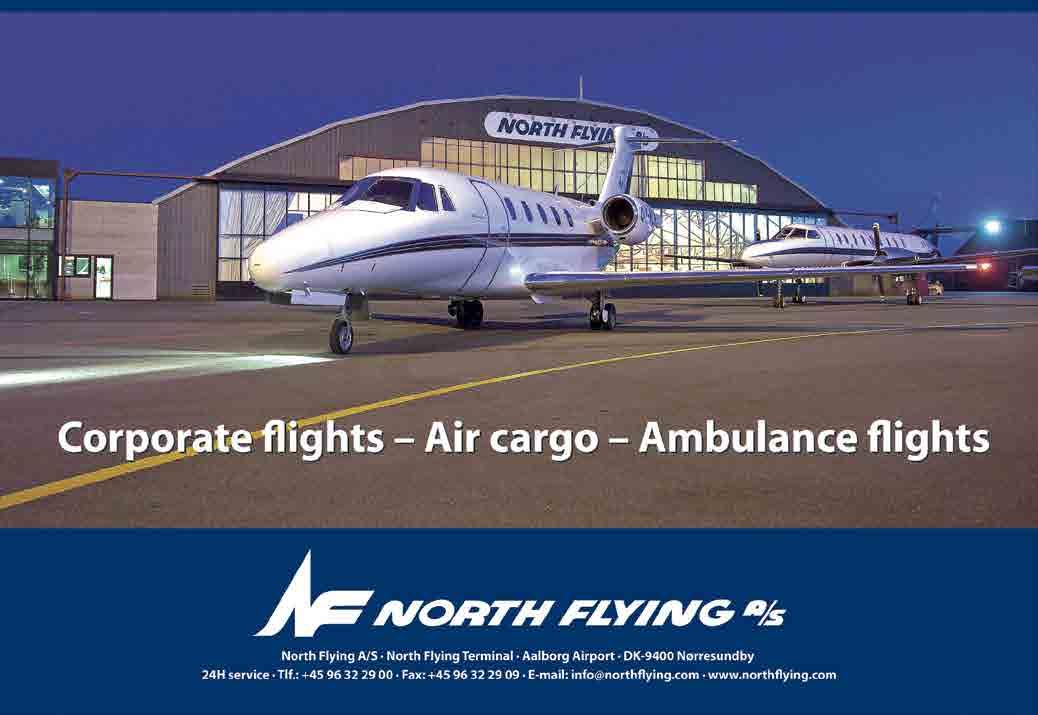
7 minute read
Organising your space Metalsistem
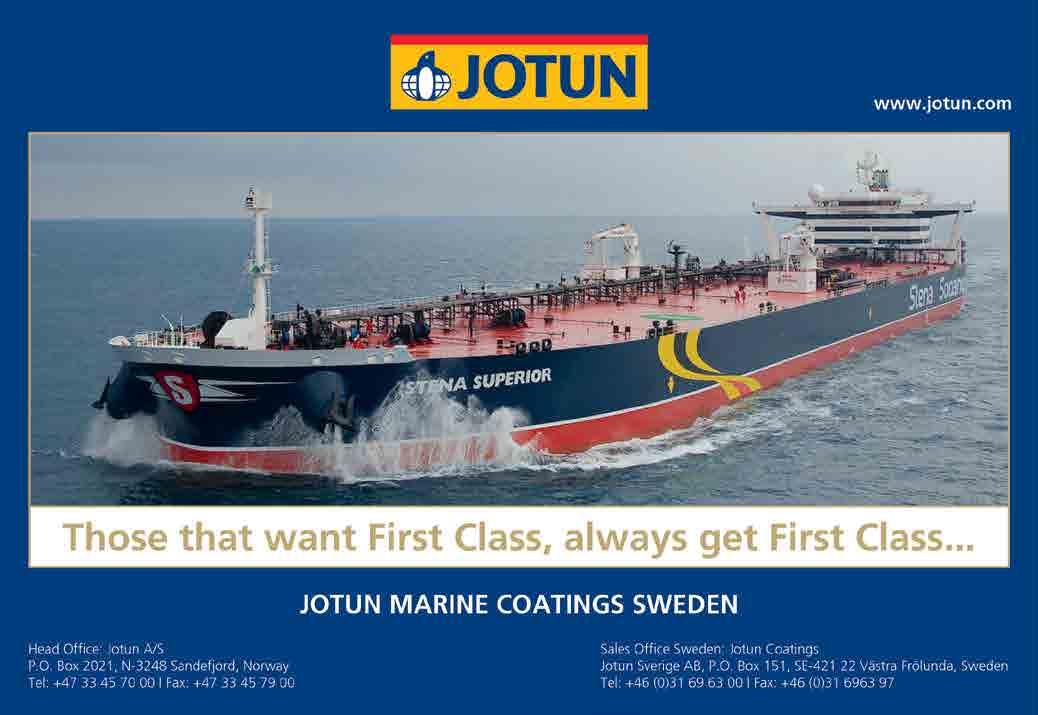
a total of 18 cargo tanks of 3,000 m3 capacity.
