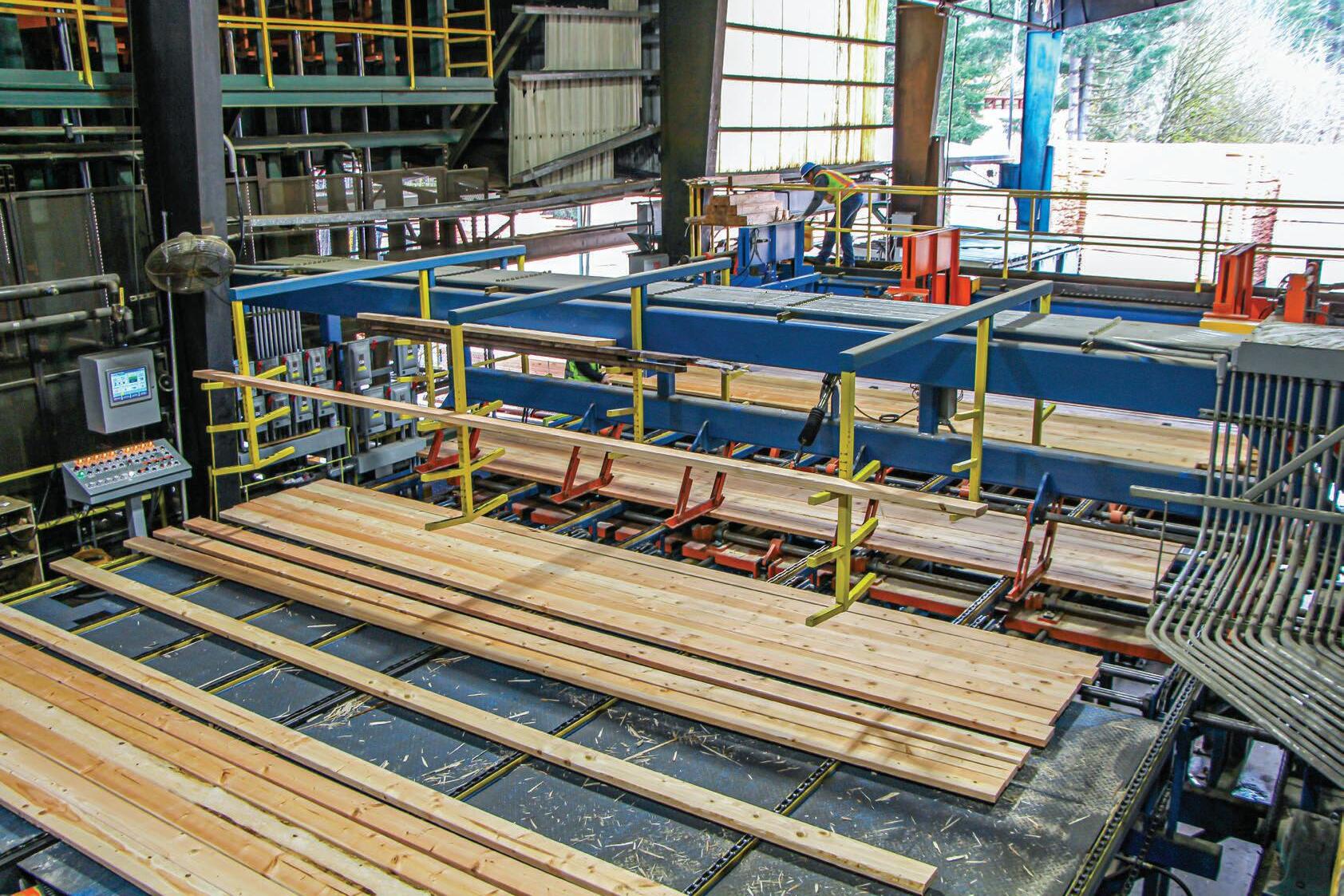
5 minute read
SORT STACK STRAP UPGRADE
By Dan Shell
NOTI, Ore.
Recent improvements at Sierra-Pacific’s Noti mill 25 miles west of Eugene, Ore. have boosted efficiency and quality at the facility that produces all-green, 100% Douglas fir products, primarily dimension lumber along with timbers.
During the past four years, the mill has added a new Lucidyne (now owned by Microtec) grade scanner, new USNR trimmer infinite fence system and most recently a Hogue Industries high speed dual fork stacking line with end-tamping feature. A Samuel strapping system with innovative batten feeding feature was added to the line shortly after.
The mill’s finishing end had been a bottleneck for the operation, says Mill Manager John Simington, adding that improvements in the area the past few years — grader, fence and new stacking-strapping line—have boosted overall efficiency.
