
17 minute read
High-In-The-Sky Roofing
High-In-The-Sky Roofing Kemperol resin membrane seals the roof at New York’s One World Trade Center.
Challenges involved with roofing/ waterproofing a high-rise are magnified with height. One World Trade Center in New York is protected with a roofing system from Kemper System America. Photo Credit: Polina Ryazantseva| Dreamstime.com
Advertisement
Above Left. Huge bolts at the base of the spire were among hundreds of exposed roof details protected with the Kemperol system.
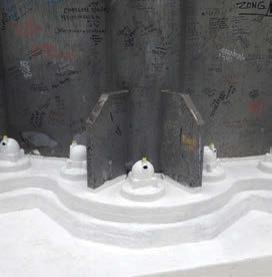

Above Right. What appears to be a simple white coating is actually the top layer of the Kemper system. The membrane is fleece-reinforced and forms a seamless surface that is unaffected by standing water, snow, or ice. It also resists chemicals, corrosives, and UV light. A fter almost a decade of construction, New York’s $3.9 billion One World Trade Center (1 WTC) opened its doors in 2014. The challenges involved with roofing/waterproofing a high-rise are magnified with height, and at an official height of 1,776 ft., 1 WTC (formerly Freedom Tower) offers some valuable lessons. The 408-ft. spire atop 1 WTC weighs more than 750 tons and makes the skyscraper 326 ft. taller than the Willis Tower in Chicago, making it the tallest building in the United States.
With most new construction the building envelope, including the roof, is completed first. In this case, the main roof was one of the last structural items to be completed. Steve Guarino, general superintendent for waterproofing contractor, The Jobin Organization Inc., Farmingdale, NY, shared some experiences working on the iconic structure while, as he put it, “A billion eyes were watching.”
The Jobin Organization, originally established as Jobin Waterproofing Inc. in 1968, is a major presence in the New York construction market in areas such as roofing, waterproofing, exterior restoration, and construction management. The company is a Kemper System America Inc., West Seneca, NY, certified applicator and has completed many projects with the cold-fluid-applied reinforced membrane systems.
FLEXIBLE SOLUTION The 1 WTC main roof is about 19,000 sq. ft. “One of the primary reasons we won the bid with the Kemperol system was all the exposed steel and many penetrations. There were hundreds, maybe 300 or 400 penetrations on the main roof. That included the structure for the three cooling towers above us, the spire, as well as the everyday vent pipes, drains, conduits, plumbing, and other piping. There were no areas bigger than about 10 ft. x10 ft. without some penetration,” said Guarino.
The Jobin Organization ran a 15- to 20-person crew on the job. “There were so many configurations that needed waterproofing–curbs, drains, HVAC, beams, nuts and bolts, and around the base of the spire. There was so much steel, sometimes we were ‘bumping heads’ with our hardhats,” continued Guarino.
For the main roof, insulation, and pre-primed cement board were first installed and adhered with beads of foam adhesive. The cement board was staggered in a joint pattern over the insulation and sealed at the seams with beads of NP1 polyurethane sealant. The seams of the cement board were also sealed with 4-in. continuous stripping plies of Kemperol.
The Kemperol resin membrane was specified for the main roof and louver areas on lower floors that were enclosed on three sides. The liquid-applied resin membrane systems are reinforced with Kemperol 165 fleece and conform around any shape. Penetrations, drains, curbs, and perimeters were also sealed with the system and then overlapped by the membrane in the larger expanse to provide durable waterproofing protection.
The work on the main roof membrane began in mid-June 2014 and was completed in mid-October. At nearly a third of a mile high, the roof weather could be a surprise. “A lot of times when it was a cloudy day on the ground, it could be foggy. Or if it was foggy on the ground, it could be raining when we got to the top. But the heat was not too bad, and there was no sweltering hot weather,” reported Guarino.
GETTING THERE One obvious challenge in waterproofing a high-rise is simply getting materials to the roof. “By the time we got to the roof, the outside hoist had been taken down, which might have saved a little time,” Guarino said. “But with the Kemperol system, there’s no heavy equipment, so we were OK. The heaviest tool we used was a hand mixer for the resin.”
The trek to the 105th floor could take as much as two hours because of all the trades on the site. The Jobin Organization crew would bring materials up through the building on the elevator cars, many times on Saturdays and Sundays to have all the required materials ready to go.
Guarino explained, “We would take materials from the loading dock to the main-floor elevators, up to [floor] 102, and then transfer to 105. The insulation and cement board were loaded on 4 ft. x 4 ft. skids and some stored on 104 during the job.” Also easy to transport, the Kemperol resin is packaged in 2 1/2- and 5-gal. containers, and the fleece reinforcement in rolls to 41-in. wide.
