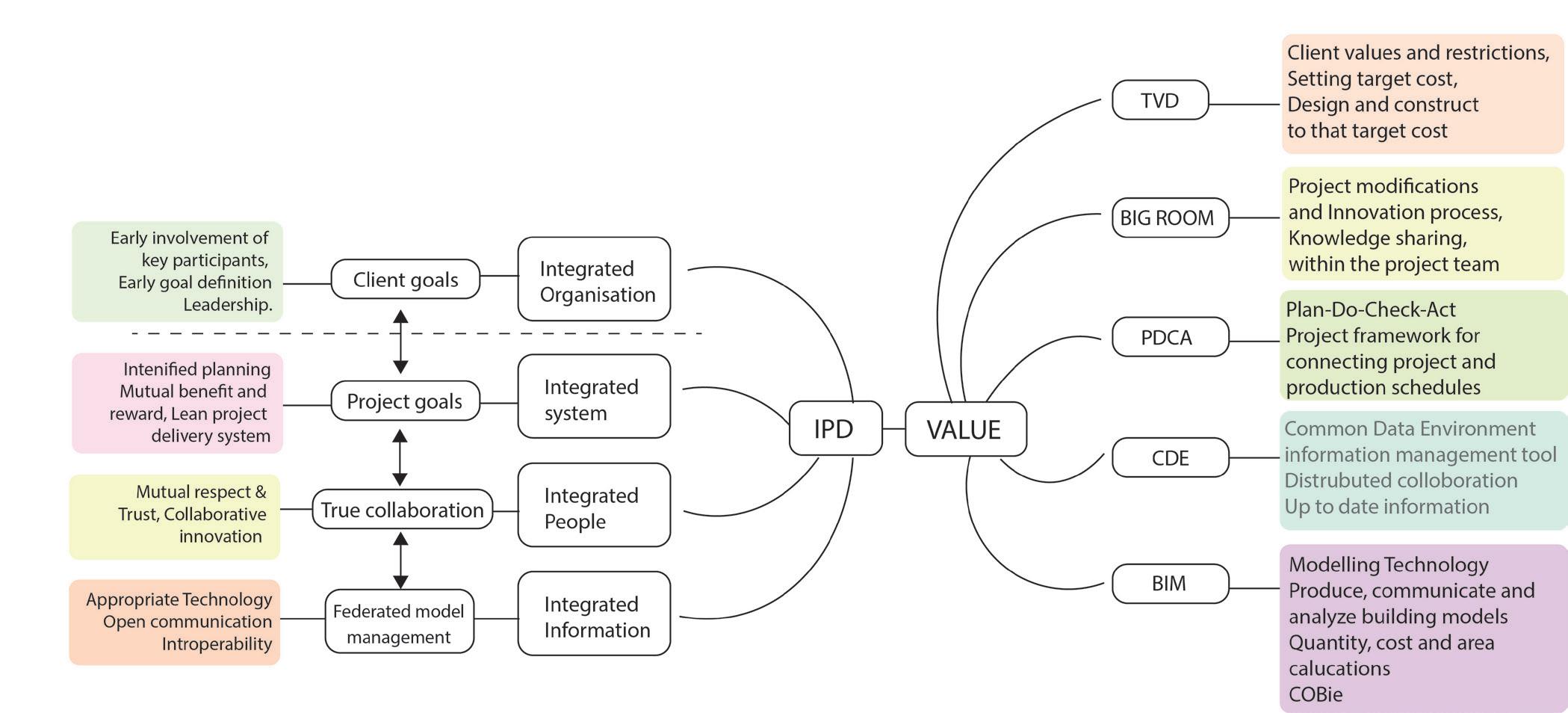
6 minute read
Research Methodology and design
This section depicts the research methods used to collect data in an attempt to answer major issues and objectives. The research also focused on the value generation techniques to achieve a highly valuable building with an integrated approach to project delivery. This research based on methodology of ‘Thematic analysis’ in particular ‘deductive approach’ to data analysis (Braun & Clarke, 2006). The study focuses heavily on qualitative data gathering methods, both primary and secondary. The primary data gathering approach was a literature review, which informed the interview questions, whereas the secondary data collection method was one case study for UCSF Mission Bay Hospital in California combined with a literature review to answer the following research objectives:
