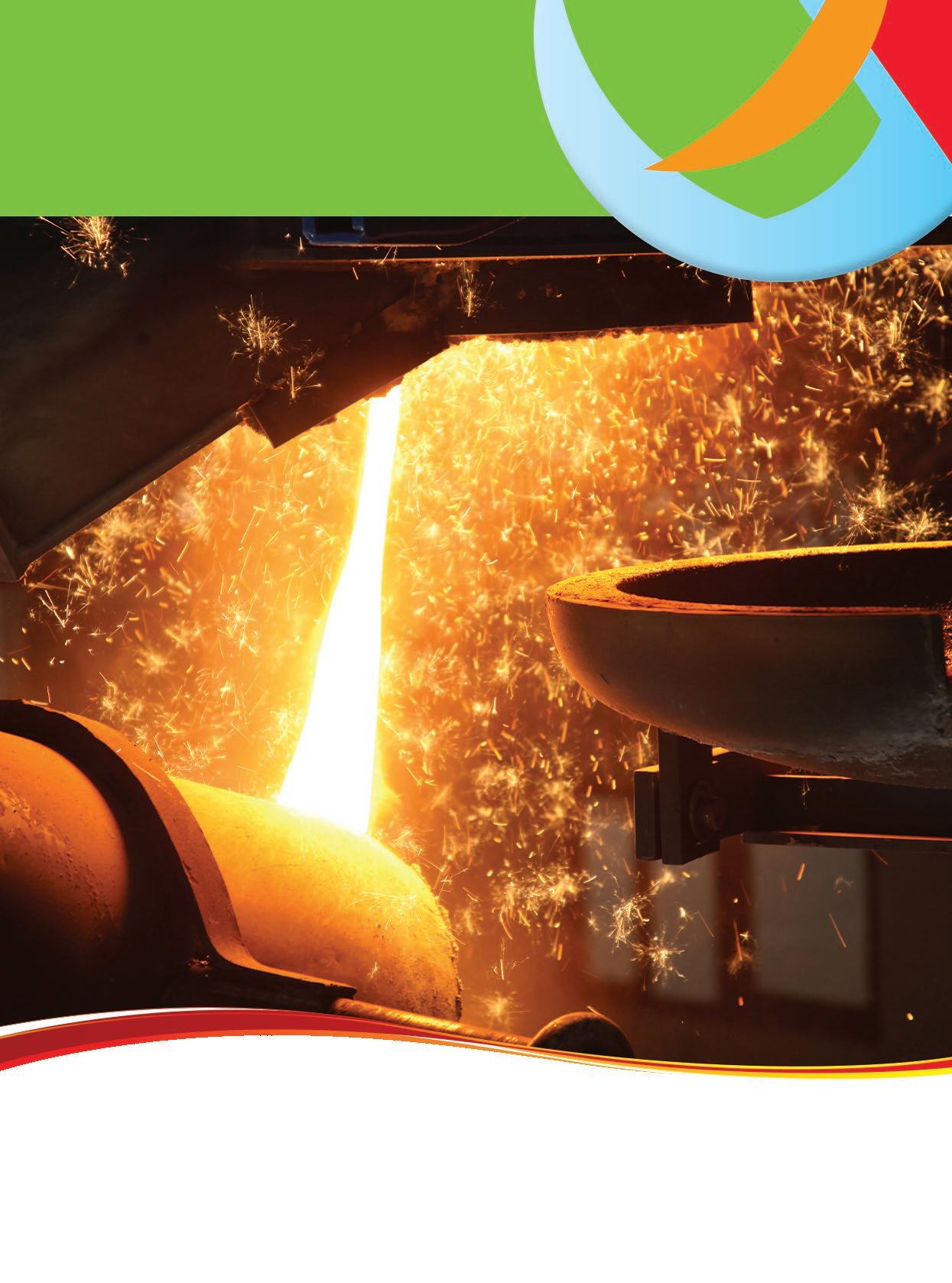

Welcome back to the first edition of ASA Connections 2023! Since our last connections at the end of last year, we’ve seen growth in new slag-related products and innovation with slag.
