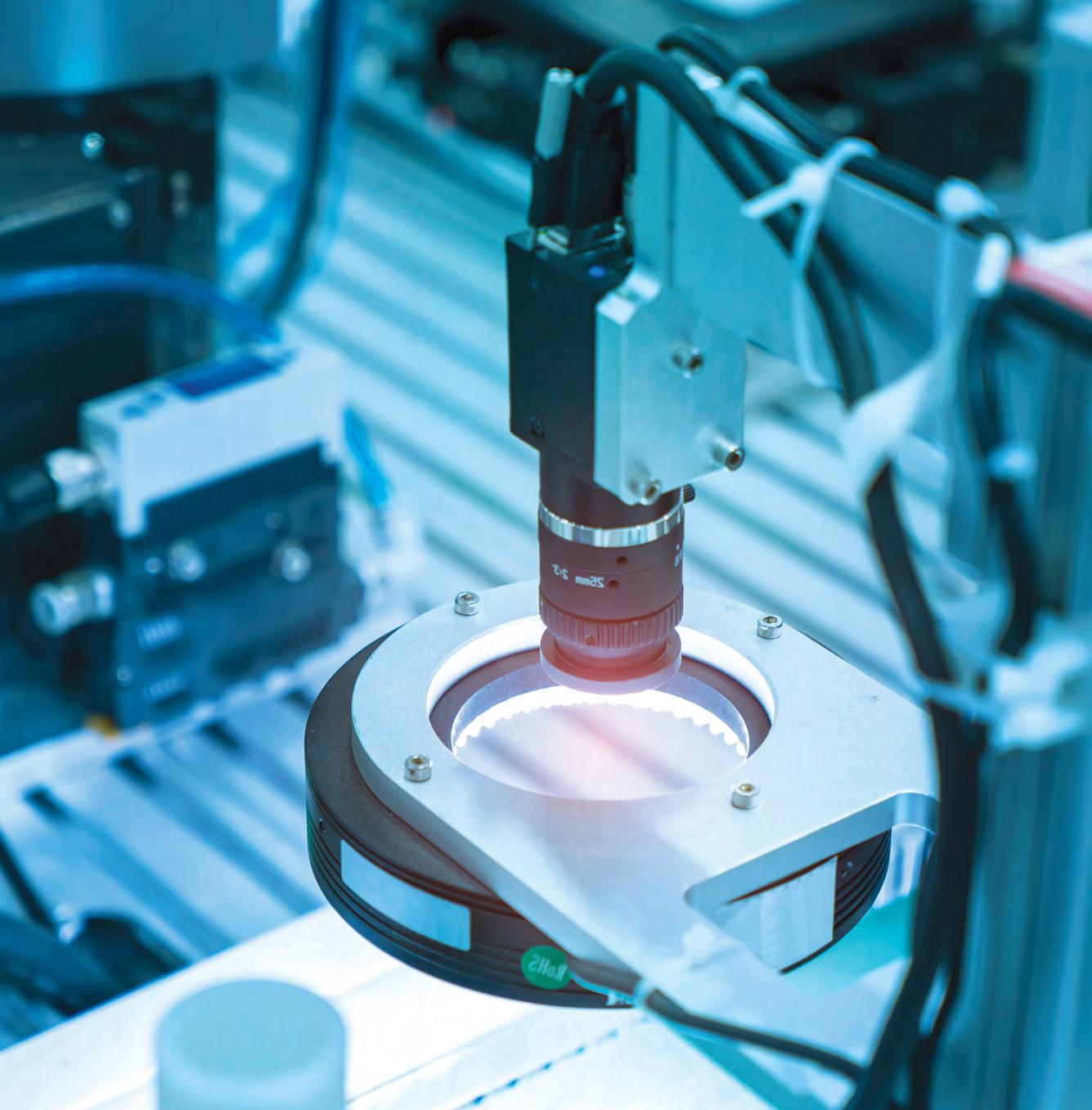
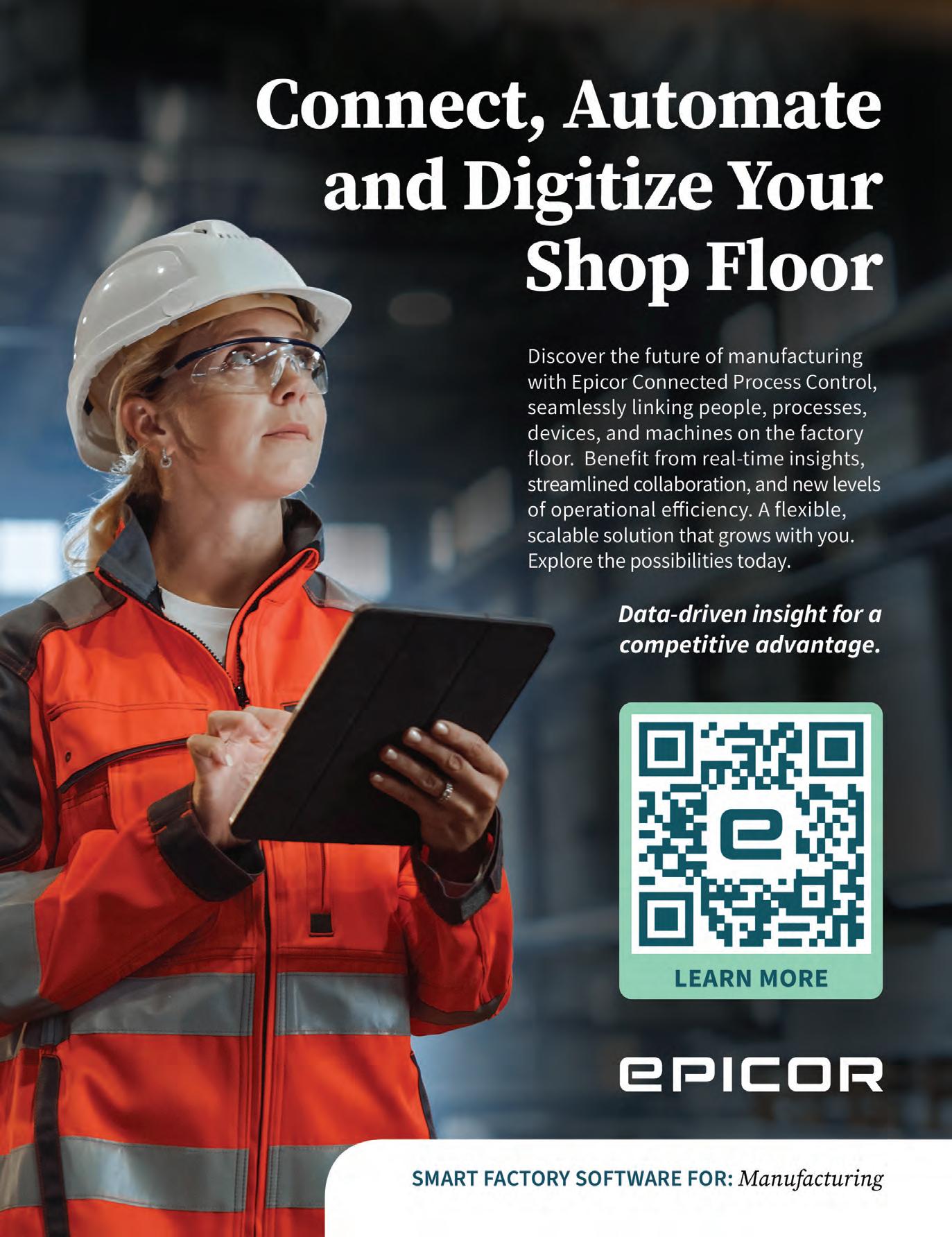
FALL 2023
8
ONTARIO BEGINS MATERIAL HANDLING INSPECTIONS
The Government of Ontario inspectors recently began visiting manufacturing production workplaces in the province to make sure that businesses are compliant with the Occupational Health and Safety Act.
12
NIAGARA MANUFACTURER RECEIVES GOVERNMENT OF CANADA INVESTMENT
FBT Inc. received an investment from the Government of Canada’s FedDev Ontario.
13
GENERATING MORE SALES USING ADVANCED MANUFACTURING
Asking manufacturing executives their definition of advanced manufacturing, will get different responses.
14
16
THE CHAKU CHAKU EFFECT
The term chaku chaku is a serious base line discipline that underpins automation.
Q&A WITH CEO OF SKILLS ONTARIO
Plant spoke with Ian T. Howcroft, CEO of Skills Ontario about what it are in-demand skills and why training is important.
18
20
KEEPING CURRENT ON WHMIS
If you work with hazardous products, you should know that Canada’s WHMIS was updated earlier this year.
STRIVE FOR CAPITAL EFFICIENCY WITH ADVANCED MANUFACTURING DOLLARS
What do big companies have in common? All are involved one way or the other in driving innovation and advanced technology, and are all highly capital efficient.
22
NEXT GENERATION OF MANUFACTURING
In 2023 Canadian manufacturers battled supply chain issues, the rising costs of raw materials, and a growing labour shortage as they continued to adopt Industry 4.0 technologies.
