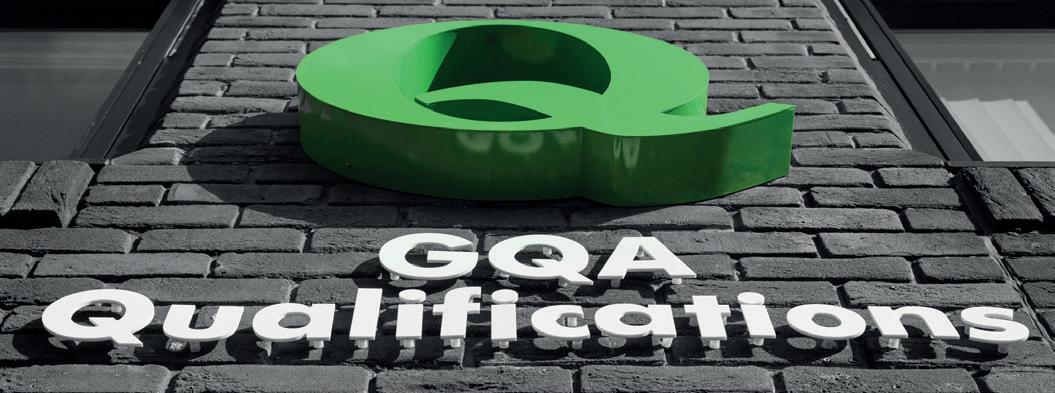
15 minute read
Careers & Qualifications in Fenestration
SPONSORED BY GQA AND BUILDING OUR SKILLS
GQA Qualifications is the only issuer of CSCS cards for the Glass and Fenestration industries. Building Our Skills is a strategic campaign designed to help bridge the growing skills gap in the Fenestration Industry
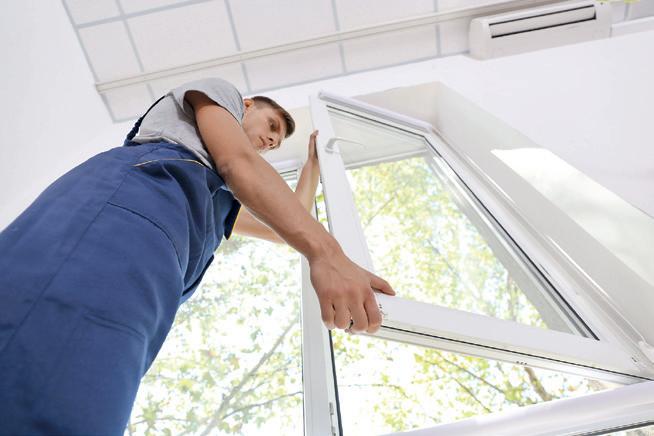

CAREERS NEW APPOINTMENTS
FREEFOAM TEAM CELEBRATE 60 YEARS OF LONG SERVICE
Freefoam Building Products are delighted to award Long Service awards to five team members. Four have been with the company ten years, and one for 20 years – an amazing achievement – making a total of 60 years loyal and committed service to Freefoam.
Coming from different areas of the business, all have seen significant changes over the years and all have adapted and developed within their roles.
Paul McKee, General Operator, has found that his role has grown and developed over the years with the expansion of the production capacity and additions to the site infrastructure. He manages and moves finished goods and stock around the site, manages our stores and takes in deliveries and transports goods from suppliers around the site. Paul can most often to be seen on his forklift!
Gursharan Singh, Senior Tooling Technician, plays a vital part in the tooling team who, in accordance with the production plan, manage the tool changes efficiently and effectively from one product type to another. His experience, attention to detail and personable nature positively contributes to the team dynamics, ensuring quality and operational performance targets are achieved safely and efficiently. Paul Clark, Warehouse Administration/ Stock Control, joined as Customer Service Representative, placing orders and helping customers. He moved to the warehouse department where his extensive knowledge of products, product codes and back-office processes has been a very useful addition to the team.
Grant Robinson, Customer Service Representative, has been at Freefoam from the very first days of the operation in Northampton and is a familiar voice to many customers. He joined when Freefoam UK was simply a warehouse and distribution function and has seen all the major developments on site. He has worked in a variety of roles in warehouse and customer service and continues to bring his expertise and knowledge to support our customers.