We begin this Connections at a fast pace, literally! Harsco has been busy contributing to racetrack resurfacing projects in Adelaide and Melbourne, which have been put on display in the Australian Supercars and Formula One World Championships.
We revisit our Formula One theme with ASA members Infrabuild, who have also played a critical role in the resurfacing of the Albert Park Grand Prix circuit.
Moving overseas into the UK and a newly enhanced steel slag solution is being developed in a strategic move to utilise the 62 million tonnes of steel slag going to landfill each year in the UK. This is being developed in a project called Mevocrete, in collaboration with Teesside University and industry partners.
Moving into Africa, and South Africa is steaming ahead with Slag! The South African concrete industry is leading the charge, championing the use of blast furnace slag, resulting in a substantial reduction in its clinker factor without compromising the quality of products.
From one continent to another, we then visit the USA where slag is literally improving road safety. Researchers reporting in the American Chemical Society (ACS) Omega have filled microcapsules with a slag-based mixture, designed to be added into asphalt before roads are paved, providing long-term snow melting capabilities in a real-world test.
Have you seen the new Cement 2 Zero project launched recently in the UK? It was officially launched in February as a pilot of the Cambridge
We then head back home to Penrith, which has become the first suburb in Australia to input a road that included recycled coffee cups in in construction. The fibres from the cups will aid in creating a road that is reported to be safer and much quieter than regular asphalt, and also accounts for a 24% reduction in carbon footprint.
Following this, we then explore how cement manufacturers can immediately reduce their carbon footprint. We’ll give you a sneaky hint, use slag!
We then explore three reasons how companies can utilise slag in a circular economy, exploring the benefits and reasons to use slag in the modern day.
Finally, we check out Australian Steel Mill Services’ new ABF222 product which has been recently launched. And guess what? They have another exciting product coming. You’ll have to check out the next ASA Connections for that one!
The Australasian (iron and steel) Slag Association would like to say a massive thank you to our members for their support and contributions to this edition of Connections. Connections would not be possible without our members, and we would love to report on your stories for the Connections to follow!
RESURFACING PROJECTS IN ADELAIDE AND MELBOURNE.
CAMP HILL, Pa. - December 8, 2022 - Harsco Corporation (NYSE: HSC), a global market leader providing environmental solutions for industrial and specialty by-products, announced that its Harsco Environmental division has supported two recent Australian racetrack resurfacing projects by providing electric arc furnace (EAF) aggregate derived from steel slag.
Starting in 2020, the Australian Grand Prix Corporation, iEDM and Formula 1 embarked on an extensive renovation project at the Albert Park Circuit, home to the Australian Grand Prix, including the first resurfacing of the racetrack since 1996. Working with Downer Group, Harsco tested asphalt mixes with different proportions of EAF aggregate material to meet the precise project specifications. Ultimately, Harsco provided 10mm and 14mm aggregate, and the asphalt mix improved grip and abrasion, resulting in more competitive racing conditions. The project was completed in advance of the Australian Grand Prix in April 2022.
Following the success of the Melbourne project, iEDM approached Harsco to provide EAF aggregate for a resurfacing project for the Adelaide Street Circuit, which was the site of the 2022 VALO Adelaide 500 Supercars race in December.
"We were very happy with the steel slag durability, affinity for bitumen and outstanding shape," said Michael Gardner, Associate Director, iEDM. "Both micro and macro texture were important metrics for the mix design, and we felt that inclusion of the steel slag assisted in both of those categories. Increased grip, abrasion and tyre degradation were all features within the return to racing at Albert Park in 2022.
"Together with our stakeholders, we have worked together to develop innovative EAF mixes that meet the precise specifications for these two racetrack projects," said Andrew Hayes, Site Manager, Harsco Environmental, Australia. "We are proud to be part of these projects which represent advancements in Australia Formula 1 and Supercar racing."
