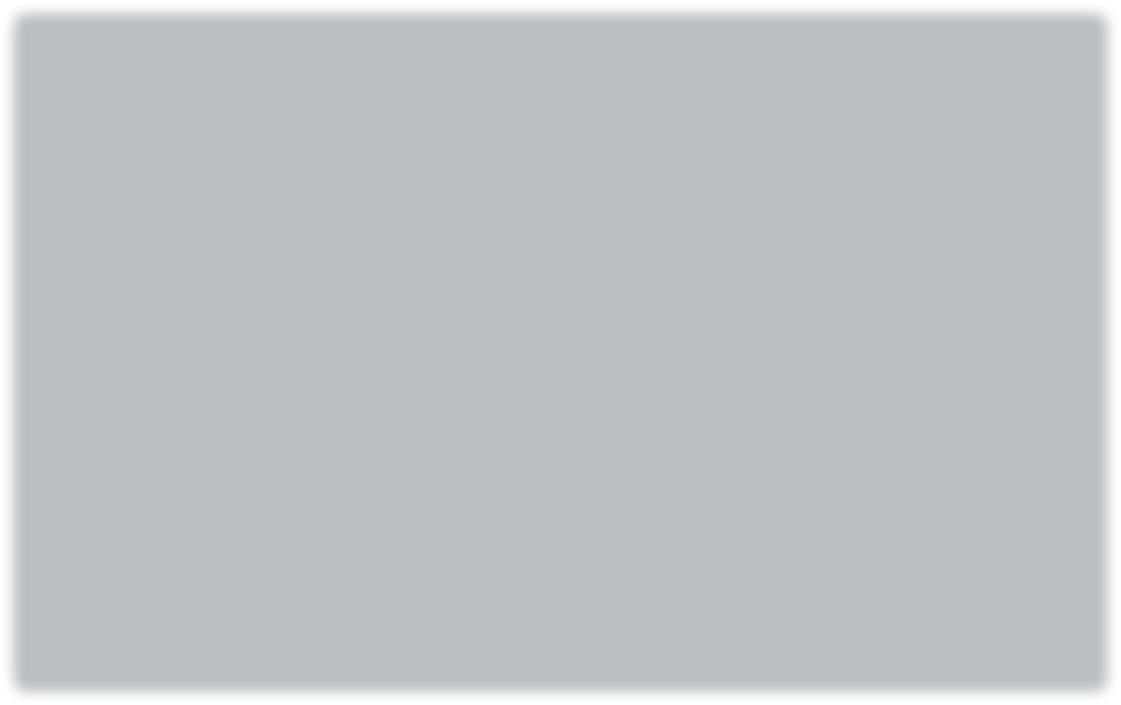
2 minute read
THE NEW GENERATION OF DIP COATING
The combination of pretreatment and coating
The Surface Treatment global business unit of the Coatings division within BASF, operating under the Chemetall brand, has developed an innovative coating technology. It is used successfully by selected customers in the metal fi nishing sector.
The new technology is a corrosion protection system designed for coating steel. This revolutionary process combines pretreatment and paint in one single step. In contrast to conventional corrosion protection systems, the technology provides excellent and complete coating on both external and internal surfaces including cut edges. Internal threads are excellently coated with an even layer. Corrosion tests (field tests) so far show that creepage from scribe after 504h neutral salt spray testing was not more than 3 mm. Depending on the steel quality also good results after 720h have been reached.
Functionality
This innovative corrosion protection coating works without electricity in the immersion baths. The thickness of the coated layer is approximately 20 µm. Curing time ranges between 20 to 25 minutes at about 200 degrees Celsius peak metal temperature. The unique coating technology meets the coaters’ market expectations including process cost and energy savings. Based on in-field evaluations during the pilot phase, we can assure process stability, bath output and reproducibility. After a primary degreasing or degreasing/pickling phase, the new anticorrosive coating process takes place by immersing a component in a single tank, where the new coating technology is deposited on the metallic product in about one minute for 20 µm coating thickness. For the near future it is planned to make the coating also available for galvanized steel.
Savings
Due to the technology’s unique formulation of combining pretreatment and paint, multiple process cost savings are achieved. The process, which is applicable on steel, does not require an electrical current.
Accordingly, electricity costs can be reduced as the cooling of the baths contents is not required and the temperature control of the coating bath is no longer necessary. Additionally, also the contents of the coating tank only need to be circulated slightly during production. As a result, the process footprint is significantly decreased with fewer baths used, water and electricity consumptions.

Advantages
The major advantage of the new technology is its high capacity of covering edges, such as cut edges and internal surfaces offering 100% complete coating. In addition, the new coating technology enables the significant reduction in both process costs and energy costs.
