
10 minute read
Greening maintenance operations
BY MARIO CYWINSKI
Keeping engines in tune and fuel system adjustments in spec helps minimize fuel consumption. In the case of variable frequency (speed) drives, the drive control apparatus must be kept free of dust and dirt. Electrical panels and cabinets often have cooling fans and air filters - they must be clear and able to pass air for correct cooling to keep electrical devices operating with their design ranges.
Climate change is on everyone’s minds today, and the maintenance industry is no exception. From reducing leaks to make sure environmentally unfriendly substances don’t escape, to using AI, drones, and other technology to keep an eye on hand to get assets, or replacing current assets for a more efficient version; maintenance managers have their hands full navigating the new reality.
We reached out to experts come from utilities, manufacturing, analytics, asset management, and consultant ser vices, to get a complete look at how greening maintenance operations is being done. They include Susan Lubell, principal consultant, Steppe Consulting Inc.; Erika Mazza, Acting Project Manager, Systems Policies Process Group - Works Department, The Regional Municipality of Durham; James Reyes-Picknell president and principal consultant, Conscious Asset; Stan Shantz, Co-founder and vice-president,
Perspect Analytics Inc.; and Hugues Therrien, Head of ABB Motion Services, Canada.
What effect do maintenance activities have on the environment?
LUBELL: Predictive maintenance activities that detect fug itive emissions are a key to detecting and repairing leaks quickly, thus avoiding unwanted emissions. In the case of instr ument air leaks, detection and repair of leaks can result in reduced requirements to compress the air, thus a reduced energy demand to produce the compressed air. It may also mean that existing compression systems are adequately sized to meet plant operating demands.
Predictive or condition-based maintenance that is performed while the equipment or asset is still running minimizes the number of times that assets go through star t-stop cycles, thus avoiding any emissions or off-spec product that might occur during this transition in operating state.
Design and component choices, like installing low emission valve packing, further minimize fugitive emissions.
MAZZA: Maintenance activities are executed during the longer phase of the asset life cycle so they can either have a positive or negative impact on the environment. It comes down to how harmful are the consumables we use; how frequent the maintenance activities are done and the way we disposed of the waste generated from these activities. Maintenance activities also impact the efficiency of the asset, hence the environment footprint they draw.
REYES-PICKNELL: Equipment operating at peak efficiency consumes the least energy. Well maintained equipment can be operated at that point, provided it is suited to the role that operations use it for. Energy conversion is degraded if the motor operates too hot, so maintaining the motor’s cooling fins helps in keeping energy consumption optimized.
Good proa ctive condition monitoring using ultrasound, thermal imaging and vibration analysis can spot equipment that is deteriorating, find leaks, identify electrical faults while they are still minor. Acting on any defect while it is still early in its degradation state can help in terms of energy efficiency.
When equipment must be replaced, a like for like replacement may miss opportunities for applying technolog ical advances that help in energy conservation, consider the latest technologies that are available and the benefits they may have.
SHANTZ: Maintenance activities can have either a positive or negative impact on the environment. For example, a person is assigned to change out a defective 100hp electric motor. The motor is driving a gearbox through a multi-V belt drive system. The person feels pressure to complete the repair quickly. They install the electric motor and make a business decision to avoid taking the time to align the belts properly. They will generate a new work order to go back and properly align the belts. However, they are called to an urgent job before developing the new work order and forget to generate it.
Misalignment can increase the energy draw of the electric motor by up to 10 per cent. That means you must purchase 10 per cent more electricity, which means additional carbon emissions because of a business decision not to take 30 minutes to align the motor correctly. Multiply this a plethora of electric motors at a facility, and you see the impact maintenance activities have on the environment.
