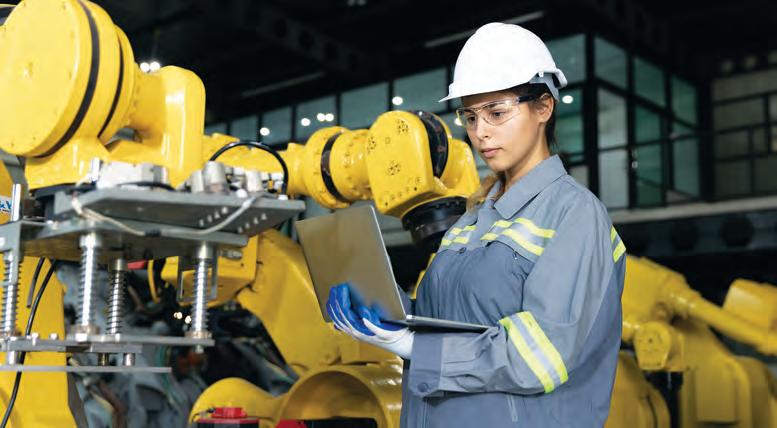
2 minute read
Conducting effective workplace inspections
BY CANADIAN CENTRE FOR OCCUPATIONAL HEALTH AND SAFETY
dust. Psychosocial hazards affect mental health or well-being, like excessive workload, workplace stress, bullying, or violence and harassment.
The inspection team
Health and safety committee members and representatives are a good choice to carry out formal inspections, especially if they have received training or certification. The inspection team should have knowledge of regulations, procedures, and potential hazards, and experience with the work involved.
Engineers, maintenance personnel, occupational hygienists, health and safety professionals, supervisors or managers may be a part of the inspection team, or they may be called upon to help with certain aspects of the inspection or to help explain equipment or processes. Supervisors may be included in inspections and should remain objective and receptive to feedback. Any hazards must be reported whether a supervisor is on the inspection team or not.
Inspection good practices
Never ignore a hazard because you feel you do not have the knowledge to make an accurate judgement of safety. Ask questions and be sure to note each item of concern, clearly describing the hazard and its exact location in your notes. Take photos as needed.
Inspections help identify hazards, and to uncover underlying causes, assess risks, and determine corrective actions.
Planning the inspection
Collect all the relevant information beforehand. Useful documents include a diagram of the inspection area, inventories of equipment, hazardous products and chemicals, past inspection records, and customized checklists. Consider every workplace element, including personnel, equipment, materials, processes, and the environment.
Note the number of workers, demographics, shift schedules, and supervision in the workplace. Inspections of equipment should include machinery, tools, and any safety devices and PPE that may be required with their use.When inspecting materials, include any parts, ingredients or chemicals used.
When inspecting processes, consider how the worker interacts with the other elements in a series of tasks or operations. The working environment is the workplace structure and setting, including conditions that surround workers.
Pay particular attention to items that are unsafe or unhealthy conditions because of stress, wear, impact, vibration, heat, corrosion, chemical reaction, or misuse. You’ll want to inspect areas where no work is done regularly.
How to spot hazards
Hazards typically occur due to unsafe conditions and practices involving workplace elements. During inspection, look for safety hazards such as those caused by inadequate machine guards, hazardous energy, and operational or stationary vehicles. Look for proper housekeeping, are machinery and tools stored properly? Are walkways clear and do workers have enough space to operate equipment safely? Hazards may also exist where there is a lack of fall protection or in confined spaces.
Other types of hazards to look for and record: biological hazards, like bacteria, mould, and viruses, and chemical hazards, which include hazardous solids, liquids, vapours, gases, dust, fumes, or mists. Ergonomic hazards caused by improper work methods, incorrect handling of materials, and poorly designed workstations, tools, and equipment.
These place physiological and psychological demands on the worker that can lead to musculoskeletal injur ies. Physical hazards caused by noise, vibration, weather, heat or cold, radiation, pressure, and combustible
Draw attention to the presence of any immediate danger to the area supervisor. Request that any immediately hazardous item be shut down, locked out, and tagged out by a competent and authorized person until it can be brought to a safe operating standard.
Observe the work environment and consider ergonomic risk factors such as awkward body positioning, repetitive motions, and increased force. Rather than operating any equipment yourself, ask for a demonstration from the operator. Speak to workers when it is safe to do so, asking them questions about job design, work pace, as well as workplace stressors and workload management.
Do not rely only on your senses. If necessary, have a competent person measure levels of exposure to chemicals, noise, radiation, or biological agents. Regularly check the regulatory requirements in your jurisdiction for workplace inspection requirements.
The key to establishing an effective workplace inspection protocol is to be consistent, thorough, and meticulous in following up on all reported hazards and the prescribed actions to correct them. By reviewing inspection reports regularly, the health and safety committee can identify trends and monitor the progress of the recommendations, contributing to the continual improvement process for the occupational health and safety program.