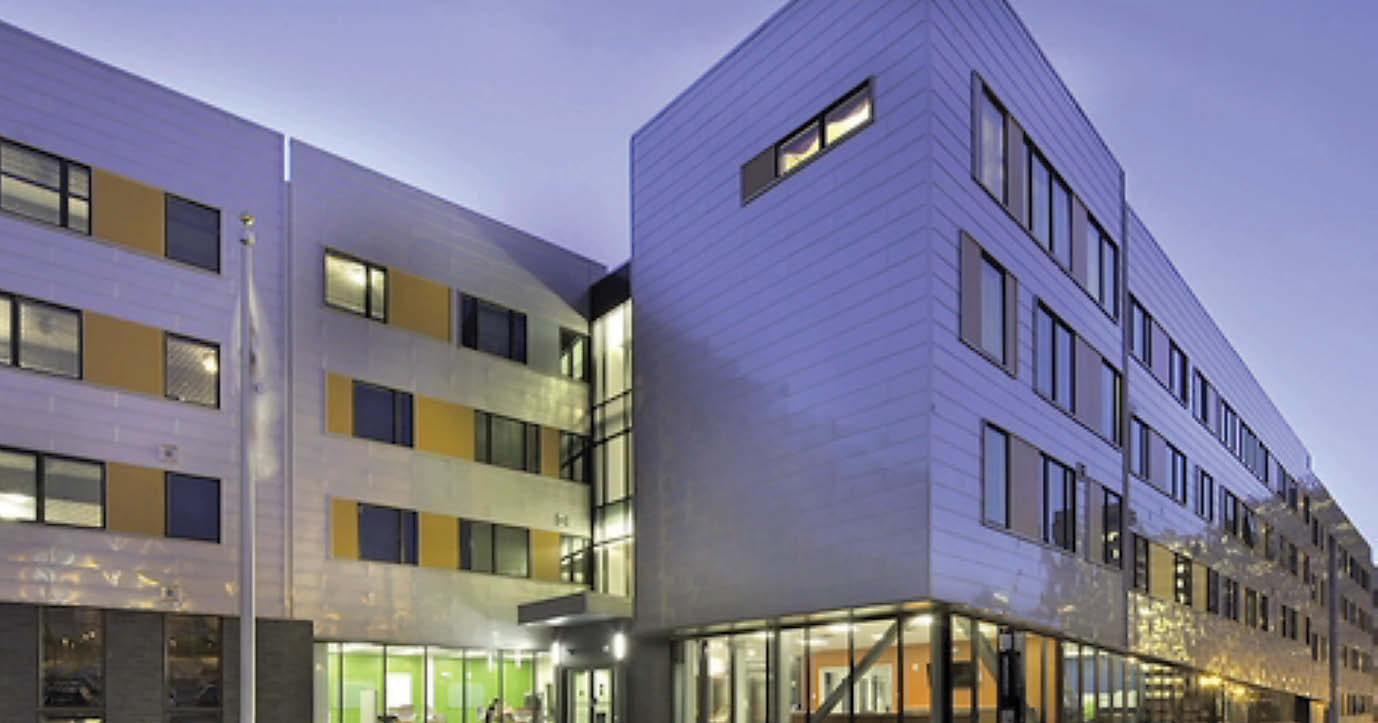
6 minute read
Aerosol Particles Plug Duct Leaks
from commARCH - June 2014
by IdeaSoil
Duct-sealing method meets stringent NYSERDA leak standards of 10 cfm/floor, resulting in a rebate of $150,000.
America’s focus on energy-efficient construction is no accident. Along with increased internal pressure to reduce operational expenditures, programs aimed at incentivizing energy-efficient building practices continue to have a real impact on the construction industry. For the contractors working with Syracuse Univ., Syracuse, NY, it was New York State’s NYSERDA (New York State Energy Research and Development Agency, Albany) program that provided the initial motivation to build green. The program’s high energy-efficiency standards led the SU HVAC team to a duct-sealing technology that ultimately saved the university thousands of dollars in construction costs and earned more than $150,000 in rebates.
Advertisement
General contractor Hayner Hoyt Corp., Syracuse, began construction of Campus West, a residence building for SU graduate students that was scheduled to open in the spring of 2012. To qualify for the NYSERDA program’s $150,000 rebate for new construction, they not only would have to exceed various SMACNA (Sheet Metal and Air Conditioning Contractors National Association, Chantilly, VA) standards for HVAC systems but, in many cases, surpass LEED (Leadership in Energy & Environmental Design, U.S. Green Building Council, Washington) certification criteria. In addition, when it came to HVAC performance, the NYSERDA requirements were, by far, the most stringent, requiring a cfm/floor limit on duct leakage of 10 cfm or less. While meeting this requirement was no easy task by standard practices, the financial rewards were worth the efforts.
