
5 minute read
FRONTEND
John King Chains
What drives a debarker? A chosen method is using a heavy drive chain and, dependent on lumber production capacities, this can vary in chain size and selection.

We like to think of the debarker as the “mouth” of the lumber mill, where logs are fed into the machine. Therefore, it’s one of the most critical applications—if this equipment runs into problems, whole mill production can grind to a halt.
It is also very difficult to control or prevent overloading. Logs double the intended size can find their way into the process, adding extra strain on the drive and system. In the accompanying photo this is exactly what was experienced from newly installed equipment. A large drive chain was experiencing premature wear and stretch with links being removed weekly. They were utilizing a local machine shop to desperately weld up the links and pins. Chain manufacturers were turning away from this as it was not a common drive chain.
When John King Chains was called and asked if we could help, the immediate answer was “yes!” With our unique chosen specifications we were able to enhance the chain life by over a year. Some of the key specifications were as follows: uprated through hardened side plates for strength, but maintaining ductility. This is fundamental to resisting shock loading; through hardened pin followed by additional surface induction hardened casing. The combination allows for optimum material and heat treatment specifications that maximize the chain service life.
John King has a wealth of knowledge in chain selection. We can assist you with all applications whether it entails upgrades, problem solving and fault finding.
Linden
The Linden Quadrant Feeder singulates one stem at a time with simple mechanical design—and only two moving parts. It is easy to install and requires very little space with no assembly required as it ships in one piece. The fixed and movable sections act as two continuous dams to accumulate, unscramble and separate a deep pile of stems. As the moveable section singulates stems, it also sweeps the entire fixed section, constantly clearing the feed area of debris.
The constant pressure of stems against the solid face of the quadrant feeder aligns and straightens the flow. Dual tempo follower cylinders ensure accurate feedback for tailoring controls requirements. The quadrant feeder handles extremely long and very crooked stems up to 60 ft. long, 3-30 in., 4-40 in. and 5-50 in. diameter, with automatic operation where stems are deep piled and crisscrossed.
Another popular model is Liden’s Self-Cleaning Double Acting step feeder which cleans debris as it unscrambles and singulates logs. It never misses a log and feeds one at a time up to 50 cycles per minute. Options include even ending systems, laser gap control and mechanical electric drives that eliminate hydraulics. Models are available in sizes to suit log lengths from 8-24 ft. and log diameters from 3-30 in. The self-cleaning double-acting step feeder will out-perform all other log singulating systems and will significantly improve the performance of any log handling system feeding a production line.
Mebor
Mebor, one of the biggest European manufacturers of sawmilling machinery, offers a wide range of machinery for small, medium and bigger scale sawmills—from horizontal band saws to complete sawing lines, as well as the log debarking machine Mebor SLH 1200.
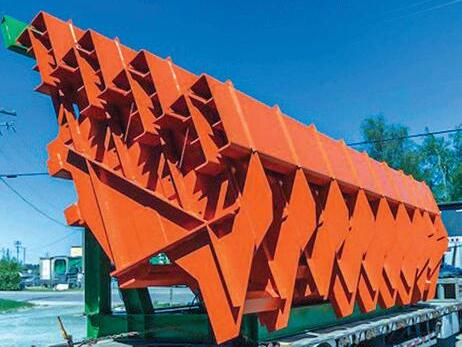
The heavy-duty, high-capacity machine features remote control and automatic operation, so constant presence of the operator is not required. The 12 t (27,000 lb.) machine is equipped with a scanner to recognize the position and diameter of the log. According to the log diameter the log is debarked automatically with suitable speed. After the log is debarked, the debarking head returns to its initial position automatically. The debarking process is therefore entirely automatic and does not require an operator to be present full time. In case of badshaped logs, manual intervention from the operator is possible. Large, toothed wheels provide good grip. The teeth on the wheels can also be replaced.
A 50 HP butt-end reducing unit is available as an option. The depth of the reduction is set automatically. Both operations, de- barking and butt-end reducing, can be executed simultaneously and work in fully automatic.
