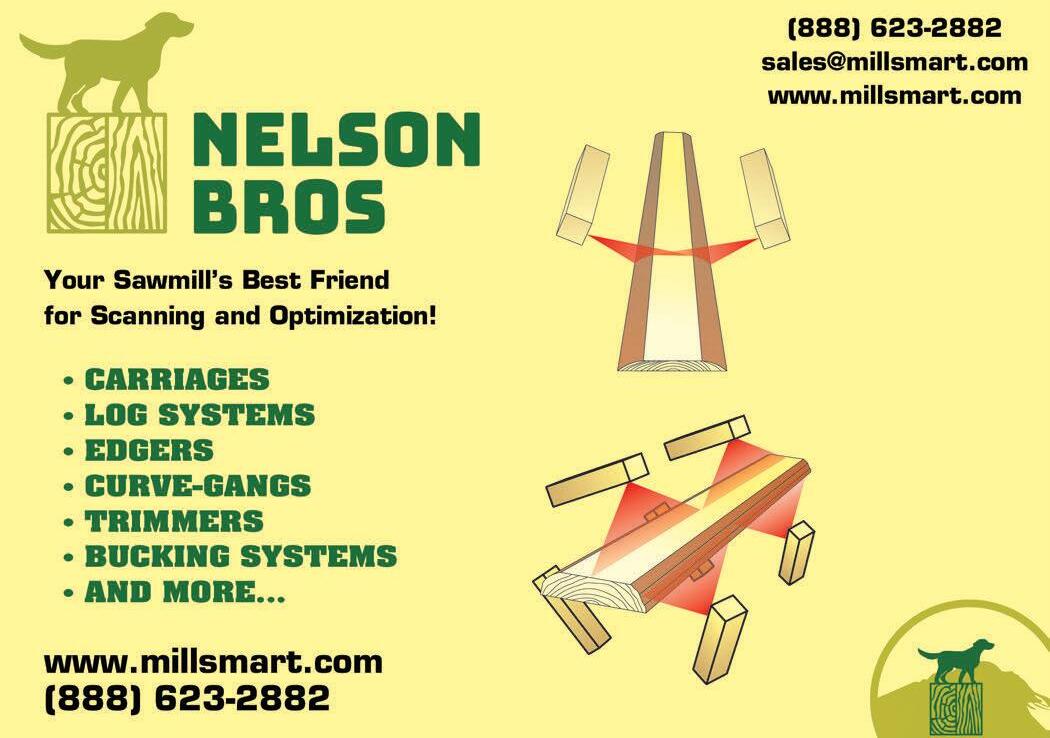
12 minute read
MACHINERYROW
NTC Produces Band Saw Filer Program
Northcentral Technical College (NTC) recognized the first group to graduate from its Band Saw Filer Certificate program. Students from Wisconsin,
Offered in-person at NTC’s state-ofthe-art Wood Technology Center of Excellence in Antigo, Wis., the program prepares learners to maintain, align and time band saw grinders; apply tradebased formulas; bench band saws (level and tension); fit band saws (swage, shape and grind); weld band saws using mill; and practice personal safety when handling saws.
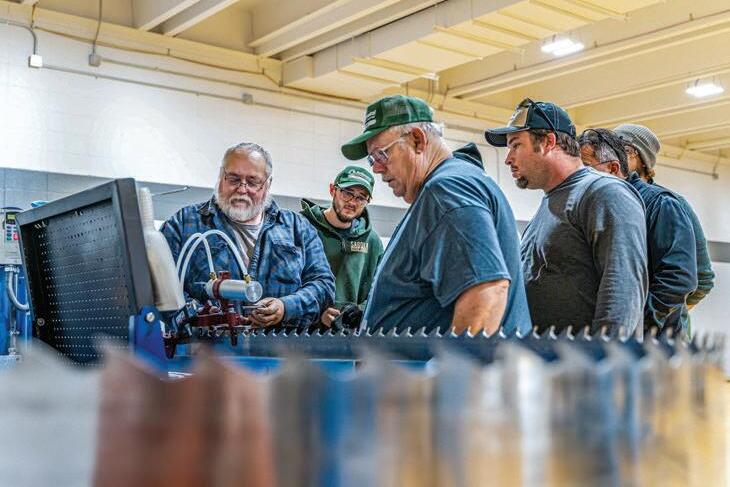
Graduate Jackson Breir says he was motivated to enroll in the training after learning about the opportunity from his employer, Granite Valley Forest Products. “I will use the skills I learned to increase the quality of our saws and hopefully in the future increase production capabilities,” Breir says.
