
6 minute read
Leading powder metal innovation
The world continues to change and GKN Sinter Metals is at the forefront of this change, with intelligent product solutions. Felicity Landon reports on the latest innovations from this global brand.

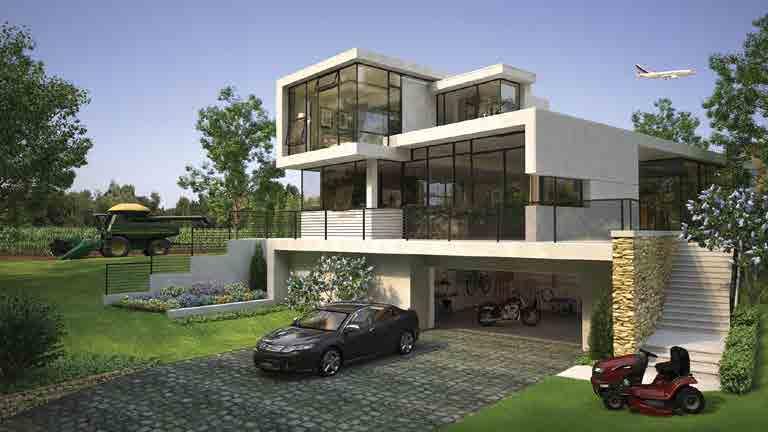
GKN Sinter Metals is the world’s largest producer of precision powder metal products. Its range of expertise, technologies, products, services and applications is immense. So is its global footprint – GKN Sinter Metals employs an experienced team of around 6500 people at more than 30 locations in 14 countries across five continents. It has production sites in Germany, Italy, South Africa, India, China, Brazil, Canada and the United States.
Among the company’s core competences are the manufacturing of highly complex sintered components by classical powder pressing and metal injection moulding, as well as powder forging and the production of sintered filters and bearings.
To open up new areas of industrial and automotive applications for powder metal (PM) components, GKN has focused its research and development activities on the manufacturing and processing of soft magnetic powders and sintered materials. This focus has delivered significant success, with GKN gradually optimising the magnetic, electrical and mechanical properties of its products so that it can manufacture even more energy-efficient components in the future.
At the Hannover Messe exhibition, the GKN Singer Metals stand will focus strongly on a collection of processes and intelligent product solutions – effectively a slice of expertise of a company whose history goes back to the 1930s. Leading the pack will be Soft Magnetic Composites for E-Motors, followed by Metal Injection Moulding Components, Design for Power Metallurgy, Sintered Bearings and Porous Metal Filters. Soft Magnetic Composites (SMC) for e-motors
Unconventional designs of high performance parts and assemblies usually require a great degree of magnetic properties in conjunction with optimum material utilisation. However, generally these designs cannot be implemented because of the prohibitive production restriction involved in conventional manufacturing processes.
“Since the use of powder metallurgical soft magnetic materials is still relatively unknown, the implementation of new components designs using this technology has been limited,” says Nils Bornemann, Global Business Development Manager.
“By using PM technology, the previous limits can be redefined, thanks to an increased freedom of part design and a significant reduction of manufacturing costs. The implementation of net shape and high density sintered components creates valueadded benefits, both from a commercial and a technological perspective, to which end customers in multiple industries can profit in cooperation with us.”
Metal Injection Moulding (MIM) components
GKN Sinter Metals plant in Bad Langensalza, Germany, is the only site in the group that produces Metal Injection Moulded (MIM) parts. It is among Europe’s top three MIM parts manufacturers.
There is a heavy emphasis on automotive applications in this field, reflecting the original focus of the plant – MIM products manufactured include numerous parts such as turbocharger components, lock caps, parts of the fuel injection system, sensor housings and valve train systems. The materials used are typically low alloy steels and the parts are case hardened.
“GKN is seeing a trend towards more complex part design in the automotive industry, integrating more functions into a component, and these complex parts can best be produced in large volumes by Metal Injection Moulding,” says Bad Langensalza plant manager Daniel Bader. “Our technology also excels over Investment Casting, thanks to higher strength and better dimensional accuracy.”
Non-automotive applications account for roughly 10 per cent of MIM production, including bicycle transmissions and an increasing presence in the medical sector – for example, the parts in a prosthetic knee joint.
Non-automotive applications have been identified as a promising market for Metal Injection Moulding. As an experienced automotive supplier GKN Sinter Metals will utilise its capabilities for the benefit of industrial customers.
Design for Powder Metallurgy (DPM)
DPM is the process of a creating a tailored component design that presents the best solution for a given application. It is initiated by a customer or by GKN, and delivers the required performance, geometric, dimensional, size or weight objectives and can economically be produced best by PM technology.
