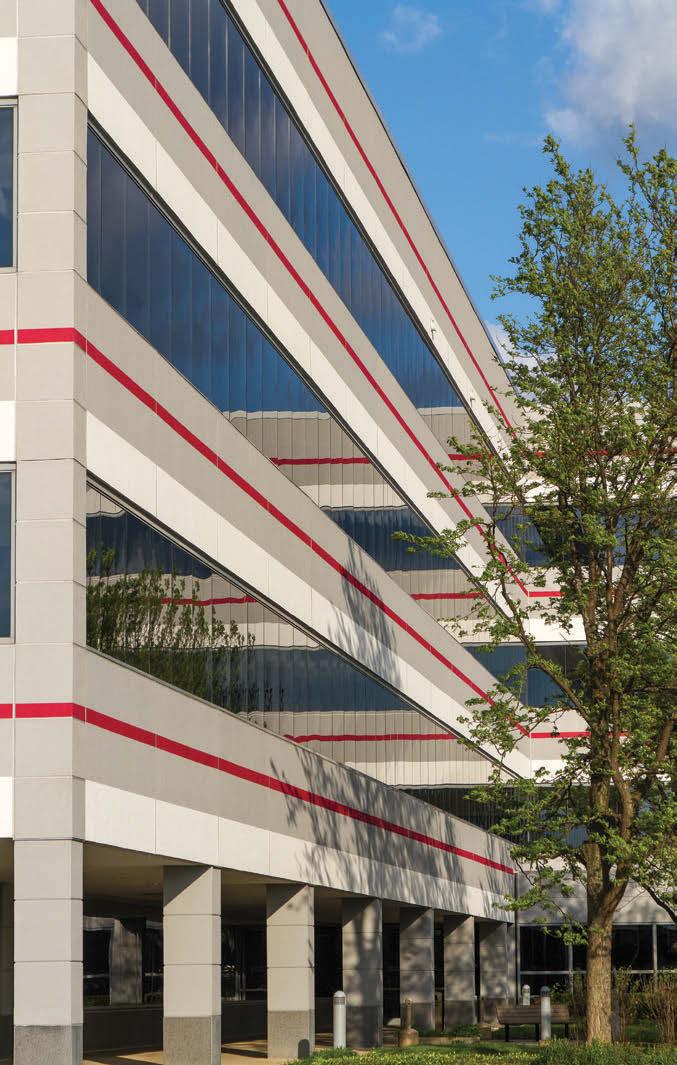
5 minute read
Nuts To Poor Insulation
Nuts To Poor Insulation Sto Corp. siding system provides energy efficiency for Fisher Nuts’ corporate facility.
Above. A façade rehabilitation project included replacement of all cladding and localized repairs of the strip windows to preserve the look but improve the performance of the exterior cladding system. All photos: Gary L. Parr
Advertisement
Right. StoPowerwall ci stucco system provides heat, air, and moisture management, along with protective and aesthetic elements for the Fisher rehabilitation project. M anagement at Fisher Corporate Center, Elgin, IL, experienced continuing moisture issues with the building’s siding, despite repeated repair attempts at failed sealant joints. In fact, water leakage began shortly after the building was constructed in 1992. Administrators at the four-story office building wanted a traditional stucco system and the most energy-efficient system they could buy to help with heat, air, and moisture management in the facility. Building Technology Consultants
PC, Arlington Heights, IL, was initially retained to evaluate potential sources of water and leakage and develop repair recommendations. BTC recommended a façade rehabilitation project that would include replacement of all cladding and localized repairs to the strip windows. Considering factors including aesthetics, durability, and anticipated future maintenance, the building owner selected a three-coat stucco system as the most effective option.
Josh Summers, principal structural engineer, and Chris Kottra, engineer with BTC, oversaw the project, and brought in contracting company,
Mark 1 Restoration, also of Elgin. Mark 1 Restoration representatives called in Carol Stream, ILbased Skyline Plastering’s team to serve as the applicator of the project. After the initial mock up, they got to work removing and recladding the
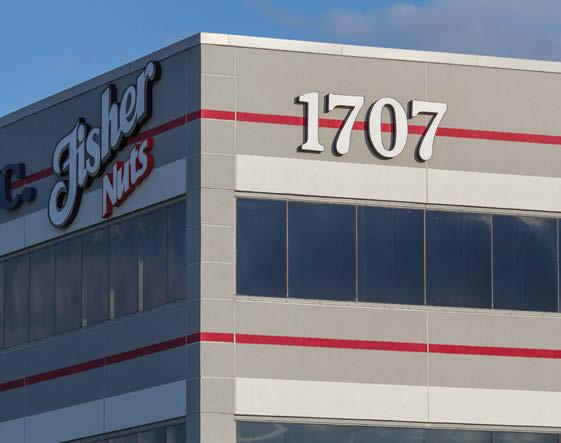
existing cladding with Sto Corp.’s (Atlanta) stucco system. StoPowerwall ci (formerly StoPowerwall EnergyGuard) was used for the project.
StoPowerwall ci is a stucco system that provides heat, air, and moisture management, along with protective and aesthetic elements. The system incorporates StoGuard air and moisture barrier, StoDrainScreen, Dow Styrofoam XPS insulation, StoPowerwall stucco, and Sto textured finishes and coatings, in this case, StoPowerflex Finish & StoCoat Acryl Plus where applicable, into a comprehensive system that supports green building and moisture protection across all climate zones.
“Our intent was to replace our underperforming system, and we were looking for long-term solutions,” said Kelly Day, director of administration for John B. Sanfilippo & Son Inc. (Elgin) for Fisher Corporate Center. “There was leaking inside the building, and the old cladding didn’t withstand the cold and heat. The new system appears to be a good one, with additional R-value for the building, providing more insulation for the 54,000 sq. ft. of outside surface.”
Energy efficiency and weather resistance were key, and so was the flexibility in design in the new system. The team tore open the walls, taking off the exterior skin down to the studs, and renovated the exterior with the new system. The results include a quieter, more energy-efficient building where leaks and drafts were eliminated.
The Skyline team replaced many studs that were rusting away and deteriorated due to water intrusion. According to Skyline Plastering’s president, Peter Klyachenko, “We kept most of the existing interior insulation intact but did add insulation where it was needed behind the sheathing. Once sheathing was installed, we first treated all the joints and then installed a continuous fluid-applied air/vapor barrier called StoEmeraldCoat by Sto Corp.”
Next they installed the Dow Insulation (which was blue in color) to provide continuous insulation outbound of the sheathing. Prior, there was white insulation (EPS), used temporarily in loca
tions where anchor points were needed for mast climbers and scaffolding around the building.
The window splices were also re-caulked under the direction of Mark 1 Restoration.
Sealant was replaced where necessary. Steel had deteriorated in areas where there was excess moisture intrusion and water was trapped. These areas were reinforced during the renovation, requiring additional work that was performed while still staying on budget.
According to Klyachenko, the system that was previously installed was actually very energy efficient for its time, but did not incorporate any kind of secondary weather barrier or drainable system behind the EIFS. The new insulated stucco system provides almost double the energy efficiency while maintaining the same thickness and appearance. The main factor contributing to the more-effective cladding was the fluid-applied air/vapor barrier system that allows any incidental moisture to weep out without any damage to the building.
“Our company is an experienced installer of insulated cement plaster/stucco systems across Chicagoland,” said Klyachenko. “It’s an interesting assembly and I am sure we will see more of it in the Chicago area–it’s a brilliant combination of old and new. The finished product is highly impact resistant, and it’s nice to have continuous insulation coupled with a drainage assembly.”
According to Kottra, the drainable stucco system was key, as most of the water is shed from outside, and with the new continuous-resistance barrier the leaks were eliminated.
The project didn’t happen overnight. Weather conditions always presented a challenge. The building owner wanted the same look of the original building, while improving energy efficiency and resistance to the elements. It was the owner’s intent that when the project was completed one couldn’t tell that anything had been done to the exterior. They loved the original look, but wanted to restore it with a system that would perform better.
“This top-of-the-line stucco system provides the owner with excellent energy efficiency, durability, as well as a visually appealing finish that matches seamlessly with the many other buildings on the Fisher Campus,” said Klyachenko.