According to Kretz Lumber Co. President Troy Brown, the Saw Filer Certificate is vital to the continued success of the sawmill industry. “The industry has been requesting NTC to provide filer training for a number of years, and NTC has been able to come through and help the industry once again by providing the only accredited saw filling program in the United States,” Brown says. “Saw filing is a highly technical skill and NTC’s saw filing program provides a comprehensive training program that we cannot provide on our own.”
Saw filing expert Mitch White, with 45 years of experience encompassing both the softwood and hardwood sawmilling industries, teaches the Band Saw Filer
Certificate program. Coming from a large family of saw filers, White learned at an early age the critical benching and fitting techniques required to prepare and repair saws for multiple sawmills.
After 30 years of working as a head saw filer for various mills, Whte joined SawPro Inc. as a saw filing consultant and traveled coast to coast training saw filers, setting up saw filing rooms, and solving complex sawing related problems. White was heavily involved in the development of NTC’s new Band Saw Filer program and enjoys sharing his knowledge and proven saw filing techniques with program students to develop the next generation of saw filers.
“Our sawmilling industry has needed a formal training program for many years, and I am very honored to be able to instruct the class,” White says. “We are now training our next generation of saw filers.”
After having more interest than spots in the first class, NTC began be offering the same four-week program in February.
“I have known Mitch White for several years and appreciate his high filing standards and abilities. We are excited about this new training opportunity and are planning on sending an employee to the upcoming February program,” adds Scott Erickson, US Saw Filing Superintendent, Interfor.
NTC recognizes the industry need for expanded saw filing training and additional programs are in development. Starting Summer 2023, NTC will be adding an accredited circular saw certificate to their saw filing program lineup.
For additional information or to get started in NTC’s Band Saw Filer Certificate, visit: www.ntc.edu/academics-training/programs/all/certificate/band-saw-filer
Cooper Machine Partners With EWD
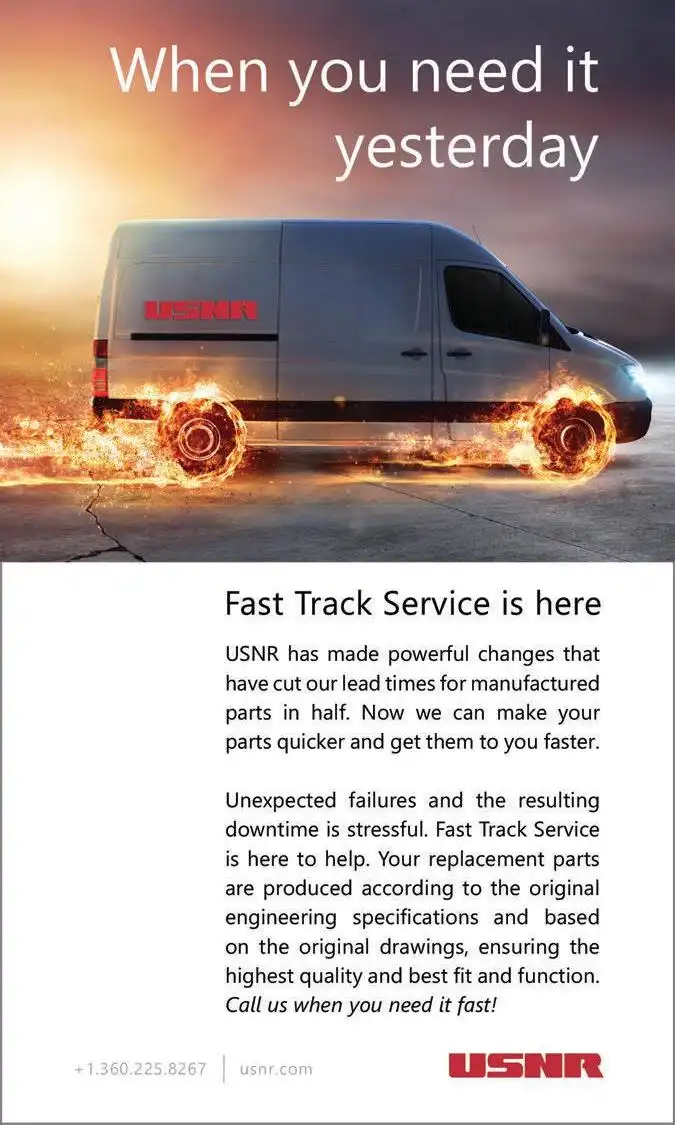
Cooper Machine Co., a long-established manufacturer of quality sawmill equipment located in Wadley, Ga., an- nounced that it is partnering with German-based sawmill machine manufacturer EWD Sagetechnik.
