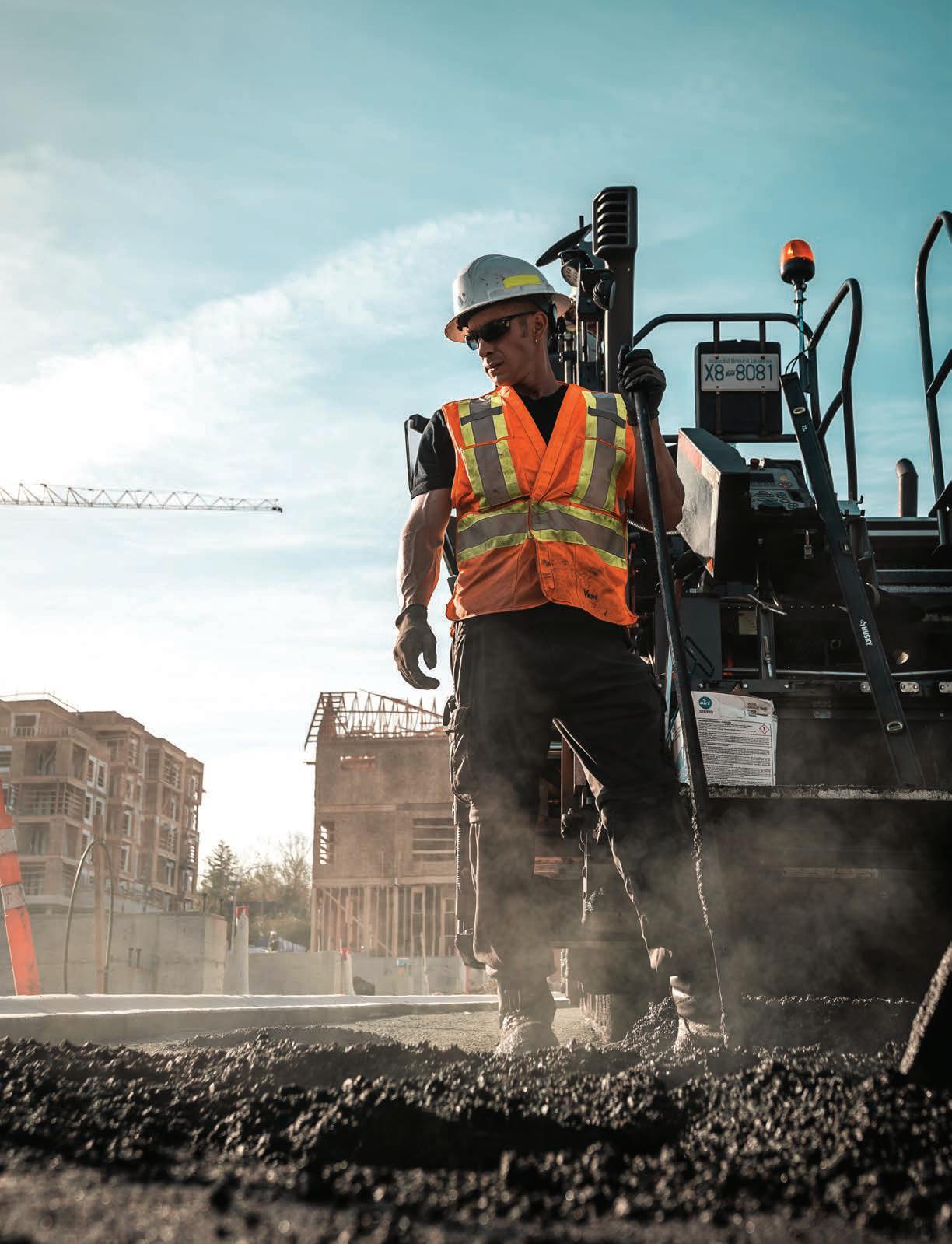
BIG IRON: MOTOR GRADERS AND DOZERS
TECHNOLOGY REPORT: THE PRACTICAL USE OF AI
PROJECT PROFILE: RECLADDING AND RENEWAL
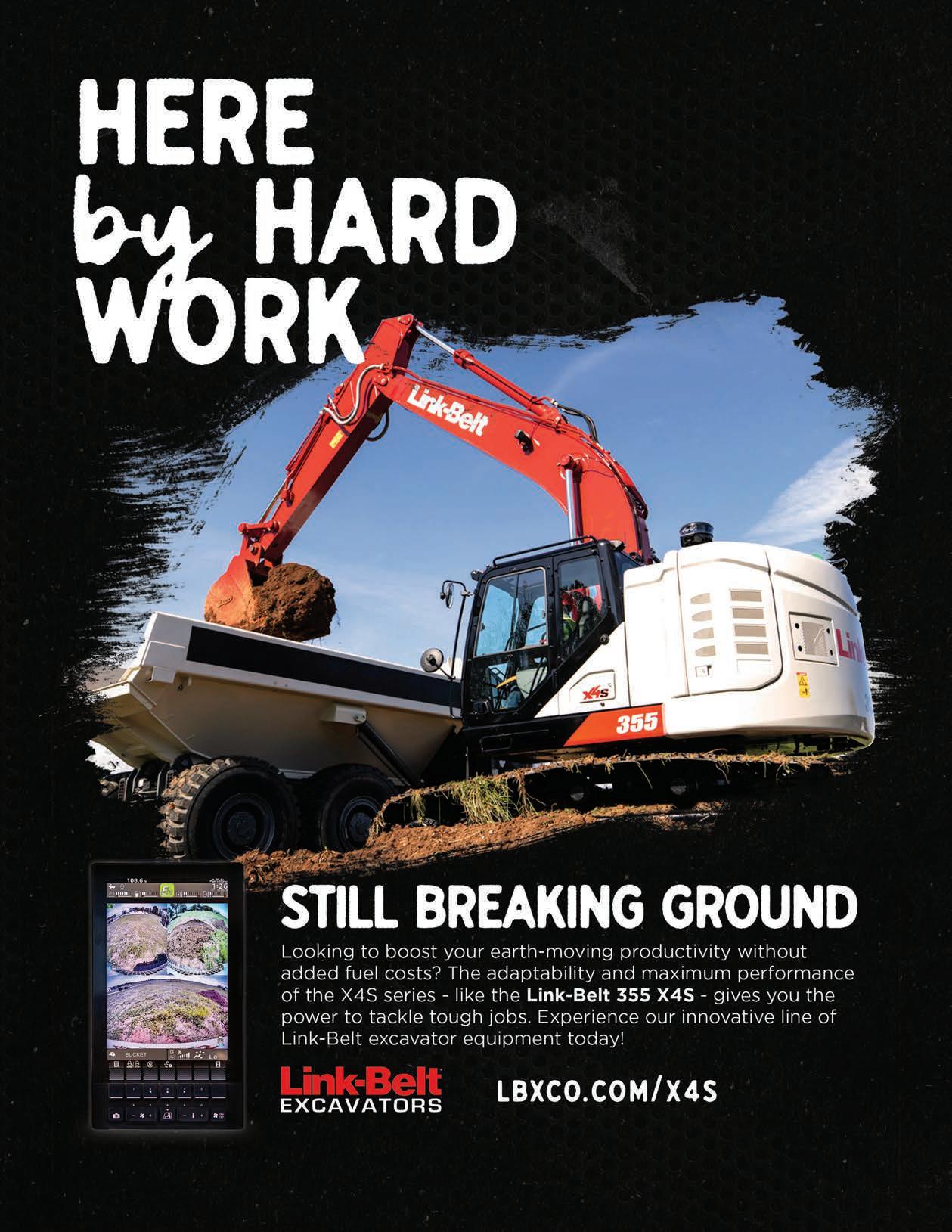
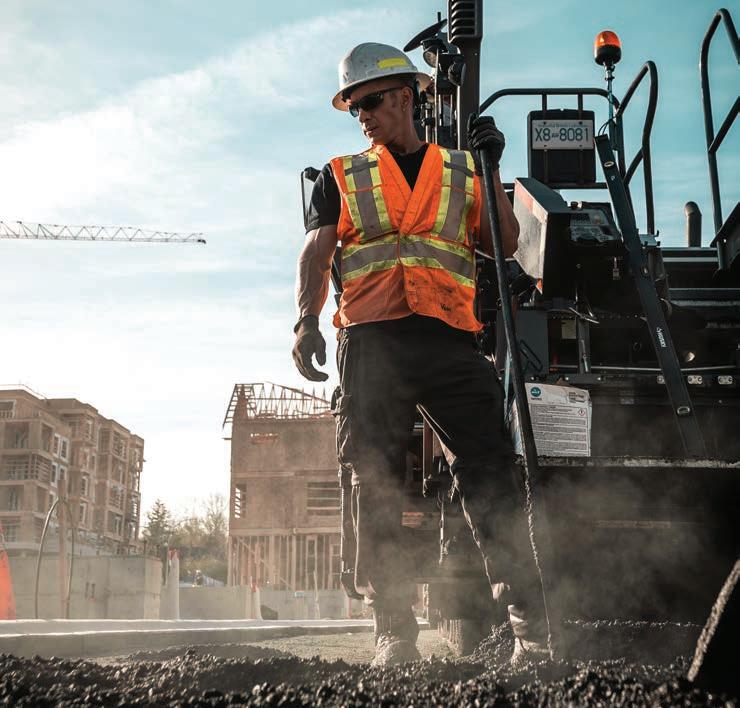

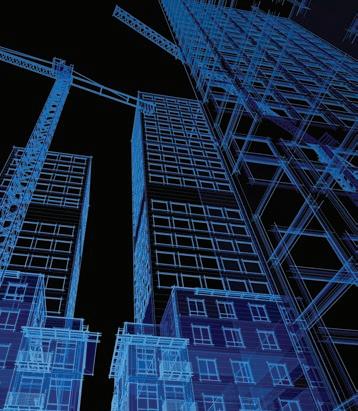
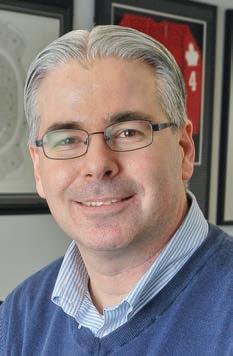
BIG IRON: MOTOR GRADERS AND DOZERS
TECHNOLOGY REPORT: THE PRACTICAL USE OF AI
PROJECT PROFILE: RECLADDING AND RENEWAL
With the uncertainty of an on-off-who-knows-wherethis-goes trade war in the air as we were preparing this edition of On-Site, I thought I’d share a few musings.
