
6 minute read
RES Technical Corner by Brett Eliasz (written by Joshua Doores
Technical Corner (written by Joshua Doores this month)
For the article this month we will take a look at overhead conductors, why one would decide to go overhead, and what conductor / cable to select.
First, lets discuss why one would decide to go overhead in the first place. Depending on your area of expertise and the industry that you are in, designing a feeder or branch to be overhead may not be something that you do very often.
As things often are, the cost is a major deciding factor, and running cables overhead vs underground is no different. Running your conductors and/or cables underground can very often cost 5x or more than going overhead. There are many factors that contribute to underground installations being expensive, but definitely not least among them are material costs. For reference, see the photo below which compares an underground conductor to that of an overhead conductor.

Figure 1: Photo taken from online PDF, 'Xcel Energy', 'Overhead vs Underground', Information Fact Sheet
Another important factor, however, is reliability. Reliability can also be looked at as the cost of maintenance and the cost of a failure to the infrastructure and how easily it can be repaired.
The battle between material cost and reliability often boils down to length of run. At a certain distance, the added cost of an underground feed is too much for the added benefit of reliability.
AAC?, AAAC?, ACSR?, Trapezoidal or round?, insulated or not?, triplex? Quadplex? Messenger? What does it all mean?
When selecting an overhead conductor, it’s important to consider the following: the weight of the conductor / cable, diameter of conductor/cable, strength of conductor / cable as it relates to maximum span, clearances required, and the environment the overhead line will be located.
The weight, diameter, and strength all relate in a very mathematical way to determine the forces experienced by the utility poles and wires themselves. These calculations, along with clearance requirements determine utility pole class, height, and span. The environment can add safety factors from ice and wind in the region. These safety factors increase the overall load of the overhead conductors on the poles, winds can cause an effect known as ‘galloping’, ice can cover the lines adding additional stress, and rain / sleet / snow / sun can lead to corrosion and loss of mechanical strength overtime. Click this link for youtube.com video demonstrating the galloping effect. The National Electric Safety Code (NESC), Sections 25-27 is a great resource for understanding how to safely select utility poles and conductors for the environment.
Aluminum is the common material used for overhead lines, granted every situation can call for a different product. ‘AAC’ stands for ‘All Aluminum Conductor’ and is considered to be the most economical solution for overhead distribution due to its low cost and high resistance to corrosion. However, its lower tensile strength does not make it suitable for large transmission or rural distribution. When it comes to shorter distribution, its hard to beat AAC. ‘ACSR’ stands for ‘Aluminum Conductor, Steel Reinforced’ and is considered the standard in most transmission lines. ACSR provides similar conductivity as AAC and similar cost, but with the mechanical strength of a steel core. ACSR can be selected with a wide range of steel content, ranging from 6% - 40%. The more steel the stronger the conductor and the longer it can be spanned across utility poles. The main downsides of ACSR is that its heavier than AAC and also susceptible to corrosion due to the steel component. ‘AAAC’ stands for ‘All Aluminum Alloy Conductor’ and this is one of the higher performing and costing overhead conductors available. AAAC is made from aluminum alloy 6201 which gives it good conductivity, good corrosion resistance, and good strength / weight ratio. And even though AAAC is more expensive than ACSR, trends continue to move in the direction of AAAC and in areas of higher corrosion, such as coastal areas, AAAC is the standard. ‘ACAR’ is another type of overhead conductor that stands for ‘Aluminum Conductor, Alloy Reinforced’, so this is very similar to ACSR, but instead of steel reinforcement, it’s aluminum alloy. This change does provide some improvement to the electrical and mechanical characteristics of this conductor, making it the more improved technology to ACSR.
