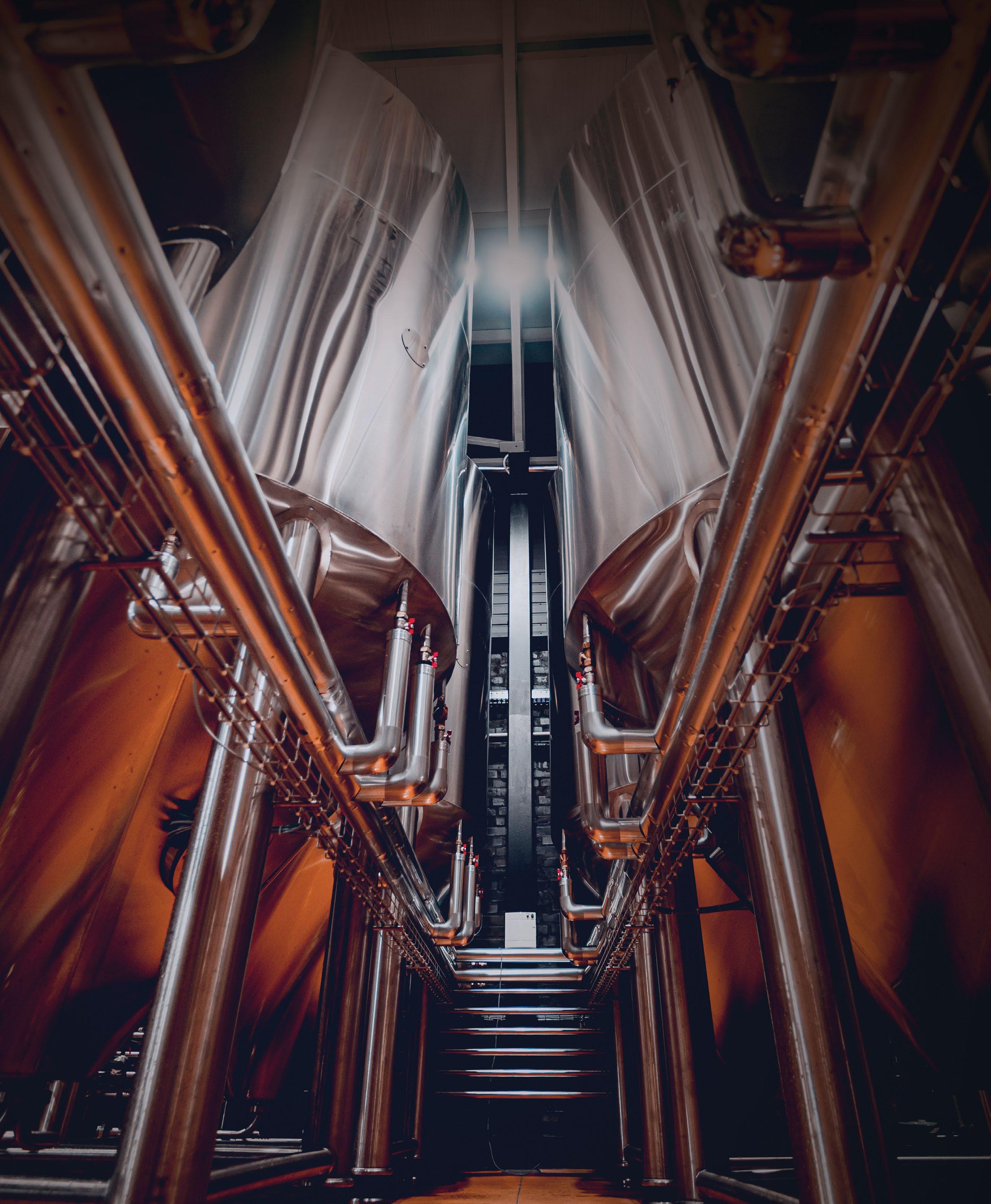

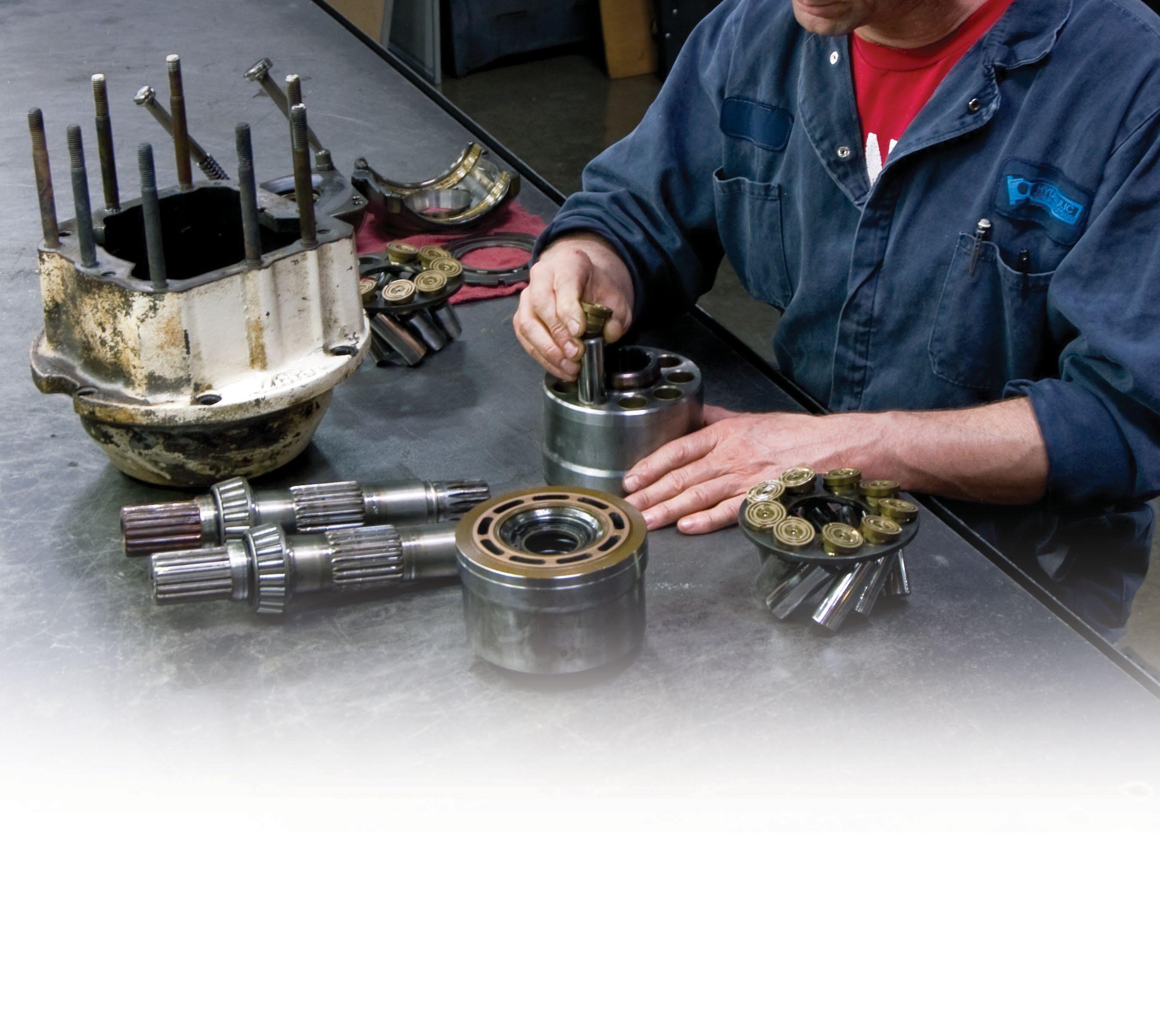
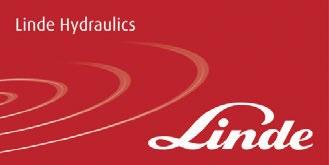
Lubriplate’s complete line of ultra high-performance, hydraulic fluids has been designed to provide a wide range of benefits including: extended fluid change intervals, cooler operating temperatures, reduced friction and reduced downtime. Products include...
•High-Performance, 100% Synthetic, Polyalphaolefin (PAO)-Based Fluids.
•Provides extended drain inter vals and excellent compatibility with seals.
• Available in ISO Viscosity Grades 32, 46 and 68.
•Premium-Quality, Petroleum-Based Hydraulic Oils (ISO Grades 32-100).
• Anti-wear fortified to protect hydraulic system components.
•High aniline points ensure long seal life with fewer leaks.
•NSF H1 Registered and NSF ISO 21469 Certified - Food Machinery Grade.
•High Performance, 100% Synthetic Food Machinery Grade Fluids.
• Available in ISO Viscosity Grades 7, 15, 22, 32, 46 and 68.
•Fortified with Lubriplate’s proprietar y anti-wear additive
•High-Performance, FM Approved, Fire Resistant Hydraulic Fluid.
•NSF H1 Registered and NSF ISO 21469 Certified - Food Machinery Grade.
•ECO-Friendly, Readily Biodegradable (OECD 301F).
•Fortified with Lubriplate’s proprietar y anti-wear additive
•Hea vy-Duty, High-Performance, Extended Life, Hydraulic Fluids.
•ECO-Friendly - Free of zinc or silicone compounds.
•Provides long ser vice life and extended fluid change intervals.
• Vegetable-Based Oils for use in environmentally sensitive applications.
•ECO-Friendly - Ultimately Biodegradable (Pw1).
•Zinc-free additives provide exceptional anti-wear and anti-rust protection.
•For equipment operating in environmentally sensitive locations.
•Zinc-free and non-toxic to aqua tic life.
•Exceeds U.S. EPA LC50 and US Fish and Wildlife requirements.
•Meets or exceeds the requirements of most hydraulic equipment
• Advanced Synthetic Polyalkylene Glycol (PAG)-based hydraulic fluids.
•Designed for environmentally sensitive industrial and marine applications.
• Meets U.S. EPA Vessel General Permit (VGP) Requirements. Readily biodegradable.
•Does not leave a sheen on the water.
Newark, NJ 07105 / Toledo, OH 43605 / 800-733-4755
To learn more visit us at: www.lubriplate.com
August 2023
VOLUME 30 • ISSUE 8
6 Cover Story
Using Multimedia Monitoring to Optimize Energy Consumption
Real-time monitoring of utilities such as compressed air can help reduce energy consumption and improve process efficiency in food and beverage operations.
8 Duplex Filter Solutions for Power Generating Turbines
The best way to achieve optimal oil filtration for power generating turbines.
18 The Next Step in Predictive Maintenance for Mobile Equipment
Failure in machinery or equipment can have catastrophic impacts, and so breakdowns need to be proactively prevented.
23 Test Your Skills
The “STAMPED” Method Designing & Specifying Tube Assembly Components
26 The Impact of Smart Manufacturing on Maintenance Practices
Smart manufacturing integrates advanced technologies for companies seeking leverage in efficiency
Publisher’s Note: The information provided in this publication is for informational purposes only. While all efforts have been taken to ensure the technical accuracy of the material enclosed, Fluid Power Journal is not responsible for the availability, accuracy, currency, or reliability of any information, statement, opinion, or advice contained in a third party’s material. Fluid Power Journal will not be liable for any loss or damage caused by reliance on information obtained in this publication.
Routine and scheduled maintenance of hydraulic systems are vital to getting the most out of your Hitachi Mining Excavator. While maintenance plays the largest role in the prevention of unnecessary machine downtime, it can also expose the hydraulic system to high levels of contamination rapidly decreasing component longevity. The importance of contamination control is sometimes overlooked when performing maintenance due to incorrect practices being used.
THE FLANGELOCK™ TOOL AND CIRCUIT BLANKING CAPS
The FlangeLock™ tool and caps are the ultimate contamination control tools for protecting your hydraulic system. The FlangeLock™ allows for the simple sealing of open hydraulic flanges without tools while the caps can be bolted in place of a flange connection. Easy on, easy off, they offer a leak-proof solution to hydraulic systems and environmental cleanliness. FlangeLock tools and caps stop the mess.
