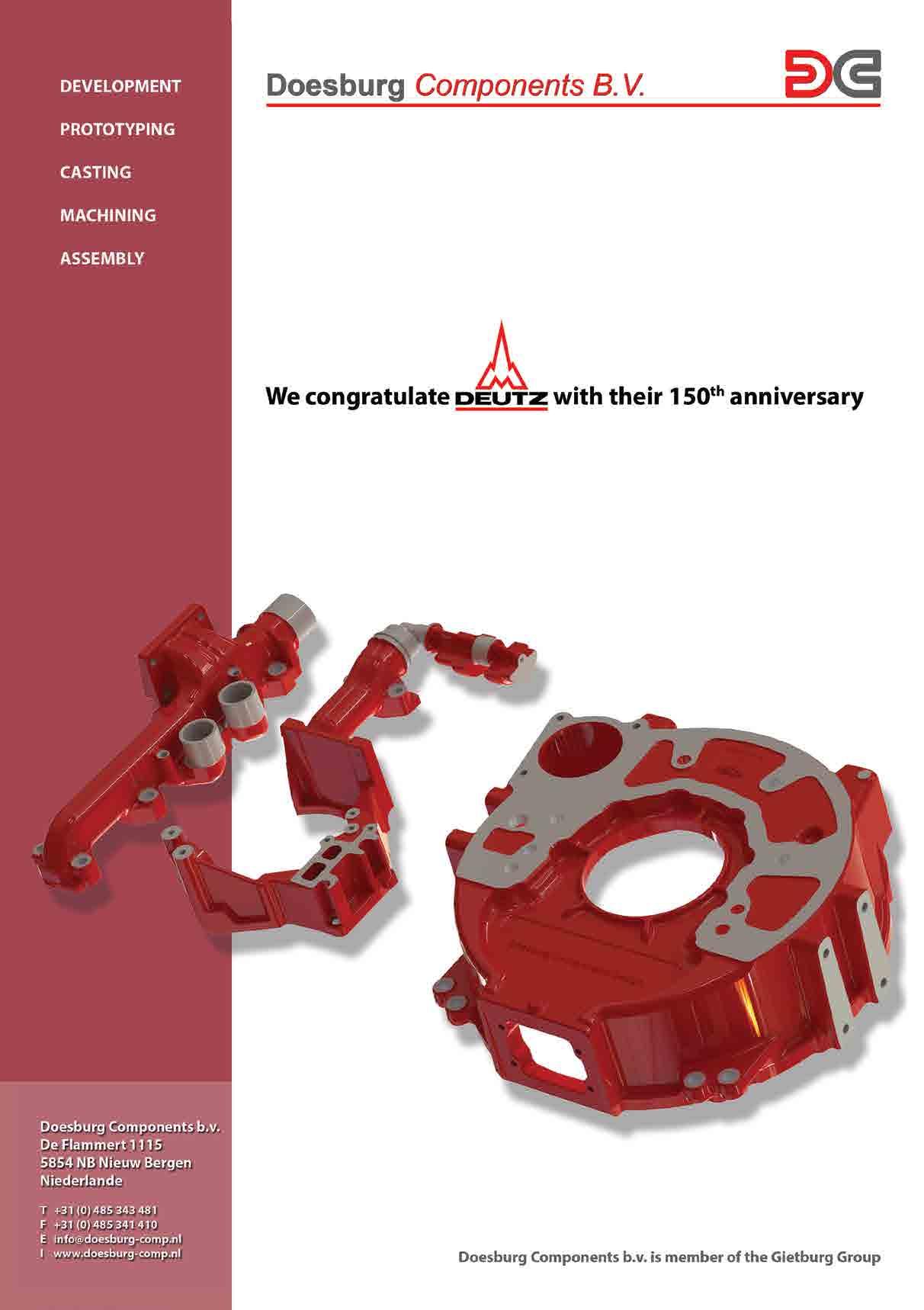
5 minute read
Meeting your needs, wherever you are
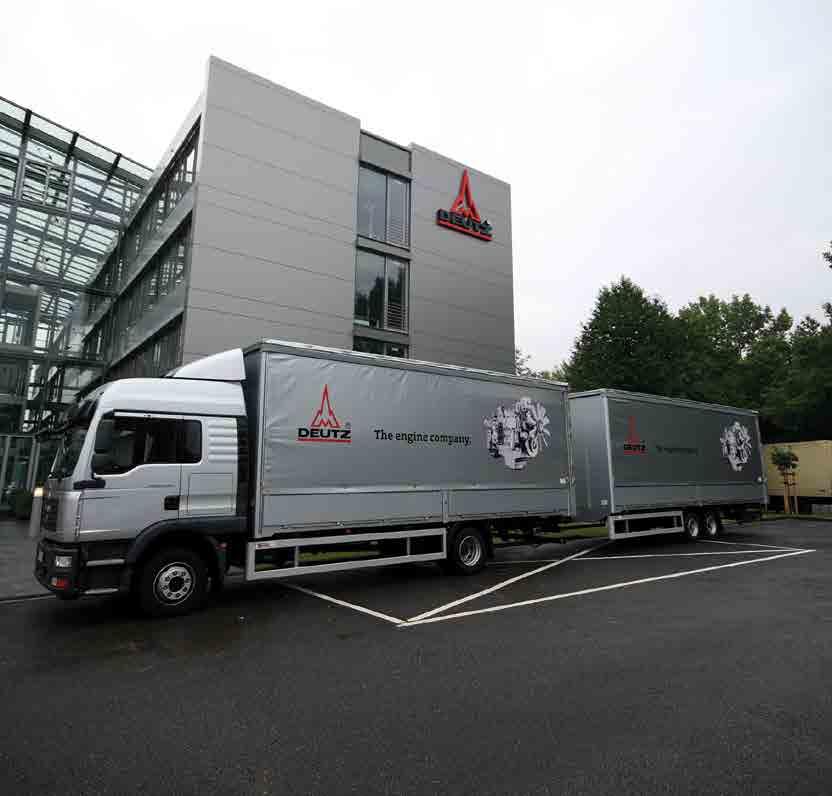
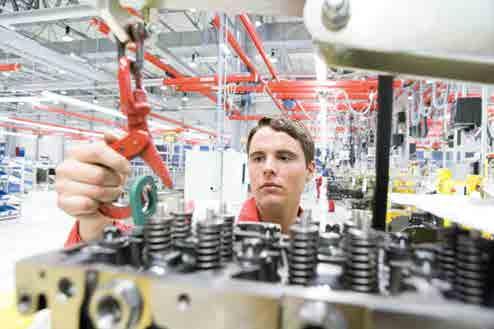
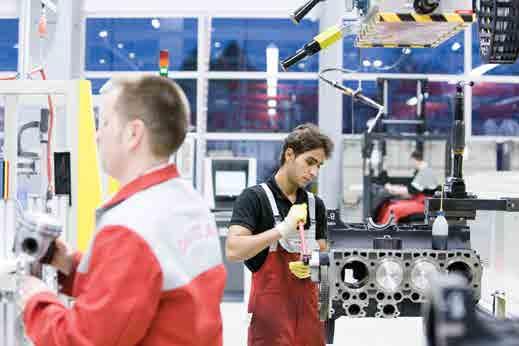
Limiting emissions
One of the greatest challenges facing diesel engine manufacturers today is making their products compliant with current and future exhaust emission regulations. This means reducing the concentration of pollutants such as NOx (nitric oxide), CO (carbon monoxide), HC (hydrocarbons), particle emissions and CO2 (carbon dioxide).
“We have succeeded in meeting the European and US emission reduction regulations – NOx from our engines is down by 95 per cent and particle emissions by 99 per cent – and we are now addressing the next stage of legislation,” explains Michael Wellenzohn. “This is undoubtedly a great challenge to engine manufacturers and will require the addition of further technology modules to our engines. It’s really like having to construct a small chemical plant around each engine to treat the exhaust gases. To reduce CO and HCs, for example, you need a Diesel Oxidi- sation Catalyst system, to remove particu- lates you need a Diesel Particulate Filter or a Diesel Oxidisation Catalyst depending on application and to remove NOx you have to have a Selective Catalytic Reduction system.
“Of course the simplest way to reduce pollutants is to improve engine performance and efficiency and reduce fuel consumption with established technology such as fuel injection, turbo-charging and electronic engine management systems and we have been doing that for years. But the continuing demands of regulation are very costly for the industry and make it ever harder to get a payback so it’s essential that we continue to develop ever-smarter solutions.”
Directions for growth
At November’s Agritechnica show in Hanover Deutz presented four new engines developed specifically for use in agricultural equipment. These four and six cylinder engines cover a power range from 55.4 kW to 390 kW and the compact TCD 2.9 is particularly suitable for use in narrow-track tractors.
“With our engines for use in agriculture we have already been able to obtain a number of new customer projects and new applications with existing customers, further expanding our customer base in the area of engines smaller than four litres,” explains Michael Wellenzohn. “We are currently completing the final project phase with multiple new OEMs in Europe and the Far East. Serial production with these customers will commence in the first half of 2014.” Deutz’s new compact engines are also proving popular for applications such as work platforms, material handling machines, scissor lifts and all kinds of construction equipment.
Worldwide service
Extending its sales in the agricultural sector is not the only strategy that Deutz is pursuing to support its future growth. The company is also focused on continuing to take market share from its competitors in the construction and stationary applications areas worldwide and on adding value to its engines by providing complete power packs, including control units, frames and systems interfaces. But perhaps most important of all for the future is the expansion of Deutz’s global service business.