JOB-SITE COORDINATION Kemper System specialists were on-site weekly to inspect and advise on the job. In addition, a building-envelope consultant photographed progress daily to provide feedback to the A/E/C management team.
There were conversations with the management consultants every morning to make sure everything was running smoothly, Guarino said. But there was no cell phone service available on the roof during construction because of the thickness of the slab. So more-urgent messages were often relayed a couple of floors down the old-fashioned way–by walkie-talkie.
“The biggest challenge was coordination on the
job site. There were a lot of trades there at the same time, so we had to constantly clear people out of the way. The deck needed to be prepared ahead of us. The concrete was too rough in some areas. Overpours needed grinding and debris removed, or grease needed to be cleaned off. There was also a crew working above us on
Want more information? The resources below are linked on our website and in our digital magazine at cbpmagazine.com/digital/julaug2015.
Circle 16 on the Reader Service Card.
Download a Kemper System product applications guide. View project profi les.
Browse a list of AIA CES accredited seminars.
the cooling towers, so we needed to inspect if any areas had become wet before the membrane was cured. When things happened, the Kemper System made it possible to redo or repair small areas,” Guarino said.
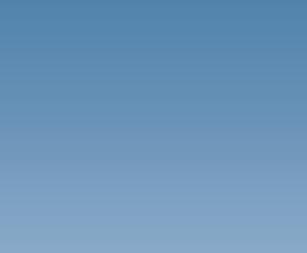
Breaking the Curve
FROM THE GROUND UP The waterproofi ng story at 1 WTC really began at the ground fl oor, or actually more than 30 ft. below it. The Jobin Organization originally submitted bids on the 1 WTC project with Kemper System America circa 2004. Following the resolution of project design and fi nancing issues, construction fi nally got underway in the spring of 2006.
Ironworkers erected the steel at a fairly steady pace, though heavy winter storms dampened the pace toward the end. Every tenth floor required temporary waterproofing with EPDM sheet and caulking until a new slab, ten stories above, could be poured. Skyscraper cranes would lift bundles of steel and pallets of materials from the ground up or from one completed section to the next. Month after month, the arm would swing from the outside frame of the building, and deposit bundles stories above.
The outside frame of the Tower is very slightly tapered with a notch-in at several floors as the shaft rises skyward. The Jobin Organization crew waterproofed the roof perimeter and exposed steel at these levels, as well as the top three floors of the main roof, 103 to 105, which are exposed to the elements.
Kemperol 2K-PUR resin system contains 80% renewable materials, which fit the overall design goals for the project. Nearly 75% of 1 WTC is made from recycled or eco-friendly building materials, and the building’s green design earned LEED Gold certification. CBP Architects designing Legacy Junior High School faced a challenge: create a space to inspire and excite students. Through lively community collaboration, the project came together, incorporating sinuous and sophisticated green metal contours hip enough to intrigue students.
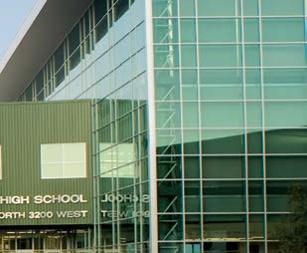
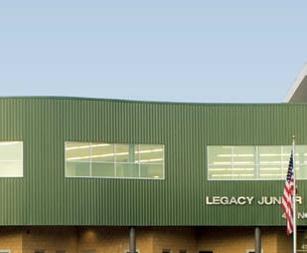
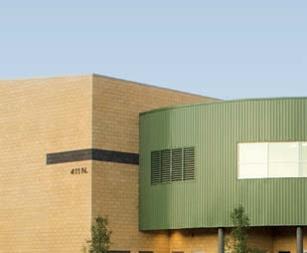
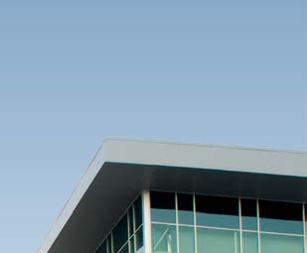

Visit www.mbci.com/curve for more information.
