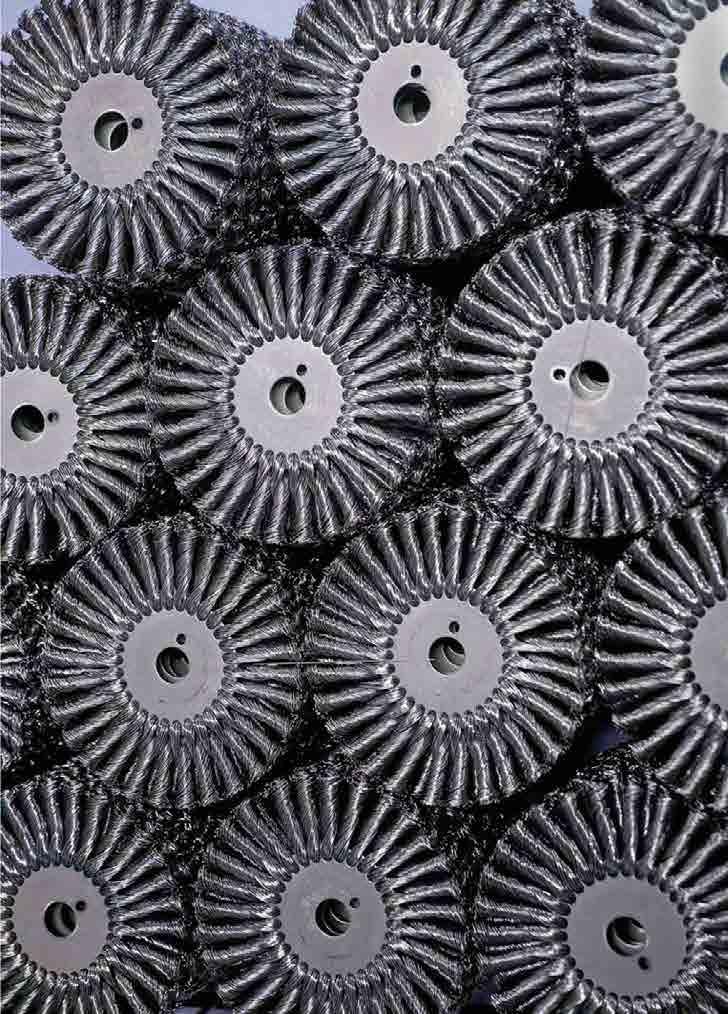
5 minute read
A polished operation Osborn

A POLISHED OPERATION
Osborn is the world’s largest and most complete solution provider of high-quality surface treatment and finishing tools and brushes. Abigail Saltmarsh looks at the company.
AT Osborn International there has always been a clear strategy. This, according to the managing director, Albrecht Teich, and vice-president of marketing, Luis Hereza, has seen it hold its position as the world’s largest and most complete solution provider of high-quality surface treatment and finishing tools and brushes.
“The key for us has always been a strategy of focus,” explains Mr Teich. “If you want to be everything to everyone, you end up being nothing. Focus is what we have done in the past and is how we plan to move forward.
“We have selected key areas and key industries that we believe, because of our positioning and our technology, we should be focusing on in order to continue to achieve organic growth. Our aim is to do this as we also put effort and energy into coming up with the right solutions for our customers.”