“The complexity of our engines has increased considerably over the last ten years, most obviously through the addition of all the different exhaust treatment systems, so whereas in the past an end user such as a construction company could service its own machines, today it is essential for servicing to be carried out by trained specialists,” says Mr Wellenzohn. “That means that we have to put a lot of work into training our distributors and service partners throughout the world to ensure that the end customer gets the service at the distributors and in the field that keeps his equipment running. When we provide this complete service it brings us closer to our end customers who are then more likely to ask their equipment suppliers – our direct customers – to specify our engines. Effectively we are then approaching the market from two sides – getting OEMs to use our engines and encouraging end-users to ask the OEMs to use our engines. What’s certain is that if you don’t deliver a comprehensive and efficient service package, you don’t sell engines in today’s market. Deutz will never make that mistake – we are, after all, ‘The Engine Company’. n
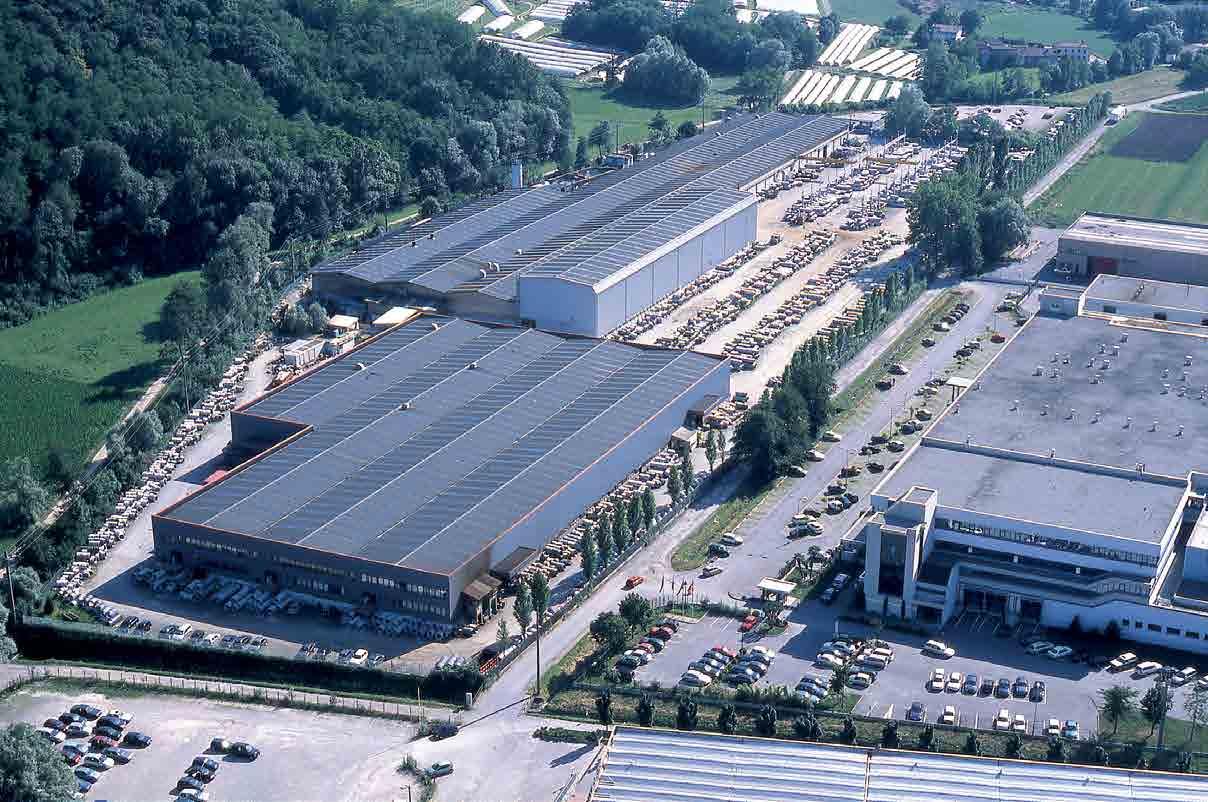
Over the past few decades, Swiss-based Ferriere di Stabio S.A. has become a leader in the manufacture of stainless steel parts for the automotive sector. Barbara Rossi talks to sales manager Antonio Marenco to find out the latest news from the company.
Ferriere di Stabio S.A. started its activity in Stabio (Switzerland) where its headquarters and main production site are still based today. Initially it was engaged in the production of steel rods, but the first major turning point came in 1966 when it started manufacturing carbon steel bolts. Further expansion was achieved in 1972, when the product range was widened to include stainless steel bolts. Thanks to its success in this area, in 1982 the company decided to focus its entire range solely on stainless steel fasteners. This move allowed it to develop in a short time, gaining and consolidating its position as a leading producer at global level. While initially FdS (Ferriere di Stabio) was only a small operation, today the company employs more than 150 people.
A market leader
Currently the company, which is part of a larger Swiss Italian group, is one of the largest manufacturers of stainless steel bolts, screws and special cold-formed parts worldwide. It makes both standard fasteners (in a very wide dimensional range) and special parts. Over the years, thanks to a series of investments, the share and importance of the special parts production has increased steadily. The company holds a number of international certifications, including ISO 9002, ISO TS 16949 and ISO 14001. The production range is such that the most demanding requirements can be fulfilled both in terms of the standard offer and special components.
Its main plant occupies a 120,000m2 area, of which 35,000m2 are dedicated to production. Over the years this has