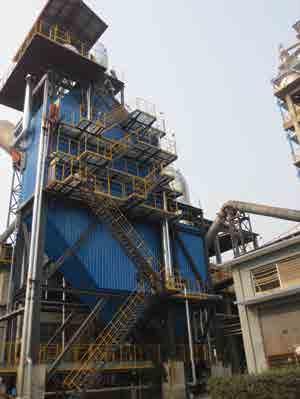
6 minute read
Well done containers Weldon
Shanghai Triumph Energy Conservation Engineering Co., Ltd (STEC) is a high-tech joint venture located in Shanghai, China and was established by China Triumph International Engineering Co., Ltd (CTIEC) in China and Mitsubishi Corporation (MC) in Japan. We are specialised in professional engineering services for Waste Heat Recovery System and energy-saving type Vertical Roller Mill.

Waste Heat Recovery (WHR)
• Integrated waste heat recovery solution. • Technical cooperation with world leading company in BTG system and ORC system. • Services in industrial fields: cement, glass, iron-steel making and chemical plants etc. • Rich experience: near to 50 references WHR projects worldwide with the installed capacity of 3MW to 20MW. • Professional technical team: system design, quality control, project management and technical service. • Vartious service types: E, EP, EPC, BT and BOT.
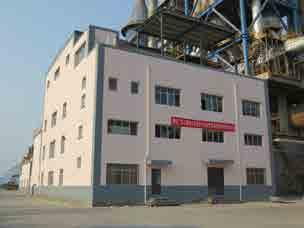
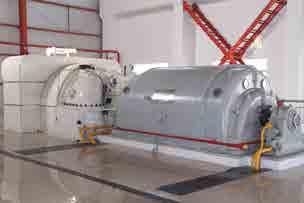

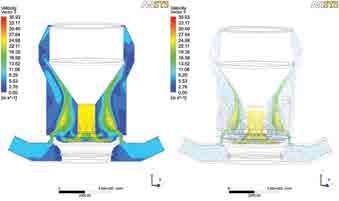

Energy-saving Vertical Roller Mill • Technology licensed by Mitsubishi Heavy Industry. • 60% power saving compared with the tube mill system. • Stable operation and longer service life. • Personalised 3D design according to clients’ request and material characters. • Wide applicable scope: raw material, clinker, coal, pekcoke and slag etc. • Professional technical team: design, quality control and technical service.
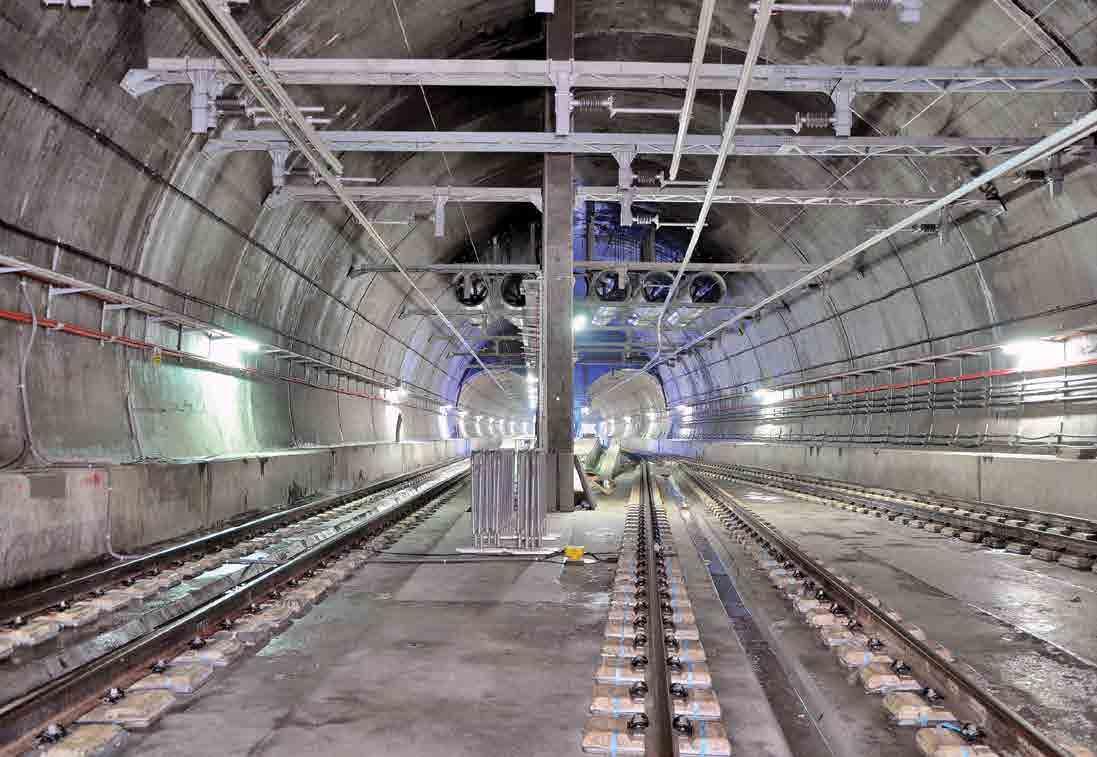
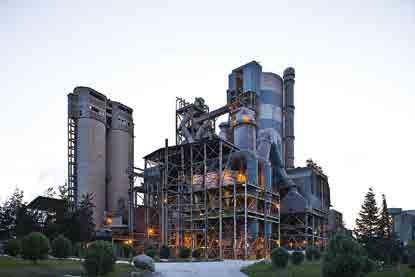
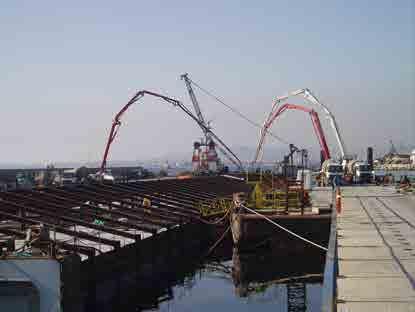
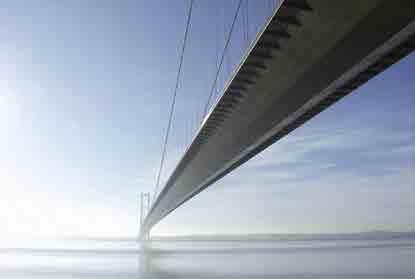
will cost €75 million, and will yield one million tonnes per year when production begins in May 2015. This new capacity will be used in the rapidly-developing Central Anatolian region. The Group is also investing in two waste heat recovery projects.
While sales are focused on the domestic market, the Group is also mitigating excess capacity by selling to Middle Eastern and Black Sea countries. OYAK believes that export markets will fuel growth in sales in products like white cement, slag cement and oil-well cement.