I’m not a fan of over-simplified reactions born out of speed to action rather than careful assessment and well thought out calculated risks. As such, it was good to see our country’s list of retaliatory tariffs were rather targeted and potentially less damaging to Canadian wallets compared to the broad-based penalties set out by our trading partner to the south.
That’s not to say that we won’t take our licks in a trade war, but tariffs tend to impact the disposable incomes of taxpayers in the importing country first, followed by job losses at manufacturing plants of exporters, ultimately causing economic pain and increased prices for all consumers on both sides, but it starts with financial penalties to the population in the country that triggers tariffs first, so in this case, the United States.
Perhaps the message that our politicians should be spreading is that if Americans start to feel the squeeze on their disposable incomes, it’s not because of Canada – Canadians can’t add taxes or tariffs in other nations, after all.
www.on-sitemag.com
READER SERVICE
Print and digital subscription inquiries or changes, please contact Angelita Potal
Email: apotal@annexbusinessmedia.com Tel: (416) 510-5113
Fax: (416) 510-6875
Mail: 111 Gordon Baker Road, Suite 400, Toronto, ON M2H 3R1
PUBLISHER | Peter Leonard (416) 510-6847 pleonard@on-sitemag.com
EDITOR | Adam Freill (416) 996-2391 afreill@on-sitemag.com
MEDIA DESIGNER | Lisa Zambri lzambri@annexbusinessmedia.com
ASSOCIATE PUBLISHER | David Skene (416) 510-6884 dskene@on-sitemag.com
ACCOUNT COORDINATOR | Kim Rossiter (416) 510-6794 krossiter@on-sitemag.com
AUDIENCE DEVELOPMENT MANAGER | Urszula Grzyb (416) 510-5180 ugrzyb@annexbusinessmedia.com
CEO | Scott Jamieson sjamieson@annexbusinessmedia.com
Established in 1957, On-Site is published by Annex Business Media 111 Gordon Baker Road, Suite 400, Toronto, ON M2H 3R1 Publications Mail Agreement No. 40065710
ISSN: 1910-118X (Print) ISSN 2371-8544 (Online)
Get the latest construction news!
Follow us on @OnSiteMag
Within our sector, a lot of projects can’t simply stop on a dime, and if the trade dispute continues we can expect to see cost escalations. While it was not a fun time to navigate, one of the positive things that came out of the post-Covid supply chain crisis was an examination of construction contract language, and the need to include clauses addressing prices and other risks.
With almost four more years of uncertainty from Washington ahead of us, those clauses may be lifesaving terms for companies in our sector going forward. If you are not sure if the risk of increasing costs is not addressed in your contracts, it might be a good time to conduct a review of your contacts.
On a more positive note, we are celebrating the industry this issue with our annual photo contest. Be sure to check that out, starting on page 12.
Until next time, stay safe, do good work, and start gathering your photos for next year’s contest.
Adam Freill / Editor afreill@annexbusinessmedia.com
SUBSCRIPTION RATES Canada $50.49 CAD per year, United States $115.26 CAD per year, Other foreign $139.23 CAD, Single Copy Canada $13.50 CAD. On-Site is published 5 times per year except for occasional combined, expanded or premium issues, which count as two subscription issues. Occasionally, On-Site will mail information on behalf of industry-related groups whose products and services we believe may be of interest to you. If you prefer not to receive this information, please contact our circulation department in any of the four ways listed above.
Annex Business Media Privacy Officer privacy@annexbusinessmedia.com Tel: 800-668-2374
Content copyright ©2025 by Annex Business Media may not be reprinted without permission.
On-Site receives unsolicited materials (including letters to the editor, press releases, promotional items and images) from time to time. On-Site, its affiliates and assignees may use, reproduce, publish, re-publish, distribute, store and archive such unsolicited submissions in whole or in part in any form or medium whatsoever, without compensation of any sort.
DISCLAIMER This publication is for informational purposes only The content and “expert” advice presented are not intended as a substitute for informed professional engineering advice. You should not act on information contained in this publication without seeking specific advice from qualified engineering professionals.
MEMBER OF
Set for March 11 to 14, the 2025 Canadian Construction Association (CCA) Annual Conference will bring some 500 construction professionals to Quebec City for an exceptional line-up of speakers, engaging breakouts, and valuable networking opportunities, all within the intimate setting of the historic Fairmont Château Frontenac.
The event kicks off on the 1th with an opening keynote featuring freelance political journalist Chantal Hébert, whose Charting the future: Canadian politics in transition, presentation promises to be lively as timing will see a new Liberal Party leader be announced just days before she takes the stage – just one of several topics she will explore as she shares her expert insights into Canada’s evolving political landscape.
Among the key sessions on the Wednesday will be the CEO power lunch, as Patrick Lamarre, president of Kiewit Canada Group Inc., and Heather Masterson, president and CEO of Travelers Canada, join CCA president Rodrigue Gilbert for an exploration of emerging business trends and growth opportunities in a
rapidly changing market.
Paul Smetanin, president of the Canadian Centre for Economic Analysis, will follow that with a presentation delving into how politicalization, questionable leadership and the misuse of resources has exposed the construction industry to significant risks.
And back for another year, but always a favourite program, is the Innovator’s Pitch: CONtact Mentorship. Sponsored by Pomerleau, five new innovators will be vying to be voted the most promising innovation this year, with live voting from the convention floor.
In addition to the conference, the CCA event will play host to a number of pre-conference business meetings. The National Advisory Council meetings and the CCA Annual General Meeting are open to delegates who have pre-registered, although voting at the AGM is only open to CCA members.
For more details about the conference, including a full schedule and details on registration, hotel, and travel arrangements, visit www.cca-acc.com.
At Kubota, we’ve been building a legacy of excellence for the past 50 years. No matter the job on the build site, ambitious plans can become reality with the help of tough, versatile equipment and attachments from Kubota.
It was a logical choice with Acumatica we can communicate and integrate with other tools easily which is a big plus as we use tools like Procore, Excel, ProEst and Building Connected.
Citing growth potential in major markets, and significant civil infrastructure experience and geographical reach, Javier Sevilla, CEO of FlatironDragados, recently announced that Flatiron and Dragados North America have successfully integrated to form FlatironDragados. Plans for the merging had been announced by shareholding companies Dragados, S.A., and Hochtief in July of last year. Dragados owns 61.8 per cent of the integrated company, with Hochtief owning the other 38.2 per cent.
FlatironDragados is a major partner in the Bridging North America joint venture building the Gordie Howe International Bridge via a P3 contract.
“With the successful integration of FlatironDragados, we are set to redefine engineering and construction in North America, unifying the complementary strengths of two industry leaders to deliver outstanding outcomes for our clients, people and communities,” stated Juan Santamaría, chief executive officer of ACS Group (parent company of FlatironDragados) and Hochtief. “Through strengthened collaboration and an expanded geographic footprint, we are more equipped than ever to deliver complex, large-scale projects across the United States and Canada.”
Sevilla is the new entity’s CEO, while Peter Davoren serves as chairman, a role he holds in addition to his role as chairman and CEO of Turner Construction Company. And while new in name, the company is building on a significant history and a strong backlog. FlatironDragados, which has an established presence in 24 U.S. states and eight Canadian provinces, says it entered 2025 with a backlog of US$18.5 billion. Combined revenues for 2023 were US$6.1 billion.
With the integration of the two companies, FlatironDragados says it has become the second largest civil engineering and construction company in North America.
The Ontario government has approved Ontario Power Generation’s (OPG) plan to proceed with the Project Definition Phase, the next step toward refurbishing Pickering Nuclear Generating Station’s “B” units.
As part of the preparation for refurbishment, the government has authorized OPG to sign a $2.1 billion contract with CanAtom, a joint venture of Aecon and AtkinsRéalis, for early engineering and procurement to prepare for the execution of the Retube Feeder and Boiler Replacement Program.
“The Pickering Nuclear Generating Station has powered cities and towns across Ontario with affordable, reliable and zero-emissions electricity for more than 50 years,” said Stephen Lecce, Minister of Energy and Electrification. He added that the refurbishment would “provide the
affordable and reliable power our province will need for decades to come.”
Once refurbished, Pickering is expected to produce more than 2,000 megawatts (MW) of electricity, equivalent to powering two million homes, to help meet increasing demand driven by electrification and the province’s economic growth. Based on OPG’s preliminary schedule, the refurbishment is anticipated to be completed by the mid-2030s.
A selection of data reflecting trends in the Canadian construction industry
Investment in building construction edged down slightly in November, reports Statistics Canada. The 0.5 per cent slip brought investment to $21.4 billion for the month. This followed a 1.1 per cent decrease in October. Year over year, investment in building construction grew 2.7 per cent in November.