Hitachi have packaged FlangeLock™ tool and caps specifically for Hitachi mining excavators. The Hitachi customised kits make sure no matter which component routine maintenance is being performed on, you will always have the exact number of FlangeLocks™* and caps to help reduce contamination.
*Note: FlangeLocks are not to be used under pressure
The FlangeLock™ Tool is the ultimate contamination control tool for protecting your hydraulic systems. It allows for the simple sealing of open SAE code 61, 62 & CAT-Style hydraulic flanges without tools. Constructed from lightweight aluminum. Easy on, easy off. Offers a leakproof solution to hydraulic system and environmental cleanliness. FlangeLock™ Tools stop the mess!
• No tools required
• No expensive hardware needed
• No more rags stuffed into hoses
• No more messy plastic caps
• The ultimate contamination control tool
ERGONOMICS PLAYS AN important role in optimizing the design of industrial filtration systems by making them easier to maintain and safer for the user. Operators who change out consumable filter bags will benefit from systems that minimize physical strain, the time it takes to complete their tasks, and potential exposure to dangerous conditions and substances.
Per the U.S. Bureau of Labor Statistics, most nonfatal occupational injuries resulting in missed work are caused by musculoskeletal disorders (MSDs) including sprains/strains, pinched nerves, bruises, and lacerations due to lifting/pushing/pulling heavy items, bending down, reaching overhead and/or working in awkward body positions. OSHA further estimates that U.S. employers pay almost $1 billion per week for direct workers' compensation costs alone—a reminder that implementing improved safety measures is always good business. Here is how functional design can make a big difference in the overall efficacy of industrial filtration systems and how ergonomics can have the added benefit of positively impacting your profits:
Large-sized filters (where housings will tend to have a high access point) are popular for the efficiencies they create. However, it may be more practical to design a smaller filter unit having a lower access point, where filter bags are also smaller/shorter, thus enabling personnel to easily remove them while standing on the ground. This eliminates the need for special lift equipment or scaffolding that is labor-intensive, disruptive to operations, and can pose a safety risk. In certain cases, a high-capacity filtration solution in a shorter size can even outperform a larger, standard-capacity model while offering better height accessibility.
Note that smaller-sized systems are often preferable for filtering viscous liquids such as glues, paints, or resins. This is because the weight of the loaded bag that is potentially filled with liquid (when draining is more difficult) can be significant. A size #2 bag will weigh roughly twice as much as a size #1 bag for example. Furthermore, the contact area between a #1 filter bag and filter basket is also substantially reduced compared to a #2 bag, and as such the extraction becomes much easier when working with sticky liquids. Notable is that a filter balloon can further aid in displacing nonfunctional internal volume by reducing the internal volume in a size #2 bag from 16 L down to 7 L, thereby reducing the weight of the bag for extraction.
Typical working height restrictions can be overcome in other ways as well. For instance, where filter housings are normally positioned in a vertical setup, changing to an inclined or even horizontal position may dramatically reduce the working height. The market offers a variety of inclined or fully horizontal configurations for single- and multi-bag filter housings that allow fast removal or insertion of consumables without having to lean over the opened housing. This type of setup helps limit operator exposure to dangerous temperatures, chemicals, solvents and other ambient hazards and is ideal for reducing physical fatigue where filter bags become heavily loaded.
The method of opening and closing the filter unit can also make a difference to operators. Single central T-bolt or V-clamp quick closures can require much less time and effort to service compared to housings with multiple eyebolts. These more operator-friendly, quick-open-andshut systems permit access to consumables in seconds as opposed to minutes of more difficult manual labor. For instance, some quick-lock units allow the operator to stand in place and rotate a hand wheel to open the cover—there is no need to have full movement around the housing or to use any tools, as is the case with
bolted closures. Some multi-bag V-clamp housings may also use a spring-assisted mechanism to facilitate easier closure.
Safety is paramount in these instances and that is why Eaton designs all of its quick-opening bag filters with a proper system that blocks the opening mechanism while the housing is under pressure. When specifying a filtration unit, you should further evaluate options to customize the cover opening direction so that it easily adapts to different piping layouts or to accommodate walls, posts or other obstructions depending on the facility.
The difference is in the detail.
Ergonomically designed grab handles that hold up in harsh environments can make the removal of filter bags much easier and faster as well. Other features like bag positioners can make it simple for operators to insert a bag correctly without having to lean over the housing and push the bag down in the basket, so take time to understand all the factors that will make a difference to operators over years of service.
It is also wise to consider automatic self-cleaning filtration systems where volatile organic compounds (VOCs) can be released during consumables change out. These systems help keep operators safe by minimizing the need for manual intervention and thus potential exposure to VOCs. High-capacity filter bags, offering extra filtration surface in the same filter housing, can here again help to limit operator exposure by extending the time between change outs.
The industry is constantly striving to make industrial filtration solutions lighter, easier and safer for personnel to manage, and more effective in terms of reducing product waste and process inefficiencies. This helps to protect operators and lower expenses by enabling systems to stay online longer with less attention required. If your maintenance routine has become a costly production that uses special equipment and puts an extra burden on people, take a closer look at all the ergonomic advantages that are available.
P u BLI s HER
Innovative Designs & Publishing, Inc.
3245 Freemansburg Avenue, Palmer, PA 18045-7118
Tel: 800-730-5904 or 610-923-0380
Fax: 610-923-0390 • Email: Art@FluidPowerJournal.com www.FluidPowerJournal.com
Founders: Paul and Lisa Prass
Associate Publisher: Bob McKinney
Editor: Janis Adams
Technical Editor: Dan Helgerson, CFPAI/AJPP, CFPS, CFPECS, CFPSD, CFPMT, CFPCC
Marketing and
Social Media Consultant: Kristy O'Brien
Graphic Designer: Nicholas Reeder
Accounting: Donna Bachman, Sarah Varano
Circulation Manager: Andrea Karges
IN t ERNAt IONAL FL u ID POWER s OCIE t Y
1930 East Marlton Pike, Suite A-2, Cherry Hill, NJ 08003-2141 Tel: 856-424-8998 • Fax: 856-424-9248
Email: AskUs@ifps.org • Web: www.ifps.org
2023 BOARD OF DIREC t OR s
President: Scott Sardina, PE, CFPAI, CFPHSWaterclock Engineering
Immediate Past President: Denis Poirier Jr. CFPAI/AJPP, CFPHS, CFPIHM, CFPCCDanfoss Power Solutions
First Vice President: Jeff Hodges, CFPAI/AJPP, CFPMHM- Altec Industries
Treasurer: Lisa DeBenedetto, CFPSGS Global Resources
Vice President Certification: James O’Halek, CFPAI/AJPP, CFPMIP, CMPMM - The Boeing Company
Vice President Marketing: Chauntelle Baughman, CFPHS - OneHydraulics
Vice President Education: Daniel Fernandes, CFPECS, CFPSSun Hydraulics
Vice President Membership: Garrett Hoisington, CFPAI/AJPP, CFPS, CFPMHM - Open Loop Energy
DIREC t OR s-At-LAR g E
Stephen Blazer, CFPE, CFPS, CFPMHM, CFPIHT, CFPMHTAltec Industries
Cary Boozer, PE, CFPE - Motion Industries
Bruce Bowe, CFPAI/AJPP - Altec Industries
Bradlee Dittmer, CFPPS - Norgren/IMI Precision Engineering
Brian Kenoyer, CFPHS - Cemen Tech
Wade Lowe, CFPS - Hydraquip Distribution
Jon Rhodes, CFPAI, CFPS, CFPECS - CFC Industrial Training
Mohaned Shahin, CFPS - Parker Hannifin
Randy Smith, CFPHS - Northrop Grumman
Ethan Stuart, CFPS, CFPECS - Quadrogen
Bradley Wagner, CFPAI/AJPP - Manitowoc Crane Group
Brian Wheeler, CFPAI/AJPP, CFPMM, CFPMIPThe Boeing Company
CHIEF EXEC ut IVE OFFICER (EX-OFFICIO)
Donna Pollander, ACA
HONORARY DIREC t OR (EX-OFFICIO)
Ernie Parker, CFPAI/AJPP - Hydra Tech
IFP s stAFF
Chief Executive Officer: Donna Pollander, ACA
Communications Coordinator: Victoria Piro
Technical Director: Thomas Blansett, CFPS, CFPAI
Assistant Director: Jenna Mort
Certification Logistics Manager: Kyle Pollander
Bookkeeper: Diane McMahon
Administrative Assistant: Beth Borodziuk
Instructional Designer and Layout: Chalie Clair
Fluid Power Journal (ISSN# 1073-7898) is the official publication of the International Fluid Power Society published monthly with four supplemental issues, including a Systems Integrator Directory, Off-Highway Suppliers Directory, Tech Directory, and Manufacturers Directory, by Innovative Designs & Publishing, Inc., 3245 Freemansburg Avenue, Palmer, PA 18045-7118. All Rights Reserved. Reproduction in whole or in part of any material in this publication is acceptable with credit. Publishers assume no liability for any information published. We reserve the right to accept or reject all advertising material and will not guarantee the return or safety of unsolicited art, photographs, or manuscripts.
»A DAM OUT west had a hydraulic system installed to replace an old system that was just giving them too many maintenance problems.
The new system was very similar to the old unit except its directional valve was ungraded to a proportional pilot operated valve with spool feedback on the main spool. The unit would open gates allowing flow to all the downstream rivers during the dry season to keep them from totally drying up and causing large fish kills.
Every time they would start it up, which could be about every 2 to 3 months, the proportional valve would stutter and oscillate making it difficult to trust and worried that it could fail at a critical time, possibly spilling too much water. The oscillation would only last 30 to 50 seconds and then smooth out and work fine.
Oscillating Proportional Valve at Start up Set 150 PSI higher than Pump compensator
PT
For the solution, see page 29. 3:1
The unit was built with the reservoir mounted over the pump motor units and the valving and filters were mounted on top above the reservoir to conserve floor space. Replacing the expensive valve did not solve the problem.
Studies have demonstrated that a quarter of global emissions are generated by industrial processes.1 Many industries, including food and beverage manufacturers, seek more effective tools to reduce industrial energy use and help lower global emissions levels. To do this, long-term sustainability strategies are needed that can reliably decarbonize operations. What are the elements of a successful industrial sustainability strategy? Fundamentally, solutions need to use less energy and perform existing processes more efficiently. Real-time system data is key and multimedia monitoring of utilities such as compressed air systems can supply that data. Multimedia monitoring gives manufacturers greater visibility into utility consumption, so they can analyze system performance and take control to reliably reduce utility use while simultaneously improving food and beverage production efficiency and productivity.
Food and beverage companies, faced with increasing costs and heavy competition, place a high priority on identifying waste in their energy use, to better control energy consumption in bottling lines and food processing lines. In these kinds of plants, compressed air systems are major energy users — a typical manufacturing facility that makes extensive use of pneumatics and compressed air actuators can dedicate 20-30% of its electricity use to producing and supplying compressed air throughout the plant.
Yet up to 30% of compressed air can be lost due to leaks and suboptimal utilization, costing about $43k per machine. Finding and correcting these leaks is often costly and inefficient. About 75% of businesses manually test for leaks. However, standard manual tests are periodic. This means leaks can grow between tests. In comparison, continuous compressed air monitoring allows manufacturers to quickly detect and address early-stage leaks, reducing compressed air use by 20-30% and improving energy efficiency as well as overall equipment effectiveness (OEE).
Multimedia monitoring solutions include intelligent sensors and smart devices, a programmable automation controller (PAC) or edge device, open standard technology with secure connectivity and advanced analytics software. By replacing manual, periodic maintenance with continuous compressed air monitoring, food and beverage manufacturers can gain real-time visibility and control over energy use, equipment health and processes.
Continuously monitoring airflow and then aggregating and visualizing data, food processing and bottling line operators leverage the power of intelligent automation tools to anticipate pneumatic energy trends, visualize energy optimization opportunities and spot leaks early on.
These companies can significantly reduce energy consumption, increase sustainability and quickly achieve net-zero goals by fixing leaks and optimizing pneumatic-related processes. Food and beverage companies that typically spend over $1 million per year on energy costs can avoid over $80k in compressed air wastage per year.