Results
Process optimization and sustainability (i.e. with regard to water and energy consumption) are key R&D drivers in the designing and development of Chemetall technologies. That is why technologies incorporate the entire cost structure of customers’ processes rather than limiting to the individual parameters, e.g. chemical prices per square meters. The development of individualized solutions for customers are tailored to their specific business needs. By reducing production and equipment costs while enhancing quality, efficiencies and sustainability, this new technology opens a new era offering opportunities in coating steel. Learn more about our innovative coating technology! Telephone: 01908 649333/ 01908 361800 Email: chemetall.ukinfo@basf.com Visit: www.chemetall.com
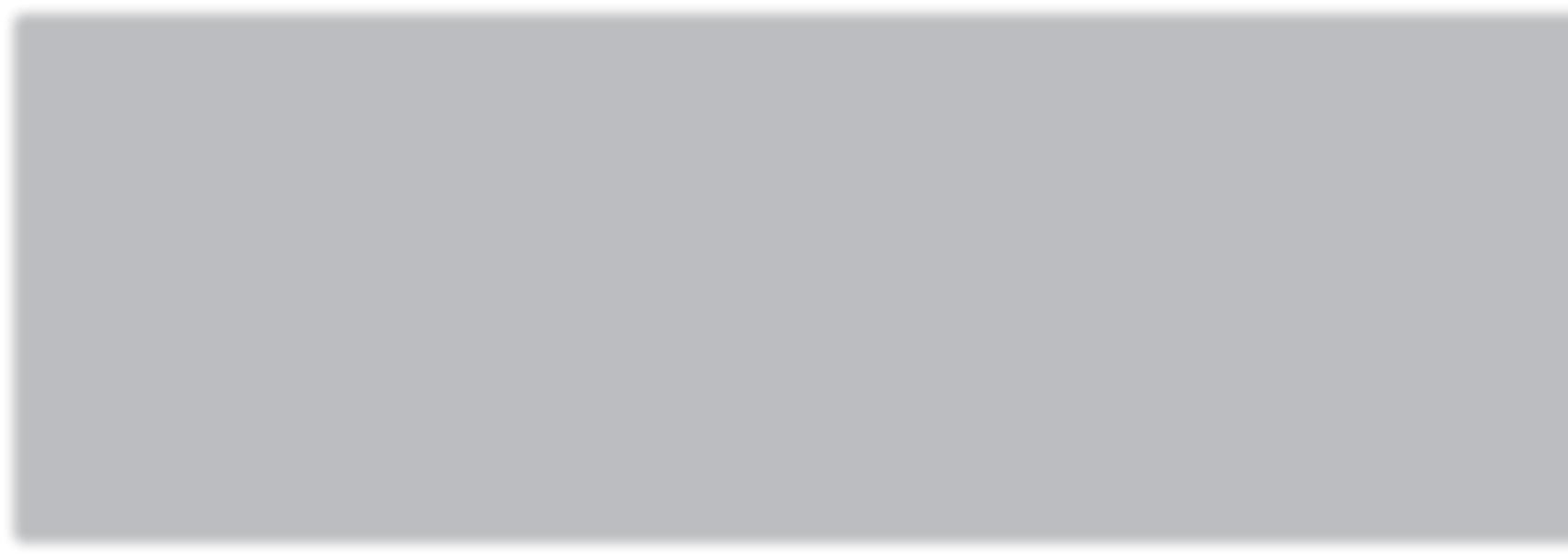
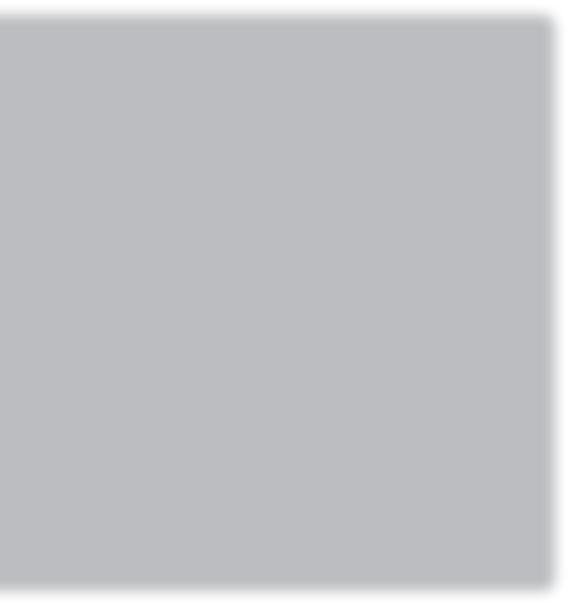
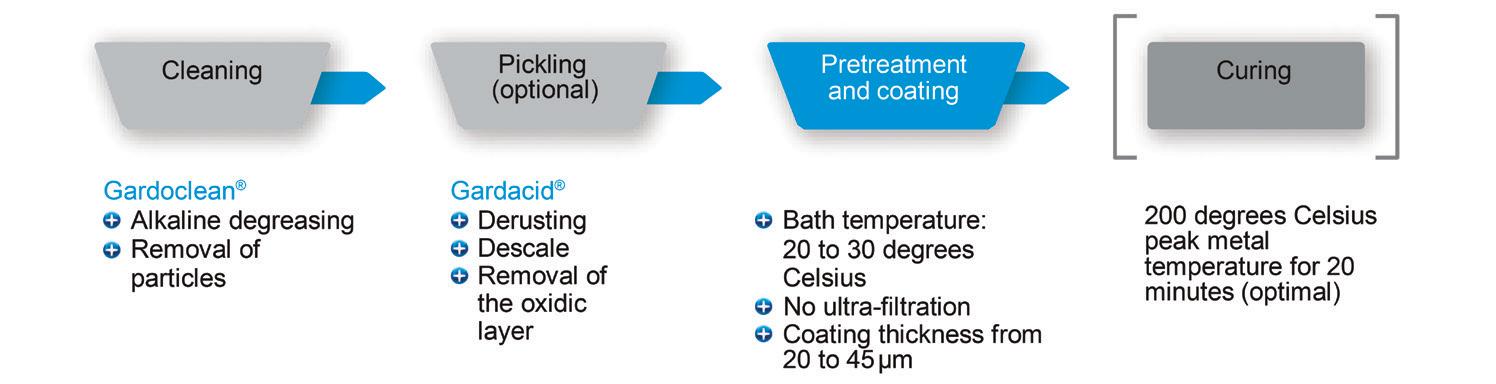