Despite this, the Turkish cement industry still has an excess in capacity, partly due to the fragmentation of production: 50 factories are owned by 20 different groups. OYAK is the market leader, with a 14 to 15 per cent share of domestic sales and expects to end the year with sales in excess of TRY1.6 billion (around $750 million). It also expects that 2014 sales will grow by no less than five per cent.
OYAK’s cement sales are relatively untroubled by the European economic problems, since its export markets are mostly elsewhere, but the weakness of the Turkish Lira has become an emerging problem, since 50-55 per cent of its costs are tied up in fuel and electricity costs that are pegged to the value of foreign currencies.
Lean and focused
The OYAK Cement Group’s vision is to maintain its status as a market leader and to continue supplying high-quality cement for Turkey’s biggest construction projects. It also aims to consider any organic and inorganic growth opportunities that may arise inside and outside the country.
The Group believes in efficiency, lean management and a focus on results. All the constituent companies have highly competent management teams that can sense and respond to the needs of their markets, and its experience as one of the oldest cement manufacturing groups in the country informs all its decisions. The need to make the best possible use of an important pension fund means that efficiency is a top priority; innovation is an intrinsic company value. This has allowed it to develop simple products into valuable commodities and to build the most diversified range of products in the industry. n
STEC is specialized to provide integrated waste heat recovery solutions (WHR) for industry clients and especially cement plants. Our professional engineering services, leading technology and advanced philosophy can help clients enhance their competitiveness and realize a more social contribution, which is what we are endeavouring to do for the OYAK Group’s cement division now. To equip the OYAK Group with a high efficient and stable WHR system, STEC is committed to supporting the OYAK Group for cost optimization, emission reduction and environment protection to consolidate their pioneering corporate image in Turkey. The cooperation experiences with OYAK will also be the milestone of STEC for worldwide WHR business.