Every few years the domestic automotive industry in Canada (mainly Ontar io) goes through a round of negotiations with Unifor, the union that represents some workers at the Detroit three automakers (Ford, General Motors, and Stellantis). Each round of negotiations is different, based on the outside forces with the economy and government, and how plants are doing (number of products, shifts).
Sometime the negotiations between the OEMs and Unifor can be real fights, with threats of strikes, and posturing back and forth. Which we are seeing currently with the United Auto Workers (UAW) and the Detroit three in the US (more on that later).
Each negotiation period, Unifor picks a target company to begin with, and from that they conduct pattern negotiations with the other two manufacturers. This time Ford of Canada was the target OEM. While a strike deadline was set, it was extended, and an agreement was ironed out. After a ratification vote, the deal was made official at the end of September
A few of the specifics of the deal include a $10,000 ratification bonus for full-time permanent workers, with a $4,000 bonus for temporary workers, a 15 per cent wage increase over the life of the deal (three years), increases to retirement programs, and reduction of new hire wage progression (by up to 50 per cent). This deal which runs until September 20, 2026, covers over 5,600 unionized workers at Ford facilities in Canada.
Unifor has announced that it will be negotiating with General Motors Canada next. It covers 4,300 workers at the company’s Oshawa, St. Catharines, and Woodstock locations. Expect the agreement that was made with Ford to be the basis for the agreement with GM. Once those negotiations are done, Unifor will move on to Stellantis.
Interestingly, only 54 per cent of Ford unionized membership voted in favour of the agreement. A low number for what looks like a good deal for workers. However, with the unions making concessions in previous negotiations (during COVID-19, and when two of the three OEMs were facing bankruptcy), this time it seems that is not going to be the case.
Across the border in the US, the Detroit three are facing a much harder negotiation with the UAW. As with their Canadian counterparts, the unions are looking to make up for the concessions made in previous negotiations.
Workers at three plants in the Detroit area went on strike, when negotiations broke down, and now that has spread to many states, and as of this writing, the UAW is planning on expanding the work action even further. Even President Joe Biden has weighed in on the negotiations, telling workers to fight for what they deserve. Reports have said that the UAW is looking for a 40 per cent pay increase.
The UAW action is already having outside effects, as Ford Motor Company has paused the building of an electric vehicle battery plant in Michigan. While experts in Canada are expecting to see supply chain issues for Canadian Detroit three production, if the strike south of the border drags on.
MARIO CYWINSKI, EDITOR Comments? E-mail mcywinski@annexbusinessmedia.com
READER SERVICE
Print and digital subscription inquiries or changes, please contact customer service
Angelita Potal
Tel: (416) 510-5113
Fax: (416) 510-6875
email: apotal@annexbusinessmedia.com
Mail: 111 Gordon Baker Rd., Suite 400 Toronto, ON M2H 3R1
EDITOR Mario Cywinski
226-931-4194 · mcywinski@annexbusinessmedia.com
SENIOR PUBLISHER Scott Atkinson
416-510-5207 · satkinson@ annexbusinessmedia.com
NATIONAL ACCOUNT MANAGER Ilana Fawcett
416-829-1221 · ifawcett@annexbusinessmedia.com
MEDIA DESIGNER Svetlana Avrutin
ACCOUNT COORDINATOR Debbie Smith
416-442-5600 ext 3221 · dsmith@annexbusinessmedia.com
AUDIENCE DEVELOPMENT MANAGER Beata Olechnowicz
416-510-5182 · bolechnowicz@annexbusinessmedia.com
GROUP PUBLISHER Paul Grossinger pgrossinger@annexbusinessmedia.com
PRESIDENT/COO Scott Jamieson sjamieson@annexbusinessmedia.com
ANNEX BUSINESS MEDIA 111 Gordon Baker Road, Suite 400 Toronto, ON M2H 3R1 Tel (416) 442-5600 · Fax (416) 510-5134 www.annexweb.com
SUBSCRIPTION RATES
Canada – $76.00 per year
USA – $201.00 (CAD) per year
International – $227.00 (CAD) per year
Single copy – Canada $12.00
Add applicable taxes to all rates. Combined, expanded or premium issues, which count as two subscription issues.
ISSN: 1929-6606 (Print), 1929-6614 (Online).
PUBLICATIONS MAIL AGREEMENT NO. 40065710
Return undeliverable Canadian addresses to: PLANT Circulation Department, 111 Gordon Baker Rd. Suite 400, Toronto, ON M2H 3R1
©2023 Annex Business Media. All rights reserved. Performance claims for products listed in this issue are made by contributing manufacturers and agencies. PLANT receives unsolicited materials including letters to the editor, press releases, promotional items and images from time to time. PLANT, its affiliates and assignees may use, reproduce, publish, re-publish, distribute, store and archive such unsolicited submissions in whole or in part in any form or medium whatsoever, without compensation of any sort. This statement does not apply to materials/pitches submitted by freelance writers, photographers or illustrators in accordance with known industry practices.
PRINTED IN CANADA
• Less expensive to purchase than refrigerant A/C units
• Less expensive to operate than refrigerant A/C units
• Quicker to install than heat exchangers and refrigerant A/C units
• Little to no maintenance
• More reliable in dirty, hot, or remote environments than alternative cooling products
• Not a ected by machine vibration which can cause refrigerant leaks
• Ambient temperature does not a ect performance like it will with alternative cooling products
It is an OSHA violation that presents a shock hazard to personnel.
The fan blows hot, humid, dirty air at the electronics.
Stop electronic downtime with an EXAIR Cabinet Cooler System! The complete line of low cost Cabinet Cooler Systems are in stock and can ship today. They mount in minutes through an ordinary electrical knockout and have no moving parts to wear out. Thermostat control to minimize compressed air use is available for all models. All Cabinet Coolers are UL Listed, UL Classi ed and /or CE Compliant.
NEMA 12
For large heat loads up to 5,600 Btu/hr.
• Enclosure remains dust-tight and oil-tight
• Measures 8" (203mm) high
• Mounts top, side or bottom
NEMA 4 and 4X
For heat loads up to 5,600 Btu/hr.
• Enclosure remains dust-tight, oil-tight and splash resistant
• Suitable for wet locations where coolant spray or washdown can occur
For NEMA 4X applications available for heat loads up to 5,600 Btu/hr.
• Resists harsh environments not suitable for Type 303/304SS
• Ideal for food and chemical processing, pharmaceutical, foundries, heat treating and other corrosive environments
For use with classi ed enclosure purge and pressurization systems. Available for classi ed environments up to 5,600 Btu/hr.
• Maintain NEMA 4/4X integrity
• For hazardous/explosive environments
• CE compliant
For NEMA 12, 4 and 4X applications. Available for heat loads in many capacities up to 5,600 Btu/hr.
• Suitable for ambients up to 200°F (93°C)
• Ideal for mounting near ovens, furnaces, and other hot locations
Keep a slight positive pressure on the enclosure to keep dirt from entering through small holes or conduits. For use in non-hazardous locations.
• Uses only 1 SCFM in purge mode
• For heat loads up to 5,600 Btu/hr.
• NEMA 12, 4 and 4X
Tata Steel Ltd and ABB have signed a Memorandum of Understanding (MoU) and will collaborate to create innovative models and technologies to help reduce the carbon footprint of steel production.
“Steel companies know there are opportunities to improve their processes, and Tata Steel is one of the leader s in this movement towards energy efficiency and reduction of carbon footprint,” said Vipul Gautam, Group Vice President, Global Account Executive for Tata Group, ABB.
ABB and Tata Steel will focus on system-level assessments of Tata Steel’s manufacturing plants and production facilities for evaluation and co-development of short and long-term options for energy efficiency, decarbonization and circularity.
The two companies will explore energy optimization via hydrogen as an alternative fuel for upstream processes and energy reduction and substitution through fully integrated electrification and digital systems.
Tata Steel has committed to major sustainability targets of carbon neutrality by 2045. The steelmaker has a medium-term target to reduce carbon emissions to under two tons of CO₂ per ton of crude steel in its Indian operations by 2025.
To ensure sustainable growth, the company is working on deployment of key enablers for deep decarbonization, including the use of more scrap in steelmaking , use of alternate fuels, use of renewable energy and deployment of carbon capture and storage/ utilization technolog ies.
Ford Motor Company of Canada and Unifor have come together to reach an agreement on a new three-year labour contract.
Casselman, Ont., and Leduc, Alberta.
ABB and Tata Steel will carry out system-level assessments for manufacturing plants like Tata’s Jamshedpur.
“Our Unifor-represented autoworkers are the heart of Ford of Canada,” said Bev Goodman, president and CEO, Ford of Canada. “This contract invests in our talented and dedicated employees, who remain consistently focused on the critical work of assembling our vehicles, building our engines and components, improving customer satisfaction, and expediting parts delivery service to our more than 400 dealers.Together, we are ensuring our Canadian operations continue to deliver with the skills, knowledge, and processes to compete and win.”
