
14 minute read
PEX Quickens Renovation
by IdeaSoil
PEX Quickens Renovation Gut-renovating 235 units on 10 floors, while the Hollywood Roosevelt Hotel continued to operate, was no easy task.
Marilyn Monroe once resided at the iconic Hollywood Roosevelt Hotel, which received a new plumbing system as part of piecemeal, gut renovation that took place while the facility was operational. Shown is the renovated Marilyn Monroe suite. Photos: Hollywood Roosevelt Hotel A ny large-scale, commercial-building renovation brings its own special construction challenges. When the structure is an 87-year-old icon—the birthplace of the Academy Awards, the one-time residence of Marilyn Monroe, and with a David Hockney painting on the floor of its swimming pool—the game inevitably jumps several notches.
Advertisement
“Historic renovations can be tough because of all the limitations on how much you can change the existing structure, its façade, or even certain interior finishes,” commented Mark Shamim, whose Tarzana, CA-based firm, Shamim Engineering, was involved in the recently completed renovations at the Hollywood Roosevelt Hotel in Los Angeles.
Beyond historical concerns, the renovations at the venerable Roosevelt added one more layer of complexity and interest; they happened while the hotel remained open for business, operating at a capacity level of around 90%—at least for those rooms that were available.
“For our engineering firm,” continued Shamim, “one of the biggest challenges of this landmark project was designing and installing a new plumbing system” as part of a piecemeal, gut renovation of an operational facility. Spanning a projected 18 months from 2013 through 2015, the work had to be done in an unobtrusive manner that would never inconvenience—or even be noticeable to—hotel visitors and guests.
This reality led to the choice of plastic piping, rather than copper, to re-pipe all 235 guest spaces. Rigid, heat-fusion welded, polypropylene-random (PP-R) piping was used for larger-diameter lines in the mechanical room and for the vertical risers from the ground level to the 10 guest floors. In the corridors and inside the guest rooms themselves, flexible cross-linked polyethylene (PEX) piping connected the toilet, sink, and tub/shower to the risers. In all, roughly 14,300 ft. of Uponor Inc., Apple Valley, MN, PEX—in six different sizes, from 1/2 through 2 in.—were installed at the Roosevelt.
The branch lines from the corridor piping were “straight runs with no line breaks and, therefore, no need for making connections that would slow the installation,” explained Andrew Valenzuela, director of field operations for the general contractor, City Constructors Inc. (CCi), Los Angeles. “With copper, there would have been so much more cutting and soldering, which would have added significant amounts of labor and materials. Also, with PEX, relocating a run or a stub-out because of an error or miscalculation is so much faster and easier.”
Valenzuela said the decision to go with PEX significantly cut installation time on the project. “Copper has its place, but with all the tight spaces we must inevitably run our plumbing through, PEX is so much better,” he said.
DECADE OF RENOVATIONS Originally constructed in 1927 by a group that included Hollywood luminaries of that era—Mary Pickford, Douglas Fairbanks, and Louis B. Mayer of MGM Studios—the Roosevelt Hotel is located in the heart of the entertainment district, situated on
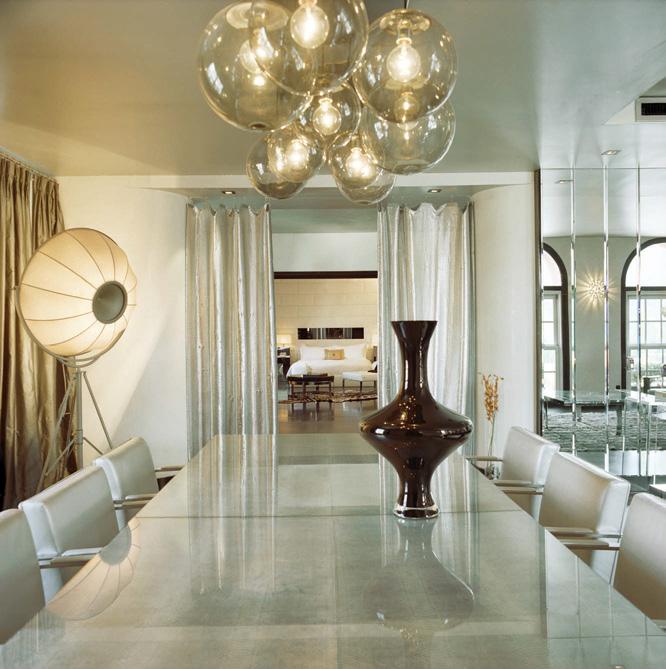
Spanning 18 months, the plumbing work had to be done in an unobtrusive manner that would never inconvenience, or even be noticeable to, hotel visitors and guests.