The monthly decline from October was driven by the residential sector, which fell $168.1 million to land at $14.8 billion. This drop was partially offset by a $71.5 million gain in the non-residential sector, which came in at $6.6 billion. The retraction in November’s residential building investment figures was the result of a 4.8 per cent drop in multi-unit dwelling construction, much of which was attributed to Ontario.
Non-residential construction investment reached a record high in November. The $6.6 billion posted marked the fourth consecutive monthly increase. By segment, the industrial component increased 2.2 per cent to $1.4 billion; commercial construction edged up 0.4 per cent to $3.3 billion; and the institutional component rose 1.5 per cent to $1.9 billion.
The total value of building permits issued in Canada decreased by $739.5 million in November, falling to $11.7 billion, reports Statistics Canada. The 5.9 per cent dip was a second consecutive monthly decline, but permits remained 5.1 per cent higher than November of 2023 thanks to strong gains in two of three non-residential segments.
On the residential side, the total value of permits decreased by $588.1 million, or 7.5 per cent, in November, coming in at $7.2 billion. A more than half-billion-dollar drop in multi-unit construction intentions drove the decrease, although the single-family component also contributed to the decline.
The non-residential sector saw mixed results as well, as the combined ICI segments weathered a 3.2 per cent drop in November, coming in at $4.5 billion, $151.4 million lower than in October. Overall, the industrial component fell more than 20 per cent on the month to land at $901 million, while the institutional and commercial components increased to come in at $1.6 billion and $2.1 billion, respectively.
Compared to November of 2023, the industrial segment was down 2.2 per cent, the institutional segment was up 10.6 per cent, and the commercial segment was up 18.6 per cent.
Total Employment in Canada
20,738,300 Unemployment Rate
6.7% Construction Employment
1,605,400
Canada’s employment ranks increased by 91,000 in December, mostly in full-time work, reports Statistics Canada in its most recent Labour Force Survey. The gains followed an increase of 51,000 in November and are the third employment gain in the past four months. Last year ended with 413,000 more people working in December compared with 12 months earlier. Employment in Canada’s construction sector trended in line with the overall picture, rising 0.4 per cent from November to add 6,100 workers to the employment ranks. Compared to 12 months earlier, employment figures for the industry grew 1.5 per cent, adding 23,700 workers over December of 2023. Seasonally adjusted, there were 1,605,400 workers in the sector in December of 2024.
A comprehensive renovation at TD Centre’s 95 Wellington Street, inside and out, brings an update in comfort, looks and performance.
BY ADAM FREILL
Looking to pull 95 Wellington Street West into a modern aesthetic of design, Cadillac Fairview brought in WZMH Architects and PCL Constructors Canada for a project that has breathed new life into the building, inside and out.
The 23-storey office tower in Toronto’s downtown core was built in the mid 1980s and was navigating an existing cladding system close to the end of its lifespan.
As the building owner, its architect and its general contractor explored the state of the structure’s exterior, Cadillac Fairview was also exploring a separate plan to update the lobby. Deciding it would be best to link the two projects, the choice would put them on a path towards an even more robust renovation, one that would include updates to the roof, walls and lobby, but all to the betterment of the structure and its users.
“It was an unexpected opportunity where it all started with a routine inspection of the cladding system. Through that process, we discovered a level of degrading of the of the envelope structure from within, and that that led to further investigation,” explains Carlo Guido, senior director of project management and development at Cadillac Fairview. “We contemplated a lot of different things to do with the building. It wasn’t that old, and it
was a building that we had purchased, as opposed to developed and built ourselves, so we ran through a lot of options. PCL helped us develop those options. Ultimately, keeping it in place and recladding it to make it better than it was before is what we landed on.”
“When you talk about repurposing or refreshing buildings like this, there was an option at one point to consider whether to take the thing down and restart,” says Mark Henderson, manager of sustainable retrofits and decarbonization at PCL Constructors Canada. “The greenest buildings, or the lowest carbon buildings, are the ones that already exist, however.”
Aiming to update rather than to replace, WZMH’s team dove into design meetings and presentations of building renderings, detailed building sections and technical detailing in the search for a style that would align with its client’s desire to enhance the overall appearance of the building.
While the building is part of the Toronto Dominion complex, it differs significantly from the other TD towers in proportion, massing and façade detailing, facts that played into the design considerations. Working with a plan to make the building stand out in a sea of tall buildings, the companies explored a number of material options and
styles before deciding the contrast of a white granite was exactly what was needed.
“The old building was an old pink granite building, inside and out, and now it’s a stark white contrast to its cousins… the Toronto Dominion Centre’s Mies van der Rohe black towers,” says Guido. “It looks incredibly different.”
“Interior material selections and design
direction was somewhat easier because [by then] the exterior design was done, and those things could be carried inside,” says Jee-Young Kang, principal at WZMH Architects. “But for the exterior, there were a lot of design options, and even the consideration of other materials such as metal and spandrel glass.”
The Bethel White granite stone selected was chosen for its sustainability, along with its strength and durability – the hope is for the cladding to last at least 50 years.
“With the way the envelope had deteriorated, we weren’t sure if a traditional envelope system would be able to just go back in place,” explains Henderson.
“We ended up going through an entire envelope, roof, exterior redo,” says Guido. “We decided the lobby needs to speak to the exterior, and so we delayed that a little bit until we figured out the exterior component, and then we integrated a full lobby refresh to align with what we were doing on the outside.”
Once the existing exterior granite panels were removed, new insulation and air and vapour barriers were installed to enhance the envelope’s thermal performance before the heavy lifting of the new granite took place. The installation crews made use of mast climbers on all four façades of the structure for that task, and panels were built to fit the
building as well as the climbers used during the installation process.
“You couldn’t make them too big, otherwise you couldn’t actually get them up in the climber comfortably with a few individuals,” says Guido. “It was all staged with a forklift, and that platform had to not only sustain the weight of the stone, but also a forklift driving around so that it could actually feed climbers. It was a pretty delicate system that actually worked really well.”
One of the biggest challenges to overcome was working in a busy downtown core, as PCL and its trade contractors navigated tight sites while looking to minimize disruption to neighbouring properties and tenants. “We want to try to be invisible,” says Henderson. “We want to try to work behind cloaks or work behind the scenes, and really try not to disrupt anybody. If they can hear us and they can see us, and we’re causing an issue, that’s a problem.”
On the exterior, the old mounting system was replaced with a hanging clip system that will help with any future need to maintain the cladding.
“You can technically replace any piece of stone anywhere on the building without it relying on its neighbour,” says Guido. “That gives us longevity, and it gives us the ability to service what’s behind the façade without spending too much money doing it.”
Knowing that the building will need its windows washed and occasional other exterior maintenance, a track system with a small crane was added to the roofing project.
“We spent some money now to do it right, and it’s going to save us in the future,” explains Guido.
Along with the new maintenance system, expanding the focus of renovation beyond the lobby and cladding afforded Cadillac Fairview the opportunity to upgrade what’s behind the façade, bulking up the wall system with more insulation and a self-adhering water vapour barrier, all of which was tied into the roof, which was also upgraded.
As he states, “Waterproofing, more insulation and everything’s tighter… all of those come with the opportunity of a reclad.”
One of the finishing touches on many projects is paving, and that was no different with Zenterra Developments’ Solana community, part of the Willoughby neighbourhood of Langley, B.C. The $60 million project brought together a crew of 80, including contractors, sub-trades and a general contractor to build an award-winning community.
With steam rising from the asphalt, a photographer from BeFound Media Inc. captured the paving crew in the thick of putting down the final touches, and looking large and in charge while doing it. The resulting photo was selected by this year’s judges as the top shot from a field of almost 150 photos that were submitted for the 2024 Canadian Construction Photo Contest, as presented by On-Site Magazine
“This photo captures a simple but powerful moment. The morning sun hit the steaming asphalt as the foreman took a wellearned break. The light, the heat, and the hard work all come together in a shot that feels real and timeless,” said Zenterra vice-president Derek Fenton. “It’s a great reminder of the hard work and teamwork that goes into every Zenterra project. This photograph beautifully captures our commitment to quality and the effort our teams put into building lasting communities with care and integrity.”
As is tradition with our contest, a donation has been made in the company’s name to a charity of their choice. This year we are proud to recognize the winning photo with a donation to Surrey Schools Meal Program.
Well done, Zenterra! And keep those photos coming.
Anyone who has served as a judge for this contest can attest, that it is not easy to select a winner. As such, we would like to also recognize a number of honourable mentions from the photos received this year. These, and some of the other submitted photos may find their way into future editions of the magazine. To everyone who submitted photos, thank you for sharing these moments from your jobsites, and for taking the time to send them our way. The diversity of work was great to see, as were some of the impressive settings in which some people get to ply their trades.
The contest will return again next year, so please keep your cameras rolling throughout 2025. The next contest will launch in December and you can’t enter a photo that was not captured. Happy, and safe, shooting!
On the job, at Zenterra Developments’ Newbury community. Roadways are what connect a community, and a photographer from BeFound Media Inc. was on the scene as paving of these critical connection points was underway in the Willoughby neighbourhood of Langley, B.C.
Company: Zenterra Developments
Photographer: BeFound Media Inc.
Location: Langley, B.C.
Choosing one winner from a field of almost 150 pictures is never an easy job, especially when you are looking to choose a shot that is dynamic, represents the industry, and also works well in digital formats as well as on the printed page. Once again this year, there were a lot of great shots in the photos submitted. Not surprising is that the stack of submissions had our judges debating selections right down to the wire. We would like to extend our thanks to everyone who took the time to share their pictures. There were a lot of impressive shots of hard work and great scenery sent our way. Congratulations to our overall winner for their great shot from Langley, B.C. And congrats, also, to the following honourable mention winners.
