
6 minute read
Austrian innovation in timber technology Binderholz
plex engine and battery cooling assemblies. For the global offer of Engine and Battery Cooling systems, Tristone also provides a broad range of water pipes and radiator air guides.
Tristone's key Air Charge products include high-tech reinforced rubber hoses, plastic blow-moulded ducts and plastic injected subsystems. High performance Eur 6-ready materials combined with smart integrated solutions and full system expertise in airflow, acoustics, structure, thermodynamics and decoupling mean that complete system development and manufacturing can be offered.
Air Intake products include compact air intake cassettes, air filter cartridges, ducts, hoses, guides, flaps and extractors; all combine full system expertise in airflow, acoustics, filtration and decoupling.
Günter Frölich: "Our commitment to a strong R&D investment programme has kept us ahead of our competitors, especially in providing Engine and Battery cooling solutions. I believe that our technological edge is the main driving force that allows us to expand on the growing Passenger car industry market worldwide. In the hybrid or electric battery sector we have a 25 per cent market share – for the moment a small proportion of the total production market, but the one that is seeing the highest growth potential."
Günter Frölich Beyond Europe
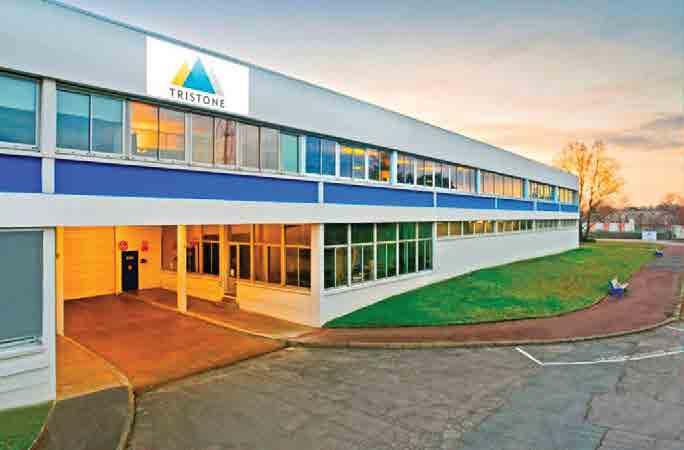
Tristone has manufacturing sites in nine countries and has teams of engineers working on several clients' sites. The Mexico plant the group took over in 2011 now employs more than 250 people, and manufactures engine-cooling and battery-cooling applications for the automotive industry in Mexico and the USA. In Asia, the cooperation with Indian Bony Polymers allows both companies to combine their joint strengths and expertise by working together on common projects. Tristone provides technical support in the areas of production and logistics for engine cooling hoses, pipes, surge tanks and turbocharger hose applications. The Shuzhou plant in China started manufacturing for Volvo in August 2013 and production for Ford is scheduled for the beginning of 2014. Other new clients Tristone is working with are Suzuki and Nissan.
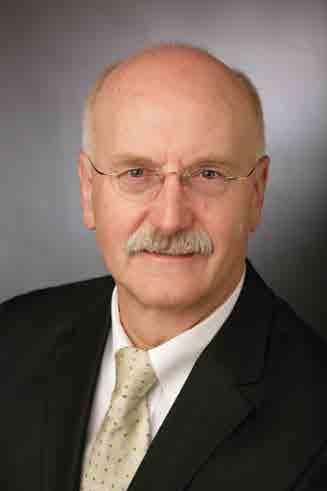
Top in technology and leading in the market.
Mubea Spring Band Clamps
Self-tensioning sealing component which always produces suffi ciently high sealing forces.