Graham Buckby, Production Services Manager, spent several years as Production Line Shift Supervisor and is now managing all aspects of our new off-line manufacturing processes. This includes foiling fascia trims, off-line venting of soffit boards and routing base products to create decorative fascia. He played a key part in the setting up these processes and brings experience and technical know-how to his team of 15. Using his expertise Graham also delivers our in-house training including forklift, crane operation, mobile elevating work platforms (mewp) and manual handling. Geoff Barnett, Freefoam General Manager, summarized “In today’s volatile employment market it is a proud moment for us to celebrate such longevity and continued commitment by so many of our team members. I’ve also been with Freefoam for almost 14 years, so have seen these guys develop over time and make significant contributions to our business. It’s a testament to our culture and way of working that people want to stay at Freefoam and play their part in our expansion and growth.” www.freefoam.com
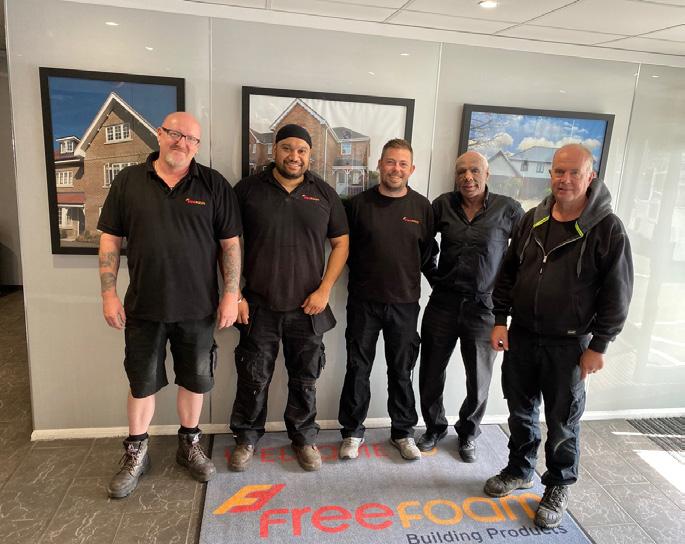
L to R: Paul McKee, Gursharan Singh, Paul Clark, Grant Robinson, Graham Buckby
NEW ERA FOR COTSWOLD ARCHITECTURAL PRODUCTS AS TIM FERKIN APPOINTED AS MD
As world-leading friction stay maker Cotswold Architectural Products begins a bold new chapter in its history, longserving employee Tim Ferkin has been appointed as Managing Director.
Tim, who joined the business in 2002, had risen through the ranks to become General Manager by the time it was acquired by Caldwell UK in 2014. He then spent the next eight years in various senior roles across the wider Caldwell group, most recently as Market Development Director, where he led the establishment of Caldwell South-East Asia.
However, in June this year, Caldwell’s owners announced that they would be disposing of the business by selling it to Assa Abloy. Despite this, they will be retaining control of the long-established and internationally respected Cotswold brand, which will become an independent business not owned by Assa Abloy. Tim was quickly appointed Cotswold’s new Managing Director. “I’m absolutely delighted to be leading Cotswold into an exciting new phase in its history,” Tim comments. “I’ve been passionate about this business since I first joined in 2002, and as its MD, I’ll be seeking to build on its global reputation for excellence and innovation. “Cotswold is the largest independent friction stay manufacturer in Europe, and the only business of its kind to totally own its supply chain, giving us unparalleled control over quality, and allowing us to offer the best possible service to our customers.
“I’m also extremely pleased to be joined by Ian Greaves, our new finance director, who also previously worked at Caldwell, and will form a crucial part of our highly experienced management team.” In 1976, Cotswold became the very first British business to manufacture friction stays, and in the 46 years since, it’s established itself as a world leader in the field.
Today, the company has factories in the UK and India and supplies quality friction stays to 56 countries around the world. For more information email info@cotswold-windows.co.uk, or visit www.cotswold-windows.co.uk.
