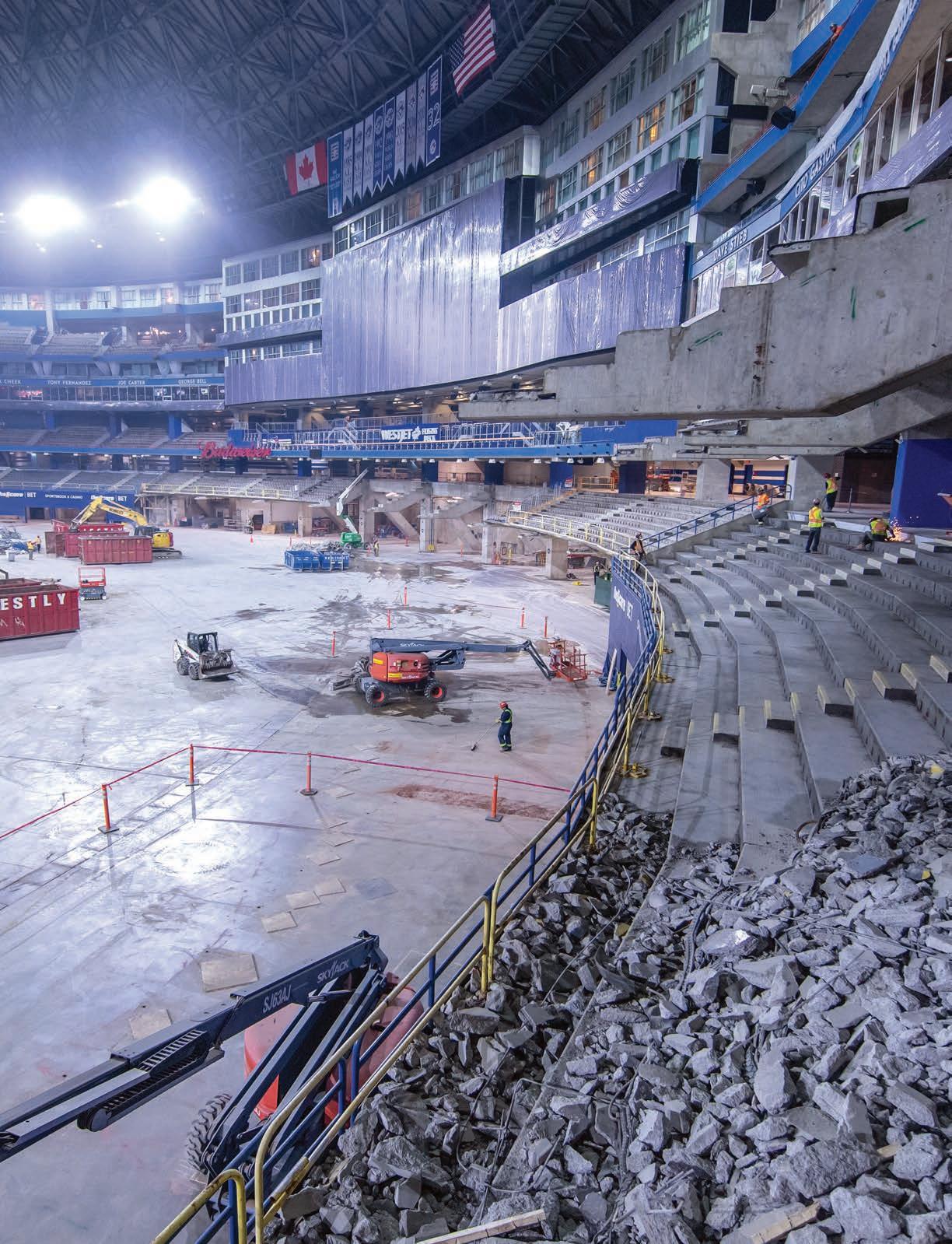
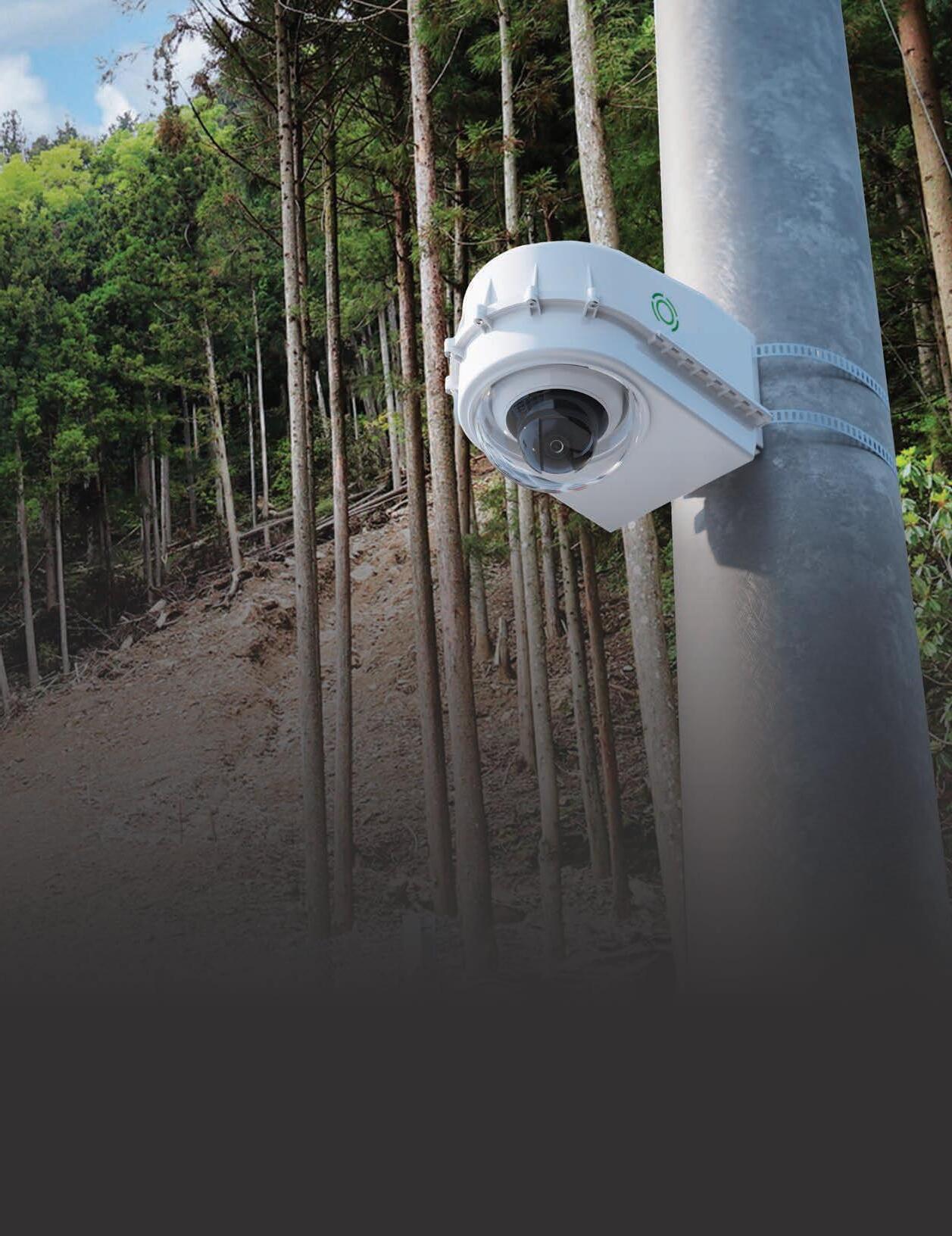
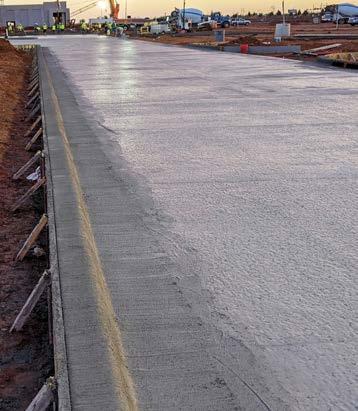
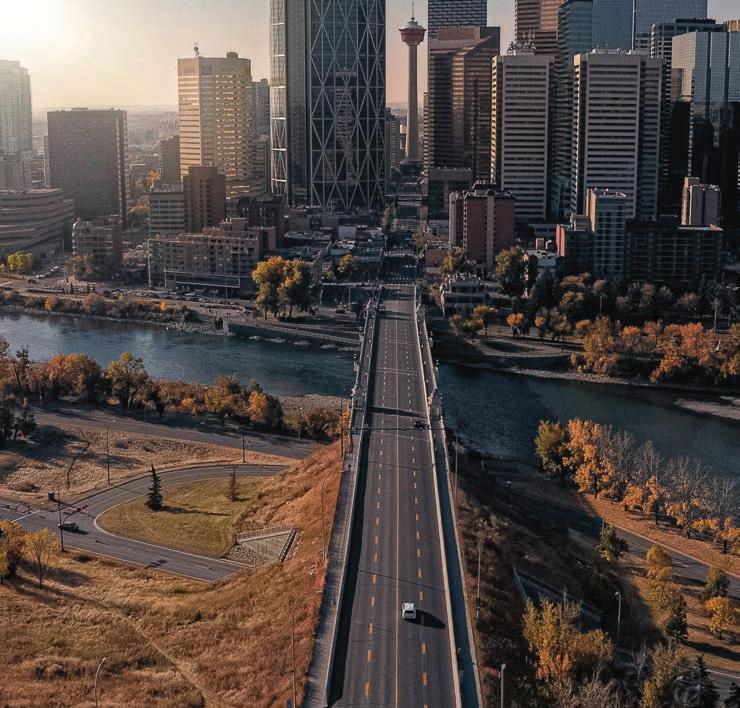
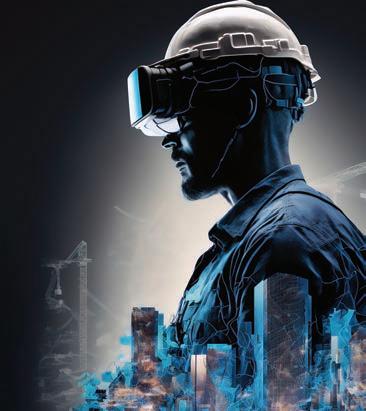
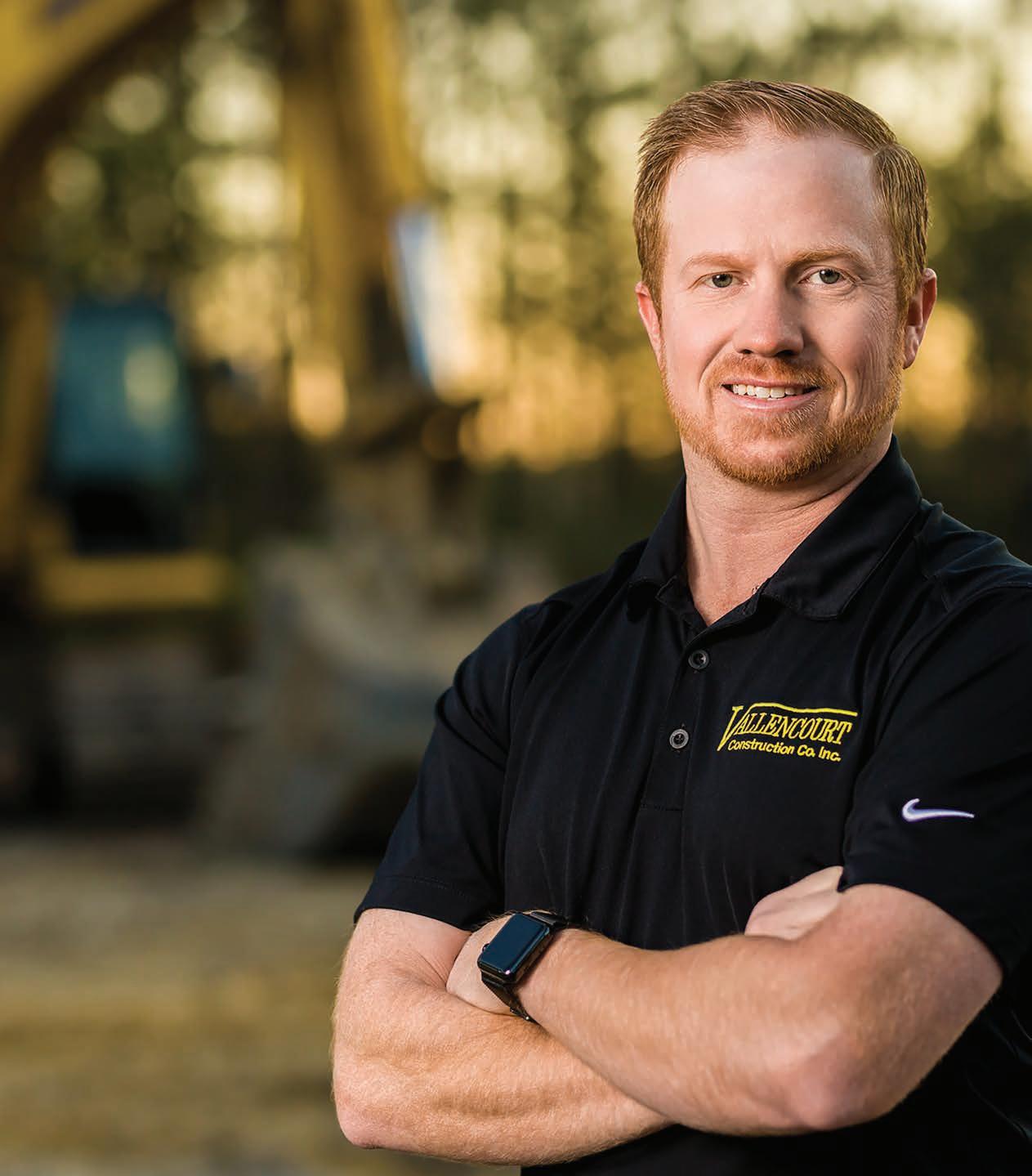

The past few months have made for busy times. Shows and events were being held ahead of seasonal construction work; federal and provincial governments were making their budget releases and announcements: and all of us have been trying to navigate uncertain economic times, both at home and on the job. As I made my way through some of the trade shows and conferences on my travel agenda, a few themes stood out.