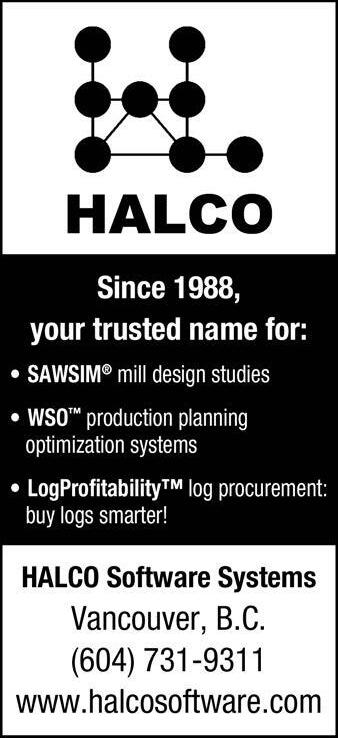
Cooper Machine has been offering equipment for sawmill, pallet, and post and pole mills since 1965. The company is in its third generation of successful management.
EWD dates back to 1862 and today employs 250 in Germany. The partnership with EWD allows Cooper Machine to offer an expanded range of sawmill equipment.
“In the future, with labor getting more expensive and harder to find, we want to offer our customers fully automated sawmills. With the same shared beliefs, we believe we have found the ideal partner in EWD Sagetechnik,” explains Frances Cooper, CEO of Cooper Machine.
Working with EWD will offer many advantages for Cooper Machine customers since it will be able to offer a wide array of well-designed, German engineered sawmill equipment, along with service and parts located in the U.S. Cooper Machine has committed to providing customer service on all EWD equipment it sells and will stock the parts needed to back the service.
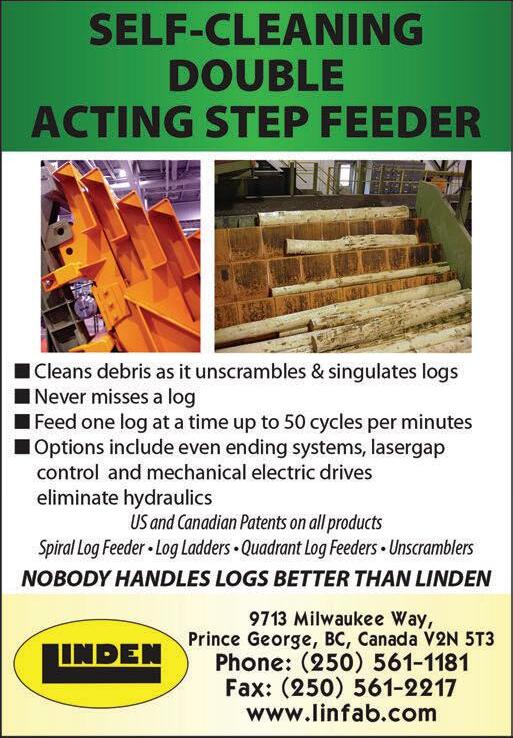

Con-Vey Names Buck As Product Manager
Con-Vey has announced the promotion of Joe Buck from sales engineer to Product Manager, having been with the company for nearly four years. In his new role, Buck will lead the strategy development and execution of several products at ConVey, and will be working closely with the engineering, sales and marketing teams. Buck’s extensive experience in both sales and engineering makes him especially qualified to drive the growth and success of these product lines for Con-Vey.
Dave Larecy, CEO of Con-Vey, comments, “Joe has been a valuable member of our team these last few years, and we’re excited to see him take on this new role. His expertise and dedication to our customers make him the perfect fit for Product Manager, and we’re confident he will excel in this position.”
Jeremy Goebel, Vice President at Con-Vey, also shared his excitement about Buck’s promotion: “Joe’s deep understanding of our customers’ needs will be invaluable in driving our product strategy forward.”
Canfor DeRidder Has Log Cranes In Place
Fulghum Industries, Inc. reports the commission of two recently installed 170 ft. 45-ton log cranes for Canfor. The cranes will be feeding the new $160 million, 250MMBF sawmill at DeRidder, La. The log cranes were commissioned and certified for operation on January 31.