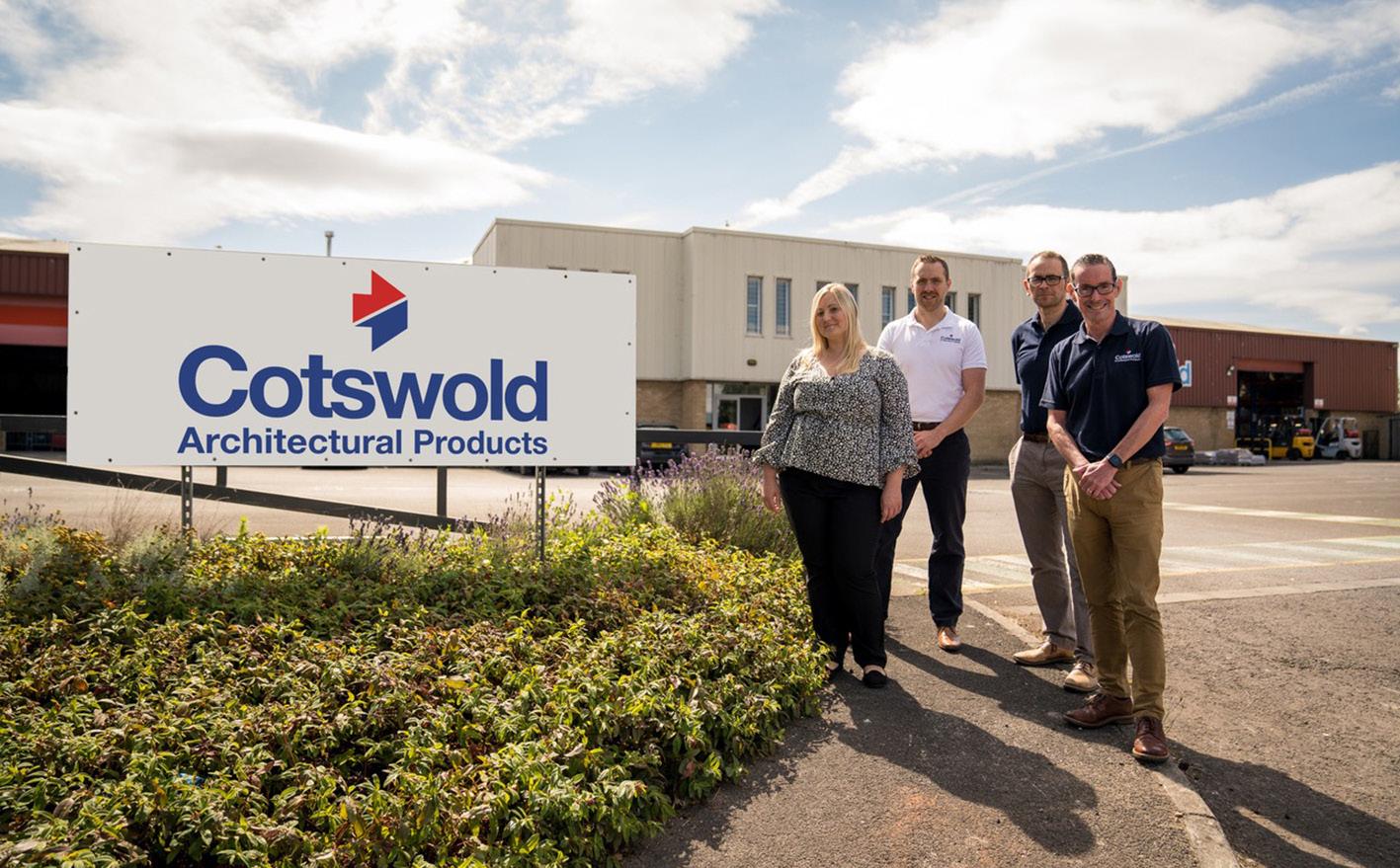
CAREERS
GQA TECHNICAL TEAM THE LATEST TO VOLUNTEER TO TAKE THE INDUSTRY TO THE EDUCATION SECTOR
Building Our Skills - Making Fenestration, Glass and Glazing a Career of Choice has received a further boost to its campaign to take the industry to the education sector as the starting point for creating a workforce for tomorrow. Four members of the technical team from GQA Qualifications have enrolled to be a part of the ‘Inspiring the Future’ programme that Building Our Skills is promoting alongside the Education and Employers Charity.
Setting a great example to employers in the industry, the team from the fenestration industry’s leading awarding and qualifications-writing organisation has signed up to support the campaign by volunteering to visit schools to help inform youngsters about the possibilities for their future careers, and what they could achieve if they join the Fenestration, Glass and Glazing industry. Inspiring The Future has been designed to connect young people with the world of work through volunteers. It is seen by Building Our Skills as key in helping to acquaint school age children and their teachers with the industry, and to communicate to them the broad range of job roles and career paths it offers. The campaign connects volunteers to state primary and secondary schools via its free match-making platform. Volunteers are asked to give just one hour a year to the programme, although they can choose to do more if they wish in order to help inspire children. The first step is to register on the website of Building Our Skills and complete a very simple application form. Teachers who have signed their schools up to the programme can see details of the volunteer, where they are based and the industry they are in, and then invite them to talk to their school about the job they do and the industry they do it in. Invitations for in-person school visits are based around volunteers being local to the school in question. Virtual visits can also be delivered from anywhere in the UK. Volunteers are supported by the Inspiring the Future team and are given access to training videos as well as training webinars and forums should they wish. Building Our Skills has highlighted the Education Sector as the single most important area for the industry to focus on to raise awareness of the opportunities it offers and to inspire future generations to look to Fenestration, Glass and Glazing as a career of choice.
