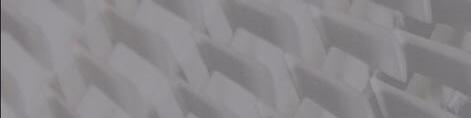
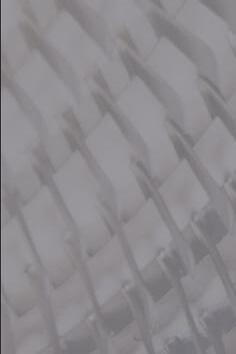
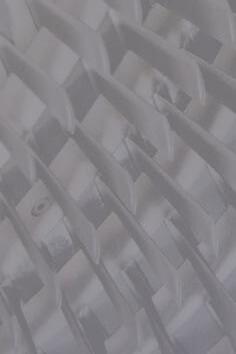
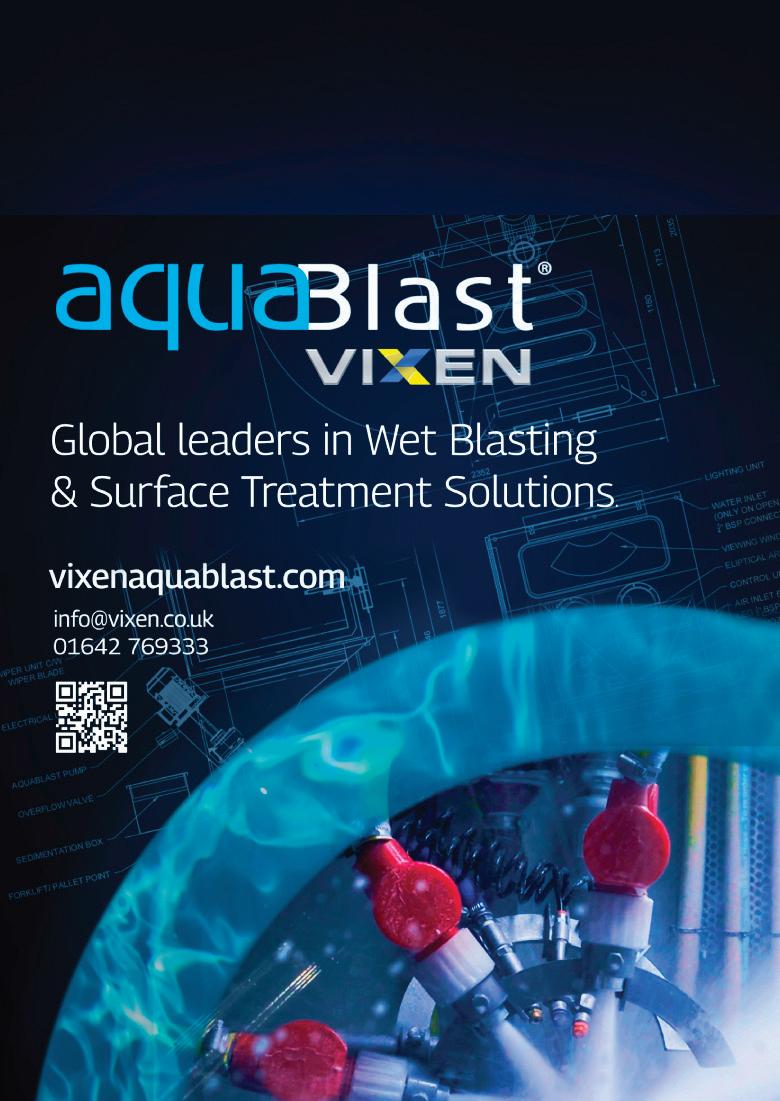
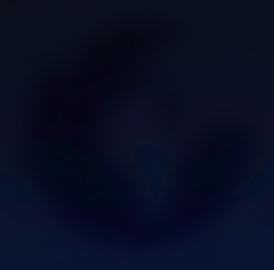

Measure the adhesion of coatings to metal, wood, concrete and more
n Impact and scratch resistant color Touch Screen display with keypad
n Wirelessly connect the PosiTest AT-A to your smart device using our free app
n Record the results as pass/fail and the nature of fracture cohesive, adhesive and glue failures
MANAGING DIRECTOR & ADVERTISEMENT DIRECTOR
Nigel Bean
t: +44 (0) 1442 826826
e: nigelbean1@aol.com nigelbean@surfaceworld.com
EDITOR & GRAPHIC DESIGNER
Jane Soones
e: janesoones@aol.com janesoones@surfaceworld.com
CIRCULATION & SUBSCRIPTION DEPARTMENT
Sheena Burrus e: sheenaburrus@hillmedia.com
EXHIBITION ORGANISER
Sheena Burrus e: sheenaburrus@hillmedia.com
Hill Media Ltd, Marash House 2-5 Brook Street, Tring, Hertfordshire HP23 5ED, United Kingdom.
The Surface World magazine is published 12 times a year by Hill Media Ltd. Although every effort is made to ensure the accuracy and reliability of material published in Surface World, Hill Media Ltd and its agents accept no responsibility for the veracity of claims made by contributors, manufacturers or advertisers. Copyright for all material published in this journal remains with Hill Media Ltd and its agents. © Hill Media Ltd – 2024 ISSN 1757-367X
All the major UK & Ireland architectural powder coaters are either licenced QUALICOAT members or in the process of approval. With coating specifications now requiring QUALICOAT, should you not be looking to join?
COMPANY SPOTLIGHT LEADING THE FUTURE OF ROBOTIC BLASTING. 2
QUALICOAT UK & IRELAND
INSTITUTE OF MATERIALS FINISHING
JOIN US AS WE CELEBRATE 100 YEARS. 10
BRITISH COATINGS FEDERATION
BCF CEO TOM BOWTELL WINS PRESTIGIOUS AWARD FOR OUTSTANDING LEADERSHIP OF THE UK COATINGS INDUSTRY. 14
BCF WELCOMES GOVERNMENT’S INDUSTRIAL STRATEGY GREEN PAPER: SEES IMPORTANT ROLE FOR UK COATINGS SECTOR IN ITS DELIVERY 16
SURFACE WORLD 2025 The Vital Role of Trade Shows in the Surface Finishing Industry: A FOCUS ON SURFACE WORLD.
SUSTAINABLE
SURFACE PREPARATION, DEGREASING & CLEANING
THE
EUROPE UPGRADE COMPONENT CLEANING
OVERVIEW OF SURFACE PRE-TREATMENT PROCESS WITH VERA GROUP. 54
SURFACEPREP UK HIGHLIGHTS HIRE DIVISION AND HOW IT’S SUPPORTING INDUSTRY. 56
PRETREATMENT, SURFACE PREPARATION, DEGREASING AND CLEANING WITH VIXEN.
Quality assurance by monitoring ultrasound frequency and power FINAL CLEANING PROCESS FOR LENS SYSTEMS FOR MEDICAL ENDOSCOPES.
Shot peening machine meets demands for excellent results and high throughput: FULLY AUTOMATIC SHOT PEENING OF GEAR PARTS FOR E-VEHICLES.
PAINT & POWDER
Paint applicator used outside the automotive industry for the first time PAN-DUR PAINTS REFRIGERATION EQUIPMENT WITH DÜRR’S ECOPAINTJET – WITHOUT THE
58
62
66
Blastman Robotics has been a global leader in industrial blast cleaning since the beginning. Our robotic systems are used in many industries worldwide, making blasting safer, faster, and more efficient. From the beginning in the 1980s, Blastman Robotics has developed into an expert in robotic blast cleaning by offering customer solutions to fit their specific needs, whether it is a turnkey solution or retrofitting existing facilities.
Today, Blastman Robotics is recognised as a robotic blast cleaning technology leader. One of the main reasons for our success is that we design robots specifically for blast cleaning, instead of modifying standard industrial robots. This makes the machines much more durable and reliable in the harsh conditions of blasting rooms.
Another strength of Blastman Robotics is its ability to provide custom solutions. Every customer has different needs, and we work closely with them to design robots tailored to the job. Whether it’s cleaning large structures or smaller components, Blastman can provide a solution that works.
We have also developed our own offline programming tool called “Blastman Studio” where customers create programs based on their 3D models. Of course, robots come with the possibility to use methods like teach-in or point-to-point programming, depending on their needs. This flexibility helps ensure that our robots are not only highly effective but also user-friendly.
In addition, the robots can be programmed to automatically clean workpieces after blasting, using compressed air to remove dust and abrasive. This makes the process even more efficient and allows the blasting room to be ready for the next job.
One of the biggest advantages of robotic blast cleaning is that it improves safety for workers. Manual blast cleaning can be dangerous, exposing workers to dust, noise, and physical strain. By using robots, companies can remove workers from the blasting room and control the process from a distance. This reduces health risks and creates a safer working environment.
Robotic blast cleaning is also much more efficient than manual blasting. Robots can reach an efficiency of up to 200m2/h. This saves time, reduces energy use, and lowers labor costs. Robots also don’t get tired, meaning they can work continuously at high performance without breaks. This makes the entire process more cost-effective for the customer.
Our robots have been deployed by Alstom in Derby, UK, to clean passenger coaches, helping them maintain the high-quality standards expected in the rail industry.
Blastman systems have been instrumental for Swire in Aberdeen, Scotland, where they are utilised for
blasting containers, offering both efficiency and safety for their operations.
In Ireland companies such as Liebherr in Killarney, Ireland, have experienced these benefits firsthand, using our robots for crane component blasting, where continuous operation without breaks has increased their overall productivity.
At Blastman Robotics, we’re not just focused on safety and efficiency— we’re also embracing the future with digital technology. Our fully automated blastrooms now include smart digital controls that allow real-time monitoring, easy adjustments, and preventive maintenance activities. By linking these systems to manufacturing execution systems (MES), customers can better manage
their blasting processes and maximise their investment.
Our latest innovation is Robot Blastroom 4.0. This new system brings all parts of the blasting process together into one advanced solution. Key features include:
Unified Control System:
This system allows full control of the blasting process through one interface. It includes self-monitoring, troubleshooting, predictive maintenance, and easy connection to customer systems (MES).
Advanced Use of Data:
The system collects and analyzes data to optimise performance, reduce maintenance needs, and ensure cost efficiency. Data related to energy and abrasive consumption, machine condition, and maintenance are monitored and reported.
Abrasive Handling:
The system ensures a stable abrasive mix with automatic refills and monitoring. This results in less consumption, reduced wear on parts, and lower costs.
Ventilation:
Optimized ventilation with energysaving modes ensures dust removal and clean air while maintaining efficiency through smart controls.
Maintenance-Free Scraper Floor:
Our heavy-duty scraper floor is designed for minimal wear, providing long-lasting durability and energy savings.
Room Interior:
The design is optimised for both robot and manual operations, reducing maintenance costs and improving efficiency. Robot operations focus on durability, while manual operations focus on visibility and accessibility.
Overall, the Robot Blastroom 4.0 is our way of providing a safer work environment, reduced manual labor, and increased overall production efficiency.
Blastman Robotics has always been committed to improving its technology and customer service. We invest heavily in research and development to keep our robots at the top of the blast cleaning technology. Over the years, we have fine-tuned the designs and continue to make improvements based on customer feedback and technological advancements.
We value a long-term relationship with our customers. Each project is the start of a long-lasting partnership. Blastman provides ongoing support, including maintenance services and spare parts, to ensure that our robots continue to perform at a high level. This commitment to customer satisfaction has been key to Blastman’s success over the years.
As more industries embrace automation, Blastman Robotics is
well-positioned to lead the way in robotic blast cleaning.
We are focused on today’s needs and the future. As the demand for automation continues to grow, the company is ready to meet the challenge with its advanced robotic systems and commitment to continuous improvement.
With decades of experience and a clear vision for the future, Blastman Robotics will remain a key player in industrial automation, helping industries around the globe transition to safer, more efficient blast cleaning.
Tuomas Heikonen Sales Manager Blastman Robotics Ltd
Email: tuomas.heikonen@blastman.fi Visit: www.blastman.com
SIEBEC UK Ltd, Stafford +44 (0) 1785 227700 sales@siebec.co.uk www.siebec.co.uk
L SERIES | Medium flow rate filter
P SERIES | Ultra-high flow rate filter
A SERIES | Mechanical seals pump
M SERIES | Magnetic drive pump T SERIES | Vertical pump
By Chris Mansfield - QUALICOAT Chair
As the name suggests, an architectural powder coating to be used in coastal applications, but what does this additional endorsement mean for QUALICOAT licensed applicators?
