INDUSTRY EXPERT ARTICLES
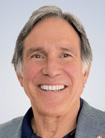
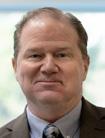

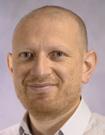
Spring 2023
Annual Supplement: Building Energy / MEP

Spring 2023
Annual Supplement: Building Energy / MEP
Mechanical, electrical, and plumbing (MEP) systems are critical components for a new, state-of-the-art lab or cGMPready building. How these systems are integrated into the core and shell lays the groundwork for future tenants to come in and design a space that meets their distinct needs. Developing a quality base building MEP program early on to guide the design, purchasing, and construction efforts is crucial to creating the kind of cutting-edge life science facility companies will want to move into.
A life science facility’s overall design determines the location of the MEP systems. Main fire protection, electrical, and plumbing services enter below-grade and are distributed throughout the building core based on the desired program. The most efficient use of space is typically through shafts and risers that are adjacent to the elevators and stairwells. Building Information Modeling (BIM)
helps establish construction tolerances and alignment relationships between the intended structure, utilities, and finishes. Developing a 3D model by combining the structural intent from the architectural design drawings with subcontractor shop drawings allows identification and correction of any potential fit and location issues well before construction begins. Finding the right balance for the desired core and shell program stems from understanding the tenant market needs. Developers are partnering with construction managers like Erland to determine the best way to meet their pro forma while ensuring the base building is as attractive as possible. Determining what falls under the core and shell versus what would be better suited for the fit-out upfront minimizes rework and allows developers and tenants to initiate a lease and occupy a space much sooner.
Generally, a developer would own the MEP infrastructure required to provide a building that meets standard code requirements and is deemed safe for occupancy. However, there has been a recent shift where some developers are providing bare-bones HVAC, choosing to only support very minimal heating and cooling loads in more of a temporary service capacity before a tenant agreement. We do still see some developers choosing
to provide systems large enough to support the whole facility and future fit-out work upfront. Others will include some of the wants and needs of a specific tenant(s) based on experience, location, or desired industry.
During the preconstruction process, we recommend procuring major components as far ahead of the scheduled installation date as possible. Ongoing supply chain and escalation issues are industry-wide, with excessive lead times on major components like switchgears, generators, and HVAC equipment that range from eight months to a full year away from the order release to delivery. As part of this trend, we are making efforts to procure major components as far ahead of the scheduled installation
date as possible. Material lead times are being coordinated with best practices for construction schedules based on information provided by manufacturers. Creative “workarounds” are now the norm when approaching most projects regarding these schedule unknowns and shortcomings. In some cases, the equipment has even been shipped “loose” for fabrication onsite or completion at subcontractor fabrication facilities to expedite its availability.
A quality base building MEP program calculated at the beginning of a project brings value to the client and prevents issues that could be detrimental to the budget and schedule.
George Waddell is senior MEP project manager at Erland Construction, Inc.
The process starts with a thorough assessment of the building’s energy use, identifying areas to reduce consumption. It looks at the intersections between water, mechanical systems, building envelope, and products used. It explores incentive programs to encourage policies that drive sustainable behavior.
by Carl Salas and Alan VanagsClients across a wide variety of sectors have improved the sustainability of their buildings through green retrofits. But once the basics have been implemented, what needs to happen to achieve a deeper level of energy savings and sustainability?
What Exactly is a Deep Retrofit?
A deep retrofit is a comprehensive upgrade of a building’s systems and components, with the aim of dramatically improving energy efficiency, reducing maintenance issues, and reducing carbon emissions. While a “green retrofit” might focus on a singular strategy – like a lighting upgrade – a deep retrofit involves a holistic look at the connections between energy, water, products, and operations. By applying multiple strategies together, the results become exponential.
Consider that people go annually for a checkup. The doctor will look at heart rate, blood pressure and weight, and will run basic blood tests. There will be questions designed to uncover symptoms of an underlying health issue. A similar approach works for buildings and facilities.
Simple tests and questions can uncover opportunities for substantial energy savings and more sustainable use of resources. Salas O’Brien finds that many times a minimal investment surprises owners with the capacity to simplify, save, and decrease carbon emissions.