Mark Handley, Building Our Skills’ Partnerships Manager, says: “I’m delighted that GQA’s technical team has agreed to support the Inspiring the Future campaign by volunteering. We’re now well on the way to achieving our primary objective of securing 50 industry volunteers. I’ve been very pleased with the response, but I urge the fenestration industry to acknowledge the need to get more involved with schools and colleges. Working with Inspiring the Future is a great approach to attracting new talent to the industry, and teaching youngsters about the sheer breadth of roles it has on offer. I think anyone volunteering would find it all very rewarding.” Those interested in volunteering can do so by clicking here https://buildingourskills. co.uk/campaigns/inspiring-the-future/ Or for more information on this campaign and Building Our Skills - Making Fenestration, Glass and Glazing a Career of Choice - visit www.buildingourskills.co.uk
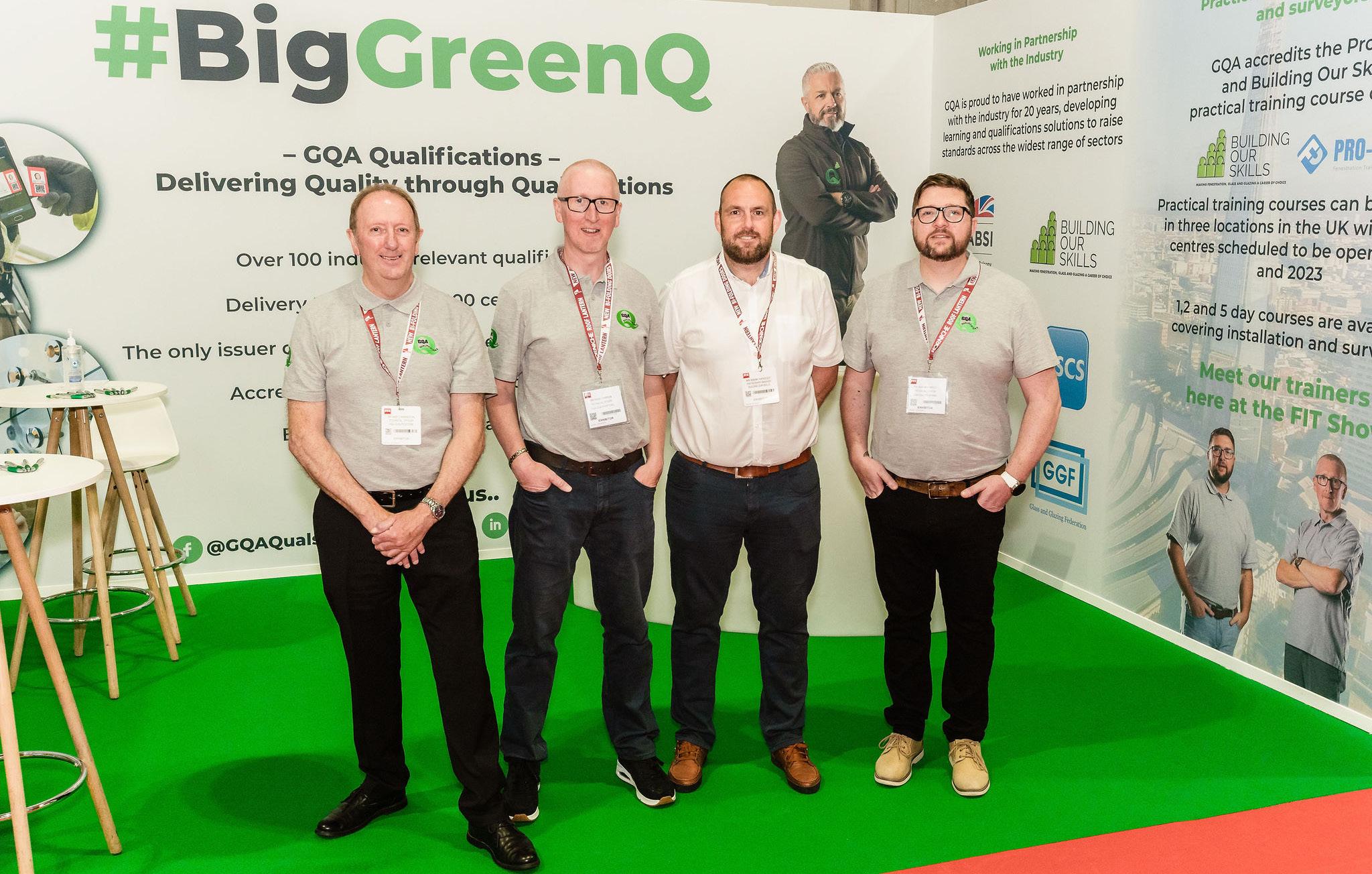
Quality through Qualifications
GQA is the specialist awarding body for Fenestration and the only issuer of CSCS Cards for the Fenestration Industry

SEE US AT THE FIT SHOW
Visit our website at: www.gqaqualifications.com Or contact us on: 0114 272 0033
Product Trainer
Buckinghamshire
For Schüco, a well-respected recognised market leader in innovative façade solutions, we are recruiting a Product Trainer.