An architectural powder coating finish relies on its ability to adhere to the aluminium substrate. If there is no ‘key’ to adhere to, as is the case for untreated aluminium, the powder coating is prone to chipping or flaking off in over time. Powder coating is porous at the molecular level and a coating on an untreated aluminium substrate, subject to weathering, will continue to oxidise under the coating. So, no matter the quality or thickness of the powder coating that is applied, it will not offer the anticipated life expectancy. Crucially, a thin ‘conversion coating’ on the base metal, which is part of the pretreatment process, offers the vital seal the metal surface and a key for the powder coating to adhere to.
The surface of extruded fenestration aluminium also carries contaminants from the extrusion process which, if left on the surface of the aluminium, will reduce the performance of the ‘conversation coating’. Removing these contaminants from the extrusion is part of the pretreatment process undertaken by either dipping or spraying an acid or alkaline solution which etches the surface of the aluminium removing a minimum of 1g/ sm of aluminium. Without this surface etch potential corrosion could form around the contaminants on the aluminium substrate once coating has been completed. Given that the pretreatment process is undertaken correctly, in accordance with the QUALICOAT Specification, architectural powder coated products will offer an extensive life expectancy in most locations. The pretreatment process is actively monitored by
members of the Association and third party inspected by IFO, QUALICOAT UK & Ireland’s independent test house.
Introduced in 2008, QUALICOAT also offer a ‘Seaside’ class of powder coating where the minimum removal of aluminium surface is increased to 2g/sm using a dip or spray process of either an acid or a combination acid/ alkaline etch. This deeper etch removes more contaminants and therefore offers a more robust pretreatment for areas where atmospheres carry corrosive salts (chlorides) and other aggressive pollutants.
QUALICOAT licensed applicators who wish to offer ‘Seaside’ class coatings need to apply for an additional licence. The applicator needs to demonstrate that they can remove the 2g/sm by process and monitoring, plus the applicator must offer a coated ‘Seaside’ sample for an additional filiform corrosion test carried out in the IFO laboratory. Licensed coaters who are licensed to offer ‘Seaside Class’ are clearly identified on the Associations website.
Filiform corrosion is a spider like blistering that creeps under the powder coating and runs along the aluminium grain boundaries. A deeper acid or alkaline etching removes more trace elements from these areas making the grain boundaries more resistant to corrosion. Statistically, with this greater etch of 2g/sm, filiform resistance is increased significantly. The following pretreatment conversion coating can then be applied using any of the QUALICOAT approved systems.
Another method of increasing resistance to filiform corrosion is by using a ‘pre-anodisation’ process, sometimes referred to as PREOX or Flash Anodising. A more expensive pretreatment, this thin anodising film of just 4-8 µm (microns) totally removes all the grain boundaries, so there are no places where filiform corrosion may take hold, consequently the protection rate is statistically increased to 100%. Licensed applicators may now source preanodised profiles from other licensed plants so that they may take advantage of the increased level of protection that this process can offer.
Released in early 2024 QUALICOAT released the Technical Information Sheet No.4, ’Recommendations for Corrosion protection’. This document offers specifiers more detailed guidance on the recommended pretreatment system to specify for various “Corrosivity Categories” according to ISO 18768-1:2022 Table 1 and ISO 9223:2012 Table C.1. Whilst it is still strongly recommended that specifiers continue to seek guidance from a QUALICOAT licensed powder coater or powder manufacturer when specifying finishes, the guide offers an insight as to the levels of protection
offered when specifying QUALICOAT architectural powder coating. These various pretreatments and etch requirements can make it confusing what to specify and this is why the Technical Information Sheet has been produced by the Association to offer advice and guidance to specifiers. The Technical Information Sheet also offers guidance when specifying QUALICOAT 3.0. This specification controls further trace elements in the aluminium that can cause issues, which is often present in recycled aluminium. Controlling the quality of the extruded aluminium therefore offers additional life expectancy of the pretreatment system and the adhesion of the powder coating.
The Technical Information Sheet offers a simple chart that allows specifiers to choose all pretreatment options for a given exposure category. It is freely available to download from the Association website. It is still strongly recommended that guidance is requested from a QUALICOAT licence holder when specifying coatings in harsher environments.
Technically, the QUALICOAT standard is the most robust specification readily available in the UK & Ireland as it specifies minimum etch requirements within the pretreatment process for enhanced ‘Seaside’ applications and includes regular finished powder coated surface laboratory tests for filiform corrosion resistance, something which BS EN 12206-1 does not require.
The up-to-date QUALICOAT Specification is freely available for download via the UK & Ireland Association website, qualicoatuki. org and the website offers an up-to-date list of licensed UK and Ireland Powder Suppliers, Pretreatment Suppliers and Applicators including the applicators who carry the Seaside class accreditation. Telephone support is available from QUALICOAT UK & Ireland Head Office in the Midlands on 0330 240 9735, the Association can also be followed on Twitter @ Qualicoatuki or on LinkedIn www. linkedin.com/company/qualicoatuk-&-ireland.
In 2025 the Institute of Materials Finishing is celebrating our 100 birthday.
Founded in 1925 as the Electrodepositors Society to serve the electroplating industries, we became the Institute of Metal Finishing in the 1950’s. In 2012 we re-badged ourselves as the Institute of Materials Finishing, to better reflect our involvement with all aspects of surface engineering.
Our celebrations begin in February 2025 at the Surface World exhibition, with a centenary dinner taking place on the first evening, Wednesday 26th February 2025.
Tickets will be £40 per person or you can take advantage of the Early Bird Offera table of 10 for £375.
There will be a 3 course dinner followed by entertainment.
Please let Helen know soonest if you would like to attend by email: helen@materialsfinishing.org.
Further events are being planned throughout 2025, which we are sure will interest and engage all our members. Please keep an eye out for announcements in future editions of IMFormation! Please try to join us as we mark our Centenary!
Email: helen@materialsfinishing.org Visit: www. materials-finishing.org
• AirBench takesdustandfumes awayfromyourbreathingzone
• AirBench drawsthemthrough theworksurface,capturingthem insidethebench
• AirBench isavailableinawide rangeofsizesandfiltertypes tosuityourapplication
• AirBench isplugandgo-only needingunwrappingandplugging intoa13ampsocket
•Yougetextractionandwork benchinonecompactunit
Contactusforanon-sitedemonstration. Doubtitcanbethatsimple?
TheVertExmodularbooth system.Dustissuessolved...
• Modular systemforfast installationandassembly.
• LowEnergy throughtheuse ofhighefficiencyfans-upto 20,000m3/hat3kw.
• FiltrationOptions fromthe standardAirBenchrange.
• WeldingandGrinding boothsalso availablewithHEPAfinalfilter.
• RapidReconfiguration -standard componentsmeanVertExbooths canbereconfiguredondemand.
Doubtitcanbethatsimple?
British Coatings Federation CEO, Tom Bowtell, wins Memcom’s ‘CEO Leadership Award’ for 2024.
BCF also won a ‘Highly Commended’ rank for sustainability and was shortlisted for ‘Best Use of Video’ and ‘Team of the Year’.
Collectively, the awards demonstrate the continued support and added value BCF strives to deliver for its members across the coatings sector.
Tom Bowtell, Chief Executive Officer of the British Coatings Federation (BCF), was awarded the highly contested CEO Leadership Award at the 2024 Memcom Excellence Awards in London on 27th September. The award is given to a CEO
who, in the opinion of the judges, ‘has delivered outstanding leadership and has shown how their organisation has advanced under their leadership.’ The award is recognised as ‘one of the most prestigious awards for an individual within the membership sector’. Tom’s success follows BCF winning the Best Trade Association Award at last year’s Memcom Excellence Awards.
Since taking over as CEO of the BCF in 2012, Tom has had a major impact on the organisation, initiating changes and improvements for the benefit of the UK coatings sector. In the 12 years of his tenure to date, he has driven leadership within the industry, delivered outstanding service for the members, and created a friendly, collaborative team atmosphere for employees to thrive in. Tom’s influence on financial planning and management has created a solid base from which new initiatives for the benefit of the members can be launched. This has substantially
increased BCF’s membership as a result, leading to membership retention levels of 96% in 2023 and, significantly, 100% in 2022, the period on the back of Covid-19 and Brexit. This financial position has also allowed BCF to increase campaigning efforts, most recently through the Essential Coatings campaign, which is contributing to building awareness of the sector with Government and gives coatings better representation when tackling key issues within the chemical supply chain.
Tom has also been the key driver in shaping a more forward-thinking approach for the sector, most notably in the areas of sustainability, diversity and inclusion, and in engagement with the next generation of leaders in the industry. This progress can be measured, in part, through the launch of BCF’s Net Zero Roadmap in 2023, and the launch in 2024 of an industry Equity, Diversity and Inclusion Charter, together with the creation of a Coatings NextGen Council. Through these and other ongoing initiatives, Tom has worked with the membership to ensure the coatings sector is pursuing a progressive outlook for the future.
Tom is a recognisable figure not only in the UK coatings industry but also throughout the supply chain. He is the current chair of the Alliance of Chemical Associations (ACA) in the UK; a member of the CEPE Operational Board at a European level; and is in his second consecutive term as President of the World Coatings Council.
In addition to Tom’s win, the BCF was also ‘Highly Commended’ for the Memcom ‘Sustainability Award’ at the event, recognising the efforts of
Working Across Aluminium Industries to Improve Your Processes
Specialist in the Supply of Anodising & Metal Finishing Technologies
QUALICOAT Approved Chrome & Phosphate Free Technologies
Low-Temperature Degreasing & Sealing Solutions Supplied
the organisation on its Road to Net Zero publication, leading the way on the industry-wide commitment to reaching Net Zero by 2050 and supporting its members on the journey. They were also shortlisted for awards for ‘Best Use of Video’ and ‘Team of the Year.’
Tom said of his commendation:
‘I’m really honoured to have won the Memcom CEO Leadership award. Thanks to the wonderful team at the BCF for nominating me - the art of good leadership is to surround yourself with very talented people who make you look good! The award is a recognition of that wider teamwork and the success we have had as a
group working to deliver for BCF’s members. That was why I was so pleased we were also shortlisted for Team of the Year.
‘At the end of the day, we are a membership organisation and everything we do must be focussed on the membership and their needs. That forms the basis of our approach at BCF and, together with genuine, honest, and meaningful collaboration with members themselves, has helped lead to significant success and progress in recent years.’
The judges commented:
‘Tom is a worthy winner, showing a breadth of competence across all
areas. His approach to finance and governance has left the BCF financially secure but this ‘quiet revolution’ was not just about processes but about creating a sound base for the delivery of more benefits to members. The BCF's retention rates and membership satisfaction are a testament to the success of his approach. After 12 years as CEO Tom is still leading and inspiring his team and innovating for the future.’
Visit: www.coatings.org.uk
Email: info@bcf.co.uk
For more information and the full list of winners, please visit: https://www.memcom.org.uk/ awards-winners-2024
The British Coatings Federation (BCF) - representing more than 140 members that contribute £4 billion annually to the UK economy and export £1 billion of products a year - supports the vision for a joined-up, long-term Industrial Strategy set out in today’s Green Paper.
It welcomes the Green Paper’s recognition of the importance of ‘foundational’ or ‘enabling’ sectors to the wider manufacturing industrysuch as coatings - without which other sectors could not function.
Coatings are relied upon downstream by companies worth £300 billion a year to the UK economy, including in the eight ‘growth-driving sectors’ identified in the Green Paper.
BCF looks forward to responding to the consultation and engaging with the Government to make the vision for an Industrial Strategy a big success.
The British Coatings Federation has welcomed today’s publication of the Government’s Industrial Strategy Green Paper. The organisation has consistently called for a long-term and robust UK
industrial strategy, with industry itself involved in its development. The proposals outlined in the Green Paper today provides the bedrock for that vision to be delivered upon.
The overall Strategy focuses on building on already identified strengths, namely eight growth-driving sectors: Advanced Manufacturing, Clean Energy Industries, Creative Industries, Defence, Digital and Technologies, Financial Services, Life Sciences, and Professional and Business Services.
Crucially, however, the plan also identifies the need to provide policies ‘for those subsectors on which the growth-driving sectors have critical dependencies….’ Including ‘“Foundational”’ sectors…which provide critical inputs and infrastructure to our growth-driving sectors.’ It ‘identifies the importance of strong supply chain linkages between sectors, as supporting upstream sectors can enhance the productivity of downstream sectors.’
