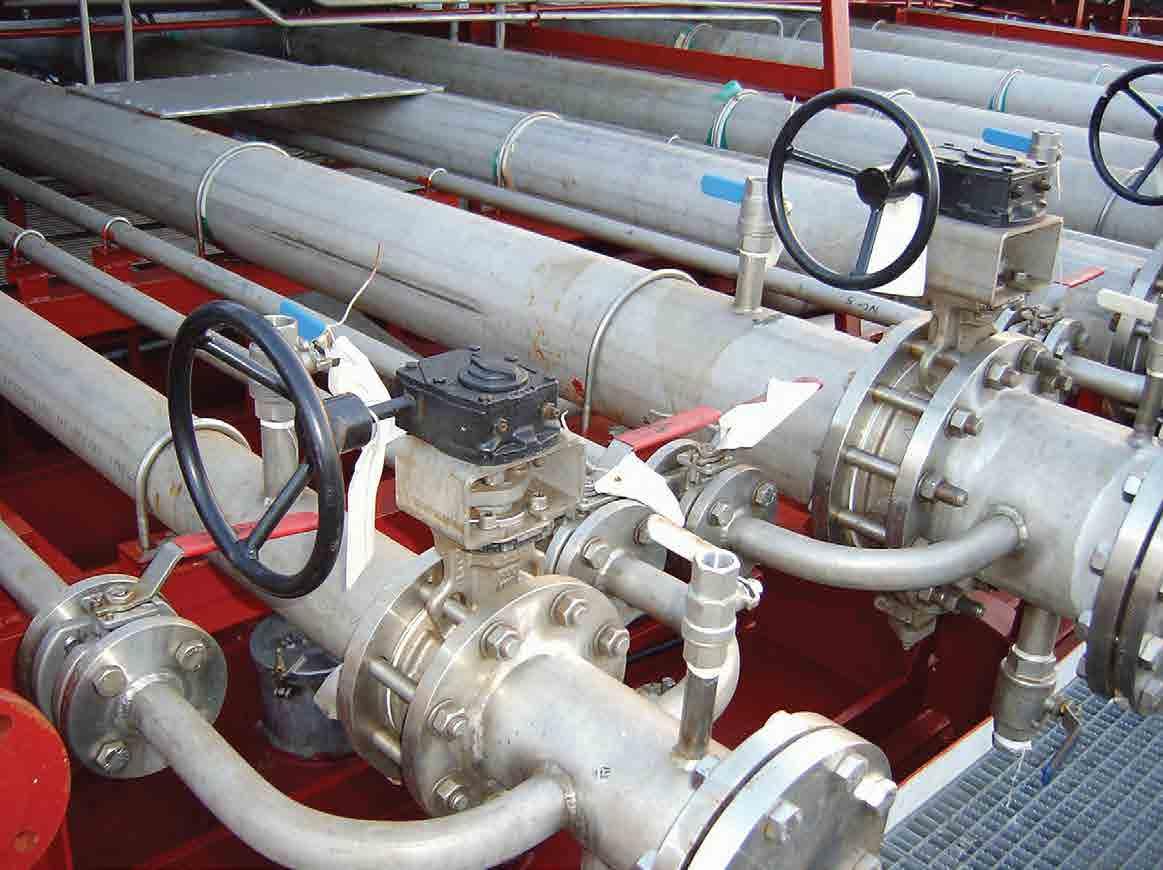
9 minute read
Smart, versatile machine-tool solutions LNS
butterfly valves with all the relevant approvals in place. These were available in sizes ranging from 50mm to 1,400mm. Following strong growth since its acquisition by AVK, the company needed to expand its manufacturing capabilities and in 2008 extended its existing state-of-the-art facilities by a further 3,500 square metres. Today the AVK Group is represented in over 80 countries worldwide and employs more than 3,000 people, of which over 250 are located at the Wouter Witzel EuroValve plant in Losser.