On the economic front, there’s an interesting mix of concern and optimism happening. With the rapid rise to lending rates, the market is still adjusting to the changes, and that has created a slowdown in some segments of the construction world. While mainly impacting the residential side, rising costs and a tighter lending market are increasing worries about project cancellation or delays in all sectors.
But immigration is up, significantly, and several provinces have announced considerable infrastructure plans and spending in their budgets, all of which should help drive construction activities and keep backlogs healthy. As Tooey Courtemanche, CEO of Procore said at last month’s Canadian Construction Association conference, companies are busy.
Of course, busy has not made life easier for contractors in need of skilled workers. Labour continues to be a challenge, although provincial negotiations that have resulted in more say in immigration controls should help.
Here in Ontario, the provincial and federal governments recently announced a structure to double the number of economic immigrants the province selects by 2025. Manitoba’s provincial nominee agreement is also being adjusted. It will see more than 3,000 additional spots in 2023 over its 2022 allocation, and Alberta is expected to have an additional thousand or so spots in its program as well. These moves will allow provinces to better align the selection process to match more immediate labour needs, including those in the construction sector.
Technology is also stepping up to help
companies do more with either the same or fewer people on their sites. Our recently held Cameras in Construction webinar took a look at some of the imaging technologies that can be used to help make contractors more efficient on their projects. From drones to apps that automate reporting, tools are available to help reduce time spent on planning, tracking and paperwork.
Being able to walk through a jobsite to create a progress report via a camera mounted on a hardhat, or to map a site in minutes rather than hours or days, are developments that can have a considerable impact on the speed at which tasks can be completed, and it’s becoming easier than ever to dive into the digital stream.
Automation was also front and centre at the CONEXPO show, held last month in Las Vegas, as several heavy equipment manufacturers brought concept machiness to this once-every-three-years show that will influence equipment as well as jobsites in the years to come.
Battery technology is top of mind for equipment manufacturers as the move to go carbon-free is well underway and was definitely on display at the show. It was interesting to note that electric vehicles and machinery were not the only green options gaining traction at this year’s show, however. Several manufacturers put hydrogen-powered equipment on display, which might be a solution for contractors whose work tends to take them away from the electrical infrastructure necessary to recharge battery-powered machines.
Now that spring has hit, sites in need of warmer weather are going to be getting busy, but don’t forget to set aside a few minutes to fill out your Canada’s Top Contractors survey for 2023. It’s available at www.on-sitemag.com and will inform our annual look at the leading general contractors in Canada, available in the June edition of On-Site
Until next time, stay safe and do great work.
Adam Freill / Editor afreill@annexbusinessmedia.comOn wireless platforms for next generation construction sites:
“This new way of working means jobsites must be connected to the internet. That can be hard to achieve when infrastructure is yet to be built, but Wireless Wide Area Networks (WWANs) and the latest generation of cellular technology, 5G, fit the bill to help move massive amounts of data between many people and devices throughout the construction lifecycle.”
On the use of telematics as an essential source of enterprise data:
“Equipment managers are getting requests for data from parts of the organization that until recently had little interest in what the equipment was doing… It’s not just executives that need the numbers, however. Data can be a powerful tool for encouraging field personnel to pay more attention to their own impact on the environmental footprint.”
On the impact of broad-based inflation on the insurance industry, and customers in the construction industry:
“When it comes to property and casualty insurance, especially within the construction sector, global price increases have been substantial with prices going up 25 per cent for each of the past four years. These increases have hit construction stakeholders in two ways: first on their practice, or annual, insurance policies; and second, and perhaps more expensively, on their project-specific insurance policies.”
On change and amendment provisions of contracts:
“… depending on the circumstances of the contract at issue, it is always a possibility that a contractor who carries out change work without proper authorization risks being denied payment for the unauthorized work. Accordingly, it is important that contractors understand the change and amendment provisions of their contracts and follow the required processes under those provisions prior to undertaking any work outside of the base scope of their contract.”
www.on-sitemag.com
READER SERVICE
Print and digital subscription inquiries or changes, please contact Angelita Potal
Email: apotal@annexbusinessmedia.com
Tel: (416) 510-5113
Fax: (416) 510-6875
Mail: 111 Gordon Baker Road, Suite 400, Toronto, ON M2H 3R1
PUBLISHER | Peter Leonard (416) 510-6847 pLeonard@on-sitemag.com
EDITOR | Adam Freill (416) 510-6821 afreill@annexbusinessmedia.com
MEDIA DESIGNER | Lisa Zambri lzambri@annexbusinessmedia.com
ASSOCIATE PUBLISHER | David Skene (416) 510-6884 dskene@on-sitemag.com
ACCOUNT COORDINATOR | Kim Rossiter (416) 510-6794 krossiter@on-sitemag.com
AUDIENCE DEVELOPMENT MANAGER | Urszula Grzyb (416) 510-5180 ugrzyb@annexbusinessmedia.com
PRESIDENT/COO | Scott Jamieson sjamieson@annexbusinessmedia.com
Established in 1957, On-Site is published by Annex Business Media 111 Gordon Baker Road, Suite 400, Toronto, ON M2H 3R1 Publications Mail Agreement No. 40065710
ISSN: 1910-118X (Print)
ISSN 2371-8544 (Online)
SUBSCRIPTION RATES Canada $49.50 per year, United States $113.00 per year, Other foreign $136.50, Single Copy Canada $13.50. On-Site is published 7 times per year except for occasional combined, expanded or premium issues, which count as two subscription issues. Occasionally, On-Site will mail information on behalf of industry-related groups whose products and services we believe may be of interest to you. If you prefer not to receive this information, please contact our circulation department in any of the four ways listed above.
Annex Business Media Privacy Officer privacy@annexbusinessmedia.com
Tel: 800-668-2374
Content copyright ©2023 by Annex Business Media may not be reprinted without permission.
On-Site receives unsolicited materials (including letters to the editor, press releases, promotional items and images) from time to time. On-Site, its affiliates and assignees may use, reproduce, publish, re-publish, distribute, store and archive such unsolicited submissions in whole or in part in any form or medium whatsoever, without compensation of any sort.
DISCLAIMER This publication is for informational purposes only The content and “expert” advice presented are not intended as a substitute for informed professional engineering advice. You should not act on information contained in this publication without seeking specific advice from qualified engineering professionals.
The initial designs have been released for the Dani Reiss Modern and Contemporary Gallery at the Art Gallery of Ontario (AGO), a massive expansion project set to increase the museum’s gallery space by 40,000 square feet. The downtown Toronto project will increase the AGO’s total available space to display art by 30 per cent adding at least 13 new galleries across five floors. The design of the addition has been the work of architectural partners Diamond Schmitt, Selldorf Architects and Two Row Architect.
The project is being made possible through a lead gift of $35 million from Dani Reiss, the chairman and CEO of Canada Goose. The Dani Reiss Modern and Contemporary Gallery will sit one story above the AGO’s existing loading dock, nestled between the AGO and OCAD University.
The addition will feature an all-electric mechanical plant that uses no operational carbon and creates no emissions. The AGO plans to seek CAGBC Zero Carbon Operating Building certification,
Maple Reinders has been awarded a $204.8-million contract for the construction of the Royal B.C. Museum (RBCM) Collections and Research Building in Colwood, B.C., Lekwungen Territory. The procurement and partnering process was conducted by the Province of British Columbia, Royal B.C. Museum, and Esquimalt and Songhees Nations.
The new 15,200-square-metre (163,611-square-foot) facility will be an advanced, sustainable, and culturally sensitive building that will serve as a community and learning hub for the region. Once complete, the new facility will house the museum’s collections, research departments, learning spaces and the B.C. Archives. Plans call for extensive use of mass timber construction, and that the building be constructed to meet CleanBC energy efficiency standards, and be LEED Gold Certified.
“We are humbled to have been chosen to design and construct this important cultural facility,” said Reuben Scholtens, vice-president of major projects at the Maple Reinders Group. “Our team is committed to delivering a world-class facility that will not only serve as a community and learning hub but will reflect and pay respect to the deep cultural connections the local Indigenous peoples have to the place where the facility will stand.”
Construction on the project is set to begin this summer, with completion expected in 2026.
which would make it one of a very small number of museum spaces to accomplish this. It will also be built to Passive House standards, for maximum heating and cooling efficiency.
Construction is expected to commence in 2024, with EllisDon serving as the project construction manager.
The Ontario government has proposed several new washroom initiatives that focus on facilities on construction sites, saying the moves aim to make site washrooms private, clean and safe.
Citing that only one in 10 of the nearly 600,000 construction workers in Ontario are women, the government says proposed changes like a requirement to have at least one women’s-only washroom on jobsites and properly fitting equipment such as uniforms, boots and safety harnesses, will make the skilled trades more accessible to women.
“We applaud measures that make all job sites more accessible and safer for all, including women,” said Andrew Regnerus, Ontario construction coordinator at CLAC. “Given the trades shortage, all barriers to entry and retention must be eliminated and this is an important step in the right direction.”
If passed, the legislation would require washrooms on construction sites to be private and completely enclosed, and have adequate lighting and hand sanitizer (where running water is not reasonably possible). Additionally, the government is doubling the
number of toilets on most jobsites.
These changes are part of a larger package that expands on the actions introduced in the Working for Workers Acts, 2021 and 2022. If approved and filed, the proposed regulatory amendments would come into force on July 1, 2023.
On the jobsite you need a truck that’s tough, safe, and smart. So, we built the new Volvo VHD to be the best-looking, most rugged vocational vehicle in the industry, packed with innovative ideas like Volvo Active Driver Assist and the revolutionary Volvo Dynamic Steering. Your toughest jobs just got easier. Learn more at volvotrucks.ca/en-ca/trucks/vhd/
Investment in building construction increased 1.5 per cent in January, landing at $20.4 billion, reports Statistics Canada. All components posted gains for the month. The residential sector was up 1.9 per cent, reaching $14.9 billion, while the non-residential sector was up a half-per-cent, hitting $5.6 billion. The jump in residential building construction was a welcomed rebound following the four consecutive monthly declines recorded to end 2022.
The non-residential construction generated small monthly gains but continued to climb in January. Industrial construction investment rose 1.1 per cent on the month, reaching $1.1 billion, a gain of 25 per cent over January of 2022, and the 14th consecutive monthly increase.
Commercial construction edged up 0.1 per cent to sit at $3.1 billion. And institutional construction investment was up 0.7 per cent as it reached $1.4 billion.
20,054,000
5.0%
1,609,400
The number of people working in construction was little changed in February, following two consecutive monthly gains. The sector actually lost 1,500 positions for the month, reports Statistics Canada, after gaining 27,000 in December and 16,000 in January.
Overall, Canadian employment held steady in February, gaining roughly 22,000 positions and maintaining an unemployment rate of five per cent, just shy of the record-low 4.9 per cent observed in June and July of 2022.
Employment has trended upward since September of 2022. In February, there were almost 350,000 more employed persons in Canada than in August of 2022.
The monthly total value of building permits in Canada decreased four per cent in January, coming in at $9.8 billion, reports Statistics Canada. Eight provinces had contractions in January, with the multi-residential sector in British Columbia contributing significantly to the national fall. Overall, the residential sector declined 6.6 per cent, reporting in at $6.1 billion for the month. Conversely, the non-residential sector was relatively stable thanks to a 5.4 per cent rise in commercial permits. Cumulatively, the industrial, commercial and institutional segments managed a modest increase of 0.7 per cent to $3.7 billion, although the commercial gains masked red ink in the other two components.
The downward trend in multi-family home permits continued as construction intentions declined 8.3 per cent for that segment in January.
Gains in the non-residential sector were on the strength of the commercial component, which rose 5.4 per cent. Ontario was leading the charge with a rise of almost 23 per cent. This was the second consecutive monthly increase.
Permits in the industrial component were off almost four per cent in January, and intentions in the institutional sector decreased almost six per cent.
RESIDENTIAL -6.6% Multi-Family -8.3%
INDUSTRIAL -3.9% INSTITUTIONAL -5.9%
COMMERCIAL +5.4%
Construction Association. He explained that the competition for workers from other countries is global, and Canada’s immigration system is often viewed as difficult to navigate, with challenges that work against the construction industry’s labour needs. His advice: “Give the provinces more say in the who they are bringing in.”