THE ROLE
• The Product Trainer will be responsible for delivering training courses to develop customers’ knowledge of products and processes, ensuring they are able to specify, fabricate and install products to the highest standards.
• Delivering theoretical and practical training seminars through multiple channels (online and face to face), the Product Trainer will aim at increasing customer engagement at all times.
• They will develop and maintain a high level of knowledge of construction industry standards and legislation to ensure optimum compliance.
THE PROFILE
• With relevant technical experience, you are a professional fabricator / foreman with a natural ability for developing relationships and sharing your knowledge.
• Whilst training experience is not essential, the Product Trainer will need to have an inclination for absorbing and imparting knowledge on new products, new ideas and technologies.
• With a passion for engaging your audience, as brand ambassador you will train customers to ensure they maintain the highest levels of compliance and reputation for the Schüco brand.
If you are an ambitious construction professional willing to contribute to building the brand of the world leader in their field, we want to hear from you. Please send your CV and cover letter with current remuneration package to our retained consultants at Cooper Edwards: cv@cooperedwards.com.
CAREERS RAPID RISE FOR VAS DURING 15 YEARS AT WINDOW WARE
Vas Lazarevych is celebrating 15 years at Window Ware, following a meteoric rise through the ranks since he started at the marketleading independent hardware distributor back in 2007.
Having joined the business as a picker and packer in the warehouse, Vas soon progressed to the roles of junior operative and then senior operative responsible for moving, loading, and unloading goods using the forklift truck. When the opportunity arose to apply for a job in the trade counter, he didn’t hesitate. And it was this role which ultimately opened the door for Vas to a role in purchasing. Just 5 years later, Vas successfully landed a promotion to Purchasing Manager in October 2021. Today, Vas leads a small team and manages all the daily purchasing activities, including procuring all goods, helping to build strong relationships with brand partners, and managing inventory levels to maintain service levels, stock availability and all-important OTIF delivery performance for customers.
Every day, he works closely with colleagues across all primary business functions to strike that perfect balance between supply and demand; that means carefully managing inbound lines, so the warehouse team is never overloaded with goods-in, as well as maintaining constant lines of communication with the sales team so they have everything they need to meet their customers’ needs.
Vas said, “Even though joining the Purchasing Team in 2016 was undoubtedly a careerdefining moment for me, every single role I’ve held at Window Ware has helped me to get where I am today. Together, they’ve given me a comprehensive understanding of the whole business.”
Reflecting on his 15 years at Window Ware, Vas added: “I’ve always felt there’s a real familyfeel to working at Window Ware and we’ll go the extra mile to support each other and build strong, long-lasting working relationships both in- and outside the organisation.” Sam Nuckey, Window Ware’s MD, said: “After 15 years, and with 6 different roles under his belt, Vas has a wealth of knowledge about every aspect of our business, so he’s a tremendous asset to the team.”
“A business is only as good as its people, so making sure we have a skilled and experienced team that knows its stuff is the surest way to create a better service for our customers and set the company up for success.” For more information, call 01234 242 724, email sales@ windowware.co.uk, or visit www.windowware.co.uk.