Project
The largest of the projects included an all-electric Hogue Industries high speed dual fork stacker with secondary hoist system and Samuel strapping system. The project helped speed up the planer mill and added more precision and efficiency on the stacking-strapping end, contributing to a 25% overall increase in stacking capacity.
Simington says he really likes the indexing and sequencing features of the stacker’s control system, which also allows pre-programming for every individual product the mill stacks.
“The previous stacker would take up to a minute and a half for each package,” Simington says. “But this unit will do it in 47 seconds.” He adds that the secondary hoist that takes the first few courses of a unit while the primary hoist cycles down to exit a full unit has helped speed up throughput at the planer mill even more.
The Samuel strapping system including batten feeding and strapping was a significant upgrade, Simington says, because it automated a process that had formerly been done manually by forklift drivers, resulting in a win for the mill on ning to demand it,” he adds.
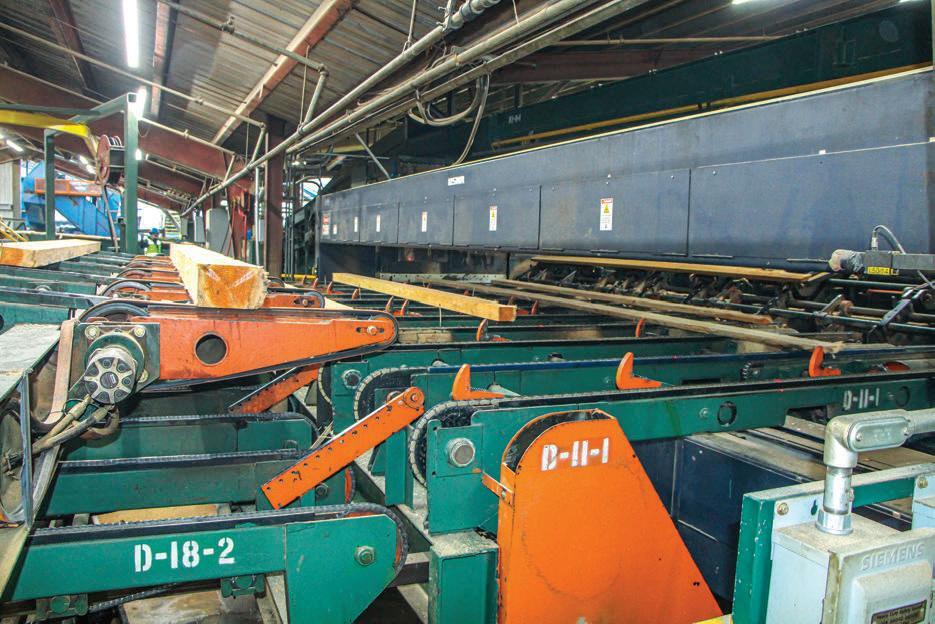
