billion border plan—reinforcing the border with new choppers, technology and personnel, enhanced coordination with our American partners and increased resources to stop the flow of fentanyl. Nearly 10,000 frontline personnel are and will be working on protecting the border.
“In addition, Canada is making new commitments to appoint a Fentanyl Czar, we will list cartels as terrorists, ensure 24/7 eyes on the
border, launch a Canada-U.S. Joint Strike Force to combat organized crime, fentanyl and money laundering. I have also signed a new intelligence directive on organized crime and fentanyl and we will be backing it with $200 million. Proposed tariffs will be paused for at least 30 days while we work together.”
Since then, Kevin Brosseau, a former deputy national security and intelligence adviser, has been named Canada’s fentanyl czar.
The 30-day delay was announced Feb. 3, putting a halt to the tariffs that were set to take effect the following day.
Despite this, Trump announced Feb. 9 he would place tariffs on all steel and aluminium entering the U.S., including from Canada.
The Canadian Steel Producers Association (CSPA) immediately called
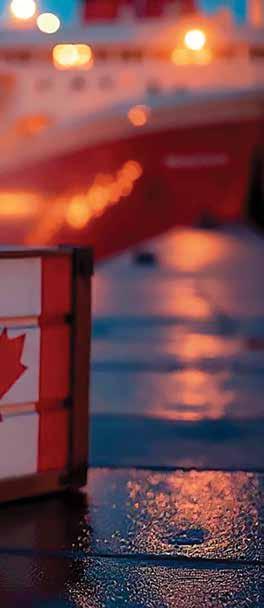
“The reality is the tariffs are unreasonable and are out of proportion to the problem. The tariffs are like taking a sledgehammer to crack a nut.”
– Stephen Laskowski, Canadian Trucking Alliance president.
on the federal government to respond swiftly if Trump followed through with the 25 per cent tariffs.
“We are deeply concerned that U.S. President Donald Trump is again threatening more tariffs on Canada, this time directly targeting the steel and aluminium sectors,” CSPA president and CEO Catherine Cobden said in a statement.
Cobden warned that similar tariffs in 2018 caused major disruptions in both countries, harming businesses and workers. She emphasized the close economic ties between Canada and the U.S., noting that steel trade between the two nations is valued at $20 billion annually, with 40 per cent of Canada’s steel imports coming from the U.S.
“This at a time when Canada has worked tremendously hard to align our trade policy with the United States to protect both markets from unfair trade that threaten jobs and communities,” she said. “For example, Canada implemented its own Section 53 tariffs on Chinese steel imports and a monitoring system of all imports to ensure it can identify the country of melt and pour.”
Canada reacts to original tariff threat
In addition to several provinces eliminating U.S. products from their shelves, the federal government moved forward with 25 per cent tariffs on $155 billion worth of goods in response to the tariffs imposed by the U.S. on Canadian goods.
The government said the Canadian tariffs had one goal: to protect and defend Canada’s interests, consumers, workers and businesses.
“The first phase of our response will include tariffs on $30 billion in goods imported from the U.S., effective Feb. 4, 2025, when the U.S. tariffs are applied,” a release said. “The list includes products such as orange juice, peanut butter, wine, spirits, beer, coffee, appliances, apparel, footwear, motorcycles, cosmetics, and pulp and paper. A detailed list of these goods will be made available shortly.”
The Canadian Trucking Alliance (CTA) released a statement urging the Canadian government and provincial premiers to meet with U.S. officials to bring an immediate end to what it called an “unwarranted trade conflict.”
“This has gotten out of hand,” said CTA president Stephen Laskowski. “The reality is the tariffs are unreasonable and are out of proportion to the problem. The tariffs are like taking a sledgehammer to crack a nut.
“We support Team Canada and our provincial and territorial governments, along with business, labour and other leaders that have been working vigorously on a robust response. But the reality is the Americans clearly believe we are not doing enough to address their concerns. We therefore need Ottawa and Washington to come together to find common solutions to this specific challenge rather than bringing economic chaos to both countries.”
Trump announced Feb. 1 that he would move forward with the 25 per cent tariff on Canadian goods, with the exception of oil and gas, which was to have a 10 per cent tariff imposed. Trump has continued to say the reason for the tariffs is to force Canada—and Mexico, which will also see a 25 per cent tariff on goods entering the U.S.—to secure its border and stop the flow of fentanyl and illegal immigration into the U.S. He also claims the U.S. has been the victim of unfair trade policies and has been “subsidizing” Canada for several years.
“Parliament is where the business of government functions, and so it’s imperative it is restarted as we face this crisis,” said Laskowski. “As a nation, we must support Team Canada to withstand these unfair tariffs while also sending a strong message to the Americans that we are ready at the highest levels to work together.”
The Mining Association of Canada (MAC) said both sides need to find a solution.
“The partnership on critical minerals between Canada and the U.S. began in earnest with the development of the Joint Action Plan on Critical Minerals Collaboration in 2020 under President Trump,” said Pierre Gratton, president and CEO of MAC. “In lieu of tariffs, Canada and the U.S. should be focusing on how to deepen this collaboration. The minerals and metals industry in Canada stands ready to strengthen our relationship with the United States, ensuring the free flow of these essential resources that drive economic growth, defence capabilities and technological advancement on both sides of the border.”
Trudeau met with Canadian business leaders in Toronto Feb. 7 to discuss the country’s way forward amid the tariff threat.
THE FUTURE OF FREIGHT
How AI and telematics are reshaping trucking and rail
Trucking is a dominant force in the North American supply chain and logistics sector. In Canada, more than 90 per cent of consumer products are shipped, either in part or solely, by truck, according to the Canadian Trucking Alliance. Approximately two-thirds of Canada’s trade with the U.S. is done by truck—followed by rail—with over 10 million trucks crossing the border each year.
In the U.S., the numbers are similar, with the American Trucking Associations saying around 73 per cent of the country’s freight by weight is moved by truck.
Given these statistics, it’s not surprising there is a continued push to improve the efficiency of truck transportation for the betterment of the industry, consumers, businesses and the environment.
This is what excites Derek Luke and his team at Geotab, where innovative new technolo-
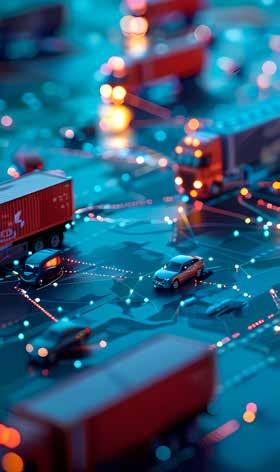
Logistics and transportation security
From transportation to warehousing, inventory management, last-mile delivery and more, you can count on GardaWorld Security to strengthen the security of all vulnerable links in your supply chain, ensuring that your operations can proceed safely and without interruption.
garda.com/logistics
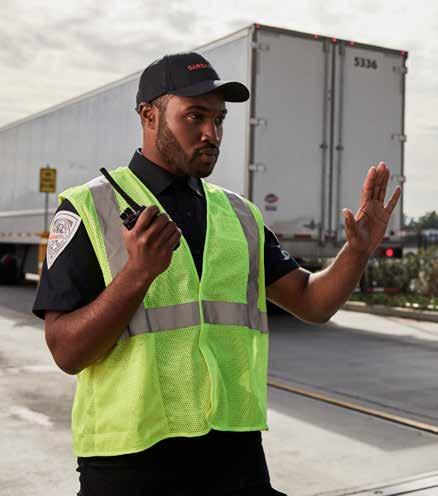
image: freepik.com
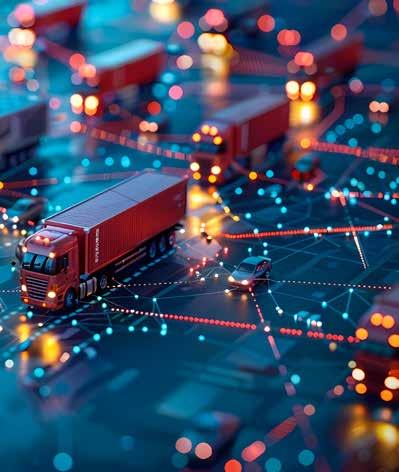
gies are being developed to help transform the supply chain over the next decade.