Crews work diligently throughout the overnight hours in Montreal to pour the new deck for the Saint Laurent Boulevard overpass, as the deck finisher smooths the concrete amidst a brand-new pour.
Company: Construction Demathieu & Bard (CDB) Inc.
Photographer: Andreas Pandikiu
Location: Montreal, Que.
While on nightshift for a creek bypass/riverbank remediation job, workers were treated to a rare spectacle of Lady Aurora absolutely exploding in the sky. Graham Charles, who managed to capture the aurora borealis that night, says the camera shots looked less intense than real life.
Company: Farlinger and Associates
Photographer: Graham Charles
Location: Whitecourt, Alta.
Building a vertical village at 544 King St. West in Toronto: Boasting Elton John as a future resident, this 16-storey, 800,000 sq. ft. project will include 440 residential units, commercial spaces, public areas, rooftop terraces and a park.
Company: RJC Engineers
Photographer: Anna Wdowczyk
Location: Toronto, Ont.
In March, Zenterra Developments continued work on the Commons, a 199-unit condo community located in Willoughby, in Langley, B.C. Here, we see the Tower 2 crane being installed against the stunning backdrop of Golden Ears Provincial Park.
Company: Zenterra Developments
Photographer: BeFound Media Inc.
Location: Langley, B.C.
Rising high above the surrounding lands, the Apuiat Wind Farm is a flagship EBC project illustrating the company’s commitment to innovative, environmentally friendly and forward-looking projects. It is located on the traditional territory of the Uashat Mak Mani-utenam First Nation, the Nitassinan, near Port-Cartier, Que. The wind turbines stand at a height of 119 metres.
Company: EBC
Photographer: Reference Media
Location: Port-Cartier, Que.
Moving materials for the ONE at One Bloor St. West in Toronto, a stunning mixed-use project that is three-quarters of the way to its full height. Completion is anticipated in 2027.
Company: RJC Engineers
Photographer: Cora Pulnicki
Location: Toronto, Ont.
Less than a month after tunnel boring machine (TBM) Rexy broke through to the extraction shaft, the second TBM digging the western underground segment of Toronto’s Eglinton Crosstown West Extension, Renny, emerged from the tunnel and completed its two-year, 6.3-kilometre journey.
Company: Metrolinx
Photographer: Lisa Kannakko
Location: Toronto, Ont.
In March 2024, Montreal’s landscape was transformed with the installation of the final sections of the skybridge that connects Royalmount to the De La Savane Metro station. The work involved closing Montreal’s busiest highway and the use of one of the largest cranes available in North America.
Company: Carbonleo
Photographer: Marc-Aurèle Courchesne-Paré
Location: Montreal, Que.
Tasked with installing bird netting on the Ironworkers Memorial Bridge as part of a major coating project, workers completed the project with minimal traffic disruption, while helping to preserve the bridge’s integrity for years to come.
24_014598_OnSite_Magazine_FEB_CN Mod: December 27, 2024 12:29 PM Print: 12/27/24 4:24:41 PM page 1 v7
IN STOCK
ORDER BY 6 PM FOR SAME
Company: Tatras Group
Photographer: Tatras Industrial Ltd.
Location: North Vancouver, B.C.
Backgrounded by Toronto’s iconic skyline at dawn, construction activity at the CAMH Community Centre is highlighted by pops of yellow and misting for dust control as Priestly Demolition sorts materials and Michael Bros Excavation prepares the site for shoring.
Company: PCL
Photographer: Katie Dalla Pozza
Location: Toronto, Ont.
Shot at the Yarmouth yard rail spur site, which will connect the CN rail line to one of Ontario’s newest battery plant sites, crew members are ensuring the steel is correctly positioned before the pile driver drives the steel into the ground.
Company: Amico
Photographer: PAVIC
Location: St. Thomas, Ont.
An team of ironworkers from Universal Structures takes a brief pause after placing the first part of a bridge crossing Autoroute 20.
Company: Universal Structures
Photographer: Pierre Seager
Location: St. Louis, Que.
Showcasing the serene beauty of the worksite at dawn, Mark Krampitz captured a breathtaking sunrise over Orion’s IndustriCore project.
Company: Orion Construction
Photographer: Mark Krampitz
Location: Richmond, B.C.
BY NATE HENDLEY
For all the buzz about compact equipment over the past few years, large size dozers and motor graders still offer unmatched power, productivity and durability for a variety of construction applications.
“Motor graders are mobile, versatile machines that can be used for more than finish-grade work. They can also be used for moving material, cutting ditches, cutting back slopes, high bank slope work, cutting passes, material spreading and haul road/ loading area maintenance,” explains Eric Kohout, product application specialist at Caterpillar. “The motor grader is also an
excellent machine for processing materials to mix and incorporate different materials if needed.”
He adds, “The size of the site and the time required to complete a job will determine the best [motor grader] for the job and its applications … If more blade pull and blade down force are needed, then a larger machine may be required.”
In a similar manner, Matt Costello, product marketing manager at John Deere, notes, “All dozers have their place. The jobsite you’re going to be on typically is going to determine the size of the dozer you’re going to have on it.”
Beyond choosing the right-sized machine for the requirements of the job, maintaining the equipment is a must-have best practice, advises Carlos Martinez, product manager for dozers and motor graders at LiuGong North America. “Maintenance is the cornerstone of reliability for all dozers, whether large or compact,” he says. “For optimal performance, routine checks and proactive servicing are essential to keep these powerful machines running at their best.”
The same advice obviously applies to motor graders. Dozers and graders alike have also been impacted by industry-wide trends.
“Safety features and tech enhancements are a big player in the construction [sector] right now,” states Costello.
It is not an industry secret that the volume of construction workers who are reaching retirement age is outpacing the number of young people who are entering the sector to take their places. Since contractors can’t afford to spend years training new operators, user-friendly high-tech features can help fill the labour gap.
“Automation is already making its way into graders, reducing the number of inputs an operator needs to complete tasks,” explains Costello. “Technologies that help novice operators get more out of the machine faster, while enhancing the skills of seasoned operators, allow the focus to remain on the task at hand rather than on learning the machine.”
With this in mind, here’s a look at what’s new and/or noteworthy in large motor graders and dozers:
John Deere’s biggest motor grader, the 872G/GP has an operating weight of 47,620 lb. (21,600 kg), a 300 hp engine, and a blade pull of 49,500 lb. (22,453 kg).
“One standout feature is the Adjustable 6WD (six-wheel drive). With the hydrostatic motors in the front wheels, the systems can be adjusted on the fly for varying ground conditions or work on slopes. By simply turning a dial to the desired ground condition, the aggressiveness of the front wheels accommodates to the ground condition to maintain productivity,” says Costello. “This also allows an operator to utilize the full weight of the grader when working with the blade.”
A Grade Pro (GP) option “equips the machine with EH controls and offers a choice of mini joysticks that replicate the feel of an antler rack or T-handle joysticks, which are intuitive and user-friendly for operators,” he continues.
Automation solutions on the 872G/ GP motor grader include Auto Articulation, which Costello says combines front steering and rear articulation through a single control; Blade Flip, which is an exclusive solution that allows operators
to automatically rotate the blade to a predetermined angle; machine presets; and Auto-Shift Plus, which Costello says “allows operators to seamlessly transition from a stop to full speed without shifting or using the inching pedal.”
In February of last year, John Deere introduced the 950 and 1050 P-Tier Large Dozers, an evolution from its 950 and 1050K machines.
The 950 P-Tier weighs between 65,300 and 73,700 lb. (29,606 to 33,431 kg), offers 265 to 280 hp at 1,800 rpm, and has a 184-inch (2,134-mm) blade. It’s the largest dozer in the industry with a six-way Power-Angle Tilt (PAT) blade, says Costello.
Capable of performing bulk or mass excavation activities, the 950 P-Tier can also be fitted with the 3D SmartGrade system for precise, speedy grading, he continues.
At 94,000 to 94,580 lb. (42,640 to 42,900 kg), with a JD14 engine capable of 354 hp at 1,700 rpm, the 1050 P-Tier is John Deere’s largest dozer used for construction work. The blade is 168 inches (1,727 mm) and has been moved back 17 inches for improved visibility. The cab has been built with more glass for the same reason.
The 950 and 1050 P-Tier both boast dual path hydrostatic transmissions, which enables dynamic braking for increased safety and stability. Additional features include standard LEDs, ergonomic joystick controls and automatic temperature controls.
Other shared features include a load-sensing system that allows the machine to adjust based on the load in
front of it. “The engine and transmission adjust together, so we’re only giving power to the blade and tracks when it’s needed to maintain productivity and enhance fuel savings,” says Costello.
LiuGong offers a series of motor graders with Tier 3 engines that are suitable for road construction and grading applications, but “the 4215D, which features a T4f/V engine is the only model available in North America due to engine emissions regulations,” states Martinez.
Weighing 39,683 lb. (18,000 kg) and capable of 225 hp at 2,200 rpm, the six-cylinder 4215D features a fuel saving, six-speed forward, three-speed reverse ZF powershift transmission, and spacious cab, which the company says ensures operator comfort on long shifts. Maximum travel speed going forward is 27.3 mph (44 km/h), and 19.9 mph (32 km/h) going backwards.
In terms of working capabilities, the 4215D has a 14-foot (4,270 mm) moldboard that’s adjustable for precise grading, and capable of 600 mm, or roughly two feet, of lift above ground. The machine also offers a maximum draw pull of 22,031 poundsfoot, or 98 kN, and 19,290 lb. (8,750 kg) of cutting pressure.