Stena Teknik, working with Guangzhou Shipyard in China, has succeeded in developing a design that is probably the most energy efficient Eco MR Tanker existing today. Completely new and revolutionary hull lines together with specially designed propeller, rudders, engines, exhaust gas energy recovery and onboard systems will reduce the overall energy consumption to a minimum. “We estimate that the fuel consumption of the IMOIIMAX will be less than 20 tonnes per day at 12.5 knots. That’s 20 to 30 per cent less than was achievable only five years ago,” says Erik Hanell.
Thanks to the eighteen cargo tanks arrangement no single tank is larger than 3,000 m3 which means that the IMOIIMAX can load a full IMO 2 cargo in each tank. High performing well proven cargo tank coating ensure the charterer will have full flexibility to carry an extensive spectrum of products and chemicals at desired temperatures. Tank cleaning on the new vessels is carried out with clean nitrogen, produced by a nitrogen generator, rather than with traditional inert flue gas. The faster tank cleaning this makes possible will significantly reduce the time between discharge and loading.

Partners for growth
In early 2011 Stena Bulk consolidated all its MR business in a joint venture with the Danish shipping company Weco, creating a new company, Stena Weco. Weco was already the market leader in the transportation of special-type products such as, edible oils and palm oil. The JV doubled the common MR fleet to a critical mass of some 35 tankers within the segment and added Stena’s existing strength in the transport of petroleum products and chemicals.
“Since Stena Weco was established we have increased the number of ships it operates to more than 50 and the new IMOIIMAX will be a key vessel in its future operations,” says Erik Hanell. “With offices in Europe, USA and Singapore we have significantly increased our global trading area and our large and flexible MR fleet now services the world-wide requirements of our customers. Stena Weco has proved itself to be the right concept ant the right time.”
In June 2012 Stena Weco itself entered into a joint venture with Golden AgriResources Ltd (GAR), the Indonesian palm oil plantation company; GAR produces palm oil from a total planted area of more than 400,000 hectares and processes it into palm-based edible oil and fat. The 50-50 JV, Golden Stena Weco, was aimed at providing an overall solution for the international transportation of GAR’s palm oil products.
Now Stena Bulk and GAR have set up a new JV, Golden Stena Bulk, which initially took over four product tankers ordered by Stena Bulk. These vessels were deployed in Stena Weco’s logistics system in the global market. The partnership now has a total of six ships,.
“Golden Stena Weco can be seen as the second step in our collaboration with GAR,” explains Erik Hanell. “For us it’s also a gateway to Asia. Such strategic partnerships are a welltried concept for us and involve coordinating complementary assets and experience. With GAR’s robust network and intimate knowledge of the region, this partnership gives us greater access to the Southeast Asian market as well as to local competencies.”
Through the ice
In autumn 2013 Stena Bulk took another important step towards expanding its partnerships in Asia with the arrival of the Stena Polaris at the port of Yousu in South Korea after a voyage through the icy North-East Passage along Russia’s northern coast. The voyage was a joint project between Stena Bulk and Hyundai Glovis, the shipping arm of the Hyundai Group. It began on 17 September at the port of Luga in the Gulf of Finland, where the Stena Polaris loaded 44,000 tons of naphtha.
The Stena Polaris is built to ice class 1A specifications, which means that it is equipped to sail in ice-covered waters where broken ice can be up to 0.8m thick. In addition to an ice-strengthened hull her rudder and propellers are adapted for operation in icy waters and her main engines modified to deliver greater power.
“In fact this was the eighth time we have made this voyage through the North-East Passage but it is the first time to Korea,” says Erik Hanell. “It is also the first project in which technology and operational knowhow have been transferred from Stena to Hyundai Glovis. It shows we can speed up the freight routes to and from the Northern Asia region and is the beginning of an important collaboration towards realising our strategy to expand in this region together with good partners.” n
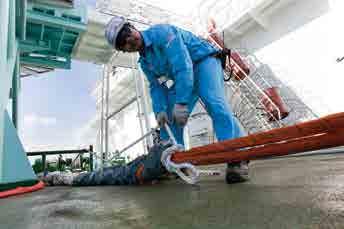
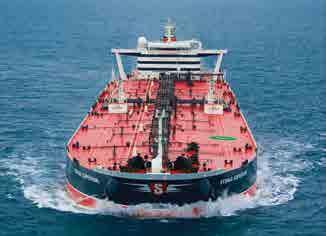
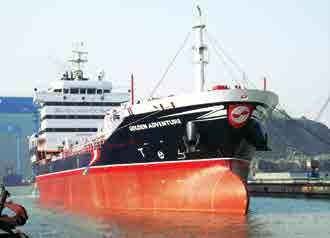

ORGANISING YOUR SPACE
A vertically integrated production system, regular investments in R&D, a continuous Innovation Process, productivity run rate and a wide range of products are the factors which have determined the success of Metalsistem SpA - Italy’s largest manufacturer of modular storage systems and integrated material handling solutions. Barbara Rossi talked to Mr Carlo Schiavini, who became the company’s CEO in May last year.