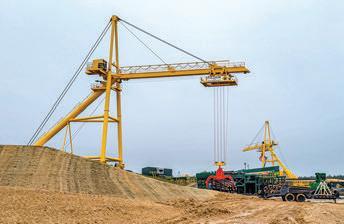
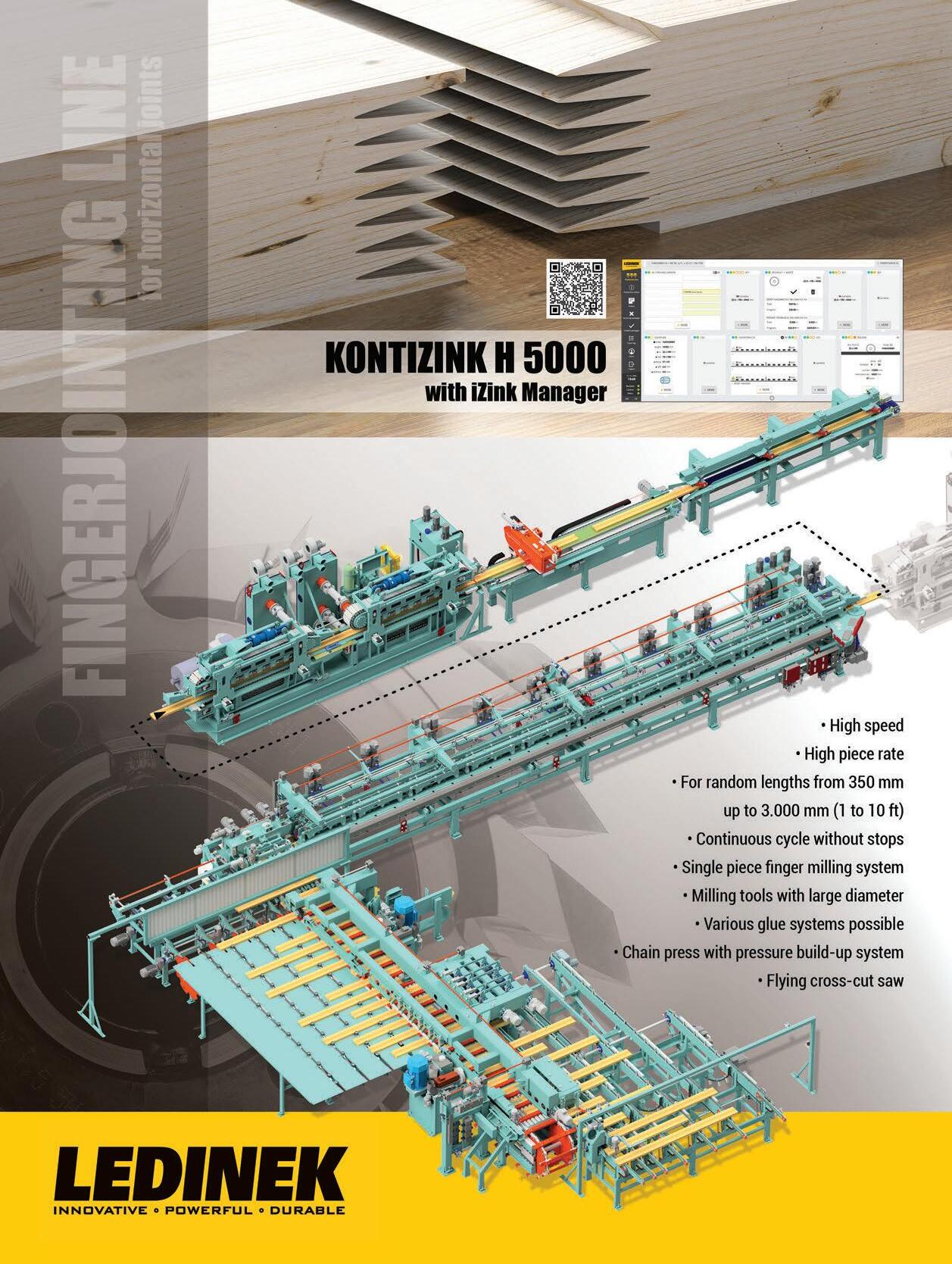
Homan Industries Names Reaves CEO
Homan Industries, which operates a SYP sawmill, dry kilns, planer, pressure treating facility, reman operations and a logistics company in Fulton, Miss., named Bud Reaves as CEO, succeeding Larry Homan, who after 56 years in this position assumes the role of Chairman of the Board.
Reaves becomes responsible for the four business operations of Homan Industries: Homan Forest Products, TriState Lumber, Homan Logistics, and Homan Wood Products. Reaves has more than 20 years of wood products experience and has been with Homan Industries for 16 years, holding leadership positions as COO and plant controller.