Luke, chief operating officer at Geotab, first pointed to the integration of artificial intelligence to help provide actionable insights to fleets.
“Rapid advances in artificial intelligence are leveraging billions of data points to solve complex customer problems with unparalleled precision,” said Luke. “These models can identify collision risks, predict safety-critical maintenance needs and deliver actionable insights that set new benchmarks for operational efficiency.”
With the incorporation of AI in telematics, Luke said not only will there be improvements in fleet performance, but also driver safety.
To monitor fleet performance, real-time tracking is essential, something Luke said must work seamlessly with transportation management software.
“These integrations streamline logistics and operations by enabling route optimization, real-time tracking and automated processes,” he said. “Backed by a powerful rules engine for real-time data to ensure a safer, sustainable, efficient and effective supply chain management.”
Telematics can also be better integrated with warehouse management and inventory systems, Luke said, by using advanced asset tracking technologies that provide real-time visibility and communication across the supply chain.
“Solutions like Bluetooth and Wi-Fi beaconing technology enable precise tracking of assets within warehouses and transportation hubs, offering location-based insights that improve inventory management and streamline operations,” said Luke.
Jason Gillespie, senior director of continuous improvement innovation at DHL, is also seeing continued expansion of AI to predict delivery times, using machine learning and enhanced data sources like traffic and weather.
Fully autonomous Class 8 trucks are another area Gillespie said DHL is leveraging new truck technology, working with Volvo Autonomous Solutions on this project and launching its first autonomous operation in the U.S. in December.
“The operations will be enabled by the purpose-built, production-ready Volvo VNL Autonomous, which is powered by Aurora’s SAV Level 4 technology. This truly enhances our operations, as we will use DHL Supply Chain drivers to deliver to the autonomous hubs, as well as final mile from the AV hubs, to complement the longer autonomous haul,” said Gillespie, adding that there will be a safety driver in the vehicle for the foreseeable future.
Ensuring cargo integrity is always an area of concern for any shipper, whether it be high-value goods or temperature-sensitive shipments.
“For temperature-sensitive goods, telematics systems can integrate with cold chain management solutions to monitor and maintain optimal conditions during transit,” said Luke. “This ensures compliance with regulatory standards and minimizes the risk of spoilage or damage, which is especially critical for industries such as food and pharmaceuticals.”
DHL Supply Chain uses an Internet of Things (IoT) solution, partnering with several providers to establish a solution for every use case—passive or active, temperature, impact, light exposure, etc.
Sustainability is another area DHL prioritizes, operating around 130 alternative-fuel Class 8 trucks, including renewable diesel and natural gas, hydrogen fuel cell electric and battery electric, to help reach its environmental goals.
And, as Luke highlights, telematics can help companies meet sustainability goals. Smarter routing, reduced idle time, monitoring driver behaviour, predictive maintenance and sustainability metrics and reporting are all key to reaching those goals.
“By leveraging telematics, companies can take significant strides toward achieving sustainability goals while simultaneously enhancing operational efficiency and reducing costs,” said Luke.
Moving forward, the trucking sector will always have its share of challenges, and for individual fleets, the cost of these new technologies is top of mind.
“With our electric yard trucks, we’ve proven that there is a return on investment and, in many ways, better than a traditional diesel due to reduced maintenance and driver comfort,” said Gillespie.
But new technologies like fuel cells and battery-electric trucks bring their own challenges, like weight—reducing cargo capacity— and scalability.
“Can the solution scale outside of a specific use case?” questioned Gillespie. “The availability of EV charging stations or hydrogen fueling stations is a key issue for scalability, and something that we are working to solve with our partners.”
On track
The efficiency, safety and sustainability of rail have also improved with the use of AI and machine learning (ML).
Danny Dever, senior product manager at rail management software company TransmetriQ, said shippers are seeing improvements in how their cargo is being tracked.
“More accurate ETA predictions are supported by massive amounts of data coming from a sophisticated network of wayside detectors, GPS and other on-board sensors and railroad dispatching systems,” he said. “AI and ML are being applied to instantly bring shippers the data they need in a format they can use.”
Dever also pointed to the efficiency of rail transportation, and although trucking has benefited from its flexibility, that is now changing.
panding the number of intermodal terminals to make rail shipping attractive to more shippers.”
Advanced technology in the rail sector is helping to attract more shippers to the mode, including the development of autonomous terminal operations and AI-enabled shipment tracking.
The sharing of technology tools by railroads at high-volume terminal locations is another way the sector is trying to improve operations and prevent congestion.
“This not only keeps shipments moving on schedule, but it also enables more efficient crew deployments, reduces locomotive idling and supports more accurate shipment ETAs,” said Dever.
Like the trucking sector, predictive maintenance technology helps improve the reliability of rail and its infrastructure.
AI and ML support operational safety and reliability by identifying issues on railcars.
“Railroads have installed an extensive network of track-side detectors that collect images, measure bearing heat and sound signatures, identify dragging equipment and develop other data from moving trains,” said Dever. “With advanced technology, this data is instantly analyzed and—when necessary—alerts are immediately generated for managers to order corrective actions.
“Railroads, car owners and lessors now have much more detailed data that enables the identification of equipment and component wear trends for early intervention that can extend the life of rail assets.”
With the vast network of the North American rail industry, the amount of data produced can be overwhelming. Dever said this data has been optimized in recent years through auditing of gathering techniques and the use of advanced technologies to produce more useful analysis.
“Though there is more work to do, rail industry planners now have accurate and insightful predictive tools to support improvements across a wide range of critical management functions,” said Dever, underscoring safety, system integration and cybersecurity as a few examples.
In the coming years, Dever sees improved real-time visibility, greater reliability and flexibility and more use of autonomous technology, drones and robotics playing a significant role in advancing the rail sector.
WORKING TOGETHER
Though at times they are competing modes in the North American supply chain, trucking and rail are not always jostling each other for position. As Dever points out, better intermodal connections between rail, highway and ocean open new options for logistics planners.
“AI and ML technologies empower managers to make real-time routing and schedule adjustments based on dynamic conditions, which facilitate more accurate planning for an efficient handoff at terminals,” he said.
Geotab provides solutions for greater intermodal compatibility, integrating with transportation management systems and leveraging location data to allow telematics to facilitate better collaboration across transport modes.
Working together also helps address sustainability.
“Coordinating with other transport modes often enables more sustainable logistics solutions,” said Luke. “Telematics helps identify opportunities to shift portions of cargo to rail or maritime—modes with lower carbon footprints—while ensuring that trucking remains an integral part of the supply chain for last-mile delivery.”