Continuous innovation and improvement
All Wouter Witzel EuroValve products meet the most stringent international quality requirements and are extremely durable. The company is active in seven key markets which range from oil & gas and desalination to shipbuilding and construction. In addition, the company is also active in the water treatment, district cooling and power station industries. Each market segment is treated as a separate entity and products are designed to meet their individual, specific requirements. The company’s highly qualified engineering consultants specialise in each of their individual segments and have knowledge of many applications, processes and developments in their diverse areas of expertise. This clear and targeted focus allows the company to optimise its services and product knowledge, which is unparalleled in the industry.
Luttikhuis said, “Traditionally we started with shipbuilding and water treatment valves and are now involved in seven distinct market areas. Our greatest opportunities for growth today are in the oil & gas and industrial sectors where there is strong growth globally. Our route to market is different in each country and like our products we meet clearly defined needs and objectives in each sector. Today more than 90 per cent of our production is for export markets. Since being under the umbrella of the AVK Group, we have been able to leverage our sales activities through their extensive global offices, agents and partners. This is particularly advantageous in our important water, marine, oil & gas, chemical and power sectors. Our customer base is extensive and incorporates the world’s leading shipyards, oil & gas companies and international water treatment companies.
“Our product offering is second to none and our unique vulcanisation process means that our valve liners are permanently fixed to the valve body, which offers sig-

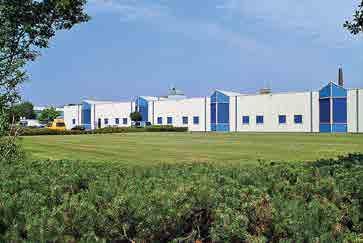
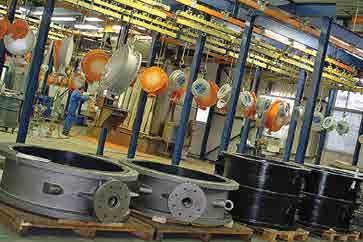
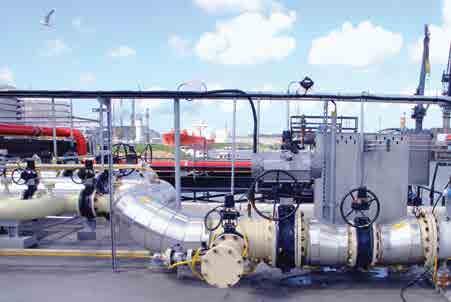
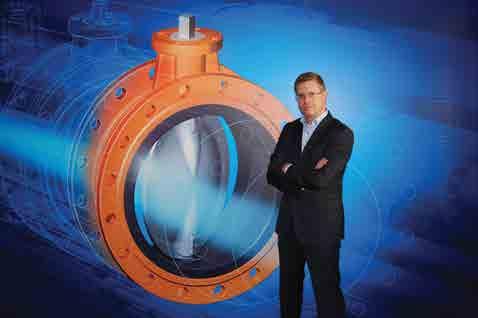
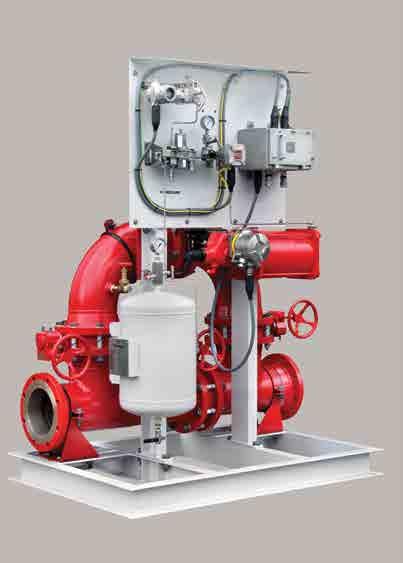
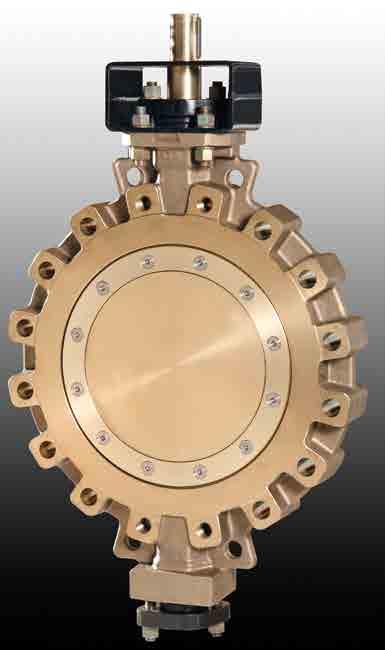
nificant advantages over loose-liner valves. This is particularly the case in a vacuum application, as liners cannot be pulled in and furthermore, this results in significantly lower torque figures. Later this year we plan to launch our next generation of high performance butterfly valves. These have been developed especially to meet the challenging needs of the shipbuilding, oil & gas and chemical industries.