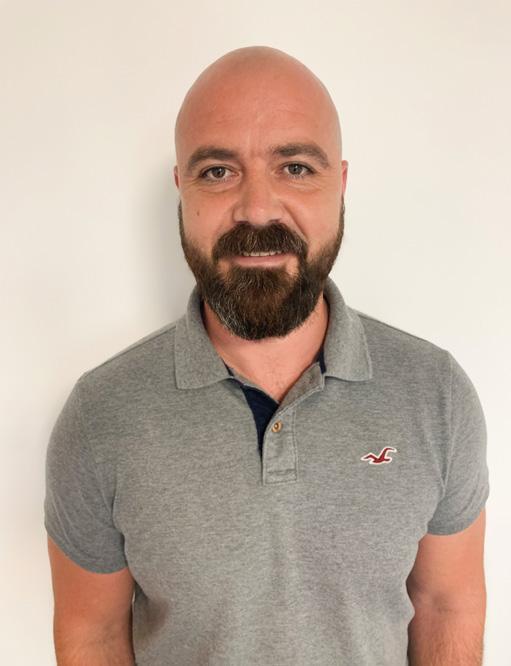
CAREERS HWL FORGES NEW PARTNERSHIPS TO ADDRESS THE SKILLS GAP
HWL Windows has developed a series of partnerships with leading colleges to recruit high calibre engineering students into the window and door industry.
Developed following HWL’s support for the Leeds Manufacturing Festival, the specialist fabricator of flush products, has formed new partnerships with Leeds City College (LCC) and University Technical College Leeds (UTC). This includes running ‘manufacturing treks’ where students spend half or a full day touring and working in its aluminium and PVC-U factories, and a commitment to create a new training centre and student classroom on site.
Phil Gray, Operations Director, HWL Windows, explained: “The kids get the opportunity to see how we operate and to ask questions in a real working environment.
“It’s been massively successful. They’re engaged, they’re asking lots of questions, they want to connect with you on social media after they’ve been. It’s like a switch goes on.” The new HWL manufacturing school will give students the opportunity to learn about the principles of manufacture from from product design to installation. This includes manufacture of aluminium and PVC-U windows.
Phil added: “It’s about the hands-on experience. Showing them what goes into product What they fabricate is then going back to the UTC facility where they are being taught about how to install it.”
HWL has also committed to create a series of new apprenticeships offering students the opportunity to gain a formal qualification in fabrication.
HWL took the decision at the end of last year to drop manufacture of ‘standard’ product, focussing instead on the manufacture of specialist products. This has built around Timberweld®, which it used in its pioneering development of a non-glass-bonded 90° jointed R9 window in 2017, replicating a traditional 90° mechanical joint on both sides of a welded sash, also offering an R9 open-in door and R7 in a Timberwelded format.
The move also saw HWL add the Sheerline Prestige Aluminium to its offer as well as its complete casement range. It’s decision to partner with local colleges has given HWL a route to students who have already expressed an interest in engineering but who might not have otherwise considered a career in manufacturing. Phil said that this had also delivered a significant uptick in the skills base of its recruitment pool. “When you’re going through a recruiter, you’re scraping the bottom of the barrel. You don’t get people who want to do the role.
“With what we’re doing now, we’re getting people with an interest in engineering. They’re coming to us and they already know a little bit about processing, manufacture but the biggest thing is they have a positive attitude towards learning. “If we can show them how to build window, get them out onto the factory floor, we’re bringing the future leaders of our business into our industry.” For more information email sales@hwlwindows.co.uk call 0113 2449006 or log on at www.hwlwindows.co.uk.
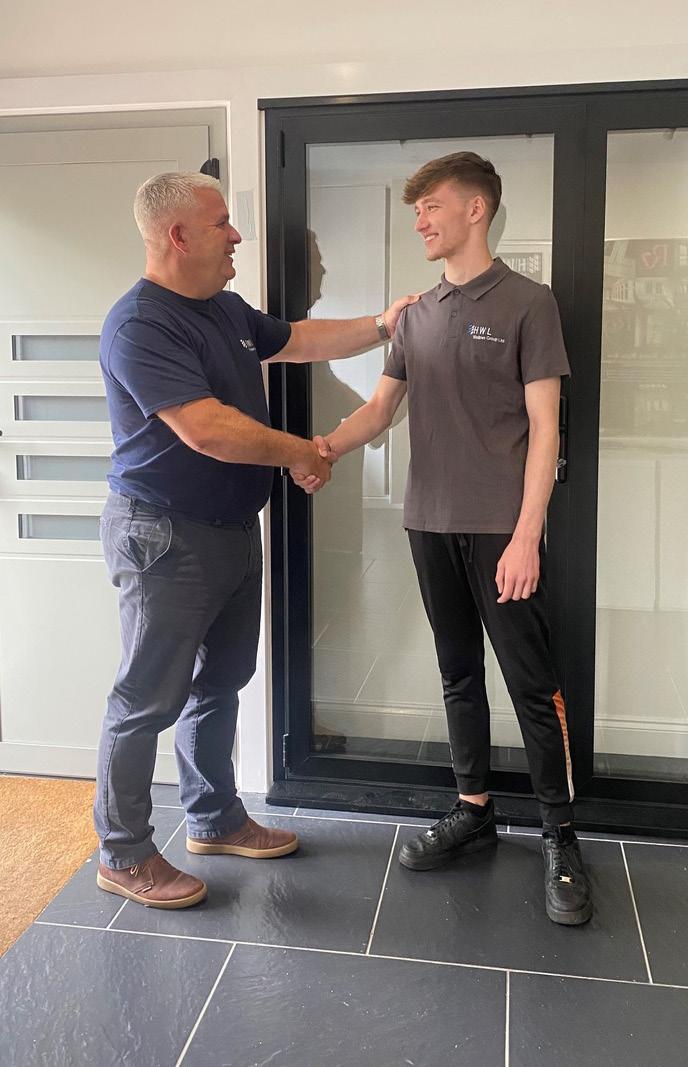
NEW APPOINTMENTS COTSWOLD PUTS QUALITY AT THE FOREFRONT WITH EXPERIENCED NEW QA SUPERVISOR
A long-serving fenestration sector specialist with a wealth of friction stay expertise is the latest addition to the team at Cotswold Architectural Products.