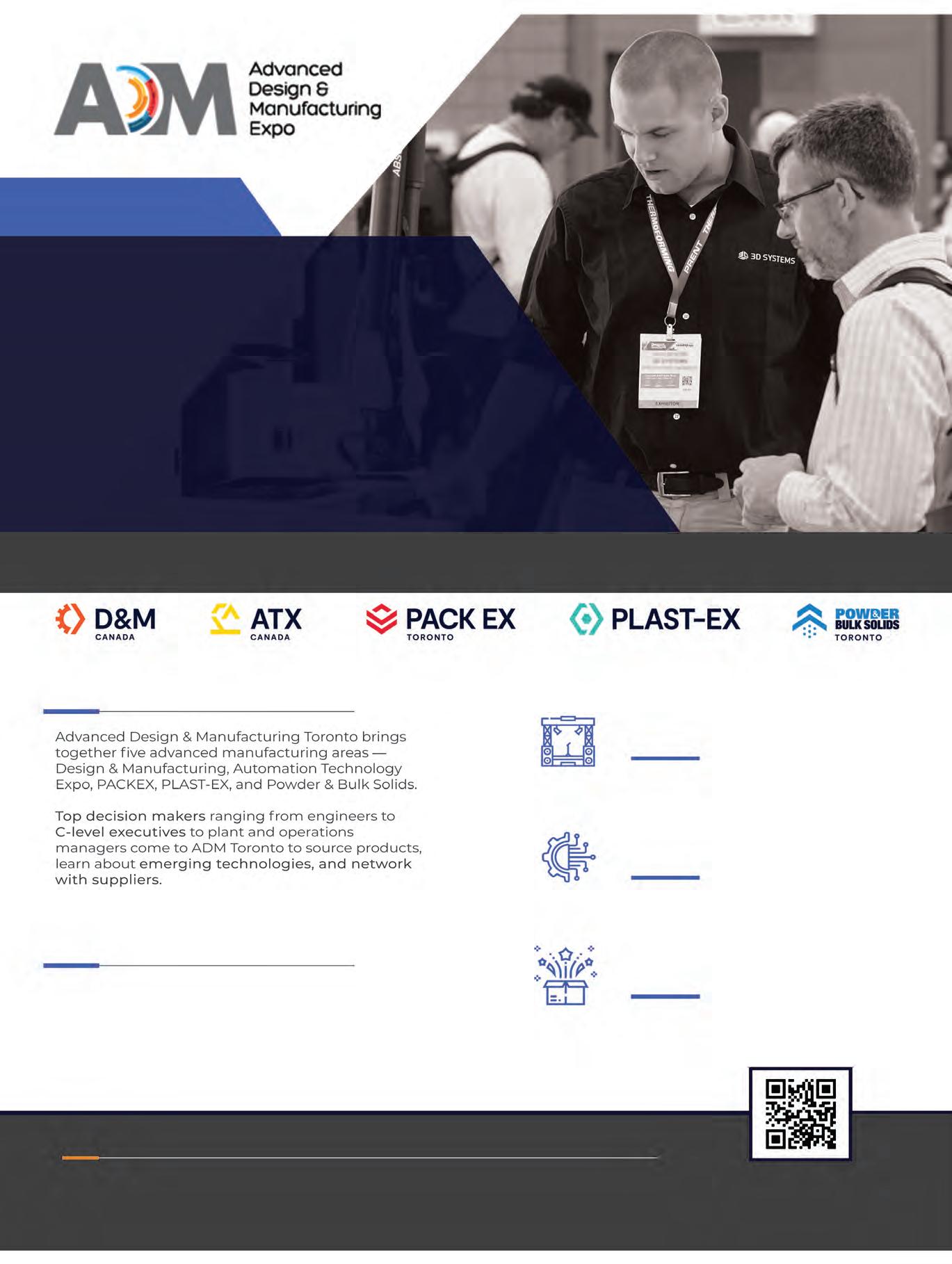
THERRIEN: Maintenance can extend the lifecycle of equipment, which means the turnover and disposal of components is less frequent. With planned rather than unplanned maintenance this can be even more effective, avoiding downtime, reducing wasted resources, and ensuring predictability. The right level of performance of equipment can save energy and CO2 through optimised equipment performance and the avoidance of unplanned interventions. For example, significant improvements in energy saving are possible with the correct set up of a motor and drive combination, less physical interventions mean less travel and good maintenance can avoid early replacement and disposal of components.