To learn more about Harsco Environmental, please visit website www.harsco-environmental.com or follow the company on Facebook, Twitter, or LinkedIn. To view Harsco's latest Environmental, Social and Governance Report (2020-2021), please visit www.harsco.com/ sustainability
Harsco's Environmental division is the largest and most comprehensive provider of onsite material processing and environmental services to the global metals industry, with operations at over 130 customer sites across more than 32 countries. The division is a technology partner to cleaner, more efficient metal production, providing customers with economically and environmentally viable solutions for the treatment and reuse of production by-products. Visit www. harsco-environmental.com to learn more.
Harsco Corporation (NYSE: HSC) is a global market leader providing environmental solutions for industrial and specialty waste streams, and innovative technologies for the rail sector. Based in Camp Hill, PA, the 12,000-employee company operates in more than 30 countries. Harsco's common stock is a component of the S&P SmallCap 600 Index and the Russell 2000 Index.
Additional information can be found at www.harsco.com
The concrete alternative will be developed in a significant $13.3m project called Mevocrete through a collaboration with academics from Teesside University and industry partners.
The project aims to create the solution from the by-products of the steel and chemical industries, resulting in a product that emits up to 85% less carbon dioxide when compared with Portland Cement. The project will focus on examining the entire supply-chain from the feedstock to end user.
Researchers from Teesside University will analyse the steel slag and its chemical composition, whilst measuring how efficient it is at sequestering carbon. The steel slag solution is patented by UKbased company Material Evolution Ltd
Teesside University won funding from Innovate UK to collaborate with Material Evolution to aid in scaling up its technology to create a full-scale on-site facility for cement production utilising steel slag waste at Teesworks.
Concrete is one of the biggest single emitters of carbon dioxide, equating to 8% of global greenhouse gas emissions. Therefore, it
is vital that new ways to decarbonise the construction and steel industry are found and utilised in a substantial way.
Associate Dean (Research and Innovation) Professor and co-lead of the Mevocrete project, David Hughes emphasised his gratitude in the collaboration explaining, "We are delighted to be able to help Material Evolution create a circular approach to dealing with the historic waste material from the region's steel production while simultaneously reducing the carbon footprint of the construction industry," he said.
Founder and CEO of Material Evolution, Dr Elizabeth Gilligan communicated the end results of the project explaining that they "will have a dedicated Mevocrete production line, delivering a truly carbon negative cement, which importantly, will have been independently tested and verified".
She went on to say that, "by utilising our ultra-low energy alkali-fusion technology, and using hyper-local waste streams, we can eliminate the need for Ordinary Portland Cement in concrete products. The industry has to have innovations like this if we are to meet our need to rapidly and radically decarbonise".
Electric arc furnace (EAF) slag produced during the steelmaking processes of ASA member, InfraBuild, has been used as part of an extensive renovation of Melbourne’s Albert Park racing surface.
Electric arc furnace (EAF) slag produced during the steelmaking processes of ASA member, InfraBuild, has been used as part of an extensive renovation of Melbourne’s Albert Park racing surface.
The EAF slag was showcased on the world stage yet again, after the same slag was used for the 2022 edition of the Melbourne Grand Prix, as well as being utilised as a track resurfacing material for the Adelaide Street Circuit which hosted a Supercars event in December.
The slag was deemed by project developers for the track resurfacing to have improved grip and tyre abrasion on the Melbourne circuit's surface and as a result, improved the quality of racing in 2022.
The use of the slag in a high-performance environment has showcased how much potential value EAF slag has in road-making and resurfacing projects, with this project showcasing the value in which the steelmaking by-product has.
The South African concrete industry is leading the charge, championing the use of blast furnace slag, resulting in a substantial reduction in its clinker factor without compromising the quality of products.
Blast furnace slag (BFS) is formed in a blast furnace with molten iron from iron ore in the reducing presence of heated air, coke and limestone. The resulting molten slag and iron, once removed from the furnace, are subject to further processing to form a crystalline aggregate or ground blast furnace slag (GBFS).