The new agreement covers over 5,600 unionized Unifor members at Ford’s Oakville Assembly Complex; Annex and Essex engine plants in Windsor, Ontario; and part distribution centres in Bramalea, Paris and
“Our bargaining team showed exceptional leadership and successfully pushed Ford of Canada on every front,” said Unifor National President Lana Payne. “This contract will change lives in a profound way. It fundamentally transforms pension plans, provides protections during the EV transition and includes the highest wage increases in the history of Canadian auto bargaining.”
Ratification meetings had Ford union members vote 54 per cent in favour of the new agreement. The agreement offers hourly wage increases, a ratification bonus, retirement programs increases, and reduction of new hire wage progression period.
“We know this is a challenging time for all workers and this agreement tackles the affordability issues so many face today,” said Ford Master Bargaining Chair John D’Agnolo. “I’m so proud of what we’ve accomplished, and that the membership voted for a contract that will set a new standard for autoworkers for years to come.”
Ford was selected as the target company by Unifor for its Detroit Three negotiations. With General Motors Canada selected as the second automaker to negotiate.
The Federal Economic Development Agency for Southern Ontario (FedDev Ontario) has invested in nearly $4 million in Rex Power Magnetics.
(Credit: Tata Steel)“We are very pleased to embark on our expansion plan, with the help of FedDev Ontario, which includes new space, new equipment, facility improvements, and plenty of hiring,” said Simon Hasserjian, president, Rex Power Magnetics. “These updates will allow Rex to better support Canada’s transition to a renewable power infrastructure and greener future for everyone.”
Rex Power will now add a new transformer production cell at its current 145,000-square-foot facility in Concord, Ont., and create a new production line at its new facility in Etobicoke, Ont. The company hopes to increase sales, create 35 jobs, and improve lead times.
“Today’s investment reassures our federal government’s commitment to help grow and expand Canada’s thriving manufacturing sector,” said Francesco Sorbara, Member of Parliament for Vaughan–Woodbridge. “This nearly $4 million enables this Vaughan manufacturer to stay competitive, increase its production of
green, energy-efficient products, and help create and maintain 320 good jobs across the region.”
Rex Power is a family-owned transformer design and manufacturing company used in the generation, storage, and transmission of electricity for schools, homes, hospitals, and businesses.
Linamar Corporation through its subsidiary Linamar Structures USA (Michigan), Inc. has reached a definitive agreement with Mobex Fourth and 1, LLC, to acquire a portion of its US-based assets.
“We are very pleased to announce this acquisition, the latest step in building our revenue profile for non-ICE dependent products in alignment with our overall Mobility Structures and Chassis strategy.,” said Linda Hasenfratz, executive
chair and CEO, Linamar. “The addition of the sales from this business takes our EV and propulsion-agnostic business to nearly 60 per cent of our total Mobility sales in just a couple of years, a great way for us to stay flexible in a shifting marketplace.”
Linamar Structures will acquire assets that consist of manufacturing operations for propulsion-agnostic chassis and suspension modules and components, including steering knuckles, control arms and subframes. The Mobex facilities will be integ rated into Linamar.
“We are excited about this latest business acquisition and the capabilities it gives us for growing our Structures and Chassis business”, said Jim Jarrell, president and COO, Linamar. “We look forward to working with our OEM customers to help fill their growing needs for high quality, technologically advanced Structural components.”
The transaction is subject to customary consents and regulatory approvals and is expected to close in mid-Q4 2023.
The Government of Ontario inspectors recently began visiting manufacturing production workplaces in the province to make sure that businesses are compliant with the Occupational Health and Safety Act.
The main area of focus for the inspections was material handling, including forklifts, conveyor belts, and other equipment which has movement.
Plant spoke with ministry spokesperson, Jennifer Rushby at the Ministry of Labour, Immigration, Training and Skills Development, to find out more details about the inspections.
PLANT: What sort of manufacturing plants will be inspected?
RUSHBY: This campaign will focus on sectors where material handling is common, and production is taking place.
In the food and beverage sector, this may include workplaces manufacturing animal food, meat products, sugar and confectionery products, dairy products, beverages, tobacco, and cannabis products.
Inspectors may visit any kind of workplace within the sector. The workplaces inspectors visit are determined using a risk-based process that considers:
• injur y, illness and fatality data;
• health and safety research; and,
• feedback from industr y partners and inspectors.
PLANT: What will the inspectors be looking for?
RUSHBY: Material handling continues to be a significant cause of workplace injuries and fatalities in these sectors, which is why it’s the focus of this year’s campaign.
The focal point for inspectors will be on workers who handle materials and the equipment used to handle these materials, and that employers are taking appropriate action to assess and address these hazards in industrial workplaces.
BY MARIO CYWINSKIIn addition to looking specifically at material handling hazards, inspectors will check that employers are identifying other workplace hazards, complying with the Occupational Health and Safety Act (OHSA), and have workplace safety policies in place.
Our preventative, proactive approach emphasizes safety first, preventing, or correcting workplace hazards to protect workers before injuries occur.
PLANT: What happens to companies that are not in compliance? Are they closed? Have a certain amount of time to comply? Will companies get a pass/fail (like they have in the food industry)?
RUSHBY: Ministry inspectors conduct a review of workplace policies and procedures and will typically complete a physical inspection of the workplace. They may issue orders or requirements to enforce compliance with
Photo ©koldunovathe OHSA and its regulations and support worker health and safety. Orders and requirements may have specific time frames. If warranted, they may issue a stop work order until a hazard is addressed.
Workplace parties who contravene the legislation could face penalties or fines.
PLANT: Once a company has passed, will they be inspected again the future?
RUSHBY: Yes, once an initial visit is completed, workplaces can be visited again. At times, a follow-up visit is required as part of the campaign.
In addition to this specific campaign, ministry inspectors will continue to conduct proactive and reactive visits in the sector and across Ontario’s workplaces as usual, so workplaces may also be visited as part of future campaigns or because of a call or report about the workplace.
PLANT: How long will the inspections be going on for?
RUSHBY:The campaign will continue until March 31, 2024.
PLANT: Anything to add?
RUSHBY: Yes, you may also be interested to know that the ministry announced to the sector that we will be conducting a campaign; however, individual workplaces are not notified of visits in advance.
Additionally, the ministry conducts thousands of proactive visits each year, including compliance campaigns. Last year, ministry inspectors conducted over 67,800 field visits, including nearly 36,000 proactive visits, and issued over 98,900 orders.
The ministry’s proactive campaigns are conducted in two phases:
During the education, outreach, and awareness phase, the ministry works with health and safety associations to engage workplaces about related hazards, giving them the tools and knowledge to comply before inspections begin.
During the enforcement phase, ministry inspectors conduct workplace inspections to check on compliance with the OHSA.
If you’ve struggled to keep your manufacturing business staffed in recent years, you’re not alone. And the issue isn’t going away any time soon. A 2021 study by Deloitte and The Manufacturing Institute found three out of four manufacturers expect to have “ongoing issues attracting and retaining workers” in the years ahead. The study predicted a shortfall of 2.1 million unfilled manufacturing jobs by 2030.
Demographics account for part of the problem, says Andrew Robling, principal product marketing manager for Epicor Software Corp. Baby boomers are now at retirement age, and Covid caused a further exodus out of manufacturing.
But, he says, although those larger trends play a role, in many cases, the hiring churn is worsened by manufacturers’ own ineffective training systems. “When new hires are trained and onboarded quickly and effectively, they can hit the ground running,” he says.
That means fewer costly errors and safety concerns on the shop floor, greater employee satisfaction and higher retention rates. In fact, LinkedIn’s 2020 Global Talent Trends report indicates companies that rank highly for employee training see 53 per cent lower attrition.
The problem with traditional methods Training manuals and on-the-job shadowing
have long been the go-to tools for onboarding new employees in the manufacturing industry. In practice that means new hires typically receive orientation and training off the shop floor, then follow a more senior employee around the plant for a couple of days watching what they do.
When the training period is over, the new hires are turned loose, frequently with nothing to guide them but “a dusty old three-ring binder that likely has outdated reference material,” says Dan McKiernan, senior sales manager with Epicor. “They just have to dive in and try to do the best they can with the information provided. They might be confused and sometimes they are afraid to ask questions. Next thing you know, they’ve produced 100 parts and they’re all bad.”
Even worse, the employee may feel incompetent and opt not to stay. “There’s nothing worse than feeling like you’re lost,” McKiernan says.
The “smart” approach
It doesn’t have to be that way, McKiernan contends. Manufacturing solutions, such as Epicor’s Connected Process Control, integrate smart tools and technologies for manufacturing that modernize the workplace and revolutionize the process of training and teaching new skills.
Rather than being left to flounder on the shop floor after initial training, Epicor’s connected frontline workers use tools like industrial PCs or tablets to access step-by-step instructions in the form of videos, text, GIFs and PDFs. “They ensure that proper instructions are there for the operator in real time, right when they’re required,” McKiernan says.