“It is our moral responsibility to lift others to success,” said Tareq Hadhad, CEO of Peace by Chocolate (pictured in middle photo), during his opening keynote presentation at the Canadian Construction Association’s annual conference in Tucson, Ariz. More than 500 construction industry professionals attended the event, held in early March.
As refugees fleeing war in Syria, Hadhad’s family came to Canada in 2016 where they navigated barriers that many new Canadians face. His company, started in a modest residential kitchen, is now the third-largest employer in Antigonish, N.S.
“We didn’t come here to take jobs. We came here to create them,” he said, adding that his family are now proud Canadian citizens who use their story and values to give back both in Canada and abroad.
Immigration is a hot topic for the construction industry, as companies look to address the country’s skills shortage, but the movement of new Canadians into waiting construction jobs is less than seamless, delegates heard.
“Prioritizing educational certifications does not help the construction sector,” explained Patrick McManus, executive director of the Ontario Sewer and Watermain
Looking at how construction companies can ready themselves for net-zero and green public procurement, Stephan Dery, of Public Services and Procurement Canada, outlined the federal government’s commitment to Net-Zero by 2050 and its influence on selection of materials. “Government infrastructure has always been a catalyst for change,” he said.
In another session, Jean-Pierre Gauthier of Peter Kiewit Sons ULC discussed approval processes as he cited a need for infrastructure works that will facilitate the movement of goods both within Canada and for export, stating, “You need to have a plan for the entire country.”
Discussing expectations for 2023 and 2024 during the CEO Roundtable, Silvy Wright of Northbridge Insurance stated, “I think we can all agree, there is a lot of uncertainty.”
She explained that a dip in GDP growth has elicited worries about recession, but also pointed out that Canada is the only G7 nation with a growing population. She expects the country’s low unemployment rate to help temper any potential recession. “I think Canada is very stable,” she said.
Procore’s Tooey Cour-
temanche explained that he leads most conversations with owners of construction companies with the question, “How are your backlogs?” Those, he said, have remained strong and healthy, despite labour shortages and inflation. “There’s a little bit of cognitive dissonance that happens,” he said. “If you read the news about all the stuff that’s happening, it sounds awful, but these folks are running their businesses, and they’re seeing that there are still areas of opportunity… Ultimately, there seems to be a fair amount of optimism about the future.”
Part of that future will involve greater reliance on technology, both in project management and in the materials and tools used to build these projects. Exoskeletons, an automated QA system, and environmentally friendly bricks were presented by three companies who are part of the association’s CONtact mentorship program during “The Innovators Pitch,” a competitive set of presentations won by Bio-Brick this year. “Tough, physical work can lead to high turnover and injuries,” stated Laurent Blanchet, CEO of Biolift, as he discussed the benefits of his company’s exoskeleton technology.
Bio-Brick Labs CEO Adrian Simone (pictured bottom, left), whose company’s brick technology dramatically reduces the environmental impact of manufacturing bricks, explained, “We want to make green building as easy as possible for everyone. We want to build the future.”
Next year’s CCA conference will be held in Punta Cana, Dominican Republic, from March 12 to 15.
Building in Canada has its own challenges. What you need for downtown is different from what you need out-of-town. It’s why our equipment is cold weather tested. It’s also why we offer compact sizes for flexibility, versatile attachments for multitasking, and comfort for long days on the job. Best of all, with a range of financing and extended warranty options, you can get started and keep working from dawn until deadline.
The Canadian Apprenticeship Forum (CAF) and its partners, the Canadian Construction Association, Aboriginal Apprenticeship Board, Apprenticesearch.com, BuildForce Canada and SkillPlan want to help employers hire workers to become apprentices, and they can facilitate access to as much as $20,000 in grant money per year to help with the hiring and training of this next generation of the workforce.
Stephanie Shrum, program manager with Canadian Apprenticeship Forum, presented details of the Canadian Apprenticeship Service (CAS) program during a recent webinar moderated by Doug Picklyk, editor of Heating, Plumbing & Air Conditioning (HPAC) Magazine
The program distributes grants to smalland medium-sized employers who hire first-year apprentices. Available for up to two new apprentices per year in 39 eligible trades, the program provides $5,000 per apprentice, and $10,000 for apprentices who identify as being within an equitydeserving group.
“The Canadian Apprenticeship Forum is one of 19 service providers across Canada who are providing this program to employers,” stated Shrum.
CAF launched its participation in CAS in September of 2022, but there is only one year left in the program’s mandate at this point, as it will wrap up on March 31 of 2024. The decision to work with partners
has allowed CAF to differentiate its offerings, with each partner offering additional supports unique to this group’s version of the grant program.
“There are 19 service providers across the country. It’s going to be the same in terms of the timeframe that the program’s available, the money that’s available, the trades are all the same. Also, the application process is the same,” explained Shrum. “What’s different about us is we offer wraparound services in addition to the grant that you may want to take advantage of.”
She outlined several of CAF’s valueadded items.
“The first is a complimentary matching service. It goes by region, and it goes by trade. We also have job developers that work with you to get good connections. It’s not just an algorithm that matches you up.
There are real humans on the back end trying to make sure that it is a good match.”
The organization also offers complimentary access to a mentorship course and a mentorship app for apprentices and journeypersons.
“Maybe you haven’t had an apprentice before; this program allows you to see the six competencies that are important for transfer of knowledge,” she explained. “It’s self-directed; it’s online; it’s about two hours long; and it just walks the mentor through some of the skills that we find are particularly helpful.”
The app can help apprentices review competencies for their trade and check with their mentor.
“It doesn’t replace the logbook,” said Shrum, “but it can give you a printout at the end of that first year to easily go through a logbook and check off all the competencies, so it helps to stay organized.”
Skills training through SkillPlan and BuildForce is also complimentary for companies making use of the CAF portal to these apprenticeship grants. This can help apprentices who may not be fully confident in such skills as numeracy, percentages and measurements.
So, how does one sign up to receive a $5,000 or $10,000 grant?
“The first thing you’re going to do is go to apprenticesearch.com/cas to register,” said Shrum. “That’s the ApprenticeSearch website where you’re going to fill out just a little tiny registration page.”
The process involves some basic documentation, including a sub-agreement saying that the company will not work with another service provider during the time they are working with CAF.
“The reason for that is that we need to
ensure that employers are just using the program for two apprentices a year. We need to be able to track,” she explained. “We also want to make sure that you’re getting the best service and the easiest way to do that is to keep with one service provider.”
As the program is intended to foster the signing of new apprentices, registration for the grant program needs to happen before an apprentice is registered with the jurisdictional authority.
“If nothing else sticks from today, that’s the main thing: Register with us, then register your apprentice,” stressed Shrum. “The reason for that is that it’s not a retroactive program. It’s a move forward program.”
Brett Butler, owner and president of Aaron Machine Shop in Alberta, shared his insights into the program, which he accessed for two apprentices for his company.
“SAIT introduced us this program and encouraged us to enroll in it,” he said, adding that he registered online, and found the process very easy and straightforward.
“Our two candidates were actually in-house employees who wanted to upgrade their skillset… If you have employees that are interested in upgrading their education, eventually getting paid more, we show them a path to making more money and building their career.”
As an owner, he takes a broad view of the program, the need to find new workers, and the costs involved in training people.
“Your best journeypeople are meant to go out there and make money for your business and to pull them off that to train someone for even a few hours a day, well, that is a very real cost for an employer,” he says. “So, if you have a $5,000 or $10,000 grant, the way I think about it is that buys you training time for a few months, which helps justify sending that person to school… I’m a business owner, and I would encourage everyone to do it.”
Details about the CAS program, including a list of eligible trades, is available on the www.apprenticesearch.com/cas website.
The film franchise, Back to the Future, predicted that people would be operating hoverboards and flying cars in 2015. This fantastical prediction, which envisioned a world that revolved around innovation and technology, may not have been entirely accurate, but it lends itself to some truths today. The global population is not yet getting stuck in sky traffic after work or programming their robot for a day of chores like Hollywood envisioned the future to look like, however, advances are underway to transform the way society operates for the better.
The construction industry is an example of an industry expanding to adopt new ideas and pathways of thinking to evolve. Pomerleau is one of the general contractors leading the industry toward an innovative breakthrough. Having integrated technological tools on its projects like Building Information Modelling (BIM) in 2012, the company has built a reputation for its practices, emphasizing the importance of investing in innovation to remain at the forefront of change. When it comes to the future, it can be difficult to forecast where construction might be, but there are some exciting predictions. Just like in Back to the Future, choices made today can change the course of tomorrow. Here is a quick look at what Pomerleau thinks innovation in the construction industry will look like in ten years.
In 2019, Pomerleau launched the Foundation for Operational Excellence (FOX), a program aimed at facilitating change management at Pomerleau and optimizing processes through innovative solutions. Shortly after, in 2021, Pomerleau partnered with La Factry, Canada’s first training centre that specializes in developing creative skills, to create AXLAB, an accelerating lab dedicated to researching the potential of technology in construction processes. AXLAB and FOX now work together to execute research, development, and change management to remove non-value-added tasks, create value, and improve efficiency across Pomerleau’s sites and shared services.
“We have a clear innovation strategy and culture at Pomerleau. It is one of our values and drives our success as a company. As the industry grows and we accept more large-scale projects, innovation will always be present. Support for design and building coordination is provided using tools like 4D simulations, drones, 360 cameras, and Geographical Information Systems (GIS). We are working on expanding this expertise by tracking and optimizing the lifecycle of a project in real time. To complement and support expertise on-site, tools like drones, robots, and artificial intelli-
gence will be used to generate data-driven decisions and detect hazards. Evaluating technology with methods of construction will enhance the way we build and create safer sites,” said Yuri Bartzis, Innovation DirectorBuildings Operations.
In 2021, Pomerleau released its inaugural Environment, Social and Governance (ESG) report and platform, Perspective. The report outlines several specific ESG objectives that are to be achieved in a specific time frame. The Innovation team collaborates with the Environment team and employees on-site to reach these targets. By 2025, Pomerleau aspires to offer its clients traceability of residual materials across all its projects, and adopt a target for the reduction, reuse, and diversion of residual materials. The company is also working to reduce its GHG emissions by 40% by 2030 and electrify its fleet by 2025. These are all objectives the Innovation team is supporting.
“The focus in the future will be on sustainability. We are actively working on creating innovative, sustainable solutions to address prevalent construction challenges, as we recognize the urgency of the
environmental crisis and the need to adapt to evolving regulations in the construction industry. When it is required by law to include impact reducing measures, we will be ready and will be a reference in the industry. We want to have full traceability of waste generated on-site using technologies like the Internet of Things (IoT) and GIS. To facilitate lifecycle assessment, BIM can be used to factor in the carbon footprint of a project to make decisions before it has commenced. Through prefabrication, we can replace harmful materials and reduce waste by fabricating building parts off-site. It is not only our goal to construct sustainable buildings but also to build sustainably,” said Vincent Melanson, Innovation Manager- R&D and Special Projects.
As Pomerleau continues to invest in innovation and expand its teams, the company will continue to partner with academia and industry experts to propel its vision. Students are encouraged to apply for internships and be a part of the next generation of construction.
“We are looking forward to seeing what new changes we can adopt in our team to maintain our edge. The possibilities are endless,” said Bartzis.
BUILDING TO SUPPORT GROWTH
Supply chains continue to be stressed, labour shortages remain chronic, and the economy is delivering inflation and recession. Yet road and rapid transit projects enjoy considerable momentum across Canada even as the various players manoeuvre, with varying degrees of success, to obtain approvals and keep financing and timelines in order.
Ontario offers a classic illustration of the drive to expand transportation capacity. The Toronto area is growing rapidly and the current provincial government has been jockeying to expand the network of roads and bridges to alleviate congestion.
“We have $785 million worth of goods per day traveling on our highways, and we know that the population of the Greater Golden Horseshoe, alone, is expected to grow to almost 15 million people by 2051,”
says Andrew Hurd, director of policy and stakeholder relations with the Ontario Road Builders’ Association.
The Bradford Bypass, a high-profile $800 million project that stands to connect Highways 400 and 404 north of Toronto, was taken off the table by an earlier provincial government but was subsequently revived, and its future looks promising. Early work began last fall on a bridge crossing the bypass near Yonge Street, and environmental assessment work could be completed by year’s end. A second major project northwest of Toronto, Highway 413 appears to also be moving forward as well, although it continues to face a possible federal environmental assessment even as it undergoes preliminary design.
Hurd is optimistic that both projects will succeed and says, despite inflation, supply chain pressures and a tight labour market, the roadbuilding segment remains
strong across the province.
“We’re looking at approximately $87 billion over the next 10 years,” Hurd says, drawing on government budget numbers to peg highway and bridge construction in Ontario at $3 billion and public transit at more than $8 billion over each of the next three years.
“It’s a strong outlook,” Hurd says, contextualizing transportation as the backbone of the province’s domestic and exportdriven economy. “With immigration increasing, with more people coming to Ontario, we think it’s essential that infrastructure projects such as Highway 413 and the Bradford Bypass are built as part of a multimodal strategy to keep Ontario moving.”
