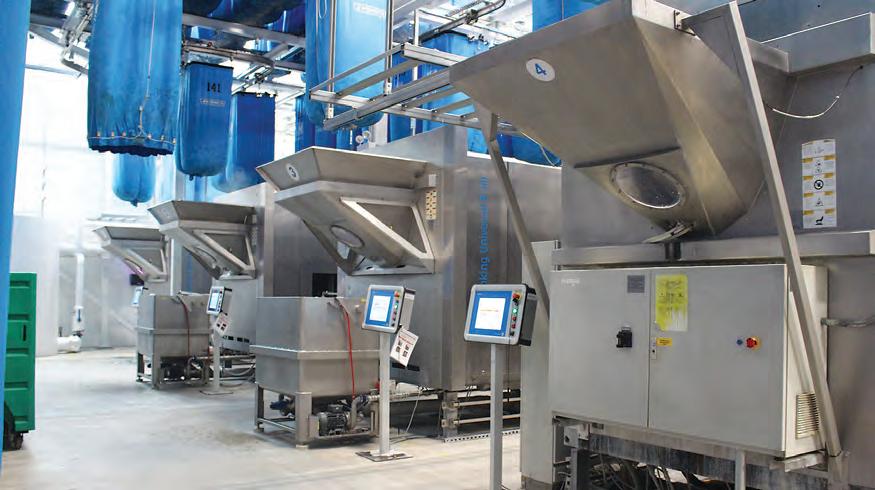
4 minute read
Focus on the linen, uniform and facility services industry
An industry that has existed for many years, and anyone working in an industrial environment, has been exposed to its service.
BY PETER PHILLIPS
This service industry does not get much press and operates in the background, providing essential services to almost every industry and service sector.
The business supplies, launders, and maintains linens, uniforms, towels, mats, and other products for about 100 locations in Canada. You may know it has industrial or commercial laundry or linen supply or textile rental or services. Today, The Association for the Linen, Unifor and Facility Service Industry (TRSA) is a worldwide association that promotes and protects the industry and call it “linen, uniform and facility services.”
The industry services hospitals, manufacturing, food processing, restaurants, and more. Anywhere there is a high volume of cleanable linens, fabrics and uniforms this industr y is present.
For example, many of us who have been involved in manufacturing and processing have used unifor m cleaning services for many years and have given it little thought, if we have fresh and clean uniforms and coveralls to wear.
Linen and unifor m service companies rent most items to customers with fees for laundry and pick-up/delivery included in the rental charge, such as industrial uniforms, linen garments, tablecloths, napkins, walk-off mats, towels, and mops. Some items such as high-fashion garments or promotional items are customized with a customer’s company logo and are sold directly with or without laundry service, while others are leased without laundry service, including outdoor walkoff mats and some uniforms.
Businesses that cannot economically launder textiles in-house have been the best customers. Fine-dining restaurants are the classic example because of their extensive use of linen napkins and tablecloths.
Manufacturing and auto-related business owners whose workers’ uniforms are soiled with oil and chemicals require the heavy-duty laundering of a professional service. Increasingly, hospitals and other medical services and hotels have closed their on-premises laundries in favour of higher quality, more cost-effective and environmentally friendly rental services.
Last January the TRSA asked me to co-facilitate a roundtable for general managers in the linen and uniform industry, with a focus on their recruiting of maintenance professionals. In preparation for this online event, I endeavored to learn about the industry. Prior to my education, my assumption was the industrial
Researching on the TRSA web site (www.trsa.org) and with conversation with Ken Koepper (director of member and industry relations) showed how this industr y is just as technologically advanced as any manufacturing facility. The equipment has sophisticated control systems that process and sor t the linens and uniforms through barcodes and RFID labels that interface with high end tracking systems.
Most people envision a “washing machine” as a unit comparable in size to a home washer. however, the smallest such machine used for regular laundry work by a linen and uniform service accommodates loads over 20 times the size of the largest high-tech home unit. These more closely resemble manufacturing facilities than laundromats and operate with increasing proficiency with great attention towards workplace safety practices.
The economies of such massive equipment result in high efficiency and add sustainability by using up to 250 per cent less water and 160 per cent less energy per pound of laundry than consumer s’ machines. Such central laundering also relieves workers of the burden of washing their own work clothes, which prevents carrying contaminants from their workplaces to their homes, a plus for hygiene and disease prevention.
Millions of Canadians and Americans benefit each day from clean, comfortable, professionally laundered linens, uniforms, and other textiles, and other products for businesses from the linen, uniform, and facility services companies. Industrial uniforms are supplied to an estimated 20 million workers in all industries; linens and towels are provided to hundreds of thousands of facilities. Most customers receive deliveries at least weekly from a laundry or service center as the industry deploys a fleet of more than 25,000 trucks.