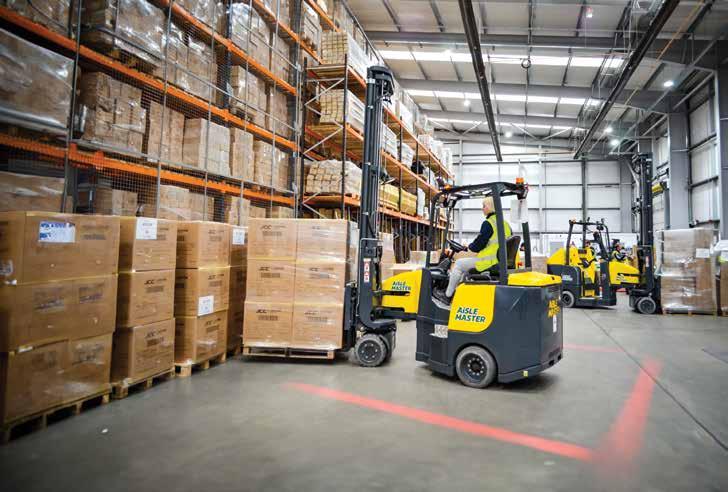
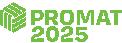
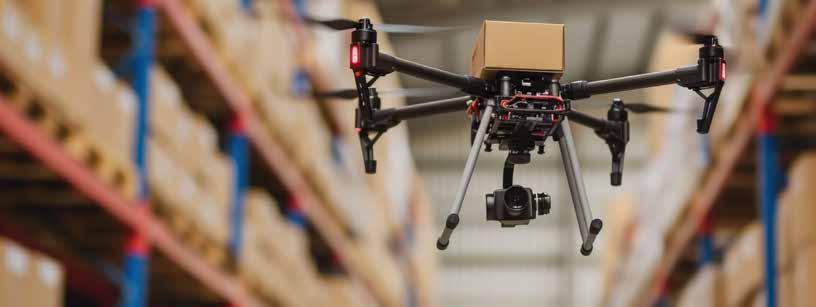
BUZZING AROUND THE WAREHOUSE
How drones are being used to improve warehouse inventory accuracy and efficiency
Warehouses are becoming more and more automated as companies search for new and innovative ways to not only reduce costs but also help their workforce become more accurate and efficient, all while minimizing the intensity of their day-to-day responsibilities. One way warehouses are achieving this goal is through the use of drones.
During the NextGen Supply Chain Conference in Chicago late last year, AJ Raaker, director of warehouse development with Taylor Logistics, highlighted the benefits of using drones to enhance inventory accuracy and efficiency, particularly how the adoption of artificial intelligence, such as vision-based systems, offers richer data compared to more traditional methods like barcodes.
“Here’s what it looks like: a commercially off-the-shelf drone flies itself, takes images of inventory locations and converts those into data like case counts, occupancy levels and inventory matches,” said Raaker.
Offering gains in efficiency, Raaker said drones collect billions of data points every week, providing insights into inventory health, damage and positioning, all of which come with an array of benefits, including customer visibility, service level agreement accuracy and labour reduction.
“In a facility with about 20,000 rack locations, we were able to cut about 87 per cent of the labour required for inventory management, giving time back to other programs,” said Raaker.
Installation and challenges
With a company like Gather AI – which supplies drones to warehouses for inventory management to help companies save money, reduce losses and improve productivity and revenue – the installation process includes mapping a warehouse’s rack locations using QR codes, integrating the drones with the warehouse management system and training staff on how to properly utilize the new technology.
The drones operate autonomously and do not require Wi-Fi, making them easier to deploy and scale across the facility.
Raaker said initially, the AI did struggle to complete certain tasks, such as counting the number of bags of dog food on hand. But over time, data collection and machine learning improved and accuracy numbers increased.
“Early on, we were bad at counting dog food bags. But as we collected more data, our learning got better,” he said.
Overall, Taylor Logistics saw significant improvements in inventory accuracy while also achieving cost savings and greater customer satisfaction.
“Our customers can virtually walk through the warehouse from anywhere in the world,” said Raaker. “This is AI having a real, tangible impact on supply chains—improving inventory accuracy while reducing labour.”
DRONE DETAILS
■ Gather AI’s drones operate at temperatures as low as zero degrees Celsius (32 Fahrenheit) and can fly for approximately 20 minutes before needing to charge their battery.
■When the drone battery is low, it lands and an operator swaps out the drained battery for one that is fully charged.
■ One drone can scale 300 pallets per hour, including the time it takes to swap batteries.
■Set-up time depends on the size and density of the warehouse but typically ranges from four to six weeks.
■Integrated into a warehouse’s operating system, the drones’ AI scans barcodes, text and additional information in the images it takes of the products and compares that with what is in the WMS.
■ Companies do not purchase the drones from Gather AI, as they are included in the service fee. If a drone breaks down, a new one is sent to replace it at no cost.
FACING UNCERTAINTY
Trucking industry grapples with political shifts, ZEV adoption and labour gaps
Canada’s
leading partner for end-to-end Toyota forklift and material handling solutions.
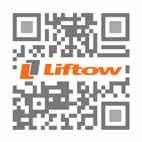
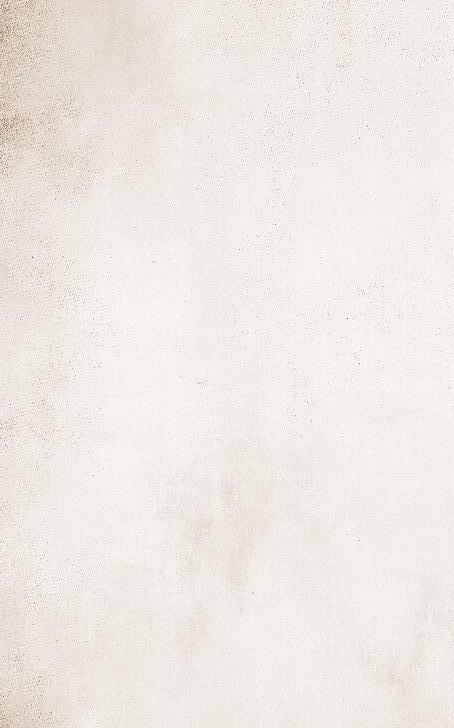

The slow adoption of zero-emission vehicles (ZEVs), a lingering driver shortage and the continued push toward the integration of new technologies, including artificial intelligence (AI), are some of the key issues facing the trucking and logistics sectors in the coming year, according to a survey from Trucking HR Canada and Abacus Data.
Speaking during a webinar Jan. 22, David Coletto, founder, chair and CEO of Abacus Data, offered some insight into the Trucking Leaders’ Outlook 2025, saying uncertainty about the impact of government policies and external disruptions has resulted in limited optimism among respondents.
“One in four leaders—28 per cent—say, ‘I’m not sure,’” Coletto said of respondents’ future expectations. “That reflects the challenge we’re all grappling with: it’s hard to predict the full impact of these changes.”
Part of that apprehension stems from expected complexities in cross-border, as well as interprovincial, trade dynamics.
“We don’t really know exactly what’s going to happen because we don’t know what [Donald Trump] is going to do, how long he’s going to do it and what our government’s capacity is to respond,” said Coletto.
Closer to home, Coletto said the survey highlighted respondents’ expectations that political policies in Canada will change with what appears to be an imminent federal election. This could mean changes to regulations, taxes and carbon pricing.
“Political change is coming,” said Coletto, “and we’re on the cusp of profound technological change in the industry. Both will define the next decade.”
Trucking and logistics sector
Three of the most significant challenges facing the trucking and logistics sector have long been on the industry’s radar.
Labour shortages, particularly of drivers, have been an issue facing the trucking sector for years, with the average age of truck drivers
“The shift to AI is creating a demand for workers with tech backgrounds. Every sector will be competing for this talent, making it critical for trucking to position itself as an employer of choice.”