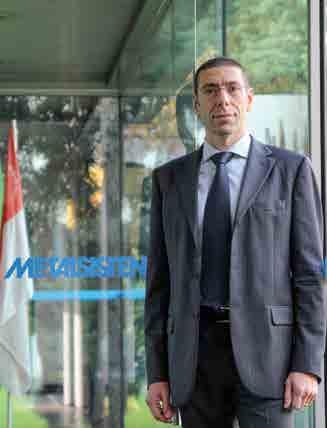

The Metalsistem group was established in 1970 in Rovereto, near the northern Italian town of Trento, by Antonello Briosi, who is still the President of the Metalsistem Group. At first the company designed and produced machines for the cold profiling of metals but soon, thanks to the experience gathered and the numerous innovative patents developed, it started to manufacture cold form zinc coated profiles. Over the years, the success obtained in these activities led the company to expand its activity to the production of actual components (modular shelving systems), manufactured on self-produced machines.
“We are very independent, thanks to our vertical integration. In fact, within our group we manufacture the machines that we then use for manufacturing our own products” said Mr Schiavini.
The group is today present in over 70 countries and has an aggregate turnover of €260 million. The first of its two main areas of activity is warehouse logistics (with a range of products serving the entire spectrum of warehouses solutions) through the Metalsistem brand, which accounts for about 80 per cent of turnover. This is followed by display & shop fitting solutions, offered through the SIDAC brand, which generates 20 per cent of turnover. The sectors served by the SIDAC range include food and non food outlets, supermarket chains and individual retail shops.
Alongside these two main fields of specialisation, the group is also engaged in making furnishing products and components for the alternative energy sector. With regard to the latter, as well as producing modular steel structures for photovoltaic panels, the company has recently presented a medium wind turbine prototype, ‘Libellula’ (Dragonfly), designed for Enel Green Power by the famous architect Renzo Piano. This turbine offers subtle elegance and up to 55kW of power; it is sensitive to low speed winds and has a low environmental impact.
All production takes place in Italy, at four plants. First of all, there is the Rovereto facility, which houses the headquarters, as well as the production plant for the Metalsistem storage systems and material handling solutions; then there is the Treviso works where roll forming and automation machines, designed for the production process, are manufactured. The two sites located in the Brescia area, in Gambara and Gussago respectively, are engaged in manufacturing the SIDAC products. “Our automated production facilities for the cold profiling of metals have enabled us to achieve one of the highest levels of productivity in the world today.”
While production is entirely Italian based, the sales network has a wide global coverage. Export is very important, reaching 70 per cent in terms of the logistics range and 40 per cent for display and shop fitting solutions.
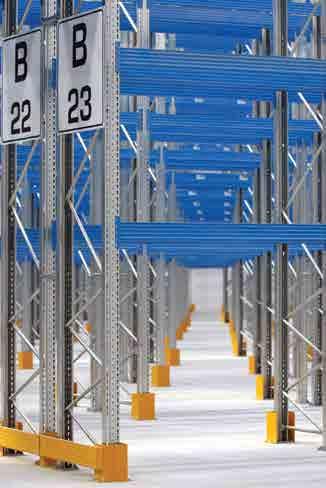
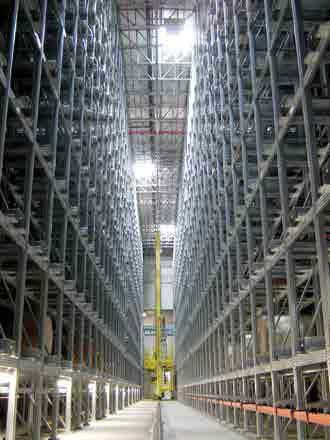
A strong focus on R&D
“For us R&D has always been and still is extremely important, integrating both production process and products. For this reason we regularly invest in this area, for which we have a dedicated internal division, which works on both of the two previously mentioned levels, making us particularly effective. We are continuously optimising our products, so much so that we produce a weekly internal newsletter to keep all our Metalsistem Group network informed on product development and new additions to our range. Recently a lot of work has been done on anti-seismic components (mainly for the logistics range). Our high auto-