Each building is unique, formed by details like orientation, piping, how equipment was installed – the variables are exponential. And while computer modeling can inform strategy, retrofits require “boots on the ground” going through the physical details of the building to form the assessment.
Addressing multiple strategies together
Salas O’Brien enhances the human experience through engineering and technical consulting. Our diverse and integrated team is engineered for impact, understanding projects holistically and delivering cohesive solutions that are reliable, resilient, versatile, and efficient.
salasobrien.com
can generate efficiencies that lead to cost savings, carbon footprint reduction, decreased equipment requirements, and the ability to repurpose existing space.
For example, improving the building envelope by enhancing insulation and air tightness is a common strategy that can reduce heat loss in winter and heat gain in summer, thus decreasing energy consumption. Using next-generation climate control systems, such as lowtemperature water systems, closed-loop hydronic systems, or geo-exchange systems, can also save energy and water usage, leading to significant cost savings.
Greywater reuse is another effective strategy that involves collecting and treating greywater from sinks, showers, and other sources for non-potable purposes like irrigation and toilet flushing. This reduces the amount of fresh water required and relieves the burden on local sewage treatment facilities.
Heat recovery systems are also an excellent way to reduce energy consumption by recovering wasted heat from cooling processes and sanitary systems. Combining renewable energy sources like wind and solar power with electrification through power purchase agreements and installing renewable local energy systems can significantly reduce carbon footprints and improve energy efficiency. Energy
management systems and SCADA systems can monitor and control energy usage, helping to save energy and reduce costs.
There are financial and tax incentives to help owners undertake deep retrofits. Grants, loans, rebates, and other programs are available. For example, some state and local governments offer grants and low-interest loans for energy efficiency upgrades. The federal government offers incentives through programs like the Energy Policy Act and the Inflation Reduction Act.
Tax incentives can also provide significant savings for building owners. For example, the Energy Efficient Commercial Buildings Tax Deduction, also known as Section 179D, provides tax deductions of up to $1.80 per square foot for energy-efficient upgrades in commercial buildings. This includes deep retrofits that result in a 50% reduction in energy consumption compared to the building’s baseline energy use.
Deep retrofits return profits in the form of energy savings, resilience, rebates, and better environments for people, along with sustainable practices to protect our planet.
Carl Salas, PE is co-founder, and Alan Vanags, PE, LEED AP is principal, at Salas O’Brien.
This article originally appeared at EvolveMEP.com.
Being an MEP contractor is not always a walk in the park. Many variables are at stake in an MEP project and contractors need to be prepared for any, or all of them, to go awry. Here are some of the top challenges faced by MEP contractors and potential solutions to overcome them:
Coordination issues: MEP systems are complex and need to be well-coordinated to ensure smooth installation and operation. Coordination issues may arise due to design changes, communication problems, or inadequate planning.
Solution: Adopting BIM technology can help MEP contractors to coordinate and visualize the installation of MEP systems. BIM enables all stakeholders to work collaboratively and share project information in real-time, minimizing the risk of coordination issues.
Skilled labor shortage: Finding skilled workers with adequate training and experience in MEP work is a persistent problem. The construction industry has seen a shortage of skilled
workers in recent years, and MEP work requires specialized skills that are hard to come by.
Solution: BIM can help solve the problem of the skilled labor shortage in MEP work by making the construction process more efficient by reducing the need for specialized skills. BIM programs also provide better visibility and communication across teams to enable contractors to plan and coordinate the installation of MEP systems with greater accuracy and efficiency. In short, you can do more with fewer people on staff.
Material waste: MEP systems often involve significant amounts of materials, and any wasted materials can lead to increased project costs and reduced profitability.
Solution: With better models, BIM also provides MEP contractors with accurate measurements and quantities of materials needed for the project, reducing the risk of ordering too many materials and increasing the chance of reducing the amount of leftover materials at the end of the project. Some programs like EVOLVE can also use data from previous
continued to page 6
Bennington, VT – Fitzemeyer & Tocci (F&T) announced it is providing MEP/FP and construction administration services for a Southwestern Vermont Medical Center (SVMC) project, which includes the complete renovation and expansion of the emergency department, main entrance, and other key areas. The project is currently under construction.