How do you see the maintenance world changing to become more environmentally friendly?
MAZZA: Innovation on new consumables that are ecofriendly are key to reducing waste, AI predicting with more accuracy preventive maintenance models that will reduce the number of interventions but keeping the asset reliable, industry eco responsibility being now embedded on the strategic asset management plans that then cascade down to how eco responsible we execute out maintenance activities. These are changing the way we do business and improve positive effects of the maintenance activities.
REYES-PICKNELL: Our first step is to recognize our role in protecting the environment around us. We need to keep “stuff” contained where it belongs and address breaches of that containment quickly if it occurs. Survey to identify possible locations where maintenance may not have been “set up” originally and include it on inspection routes. Inspections may be enhanced using specialized monitoring equipment or using drones that are set up to read signals from “near field” devices or use vision systems to spot anomalies such as leaks, ultrasound to detect leaks, infra-red to identify defects in thermal insulation or possible electrical device problems in hard to access areas.
Specialized robotics (autonomous or remote operated) may take over some hazardous functions in shop environments or handle remote activities in difficult or dangerous locations. Robots don’t get tired and make mistakes, so if they are programmed correctly, some repetitive jobs could be removed from the human maintainer and placed in the “hands” of the robot, eliminating human error risk.
THERRIEN: Products themselves are becoming more reliable with lower component counts and less frequent maintenance required. This is moving in the right direction to help the environment. Maintaining each asset’s reliability is a part of the equation, but expertise should be focussed on maintaining the best efficiency standards of a fleet of assets. It may benefit the application with replacement and upgrades to take advantage of new technology to deliver better environmental performance. Also, circularity is a topic that is important in the maintenance industry now. Recycling and re-use of equipment and tools are examples. How to extend the lifecycle while improving performance is a key question to address.
LUBELL: Greater use of compressed air tools; focus on detecting and repairing sources of fugitive emissions and air leaks; more options for recycling of used components. Also, solar powered battery back-ups in more remote locations; and installation of wind turbines to generate electricity at remote mining sites. Finally, an increased demand for maintenance skilled trades with competency in maintaining renewable energy production equipment such as wind turbines, solar panels, or hydroelectric power.
What are some steps that have been taken recently that are making maintenance more sustainable?
SHANTZ: There are some simple steps manufacturers can take to be more sustainable. Instead of changing the oil regularly, r un the oil through a “kidney” machine, change the filters and top up if required. Test the oil through an oil analysis to determine if it needs to be changed or if you can add additives to bring the oil back to OEM standards. This approach uses less oil and minimizes spills, which can drive environmental sustainability.
Focus trades and technicians on quality of workmanship. Help them understand how their daily decisions affect the environment. Quality of workmanship standards helps floor employees to make the correct business decision to balance production throughput and environmental sustainability. Marry the equipment reliability program to the corporate environmental sustainability initiative. This enables the ability to properly manage the corporate environmental risks.
THERRIEN: The real opportunity going forwards with sustainable maintenance practices comes from digitalisation. Being able to monitor, in real time an asset’s performance both from a reliability perspective but also monitoring its efficiency will help. Going further, with better analytics and AI technology, maintenance will be more predictable and help operators to make better manual and automated decisions for their asset performance and application.
MAZZA: In Canada some tiers of government offer incentives for power consumption reductions that could be a direct result of an efficient asset perfor mance. Sustainability is becoming a cornerstone for competitiveness in the industry, cascading in reviewing maintenance strategies to support the achievement of corporate goals.
What can facilities do to be more eco-friendly, short and long term?
REYES-PICKNELL: Short term - maintain to high standards. Upgrade to improve energy efficiency, waste handling, using newer technolog ies as the need to replace older systems and equipment arises. It’s gradual and piece-meal, but it can eventually result in a big change. Survey buildings for thermal, water and air leaks - correct or upgrade as needed. Long term - consider programs aimed at energy efficiency, improved air quality, balancing of air distribution and exhaust systems.