The $3 billion annual figure for Ontario’s roads and bridges includes roughly $2.3 billion worth of rehabilitation and expansion work. Crews are currently widening Highway 401 in Mississauga and Milton, improving
Despite economic, supply chain and labour challenges, road and rapid transit projects continue to take steps forward.
Highway 7 between Kitchener and Guelph, and rehabilitating the QEW Garden City Skyway, which includes a new twin bridge over the Welland Canal to connect St. Catharines and Niagara-on-the-Lake.
Design work is also underway on a replacement of the aging Frederick Street Bridge in Kitchener, and EA and engineering is slated for later this year for a dedicated passing lane on Highway 11 north of North Bay. In the northwest, the province is looking to widen Highway 17 from Kenora to the Manitoba border.
Rapid transit projects have also been active. Despite delays and rising costs on light-rail lines in Ottawa and Toronto, new routes such as downtown Toronto’s Ontario Line are breaking ground.
Activity is also strong out west. Alberta Roadbuilders and Heavy Construction Association CEO Ron Glen says Calgary West, the final segment of a substantial Ring Road undertaking, should be completed in about a year, and crews are working on Edmonton’s Yellowhead Trail Freeway conversion, assorted bridges, underpasses and rehabilitation projects, and an overpass on Highway 1A near Cochrane.
Future plans include twinning Highway 3, the southernmost east-west connection between Saskatchewan and British Columbia.
Public transit projects, meanwhile, include extending the Edmonton Valley Line West and Valley Line East LRTs, though the latter, like light-rail lines in Ottawa and Toronto, is behind schedule. Calgary, meanwhile, is planning its new Green Line LRT as a P3.
For all the activity, however, Glen says municipalities anticipate reduced provincial funding over the next few years, which could impact transportation capital programs.
One provincial project has faced a significant struggle: The province halted plans last year to employ a P3 to upgrade Deerfoot Trail, a major north-south freeway in Calgary, opting instead to procure the bulk of the plans in smaller, more manageable sections. At the time, transportation minister Prasad Panda said pricing volatility and
historically high inflation in the construction sector meant a P3 approach was no longer economically viable.
“We will focus on improving the most congested areas on the highway first to improve traffic flow and reduce travel times for commuters in the Calgary region,” Panda said in announcing the change.
Work is underway to identify the most critical areas for improvement that can be tendered and completed as quickly as possible, and the province has pledged $210 million towards sections deemed highest priority.
Of course, when the province finally changed course from the P3 plan, $15 million worth of design work already completed by the three consortiums vying for the contract “was just shot out the window,” Glen says. The ARHCA is pressing the province to establish a new highway trust company to manage projects and make the process more predictable and stable.
“As soon as you start getting really complex you increase the risk,” Glen says. “Fluctuating interest rates makes it very risky to do these risk transfer projects.”
Uncertainty and risk aren’t always dampers for transportation projects, however. In British Columbia, chaotic weather is actually driving construction. Kelly Scott, president of the B.C. Road Builders and Heavy Construction Association, says rehabilitation and flood-proofing continues along sections of the Coquihalla Highway where intense atmospheric river rainfalls damaged roads and bridges in late 2021.
“They’re engineering it so it can withstand 1,000-year floods like the one we had,” Scott says, describing work improving dike systems along the Lower Mainland and enhancing bridge abutments to strengthen vulnerable pinch-points. Crews are also adding layers of rip-rap and other armour rock along riverbanks where the worst flooding occurred to prevent erosion and keep the river in the riverbed.
“Emergency repairs have been completed and we’re now improving the pinch-points to make them more climate resilient,” Scott says, noting significant upgrades to three bridges.
As with the other provinces, additional
routine activity is ongoing. Projects range from the Pattullo Bridge replacement in the Lower Mainland, to ongoing widening along Highway 1 from Kamloops to Golden, and an expected announcement about widening towards Chilliwack.
“It’s recognition that the Port of Vancouver needs to have a dependable infrastructure system to ship goods across the world,” Scott says, forecasting three to four years of work.
“I think you’re going to hear more about investments in a national infrastructure corridor through the ports of Vancouver and Prince Rupert,” he says, noting that climate change impacts on infrastructure and the economy have stakeholders investing to build back better.
While transportation projects are strong in Ontario and Canada’s two westernmost provinces, crews are busy from coast to coast to coast. From Highway 104 improvements in Nova Scotia, to tunnel and bridge work in Quebec, to new all-season roads in the far north, each region has its own narrative, but Canadian Construction Association president Mary Van Buren describes transportation infrastructure as a national imperative requiring ongoing attention.
The CCA’s most recent infrastructure
report card, released in 2019 before Covid throttled the global economy, noted 40 per cent of roads and bridges in fair, poor or very poor condition.
“It showed there’s a need to fix what we have,” says Van Buren. “As a nation we need to invest in order to enable our economy.”
With the Investing in Canada Plan allocating $180 billion over 10 years for everything from public transit to climate change impact mitigation, to enabling rural and northern communities, she acknowledges the federal government is paying attention. Still, 65 per cent of Canada’s GDP comes from trade-enabling infrastructure, and she says the country is under-investing relative to other strong exporters such as Australia and the United States.
“One of the challenges is that, as a nation, we don’t have a long-term infrastructure plan. Everything tends to be done on political cycles.”
Van Buren is calling for a 25-year plan prioritizing infrastructure spending.
“That would allow us to line up the labour force we need and would give confidence to businesses and industry to invest in technology, to invest in greening — all those things,” she says. “Otherwise, we can fall into boom-and-bust, which isn’t effective or productive.”
While long-term planning could address the shortage of skilled workers, unemployment in construction remains chronically below historical levels.
“The availability of labour will continue
to have an impact on project schedules, particularly in regions where labour market tightness is particularly acute,” says Bill Ferreira, executive director of BuildForce Canada, which specializes in labour market analysis.
Still, he points out the shortage isn’t unique to construction. It reflects a broader demographic reality, with 20 per cent of Canada’s population between the ages of 50 and 64, and only about 16 per cent of the country’s population under the age of 15.
“More people will be entering into retirement than will be available to backfill for those individuals,” he says. “The scarcity of young people means competition for young talent is going to be incredibly intense.”
Ferreira says immigration can help maintain a core working age cohort, as can promoting careers in the skilled trades, and the industry continues to engage people who have historically been underrepresented.
“We’re starting to see positive signs. When we look at apprenticeship registrations, particularly in the Red Seal trades, we’re starting to see the number of women registering in programs is just under six per cent now. That’s up from about three and a half percent ten years ago.”
The sector also collaborates with Indigenous communities and businesses. “It depends on the region and the size of Indigenous communities,” Ferreira says.
Labour market and economic uncertainties notwithstanding, Pedro Antunes, chief economist with the Conference Board
of Canada, says signs point to a gradual recovery and relatively strong prospects for infrastructure. Steadily increasing immigration, especially in larger urban centres, necessitates improved mobility yet also helps supply labour power to keep projects moving.
“We’re seeing a supply of workers coming in available to work and a lot of organizations picking up those workers because they’ve been having trouble meeting demand,” Antunes says.
The same duality applies to economic pressures. Inflation has sent costs soaring, yet higher price tags have enabled tax revenues, helping raise funds for infrastructure.
“Weaker economic growth this year is going to stress a lot of governments, and some of them will see weaker revenue growth,” Antunes says. “But I think the fiscal situation is better than it was looking even a year ago.”
One source of financing aimed at helping projects deemed particularly worthy but otherwise vulnerable is the Canada Infrastructure Bank. The Crown corporation currently has $3.7 billion invested in rapid transit and trade and transportation buckets, with a view to helping finance projects meeting federal imperatives such as reducing greenhouse gas emissions and serving remote regions.
Two of its higher-profile projects include the rebuilding of the New Westminster Bridge, which provides rail service to the Port of Vancouver, and modernizing Tshiuetin Rail Transportation, a freight and passenger service connecting three northern Quebec First Nations.
“Our mandate is to be a force to unstick important projects that wouldn’t otherwise get done. We have the ability to be patient capital and wait until demand ramps up for repayment to start, where traditional lenders wouldn’t be able to wait,” says CIB chief investment officer John Casola.
“It doesn’t matter what your political perspective is — at the end of the day there’s very little disagreement about the fact that we need lots of important infrastructure in this country.”
With a full line-up of the world’s top equipment for Canada’s roadbuilding industry, Brandt Road Technology delivers all the tools, equipment and support you need to own the road. We are the exclusive Canadian dealer for John Deere construction equipment, Vögele pavers, Kleemann aggregate crushing and screening equipment, Hamm compaction equipment, and Wirtgen milling and concrete paving products. Our highly specialized and experienced teams are focused exclusively on this industry, so you can rest assured that your equipment is backed by the besttrained and most committed 24/7 after-sales support in the business. That’s Powerful Value. Delivered.
brandt.ca 1-888-227-2638
By weight, asphalt from roads is the most recycled commodity in North America, reducing the carbon impact of the roadbuilding industry and contributing to the circular economy while allowing contractors to deliver surfaces that match or exceed the performance of roads built without reclaimed materials.
“Asphalt pavement should be considered a green product because 100 per cent of asphalt pavement can be recycled,” says Alan Lichwa, asphalt and construction quality manager for Western Canada at Lafarge Canada. “Both components, asphalt binder and aggregates, can be reused in new asphalt pavements.”
The amount of Reclaimed Asphalt Pavement (RAP) permitted in a new mix varies from jurisdiction to jurisdiction in Canada, with some allowing up to 40 per cent, although comfort zones tend to be closer to 10 to 15 per cent, he explained. In addition to local regulations, Lichwa says the type of roadway being constructed, specifications being followed, and the availability of the recycled material are also factors.
“If the quality of the asphalt road being ground out is deemed to be questionable for re-use in new asphalt, it can be recycled within the granular base layer constructed beneath the roadways,” adds Mate Jurkin, GTA asphalt plants manager with The Miller Group, further illustrating the ways that paving firms can reduce their reliance on virgin materials. “The only exception where
an asphalt roadway would not be recycled is if it is deemed to have a contaminated product.” These, he says, would be disposed of with utmost caution.
As pavement ages, the oxidizing binder becomes more brittle, so when using RAP, the loss of this flexibility in the old surface will impact the chemistry of the new mix.
“The challenge is to create a new asphalt pavement that is flexible using less flexible material,” says Lichwa. “This challenge can be overcome with the use of additives and different technologies that allow us to produce asphalt pavements with high amounts of recycled material.”
Where once concerns about the longevity and performance of roads using RAP were common, quality control measures and best practices are illustrating how the use of these recycled materials can create a road that meets or exceeds expected life cycles.
“With the proper additives and technologies, an asphalt pavement using recycled materials can outperform an asphalt pavement without recycled materials,” says Lichwa, adding that the percentage of recycled materials influences the other components in the mix, including the chemicals that help incorporate the recycled material.
Best practices are essentially the same whether reclaimed materials are used or not, however, both before the mix is created and after the roadway is paved.
“Best practice starts with a thorough pavement design, including analysis of traf-
fic and climate data, to select the best type of mix for a road,” says Jurkin. “In order for the road to live to its long-term expectations it should undergo routine maintenance, such as crack sealing, and scheduled preventative maintenance.”
Lichwa adds that reducing and monitoring moisture in the recycled material, quality control testing on recycled material, and quality control testing on the final product are also practices that should be followed.
As the use of recycled asphalt in roads has evolved, so too have industry specifications, testing and paving methods.
“We are moving towards more performance-based specifications, a different method of processing the RAP, use of asphalt cement rejuvenators, and more robust testing parameters,” says Jurkin. “It is more common internationally, but we may soon see cold-recycled mixes which make use of up to 100 per cent RAP and recycled with an asphalt emulsion at a mobile plant.”
“As a whole, the asphalt industry is changing not just because the addition of recycled materials,” says Lichwa. “There is a strong push for performance-based testing to be done on pavements to help quantify the effects of recycled materials… new technologies in asphalt mix design have changed how we understand asphalt mixes and help us design with high amounts of recycled materials.”
That’s good for the end customer, as well as for the environment.
As one of the most recycled materials in North America, asphalt pavement is reducing reliance on virgin materials.
Our new electric lineup made a lot of noise in Vegas. Which is impressive, since they cut noise in half while keeping the same power. That means you can work overnight or indoors. And we also built them to fast charge at a station, or recharge directly on the jobsite, because even small machines should deliver big results.
Current trends in road construction equipment put a spotlight on greater efficiency and improved operation with less environmental impact than ever.
“Right now, manufacturers are continuing to push for greener technologies like battery-powered and alternative-fuelled equipment, but they’re also focusing on increasing efficiency and output quality, as well as safety,” explains Sheldon Allan, paving industry support specialist at
Finning, a major Canadian CAT distributor. Martin Hilken, product marketing team lead at Vögele, also highlights sustainability, but points to user-friendliness, process automation and cost-effectiveness as well.
“The aim is to make the machines even easier and more intuitive to operate and learn,” he says.
Intuitive and efficient operation are driving innovations for manufacturers of pavers, as well as compaction equipment.
“Many of the changes and updates to
asphalt compactors have revolved around making the operator’s job simpler, to give them more confidence and ultimately greater satisfaction in a job well done,” says Jeremy Dulak, product manager with CASE Construction Equipment. “This has included more comfortable operator stations, improved visibility, more intuitive control locations, and giving the operators greater control flexibility.”