In today’s increasingly complex manufacturing facilities, that translates to greater accuracy, fewer defects and faster training. “We can usually reduce training time by 50 per cent, but often it’s far more,” McKiernan adds.
He points to a client who took on a job building robotic cells. “They struggled to find operators,” he says, “so they were bringing in people with minimal experience. It took two weeks of non-productive orientation time before they could do anything at all.” In contrast, “by four days, we had the employees on the floor, in their own cell, building their first machine,” he says.
Once new hires hit the shop floor, you need some way of monitoring their readiness and outcomes. That’s where integrated “smart” sensors and devices such as scales, gauges, cameras and DC torque tools come into play, helping you to measure and verify correct assembly.
“We can monitor how long it takes the new hire to do each task,” Robling says. “And we know how long a task should take. The employee gets instant feedback so they know if they’re meeting expectations.” The system also tracks whether any single person is sending an abnormal amount of stuff to be reworked. “That might be a training issue,” McKiernan notes.
Alerts and notifications of faults in parts or assembly are also a critical piece of the puzzle, he says. In the past, he points out, you’d have to wait for a supervisor to tell you what to do. But with Industry 4.0 technology, new hires know right away when there’s a problem and they’re prompted (via digital instructions) to take appropriate steps to remedy the situation. “You can’t advance unless you have a good outcome,” McKiernan says.
Ultimately, says Robling, even the ability to use technology on the plant floor is a draw, particularly for young people who may not have considered a career in manufacturing because they perceive it as a “dirty” job. “Young people want to use technology,” he says. “If we can bring technology to the shop floor and give them tools that make their job easier and make them feel more valued, that all helps with recruitment and retention.”
For more information, visit www.epicor.com.
FBT Inc., received a $4 million investment from the Government of Canada’s Federal Economic Development Agency for Southern Ontario (FedDev Ontario), for its 40,000 square-foot facility in St. Catharines, Ont.
“Embracing innovation has always been at the core of FBT Inc.’s values,” said Rob Forstinger, President, FBT Inc. “The enhanced efficiency will benefit existing clients and open up new capacity to engage in dedicated partnerships with businesses seeking long-term collaboration. Our commitment to fostering dedicated partnership opportunities is driven by our desire to forge strong , mutually beneficial relationships with our clients.”
As a result of the investment, FBT will be able to upgrade its climate-controlled facility. It will be able to adopt new robotic and automated solutions, which will increase its machine components and parts production by up to 75 per cent. FBT will also be able to fulfill its growing list of orders, while creating 40 skilled jobs.
Government officials, executives, and guests were on hand for the announcement.
FBT’s plant has a wide array of equipment. Including milling machines, mill turns, lathes, punch presses, measur ing equipment, wire EDM, vertical EDM, jig grinding, cylindrical grinding, drilling machines, CAD cam, de-burring equipment, surface grinding, and many others. An inspection lab features five coordinate measuring machines.
“Today’s investment in FBT Inc. will help the company increase productivity while creating good jobs in St. Catharines,” said Chris Bittle, Member of Parliament for St. Catharines. “By investing in businesses like this, our government is taking the necessar y steps to boost Canada’s manufacturing sector and domestic supply chain in critical sectors while contributing to a more resilient future.”
FBT was established in 1945 as F-B Tool & Die Limited, it has grown over the years to become an advanced manufacturing company specializing in the design and manufacturing of precision tooling components for SMEs and Fortune 500 companies in North America. Its par ts are used in
automotive, mining/oil and gas, packaging, and power generation/energy industr ies. Its name, FBT, stands for Forstinger Baumann Technologies, named after its founders.
“Ontario’s manufacturing industry is the engine that drives our national economy forward. Our government is investing in the people that make it run,” said The Honourable Filomena Tassi, Minister responsible for FedDev Ontar io. “By making smart investments in manufacturers, like FBT Inc., we are working together to help these businesses grow which will create good paying jobs for our communities, and ensure a healthy environment for generations.”
Tassi, Forstinger and Bittle, were joined by Vance Badawey, MP for Niagara Centre, members of the media, invited guests, and FBT employees for the announcement.
“Today’s announcement is great news for the Niagara region,” said Badawey. “This is a leap forward in developing made-in-Canada capabilities to strengthen our regional economy, while creating important jobs for the community.”
If you were to ask five manufacturing executives from different companies their definition of “advanced manufacturing,” chances are you would get five different responses.
Most responses tie back to automation, robotics, materials, and achieving increased operational efficiencies. No doubt, these are all valuable outcomes achieved through the adoption of advanced manufacturing practices, but they most often require an investment of time and/or money.
What if there was a way to use the intelligence and information gained from advanced manufacturing to generate more sales or even new selling opportunities? Intrigued?
When you tap into the outcomes of advanced manufacturing, that is, the additional information, newly gained efficiencies, or new opportunities, you suddenly have access to new opportunities to generate sales revenue.
For example, what if you could:
Use insights gained from social media to enhance the development of your products. Introduce 3D-printed samples to prospective customers within hours rather than weeks. Capture intelligence from production data that informs your unique competitive advantage.
These aren’t future trends or opportunities to watch for but actual opportunities
that exist right now for you to identify new products, services, and (most importantly) new revenue.
Does that sound too good to be true?
I have a manufacturing client who adopted new technology to increase the efficiency of their older and outdated production equipment. Initially, they researched the market to find a solution to their low production outputs, only to come up short-handed. They par tnered with a technology company, who, working closely with their engineer, helped to develop technology to produce more products faster and with less downtime.
It likely sounds familiar; however, this is only the beginning.The plant manager found that friendly competitors touring her facility were highly interested in their improvements to the production line. They began contracting out their engineer to help their competitors achieve similar results, and before you knew it, they had an entirely new business.
Another client whose sales team was constantly bombarding production with sample runs. Time and again, prospective customers wanted samples; however, costs associated with small material orders were prohibitive. When one of their employees, a self-taught enthusiast of 3D printing, offered to make them some samples, they suddenly realized an entirely new way of presenting their products to customers.
Unlike competitors, who were facing the same cost challenges and delays in producing samples, they began to create custom one-off
pieces with a 3D printer overnight, allowing sales the chance to beat competitors in the race for new business by being able to produce real-world samples quickly.
In m y experience, generating new business opportunities using intelligence from advanced manufacturing requires three ingredients:
• The willingness to try new things and be open-minded to new possibilities.
• An appetite for new revenue opportunities that expand upon existing sources.
• A fearless desire to collaborate with others to generate new business opportunities.
Historically, manufacturers have worked in isolation, sometimes for fear of competition and other times due to capacity or investment constraints. Whether you partner with a technology company to help you scrape the Internet for product improvement insights or align yourself with a 3D pr inter to print your product samples for customers, the key is collaboration.
If you’re tired of hearing why, you should adopt advanced manufacturing for benefits that aren’t alluring, think instead about how you can collaborate to drive new business opportunities.
machines are inexpensive, easy to maintain, and can create a slight buffer between operations.
Applying the principal of chaku chaku will require nerves of steel, as it will require breaking down many barriers along the way. Starting on this will reveal just how many absurd paradigms have infected your business just by wanting to slide operations closer.
While you are in the mode of breaking paradigms, go all of the way:
• Challenge eng ineering to reduce the part count by 50 per cent;
• Reduce the number and types of fasteners by 50 per cent;
• Make sure only one size of tool is need for assembly or disassembly; and,
• Run several exercises on set-up reduction, with a goal of doing a change within one cycle.
When people and organizations start discussing automation, visions of robots dancing g racefully like dancers comes to mind. For that vision of automation to become reality you need to look and concentrate on the connector. Here is where you will see chaku chaku in action.
Japanese for “load load”, chaku chaku is an efficient style of production in which all machines needed to make a par t are situated in the correct sequence, close together. The operator simply loads a part and moves on to the next operation. Each machine performs a different stage of production, such as turning, drilling, cleaning, testing, or sandblasting. There should be no WIP in between the operations or perhaps one piece in queue to reduce changeover time.
Here is where you get started. Typically, many of these operations reside in stand-alone technology islands or companies devote entire departments to a process. Immediately, scheduling
and material handling become management obstacles. At La-Z-Boy we were proud of our technology departments from cutting, sewing, making frames and ultimately coming together at upholstery to become a final product.
Move your machines and operations into a new chaku chaku line. Look for ways where the output from one machine or process automatically loads into the next process step or machine. You may need to slow down a machine to achieve a balance between the operations, but predictable consistency is better than a series of sprints.
Gravity is your friend when it comes to automation and the use of chaku chaku. Simple slides between
Once you have completed this list make sure you apply the five S’s of process improvement. Simplify, simplify, simplify, simplify, simplify, and automate.
Just applying chaku chaku to existing product realization will yield awesome results. The adrenalin will be flowing, and innovation will start to seep from the pores of your team. That is when you can start to look at replacing that precious labour with cobots or robots. Innovative design of end-of-arm tooling for your robots. Does chaku chaku work? At La-ZBoy it used to take 14 to 16 weeks from work order release to get a chair into a box. Today the average is 90 per cent of production requirements in a box in under two hours.