SVMC is investing $25.8 million to enhance its facilities and services, with a focus on improving patient safety, privacy, and infection prevention. F&T is working closely with SVMC, Lavallee Brensinger Architects, and PC Construction to ensure a smooth and efficient project delivery.
low-acuity conditions, an expanded mental health crisis care area, and increased telehealth connectivity with Dartmouth-Hitchcock Health. The extended emergency department will have 18 treatment spaces to further enhance patient care. In addition, the project includes renovations to the main entrance, cafe, outpatient registration area, Imaging Department waiting area, and phlebotomy and laboratory upgrades.
The existing emergency department was in need of a renovation and expansion, as it was designed over 40 years ago to handle 14,000 patient visits per year. Today, it serves nearly 25,000 annually. The project will double the size of the department and feature vertical treatment areas for highly efficient treatment of
The MEP/FP design by F&T includes flexible negative pressure zones, arranged in pods, that can accommodate current or future pandemic concerns and maximize staff and patient safety, as well as flexible equipment that can adjust flow to accommodate the phasing. All available methods of existing condition verification were incorporated into the design: visual investigation, SD scanning and modeling, and existing (old) drawing research. Additionally, the hospital’s hot water heating plant system is upgraded to facilitate re-heat conversion from steam to chilled water, not only serving the project but also improving the overall hospital heating systems.
The emergency department is remaining operational during the expansion, which requires effective coordination and communication from project team members throughout construction. The project is scheduled to be completed in early 2024.
This article originally appeared at MassPlumbers.com.
A topping off ceremony was held in December for the Josiah Quincy Upper School project under construction on Washington Street in Chinatown. On track to open in September 2024, the 6-story, 185,000sf building will welcome 650 students in grades 6-12. Turner Construction is the general contractor for the $170 million job, and Greater Boston Plumbing Contractors Association (GBPCA) contractor PJ Kennedy & Sons is handling the plumbing and HVAC.
On location at the construction site, Gene Moscone, PJ Kennedy’s foreman for the project, showed an oil/water separator his crew had installed adjacent to a sump pump at the base of the building’s elevators. “I’ve never done a separator like that inside a building before,” said Moscone, who has been a Plumbers & Gasfitters Local 12 member for more than 30 years. “It’s unusual.”
Bob Collins, project manager with PJ Kennedy, explained that the project also includes an in-ground rainwater infiltration system. It will distribute water from the roof’s drain storm piping system. “We installed approximately 2,000 feet of
12-inch PVC Schedule 40 pipe,” he said. “We pre-drilled out the pipes’ holes at our prefab shop in Dorchester.”
Located in a densely populated neighborhood, the compact, one-acre site could not accommodate any outdoor space at the ground level. Designed by HMFH Architects, the building will include an outdoor classroom, activity complex, and gardens on its roof where
students and faculty will be able to get some fresh air. Other amenities will include an auditorium, a black box theater, media center, cafeteria, and gymnasium.
The school’s designers also considered the site’s close proximity to the Southeast Expressway and the Mass. Pike, and the highways’ impact on the building’s indoor environment. The project includes an advanced displacement ventilation system with high-performance filters and rooftop air handlers to maximize the air quality.
According to Mike Pirrello, superintendent with Turner Construction, the building has some other unique design aspects that make it a challenging build. “For a shorter building, it has complex steel,” he says. “There’s a big cantilever at the auditorium and another at the gymnasium with a 3-story truss supporting them.”
There are structural constraints imposed by the way the truss system works in the building, Pirrello explains. The crew will be pouring concrete from the first floor through the third-floor level,
and then waiting until the building is fully erected to pour the roof concrete. “The roof concrete will engage the truss system within the building,” he says. “Then we can go back and load the other floors.”
A long time in development, plans for the Josiah Quincy school go back to Mayor Tom Menino and have spanned three administrations, Moscone notes. It is one of the biggest ground-up public buildings that the city has erected in many years.
continued from page 4
projects to create more accurate BOMs and minimize wasted materials.
