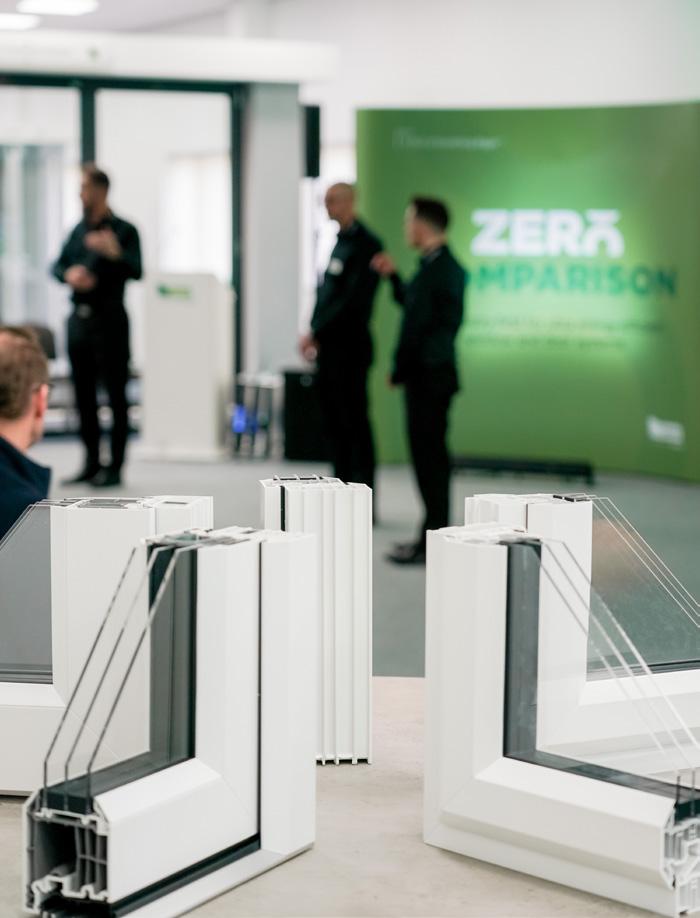
6 minute read
LINIAR’S ZERO|90 WINDOWS AND DOORS – FUTURE PROOFING PVCU
Glass News’ Managing Director, Christina Shaw, and Editor Chris Champion, joined fenestration and building trades representatives for Liniar’s launch of Zero|90. The welcome and enthusiasm from the Liniar staff seems to be something inbred in their employees – perhaps it’s infectious. The presentation by Design and Development Director, Chris Armes, and
Technical Director, Paul Garforth, was slick, professional, and very informative and with ‘ringmaster’ Nigel Bishop, Liniar’s Group Sales Director hosting the event, it really was up there with the best of trade events. It’s really not that far away. 2025 will bring the Future Homes Standard and Future Buildings Standard into force and that will mean reducing CO2 emissions produced by new homes to 75-80% lower than those built to current standards. Homes will need to be ‘zero carbon ready’, with no retrofit work required to benefit from the decarbonisation of the electricity grid and the electrification of heating. Fossil fuel heating (such as gas boilers) will be banned in new homes, with an expected shift to reliance on heat pumps and heat networks. You could say systems house Liniar has seen the future. It has recognised the need for Passivhaus standard windows and doors and has taken a giant step towards future proofing fenestration products and ensuring that PVCu is seen to be playing an important part in achieving the standards we expect to come into being in 2025. Calling their new range Zero|90, is this a gamechanger for PVCu windows and doors? Interestingly, Design and Development Director Chris Armes is making no such claim. His view is that Zero|90 is simply another product in Liniar’s impressive armoury of products. The 90mm system will, naturally, be more expensive than the 70mm systems and although he has cleverly come up with a 90R version of the profile that can be used for retrofit where 70mm is being removed, he is expecting the bulk of product will go to new build. The 90R is clever in that it has a rebate that covers over the plaster, or plasterboard line, which actually produces a very neat finish.