“Our motor grader is equipped with rear camera, full panel controls in the armrest … We have attachments like front dozers, scarifier, ripper, etc., making the machine very flexible for many types of jobs,” says Martinez. These jobs can include road construc-
Sized right for tight spaces. Steel-built for heavy-duty work. With groundbreaking power in a nimble package, Takeuchi Compact Excavators are proof positive that it’s not the size of the machine in the work, it’s the size of the work in the machine.
THE MARK OF TOUGHNESS
tion and maintenance, among others.
The Dressta TD-25M, meanwhile, represents “the pinnacle of our heavy-duty crawler range, specifically tailored for the North American market,” he continues.
Weighing between 90,940 and 92,410 lb. (41,249 to 41,916 kg), the company’s flagship TM-25M crawler dozer has a fuel-efficient 375 hp Cummins QSX15 engine and offers 794 kN of drawbar pull. The machine also boasts a two-speed steering drive system that can prove handy for difficult slopes, along with LED lighting, standard rear-view camera set-up, two side doors, and tinted glass in the cab to enhance visibility and reduce glare.
“Our Dressta dozers are engineered with heavy-duty applications in mind, boasting the highest drawbar pull force in the industry. This strength, combined with their robust design, makes them ideal for demanding environments like mining and construction,” says Martinez.
“The machine is Trimble-ready, offering seamless integration for advanced telematics solutions. We also provide an automatic lubrication system to ensure optimal performance and minimal downtime. Additionally, if customers require specialized attachments, we offer customized solutions to maximize the machine’s functionality,” he adds. “Maintenance has been simplified with a modular design and essential points like filters and oil fill locations are easily accessible, saving time and increasing productivity.”
Caterpillar has multiple motor graders that are well-suited for construction work,
ranging from the company’s 120 GC to the model 18.
“The 120 GC and 120 are purpose-built frame machines that are very agile and work well in more constrained environments,” says Kohout. “The 140, 150 and 160 are excellent, all-around choices for all motor grader applications. The 14, 16 and 18, are larger frame machines with excellent downforce for a larger project or jobsite, bulk material movement, haul road maintenance, as well as many other applications.”
As the largest machine in Cat’s motor grader construction fleet, the six-cylinder model 18 has an operating weight of 74,324 lb. (33,712 kg), 18-foot moldboard, and 304 hp base power. An adjustable electric arm rest, information display touch screen, joystick hydraulic controls for transmission, implements and steering, and leftand right-side lights come standard.
Safety features on model 18 include a rearview camera, LED enclosure service lights, and a fire suppression system.
Productivity is enhanced through a fuel-saving Eco mode, which reduces high idle engine speed without sacrificing machine power, a modular cooling package that allows for easy removal and installation of cooling system components, reducing service time, and a front guard that protects the front axle from debris and rocks.
Caterpillar has been introducing new features on its 140, 150 and 160 joystick graders as well, says Kohout. These include a 10-inch touchscreen display that includes HD rear vision camera images and Planned Maintenance Alert Sync, which alerts the operator to needed maintenance.
The company has also been tweaking its optional Cat Grade solutions. The Cat Grade Attachment Ready option now boasts a side shift position-sensing cylinder for the moldboard, while Cat Grade Cross Slope Assist has been upgraded. Upgrades include sensors and a moldboard side shift positioning cylinder, to augment versatility and 2D Grade accuracy. An E-fence solution is also available for graders fitted with Cat Grade Cross Slope Assist.
“E-fence can be utilized to protect the drawbar from contacting the link bar and/ or limit the moldboard angle to prevent the moldboard from contacting the front tires, tandem tire or ladder,” explains Kohout.
Nate Hendley is a freelance writer and author, and is a regular contributor to On-Site Magazine.
Sean Smithson is a big proponent of the positive effect the building sector can have on society, and that belief helps drive his plans for Pomerleau’s GTA region.
An industry veteran with almost 20 years experience as a sub-trade, Smithson joined Pomerleau in July 2023 as the Regional Vice-President of the Toronto office. Charged with growing Pomerleau into a top player in the GTA and beyond, Smithson’s enthusiasm is palpable and infectious.
“I’m passionate about the impact that construction has on the world around us,” he says.
Building infrastructure in a manner that considers community needs, sustainability and innovation—is at the heart of Smithson’s vision.
“Each project we take on starts with
transparency and collaboration. We truly become partners with our clients and trades to deliver the amazing work. This, paired with our vast wealth of talent and experience, is our recipe for success,” he explains.
Smithson believes another one of Pomerleau’s strengths is its ability to tackle jobs ranging from complex infrastructure projects all the way to smaller, often retrofit work.
A prime example of the former type of project, and one that will have far-reaching benefits for the local community, is the City of Hamilton’s bus maintenance and storage facility (MSF Hamilton project). In response to a tender from the city, the company is helping Hamilton address overcapacity issues at its existing facility and provide space to grow as the transit network develops. This project helps meet the city’s transit goals by employing an expandable design that will allow Hamilton to scale up as its population
increases.
The MSF Hamilton project team encountered some unforeseen site conditions that could have created a setback, but by leveraging their extensive experience, were quick to document the issues in a transparent manner and work together with the City, consultants, trades, and testing agencies to address the concerns and keep the project on track. By reclaiming concrete from the demolished warehouse and industrial building structures and using it as backfill in various locations on the project site, the company was able push its environmentally friendly agenda even further.
“Very early on we established a sense of trust and collaboration with our clients and partners,” says Nuno DaSilva, Project Director at Pomerleau. “They quickly understood that we were here to work as a team for the project.”
This project is yet another example
of how construction can affect the community in a positive manner.
“With our growing population, transit infrastructure is going to be a major area of growth going forward,” Smithson says. “Having a successful project of this magnitude under our belt will enable us to do more of these projects in the future.”
Another key component of Smithson’s strategy is to increase the company’s capacity to tackle small- and medium-sized projects in the educational, industrial, healthcare and commercial sectors.
Pomerleau’s GTA region recently launched the Special Projects Division (SPD), which provides the company with the agility to take on smaller and shorter timeline projects (18 months or less) such as retrofits and facility upgrades.
“The SPD allows us to be more nimble, broaden our reach and solidify relationships with existing clients,” Smithson explains. “Shorter project timelines also present an excellent opportunity for our young professionals to gain comprehensive, full-cycle exposure to construction projects, and develop the ability to solve problems quickly by working collaboratively with our clients and partners.”
One such client is the University of Toronto, with which Pomerleau has a long history, having completed Harmony Commons, a certified Passive House student residence, and the Academic Tower, currently under construction and expected to be the tallest academic mass timber structure in Canada.
The SPD is currently involved in the first phase of an eight-stage project to upgrade the University of Toronto’s Hart House over the next decade. Not only is the project a challenge because of the historical nature of the building, but the facility needs to remain open during the renovation.
Working closely with the university, Pomerleau came up with a variety of planning strategies, including safe al-
ternate pedestrian routes and signage, to minimize the impact on student activity while also protecting the integrity of this heritage site.
“Our team works with clients to come up with solutions to restore the beauty of our historical buildings,” says SPD Director Marius Tawembe.
“Our vision is to make the complex simple, reimagine, build, and elevate the experience for clients and partners working with us—and for the people who will work and play in these spaces.”
Smithson says that Pomerleau’s ability to combine comprehensive expertise in constructability, efficient schedule development, tailored design solutions, and a strong trade partner network successfully helps clients with projects of all sizes, not only within the GTA but sometimes even beyond the region’s traditional boundaries.
For instance, Pomerleau’s work as a development partner on the Weeneebayko Area Health Authority (WAHA) health care campus in Moosonee near James Bay is another example of its ability to tackle large-scale and complex projects, but in this instance, it also shows cultural sensitivity in the navigation of a planning and contract negotiation process involving six different First Nations communities.
“By prioritizing collaboration at every stage with the local communities, the redevelopment project not only enhances healthcare infrastructure, but it also supports local employment, economic growth, and longterm community development.”
“We’re stewards of what we’re delivering, so we’re proud of our work on this project,” says Magda Sabat, Vice-President - Commercial, Major Projects, who oversaw the pre-construction phase.
Engagement with the community has been a cornerstone of this project. “We really had to make sure we had buy-in, not just also from the health authority, but from all of the local communities,” adds Sabat. Through regular
in-person consultations up north with Elders, local leaders, and community members, Pomerleau has been able to successfully incorporate their input into the project’s design and execution so that their cultural traditions and values are honoured and celebrated.
In addition, ensuring that local communities could participate in the employment opportunities created by this project contributes to increased collaboration efforts. By fostering twoway communication, trust, and transparency, Pomerleau aims to ensure the community feels heard and involved at every stage.
“We are committed to working in true partnership with the First Nations communities to create lasting benefits beyond construction,” explains Paul Kundrat, Vice-President of Operations, who is overseeing construction on the project.
Smithson says that while this job is not in the GTA, it demonstrates Pomerleau’s ability to oversee major projects. “Reputation matters, and that’s what we’re building—and it’s rooted in how we provide value for our clients,” he says.
Under Smithson’s leadership, Pomerleau’s GTA region office has transformed into a construction partner that prides itself on its adaptability, expertise, intuitive understanding of client needs and its ability to collaborate with clients of all sizes.
He firmly believes that Pomerleau is well positioned to become one of the city’s go-to infrastructure development partners.
“We’ve got the right people here who are engaged and growing. The Toronto market will benefit from the resources and expertise we bring as a national player,” says Smithson. “As Pomerleau sets its sights on the next five years, the positive impact the company will have on community infrastructure and the overall quality of life for GTA residents will become increasingly evident—and I’m honoured to be a part of the team that will make it happen.”
NAVIGATING THE AI ERA Page 30 THE PRACTICAL REALITIES OF AI Page 31 THE AI IS READY, ARE YOU? Page 32
Where articial intelligence and human ingenuity meet, to help you minimize risk and maximize potential.