Strapping system with batten feeder has helped make operations smoother, safer. Noti mill produces primarily dimension lumber, with some crossties and timbers.
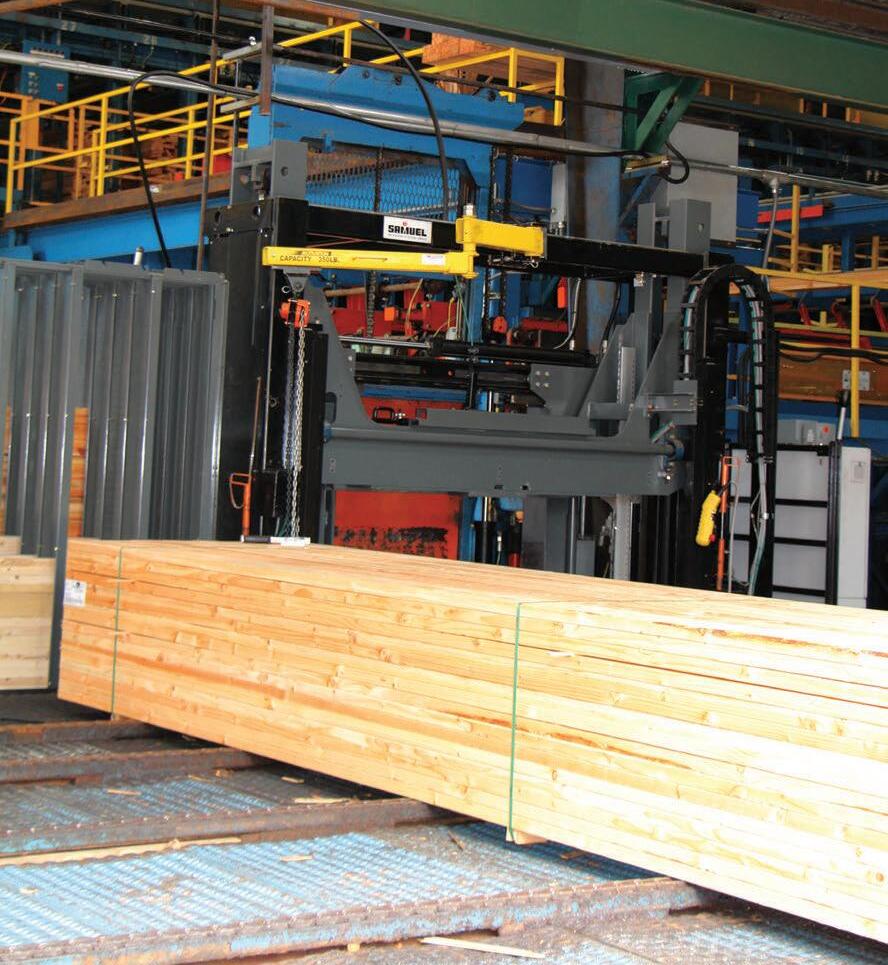
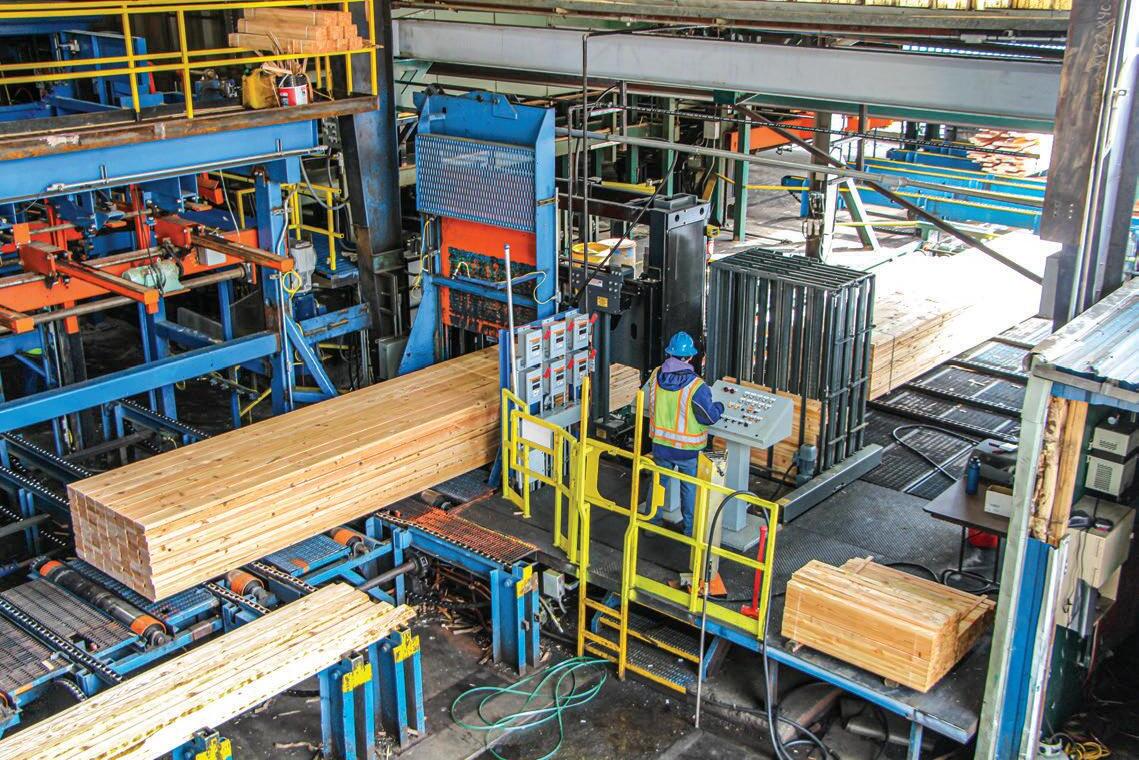
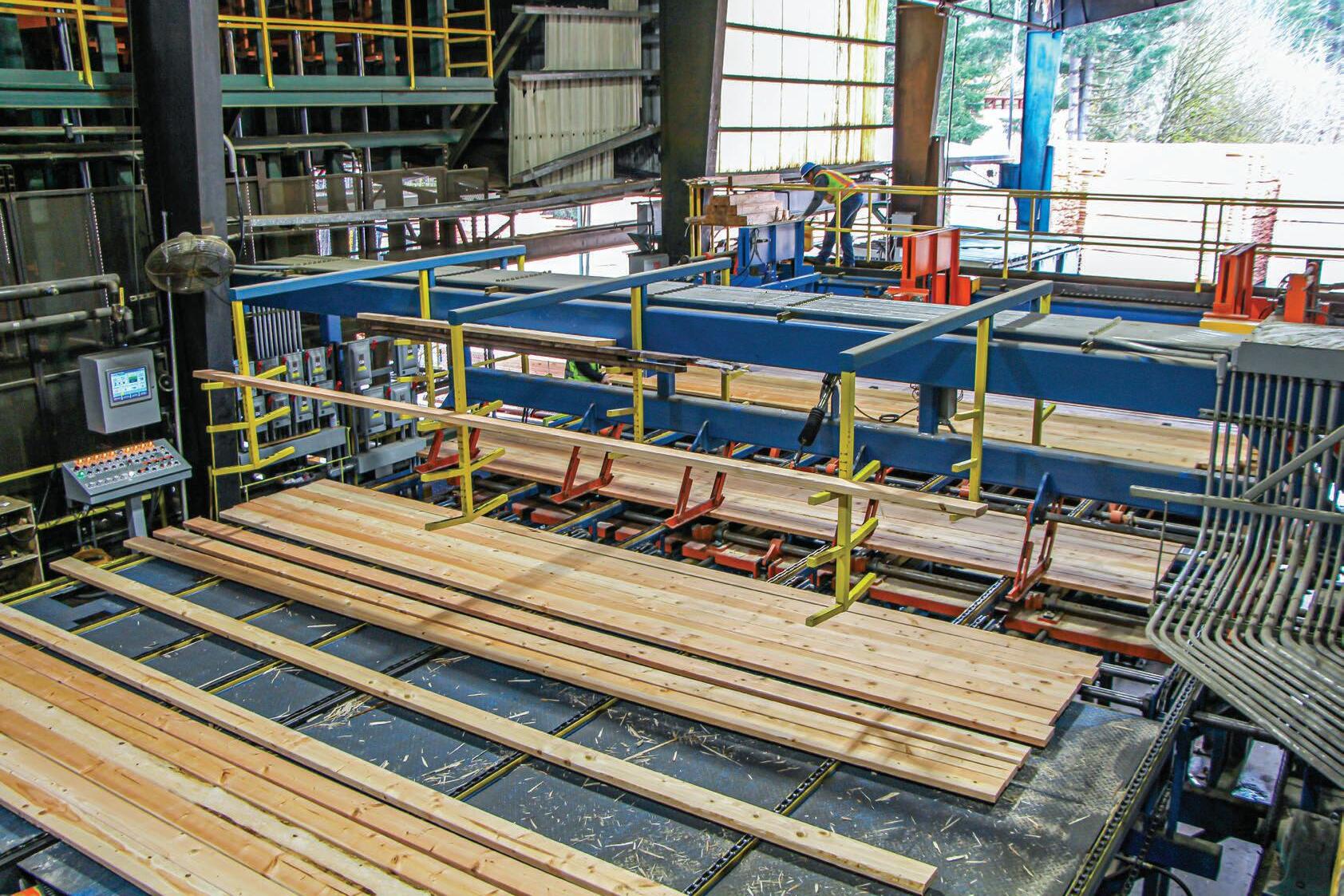
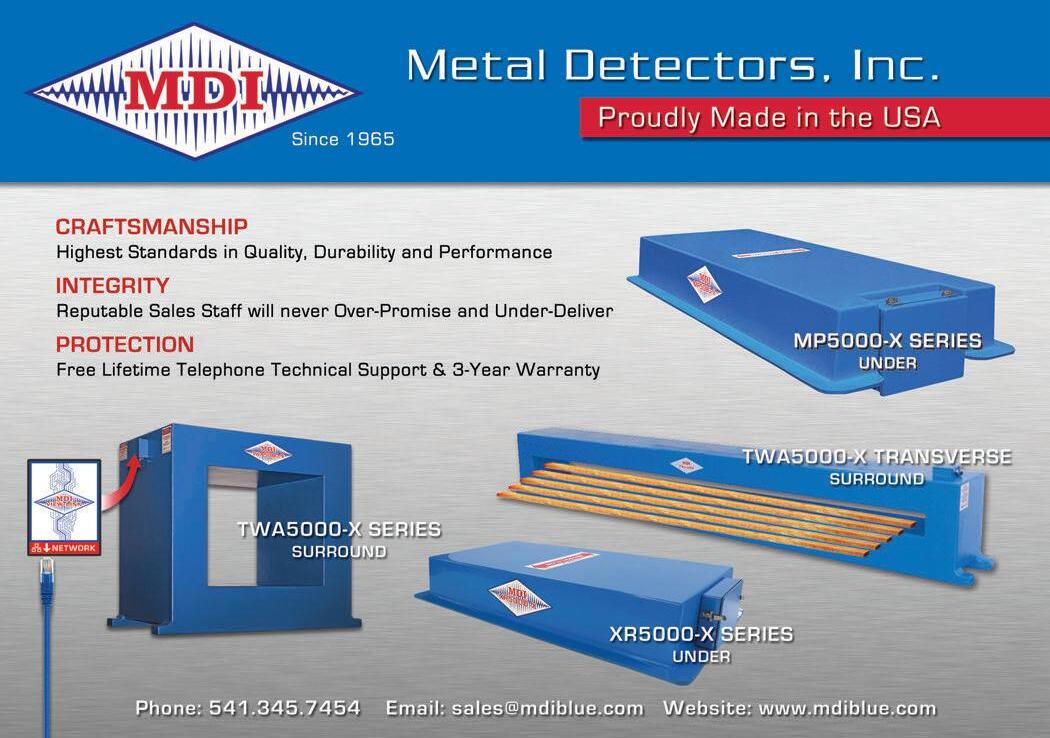

The new stacker installation in 2021 went smoothly, with good teamwork between SPI in-house personnel and supplier and contractor employees, Simington says. Once the new stacker started up the first of January 2022, “Within