Rigid, heat-fusion welded, poly-propylene-random (PP-R) piping was used for larger-diameter lines in the mechanical room and for the vertical risers from the ground level to the 10 guest floors.
Hollywood Boulevard across the street from Grauman’s Chinese Theater Restaurant and the Hollywood Walk of Fame. Now owned by Thompson Hotels, the structure has been undergoing stem-to-stern renovations for the better part of a decade, including an updating of the Blossom Ballroom where the inaugural Oscars ceremony was staged in May 1929. (Best Picture: The World War I romance “Wings,” starring Clara Bow, Buddy Rogers, and Richard Arlen.)
CCi, whose renovations portfolio includes historical gems such as the Rowan Lofts, the El Dorado, and the Douglas Building, all in downtown Los Angeles, has served as the construction manager and general contractor for all the construction work at the Roosevelt since it commenced in 2005. The most recent phase consisted of a complete makeover of all the guest rooms on floors 3 through 12 in the building’s T-shaped tower.
According to CCi’s Valenzuela, the renovations involve getting the rooms down “almost to the bare structure,” encompassing all new walls and paint, new electrical service, and a new heat pump for heating and cooling each room. Over its previous nine decades, the hotel had never undergone a remodeling this extensive.
“Of course, the building was redecorated many times with new paint, new carpet, and so forth,” said Valenzuela. “When we opened the walls of the guest rooms, it was a little scary. And when we found three layers of tile, we briefly considered simply adding onto those layers, but we knew that wasn’t the right approach. So we decided to strip it down to the bones to get everything true, square and, ultimately, right.”
“Right” has multiple meanings and benefits, depending on what is being made over. For example, the new heat pumps will not only make the room environments more comfortable, but also eliminate the irritating mechanical noise of the older equipment. How bad was it? Enough that certain rooms were rigged with sliding “barn doors” several inches thick to help block the noise of the old heat pumps located in the ceilings.
To further mute noise between guest rooms, all common walls were rebuilt with a 1/2-in. acoustical board and 5/8 in.-thick drywall. In addition, an air gap between these two layers and the metal stud further dampens sound between the rooms. “The layers and that gap make a big difference,” said Valenzuela.
BUSINESS AS UNUSUAL As noted, the biggest challenge for CCi, specifying engineer Shamim, and the various subcontractors involved was “changing the tires of a moving vehicle;” that is, remaking every single room while the hotel remained open for business.
Beginning in September 2013, the guestroom makeovers were scheduled in five phases. Work commenced at the top of the Roosevelt’s T-shaped towers on floors 11 and 12. Once these rooms were done in four months, the crews moved to floors 8, 9, and 10. In September 2014, activity finally shifted to the lower levels, floors 3 through 7. Throughout these months, hotel guests stayed either in renovated rooms or in rooms yet untouched.
“At the outset, we worked on two floors at once, while leaving a buffer floor between the parts we were tearing up and the floors where guests were staying,” said Valenzuela. “But after a while, to accelerate the timetable and lower costs, we started doing ‘quiet’ work on the buffer floor. From that point onward, we were effectively working on three levels at once.”
Keeping the guests all but oblivious to the construction happening around them took careful planning and, above all, close and frequent internal communications, according to Valenzuela. “At a minimum, we met twice daily with the building engineer Randolph Caravantes and the head of guest services Ingrid Braun,” explained Valenzuela.
TIME FOR A CHANGE The decision to gut-renovate the Roosevelt opened the door for a full-scale replacement of the existing plumbing infrastructure. Prior to this total rehab, chief engineer Caravantes had been changing out the original galvanized piping for copper piping on a piecemeal basis, but with less-than-happy results.
“With the old system, the copper lines frequently came in contact with the electrical lines,” said Caravantes, who explains that this contact generated an electrostatic charge in the water running through the copper, causing
In the corridors and inside the guest rooms themselves, fl exible cross-linked polyethylene (PEX) piping connected the toilet, sink, and tub/shower to the risers. In all, roughly 14,300 ft. of Uponor PEX in six different sizes was installed at the Roosevelt.

turbulence and, ultimately, pinhole in the pipe leaks.
“We have replaced certain sections of copper piping three or four times, but pinholes continue to develop,” he continued. “Those lines were the first we replaced with PEX, which is not affected by contact with the electrical lines.”