“When it comes to new business, we have an active market approach and use our own dedicated sales forces in our key markets. Our main geographic markets vary with each product sector, however when it comes to the oil & gas and industrial segments we are looking to Europe, South America, the Far East, South East Asia, the Middle East and China for our strongest growth potential.”
Luttikhuis added, “We work on high-spec products and offer our customers optimised tailor-made solutions. Testing is mainly done in-house unless there are very special configurations required. The environment is also a key focus area for us and our production processes are constantly being upgraded in this respect. We are currently in the process of acquiring the environmental quality certifications, ISO 14001 and OHSAS 18001 and expect to have these in place later this year. We also have a very positive outlook when it comes to the future and we project double digit growth in the years ahead”
Infinite range of materials and coating systems
Wouter Witzel EuroValve products are designed specifically to meet the individual requirements of each market sector. For example, valves designed for the oil & gas industry, like those in other sectors, are available with a wide choice of materials and coating systems. A material that the company often uses for its valve control discs is corrosion proof, wear-resistant duplex stainless steel. This exceptionally hard material is ideal for use in membrane filtration or demineralised water because of its high resistance to chemicals and it is strong enough to accommodate pressures up to 25 bar.
In addition, the company offers many advanced sealing materials such as EPDM, NBR, Viton and Silicon rubber. The oil & gas refining processes impose high pressures, high temperatures and exposure to water that is laden with aggressive chemicals. This may make it impossible for rubber lined butterfly valves to be used in certain circumstances. This is when the company employs its Dynaxe high performance butterfly valves, which are available in many high quality materials such as stainless steel 316, duplex stainless steel, aluminium bronze up to titanium. These products also come with a variety of sealing materials. n
For further details of Wouter Witzel EuroValve products and services visit: www.wweurovalve.nl
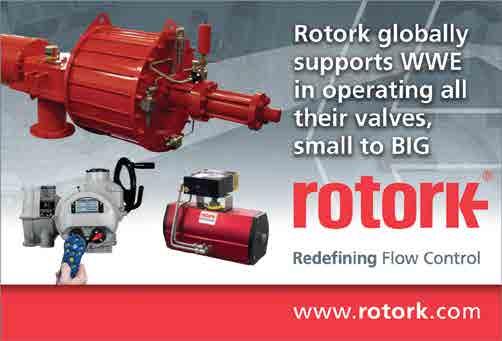
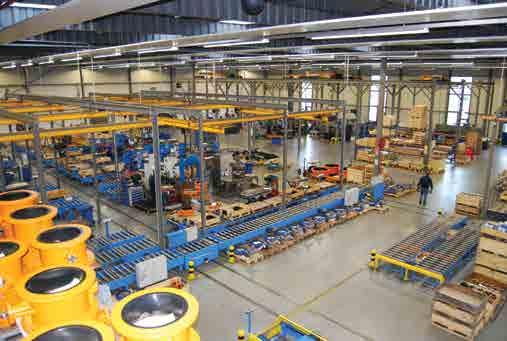
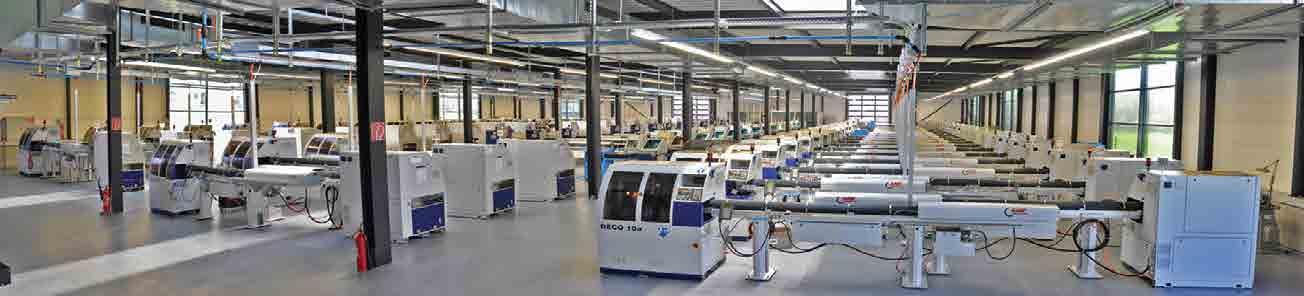
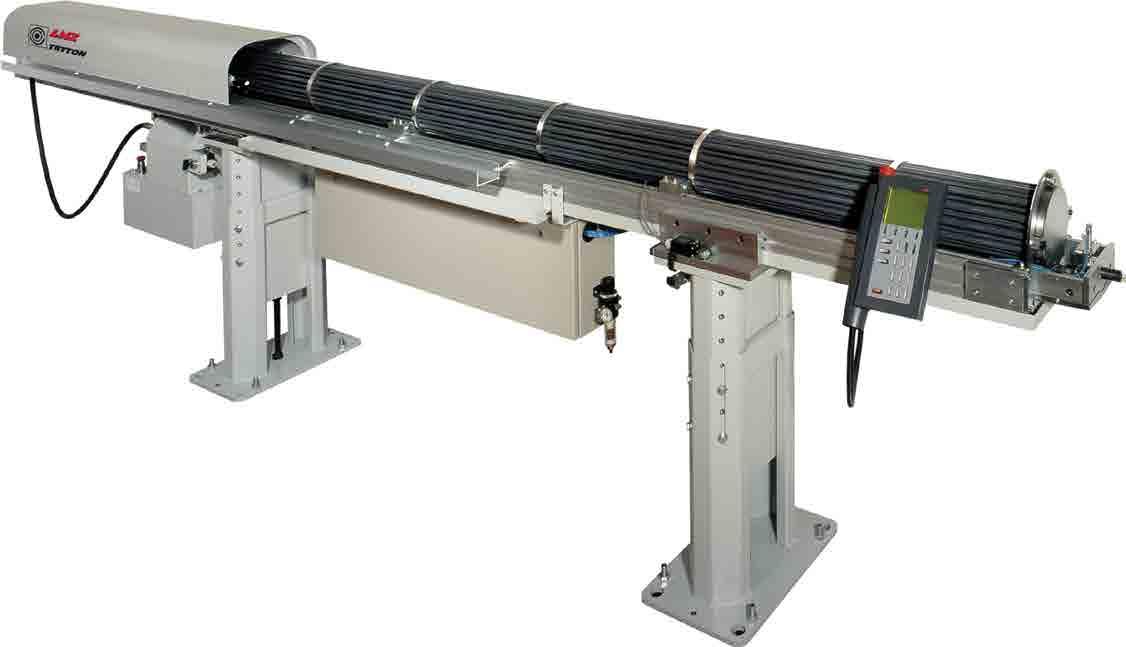
SMART, VERSATILE
MACHINE-TOOL SOLUTIONS
The LNS Group is the global market leader in the development and manufacture of automation systems for the machine tool industry. Philip Yorke talked to Gilbert Lile, the company’s CEO for Europe, about its latest ‘Smart’ chip conveyors and innovative bar feeding systems.
