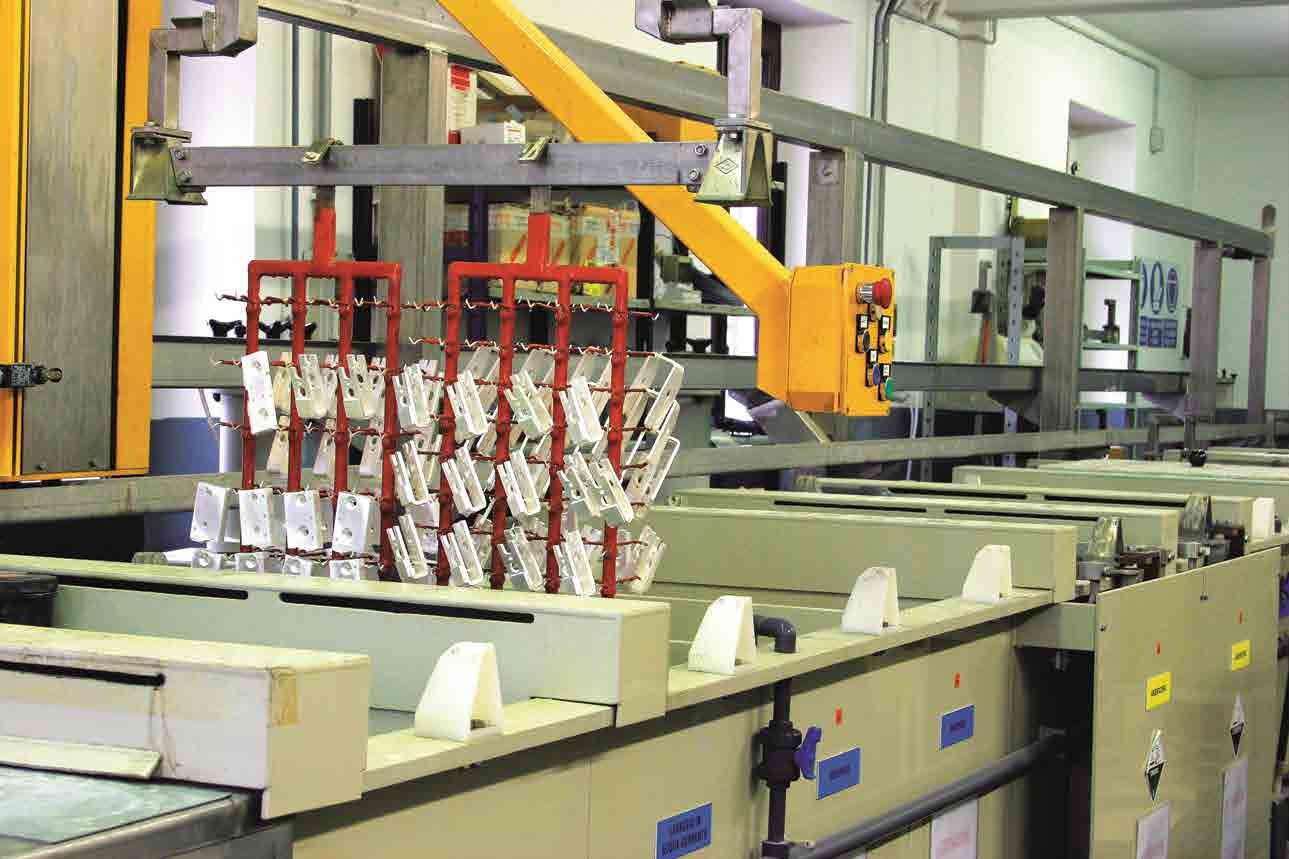
5 minute read
Italian leaders in electron beam welding OMCD Celsia
ITALIAN LEADERS IN
ELECTRON BEAM WELDING
Celsia will be present at Hannover Messe 2015 (Hall 12, stand D 35), together with its ANIE (National federation of electro-technical and electronic companies) co-members. The Italian company, which is part of the OMCD Group, is particularly proud of its use of electron beam welding (EBW) technology. Barbara Rossi reports.