Articial intelligence is changing the way the world works. But, to successfully manage the complex risk of construction, you still need the insight and ingenuity of an experienced broker. At American Global, we provide valuable guidance and best-in-class service to help you meet today’s challenges and achieve tomorrow’s potential. Expect more from your broker.
100% Privately Owned & Solely Construction Focused
• Diverse Technical Resources with Deep Industry Expertise
• Local Presence with a Global Platform
• Collaboration That Drives True Innovation
•
• P3 Awards: Insurance/Risk Advisor of the Year 2023 & 2024
www.americanglobal.ca
The notion of Artificial Intelligence (AI) is something many still associate with sci-fi movies. In a matter of a few short years, AI evolved from serving as the subject of a futuristic fictional plot to becoming an integral part of our daily lives. The pace at which this change has occurred, and the thought of AI’s unlimited potential, is nearly as overwhelming as the concept of AI itself.
The infinite possibilities that AI presents often makes it more difficult for business owners to determine where to start. Understanding both the promise – and pitfalls – of AI must be the first step in the process of change. That’s why American Global is proud to sponsor to this year’s On-Site Construction Technology Report. This report builds on their recent webinar on AI in Construction, where On-Site asked experts to explore and explain how to deploy some of this new technology while setting realistic expectations as to what, where and how AI can best be used in the construction industry.
In my article contained herein, “The AI tools, trends, and tactics for success” (see pg. 32) I also offer some insights on how contractors can utilize the impressive data analytic capabilities of AI to identify issues related to claims, safety, supply chain, and much more.
However, it is important we all realize that AI alone is not the answer to all our problems. It is simply another tool, powerful though it may be, to help us move our businesses and the industry forward, with greater understanding, efficiency and predictability.
As I recently read somewhere, “AI will not take your job, but someone who knows how to use AI will.”
At American Global, we help contractors, owners and developers maximize business potential while minimizing risk. We succeed by combining a talented team of industry experts with innovative technology like our C-RISQ solution, providing clients the best of both worlds… human ingenuity and artificial intelligence.
I hope you find this year’s Construction Technology Report intriguing and informative. I want to thank On-Site for their continued efforts to keep their readers engaged and educated on the latest trends.
Sincerely,
Chris Greene Vice-President, Innovation & Insights American Global
By Ezequiel Machabanski
he integration of Artificial Intelligence (AI) in general contracting has ushered in a new era of efficiency, precision, and innovation. However, like any powerful technology, it comes with its own set of challenges and risks. For general contractors (GCs) to harness AI effectively while ensuring safety and reliability, a strategic approach is paramount.
AI has the potential to revolutionize general contracting by enhancing project management, optimizing resource allocation, improving safety protocols, and predicting maintenance needs. For example, AI-driven tools can analyze vast datasets to forecast project timelines, identify delays and streamline workflows. AI can also assist in designing more sustainable and cost-effective building solutions.
Nevertheless, the adoption of AI brings challenges general contractors must address. Data privacy, cybersecurity, and the ethical implications of AI are significant concerns. GCs must also integrate AI with existing systems and address workforce apprehensions about potential job displacement. A well-balanced approach is required to leverage AI’s benefits while mitigating related risks.
At its core, AI operates at the intersection of data, applied mathematics, and computer and data science, with data forming the foundation of robust and scalable AI systems. For construction purposes, data such as project plans, material specifications, workforce schedules and financial transactions fuel AI algorithms. Ensuring the privacy and security of this data is crucial; contractors must implement robust data protection measures, including encryption, secure access controls and regular audits to build safe AI systems.
While the industry often focuses on AI model or data-related risks, GCs should allocate resources to advanced cybersecurity solutions and vulnerability assessments. Employee training on data security is equally important, as human error remains a substantial risk. AI systems often make decisions that impact project outcomes, making it critical to ensure that these decisions are ethical and unbiased.
For example, EllisDon has established clear guidelines for AI decision-making processes and regularly reviews outcomes for fairness and accuracy on use case by use case basis. Transparency in AI operations fosters trust among stakeholders, which ultimately accelerates adoption across organizations.
Additionally, involving human oversight in AI decision-making can help prevent biases and errors. At EllisDon, we prioritize scoping use cases with a “human-in-the-loop” approach as an absolute necessity. While AI processes data at unprecedented speeds, human intuition and expertise remain invaluable. A collaborative
approach, where AI assists rather than replaces human decision-making, ensures balanced and ethical outcomes.
The integration of AI with existing systems and processes is vital for maximizing its potential. GCs should conduct thorough assessments of their current technologies and workflows to identify areas where AI can add value. Ensuring interoperability between AI systems and traditional tools facilitates a smoother transition and, though time-consuming, this exercise is essential for successful deployment across organizations. As stated earlier, AI should assist your organization in meeting its goals and keeping its workers safe instead of replacing the functionality of human intuition.
Pilot projects are an effective way to test the integration of AI applications before full-scale implementation. These projects allow GCs to evaluate the performance, identify issues, and adjust. Continuous feedback from project teams is essential to better align with real-world needs.
As AI becomes more mainstream, it is essential to acknowledge and address workforce concerns. The construction industry already faces labour shortages. This, coupled with workers’ apprehensions regarding the impact of AI on their roles, could exacerbate retention challenges. This represents the single biggest risk in deploying AI.
To address this, the industry must develop a comprehensive strategy that includes transparent communication and effective messaging to alleviate these concerns. Engaging employees through open dialogues and involving them in the AI adoption process can foster a sense of ownership and collaboration. Offering training and upskilling programs equips the workforce with the skills needed to work alongside AI technologies, enhancing adaptability and ensuring a smoother transition. Addressing these concerns with sensitivity builds trust and acceptance among employees.
The safe navigation of AI technologies for GCs requires a strategic and multifaceted approach. Prioritizing data privacy and security while ensuring ethical decision-making lays the foundation for building and integrating AI systems. Simultaneously, addressing workforce concerns through engagement and education is essential to fostering acceptance.
By balancing innovation with caution, GCs can harness the power of AI, responsibly. As the industry continues to evolve, a thoughtful and proactive approach to AI will pave the way for a more efficient, ethical, and sustainable future in construction.
Ezequiel Machabanski is the vice-president of insights and analytics at EllisDon.
Webinar explores the practical application and implementation of AI-enabled technologies.
BY ADAM FREILL
In January, On-Site Magazine continued its AI in construction series of webinars, turning to a collective of experts from leading construction technology development companies to explore how Artificial Intelligence (AI) is impacting many of the digital tools available to general contractors in Canada.
The session, sponsored by American Global Canada, saw Hammad Chaudhry, vice-president of market development and partnerships at Timescapes, moderate a conversation with Gabe Guetta, CEO and founder of Salus, Kris Lengieza, global technology evangelist at Procore Technologies, and Steve Smith, director of partnerships at Bluebeam.
The group approached some of the reasons why AI is making inroads into many companies in the construction sector, touching on its implementation, industry buy-in and how to make practical gains through the use of AI-enabled technologies.
“I really do think it’s going to drive the future of productivity,” stated Lengieza as he opened the discussion. “It’s the combination of what we can do in both automation and augmentation that will allow us to be more productive as an industry.”
He explained that AI already commonly used in the industry.
“We’re seeing it show up in the back office and with our project managers and our project engineers for simple things like creating monthly reports or maybe even reviewing a submittal to see if it is accurate against the specification,” he explained.
The pace of adoption of technology is getting faster, and it is touching on all aspects of business, from project plans and details to health and safety, as well as
security, but Smith advised companies to find their own pace.
“Move at the pace that feels right for you,” he said. “Tried-and-true methods have been working for you, but let’s make you faster and better using things like AI.”
“I think the biggest thing that excites me is it empowers the industry around the things that I don’t actually think humans should be doing… the mundane tasks,” added Guetta.
Much as hammer drills make tasks faster, AI can help with productivity on the job. “I think when you look at AI, it’s the next layer of intelligence that we can empower the workforce to have,” he said.
Smith explained that putting themselves in their customer’s shoes helped his company develop its platform. “One of the things that we did is we tried to keep it more in the meat and potatoes vein of AI: What
are our users doing every day? And how can we make that easier?” he explained.
The fact that AI is an evolving tool that is designed to get better at its job by getting trained by the user requires a new approach. “You’ve got to use it the right way, and you’ve got to teach it the things you want it to know,” stated Lengieza.
“You won’t get the full benefits out of it unless you actually interact with it and start training these models,” agreed Guetta.
At the end of the day, it is about efficiency, and ultimately, AI “has to be extremely practical. It has to be useful,” said Smith. “Look at the overall jobs that need to be done, where are the sticking points in your operation?”
To check out the full AI discussion, scan the QR code, or visit the On-Site YouTube channel.
BY CHRIS GREENE
AI is transforming industries at an unprecedented pace, and construction is no exception. However, AI means different things to different people. For some, it’s about large language models (LLMs) like ChatGPT. For others, it’s machine learning, robotics or advanced pattern recognition.
No matter how you define it, the impact is undeniable. While AI isn’t replacing workers outright, it’s clear that workers who know how to leverage AI will have a competitive edge over those who don’t. Despite the industry’s traditional reliance on deterministic (black-andwhite) thinking, the average construction professional can use probability-based AI tools of today.
AI has a role to play in risk management, budgets and schedule improvements, so the next generation of construction workers will need to master AI tools in the same way past generations were taught to memorize times tables, except this time, they’ll have a PhD-level assistant in their pocket.
AI’s history goes back to the 1950s, but many people don’t realize they’ve been using AI for decades. Everyday tools like Roomba vacuums, Spotify’s music recommendations and fraud detection algorithms are all powered by AI.