GBFS is an old practice, having been used in the manufacturingof cements since the second half of the 19th century. Back then, it was recommended to intergrind the blast furnace slag with the clinker. However, in the 1950's, companies pioneered the use of separately grinding granulated blast furnace slag (GGBFS) for the construction industry, giving rise to a more popular concept in the South African market. The availability of GGBFS is common place through the major industrialised economies.
By using blast furnace slag in concrete, not only does it reduce carbon emissions and minimise waste to landfill, it provides enhanced long-term strength and durability, advancing the built environment with high quality products that do not compromise the natural environment.
Want to know more about iron and steel slags in South Africa? Get in touch with the Slag Association of Southern Africa https://saosa. africa
According to the Association of Cementitious Material Producers (ACMP), the clinker substitution rose from 12% in 1990 to 23% in 2020, and a staggering 41% in 2009. A 60% rise is anticipated for 2030.
As a result, the industry has witnessed significant year-on-year reductions in emissions, showcasing how the beneficial use of slag can drive strong and coherent action towards achieving net zero.
SAOSA are a non-profit lobby and advocacy group focused on the recycling, repurposing and reuse of slag (stony waste matter separated from mineral commodities during mineral processing) as a reclaimed alternative construction and raw material for the much needed infrastructure development in Southern Africa.
Researchers reporting in the American Chemical Society (ACS) Omega have filled microcapsules with a slag-based mixture, designed to be added into asphalt before roads are paved, providing long-term snow melting capabilities in a real-world test.
Researchers have recently incorporated salt-storage systems into “anti-icing asphalt” to remove snow and prevent black ice from forming. However, these asphalt pavements use corrosive chloride-based salts and only release snow-melting substances for a few years.
The aim of this real-life test was to develop a longer-term, chloride-free additive to effectively melt and remove snow cover on winter roads. Blast furnace slag was used as a key ingredient to create a polymer solution which formed tiny microcapsules that were incorporated into the asphalt mixture.
A real-world pilot test of the anti-icing asphalt on the off-ramp of a highway showed that it melted snow that fell on the road, whereas traditional pavement required additional removal operations. Because the additive used waste products and could release salt for most of a road’s lifetime, the researchers say that is a practical and economic solution for wintertime snow and ice removal.
This American test is sure to become a pioneer for utilising slag in the road-making process worldwide, improving the safety of roads across the globe and particularly in cold climates where ice and snow are prevalent on roads.
Penrith, NSW has become the first suburb in Australia to input a road that included recycled coffee cups in in construction. The fibres from the cups will aid in creating a road that is reported to be safer and much quieter than regular asphalt, the road also accounts for a 24% reduction in carbon footprint.
The select sustainable asphalt is known as Pak-Pave and has been developed by State Asphalts NSW in close partnership with Closed Loop Environmental Solutions. Closed Loop managing director Rob Pascoe commented that this specific project has been 3 years in the making and that Pak-Pave is a substitute for a previously imported product made of crude oil from Germany.
The Pak-Pave roads pilot project is situated along a stretch of Jamison Road in South Penrith, NSW with a second project to be implemented shortly after on Swallow Drive in Erskine Park. Over 135,000 recycled paper cups / including coffee cups will be used in these two initiatives, accounting for 85% of the paper cups collected for recycling in the Penrith LGA in 2022.
Additionally, Pak-Pave roads will also incorporate 1.2 million glass stubbies along with reclaimed asphalt pavement and steel furnace slag. Collectively, the select materials will contribute to over 50% of all the materials used in the construction of the roadway.
Director of State Asphalts NSW John Kypreos has stated “It is exciting to be delivering a practical circular economy solution in partnership with Closed Loop, and we hope that other councils and state governments will start specifying Pak-Pave roads, both as a high-quality road surface and a product that uses a high
percentage of recycled materials.”
Penrith Mayor, Tricia Hitchen also commented that the Penrith council is proud to be leading the way to becoming a more sustainable circular economy and ensuring that our roads are environmentally friendly.
The Simply Cups initiative has been in operation for over 6 years as of 2023, and in a partnership with 7-Eleven to collect paper cups from around the country.