PROJECT: Legacy Junior High School LOCATION: Layton, Utah
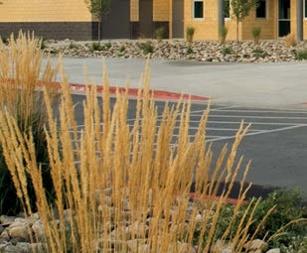
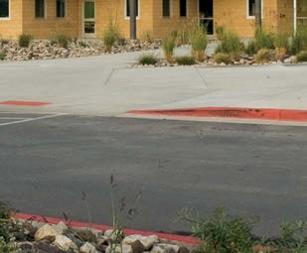
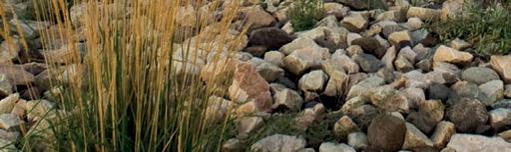
ARCHITECT: VCBO Architecture
CONTRACTOR: All Metals Fabrication
PANEL PROFILE: PBU (Tundra / Laurel Green / Galvalume Plus ® ), Artisan (Tundra), Flat Sheet (Tundra / Laurel Green)
Copyright © 2014 MBCI. All rights reserved.
Copyright © 2015 MBCI. All rights reserved.
Scan each product’s QR code for detailed information.
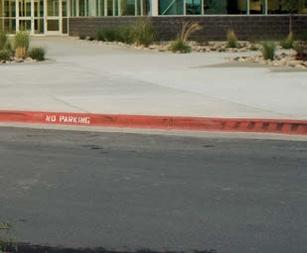
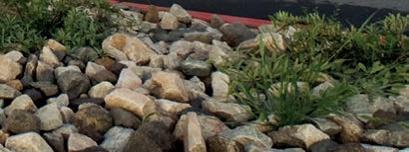
PHONE: 877.713.6224 E-MAIL: INFO@MBCI.COM
EDITORS’ CHOICE
Simulated metal roof
SMRP:
Simulated metal roof profi le Provides metal look with heat-sealed seams Available in 100-ft. coils
e company’s SMRP simulated metal roof pro le provides the look of metal with heat-sealed seams for reported superior long-term leak protection. e pro le includes a thermally activated KEE adhesive strip on the bottom for installation over the company’s Fleece Back membranes. Available in exible 100-ft. coils, the pro le is secured at speci ed intervals to simulate the aesthetics of a metal roof system.
FiberTite, Wooster, OH Circle 55 fi bertite.com
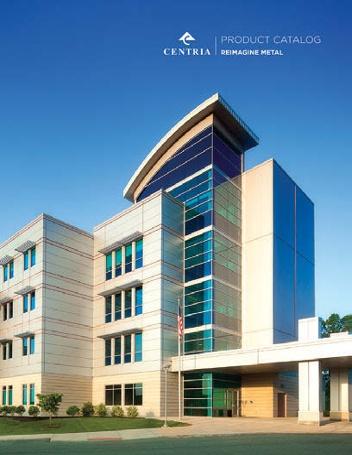
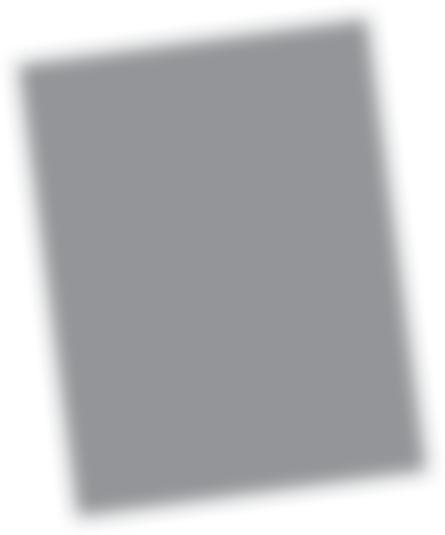
Product catalog An updated product catalog details the company’s wide range of architectural metal wall and roof products. Products described include Intercept modular metal-panel system, Metalwrap insulated composite backup panels, and Formawall insulated metal-panel system.
Centria, Moon Township, PA
Circle 56 centriaperformance.com
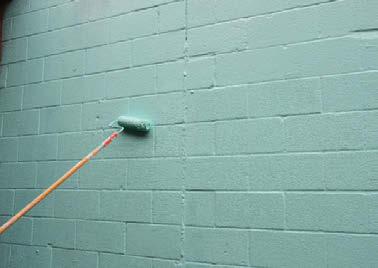
Air, water barriers Aero-Perm permeable air and water barriers control the movement of air through a building envelope, reportedly reducing condensation, moisture development, and energy loss in the wall assembly. Systems are available in a fl uid-applied or self-adhering version.
