
3 minute read
Case Study
ONLINE AND OFFSITE
– HOW DEMPSEY DYER MANAGED FRESH CHALLENGES AT THE RIVERSIDE
Deceuninck fabricator Demspey Dyer was recently involved in the construction of new student accommodation at The Riverside at Canterbury, which drew on 45 years of experience.
The trade fabricator delivered 666 Deceuninck 2500 Heritage Chamfered windows as part of a £115 million mixed-use development, and was involved in every stage of the project – design, build and delivery. In a bid to drive efficiency and quality, and to overcome obstacles, Dempsey Dyer pioneered new ways of working including shipping products and expertise between continents.
The Riverside is a £115 million mixed use development at the centre of a new leisure quarter in the historic city of Canterbury. The development has a new public square at its heart and overlooks the River Stour that runs through the city centre. This leisure-led destination will be anchored by a five-screen Curzon Cinema, with restaurants, external public seating, and areas to host pop-up events. The wider development also delivers 189 new homes and 491 student bedrooms, all within a pedestrian-friendly neighbourhood. Main contractor Bouygues UK wanted to drive a new approach to modular building, and enlisted the help of Dempsey Dyer as its fenestration partner. To ensure the windows fitted the modular build efficiently, Dempsey Dyer worked closely with systems partner Deceuninck to meet certain requirements, such as 100mm openings. Deceuninck was also involved in the architect’s drawings and submission. Over a two-year period, Dempsey Dyer supplied 666 Deceuninck Heritage Chamfered side-hung casements, foiled in smooth anthracite grey, with chrome hardware from Fab&Fix