Celsia is based near Lake Maggiore, in the Verbania area of northern Italy, situated between Milan and the Swiss border (specifically in Anzola d’Ossola). Established in 1963 by by Silvio Tedeschi and Antonio Bionda, the company started out as a manufacturer of low-voltage electrical contacts, aided by the know-how and the technology of its associated company, F.I.L.M.S, which had been active in the sinters sector since 1955. Towards the end of the 1960s, Celsia began producing composite materials made through infiltration (silver/ tungsten and copper/tungsten), both for the electrical and electro-mechanic sectors.
Today, the ISO 9001 and ISO 14001 certified company has a range of tungsten-based sinters, brazing alloys and electrical contacts for medium and high voltage applications. Celsia products can be used in a wide variety of fields, namely mechanics, electro-mechanics and high precision mechanics. The company supplies some very high-profile clients, including ABB, Schneider, Siemens, Luxottica, Gerdau and Toshiba, amongst others. It has a modern and efficient R&D laboratory to support both production quality control and new product development. It is also equipped with innovative machinery, such as that for electron beam welding.
In terms of sintered parts, the company manufactures electrodes for the production of electro-welded wire mesh, electrodes for diamond tools sharpening, and electrodes for EDM die-sinking machines. With regard to electrical contacts, the Celsia range includes electrical contacts for medium and high voltage switches and electrical contacts for medium and high voltage disconnecting devices. Finally, for brazing alloys, the products on offer supply the goldsmith, glasses-making, clock-making and precision mechanics industries.
Globally leading companies
Celsia and F.I.L.M.S. are two companies merged into one to offer the highest level of efficiency, competitiveness and reliability. Both belong to the OMCD group, which started its activity in 1967 and comprises several companies working in the field of hard metal sintering. Today the group, also based in Anzola d’Ossola, has six plants in Europe and South America, employs almost 250 people and has been led by the Tedeschi family for two generations.
Celsia is a trustworthy partner focused on the needs of its clients. It operates on the Italian and foreign markets, either directly or indirectly, through its subsidiaries in Brazil and Bulgaria.
It is very strong on scrap metal recycling, through which 25 per cent of the sourcing needs of the group are met. This offers clear advantages in terms of freedom from production policies and the possible monopoly of the Chinese and sector multinationals.
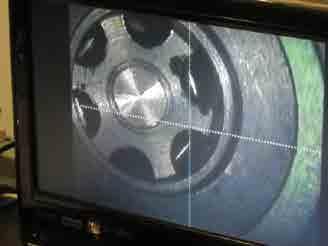
EBW
As mentioned above, Celsia is particularly proud of the technologies it employs. As well as galvanisation, a process through which items or components are coated with a thin metallic layer, it employs electron beam welding. EBW is a fusion welding technology in