Programming-free coating of any shape! Gema
The second generation of Dynamic Contour Detection detects the object contour fully automatic and positions the guns individually even for thin objects and at high conveyor speeds. Due to the programming-free adaption of all relevant line settings the application range is significantly extended.
Email: uk.sales@gema.eu.com
This is a clear recognition that if the Government wishes to bring in more investment from companies working in fields such as aerospace, automotive, life sciences or green energy, it also needs to ensure that there is a strong domestic manufacturing supply chain of ‘enabling sectors’, like coatings, without which those other industries will not succeed. This addition goes much further than the previous Government’s Advanced Manufacturing Plan and is a positive step.
BCF also welcomes the recognition that a broader ‘pro-business environment’ needs to be in place for the Strategy to work. The Green Paper notes this being created with positive policies on ‘people and skills, innovation, energy and infrastructure, the regulatory environment, crowding in investment, and international partnerships and trade.’
BCF agrees with all of those areas,
particularly creating the correct regulatory environment. Crucial to the coatings sector, and all those within the broader Chemicals Industry, is to finally deliver a solution on chemical regulation in a way that delivers an ambitious and proportionate regulatory environment within which UK businesses can compete as world leaders, including a swift resolution to UK REACH.
BCF CEO Tom Bowtell said:
“We welcome the publication of the Green Paper and the vision for a holistic and long-term UK Industrial Strategy. In particular, we are pleased to see the recognition of the importance of ‘foundational’ sectors – such as coatings – in the Strategy. It is also pleasing to see a joined-up approach with references to a need for a pro-business regulatory environment. This latter is fundamental to those businesses working in the
chemicals sector and where we need to see, finally, workable and proportionate post-Brexit regulatory regimes put in place, especially for UK REACH.
“BCF looks forward to responding to the consultation, and talking with Government, to set out how the coatings sector can help deliver on the positive plans for a strong and growing domestic UK manufacturing base. We already have a positive story to tell but with the right policies we can, collectively – Government and industry working together – make British manufacturing an even greater success.”
Visit: www.coatings.org.uk
Email: info@bcf.co.uk
Affordably measures uncured powder coatings using non-contact ultrasonic technology to predict a cured thickness
Dedicated stand-alone unit is ready to measure right out of the box
Fast measurement speed—ideal for moving lines and swinging parts
Scan Mode continuously takes measurements—ideal for analyzing large areas
Storage of 999 readings with onscreen averaging. Stored readings can be downloaded to PosiSoft Desktop Software
Powder Inspection Kits
Complete solutions for measuring powder coating before and after cure are available
New and used vibratory finishing machines and systems from 2 litres to 4000 litres
Finishing media; Ceramic, Plastic, Wood, Steel and Maizorb
Liquid / powdered / paste compounds
Abrasive finishing wheels
Vibratory separators / sieving machines and re-meshing service
Repairs and relines
Effluent water treatment systems
Redundant machines purchased
Consultancy
Subcontracted finishing and industrial sieving services
Experienced Engineers After sales technical support Nationwide deliveries
Sharmic Engineering Ltd
Tel: +44 (0)1299 822135 / 878123/4/5
Email: info@sharmic.co.uk www.sharmic.co.uk
The surface finishing industry is a cornerstone of modern manufacturing, encompassing processes like cleaning, coating, plating, anodising, galvanizing and polishing that are essential for enhancing the appearance, durability, and performance of products across various sectors. In this highly specialised and technical field, trade shows such as Surface World play an indispensable role, acting as an essential platform for innovation, networking, and business growth.
Trade shows are crucial for driving innovation within the surface finishing industry, and Surface World stands out as a premier event in this regard. As technological advancements continue at a rapid pace, Surface World provides companies with the perfect venue to unveil their latest products, processes, and innovations to a focused audience. Whether it’s the introduction of a new electroplating technology or a breakthrough in eco-friendly coating materials, Surface World offers a critical opportunity for showcasing cutting-edge solutions.
For attendees, Surface World is an invaluable opportunity to see the future of the industry firsthand. The event allows them to explore the latest technologies that could revolutionise their operations, often through live demonstrations and hands-on experiences. This direct exposure to innovative solutions accelerates the adoption of new technologies, helping companies maintain a competitive edge in a fast-evolving market.
In the surface finishing industry, relationships are key. Surface World excels in bringing together a diverse group of stakeholders, including manufacturers, suppliers, researchers, and end-users, creating a rich environment for networking and collaboration. This event provides a rare opportunity for industry professionals to meet face-to-face, exchange ideas, and forge new partnerships. The connections made at Surface World often lead to longterm business relationships and collaborative projects.
Surface World also serves as a vital tool for market research and competitive analysis in the surface finishing industry. This event offers a comprehensive overview of market trends, customer preferences, and the competitive landscape. By attending Surface World, companies can gather real-time insights that inform their strategic planning and product development efforts.
Observing the offerings and strategies of competitors is another critical aspect of trade show participation. By understanding the competitive landscape at Surface World, companies can better position themselves in the market, identify opportunities for differentiation, and refine their business strategies.
One of the most significant benefits of participating in Surface World is the potential for business development and lead generation. The event attracts a highly targeted audience of professionals who are actively seeking solutions and services in the surface finishing industry. Exhibitors can engage directly with potential customers, discuss their specific needs, and present tailored solutions.
The concentrated environment of Surface World often leads to more qualified leads and accelerates the sales process. Face-to-face interactions help build trust and rapport, which are crucial for closing deals and establishing long-term business relationships.
The surface finishing industry is technically complex, and staying informed about the latest advancements is crucial for professionals in the field. Surface World provides a robust educational component where industry experts share their knowledge on a broad range of topics, including new technologies, regulatory updates, sustainability, and quality control.
For attendees, these learning opportunities at Surface World are invaluable for enhancing their expertise and staying ahead of industry trends.
For companies, contributing to these educational efforts can position them as thought leaders and strengthen their influence within the industry
As environmental concerns grow, the surface finishing industry faces increasing pressure to adopt sustainable practices. Surface World plays a critical role in promoting sustainability by highlighting green technologies, eco-friendly materials, and best practices that reduce environmental impact.
Exhibitors at Surface World use the event to demonstrate how their products and processes align with sustainability goals, appealing to customers who prioritise environmental responsibility.
Share - Learn - Connect
Trade shows like Surface World are more than just exhibitions; they are
dynamic hubs of innovation, collaboration, and growth within the surface finishing industry. By offering a platform to showcase new technologies, foster networking, conduct market research, and promote sustainability, Surface World plays a critical role in helping companies navigate challenges and seize opportunities in this ever-evolving field.
Mark your calendars for the 26th and 27th of February 2025, and join industry leaders in Hall 11 at the NEC in Birmingham to experience firsthand the advancements shaping the future of surface finishing.
Share - Learn - Connect - Shape The Future
For more information about Surface World 2025, please contact Nigel Bean: nigelbean1@aol.com
AkzoNobel has launched the Interpon A5000 range of powder coating to give reliable, consistent and long-lasting protection to commercial vehicles for original equipment manufacturers (OEMs) and suppliers looking to combine performance with sustainability.
Interpon A5000 is a range of powder coatings for the chassis, body, and multiple parts of a commercial vehicle that addresses a series of customer needs. It delivers optimum levels of corrosion protection in challenging environments, with a durable finish in a choice of colors that last longer, protecting a manufacturer’s brand reputation. It’s a product that OEMs can also trust to be consistent worldwide, thanks to AkzoNobel’s global manufacturing footprint.
From trucks and trailers to buses and specialty vehicles, commercial vehicles need powder coating solutions that are as robust as the parts they protect. The full range comprises
With our new Interpon D1036 Low-E powder coating, we’ve created an industry first: a powder coating that can cure as low as 150°C while still being Qualicoat class one certified. It can also cure up to 25% faster than conventional powders, reducing both energy consumption and carbon emissions, and significantly improving your coating line efficiency. Easy to apply Interpon D1036 Low-E has the same application properties as standard formulation, is backed by an Environmental Product Declaration (EPD) and has a global warranty of up to 15 years to deliver the quality performance, color and style your customers need. It is an innovation that supports our collective commitment to sustainability throughout the value chain.
not only primers but also topcoats and clearcoats, and coatings that are designed to withstand multiple challenges. These include damage caused by corrosion and UV light, or through chemicals like petrol, diesel, oil and other chemicals.
Commercial vehicle manufacturers are also looking for solutions that support their sustainability agenda, that reduce their energy consumption, carbon emissions and cost. To this end, the range is designed with sustainability in mind. The powder coatings are easy to apply for a right first-time finish that accelerates production volumes and avoids the need for costly re-working.
The range also includes products with lower curing temperatures, further reducing processing times, energy consumption and waste while delivering consistently high levels of performance and quality. And being powder coatings, they are free from Volatile Organic Compounds and generate almost zero waste, since any overspray can be recycled and reused.
Central to the range is the Interpon A5500 powder coating, a smooth primer that is ideally suited for use on the body of truck cabs, front grills, and bumpers. The primer is more sustainable than ‘traditional’ alternatives, thanks to the absence of any VOCs and flexibility in the coating process. It serves as the perfect basecoat not only for powders, but also for a liquid topcoat, enabling manufacturers to harness the benefits of both coatings.
Martina Lösgen, Global Segment and Key Account Manager ACE and CV says: “Interpon A5000 range is trusted by many of the major OEMs and fabricators for their reliability and performance, but also for the flexibility and efficiency that they can bring to their operations. Partnering with us enables manufacturers to add world-leading protection, color and finish to their world-class vehicles and parts.”
To complement the range, AkzoNobel also delivers worldleading technical support services to help OEMs and their suppliers optimize their powder coating application lines, and the performance of the Interpon solutions they choose.
Other products within the range include Interpon A5150, which is ideal for delivering high levels of durability and corrosion resistance for trucks, trailers, and buses, and meets OEM surface friction standards; and Interpon A5160 which has all of the benefits of A5150 but with further improved UV light resistant. Specific powder coatings have also been developed for components like pressure containers and fuel tanks, including Interpon A5250, which resists petrol, diesel, oil, chemicals, and weathering, and Interpon A5260, designed for pressure tanks with high resistance to road debris and excellent gloss retention.
For the body parts and cabs, the range includes Interpon A5550, which is a full powder coating system and Interpon A5552 and Interpon A5554 which are specifically designed to balance Class A surface condition with an optimized cost per unit. The latter has superior levels of UV-durability for premium truck builders and other vehicles which require the highest quality finish. The range also includes Interpon A5560, a high quality clearcoat, and Interpon Redox, a series of primers that provide customers with a one-stop-shop for corrosion protection, even in the most challenging environments (up to C5 corrosive environments).
For more details about the complete range of Interpon 5000 powder coatings, please visit our website at www.interpon.com.
• low space requirement
• high thermal and mechanical stability
• easy to clean
• custom-made dimensions
+44 / 1509 673 656
• for process liquids with strong acids
• anti-adhesive coating made of thermal conductive fluorpolymer
significant reduction in encrustations
• different dimensions
• highest chemical resistance
• several planar layers of tube coils made of PFA large heat transfer surface to volume ratio high temperature- and pressure resistance
Unrivaled probe interchangeability for all of your inspection needs.
Coating Thickness Probes
n Ferrous n Non-Ferrous n Combination n Ultrasonic
Surface Profile Probes
n Depth Micrometer n Replica Tape Reader
Environmental Conditions Probes
n Integral n Cabled Magnetic Probe n Anemometer Probe
n 1/2” NPT n Infrared
Hardness Probes
n Shore n Barcol
Salt Contamination Probe
n Bresle Method
Ultrasonic Wall Thickness Probes
n Corrosion n Multiple Echo Thru-Paint n Precision
n Low Frequency n Xtreme
Customized Inspection Kits...
Build your own kit from a selection of gauge bodies and probes to suit your needs.
Backwards Compatibility! The redesigned PosiTector gauge body accepts ALL coating thickness (6000/200), environmental (DPM), surface profile (SPG/RTR), salt contamination (SST), hardness (SHD/BHI), and ultrasonic wall thickness (UTG) probes manufactured since 2012.