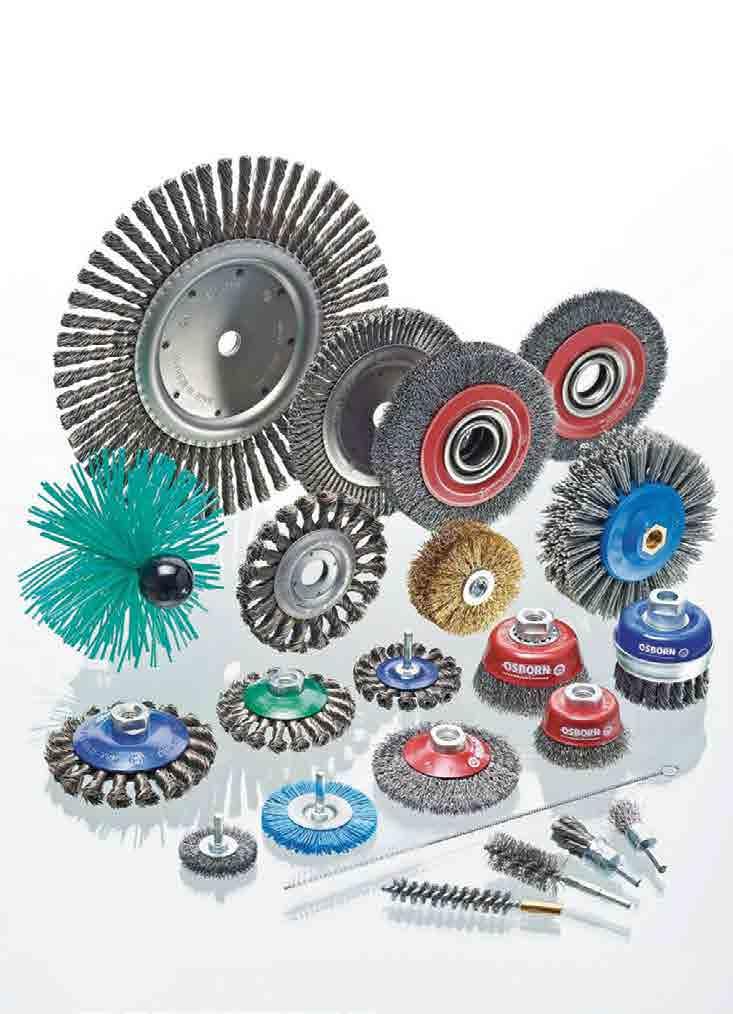

Rewarding relationships
Osborn has a long history. It was founded back in 1897 and today, owned by Jason, Inc., it holds more patents on more products and processes than all other competitors combined. For its 125-year history, it has remained dedicated to building rewarding customer relationships in the provision of high-quality surface treatment and finishing tools for hundreds of commercial and consumer applications such as metal finishing, honing and surface polishing.
Through brands such as JacksonLea, Lippert-Unipol, Sinjet, Load Runners and Dialux, Osborn serves customers directly in such diverse industries as aerospace, automotive, primary metal finishing, industrial pipeline, woodworking, finishing and polishing and road sweeping, offering more than 10,000 standard products and 100,000 custom-tailored solutions.
A global operation
With more than 2000 employees and 18 operations facilities serving customers in more than 120 countries, Osborn’s global reach offers greater access to new product ideas, economies of scale, and new techniques for unique surface treatment and finishing needs. It has the advantage of worldwide engineering and manufacturing support to modify any product or machine in its offering.
“The company has changed quite a bit in its more recent history from being primarily a US company to being a global operation with locations across the world,” says Mr Hereza. “We have also significantly increased our product lines within our portfolio.”
New products
He explains that brushes, machines and load runners are now being created for a wide variety of industrial markets and uses, ranging from rust removal and burring of NF-metals, steel, structural steel or aluminium to the manual or automated cleaning of welding seams and cleaning, dust removal and surface processing of
Abrasive filaments from Hahl Pedex The right choice for when the going gets tough
Hahl Filaments GmbH Rottenacker Straße 2-18, 89597 Munderkingen, Germany Phone: +49 (0) 7393 53-0 | Fax: +49 (0) 7393 53-220 | E-mail:hahl.de@hahl-pedex.com | www.hahl-pedex.com
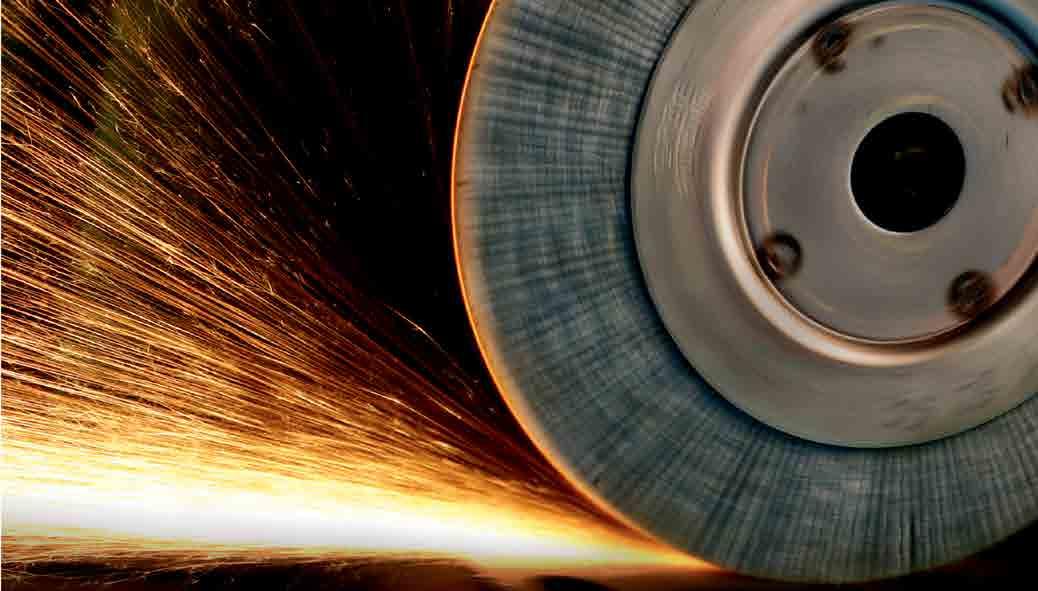

almost all materials. Industries particularly being targeted at the moment include food and beverage, primary metals, transportation and roads, as well as automotive.