When a manufacturer integrates multimedia monitoring into the system of a food processing facility, it sets the See, Decide, Act cycle in motion and has the potential to continuously improve operator expertise and efficiency. The See, Decide, Act cycle continuously optimizes operations efficiency in terms of energy utilization and emissions reduction, but it can also improve worker safety and process and increase reliability and uptime. During the See stage in compressed air monitoring, intelligent sensors across the plant floor are securely connected to a factory network that continuously monitors airflow. Real-time data feeds provide insight into pneumatic system energy consumption, compressed air utilization and pneumatic systems health.
The Decide stage includes analysis of collected data into a PAC or edge device equipped with advanced analytics software that continuously aggregates, contextualizes, and translates data into actionable insights that scale on premises or in the cloud. Multimedia monitoring solutions can detect anomalies, excessive condensation, and energy loss in systems, as well as monitor and trend resources usage. Using the analytics dashboard, operators can visualize trends like energy efficiency and use insights to make fast, informed decisions.
During the Act stage, this solution sends notifications that contain clear instructions and prescribed actions on how to improve efficiency and find leakages. By following these directives, personnel can resolve issues faster and companies can waste less energy.
Multimedia monitoring provides the kind of tools today’s food and beverage companies are looking for to gain real-time visibility and more precise control of their utility energy consumption. The use of key process inputs, such as air, water, steam, chemicals, gases and electricity, can be monitored and analyzed in real time, so effective and agile decisions about adjustments to compressed air systems can be made to help meet net-zero targets.
When companies that are heavy users of pneumatic technologies incorporate real-time compressed air monitoring into their operations, identifying and correcting leaks earlier and faster, the energy savings often prove to be dramatic.
Analysis and visualization for faster and better decision making
Mobility tools on multiple platforms to access alerts, information, and prescribed actions
Measurable Inputs i.e., cycles, temperature, contact status, and position
Implementing multimedia monitoring is not complex. To begin, start with one machine, line or factory. Identify and track how to improve energy use in one area of opportunity, prove a return on investment (ROI) and then scale up from there.
For food and beverage companies, monitoring compressed air does more than help meet net zero energy use goals. It can help improve equipment efficiency and ultimately lower costs. Smarter factories leverage sensors and utility monitoring systems to gather data, analyze where energy is being wasted, and take the positive steps to continuously improve sustainability and achieve their most critical goals. •
Hydraulic and lubricating oil contamination, be it abrasive solid particles or moisture, is the leading cause of shortened service life and reduced reliability in steam, gas and hydro turbines and turbo compressors. A cool, clean, consistent stream of oil is key to protecting bearings, shafts and other machine components at challenging temperatures and pressures. Likewise, continuous management of oil contamination is essential to maximize the potential of power generating turbines and to prevent unplanned shutdowns.
Poor oil quality caused by inadequate filtration costs the power generating industry millions of dollars a year in terms of lost production, spending for new oil and the added burden of unscheduled maintenance and repairs. To achieve optimal performance, it is important to consider the various aspects of hydraulic and lubricating oil filtration when operating and maintaining turbines and turbo compressors.
Proper filtration removes water and particulates like dirt and scale that cause precision machine parts to wear down and can block cooling pathways, making turbines more vulnerable to overheating and the effects of vibration. Acids and corrosive compounds also can be deposited on metal surfaces causing permanent damage. Water and air meanwhile can enter through seals in turbine and extractor vents, potentially pulling moisture and debris into the system. Steam turbines can also have leaking gland seals or steam joints. Ultimately, contaminated oil compromises turbine efficiency and power output. In turn, performance suffers, and vibration and noise levels may increase as rotating components like bearings and shafts bear the brunt of the damage.
Oxidation stability, being the relative susceptibility of oil to degradation by oxidation, is the main determinant of hydraulic and lubricating oil usefulness in turbines. High temperatures and pressures, the presence of water and air, and contaminants of all types can greatly accelerate this process. Lubricating oils use inhibitors and antioxidants to combat oil breakdown; however, this balancing act requires a precisely tuned filtration solution to keep turbines and turbo compressors running smoothly.
that one chamber is always in operation, thus eliminating the need to shut down the system as a clean chamber remains in standby mode at all times. An effective duplex filter solution will have the following performance characteristics including:
The pressure loss at the filter should be as low as practically possible to maintain optimum system flow rate and pressure. A low pressure drop also means lower energy loss.
The filter will be designed to adequately support the flow rate of the facility process.
The filter will be equipped with a sufficient amount of filter media to remove contaminants efficiently while maximizing the element’s useful life/extending change intervals.
The filter will be designed to operate efficiently at system pressures which can be up to 6.3 MPa (914 psi), thus ensuring it remains intact during normal operations with minimal risk of bursting.
Optionally, the filter can be equipped with a system designed to allow oil to bypass the filter if the element becomes clogged, thus preventing the element from collapsing. Filter bypass systems are generally not applied to contamination-sensitive lubrication systems.
Switchover valves require high-integrity design and material construction to prevent leaks that could potentially pose fire hazards.
There are additional considerations that turbine and turbo compressor operators must be aware of. Besides low-pressure duplex filtration, a complete hydraulic system, whether for the lubrication system or auxiliary systems, requires additional oil conditioning solutions including:
When a filter element changeout or service is required, filtration flow can be diverted from one side to the other. A pressure equalization system will ensure consistent pressure while the flow is being transferred.
Simplex filtration is a system that uses one filter that usually requires frequent changing and maintenance to ensure the filter element is functioning properly and free of blockages. Conversely, most turbines and turbo compressors employ a duplex filter solution.
Under normal conditions, duplex filters operate continuously with minimal maintenance. Having two filter chambers connected by a changeover valve, a duplex filter is ideal where taking machines offline is impractical or disruptive, such as in the power generating industry.
Duplex configurations help turbine operators improve oil cleanliness and eliminate downtime due to filter element changeout. This design allows the process flow to be diverted to a secondary filter chamber so
Turbine control and auxiliary hydraulic systems require continuous filtration to protect equipment and components. For lubrications systems the market offers standard and custom-built duplex filter solutions to meet different requirements for connection size (commonly 3"/DN80 to 8"/DN200) and operating pressure from 1.6 to 6.3 MPA (232 to 914 psi). In addition, common auxiliary systems can use duplex or simplex high-pressure filters with pressure requirements up to 41.4 MPa (6,000 psi). All applications must be designed to allow a sufficient margin of safety for pressure peaks in the system to be absorbed.
Additional offline filtration of lubricating oil is recommended for power generating turbines and turbo compressors. These units tend to use a side-stream return line to remove solid particles and some free and emulsified water from the oil. Offline filtration goes further to reduce oil aging and in turn spending for new oil or worse—bearing and shaft repairs. Offline filtration units have been developed for all viscosity ranges, from transformer to heavy gear oils.
continued on page 10
continued from page 9
In all types of power plants, filtration products help to ensure a reliable supply of clean, cool hydraulic and lubricating oil. These solutions (from left to right) typically include mobile filter units, oil purifier systems, clogging indicators and offline filter elements having water absorption layers.
Solutions for the effective removal of free water.
Water is a particularly destructive foreign substance in hydraulic and lubricating oil systems. Duplex filtration solutions may also employ automated purifiers to effectively remove free emulsified and dissolved water, free and dissolved gases, and particulate contamination down to 3 microns. These water removal devices are also known as vacuum dehydrators and can be added to online or offline oil systems or reservoirs.
Solutions for continuous contamination control.
Reliable indication of when to change the filter element can be important. As the filter element becomes clogged the differential pressure increases. A clogging indicator monitors the differential pressure and alerts operators when a replacement filter element is needed. Indicators should be of rugged quality and electric-explosion-proof, having multiple set points (e.g., 70% and 100% clogged) to accommodate different system requirements.
Solutions for oil conductivity.
Electrostatic discharge is common with zinc-free hydraulic and lubricating oils that do not contain the heavy metals of the previous generation of fluids. With the increasing use of synthetics in oils to replace zinc additives, oil conductivity is lowered. In turn, static charges can be generated as oil flows through the filter, causing sparks to propagate from the filter media to the filter’s metal supports. Including the risk of explosions, this can degrade the oil and create varnish, which can cause valve spools to seize up, solenoids to overheat and filters to clog.
This discharge can further damage the filter and possibly interrupt electrical systems. For oils with a conductivity below 300 pS/m (picosiemens per meter, a measure of a fluid’s electrostatic chargeability), it is recommended to use high surface area filters with anti-static elements that are designed to provide optimum filtering efficiency while reducing electrostatic discharge.
The benefits are many, including increased machine and operator safety, protection for sensitive electronic systems, low pressure drop, high dirt-holding capacity and long filter life.
Solutions for industry compliance.
Duplex filtration products and solutions may need to be designed to applicable EN 13445 (Unfired Pressure Vessels), AD 2000 (per the German Pressure Vessel Association) and ASME Sec. VIII, Div. 1 (Rules for Construction of Pressure Vessels) standards, as well as meet Pressure Equipment Directive (PED) requirements including CE Marking
where necessary. Eaton can meet the stringent design, manufacturing and testing standards that govern the supply of hydraulic filtration products to the power generating industry. Solutions and components of indefinite origin should never be considered—all products must conform to major industry certifications.
Eaton’s Filtration Division can help turbine and turbo compressor operators determine a specification for their hydraulic and lubricating oil that considers the fluid’s particulate and water removal requirements. Typically, these specifications are based on SAE (Society of Automotive Engineers), AGMA (American Gear Manufacturers Association) or ISO (International Organization for Standardization) classifications.
The need for oil cleanliness has changed over the past 20 years. Driven in part by demands from bearing manufacturers for improved oil purity and also due to environmental concerns, requirements for filter fineness have grown more stringent as the working relationships between bearing and turbine manufacturers deepen. OEM recommendations for some oil cleanliness levels are as high as 16/14/11 per ISO Cleanliness Code requirements where 16 means there are 200 to 640 particles per ml greater than 4 microns in size, 14 indicates 80 to 160 particles greater than 6 microns, and 11 indicates 10 to 20 particles greater than 14 microns.
Experts can also help to ensure the most efficient filtration process by recommending a regular maintenance schedule, one that includes steps to identify leaks and blockages. Additionally, a specialist can assess any changes in the operating process, such as using a new filter media type, and adjust the filtration strategy accordingly to maintain oils to target cleanliness levels and with minimal water content.
When oil cleanliness is a problem, often the solution is to design a single filter with a pump and motor to move the oil; however, this tends to overlook the value a new or upgraded duplex filter solution can bring. Taking steps to ensure oil cleanliness is equally important for alternative power generating sources such as wind turbines and hydrogen compressors. Reliable filtration will help various wind, solar and hydro power sources reach their full operating potential in the years ahead. While system sizing and operating pressure requirements may change, the fundamentals of effective oil filtration remain the same for power generating equipment of all types. There also exists a balance between
filter fineness and system performance that can be hard to achieve— hydraulic filtration experts can help companies achieve this balance and avoid costly mistakes and miscalculations.
Oil filtration is a critical component of reliable turbine and turbo compressor performance. Proper selection and installation of a duplex filter solution, including regular maintenance of the system, are essential for optimal performance and to prevent downtime and repairs caused by poor oil quality. A hydraulic filtration specialist can help turbine owners ensure smoother operations day in and day out by keeping hydraulic and lubricating oils clean. •
Data published by the National Fluid Power Association shows the 12 month moving average of shipments for pneumatics, hydraulics, and total fluid power starting to plateau. The year-to-date % change for total fluid power shipments in February 2023 is 10.7%. Mobile hydraulic orders received from May 2022 to April 2023 are currently 97.4% of the orders received from May 2021 to April 2022. When looking at raw index data of shipments decreased, when compared to last month. These charts are drawn from data collected from more than 70 manufacturers of fluid power products by NFPA’s Confidential Shipment Statistics (CSS) program.