Long Drive, Meadway, Berkhamsted, Herts HP4 2PN t: 01442 879494 f: 01442 879595
www.dftinstruments.co.uk e: sales@dftinstruments.co.uk
SurTec 717 - Modular, Alkaline Zinc/Nickel Process for all Applications
Modular process for rack, barrel and special applications
Tolerates higher process temperature up to 35°C
Easy to control, automatically limits the nickel content below 16%
SurTec 680 - Cr(VI)-free Thick Layer Passivation for Zinc & Zinc Alloys
For highest quality requirements (heat resistance & corrosion protection)
Usage without waste water is possible
Highest cost-effectiveness when using the SurTec regeneration process
precote Product Range - Thread Locking and Sealing
Specially developed pre-coating products for locking, sealing & clamping
Based on unique microencapsulation technology
Excellent service and high-quality products made in Germany
expand our offering further and increase our presence in this niche market.”
Chemical specialist, Airedale Group, has added a new range of anodising dyes to its portfolio of specialist products.
Anodaire is a selection of dyes which offer excellent colour, corrosion protection and longevity and have been brought into the company’s specialist Metal Surface Treatment portfolio which offers solutions across all processes in the specialist surface treatment sector.
Andrew Roper, Commercial Manager of Airedale Group’s Metal Surface division, explains: “We have invested in extending our range of metal surface treatment products with a number of more specialist products over recent years. The addition of our own range of anodising dyes will
Available in black, blue, orange, gold and red, Anodaire dyes are fast colouring with maximum effect taking just five minutes. Their strong coverage is highly effective on all types of aluminium material making them ideal for decorative and architectural anodisers.
For more information in Airedale Group’s Anodair range of anodising dyes, visit https://airedale-group. com/product-category/anodising-dyes/ or contact emquiries@airedale-group.com.
Airedale Group, founded in 1973, is based in Cross Hills and provides chemicals and related services to the UK and Europe.
To find out more visit www.airedale-group.com.
When it comes to heavy equipment, there’s no room for error.
From demanding durability requirements to exacting color and finish criteria, the toughest of applications require the most formidable of solutions. BENEFIT FROM GLOBAL SOLUTIONS DELIVERED WITH THE CONFIDENCE OF LOCAL SUPPORT
Contact: gi.emeai.marketing@sherwin.com
Visit: www.sherwin-williams.eu
SuperCORR A is an advanced corrosion protection spray that was originally designed to prevent electrical and electronic components from systems failures caused by corrosion. Developed for the U.S. Air Force and within strict safety specifications (complies with MIL-DTL-87177B), it has been the proven standard for avionic corrosion protection within MROs (maintenance, repair and operations) and OEMs (overhaul and original equipment manufacturers). It’s unique ability to displace water and provide a performance enhancing level of corrosion protection has led to it being used in many other applications and industries worldwide.
SuperCORR A works particularly well in environments where corrosive gases such as salt laden air or hydrogen sulphide are present. It is unexcelled in preventing deterioration and contamination of metal surfaces and is used in many applications worldwide, including industrial manufacturing, rail and road transport, oil and gas industries, wastewater treatment plants, electrical power facilities, paper and pulp mills, marine and military industries.
Advanced corrosion protection for a range of industries and applications
SuperCORR A is a unique and proprietary formulation with longlasting, anti-corrosion inhibitors providing a superior lubrication coefficient and protection against moisture, wear, general and fretting corrosion, static electricity, corona, and other electro migration problems. The non-flammable film is only 7 microns (0.007mm) in thickness, is not a wax or oil-based product and is formulated without sulphates, chlorides, petroleum-based material, or halogens, to meet the EU RoHS directive.
The use of SuperCORR A for corrosion prevention can not only bring financial savings in reduced maintenance and replacement costs but more importantly greater safety.
It is much simpler and a lot less costly to prevent corrosion than to repair or replace damaged aircraft equipment or a component that failed because of corrosion. It is very effective at preventing corrosion of electronic and electrical equipment in demanding work environments.
SuperCORR A is a “self-healing” ultra-thin film lubricant with a proprietary corrosion preventive compound that will not harden or crack, is not a wax or oil-based product and is formulated without sulphates, chlorides or halogens.
SuperCORR A is packaged in aerosol cans making application to component parts easy for engineering crews in difficult locations and conditions. Unpainted mild steel will
not rust on exterior surfaces directly exposed to sea water environments for at least 6 months, protecting electrical connectors, switches, chains, drive shafts from corrosion while maintaining lubrication on moving surfaces.
Extremely long-lasting, specially formulated and proprietary anticorrosive inhibitor.
Eliminates premature failure of components created by moisture, general or fretting corrosion.
Prevents deterioration and contamination on all surfaces of electronic and electrical equipment and mechanical close tolerance moving components.
Reliability increased, maintenance intervals increased, costs reduced, manufacturers save costly warranty service calls or product re-call.
Non-flammable.
Please visit our website https://www. envirotech-europe.com/supercorr-a for information about other uses and applications for SuperCORR A.
For more advice, please telephone us on +44 (0) 20 8281 6370 or use our website contact form. Manufactured in the United Kingdom and available on short delivery times through our dedicated team of distributors worldwide.
Product Overview
Manual Monorail Systems
Unit loads up to 3000kg
Monorail Chain Conveyors
Unit loads up to 300kg
Power & Free Conveyors
Unit loads up to 7000kg
Floor Conveyors
Unit loads up to 500kg
Stewart Gill Conveyors Ltd have been supplying overhead conveyors into all sectors of industry for over 70 years.
As a long time member of the Railtechniek van Herwijnen BV Group based in the Netherlands, Stewart Gill Conveyors can offer a comprehensive range of overhead conveyor products which are capable of handling unit loads up to 7000kg.
Stewart Gill Conveyors Ltd offer complete manufacture, installation and commissioning, coupled with fully documented instruction, operation and maintenance manuals.
We do:
In-House 3D CAD engineering
In-House manufactoring in the UK and EU
In-House design of PLC/PC control systems
Industry 4.0
Worldwide installation and commissioning
Remote support, service & inspection Stewart
Part of the
Sensor Coating Systems (SCS) is thrilled to announce its award-winning achievement at the 2024 Barking & Dagenham Chamber of Commerce Business Awards ceremony held at Dagenham & Redbridge Football Club, UK in June.
For SCS Net Carbon Zero is the goal! The deep-tech company has developed a unique thermal mapping technology which is offered as a service to the global power and aviation industry. The accurate mapping of temperatures is directly linked to the improvement of efficiencies of power producing engines such as gas turbines, jet engines or automotive engines. A niche technology addressing a global issue and a global market!
The company proudly received two distinguished accolades: the small and medium sized enterprise ‘SME of the Year’ Award’ and the ‘Sominder Panesar’ Commemoration Award which was won by SCS’s Managing Director Dr Jörg Feist, acknowledging his continued efforts to make a difference to the local business community. Demonstrating to the judge’s support for local disadvantaged communities to improve their knowledge and skills by offering work experience and internships from local schools & colleges to support a pathway towards STEM careers. SCS works alongside schools such as Barking & Dagenham College, Brook 6th Form & Academy - A University Technology College, the AngloEuropean School and Brampton Manor Academy . Jörg cultivates a dynamic entrepreneurial spirit amongst the young and diverse team of engineers, analysts and support staff, demonstrating good business ethics creating trust within the team as well as with long standing customers and suppliers which really impressed the judging panel.
The SME award recognized SCS for its outstanding contribution to the community, innovation in technology & its dedication to sustainability, highlighting the company as a trailblazer in its field of engineering. The company has proven to the judges its exceptional approach to business development and marketing of its technology.
Through local events, forums and industry speaker opportunities including conferences such as the ASME Turbo Expo which it recently attended at the ExCel, London with 3 technical papers and included an industry tour to the SCS laboratory facility. The award highlights the dedication that SCS gives to maintain long standing and loyal customers whilst forging new and strong relationships across the globe and has innovative and collaborative plans for the next 12 months.
Dr Feist commented: “The SME Award is for our team! It recognises the outstanding efforts of a truly diverse team of people with a multicultural and multi-skill background. We developed from scratch and commercialise deep-tech on a global scale from the the east end of London. This is remarkable.’
Further Dr Feist explained, ‘The Sominder Panesar Commemoration Award touches me personally. I met Mr Sominder Panesar and his son some years ago here in the local community and we collaborated with each other. Sominder sadly and unexpectedly passed away.’
Sensor Coating System Limited (SCS) was spun out of Southside Thermal Sciences, an Imperial College London start up and is privately funded. Its award-winning technology (British Engineering Excellence Award, Royal Society of Chemistry, American Society of Mechanical Engineers) enables accurate temperature detection and, in doing so, assists in optimising the operation of machinery, lowering fuel costs and maintaining material integrity.
SCS is an award-winning high-tech company which provides a temperature data service on mission-critical components to a global client base in the areas of aerospace, power generation, automotive and industrial sectors. The technology is an enabling technology assisting in reducing CO2 emissions by providing crucial temperature data to design engineers. The benefits are lower emissions, but also quicker market entries for new products and less failure rates once the product goes into the marketplace.
• Ideal for frequent & fast color changes
• High degree of automation for optimum efficiency
• Double-designed fresh powder station for increased productivity
The company works progressively and collaborates with a number of UK and global based organisations, educational institutions, and research councils to help facilitate its R&D projects and growth in the technology sector. Imperial College London, Royal Commission for the Exhibition of 1851, Innovate UK and NATEP to name a few, where close relationships are critical for advancing projects and funding research opportunities.
The Thermal History Technology is a unique luminescencebased sensing technology which enables engineers to record past temperatures on inaccessible components. The temperature measurement capability reaches from around 150°C to 1,600°C. This makes the technology very useful for the evaluation and design of mission-critical
components in harsh environments such as a gas turbine or internal combustion engines.
The materials used in the Thermal History Technology have innate luminescence which permanently changes due to thermal exposure, allowing the temperature to be measured by non-destructive excitation and detection of the luminescence light. The measurement device can be scanned across the surface to produce an accurate thermal profile of the surface. The materials are deposited using techniques pioneered for the most challenging applications and can survive for a long duration under high thermal and mechanical loads, offering both short- and long-term measurement of thermal characteristics.
Visit: www.sensorcoatings.com
Thanks to community support – including both a local manufacturer and a galvanizing firm – a commemorative plaque will take pride of place at Lavenham Airfield.
Suffolk-based and family-run Jordan Engineering, who build small seed drills for conservation work, was commissioned to fabricate a plaque to commemorate the 80th anniversary of the arrival of the 487th Bomb Group in Lavenham.
Their Owner, Jerv Jordan, said: “The ‘Friends of Lavenham Airfield’ recently got in touch asking for our support ahead of the 80th anniversary. We were all too happy to help, and designed a commemorative plaque replicating the tail fin of a B24 Liberator with the Lavenham ‘P’ marker included too.
“It took around five days to fabricatethe majority of which was ‘thinking time’ to ensure it was a fitting commemoration for this 80th milestone. In total, around 15 kgs of steel was used, consisting of an outer frame which was rolled out of 22mm tube, some steel lengths around 600mm for the legs, and 5mm plate profiles cut out on our CNC Plasma Cutter for the lettering and detail plaque mount.”
After design was complete, the plaque was then transported to Acrow Galvanizing Ltd to be immersed in a bath of molten zinc at temperatures around 450C to allow for a metallurgically-bonded coating to be formed, which would protect it from rust and corrosion for up to 70 years.
“It was a real pleasure to work with Acrow Galvanizing once again,” Jerv continued.
“Several years ago, we used to fabricate small trailers which we’d regularly take to their old Saffron Walden site for galvanizing.
“The whole team always was (and still are) brilliant, helpful, and efficient. In fact, their personable and friendly approach is one of the main reasons I choose to collaborate with them time and again. Back then, I had a Golden Spaniel (Freddie), who always came to work with me, and as soon as I’d enter the yard, their forklift driver, Mick Rusling (Ruzza), would climb into the truck for a cuddle with Fred before unloading the trailer. What a reception! Truly, why would I go anywhere else?”
Sam Longstaff, Sales Coordinator at Acrow Galvanizing Ltd, added: “At Wedge Group Galvanizing Ltd, we’re always eager to support and collaborate with our local communities. Jerv contacted us about this particular project and we were eager to be involved – excited to mark such a poignant part of our local history and heritage, and keen to ensure that this commemorative plaque remains fit-for-purpose for generations.”
The plaque was officially unveiled at the 487th Bomb Group Memorial Day on Sunday 26th May 2024, underneath a commemorative oak tree. The event was a remembrance and rededication to those who lost their lives whilst serving at USAAF Station 137 in World War 2, and was attended by the three sons of a 487th Bomb Group Ground Officer and the daughter of an Aircraft Radio Operator.