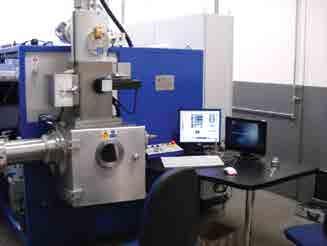

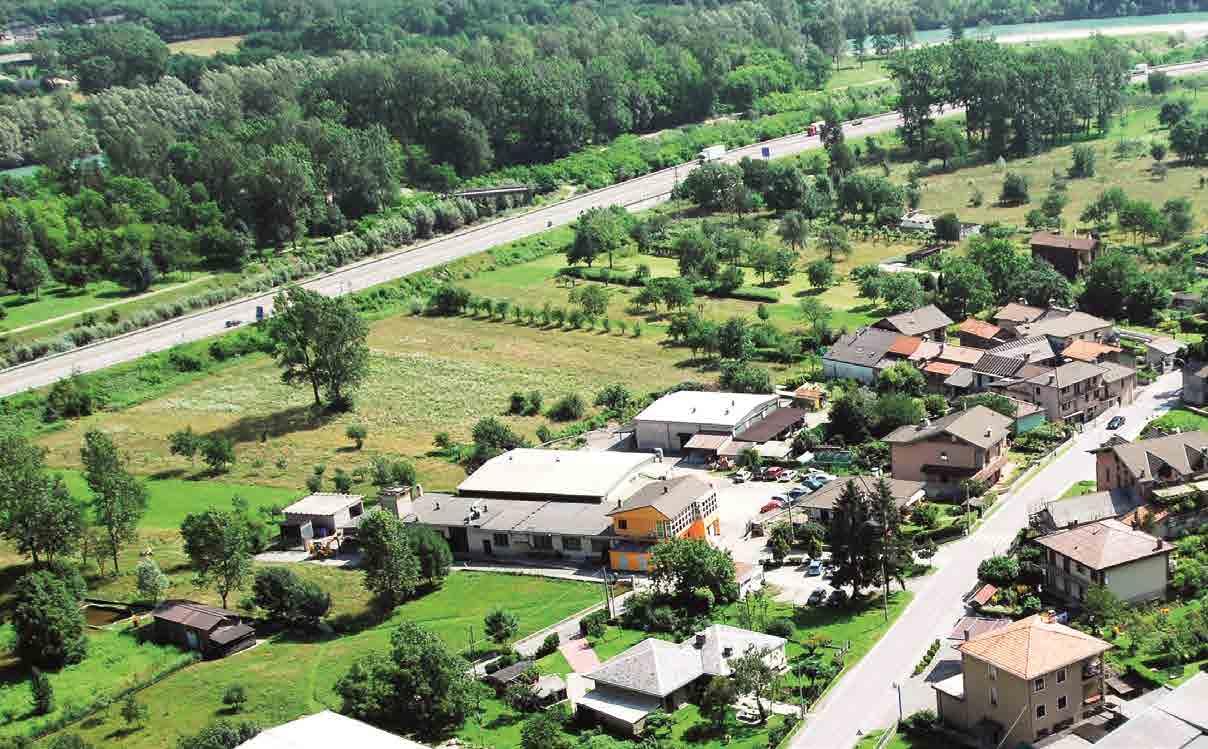
which an electron beam hits at high speed the surface of the welding pieces and penetrates into their material. The kinetic energy of electrons is transformed into thermal energy, which can be used for materials processing. The electrons are emitted by a heated gun. A vacuum must be produced and maintained in the entire beam generator area and in the working chamber in order to avoid too strong a divergence of the electron beam caused by the collision of the electrons with the air molecules.
The high energy concentration in the focal point of the electron beam results in a very high power density (the power density is 100 to 1000 times higher than in arc welding methods) and means it is possible to weld different materials with each other. Furthermore, the electron beam is, by means of the electromagnetic fields, deflected almost without inertia, which leads to the generation of extremely high-frequency oscillation movements entailing different welding advantages. This means virtually distortionfree joining of finished products can be achieved, as through the high power density of the electron beam the energy input into the part is relatively low. In addition to this, automated welding in a vacuum with electrically controllable welding parameters means extremely consistent weld quality. Moreover, the high welding speeds and the favourable total efficiency allow for high productivity with a relatively low energy consumption.
The CVE Model CW60.15 recently purchased by Celsia has some outstanding features, including a 60 kV electron gun with a turbo-molecular pumping system, a filament alignment jig for accurate and repeatable filament change, a 15 kW switch mode power supply and beam deflection. Furtheremore, it also boasts a focus & function generator, a 450mm cube chamber with hinged door opening to the left and chamber extension, and an enhanced fully automatic pumping system for operating in the 10-4 mbar range. In addition to this, it is equipped with an external rotary manipulator, an external pneumatic tailstock and a PC based operator interface with colour monitor, keyboard, mouse and data logging.
The machine has two separate pumping systems for the work chamber and the electron gun. The chamber can operate in either high vacuum (10-4 mbar range) or low vacuum (10-2 mbar range). Another feature is that an isolating valve is incorporated in the gun column so that the gun is maintained at high vacuum when the chamber is vented. This model enables the welding of materials with a thickness of up to 40mm. Moreover, the distance between the welding gun and the work-piece (the stand-off distance) can reach 70cm. n

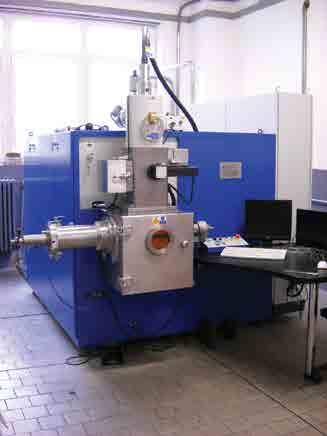