Safety risks: MEP work involves several safety hazards, including electrical shock, falls, and exposure to hazardous materials.
Solution: BIM programs can identify potential safety hazards in MEP systems through 3D modeling and simulation. Specialized software will detect clashes and interference between MEP systems and other building systems, reducing
the risk of accidents due to improperly installed or conflicting systems. This can prevent costly rework, delays, and potential safety hazards.
By implementing BIM, MEP contractors can overcome these challenges and improve their efficiency, profitability, and overall success in the construction industry.
Marina Lucier is a marketing specialist for Evolve MEP.
IBEW Local 103 and NECA Greater Boston contractors are proud to maintain the safest worksites in the region, and the world. Our professionals are the best-trained and most efficient in the industry, and the safety of our workers, our clients, and our communities is our top priority.
Today and always, we are committed to raising the standards of the construction industry by standing as a strong advocate for working people, and responsible employers, across the region.
ThePowerProfessionals.com
Worcester, MA – Altieri Sebor Wieber, LLC (Altieri) announced it provided comprehensive MEPF engineering design services for the Prior Performing Arts Center at College of the Holy Cross, completed at the end of 2022. The 84,000sf hub for multi-disciplinary learning and creative collaboration serves as a campus and community focal point, providing facilities for both the fine and performing arts.
The $110 million project, awarded to a design team led by Diller Scofidio + Renfro with Perry Dean Rogers Partners Architects in 2015, includes Luth Concert Hall, a 400-seat multipurpose proscenium theatre; Boroughs Theatre, a 200-seat flexible black box performance space; Booth Media Lab, multimedia space with state-of-the-art sound recording, sound editing, video editing, film, lighting and set design; support spaces such as scene and costume shops; the Iris and B. Gerald Cantor Art Gallery; and collaborative workspaces, multipurpose rehearsal and gathering spaces, a lobby, and cafe. At the core of these program elements is the “Beehive,” a high-tech atrium completely open to circulation balconies on all four floors, designed to highlight the college’s vision and design team’s intention to encourage collaboration among students from all academic disciplines. The project is pursuing LEED Silver certification.
“At Altieri, we have particular interest in theatre and performing arts projects, the design challenges they present and their ability to enrich the people and communities they serve,” said Michael Freliech, Altieri’s principal in charge for the Holy Cross project. “For engineering building systems design, a deep understanding of theatre design and acoustics is critical to the success of a bold and aspirational program such as Prior Performing Arts Center. A highly collaborative design team allowed us to anticipate the range of program requirements, work together to achieve best solutions, and deliver systems that met a wide variety of critical program requirements including low noise criteria, vibration isolation, and humidification and dehumidification sequences to maintain a healthy environment for performances, musical instruments, and artwork.”
The project team also included OLIN, landscape architect; Nitsch Engineering, civil engineer; Silman, structural engineer; Fisher Dachs Associates, theater planning; Jaffe Holden, acoustics; Transsolar, sustainability; and Tillotson Design Associates, lighting.
This article originally appeared at MassPlumbers.com.
When Saint Theresa’s Catholic School, which was founded in 1923, wanted to update its aging bathrooms, Plumbers & Gasfitters Local 12 and the Greater Boston Plumbing Contractors Association (GBPCA) answered the call. The union’s members provided the labor for the remodeling project, and the contractor group donated the fixtures and the materials.
According to Rick Carter, director of Local 12’s training center, the crew for the project was mostly first-year apprentices. As he explains, it’s great to be able to help a needy organization, but the project was also a wonderful learning experience for the new apprentices. Because they were retrofitting and demoing the existing bathrooms, it offered a rare opportunity for them to see and work with older fixtures, piping, and materials.
“The great thing about doing a job where we are donating our time is that there is a lot less stress. The deadlines are often less strict,” Carter notes. “The journeymen aren’t under the gun either, so they can take the time to really watch over the apprentices and make it educational.”
The project included the replacement
of 16 toilets and two sinks in the girls’ bathroom as well as eight toilets, eight urinals, and two sinks in the boys’ bathroom. The work was done off hours on Saturdays. Business agents Jim Vaughan and Frank Amato helped oversee the project.