Acrow Galvanizing is part of Wedge Group Galvanizing, the largest hot-dip galvanizing organisation in the UK with a history dating back over 150 years. With 14 plants strategically placed across the country, the firm offers a truly national galvanizing service. For further information, please contact Wedge Group Galvanizing on 01902 601944 or visit www.wedge-galv.co.uk.
• Custom Designed & Built Control Panels
• pH & Redox Controllers & Electrodes
• Conductivity Controllers
• Liquid Level Controllers
• Open Chanel & Magnetic Flow Meters
• Data Loggers
• Dosing Pumps & Tanks
Call today for a quote or to inquire.
House, Antom Court, Tollgate Industrial Estate, Stafford, ST16 3AF
01785 254 597
Hot dip galvanizing provides you with long-term protection against rust and corrosion of steel products. With 14 plants across the UK, Wedge Group
Galvanizing is the UK’s largest hot dip galvanizing organisation offering a national service, collection and delivery and 24hr turnaround on request. The group can process anything from small components to 29m structural beams.
Component cleaning has evolved far beyond just selecting the right fluids—it’s about leveraging the latest technology to ensure superior performance, sustainability, and long-term viability. That’s where Fraser Technologies comes in, leading the charge with cutting-edge cleaning solutions that combine state-of-the-art equipment with advanced chemistries. Our mission? To empower businesses with the most effective, innovative, and future-proof cleaning systems available. And today, we’re excited to introduce “The Newborn”, a groundbreaking solution that’s set to revolutionise industrial component cleaning.
The Newborn isn’t just another cleaning machine— it’s a leap forward in the way businesses approach cleaning operations. Designed with adaptability, efficiency, and environmental consciousness in mind, this fully sealed, *near-zero emissions cleaning system represents the pinnacle of modern engineering. Here’s why The Newborn is the perfect choice for businesses looking to stay ahead of the curve:
* PCE – 28 g/hr fugitive emissions
1. Patented Cooling Technology: Maximise Efficiency, Minimise Maintenance
One of the standout features of The Newborn is its patented cooling system. Unlike other machines that rely on either external abatement systems or carbon absorption / desorption (which can be bulky and require constant maintenance), The Newborn captures and recycles solvents internally using the patented recycling system, reducing both your operational complexity and maintenance costs. This not only lowers your carbon footprint but also simplifies your cleaning process, allowing you to focus on what truly matters—productivity.
Many traditional cleaning machines limit you to a single solvent, forcing you into expensive retrofitting or even new equipment when regulations or cleaning needs change. The Newborn allows seamless switching between
multiple solvents—including Perc, modified alcohol, and hydrocarbons—without the need for costly adjustments. This flexibility future-proofs your operation, allowing you to adapt quickly to evolving industry standards and customer demands.
3. Near-Zero Emissions: A Cleaner, Safer Environment
Environmental standards are becoming more stringent, and The Newborn is ready for the challenge. Its fully sealed design ensures near-zero emissions, eliminating the need for external abatement equipment and providing compliance with even the most rigorous safety and environmental regulations. This means you get top-notch performance while keeping your workplace safer and greener, all without the added costs of extra equipment or modifications.
Downtime can be costly, especially when you’re dealing with cleaning machines that need to be shut down for hours each week for routine maintenance. The Newborn is designed for continuous operation with minimal interruptions. Its dual stills and filters allow for in-process cleaning and maintenance, ensuring that your system stays up and running 24/7 while still maintaining high performance. This means more productivity and less disruption to your workflow.
5. Built for High-Volume, Complex Cleaning Tasks
The Newborn excels in handling medium to high-volume production rates, making it perfect for industries with demanding cleaning requirements, such as aerospace and automotive. Whether you’re dealing with complex geometries or intricate components, The Newborn’s high throughput capability ensures you get fast, efficient results without compromising on quality.
6. Adaptable to Future Regulations: Stay Ahead of the Curve
As environmental regulations continue to evolve, so do the demands on cleaning equipment. The Newborn is built to adapt to future solvent types and regulatory changes, meaning you don’t need to worry about frequent and expensive upgrades. This adaptability ensures your investment remains relevant for years to come, offering a long-term, cost-effective solution.
7. Cost-Effective and Efficient: Lower Costs, Higher ROI
Advanced technologies traditionally came with high capital costs, but thanks to modern innovations, The Newborn offers a highly competitive price point without sacrificing quality or performance. Its efficient solvent recovery system reduces chemical usage and waste, further lowering operational costs and providing a strong return on investment.
8. Local UK Support and Service: Always There
The Newborn is backed by Fraser Technologies’ unparalleled UK-based support. From on-site training to expert servicing and waste management, you can count on fast, reliable assistance whenever you need it. Say goodbye to long wait times and expensive overseas support—Fraser Technologies provides the dependable service that keeps your operation running smoothly.
9. Enhanced Safety: A Safer Work Environment for All Safety is paramount, and The Newborn prioritises operator well-being with its fully enclosed, highly controlled cleaning process. By minimising exposure to chemicals and fumes, The Newborn creates a safer work environment, giving you peace of mind without compromising performance.
Fraser Technologies is proud to introduce The Newborn, an advanced cleaning system that stands out in terms of versatility, efficiency, and environmental responsibility. This machine is not just a step forward in cleaning technology—it’s a leap toward the future.
Whether you’re upgrading from an older system or seeking a new solution for your cleaning needs, The Newborn offers unmatched performance and future-proofing, all at a competitive price.
As Graham Fraser, Managing Director of Fraser Technologies, says, *“The Newborn is designed to outperform and outlast other technologies on the market, combining versatility, efficiency, and safety in ways our competitors simply can’t match.”*
Fraser Technologies is your one-stop solution for comprehensive cleaning systems. From evaluation to supply and support, we offer a complete package that ensures your cleaning processes are optimised for peak performance. Our services include analytical assessments, component cleaning audits, process optimisation, and hands-on cleaning trials, all aimed at driving efficiency and success.
Contact Fraser Technologies today to discover how The Newborn can transform your cleaning operations and help your business stay ahead of the competition. Schedule a demo and explore the future of cleaning technology!
with metal pre-treatment process solutions; the better they are controlled, the more consistent the results.
In the past, when the majority of cleaners and lightweight iron phosphates were powder chemicals, automatic dosing was the exception rather than the rule. However, in recent years the trend has been to liquid chemical concentrates, which has resulted in the increased use of automatic dosing equipment.
Brian Carroll comments: “Having introduced automatic dosing equipment into many companies, we have not had one single complaint.”
Automatic dosing can be effected in many ways: from a simple dosing pump to a fully integrated computerised system. Typical applications include:
require the regular use of manual input in order to make the adjustments and solution strength variations. However, this is better than chemical checks alone and small manual chemical additions are always better than one large shock addition. Moving on from this are control systems that are fully automated and which require the use of conductivity or pH sensors to be fitted in the process solution. Process solutions on pre-treatment plants are normally controlled using conductivity. However, in some instances, pH control is required.
by Brian Carroll, BC Metal Finishing Services Ltd
In life in general, if something is under control it performs well. This is no different with metal pre-treatment process solutions; the better they are controlled, the more consistent the results.
Timed dosing
In the past, when the majority of cleaners and lightweight iron phosphates were powder chemicals, automatic dosing was the exception rather than the rule. However, in recent years the trend has been to liquid chemical concentrates, which has resulted in the increased use of automatic dosing equipment.
As the name implies, this is achieved by using dosing pumps which dose the chemicals on a predetermined time scale. The solution strengths are regularly checked and the timers adjusted.
Brian Carroll comments: “Having introduced automatic dosing equipment into many companies, we have not had one single complaint.”
This is carried out by installing an adjustable dosing pump. This is set to administer chemical at a set rate. When the solution strength is checked, the rate can be altered by adjusting the speed control on the pump to cater for any change.
Proportional dosing
On solutions such as rust inhibitors, which do not show a significant pH or conductivity change, a pump can be fitted to the water
overflowing to foul sewer. Historically, it has been used on effluent treatment plants which rely on close pH control to drop out heavy metals and ensure the discharges to foul sewer are in the desired range. This method operates in the same manner conductivity control, whereby the dip cell immersed in the process solution to monitor the solution strength. This obviously reads the pH of the bath and activates the pump of the solenoid valve in the case of rinse control when the set point is reached. Although reliable, this method is not as robust in use as conductivity control. The dip
controlled using conductivity. However, in some instances, pH control is required.
This method of control measures the electrical resistance of the process solution and is known as electrodeless conductivity.
Automatic dosing can be effected in many ways: from a simple dosing pump to a fully integrated computerised system. Typical applications include:
As the name implies, this is achieved by using dosing pumps which dose the chemicals on a predetermined time scale. The solution strengths are regularly checked and the timers adjusted.
This is carried out by installing an adjustable dosing pump. This is set to administer chemical at a set rate. When the solution strength is checked, the rate can be altered by adjusting the speed control on the pump to cater for any change.
This method of control measures the electrical resistance of the process solution and is known as electrodeless conductivity.
The system operates by immersing the dip cell in the process solution, which in turn sends a signal to the electrodeless conductivity controller. When the solution strength falls below the pretermined set point, the dosing pump is activated and supplies chemical until the process is back to strength. The control is very accurate and a digital display of the strength is shown on the control which operates around a narrow range above and below the set point, known as the hysteresis.
When used for rinse control, the units are set on a lower scale and when the set point is reached, this activates a solenoid valve which supplies the fresh water.
On solutions such as rust inhibitors, which do not show a significant pH or conductivity change, a pump can be fitted to the water feed supply which will add chemical at a predetermined ratio. These installations require the regular use of manual input in order to make the adjustments and solution strength variations. However, this is better than chemical checks alone and small manual chemical additions are always better than one large shock addition.
overflowing to foul sewer. Historically, been used on effluent treatment which rely on close pH control heavy metals and ensure the foul sewer are in the desired This method operates in the as conductivity control, whereby is immersed in the process solution monitor the solution strength. reads the pH of the bath and pump of the solenoid valve in rinse control when the set point
Although reliable, this method robust in use as conductivity cells are usually glass and are The dip cells require calibrating basis and have a limited life.
The system operates by immersing the dip cell in the process solution, which in turn sends a signal to the electrodeless conductivity controller. When the solution strength falls below the pretermined set point, the dosing pump is activated and supplies chemical until the process is back to strength. The control is very accurate and a digital display of the strength is shown on the control which operates around a narrow range above and below the set point, known as the hysteresis.
In summary, conductivity control preferred choice and pH control be used when the application use.
With all chemical solutions, titration testing should be carried regardless of the use of automatic equipment. However, there is reduced checking frequency.
When used for rinse control, the units are set on a lower scale and when the set point is reached, this activates a solenoid valve which supplies the fresh water.
Electrodeless conductivity control is well practiced and proven within the pre-treatment industry, proving to be extremely reliable in service. The instrumentation is sound and the dip cells very robust, which after the initial calibration require little maintenance apart from regular cleaning of the contact area.
The units can be supplied as stand-alone or integrated into a fully controlled computer program.
Moving on from this are control systems that are fully automated and which require the use of conductivity or pH sensors to be fitted in the process solution. Process solutions on pretreatment plants are normally
Electrodeless conductivity control is well practiced and proven within the pre-treatment industry, proving to be extremely reliable in service. The instrumentation is sound and the dip cells very robust, which after the initial calibration require little maintenance apart from regular cleaning of the contact area.
Automatic control and dosing supply in larger containers, eliminates handling, reduces chemical and and above all gives accurate with consistent results.
The units can be supplied as standalone or integrated into a fully controlled computer program.
The method is used on certain installations where the process solution does not show a conductivity change or where a visual display of the pH is required on a rinse
Over the last 20 years, BC Metal has gained valuable practical through the supply of many pre-treatment installations. As a specialist pre-treatment chemical supplier, we closely the specific needs of its customers. offer a range of pre-treatment from simple dosing pumps to the-art conductivity and pH controllers.
BC Metal Finishing Tel: 01204 495818
The method is used on certain installations where the process solution does not show a conductivity change or where a visual display of the pH is required on a rinse overflowing to foul
Email: brian@bcmetalfinishing.co.uk www.bcmetalfinishing.co.uk
sewer. Historically, it has been used on effluent treatment plants which rely on close pH control to drop out heavy metals and ensure the discharges to foul sewer are in the desired range.