• Worldwide production facilities • Manufactured 100% inhouse • Certified according to ISO/TS 16949 and ISO 14001 • Corrosion protection according DIN EN ISO 9227 • Nominal diameters from 9mm up to 98mm
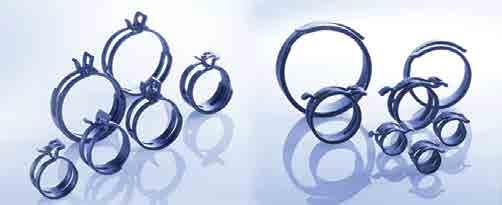
Muhr und Bender KG | Postfach 360, 57439 Attendorn, Germany federbandschellen@mubea.com | www.mubea.com
Plastic technologies
Plastic extruded pipes have been developed over the past few years to allow important weight and cost reductions as well as improved recyclability, as an alternative to rubber in specific applications. Tristone still maintains important investments in this technology and it is developing and proposing a large range of material solutions including multi-layer pipes.
The company integrates and develops various plastic technologies including injection, 3D suction blow-moulding, extrusion and welding technologies to provide more solutions to plastic pipe design. This process flexibility is vital for meeting new, demanding constraints on engine packaging.
Tristone's process solutions across semiautomatic and fully automated production cells are adapted to high volumes and quality levels with single digit ppm.
Günter Frölich: "Our latest generation of products are much lighter and offer greater innovation and value than ever before. We work closely with our OEM partners to develop new energy-efficient products, especially in the integrated engine and battery-cooling system areas. As a growing medium-sized player, we are not as big as the market leader but I believe that we are more flexible and more innovative with a best-in-class quality level." n
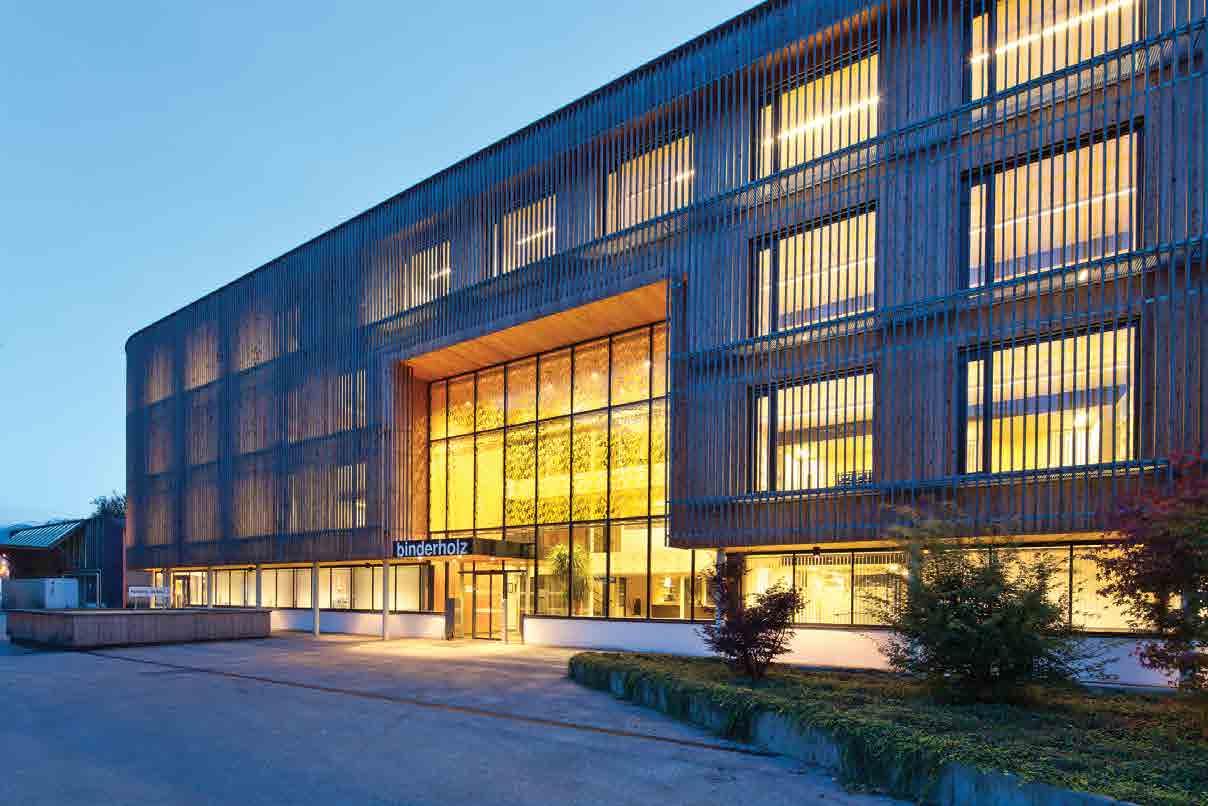
AUSTRIAN INNOVATION IN TIMBER TECHNOLOGY
Binderholz Bausysteme provides products and solutions for solid-wood construction projects and is part of the binderholz group.