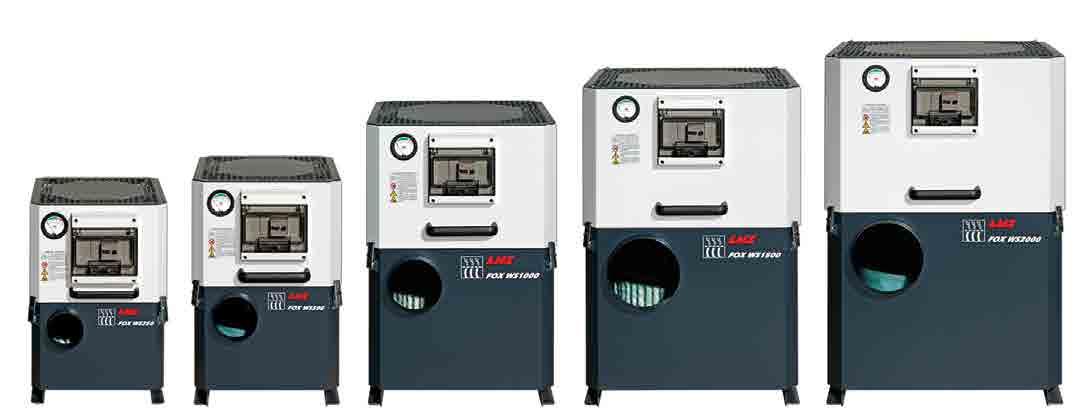

LNS was founded in Switzerland in 1973 by three entrepreneurs with a technical background who decided to design bar feeders that improved the speed and efficiency of fixed and sliding headstock lathes. Their success is now recognised worldwide and innovation remains at the heart of all LNS Group operations. This year the company celebrated 40 years of pioneering innovation that has revolutionised the machine tool industry.
Today LNS is the global market leader in automating machine tools with more than 800 employees worldwide. The group operates nine state-of-the-art production facilities located in Switzerland, the UK, Italy, Turkey, North America, China, Taiwan, and Japan. To date, more than 120,000 bar feeders have been produced and delivered by LNS and over 250,000 chip conveyors installed worldwide.
Optimising productivity
The LNS group mission is simple - to be the global partner of choice in automating manufacturing with innovative solutions. The group offers ‘one-stop-shop’ solutions for the machine tool industry and is committed to providing the highest levels of innovation and customer-focussed service. LNS supports its customers with a wide range of peripheral products designed to optimise their efficiency in its key markets. At the 2013 EMO trade show in Hanover the company showcased its latest entry-level, Alpha 552 bar feeder in Europe for the first time. Other innovative products were also on display including its allnew oil mist collector: the Fox WT700 which will become available during 2014, as well as its Fox SC500 spray cabin.
Gilbert Lile said, “With the development of the SC500 spray cabin, we want to contribute to providing a healthy, clean and safe working environment for operators. The SC 500 achieves this with its high efficiency filtration, low noise level and mobile, compact design.
Similarly, with our introduction of the Alpha 552, we have increased operator efficiency and extended our entry-level bar feeder range.”
“Looking to the future, whilst our high-end bar feeders such as the Express and Sprint series continue to be very successful, we expect the entry level sector to grow significantly in the coming years. The main characteristic of the Alpha 552 is its outstanding reliability and ‘quick-change system’, which allows the operator to replace the guiding elements without the need for any kind of tool. In addition, the touch screen is also very user friendly with its enhanced memory and supported languages. Last but not least, the Alpha552 meets the highest safety standards.”
Gilbert Lile added, “As far as our European markets are concerned, Switzerland remains our biggest single market. However, Germany and Italy also have very large machine tool markets, as do France, Spain and the UK. What’s more, despite being a global company we think and work on a local level and our facilities are strategically located to be as close as possible to our customers. We are the only company in our sector that can offer a truly ‘one-stop-shop’ service, because none of our competitors are able to match our comprehensive package of products and services.