Once the decision was made to redo all the guestroom plumbing— behind and in front of the walls—CCi studied several material options with the goal of shrinking installation time and installed costs as much as possible. Shamim Engineering took a consultative role in the research, according to Mark Shamim, “We helped them to make an educated decision, but the final choice was the general contractor’s.”
Shamim attributes the rising PEX trend in his locale to several factors. It is no longer difficult to find a competent installer. A half-decade ago, not enough contractors had been properly trained to install PEX in the Los Angeles market. That has changed in recent years, thanks to the efforts of PEX manufacturers and their local sales and technical reps. “Today, the majority of Los Angeles mechanical con
Want more information? The resources below are linked on our website at commercialarchitecturemagazine.com and our digital magazine at commercialarchitecturemagazine.com/digital/apr2016
Circle 6 on the Reader Service Card.
See a video about the renovation of the Cavalier Hotel.
Watch a video on PEX piping systems. Learn about Uponor design services.
Download a design manual.
Download an installation guide. tractors are familiar with PEX,” said Shamim.
Plan checkers and project inspectors are also more familiar with PEX. Building officials with the City of Los Angeles and other neighboring communities have also become more aware of—and more comfortable with—the use of PEX for commercial plumbing. This is good news for developers and general contractors, who do not relish spending long hours fighting with government officials on behalf of their buildings’ specifications.
Securing material approvals from the Building and Safety Division of the Los Angeles County Dept. of Public Works is “the main job we do,” according to Shamim, who added that the use of PEX at the Roosevelt “went through in about a month without any issues, problems, or corrections. It was very smooth”—no small accomplishment, given how strictly Los Angeles enforces its codes.
This track record of success is also due, in part, to the care and attention that is paid to proper system design. When converting a system from copper to PEX, the designer must incorporate the flow characteristics of PEX into the system design and system sizing. For example, when comparing nominal pipe sizes, PEX has a slightly smaller internal diameter (ID) than copper due to the thicker pipe wall of PEX. Because PEX is not susceptible to pitting, corrosion, or scaling like copper pipe, its smooth inner wall can allow higher design velocities. Thus, each segment of pipe is resized to accommodate the friction-loss characteristics of PEX, resulting in certain PEX segments being sized differently than copper segments.
In addition, the flexible nature of PEX and the long coil lengths eliminate most couplings and elbows for runs of 1/2 to 1 in. This results in less pressure loss associated with fittings, as well as greater time and material savings. For Roosevelt’s plumbing system design and system sizing, Shamim worked closely with local manufacturer’s representative Phil Valles of Keyline Sales Inc., Downey, CA, and used the Uniform Friction Loss method. (Note that PEX pressure-loss tables can also be found at www.uponorpro.com/calculator.)
PEX offers substantial savings in material and labor costs. PEX pipe and fittings offer significant savings over their copper-plumbing counterparts, whether the latter involves press-type or sweat connections. Factor in the reduced labor—from not having to create a connection every time the pipeline changes direction—and the overall savings to the building owner is even greater.
SECURING THE GUEST EXPERIENCE Now that the hotel is fully operational again, guests and visitors—celebrity and non-celebrity alike—are free to be enthralled by the new décor, the plush accommodations, and the many attractive amenities of the renovated Roosevelt. And while most will appreciate the new fi xtures on the front side of the bathroom wall, they aren’t likely to spend much time contemplating what’s happening, out of sight, behind those walls.