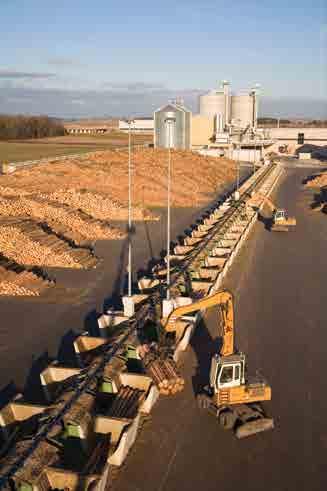
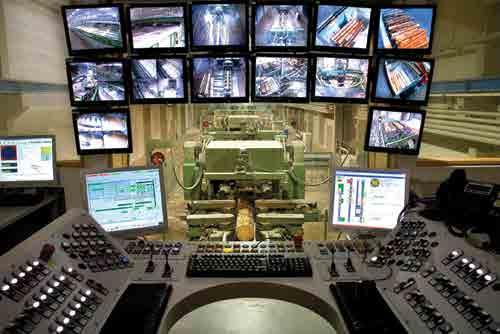
The binderholz group manufactures lumber products, solid wood panels, glulam beams, cross-laminated timber BBS, pellets and briquettes, while two of its production plants produce green energy that is directly delivered to the neighbouring towns. The products are manufactured at six locations in Austria and Germany and exported all over the world. 46.2 per cent of Austria is covered by forests. The yearly increment in productive stands is 31.4 million m3 with about 19.8 million m3 of felling. Therefore, the sustainability of timber production is assured. The timber industry forms an important, exportoriented part of the Austrian economy. The diverse foreign markets with varying needs and a demand for ever more modern and innovative technologies present an ongoing, interesting challenge for the industry. With in-depth knowledge of the markets and by accommodating the specific requests of partners, Austrian companies deliver timber technology to customers all over the world.
Binderholz Bausysteme managing director Helmut Spiehs says, “Austria’s timber technology is at the very top of the industry in many sectors. The industry’s export successes extend beyond Europe, where partners from China, Japan and the USA also believe in Austrian quality.”
In the timber industry the name Binder stands for high technology and innovation. Founded 50 years ago by Franz Binder, today the company’s three divisions are run by his three grandsons and the company is still fully owned by the Tyrolean Binder family, safeguarding tradition and integrity. The binderholz group today is a leading European company, equipped with advanced technologies and production methods, with a corresponding reputation on the timber material market.
At five Austrian sites - Fügen, Jenbach, St. Georgen, Hallein and Unternberg - and one German site - Koesching/Interpark - the binderholz group employs about 1,200 people.
Solid economic arguments
Of all construction materials, wood features the best relation between weight and loadbearing capacity. Wood is the material that is selected most often when it is a matter of passive houses and houses with low energy consumption. And for good reasons: wood succeeds in complying with structural-physical requirements to the greatest possible degree.
Helmut Spiehs: “People opt for wood because of its atmospheric characteristics: the agreeable surface temperature, its capacity to balance temperature and moisture peaks. Likewise, wood - like plaster - exercises a positive influence on the well-being of people and thus on their health - which also constitutes an economic factor.”