More noticeable was the AI tidal wave that hit not long ago, when ChatGPT reached 1 million users in just five days, accelerating AI’s mainstream popularity. For many, it was their first encounter with generative AI and the realization that an AI assistant could handle creative, analytical and even strategic tasks.
In construction, AI’s presence has been more subtle, but it’s here, and it is growing. Companies like the one I work for are pushing the envelope by integrating platforms that enable contractors to do things like streamline risk assessment and automate compliance tracking, creating new levels of efficiency.
For the average construction professional, the most accessible form of AI today is the large language model. Tools like ChatGPT are transforming how workers manage schedules, draft reports, create budgets and even analyze contracts. Imagine being able to generate professional-grade emails, automate reports or analyze site data, all in minutes.
At American Global, our AI automations have gone a step further by integrating LLMs into client advisory platforms, enabling brokers to provide more precise, data-driven recommendations for insurance and risk management, but the possibilities extend right across the construction spectrum.
For example, estimators can use AI to
generate cost breakdowns, predict future material costs and optimize procurement strategies; project managers can summarize meeting notes, identify risks and communicate project updates; and site supervisors can draft incident reports and site instructions more quickly, focusing their time on higher-value tasks.
At American Global, we use AI to enhance the capabilities of our C-RISQ platform. By pulling in project data, failure data and risk finance technology, C-RISQ identifies patterns that allow project managers and site supervisors to focus on the most critical areas of risk.
The takeaway? Workers who learn to see AI as an extension of themselves—like a second set of hands or additional brain power—will outperform those who don’t.
Construction is a world of absolutes. Either the concrete cures properly or it doesn’t. Either the beam supports the load, or it fails. This deterministic, black-and-white thinking is necessary in areas like structural integrity. But AI’s approach is different— it’s probabilistic, meaning it operates in shades of grey.
AI provides predictions, suggestions and probabilities, not guarantees. This distinction is important. An AI tool predicting the likelihood of project delays
is helpful, but not absolute. Construction professionals must interpret these probabilities and make judgment calls. This requires a shift in mindset. Rather than searching for binary yes-or-no answers, AI asks us to embrace probabilistic thinking and make choices based on the likelihood of outcomes.
When we were kids, teachers told us to memorize our multiplication tables because “you won’t always have a calculator.” Today, not only do we have calculators in our pockets, but we have AI models that can solve PhD-level problems, generate essays and provide business strategy—all in seconds.
So, what’s the modern equivalent of, “Learn your times tables?”
It’s, “Learn how to use AI effectively.”
The next generation of workers won’t just need to know how to operate power tools, they will need to know how to use AI tools. That’s why education and training must evolve. This evolution is already in motion at companies like mine.
Our training programs emphasize “prompt engineering.” This involves teaching employees how to ask AI for exactly what they need to streamline workflows, draft policy language or enhance risk analysis.
The shift to incorporate AI into
education and training programs will be crucial for the construction industry’s future. Workers who know how to operate AI-empowered tools will be the leaders of tomorrow’s construction sites.
Risk management is key in construction, and it’s an area where AI’s predictive capabilities can shine. As Mark Bryant, CIO of PCL noted, “AI in construction transforms vision into precision, turning data into decisions and innovation into stronger, smarter, and more sustainable structures for the future.”
AI is driving change in a number of ways. For example, when it comes to claims analysis, AI can review historical claims data and identify patterns, helping contractors anticipate potential losses. If claims data shows a spike in incidents in April, construction firms can investigate causes and prepare better for that period.
AI can also analyze safety reports and Internet of Things (IoT) sensor data to predict potential hazards on-site, enabling proactive measures to reduce risk. Platforms like C-RISQ use AI to integrate feeds and create real-time risk dashboards for site managers.
Predictive models can also analyze weather forecasts, supply chain issues and project schedules to identify potential delays before they occur. The ability to analyze vast datasets is especially impactful. By predicting potential delays,
identifying supply chain bottlenecks and forecasting price fluctuations, AI can reduce the risk of budget overruns and missed deadlines.
AI tools can help predict fluctuations in the cost of materials like steel and concrete, so that contractors can lock in prices before spikes occur. They can also identify supply chain risks in real-time and analyze historical data from similar projects to recommend optimal sequencing of tasks. These capabilities don’t replace the role of human judgment, instead, they empower construction managers with the insights they need to make better, faster decisions.
AI is no longer a distant future concept. It’s here, and it’s changing the way we build.
From LLMs that boost personal productivity to predictive analytics that can minimize project risk, AI is a tool that every construction leader should embrace. It’s not a matter of being replaced by AI, but rather, it’s about being replaced by someone who knows how to effectively use AI.
The construction industry has always had its roots in raw materials like wood, concrete and steel. But the most valuable material of the future might just be data. Forward thinking companies like mine are helping clients and contractors realize that those who harness AI to analyze, predict and then act on those data-driven insights, will be the ones who thrive.
As AI continues to evolve, construction firms will face a choice: Adapt and leverage these tools to increase productivity, manage risk and stay ahead of the competition, or be left behind. The choice is clear. The tools are ready. The next generation of builders must be too.
Chris Greene is the vice-president of innovation and insights at American Global, one of the largest privately held insurance and surety brokerage firms in North America specializing in all aspects of construction risk management.
By Jacob Stoller
Can tech assist the balancing act between legal compliance and proactive measures?
hen it comes to digitization, safety presents an interesting paradox. On one hand, safety involves a plethora of compliance-related taskwork that’s prime territory for automation. On the other, safety ultimately depends on culture and the strength of personal relationships – two elements that can never be automated.
“Technology is a tool, but we need to rely on the human element to help calibrate it,” says Steve Chaplin, senior vice-president, Health, Safety and Environment, at EllisDon. “Where we can use technology to advance and to make things simpler, we should. But there is a human element to this that I don’t think we ever want AI or any other technology to completely erode.”
When EllisDon’s HSE group polled their operations teams, they found that reducing safety-related administrative work was a key priority.
“The actual ask from our operations teams was, ‘We want our people to be out of the trailer doing their job and meeting with their teams,’” says John Martin, senior HSE director for Eastern Canada at EllisDon. “So, from a technology perspective, what that means is that you don’t want to replace humans in the loop. You want to replace administrative, menial tasks that a person would do at the end of the day but are not really part of the job description. A four-year-old can fill out a form. We don’t hire a site superintendent to do that.”
Technology is a tool, but we need to rely on the human element to help calibrate it.”
Mobile apps can help superintendents spend more time with their teams, and critical safety information readily available to workers in the field.
“When you give workers instant access to all these safety regulations and safe work practices, that makes it much more efficient for everybody,” says Brandon Milner, CIO and senior vice-president, Digital and Data Engineering, at EllisDon. “When they need to know about a chemical they’re using and they’re on the 40th floor, they’re not going to have to run downstairs to the basement when they can pull out their phone and it’s there on a map for them.”
Getting the right fit between the software and the specific workflows in a construction company is complicated, however, particularly for a large national organization like EllisDon.
“There’s not one piece of software that does it all exactly the way
we need it done,” says Milner.
For example, he notes, construction unions don’t allow cell phones. “There’s no software that deals with union, non-union, hourly and salaried employees,” he says.
Requirements are also constantly changing. “We have unique needs that are constantly evolving with the market,” he explains.
“The technology market will never keep up with that pace of constantly evolving changes. So, it’s very important for us to work closely with the technology and the site operations people to make sure we’re constantly out there looking for software that can solve some of the problems some of the times.”
To stay on the leading edge, EllisDon, through its Technology Accelerator Program, partners with construction software startups with promising solutions. The selection criteria, Milner points out, are less about technology and more about construction expertise.
“We pick companies whose leaders understand what our problems are and are interested in helping our operations teams,” he says.
Putting an app on a phone is no guarantee that workers will use it, particularly when it comes to submitting reports, but AI technology is evolving to bridge that gap. Kris Lengieza, global technology evangelist at Procore Technologies, explains that software using large language models (LLMs) can provide an alternative to filling out forms.
“What if instead of filling out a form, you could ask an AI [agent] to talk you through a task you are doing today on a job site, and what the risks are,” says Lengieza. “If you’re installing a handrail, for example, the AI could prompt you to explain all the measures you’re taking. Maybe you need to flag the area, make sure you are tied in, and if you’re drilling concrete, making sure you have eye protection and ear protection, and you’re wearing a mask.”
Getting employees to talk with an LLM, however, involves a degree of trust. As Lengieza explains, that all boils down to culture.
“Whenever people take on a technology, they have to ask themselves, ‘What’s in it for me?’” he says. “If they think you’re just collecting data that you don’t really care about, that’s going to be really hard. But if they believe that the company has their best interests in mind, and they’re asking you to use the technology because they want to make sure that you go home safe every day, then there will be a lot less hesitancy.”
Jacob Stoller is principal of StollerStrategies. Send comments to editor@on-sitemag.com.
Industry transformation is coming via AI-enhanced pattern recognition.
n today’s fast-paced, technologically driven world, the construction industry is undergoing a transformative shift. Historically characterized by manual processes and siloed operations, the industry is now embracing digital technologies and artificial intelligence (AI) to solve age-old problems and discover new opportunities. At the heart of this revolution lies the ability to decipher patterns, within data, operations and industries, and to harness them to drive better decisions, innovation and efficiency.
As AI becomes more integrated into the construction sector, it promises not only to streamline processes but also to revolutionize the way leaders approach challenges and opportunities.
A substantial amount of the information related to construction projects is now stored, communicated and analyzed in digital formats. Two primary sources of this digital information, or data, come from digital twin components and digital correspondence.