According to Pascoe, the Simply Cups campaign began six years ago with a collaboration with 7-Eleven to gather throwaway cups from all over the nation. He explained that many firms and small businesses are now becoming interested, and all they need to do to take part is install a dedicated collection tube for people to dispose of their cups in their office or store.
Individuals that wish to donate their paper cups can do so at nearby at over 630 7-Eleven stores across Australia.
Around 30 million paper cups have been collected in this way since the launch of Simply Cups, enabling recycling and preventing landfilling in order to promote a truly sustainable circular economy.
The Cement 2 Zero project, a pilot of the Cambridge Electric Cement (CEC) process, officially launched in the UK at the beginning of February.
A two-year funding of approximately 7 million Euros by the UK Research and Innovations (UKRI) has kick-started the project, which partners with entities such as the University of Cambridge and the Celsa Group.
This project revolves around the use of recycled concrete paste in the cement making process, which is utilising slag as a key part of the process. The recycled concrete paste replaces lime-flux in the steel recycling process. As the steel melts, slag is formed and in turn is used instead of clinker to make more cement.
The slag is being used as a primary supplementary cement material, and a point of interest in this project is to discover how higher levels of steel recycling in a process like this would affect slag’s usage as a supplementary cement material.
This process leads to the decarbonisation of the limestone step from conventional clinker production.
The use of slag as a key ingredient in this process of combining steel and cement recycling in a single process, in turn, led to the decarbonisation of the cement making process and created a more sustainable way of making cement.
The Cement 2 Zero project's two year trial has begun and will focus on scaling up production of the net-zero carbon cement.
A new report from The Rocky Mountain Institute states that there are ways in which the construction sector can act immediately and reduce industry carbon levels, despite the industry goal of eliminating all carbon in concrete by 2050.
Authors of the report, Radhika Lalit and Ben Skinner, say that Supplementary Cementitious Materials (SCM's) like slag and fly ash can be of use to the industry's goals of reducing carbon levels - because of the little to no emissions associated with slag and fly ash use.
Lalit states that by using these SCM products, manufacturers can immediately begin contributing to lower carbon levels in the industry by reducing the amount of concrete needed.
"Around the laying of the concrete, you can use less concrete in the first place. SCM's such as fly ash, slag, volcanic ash and calcined clays have little or no associated emissions and can be introduced into the cement blend to replace a portion of clinker", Lalit said.
"What gives us hope is the fact that there is a big rise in ambitions across the industry (to reduce emissions), where companies, corporations, real estate players, anybody who's constructing new buildings, new ports, new highways, new roads, is looking into these materials".
Skinner stated that "Historically the construction industry hasn't been incentivised to consider embodied carbon when creating our built environment. The focus has been on reducing costs, not carbon. Companies are hesitant to take on anything perceived as additional risk. With that being said, we are starting to see some great developments all across the value chain, and it's an exciting time in the construction space".
The report emphasises the need for a more comprehensive systems approach towards lowering carbon emissions, and that it has to be a combination of everything - from more efficiency in cement and concrete production through using SCM's, to utilising more efficient designs in construction.
Should the concrete industry effectively meet their goal of eliminating all carbon in concrete by 2050, SCM's such as slag and fly ash will be critical players in achieving the industry's goal.
The construction industry is one of the largest in the world, with cement and concrete being massive contributors to the industry's success. However the environmental costs of cement and concrete over the years, because of large carbon emissions, make the industry a large contributor to global emissions.
With global net-zero targets in place for 2050, research shows that steel slag may be a solution to the construction industry's emissions problems - amongst a range of other benefits. Here are three reasons why companies should be utilising slag in the modern day:
Biplob Pramanik of Melbourne's RMIT University states that the global steel making industry produces over 130 million tons of steel slag every single year, while the World Steel Association states that 15.7 million tons of this steel slag is produced in Europe alone, of which 11.5 million tons are recycled. Considering there is a high level of steel slag production currently taking place worldwide, the motivation levels behind recycling slag is gaining traction.