The Somerville school serves students in pre-K through grade 8. Its diverse mix of students are from Somerville, Medford, Cambridge, Everett, Arlington, and other
We have New England’s largest fleet of mobile boilers. Steam, hot water, domestic hot water—you’re covered. Need one that fires oil or natural gas? We have those too. Our dependable mobile boilers, available in many sizes, will get you up and running with minimal disruption.
Call our 24/7 emergency hotline: 800.777.1629
www.gtwilkinson.com
surrounding communities. Saint Theresa’s also operates an after-school program.
“This was a great opportunity to give
Boston – Fuss & O’Neill has welcomed two new project managers, Joseph Saint Germain, PE, and George Baberkov, to its Boston Mechanical, Electrical, and Plumbing (MEP) team. These new team members expand the firm’s MEP offerings and enhance its fire protection (FP) offerings throughout Massachusetts and New England.
Saint Germain is an electrical engineer who has worked in both the private and public sector on Massachusetts construction projects for more than 10 years. He specializes in code-compliant electrical designs, arc flash analysis, coordination studies, and renewable energy designs.
The firm’s representatives say that Baberkov’s and Saint Germain’s talents pair well with Fuss & O’Neill’s established MEP team, which assists New England clients by providing mechanical, electrical, and plumbing design services for new and renovation projects for educational facilities, water/wastewater treatment plants, public safety complexes, and housing.
Baberkov has more than 18 years of experience in healthcare- and laboratory -related plumbing and FP system designs. His expertise is in medical gas systems and specialty FP systems within public and private industries.
Kevin Sullivan, PE, LEED AP, vice president and office manager for the Boston and Quincy offices, said, “I have always been proud of the MEP projects we’ve completed throughout Massachusetts. With the addition of George and Joseph, we are able to expand our MEP/FP offerings to better service our clients and communities and meet their energy needs. I am excited about the potential of this team.”
Nashua, NH – DECCO, Inc. has announced its newest service, 3D Laser Scanning & Virtual Design Solutions. The company’s new 3D Laser Scanning & Virtual Design Solutions supports projects with 3D scanned models and point clouds to integrate piping models and skidded systems into generated virtual environments supporting Building Information Models (BIM). These 3D scanned models illustrate how DECCO’s custom skid models fit within a facility. The 3D model verifies field tie-in requirements, facilitating installation and minimizing schedule impacts.
DECCO’s Virtual Design Solutions support:
• Site scanning presents accurate data on floor levelness/flatness and wall plumpness.
• Clash detection, prefabrication, and mitigation.
• Comprehensive data analysis.
• Piping system design.
• Concrete scanning and infrastructure assessments to locate and document existing conduits, utilities, rebar, and other components.
• Scanned data can be exported into preferred software such as Autodesk, Navisworks, REVIT, Rhino 3D, and SolidWorks.
“The use of advanced and virtual technologies in construction continues to progress at lightning speed,” said Dan
3D scanned models illustrate how DECCO’s custom skid models fit within a facility. Manzi, project engineer. “Capturing accurate as-built conditions for documentation, design, construction, renovation,
fabrication, utility installations and facility modifications supports cost-saving and time-saving options.”
Submitted by Arden
Providence College (PC) sits on a 105acre campus in Providence, R.I. The campus has evolved and expanded to meet its enrollment needs, now over 4,000 students. In 2013, PC began the Campus Transformation Initiative, a plan to create a more unified, sustainable, and functional campus.
Beneath the recently renovated sections of the school are 12-inch chilled water lines, which provide cooling to several buildings on the lower campus. With additional buildings set to come online in two years, these lines and the central chiller plant are close to capacity.
One solution discussed by PC and its longstanding mechanical and controls contractors, Arden Engineering
Constructors and Earthwise Energy Technologies, involved adding more capacity with the installation of a new chiller. However, this would require increasing the size of the chilled water line for higher flows. An alternative option was presented to reduce chilled water demand in the existing buildings, increasing capacity to accommodate growth. Recognizing this as the pragmatic solution, Arden/Earthwise and PC turned to the Belimo Energy Valve.