You don’t need to persuade Valenzuela of the long-term value of this plumbing infrastructure. “When we envision the ‘guest experience,’ of course we think about all the beautiful finishes and furnishings in a hotel room,” he said, “but having that toilet always flush, having hot water immediately, having the sink and the shower drain quickly and quietly—that’s also part of a quality guest experience, even if not fully visible. Should something go wrong, that infrastructure will become ‘visible’ to the guest quickly enough. Our goal is to minimize those future complaints as much as possible.” CA
High School Is Home To Hybrid HVAC
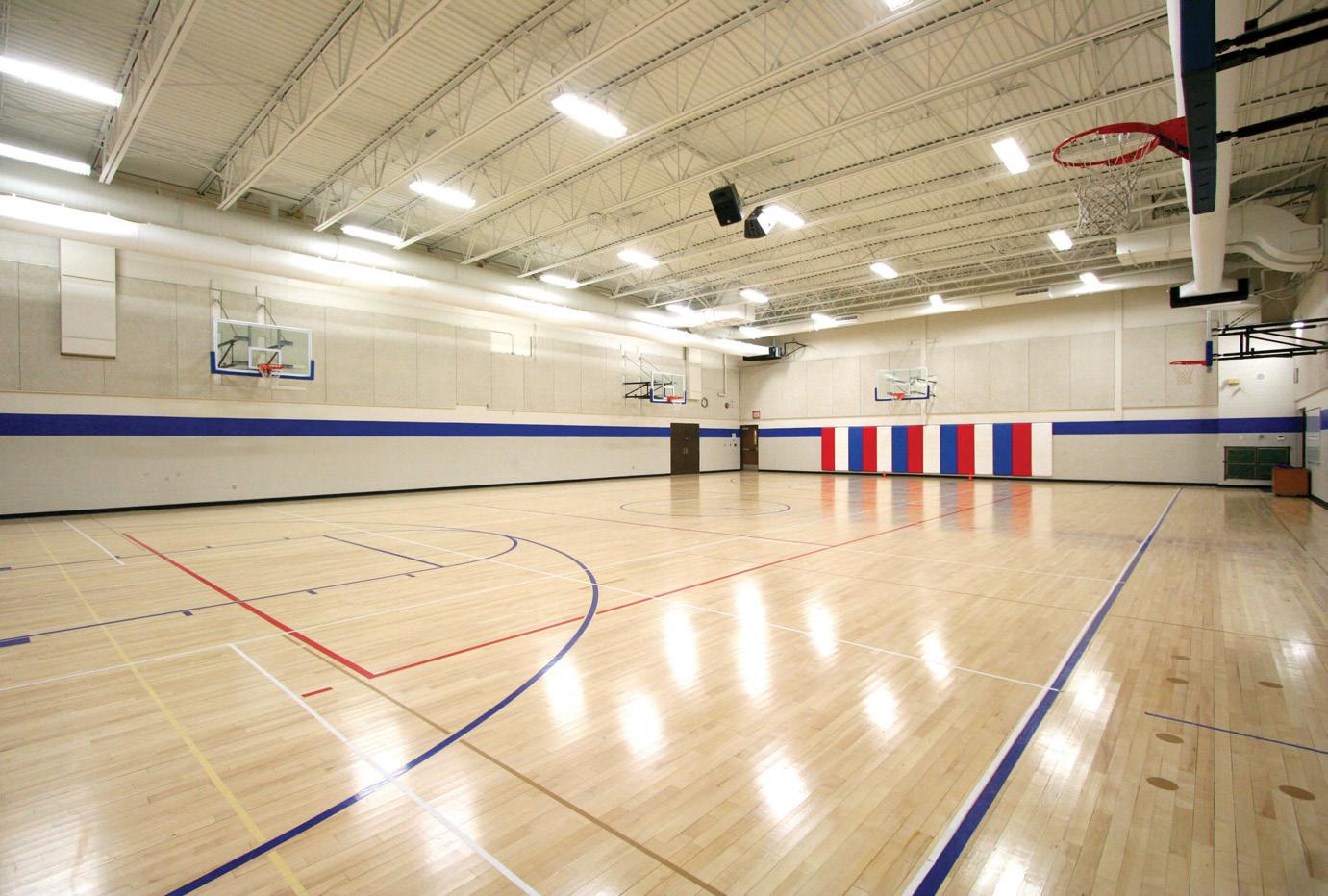
The HVAC system at an Iowa school was upgraded while classes were in session, incorporating VRF technology from LG with the geothermal system.
The building presented unique heating and cooling challenges for zoning needs. For example, the gym required a different temperature than that of the classrooms. S everal key structural and operational challenges were addressed during the renovation of Decorah High School, Decorah, IA.
First, given the project schedule, the heating, ventilation, and air-conditioning (HVAC) systems had to be installed while classes were in session, and installation had to be completed in staggered phases to meet deadlines.
Second, the design of the building presented unique heating and cooling challenges for zoning needs. For example, the gym required a different temperature than that of the classrooms. Finally, the Decorah renovation needed a system that could integrate seamlessly with its hybrid geothermal system.
To best meet the HVAC needs of the high school’s unique building, the installing contractor, Casper Plumbing and Heating, Decorah, along with DPT Mechanical, Urbandale, IA, were hand-selected to provide a heating and air-conditioning system that would allow independent, temperature-controlled environments for learning and extracurricular activities. Variable-refrigerant-flow (VRF) air-conditioning solutions from LG Electronics, Englewood Cliffs, NJ, were selected. In addition to the lower-refrigerant piping-installation costs, and the hybrid heat-recovery system offered, the system was able to provide simultaneous heat
Right. The VRF systems lend themselves well to phased installation, as they are installed and commissioned as individual systems in their respective areas of the building.