This method operates in the same manner as conductivity control, whereby the dip cell is immersed in the process solution to monitor the solution strength. This obviously reads the pH of the bath and activates the pump of the solenoid valve in the case of rinse control when the set point is reached.
Although reliable, this method is not as robust in use as conductivity control. The dip cells are usually glass and are
very delicate. The dip cells require calibrating on a regular basis and have a limited life.
In summary, conductivity control is the preferred choice and pH control should only be used when the application demands its use.
With all chemical solutions, regular titration testing should be carried out, regardless of the use of automatic dosing equipment. However, there is a case for a reduced checking frequency.
Automatic control and dosing facilitates supply in larger containers, eliminates handling, reduces chemical and water
costs and above all gives accurate solution control with consistent results.
Over the last 20 years, BC Metal Finishing has gained valuable practical experience through the supply of many pre-treatment installations. As a specialist pre-treatment chemical supplier, we closely understand the specific needs of its customers. We also offer a range of pre-treatment equipment, from simple dosing pumps to state-ofthe- art conductivity and pH controllers.
Telephone: 01204 495818
Email: brian@bcmetalfinishing.co.uk
Visit: www.bcmetalfinishing.co.uk
FD Series Packaged Oven/Dryer Burners
•Speci cally designed for process air heating applications in convection ovens and dryers
•High turndown/short ame lengths providing accurate process temperature control
•High ef ciency gas + air modulation, gas only modulation and simple high/low control options
•Heat Input Range: 9 kW – 1550 kW
TX Series Gas Fired Process Tank Heating Systems
•High ef ciency (80%+) heating of all types of spray and dip process tanks
•Compact high ef ciency small diameter immersion tube heat exchangers occupying minimum tank space
•Accurate performance modelling using Lanemark TxCalc design software
•Heat Input Range: 15 kW (1½") – 1150 kW (8")
•Direct red, high ef ciency burner systems, for high volume air heating applications such as paint spray booths, ovens and dryers.
Midco HMA Series Air Replacement or “Make-Up” Air Heating Burners
•Supplied either as Midco burner heads for OEM system integration or as Lanemark DB or FDB complete packaged systems including modulating gas valve trains and controls
•Wide range of ring rates to suit alternative temperature rise and air velocity system requirements
•DbCalc system design software
Advanex Europe has reported its latest leap forward in component cleanliness after its purchase of a MecWash MWX400. Advanex has bought three parts washing systems since initially speaking to the MecWash team in 2012. The upgrades have been required to meet capacity increases and strict requirements of its customers.
“Each of the machines we have purchased from MecWash have provided us with a leap forward in efficiency. The MWX400 has made a substantial difference in the volume and speed of the parts washing at Advanex. The previous MecWash machines exceeded our expectations and the MWX400 has done exactly the same,” said Rob Newham, operations manager at Advanex.
Alan Atkinson, sales manager at MecWash, said: “We were delighted to be chosen to supply another high specification,
high volume parts washing machine. Working with Advanex over the last 12 years has provided our team with a detailed understanding of their cleaning requirements. Choosing the optimum parts washing system was crucial for Advanex to provide consistent component cleaning.
“Many of the products made by Advanex are very delicate, so it is vital the cleaning and finishing process does not cause any damage. We previously worked alongside Advanex to create a bespoke wash chemical formulation for its application. The solution was designed to clean and protect the sensitive components and produce a bright finish. Our machines are some of the most sophisticated, connected parts washing systems in the world and the MWX400 features remote servicing, fault diagnosis, maintenance and management.
“The team at Advanex understand the reliability and cleaning capability generated by a MecWash industrial parts washer. The MWX400 is the most appropriate system to meet the demands of the increased workload and is designed to process the most intricate machined or pressed parts that require the highest standards of cleanliness, finish and dryness,” said Alan.
Advanex Europe is the European Headquarters of the global Advanex Group which has more than 20 operations worldwide. Advanex specialise in metal and plastic components, thread inserts, springs and assemblies, supplying a diverse range of markets, namely medical, aerospace and automotive.
The precision engineering firm bought their first MecWash cleaning system, the AVD 300, to replace an ultrasonic tank system. In 2018, Advanex bought a Duo from MecWash to ensure that the increased levels of demand, and the high-level standards of the cleaning and drying of their complex and intricate machined coiled or pressed medical parts continued. Since then, the business has grown substantially as demand for their quality medical products has increased, thus the need for a continual improvement in cleaning productivity over the last decade.
The cleaning capability of all the MecWash systems has impressed Rob Newham, who understands the importance of regulatory adherence for his customers.
Rob said: “The MWX400 is the most advanced of the MecWash machines, and as a long-time customer, it was the best choice to satisfy our high-volume production requirements. The machine meets and surpasses our requirements and more by giving a controlled, validated outcome on each cycle.
John Pattison, managing director of MecWash, said: “The purchase of the MWX400 and the continued relationship with a loyal customer such as Advanex is further proof of the effectiveness of a MecWash system.
“We have a proud history of repeat business due to the excellent cleaning standards that our industrial parts washing systems provide. Our engineers design and build the systems to tackle the most difficult industrial cleaning challenges from across manufacturing. We work closely with our customers throughout all stages of the manufacturing to ensure we achieve the best results possible, rather than ‘one size fits all’. This approach has resulted in a large number of long-term relationships with our customers.
“Customers trust us because we take the time to understand their needs and continue to provide support to them throughout the product life cycle. Investing in a MecWash system generates significant benefits for manufacturers, with measurable improvements in cleanliness and productivity,’ said John.
For further information about MecWash Systems Limited please
Proper material selection and surface treatment are critical to ensure the strength, durability and safety of metal structures in a variety of environments. This content has therefore been developed as a precursor to an ongoing project to investigate and provide insight into the most appropriate material and surface treatment method.
The first step in the process requires extensive research into typical materials, surface treatments and types of corrosion common to the coatings industry. It is known that the appropriate combination of materials and surface treatments can significantly improve the durability and performance of metal structures. Following the research phase, the appropriate material for the process is selected, taking into account
factors such as mechanical strength, corrosion resistance, ductility (flexibility), toughness, weldability, density and price of materials.
Continuing with the project, the next step is to determine the most appropriate surface treatment method for the material based on various factors such as the environmental conditions where the structure will be applied, performance requirements, cost and availability of the process. It is also important to evaluate the performance of the selected material under different environmental conditions. It is then necessary for the continuation of the process to determine whether the selected material is suitable for its intended use.
Thus, in the last step of the project, sustainability and circularity are analyzed. In this context, energy consumption, CO2 emissions, raw material availability, transportation and the reuse potential of the material are evaluated.
The coatings industry is increasingly focusing on surface enhancement engineering solutions to reduce wear, friction and corrosion. Surface enhancement engineering entails modifying the surface of a material by thermochemical heat treatment such as thermal spray, PVD, plasmaenhanced CVD and nitriding, or additive methods including nitrocarburizing.
Depending on the specific environmental conditions and application requirements, special surface treatments and their application sequence may vary.
It is also important to apply surface treatments prior to joining to remove contaminants and oxide layer that can inhibit adhesion and compromise the strength and durability of the joint.
In general, three types of surface preparation methods are used. The surface preparation method can be selected and applied according to the material structure and capability.
Dipping type surface pre-treatment
Spray-type surface pretreatment
Manual type surface pretreatment
In all three applications, chemical processes can be applied according to the expectation or specification.
These can be degreasing (alkaline or acidic), iron phosphate, etching, zinc phosphate or nano ceramic coatings.
To ensure that the surfaces are
optimally prepared for adhesion, these processes determine the processes to be followed, which have a significant impact.
You can contact us to have systems and lines that enable the material surface to be treated, cleaned, coated and made ready for coating with
appropriate chemical processes in order to perform a quality process for the product to be painted or coated.
Email:
SurfacePrep UK is excited to highlight its dedicated hire division, based in Newcastle. This well-established service provides a comprehensive range of surface preparation equipment and support, tailored to the needs of both large and small industrial projects. Following a recent initiative, the company has invested significantly in its equipment and a specialised workforce to ensure customers can access the best tools, expertise and advice available.
The hire division at SurfacePrep UK offers an extensive catalogue of equipment designed to meet the diverse needs of surface preparation, blasting, and paint spraying projects. From portable blasting machines to paint fume extraction systems, SurfacePrep UK’s fleet is fully equipped to handle all types of industrial requirements. Customers can expect:
Portable Blasting Equipment:
Ideal for surface preparation across a range of materials, SurfacePrep UK provides a variety of portable units, including blast-and-vac systems for dust-free operations.
Doosan Diesel Compressors:
For powering blasting and painting tools efficiently, these compressors are available on flexible hire terms.
Air Lines, Hoses, and Safety Gear:
SurfacePrep UK also supplies a full range of safety and supplementary equipment, such as blast helmets and breathing air filters, ensuring compliance with health and safety standards.
Wet Paint Spray Equipment:
From electric to petrol and air-driven models, customers can select the most suitable unit for their specific paint spraying needs.
Generators, Heaters and Dehumidification:
SurfacePrep UK has a range of these to support full hire projects.
The company’s hire service also features specialised equipment, including wet blast units, abrasive recovery systems, and portable dust extraction solutions. This comprehensive range ensures that all aspects of a project, from surface preparation to surface finishing, are fully covered.
One of the standout features of SurfacePrep UK’s hire service is its flexibility. Whether a customer requires equipment for a short-term project or needs it on a longer-term basis, the company offers adaptable hire agreements. This ensures that clients have the right tools for the job without overcommitting, providing both cost-effectiveness and operational efficiency.
Hiring equipment gives customers access to premium tools without the significant capital expenditure associated with purchasing. This makes it an ideal solution for businesses that only need specialised machinery occasionally, reducing overheads while maintaining productivity.
SurfacePrep UK’s dedication to customer service goes beyond just providing the right equipment. The company offers full support to ensure the successful execution of any project. This includes nationwide delivery and collection, ensuring that no matter where a project is located, the required tools will arrive on time and be collected promptly once the work is completed.
Additionally, SurfacePrep UK provides expert advice, including site surveys and equipment setup support. The company’s experienced team is always on hand to recommend the most suitable equipment for each project and to offer training to ensure the machinery is used correctly.
SurfacePrep UK’s hire division is a core part of the company’s ongoing investment in innovation and customer service.
For customers seeking efficiency, flexibility, and expert support, SurfacePrep UK’s hire service is the ideal partner. As the company continues to expand its offerings, clients can be confident they will have access to the latest technology and equipment
for all their surface preparation and finishing needs.
To find out more about SurfacePrep UK’s equipment hire services and how the company can support your next project contact the hire division on 0191 415 3030.
we have been working in partnership with a European aerospace manufacturer to deliver a pre-coat surface treatment line for aerospace transmission components.
For this, the process was already defined within the OEM manufacturing manual. Working in partnership we demonstrated how our processes and solutions could keep to the required manufacturing specification and deliver a consistent, controllable, and repeatable process continually and also meet their required throughput.
The process steps needed were as below:
1. Degrease, Rinse & dry following manufacturer
2. Surface prepare the components to achieve a reactive surface for better coating adherence
3. Wash, Rinse & dry prior to coating
To achieve this, we delivered a twostep process. In many cases this could be completed as a one step process, but due to the OEM requirements and aerospace specification a thorough pretreatment was needed.
Step 1 – (Degrease)
We supplied our Vixen AgiSonic gantry tank line. This solution is fully customisable and due to its modular build, it can be specified with the exact number of tanks and stages required and meet the specifications of your process.
In this instance the Tank line was a 4-stage process consisting of:
1. Wash/Degrease tank fitted with
a. Ultrasonics,
b. Heated
c. Oil water separator
d. Constant filtration with weir
e. Closing lid
f. Pumped agitation
g. Auto fill
2. First stage rinse
3. Second stage rinse
4. Drying stage fitted with recirculating dryer to aid flash drying from heated dip stages.
Step 2 – (PreCoat Surface Treatment via Wet Blasting)
We supplied our automated wetblasting single satellite solution.
For this step wet blasting is the preferred method for surface preparation due to the inherent benefits of our wetblasting process and our automatic solutions.
Wet blasting as a process is a clean, consistent and highly controllable process which gives you consistent, uniform and repeatable results every time.
Our Wet Blasting process and solutions are used globally for pre coat processing as wetblasting being highly controllable allows the process to be defined to meet your exact requirements and leaves surfaces very reactive allowing for the highest levels of coating adherence giving increased protection and long useable life on components and tools.