Raw Index Data, Index: 2018=100
This graph of raw index data is generated by the total dollar volume reported to NFPA by CSS participants and compared to the average monthly dollar volume in 2018. For example, the April 2023 total dollar volume for pneumatic shipments is 109.6% of the average monthly dollar volume in 2018. (Base Year 2018 = 100)
The table above is expressed in terms of cumulative percent changes. These changes refer to the percent difference between the relevant cumulative total for 2023 and the total for the same months in 2022. For example, April 2023 pneumatic shipments figure of 7.4 means that for the calendar year through April 2023, pneumatic shipments increased 7.4% compared to the same time-period in 2022.
Each point on this graph represents the most recent 12 months of orders compared to the previous 12 months of orders. Each point can be read as a percentage. For example, 112.1 (the April 2023 level of the industrial hydraulic series) indicates that industrial hydraulic orders received from May 2022 to April 2023 were 112.1% of the orders received from May 2021 to April 2022.
(Base Year 2018 = 100)
Each point in this graph represents the average index for the 12 most recent months of shipments. Moving averages help clearly identify trends. The latest data shows total fluid power, total pneumatic, and total hydraulic shipment indexes starting to plateau. (Base Year 2018 = 100)
Originally from Bombay, India, Kishor J. Patel emigrated to the United States at age 17 in order to attend college. At the Milwaukee School of Engineering (MSOE), Patel earned a Mechanical Engineering degree in 1963 and started his working career at Webster Electric in Racine, Wisconsin, learning about gear pumps.
From Webster, Kishor progressively worked for Racine Hydraulic (1968–1972) and Applied Power (1972–1990). He worked for several different Divisions within Applied Power, including Power Packer, Enerpac, Dynex Rivett, and Apitec.
Patel joined G.S. Hydraulic Sales in 1990 as the general manager with the option to purchase the business and subsequently executed the acquisition in 1992. He began the transition
»A SPECIAL AWARD was established to acknowledge individuals who have dedicated their careers and have made significant contributions to Fluid Power technology. The International Fluid Power Society (IFPS) is excited to announce the induction of Kishor Patel and Myron J. Moser.
for G.S. Hydraulics from a fluid power component distributor business into a custom engineered solutions provider.
During his design career Kishor was either the primary or contributing inventor for 9 different patents, all involving proportional and pressure control valves, along with his early effort to integrate digital electronic controls. At the transformed G.S. Hydraulics, he continued to be an early adopter of integrated electronic / hydraulic solutions for equipment manufacturers.
Patel created one original patent and 10 more patents (two after retirement) to “fine tune” the original proportional electronic/ hydraulic design. Each time there was enough additional design and technological innovation to require a full stand-alone patent.
Myron J. Moser is a devoted husband and father of two. His professional contributions include creating successful tools for talent recognition, as well as global sales planning. He is also the creator of CPR(r), a trademarked customer ROI-proving process. Myron is a regular speaker at high schools, where he teaches high school youth how to discover their life’s purpose and build a pathway toward it.
As the Chairman of the Hennepin Technical College Foundation Board, he raises funds for grants, scholarships and in-kind donations. The HTC Foundation Board has raised over $18 million since inception in 1999.
Additionally, he serves as a board member for a national building products manufacturer and as a Strategic Advisory Board member for an international tax credit firm. He has also lobbied U.S. Senators and Representatives in Washington, D.C., advocating for increased Pell Grant and Perkins funding to benefit underserved populations.
Myron’s educational achievements include a degree in Fluid Power Technology from Minnesota West College. He completed Distribution Management at Texas A&M. He also completed Designing the Innovative Organization at Stanford Graduate School of Business, where he was
chosen as one of the five Finalists to present his project findings to the International class. His career began at Fauver Company (now Sunsource), working there from 1980 to 1987 before joining Air Automation Engineering, where he worked from 1988 to 1990. From 1990 to 2021, he dedicated himself to Hartfiel Automation Inc., progressively assuming roles of increased responsibility, including Vice President in 1994, President in 1995, and CEO in 1997. Myron bought out the Founder in 1999 and continued as Majority Owner, President, CEO, and Chairman from 2000 to 2021. Under Myron’s leadership, Hartfiel Automation expanded significantly. Since 2000, Myron and his Hartfiel Automation Team purchased (5) Companies and founded (4) more. Today, all (9) locations are growing and thriving in Pneumatics, Automation, Motion Control, and Robotics.
Beyond his professional life, Myron enjoys traveling, flying his family as a fully Instrument rated private pilot. He is an avid reader. He collects and restores antique cars, trucks, and tractors. Myron holds a 1st degree decided Black Belt in Tae Kwon Do. He is also the founder and former drummer of a successful classic rock band.
IFPS WELCOMES BRADLEY (BJ) Wagner as the newest addition to our team. We are delighted to introduce BJ as the second technical member of the IFPS staff, focusing on training and curriculum development. With a wealth of knowledge in fluid power, BJ brings valuable expertise to our organization. He graduated from Penn State University in 2004, earning a BS degree in Agricultural & Bio Engineering with a specialization in Power & Machinery and Fluid Mechanics. In addition, he holds minors in Off-Road Power Equipment and Youth & Family Education.
During his college years, BJ obtained his first IFPS certification as a Hydraulic Specialist. Over the course of 18 years, he gained extensive experience in the hydraulics and off-road power machinery industry, specifically in agricultural and construction mobile equipment.
BJ has a substantial background in training, expressing his passion for teaching others since his college days. He served as a 4-H leader and advisor for over 10 years and has provided training to colleagues throughout
» THE IFPS ANNUAL Meeting will be held in-person and virtually September 25-28, 2023. The in-person meeting will take place at the Pfister Hotel, Milwaukee, WI. Why attend? You’ll meet a dedicated (and fun) group of professionals who exchange ideas and technologies, on ways to improve and educate the fluid power workforce. Our board members have diverse backgrounds and work in many different segments of the industry. So, the discussion is lively and informative. Imagine the things you’ll learn!
Each of our committees, Education, Certification, Membership, Marketing and Finance, follows a mission statement and each team works together on projects to meet those goals. Our members’ input is vitally important, so if you can’t attend in person, consider joining one of our committees. Contact Jenna Mort at jmort@ifps.org.
In addition to committee meetings, tours, and networking, a Technical Workshop, Hydraulic Fluid - The “Life Blood” of Hydraulic Systems – Purpose, Performance Characteristics, Maintenance & Monitoring, will be held on Monday, September 25th Register by visiting ifps.org
his professional career. Obtaining his accredited instructor certification has allowed him to discover his true calling—educating and sharing his hydraulic experience. As an IFPS Accredited Instructor, he has taught hydraulics for over 3 years, with 2 years of formal experience in this role. BJ recognizes the importance of education and training in the industry, emphasizing the significance of safety and success in the hydraulic field.
Impressively, BJ possesses the following certifications:
• Hydraulic Specialist (CFPHS)
• Pneumatic Specialist (CFPPS)
• Specialist (CFPS)
• Mobile Hydraulic Mechanic (CFPMHM)
• Mobile Hydraulic Technician (CFPMHT)
• Connector Conductor (CFPCC)
• Master of Mobile Hydraulics (CFPMMH)
• Authorized C&C Job Performance Proctor (CFPAJPPCC)
• Authorized Job Performance Proctor (CFPAJPP)
• Accredited Instructor (CFPAI)
May 2023
Connector & Conductor (CC)
Luke Lovato, Flint Hydrualics
Toney Tolbert, Hydraquip
Brent Basham, SIT
Chris Ford, SIT
Juan Delgadillo, SIT
Rob Gingles, SIT
James Hancock, SIT
Tim Horace, SIT
Zak Brush, SIT
Brandon Holt, Supreme Integrated Technology
John Gillian
Electronic Controls Specialist (ECS)
Mark Lasch, Kraft Fluid Systems
Jordan Reisinger
Hydraulic Specialist (HS)
Sam Dallas, Hydraquip
Jeffrey Kaas, IFP Motion Solutions Inc
Eric Riegelsberger, Kraft Fluid Systems, Inc.
Weston Wedeward, Marine Travelift Inc.
Charley Shin, The Boeing Company
Daniel Wojanis, Triad Tech Llc Vandalia Oh
Cade Capps
David Check
Deepak Kadamanahalli
Jenna Sanchirico
Michael van Damme
Pawan Panwar
Industrial Hydraulic Technician (IHT)
Gerry Morgan, Hyflodraulic
Shane Froude, Hyflodraulic
Mobile Hydraulic Mechanic (MHM)
Cody Wiles, AEP
Aldann Pregillano, Altec Industries, Inc.
Daniel Schultz,Altec Industries, Inc.
Eric Herr, Altec Industries, Inc.
Garrett Hall, Altec Industries, Inc.
Jose Guzman, Altec Industries, Inc.
Erik Ramirez Rosales, Altec Industries, Inc.
James Dale, Altec Industries, Inc.
Shawn Lanter, Altec Industries, Inc.
Tony Archer, Altec Industries, Inc.
Chris Rathbun, Clay Electric
Joe Ruby, Clay Electric
Daniel Ricker, Columbia River PUD
Matthew Langenberg, Dawson Power
Jared Dahlheimer, Great River Energy
Zachary Sirrell, Kissimmee Utility Authority
Ian Lofberg, Skamania PUD
Tyler Turrietta, Skamania PUD
Ross Wood, Suwannee Valley Electric Coop
Daniel Einspahr, Tampa Electric Company
Michael Pope
Pneumatic Specialist (PS)
William Venable, Cross Company
Joshua Rodman, Motion Industries, Inc.
Specialist (S)
Joshua Rodman, Motion Industries, Inc.
» THE IFPS RELEASED a new and upgraded Connector and Conductor Certification and is now available to order! The new release includes an enhanced study manual and test.
In addition to the study manual, and tests, a companion PowerPoint presentation has been released, and Interactive Training Modules are coming soon!
• Both the written and Job Performance portions are included in one study manual.
For more information, visit www.ifps.org/web-seminars.
UPCOMING WEB SEMINARS
How to Read Hydraulic/Pneumatic Schematics
When: Aug. 17, 12-1 p.m. [ET]
Principals of Hydraulics: Is It Really Magic?
When: Sept. 14, 12 p.m. [ET]
Conductor Identification
When: Oct. 5, 12 p.m. [ET]
Calculating the Useable Amount of Oil from a Pneumatic Accumulator
When: Nov. 2, 12 p.m. [ET]
• Additional Safety Information, including over 25 Safety tips!
• Pages and pages of full-color photos and graphics are available to download!
• Additional information on measuring implements.
• Added additional Fluid Compatibility information.
• Updated/added pressure rating and pipe tubing information.
• Added metric units throughout.
• Standards updated/added to conform with the latest:
› ISO 1219
› SAE J517
› ISO 8572
› ISO 6149-1
› ISO 9974-1
› Code 61 & 62 Flanges
• Improved graphics throughout and many real-life photos to assist in visualization.
ALABAMA
Auburn, AL
Birmingham, AL
Individuals wishing to take any IFPS written certification tests can select from convenient locations across the United States and Canada. IFPS is able to offer these locations through its affiliation with the Consortium of College testing Centers provided by National College testing Association.
Contact Kyle Pollander at Kpollander@ifps.org if you do not see a location near you. Every effort will be made to accommodate your needs.