– David Coletto,founder, chair and CEO of Abacus Data
ers, have been an issue facing the trucking sector for years, with the average age of truck drivers in Canada in the mid-50s.
“Eighty-four per cent of industry leaders believe driver shortages will continue to shape business conditions, showing how urgent this issue has become.”
With changing immigration policies also impacting the industry’s labour needs, Coletto said technology and AI will have an effect as well.
As the integration of AI into fleet optimization becomes more widely accepted, the need for skilled, tech-savvy workers continues to grow.
“The shift to AI is creating a demand for workers with tech backgrounds,” said Coletto. “Every sector will be competing for this talent, making it critical for trucking to position itself as an employer of choice.”
Other truck technologies, such as ZEVs and autonomous vehicles, have made strides in the past few years, but adoption remains slow, and only a small percentage of fleets have added them to their portfolio.
“Despite ambitious federal targets, the move toward zero-emission vehicles is not happening yet,” said Coletto. “Only 14 per cent of fleet leaders plan to add ZEVs to their fleets in the next few
years. The vast majority of zero-emission vehicles in fleets today are battery-operated, with only a handful being hydrogen-powered, showing just how early we are in this transition.”
As for autonomous trucks, Coletto said while they appear to be years away, the use of AI to optimize fleet operations is here, with half of industry leaders saying they either use it or plan to.
Bringing about change
Coletto said in order for the trucking and logistics sector to create change in the industry, leaders must frame their issues in a way that shows how they directly impact consumers and workers if they want to persuade policymakers.
“If you’re advocating for change, frame your issues through the lens of how they make the average person’s life harder,” he said. “Politicians care most about consumer challenges and worker impacts.”
Coletto added that disruption and crisis can create unique opportunities to push for change, whether it be through government policies or on the technology front.
“We overestimate how much will change in one year, but we underestimate how much will change in 10,” said Coletto. “The trucking sector is no exception to this rule.”
THE TRANSPORTATION TRANSFORMATION
Collaboration and innovation drive the future of transportation in supply chains
Assessing what the future of transportation will look like has been a popular topic of discussion for several years, and 2025 will be no different. Whether it is automation, electrification or alternative fuels, the ideal path forward has never been a certainty — though that is not to say the options available are not viable.
However, to move forward with anything new, there must be a collaborative effort from everyone involved, which Vijay Cherukuru and Dr. Yanfeng Ouyang underscored during the NextGen Supply Chain Conference in Chicago this past October.
During a presentation on the future of transportation and logistics in relation to the movement of goods, Ouyang, a professor at
the University of Illinois Urbana-Champaign, said collaboration between communities and urban planners is essential if the necessary infrastructure is to be incorporated.
“In some cities, there are new planning codes requiring developments to accommodate new technologies, such as infrastructure for drone deliveries,” he said.
Ouyang said cities play a crucial role in adopting new technologies, particularly those related to electric and autonomous vehicles, adding that governments and urban planners are becoming key partners in shaping the future infrastructure needed to accommodate these innovations.
Urban infrastructure also plays a role in the efficiency of freight

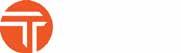

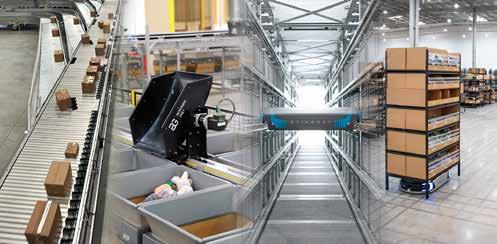
delivery. How cities redesign their infrastructure — such as curb management and accessibility — will help spur the rise in autonomous vehicle delivery systems.
“The design of curbs and parking for delivery vehicles will change as autonomous systems become more prevalent,” said Ouyang. “Autonomous vehicles will likely reduce the need for traditional parking spaces, allowing for more development in central areas. It’s crucial to work closely with local governments in defining standards and policies to ensure that both community needs and business goals are met.”
Ouyang said it’s important to engage with government on infrastructure projects, but that requires a strategic approach: understanding the local government’s priorities, aligning community interests with business goals and considering challenges and regulations.
Integrating new technologies can also be challenging when it comes to public acceptance, especially with autonomous vehicles. Not only are there concerns surrounding driverless vehicles, but these kinds of technologies and the infrastructure they require impact how people live and the way businesses operate.
“Cities have to balance community interests and urban form changes,” said Ouyang. “New technologies impact where people live and how they choose to travel.”
Warehouse operations and delivery schedules are also affected by the integration of autonomous and electric vehicles. Cherukuru, director of product for Walmart, said companies must make adjustments to accommodate new technologies, particularly around weight distribution and operational software.
“As new technologies are implemented, delivery operations must be adjusted to handle changes in weight distribution and scheduling,” he said. “Software and human factors need to evolve to support new operational models, and companies must ensure the stability of their supply chains.”
Cherukuru added that although alternatives like hydrogen and electric — including battery-swapping — have promise, barriers remain that hinder widespread adoption.
“Battery swapping is an interesting technology, but it faces challenges around standardization and inventory management,” he said. “Swapping batteries may introduce risks to operational safety and could be logistically complicated, especially with the large size
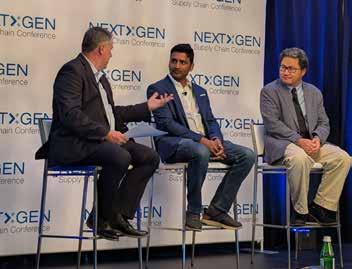
“Cities have to balance community interests and urban form changes. New technologies impact where people live and how they choose to travel.”
–
Dr. Yanfeng Ouyang, professor at the University of Illinois Urbana-Champaign
of truck batteries.”
Despite the challenges, both Cherukuru and Ouyang see the future of the logistics industry heading toward electric and autonomous vehicles.
“We envision a future where electric vehicles have longer ranges,” said Ouyang, “and the cost difference between electric and traditional vehicles is negligible.”
WAREHOUSES | By
Jeff Larson
ELIMINATING THE PUTAWAY ODYSSEY
Autonomous mobile robots – fast tech to better manage returns
The holiday season may be behind us, and it was a fast one. The shopping period between Black Friday and Christmas was six days shorter than in previous years, putting logistics leaders under significant stress during their peak. After shipping an estimated $989 billion in goods during the holiday season, they quickly transitioned into the return season. In the blink of an eye, warehouses shifted from
shipping outbound goods to receiving returns — no small task. In 2023, $247 billion worth of merchandise purchased online was returned, according to the National Retail Federation.
To some degree, high online return rates are an outcome of industry practices. Free returns for online purchases have become ubiquitous, complicating warehouse operations. If returns are not processed quickly, they lose resale value and can lead to
Vijay Cherukuru and Dr. Yanfeng Ouyang say the future of transportation in logistics is autonomous and electric.
losses, especially in fashion and apparel, where products have a 90-day cycle before becoming obsolete.
Unfortunately, the industry does not typically approach returns with the same precision as sales. Many “putaways” are tossed into bins with multiple SKUs grouped together. Armed with RF scanners, associates walk the warehouse floor to locate the correct location for each item. Digging through totes to find the right SKU takes time, and while associates may have item descriptions, they often lack photos for reference.
To manage returns more effectively, some facilities create designated return areas inside the warehouse and place products i n speed cells. Employees are encouraged to start there when filling new orders. However, these areas are often mixed-SKU, which slows fulfillment, and items may be handled multiple times during the process.