This specific solution and specification was driven by our knowledge and our customers requirements and so we decided on a flexible solution that enables fully automatic processing with the flexibility of a manual processing station also.
The process of wet blasting is a media (aluminium oxide in this case) mixed with water and kept in constat suspension to give an even distribution. This is then pumped to process nozzle where compressed air is introduced to the mixture before exiting the processing nozzles and flowing over the components surface.
To reach the exact surface requirements such as surface roughness maybe or in some cases just visual appearance,
cleaning or material removal there are many parameters that allows us to define the process to achieve this such as media choice, media concentration, air pressure, nozzle specifications and many more that go toward defining the process for you.
After being processed the components are automatically rinsed within the wet blasting cabinet.
For this step the parts are again put through the Vixen AgiSonic gantry tank line but this time not all tanks are utilised. The programme allows for baskets of parts to automatically follow a programme chosen within the HMI. In this case the parts are rinsed and dried missing the wash/ degrease stage prior to being taken straight to coating.
Visit our website www.vixenaquablast.com or scan the QR code to see videos of this equipment plus many more videos and see what applications, and solutions fit your requirements and contact us to setup sample processing of your components at our test centre or to arrange a visit to our experience centre to view our solutions and process.
The requirements for product safety and quality management are stricter in the medical industry than in almost any other. A leading manufacturer of medical endoscopy solutions ensures that the requirements for the final cleaning of coated precision optics are met using the modular UCMSmartLine ultrasonic multi-stage immersion system combined with a customized service concept. This includes regular monitoring of the ultrasound power and frequency with the innovative Acoustic Performance Measurement (APM) system from Ecoclean, which enables contact-free and reproducible measurements.
Olympus Surgical Technologies Europe in Hamburg is the Olympus Group’s European development and manufacturing center for medical technology. The company stands for top performance in diagnostics, therapy, processing and system integration and covers the entire range of state-of-the-art endoscopic applications, from products to procedure-oriented system solutions.
In the manufacture of around 3,500 different medical products, great importance is attached to vertical integration, beginning with the machining of the blanks and ending with the packaging of the finished products. This calls for precision in the micrometer range and demands a wide variety of production systems that must be individually tailored to the respective products. One of these is
a system for the final cleaning of coated precision optics with a diameter of under two to ten millimeters and a length of between 1.5 and 40 millimeters. The optics are used in endoscopes and must meet the highest cleanliness requirements.
For this challenging task, Olympus Surgical Technologies Europe opted for an ultrasonic multi-stage immersion system from the UCMSmartLine series manufactured by Swiss company UCM AG, the division of the SBS Ecoclean Group that specializes in ultra-fine and precision cleaning. The cost-efficient system is based on standardized modules for cleaning, rinsing and drying as well as loading and unloading.
In contrast to hydrophones, the APM system is contact-free and involves no movement, thus enabling reproducible measurements. For the check measurement, the directional microphone is aimed at the respective ultrasonic tank using a mount to record the frequency and pressure level.
With architectural coating specifications now asking for QUALICOAT, should you not be looking to join?
Meet us on stand A14 at Surface World on the 25th to 27th February 2025
EFFICIENT CLEANING AND DEBURRING SYSTEMS FOR VARIOUS INDUSTRIAL PARTS AND COMPONENTS.
Learn more about our products and services: www.ecoclean-group.net
During analysis and evaluation by the software, the measured values are compared with the target parameters defined as reference values for the respective treatment station, in this case the bottom-mounted ultrasonic transducer.
The goods are transported by an integrated automated system, complete with servo drive, which comes as standard. The electrical and control technology is integrated into each unit, dispensing with the need for extra space for a control cabinet. Thanks to the flexible modular principle, systems for pre-cleaning and intermediate cleaning as well as for final cleaning applications with the highest cleanliness standards can be easily configured to suit requirements.
The system supplied to Olympus Surgical Technologies Europe has a total of six wet stations with tanks sized 370 x 420 x 390 mm (L x W x H), with four of these being equipped with ultrasound. Two additional stations are integrated for drying with hot air. The standard automated transport system for advancing parts inside the fullyenclosed cleaning system is fitted with a servo drive. An additional roll-over unit allows the product carriers to oscillate vertically. Depending on the process station - cleaning, rinsing, drying - speeds range from 200 to 1,500 rpm. HEPA filters and two laminar flow boxes above the drying station and the unloading station, which is designed to hold four product carriers, guarantee cleanroom-compliant environmental conditions. After final cleaning, the parts are discharged into a cleanroom.
Integrated modern sensor technology, including sensors for monitoring
temperature and pressure as well as other measured variables such as conductivity, ensure that all relevant process parameters are seamlessly recorded, monitored and documented, thus meeting the stringent requirements governing quality management in the medical industry.
As ultrasonic power and frequency have a significant impact on the cleaning effect, the company decided to have Ecoclean check these key process parameters for correct functioning once a year as part of a service agreement. The check is carried out by trained and competent field service personnel from the machine manufacturer with a portable version of the Acoustic Performance Measurement (APM) system developed by Ecoclean. The APM system offers various advantages over the test foils and hydrophones normally used for these measurements. For example, deviations cannot be detected with sufficient accuracy using test foils. With hydrophones, the sensor must be immersed in the media of each bath. As the immersion depth can vary, measurement results are not reproducible. There is also a risk of contamination being introduced into the baths. In contrast, the APM system
works contact-free and without movement, thus enabling reproducible measurements. The values determined for the practically new ultrasonic units during the Site Acceptance Test (SAT) - using the directional microphone specially modified for this application - will serve as the benchmark for these measurements. The values are measured individually in each ultrasonic tank, thus providing a detailed, meaningful data basis. For the control measurement, the directional microphone is aligned with the respective ultrasonic tank using a mount and records the frequency and pressure level. During analysis and evaluation by the software, the measured values are compared with the target parameters defined as reference values for the respective treatment station. All measurements are documented in reports in PDF file format for seamless verification, and a certificate is issued to confirm the perfect functioning of the ultrasonic system. This also applies to other system components such as sensors for recording the temperature, detergent concentration and pressures, the proper functioning of which is also checked during the annual service visit.
Contact: Ecoclean GmbH, Peter Lamberty, Phone +49 2472 83126, Peter.Lamberty@ecoclean-group. net, www.ecoclean-group.net
Shot peening has established itself in the automotive industry as an indispensable surface refinement operation. For this task a leading German automobile manufacturer integrated the indexing satellite table shot blast machine RST 200-S15 from Rösler into a new manufacturing line for gear components for E-vehicles. The customer decided to purchase the Rösler equipment, because he had excellent experience with machines of the same type regarding productivity, process stability and ease of maintenance.
In the automotive industry shot peening is utilized to induce a compressive residual stress in, for example, gear components and, thus, extend the life span of the material. For this challenging task, the BMW plant in Dingolfing uses satellite table shot blast machines from Rösler, which have been precisely adapted to the customer’s technical requirements. Now, the highly adaptable RST 200-S15 equipment concept was implemented in a new manufacturing line producing gear components for E-vehicles.
The indexing satellite table shot blast machine RST 200-S15 is designed for shot peening of different gear components in short cycle times. The large inspection & maintenance platform allows quick access to all critical machine sections like blast media transport and cleaning, as well as the control panel.
Efficient systems engineering and innovative technologies – powerful and economical
Individual systems engineering and intelligent process solutions –reliable and energy efficient
The full solution provider for 3D post processing equipment and 3D printing services
To safely achieve the peening results -- defined by predetermined Almen values -- in the specified cycle times, the machine is equipped with two high-performance blast turbines, model Rutten Gamma 400 with a drive power of 22 kW for each turbine. The special “Y design of the throwing blades with their precisely calculated curvature guarantees a highly precise media acceleration with maximum throwing speed, producing excellent operational efficiency. Compared to conventional turbines this results in lower energy requirements of around 25 %. Another significant benefit of this clever design is that both sides of the throwing blades can be utilized.
To meet the high standards in the automotive industry regarding process stability and traceability of the manufacturing processes, the controls of the shot peening machine allow the continuous monitoring of all relevant shot blasting parameters. This includes the control of the turbine and satellite RPM, the blasting time and the thrown blast media quantity. Replenishment of the blast media also takes place fully automatically.
Another key advantage of the Rösler shot peening system is its excellent wear protection, and how easy it can be maintained. The machine housing is made from manganese steel. And the immediate blast area is additionally protected with easily exchangeable protective plates made from highly wear-resistant material. The turbines are made of specially formulated high-strength alloys, which offer a
The two high-performance blast turbines, model Rutten Gamma 400, are mounted to doors that can be easily swung out. This technical detail allows quick maintenance of the turbines and replacement of the protective wear plates in the blast chamber.
16 times longer usable life of all major turbine components. Quick and easy accessibility to all maintenance and service points of the shot peening machine are another key feature of the RST 200-S15.The turbines are mounted on doors that can be easily swung out. This facilitates maintenance work on the turbines, for example, turning of the throwing blades, and allows easy access to the blast area for exchanging the protective wear plates. The machine sections for blast media transport and cleaning, as well as the control panel can be easily reached through the large inspection & maintenance platform.
Visit: www.rosler.com
The EcoPaintJet, initially introduced for overspray-free paint application in industrial vehicle painting, is now benefiting other industries. Refrigeration manufacturer PAN-DUR, which insulates glazing for commercial refrigeration equipment. has been using Dürr’s innovative applicator to paint glass surfaces for several months. This technology saves time and materials by eliminating the need for individual screens in the screen printing process.
We are all familiar with large refrigeration units from supermarkets: wall shelving, cabinets, or counters, behind whose glass or plastic panels a wide range of foodstuffs are stored. PAN-DUR uses enhanced safety glass
(ESG) for its glass elements. Opaque decorative stripes are applied to obscure unsightly bonded and sealed seams at the edges of the glass and the refrigeration technology behind them. Until now, PAN-DUR used a
screen printing process for this, which required a new screen or template for each colour, size, and design variation.
The EcoPaintJet’s high edge definition paint application without overspray allows PAN-DUR to avoid the complex screen printing process, increasing flexibility and speed in production while reducing paint costs. Each contour is simply programmed and applied in the desired colour to the corresponding predefined area without having to mask the glass surfaces first, eliminating the complex and costly manufacture of individual templates and the need to devote valuable space to storing them.
Dürr not only supplied PAN-DUR with the paint applicator, but also provided all process technology, from the system for extracting paint from the containers to the system for supplying paint to the applicator. The installed components include the Fluid Board colour dosing and colour changing system, the applicator cleaner, and the EcoAUC control unit. PAN-DUR developed a multi-axis portal to mount the EcoPaintJet’s swiveling and height-adjustable application head, seamlessly integrating the process technology. “We linked the Dürr process technology with our system’s interfaces.
The implementation couldn’t have gone any more smoothly,” explains Jens Verhoef, Head of Development of Electrical and Automation Technology at PAN-DUR. The biggest challenge was finding the right paint for use on glass surfaces. Specialist paint company Votteler, a long-standing partner of PAN-DUR, was also involved in the development. Project manager Uwe Schmidt explains: “Painting glass surfaces is extremely challenging. You need specially developed paints whose rheological properties, coverage, and particle distribution are perfectly tailored to the system. This paint system can also be used on other substrates. So, we needed a few practice rounds until we found the right paint.”
Other industrial applications are also possible for the EcoPaintJet, for example, in the timber industry, window or kitchen building, and inpainting railway vehicles. “There is potential for EcoPaintJet everywhere that straight stripes are applied to flat surfaces because that type of painting currently still requires masking. We’re getting many enquiries from different industries,” says Fabian Schilt, Head of the European Industrial Sales Team at Dürr. An additional advantage that makes the whole system attractive for other uses is that all components are ready to integrate into existing production systems.
Visit: www.durr.com
Beverage can makers are set to benefit from AkzoNobel’s thirst for innovation following the launch of new highperformance internal coating technology which is free of all bisphenols, styrene, PFAS and formaldehyde.
The company’s Packaging Coatings business has developed AccelshieldTM 300, an inside spray coating for beverage cans which goes well beyond established technologies in the industry to deliver advanced corrosion protection, flexibility and sensory performance.