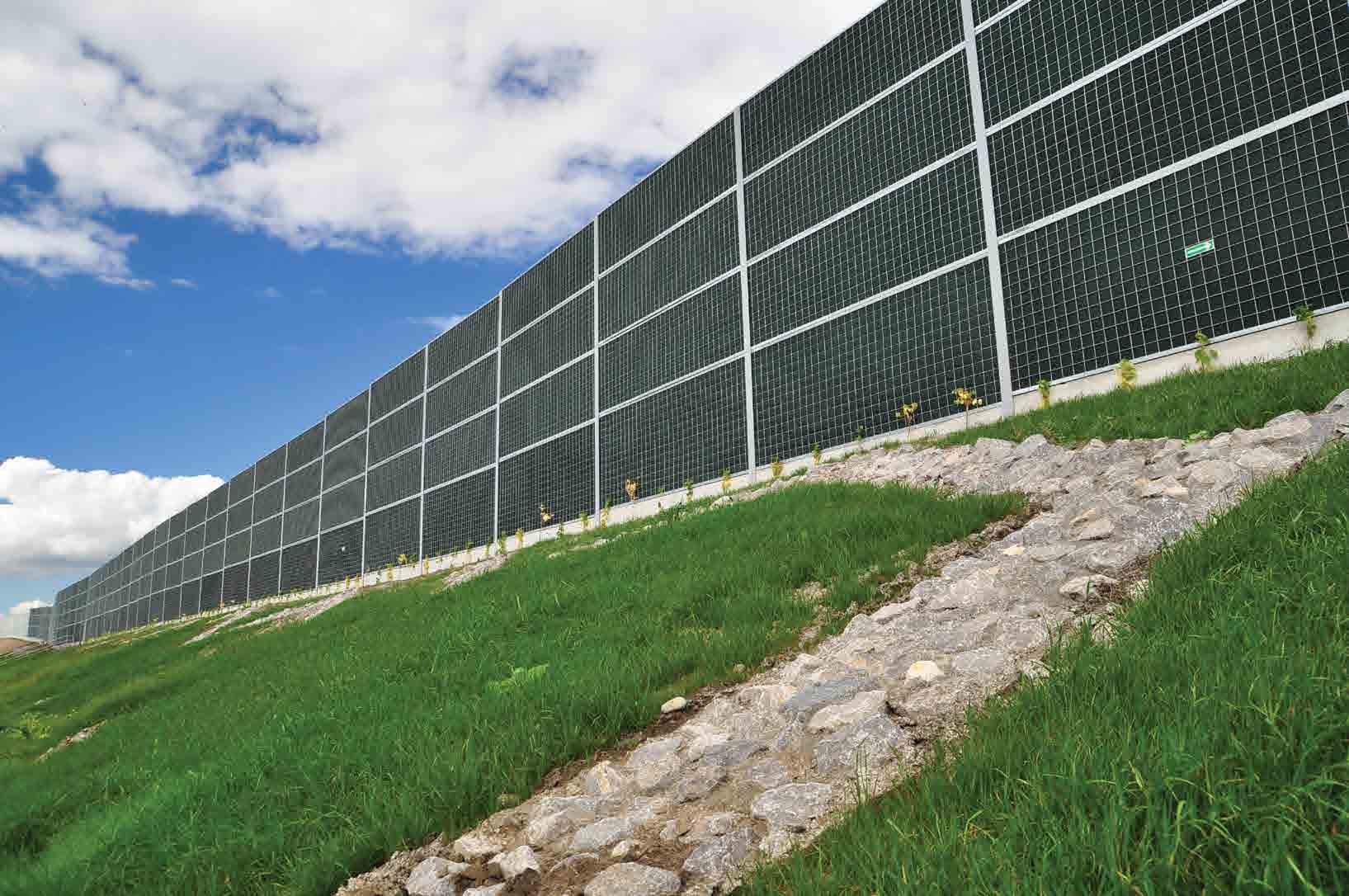
WELL DONE CONTAINERS
Weldon, a company from Podkarpacie region, is Poland’s leading manufacturer of containers, modular buildings, acoustic barriers and steel structures.
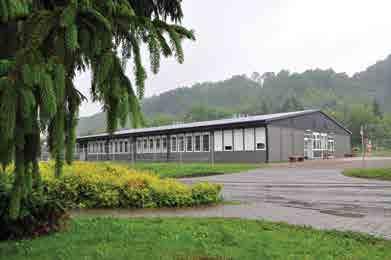
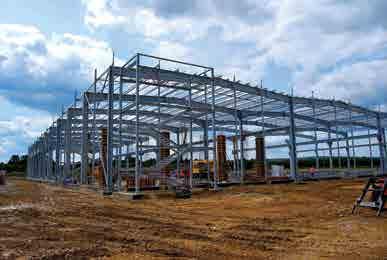
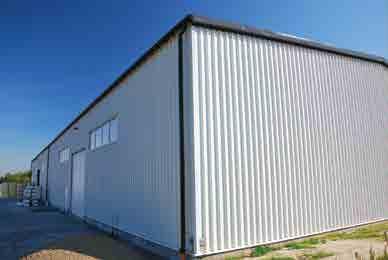
Although Weldon was established in January 2009, the company’s history goes back to 2002, when Metal System, Weldon’s legal predecessor, began operations in the metal industry. Initially, the company offered small modular buildings for small businesses. In subsequent years, rapid economic growth in Poland and the company’s flexible approach to customers’ needs have enabled it the to win many orders. The continuing boom and the prospect of the development of infrastructure investments was significant when the construction of a modern production plant in Brzezowka was decided. The process of the investments was implemented in parallel with the development and implementation of new products, including systems of modular halls and acoustic panels. The 2008 year saw more than 3,000 containers produced for the domestic and foreign markets. It made Weldon one of the leading providers of objects in modular technology in this region of Europe. Currently, the company cooperates in this area with leading construction companies and enterprises, which are specialists in the rental and distribution of modular buildings.