The four-story building includes 200 graduate-student apartments. Its massive ductwork system consists of seven individual rooftop energy-recovery ventilation systems. Both the bathroom exhaust and outside air-supply ductwork extend horizontally and vertically to each water-source heat pump HVAC unit and bathroom. Each ventilation shaft is completely sealed in sheetrock and protected with fire/smoke dampers.
METICULOUS ATTENTION PAID Knowing from the start they would need to meet stiff requirements for air-duct leakage, Hayner Hoyt worked with HVAC specialists Century Heating and Air Conditioning of Syracuse to ensure the ductwork was properly assembled from the start. Meticulous attention was paid to connecting joints and sealing seams.
“We really went through super-human efforts when first constructing the ductwork,” said David Wildrick, president of Century. “It was nice, new ductwork when we were finished. It looked beautiful and easily passed SMACNA standards. Still, it didn’t come close to meeting the much more stringent NY
The four-story Campus West, a residence for Syracuse Univ. graduate students, includes 200 apartments. Its ductwork system consists of seven individual rooftop energy-recovery ventilation systems.

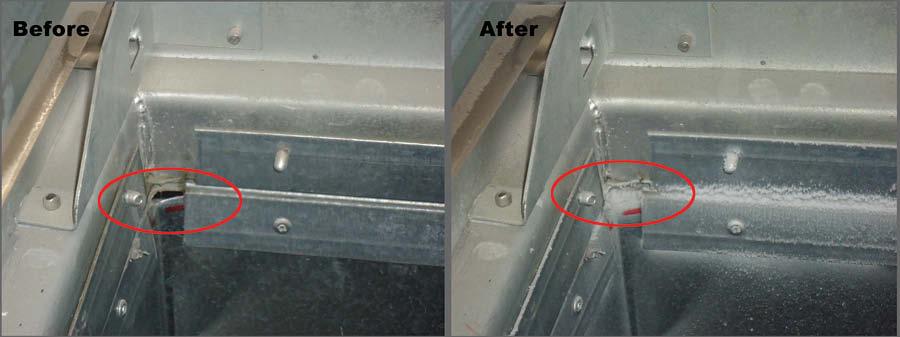
Top. Applied as an aerosol mist, the sealant is heated and blown into the duct shaft through an existing access point or through a temporary entranceway cut into the system.
Above. The adhesive particles remain suspended in air until they reach a leak. Here they begin to accumulate around the leak, bonding to other sealant particles until the entire hole is permanently filled. SERDA requirements being targeted for rebates.”
On average, post-construction tests showed the newly constructed ductwork tested out at an average leakage rate of about 120 cfm/floor—not bad by traditional standards but way beyond the near-leak-free levels required by NYSERDA. By this time, the new drywall was already put in place and most of the ductwork was inaccessible for manual inspection or traditional sealing.
“We were stumped,” said Sam Doss, project manager at Hayner Hoyt. “There were few choices outside of tearing down the newly constructed walls to try and reseal the ductwork or missing the specifications that provided the substantial rebate. Fortunately another option presented itself.”
ALTERNATIVE TO MANUAL SEALING As it turned out, Century Heating and Air was in the process of evaluating a new duct-sealing technology for another project. Developed with funding from the U.S. Department of Energy, Washington, and others, the innovative aerosol-based duct sealant from Aeroseal, Centerville, OH, offered an alternative to manual sealing.
Applied as an aerosol mist, the technology works from the inside of a duct system to seal leaks. The process
begins by blocking the wall registers so that air can only escape through the leaks in the ductwork. The duct system is slightly pressurized to 0.1 in. WC, increasing to a maximum of 3 in. WC during the sealing process. The sealant is then heated and blown into the duct shaft through an existing access point or through a temporary entranceway cut into the system. The dry, 7- to 10-micrometer-sized adhesive particles remain suspended in air as they travel throughout the ductwork until they reach a leak. At a leak point they begin to accumulate, bonding to other sealant particles until the entire hole is permanently filled.
Unlike some sealants, such as those used for weatherization or material bonding, the Aeroseal sealant is a vinyl acetate polymer with a rapid cure rate of approximately 2 hr. The sealant exhibits minimal VOC off gassing, and its non-toxic properties afford it no OSHA (Occupational Safety and Health Administration, Washington) maximum-exposure limitations. Since it was first introduced into the market nearly ten years ago, Aeroseal has been used to seal leaks in school buildings, health clinics, hospital buildings, residences, and other structures.