The Garland Co. Inc., Cleveland Circle 58 garlandco.com
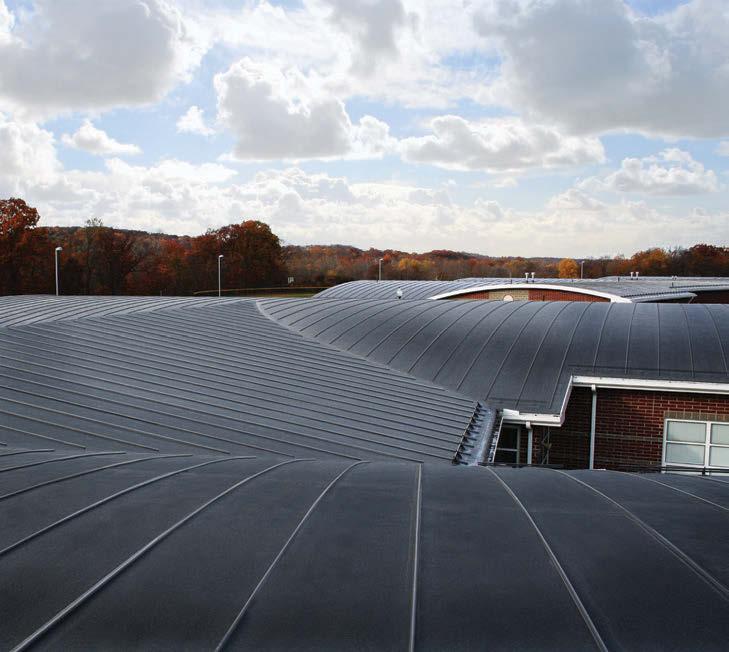
Fascia trimboard Restoration Millwork fascia trimboard is part of the INhanced trim line, a cellular PVC product with a built-in return leg said to work with a range of soffi t materials. Available in a ready-to-install Natural White, the product can be painted. TrueTexture woodgrain and smooth fi nishes provide a fi nished look.
CertainTeed, Valley Forge, PA Circle 57 certainteed.com


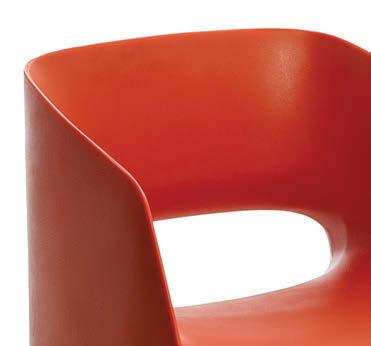
Outdoor seating OM Basic armchair is weatherproof, sculpted from a single block of solid sculpted from a single block of solid rotational-molded polyethylene, 100% recyclable, and portable. At 100% recyclable, and portable. At almost 30-in. high, there are said to almost 30-in. high, there are said to be no sharp edges or protuberances. be no sharp edges or protuberances. Colors include brown, gray, light blue, Colors include brown, gray, light blue, pistachio, red, and white.
Magnuson Group, Woodridge, IL Circle 59 magnusongroup.com
Spray-foam insulation Spider Plus blow-in insulation, Corbond opencell spray polyurethane foam, and Corbond open-cell Appendix X spray foam are additions to the company’s products. Applications include walls, fl oors, crawl spaces, and unvented and vented attics and ceilings.
Johns Manville, Denver Circle 60 jm.com

Wood stud wall system CavityComplete wood stud and concrete masonry unit wall system includes components from fi ve companies to form a compatible, code-compliant, and warranted system. Designed to take the guesswork out of specifying, the system includes the company’s EcoTouch Pink Fiberglas insulation, Foamular 250 extruded XPS rigid-foam insulation, Tremco Inc. ExoAir 230 vapor-permeable barrier, Rodenhouse Inc. Thermal-Grip ci prong washers, Heckmann Building Products Inc. Pos-I-Tie masonry-veneer anchoring system, and Mortar Net Solutions multi-plane drainage system using TotalFlash.
Owens Corning, Toledo, OH Circle 61 cavitycomplete.com
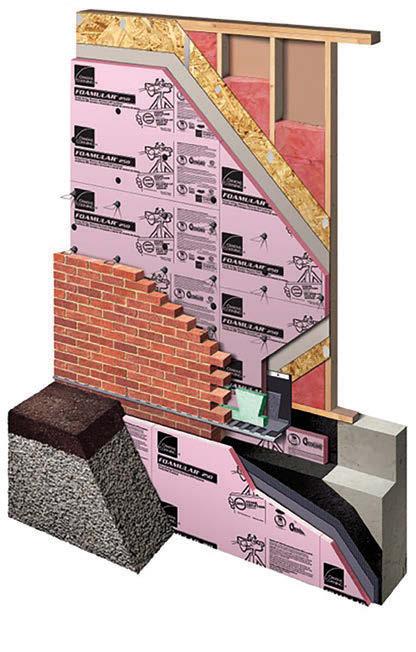
Wall-panel clip system The Ultimate Clip installation system for the company’s fi ber-cement wall panels uses a starter track and a single model clip. The system can reportedly be used for all installations. A 6-ft. panel needs only two 26-in.-long clips. The device’s larger surface area aids in increasing the overall system’s wind rating.