Calera, AL
Decatur, AL
Huntsville, AL
Jacksonville, AL
Mobile, AL
Montgomery, AL
Normal, AL
Tuscaloosa, AL
ALAsKA
Anchorage, AK
Fairbanks, AK
ARIZONA
Flagstaff, AZ
Glendale, AZ
Mesa, AZ
Phoenix, AZ
Prescott, AZ
Scottsdale, AZ
Sierra Vista, AZ
Tempe, AZ
Thatcher, AZ
Tucson, AZ
Yuma, AZ
ARKANsAs
Bentonville, AR
Hot Springs, AR
Little Rock, AR
CALIFORNIA
Aptos, CA
Arcata, CA
t EN tAtIVE t E stIN g DAt E s FOR ALL LOCAtION s:
September 2023
Tuesday 9/12 • Thursday 9/21
October 2023
Monday 10/2 • Thursday 10/26
November 2023
Tuesday 11/7 • Thursday 11/30
December 2023
Tuesday 12/5 • Thursday 12/14
Bakersfield, CA
Dixon, CA
Encinitas, CA
Fresno, CA
Irvine, CA
Marysville, CA
Riverside, CA
Salinas, CA
San Diego, CA
San Jose, CA
San Luis Obispo, CA
Santa Ana, CA
Santa Maria, CA
Santa Rosa, CA
Tustin, CA
Yucaipa, CA
COLORADO
Aurora, CO
Boulder, CO
Springs, CO
Denver, CO
Durango, CO
Ft. Collins, CO
Greeley, CO
Lakewood, CO
Littleton, CO
Pueblo, CO
DELAWARE
Tallahassee, FL
Tampa, FL
West Palm Beach, FL
Wildwood, FL
Winter Haven, FL
gEORgIA
Albany, GA
Athens, GA
Atlanta, GA
Carrollton, GA
Columbus, GA
Dahlonega, GA
Dublin, GA
Dunwoody, GA
Forest Park, GA
Lawrenceville, GA
Morrow, GA
Oakwood, GA
Savannah, GA
Statesboro, GA
Tifton, GA
Valdosta, GA
HAWAII
Laie, HI
IDAHO
Boise, ID
Coeur d ‘Alene, ID
Idaho Falls, ID
Lewiston, ID
Moscow, ID
Nampa, ID
Rexburg, ID
Twin Falls, ID
ILLINOIs
Carbondale, IL
Carterville, IL
Champaign, IL
Decatur, IL
Edwardsville, IL
Glen Ellyn, IL
Joliet, IL
Malta, IL
Normal, IL
Peoria, IL
Schaumburg, IL
Springfield, IL
University Park, IL
INDIANA
Bloomington, IN
Columbus, IN
Evansville, IN
Fort Wayne, IN
Gary, IN
Indianapolis, IN
Kokomo, IN
Lafayette, IN
Lawrenceburg, IN
Madison, IN
Muncie, IN
New Albany, IN
Richmond, IN
Sellersburg, IN
JOB PERFORMANCE
t E st LOCAtION s
Arizona
California
Colorado
Florida
Georgia
Maine
Michigan
Minnesota
Montana
New Jersey
Nova Scotia Pennsylvania Texas Washington Wyoming Western Australia
Dover, DE
Georgetown, DE
Newark, DE
FLORIDA
Avon Park, FL
Boca Raton, FL
Cocoa, FL
Davie, FL
Daytona Beach, FL
Fort Pierce, FL
Ft. Myers, FL
Gainesville, FL
Jacksonville, FL
Miami Gardens, FL
Milton, FL
New Port Richey, FL
Ocala, FL
Orlando, FL
Panama City, FL
Pembroke Pines, FL
Pensacola, FL
Plant City, FL
Riviera Beach, FL
Sanford, FL
LOuIsIANA
Bossier City, LA
Lafayette, LA
Monroe, LA
Natchitoches, LA
New Orleans, LA
Shreveport, LA
Thibodaux, LA
MARYLAND
Arnold, MD
Bel Air, MD
College Park, MD
Frederick, MD
Hagerstown, MD
La Plata, MD
Westminster, MD
Woodlawn, MD
Wye Mills, MD
MAssACHusEtts
Boston, MA
Bridgewater, MA
Danvers, MA
Haverhill, MA
Holyoke, MA
Shrewsbury, MA
MICHIgAN
Ann Arbor, MI
Big Rapids, MI
Chesterfield, MI
Dearborn, MI
Dowagiac, MI
East Lansing, MI
Flint, MI
Grand Rapids, MI
Kalamazoo, MI
Lansing, MI
Livonia, MI
Mount Pleasant, MI
Sault Ste. Marie, M
Troy, MI
University Center, MI
Warren, MI
MINNEsOtA
Alexandria, MN
Brooklyn Park, MN
Duluth, MN
Eden Prairie, MN
Granite Falls, MN
Mankato, MN
MIssIssIPPI
Goodman, MS
Jackson, MS
Mississippi State, MS
Raymond, MS
University, MS
MIssOuRI
Berkley, MO
Cape Girardeau, MO
Columbia, MO
Cottleville, MO
Joplin, MO
Kansas City, MO
South Bend, IN
Terre Haute, IN
IOWA
Ames, IA
Cedar Rapids, IA
Iowa City, IA
Ottumwa, IA
Sioux City, IA
Waterloo, IA
KANsAs
Kansas City, KS
Lawrence, KS
Manhattan, KS
Wichita, KS
KENtuCKY
Ashland, KY
Bowling Green, KY
Erlanger, KY
Highland Heights, KY
Louisville, KY
Morehead, KY
NEW JERsEY
Branchburg, NJ
Cherry Hill, NJ
Lincroft, NJ
Sewell, NJ
Toms River, NJ
West Windsor, NJ
NEW MEXICO
Albuquerque, NM
Clovis, NM
Farmington, NM
Portales, NM
Santa Fe, NM
NEW YORK
Alfred, NY
Brooklyn, NY
Buffalo, NY
Garden City, NY
New York, NY
Rochester, NY
Syracuse, NY
NORtH CAROLINA
Apex, NC
Asheville, NC
Boone, NC
Charlotte, NC
China Grove, NC
Durham, NC
Fayetteville, NC
Greenville, NC
Jamestown, NC
Misenheimer, NC
Mount Airy, NC
Pembroke, NC
Raleigh, NC
Wilmington, NC
NORtH DAKOtA
Bismarck, ND
OHIO
Akron, OH
Cincinnati, OH
Cleveland, OH
Columbus, OH
Fairfield, OH
Findlay, OH
Kirtland, OH
Lima, OH
Maumee, OH
Newark, OH
North Royalton, OH
Rio Grande, OH
Toledo, OH
Warren, OH
Youngstown, OH
OKLAHOMA
Altus, OK
Bethany, OK
Edmond, OK
Norman, OK
Oklahoma City, OK
Tonkawa, OK
Tulsa, OK
sOutH CAROLINA
Beaufort, SC
Charleston, SC
Columbia, SC
Conway, SC
Graniteville, SC
Greenville, SC
Greenwood, SC
Orangeburg, SC
Rock Hill, SC
Spartanburg, SC
tENNEssEE
Blountville, TN
Clarksville, TN
Collegedale, TN
Gallatin, TN
Johnson City, TN
Knoxville, TN
Memphis, TN
Morristown, TN
Murfreesboro, TN
Nashville, TN
tEXAs
Abilene, TX
Arlington, TX
Austin, TX
Beaumont, TX
Brownsville, TX
Commerce, TX
Corpus Christi, TX
Dallas, TX
Denison, TX
El Paso, TX
Houston, TX
Huntsville, TX
Laredo, TX
Lubbock, TX
Lufkin, TX
Mesquite, TX
San Antonio, TX
Victoria, TX
Waxahachie, TX
Weatherford, TX
Wichita Falls, TX
utAH
Cedar City, UT
Kaysville, UT
Logan, UT
Ogden, UT
Orem, UT
Salt Lake City, UT
VIRgINIA
Daleville, VA
Fredericksburg, VA
Lynchburg, VA
Manassas, VA
Norfolk, VA
Roanoke, VA
Salem, VA
Staunton, VA
Suffolk, VA
Virginia Beach, VA
Wytheville, VA
WYOMINg
Casper, WY
Laramie, WY
Torrington, WY
CANADA
ALBERtA
Calgary, AB
Edmonton, AB
Fort McMurray, AB
Lethbridge, AB
Lloydminster, AB
Olds, AB
Red Deer, AB
BRItIsH
COLuMBIA
Abbotsford, BC
Burnaby, BC
Castlegar, BC
Delta, BC
Kamloops, BC
Nanaimo, BC
Prince George, BC
Richmond, BC
Surrey, BC
Vancouver, BC
Victoria, BC
MANItOBA
Brandon, MB
Winnipeg, MB
NEW BRuNsWICK
Bathurst, NB
Moncton, NB
NEWFOuNDLAND
AND LABRADOR
St. John’s, NL
NOVA sCOtIA
Halifax, NS
ONtARIO
Brockville, ON
Hamilton, ON
London, ON
Milton, ON
Mississauga, ON
Niagara-on-the-Lake, ON
North Bay, ON
North York, ON
Ottawa, ON
Toronto, ON
Welland, ON
Windsor, ON
QuEBEC
Côte Saint-Luc, QB
Montreal, QB
sAsKAtCHEWAN
Melfort, SK
Moose Jaw, SK
Nipawin, SK
Prince Albert, SK
Saskatoon, SK
Kirksville, MO
Park Hills, MO
Poplar Bluff, MO
Rolla, MO
Sedalia, MO
Springfield, MO
St. Joseph, MO
St. Louis, MO
Warrensburg, MO
MONtANA
Bozeman, MT
Missoula, MT
NEBRAsKA
Lincoln, NE
North Platte, NE
Omaha, NE
NEVADA
Henderson, NV
Las Vegas, NV
North Las Vegas, NV
Winnemucca, NV
OREgON
Bend, OR
Coos Bay, OR
Eugene, OR
Gresham, OR
Klamath Falls, OR
Medford, OR
Oregon City, OR
Portland, OR
White City, OR
PENNsYLVANIA
Bloomsburg, PA
Blue Bell, PA
Gettysburg, PA
Harrisburg, PA
Lancaster, PA
Newtown, PA
Philadelphia, PA
Pittsburgh, PA
Wilkes-Barre, PA
York, PA
WAsHINgtON
Auburn, WA
Bellingham, WA
Bremerton, WA
Ellensburg, WA
Ephrata, WA
Olympia, WA
Pasco, WA
Rockingham, WA
Seattle, WA
Shoreline, WA
Spokane, WA
WEst VIRgINIA
Ona, WV
WIsCONsIN
La Crosse, WI
Milwaukee, WI
Mukwonago, WI
YuKON tERRItORY
Whitehorse, YU
uNItED KINgDOM
Elgin, UK
gHAZNI
Kingdom of Bahrain, GHA
Thomasville, GHA
EgYPt
Cairo, EG
JORDAN
Amman, JOR
NEW ZEALAND
Taradale, NZ
CFPs Certified Fluid Power Specialist (Must Obtain CFPHS & CFPPS)
CFPHs Certified Fluid Power Hydraulic Specialist
CFPPs Certified Fluid Power Pneumatic Specialist
CFPECs Certified Fluid Power Electronic Controls Specialist
CFPMt Certified Fluid Power Master Technician (Must Obtain CFPIHT, CFPMHT, & CFPPT)
CFPIHt Certified Fluid Power Industrial Hydraulic Technician
CFPMHt Certified Fluid Power Mobile Hydraulic Technician
CFPPt Certified Fluid Power
Pneumatic Technician
CFPMM Certified Fluid Power Master Mechanic (Must Obtain CFPIHM, CFPMHM, & CFPPM)
CFPIHM Certified Fluid Power Industrial Hydraulic Mechanic
CFPMHM
Certified Fluid Power Mobile Hydraulic Mechanic
CFPPM Certified Fluid Power
Pneumatic Mechanic
CFPMIH Certified Fluid Power Master of Industrial Hydraulics
(Must Obtain CFPIHM, CFPIHT, & CFPCC)
CFPMMH
Certified Fluid Power
Master of Mobile Hydraulics
(Must Obtain CFPMHM, CFPMHT, & CFPCC)
CFPMIP
Certified Fluid Power
Master of Industrial Pneumatics (Must Obtain CFPPM, CFPPT, & CFPCC)
CFPCC Certified Fluid Power
Connector & Conductor
CFPsD
Fluid Power System Designer
IFPS offers onsite review training for small groups of at least 10 persons. An IFPS accredited instructor visits your company to conduct the review. Contact kpollander@ifps.org for details of the scheduled onsite reviews listed below.
HYDRAuLIC sPECIALIst
Aug. 14-17, Fairfield, OH, CFC Industrial Training, Written test: Aug. 18.
Dec. 4-7, 2023, Fairfield, OH, CFC Industrial Training. Written test: Dec. 8, 2023.