“Not only do we cover all four key areas of machine tool operations: bar feeders, chip conveyors, air filtration systems and coolant

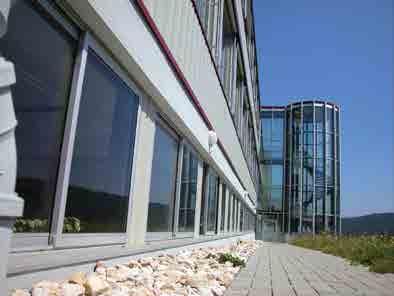
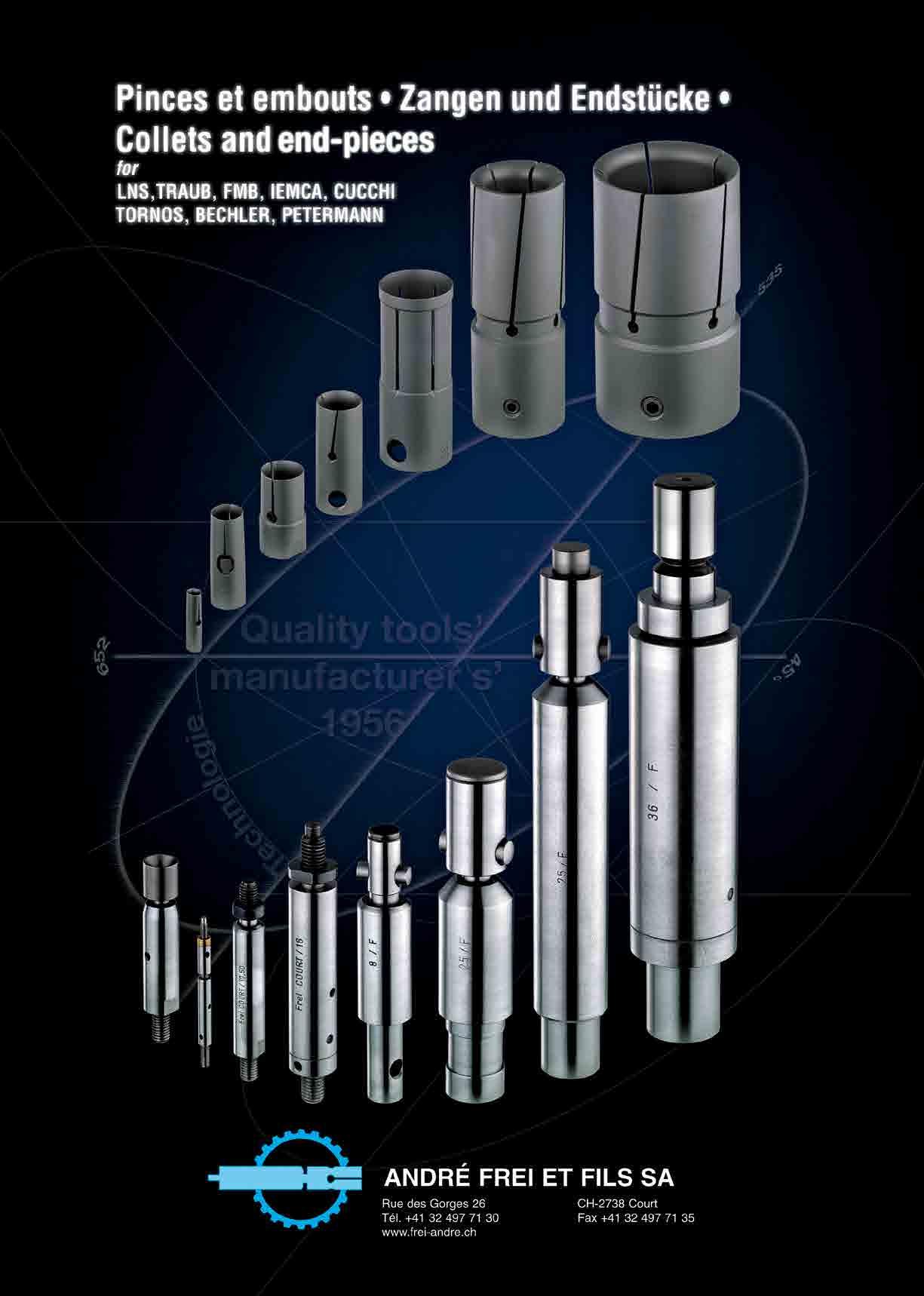
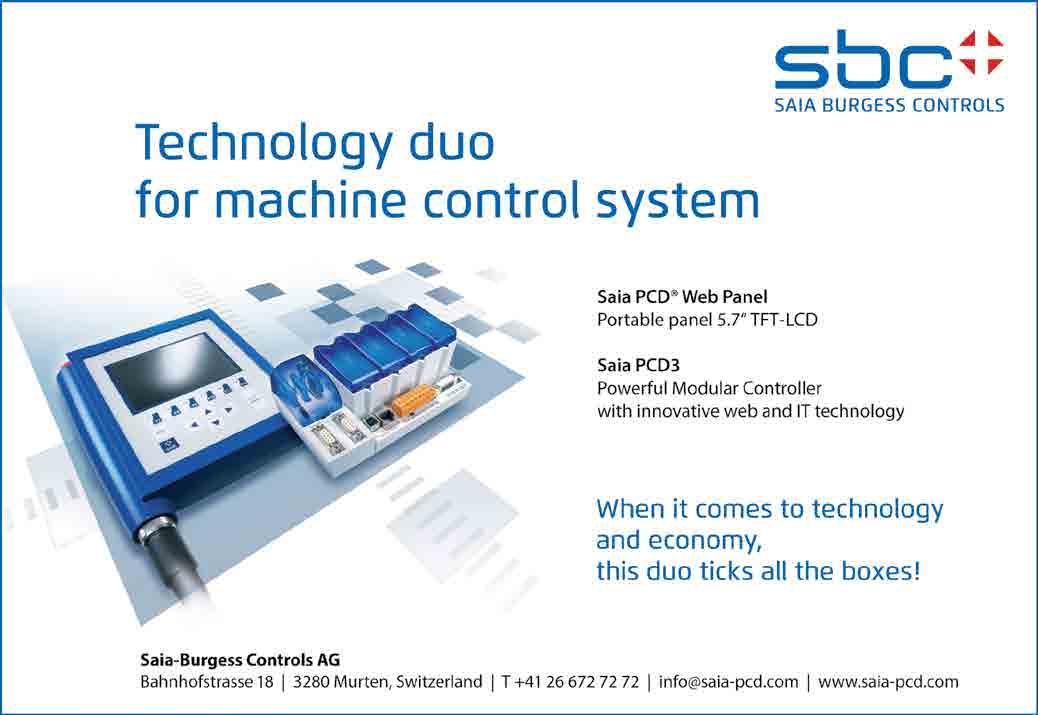