Nichiha USA Inc., Atlanta Circle 62 nichiha.com
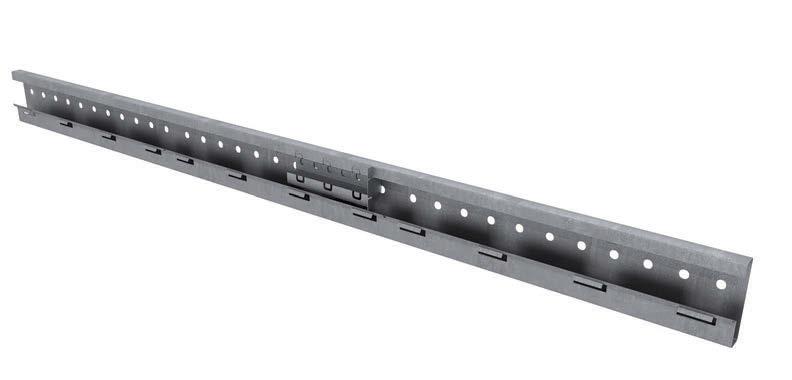
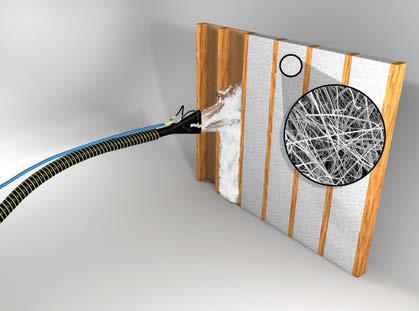


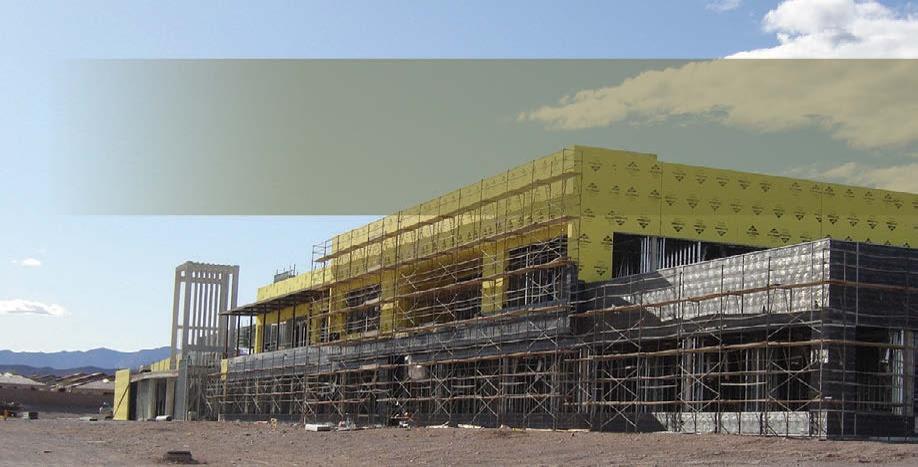
The Ultimate Waterproofing System
MFM SubSeal ™ is a pre-fabricated, self-adhering, self-sealing waterproofing membrane that stops water and moisture in its tracks! This advanced system aggressively bonds to prevent damage caused by water penetration.