ELECtRONIC CONtROLs sPECIALIst
For dates, call CFC Industrial Training at (513)874-3225 or visit www.cfcindustrialtraining.com.
PNEuMAtIC sPECIALIst
Nov. 13-16, Fairfield, OH, CFC Industrial Training. Written test: Nov. 17.
CONNECtOR & CONDuCtOR
Nov. 15-16, Fairfield, OH, CFC Industrial Training. Written and JP test: Nov. 17.
MOBILE HYDRAuLIC MECHANIC
Oct. 23-26, Fairfield, OH, CFC Industrial Training. Written and JP test: Oct. 27.
Online Mobile Hydraulic Mechanic certification review for written test is offered through CFC Industrial Training. This course surveys the MHM Study Manual (6.5 hours) and every outcome to prepare you for the written test. Members may e-mail for a 20% coupon code off the list price. Test fees are not included.
INDustRIAL HYDRAuLIC MECHANIC
For dates, call CFC Industrial Training at (513)874-3225 or visit www.cfcindustrialtraining.com.
INDustRIAL HYDRAuLIC tECHNICIAN
For dates, call CFC Industrial Training at (513) 874-3225 or visit www.cfcindustrialtraining.com.
MOBILE HYDRAuLIC tECHNICIAN
Sept. 18-21, Fairfield, OH, CFC Industrial Training. Written and JP test: Sept. 22.
PNEuMAtIC tECHNICIAN and PNEuMAtIC MECHANIC
For dates, call CFC Industrial Training at (513)874-3225 or visit www.cfcindustrialtraining.com.
JOB PERFORMANCE tRAININg
CFC Industrial Training offers an online Job Performance Review that includes stations 1-6 of the mechanic and technician Job Performance tests. Members may e-mail IFPS for a 20% coupon code off the list price. Test fees are not included. CFC also offers live distance learning Job Performance Station Reviews. To register or purchase, contact CFC Industrial Training at (513) 874-3225 or visit www.cfcindustrialtraining.com.
Left to its own devices, most machinery or equipment will sooner or later go wrong. Sometimes it will fail completely and other times it may continue to operate but at a reduced, and probably declining, level of performance. If the machinery needs to be restored to full working condition, rather than scrapped, then either breakdown or corrective maintenance will be required. Where the consequences of a failure are relatively insignificant, then this can be an acceptable maintenance approach. The failure of a bulb in a bedside light or the battery in a tv remote control would not cause too much of a problem and are easily remedied. But a sudden failure of a component on a piece of mobile equipment or agricultural machinery could be much more costly and potentially dangerous. So, on anything but the simplest of machines, reactive or breakdown maintenance is seldom the best approach, both from a cost and disruption point of view. But the fact that many motorists still make use of roadside breakdown services suggests that it may not be possible to avoid it altogether.
Considering the example of a hydraulic pump, an unexpected and catastrophic failure is likely to bring the machine it was powering to a standstill. Without even considering any safety aspects of the failure, such a breakdown is likely to cost significant money due to lost production, potential penalty clauses or spoiled crops. There will also be a cost involved in locating and shipping a replacement unit, supplying or
paying for labour to fit it, and probably flushing the system to remove debris from the failed unit. Failure to remove contamination caused by a failed pump is very likely to cause another failure shortly afterwards. So, the sudden, unexpected failures of vulnerable components such as pumps, motors, hoses etc., need to be avoided whenever possible.
The question is, how can such breakdowns be avoided? Preventive maintenance is a technique that has been successfully used to at least minimise unexpected failures even if it may not eliminate them all together. This process involves determining the useful life of a component and replacing or refurbishing it before a total failure occurs. Life estimates may be based upon manufacturer’s data, testing or experience but will also depend very much upon the operating conditions of the component. It’s a procedure adopted by many automobile manufacturers who specify such things as oil changes or cam belt replacement after recommended periods of use.
But the life of a hydraulic pump for example, is not always easy to determine. It will depend upon factors such as the working pressure and duty cycle, the pump drive speed, the type and condition of the fluid (cleanliness and temperature), the pump inlet conditions etc. With a Preventive Maintenance approach, if the life of the pump is under-estimated then it’s likely to be replaced with many hours of useful life still remaining. But if its life is over-estimated then it’s possible it will fail catastrophically before its scheduled replacement time (fig. 1).
insulated cabs where detecting a machine abnormality is not so easy. Also, the growing trend towards autonomous vehicles removes the operator completely from the machine so machine parameters now have to be sensed by equipment other than human eyes and ears.
How components are monitored or how performance level is defined will vary from one type of component to another. For a cylinder it could be the amount of port leakage in a dead-head situation for example, which would indicate the condition of the piston seals. For a hydraulic motor a vibration sensor could indicate the condition of the shaft bearings and may even be able to determine which particular bearing is starting to fail. A gas pressure sensor on an accumulator could monitor the pre-charge pressure whenever the accumulator was drained of fluid. Hydraulic components which are worn or damaged often generate more than a normal amount of heat so sensing the temperature of a component can indicate when an investigation should be carried out. Excessive heat however can be created in several areas of a hydraulic system, such as an incorrectly adjusted relief valve for example, so further investigation may be required to determine the precise source of the heat. Monitoring fluid cleanliness and water content has been possible for many years by taking fluid samples and analysing them off-line. But on-line fluid condition monitors are now readily available to continuously sense the fluid condition and create alarm signals when it exceeds pre-defined limits. However, in many situations Predictive Maintenance will involve monitoring the two basic components of hydraulic power, i.e., fluid
continued on page 20
For more about LE’s high-performance lubricants, contact us or visit our website today.
Hydraulic Oils are engineered to ensure smooth performance and superior protection for your equipment.
Monitoring pressure in a hydraulic system is a relatively simple process as it only requires a very small connection from the system to the pressure monitoring device. But unfortunately, many performance losses which can occur in a system may not be evident simply by monitoring pressure alone. For example, a deterioration in pump flow caused by wear or damage will inevitably result in reduced machine performance but may not result in any change of pressure. A pump which is only delivering half of its theoretical flow would still be able to move a load and so generate normal load pressure but would only operate the load at a much reduced speed.
But a slow cylinder speed could be caused by either a failure of the cylinder piston seals or a lack of pump flow, so without further investigation it may not be possible to determine which. A flow meter installed in the pump outlet however could provide enough information to immediately identify which component was at fault, (fig.2).
So, for a hydraulic pump or motor, volumetric efficiency may be a good indicator of the component’s state of wear. Volumetric efficiency involves comparing a pump’s actual flow output with its theoretical output at a specified working pressure, drive speed and fluid viscosity. Manufacturing clearances, internal lubrication passages and control flows mean that even brand-new pumps will have a volumetric efficiency less than 100%, but if a pump’s current efficiency can be compared to that when new and operating under the same working conditions, then a good estimation can be made of how far through its useful life it is or if its condition is deteriorating rapidly.
Fast, precise, simple and elegant.
Use Delta RMC motion controllers and graphical RMCTools software to simplify and improve complex motion.1-50 axes of synchronized position, velocity and pressure/force control.
Visit our website for videos, case studies, and specifications. Find a case study of your industry and application.
Discover simple, fast, and precise electro-hydraulic motion at deltamotion.com
Measuring system flow rates is not quite as easy as measuring pressure since full bore connections are required to be made in and out of the flow meter, often at high pressure. Also, measuring outlet flow to determine volumetric efficiency at a single point in time may not provide information that is very useful. It doesn’t provide any information about the pump’s performance history, nor does it enable its remaining life to be estimated with any degree of certainty. Wear or degradation of a component does not always occur in a gradual or linear manner and will often accelerate as the wear increases. A predictive maintenance process really requires the component’s performance to at least be monitored at regular, scheduled intervals. This will then provide a history of the pump’s performance over time and enable a more realistic assessment of its remaining life.
Even this approach, however, depends on whether provision has been made to easily connect a flow meter into the system and if the monitoring has been carried out consistently
and diligently at the specified time intervals and under the same working conditions. Care must be taken to ensure that measurements are taken at the same pump drive speed, and with the fluid at the same temperature and pressure. This may not always be practical while a machine is operating on-line, especially if the pump is a variable displacement unit when the output flow will be varying naturally. So very often measurements will need to be carried out with the machine off-line so that a predictable and consistent test routine can be carried out on the pump. How often these test routines should be carried out is another factor that will need to be determined. Too long an interval runs the risk of the pump deteriorating rapidly in between tests and a catastrophic failure could still then occur.
An even better procedure would be to monitor the pump’s performance continuously, so that any sudden deterioration in performance could
be detected immediately and the appropriate action taken. This then requires a simple, robust flow monitor permanently installed in the system such as the Webtec CTA Series turbine type flow monitor which provides both a temperature and a flow rate output signal compatible with SAE J1939 CANbus communication as used on many vehicles.
The principle of operation of the CTA Flow Monitor is a well proven design which uses a turbine wheel mounted in the flow stream and a sensor which senses the passing of each turbine blade. As flow passes through the flow monitor, the turbine blade spins at a speed proportional to the flow rate. The on-board electronics then convert the sensor pulses into a flow rate signal which can be transmitted via the CANbus signal to the vehicle’s main supervisory control system (fig 3).
continued on page 22
continued from page 21
The same sensor is also used to monitor fluid temperature which can form part of the system performance evaluation process or, if necessary, used to modify the flow monitor reading to compensate for fluid viscosity changes with temperature.
Combined with drive speed and system pressure sensor signals, a permanently installed flow monitor can thus form an important part of the predictive maintenance process on a vehicle. By communicating directly to the vehicle’s control and monitoring network, on-line performance data can be transmitted to the ‘cloud’ or Internet of Things (IoT) from where it can be downloaded and analysed in real time and appropriate alarms raised as necessary (fig. 4).
Monitoring a piston pump’s case drain has also been used as a means of assessing volumetric efficiency on the assumption that all additional leakage caused by wear enters the pump case and therefore exits via the drain connection. It might be assumed therefore that this would be a suitable location for a permanently installed flow monitor since the flow rate involved would be less than the full pump flow, and at a lower pressure, thus requiring a smaller unit. There are two considerations to be aware of with this approach however, firstly, it may not be correct to assume that all internal leakage passes through the case drain line since leakage direct from outlet port to inlet port can also occur across a worn valve plate for example. Also, some pumps are fitted with a case to inlet check valve so monitoring the drain flow may not give a true indication of the total internal leakage. Secondly, great care must be exercised in adding components to pump and motor drain lines as any additional restriction is likely to raise the case pressure causing additional stress and potential wear on the unit’s shaft seal. Over time it may also create a wear groove on the shaft itself caused by pressure acting on the lip of the seal. But particularly with variable displacement axial piston pumps, which are probably the most common type of pump used in larger mobile applications, a high case pressure can cause the piston shoes to lift off the swash plate or separate from the spherical end of the piston, both of which are likely to cause a catastrophic pump failure. It must also be remembered that very high case drain flows can be created momentarily due to the movement of the swash plate control piston. Some pumps have case pressure limitations as low as 0.03 MPa (4 psi) and the limitation in many pumps will be less than 0.05 MPa (7 psi) greater than the inlet port pressure. A common cause of catastrophic failures due to piston and shoe separation can therefore be attributed to a high case pressure combined with a low inlet port pressure.
In most applications, monitoring the full pump output flow is the recommended approach. The rugged and compact design of the Webtec CTA Series Flow Monitor make it ideal for on and off-highway vehicles and other machinery where the cost and disruption caused by downtime needs to be reduced to a minimum. Typically, this could include earthmoving and construction machines, agricultural equipment, mining and quarrying machinery, municipal vehicles and cranes and especially autonomous vehicles where reduced performance may otherwise go unnoticed.
Pump output is not the only area where flow monitoring can be useful. The volumetric efficiency of a hydraulic motor can be determined by comparing the motor inlet flow with its rotational speed. On-board speed sensors are common options on many hydraulic motors so by knowing the motor displacement, the inlet flow data from a flow monitor can provide sufficient information to determine the performance level of the motor.