Another technology out there is trapezoidal stranded conductors, see figure 2. Trapezoidal strands, as you can see, fill up the space left by the normal cylindrical strands. This configuration provides a resistance reduction of 15%-20% which gives quite a few benefits such as improved performance in high temperatures, greater conductor strength, and a higher current density for cylindrical conductors of same diameter. So depending on your specific application, trapezoidal stranding may be the right product for you.
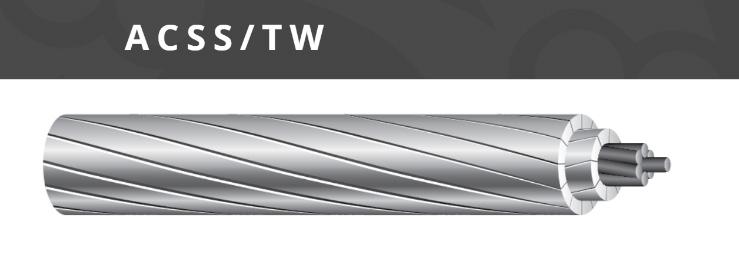
Figure 2: Photo taken from Southwire.com website
Why are some overhead conductors insulated and why are some non-insulated? Insulation is required on conductors as a means of protecting people from shock and also as a way of reducing the risk of line faults. Overhead conductors are often un-insulated because the risks of shock have been mitigated by placing the wires high in the air where people can’t touch them and also by separating them on the utility poles, which is why phases are run individually as opposed to wrapped around each other in a bundle. That would obviously create a line fault situation. Non-insulated conductors offer the benefit of reduced cost, reduced weight, and reduced diameter as insulation, of course, which adds weight and thickness to the line. As I mentioned above, the weight and diameter of your conductors can affect the utility pole class, size, and span.
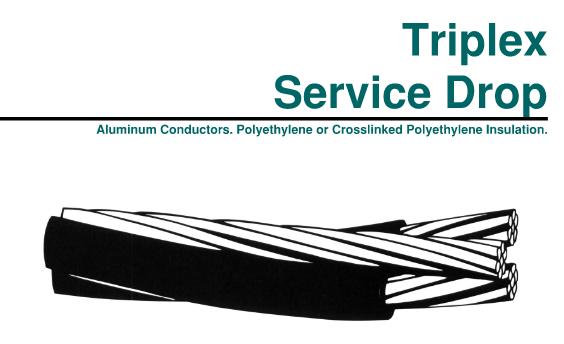
Figure 3: Photo taken from cutsheet found on Southwire.com website
This brings us to the final type of overhead conductor that I’m going to discuss here, and they are actually overhead cables; they are duplex, triplex, and quadplex overhead cables. See photo to left of a triplex cable. These cables are used between the secondary of a utility transformer and the customers switchboard. In other words, this is the cable that connects your home / business / building to the utility grid. The duplex brings single phase power, 1-Hot & 1-Neutral, and a quadplex carries 3-ph power, 3-hots & 1-neutral. The triplex cable shown above is what the USA uses to connect residential homes to the utility grid; there are 2-hots & 1-neutral which provides 120V, 1ph as well as 240V, 1ph. The neutral is bare because it’s cheaper; and where possible and safe, bare conductors are preferred to insulated for all the reasons above; cost and added weight and diameter. But why is it safe?
NEC 2017 Section 230.22 states as an exception “The grounded conductor of a multiconductor cable shall be permitted to be bare”. Therefore, the fact that it is run overhead, normally away from people, and also directly grounded to earth is what allows it to be bare. Finally, it is important to note that service drop cables generally cannot support themselves across the span from transformer to building and so messenger wires are used to physically support the cable. Next time you get a chance to look at a residential or commercial overhead service, you should note that one wire is taught and connected directly to the utility pole and building while the cable is wrapped around that wire. The taught wire is the messenger and it’s very important for reducing the risk that the triplex cable snaps and creates a very hazardous situation. In some cases, the bare neutral can double as the messenger for the cable. But be sure to confirm your specific situation with the NEC and local and state codes prior to specifying the neutral as a messenger.
Hopefully this article finds you well and can be used as a reference for your project needs. If anyone would like to contribute to the Rochester Engineer and add an article or would like to request information on a specific topic (not limited to electrical) just email me at beliasz@bergmannpc.com. As always, any comments are appreciated…! Thank you for reading.

Brett Eliasz, P.E., LEED AP BD+C , RES Director Bergmann in downtown Rochester, NY

Written by: Joshua Doores, RIT Alum, EIT, Electrical Engineer working at Bergmann in downtown Rochester, NY