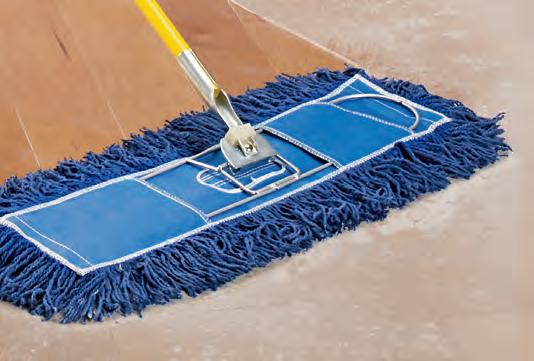
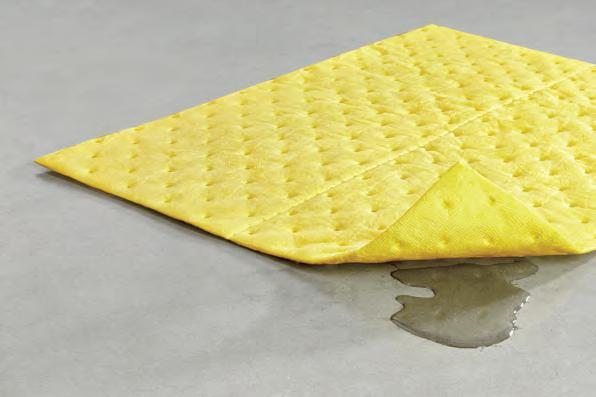
From a production and maintenance perspective linen and unifor m services measure the same key performance indicators (KPIs) as any other manufacturing and processing companies. KPIs such as machine availability, equipment breakdowns and stoppages. They monitor work order compliance, analyze failures, and employ maintenance best practices and quality control.
My research left me with a new understanding and respect for this industry.
The online event included general managers from several dozen textile, linen, and uniform facilities across the Canada and the USA. We discussed the challenges within the industry of attracting new skilled people and those looking to switch careers into the linen, uniform, and services industry.
Here are some of the more significant benefits when considering a career in this fast-moving highly technical industry.
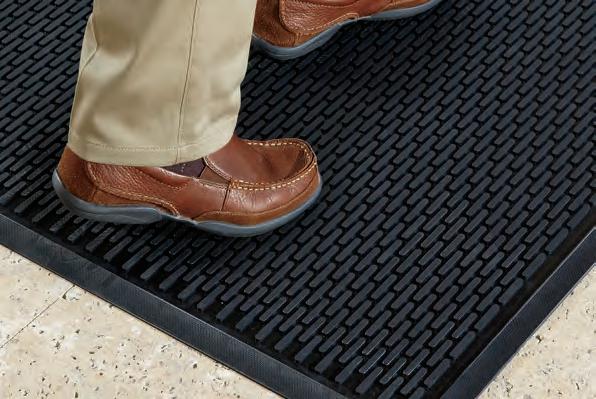
• It has technology to challenge technicians and maintenance managers’ skills and abilities.
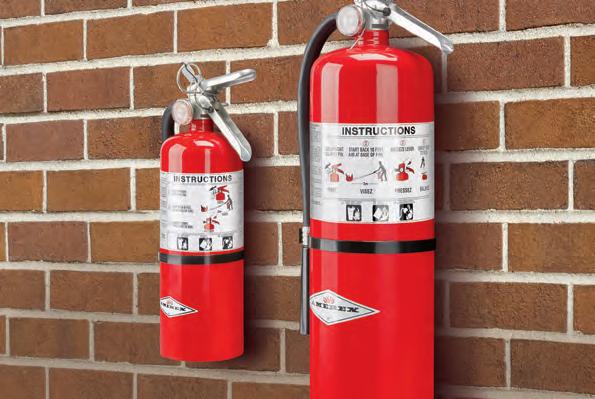
• Projects where engineers can sink their teeth into numerous projects and use their education and knowledge to improve equipment and processes.
• Room for career advancement for those who are so inclined.
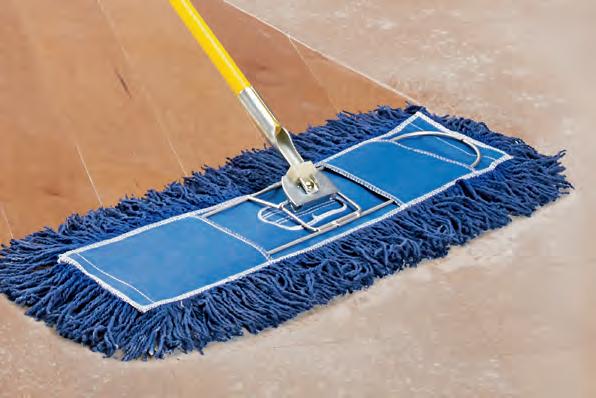
• Hour s of work are flexible as many facilities run one or two shifts 5 days a week, which is a great advantage for growing families. Identifying, recruiting, and retaining maintenance personnel, par ticularly skilled, knowledgeable managers, is one of the industr y’s most troubling issues. Through an internal task force working on certificate programs and other assessment tools, TRSA is assisting companies in developing the skill sets and improving retention of these valuable employees.
In short, this industry provides maintenance and training oppor tunities for highly skilled technicians in a secure career in both the USA and Canada. They provide extensive professional development though TRSA and their training and apprenticeship programs.
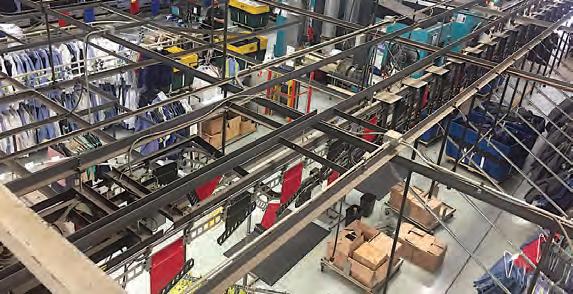
In the end, I came away with a whole new respect for the industry and the people collecting and delivering linens, and unifor ms at manufacturing and processing plants. The technology and processes are certainly impressive.
Peter Phillips is the owner of Trailwalk Holdings Ltd., a Nova Scotia-based maintenance consulting and training company. Peter has over 40 years of industrial maintenance experience. He travels throughout North America working with maintenance departments and speaking at conferences. Reach him at 902-798-3601 or peter@trailwalk.ca.