The process starts with optimizing of engineered metal powders, moving through multi-part substitution, extreme forming, 3D
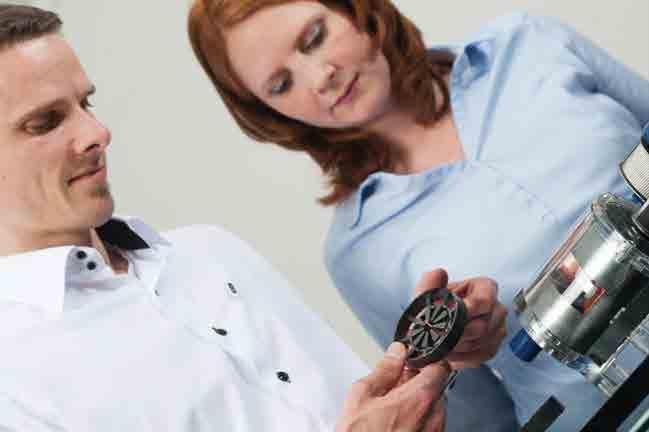
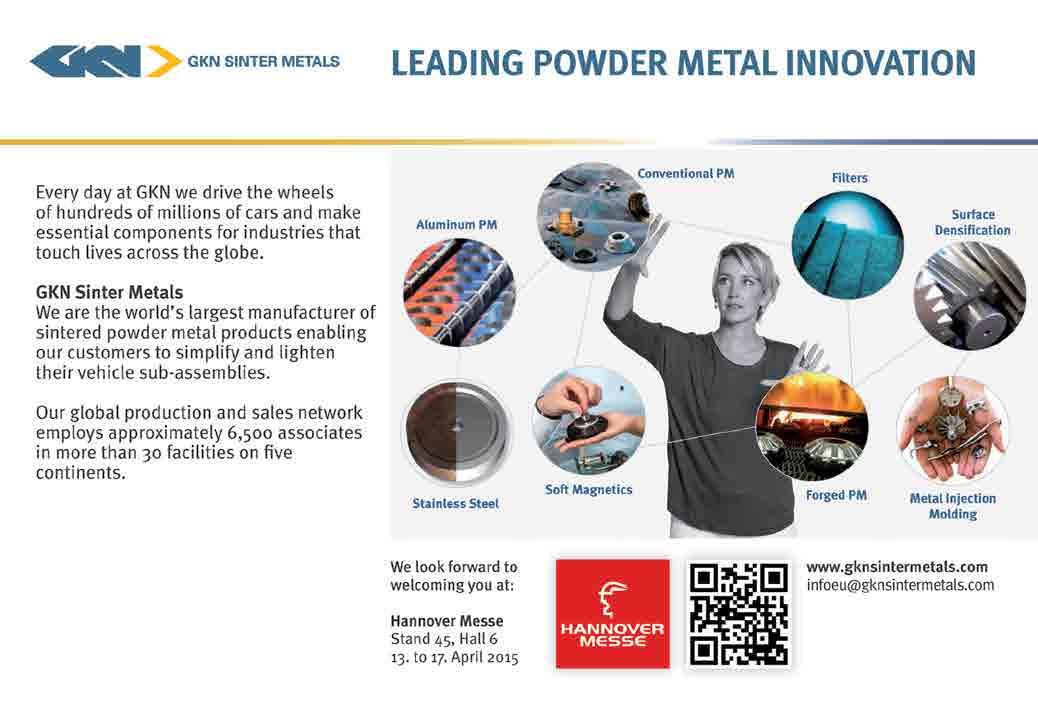
undercutting, unique joining and inventive processes – to creative designs. DPM delivers innovative solutions for all automotive and industrial applications, e.g. ranging from sensor fixtures or seat adjustments to external gear pumps and even for orthopedic components for artificial limbs.
Sintered Bearings
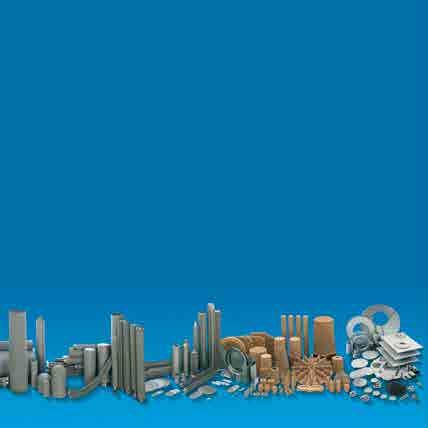
Sintered bearings have been successful for decades in numerous applications, thanks to their high precision and cost efficiency. Their properties are characterised by selflubrication and freedom from maintenance – even over very long service periods. Powder metallurgy allows the production of a variety of geometries with excellent precision, which is reflected by the extremely smooth and quiet running performance in the electric motor.
In conventional applications, porous bearings are impregnated with a liquid lubricant so that a hydrodynamic lubricating film is established during operation. Friction is minimised by the build-up of hydrodynamic pressure and abrasive wear is thereby prevented. Wolfgang Pahl, head of GKN Sinter Metals Global Development Centre for Bearings, says: “Such hydrodynamic sintered bearings have been used for many years in the automotive industry, in audio and video equipment, office machinery, in the toy industry, in computer peripherals and apparatus engineering, in domestic appliances, and in power tools. According to estimates of the PM industry, these self-lubricating bearings are used in small motors annually in the tens of billions.”
Despite all competing technologies and materials the market share for sintered bearings is growing steadily – supported by new developments in solid lubrication, material and lubricant development. GKN supplies global and local markets with sintered bearings. Its global development centre is located at Brunico, in South Tyrol, Italy. Here, new materials for a variety of applications are developed in line with market requirements. These developments are supported by cooperation with the University of Trento and AC²T, the Austrian Centre of Excellence in Tribology.
Porous Metal Filters
As the leading manufacturer of porous sinter metal products, GKN Sinter Metals offers a variety of solutions to meet customers’ requirements. Its products are applied in gas and liquid filtration, dampening, sparging, sensor protection, bulk handling and many more, and it offers solutions for high temperature and corrosive environments.
Sintered filter elements made of stainless steels, bronze, nickel based alloys, titanium and several special alloys can be manufactured seamless up to 1600mm in length. Larger elements are assembled by the inhouse welding shop. The range of possible filter grades is from 0.1 µm to 200 µm.
At Hannover, GKN Sinter Metals will be displaying a variety of discs, plates, cups, cylinders plates and silencers made of stainless steel and sintered bronze. These products are characterised by their high permeability and mechanical stability. Typically they are applied as filtration elements in pneumatic and hydraulic application. Furthermore, they are in common use as flame arrestors, sensor protectors and flow control elements. n