The bottom line: returns are often managed haphazardly, reducing productivity and eroding value. Fortunately, autonomous mobile robots (AMRs) are helping 3PLs and other logistics operators handle putaways more efficiently.
Keeping up with relentless returns
Putting returns where they belong in a warehouse is an unrelenting task, but AMRs streamline the process. Like traditional manual carts, AMRs hold merchandise for transport. The difference i s that warehouse staff don’t need to push them or decide where items should go.
These functional robots simplify picks and putaways while reducing mental and physical strain on associates. Equipped with computer vision, artificial intelligence, and light detection and ranging (LiDAR) systems, AMRs navigate warehouses autonomously and help staff distribute products more efficiently.
A MRs make smart moves, guided by software to collaborate with associates on picks and putaways. They are highly scalable,
allowing distribution centres and warehouses to add or remove units or move them between sites as needed.
AMRs direct the workflow. Instead of associates zigzagging through the warehouse, an AMR leads them to the correct destination via the most efficient route. Whether it’s a new hire o r a 15-year veteran, workers no longer need to think about where to go or how best to get there. AMRs act as sherpas for associates.
While AMRs work collaboratively, they are not assigned to specific people. Some use smart software to identify the employee nearest their destination. If a tote contains items in a isles one through three and 12 through 15, the robot pairs with the closest workers to optimize pickup and reduce travel time. It’s not just one AMR; it’s a coordinated team of them.
Once a robot arrives at the proper putaway destination, the associate doesn’t need to guess which SKU to handle or where to place it. The AMR’s screen displays the product’s picture and guides the worker to the appropriate bin. Identifying a red shirt with a bunny logo, rather than SKU 2532348, simplifies the task and improves productivity.
Increasing putaway efficiency
The flexibility and “on-the-wheels” intelligence of an AMR fleet make the entire warehouse operation more efficient. AMRs and associates can alternate between putaways and picks based on priority and easily scale to meet fluctuating demand.
Ultimately, AMRs are force multipliers, enhancing the efficiency of associates and existing warehouse infrastructure in managing the inevitable avalanche of returns after this — and every — p eak season.
Jeff Larson is the director of solutions design for Ocado Mobile Robot System at Ocado Intelligent Automation.
Full Name:
Address:_______________
Phone: ______________
RENEW YOUR COMPLIMENTARY SUBSCRIPTION!
Simply complete this form today and Email to delon@turnkey.media Or Visit
https://ww w.insidelogistics.ca/subscribe/magazine/
Company:______________________
Title:___________________
Email:__________________________________ (Email Required
YES, I WISH TO RECEIVE INSIDE LOGISTICS MAGAZINE FREE!
YES, I WISH TO RECEIVE INSIDE LOGISTICS E-newsletter FREE!
Choose your Edition: Print Digital Print & Digital
Signature:
Date:
PLEASE ANSWER THE FOLLOWING QUESTIONS TO QUALIFY FOR YOUR FREE SUBSCRIPTION:
1. Do you purchase, or influence the purchase, of goods and/or services related to distribution logistics, including warehousing operations (receiving, storage or shipping) or inventory control or materials handling? Yes No
2. If Yes, do you have plans to buy any of the following in the foreseeable future? (Check as many as apply)
(A) Forklifts and mobile materials handling equipment
(B) Racking, shelving and storage equipment
(C) Software, eg WMS, TMS, YMS, WES, etc
(D) Automated materials handling systems
(Z) None of the above
(E) Third-party logistics services
(F) Transportation services
(G) Real estate, warehouses, existing or new building
(H) Data capture and inventory control equipment
TRANSPORTATION SERVICES: LTL Trucking Truck Load Trucking Intermodal Marine Rail Courier Air Freight None
3. What is your company's PRIMARY business?
MANUFACTURING (Check one only)
(01) Food & Beverage
(02) Consumer Durables
(03) Paper & Print
(04) Automotive Parts
(05) Clothing, Apparel & Textile Products
(06) Chemicals, Petroleum & Hazardous Waste
(07) Pharmaceuticals
(09) Computers & Electronics
(10) Transportation Equipment
(11) Lumber & Building Materials
(12) Manufactured Industrial Inputs
(98) Other Manufacturing (please specify)________________________________________________________________________
NON-MANUFACTURING (Check one only)
(13) Agriculture, Forestry, Fishing & Mining
(14) Transportation Services
(15) Storage & Warehousing Distributor
(16) Distributor
(17) Construction
(18) Retail Trade
(99) Others Allied to the Field (please specify)__ _______
4. Which of the following categories best describes your PRIMARY function? (Check one only)
(A) Executive Management
(B) Purchasing / Procurement
(C) Engineering / Design Engineering / Research & Development
(D) Storage & Warehousing
(E) Financial / Administrative Management
(F) Plant Production / Operations / Maintenance Management
(G) Transportation & Distribution
(H) Materials Management
(Z) Other (please specify)____________ _
5. What is the approximate number of employees at this location?
TARIFFS, TRADE AND UNITY: WHAT TRUMP’S RETURN MEANS FOR CANADA
LIKE MY FELLOW CANADIANS, I have been anticipating the inauguration of President Trump and the trade tariffs that could come with him starting Feb. 1. During his last presidency, tariffs were applied to steel, aluminum and other products, and the impact of similar tariffs today would likely mirror some of the past consequences. If tariffs are reintroduced or increased, Canadian manufacturers and importers of U.S. goods could face higher costs, which would lead to higher prices for Canadian consumers or decreased profit margins for businesses.
Canada and the U.S. have a deeply integrated supply chain, especially in industries like automotive, agriculture and natural resources. Tariffs could disrupt this flow, delay shipments, and lead to inefficiencies or reduced access to key materials. Vehicles are the second-largest Canadian export by value at $51 billion in 2023, of which 93 per cent were exported to the U.S. Automotive is Ontario’s top export, accounting for 28.9 per cent of all exports in 2023. Pair that with the division in the energy/oil and gas sectors in the west, where four million barrels of daily exports ship to the U.S., and we could have a real issue on our hands. While 12 of the 13 premiers have agreed to stand united against the implementation of what is to come, Alberta’s premier is standing firm that the energy sector in Alberta is off the table.
Additionally, in response to tariffs, Canadian businesses may seek to diversify their sources of goods or raw materials to avoid higher tariffs, which could shift trade patterns and increase reliance on non-U.S. suppliers, particularly from countries with more favourable trade relationships with Canada. This is especially concerning for our economy as our dollar continues to fall relative to the U.S. dollar. The possibility of tariffs influencing currency exchange rates,
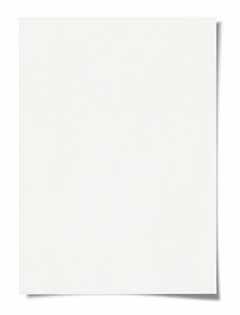
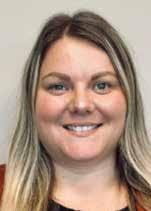
VICTORIA JONES is a supply chain specialist at Tyers Foods
and a slowdown in trade or market uncertainty, could result in the Canadian dollar weakening even further, affecting import prices and the overall economy.
Canada could retaliate with its own tariffs on U.S. goods, which might escalate tensions and lead to a tit-for-tat tariff war, further complicating the supply chain between the two countries. According to Bloomberg, Canada has drawn up an initial list of $150 billion (US$105 billion) of U.S.-manufactured items that it would hit with tariffs if President-elect Donald Trump decides to levy tariffs against Canadian goods. More tariffs from Canada might be added later, depending on what the U.S. does. The products on that initial list weren’t disclosed. When Trump placed tariffs on Canadian steel and aluminum in 2018, Canada responded with levies on a variety of U.S.-manufactured items, such as whiskey and washing machines — a pressure tactic aimed at putting the squeeze on factories in areas where Republican politicians had influence. Those tariffs were much smaller in scope, affecting about $16.6 billion
of U.S. exports at the time.
