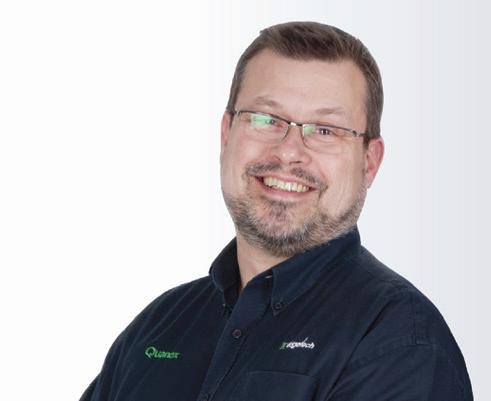
9 minute read
Letters
YOUR LETTERS
WHAT’S YOUR OPINION?
Feel free to get in touch with your views on the industry, legislation, government, or even the newspaper.
Contact Chris:
chris@glassnews.co.uk
MORE GOOD NEWS ON UKCA MARKING – BUT ARE WE STILL IGNORING THE OBVIOUS SOLUTION?
Dear Chris,
At Edgetech, we’re delighted that common sense has prevailed for a second time regarding product safety regulations and the UK’s exit from the EU – but we still have some concerns.
We’ve been closely following the government’s plans for replacing the CE mark: the symbol that, for decades, has indicated whether a product complies with EU health, safety and environmental protection laws.
When the UK voted to leave the EU, it was inevitable that system would have to change - but in the early stages, the government’s handling of the process was far from satisfactory. Ministers suddenly announced that businesses would have to start complying with its new UKCA mark by January 2022 – leaving extremely little time for thousands of companies to get vast numbers of products retested.
Faced with a backlash from industry and lobbying from trade bodies, the government reconsidered, recognised the challenges faced by industry, and extended the deadline to 1st January 2023. Now, they’ve gone further. One of the biggest challenges preventing businesses from certifying their products to the new UK standard was the lack of a mutual recognition agreement that would allow them to use test data from EU recognised notified test houses to support their certification. This has changed. The government has made it clear that AVCP System 3 testing data from an EU recognised notified body will be accepted until the 31st December 2022.
This makes things significantly easier for UK businesses to achieve UKCA marking and is therefore an extremely positive move. However, one of the core difficulties still remains. Even now that data from EU notified bodies will be accepted, there are still only a relatively small number of test centres to go around – and thousands of businesses from multiple sectors rushing to get their products tested. Our fear is that this is only going to provide short term relief, and many of these tests take many months to complete in test centres already backed up. So there’s the question of what happens in the long-term. After we reach the 1st January 2023 deadline, if testing is delayed or incomplete, or if recertification is required as a result of product introduction or changes, what happens then? If the only test resources are UK approved bodies, how does the industry cope, particularly when not all certification required is even available from a UK approved body? Currently there’s a lack of UK Approved Bodies capable of testing IGUs to certain specific requirements in EN1279 or WA17/1 thermal testing in the UK.
And then there’s the extremely complicated situation in Northern Ireland – where businesses are faced with the costly and challenging prospect of having to meet CE, UKCA, and the territory’s own UKNI marks all at once, potentially having to gain duplicate certification from different regional test bodies. Rather than a succession of quick fixes, none of which deal with the core issue, we hope we’ll see ministers in the UK and the EU agree on the most pragmatic solution – an ongoing Mutual Recognition Agreement, that sees EU body test certificates accepted in the UK and vice versa.
Yours sincerely,
Gary Shoesmith
Head of Technical & Quality, Edgetech UK
COST CONTROL IS CRITICAL
Dear Editor,
It’s been a tricky few months.
The positive is that the supply chain has now, to a point, stabilised. In most instances we’re getting the materials that we need to get product made and out the factory gates to our customers in the time frames that we would expect to be able to do it. COVID is still with us but it’s not as disruptive. What’s made things challenging are the price increases and surcharges, some expected, others coming to us from more or less, out of the blue.
Given the increase in wholesale energy prices, the massive increases that we’ve seen in glass costs was always on the cards. Increases driven by increased demand for resin were also expected to feed through. But we’ve also seen a multitude of other cost increases, further energy surcharges and on top of that, big increases in what we pay for energy and fuel and labour costs.