A native of Mississippi, Reaves holds a bachelor’s degree in Finance and Accounting from Delta State University. He currently sits on the Executive Committee of the Mississippi Lumber Manufacturers Assn.
SNA Adds Rupp As Senior Recruiter
Search North America (SNA), a leading wood products-based search, recruiting and placement firm, named Dave Rupp as a new Senior Recruiter, mainly focusing on the Western U.S. and Canada. He joins the SNA team with more than 40 years of experience in the wood products industry, working with Fortune 500 companies in North America and abroad. Rupp has extensive experience developing strategic alliances within all levels of the business, government, and environmental communities.
Rupp’s home office will be based out of the Vancouver, Wash. area, while SNA’s main office will remain located in North Carolina. Rupp graduated from The Ohio State University and most recently was a business development director at Advanced Nano Adhesives. While there, he leveraged industry contacts in pressure-treated wood, OSB, particleboard, MDF, EWP, and resin suppliers/industries to move the company forward, promoting a patented technology that improves board properties and water resistance while reducing resin costs.
Founded in 1982, Search North America has placed professionals in every area of the wood products and related industries. From entry-level positions and skilled trades to executive-level roles,
SNA helps companies find the talent they need and can help individuals with their next career move.
Richard Poindexter, SNA President and Owner, will continue to specialize in client and candidate relationships in the Eastern and Southern parts of the U.S. and Canada. Carl Jansen, SNA founder, will be stepping into a role as recruiting consultant and business developer.
Rupp can be reached at 360-601-3717; daver@searchna.com
Hunt FP Supports Forest Products Center
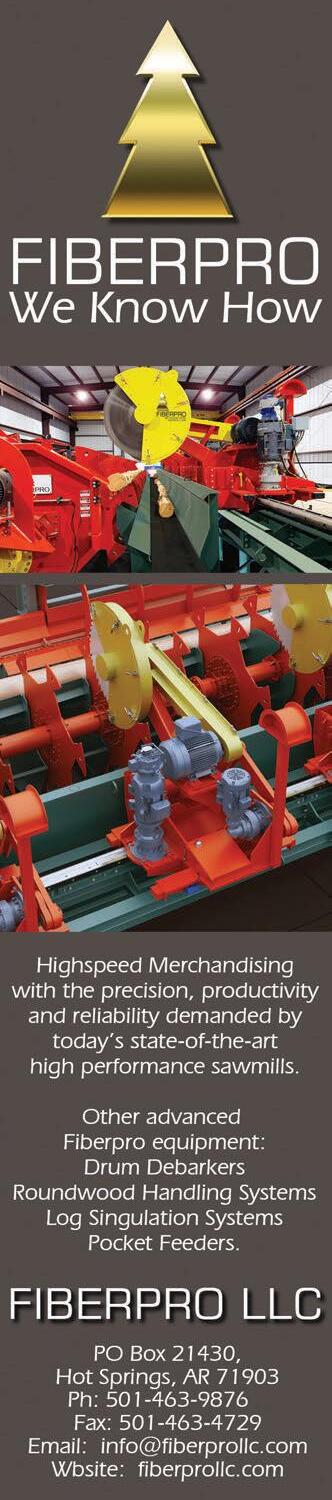
Hunt Forest Products LLC has pledged $500,000 to support the new Forest Products Innovation Center on Louisiana Tech University’s South Campus at Ruston. The Forest Products Innovation Center is slated to become a hub for discovering new methods to capture, produce and utilize the state’s renewable and sustainable forests for generations to come. It was developed in response to the University’s Tech 2030 strategic initiative to create programs and research that bolster collaboration and partnerships within academic areas.
“As co-owner and chairman of the Board of Directors for Hunt Forest Products, we value our current partnership with Louisiana Tech University,” Trott Hunt comments. “We know the collaboration between industry and academia is key to catalyzing innovation, research and growth. Realizing the knowledgebased opportunities the Center will provide for the forestry industry, as well as the important role it will play within the state and local economies, we are happy to expand this relationship by investing in the new state of the art center.”
The facility will bring together faculty and students from diverse areas like Forestry, Chemical and Industrial Engineering, Sustainable Supply Chain Management, as well as other disciplines, to collaborate on the challenges that will face the State of Louisiana in the future.