“For this project, we accessed the ductwork through the roof,” said Wildrick. “The ventilation fans were removed one at a time, and the sealing equipment was connected directly to the exposed shaft where it came out on the roof. Before blowing sealant into the duct system, we blocked all the termination points throughout the building. Now, the only exit points for the sealant would be through the various leaks in the ductwork.”
The HVAC team sealed each of the individual systems one at a time—seven systems in all. Two shafts/systems ran down the four-floor structure and branched out to the individual apartments.
Once the set-up for a system was finished, the actual sealing process took about 20 min. to complete. The computerized process allowed the crew to see the results in real time.
“An initial screen shows a graph with the beginning leakage rate,” said Doss. “As the sealant does its job, you can watch the graph dip lower and lower as leaks are systematically sealed.”
The entire project was completed in about two weeks. Each of the systems tested at or below the near leak-free levels being targeted. “The aerosol sealant provided the lowest leakage rates we’ve seen for any duct system at anytime, anywhere,” said Wildrick. “I don’t know of any [other] way we could have met these stringent requirements.”
“As energy-efficiency standards become increasingly stringent, we will need to turn to new technologies like Aeroseal,” said Doss. “It was a game-changer for this project and a key to our ability to meet the NYSERDA requirements.” CBP
Want more information? The resources below are linked in our digital magazine at cbpmagazine.com/digital/jun2014.
Circle 3 on the Reader Service Card.
Watch a video about the Aeroseal process http://www.aeroseal.com/videos/Commercial%20video%20-%20low-res.mp4 Watch a video about the Aeroseal process
Download SMACNA Technical Paper: HVAC Air Duct Leakage https://www.smacna.org/technical/download.cfm?download_fi le=TRB6_11_Duct_Leakage_Technical_Paper.pdf
Cost & Energy Effi cient Solutions by Bosch
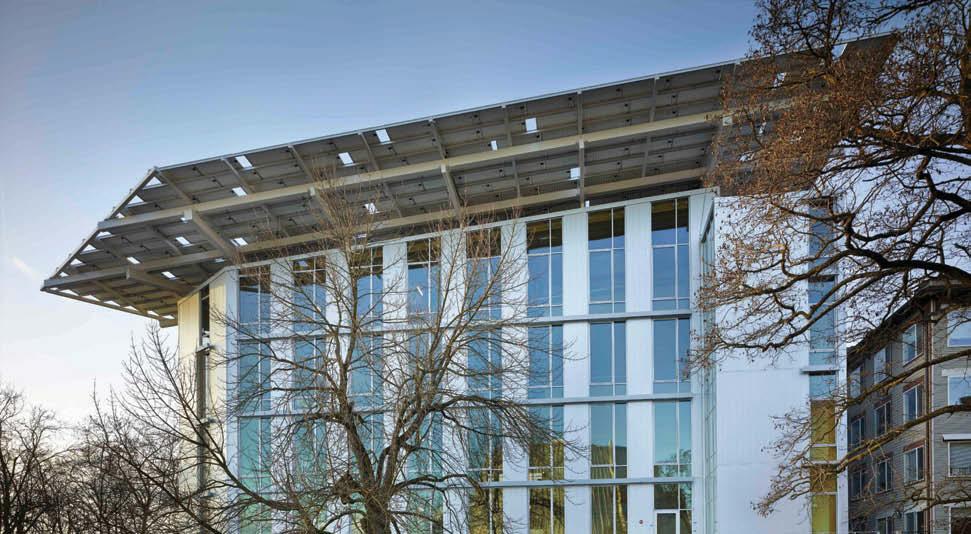
- Justin Stenkamp, PE, PAE
Seattle Offi ce Building Designed to Living Building Challenge Imperatives Bosch Geothermal Heat Pumps Help Achieve Net-Zero Energy Use in Revolutionary Bullitt Center Building*


LM Model commercial heat pumps feature:
Best-in-class 2-stage effi ciency Robust and durable construction with industry leading low sound levels Service friendly features for easy repair and installation Extensive options to meet virtually any jobsite design requirement LEED® compliant to help qualify for the greatest potential of credits with a water source HVAC system
UP TO 32.0 EER Part Load
UP TO 22.0 EER Full Load
Contact your FHP Representative for your next building project TODAY!
fhp-mfg.com or 1-866-642-3198
*Products used in the application cited may vary from those shown.