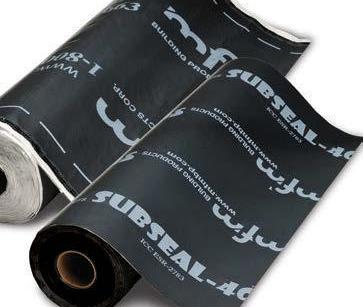
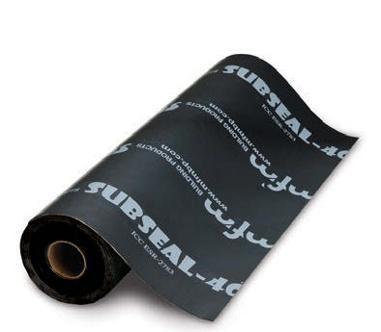
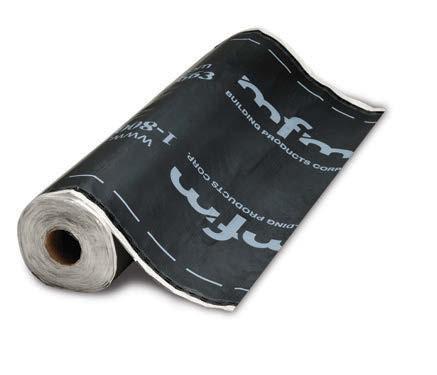
Multi-Purpose Waterproofing Protection for:
• Through-Wall Flashings • Foundation Walls • Plaza Decks • Sills, Pot Shelves, Parapets • Parking Garages
Realize maximum protection, increased savings and more than 50 years of waterproofing experience. Call 800-882-7663 to get a quote or visit www.subseal.mfmbp.com for more information.
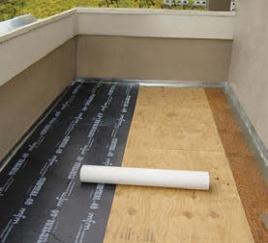
ICC-ES AC38, ICC-ES ESR 2783, ASTM D 1970
800-882-7663 www.subseal.mfmbp.com
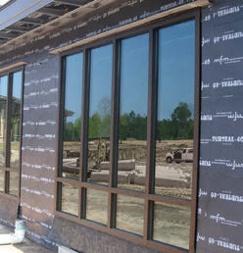
• Ideal for Below Grade Foundations and Structures • Vertical or Horizontal Applications • Aggressive Bonding Characteristics
• Extreme Moisture Protection
• Available in 40 or 60 Mil Thickness • Self-Adhering for Fast Installation
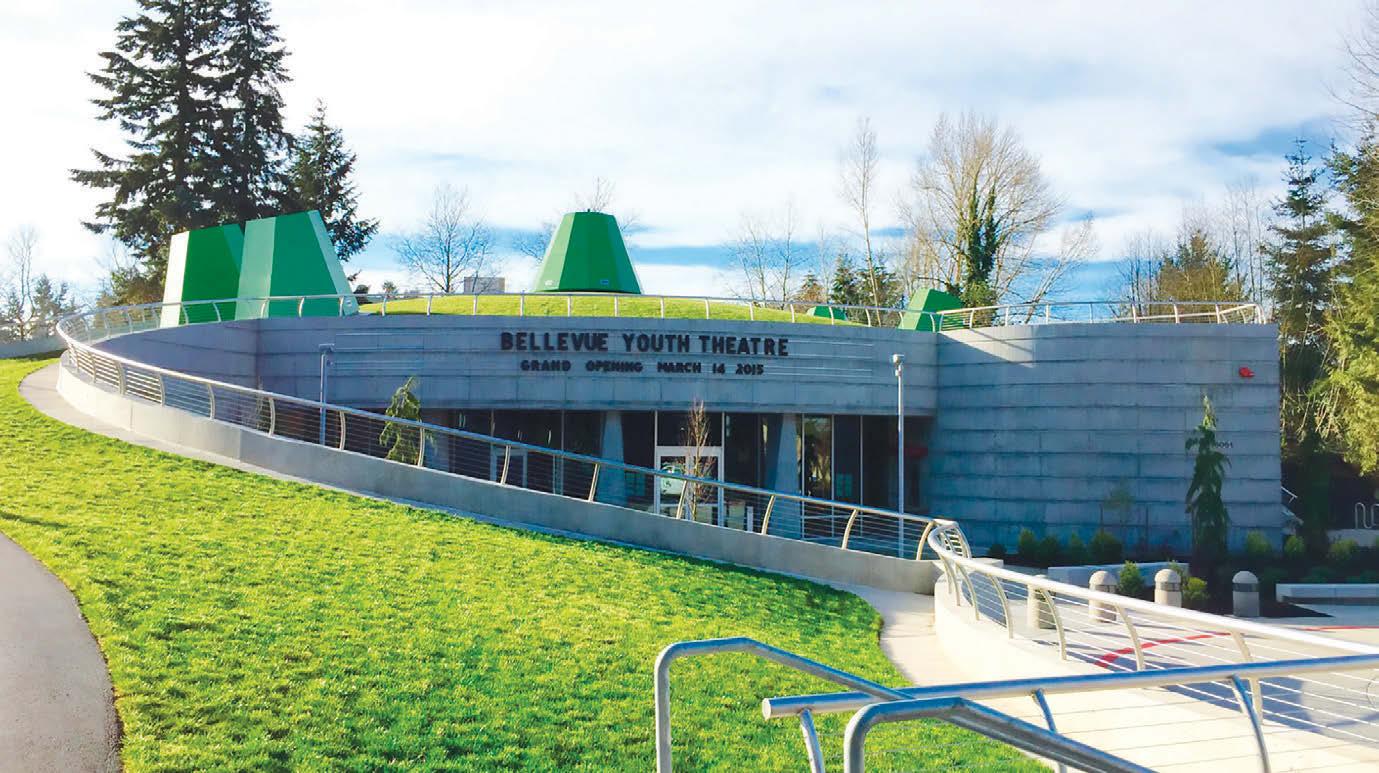
The Bellevue Youth Theatre, a 150-seat theater in the round, is integrated into the sloping hillside of Crossroads Park. The facility features a green roof.
