
4 minute read
Premium quality NSK
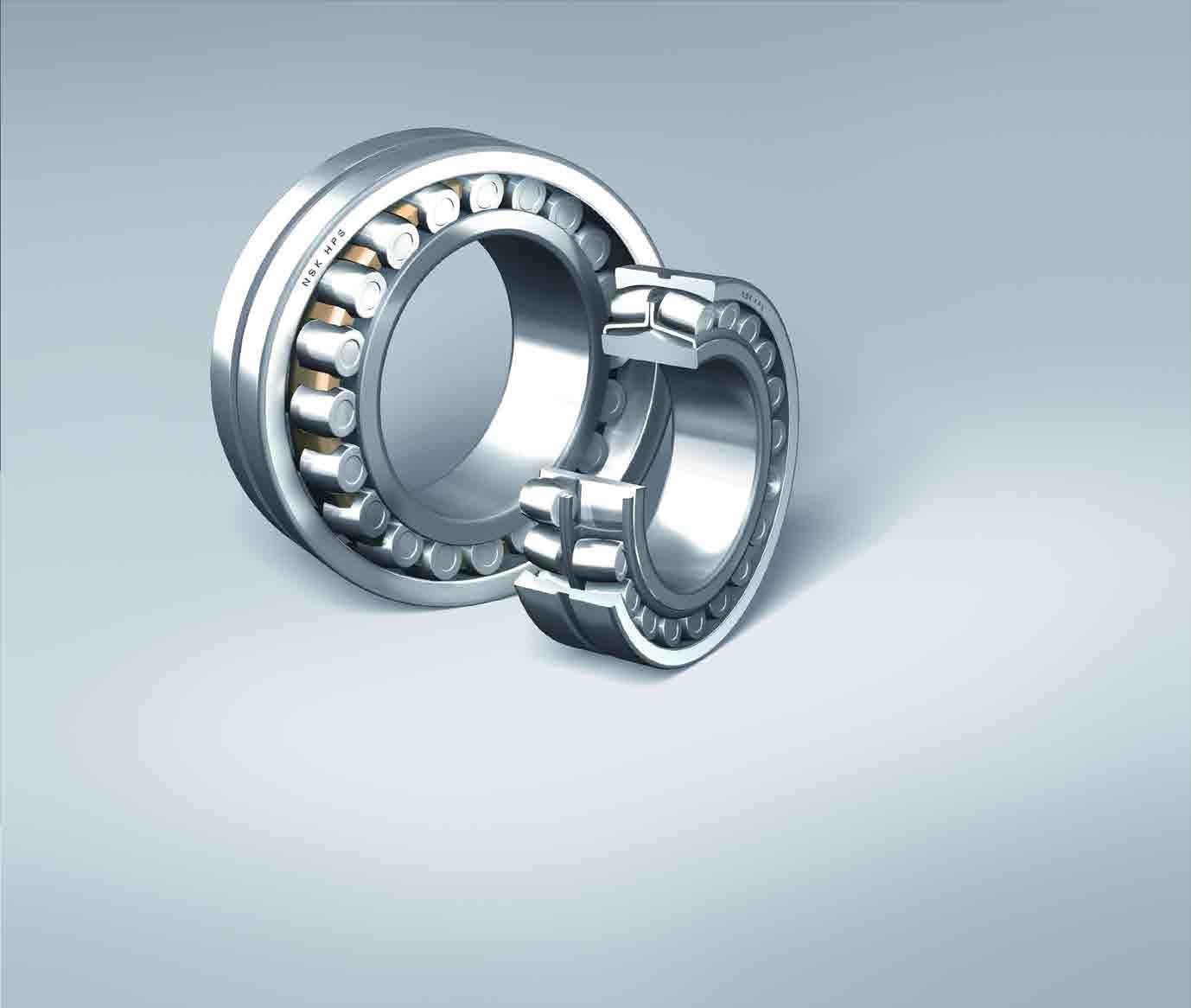
PREMIUM QUALITY
The Japanese company NSK is one of the world’s leading manufacturers of ball bearings, roller bearings and wheel hub bearings for cars. NSK has over 3000 employees in Europe and NSK Europe’s headquarters are located in the German town of Ratingen. Joseph Altham interviewed Volker Polonyi, managing director for sales for NSK’s European Industrial Business Unit, to find out more.
NSK Ltd is a blue-chip Japanese company that produces bearings for all kinds of industries and has built up a high reputation for quality and reliability. Altogether, NSK has sales offices in 26 different countries and 62 production sites around the world. With factories in Britain, Germany, Italy and Poland and a turnover of over €869 million, NSK Europe is an important part of the company’s global business.
NSK Europe’s bearings and steering systems are used in the cars produced by major motor manufacturers such as Toyota and Volkswagen. NSK Europe also produces bearings for agricultural and mining equipment as well as for machines and conveyor belts on the factory floor. Indeed, NSK Europe has customers in many different sectors of industry, from cement to food processing and packaging. “Basically we make bearings for anything that rotates,” said Mr Polonyi. “We are in the premium segment and high quality is our core philosophy.”
Working quietly
NSK Europe’s largest factory is in Poland. The company took over the factory in Kielce after the collapse of communism and transformed it into a modern site capable of producing ball bearings to Japanese standards. “The factory in Kielce uses the same kind of machines as any other NSK factory and produces bearings for customers everywhere in Europe.”