The project digital twin is made up of data from the various component parts of the project’s technology stack. This includes data from pre-construction tools like BIM, scheduling solutions, project management technologies, IoT backbones, reality capture solutions, counter-party risk assessment technologies, just to name a few of the key categories. These component parts spin off massive amounts of data that, once aggregated, allow teams to monitor project productivity and risk in real time.
Meanwhile, digital correspondence—emails, correspondence within the project management platform, and document sharing systems—tracks the day-to-day communications and decisions that drive projects forward. Together, these tools create a treasure trove of data that, if properly harnessed, can unlock insights, drive efficiency and reduce risk.
The construction industry’s greatest leaders have historically excelled at deciphering patterns within their organizations and the construction industry at large. A successful construction leader understands not only their core area of expertise but also how other functions like finance, legal, design/engineering, estimating, project management, procurement/supply chain, quality control and safety intersect and impact outcomes. This holistic understanding enables them to make informed decisions that consider the ripple effects across the organization.
Even the most experienced leaders face limitations, however. Human cognitive capacity can only process so much information, and the growing complexity of construction projects means there is more data than ever before. This is where AI steps in.
Leading companies are now working to organize their data into structured systems, or ontologies, that make it optimally accessible to AI. An ontology serves as a framework for categorizing and connecting data, ensuring that it is not only comprehensive but also easy for AI systems to process and analyze. Once data is properly organized, it can be used to train industry-specific AI models. These models act as partners to human decision-makers, providing insights, suggestions, and predictions based on vast amounts of data.
This isn’t about replacing CEOs or project managers—it’s about creating a highly functional CEO assistant, or, as some in the tech sector call them, an agentic AI partner that augments human decision-making with unmatched analytical power. These AI agents, once developed, are an extension of intelligence to all leaders within the organization.
As AI continues to advance toward Artificial General Intelligence (AGI), its breadth of knowledge and ability to decipher patterns will surpass anything humans have achieved.
AGI represents a level of intelligence where machines can understand and learn any intellectual task that a human can. In the construction context, this means analyzing data not just within the industry but across sectors, recognizing patterns that would otherwise remain hidden. For example, AI might identify trends in environmental sustainability from other industries and propose innovative ways to reduce waste in construction projects.
At its core, the integration of AI in construction is about driving better decision-making. By processing and analyzing massive datasets, AI systems can provide leaders with actionable insights, enabling them to make decisions faster and with greater confidence.
More importantly, AI has the potential to drive innovation. Innovation stems from recognizing patterns, whether they emerge from within the construction industry or from unrelated fields and translating them into new solutions. By leveraging its expansive knowledge, AI can help organizations identify opportunities for improvement and create innovative strategies that lead to better outcomes.
AI’s role in the construction industry is not about replacing human leaders but about empowering them. By augmenting human decision-making with advanced pattern recognition and cross-industry insights, AI has the potential to revolutionize construction, creating a smarter, more innovative industry.
David Bowcott is the executive vice-president of the Construction Industry Group at Platform Insurance Management. Please send comments to editor@on-sitemag.com.
By David Major, Joseph Campbell and Colleen Williams
he future of Canadian construction projects will require the smart implementation of Artificial Intelligence (AI). AI-driven technologies offer immense potential to streamline traditional processes and improve outcomes across all phases of a project’s lifecycle. AI use is already present on construction sites, but it will become even more prevalent as the industry continues to embrace these tools that improve the efficiency and effectiveness of projects.
As the adoption of AI continues to grow, owners and contractors must remain vigilant about the legal framework governing its use, however, particularly regarding the safeguarding of sensitive data and information of clients and other project stakeholders.
While many may think of AI as being specifically the realm of generative AI tools, such as ChatGPT or similar search algorithms, the reality is that AI is broader; being any sign of intelligence exhibited by a machine. Through that lens, AI has been deployed on construction projects in Canada for years to enhance produc-
tivity and efficiency related to, among other things, costs, project scheduling and labour management.
AI tools such as artificial neural networks are used to predict cost overruns based on such factors as project size, contract type and the competence level of project managers. These tools are also being used to model sequencing and predict timelines on future projects by analyzing bodies of scheduling data.
The Internet of Things (IoT) and Virtual Design and Construction (VDC) have also contributed to improved monitoring and greater productivity. For example, IOT sensors have been used to monitor site activities, including identifying structural issues such as defects and cracks, resulting in early-warning prevention and ultimately, significant costs savings. VDC provides for a digital design framework where project personnel can model and resolve design and cost issues with machine learning assistance prior to the start of construction.
AI also offers significant opportunities to optimize project resources and enhance safety. Robots, for instance, can be deployed to perform tasks that are repetitive and labour-intensive, such as bricklaying and earth moving. Drones with AI scanners can perform more hazardous safety inspections in dangerous environments, such as high altitudes, confined spaces, areas with toxic materials and structurally compromised buildings.
These innovations will also be critical in helping to address the ongoing construction labour shortage as it will allow the completion of more work with fewer personnel.
AI is also transforming project risk management by streamlining scheduling activities, optimizing resource allocation and providing real-time data insights, enabling construction projects to be completed more efficiently and cost-effectively.
In a recent article discussing AI adoption in the industry, Lina Stinnett described PCL’s HeviLift suite of programs, explaining that it uses data like the project schedule, a database of available cranes and lift objects to create thousands of possible lift
sequences, evaluating the costs and timing impacts of each sequence. It was first used in a project in Alberta where it was reported that lift productivity increased by 227 per cent, and heavy lift schedule duration was reduced by 35 per cent.
AI-driven technologies are transforming construction projects, with immense potential for greater innovation in the future.
While AI has brought remarkable advancements, its use also brings legal and risk issues that project stakeholders must thoughtfully address.
Data security and privacy concerns are two major challenges, due to the enormous amount of sensitive data and information that is produced, analyzed and distributed. Risk issues surrounding the use of AI tools include determining whether the contractor or the project owner bears responsibility in the event of a problem or data breach involving the AI technology.
Data and privacy issues in the use of AI on construction projects revolve around the collection, storage and sharing of sensitive information, including worker data and proprietary project details. Ensuring compliance with data protection laws and safeguarding against unauthorized access or breaches are key concerns for project stakeholders and should be considered carefully with counsel in advance of proceeding with the AI tool on a project.
Awareness of the applicable legal frameworks and developments is a critical responsibility and ensures stakeholders can effectively address potential risks and challenges in a complex and fast-paced project environment.
In 2022, the Canadian government introduced Bill C-27, the Artificial Intelligence and Data Act (AIDA). AIDA has not yet been enacted, and it may not become law before the government is dissolved in advance of the next election. If it is not enacted, it will be up to a future Canadian government to enact legislation to protect data arising from the use of AI.
Whether passed during this term or not, the introduction of AIDA is a step forward in ensuring that AI systems deployed in Canada are safe and non-discriminatory and will hold parties accountable for how they develop and use these technologies. AIDA serves as a reminder to AI users and the public that careful consideration and robust safeguards are essential to mitigate and eliminate the risks associated with AI.
More recently, in November of 2024 the government launched the Canadian Artificial Intelligence Safety Institute (CAISI). CAISI is part of a larger project to help researchers and businesses develop and adopt AI responsibly.
While Canada does not yet have a dedicated and comprehensive legal framework to address the use of AI, other established laws impact its use. These include the Personal Information Protection and Electronic Documents Act (PIPEDA), competition law, the Criminal Code, intellectual property rights, employment laws and consumer protection law.
Project actors need to understand the importance of safeguard-
Be informed
As AI is rapidly developing, it is important for contractors to be, and to remain, informed about the ever-evolving legal and regulatory framework.
Get trained
Effective project management requires training for their teams on best practices for data management, especially for project personnel privy to sensitive information. This can take the form of advising on the use of strong passwords, regularly backing up data, monitoring network systems, and having a plan in the event of a data breach.
Understand key contractual obligations
This is critical to protect parties from liability arising from an incident arising due to the use of AI tools. Parties can further protect themselves by ensuring that contract terms clearly articulate their roles and the roles of AI, with clauses that explicitly state who bears responsibility for defects, damages, and injury caused by an AI tool.
Seek legal counsel
If you are unsure of the implication of AI usage or contractual responsibilities on your project, seek legal counsel. This will allow for a thorough review and understanding of legal and contractual issues and guidance on how to navigate and mitigate against potential risks.
ing client and supplier information, ensuring compliance with these laws and privacy regulations and implementing robust data protection measures. If the use of an AI platform exposes internal data, the contractor could incur serious legal and/or financial repercussions, including liability for data breaches and damage to relationships with stakeholders due to loss of trust.
Accordingly, project actors must be mindful of how they engage with and deploy AI tools in their work.
The use of AI in the construction industry has already brought important productivity, optimization, sustainability and safety enhancements, with immense potential for so much more. Nevertheless, all parties involved in the construction project lifecycle, from the preconstruction stage to completion, need to remain vigilant about the legal risks and privacy issues that come with AI’s usage.
In the short term, Canada is expected to update its legal framework for AI in response to the technology’s rapid evolution and increasing attention on the topic in the United States and abroad. It is therefore imperative that parties to construction projects in Canada leverage AI in a thoughtful and informed manner, and to seek legal counsel to better understand and mitigate against potential risks.
David Major is a partner, Joseph Campbell is counsel, and Colleen Williams is an articling student at BLG. All three work in BLG’s Toronto office. This article provides an overview and is not intended to be exhaustive of the subject matter contained therein. Although care has been taken to ensure accuracy, this article should not be relied upon as legal advice.
For the past 125 years, we’ve helped our customers lay the foundation of this country, and trucks like the International® HX® Series are a big reason why. Under its hood, you’ll find the International® S13 Integrated—the bedrock of the nation’s most ambitious projects. international.com