Richard Kunst is an author, speaker and seasoned lean practitioner based in Toronto, who leads a holistic practice to coach, mentor and provide management solutions to help companies implement or accelerate their excellence journeys. You can reach him at www. kunstsolutions.com.
Photo: 3alexd/E+/Getty ImagesThe term chaku chaku may sound funny to some employees, but it’s a serious base line discipline that underpins automation.
Gravity is your friend when it comes to automation and the use of chaku chaku. Simple slides between machines are inexpensive, easy to maintain, and can create a slight buffer between operations.
Skills Ontario is an organization that connects with communities at the grassroots level by preparing youth for the jobs of the future. It partners with school boards, colleges, small business, large companies, labour groups, and governments to help tomorrow’s workforce develop skills needed for a career in skilled trades
PLANT: What are the most in demand skill during the post-pandemic economic recovery.
HOWCROFT: Manufacturing and construction trades remained strong throughout the pandemic and continue so including machining, millwrights, carpenters, and electricians. While service sector jobs, particularly in hospitality (chefs, restaurant service) and hair styling are surging back with the re-opening of the economy. Finally, despite global layoffs in the sector, the pure technology skills are still in very high demand including coding and cloud computing.
PLANT: Plant: What do you think manufacturer’s need to do to fix their staffing shortages?
HOWCROFT: Be proactive. Get involved with organizations like Skills Ontario to help engage and build their talent pipeline. No need to re-invent the wheel. Skills are in the schools, by doing presentations, having events, and generating excitement. We need more good employers to step up and hire. Be sure to sponsor, volunteer, contribute materials/equipment, hire, train; rinse and repeat. Ultimately, poaching people from one another is no longer a viable strategy for the long-term.
HOWCROFT: It’s very important. With the rapid advancement of technology, the competitive landscape and the demand for skills, employers must be involved in training and helping to facilitate life-long learning.
PLANT: Do you see AI (future technology) further impacting staffing/skills in the manufacturing space?
HOWCROFT: Yes. It’s difficult to know how AI will impact staffing and skills within the manufacturing space, but it will impact it (and already has). It is likely that the manufacturers that are best able to harness these new technolog ies, will be the best able to increase their productivity and be most successful in the future.
As with previous technological revolutions, many jobs will be disrupted, and new jobs will emerge and evolve. In manufacturing specifically, AI is already used to analyze data for predictive maintenance and safety. In the future it is likely AI will penetrate many aspects of manufacturing.
From a skills perspective, skills associated with working with and leveraging AI for continuous improvements will be in higher demand. These will be high value skills. Technology will become even more important in all that we do.
PLANT: How much of an impact are supply chain shortages on manufacturing and it’s staffing?
HOWCROFT: Manufacturers are still experiencing latent supply chain shortages resulting from pandemic and demographic related skills shor tages. These skills shortages meant that manufacturers could not produce sufficient parts and supplies to keep up with demands, which caused a ripple effect throughout the manufacturing supply chain.
One high profile example was the micro-chip shortage that continues to affect t he automotive supply chain, which was further exacerbated by geopolitical tensions between the USA and China. Supply chain challenges add delays, cost increases and the need to make significant changes to plans.
PLANT: How can tomorrow’s workplace be ready for a job in the manufacturing sphere?
HOWCROFT: The manufacturing sector in Canada is quickly adapting to changes in the economic environment. It’s very technology intensive, fast-paced and critical to our eco-
nomic success as a country. Careers in manufacturers will continue to be in high demand and become increasingly high-value as the deployment of advanced technologies continues to accelerate.
Meanwhile, many of the skills and competencies that are in high demand in the manuf actur ing sector are also sought after in other industries including construction, technology and even service (teamwork, problem solving, use of technology). Manufacturers should be engaged in the talent pipeline at an early age to foster the next generation of skilled trades and technology leaders by engaging with groups like Skills Ontario; hiring apprentices, co-op students; and providing ongoing training to keep pace with the quickly evolving landscape.
PLANT: Anything to add?
HOWCROFT: Skills Ontario’s mission statement is “to champion and stimulate the development of world-class technological and employability skills in Ontario youth.”
Diversity, equity, and representation are top priorities for Skills Ontario. We are looking forward to continuing to work with communities across Ontario to ensure that
we are providing equal opportunities for all youth and building a diverse and robust skilled workforce.
PLANT: Can you speak about your background and how you came to Skills Ontario?
HOWCROFT: I joined Skills Ontario as CEO in January 2018. Previous roles were at Canadian Manufacturers and Exporters (CME), heading CME’s Provincial Operations and Corporate Counsel as senior vice-president, and led several strategic initiatives to improve and support the health and safety, diversity, and workforce training in the manufacturing and industrial sectors. I have experience working in advocacy, government relations, and public policy for the manufacturing and industrial sectors. As CEO of Skills Ontario, I am driven to build and expand skill development initiatives across the province.
Canada amended its Hazardous Product Regulations (HPR) to align with the seventh revised edition and certain provisions of the eighty edition of the Globally Harmonized System of Classification and Labelling of Chemicals (GHS). These amendments introduce key changes to WHMIS that employers, workers, and suppliers need to know. What hasn’t changed is the requirement to train workers on WHMIS, so they have the knowledge to protect themselves and others from hazardous products in the workplace.
As further updates are expected over time, WHMIS 2015 is now referred to as WHMIS, and versions of the Hazardous Products Regulations will be referred to using the ter ms “former” and “amended”.
For most workplaces, the more noticeable change from WHMIS 2015 to the amended
WHMIS is the adoption of a new physical hazard class (chemicals under pressure), the adoption of a non-flammable aerosols hazard category (aerosol - category 3, non-flammable aerosol), and new subcategories for flammable gases. A full breakdown of the changes and a comparison with WHMIS 2015 is outlined in the amendments to the Hazardous Products Regulations on the Health Canada web site.
There are also changes to the information elements required on safety data sheets, primarily a change to some of the required elements in the physical and chemical properties in section nine. New or more specific elements were introduced, including physical state, colour, particle characteristics, kinematic viscosity, and relative vapour density. Some elements were removed, including odour threshold and evaporation rate. A safety data sheet can still provide these elements as additional infor mation if the additional information is not false or misleading.
Another amendment specifies that all hazardous ingredients that are present in a mixture at concentrations above the relevant cut-off levels must be disclosed, regardless of whether the hazardous ingredient contributes to the classification of the mixture as a hazardous product or not.
Employers in every industry that use, store, or handle hazardous products will need to update their education and training programs to help workers learn about and understand the changes to WHMIS. You will need to continue to provide training that is specific to workers’ jobs, your work site, and your workplace safety procedures.
Education and training must be provided to all workers who may be exposed to a hazardous product due to their work activities whether through normal use, maintenance activities, working near the hazardous products, or in emergencies, and workers who
If you work with hazardous products, you should know that Canada’s Workplace Hazardous Materials Information System (WHMIS) was updated earlier this year.
FOR OCCUPATIONAL HEALTH AND SAFETY
use, store, handle or dispose of a hazardous product. Supervisors and managers must also receive education and training, plus any workers who work nearby or are involved in emergency response.
Workers should understand any hazards related to products, how to protect themselves from those hazards, what to do in case of emergenc y, and where they can get further information.
These amendments provide more comprehensive and detailed health and safety information on product labels and safety data sheets, which will provide better protection for workers. They also help Canada meet its international commitment under the Canada-United States Regulatory Co-operation Council Joint Forward Plan. Aligning with certain requirements of the revised editions of the GHS will also have significant trade benefits for suppliers by harmonizing label and safety data sheet requirements for hazardous products.
Suppliers have until December 14, 2025, to bring their safety data sheets and labels into
compliance with the amended regulations. During the transition period, regulated parties can choose to comply with either the former HPR or the amended HPR. It’s important to note that the hazard classification, safety data sheet, and label of a hazardous product must be fully compliant with the version of the regulation chosen. This requirement means that for a product to be compliant with the amended WHMIS, both the safety data sheet and the label must meet the requirements of the amended WHMIS.
Employer obligations for hazardous products are set in federal, provincial, and ter r itorial occupational health and safety legislation. For information on how your jurisdiction is handling the transition period, and how you can update your health and safety procedures, contact the appropriate federal, provincial, or territorial occupational health and safety regulatory agency.
Infor ming workers about the amendments to WHMIS and how to work safely with hazardous products is essential to keeping them safe on the job. Through a proactive
and ongoing commitment to training and education, employers and workers alike can help foster a safe working environment for everyone.
The Canadian Centre for Occupational Health and Safety (CCOHS) promotes the total well-being — physical, psychosocial, and mental health — of workers in Canada by providing information, advice, education, and management systems and solutions that support the prevention of injury and illness.
make
What do companies such as 3M, ABB, and Pepsico, have in common? All are involved in driving innovation and advanced technology, either as an inventor or user. What stands out is that they are all highly capital efficient.
