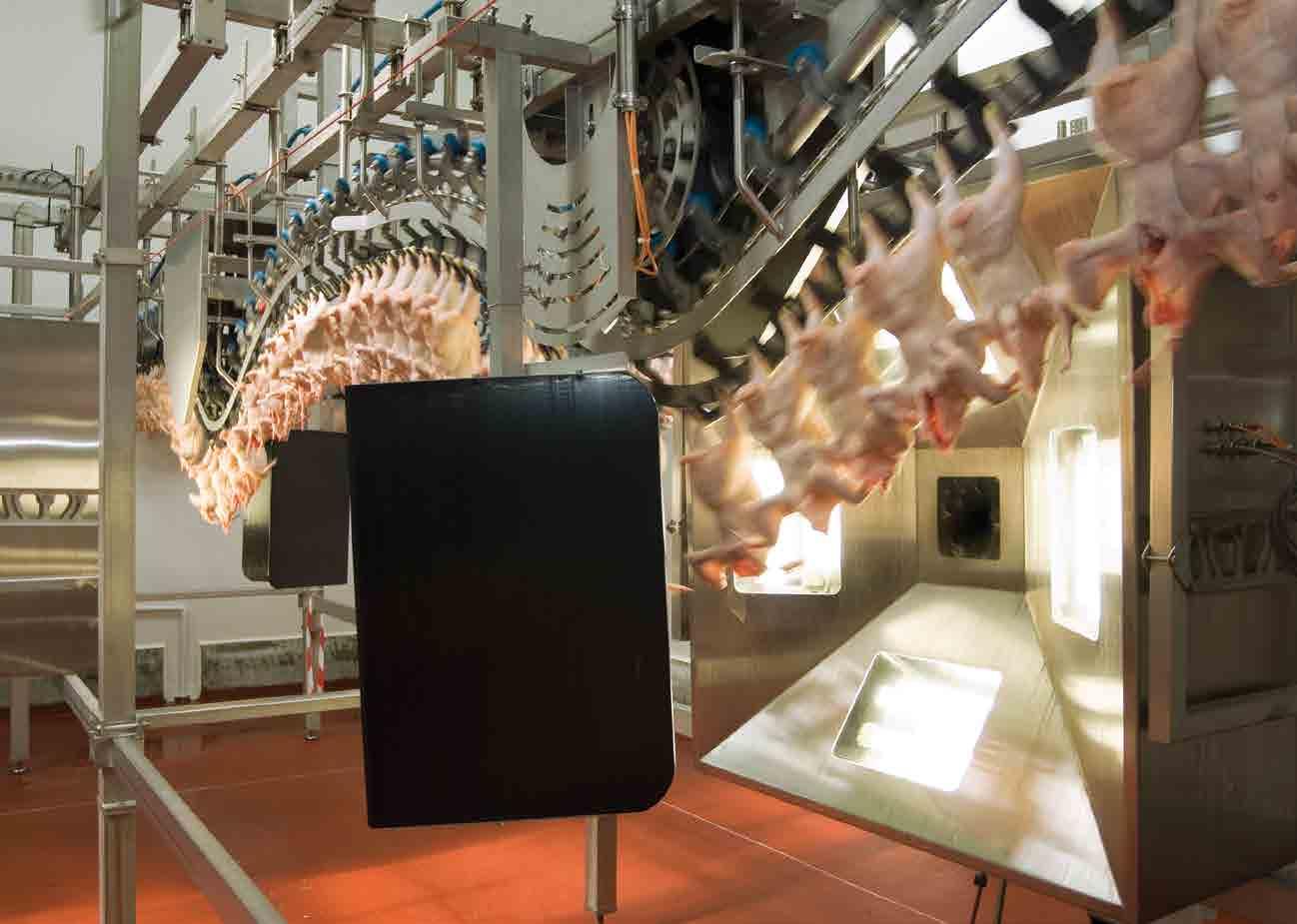
4 minute read
Advanced poultry processing
ADVANCED POULTRY
The Danish company Linco Food Systems, part of the Baader Group, is one of the world’s leading manufacturers of poultry processing equipment. Joseph Altham reports on a company that sells innovative and reliable poultry processing solutions to countries all over the world.