Although demand from eastern Europe is growing, Mr Polonyi said that Germany is still NSK Europe’s single largest market, accounting for over 40 per cent of total sales. NSK Europe’s bearings are widely used by manufacturers of white goods, including the prestigious German brands, BSH and Miele. High quality bearings in the motor of a washing machine result in a quieter appliance. “With washing machines it is necessary to distinguish between the motor bearings and the drum bearings. The noise comes from the vibration

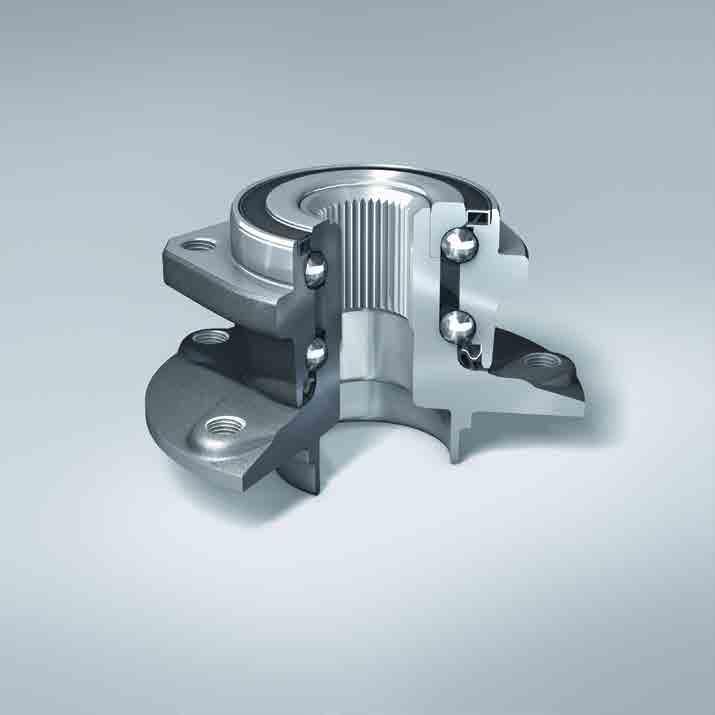
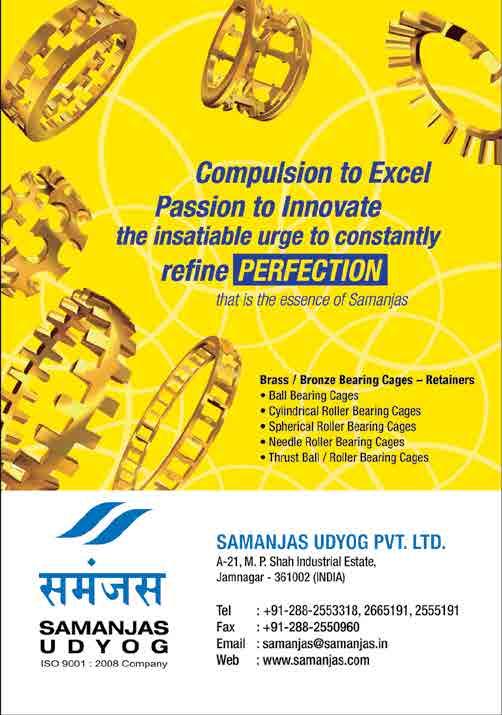
of the motor. High quality bearings allow the motor to run more quietly and smoothly. Drum bearings are designed for strength. We make drum bearings from special steel as they have to be strong enough to support five kilograms of washing up to 1600 rpm spinning speed.”
NSK Europe’s bearings also improve the performance of machines in heavy industry. One example is the papermaking industry, for which the company produces special rolling bearings that are designed to mitigate the effects of wear and tear on the calendar roll. “As the long cylinders in a paper machine heat up, they get wider, and this creates misalignments. We offer special bearings that can compensate for the misalignment.”
Total cost of ownership
NSK Europe positions itself at the higher end of the market. The company has developed various solutions to fit the requirements of different industries, working in cooperation with the manufacturers of industrial machinery. Its customers understand that quality is worth the price. The key concept, says Volker Polonyi, is total cost of ownership. “The big issue is minimising friction. The less the friction, the lower the costs for the end user.” What this means for the consumer is a washing machine that is not only quieter but also consumes less electricity and will probably last longer too.
In heavy industry, bearings that keep the machinery running smoothly help businesses avoid unscheduled stoppages for maintenance and unnecessary downtime. “Papermaking machines are big – 100 metres long – and the cost of a stoppage lasting only one hour is very high.”
Wind power
In the wind energy industry, the need for reliable bearings is even more acute. A wind turbine needs bearings for its pitch and yaw gears and in its main gearbox. Although a wind turbine may look simple, the technology is highly advanced and has to withstand many challenges. On an offshore wind farm, the environment is especially tough, and repairing equipment in the middle of the North Sea is tricky and expensive.
“We supply bearings to the main manufacturers of the gearboxes for the turbines. A turbine’s rotor and generator will need big bearings, but with the gearboxes the requirements are particularly high. The technical challenges have grown as the turbines have increased in size. In 2000, turbines produced a maximum of 1.5MW of electricity, but today there are offshore turbines producing as much as 5MW. If something fails, you have a big problem, so our philosophy is to use the best possible material for the bearings, which is toughened steel. It is a complex system and our engineering team works closely on projects with the wind turbine makers.
“The biggest part of the job is in the application engineering, where we use sophisticated computer modelling. We expect sales of bearings for wind turbines to grow in the future. Germany is planning to give up nuclear energy so here wind power will come to play a more significant role.” n