Despite this we took the decision to hold our prices for sixmonths, starting in February this year. It’s a decision which has allowed our customers to price each job effectively, particularly those operating in the commercial sector, where lead times are longer, or those running very big order books.
It’s meant that that our customers haven’t seen their margins eroded because in the space between the time they won the work and the product has been delivered, it’s gone up in price. We’ve been able to achieve this through an element of margin sacrifice in our own business – but most importantly through the operational efficiencies that we’ve achieved in the last year, which have helped us to control costs to our customers.
COVID made us review everything that we were doing. We asked ourselves a simple question, ‘how could we operate more efficiently to deliver a better service?’. We did that because we had to. Our OTIF wasn’t where we wanted it to be.
But in adapting to those challenges and changing how we work for the better, we’ve been able to drive improved quality and service, while controlling costs. This has included a redesign of our factory floor to improve efficiencies and quality; we invested in a new fleet which has helped to lower the impact rising prices at the pumps are having on all logistics businesses; the solar panels we installed on our roof have supported us in controlling energy costs.
And we’ve also driven cultural change, investing in the training and development of our people, so that they’re more engaged and better at what we do. We review, learn and do better again. That’s contributed to efficiency gains across our business of between 12 and 15% in the last year. That’s not something we’ve pocketed and set against our bottom line, we’ve passed it directly to our customers for the past six-months and will continue to do so, as far as we can, going forward. We’re also investing for that future. Glass supply has been a key pinch point. With our own IGU business, the purchasing power and the partnership we have with Saint Gobain, we’ve been able to take the edge off those price increases for those customers who buy glass from us. We will strengthen our hand, when we take receipt of a new Forel IGU line in the autumn. At more than £1million, it represents the single biggest investment ever made by an Emplas Group company and will support us in driving further efficiencies, controlling future costs.
Inflation is here to stay in the short term. That creates two key challenges for our industry. Manufacture and supply costs more, at a time when homeowners have less to spend. We can do little about the latter, but we can control costs - or at the very least some of them.
We’re family-owned, investment led and planning for the future. Will we be able to hold our prices forever? Well, you know the answer as well as I do.