Ahead of his inauguration, a presidential memo sent to U.S. federal agencies instructs them to re-examine trade policies and re-evaluate relationships with Canada, Mexico and China, but it doesn’t call for any immediate executive orders to enact new economic measures. The Wall Street Journal summarized the memo, noting that U.S. federal agencies will “now assess the impact of the USMCA on American workers and businesses and make recommendations regarding America’s participation in it.”
A review of CUSMA leaves uncertainty in the air for the Canadian supply chain, as it has been essential for trade and market access for our economy.
These are still early days in the next generation of Trump years, and time will tell if these tariffs will actually be implemented or if they are just more smoke and mirrors.
One silver lining in the political power changeover is the recognition from the Longshore Union Workers to Donald Trump for avoiding another potential port strike on the U.S. East Coast — an interesting approach considering Trump’s alignment with tech moguls like Elon Musk, given that the strike action was spurred by an overwhelming aversion to the implementation of tech and AI in the industry.
While these recent events give the illusion of division and uncertainty, Trump has united Canadians in a way I did not think possible. By suggesting we become the 51st state, he has unintentionally pushed the envelope for unity in a country that has been increasingly divided over the last five years. In an almost fortune-telling fashion, Environics did a study in 2022 showing that 83 per cent of Canadians disagreed with joining the United States. A new poll this month similarly found that only 10 per cent of Canadians support the idea.
Thanks for the renewed sense of patriotism, Mr. Trump. I’m here for it.
SAFETY ON THE LOADING DOCK
Don’t overlook one of
the most hazardous areas of your warehouse
IT’S MONDAY MORNING, and you have been selected to perform a safety inspection of the loading dock area and report back at the next health and safety committee meeting.
As you walk by the loading dock, everything appears to be fine. But be careful not to skip over this area too quickly—there may be hazards that are not immediately obvious.
Pay special attention to these areas:
Vehicle securement
Trucks and trailers parked at the loading dock can leave prematurely, even during loading and unloading, putting workers at risk of catastrophic falls.
■ Is vehicle securement adequate, and if so, is it being used?
■ Has the dock lock restraint mechanism been maintained within the last year or more frequently, based on the manufacturer’s recommendations?
■ Is the mechanism attached to the rear impact guard (RIG) of the truck or trailer to enhance safety during loading and unloading?
■ If the RIG cannot be secured—for example, when a liftgate makes it inaccessible—are other suitable restraints, such as wheel chocks, placed in front of the rear tires? Ensure the wheel chocks are in good condition, not hidden by snow and accessible.
■ Another effective way to prevent unwanted movement of dropped trailer loads is to use a glad-hand lock to prevent brake release and premature departure.
Truck movement
Drivers reversing toward loading docks have minimal visibility and many blind spots, putting outdoor workers at risk of being struck. Take a moment to observe vehicle movement outside the loading dock from a safe location.
■ Are trucks backing in squarely toward the loading dock?
■ Are there painted lines on the pavement or other guiding mechanisms, such as directional lighting, to help drivers position properly?
■ Are any workers taking shortcuts by walking between reversing trucks and the loading dock?
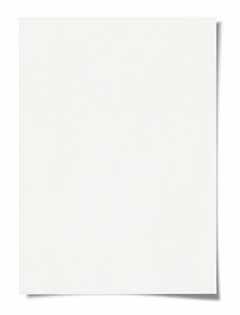
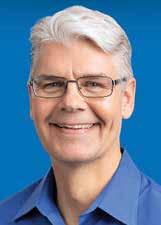
NORM KR AMER, CRSP, P.MM, provides expert, in-depth health and safety consulting services for Workplace Safety & Prevention Services (WSPS) as a warehouse specialist in the Greater Toronto region.
■ Are outdoor workers wearing appropriate high-visibility apparel that makes them easily seen by drivers?
■ Are the dock bumpers in good condition to absorb the shock of a vehicle striking the building?
Housekeeping
Take a close look at the interior loading dock. It is not uncommon to see pallets dropped off in lift truck paths if the staging area is full, space is limited, or operators are not following storage best practices. The interior loading dock often turns into a chaotic obstacle course filled with pallets, lift trucks and people, increasing the risk of incidents.
■ Is there a way to increase space around the dock to permit pallet staging?
■ Are pallets unloaded to the staging area or moved away from the dock to minimize obstructions?
■ Are there enough operators to move pallets to designated storage in a timely manner?
■ Can existing space be optimized? Some businesses have installed two-level racking directly
above the loading dock to use as overflow for lighter pallet loads.
Smooth transfer of pallets to and from the trailer
Lift truck operators are continuously moving back and forth between the loading dock and transport trailers. Gaps or uneven surfaces can imperil both equipment and operators. Look at the following:
■ Are dock levelers at the same height as the trailer to ensure safe and efficient movement of materials?
■ Has the driver or shunter dropped the airride suspension on the trailer before setting the brakes at the dock? Lowering the trailer height reduces the chance of the trailer shifting forward during loading and minimizes forward forces on the landing gear, reducing the risk of collapse. If an air-ride trailer is too high in relation to the dock, the lift truck operator will have less steering control and will experience bumps at each pass, leading to discomfort and possibly permanent musculoskeletal injuries.
■ Are the forks of the lift trucks properly positioned before entering the trailer? If the forks are pointing downward or are too low, they may make unwanted contact with the dock leveler.
■ Is there a risk that workers will get their feet crushed at the edge of the dock leveler? Fit dock levelers with toe guards to reduce this risk.
Pedestrian movement
In general, the closer people walk near loading dock doors, the greater the risk of being struck by a lift truck operator with limited vision. While it may be impossible to eliminate all pedestrian traffic, the loading dock shouldn’t be a thoroughfare.
■ Is there a walkway situated directly through loading zones with high equipment traffic? It’s better to direct people onto a path that avoids busy areas.
■ Are transport truck drivers walking through the loading dock area? Many businesses keep drivers away from danger zones by restricting their movement with a barrier while providing access to a comfortable rest area.
WILL AI SAVE OR ENSLAVE US?
THE HYPE AROUND AI seems unstoppable. Before trying to figure out what this means and where it is leading us, let’s look at some definitions. As defined by Wikipedia, artificial intelligence, in its broadest sense, is intelligence exhibited by machines, particularly computer systems. It is a field of research in computer science that develops software enabling machines to perceive their environment and use learning and intelligence to take actions to achieve defined goals.
My problem with AI starts with the word “intelligence.” We should be more careful with the language we use, as it can easily mislead people, particularly when the wrong terms gain widespread acceptance. Sorry to say this, but a machine is not intelligent.
Intelligence is the ability to learn from experience, adapt to the environment, derive information, understand and correctly utilize thought and reason. AI is a misnomer and should instead be called “technology” or “software.” It reminds me of “smartphones.” Have you looked at your smartphone lately? Do you really find it smart? Our phones aren’t smart simply because technological advances have enabled the manufacturing of a compact device that is not just a telephone, but also a computer, camera, video recorder, flashlight, movie theatre, sound system, and more, while connecting to the entire world via the Internet. That does not make it smart. In fact, instead of calling them smartphones, it would have been more appropriate to call them “compuphones” or “teleputers” to better reflect what they are: tiny, powerful, connected computers with a phone function.