two or three days we were already at 50%, and within a week we were keeping up with the planer,” he adds.

Changeovers at the stacker are quick and clean, about 15 minutes, and the sorter setup along with grade focus enables the sorter to handle two different products at the same time, further boosting efficiency.
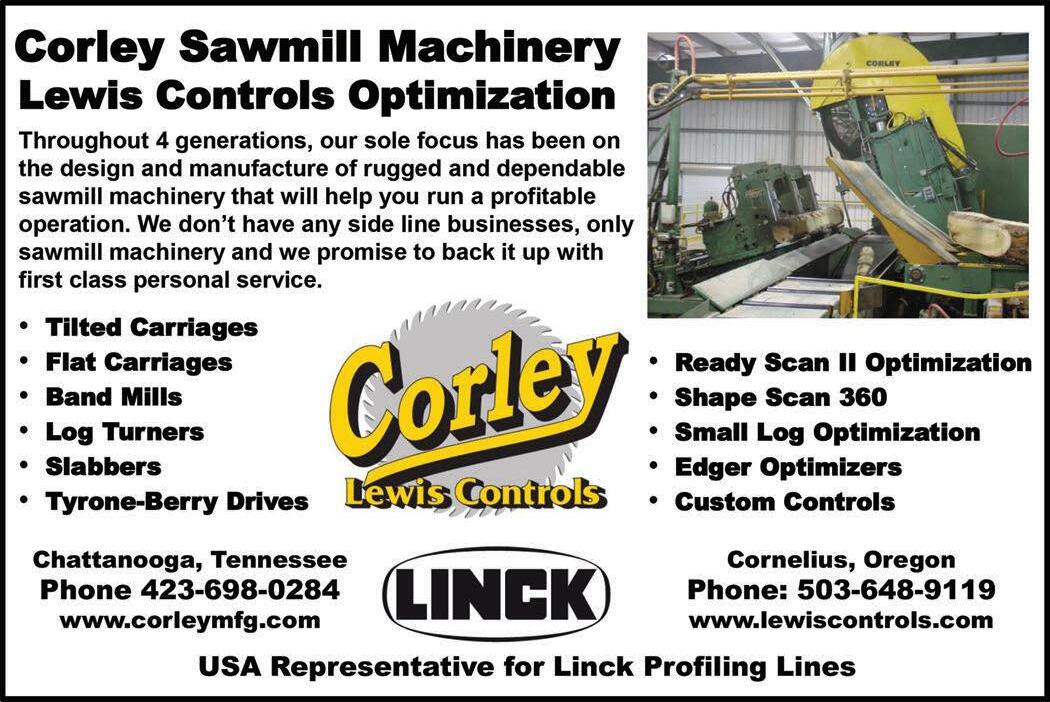
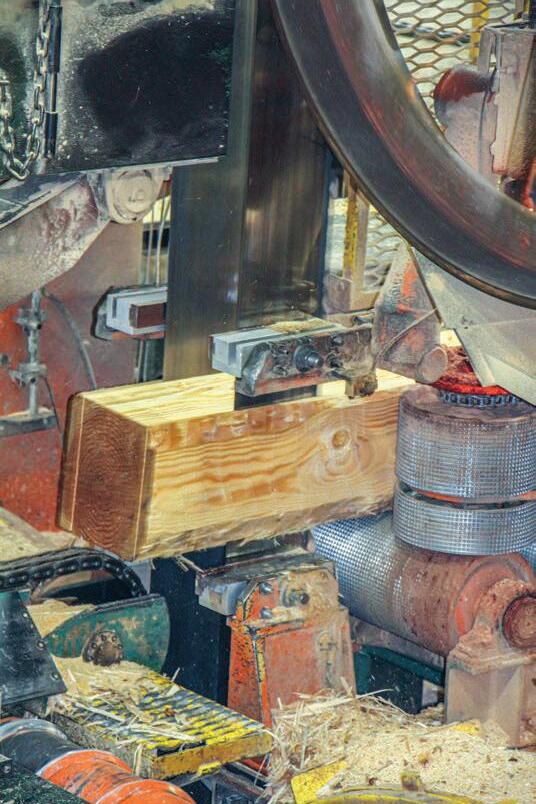
Incoming log loads are all Douglas fir, with 26 in. maximum log size. Columbia River Scaling Bureau handles scaling duties. The facility takes around 90-100 loads a day.