The situation has just started to take a similar shape in the case of acoustic screens, where a newly built plant handles the supply of panels and columns to the largest road projects in Poland.
Increasing the company’s potential
In 2011, Weldon’s new manufacturing plant in Brzezowka, near Ropczyce started its operations. In January, the administration building with the area of almost 400m2, constructed in the modular technology, was completed. A modern production hall hosts the production of containers, steel structures and acoustic panels. It is located near the A4 motorway. Currently, Weldon has two manufacturing plants – the other one is located in Debica.
In early 2013 Weldon purchased the Galvanizing Plant Debica, for PLN 18.31 million (€4.5 million). The plant is located next to the Weldon production unit. Its daily production capacity is estimated as 100 tonnes of constructions. Thus, Weldon’s offer range has been extended by the hot-dip galvanizing services, providing significant enhancement and optimization of the production processes across the company. In the long-term this acquisition will enable it to expand the assortment offered and strengthen the company’s position in the market. Currently, total employment throughout the company after the merger is about 400 people.
Containers for any purpose
Weldon’s containers are aimed at a broad range of clients. Modules can be used as comfortable offices or back-up facilities at construction sites, as living quarters and commercial and service constructions. An important advantage of the offered technology is its versatility and adaptability for industrial purposes, i.e. as rooms for various
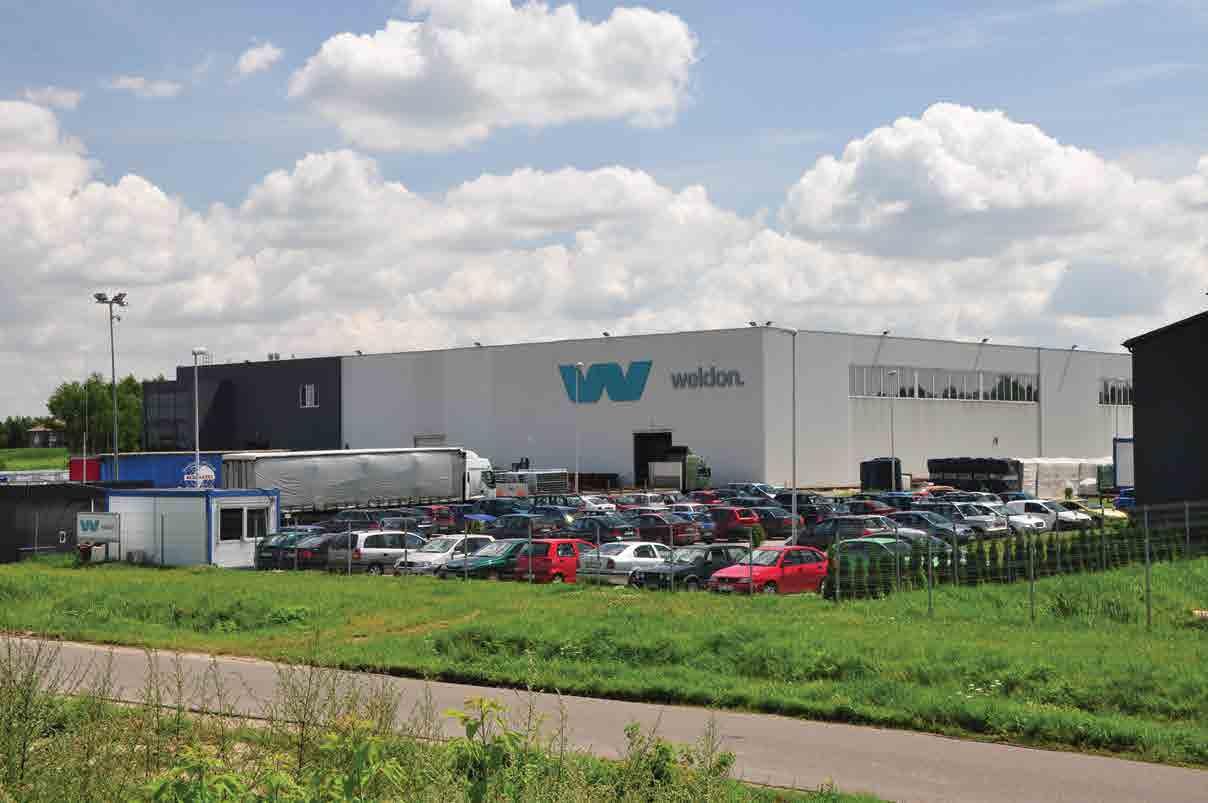