Beneficial as it may be in predictive maintenance applications, there are also other situations where Webtec’s flow monitor may be useful. In difficult environments, sensing an actuator’s speed at the actuator itself can sometimes be challenging where rain, sea-water spray, falling rocks, electrical interference etc. may present difficulties. However, monitoring the fluid flow rate to or from an actuator will give a good indication of the actuator’s speed. The CTA Series Flow Monitors have been specifically designed to be fully EMC compliant, resistant to water spray and steam cleaning, and unaffected by heavy vibration so using a flow monitor may sometimes provide an alternative feedback device when controlling the speed of an actuator.
While the cost of on-line sensors and their communication network has fallen in recent times, there will still be an initial cost penalty involved in an arrangement as shown in figure 4. However, the additional cost will be substantially less than the cost of the first unexpected breakdown.
So, when used as part of a vehicle’s control, safety, or predictive maintenance system, a permanently installed flow monitor combined with state-of-the-art communication capability can provide the next level of productivity improvements and continue the trend towards on-line condition monitoring. •
The acronym “STAMPED,” as used for hose assemblies, is equally as important to use when developing tube assemblies. The same factors apply; only the fabrication and installation will vary. Flow and pressure charts can be found from the same technical references.
SSIZE: The size of the tubing is based on:
1. Flow (GPM)
2. Flow velocity (ft/sec)
3. Pressure
4. External corrosion
All hydraulic tubing is measured on the outside diameter (O.D.). The fluid velocity is based on the flow rate, liters per minute (lpm), or gallons per minute (GPM) flowing through the tube. This can be calculated or found on charts and in technical references.
Note: When calculating cylinder extension speed, use the cap-end piston area. When calculating retraction speed, use the annulus area. When calculating the velocity of the fluid, use the area of the conductor’s I.D.
Pressure is included in sizing here as well as under the “P” later on in “STAMPED”. Flow losses (pressure drop) can affect sizing the tubing. Length of line and configuration (elbows and number of fittings) can add to pressure losses, dictating a larger tube I.D. (see example chart at the end of this outcome). Low temperatures can also affect viscosity, which in turn will affect pressure drop. Wall thickness at bent tube sections will have reduced wall size. This will require the designer to determine the amount of reduction based on the bend radius and to recalculate allowable working pressure for the particular bend.
TTEMPERATURE: The temperature can be a factor with tubing and fittings, but usually not until temperatures are extreme, above 175°C (350°F) or below 43°C (45°F). High and low temperatures can affect O-rings in fittings and the selection of tubing.
continued on page 24
continued from page 23
AAPPLICATION: The application will determine where the new or replacement tube assembly is to be used. Most often, only a duplicate of the original will be required, provided the original assembly gave acceptable service life. On some applications where corrosion is anticipated, the life of the system can be extended by increasing the wall thickness to compensate. To fulfill the requirements of the application, additional questions may need to be answered, such as:
Where will assembly be used, working and surge pressures, suction application, type of tubing, fitting type, fluid/ ambient temperature, fluid compatibility, environmental, minimum bend radius, routing, government & industry standards, mechanical loads, excessive abrasion, expected service life, and external corrosion.
MMATERIAL: The tube selection and fittings must assure compatibility with the fluid to be circulated in the system, as well as the environmental conditions.
Note: Many swivel elbow fittings contain O-rings which must be compatible with the fluid and environmental conditions.
PPRESSURE: When selecting metal tube, it is vital to know the working pressure, including pressure spikes. Pressure spikes greater than the published working pressures will shorten the system service life and must be taken into consideration. Published tube working pressures must be equal to or greater than the system pressure. Thinning of the tube wall at bends must also be considered.
Burst pressures are reference pressures intended for destructive testing purposes and design safety factors only. Typically, for dynamic hydraulic applications, the minimum burst pressure rating is four times that of the maximum working pressure rating.
EENDS: The ends identify the tube end fittings using manufacturers’ catalogs.
DDELIVERY: Delivery is determined by availability, time to assemble, special packaging, shipping, and documentation.
Note: The table example chart shown above may be used for sizing fluid passages between hydraulic components when flow rates are known. Tabulations
are based on a hydraulic oil having a viscosity of 155 SUS (CS 33.1) and a specific gravity of 1.
These pressure losses vary from the tables with changes in temperature, viscosity, I.D. roughness, and number of bends and fittings.
These notes and formulas apply to the pressure loss charts for SAE tubes and hose that follow:
• Flow is laminar if N r < 2,000
• Flow is transitional if 2,000 < Nr < 4,000
• Flow is turbulent if N r > 4,000
• To correct the pressure drop values for specific gravity other than 1.0, multiply the pressure drop values by the new specific gravity. Corrections for viscosity change may be made directly to all laminar flow pressure drop values in the table by the ratio of New value (CS) ÷ 33.1 if the new value CS > 33.1. For new values below CS 33.1 the Reynolds number (Nr) may change to a value above 2000, in which case a complete new calculation should be made. This condition of Nr > 2,000 will most likely occur near the boundary (bold line) that divides transitional and laminar flow sections of this table. •
1. All hydraulic tubing is measured by its: a.
e. Material type.
2. Anticipating a corrosion problem, one could:
a. Increase volume.
b. Decrease volume.
c. Increase pressure.
d. Decrease wall thickness.
e. Increase wall thickness. See page 29 for the solution.
Note: The chart shown to the left is an excerpt from the IFPS Fluid Power Reference Handbook where you will find full versions of these (and many other) fluid power charts. Scan the QR code to view the product page for the Fluid Power Reference Handbook.
The shift towards smart manufacturing is pivotal in the evolution of the fluid power industry, shaping how hydraulic and pneumatic systems operate. A closer look at what smart manufacturing encompasses is instrumental in understanding this transition's depth and potential.
Smart manufacturing is primarily an umbrella term, encapsulating various technologies and methods that use data, machine learning, and interconnected systems to optimize and refine manufacturing procedures. It signifies the amalgamation of IIoT — a network of devices furnished with sensors and software for data collection and exchange — with the analytical prowess of AI and big data.
In fluid power systems, these technologies endow hydraulic and pneumatic mechanisms with heightened autonomy and intelligence, fostering real-time monitoring and proactive maintenance. This combination — IoT, AI and big data — transforms the approach to maintenance through smart manufacturing, driving the industry towards predictive maintenance and beyond the traditional reactive measures.
A defining feature of smart manufacturing in the fluid power industry is its transition from reactive to predictive maintenance. Traditional reactive maintenance has long been the norm in the industry. However, it carries with it inherent inefficiencies and risks, including equipment downtime and the potential for cascading failures.
Predictive maintenance, in contrast, seeks to prevent these issues by identifying potential problems before they occur. This approach leverages the power of IoT sensors embedded in hydraulic systems, which collect real-time data on a multitude of parameters, such as pressure, temperature, and flow rate. This wealth of data is then processed by AI algorithms,
which can identify subtle patterns and anomalies indicating system failures. In essence, predictive maintenance allows fluid power professionals to address issues proactively, optimizing the performance and lifespan of the hydraulic and pneumatic systems under their care, while minimizing disruptive and costly unexpected failures.
The benefits of predictive maintenance in smart manufacturing are multifaceted, with significant improvements in efficiency and performance being most noteworthy. In the hydraulic and pneumatic systems of the fluid power industry, uninterrupted operation is key to productivity. Predictive maintenance harnesses the continuous data stream from IoT sensors to optimize the system performance, identifying signs of potential failure long before they escalate into actual problems.
This ensures timely corrective measures, drastically reducing system downtime and enhancing operational efficiency. An example is the implementation of predictive maintenance in an industrial pneumatic system. Historical data showed that the system was prone to unexpected pressure drops, leading to unscheduled halts in production. Using AI-driven predictive analysis, engineers were able to predict these events before they occurred, managing to reduce system downtime by 30%. This case underlines the transformative effect of smart manufacturing and predictive maintenance on fluid power systems.
The implementation of predictive maintenance in smart manufacturing also has significant financial implications. It can lead to considerable cost reductions primarily by minimizing unscheduled downtime and reducing the losses associated with interrupted production. However, the cost of implementing these technologies must also be factored into the equation. The initial investment may be substantial, but when balanced against the cost savings achieved, the return on investment becomes clear. Furthermore, the efficiency improvements offered by predictive maintenance lead to lower energy consumption, contributing to further cost savings. Therefore, despite the upfront costs, the financial implications of embracing smart manufacturing are predominantly positive, promising long-term profitability for fluid power operations.
Another significant impact of smart manufacturing and predictive maintenance is the enhancement of safety and compliance. This is primarily achieved by reducing the risks associated with unexpected equipment failure, which can lead to accidents and safety hazards.
Sensors and AI can monitor for irregularities or deviations in performance that, if unaddressed, could result in component failure and potentially hazardous situations. Through early detection, necessary maintenance can be scheduled proactively, thereby ensuring a safer working environment. Moreover, smart manufacturing tools also facilitate compliance with industry regulations and standards. Detailed, real-time data simplifies audit processes and compliance reporting. This offers fluid power engineers and technicians greater confidence in their regulatory compliance and adherence to industry standards. Therefore, predictive maintenance not only ensures the smooth operation of hydraulic and pneumatic systems but also contributes to safer work environments and easier regulatory compliance.
Smart manufacturing is reshaping the roles and skills required of engineers and technicians in the fluid power industry. Traditional roles, often centered on reactive troubleshooting and repairs, are evolving to incorporate elements of data analysis, machine learning, and systems networking.
The shift to predictive maintenance necessitates a new proficiency in interpreting sensor data and recognizing patterns that may indicate potential system failures. Professionals in the field must now be comfortable with a range of technologies that underpin smart manufacturing.
As part of this digital transformation, fluid power professionals must also enhance their knowledge of regulatory standards related to digital data security and privacy. With hydraulic and pneumatic systems increasingly interconnected and generating vast amounts of operational data, ensuring the integrity and security of this data is paramount.
Yet, despite the changes, the fundamental principles of fluid power systems — hydraulics and pneumatics — remain at the heart of the industry. Understanding these principles enables a more effective application of new technologies like predictive maintenance, which helps plants reap the full benefits of smart manufacturing. A combination of traditional engineering skills and a strong understanding of emerging technologies is what positions fluid power professionals to excel and drive their industry forward.
As with any significant technological transition, there are challenges that the fluid power industry faces in adopting smart manufacturing. Foremost among these is the initial investment required to upgrade to IoT-enabled machinery and systems. The complexity of new technologies also presents a steep learning curve for engineers and technicians accustomed to traditional systems.
Another significant challenge is workforce training. The shift to smart manufacturing requires not just the understanding of physical systems but also skills in data analysis and interpretation and the ability to manage digital tools and connected work platforms. This calls for considerable upskilling and continuous learning, which can be time-consuming and resource-intensive.
However, these challenges should not deter the industry's progress towards smart manufacturing. Solutions are emerging that can help mitigate these issues. For instance, the cost and technical complexities can be managed through a phased approach. When smart technologies are integrated gradually, the costs can be spread over time, reducing the impact of initial implementation.
For workforce training, partnerships with educational institutions can be forged to provide the necessary training and skill development. Alternatively, online platforms offer many courses tailored for smart manufacturing. Real-world case studies, such as those from the automotive and aerospace industries, provide evidence of successful smart manufacturing implementation and can serve as valuable guides.
As the fluid power industry moves confidently into the era of smart manufacturing, it's crucial to consider the potential future trends in maintenance and the implications of these trends on the industry. Predictive maintenance has already sparked a significant transformation, but further evolution is inevitable with ongoing technological advancements.
Machine learning algorithms, for example, are continually improving and becoming more adept at interpreting vast amounts of data from IoT devices. They will likely become more proficient at predicting failures, minimizing downtime, and maintenance costs. This may lead to the emergence of prescriptive maintenance, where systems don't just predict failures but also suggest the best corrective action, providing an even more proactive maintenance approach.
Similarly, the integration of AR in maintenance practices could enhance the accuracy and speed of repair operations. With AR, technicians could have real-time access to detailed technical information, visual guides, and even remote expert assistance, all while working on the machinery.
On the data front, we could see an increased use of edge computing, where data processing occurs close to the source of data generation. This approach can reduce latency and improve real-time decision making, further enhancing the efficiency of predictive maintenance systems.