1. Establish a clear understanding of what an integrated project delivery is?
Advertisement
2. Identify the drivers/enablers for an IPD
3. Identify challenges and barriers to an IPD approach
4, Getting to know benefits of coupling BIM technology and Lean construction on IPD projects
5. Potential way forward for an IPD approach adoption in the industry
Integrated Organization
By Distinguishing the type of interdependencies within sub-team/groups within the network. This connection of information through federated model management within the project team eliminates project delays. Also connecting people’s actions, information, and decisions in a BIG room facilitates to make better decision within project team. Any changes during the design and construction phase can solved within a matter of time, since everyone in the project is interconnected and available at all point of time, which reduces the project time delays. The constraints dictated by the client and facility users, has to delivered by the project team’s early engagement to establish concepts, estimate cost and build in multidisciplinary/cross functional environments with end goal in mind. By target value designing, the estimated cost can significantly reduce in the early stage of the project with true collaboration and innovation between the stakeholders/project team members. Achieving a highly valuable building involves clear project brief from the core team, which shows leadership and commitment towards the target goals. Also, by assisting the project team through various process mapping, workshops, defining individual targets and decision making. Above fig the value behind the integrated to approach to project delivery from the insights of literature and case studies of this research.
Integrated Project team
Project teams are essential for delivering integrated projects. A core IPD concept is early engagement of significant participants, and these early participants, like practically all IPD participants, operate in teams. The teams give the right information at the right time and encourage creativity. Collaboration, devotion, and engagement are fostered by multidisciplinary teams. Furthermore, team processes improve decision making and increase support for the chosen strategy. Having a team, however, does not guarantee success. To get the benefits of teams while avoiding these performance issues, teams must be built, managed, and motivated efficiently. One of the Integrated project delivery principles is “Mutual benefit and reward”. Based on the project team performance and achieving the target goals incentive rewards has to be shared. For example: the tips of casino staffs are collected for a week and shared equally according to their shift timings. By this means, it changes the staff’s perspective shifts to a collaborative work culture where everyone supports each other by means of knowledge and techniques. Thus, by giving rewards increases collaboration between the project team members this has to be established by the organization leaders to change the work culture to improve the performance.
Integrated Information
To offer an accurate portrayal of project reality, integrated information coordinates information from all disciplines. It also gives all participants with the knowledge they need to carry out their tasks. It enables project leaders to track project progress, understand project results, and allocate resources to meet specified project goals. For example, a construction worker’s tools are arranged and easily accessible. Similarly, integrated information organizes project information and make it readily available for all. The purpose of an integrated information system is to improve and speed everyone’s comprehension of the current situation so that the project team can frame challenges for later and, ultimately, make better decisions. Typically, each team member has their own set of tools, technologies, and applications for estimating energy performance and providing design possibilities. To attain this level of team interoperability, an integrated information system is required. However, this is frequently inaccurate owing to the employment of desperate techniques and technologies, which result in the creation of a silo of information, which leads to poor decision making. For the owners to make better project decisions, an integrated information system, common data environment, and federated model management all connect to the same goal and give real-time status of design completion, cost, quality, and quantity. By making integrated information available to owners and users throughout the project lifespan, this imitates the value of the project.
Conclusion
The key to creating a highly valuable building is to start with the end in mind, include the core team early on, and incorporate the organization’s overall project vision. working toward the objective by providing the project team with a clear and succinct brief, assisted by an integrated information system. Agreements between the project team members should have a system of rewards and benefits that is mutually beneficial and fosters teamwork. The leadership responsibilities for monitoring the project team and determining whether they are lacking in technology or skills should fall to the core team members. By assisting them by providing workshops and setting up a process map, the core team members can facilitate the integrated system and add value between the project team members. The fundamental ideas for creating a highly valuable building have been offered by the case studies and literature reviews in this study. The research’s conclusions support an integrated business model that uses an integrated project delivery strategy to provide a developed asset that is of high value. When there is a trusting atmosphere and a helpful environment, integration in construction has been shown to boost quality and save cost. When you look at some of the early outcomes of these business model changes, the sector has reason for optimism (Fischer et al., 2011). Some of the places that require more development are:
• The true collaboration - between the project team. The commitment to building a team which supports the other team as if they were all the members of the same company is critical part of the process.