Project Overview and Motivation
Reducing chilled water demand on the lower campus would create spare capacity in the chiller plant and reduce water flow through the main line. In doing so, PC could forgo the installation of a fourth chiller (Currently, three 1000-ton chillers run parallel.), and the main line would not have to be excavated and replaced.
With approximately 20 energy valves already installed across the campus, Arden/Earthwise and PC had established a close working relationship with Belimo and were familiar with their range of products.
“Our plan was to pick sections of
the lower campus where demand for chilled water was highest,” said Paul Carter, general manager at Earthwise. “Some technology in these buildings was outdated and due for an upgrade. Having seen the capabilities of the Energy Valve, we were confident it would generate the flow savings we were looking for.”
The Energy Valve is an IoT-enabled, pressure-independent valve that measures and manages coil energy by using an embedded ultrasonic flow meter, along with supply and return water temperature sensors. Its built-in Power Control and Belimo Delta T Manager logic monitors coil performance and optimizes available energy of the coil by maintaining Delta T.
A key advantage of the Energy Valve is that the Delta T setpoint can be matched to the design Delta T of the coil. As the temperature sensors start to realize a lower differential temperature across the coil, the valve begins to close and flow decreases, allowing more efficient heat exchange and elimination of overflow. When Delta T begins to stabilize, the valve increases flow back through the coil, thus maintaining optimal heat transfer.
The Energy Valve comes with a suite of cloud-based services that can benchmark coil performance, analyze glycol concentration, store energy data, send alerts, and commission for optimal performance. In addition to the standard analog signal and feedback wiring, it communicates its data to the Building Management System (BMS) via BACnet MS/TP or BACnet IP as well as Modbus RTU and Modbus TCP/IP. The built-in web server collects up to 13 months of data that can be downloaded to external tools for further optimization.
After careful evaluation, the decision was made to install 22 additional Energy Valves across the lower campus, ranging from ¾” to 2 ½”.
The retrofit project is set for completion
this spring, after which Arden/Earthwise and PC will collect data to quantify flow reductions. The reduction in pumping will lead to decreased electricity usage, which aligns with the college’s commitment to increase energy efficiency and improve environmental, social, and governance (ESG) performance.
“While future construction of new buildings may necessitate installation of a new chiller, the Energy Valves will allow us to push that project out and significantly increase efficiency of the existing system,” said Matt Basile, principal engineer I for Arden. “Every Energy Valve we install gets a data connection to the cloud and the campus’s central BMS. This provides visibility down to the individual air handlers, which is crucial for troubleshooting and identifying further opportunities for efficiency gains. It is now standard practice to flat spec the Energy Valve for any chilled water device over 10 gallons.”
“Belimo has a long-standing relationship with Arden/Earthwise and PC and is proud to be part of a project that will help the college achieve its goal of creating a more efficient and sustainable campus,” said PJ Qvarnstrom, retrofit business manager at Belimo.
In addition to the lower campus chilled water line, two other main lines come from the central chiller plant and provide cooling to separate sections of the campus. With additional buildings planned for these sections, the lower campus retrofit will serve as a demonstration project.
“Belimo’s track record of providing superior products and service has fortified our professional relationship and made them a preferred supplier to the college,” added Steve Basile, supervisor of engineering at PC. “We look forward to leveraging innovative products like the Energy Valve for future efficiency of our campus.”
In January, the Federal Register provided an updated document highlighting energy conservation standards regarding boilers and minimum efficiencies. The new boiler energy conservation standards were set by the U.S. Department of Energy (DOE) to improve boiler efficiency, reduce energy consumption and limit emissions.
The information states that the DOE reviewed Commercial Packaged Boilers (CPB) standards and concluded that updating the existing 10 CPB equipment classes to 12 equipment classes is necessary. Updated guidelines include the following:
• Draft type is no longer a criterion for equipment class.
• “Very large” commercial packaged
boilers will have separate equipment classes.
Eliminating draft type as a feature of equipment class consolidated the original four draft-specific equipment classes into two non-draft specific equipment classes; while separating “very large” commercial packaged boilers into their own equipment classes adds an additional four classes.