Bottom Right. The LG Multi V Water II VRF systems take advantage of the ground source while including the added benefi t of a VRF system.
ing and cooling to flexibly match loads in all seasons.
The VRF systems lend themselves well to phased installation, as they are installed and commissioned as individual systems in their respective areas of the building. With school being in session, this helped in executing the renovation in phases. DPT Mechanical and LG staff conducted several onsite VRF training sessions and followed a strategic approach in working in specific areas of the school at certain phases of the renovation. This staggered process required an efficient solution to work around school being in session. The team also conducted weekly site checks and visits to assess progress and make adjustments to the process as needed over the course of the three-year installation timeframe. The team phased in a flexible installation and pipe system because of school hours and chose products that would operate more efficiently than the school’s current system.
To ensure independent, temperature-controlled, energy-efficient spaces for a variety of student activities, LG VRF technology was proposed for simultaneous heating and cooling capabilities. To help maximize efficiency, the installation of the AC Smart II central controller with BACnet gateway was also recommended. The central controller with BACnet gateway monitors the HVAC systems and allows the school to program, control, and schedule heating and cooling for each zone. Additionally, LG programmable thermostats were installed to provide custom temperature control in specific rooms, allowing teachers to adjust classroom temperature accordingly, making it ideal for personalized comfort.
In Decorah High School’s building, LG water-source heat-recovery systems used the multi-port heat-recovery units to move heat from rooms in cooling mode, and then direct it to rooms needing heat instead of returning the heat to the outdoor unit to be rejected, as done in traditional HVAC systems.
Finally, the school was looking for an HVAC solution that integrated with its hybrid geothermal system. The LG Multi V Water II VRF systems were a natural choice to take advantage of the ground source while including the added benefit of a VRF system. These benefits include moving the compressors to the equipment room, zoned comfort controls, and an additional level of heat recovery beyond the ground loop. Ultimately, the water-source unit provided a higher level of efficiency, compared with a conventional air-conditioning system, resulting in energy cost savings year round.
After a three-year phased installation, the Decorah Community School District’s high school is now home to one of the largest hybrid heating-and-cooling systems in the nation. Additionally, the school added top-of-the-line technology to provide a more comfortable learning environment for its students, all while benefiting from overall cost and energy savings. CA

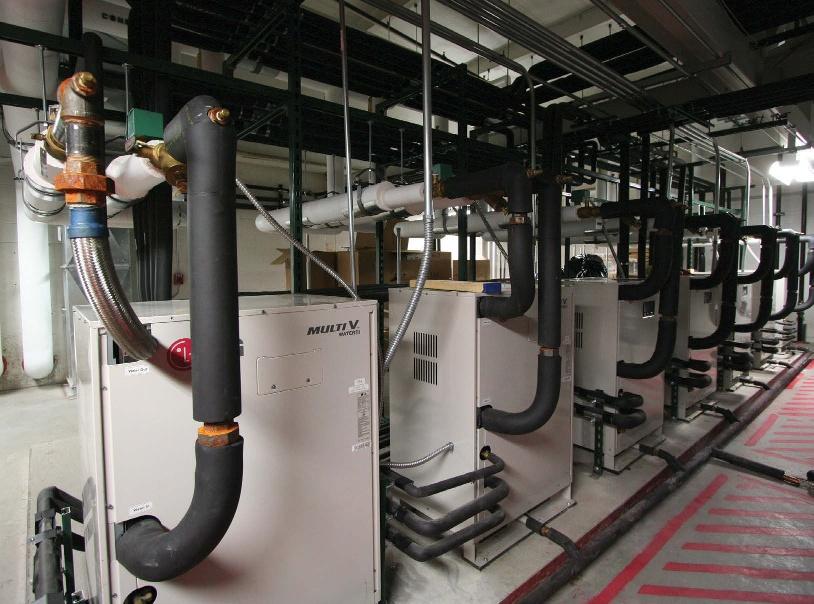
Want more information? The resources below are linked on our website at commercialarchitecturemagazine.com and our digital magazine at commercialarchitecturemagazine.com/digital/apr2016.
Circle 5 on the Reader Service Card.
Get information on the Multi V Water II heatrecovery system. Find out about ceiling cassettes.
See information about wall-mounted units.