PROCESSING
Linco Food Systems has more than 60 years of experience in poultry processing machinery. The company is based near Aarhus, in Denmark, and was founded in 1944. In 2007, Linco was taken over by the German firm, Baader. Headquartered in Lübeck, the Baader Group is a world-class manufacturer of fish processing machinery which moved into poultry processing back in 1985. Twelve years later, Baader acquired Johnson Food Equipment, an American firm specialising in poultry processing machinery. The takeover of Linco has thus enabled Baader to combine its position as a key player in poultry processing in North America with Linco’s strong presence on the European scene. As a result of the acquisition of Linco, Baader now ranks at number three in the global poultry processing market.
At Baader Linco, the focus is on the provision of complete solutions. Baader Linco encourages its customers to take a systematic attitude to poultry processing in order to achieve an optimum level of efficiency. The company supplies a range of equipment covering every stage of poultry processing, from collecting the live birds at the farm for slaughter to machines for packing the cuts. Baader Linco aims to ensure that high standards of quality are maintained throughout the entire procedure and the company is capable of designing entire processing plants.
Maxiload
Consumers are becoming increasingly concerned about the welfare of chickens prior to slaughter. As Baader Linco points out, minimising the distress of the chicken in its final hours results in a better end product. If the bird is damaged in any way, either when it is caught and transported or when it is prepared for slaughter, this has a negative impact on the meat quality, causing flaws such as blood spots or bruised wings. A system for transporting and killing the chickens quickly and cleanly also benefits the working lives of the people on the farm and at the plant. Baader Linco’s Maxiload crates make it easier for farm workers to catch live birds and load them onto a truck. The Maxiload crates are large and thus simple to load. They are supplied in a modular system for stacking on stainless steel frames. Using the Maxiload system, farm workers are less likely to push or pull crates of live birds in a rough fashion or dump them onto the floor. The Maxiload system allows the modules to be lifted onto
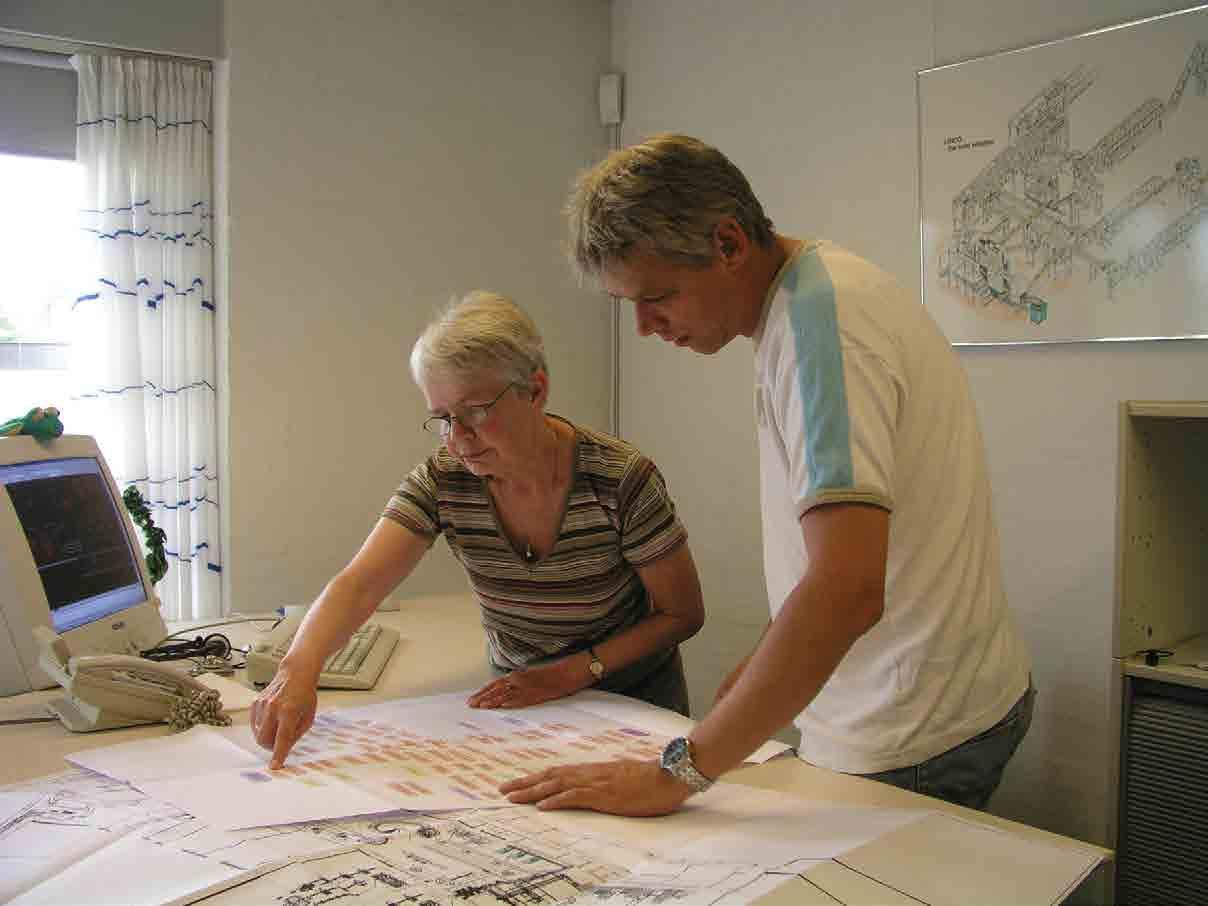
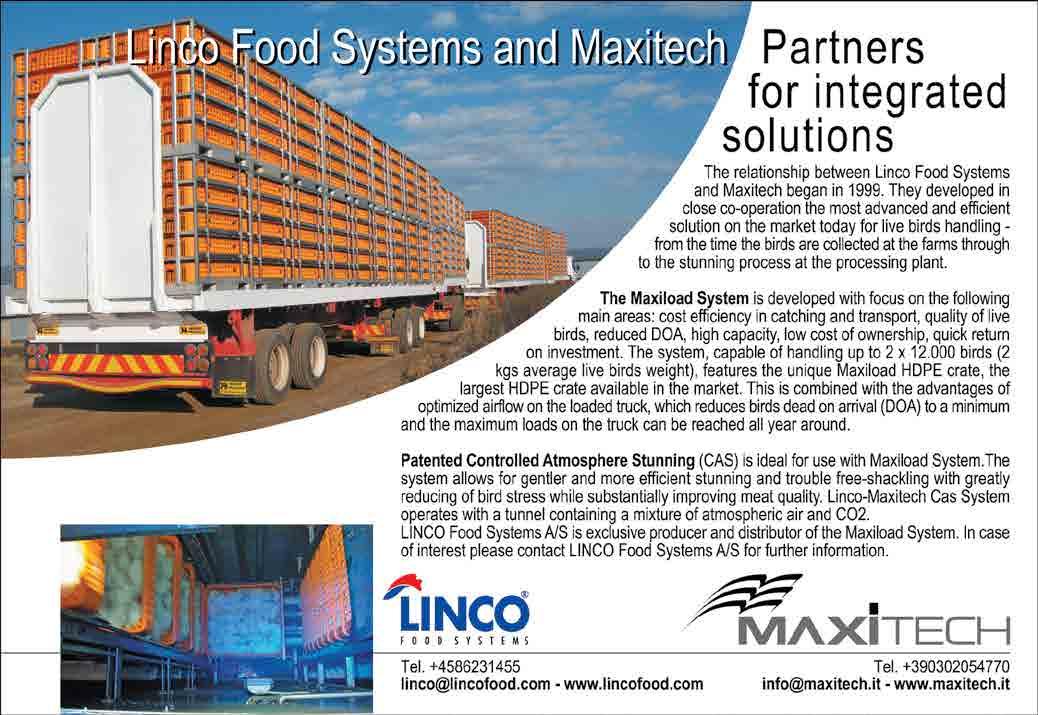
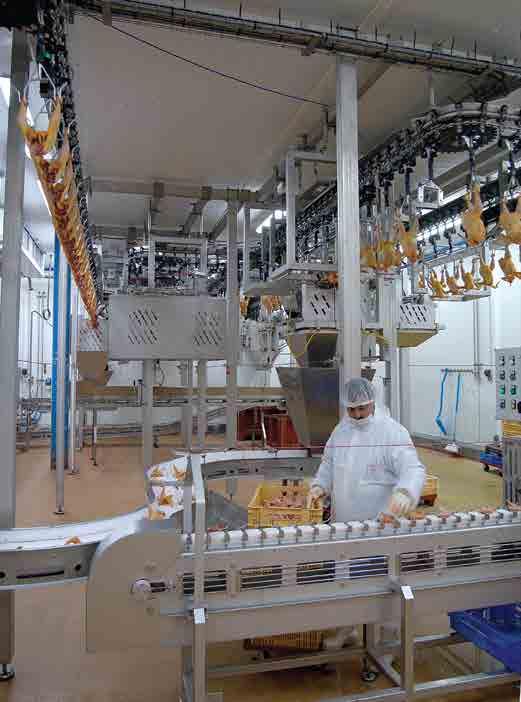
a lorry by forklift truck and the crates provide the chickens with excellent ventilation during transit. Overall, the Maxiload system reduces the number of birds that are dead on arrival at the slaughterhouse and this is an important financial consideration.