SHANTZ: Short term, focus on setting up measures and implementing simple CI initiatives. Longer term, implement measures that can track and quantify asset management and maintenance operations’ impact on the corporate environmental sustainability initiative. Then focus on linking employee behaviour and technology to bring asset management and maintenance operations into sink with the corporate environmental sustainability initiative.
THERRIEN: About 45 per cent of the world’s electricity is used to power electric motors in building and industrial applications. The first step is to identify the performance of assets today. Which elements of a plant have the potential for efficiency improvements? There are a lot of low hanging fruits that can be targeted with the right focus. This is the starting point, and the potential can then be identified. It then comes down to planning the activities for improvement and prioritising the opportunities with the biggest impact.
LUBELL: Considering increased use of electric vehicles when the travel distances are within range and charg ing facilities exist or are being built. Locations of new or expanded production facilities near public transit or providing company transit like shuttle busses to encourage staff to carpool.
Ongoing training of maintenance workers to be able to maintain the newer equipment. For example, different skills and techniques are required to maintain electric battery vs diesel engine city busses or mining equipment, or to service solar panels and wind turbines.
MAZZA: Applying for incentive programs can help drive the change in the short term. Starting to be green not just on the strategic level but on the practical level, on all aspects of the work environment, from going paperless to highly efficient toilets, it needs to become a culture of working green.
What are the greenest assets, and which need updating the most?
THERRIEN: Investments to stay ahead, improve sustainability and manage reliability will always be continuous improvement topics. The digital options available to manage this will help along this journey. However, for plant assets there are things to consider. Firstly, the assets themselves and how investing in the most efficient equipment can contr ibute to the overall green goals.
Roughly 75 per cent of industrial motors in operation run on pumps, fans and compressor s, a category of machinery that is highly susceptible to major efficiency improvements. Secondly, the application of the assets. Meaning installation and upgrades but also how equipment can work together to meet the plant specification and perform efficiently. For example, a simple motor application, operating a pump or fan. Motor performance has evolved over time and many were oversized in industry. Replacing the motor can save energy if done with the right technology and applied properly. The IE4 motor standard specifies energy losses at 15 per cent lower than the IE3 variant. Add a variable speed drive and optimizing the configuration could increase energy efficiency even further. Finally having a maintenance strategy to ensure the perfor mance continues or is improved upon for many years should be considered.
MAZZA: There are many green assets in the market, starting with facilities type of assets built from recycled materials, biodegradable, energy efficient and long-lasting life c ycle. We need to improve the way we dispose them after we are done with them, the type of consumable they required during their maintenance and operation phase of their life cycle.
SHANTZ: Municipalities and large cities are ahead of the manufacturing sector in environmental sustainability because they have no choice. The changes in weather due to climate change directly affect the life expectancy of their assets and the safety of citizens, who fund them through taxes.
How can asset efficiency make a facility more sustainable?
LUBELL: Reduced energy demand through better insulation, modernizing HVAC systems and keeping them properly maintained, window design, lighting choices.
MAZZA: Efficiency is directly connected to the number of resources require to maintenance and operate any asset, the less and greener resources are used, the more eco-sustainable the overall performance of the organization is.

REYES-PICKNELL: Efficiency translates to lower cost and that makes a facility more profitable. Profitable assets tend to last longer than those that are not. By making the best use of energy through efficient systems and equipment we reduce the facilities carbon footpr int and make the building more “attractive” to those of us who are concerned with the environment.
SHANTZ: More efficient the processes - human and technology - the more sustainably and profitable the organization is.
THERRIEN: Sustainability and maintenance aren’t either/or questions, they go together. With regulations driving the green agenda there is a lot of work to do to come into line. The performance and availability of a plant is important to stay competitive and operate successfully. Agendas should be joined up and are not separate topics. For example, a conventional pumping application has a system efficiency of around 28 per cent and with the right assets, application and support can be improved to over 80 per cent. Sustainability, efficiency, and circularity should be integral considerations when developing maintenance strategies, which in turn should go beyond reliability alone. Managing and driving asset performance can save energy, CO2, and money, and will ensure the best performance of the plant to be competitive. The key is having the right plan with the right execution.