When it happens, our customers will, however, know that it’s not for a want of trying on our part and will have and will continue to benefit, from our investment programme and the controls on costs that it has delivered, going forward.
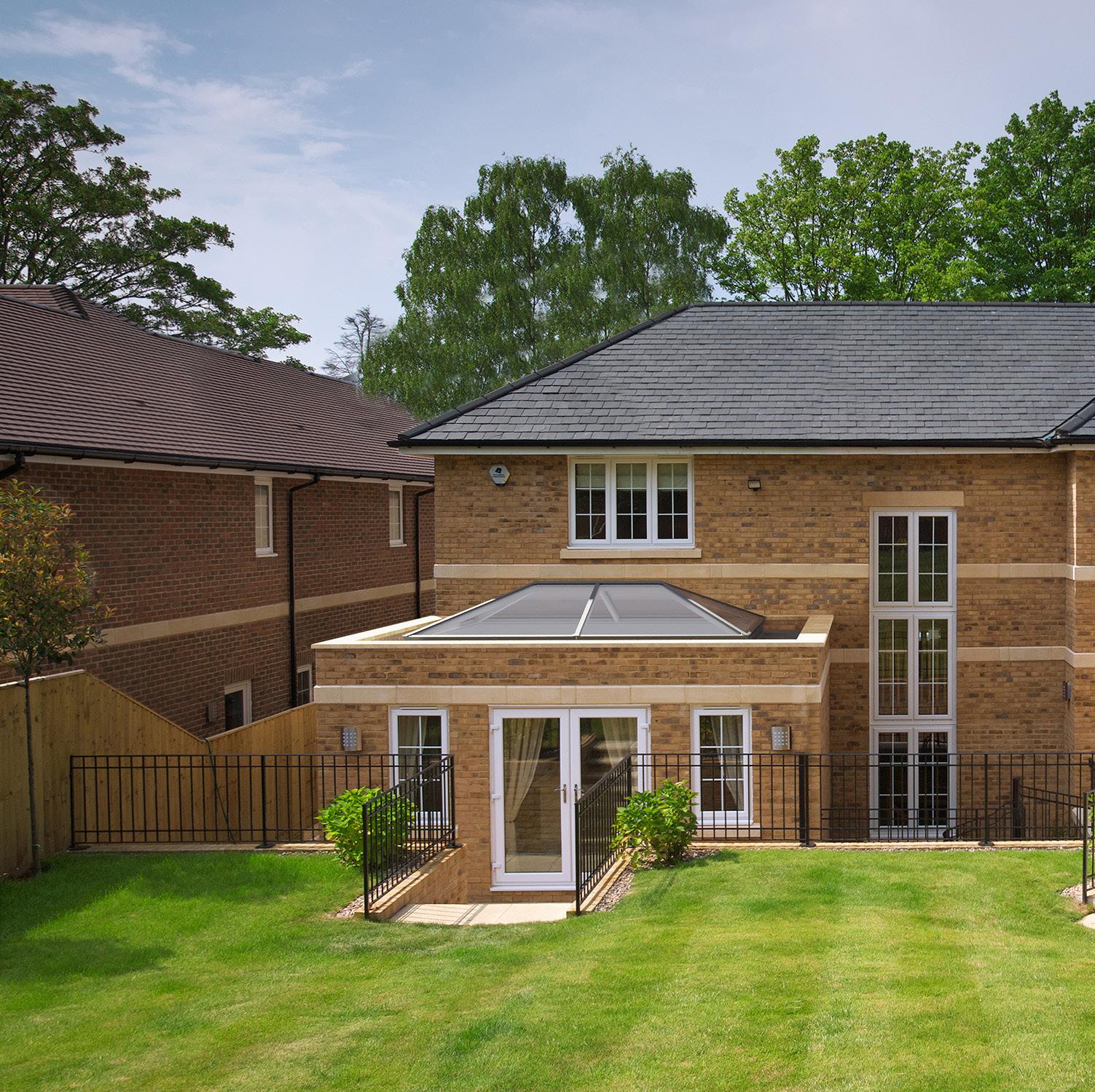
THE UK’S BEST TIMBER FRAMED SOLID ROOF Our Icospan flat roof now features the Sheerline S1 lantern as standard THE UK’S BEST TIMBER FRAMED SOLID ROOF Our Icospan flat roof now features the Sheerline S1 lantern as standard THE UK’S BEST TIMBER FRAMED SOLID ROOF Our Icospan flat roof now features THE UK’S BEST TIMBER FRAMED SOLID ROOF Our Icospan flat roof now features the Sheerline S1 lantern as standard THE UK’S BEST TIMBER FRAMED SOLID ROOF Our Icospan flat roof now features the Sheerline S1 lantern as standard THE UK’S BEST TIMBER FRAMED SOLID ROOF Our Icospan flat roof now features the Sheerline S1 lantern as standard
the Sheerline S1 lantern as standard
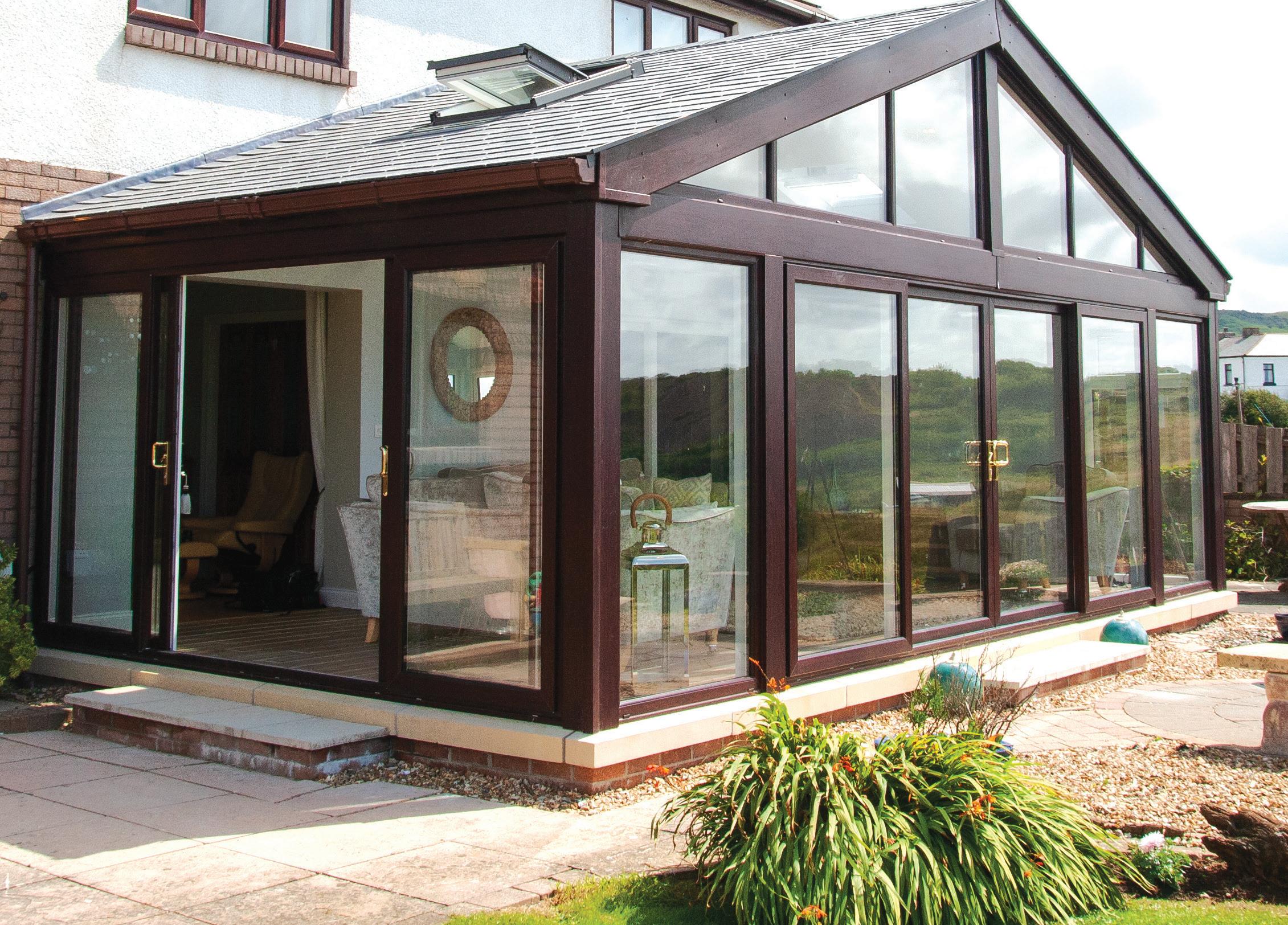
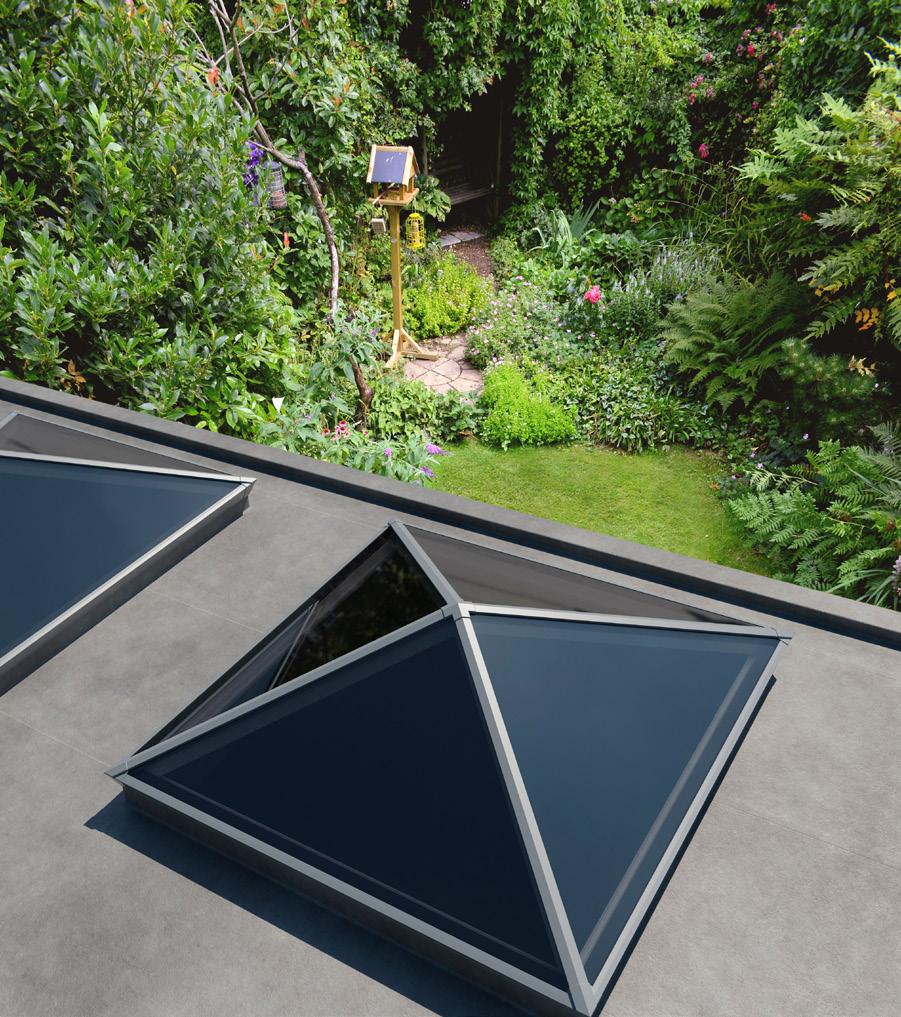
• TILES DELIVERED WITH THE ROOF, INSULATED PLASTERBOARD AVAILABLE • TILES DELIVERED WITH THE ROOF, • TILES DELIVERED WITH THE ROOF, INSULATED PLASTERBOARD AVAILABLE • TILES DELIVERED WITH THE ROOF, INSULATED PLASTERBOARD AVAILABLE INSULATED PLASTERBOARD AVAILABLE • TILES DELIVERED WITH THE ROOF, • SLATE OPTION AVAILABLE WITH: 3-WAY TOP CAPS, END