Hilken adds that asphalt paving processes are being automated as far as possible in order to reduce the workload on operators and counteract paving errors.
Allan agrees that automation is coming, saying, “Although a fully autonomous paving train isn’t available yet, the puzzle pieces are being introduced on a regular basis.”
Costs will be trimmed in paving equipment, says Hilken, through more-efficient drives, but alternative drive technologies are also being considered.
“For the smallest pavers, the focus will be on battery-electric drives, while intensive research is being carried out into other alternatives for machines in larger performance classes,” he says.
Among other advancements, a new design for screed plates is coming to the market. These plates, notes Allan, have a three-dimensional angular design that provides a kneading action as the asphalt mix passes through the grooves.
“This reduces air voids and increases density behind the screed, leading to longer-lasting roads with increased joint
density and better smoothness (IRI) scores,” he explains.
Caterpillar recently announced new features in its large asphalt pavers, like the AP1055F, a high-production, rubber track paver. These aim to reduce errors and increase consistency and efficiency.
Pave Start Assist is an optional integrated system that uses smart cylinders on the screed and tractor. Allan explains that once the paver is set up to produce the best quality mat, the screed setup can be stored into the paver’s display. This allows for repeatable performance, which reduces errors and improves mat quality and joints while also saving time.
Other new features include a hopper level temperature sensor, which identifies issues with incoming material, and thermal mapping, which identifies thermal variations early.
Caterpillar compaction equipment also incorporates sensor systems through options such as object detection, compaction control and cameras (birds’ eye and front/rear). These options improve operator effectiveness and efficiency by extending sightlines, ensuring adequate coverage and more, says Allan.
“Caterpillar has also introduced its ‘Command for Compaction’ feature, a semi-autonomous option for soil compactors that brings together machine control, positioning and object detection systems,” he says. “The operator drives the soil compactor around the perimeter and inputs passes, speed and overlap. The system then takes over.”
Vögele’s newest paver features include Road Scan, a non-contacting temperature measurement system that enables seamless control and documentation of the asphalt temperature directly behind the paving screed.
“There is a version specially developed for the North American market that enables collected data to be transmitted online via a secure serve,” says Hilken. “The data is conveniently forwarded to the Departments of Transport via a direct download from WITOS Paving Analysis. The data provided meets the VETA requirements.”
Vögele’s 3D control systems, Navitronic Plus and Navitronic Basic, are available for several pavers, including the 8-ft SUPER 1700-3i and 10-ft SUPER 2003-3i. Navitronic Basic not only provides conventional grade and slope control, but also automatically controls the paving position. Navitronic Plus has the same features but also takes over steering of the Vögele tracked pavers.
“This makes the Navitronic Plus a true 3D control system of a kind offered by Vögele only,” says Hilken.
Concrete paving machine manufacturer GOMACO recently introduced the GP460,
which is a placer/spreader that can go up to 50 feet (15.2 m) wide, and a slipform paver that can go up to 40 feet (12.2 m).
It’s built on the framework of the GOMACO two-track GP4 slipform paver with the ability to convert the prime mover into a concrete placer/spreader. The prime mover is equipped with vibrator circuits for paving and auger drive circuits for placing. Control of the new technology is achieved through GOMACO’s G+ digital control system, which handles the controls conversion needed for each application while also bringing onboard machine-to-machine communication, sonic sensors, 3D machine guidance, and more.
The GP460 is also available with an optional sonic sensor system to monitor the concrete depth as it is placed. Information from the sonic sensors is used by the G+ control system on the paver using M2M communication to provide an optimum and consistent head of concrete in front of the paver.
Among BOMAG’s newest offerings are its BM 2200/65 and BM 1200/35-2 cold milling machines. The BM 2200/65 is equipped with the company’s exclusive Ion Dust Shield technology for effective reduction of fine dust and particulate matter generated by the milling process. It turns captured fine dust into course dust, improving environmental safety on jobsites.
In its implementation of “intelligent compaction,” BOMAG
equips its new BW 120 SLC-5 combination roller with Intelligent Vibration Control. This system alerts the operator in real-time when optimum compaction is achieved.
Its highway-class BW 174 AP-5 AM and BW 206 AD-5 AM tandem rollers both feature its Asphalt Manager, which allows operators to enter the asphalt lift thickness so that the system will automatically adjust compaction force relative to material thickness and temperature. Vibration direction is automatically matched to the roller’s travel direction to prevent ripples in the mat.
BOMAG also offers electric compaction in its roller lineup, with a new tamper, single-direction plate and tandem ride-on roller through its e-Performance line. The BT 60 e tamper has a plug-and-play system for easy charging without tools, and an optional quick charger allows for the battery to charge in less than two hours.
The new BP 18/45 e single direction plate uses the same battery as the BT 60 e and features an optional water tank for asphalt compaction.
The BW 100 AD e-5 tandem roller is designed to operate for a full typical workday with one charge. Two high-efficiency electric motors independently control the drum vibration and travel/steering, so only one motor is needed for travel mode to conserve power.
Sensor systems and autonomous operation that improve efficiency, consistency and overall performance are the latest trends in rollers at Volvo Construction Equipment.
“Intelligent compaction has come a long way in the last several years and is growing in use,” says Mark Eckert, the manufacturer’s product manager for compactors.
Volvo CE’s most advanced sensor system, Compact Assist for Asphalt with Density Direct, provides operators with real-time density estimates of the surface area being compacted, enabling greater accuracy and consistency.
The company introduced its newest compactor, the DD25 Electric asphalt compactor, in January. It’s a smaller machine for jobs like street repairs and bike paths and the company’s first electric machine for the road segment. Volvo CE also makes three electric excavators and two electric wheel loaders.
Due to the size of its components, the DD25 Electric is more responsive in terms of speed and vibrations, providing better performance on grade. It’s also better at high elevations compared to a diesel machine, says Eckert.
On that note, Volvo CE’s newest diesel compactor is the DD128C, which offers the highest frequency in the industry.
“The rear 55-inch drum has auto-reversing eccentrics that ensure eccentric rotation in the direction the machine is traveling for unparalleled smoothness,” Eckert explains. “It’s also equipped with an automatic drum wetting system that provides speed-de-
pendent water flow to minimize water usage and ensure uniform coverage to prevent material pick-up.”
At CASE, the aim is to provide contractors with the flexibility to choose equipment that fits their company’s workflow.
“If you look across the line, we give people options in size, drum type, and setting and performance capabilities that really allow a contractor to select the machine that is best for them,” says Dulak. “There’s no forcing one size to fit all. As you look at our more compact rollers, they now have many of the control settings and capabilities of large-frame rollers in terms of frequency and amplitude and dialing in that machine.”
The manufacturer’s focus on providing a comprehensive line of asphalt paving equipment that meets the need of every paving contractor provides a lot of choice in its equipment, which ranges from compact double-drum and combi rollers to full-sized doubledrum vibratory rollers. CASE also offers large-scale pneumatic tire rollers for larger highway and roadbuilding projects.
“If you look at compact solutions from 39 inches up to largeframe drums at 66 inches, we have 11 machines in that range with various drum and tire styles, compaction settings, et cetera, to fit every business,” illustrates Dulak. “And then if you need the true
CLOSE TOOUR CUSTOMERS
ROAD AND MINERAL TECHNOLOGIES. The WIRTGEN GROUP owes its strength to the excellence of its product brands – WIRTGEN, VÖGELE, HAMM and KLEEMANN – with their unique wealth of experience. Put your trust in the WIRTGEN GROUP team.
CAMERAS IN CONSTRUCTION
Page 34
CYBERSECURITY FOR CONSTRUCTION
Page 38
5G ON SITE
Page 40
TELEMATICS FOR EFFICIENCY
Page 42
We analyzed 64 global construction projects, representing 82 years of combined construction time, to explore construction site inefficiencies at a more granular level than ever before. Our research identified 4 metrics of inefficiency that are often overlooked and can be used to optimize efficiency going forward.
The number of trades that return to a work zone to finish incomplete work (not including rework).
The instances of activities being started out of sequence in each area.
Buildots is delighted to feature in the Construction Technology Report emphasizing the importance of technology in the construction industry. When my co-founders and I founded the company in 2018, the industry was being inundated with advanced technological innovations, but there was still a lack of tech to address its core challenge — how can we deliver projects more efficiently?
With today’s challenges, the question is even more relevant. Facing skills and labour shortages, design complexities, new regulations, financial uncertainty and more, professionals are still expected to successfully deliver on construction projects.
We recently published a study in which we analyzed 64 projects worldwide, the equivalent of 82 years of combined on-site construction, to measure project efficiency at a more granular level than ever before. Our research revealed the impact today’s challenges have on our industry’s productivity, but also the potential for improvement.
We highlight four metrics of inefficiencies, from low utilization of available work areas to weekly trade output inconsistencies — metrics that are a result of challenges project teams previously had no advanced tools to help with. But there are tools and methodologies now, from AI to Lean Construction, that can support teams. We’re proud to be one of these tools. Buildots AI-based technology fully automates progress tracking for enhanced control and visibility on-site.
We set out on a mission to make construction more efficient — not accepting the status quo. We’ve been helping construction professionals do what they do best, with less stress and more certainty. It’s exciting to see the change the industry is going through, and it’s a great honour to be part of it.
All my best,
Aviv Leibovici, Co-Founder and Chief Product Officer at BuildotsCameras and imaging systems are changing construction sites. From site mapping to project tracking, cameras, drones and lasers are providing very accurate and precise information that can be harnessed to produce more efficient builds.
On March 20, three industry experts, Steve Mahaney, VDC area manager for Eastern Canada at EllisDon; Cody Nowell, construction services manager at PCL Constructors; and Steve Rollo, national BIM/ VDC manager at Graham, took part in a virtual discussion, moderated by yours truly, the editor of On-Site Magazine to share how these technologies are being used by their teams on sites throughout Canada.
And these technologies are varied, from traditional video-shooting drones to hardhat-mounted cameras and laser imaging systems that generate point clouds – and
even photo-realistic 360-degree visuals. Thankfully, the panellists were up for all points of discussion.
To help illustrate the benefit of using drones on a project, Mahaney provided attendees with a special aerial look at the Centre Block Rehabilitation Project currently happening in Ottawa, with video provided by PCL EllisDon Joint Venture, the team working on the project at Parliament Hill.
“The teams use the drone data quite frequently,” he said, explaining that the images have been used by the BIM team in its modelling, as well as for logistics and planning purposes. “It’s an important asset that they continue to use on a daily basis.”
He and his team at EllisDon use both drones and 360-degree imagery on a regular basis for most projects and view the use of this technology as an important part of the
company’s business.
“The amount of data and how quickly you can capture it now provides our project teams with really great insight and also validates design from the consultants or the trade contractors,” he explained. “We can take that scan data and overlay it with models and see where we’re at.”
“Being able to get cameras and drones into the hands of all of our project teams, not just the mega projects, I think is something that we’ve seen a lot of advantage from,” said PCL’s Nowell. “When it comes to laser scanning, while the hardware is a little bit more expensive, I would say there are use cases, depending on the type of project.”
He says that getting a good representation of the existing geometry is very informative to his company’s BIM models, ensuring that the live site matches the
model as closely as possible.
Graham’s Rollo is also a fan of drones. “We’re definitely seeing a huge uptick, especially in the last two years in Canada,” he said. “That, along with the 360 cameras, almost becomes just a natural thing. It’s not even discussed if it’s going to be used on a project anymore. It’s just part of a project kickoff checklist.”
Although there will still be some projects and situations where drones are not a perfect fit, they can be especially helpful to map out large sites, and to capture visuals where space can be difficult to otherwise navigate.
“On larger sites, it’s far easier to get a drone up in the air to map the site out,” explained Rollo. “If we’re doing a large stretch of road or bridge, bridge, we can get the high-level scope a lot easier than just taking pictures.”
“Here in Ottawa, we do a lot of rehabilitations. Looking at older buildings, the drone technology definitely comes into play,” added Mahaney. “At Centre Block, they use it for masonry, taking a look at that going up to the Peace Tower.” With each
block expected to be rehabilitated during that project, the early look will help both with the restoration work and the rebuilding of the structures.
“The really nice thing I like about drones is being able to geo-reference things,” added Mahaney. “Being able to put a ground control point in, and then fly a survey flight, suddenly you’re providing the client with a geo-referenced map of exactly where that underground piece has gone.” Being able to reference the map years later to identify where pipe or other buried infrastructure is located is a major benefit to the contractor, and to the client, he explained.
“The nice thing about drones is that you can harness a lot of different types of data,” said Nowell. “You can use it for logistics planning, you can use it for quantity takeoffs. You can use it for inspections. There’s a lot of different use cases that you have with drones.”
“I think one of the biggest things that we leverage it for is our progress tracking and QA/QC practices, so that we can have that different visual of the big picture of the project to track how the project is going,” stated Rollo, adding yet more advantages to the use of visuals on a site. “We also
leverage it pre-pour it to identify the PT cable layout… things of that nature… it’s a lot different to get it from that overhead perspective, and then tie that in and align it with the design intent, model or drawings… We use it heavily as part of our progress tracking and progress turnover packages that we present to the client afterwards.”