Because steel slag is so dense and hard, it is resistant to weathering and tear and can withstand more load and pressure than traditional aggregates like gravel. Australian scientists tested this and found that concrete with steel waste was 17% stronger than other concrete. Other researchers found that the volume of permeable pores decreased with a higher prevalence of steel slag in the cement, improving workability. Steel slag has a lower coefficient of thermal expansion than traditional materials, and as a result reduces shrinkage cracks in concrete structures.
In terms of sustainability and the construction industry's targets of net-zero carbon emissions by 2050, utilising slag is a nobrainer. Considering that industrial by-products like slag are highly contaminating, recycling the product and giving it new value is a fantastic way to contribute to a sustainable circular economy. Slag has been recently utilised in creating sustainable concrete paste and as a result has reduced the need for primary aggregate materials - resulting in fewer natural resources being needed for concrete production while reducing carbon emissions and maintaining outstanding physical qualities for the concrete.
Furthermore, steel slag concrete produces a series of benefits beyond environmental sustainability. For example, when the concrete is placed and cured, the steel slag particles become an integral part of the concrete mix and improve the density of the concrete - improving the strength and durability of the concrete whilst being better for the environment.
Because of the amount of slag being produced, as well as the major benefits of slag previously stated - the potential of slag's use in the construction industry is sky-high. Slag's multiple uses make it a versatile material. It is already being used as a fine and coarse aggregate for asphalt road mixes - with benefits on icy roads as slag roads have been found to have helped melt ice and make winter roads safer. In addition to this, slag is being used as a raw material for clinker, a ballast for railways and as a filling material for a wide range of excavations - not forgetting slag's use in concrete paste.
Slag's environmental benefits when being used for concrete have made it an attractive material to use, and has increasingly been recognised for its environmental properties - likely meaning that it will be expanding into other uses in the future such as being used as a suitable material for high-strength concrete structures like bridge decks and skyscrapers.
All-in-all, slag is being recognised for its promising qualities as engineers and architects aim for healthier and better buildings.
ASMS has recently launched ABF222 to market - a new Densely Graded Subbase (DGS) product, meeting increasing demand for DGS and Densely Graded Base (DGB) materials due to the number and size of civil projects underway in greater Sydney.
ABF222 is an unbound material which behaves similar to a lightly bound material once placed thanks to BFS (Blast Furnace Slag)’s self-cementing characteristics. ABF222 is a blended blast furnace slag product, making use of several underutilised products ASMS produces from processing BlueScope Port Kembla’s blast furnace Slag.
After initial product design and proving trials in the field, ABF222 has seen keen interest with ASMS supplying several projects, most notably to date being 26,000T going into a project at Wetherill Park being constructed by Iron built Infrastructure where it will serve as a subbase for concrete slabs and warehousing.
ASMS are responsible for marketing approximately 1.2 million tonnes of slag-based products to industry. ASMS specifically markets to the following industries:
• Ready Mixed Concrete
• Concrete Building Products
• Asphalt
• Cement Manufacture
• Road Building
• Agriculture
To provide for these markets ASMS directly produces products at the BlueScope Steel furnaces or at one of one of their specialised facilities. ASMS create various materials using two different slag streams:
1. Granulated slag, concrete aggregates, and blended goods including road bases and masonry products are all made from blast furnace slag.
2. ASMS also develop asphalt aggregates, road base materials, specialised fill application materials, and agricultural goods from BOS slag or steel furnace slag.
Connections is produced twice a year for the benefit of ASA members and before each publication is drafted, an email is sent to all members urging them to contribute their stories.
The types of content we are looking for include:
NEW DEVELOPMENTS AND TECHNOLOGIES
NEW PROJECTS
NEW EMPLOYEES
We also have a Member Profile section, which is open to all member companies for contributions on behalf of the business in general, or a specific employee. So if you have an idea or content that you think might make an interesting article, get in contact with the Association today:
publications@asa-inc.org.au
SUBSCRIBE TO www.asa-inc.org.au
Views expressed in Connections newsletter do not necessarily reflect the opinion of the Australasian Slag Association. All contributions are welcomed, though the publisher reserves the right to decline or edit for style grammar, length and legal reasons.