Investors look for companies that are capital efficient. They love when they find companies that regularly generate free cash flow because the underlying business doesn’t need a lot of capital to grow. To achieve that year after year, companies constantly seek better ways to deliver their products and services. Sometimes that involves advanced technology, and other times it doesn’t. To be capital efficient, you need to be able to discern which is appropriate.
Masaaki Imai, who was influential in developing the concept of continuous improvement, made the case that when seeking improvement, the correct sequence of effort should be:
• Reduce rework;
• Address constraints (bottlenecks) in production;
• Provide better information to the floor;
• Improve physical flow, and,
• Add new technology.
BY HUGH ALLEYAdvanced manufacturing technology is not a good way to solve the problem of rework and is rarely required to resolve constraints. If rework and constraints are not addressed first, investments in information systems, flow and new technology will be wasted.
As an example, at one plant the constraint was the plasma cutter. When the team tracked actual performance, they found the plasma table was idle over half the time. The operators didn’t realize their first priority should be table changes. Once they understood that, the constraint at the plasma table disappeared, even as the plant doubled production. Faster, more accurate plasma cutters were available but they wouldn’t have solved the problem.
In a similar example, a powder coater could not keep up with demand, and asked what capital would be necessary to double production. Instead, over five months, through coaching, the manager implemented several changes in their internal processes. The result was clear work priorities for each member of the team. As a consequence, production doubled with no capital investment. The company could have spent tens of thousands of dollars on additional technology to increase capacity, but as the manager discovered, the capacity was already there. Advanced technologies would not have overcome the organizational issues that limited their production.
Executives often hope that new software will improve the information available where work is done. Most MRP and ERP packages claim to
provide more and better data to the shop floor. However, in most cases, work teams will do better with manual boards that they update themselves. Manual boards have two great advantages. They are more flexible than software; it’s easy to make immediate changes to the metrics to support the current needs of the continuous improvement efforts. Software packages rarely have that flexibility. Second, when the teams manage their production boards themselves, rather than having the data mediated by another department, they tend to give it more attention.
Best practice for new software is to get the current systems working well, and then automate. Otherwise, the existing poor practices are automated, baking in inefficiencies. Putting in new and improved software will rarely, on its own, improve information to the plant floor. In one plant, the accounting side of the software worked fine, but the reports needed by operations were missing. It took a day of analytical work to get the production volume for any one part, which limited the team’s ability to make good production decisions. It
Photo: metamorworks/iStock / Getty Images Plus/Getty Imageswas new, advanced technology, but it didn’t advance the work.
New technology comes into its own when it enables a step change in the process, allowing the company to do truly new things, or when it permits an operator to manage more operations.
For example, autonomation (also described as intelligent automation) is designed to stop machines when an abnormal situation arises. This frees up operators to run several machines at once, because they don’t need to be concerned about whether or not each machine is running correctly. This approach is often inexpensive, and highly capital efficient.
Adding new technology should be done with caution. First, the complexity is often underestimated. I have seen $500,000 CNC machines being used as if they were $30,000 manual machines because the company could not get past the complexity of the machine. This is not capital efficient. The other reason for caution is that advanced technologies are more prone to downtime.
The key to making good investments in new technology is to be br utally honest in your assessment
In over 20 improvement projects over the past five years, each one has shown significant gains in that period. Doubling production with the same assets or halving lead time are common outcomes from these efforts.
of current practices. In general, the current operations have much more capacity that is realized. Challenge all assumptions. If you are told that a machine is at capacity, ask how they know. Insist on seeing data about downtime, idle time, and scrap rates. Learn what speeds the machines are running at, their rated speeds, and the obstacles that are preventing operators from using the full capabilities of the machines. Understand the planned cycle time, and find out what has been done to reduce it. Get data about the work balance along the production process. Learn what improvements have been tried, and insist on seeing how those efforts were measured.
I n most cases, four months of focusing on achieving operational performance improvements will show
you whether there is a need for new technology. In over 20 improvement projects over the past five years, each one has shown significant gains in that period. Doubling production with the same assets or halving lead time are common outcomes from these efforts.
If, after all that, there is still not enough capacity, or if the technology allows you to carry out processes that you do not have the capability to do now, then, and only then is it worth exploring the benefits of advanced technology.
When a company works that way, it will become very capital efficient. It will also, inevitably, increase labour productivity. The result will be better service to customers, and, incidentally, better profits.
Hugh Alley, P.Eng. is the president of First Line Training Inc. and provides core skill training for front-line leaders and coaching for senior managers to develop skills in methodical, systematic thinking and continuous improvement. He is the author of Becoming the Supervisor: Achieving Your Company’s Mission and Building Your Team. He is based in Burnaby, British Columbia.
In 2023 Canadian manufacturers battled supply chain issues, the rising costs of raw materials, and a growing labour shortage as they continued to adopt Industry 4.0 technologies to innovate and explore new ways to flourish in a changing economy.
Supply chain troubles were brought on by geopolitical unrest, seeing manufacturers nearshore their supply chains at unprecedented rates. New security concerns, rising inflation and a g rowing labour shortage are all influencing manufacturers to change their investments to adapt through the changing market.
Plant and Canadian Manufacturing’s 2024 Advanced Manufacturing Outlook survey
BY SADI MUKTADIRfound that manufacturers are still investing in and adopting advanced technologies to improve processes, enhance operations and bolster security measures against increase threats. The survey measured advanced manufacturing (Industrial Internet of Things (IIoT) and Industry 4.0 technology) engagement among 257 manufacturing business owners, leaders, and senior executives.
For the fifth consecutive year, the research was led by R.K. Insights in Toronto, and
conducted through the months of June and July, in partnership with sponsors: Epicor, MNP, Mitsubishi HC Capital, EMC and Alps Welding Ltd. The margin of error was +/- six per cent, 19 times out of 20.
As part of our survey, advanced manufacturing is defined as manufacturers focused on interconnectivity, machine learning, automation and the analysis of real time data that involves the IIoT, the cloud, advanced computing, and artificial intelligence.
This year’s survey took a close look at the results of mass adoption across the industry, and which parts of the business these technolog ies were being integrated in. The trends continue to persist, with some stagnation and some growth in certain areas. Unrestrained g rowth was challenged by a volatile market, and an industry juggling the pressures of inflation.
Despite this, companies continue to apply IIoT technologies to explore new ways it can help their businesses. Inflationary pressures and supply chain delays have been affected by the global market, with some companies even quicker to adopt Industry 4.0 solutions to stay ahead, and in some cases slowing them down and investing in other areas of their businesses instead.
A total of 25 per cent of respondents now say there’s been no change in the amount of intended spend, compared to 32 per cent two years prior. The core challenges seem to be a lack of skilled talent across the sector, a supply chain affected by global unrest and the rebound from the global COVID-19 pandemic. Other hurdles include increased cybersecurity concerns in the face of increased and evolving attacks, and
complexities arising from the integration of advanced technologies into legacy processes. Manufacturers are juggling a myriad of pr ior ities when it comes to their Industry 4.0 investment, showing a frugal appetite with their capital amid other concerns.
“The core part of a technology investment is in the integration,” said JP Giroux, president, EMC. “This is linked to a lack of awareness on the skilled talent that’s available that can help there. A lack of skilled talent is acting as a bar r ier to take on these new technology deployments. I can see a solution around skills development related to digital adoptions that can build the capacity to take on these projects.”
This year, 34 per cent cited costs as a reason for not investing in technology,
suggesting that an Industry 4.0 investment is jockeying with other priorities for business owners. IIoT as a growth opportunity was seen by 82 per cent of respondents, with c-suite executives dropping their support for advanced technology tools to 72 per cent from 80 per cent the year prior.
However, adoption continues as manufacturers are aware of the evolving industry and the necessar y role advanced manufacturing technologies will play in their business’ success. Only 66 per cent of manufacturers now believe that investing in new technologies raises the company’s cyber security risk, a drop from 74 per cent the year prior. Only 54 per cent believe machinery replacement is too large of an investment and will cause downtime they can’t afford, down from 73 per cent the year prior.
“Global market uncertainty is certainly a factor, and based on several discussions with Canadian manufacturing CFOs, these stats can be attributed to a combination of increased costs due to labor, higher interest rates servicing debt, and inflationary pressures, but also risk mitigation, with companies preserving cash flows and choosing to “wait and see,” as opposed to taking on
Only 66 per cent of manufacturers now believe that investing in new technologies raises the company’s cyber security risk, a drop from 74 per cent the year prior.
any large technology change (like an ERP system) at the risk of failure when they don’t have the internal resource capacities for a successful deployment,” said Tony Alderdice, vice-president of sales, Epicor.
Eight per cent of respondents repor t that their operations have “no automation systems in place,” a change from two years ago when 13 per cent still had no automation systems.
The top applications of IIoT have changed somewhat because of inflationary pressures and supply chain issues. The persistent top spot still belongs to improving efficiency and productivity (36 per cent), but now, manufacturers are more interested in the visibility of data from across all manufacturing operations (27 per cent), providing visibility into production processes (25 per cent), tracking materials and shop floor assets (24 per cent), analytics functionalities (23 per cent), and improving maintenance functions (21 per cent).
