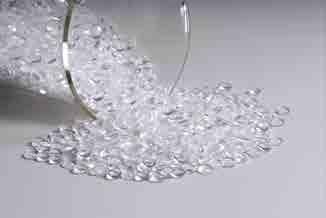
3 minute read
Moving on Relocations and expansions
NEWS
MOVINGON
Relocations and expansions across Europe
Fortum to invest in a new combined heat and power plant in Zabrze, Poland
Fortum has decided to build a new multifuel combined heat and power (CHP) plant in Zabrze, Poland. The total value of the investment is approximately EUR 200 million (PLN 870 million). The new plant is planned to start commercial operations by the end of 2018, providing district heating to some 70,000 households in Zabrze and Bytom.
The new plant will primarily be fuelled by refuse derived fuel (RDF) and coal but can also use biomass and a mixture of fuels. The amount of RDF can be up to 50% of the total fuel usage. The residential and industrial waste for RDF is sourced locally. The new plant will replace the existing purely coal-fired, outdated units in Zabrze and Bytom. The investment is expected to significantly improve the efficiency of operations and reduce CO2 and other emissions in the area. Visit: www.fortum.com
WACKER starts up new production plant for Polyvinyl Acetate in China
Wacker Chemie AG has inaugurated its new production plant for foodgrade polyvinyl acetate (PVAc) solid resins at its Nanjing site (Jiangsu province) in China. With an annual capacity of 20,000 metric tons, the plant is the largest of its kind in Asia and it is certified to the highest food standards. PVAc solid resins find use in the manufacture of gumbase for chewing gum. With this investment, WACKER intends to secure sufficient long-term capacity to meet the strong demand for PVAc solid resins and thus continue to offer its Asia-Pacific customers high supply security and product quality. The Group invested around €20 million in the expansion project. WACKER is thereby strengthening its position as the worldís leading manufacturer of PVAc solid resins for the chewing-gum industry. Auguste Willems, Wacker Chemie AG Executive Board member, said, “Asia has become one of the biggest markets for chewing gum. Thanks to the new plant, we can keep pace with our customers’ strong demand for high-quality polyvinyl acetate solid resins in the region in the future.” Visit: www.wacker.com
New water treatment plant at Lecta’s Zaragoza Mill
Lecta has successfully completed a new phase in its ambitious investment plan at its Zaragoza mill, totalling some 23 million euros, aimed at reducing its environmental impact. Lectaís goal is that the Zaragoza site become a benchmark for sustainability in the paper industry.
Following the installation of two new electrostatic precipitators in the millís recovery boilers, resulting in a 74% reduction in solid particle emissions, Lecta has started up a biological water purification plant with excellent results. In the first few months, there has already been a drastic reduction in effluent load, with values far below the legal limits. Chemical Oxygen Demand (COD) values were cut nearly in half, Total Suspended Solids (TSS) have decreased by 36% and in the case of Biochemical Oxygen Demand (BOD5), the decrease was even more pronounced: 72% compared to the average observed in 2013. Zaragoza is Lectaís only integrated mill, manufacturing both pulp and paper with a total production capacity of 500,000 tons of pulp, coated paper, uncoated paper and base paper for specialty products. Visit: www.lecta.com
Krantech expands in subsea market
Krantech Holdings Ltd have been awarded a UK Regional Growth Fund (RGF) Grant of £300K, for a £1.5 million investment of a 10,000 square foot, New Manufacturing Unit (additional to the existing workshop), based at Colliery Close, Staveley, Chesterfield.
The RGF grant is based around the creation of 15 new jobs (in addition to the circa 50 current employees of Krantech Holdings Ltd) and the New Manufacturing Unit will complement the existing medium/heavy fabrication workshop. Krantech Holdings Ltd predominant Client base is in the Subsea Oil/Gas market sector and the New Manufacturing Unit will fulfil additional requirements for precision CNC machining and large machining capacities. Visit: www.krantech.com
ThyssenKrupp Aerospace service centre in India
ThyssenKrupp Aerospace has commissioned its first location in India. On a total area of around 3,300 m≤ the new Service Center in Bangalore will store the entire range of materials used in the aviation industry: aluminum, titanium and steel in the shape of bars, plate and sheet as well as round rods.
As one of the foremost global providers in the market for production and raw materials, processing services and the management of complex supply chains, ThyssenKrupp Aerospace supplies the required materials just in time, cut and machined precisely to customer specifications
“Our new Service Center in Bangalore offers us the ideal opportunity for an even closer relationship with India’s dynamically developing aerospace sector,” said J¸rgen Funke, Chief Executive Officer of ThyssenKrupp Aerospace. Visit: www.thyssenkrupp.com