The latest addition to AkzoNobel’s growing portfolio of next generation can coatings, it’s designed to help customers navigate the future regulatory landscape. The new technology has been approved by the US Food and Drug Administration (FDA) and key beverage brands and is also compliant with current and future EU regulations restricting the presence of intentionally added bisphenols, such as bisphenol A (BPA) and bisphenol F (BPF).
“Our Accelshield 300 technology is further proof of our commitment to helping customers make the transition to a bisphenol-free world,” explains Chris Bradford, Marketing Director at AkzoNobel’s Industrial Coatings business.
“We’re providing the market with a more sustainable alternative that comes with even better performance,
and because it far exceeds current regulations, we’re confident this will be a long-term solution.”
As well as providing enhanced production efficiency by curing rapidly – helping to reduce both energy costs and consumption – laboratory and brand testing have also revealed that the Accelshield 300 technology offers improved flavor performance, compared with earlier solutions on the market. Another major benefit is that it seamlessly integrates into existing production lines.
“We’re using our expertise and experience to develop viable and safe technologies that will ensure continuity of supply to keep the can and canning lines running,” adds Bradford. “Our goal is to shape the future together with our industry stakeholders so we can help them stay ahead of the curve and seize the competitive advantage.”
The introduction of the new product closely follows the launch of AccelshieldTM 700 – a styrene-free and bisphenol-free beverage end internal coating – and the AccelstyleTM 100 and 200 overprint varnishes for two-piece aluminum beverage cans, which are free of bisphenols, styrene and PFAS.
Learn more by visiting the AkzoNobel Packaging Coatings websitehttps://packagingcoatings. akzonobel.com/en, where you can also download our white paper - https://packagingcoatings. akzonobel.com/content/dam/ akzonobel-packagingcoatings/en/ homepage/c43395-akzonobelwhitepaperpackaging-v13.pdf on the transition to a bisphenol -free world.
Visit: www.akzonobel.com
As the electronics industry makes use of ever thinner coatings, manufacturers increase their demands on measuring technologies to provide reliable parameters for product monitoring and control. The coating system Au/Pd/Ni is frequently used in the electroplating of leadframes, with CuFe2 (CDA 195) as substrate material. Typical coating thicknesses are between 3-10 nm Au and 10-100 nm Pd. For monitoring the quality of these coating systems, X-ray fluorescence instruments have established themselves as the measurement method of choice.
A series of comparative tests employing other physical measurement methods was used to determine the capabilities of X-ray fluorescence instruments within the mentioned ranges. Sample specimens were measured with the X-ray fluorescence method using the FISCHERSCOPE X-RAY XDV-SDD model, Rutherford backscatter and absolute, synchrotron radiation based X-ray.
Fig. 1: High resolution measurement of an Au/Pd/Ni coating system on a leadframe and presentation of the results with the analysis software, WinFTM®.
For Au coating thicknesses of about 4, 6 and 9 nm, the results from the X-ray fluorescence instruments were all between the two other methods, with deviations in the
sub-nm range, confirming not only the low scatter but also the trueness of measurements using X-ray fluorescence instruments. Traceability of the measurement results is ensured by using the FISCHER calibration standards developed specifically for this measuring application. The simple handling of X-ray fluorescence instruments also allows for easy scanning of a specimen to determine the homogeneity of the coating thickness, if required (see Fig. 2).
Fig. 2: Lateral coating thickness distribution of a specimen coated with only a few nm Au.
The combination of state-of-the-art detector technology and the powerful analysis software, WinFTM®, allows for reliable, accurate measurements of coating thicknesses even in ranges below 10 nm. For use on leadframes, the FISCHERSCOPE® X-RAY XDV® -SDD instruments are recommended for relatively normal-sized specimens; for very small structures, the XDV® -µ model, with its special X-ray optics, ensures a very small measurement spot of only 20 µm on the specimen.
For further information please contact your local FISCHER representative:
Telephone: +44 (0)1386 577370 Website: https://www.helmut-fischer.com/
present a hurdle for businesses due to higher costs both in time and budget.
As the UK continues to innovate on its manufacturing processes, metal coatings on plastic substrates have emerged as a fundamental innovation across industries, presenting a multitude of advantages and applications.
Metal coatings on plastics offer unique advantages that combine the best of both worlds—metals provide strength, electrical conductivity, or corrosion resistance, while plastics are lightweight and offer flexibility. Whether to influence wear resistance for tools, robust barrier coatings in electronics, elevation of aesthetics in automotive manufacturing, and even the enhancement of electronic components within semiconductor devices, the interest in applying metal coatings on plastic substrates stems from the desire to achieve precision in thin film deposition with a diverse array of available coating materials. With the rising utility of 3D printing, the precise coating of metallic alloys onto printed polymers has opened exciting avenues where traditional 3D-printed metals
Whilst the application of these coatings has evolved significantly, measuring their thickness and composition has been a challenge, particularly with respect to thin or multi-layer coatings on polymer substrates. Maintaining quality control is critical—too thin a coating may fail to meet performance standards, while too thick a coating may be wasteful and costly. X-ray Fluorescence (XRF) is the preferred method for measuring coating thickness and composition. It works by bombarding the coated plastic with high-energy X-rays, which cause the atoms in the coating to emit characteristic fluorescent X-rays. These emissions are then analysed to determine the coating’s thickness and elemental composition. The process is non-destructive and provides critical data in minutes, whilst avoiding length preparations for more physical observations such as micro-sectioning.
Traditional XRF systems have struggled to keep pace with the increasing demand for high precision in thin film coatings, particularly when it comes to detecting lighter elements or measuring ultra-thin layers. New generation systems such as those of the Bowman XRF series address the limitations of older XRFs by offering major advantages such as:
Using standard solid state silicon drift detectors (SDD) for 5 times higher
Enhanced sensitivity for faster, more accurate measurements
Close-couple geometry layout of the X-ray tube and detector provides lower detection limits, for enhanced precision for even the lightest of common elements (i.e., 13Aluminium)
For professionals working in high performance industries such as automotive, aerospace, and electronics, having the best-in-class equipment at their disposal offers a competitive advantage. It is here where SciMed and Bowman XRF offer a complete solution for speed, reliability, accuracy and precision.
For more information, or to arrange an equipment demonstration, email enquiries@scimed.co.uk or call 0161 442 9963. www.scimed.co.uk
Steel Shot (High & Low Carbon)
Steel Grit
Stainless Steel Shot and Stainless Steel Grit (Cr & Cr/Ni)
Chilled Iron Grit
Glass Bead
Ceramic Bead
Fused Alumina Cut Wire
www.ampereabrasives.com
sales.uk@ampereabrasives.com
Tel : 0121 244 1809
17 School road, Hall Green Birmingham B28 8JG
High Carbon Steel shot and Grit.
Low Carbon Steel Shot and metal Bead
Stainless Steel Cr and Cr/Ni.
No 5, Queensway Link Industrial Estate
Stafford Park 17, Telford, Shropshire TF3 3DN
Tel: 01952 299777
Fax: 01952 299008
E-mail: sales@pometon.co.uk
Scangrit has become one of the leading suppliers of blasting abrasives by meeting the rigorous demands of European Industries.
We
you
Eastfield Road, South Killingholme, N.E. Lincolnshire, UK
Tel: +44(0)1469 574715
Fax: +44(0)1469 571644
e-mail: sales@scangrit.co.uk www.scangrit.co.uk
www.babcock-wanson.com
• PLANT CONTROL SYSTEMS
• DATA MANAGEMENT SYSTEMS
• BARRELS - PROGALVANO ROTOR
• BARREL AUTO LOADING SYSTEMS
• PROGALVANO FILTERS
• SEMI/AUTOMATIC FILTER SYSTEMS
• CENTRIFUGAL DRYERS La ge Range)
• AUTOMATIC DRYING SYSTEMS
• ROTARY PAINTING/LAQUERING
• TOP COATING/SEALING SYSTEMS
• VIBRATORY POLISHING EQUIPMENT
• LUBRICATION EQUIPMENT
• RECTIFIERS Conventional & Pulse
• A/HOUR METERS & DOSING PUMPS
•
•
•
•
•
•
•
•
•
•
Hot dip galvanizing provides you with long-term protection against rust and corrosion of steel products.
✔ 14 plants across the UK
✔ 1.5mm washer to a 29m beam
✔ 24hr turnaround on request
Scan to find your nearest plant
info@wggltd.co.uk 01902 601944
telephone: 0044(0)1509 237415 fax: 0044(0)1509 264455
• ADVANCED MODULAR RANGE
• SWITCH MODE UNITS
• SCR RECTIFIERS
• PULSE RECTIFIERS
• RAMP CONTROLLERS
• PROCESS PARAMETER PRINTING
• SPECIAL COMPUTERISED RECTIFIERS
• OPERATOR GUIDANCE SYSTEMS FOR ANODISING & PLATING
• A/HOUR METERS & DOSING PUMPS
• METERS
• SHUNTS
• PLANT CONTROL SYSTEMS
• DATA MANAGEMENT SYSTEMS
RDM Industrial Services Ltd
Parkfield Industrial Estate
Kemp Street
Middleton
Manchester M24 4AA
Tel: 0161 643 9333
Fax: 0161 655 3467
www.rdm.u-net.com.
Contact: Robert Horwich or Geoff Ball
Spraybooths, rooms, ovens, conveyors, pretreatment, powder plant and air replacement units.
Final Cleaning • Spray Wash
In-process Cleaning
Aqueous Ultrasonics
Precision Cleaning • FPI Lines
Degreasing • Anodising
Chemical Cleaning for MRO
Chemical Etching/Milling
E sales@turbex.co.uk
T 01420 544 909
F 01420 542 264 turbex.co.uk
8 Valley Works, Grange Lane, Sheffield, S5 0DQ, United Kingdom
Table Wheel Blasting Machines
• Work zone mm; 1803 Dia x 1500 H
• Work zone mm; 2743 Dia x 400 H
• Work zone mm; 1500 Dia x 1000 H
• Work zone mm; 1000 Dia x 400 H
• Work zone mm; 1200 Dia x 1200 H
• Work zone mm; 1100 Dia x 500 H
• Work zone mm; 500 dia
• Work zone mm; 1250 dia x 500 H
Tumblast Wheel Machines
• Type; Rubber Belt
Volume Litre; 420 Litre
• Type; Steel
Volume Litre; 425 Litre
• Type; Rubber Belt
Volume Litre; 50 Litre
• Type; Rubber Belt
Volume Litre; 150 Litre
• Type; Rubber Belt
Volume Litre; 170 Litre
• Type; Rubber Belt
Volume Litre; 180 Litre
• Type; Rubber Belt
Volume Litre; 50 Litre
• Type; Rubber Belt
Volume Litre; 80 Litre
• Type; Rubber Belt
Volume Litre; 170 Litre
• Type; Steel Segment Barrel
Diameter; 36”
Hook Wheel Machines
• Type; I Track
Work Zone mm; 1800 Dia x 1800L
• Type; Y Track
Work Zone mm; 1500 Dia x 1700L
• Type; Y Track
Work Zone mm; 800 Dia x 1200L
• Type; Y Track
Work Zone mm; 1100 Dia x 1600L
Roller Conveyor Wheel Machines
• Type; Roller Conveyor
Work Zone mm; 1000 x 500
Wheel No; 4
• Type; Roller Conveyor
Work Zone mm; 1500 x 410
Wheel No; 4
Air Blast Hand Cabinets
• Type; Pressure
Work Zone mm; 900W x 600D x 350H
• Type; Pressure
Work Zone mm; 900W x 700D x500H
• Type; Pressure
Work Zone mm; 900W x 700D x500H
• Type; Pressure
Work Zone mm; 900W x 700D x500H
• Type; Suction
Work Zone mm; 700W x 500D x400H
• Type; Pressure
Work Zone mm; 800 Dia Turntable
• Type; Pressure
Work Zone mm; 500 Dia Basket
• Type; Pressure
Work Zone mm; 1200 x 750 x400
• Type; Suction
Work Zone mm; 700W x600D x300H
• Type; Pressure
Work Zone mm; 600W x 500D x 400H
• Type; Pressure
Work Zone mm; 1400W x 700D x 600H
Blast Rooms
• Work Zone mm; 4000L x 2000W x 2000H
Type; Room
Abrasive Recovery; Waffle Floor
• Work Zone mm; 4000L x 2000W x 2000H
Type; Room
Abrasive Recovery; Waffle Floor
• Work Zone mm; 20ft x 8ft x 8ft
Type; Container
Abrasive Recovery; Sweep Up
Dust Filters
• Various Types & Sizes