• Design simulation and automation – this will continue to develop and allow clients to optimize their design solution and predict cost as well.
• The BIG Room – Integration with lean methodology with VDC (Virtual design and construction) is enhancing the project quality and lowering the cost.
• Prefabrication and automation - The 3D models’ certainty enables prefabrication and automation, which are already paying off in the early phases of a fully integrated model before building activity.
4.
Project and Production Management portfolio
105 Sumner Street, Southwark, London planning case study
Introduction
This report illustrates design and production planning submission of a commercial development project, to UK planning authority. This report will also demonstrate the understanding, critical analysis of the building planning proposal to the government. It contains design and access statement with site introduction and planning considerations. Component B illustrates the construction management and off-site construction plan. The planning statement is prepared and submitted in support of the planning application for full planning permission made for the redevelopment of 133 Park Street and 105 Sumner Street (figure 1.0 “Site”). The proposals are described in more detail in the rest of the report, but in summary, full planning permission is sought for the following (herein referred to the ‘Proposed Development’):
“Demolition of the existing buildings on the site and redevelopment comprising the erection of two office (Class B1) buildings ranging in height from five to ten storeys plus rooftop plant, creation of a new basement, new access and servicing arrangements, creation of a new courtyard and provision of a retail (Class A1/A3/A5) kiosk, hard and soft landscaping and other associated works.”
This Planning Statement provides a comprehensive review of national, regional and local planning policy and guidance relevant to the nature of the development proposal. Following extensive pre-application engagement with the London Borough of Southwark (LBS), the Greater London Authority (GLA), and Transport for London (TfL), the planning application is being submitted. The plans have also been discussed with local people and stakeholders.
Location
The Forge 105 Sumner Street, Southwark, London
Project Partners
Client Team: Landsec, Bryden Wood (Architects), Piercy & Company, Gerald Eve, Gardiner & Theobald, Mace, Sir Robert McAlpine (Contractor) // Key Trade Contractors & Suppliers: J Coffey Construction, DAM Structures, N G Bailey, Hotchkiss, Hall & Kay, Aluprof, NACWL, Kone, Tata Steel, Schneider Electric
Building Type Office, New build (139,000 sq ft)
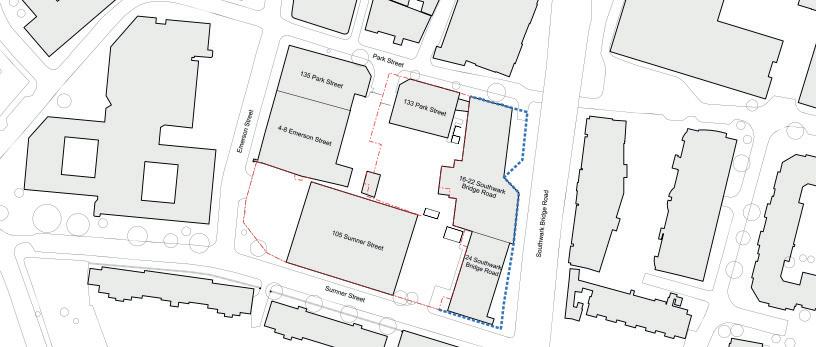
Project Status
Construction. Completion Summer 2022.
The Forge, located at 105 Sumner Street in Southwark, London, aims to be the first commercial structure constructed and operated in accordance with the UK Green Building Council’s (UKGBC) framework for net zero carbon buildings and related energy performance standards, and it offers ground-breaking approaches to the global warming problem. Thanks to funding from Innovate UK, Landsec is developing the first office block ever planned and built using the “kit of parts” approach based on a structural frame that is “Design for Manufacturing and Assembly.” This lowers the amount of on-site waste and the use of natural resources, in contrast to traditional building, where up to 30% of materials end up in landfills. In comparison to a conventional structure, it also reduces embodied carbon emissions by 25%.