From those currently applying Industry 4.0 technologies, 50 per cent are using it to improve maintenance functions, suggesting an emphasis on stable operations and business continuity.
“It’s often tough to finance IIoT deployments, but if it’s attached to machinery and equipment, it becomes more valuable to the lending community. We can certainly clear
some of the hurdles to an investment once we start to bill for the software and utilization of the equipment as opposed to the equipment itself in a traditional sense,” said Paul Green, Director, Mitsubishi HC Capital
Many businesses have been influenced by the post-pandemic economy and have adjusted their planned spend on Industry 4.0 technolog ies, with 65 per cent saying their planned spend has increased, and nine per cent saying there’s been a decrease. In the next three to five years, manufacturers plan to spend on robotics/automation (55 per cent), data capturing at machine/shopfloor (50 per cent), advanced analytics (50 per cent), ERP (47 per cent), cloud computing (40 per cent) and cybersecurity (40 per cent). The intended amount to spend on
these technologies over the next three years has dropped from last year to an average of $1.8 million, which is in line with the years prior to last.
The most significant benefits seen by manufacturers has adjusted from prior years. The top cited benefits manufacturers have seen are a lower cost of operation (37 per cent), reduced downtime (36 per cent), increased throughput (32 per cent), and an increased quality of product (29 per cent). In previous years, an increased throughput and an increased quality of product ranked higher “When we implemented our ERP system, we hired a full-time employee just to run the implementation. When people ask me what’s involved in an ERP implementation, I tell them that for a small business like ours, you basically must add full-time employee to implement and then run it on an ongoing basis. Part of the cost is in having a skilled person in-house to operate. There’s no substitute for having skilled people,” said Dennis Dussin, president, Alps Welding Ltd.
The number of manufacturers not convinced of the business benefits in a technology investment is at 17 per cent, with difficulties integrating advanced technologies in existing systems (37 per cent) being listed as the top reason for not implementing new technologies. Last year, the leading reason for not implementing new
Photo: ©Lubos Chlubny / Adobe StockMany businesses have been influenced by the post-pandemic economy and have adjusted their planned spend on Industry 4.0 technologies, with 65 per cent saying their planned spend has increased, and nine per cent saying there’s been a decrease.
technologies was that it was too costly (33 per cent), which remains as a key reason still this year.
Regarding how manufacturers were collecting and using the data in their operations and influencing their decisions; 64 per cent are using spreadsheets such as Excel, 57 per cent are using integrated ERPs, 48 per cent are using accounting software, 35 per cent continue to use manual paperwork, 32 per cent are using an MRP, and 26 per cent are using sensors to capture big data (a trend that continues to increase).
“We’re realizing and noticing a lot of times that a company isn’t using its ERP system and only 20-30% of the data they are collecting. The data isn’t being translated into actionable items on how to improve the organization’s throughput, efficiency, or productivity. A lot of times, those factors are too often looked at as single variables as opposed to collectively,” said Hussam Malek, partner, consulting at MNP.
In terms of cybersecurity, manufacturers continue to express growing levels of concern in relation to their businesses, with 76 per cent rating themselves as highly concerned, versus 24 per cent not concerned. Significantly, most manufacturers have exper ienced a cyber-attack at their company (74 per cent), a large jump from the previous year (56 per cent).The leading types of attacks are phishing (57 per cent), ransomware (18 per cent), a targeted external cyber-attack (15 per cent) and a breach through a third-par ty vendor (11 per cent).
“Anytime you have connected devices they are a risk. Our ability to mitigate is proportionate to our awareness of the risk. COVID-19 heightened the awareness, but the risk was always there. People are thinking twice about having connected devices because it’s creating challenges from a cybersecurity standpoint,” said Kerry Mann, national ERP technology lead and par tner, MNP Digital
When it comes to bolstering security, 97 per cent of manufacturers have taken some measures to protect themselves
from cyber-attacks, including a security infrastructure (73 per cent), a cybersecurity strategy (62 per cent), data privacy controls (58 per cent), and a cybersecurity risk assessment/review (56 per cent). Only 20 per cent of manufacturers feel they have taken all possible precautions to protect themselves from cyber-attacks, with 80 per cent recognizing that they need to do more.
Overall, 64 per cent of manufacturers in the survey have a data governance policy
in place, and 63 per cent of manufacturers are concerned for the future of businesses that do not invest in advanced manufacturing technologies.
Manuf acturer s listed missing out on new business opportunities (47 per cent), pricing pressures because of automation (36 per cent), low margins (32 per cent) and disruption by industry outsiders (31 per cent), as their main concer ns if they do not invest in Industry 4.0 technologies.
• Patented torque traceability and curve detection for high accuracy
• Durable high resolution non-contact torque sensor for reliable torque measurement
• Efficient and long battery life
• Virtually no torque reaction from 2Nm to 100 Nm
64 per cent of manufacturers in the survey have a data governance policy in place, and 63 per cent of manufacturers are concerned for the future of businesses that do not invest in advanced manufacturing technologies.
Gladiator GECP series modular 12/24 VDC circuit protectors offer both fixed trip current versions and a version with an adjustable trip current range and adjustable trip characteristics. LED signaling with output alarms allows real-time status monitoring. It is compact and lightweight.
The protection modules, in ratings up to 10A, can be used as standalone devices or integrated into a modular system using optional supply and ground modules, busbars, and comb jumpers. The modules offer a remote set/reset function. automationdirect.com/electronic-circuit-breakers
against industry best practices, and deliver actionable, prioritized savings recommendations.
Energy Analytics, organizations can enable access to historic telemetry data from their existing measurement infrastructure, which is then mapped, cleaned, and pre-processed to enable structured analysis within the analytics platform. Samotics’ enables organizations to realize and report energy savings of up to 15 per cent through continuous optimization.
Energy Analytics complements SAM4 technology ecosystem, which uses electrical signature analysis (ESA) to enable continuous monitoring of the assets’ health, performance and energy efficiency. Where an organization’s existing monitoring data is incomplete in terms of volume or quality, SAM4 Energy sensors can be installed. samotics.com
transfer, has a maximum read/write distance of 220 millimetre depending on the type of tags used, operates on RFID high frequency of 13.56 MHz per ISO 15693, and features an IP67 protection rating. automationdirect.com/rfid-devices
H. G. Schaevitz LLC, Alliance Sensors miniature position sensors. LZ-13 series are inductive, contactless devices designed for use in factory automation or assembly machinery applications. LVIT (linear variable inductance transducer) is offered in nominal full-scale ranges from 2.5 to 200 millimetres. The sensor has 12.7 mm outside diameter stainless steel body with a one metre cable for I/O connections. The 4.78 mm diameter through-bore of an LZ-13 provides clearance for its four mm diameter moving target rod with M4 thread and hex nut, made of the same material as its housing.
LZ-13 Features:
• LVIT technology;
Samotics latest energy efficiency solution, Energy Analytics platform, enables industrial organizations to help with energy savings and reduce associated CO2 emissions.
Energy Analytics provides insight into the efficiency of rotating equipment, benchmark performance
All-in-one RFID standalone R/W unit comes with an RFID R/W device, antenna, and EtherNet/IP interface built in and is designed for integration into an existing EtherNet/IP network.
This standalone unit is optimized for high speeds and large data
• Contactless operation. Excellent stroke-to-length ratio;
• Through-bore design; Full-scale ranges from 2.5 to 200 mm. LVIT linear position sensors offer senset field programmability. alliancesensors.com
• MPW series manual motor protectors in ratings up to 65A;
• CWB series IEC contactors in ratings up to 125A;
• RW117 series overload relays in ratings up to 140A automationdirect.com/safety-contactor
WEG Electric CWBS series IEC safety contactors control electrical power in industrial and commercial applications. Available in ratings up to 80A, they comply with IEC and UL standards, providing mechanically linked and mirror contacts.
WEG Electric motor control offering include the following:
• ESWS/PESWS series single-phase general purpose and washdown manual motor starters in ratings up to 3hp at 230 VAC (23A); ESW/PESW series three-phase general purpose and washdown enclosed manual motor starters in ratings up to 50hp at 575 VAC (80A);
24-7-365
Carlo Gavazzi SPDE Power Supply Series, two-phase (bi-phase) and three-phase DIN-rail mount power supplies for electrical panels with limited space. They offers power ratings from 120 to 480 W with 24 and 48 VDC output, and input voltage range with AC voltage or with DC voltage. SPDE Series is certified by a series of industry
approvals: CE, UKCA, UL61010, EN62368-1. Integrated diagnostics and protection functions such as output short circuit, over current, over voltage, and over temperature provide output protection. Features include: Universal AC/DC input voltage range; output voltage range of 24 VDC or 48 VDC; output power range for up to 120 up to 480 W; built-in active PFC; DC OK relay indication; overvoltage category III. gavazzionline.com.
and an external thread mount on the shaft end of the spindle to mount ball heads, clamping hooks or other common adapters.