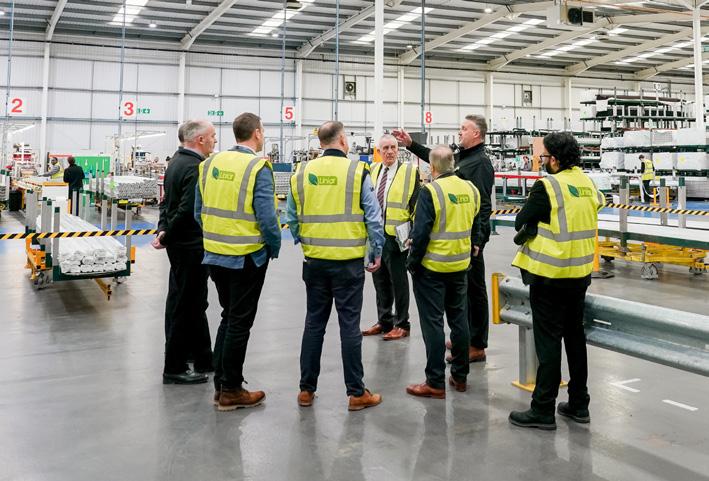
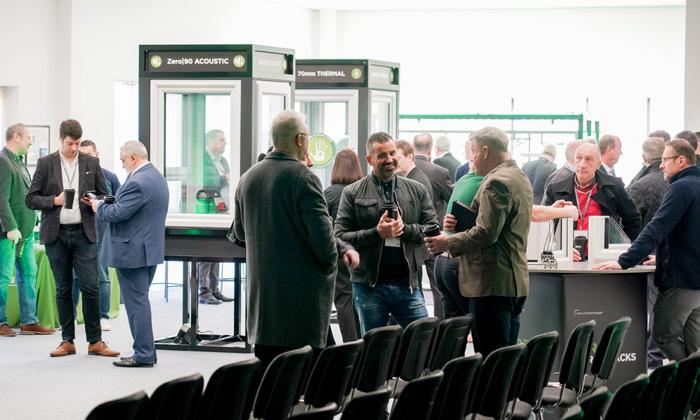
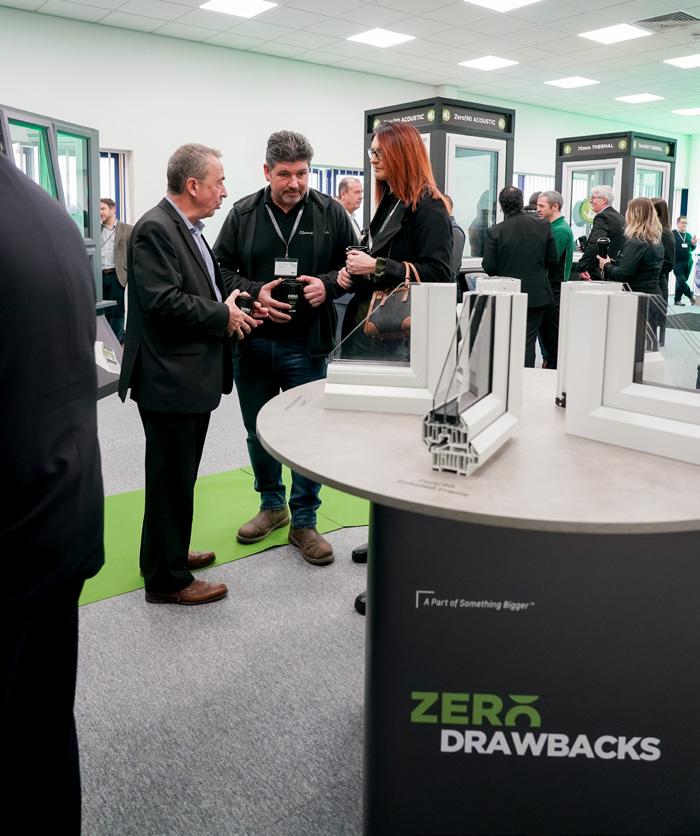
If the development of Zero|90 has been matter-of-fact and viewed internally as something that needed to be done as a responsible systems house, looking after Liniar’s fabricator customers and providing them with the tools for the future, does Zero|90 become the standard PVCu window? If not, Liniar is certainly providing future proofing with their range of casement windows, tilt ‘n’ turn windows, French windows, bay and bow windows and mock sash windows. Add to those residential and French doors and you have a full offering boasting U-Values as low as 0.66 W/m2K, noise reduction by up to 42dB (halving the transmissible sound compared to a standard double-glazed window), and certainly innovative as it includes the UK’s first Passivhaus certified PVCu window. Security is also important and Zero|90 is fully tested to PAS24 and Secured By Design meeting Part Q Building Regulations. On top of all that it is sustainable with a recycled core and is available in popular colour foiled finishes and a 4 to 6 week lead time for special colours.