Use of drones is not without its challenges, risks and regulations, however.
“The RPAS [Remotely Piloted Aircraft Systems] pilot has to be aware of what those inherent risks are,” advised Nowell. Once the risks have been assessed, a decision can be made on whether a traditional approach or the flying digital technology is best for the situation.
“There’s a perception out there that even with a sub-250-gram or smaller drone that basically anyone can just go out and fly,” said Rollo. “And while that’s true to a certain extent, there are a lot of rules.” He explained that failure to follow proper procedures, file appropriate flight plans when necessary, and encroaching into restricted airspace can result in Transport Canada shutting the flight down, and possibly
issuing financial penalties. “You need to be conscious of that,” he advised.
“Client communication is another key part,” said Mahaney, explaining that not all clients would understand why a general contractor would want to fly a drone, and may be worried about their airspace security. He suggested communicating details about what information would be gathered, and how it would be gathered, including how RPAS requirements are to be safely met, can ease the client’s mind.
While much of the discussion focused on drone technologies, panellists also spent time discussing how laser scanning is also assisting contractors work up 3D models so that they can work more effectively and efficiently.
“I think we where we see the most value is where we are recapturing the existing geometry,” said Nowell. His company used laser imaging technology to help with the build of a new 10-storey building on top of an existing parkade structure. New foundations were needed, which necessitated the cutting of openings in the slab and driving piles, but it was discovered that the as-built information was not accurate, which would have created significant problems.
“We use the laser scanner to capture that geometry, adjust the design and make the changes before the piling rig was even mobilized,” he said. “And that’s really where we see tremendous value in those applications. Yes, that laser scanner is an expensive piece of kit. But in the right
application, it’s a lifesaver.”
“With rehabilitations, we like to have the laser scanner go out and do the ‘as-found’ conditions, so that we can really validate the information that we’re getting,” said Mahaney, who explained that the measurement accuracy has also helped in other ways as well.
“Just looking at the speed of the laser scanner now, you’ll get a superintendent who says, ‘Hey, I need a custom grate for this entryway, can you come scan this?’ And it’s like, ‘Yeah, that’s a 15-minute job, no problem, we’ll get you the most accurate data,’” he said. “It’s a great tool for the project teams to be able to scan data and start taking measurements.”
Of course, that begs the questions, “Can I trust the data?” and “How do I know I have accurate and trustworthy measurements?”
“With photogrammetry… it’s this magic box. I take these photos, I put it into the magic box and magic spits out: I get these quantities, and this digital model, and this point cloud,” said Nowell. “Our teams are always so amazed with the data that we can pull from this thing, but how much do you really understand about what you’re capturing and what the outputs are? How are you verifying the accuracy of the information that you’ve captured?”
He explained that the software is so easy to use that can be easy to make mistakes, which may not be picked up right away.
“We’ve made a focus of trying to make sure that we’re training our people to understand what ‘good’ looks like, and to understand what common errors are,” he said. “If you’re turning over data that you don’t know what the accuracy is like, there’s big risks associated with that… there’s a lot that goes into making an accurate scan and capturing an accurate model that you can rely on. And it’s not just putting pictures into a software and then spitting it out.”
Of course, photos, videos and imagedriven apps can also help with project tracking to ensure that project errors are caught as early as possible.
“Something we implement on almost every single job that that we’ve done, at least on the building side, is a hardhat-mounted 360-camera,” stated Rollo. “Similar to doing our drone flights for select jobs, this has been going on, I would say for a vast majority of our jobs now, to be able to capture our progress.”
The use of the camera and app leans on the daily site walk that needs to be done anyways, but it has now become a handsfree experience that they don’t even have to think about.
“And they don’t have to walk the same path every time,” he added, one of the ways that the geo-referenced data differs from the traditional methods formerly used for progress tracking.
The fact is that imaging is changing the way that construction sites operate, and for the most part, technology is proving its value to project owners, construction managers and workers on the sites.
“The value cases are there, and they’re proven,” stated Nowell. “If you’re not there yet, you should be.”
“I think the biggest thing is that this is data that we need for our jobs anyways, and these technologies provide a very low-cost, efficiency gain to the project and are actually capturing the data accurately,” added Rollo. “Not only does it add a value benefit to the owner, but for your own internal record keeping, it’s huge value down the line, should that data need to be recalled at any given point.”
And for those who have already embraced the change, Mahaney says there are still next steps and technologies to look forward to.
“I think the next thing we have to look at is artificial intelligence,” he said. “Getting this imagery up into the cloud so that the machines can take a look at it, and we can start doing stuff like progress tracking and talking about billing and that sort of thing.”
To watch the full webinar, please visit On-Site Magazine’s YouTube channel, or visiting https://youtu.be/w1BqtR_U4Oc.
With photogrammetry… it’s this magic box. I take these photos, I put it into the magic box and magic spits out: I get these quantities, and this digital model, and this point cloud.”
Move away from tedious manual subcontractor payments, and put an end to headaches. Easily manage contracts and meet deadlines. Guarantee lien waivers are present and error free. Stop back and forth emails with automatic and custom waiver generation. All with ERP integrations with platforms like Viewpoint, CMIC, and Sage.
Help your entire team complete more projects—smoothly.
Stay in the flow.
GCPay.com
In early 2020, a major Canadian construction firm, announced it had been hit by a ransomware attack. Although the company provided reassurance that they were able to continue with business as usual, there’s no doubt that sensitive information had been compromised.
But they are not alone. In fact, they are in good company. More than 85 per cent of Canadian companies were hit by cyberattacks over a 12-month period in 2021, and companies hit by these attacks spent $600 million to recover.
With the cost and frequency of cyberattacks rising, construction companies and contractors must adopt technological solutions with the right supports in place.
Whether adopting a complete software solution or even using a drone to survey a single site, business owners and leaders will need to learn all they can about cybersecurity, including why the construction industry is being targeted, what the risks are, and how to protect against them.
Though slow to adopt technological solutions, in recent years the construction industry has become more digitally focused. Today, construction firms are using digital tools not only to send invoices and plan projects from the back office, but also on site to build walls and foundations or to survey progress in real time.
Portable devices such as mobile phones
and tablets are used regularly by a variety of workers, full-time employees and contractors alike. And even personal devices may be used to connect to Wi-Fi as well.
Each of these changes comes with benefits. For example, it may be a smart business decision to bypass the chronic labour shortage by building a brick wall with a robotic arm. Yet the change also leaves the industry vulnerable to attack.
Employees who are not careful to protect their own personal devices may not understand how susceptible they may be to bad actors seeking to infiltrate their systems. Business owners may not have the IT support they need in-house. And supervisors and other managers who work from home regularly may be unwittingly leaving their devices vulnerable as well.
Keep in mind, savvy cybercriminals
know the big construction companies are already protected, so they are also going after the small and medium-sized firms, the ones without an IT department or other support team on call. But there’s no reason to leave yourself vulnerable to attack.
THE MOST COMMON CYBERATTACKSCommon cyberattacks include:
RANSOMWARE
Ransomware is software designed to prevent a person or company from accessing their files. Cybercriminals take control of a company’s digital system and demand a ransom payment before releasing it.
While ransomware targets all types of businesses, the construction industry seems to be especially susceptible. In fact, construction firms – like Bird or France’s Bouyges Construction – accounted for nearly 10 per cent of all ransomware attacks in Canada in 2021, likely due to the rapid adoption of technology solutions and the lack of security around them.
In this attack, the criminal poses as an expert or trusted source and uses email to trick someone into sending money or sharing valuable information. The criminal can then use this information to his or her benefit, whether to gain access to banking or other financial information, or to steal money or other resources outright.
As the industry goes digital, the need to protect against bad actors is rising.PHOTO: © PANUWAT / ADOBE STOCK
Construction is vulnerable to such attacks in part because construction firms work with so many other entities. Whether it’s subcontractors or suppliers, goods and money flow back and forth regularly, making it a challenge to spot a false claim or a scammer among all the legitimate transactions. In addition, some construction projects begin as part of a bidding process, which makes the details of a particular job public knowledge and easier to exploit.
For contractors working with multiple companies on multiple projects, security can come down to the strength of a single password. A bad actor gaining access to a system with one vendor may be able to gain access to multiple systems if they are linked.
That’s a risk in the construction industry, where subcontractors may work with a variety of general contracting firms or suppliers who together complete a single job. The subcontractor must have access to the digital project management system at the larger company, but this may create a weak link in the digital system that criminals would love to exploit. And a breach could impact any of the connected companies.
With so many traps, construction firms must be careful when they adopt a digital solution. Technology can make life easier, but only if it’s secured and used appropriately. The proliferation of technology on-site only magnifies the risk, with an increasing number of devices and users to support and protect from attack.
Construction leaders looking to adopt new technology must stay on top of security needs and best practices to protect themselves, their businesses, and other companies they do business with.
Old software and obsolete applications are some of the easiest ways for cybercriminals to gain access to your organization’s data. In many cases, an exploit is made possible through vulnerabilities that may have been overlooked in a program’s outdated coding. Be sure to update software regularly and patch vulnerabilities.
Computers and hard drives, cell phones and tablets, and even printers and copy machines contain data that may be valuable to a cybercriminal. Before disposing of any equipment, be sure that the data is completely wiped so that it cannot be recovered.
Many of your employees may not understand how serious the risk is. Include cybersecurity training as part of your annual safety training and take it seriously. Teach all employees how to handle confidential information, how cybercriminals try to exploit weaknesses, and the different types of cybercrimes. Create a process for reporting suspicious activities.
Where a simple password isn’t enough, multi-factor authentication is a more advanced system that requires a user to verify his or her identity through multiple pathways. For example, in some cases a user may be required to sign in with a password as well as a system-generated code sent to a mobile device.
Adding extra layers of security makes it
harder for cybercriminals to gain access to your sensitive data. Confidential information such as invoices, contracts, and other financial and legal documents all belong behind that extra security. Be sure employees have to submit multiple credentials before gaining access.
The risks are multiplying. And with human error generally understood to be the most significant concern, it’s no surprise that actively managing the risk can make a real difference. Insurers understand this too, and they are requiring construction companies to prove they’re a good risk before offering coverage. In 2023, construction professionals who understand cybersecurity, and who can demonstrate their care, will have the edge.
Jonathan Weekes is cyber leader at global insurance brokerage Hub International. He has more than 13 years of experience in commercial insurance with a focus on professional liability and cyber risk.
From two-way radios to the now-shuttered Clearnet Mike push-to-talk mobile phone network, wireless technology has been used on construction sites for decades. More recently, site communication has meant not just speaking from a distance, but also sharing digital drawings, photos and videos.
This new way of working means jobsites must be connected to the internet. That can be hard to achieve when infrastructure is yet to be built, but Wireless Wide Area Networks (WWANs) and the latest generation of cellular technology, 5G, fit the bill to help move data throughout the construction lifecycle.
A WWAN is a telecommunications network that uses public or private cellular routers or adapters as infrastructure to connect various networks and cloud servers. Enterprise WANs allow users to share access to applications, services, and other centrally located resources. WWANs connect people, places and things anywhere, and have become a staple of enterprise networking.
Cellular wireless has always been ideal for failover and connecting critical assets in places wires can’t go, and today’s cellular networks are more pervasive and getting faster with the deployment of Gigabit-Class LTE and 5G. With flat-rate pricing beginning to eliminate overage anxiety, WWAN is becoming the preferred broadband connectivity for fixed sites.
5G, in particular, has been getting a lot of attention as it continues to roll out across Canada. If you replaced your phone in the last year or two, there’s a good chance it has a 5G modem in it. The specification uses more channels than 4G, which means faster data transfers. It can handle more devices at once, and is better-suited to managing the array of smart devices and sensors now involved in the construction workflow. It is also more responsive.
The 5G specification includes low-band frequencies, which are about as fast as 4G, and mid-band and high-band frequencies that can be 10 times faster.
What does this mean for construction? The amount of data flowing through a modern construction site requires a reliable and fast internet connection that can’t always be provided by Wi-Fi, especially in the early stages of a project.
5G can deliver a fast wireless connection to a site with less of an investment in hardware. A traditional wired connection can take up to 120 working days to set up, and it’s costly to relocate wires as a project proceeds. In contrast, 5G can be deployed earlier, easier and with less hardware. Set up can be handled at a central office and remote sites can be deployed within a day.
The technology supports connectiondependent activities that are already happening on construction sites. For
example, drones serve many functions in the industry: gathering visual information that can be used to create topographic maps and 3D models, assessing the location of equipment, taking measurements, and creating photo and video records of a project’s progress. All of this involves a lot of data.
But the need for bandwidth is only part of the story because drones need to be piloted. With 5G’s low latency, they can be operated from a distance without lag.
Sensors are also playing a greater role in the industry, during and after construction. Internet of Things (IoT) sensors can detect humidity levels that might affect materials and detect gas and chemical leaks. Smart sensors affixed to rebar and embedded in concrete aggregate can send data to the cloud via 5G. This helps ensure the quality of the work and minimizes guesswork.
Sensors can also help track assets on sites, note when supplies are needed, and mark when they have been delivered.