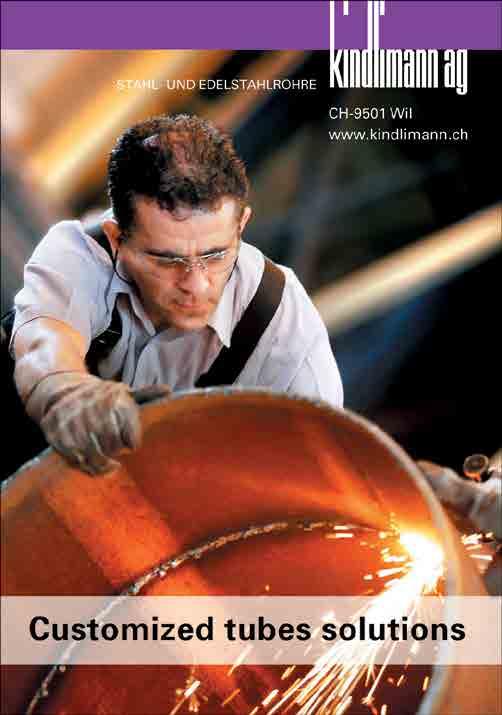
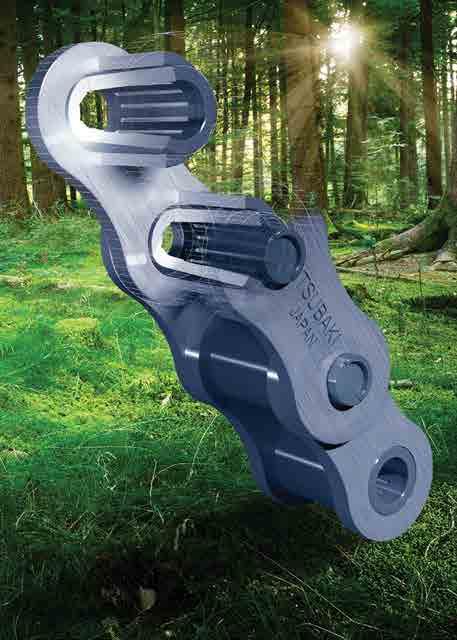
Tsubaki is the world leader in the manufacture of drive and conveyor chain and sprockets; reducers and variable speed drives; couplings and clutches; and cable and hose protection and guidance systems.