Although this is a 90mm system, the sightlines match those of the 70mm slim sightlines but, of course, the 90mm depth allows for triple and quadruple glazed units. This system was definitely designed around the future needs in new build but that rebated 90R means it can replace the 70mm PVCu window and this will mean it will be in big demand in the case of Local Authority retrofitting where council housing will be required to meet the Future Homes Standard.
The low U values and noise transmission is down to using the best of insulation – air.
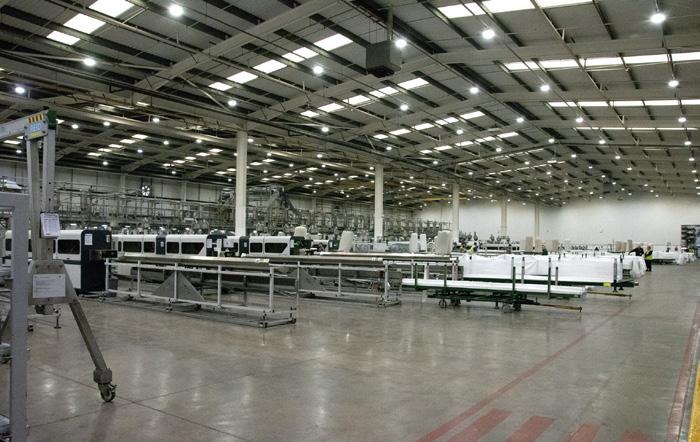
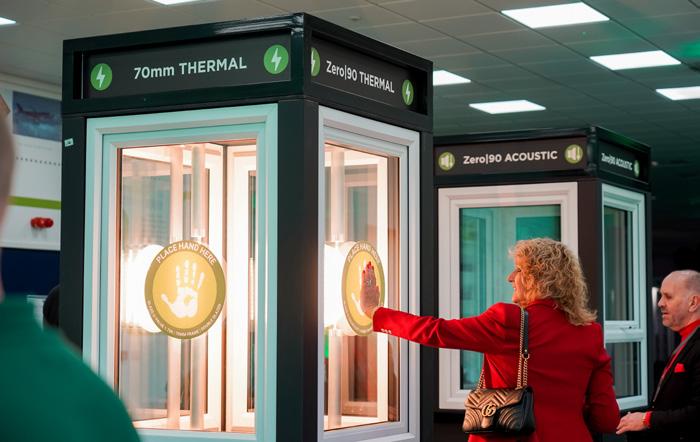
The 90mm size and multi-chambers means that no steel reinforcement is required for the Zero|90 window range although extra reinforcement for doors make sense. Meeting the increasing demand for Passivhaus-capable fenestration products, Zero|90 will help specifiers tackle the challenges of cutting carbon emissions, reducing energy consumption, and advancing sustainable construction methods using renewable and recyclable materials.
Chris Armes explains, “By significantly enhancing a building’s energy performance and therefore reducing its carbon footprint, Liniar’s latest window and door system will help developers and homeowners transition towards Net Zero living. Our calculations show that replacing standard doubleglazed windows with Zero|90 can save a UK household over £15,000 during the products’ lifespan.”
He continues, “Not only will Zero|90 lower energy consumption and the costs associated with running heating and cooling systems, it also provides superb sound reduction, ensuring occupants enjoy all the well-being benefits that come with living in a comfortable, quiet home. With more and more developments being built in urban areas, cutting noise is high on the list for many specifiers and Zero|90 can reduce sound by up to 42 decibels. This means that in real terms, Zero|90 windows actually halve noise transmission, compared to a standard double-glazed window.”
