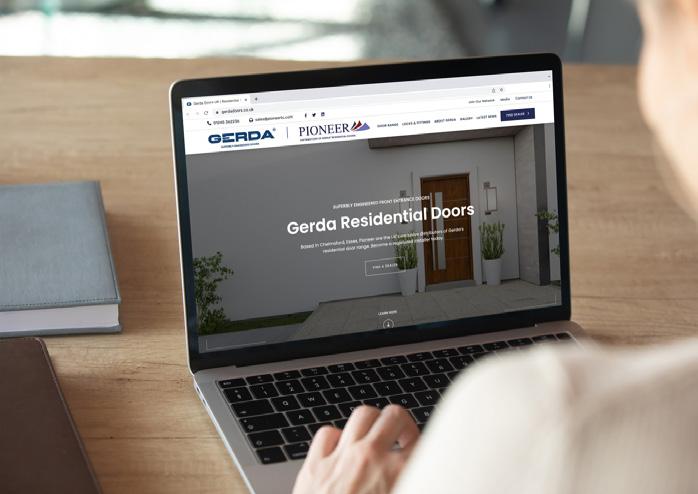
2 minute read
GERDA RESIDENTIAL DOORS LAUNCHES NEW UK WEBSITE
PERFECT PVC-U CIRCULAR ECONOMY CREATED WITH GLAZERITE/ VEKA RECYCLING DEAL
An agreement between leading VEKA and Halo window and door fabricator Glazerite UK Group Ltd and VEKA Recycling Ltd, for all virgin offcut material and limited volumes of post-consumer frames to be collected and recycled, has created a perfect model of the ideal window industry circular economy arrangement.
Following a highly successful launch at last year’s FIT Show and a year of establishing a nationwide dealer network, GERDA Residential Doors has launched a brand-new UK specific website through which British homeowners can specify products developed specifically for the UK market.
Pioneer Trading, exclusive distributor for Gerda in the UK, used the FIT Show to launch the range of Gerda unique steel and aluminium front entrance doors. Stylish, elegant and with an emphasis on high security with superior thermal performance across all of its products, Gerda Doors are superbly engineered using the finest steel and aluminium door construction techniques. With high performance levels and unique construction methods and materials, Gerda Doors are an effective alternative to conventional composite doors. The website – www.gerdadoors.co.uk – offers details of the four key ranges available –Optima, Thermo Premium, Thermo Prime and Altus – and describes each in detail including handles and hardware. A Q&A section offers homeowners advice on Gerda and particularly, why Gerda Doors are different from any other brand of residential door currently available in the UK.
An extensive photo gallery offers examples to guide homeowners, following which they may find their local Gerda dealer.
Tel: 01245 362236 - www.gerdadoors.co.uk.
The deal sees virgin offcuts from Glazerite’s Wellingborough, Peterborough and Bolton manufacturing operations, in addition to frames removed from selected installation sites, collected and returned to VEKA Recycling’s advanced PVC-U reprocessing facility in Wellingborough. With VEKA PLC’s Burnley extrusion facility now a large volume user of recycled pellet from its sister organisation, much of the material returned from Glazerite may be returned to them in the form of brand-new profiles to again be manufactured as new windows and doors.
Darren Rhodes, managing director of Glazerite’s North West Division, led the negotiations for the new contract: “Inevitably there are offcuts from the production of new frames despite Glazerite using advanced manufacturing techniques throughout our facilities, but this material remains intrinsically valuable. We also have agreements on a number of installation sites for which we support installer customers, by removing old frames from site.
“VEKA Recycling has provided a solution for Glazerite and a number of our customers, by efficiently removing the material through bins placed at our sites. This reduces disposal costs and contributes significantly to Glazerite’s commitment to reducing the company’s carbon footprint. It also enables us to support our customers by providing recycling facilities, now a commitment demanded by public sector and larger landlords for refurbishment projects,” added Darren. Collection bins are placed at Glazerite’s factories and at sites such as the eightstorey housing project being installed for Warrington Borough Council housing by Glazerite customer K2 Aluminium Systems, from where they are returned directly to VEKA Recycling’s Wellingborough site for immediate reprocessing. The reprocessed PVC-U Pellet is 100% quality inspected to specification and ready to be extruded into new products such as ducting for air conditioning and electrical cabling, and new window and door frames such as at sister company VEKA PLC, Glazerite’s principle system supplier.