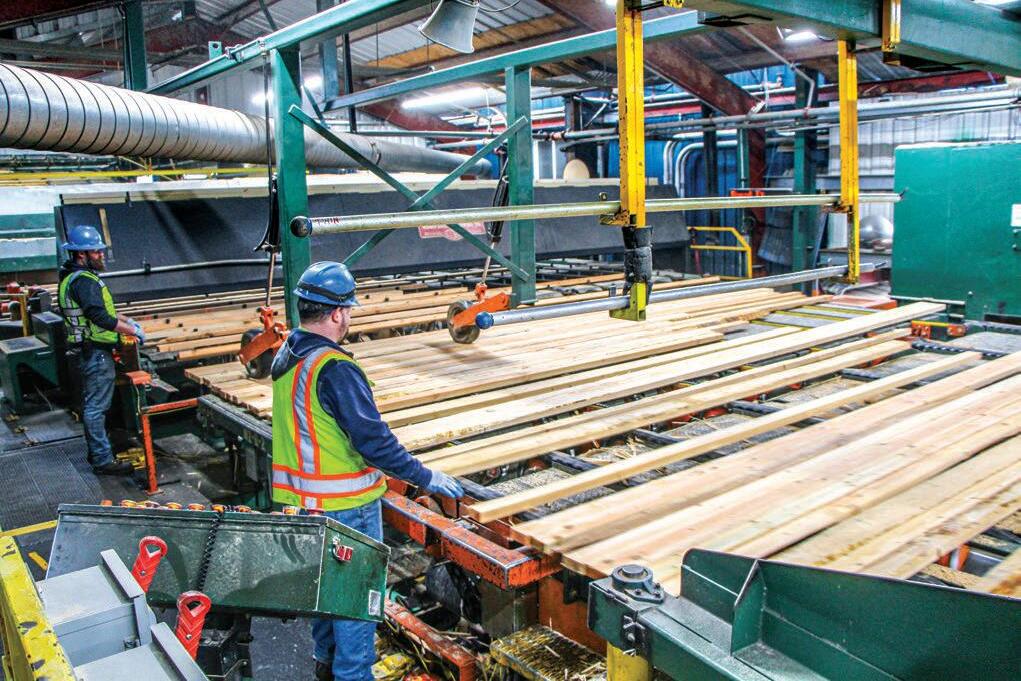
Logs are unloaded with a LeTourneau unit and handled with Cat 980 and Komatsu 500 wheel loaders that also feed the mill. Outside of a small sort for obvious tie logs, there are no species sorts at the all Douglas fir mill, and the goal is to feed a consistent log size to the canter line.
At the infeed deck, a log shovel helps orient logs and blends incoming log sizes to maintain an even flow. Logs are debarked with a Valon-Kone 27 in. debarker.
The primary breakdown system at the mill is an Optimil canter with USNR dual zone scanning and optimization and log turning system. (USNR scanning and optimization packages using the Mill Expert platform handle primary and secondary breakdown at the canter, double arbor gang, board edger and trimmer.) The canter handles logs up to 26 in.

From the canter, much of the mill’s output goes through a Schurman 15 in. double arbor gang that’s been modified over the years. The gang is “an amazing production machine,” says Simington of the machine’s consistency and accuracy. Cants 15 in. and under are routed to the gang from the canter. Cants that are larger than 15 in. flow straight to a Kockums twin band resaw.