Other devices on sites include cameras, which capture photos and videos to track project progress, provide security and identify safety issues. Those files need to be transferred, usually in real-time. Additionally, wireless WAN is an excellent solution for mobility applications. Managing fleets, providing in-vehicle Wi-Fi for mobile data transfers, and video surveillance for added security can all be enabled using the same 5G network infrastructure.
Contractors are also increasingly turning
to specialized construction management software to manage all this information. This software, too, needs connectivity in the field.
Superintendents now walk sites, tablets in hand, accessing BIM documents, drawings, project specifications and worker schedules. The digitization of construction management started with obvious quality-of-life improvements, such as being able to send new drawings from the office to the field instantly, and has seen the emphasis shift from physical documents and disparate programs and files to comprehensive platforms that manage all aspects of a project.
Setting up a WWAN must factor in several considerations. For example, will the network be in place to enhance network failover or to augment existing network bandwidth? Will it be the primary link, such as in the case of an unserviced job site, where there are no wires to connect to?
An enterprise network solution provider
– in particular one focused on wireless network edge solutions – can help to assess the best strategy and determine the scale of the deployment needed for a particular site.
5G will not be an option for every construction site and it isn’t available in every city, so companies considering using it should assess availability as a first step. As well, local coverage and speeds can vary.
The nature of high-band frequencies means 5G signals behave a little differently than 4G as well. The higher frequencies offer greater speed and bandwidth but carry over a shorter distance; about 500 meters. The signal can be degraded by brick, cement, and the human body. Low-band and mid-band 5G frequencies are less prone to signal attenuation, while still offering high speeds and low latency.
As with any technology implementation, companies should understand any security-related considerations.
Fortunately, 5G was developed with security in mind and will scramble commu-
nications between a user’s device and a cell tower. It also allows for different networks to use the same infrastructure but be separated from each other. This could allow a company to provide subcontractors with access to one network through on-site hardware, but not another containing sensitive files.
While 5G includes built-in security enhancements, it also introduces more complexity. With more IoT devices, there is more rist of compromise. To mitigate security risks, contractors can turn to new security measures such as zero trust network authentication (ZTNA), and practices like keeping devices updated with the latest software and creating back-ups of data.
As construction becomes more reliant on data, there’s a need for high-speed internet connection, which 5G can provide.
As environmental performance becomes a common qualification for construction projects, contractors are increasingly faced with requests to “show the numbers.” The trend is helping drive the evolution of telematics from a fleet manager’s tool to an essential source of enterprise data.
“A big telematics driver for us is the environmental side,” says Tim Giggee, construction equipment maintenance and repair manager at Blattner Company, a contractor that specializes in alternative energy projects, and a board member at Association of Equipment Management Professionals (AEMP). “That includes idle time, equipment utilization, drive distance, and not letting machines burn fuel for no reason – things that allow us to really sharpen the pencil on the that side.”
The trend is also pressuring equipment OEMs to move telematics from add-on to essential feature.
“In the past, telematics was a nice-to-have, and the aftermarket would fill that void,” says Michael Granruth, business development director at Trimble and AEMP board member. “But today, it has become fairly standard. Every major OEM in the construction space offers factory-fitted telematics. The underlying trend here is that it’s all about the data.”
Equipment managers are getting requests for data from parts of the organization that until recently had little interest in what the equipment was doing.
“There are really three stakeholders here,” says Granruth, “the OEM, the dealer, and the end-customer. The OEM is looking at data for product performance and regulatory issues. For the dealer, it’s about parts and service. For the end user, it’s about productivity and utilization.”
The latter category is by far the most difficult because it involves not only single machines, but the entire ecosystem of machinery on a jobsite. To reduce fuel consumption, for example, it’s necessary to understand what all the equipment is doing so that workflows can be adjusted.
“Telematics used to be all about what a machine is doing,” says Granruth. “Today, you have to look at adjacency – what equipment is nearby, what attachment is the machine running, who is operating the equipment? So, it’s not just about the machine; it’s about the site and ultimately about the business.”
The need to see the big picture is forcing the industry to meet the challenge of consolidating data from multiple equipment and machine control vendors. How to manage mixed fleets is, in fact,
one of the top web queries at SMS Equipment, a Canada-wide Komatsu dealer and service provider.
“Contractors didn’t operate mixed fleets until fairly recently, but today it’s considered normal,” says the company’s smart-construction sales representative, Jeff Martin. “As technology changes and you want different features on different machines, and with the integration of more and more machine control, companies have no choice but to mix now.”
Martin explains that, until fairly recently, mixed fleet management required expensive and cumbersome workarounds.
“The problem with mixed fleets has been that the control vendors use different file types,” he says . “But the industry is standardizing that now, and once this gets figured out we’re going to see a massive increase in mixed fleets.”
“AEMP worked closely with the construction OEMs to develop the ISO 15143-3 telematics standard, which allows aggregators, including companies like Trimble, to present machine data in a unified way to the end customer,” says Granruth. “This was done because the end customer was saying, ‘I want to make decisions based on what’s happening across my mixed fleet.’”
Availability of data, however, is only the beginning. Companies have to be prepared, like their predecessors in manufacturing, to develop comprehensive strategies for sharing and analyzing that data.
“The equipment manager is responsible for the second largest cost for contractors after labour,” says Granruth. “But oftentimes that person doesn’t have a seat at the table for C-Suite level decisions that affect the whole company.”
The Association of Equipment Management Professionals has a certification program for equipment managers that gives them the technical and financial skills to bring telematics decisions into the boardroom. It’s not just executives that need the numbers, however. Data can be a powerful tool for encouraging field personnel to pay more attention to their own impact on the environmental footprint.
“The data can be educational,” says Giggee. “You can tell people not just how much they’re idling, but how much fuel that’s wasting and how that’s impacting the company’s carbon footprint. Once they’re aware of what they’re doing, that’s when the behaviour starts to change.”
Telematics used to be about optimizing performance of individual machines. Today, it’s also about efficient jobsites.
Unlike previous inflationary periods over the past 40 years where specific commodities like fuel or steel have gone up in price, this go-round we are seeing broad-based inflation where almost every product or service in the market is seeing a price jump. Some items have gone up a little and some have gone up a lot.
When it comes to property and casualty insurance, especially within the construction sector, global price increases have been substantial, with prices going up 25 per cent for each of the past four years. These increases have hit construction stakeholders in two ways: first on their practice, or annual, insurance policies; and second, and perhaps more expensively, on their project-specific insurance policies.
When market pricing was falling, most insurance intermediaries (or insurance brokers) could more easily track where the best insurance terms were in the market. In the hard market of the past four years, with insurance prices rising dramatically, it has become more difficult for construction stakeholders and their insurance intermediaries to find the best terms.
Insurance capacity within the global construction insurance market has receded substantially across most relevant construction lines leaving many searching not only for capacity, but improved broking and underwriting methodologies to achieve the best terms from the market.
So, what are these “improved broking and underwriting methodologies” and how are they providing better insurance terms?
Rather than providing an exhaustive list of these methodologies, let’s just focus on a few key vehicles that tend to grow in importance, and in numbers, when a hard insurance market hits the economy.
These vehicles are wholesalers, Managing General Agents (MGAs) and Managing General Underwriters (MGUs).
In many respects, these vehicles are hidden behind the scenes within the insurance industry and their value is often downplayed by those in the primary intermediary role, but they are vital tools that every construction stakeholder should be aware of, should be introduced to, and should incorporate into their risk finance strategies.
A wholesale insurance broker acts as an intermediary between the retail insurance broker and an insurance company. These wholesalers often possess specialized skillsets when it comes to specific lines of cover, which can gain them greater access and/or influence with insurance capacity.
MGAs and MGUs have specialized skillsets that allow them to gain underwriting authority from an insurance or reinsurance company for specific insurance products. They can administer programs, negotiate contracts for insurers, bind coverage and even settle claims.
Insurers provided delegated authority to these MGAs and MGUs because they have specialized underwriting capabilities and/ or proprietary risk management tools that are not available to the insurer. The difference between an MGA and an MGU is the MGA handles all the administrative tasks and the MGU focuses more on providing a platform for selling insurance.
These vehicles have access to specialized talent and solutions that the broader insurance intermediary marketplace does not necessarily have access to. Some may have a specific individual that has a deep understand of specific risks and how to prevent them. Some may have sole access to a technology or methodology that has a proven track record of mitigating insured risks. Whatever the secret sauce of the wholesaler, MGA or MGU, the insurance capacity supporting these vehicles believes they will obtain improved return by deploying their capital through these vehicles.
It is the specialization these vehicles bring to the table that allows them to offer best terms and conditions in the insurance market, and thus help construction stakeholders curb the impact of the insurance pricing inflation that we have seen over the past few years.
If your organization is unfamiliar with these vehicles, you should look into them. Further, if your primary intermediary isn’t harnessing the power of these vehicles in their brokerage strategy, they should be.
In some cases, primary insurance intermediaries (or brokers) are advised by their management to not bring in these specialized vehicles due to organization financial drivers. As a result, these organizations are putting their financial interest ahead of the interest of their clients.
At the end of the day, isn’t it best to have the people with the best knowledge of the specific risk you are looking to insure at the table when seeking to achieve best terms from the insurance marketplace?
editor@on-sitemag.com.With attendees showing genuine interest in the products and technologies on display, exhibitors were happy with the flow on the floor, and the discussions they were able to have with current and potential customers.
“Traffic has been amazing. I am very surprised and impressed on the amount of traffic from open to close on both days. And it’s been engaging. So, there’s been both a quantity and quality engagement with attendees,” stated Carl Seleem senior manager, marketing, at Brafasco, National Concrete Accessories and Brock White. “We’ve spoken to people that are in flat work, as well as in mid-rise and high-rise commercial… everywhere from small to large commercial to multi-family to residential. It’s just nice to see a good mix and everybody ready to just hammer out a good year.”
Over 6,000 members of the concrete, aggregates and construction industries made the fifth edition of the Canadian Concrete Expo (CCE), Canada’s national trade show for the concrete construction industry, the busiest one yet.
The show, held at the International Centre in Mississauga, Ont., on February 16 and 17, had aisles that were filled and booths that were buzzing. In addition to displays from more than 300 exhibitors, the show offered a mix of conference sessions, technology demonstrations, and even a special appearance by mixed martial arts legend Georges St. Pierre, who delivered a message of finding strength and using focus to build forward, both on and off the job.
“We hit record attendance yesterday. And it was by far the best day we’ve ever had at the Canadian concrete Expo,” stated show president, Stuart Galloway, from the show floor on Day 2. “It’s nice to see the trade show industry back on his feet. We weren’t 100 per cent certain where it was going to go after COVID. Were we going to get everybody to come back? Were the sellers going to want to exhibit? It looks like the demand is there for face-to-face.”
“The show attracted a good number of local contractors and crew members… we always enjoy the opportunity to meet and discuss Hydrodemolition with them,” stated Keith Armishaw, Aquajet’s business development manager for North America. “Many of the trade shows I attend are in the U.S., so as a Canadian resident, it was also exciting to attend a show in Canada dedicated to the concrete industry. We hope Canadian Concrete Expo continues to have a solid turnout.”
“It was nice to get face-to-face with some of our existing and bigger customers,” added Sean McElroy, head of marketing and IT at Plastruct Polyzone. “We definitely have had some more traffic compared to last year.”
And if exhibitor feedback is correct, attendees were using the show to research and plan for their upcoming construction season.
“Overall, show attendees were very optimistic about the year ahead,” said Seth Ulmer, sales manager at Curb Roller Manufacturing. “We spoke with many contractors who are either already fully booked or expect to be soon. The Canadian Concrete Expo was an excellent venue for them to prepare for the working season.”
“If Canadian Concrete Expo was an indication of what this year’s trade shows will be like, I believe we’re in for a busy and successful year at the events we attend,” said Troy Steele, Brokk’s regional sales manager for Western Canada.
Plans are already underway for the 2024 edition of the show, which will once again take place at the International Centre. Show dates will be February 14 and 15.
The 2023 edition of Canada’s national concrete show returned to February, and the crowds came out to see all that is new, and to get some advice from MMA legend GSP.
GOMACO offers the full range of concrete slipform pavers, curb and gutter machines, trimmers, placer/spreaders, texture/ cure machines and bridge/canal finishing equipment. GOMACO equipment features our exclusive and proprietary G+® control system, created in-house by our software engineers from the wants and needs of contractors paving in the field. At the heart of GOMACO equipment is our passion for concrete and our commitment to our customers. We look forward to visiting with you about your upcoming paving projects and your concrete paving equipment needs. Our worldwide distributor network and our corporate team always stand ready to serve and assist you.
Throughout history, new processes have come along to improve how people achieve end results. Innovations, even those that eliminate just one step, often lead to dramatic increases in productivity and efficiency.
Developing film is a good example. When digital cameras entered the market, they cut out the step of going to the store to develop a roll of film, accelerating the process of viewing family photos.
When it comes to concrete, monolithic pours are one process that contractors can use to drive efficiency. Monolithic pours streamline concrete work by pouring curb and gutter simultaneously with flatwork, instead of completing these pours one at a time. If completed with the right equipment and considerations, contractors can reap the benefits without sacrificing quality.