When Thomas Edison invented the light bulb in 1879, did he call it a “smart candle?”
When Daimler and Maybach invented the first motorcycle in 1885 in Germany, did they call it a “smart bicycle?” They did not. I’d guess that in those days, people may have been smarter than us when it comes to language. They probably were not as distracted as we are— glued to our smartphones and social media, straining our eyes, developing attention-deficit disorders, memory loss and gradually losing our capacity for critical thinking.
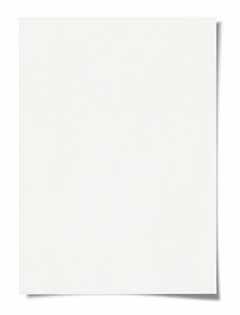
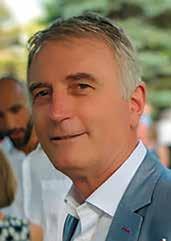
CHRISTIAN SIVIÈRE runs Solimpex, and is an international trade consultant and
lecturer. christian.siviere@videotron.ca
Even “algorithm” is a misnomer. It’s simply a set of instructions carried out in a specific order to perform a task—in other words, a computer program that conveniently tells you what to look at or buy based on your previous activity. If you bought a toothbrush, shouldn’t you buy toothpaste? Do we want algorithms or computer programs to rule our lives? Today, we see many examples of language being used in misleading ways. When high-profile people like Elon Musk or Donald Trump spread lies on X or Truth Social, some call these posts “truth” or “alternative truths” instead of what they really are: outright lies. Similarly, the terms “misinformation” and “disinformation” may lead some people to confuse them with real information. For clarity, we should simply call it “false information.” Artificial intelligence is not intelligence—it is technology developed by intelligent people. Organizations that sell AI, like IBM, want us to believe that AI can learn from new information and experiences, make recommendations to users, act independently and replace the need for human intervention—a classic example being a self-driving car. But if left unchecked and unregulated, AI could lead us to a dangerous place, controlled by a handful of companies. Europe and the U.S. have recognized the potential dangers.
Former U.S. president Joe Biden signed
an executive order on the development of safe AI and the use of personal data. That order was revoked by Donald Trump in his first week back as president, signaling that under Trump, the U.S. will let the industry do what it wants. This could lead to serious consequences for businesses and individuals. A bad actor—whether a wealthy businessperson or a foreign government—could launch a campaign to manipulate public opinion using deepfake videos and AI bots to amplify their message. Without regulations requiring AI providers to verify the authenticity of content, misinformation could spread unchecked, influencing voters, eroding public trust and ultimately threatening democracy.