First processing
Killing a bird and preparing it for the table is a complex process and Baader Linco provides a complete range of machines to handle the various stages. After the chickens are slaughtered, the lungs and the liver of the bird have to be removed, and Baader Linco has recently brought out a new eviscerating machine to perform this task. The company’s patented high speed eviscerator, model 218, has a special spoon to fit the shape of the bird cavity. The spoon scoops out the giblets in a single action, preserving the quality of the liver while leaving the bird’s rib cage intact.
Out of all the various stages, the most crucial is the “first processing” stage, running from when the live birds arrive at the slaughterhouse to when the freshly killed birds are defeathered. Once the birds arrive at the slaughterhouse, they are taken out of the crates and hung from shackles before being immersed in a bath of water and stunned by electrocution. Finally the chickens are killed with a blade. Baader Linco offers two types of killing machine. While the conventional model has two blades, the Halal version has only one blade and delivers a clean centre cut to the front of the bird’s neck. During the sub-processes before killing, it is vital to make sure that the birds do not suffer cruel or distressing treatment because this could have an adverse effect on the quality of the meat. Baader Linco’s “humane killing system” is intended to make the first processing stage as smooth and straightforward as possible. To this end, Baader Linco recently brought out a new high frequency water stunner, the HFS 2012, developed in cooperation with the University of Bristol.
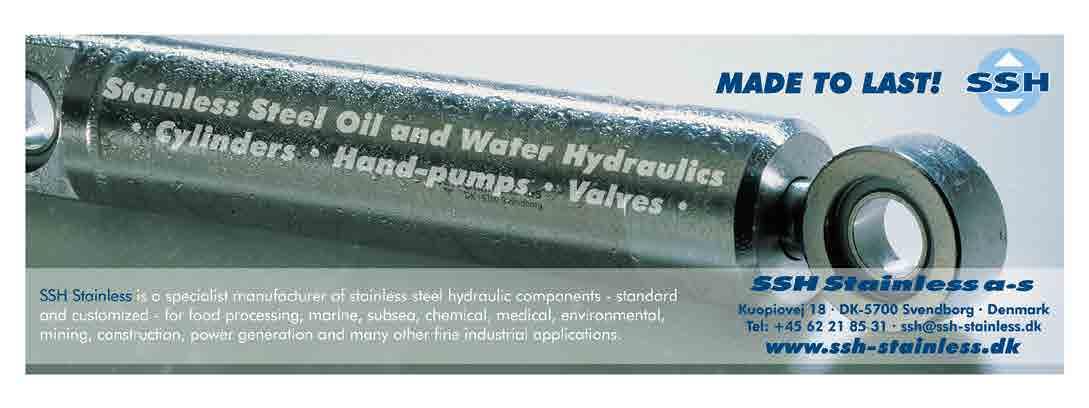
The stunner satisfies the requirements of new European Union regulations on animal welfare.