StoPowerwall ci is a hybrid system. According to Klyachenko, “I expect to see this system installed more across our climate zone due to new building codes that require continuous insulation outbound of sheathing for better
Want more information? The resources below are linked on our website and in our digital magazine at cbpmagazine.com/digital/julaug2015.
Circle 14 on the Reader Service Card.
Download a product spec sheet.
Download a specifi cation guide for stucco wall assembly.
Walls were opened, taking off the exterior skin down to the studs. The renovated exterior produced a quieter, more energy-effi cient building where leaks and drafts were eliminated.
energy efficiency.” CBP
OUR INNOVATION. YOUR INSPIRATION.
INTERCEPT™ ENTYRE MODULAR METAL PANEL SYSTEM


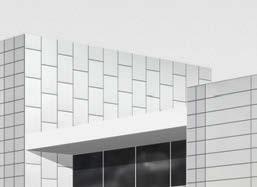


CENTRIA’s Intercept Entyre modular metal panel system unleashes architectural creativity. Intercept Entyre modular panels combine superior performance and aesthetics. Fabricated panels are o ered in an extensive color palette and can be installed in vertical, horizontal, running bond or custom patterns.

See our complete palette of possibilities at CENTRIAperformance.com/intercept To learn more call 1-800-250-9298
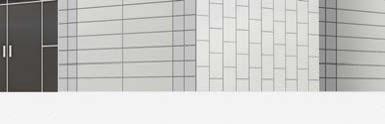
REIMAGINE METAL