
4 minute read
Principles of planning and scheduling
Not only do we spend excessive time creating and forever adjusting a detailed weekly schedule, but we also usually underload it to allow for reactive work.
Instead, the purpose of scheduling is to help us complete more work than normal. A simple list of work from the ready backlog serves to focus the crew supervisor to complete extra work. We do not need to schedule each day a week ahead. We must also fully load the schedule to match the available craft hours for the next week to defeat Parkinson’s Law. “The amount of work assigned expands to fill the time available.”
The following six principles of planning and six principles of scheduling show how to implement these programs effectively.
Principles of planning
Unfortunately, the ranking also declared planning and scheduling to be the most difficult programs to master. Planning and scheduling can frustrate almost everyone. However, because this frustration comes from simply misunderstanding the purpose of planning and scheduling, we can tweak our thinking and succeed. We can apply easy principles to harness phenomenal power in completing more proactive work and executing better quality work for all jobs.
“Planning” sounds like telling craftspersons how to do their jobs, and have all spare parts on hand. Most craftspersons resent someone telling them how to work. They pick apart every job plan and complain when any part is not ready.
Instead, the purpose of planning is to have better plans over the years. Planners simply give head starts and need craftsperson feedback to make the head starts better the next time.
Essentially, we are applying the continuous improvement of the Deming Cycle. Tell craftspersons that we expect them to exercise their judgment and skill.
“Scheduling” sounds like a master grid for the next week to set expectations and gain good schedule compliance. However, real-life maintenance has a terrific amount of daily churn: we have both slow and fast craftspersons; we do not know exactly what repairs are needed, and we do not know what reactive work will suddenly appear.
The first three principles of planning are (1) protecting planners, (2) focusing on future work, and (3) saving job plans at the asset level. Management must actively protect planners from all clerical work, being grabbed as extra craftspersons, and being put on various projects and committees. Planners must focus on giving head start plans for nearly all the incoming work requests. They must not help jobs-in-progress to the exclusion of planning all the incoming requests. Also, to complete the improvement cycle, planners must create the job plans for specific assets. Craftspersons know how to work on a generic pump, valve, or whistle. The planners need to plan for that one specific pump or valve. What is special about that one asset that the craftsperson wants to remember next time?
The next two principles of planning, (4) the labour estimate and (5) the level of plan detail, keep the planners from becoming bogged down on specific plans. Do not become overly concerned with the accuracy of the labour hours. A decent judgment on the part of the planner is sufficient to help assign and schedule work. Make the plan as detailed as possible, subject to the constraint that we must plan all the work.
Super-detailed plans help a new person and can be a reference for a senior person, but we cannot start there. Our aim is to put more detail in the plans over the years as we have time. Do not let the labour estimating and detail-setting keep planners from getting most of the work through the Deming Cycle of continuous improvement.
The final principle of planning concerns (6) wrench time. Studies show that typical workforces only spend about 35 per cent of their available time moving jobs ahead. The other time is spent getting parts and tools, in crew meetings, in breaks, and even travelling around the site.
Proper planning and scheduling should advance wrench time to about 55 per cent, a 57 per cent boost (55/35 = 1.57). Meaning if we are completing 100 work orders per week, we could be completing 157 work orders. This bump answers the management question, “how can we complete mo re proactive work when we have our hands full of reactive work?” This principle deals with the measuring itself: Measuring wrench time is not necessary, but if we do, we should use a statistically valid method. Simply following people around or asking them to report their own wrench time does not give best results.
Principles of scheduling
The six principles of scheduling are that we need (1) planned work, (2) a credible priority system, (3) the week as a timeframe, (4) fully loaded schedules, (5) supervisors doing daily schedules, and (6) schedule compliance between 40 per cent and 90 per cent. We need planned jobs for the time estimates. We also need a credible priority system to facilitate breaking the schedule today or this week and want to know what can wait until next week or longer. The single week is the right timeframe for productivity.
A single week is long enough to allow bundling of common area work and short enough to avoid shifting plant priorities. In addition, the schedule needs only be a simple batch or list of work. Then, we must load the schedule to 100 per cent of the next week’s labour capacity to defeat Parkinson’s Law. We simply leave the daily scheduling to the crew supervisor to handle as the week unfolds.
We must also properly understand schedule compliance. Our objective is not scheduling compliance itself. Our objective is to complete more work than normal. In practice, scores below 40 per cent indicate supervisors are ignoring the schedule and we fail to get the pop in productivity. Scores above 90 per cent indicate we are not loading the schedule enough to defeat Parkinson’s Law and we fail to get the pop in productivity.
Understand the purpose and apply the fundamental principles of proper planning and scheduling for a competitive edge. The phenomenal power of proper planning and scheduling shows up almost immediately in completing about 50 per cent more work than normal. Since we always manage to complete reactive work, new work is proactive work we could never complete. Work backlogs drop, which gives labour to staff more proactive programs. Low backlogs also encourage operations to start reporting more little problems that head off reactive events. Equally phenomenal, but more gradual and thus harder to perceive, is the working more intelligently from the growth of improved job plans applying lessons of the past across our workforce.
Doc Palmer, PE, MBA, CMRP is the author of McGraw-Hill’s Maintenance Planning and Scheduling Handbook and helps companies worldwide with planning and scheduling success. For more information about online help and currently scheduled public workshops including Alberta and Ontario visit www. palmerplanning.com or e-mail Doc at docpalmer@ palmerplanning.com.
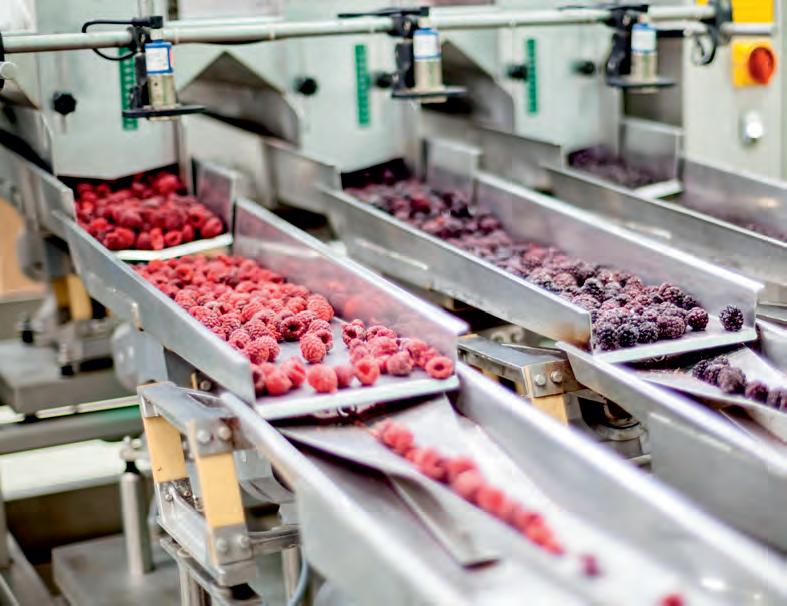