Since the tare weight of wood constructions is lower, the expenditure for the substructure and foundations is reduced. The high degree of prefabrication makes processes at the construction site easier and ensures a standardized and verifiable quality. Construction site facilities can be kept on a smaller scale, the expenditure in terms of logistics is lower. The dry construction method shortens construction times substantially, thus making an earlier use possible, which in turn reduces financing times.
Prefabrication saves time
Binderholz Bausysteme prefabricated timber construction solutions, are designed and supported by the company’s in-house
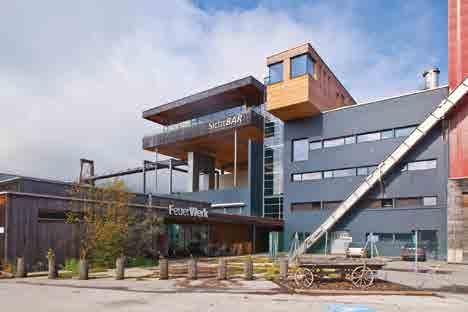
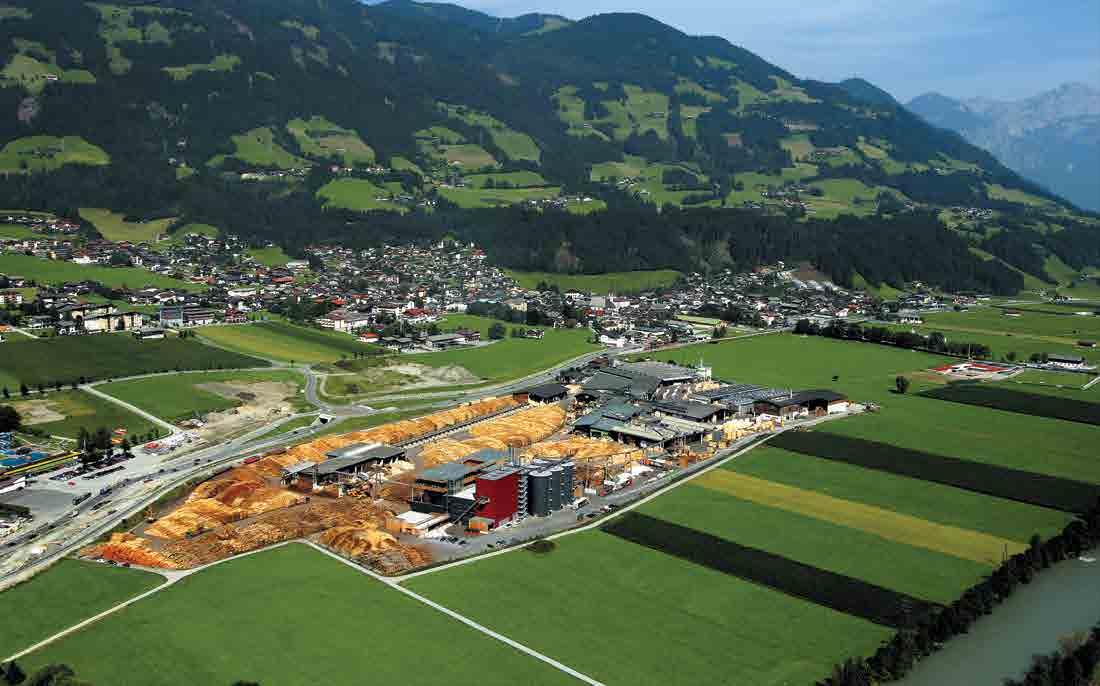
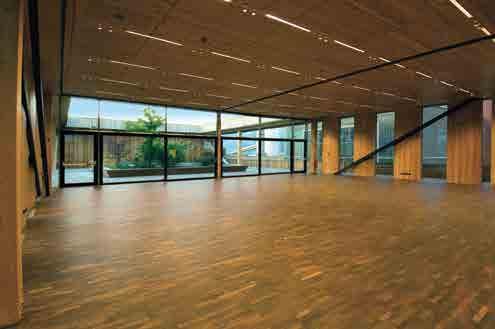