Driving to be the “global best”, the Tsubaki Group focusses its comprehensive strength on maximizing our corporate value whilst remaining committed to customer and manufacturing excellence.
Product innovation ensures your continued motion.vation ensures your continued motion. Customer service and quality ensures your continued satisfaction.
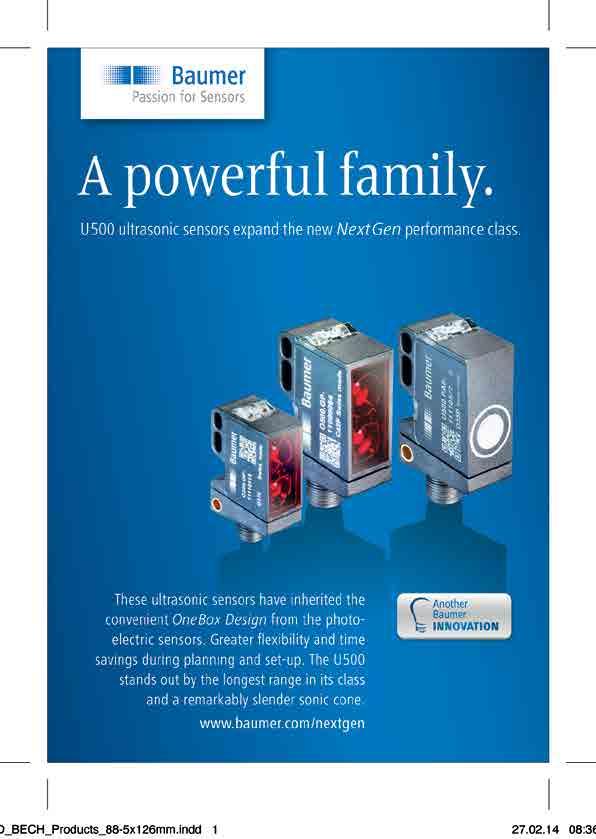
FDM F.LLI MAZZOLA SRL Certified company UNI EN 15085 and UNI EN 3834.
The company specialises in bespoke work and welding, according to the quality requirements of European regulations UNI EN 15085 and UNI EN 3834, for customers operating in the rail industry, manufacturers of machine tools, textile machinery, machinery for the alimentary fi eld, furniture and design.
From their solid experience in the fi eld and continuous technological updating, FDM SRL is able to supply products or patterns provided by customers, with particular attention to the choice of materials and fi nishing treatments, following the customer from prototype to fi nished product.
Thanks to their fl exibility, FDM SRL has developed good relationships with all its customers, ensuring full satisfaction in terms of quality and economy.
Care to detailor excellence of the products
Company Certified Welding UNI EN ISO 3834-2 Uni en ISO 15085-2 Sheet Metal Working Laser Cutting
Office & Work I-24040 Capriate San Gervasio (Bg), Via Giovanni XXIII, 50 T: +39 02 90962826 | F: +39 02 90962677 | E: info@fdm.it | www.fdm.it
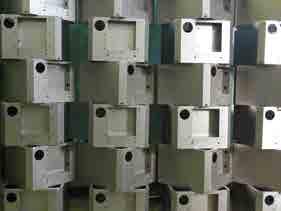