Amber Dangerfield, a qualified engineer, has spent the previous 18 months as the company’s Operations Supervisor, before which she served in a variety of senior engineering roles at a leading European hardware supplier for more than a decade. In her new role, Amber will be tasked with ensuring Cotswold adheres to the exacting standards of QMS and ISO, and maintains outstanding quality standards across the board. “This is an extremely exciting opportunity for me to help shape the next phase in Cotswold’s history,” Amber comments. “Drawing on both my engineering background and years of friction stay experience, I’m confident I can ensure that we live up to the reputation for quality and reliability that made the Cotswold name.” Cotswold Managing Director Tim Ferkin comments: “Since re-joining Cotswold as MD earlier this year, my top priority has been assembling the outstanding group of people I know I’ll need to help me lead the business into the future.
“Amber is a fantastic addition, and her extensive technical knowledge will prove invaluable in the months and years ahead. I’m delighted to be welcoming her to the team, and can’t wait to see what we can achieve together.” In July, Cotswold split from Caldwell Hardware to become Europe’s biggest independent friction stay manufacturer. The company’s former owners decided to sell the Caldwell side of the business, while retaining the Cotswold side, bringing in long-serving Cotswold employee Tim Ferkin as Managing Director. Today, Cotswold is the only business of its kind to totally own its supply chain, giving it unparalleled control over quality. For more information email info@cotswold-windows.co.uk, or visit www.cotswold-windows.co.uk
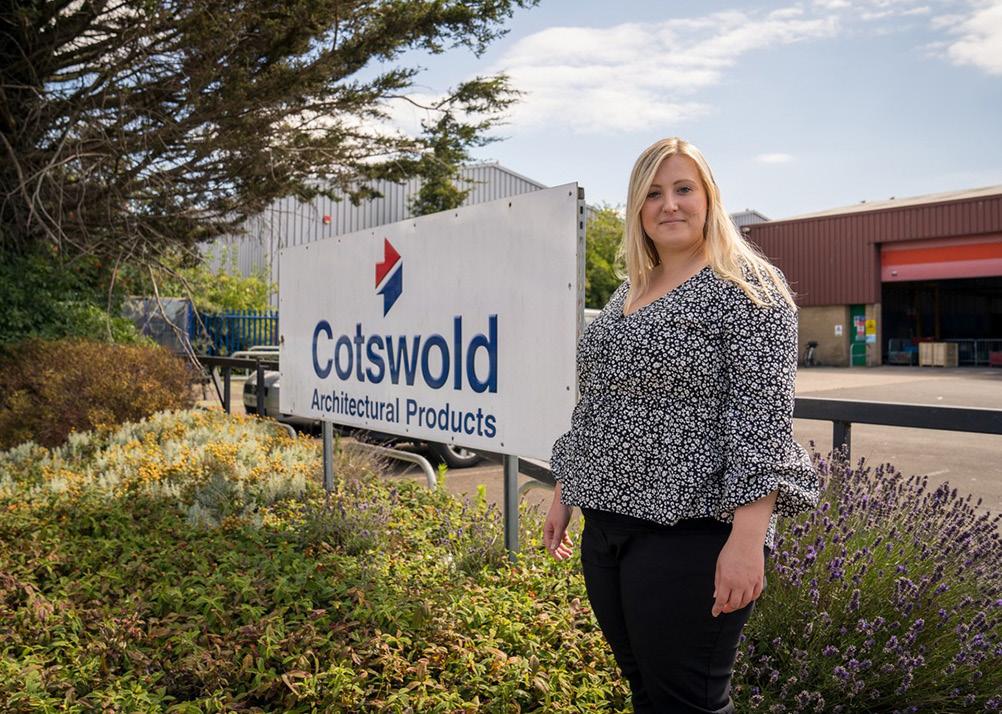
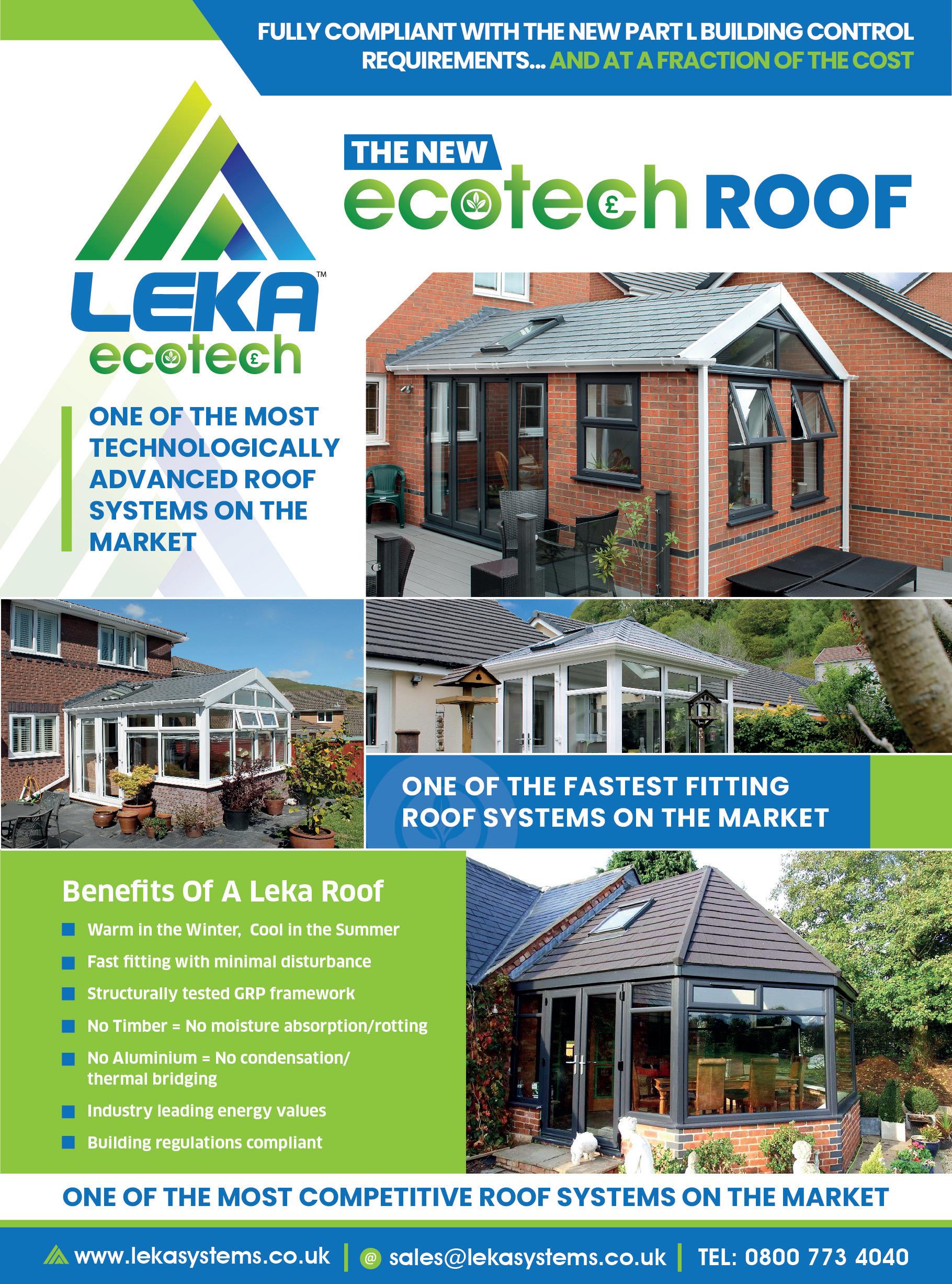