CAPS• TILES DELIVERED WITH THE ROOF, • SLATE OPTION AVAILABLE WITH: 3-WAY TOP CAPS, END CAPS• SLATE OPTION AVAILABLE WITH: 3-WAY TOP CAPS, END CAPS INSULATED PLASTERBOARD AVAILABLE • SLATE OPTION AVAILABLE WITH: 3-WAY TOP CAPS, END CAPS INSULATED PLASTERBOARD AVAILABLE • PRECUT SHINGLE TILES AVAILABLE (CONDITIONS APPLY); 3-WAY & 5-WAY TOP CAPS• PRECUT SHINGLE TILES AVAILABLE (CONDITIONS APPLY); • SLATE OPTION AVAILABLE WITH: 3-WAY TOP CAPS, END CAPS • PRECUT SHINGLE TILES AVAILABLE (CONDITIONS APPLY); 3-WAY & 5-WAY TOP CAPS • PRECUT SHINGLE TILES AVAILABLE (CONDITIONS APPLY); 3-WAY & 5-WAY TOP CAPS • SLATE OPTION AVAILABLE WITH: 3-WAY TOP CAPS, END CAPS 3-WAY & 5-WAY TOP CAPS• PRECUT SHINGLE TILES AVAILABLE (CONDITIONS APPLY); • LOW PITCH VELUX AVAILABLE • PRECUT SHINGLE TILES AVAILABLE (CONDITIONS APPLY); • LOW PITCH VELUX AVAILABLE • LOW PITCH VELUX AVAILABLE 3-WAY & 5-WAY TOP CAPS • LOW PITCH VELUX AVAILABLE 3-WAY & 5-WAY TOP CAPS • NATIONWIDE DELIVERIES• NATIONWIDE DELIVERIES • NATIONWIDE DELIVERIES• LOW PITCH VELUX AVAILABLE • NATIONWIDE DELIVERIES• LOW PITCH VELUX AVAILABLE • NATIONWIDE DELIVERIES • NATIONWIDE DELIVERIES
0.15 U-VALUE BUILDING REGS COMPLIANT 0.15 U-VALUE BUILDING REGS COMPLIANT 0.15 U-VALUE 0.15 U-VALUE BUILDING REGS COMPLIANT 0.15 U-VALUE BUILDING REGS COMPLIANT 0.15 U-VALUE BUILDING REGS BUILDING REGS COMPLIANT COMPLIANT
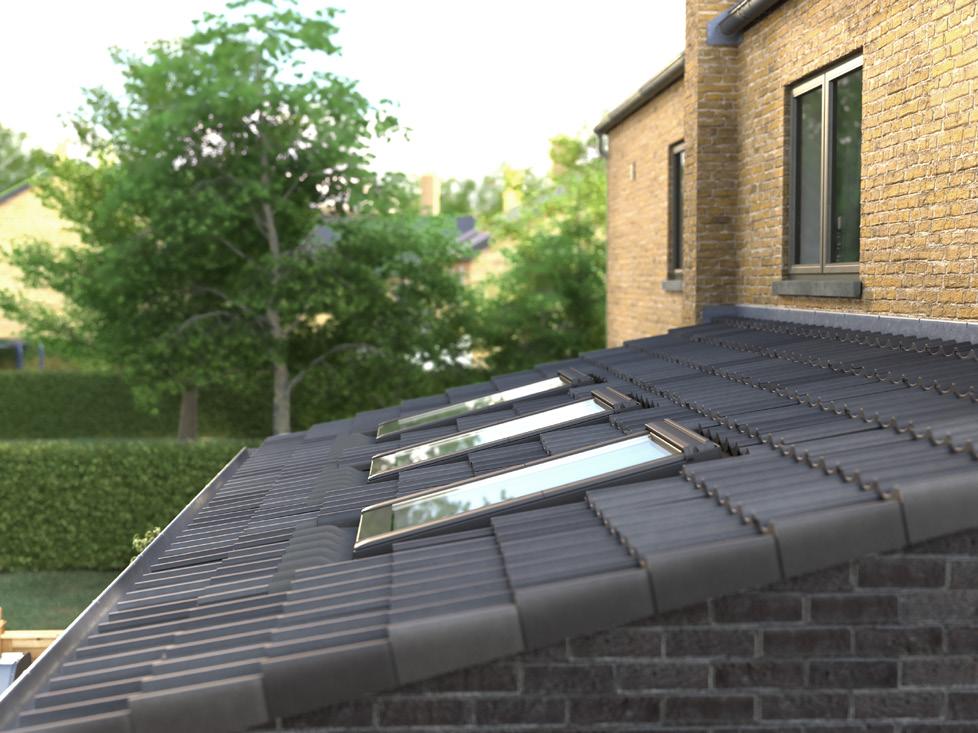