Flexibility
Exiting the canter, cants receive a spray-on code from a Diagraph ink jet system that corresponds to their sawing solutions. Cants going to the double arbor receive a number representing one of 24 cutting patterns. Cants destined for the twin receive a three-digit tracking number that allows visual verification that the cant about to be sawn aligns with the cut pattern sent by the canter optimizer. The twin also receives a data packet that allows automation of feed rate, guide height settings, pass count, rotation and destination. According to Simington, the system allows the operator to focus more intently on flow control and efficiency.
The twin band handles material destined to produce ties and timbers, which are routed to a timber deck on the north side of the mill, and also can route cants back to the double arbor gang after removing sideboards.
“We run with a lot of flexibility,” Simington says. “You can’t focus on just recovery or just highest value. We have to find a cross section between those to get to the best bottom line we can.”
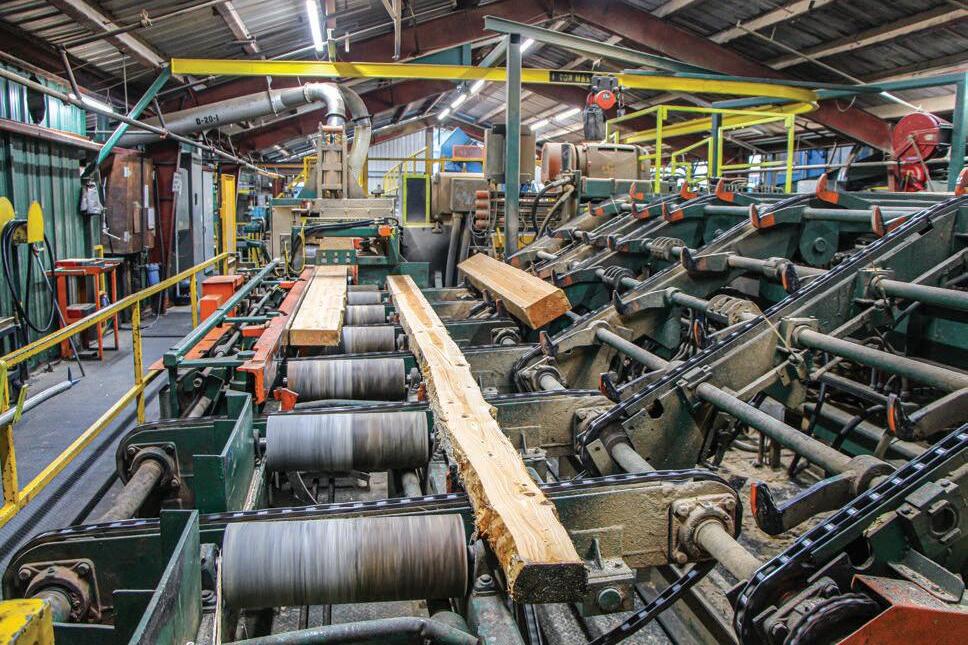
Generally, the plan is to keep the double arbor gang, with its five sawlines, as busy as possible. The twin band produces most of the mill’s higher value products, but as much as 70%-75% of output goes through the gang.
The double arbor feeds into a standard linebar gang or to a 6 in. board edger. Lumber flows to USNR trimmer and USNR 18 bin sorter and USNR rough stacker, with USNR trimmersorter controls.
The planer mill features a Newman machine that’s been well modified, with pineapple roll tensioning and upgraded electric drive system. Lumber exiting the planer goes through the Lucidyne grade scanner, then past a check grader before flowing to the Newnes trimmer with USNR infinite fence upgrade, and on to a 42 bin LSI sorter. The finishing end trim-sort line is controlled by Lucidyne’s sorter control package.
The Noti mill produces dimension lumber in 8-24 ft. lengths, 2x4 thru 2x12. Roughly 10% of total volume is tie/timber products (not surfaced). Noting the all-green production, Simington says drying material has been discussed, but the facility has been a strong green producer for decades, and the product is a good complement to SPI’s strong KD lumber product manufactured at other sawmills. While not as large overall, the green market also provides premium pricing for many of the items produced at the Noti mill, he adds.
Simington points out the recent finishing end improvements not only put the mill in a more competitive position, but have also created better, more productive working conditions for employees as well.
These upgrades produce a good product at a faster rate, while doing it safer with less hands-on labor. “That’s good for everybody, especially the employees,” Simington says, noting the facility is approaching two years without a losttime accident. The mill currently employs 112 and is running two shifts.