With these new equipment classes comes more stringent standards for eight of the 12 equipment classes (including all classes except for the new “very large” CPB classes). The table clarifies the updated standards for all equipment listed, including prescribed minimum thermal efficiencies or combustion efficiencies as well as compliance dates.
The benefits of energy conservation for
boilers include reduced energy costs, lower gas emissions, improved energy efficiency and a longer lifespan for the boiler. These are great benefits, but updating and replacing equipment that complies with new standards may present a challenge.
Currently there is no deadline to replace boiler room equipment that is in use, but as this outdated equipment begins to fail, facilities will need to plan on how to replace their old equipment with something that meets the updated standards.
“This is going to require proper planning, well in advance of equipment failure. There are still extensive supply chain issues across the industry and new equipment is unavailable. Manufacturers are in the process of figuring out how to replace current equipment. Their older models no longer meet the energy
efficiency act standards and they have to consider how to produce viable options for replacement. Customers will also have to consider the cost of updating venting to match the new boiler equipment. When installing a new condensing boiler, venting needs to be replaced with polypropylene or stainless-steel materials to meet modern codes,” said Jay Higgins, sales engineer, The Wilkinson Companies. As options and solutions become available, The Wilkinson Companies can help keep you informed and provide recommendations for your facility. Contact our sales department at 800.777.1629 with questions or to find out about available options.
Elaina Schlumper is marketing communications specialist at The Wilkinson Companies.
Manufacturers are in the process of figuring out how to replace current equipment. Their older models no longer meet the energy efficiency act standards and they have to consider how to produce viable options for replacement.
The reason is that high water flow density is necessary in the design of the sprinkler systems in such warehouses, which is similar to the need for high water flow on electric battery fires.
With the market for electric vehicles projected to grow from 2.5 million units in 2020 to 31.1 million units in 2030, concerns about public safety related to their lithium-ion batteries have also increased. The problem arises when a short circuit occurs in these batteries. The heat from the short circuit makes the battery’s internal temperature rise to the point where a chemical reaction can start and spread to the adjacent cells, known as a “thermal runaway,” which is difficult to stop.
Battery fires also release toxic gases that can threaten first responders and building occupants. These fires are difficult to extinguish and even frequently reignite. Tesla itself warns that a battery fire can require up to 3,000 gallons of water for full suppression, which can take up to 24 hours. It has even been proposed to let the battery burn while protecting adjacent areas from further exposure. When
multiple vehicles are housed in enclosed spaces like parking garages, the likelihood of this risk increases significantly due to the multiplication of the fire load.
Throughout the past century, sprinkler systems have been a reliable and effective fire protection feature. While many states mandate sprinkler installation, the National Fire Protection Association’s (NFPA) code, known as NFPA-13, is the U.S. standard that has been continually updated and provides the design criteria for the required sprinkler flow to extinguish or control fires. However, until the most recent edition of NFPA-13, published in 2022, there had been no design criteria for sprinkler flow that would be required
to extinguish fires caused by electrical vehicles inside of facilities like public garages, where many of these vehicles are stored. The NFPA is now conducting research to investigate the storage of electric vehicles inside parking structures to determine the required sprinkler flow that would help lower the risk for first responders and others.
As a result of this design challenge, transitional approaches have been developed to apply existing fire suppression concepts and approved design flow rates to structures housing electric vehicles. The most common approach has been to consider the fire risk to be similar to a warehouse used for storing plastic.
This analogy with plastic warehouses also stems from the fact that today’s vehicles are made of more plastic than ever before and that sprinklers have proven effective in controlling fires in plastic warehouses. NFPA-13 has design criteria that provide water protection for warehouses that store plastic, listing three different types of sprinkler heads that are to be used. The design criteria for those sprinkler heads can be used to develop an appropriate engineering design that can fit with the needs of sprinkler systems in garage structures that store electric vehicles. It is difficult to know the adequate water density for the sprinkler system before a NFPA standard for such sprinkler systems is published. The answer to this design challenge will be based on actual large-scale fire tests. In the meantime, as large a water flow as possible should be considered necessary to help extinguish electric battery fires and prevent further spreading.