Construction Management
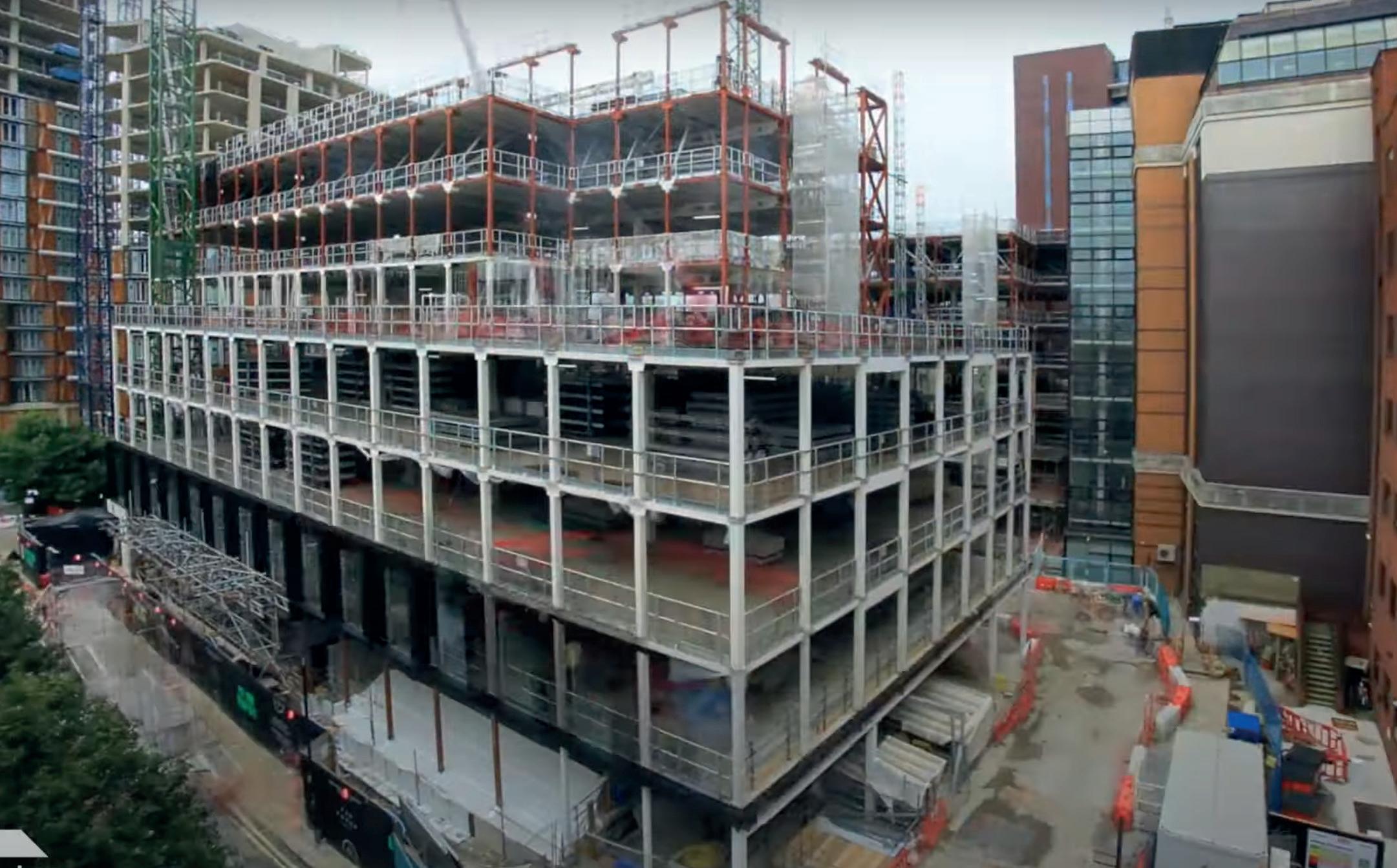
Proposed Project Schedule : key Milestones :