SHEERLINE - STYLE 3 SHEERLINE - STYLE 3 SHEERLINE - STYLE 3 SHEERLINE - STYLE 3
SHEERLINE - STYLE 3
SHEERLINE - STYLE 3
SHEERLINE - STYLE 1 SHEERLINE - STYLE 1 SHEERLINE - STYLE 1 SHEERLINE - STYLE 1
SHEERLINE - STYLE 1
SHEERLINE - STYLE 1
LOW PITCH LOW PITCH LOW PITCH LOW PITCH
LOW PITCH
For a quote, please call us on 01204 773040, or email us on sales@icotherm.co.ukThe Solid Roof Company Building Control Compliant: We recommend MFA for your building control certification needs. They know the Icotherm roofs, they understand your needs. For a quote, please call us on 01204 773040, or email us on sales@icotherm.co.ukThe Solid Roof Company Building Control Compliant: We recommend MFA for your building control For a quote, please call us on 01204 773040, or email us on sales@icotherm.co.ukThe Solid Roof Company LOW PITCH For a quote, please call us on 01204 773040, or email us on sales@icotherm.co.ukThe Solid Roof Company Building Control Compliant: We recommend MFA for your building control certification needs. They know the Icotherm roofs, they understand your needs. For a quote, please call us on 01204 773040, or email us on sales@icotherm.co.ukThe Solid Roof Company Building Control Compliant: We recommend MFA for your building control certification needs. They know the Icotherm roofs, they understand your needs. For a quote, please call us on 01204 773040, or email us on sales@icotherm.co.ukThe Solid Roof Company