Support space encircles the theater with a lobby, dressing room, storage, green room, rehearsal areas, an office, workshop, restrooms, and sound/lighting booths. An outdoor amphitheater provides seating for at least 400 patrons.
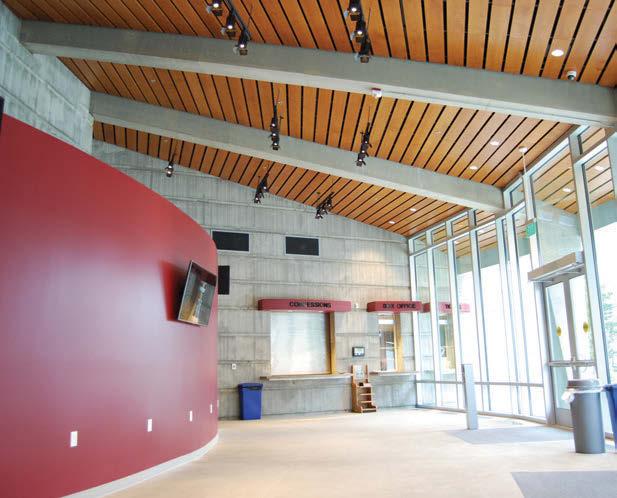
Youth Theatre An Engineering Challenge
Curved, precast concrete roof beams connect to a center compression ring to form a dome-like structure.
Building a circular 12,000-sq.-ft. theater integrated within a hillside proved an engineering challenge but, after two years of construction, the
Bellevue Parks and Community Services Department’s new $8.8 million Bellevue Youth Theatre (BYT), is open to the public.
The City of Bellevue, WA, and BYT wanted a round performance venue that offered versatility of use and environmentally friendly features. They contracted Becker
Architects, Bellevue, and Pease Construction Inc., Lakewood, WA, to bring their vision to life.
The new theater, located in the Crossroads Community Park on a site southeast of the existing Crossroads Community Center, is described by principal Robert George Becker, Becker Architects, as an “environmental sculpture.”
Support space encircles the entire theater with a lobby, dressing room, storage, green room, rehearsal areas, an office, workshop, restrooms, and sound/lighting booths. An outdoor amphitheater provides seating for at least 400 theater patrons or concert attendees.
The new 150-seat theater in the round is integrated into the sloping hillside of Crossroads Park. The facility features a natural, insulating, green roof where the lawn rolls up and over the roof of the theater, creating an earth-sheltered building. The results are significant energy savings and limitation of the effects of storm-water runoff, since much of the precipitation can be absorbed into the earthen roof rather than flowing from a conventional roof into storm drains.
The facility is designed to meet LEED Gold certification standards.
In an interview with the Bellevue Reporter, Steve Kathman, project superintendent for Pease said, the 12,000-sq.-ft. theater was his most challenging venture yet. Building segments of circular design for the theater results in multiple radiuses and angles to consider, he explained. “Then you have flat walls in between,” said Kathman. “It’s a lot of intricate math.”
Because of the complex design, Becker and Pease decided to use cast-in-place and precast concrete. To construct the theater’s domed roof, Pease contracted Oldcastle Precast of Spokane, WA, to manufacture and supply the distinctive precast concrete components that were required to construct the circular roof structure, including precast concrete roof beams, a precast concrete compression ring, and hollow-core plank for the project.
The curved, precast concrete roof beams were connected to the centered compression ring to form the dome-like structure. The hollow-core planks were then installed between the roof beams, filling in the open spaces to complete the roof structure. The roof planks were eventually covered with a 3-in. concrete topping slab.
“The precast concrete elements were specified because it would have been difficult to cast them in place,” said Eric Holje, project manager for Oldcastle. “This was an unusual project with complicated pieces that had to fit together precisely. The precast beams, which are very large pieces, had to be manufactured within exacting tolerances, within fractions of an inch, in order to site-assemble the precast components, and achieve the requirements of the roof specifications.”