“We anticipate research in new uses of our vast forests to create greater economic opportunities for our state by focusing on more effective and efficient processing of forest products while also contributing to sustainability and a low carbon future,” says Dr. Les Guice, Louisiana Tech President. “This new building will also provide space for research collaborations with the industry and other partners, and each of these ini- tiatives will help our students be better prepared for careers in the forest products and other industries.”
“We believe this Center will have a tremendous impact on the forestry industry by connecting people, ideas, research and resources,” adds Jimmy Hunt, co-owner and vice-chairman of the Board of Directors of Hunt Forest Products. “Louisiana Tech has a discovery-driven culture, and we are thrilled to be a collaborating advisor in the development of the Forest Products Innovation Center.”
Hunt Forest Products (HFP) was founded in 1978 as a full-service wood products company. HFP manufactures plywood, lumber and other specialty wood products. Mike Walpole of Ruston has been chosen as the designer for this phase of the building construction.
Roseburg Enhances Executive Team
Roseburg named Matt Lawless as Vice President-General Counsel and Corporate Secretary. He joins the company’s Executive Team and will help set strategy and overall direction for the business.
“Matt is an accomplished legal strategist and litigator, and we are fortunate to have him on the team,” Roseburg President and CEO Grady Mulbery says. “He has shown a passion for the business and our industry, and a clear understanding of our strategic objectives. We look forward to his continued contribution to Roseburg’s growth and success.”
Lawless joined Roseburg in November 2019 as Assistant General Counsel. His scope of responsibility expanded in January 2022, when Stuart Gray moved out of the General Counsel role to become Chief Operating Officer for Roseburg.
“Matt has a keen legal mind and deep appreciation of Roseburg’s values and goals as a business,” Roseburg COO Gray adds. “His leadership and skillset have proven invaluable as we address the complex legal issues regarding our timberlands, operations, and ongoing work to expand our geographic footprint in North America.”
Before Roseburg, Lawless practiced law at Arnold Gallagher PC in Eugene, Ore.; and Jones Day in Cleveland, Ohio. He began his career at Howard, Stallings, From, Atkins, Angell & Davis PA in Raleigh, NC. He earned his law degree from the University of Memphis Cecil C.
Humphreys School of Law, and his bachelor’s degree from Washington and Lee University in Virginia.
Cal-Tex Purchases
and MiCROTEC have a long relationship, with the first Lucidyne Grade Mark Reader being installed in 1991. Over the years, these GMR systems have been upgraded to the latest version.
The Lucidyne scanner will be installed near the beginning of 2024. For more information about the Lucidyne scanner, MiCROTEC Ai, or QC Assist software, visit microtec.us.
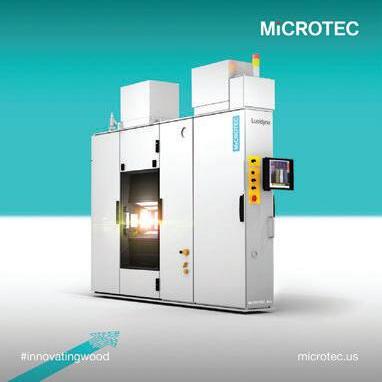
McDonough Acquires New Brunswick’s B.I.D.
proximity to the Trans-Canada Highway and various seaports, B.I.D. Canada has been a sought-after manufacturer in the coal, cement, potash, nickel, biomass and pulp and paper industries ing production processes, minimizing downtime, reducing trim loss, and increasing product consistency with the purchase of a MiCROTEC Lucidyne scanner for installation in its Nacogdoches, Texas facility.
The Lucidyne scanner, equipped with MiCROTEC Ai and the QC Assist quality control tool, offers precision and efficiency in wood processing and quality control, allowing Cal-Tex Lumber to get the most value and recovery out of their system.