These prospective advancements, while exciting, will carry their own challenges and implications. For instance, the further we delve into AI and machine learning, the more critical data security and privacy will become. Furthermore, as systems become more complex, so too will the necessary skills and expertise required of our engineers and technicians.
Yet, if the fluid power industry navigates these developments with the same tenacity and forward-thinking approach as it has thus far, there's no doubt it will continue to realize the immense potential of smart manufacturing. This will not only reinforce the industry's resilience and adaptability but also its crucial role in the broader manufacturing landscape.
The integration of smart manufacturing in the fluid power industry has transformed maintenance practices. This shift from reactive to proactive predictive maintenance is significant, addressing efficiency, performance, and safety while reducing costs and ensuring compliance. This transformation is crucial for remaining competitive in a rapidly advancing technological era. Engineers and technicians play a vital role as their roles evolve in response to these changes.
Embracing the challenges of smart manufacturing has allowed the industry to grow and advance. Future trends will continue to drive evolution in maintenance practices, underscoring the importance of learning and adaptation for industry professionals. Smart manufacturing is a testament to the industry's innovation and adaptability. •
www.deltamotion.com
Delta Motion is a leading manufacturer of industrial automation products, specializing in high-performance hydraulic motion control. Our RMC Motion Controllers are capable of controlling systems with up to 50 axes, providing precise closedloop position and pressure/force control. With a strong reputation built over 40 years, Delta is recognized for delivering best-in-class products and providing responsive, knowledgeable support.
www.diamondhydraulics.com
Diamond Hydraulics is a veteran owned small business that manufactures, rebuilds, and repairs hydraulic equipment including cylinders, pumps, motors, valves, power units, and much more. We were established in 1999, and have over five decades of experience in hydraulic equipment repair.
Diamond Hydraulics provides quality workmanship, extensive industry knowledge, and fast turnaround time on repairs and replacements. All repairs are brought back up to OEM standards and tested with state-of-the-art test equipment.
The FlangeLock™ Tool is the ultimate contamination control tool for protecting your hydraulic systems. It allows for the simple sealing of open SAE code 61, 62 & CAT-Style hydraulic flanges without tools. Constructed from lightweight aluminum. Easy on, easy off. Offers a leakproof solution to hydraulic system and environmental cleanliness. FlangeLock™ Tools stop the mess!
Discover
Have a Purchase Order? Please email to sales@flangelock.com or fax to 203-622-1238
www.inserta.com
www.adaconn.com
Adaconn® + Inserta® offer a variety of components including flange adapters and connectors, ball valves, check valves, pressure controls, and modular fittings that can be used to make smartly designed compact hydraulic systems. A large inventory of finished components allows most standard items to ship from stock. Custom components and assemblies are available. Visit our website to learn more about our expanding product offerings.
www.orbitalmotors.net
Hydraulex — Genuine Metaris® Orbital Motors are your best low speed high torque motor option in an economical and compact design. The motors are engineered with Roller-Star technology, come in a range of displacements and we offer multiple flange options including wheel mount. You’ll find that our motors are a perfect fit, form and function replacement for common OEM motors in the market today, such as Eaton®/ Char-Lynn®, Danfoss®, Parker® and White®.
Visit
www.hiigroup.com
Hydraulics International, Inc.
No Compromise on Quality or Performance.
Established in 1976 and headquartered in Chatsworth, California, Hydraulics International, Inc. (HII) is a leading provider of pneumatically driven hydraulic pumps, portable and skid mounted high pressure hydrostatic test units and accumulator charging units on a global basis. Since inception, HII has maintained an intense focus on design and engineering, striving to stay at the forefront of fluid power technological advances.
Proudly made in the USA.
When reliability counts, depend on the strength of a leader…HII, the leading name in high pressure pumps and gas boosters.
www.mainmanufacturing.com
Main's website provides quick access to the 120 page catalog that includes popular styles of MAIN Manufacturing’s extensive offering of carbon and stainless Hydraulic Flanges and Components – ready for immediate shipment. Metric ordering information, weld specs, and dimensional information included. The “Quick Reference Guide” helps specify less popular items often stocked or quickly manufactured (generally 3-4 days) at our US plant. “Create-A-Flange” offers more parts than the catalog — by picture. If it’s not here, or for questions, E-mails may be sent to get your answer quickly.
1-800-521-7918
info@mainmfg.com
www.maxmachinery.com
/low-flow-experts
Measure low flows below 1-100 cc/min with 0.2% accuracy and response rates as low as 1.6 milliseconds. Because you value your flow, find value in the data from a Max Flow Meter. High resolution, high accuracy, bi-directional, and quadrature signal output options make Max Meters the choice in measuring low flows. Reach out to us today for pricing and availability.
Precision Flow Meters
Max Machinery, Inc.
33A Healdsburg Ave. Healdsburg, CA 95448 707-433-2662 | www.maxmachinery.com
Here is the solution to Figure It Out on page 5
» WHEN WE ENCOUNTER this type of problem, we install a tank line check valve with a 5 to 10 PSI spring to solve this problem. Proportional valves with feedback are very sensitive to air bubbles that could collect in the coils. The height of the valve above the reservoir to the pumps was over 7 feet allowing the weight of the oil pulling down to cause about a 5” hg vacuum and allowing air to enter the system. Air can enter a system where oil will not leak out if there is a vacuum present.
The correct answers to Test Your Skills on page 25 are 1-a and 2-e.
Precision cut-to-length tubing. Eagle’s manufacturing facilities enable the cutting and deburring up to 2” diameter and any quantity of fractional, metric, pipe and hypodermic tubing. Burr-free production – No work hardening – No ReCast – Faster than EDM. High quality designs need high quality components. Eagle has ISO 9001 and ISO 13485 quality management certifications in place.
10 Discovery Way | Franklin, MA 02038-2555
(800) 528-8650 | www.eagletube.com
Keep your oil clean and dry with Xtract Filter Carts from Lubrication Engineers. These portable filtration systems make it easy to pull oil samples, clean the oil, and maintain oil cleanliness in multiple applications using the same fluid. They enable you to both screen oil to remove large particulates and clean oil to remove small particulates.
www.lelubricants.com
info@le-inc.com
800-537-7683
The compact, rugged and resilient design of the new Webtec CTA series flow monitor makes it ideal for permanent installation on both on- and off-highway vehicles, where it can monitor, record and transmit data, in real-time, about oil flow rates and temperature via a J1939 CAN-bus interface. This innovative device is perfect for use in predictive maintenance/IoT systems.
Beach Filters has been manufacturing desiccant air filters for over 70 years now. With no fundamental changes to our T-Line series, we have added an FDA compliant Buna gasket and a special assembly process. Compressed air and gasses are still processed through our 3 stage filtration and .3 micron filters to remove water and hydrocarbon vapor.
BEACH FILtER PRODuCts, INC.
555 Centennial Ave • PO Box 505 • Hanover, PA 17331
Phone: (717) 698-1403 • FAX (717) 698-1610
1-800-BEACH-85 • www.beachfilters.com
PUMPS
1.800.422.4279 sales@hydraulex.com www.hydraulex.com
THE “SPECIAL” YOU WANT IS PROBABLY ON OUR
Adaconn + Inserta | p 28 1-215-643-0192 | inserta.com
Almo Manifold | p 31 989-984-0800 | almomanifold.com
Beach Filter Products | p 30 717-698-1403 | beachfilters.com
CFC-Solar | p IBC
1-513-874-3225 | cfcindustrialtraining.com
Clippard Instrument Lab, Inc | p 31 877-245-6247 | clippard.com
Wojanis Supply Company, in business for 40+ years, is seeking a full time Hydraulic System Design Engineer/Manager in the Pittsburgh, Pennsylvania area.
This position requires daily interaction with internal and external customers. Hydraulic System Design Engineers recommend components, troubleshoot systems, design and oversee the integration of intricate fluid power systems across all markets. Extensive knowledge and hands on experience with fluid power products, systems, and processes that make these systems work is paramount. Essential functions include troubleshooting, designing, analyzing and preparing customer proposals; directing system designers and drafting staff.
Requires: Bachelor’s Degree in Engineering, 10+ years of hydraulic experience including field experience, Inventor 2023 or comparable 3D modeling software experience.
Preferred: Certified Hydraulic Engineer (CHE) or other relevant professional engineering licenses and PLC experience
Our valued employees can expect engaging work, competitive pay and benefits package, and a supportive environment.
Qualified candidates may send a resume and cover letter to ChrisS@wojanis.com to apply.
We are hiring for the following positions: Application engineer | Inside sales support person Contact Carlo A. Pecorari for more information. Young Powertech Inc. 3060 Plaza Dr. Garnet Valley PA 19060 Ph. 610-558-0760 carlo@youngpowertech.com
Continental/Hydreco | p 27
continentalhydraulics.com
Delta Motion | p 20, 28
1-360-254-8688 | deltamotion.com
Diamond Hydraulics | p 3, 28 409-986-3957 | diamondhydraulics.com
Eagle Stainless | p 30
1-800-528-8650 | eagletube.com
Flange Lock | p 3, 28 203-861-9400 | flangelock.com
FluiDyne Fluid Power | p 31 586-296-7200 | fluidynefp.com
Harvard Corporation | p 21 608-882-6330 | harvardcorp.com/filters
Hydraulex | p IFC, 28, 31
1-800-422-4279 | hydraulex.com
Hydraulics International | p 29, IBC 818-407-3400 | hiigroup.com
Lubrication Engineers | p 19, 30
1-800-537-7683 | lelubricants.com
Lubriplate, Inc | p1
1-800-733-4755 | lubriplate.com
Main Mfg Products | p 29, 31
1-800-521-7918 | mainmfg.com
Max Machinery Inc | p 25, 29 707-433-2662 | maxmachinery.com
VEST Inc | p 11 netskeme.com
Webtec LLC | p 30, IBC
1-800-932-8378 | webtec.com
Wojanis Hydraulic Supply Co | p 31 724-695-1415 | wojanis.com
Young Powertech, Inc | p 31 610-558-0760 | youngpowertech.com
FILL O ut t HI s CARD COMPLE t ELY, DE tACH, AND MAIL I t tO stAR t YO u R su B s CRIP t ION
MAIL tO: PO BOX 293142 • KETTERING OH 45429
YOU CAN ALSO SUBSCRIBE ONLINE AT WWW.FL u IDPOWERJO u RNAL.COM.
YES! Please start/continue my complimentary subscription to the Fluid Power Journal 02 NO. Not interested.
Check here if you would like to keep your name, address, phone and fax numbers confidential, and not released to third parties The address above is my:
Address Which edition would you like to receive? Print
Digital Both (View a sample of our PAPERLESS digital edition at www.fluidpowerjournal.com)
1. Do you specify, select or influence the purchase of components & systems, on new or existing machinery?
If yes, which technologies? (check all that apply)
2. What is your primary job title? (check only one)
Secretary, Treasury, General Manager, Owner, Business Manager, Director, etc.
MY COMPANY SHOULD BE ADVERTISING IN OR SUBMIT AN ARTICLE TO THE FLUID POWER JOURNAL.
PLEASE CONTACT THIS PERSON:
NAME:
TITLE: PHONE:
• Resolution ≤5 mV
• Accuracy ±0.25% of full scale
• Real-time adjustable PID control
• Integrated 0 to 10 VDC, 4-20 mA signal, or 3.3 VDC serial communication
• 0 to 10 VDC feedback pressure monitor
• Virtually silent
• No integral bleed required
• Multiple pressure ranges from vacuum to 150 psig
• 2.7 to 65 l/min flow control
The future of proportional control has arrived— and it’s digital. The Clippard Cordis is a revolutionary microcontroller primed for escape velocity from a proportional control market that has grown stagnant.
With unparalleled performance and flexibility not possible with current analog proportional controllers, the Cordis makes everything from calibration, to sensor variety, to future development opportunities more accessible and less complicated.
Contact your distributor today to learn more about how the Cordis can provide precise, real-time control for your application, or visit clippard.com to request more information.
877-245-6247
Precise, Linear Digital Pressure Control