Bouygues UK moved the construction of the student accommodation pods to Rabat in Morocco. Once constructed, these were shipped back to the UK where they were assembled on site. This took place over a 12-week period. To ensure the safe transit of the windows to Morocco, Dempsey Dyer designed a crate to suit the window sizes, and the windows slotted down inside the crate. It was important that there was no room for movement because it was being transferred by sea. There were ten per crate, and each crate was fully padded. The crates were packed at Dempsey Dyer, and loaded into shipping containers, which were transported by lorry to the port at Dover, before being shipped to Casablanca in Morocco. From there they were transported by lorry to Rabat, where the factory was located.
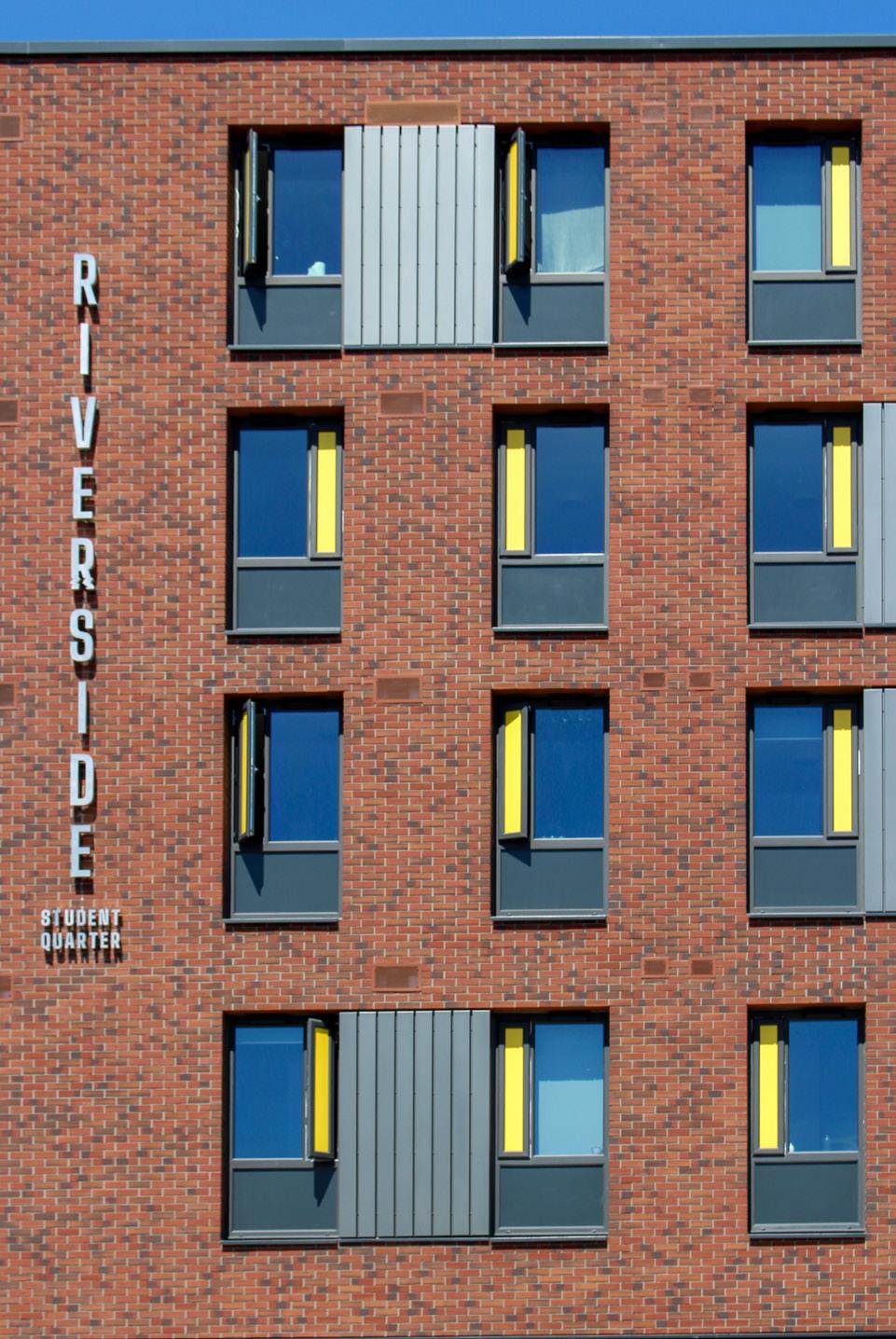
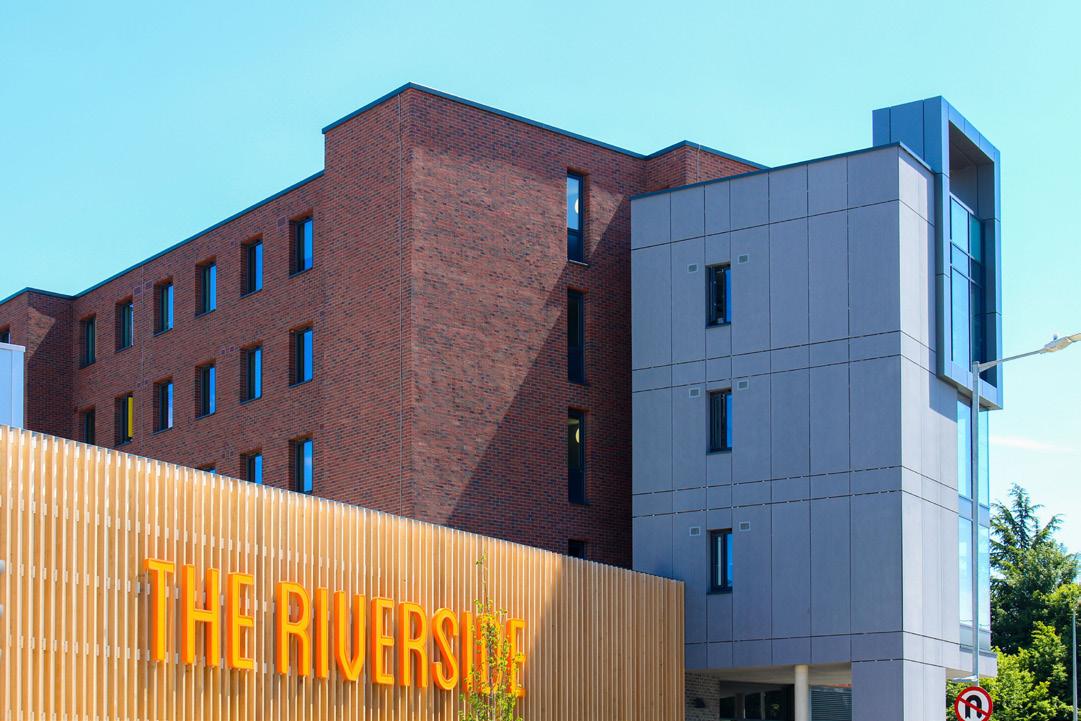
Dempsey Dyer’s Project Manager Anna Cusworth and Installation Manager Steve Burton spent two weeks in Rabat in Morocco to teach the construction workers at the modular construction factory how to install windows correctly. “The workmanship in the factory in Morocco during our time there far exceeded the standard we see in UK construction,” Anna said. “Modular build enables a level of quality that is much harder to produce in the UK due to the nature of a construction site and all that affects it – weather, access, tolerances of all trades.”
As the pods were constructed and returned to the UK, they were assembled on site in Canterbury, where Dempsey Dyer installed bespoke cills for each window. The main challenge facing all parties on the project was the restriction on movement following the Covid outbreak. This meant that during the design phase, Dempsey Dyer worked alongside the design teams from other organisations via Teams.
“In theory this was considered a negative, but in practice it worked exceptionally well, and it was a big positive for the project because most problems were ironed out thanks to swift collaboration,” Anna said.