Not surprisingly, local authorities are well aware of the need to be ready for the 2025 Future Homes Standard and Mansfield
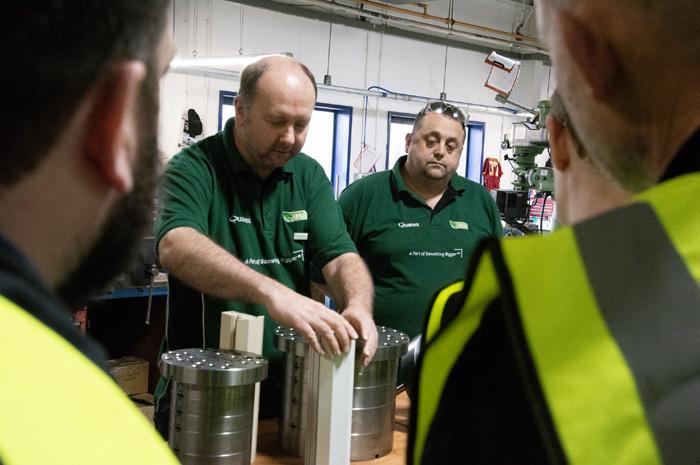
District Council is one of those authorities with a pro-active Green agenda such that, in 2022, they commissioned four ultra-low energy homes for social housing rental with the aim of achieving Passivhaus accreditation. When it came to windows for the project the Quantity Surveyor searched the Passivhaus database and only one company appeared for PVCu windows in the UK – Liniar, whose headquarters just happened to be less than 15 miles from the planned construction site!
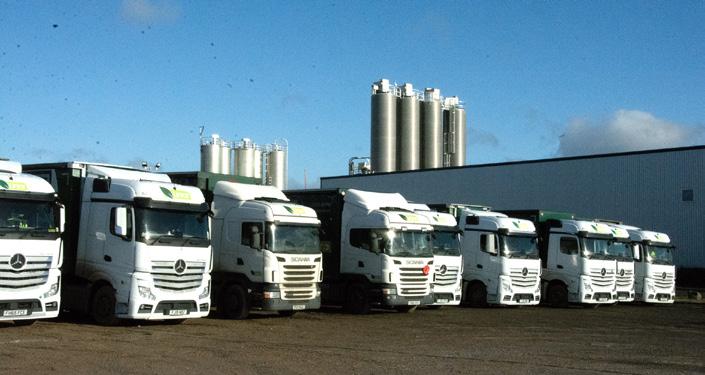
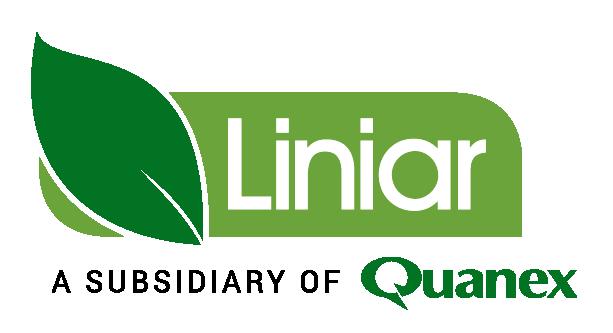
It’s long been recognised that PVCu is a cost-effective, thermally efficient construction material. Zero|90 windows and doors can deliver U-Values as low as 0.5 when fitted with quadruple glazing, making it the ideal choice for Mansfield Council’s test project. And once the Mansfield QS had discovered Liniar’s product range, he worked closely with Liniar’s design team to establish the exact specification for the windows he needed on the project. Chris comments, “My team and I were very confident the Zero|90 windows specified would ensure the overall performance of the homes reached the Passivhaus standard. Everyone involved in the project was careful to ensure not only that the houses would be the most energy efficient for the tenants, but that the team would also be able to take learnings and apply them to future social housing builds.”
Liniar’s Group Sales Director Nigel Bishop explains why the project is important, not only in establishing the best materials and processes for achieving Passive Houses but also for improving the quality of life for tenants across the UK. He quotes one of the Mansfield tenants, who has said, “My family and I are so happy to be living in our beautiful new home. We’re already seeing such a difference in our energy bills and although the winter hasn’t properly kicked in yet, the few cold evenings we have experienced outside haven’t impacted us at all. Our home is warm and cosy, and we also noticed a big difference during the summer in keeping the house cool. With the additional insulation and the triple glazing, we were able to keep the heat out. Being a family of four with a young child, a good night’s sleep is really important; we’ve all noticed such a difference in the reduced noise levels inside, compared to our previous house, which has been an additional bonus.”
The Mansfield build team was extremely proud to receive confirmation the four homes have been certified as Passive Houses, meaning they need very little energy for both heating and cooling – which significantly reduces their carbon footprint and running costs. Even better, the project used mainly local suppliers, delivering high social value.