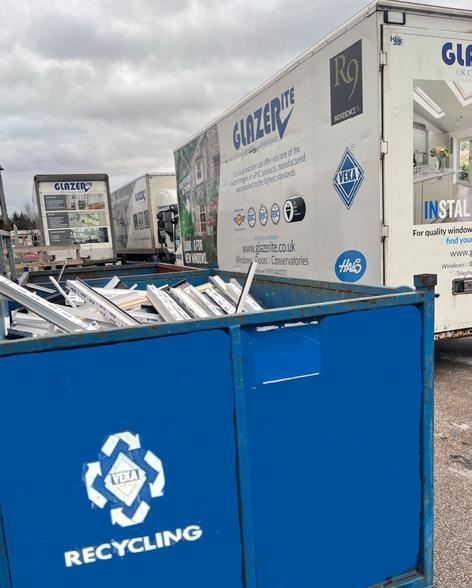
VEKA Recycling managing director Stuart Stockley says that the Wellingborough facility reduces carbon both through its processes and its location: “We have the most advanced PVC-U recycling facility in Europe which produces the highest quality PVC-U pellet, whilst our central location also contributes towards carbon reduction by ensuring all processes are completed within the UK. The loop between extrusion, through fabrication, installation, recycling and back to extrusion again, is perfected by this arrangement, and one that we will work towards repeating.”
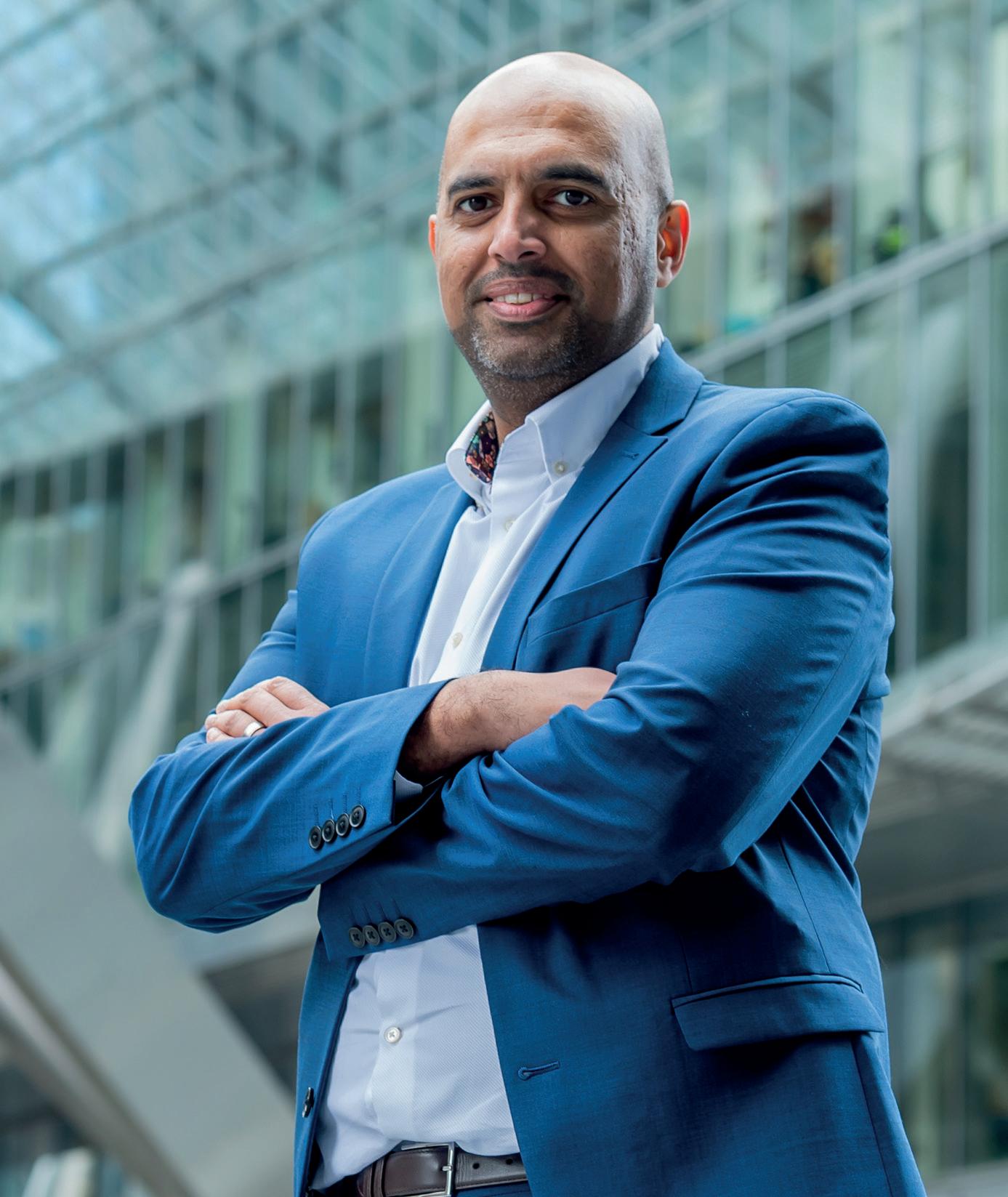