In all, Oldcastle manufactured and shipped 20 curved precast concrete beams, the longest measuring approximately 1 x 4 x 58 ft.; a circular precast concrete center hub; and 204 pieces of hollow-core plank, the longest measuring 8 in. x 4 ft. x 15 ft.
A cast-in-place 3-in. concrete topping slab, 18 in. of soil, and grass were added to complete the roof. The dug-up earth around the roof was used to backfill, and a guard net was installed to keep the landscaped roof in place.
To complete construction of the theater, cast-in-place concrete was used to fill the top of the inner ring and create the exterior walls, the front sidewalls, and the radius parapet walls. The exterior and lobby walls are exposed concrete with a random, striated vertical pattern, giving the impression that the walls are pushed out of the earth.
“Pease Construction has completed many projects with Oldcastle Precast. This Bellevue Youth Theatre was the most challenging to date,” said Kathman. “Oldcastle Precast became engaged early on in the project, collaborating with Pease and CT Engineering (Seattle) on dimensions of the precast beams, as well as the poured-in-place walls. The precast beams fit like a glove. The erection of the beams and the planks was like watching poetry in motion. The use of precast in this situation saved months on the overall schedule. Oldcastle Precast was also a great help with the logistics of bringing 60-ft. beams into Bellevue.”
Another environmentally friendly feature incorporated into the facility is a geothermal water-source system. Fourteen geothermal wells, 300 ft. deep, keep the theater at 69 F and are used as a heat exchanger to supplement the heating and cooling demands. Six light “trumpets,” or columns, that rise from the lawn that covers the roof, bring natural light into the building. Three of the trumpets will also release mechanical and plumbing ex

haust, and the other three will have air-supply ducts.
Funded by a $2 million match from the city through a voter-approved parks levy and an additional $2.5 million from King County Green Building and 4Culture grants, the new $8.8 million Bellevue Theatre will increase capacity for continued growth of one of Bellevue Parks & Commu
Above. Oldcastle Precast supplied precast concrete components, including roof beams, a compression ring, and hollow-core plank.
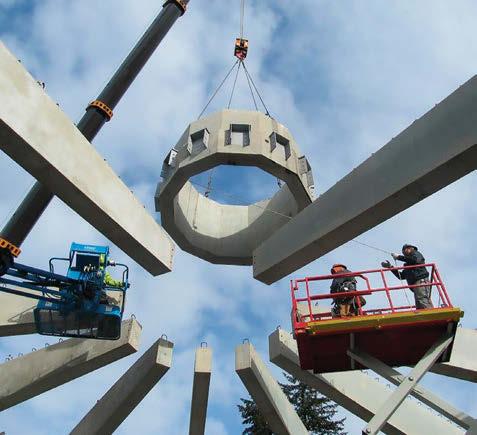
Right. The curved, precast concrete roof beams were connected to the center compression ring to form the dome-like structure.
nity Services’ most successful programs. CBP
Want more information? The resources below are linked on our website and in our digital magazine at cbpmagazine.com/digital/julaug2015.
Circle 15 on the Reader Service Card.
Download Oldcastle building structures' brochures.
Read more precast case stories.
Obtain product specifi cations.
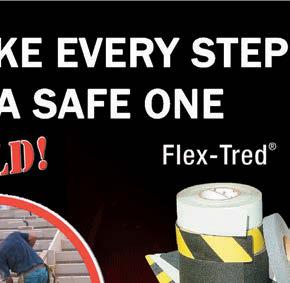

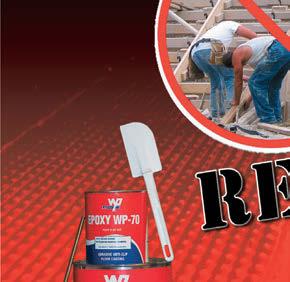
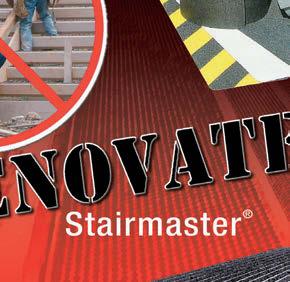

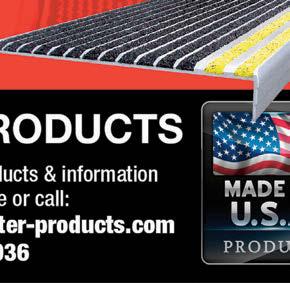