A traditional pour most often requires curb and gutter work to be poured, finished and cured to outline the pavement area. Then, the crew returns at another time to pour and complete the flatwork. A monolithic pour, or an all-in-one pour, improves efficiency by completing curb and gutter at the same time as flatwork, saving a considerable amount of time.
Driven to continually seek new ways to keep up with ever-growing demand, more contractors are seeing the benefits of monolithic pours, especially for parking lots and streets. Contractors who streamline the most time-consuming aspects, such as hand-shaping curb and gutter, experience
the most significant spike in efficiency and often double production. Just as the digital camera created a more productive photo development process, monolithic pours can drive up efficiency for contractors.
As contractors look for ways to maximize efficiency, many turn to laser screeds to boost flatwork capabilities. Their ever-wider adoption in the market has significantly sped up the process of screeding large areas of flatwork. But contractors lose the efficiency gained with a laser screed if the curbing work falls behind during a monolithic pour.
Crews that are responsible to shape and
finish the curb by hand typically operate at a slower pace than a laser screed. This can slow the whole operation as they wait for the curb to be completed before moving to the next section. While slipform pavers can be an option, their size may complicate a busy jobsite and they may not be ideal for relatively complex areas of curbing associated with monolithic pours.
Walk-behind curbing machines are able to maintain the production pace of laser screeds while eliminating the physical labour and need for large machinery for curbs. These machines consist of a handle attached to a metal drum that is connected to a hydraulic power source.
The single-operator machines reduce the manual labour needed when shaping the curb and gutter while producing a consistent result, even for operators with minimal experience. While these machines were originally developed for completing curb and gutter work on traditional pours, most can be modified to adapt them for use during monolithic pours.
Newer entries to this class of equipment incorporate battery power and a design specifically created for monolithic pours. These machines combine the benefits of traditional walk-behind curbing equipment with lightweight portability to quickly move throughout the jobsite.
A concrete contractor hired to install a large parking lot for a private company used a laser screed due to the sheer size of the project. Working during the night to limit traffic interference, they were able to pour about 2,000 yards of pavement per night. The operation was limited by the finite amount of curb the crew could shape by hand, however: only 300 to 400 feet
per night. When the contractor invested in a battery-powered walk-behind curbing machine, the crew doubled productivity, shaping closer to 700 linear feet per shift and achieving their target efficiency.
Laser screeds and walk-behind curbing machines are ideal for projects like parking lots — jobs with large amounts of flatwork and multiple areas of curb. However, a single machine that can shape curb and gutter simultaneously with flatwork is more ideal for certain monolithic pour applications like street construction or replacement.
Traditionally, large slipform machines have been the most efficient solution if the project matches the machine design parameters and has enough volume to justify their operation and overhead costs, but new equipment offerings are expanding the options for these jobs.
Some manufacturers offer custom drum options for hydraulic screeds. These
drums, typically up to 16 feet long, are designed to match a specific shape, like half of a street, including the curb and gutter. Custom drums replace the pipe on a hydraulic roller screed and use a spinning motion to shape the concrete.
This monolithic pour method is ideal for streets due to the long stretches of pavement that are the same shape, and it can be convenient for replacing existing streets because it allows one lane of traffic to remain open.
In the past, this was only possible with large, slipform pavers or through manual labour, but a custom drum with a hydraulic screed now provides an additional method to complete the work.
A common misconception is that monolithic pours produce low-quality curb work. This may be true if the crew has little experience in curb and gutter work and is hand shaping the curb while being primarily focused on flatwork, which is the larger
portion of the job. But properly equipped, a key advantage to a monolithic pour is increased all-around quality — if contractors use the proper equipment.
Replacing manual curb work with a mechanized system makes it easy to achieve consistent, spec-matching results, even with an inexperienced crew. The equipment is user friendly and enables contractors to accomplish more with less labour, a key advantage in a difficult employment environment.
A key consideration when determining whether a monolithic pour is the right solution is the weather. Monolithic pours really shine in tough weather conditions. As seasoned concrete workers know, the weather dictates when and how efficiently they can pour. Dealing with a small pour window becomes less of an issue with a smaller number of pours.
With the right equipment, monolithic pours can double or even triple production
and help crews maximize the work they can complete before that window closes.
Despite all the advantages, there are some cases where a monolithic pour is not the best solution. These situations will come into play in colder climates.
If a job uses asphalt for the pavement, the concrete curb and gutter must be poured separately. Additionally, the monolithic pour method is not ideal if the curb and gutter or flatwork may need to be replaced separately. In some regions, freeze and thaw cycles can lead to a shorter life for the curb and gutter than the pavement.
Contractors can maximize their investment in concrete equipment by purchasing machines that increase productivity for a variety of applications. Beyond custom drums for monolithic pours, hydraulic screeds also pair with standard pipes to screed flatwork for jobs such as streets and sidewalks.
Walk-behind curbing machines have multiple drum options and can also complete curb and gutter for traditional pours. Additionally, battery-powered walk-behind curbing machines effectively complete patch and repair work and complement slipform machines to complete corners and tight radii.
The demands of the construction industry are shifting rapidly. There is a high demand for work, and contractors can capitalize on these opportunities by finding innovative solutions that improve their processes and increase their capacity. Monolithic pours are not the answer for every concrete project, but with the right equipment and the right application, a monolithic pour may be what drives an operation to peak efficiency.
At the crack of the bat at the Toronto Blue Jays’ home opener in April, the fan experience at Rogers Centre will be elevated, thanks to some impressive off-season work by PCL Constructors for Rogers Stadium Limited Partnership.
The stadium now features four brandnew outfield neighbourhoods plus a redesigned WestJet Flight Deck, all completed during the first phase of a $300-million multi-year renovation aiming to transform the facility into a ballpark with a modernized fan experience, as well as world-class player facilities.
“PCL and our partners are passionate about bringing the Toronto Blue Jays’ reimagined vision for Rogers Centre to life,” says Monique Buckberger, vice-president and district manager, PCL Toronto. “Following months of preconstruction planning, our team hit the ground running on the first phase of renovations to give the home of Canada’s major league baseball team a new look for the 2023 home opener.”
The first phase began shortly after the final pitch of the 2022 season, starting on October 14 with 35 days of demolition work. Construction of the new areas started on November 14 as work continued six days a week until shortly before the scheduled first pitch on home turf for 2023.
“As soon as our last game was played, we were able to roll up the playing field and remove our outfield walls to use that area as a staging space,” says Sanj Perera, senior manager of project management with the Toronto Blue Jays.
A 200-tonne crane was used for heavy structural removal, while small machinery was used to break up concrete. In total, 2.2 million pounds of materials were recycled from the stadium, including 1.3 million pounds of concrete and 900,000 pounds of steel and metal.
The size of the stadium allowed for multiple projects to progress at the same time, so while demolition was being completed, building was able to start during the second week of November with concrete
being poured in the 500 level and new structural steel installation.
“We were able to bring in pump trucks,” says Perera about the concrete work on the project. “For areas which we could not reach with a crane in this renovation, we used buggies to move concrete. In total, we poured approximately 500 cubic metres of concrete in 160 locations.”
Changes to the stadium include a players’ family room, 5,000 sq. ft. weight room and staff locker rooms at field level; multiple new social spaces, like The Stop bar behind the batter’s eye in centre field and The Catch Bar perched above the visitor’s bullpen; raised bullpens; and two new social decks on the 500 level, the Corona Rooftop Patio in right field and Park Social in left field. Additionally, seats have been brought forward to new outfield walls that will bring fans closer to the game, and every 500-level seat, which dated back to the building’s opening, has now been replaced.
“Creating the new social spaces was the most intensive component of the renovation,
from an engineering perspective,” states Perera. “Key challenges included the cutting of the existing bowl and rakers to open up the concourse sightlines and accommodate new steel structure to support the new social decks, as well as the coordination and installation of steel beams.”
One challenge that did not exist, given that Rogers could keep the roof closed through the winter months, was the weather.
“We were fortunate to be working within an enclosed facility and did not have to accommodate for weather delays,” says Perera. “Having a secure facility also allowed us to procure long-lead items and have them staged on site, which was needed as the construction industry is still experiencing delays on material due to the global pandemic.”
Workers, many of whom could been seen sporting Blue Jays hats, T-shirts and sweaters, were also able to make use of the stadium’s lighting system, allowing them to work into the night, which was a big plus during the shorter days of winter.
With an average of 110 workers on the site in a given day of construction, the Blue Jays fostered the sense of community and pride of a job well done by supporting their efforts with a few extras along the way, like water bottles, hats, and Blue Jays and Rogers Centre stickers to recognize workers’
efforts to create a great fan experience for the coming season.
“We know many construction workers wear that sticker on their hardhat as a badge of honour,” says Perera. “They take that hardhat to subsequent jobs and are able to say they were a part of this amazing project.”
Rogers Centre was conceptualized as a multi-purpose stadium when it opened in 1989 and has not undergone a largescale renovation in its 33-year history. The next phase of the current renovation plan is expected to take place in the 20232024 offseason, with a focus on field level premium clubs and social spaces as well as the clubhouses and player facilities.
Stated Mark Shapiro, president and CEO of the Toronto Blue Jays as he unveiled the renovation plans, “We are committed to building a sustainable championship organization for years to come, and this renovation to Rogers Centre will give new and lifelong Blue Jays fans a ballpark where they can proudly cheer on their team.”
Many construction contracts contain change and amendment provisions governing the circumstances under which change orders will be authorized. More often than not, these change provisions require that payment for work performed outside of the base scope of the contract will only be authorized when both parties to the contract agree and have confirmed that agreement in writing.
In some cases, the change or amendment provisions go a step further and require that only certain individuals or types of personnel within an organization are authorized to approve and sign off on changes and contract amendments.
Such was the case in Whissell Contracting Ltd. v Calgary (City), 2017 ABQB 204 (CanLII), an Alberta Court of Appeal decision considering the circumstances surrounding the proper authorization of changes and amendments in the context of a summary judgment application.
The case involved a subcontract that was entered into between a contractor and its subcontractor on a unit rate basis, with the subcontractor’s overhead and profit being included in the unit rates. The subcontractor alleged that shortly after commencing the work it discovered that the scope of work and site conditions varied significantly from what was expected at the time its bid was submitted. As such, the subcontractor argued that the unit rates included in the original contract were no longer applicable.
At the beginning of the project, the subcontractor submitted field verification sheets to the contractor summarizing the labour, equipment and materials used in respect of the work; however, in the fall of 2010, the subcontractor began issuing force account summaries to the contractor, which included language suggesting that the subcontractor would be paid force account rates, which are typically significantly higher than agreed unit rates, for the work performed in the summaries and that such force accounts were over and above the unit rate values contemplated in the original contract.
These force account summaries were executed by the contractor’s field staff who, according to the contractor, believed that they were executing the summaries solely to verify that the work had been completed.
The contractor admitted that the force account summaries which purported to amend the payment terms had been executed by its field staff, however, it argued that the subcontract required that only certain personnel were entitled to authorize such amendments and that those amendments had not been properly authorized in accordance with the terms of the subcontract.
Furthermore, the contractor argued that as soon as it became
aware of the language purporting to amend the payment terms of the subcontract in the force account summaries, it disputed the validity of the subcontractor’s attempt to amend the payment terms. The subcontractor admitted that the notations on the force account summaries it was relying upon to support the purported amendment had not been negotiated or otherwise discussed with the contractor’s personnel.
Ultimately, the court concluded that the contractual basis upon which the subcontractor was to be paid was not sufficiently clear to award summary judgment. In doing so, the court commented, “There was an issue as to whether or not [the subcontractor] had any reasonable expectation that the notations attached to the force account sheets would operate under these circumstances to amend the written contract.”
In particular, the court appeared to be concerned that the notations on the force account summaries purporting to amend the payment terms of the subcontract had not been negotiated or specifically brought to the attention of the contractor and, in particular, had not been discussed with the personnel that had been involved in negotiating the original subcontract.
Fundamentally, this case emphasizes the importance of understanding the provisions in a contract that govern from whom amendments or changes are to be requested and the steps that must be taken in order to ensure that any amendments or changes are contractually authorized prior to the work being carried out.
As the court was considering a narrow issue for the purposes of a summary determination, it did not consider the impact that might be suffered by the subcontractor in the event that the purported amendments to the payment terms of the subcontract were, in fact, invalid.
Of course, depending on the circumstances of the contract at issue, it is always a possibility that a contractor who carries out change work without proper authorization risks being denied payment for the unauthorized work.
Accordingly, it is important that contractors understand the change and amendment provisions of their contracts and follow the required processes under those provisions prior to undertaking any work outside of the base scope of their contract.
Erin Cutts is a partner in the construction group at Borden Ladner Gervais LLP. This article provides an overview and is not intended to be exhaustive of the subject matter contained therein. Although care has been taken to ensure accuracy, this article should not be relied upon as legal advice.
Meet the International ® S13 ® Integrated powertrain. Now available in the HX™ Series.
After revolutionizing highway driving in the LT ® and RH™ Series, the S13 Integrated is now ready for severe duty work in the HX Series. A huge step forward in performance, design, and operating economy, the S13 Integrated is the lightest 13L in North America. But it still brings 515 horsepower, 1,850 lb-ft of torque, and optional factory-installed PTOs. Not to mention simpler serviceability for more uptime. Now all that’s left to do is get to work. SHIFT