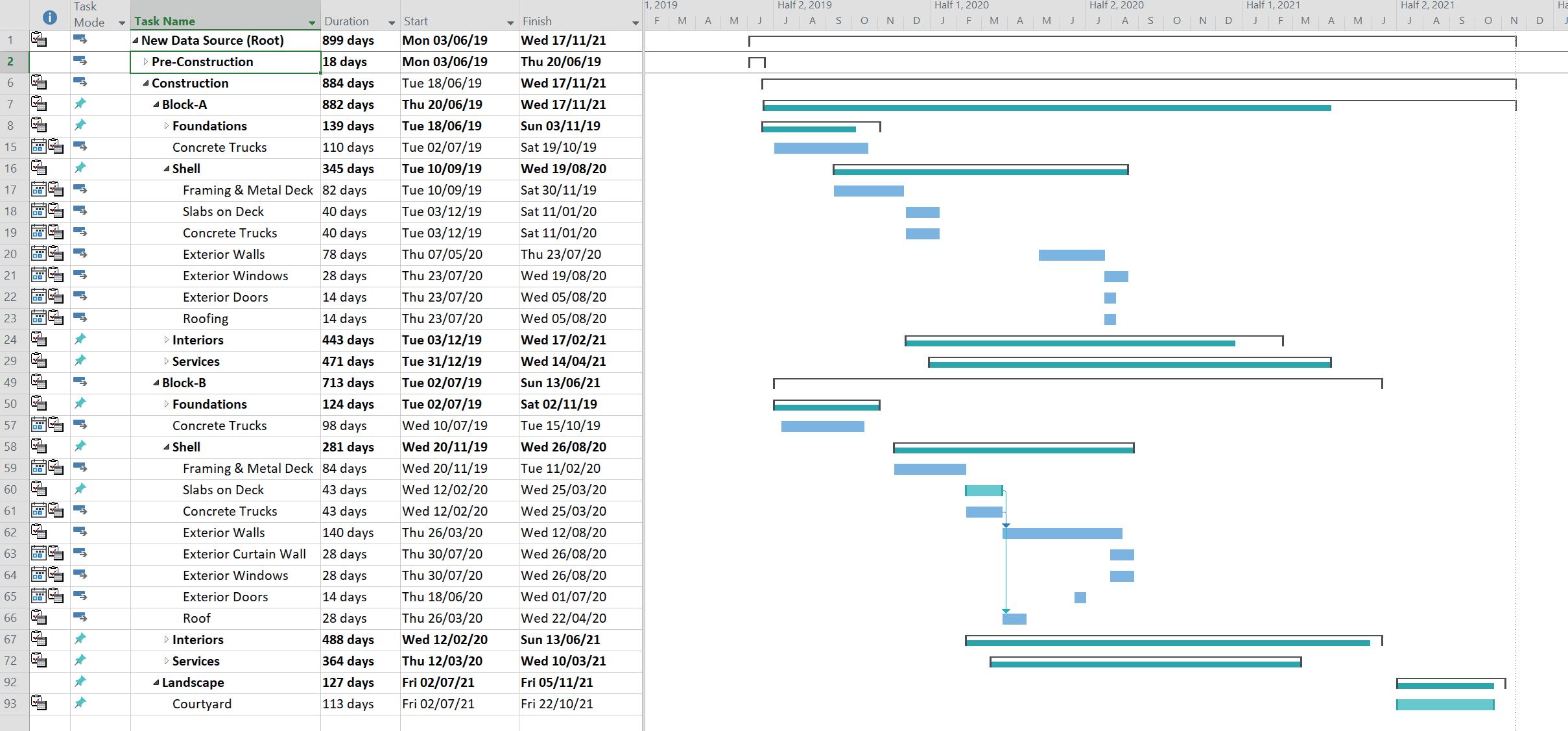
Project Start Date : October 2019
Project Completion : November 2021