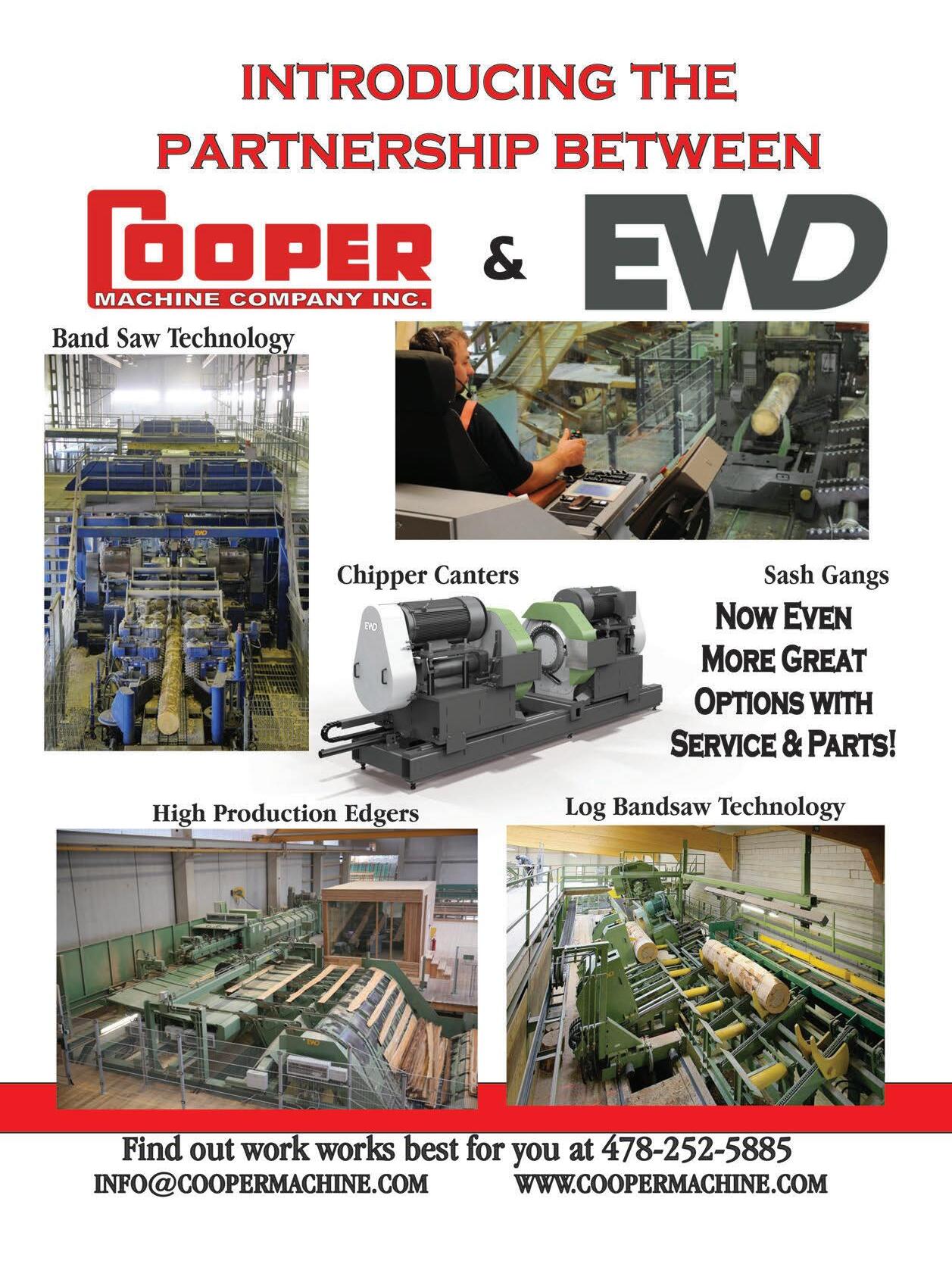
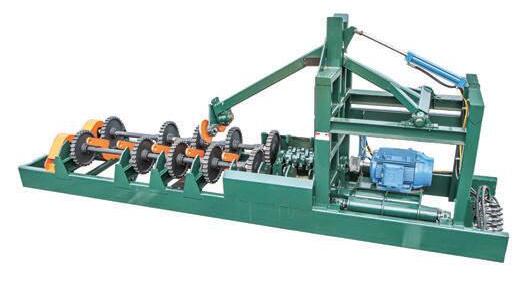
The Mebor SLH 1200 can process logs up to 1200 mm (4 ft.) in diameter. The debarking head with knives is powered by 30 HP motor. Hydraulic pressure and debarking depth can be adjusted. Wide range of additional options and equipment includes log loading decks, log sorting and cross cutting systems, metal detecting systems, waste conveyors and more.
All Mebor machines are equipped with high quality and reliable components from worldwide and renowned manufacturers.
Mellott
Mellott Manufacturing, known for its brand of log and lumber handling equipment, has been expanding its product line to offer more complete systems.
Mellott offers several models and sizes of rosserhead debarkers. Like the rest of the company, over the years Mellott debarkers have continued to evolve. The company’s most popular models are the LMR 48 in. and LMR 36 in. debarkers. Mellott debarkers are ruggedly built and are of heavy-duty construction. Features include cast steel alloy bull wheels, 3-7/16 in. shafts with urethane lined bearings and replaceable inserts, and remote lubrication system. The shock cord arrangement on the head and proportional joysticks allow smooth control to follow the contour of the log.
Mellott is now offering the Model 70E log flare butt reducer. It is designed and built with the same rugged quality as the LMR debarkers and all the Mellott product lines. The log flare butt reducer is designed to be added to a mill infeed system to reduce log handling problems and improve productivity. The butt reducer has an automatic control system with the option of a wireless remote control.
With ring debarkers gaining popularity due to their increased production, the Mellott LMR debarker as well as the log flare butt reducer are being used in conjunction with some ring debarkers. Installed ahead of the ring debarker the removal of butt flares and oversized knots provides a more efficient debarking system. Then the log is transferred through Mellott heavy duty log decks to infeed and outfeed log troughs specifically designed to work with the ring debarker. A belt conveyor with a MDI metal detector system is an option that can be added to the conveyor line. Mellott engineers design a custom layout for each project.
Whether your company is replacing a machine or putting in a new system, Mellott Manufacturing can supply quality, rugged equipment that is designed and built to provide reliable, durable performance. All Mellott equipment is designed and built by Mellott with an experienced staff of sales, mechanical and controls engineering along with a knowledgeable customer service team.
METAL DETECTORS INC.
The most advanced metal detector MDI has ever produced to date is the TWA5000-X. The new technology provides more consistent targeting of contaminants, better interference rejections due to environmental noise and product effect.
The TWA5000-X most important new feature is the highly successful MDI View-Link Remote Diagnostic Module, which allows MDI to remotely connect to your MDI metal detector to monitor, diagnose and calibrate your system. This optimizes your metal detector for maximum sensitivity and stability right in your own unique mill infeed.

Customers say: “It’s like having an MDI technician right in your mill, but only a phone call away!”
The TWA5000 can scan up to 60 in. diameter softwood or hardwood logs and comes with a three-year product warranty and a threeyear ViewLink remote service package. In addition, MDI offers unlimited lifetime telephone technical support for all of its products at no additional charge.