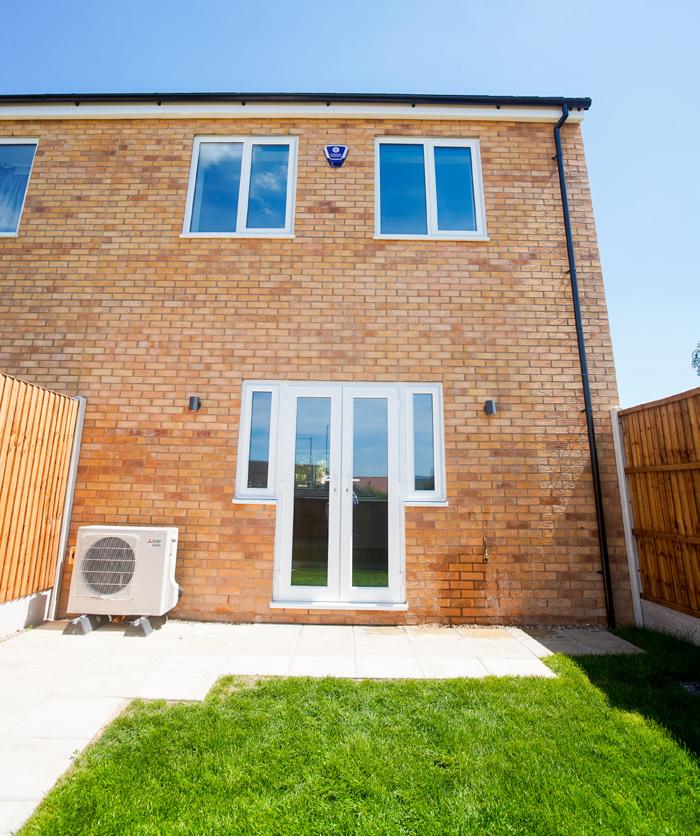
Nigel concludes, “I couldn’t be prouder that Liniar’s Zero|90 casement windows, along with our French doors, helped the Saundby Avenue homes receive Passivhaus accreditation. Knowing four local families will be living in super low energy homes, especially in the current energy and costof-living crisis, is a great feeling. High environmental standards must be the future of housing construction, and as such Liniar is well positioned, with a fully