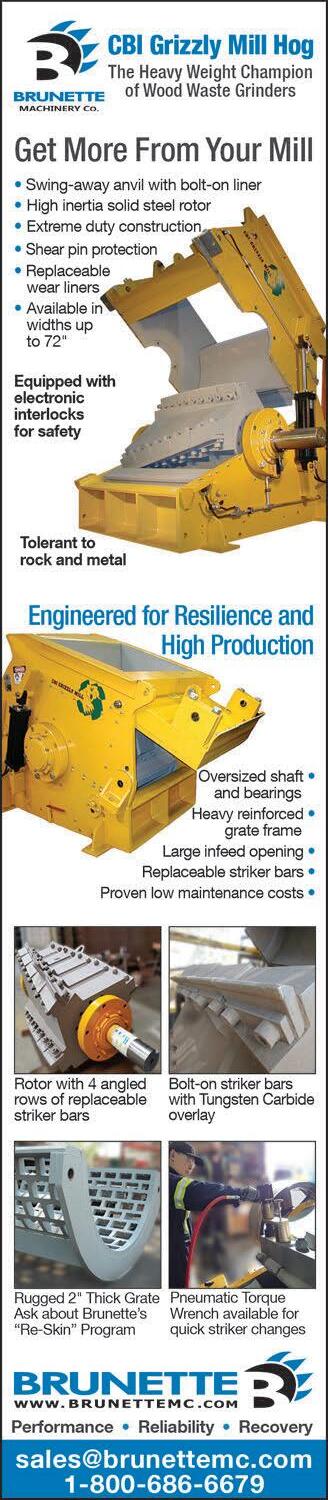
The mill’s history and background date to the 1950s when it was operated by one of the founders of what eventually became the Swanson Group in Glendale (now Roseburg), Ore.
Seneca Sawmill Co. purchased the Noti sawmill from Swanson Group Manufacturing in October 2011. Ten years later, the Noti sawmill was part of the Sierra Pacific Industries acquisition of Seneca Sawmill Co. in October 2021. The acquisition included a 175,000-acre tree farm, and the Eugene, Ore. site with three sawmills and a biomass power plant.
Including its Oregon operations, SPI owns and sustainably manages more than 2 million acres of timberlands, 18 sawmills and eight renewable biomass energy cogeneration facilities across three states. SPI also owns and operates millwork, remanufacturing and windows operations.
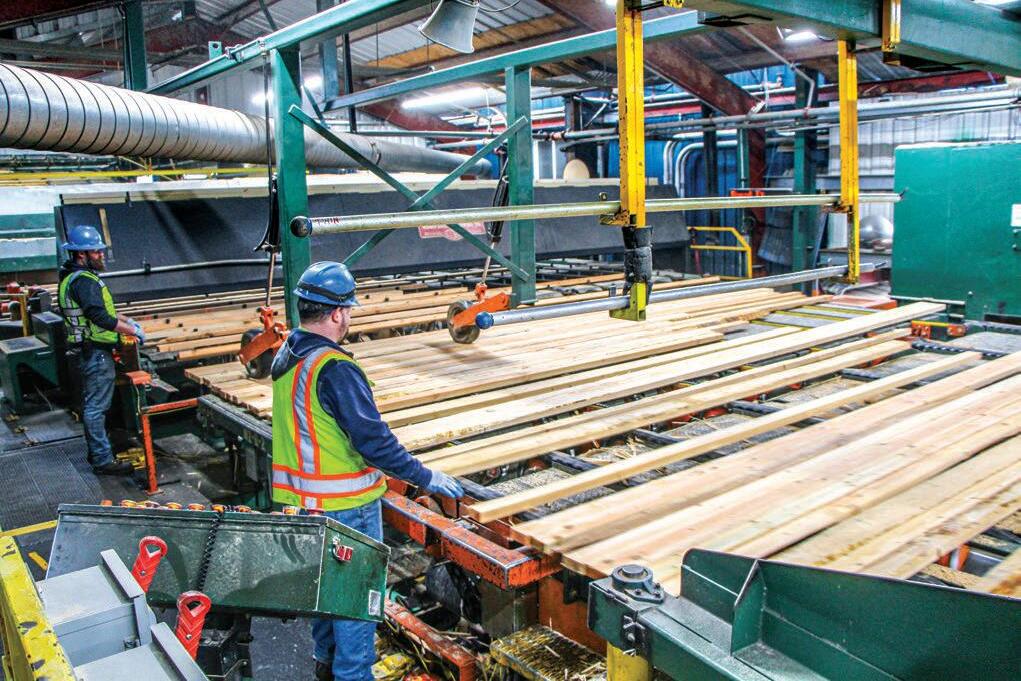