• AA3123 - 5,300 N peak force, 1,300 N continuous force and 0.28 m/s maximum speed. Or 2,650 N peak force, 650 N continuous force and 0.56 m/s maximum speed.
• AA3133 - 12,500 N peak force, 2,800 N continuous force and 0.12 m/s maximum speed. Or 6,000 N peak force, 1,400 N continuous force and 0.24 m/s maximum speed.
Photo:Beckhoff.. Beckhoff AA3100 is designed as a drop-in replacement for hydraulic or pneumatic actuators. AA3100 devices leverage an ISO 15552 flange size and bolting points on both sides
AA3100 features: integrated mechanism: devices feature roller bearings, ball screw and guide. Commissioning: 24-bit multiturn encoder with high resolution, one cable and an electronic identification plate. Data access: TwinCAT 3 automation software. Customizability: a range of spindle pitches and a backlash-free holding brake are available.
beckhoff.com
Visit
bramaleamro@sew-eurodrive.ca
Manufacturing is critical to the economic prosperity of all Canadians. It’s more important than ever in a world of escalating geopolitical risk, where we are faced with many global challenges. These include climate change, food and water shortages, and health crises. However, the future for manufacturing in Canada will be brutish, nasty, and short, if manufacturers themselves are unable to take advantage of the transformational challenges that lie ahead.
Manufacturing is the business of making things. However, if that’s all companies do – get more and more product out the door at lower and lower costs – manufacturing will not survive in Canada. That’s a commodity game in which companies are being rapidly dr iven out of business.
Manufacturing in Canada must become a solutions-based business focused on customized value, not just volume and cost reductions alone. The future lies in advanced manufacturing.
Advanced manufacturing entails the use of leading-edge technologies
and techniques to grow the business by solving problems and making things – often new things – for customers, in significantly better ways. How companies make the transition to advanced manufacturing will determine their ability to sustain customer demand, compete, and grow.
What companies make is important; so too is how they make them. Manufacturers need to offer their customers a unique value proposition to compete and grow in today’s f ast-paced and highly competitive business environment. They need to offer a solution – a product or service – that their customers can manage, at a level of quality and convenience their customers expect, at the time their customers want, at a price point their customers can afford, and do all that better than anyone else.
Innovation is key. It’s a global race. Manufacturers around the world are in a rush to create new and better solutions, new ways of adding value through the products and services they offer, new ways of generating revenue, and better ways of responding to and taking advantage of the
transformations that are reshaping the industry around the world.
Stepping back a bit, you can see five interrelated transformations that are creating new and unprecedented business challenges, opening new commercial opportunities, and leading to new ways of doing business for manufacturers in Canada and elsewhere.
First, market conditions are rapidly changing as competition intensifies and customers, stakeholders, investors, and governments are demanding more customized products and services, immediate response, and more stringent compliance with responsible environmental, social, and governance practices. The short-term weakness manufacturers are currently experiencing in market demand created by inflation, higher interest rates, and a slowing economy is temporary. It will be structural changes in global markets and customer preferences that will disrupt manufacturers long-term.
Supply chain disruptions are a second source of structural change. They are elevating the risks of global sourcing, forcing companies to restructure their supply base, while creating new
Photo: Mick Koulavong /iStock / Getty Images Plus/Getty ImagesThrough Canada’s largest and only not-forprofit energy buying group for manufacturers, EMC is helping hundreds of manufacturers and processors to mitigate energy price volatility and access savings, driving waste and costs out of their supply chain.
For over 20 years, EMC has offered the WSIB recognition program to Ontario manufacturers. We are a WSIB-approved HSEp provider that will help you along the journey to Health and Safety excellence.
Developed in collaboration with the country’s leading manufacturers, the Learning Centre provides an extensive catalogue of learning options to suit the needs of all employees, including self-directed online, virtually facilitated and in person training.
business opportunities for companies agile and innovative enough to offer new solutions to new customers.
Sustainability is a third long-term transformative force. The need to cut emissions, eliminate harmful products, and address global challenges related to industrial impacts on the environment is forcing manufacturers to adopt new technologies to monitor and reduce their carbon footprint and their resource requirements, but also create new business and supply chain models based on environmentally-friendly products, circular economies, supplier traceability, and full life-cycle product m anagement. Sustainability will become a hot topic in 2025 when Canadian insurance companies and banks begin to require their industrial clients to report their carbon emissions and those of their suppliers.
Demog raphic challenges are also driving transformation in manufacturing. Labour shortages will only get worse as a quarter of Canada’s manufacturing workforce will retire by 2030 and fewer workers are entering the labour pool. Companies will need to automate simply to keep production levels where they are today, let alone grow. Skills shortages will also become more acute. The problem will not be solved through immigration. It must be addressed through a concerted effort to skill, upskill, and reskill workers in manufacturing occupations.
Finally, there is the impact of technology itself. The rapid development and deployment of advanced digital, materials, and production technologies are helping manufacturers
make significant improvements in productivity by increasing operating efficiencies, enhancing production flexibilities and employee capabilities, speeding up new product design, testing, and engineering, and strengthening supply chain collaboration by connecting customer s and suppliers more effectively. They are enabling the creation of new products, new data-based services, and new lines of business. At the same time, they are threatening the long-term viability of manufacturers whose businesses are being disrupted by new and improved products and services. Canada’s auto parts sector is on the front line of disruption as the industry transitions to electric vehicles.
Manufacturing is the ultimate integrator of technology. Technologies are the modern tools that manufacturers use to generate value for their customer s, improve operating efficiencies, and connect with customers and supplier s. However, technologies by themselves are not sufficient to achieve desired business outcomes. Their commercial potential in manufacturing can only be realized when they are applied and integ rated in manageable, cost-effective solutions that can be demonstrated to work at full-scale levels of production.
It takes strategic leadership to determine business objectives and to navigate the challenges and pursue the new opportunities arising in a dynamic economic environment. Specialized management skills are needed to implement technology solutions, continuously improve business and production processes to maximize
operating efficiencies and enable the value chain collaboration required for rapid innovation. Most importantly, people need to be employed who can work together with the skill sets necessary to use technologies productively, sustain process excellence, and achieve desired business results.
No single company can manage all the risks or take advantage of future opportunities on its own. Collaboration will be critical for business success – researchers, technology providers, and manufacturers working together to develop, adopt, scale up, and commercialize new products and processes fast. Industry coming together to solve common skills challenges, demonstrate best practices, and build the infrastructure required for successful scale-up of new manufacturing companies. Governments, businesses, and financial services need to understand what it takes to run a successful manufacturing operation, not just develop a new technology.
We need to look at what it takes to support the development and scale-up of new manufacturing businesses in emerging fields like biomanufacturing and life sciences, robotics, advanced materials, microelectronics, and smart devices. The ability of Canadian technology companies to commercialize solutions, scale up, and grow into globally competitive enterprises has long been recognized as a weakness in converting Canada’s stellar record in research and development and our world-leading start-up ecosystems into real economic benefit for Canadians. It all depends on manufacturing – on innovation partnerships and developing and applying the value-adding solutions that our tech companies can bring to the sector.
Is this a role for government?
Partially. However, leadership must come from manufacturers themselves. It will be the ingenuity and entrepreneur ship of business leaders who want to build and grow their business in Canada and who see that as an industry and economy-wide endeavour that will make the difference. Let’s hope we are up to the task.
Photo: gorodenkoff/iStock / Getty Images Plus/Getty Images Jayson Myers, the CEO of Next Generation Manufacturing Canada, an award-winning business economist and advisor to private and public sector leaders. E-mail jayson.myers@ ngen.ca. Visit www.ngen.ca.RS-232
Advanced motion control with up to 400 moves per axis and various single- and multi-axis operations including position and speed control, helical interpolation, and ellipse interpolation
FREE IEC programming with structured text, ladder logic, and more
Multiple networking options including support for EtherNet/IP, Modbus TCP, Modbus RTU and ASCII
High-density I/O (32 points embedded on CPU and select I/O expansion modules)
High-speed I/O (integrated 2- or 6-axis pulse/direction motion inputs/outputs (up to 200kHz) on the CPU module, and up to 4 channels of high-speed inputs at up to 500kHz on each high-speed counter module)
FREE award-winning service and technical support
The XGB PLC from LS Electric has many great features including cutting-edge motion control and powerful software, but add to that the customer satisfaction, the amazing $299.00 starting price, and the FREE tech support provided by AutomationDirect, and you’ll de nitely say “YES!” to LS!
HS Pulse positioning Highspeed I/O Advanced motion control FREE IEC-based software Research,
I/O
Orders over $49 get FAST FREE SHIPPING
*Free shipping does not apply to items requiring LTL transport, but those shipments can take advantage of our negotiated super-low at rates (based on weight) that include brokerage fees.
See Web site for details and restrictions at: www.automationdirect.com/canada
To see all products and prices, visit www.automationdirect.com All prices shown are U.S. Dollars
45 4 5dayMoney-BackGuarant e e