Cal-Tex Lumber is committed to investing in the latest technology and processes to remain a leader in the wood processing industry. Cal-Tex Lumber
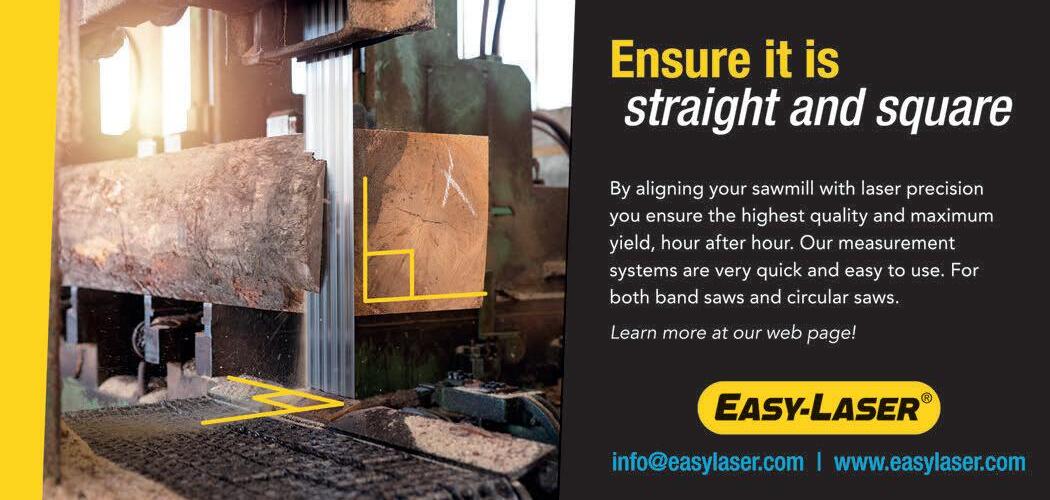
McDonough Manufacturing has acquired Woodstock, New Brunswickbased B.I.D. Canada Ltd. into the McDonough group of companies. This acquisition partners two of New Brunswick’s premiere manufacturing teams and facilities (McDonough expaneded operations to Mactaquac, New Brunswick in 2017), combining them with McDonough’s flagship location in Eau Claire, Wis. The transaction allows McDonough to increase production capacity, human resources, and product offerings.
“Increasing demand of our machinery has necessitated a further expansion to increase capacity and meet changing market needs,” McDonough stated.
Founded as Basic Industrial Design, B.I.D Canada Ltd. has more than 50 years of experience in the design and manufacturing of bulk material handling systems, making it one of North America’s leaders in the industry. Within close
This acquisition is part of McDonough’s business strategy to continue to offer the best machinery on the market, while employing teams of experts to service its customers. B.I.D. Canada will continue to operate in its facility in Woodstock, New Brunswick, retaining existing team members under the McDonough umbrella. The B.I.D. Canada location will remain focused on its existing customers and projects, while contributing to the production of McDonough sawmill machinery. The experience of the McDonough sales and marketing teams will allow McDonough to further expand B.I.D. Canada’s horizons across North America.
Hampton Gets Busy With The Bees
A Northwest timber company is studying how to support bees among trees. Hampton Lumber, a fourth-generation family business, is building pollinator habitats at its timber harvest sites throughout Oregon and Washington. “I love this project,” says Andony Melathopoulos, Oregon State University’s pollinator health expert. “It’s so innovative. They’re way out ahead of the rest of the industry in the West.” The project, says Melathopoulos, supports bumble bees, carpenter bees, mason bees and other pollinators.
The idea originated with David Hampton, an owner and board member of Hampton Lumber, after he attended a conference presentation about the decline of native pollinators. Hampton approached Jed Arnold, then the company’s stewardship and community outreach coordinator, about building pollinator habitat in timber stands.
Arnold began researching in 2016. He talked with pollination experts, including OSU researchers, who encouraged him to experiment with ecosystems and track what worked. In 2017, Arnold planted native seed to support pollinators. He also maintained woody debris piles and lightly disturbed topsoil for different bee species to use for nesting.
Each year, he experimented with different types of seed, elevation, planting techniques, timing and other factors. During the winter of 2019-2020, he ran a controlled experiment. In some plots, native flowers struggled to survive; in others, they thrived.
From his experiments, Arnold gleaned four key takeaways:
First, he learned that timing matters. Plots where he planted seed late in the fall or early in the winter—after birds had migrated but snow had not yet fallen—performed best.
Second, he discovered the best places to plant native seed are in the burn scars of slash piles at recently harvested sites. Logging generates woody debris that foresters often clump into slash piles and then burn. These piles can become rich soil for flowers.
Arnold says seeding burn scars is affordable and effective. Planting as little as two ounces of native seed in a 40foot-diameter burn scar can produce a carpet of wildflowers. In some sites, flowers are now naturally re-seeding.