Despite the negatives of AI and the job losses it is creating—not just in manufacturing, but also among journalists, writers, translators and others—many people rave about its benefits and promise a better world. To put this into perspective, let me mention an in-depth article published in The Globe and Mail last September. It focused on a Canadian biotech company called Deep Genomics, which had raised US$238 million and was researching new drugs using AI. The article quoted the head of Deep Genomics: “AI has really let us down when it comes to drug discovery. We’ve just seen failure after failure.” Another interesting point was that AI experts are not necessarily experts in pharmaceuticals.
So, if you work in supply chain management, distribution or logistics and an AI company wants to sell you its services to solve all your problems, keep in mind that they might not know anything about supply chain management, distribution or logistics.
Of course, technology (or AI, as we call it) can help optimize warehouse operations, improve inventory management, design more efficient transportation routes and boost productivity. Having the tools and data is essential for decision-making, but we don’t want these systems to operate independently. Let’s continue to develop tools that help us be more efficient—but we don’t want a world ruled by AI. Human intelligence must remain in control.
THE LOGISTICS LOWDOWN
WITH DEREK CLOUTHIER
SCAN TO LISTEN
INNOVATING SUPPLY CHAINS: INSIDE THE PIER AT THE PORT OF HALIFAX, WITH DAVID THOMAS, EXECUTIVE DIRECTOR OF THE PIER
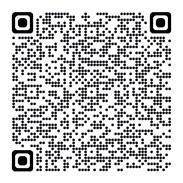
Discussing the topics that impact the supply chain and logistics sector
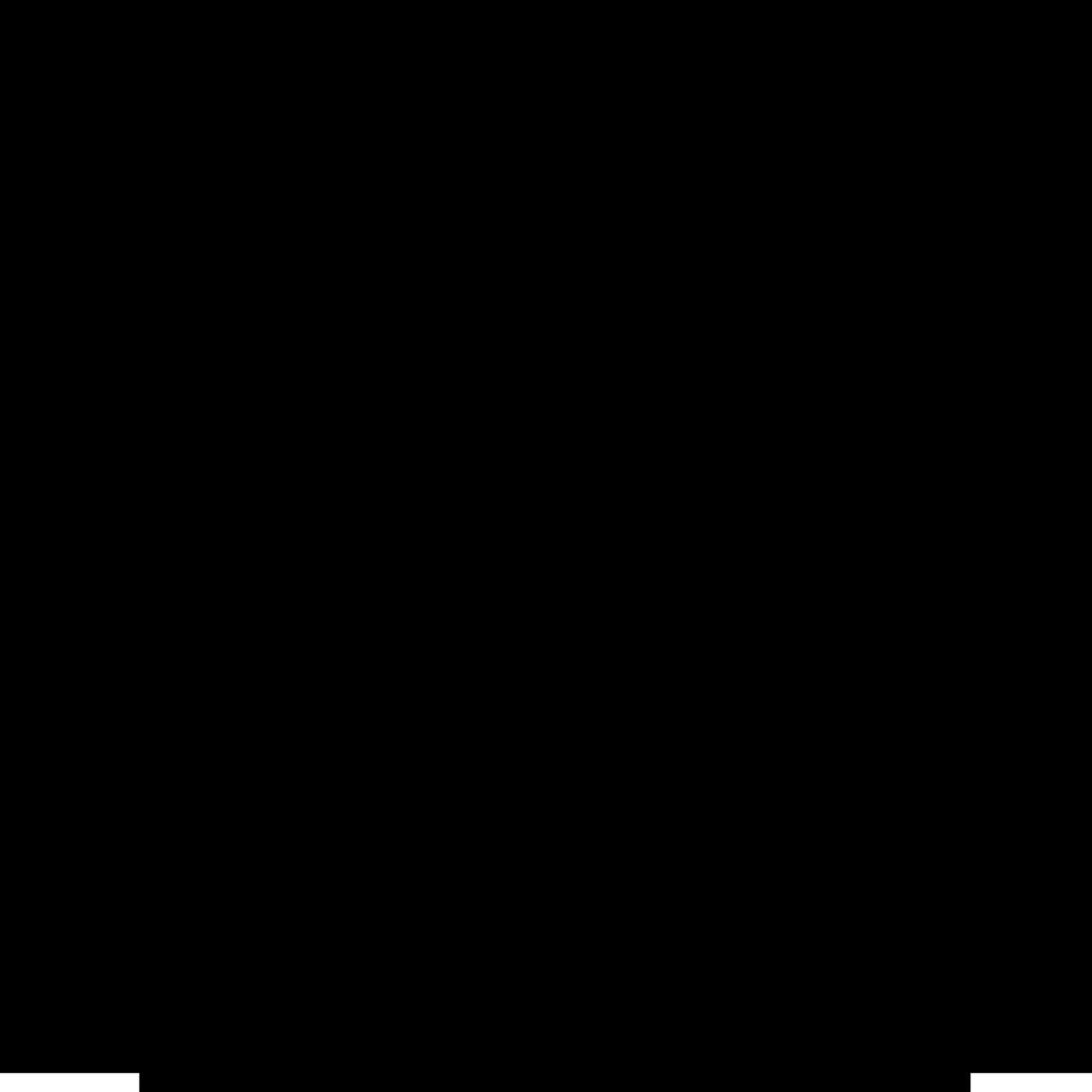
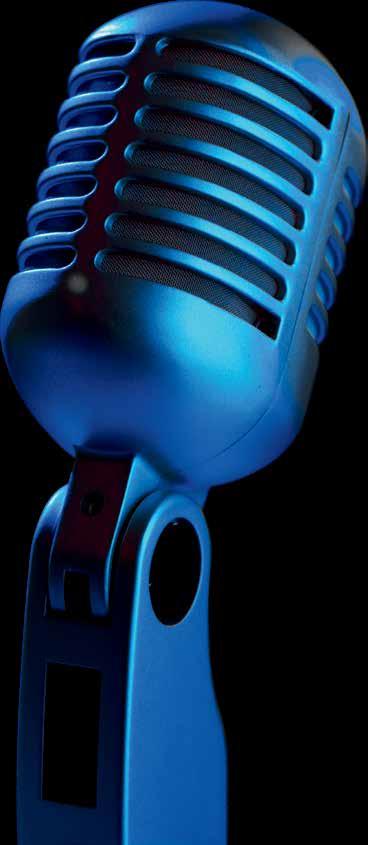
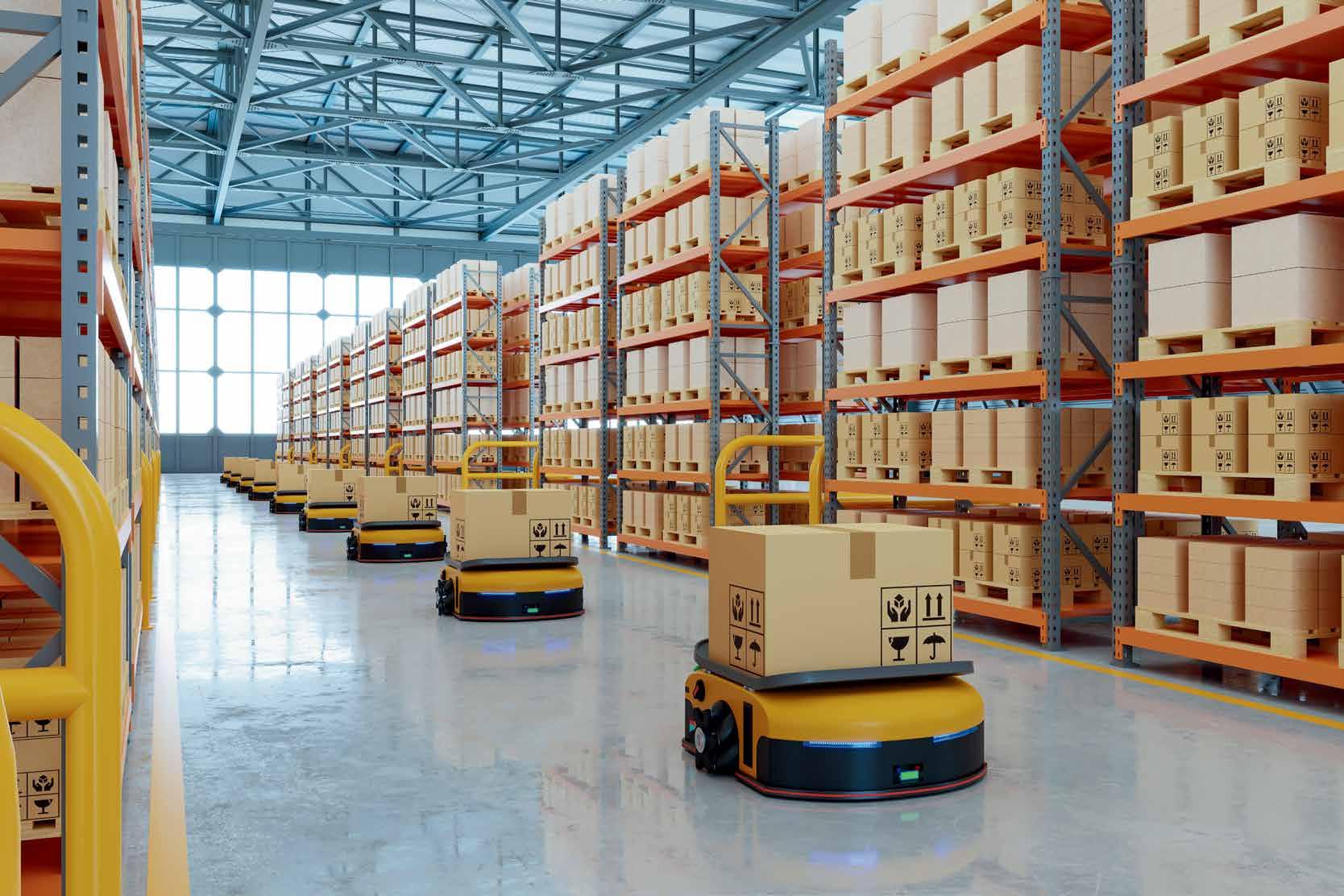
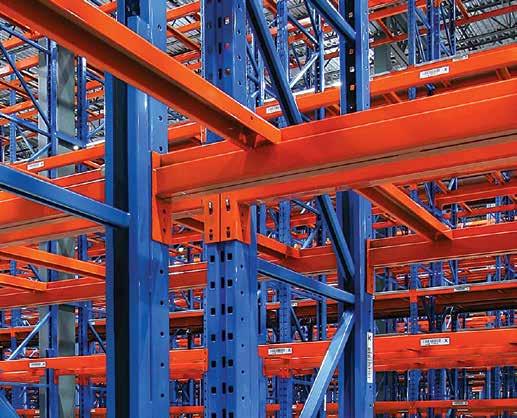
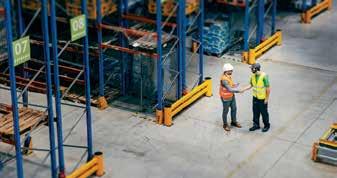
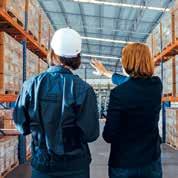
Your partner in facilities evolution
Strong foundations. Smart evolution.
To stay competitive and get ahead, you need innovative, scalable and safe solutions. These solutions can help with better storage, distribution, fulfillment or any combination that can grow with your business as it adapts to change.
As your partner in facilities evolution, you can count on Konstant to transform your facilities. Collaborate with our team to optimize your facility today and evolve, anticipate, adapt and imagine the facility of your future.
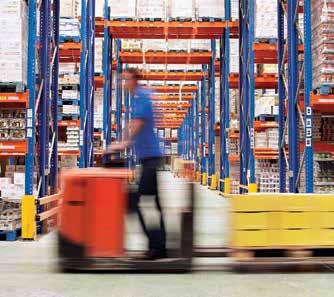
ECOSYSTEM
Get integrated logistics solutions: racks, shelving, trucks and robotics from our partners including Johnston Equipment and GNJ Automation.
EXPERTISE
Access comprehensive services for your project lifecycle, from planning to ongoing management with a skilled team ensuring quality at every step.
EXPERIENCE
For more than 50 years, Konstant has served businesses across Canada, adapting our services to evolving facility management needs.