Innovation takes the form of adaptation and modifications to existing products as well as the launch of ground-breaking concepts. In primary metals, for example, there are innovations like the Osborn HDL brush rolls – high density and long-life, he says. This is a brush-based innovation for strip processing lines, with improved high-quality abrasive filaments for carbon and iron-fine removal, non-abrasive multi-filaments for micro-cleaning and improved degreasing. Its high-fill density ensures excellent brush performance and improved strip cleanliness while long life-times reduce maintenance and production costs.
“Then we have other products such as one for the treatment of railway lines in cold weather and another that goes into coal-fired power plants for insulation purposes. This increases efficiency,” says Mr Hereza.
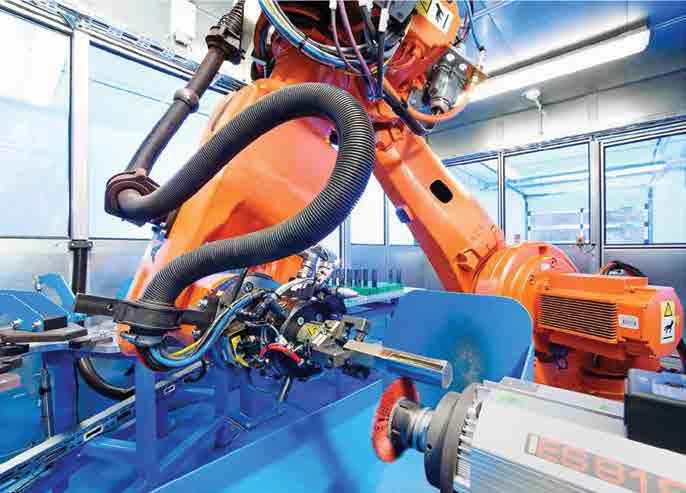
Excellence at all times
In both Burgwald, in Germany, and Richmond, USA, Osborn uses an industrial robot, within a state-of-the-art laboratory. These robot cells have been developed for performing product tests on an ongoing basis.
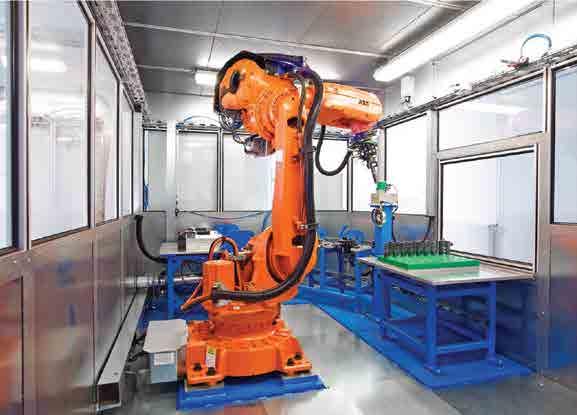
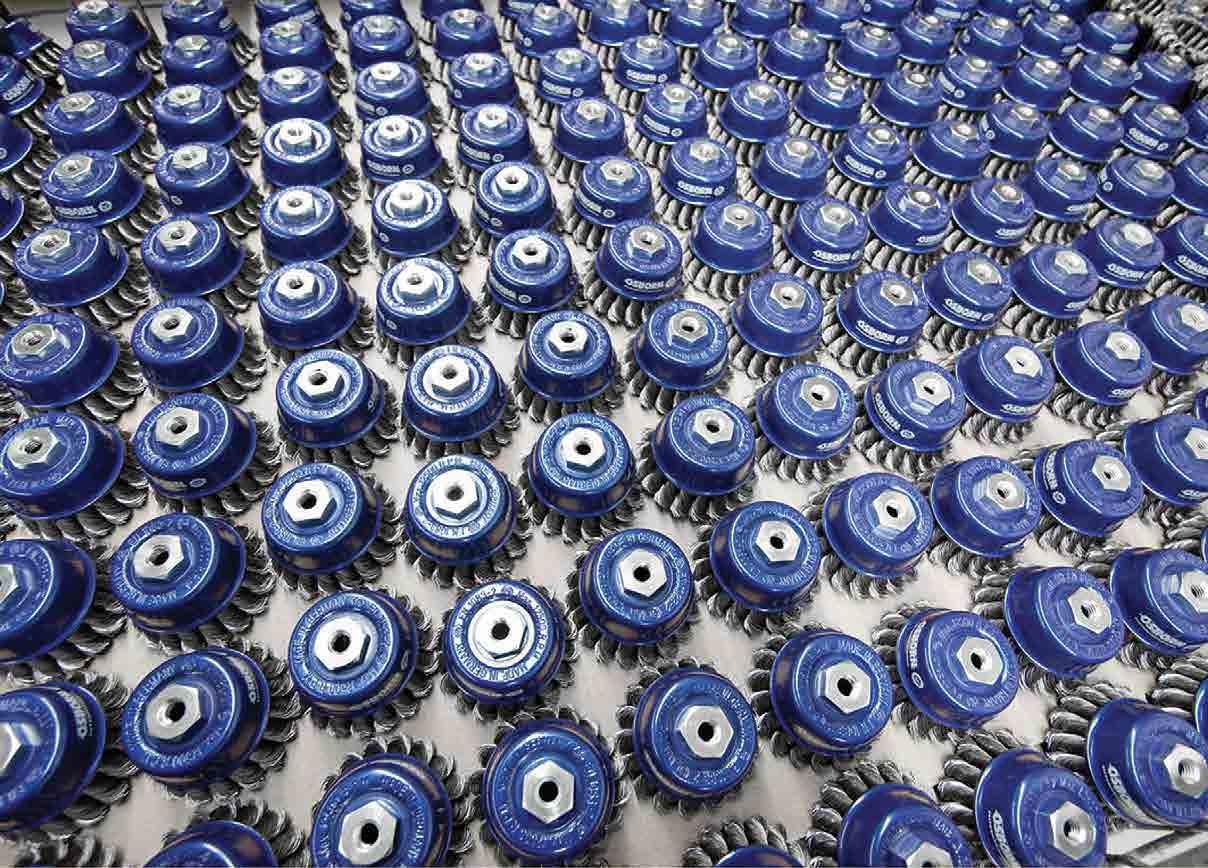

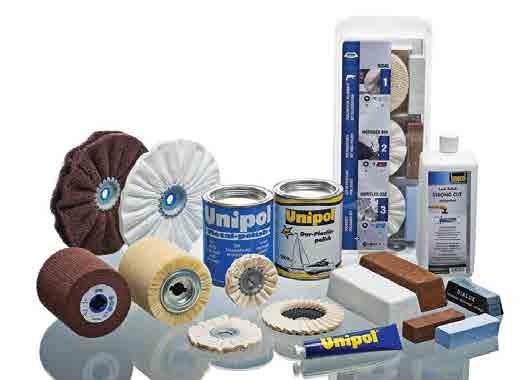
“We are now in the position to perform precise testing procedures, and to reproduce and verify the results any time. This way we can reliably monitor our excellent quality of production and assembly, and continually advance product development,” says Mr Teich. “With this step in innovation, we can reproduce very complex processes of our customers and optimise the tools and processing parameters with the help of realistic simulations.
“As we simulate the processes of our customers, we aim to find solutions for them. Overall, this is the direction in which we wish to move – to become more of a solutions provider.” Finding solutions
Mr Hereza explains that there are several lines of ongoing investment at Osborn, in addition to the robot cells and laboratory facilities. Plants are constantly being upgraded and capacity improved.
The drive for continuous improvement has also seen a new campaign to promote the Osborn name much more robustly. This is seeing Osborn positioned more clearly as the over arching brand name for all its products.
“We have streamlined our many different brands and created stronger brands that are more visible,” he says. “We have heightened awareness of Osborn, choosing the brands that are most relevant now and strengthening their attributes.”
The focus on the traditional markets of central Europe and North America continues, with an eye on the emerging markets too. Energy efficiency will be a key consideration in the future as well as Osborn’s strategy for clear focus.
“We have intimate relationships with our customers within the key areas we have selected and this will help us to continue to achieve growth,” adds Mr Teich. “This will continue as we work with them to help them achieve better performance for their systems.” n