recyclable, Passivhaus-capable, superior energy efficient window and door system that also contains recycled material – all manufactured in the UK and helping to reduce the embodied carbon as a result.”
To have a project such as the Mansfield build on Liniar’s doorstep was certainly fortuitous and has instantly become a proving ground for Zero|90.
Is this the future for new build? With the 2025 standards just a short while away the timing for Liniar’s Passivhaus accredited PVCu window couldn’t be better and one suspects that other local authorities will be looking at the Mansfield project with interest. And what about private new build homes and even retrofit for private homes?
The general buzz surrounding the launch of Liniar’s Zero|90 and 90R window and door ranges seems to suggest future proofing is high on the agenda for those in the know across our industry.
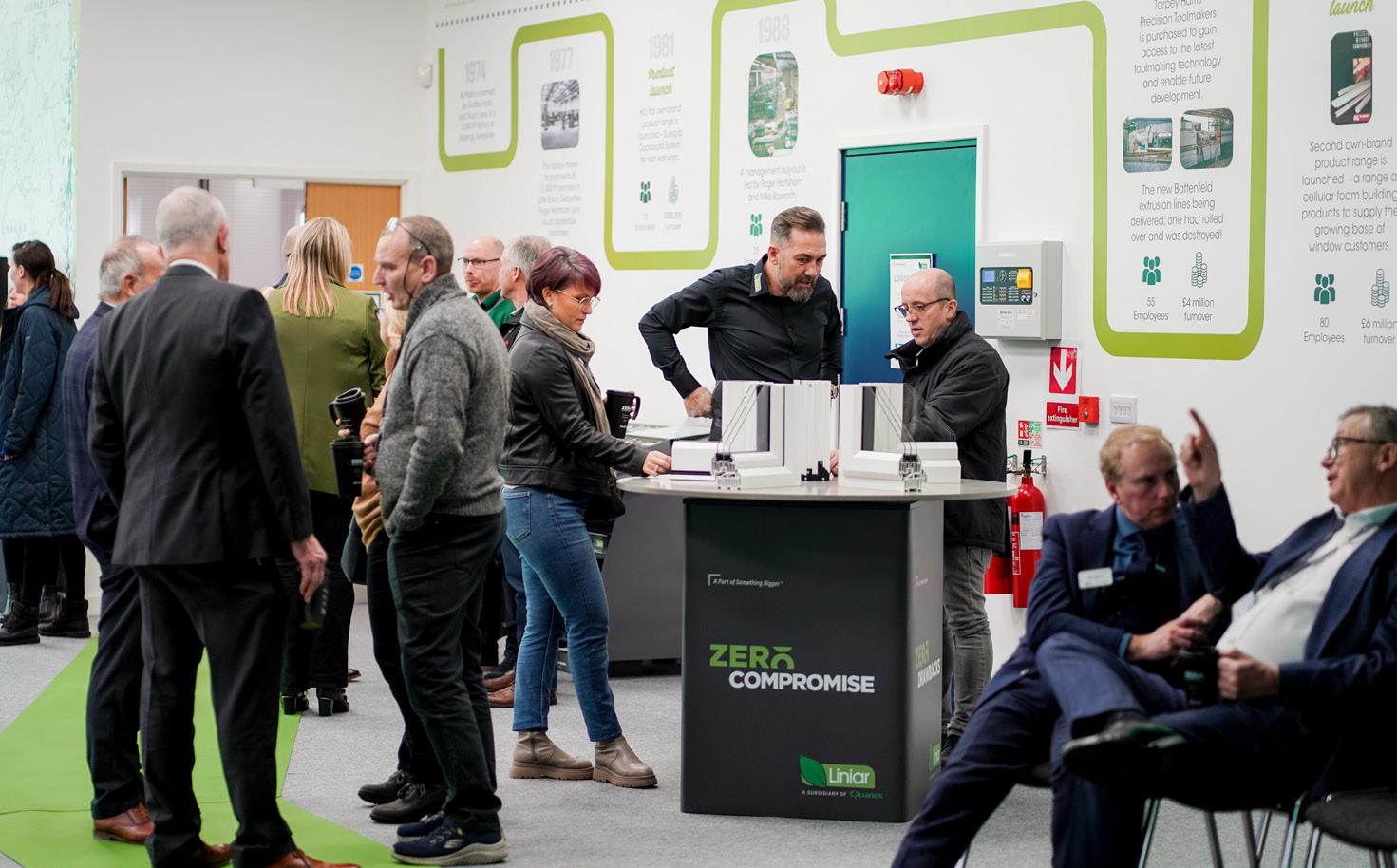
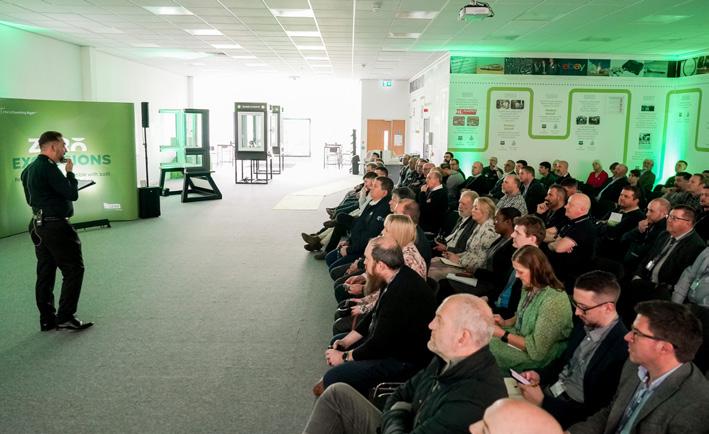
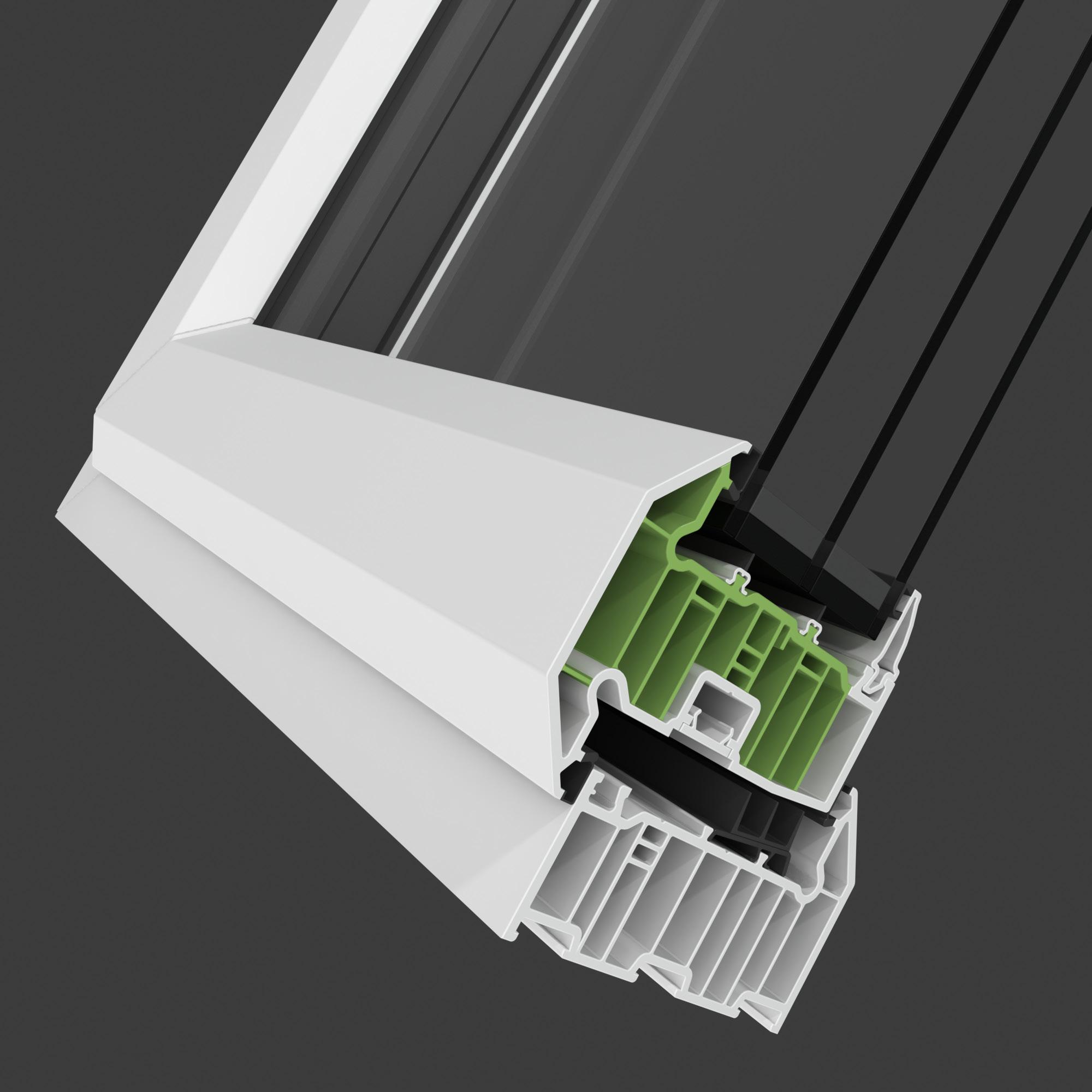
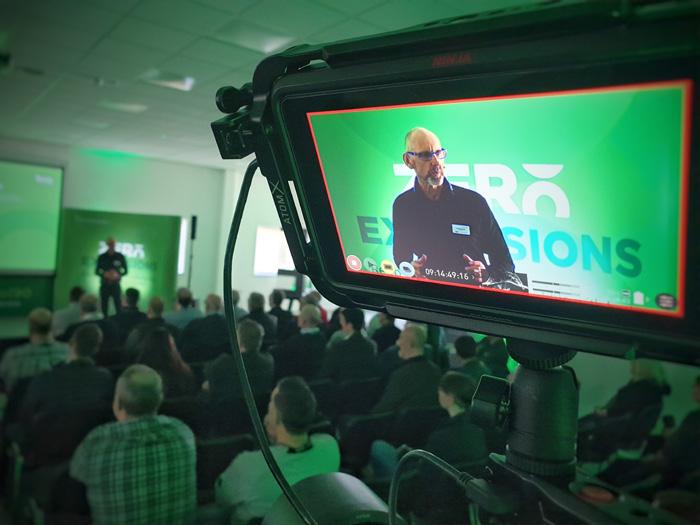