Emerging markets
Growing prosperity in the BRIC economies is stimulating the demand for white meat and Baader Linco is well placed to benefit from this trend. One example is in Brazil, where Linco’s presence dates back to the early 1990s. In 1994, the Holambra Agricultural Cooperative installed an automatic cutup machine and an evisceration line from Linco at its plant near São Paulo. This year, Holambra plans to increase its slaughtering and processing capacity to 12,000 birds per hour and Baader Linco will once again be supplying the necessary equipment. n
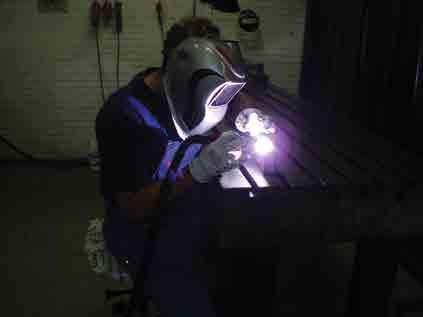
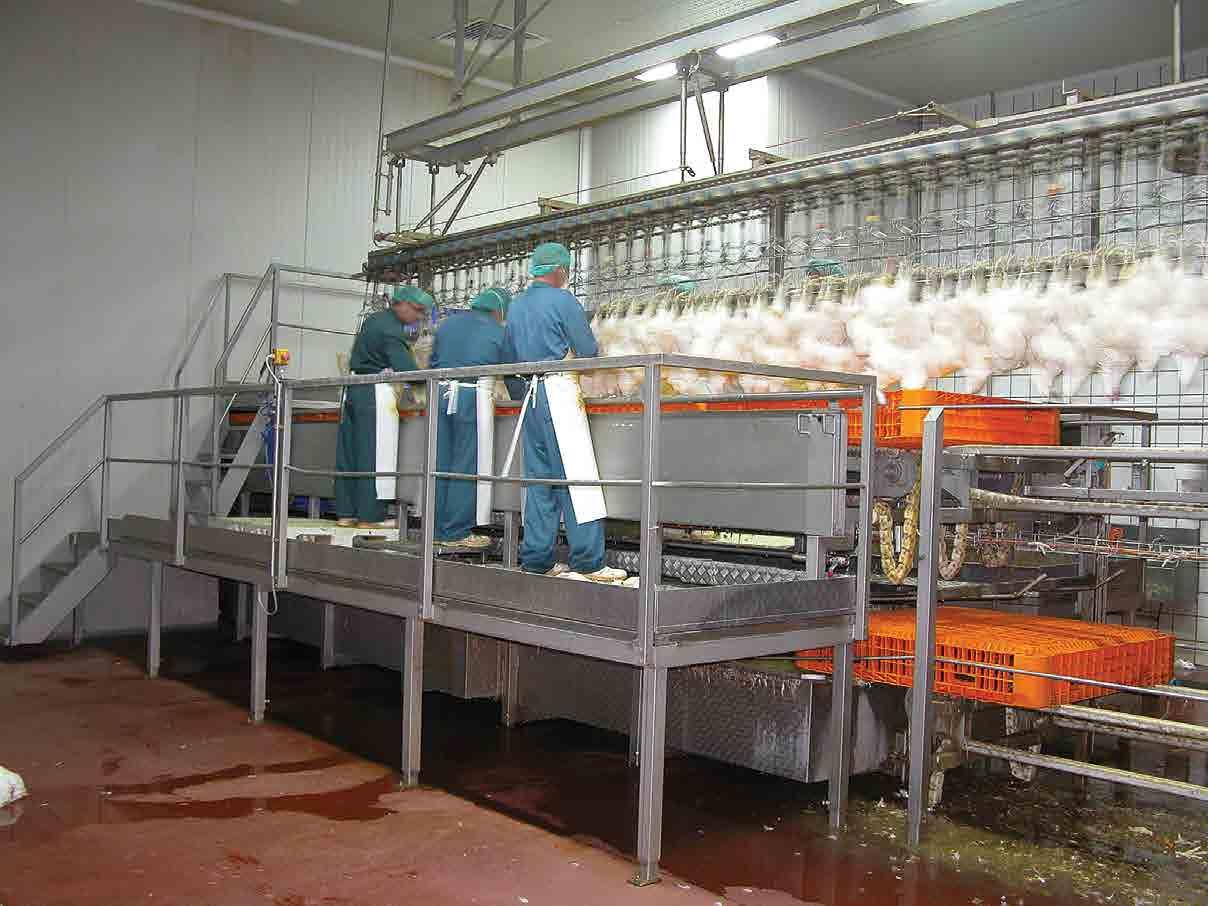