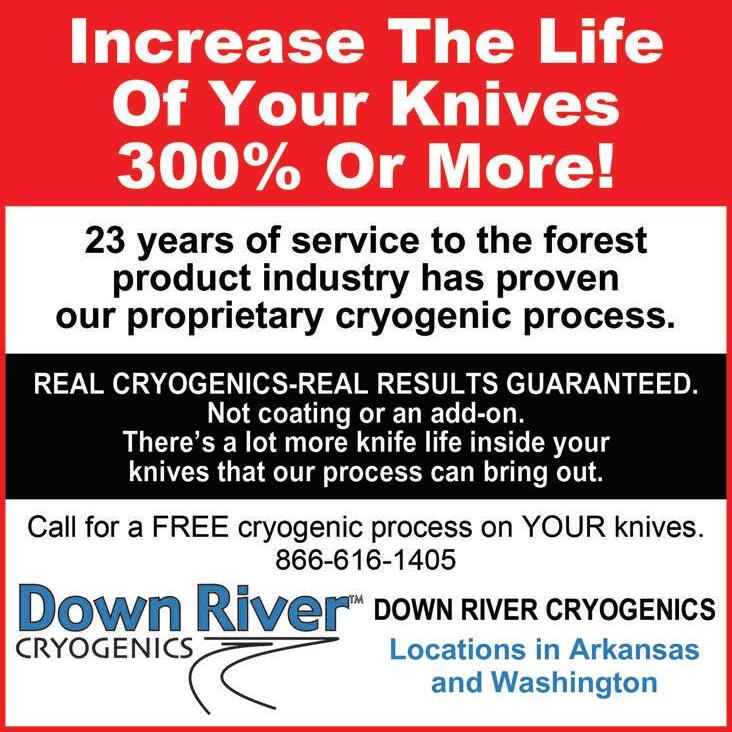
Third, Arnold learned that seed selection is important. He encourages foresters creating pollinator habitat to talk with an extension specialist or reputable seed company about which flowers are best suited to the terrain and microclimate.
Finally, he learned it is important to have an herbicide regimen that complements rather than disrupts the habitat.
In 2021, Arnold accepted a forestry job in Nevada and passed the project on to Lindsay Davis, Hampton Lumber’s new stewardship coordinator for the pollinator project. Davis is planning how to support bees for years to come.
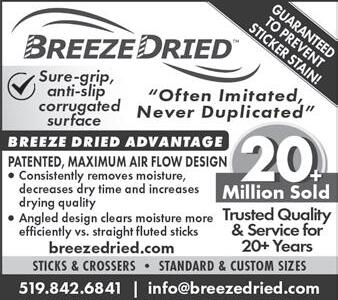
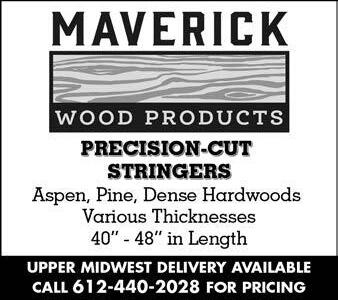
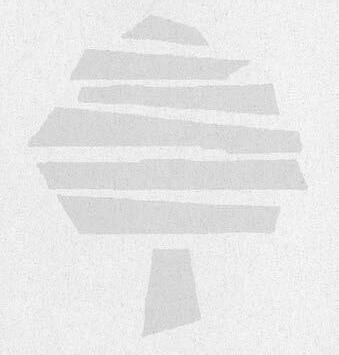
One of Davis’ goals is to create a plan—like “choreography for a dance”— so that when the canopy eventually closes over a unit, shading out the flowers, the bees can easily transition to a new unit a quarter of a mile away with a trail of plants bridging the sites.
Arnold and Davis say other foresters can replicate Hampton Lumber’s lowcost practices.
“I believe this is a technique that is very replicable,” Arnold says.
Davis agrees: “Whether you’re sitting on one acre or 100 acres, anyone can participate in this.”
Article as appeared on Hampton Lumber web site, written by Sierra McClain of Capital Press (www.capitalpress.com).

Hancock Lumber Expands Executive Team
Hancock Lumber, which operates four sawmills in Maine and New Hampshire, has expanded its executive team, adding a full-time Chief Financial Officer, Florian Knappe. Knappe joins the Home Office executive team, and will be focused on the financial, legal, technological and structural aspects of the company.

With Knappe’s arrival, Paul Wainman transitions from President and CFO to President and CEO. Kevin Hancock transitions from CEO and Chairman to Chairman.
Born in Germany, Knappe has an extensive geographical and financial background, having held several executive leadership roles in Europe and the U.S. Additionally, he has building products experience having been CFO for a Maine based deck manufacturer. Most recently he served as the Director of Finance for Maine Technical Source, serving surveyors, engineers, and commercial contractors.
“Florian’s arrival expands the capacity of our senior executive team from two people to three,” Hancock says. “This is an intentional investment designed to support the continued growth and expan- sion of our company.